Методика определения составляющих погрешности механической обработки детали - дроссель



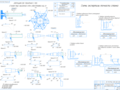
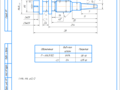
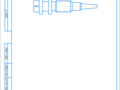
- Добавлен: 25.01.2023
- Размер: 1 MB
- Закачек: 0
Описание
Состав проекта
![]() |
![]() |
![]() ![]() ![]() ![]() |
![]() ![]() ![]() ![]() |
![]() ![]() ![]() ![]() |
![]() ![]() ![]() |
![]() ![]() ![]() |
![]() ![]() ![]() |
![]() ![]() ![]() |
![]() ![]() ![]() |
![]() ![]() ![]() |
Дополнительная информация
Дроссель.cdw

токар ленусик.cdw

шейки шпинделя станка.
Проверка перпендикулярности
торцевой поверхности фланца (буртика)
шпинделя оси его вращения.
Проверка осевого биения
Проверка правильности расположения
осей отверстий шпинделя и пиноли задней
с механическим крепле-
Отрезной специальнный резец с
закругленными краями режущей
КР .МТЭТМиС 2010 .002. 002
Технологическая наладка
на токарную операцию
Схемы экспертизы точности
ПР-поворот резцедержателя
ОПЕРАЦИЯ 010 ТОКАРНАЯ С ЧПУ
СТАНОК МОД. 16К20Ф30 СЧПУ ЭЛЕКТРОНИКА НЦ-31
Схемы экспертизы точности станка
Резец проходной упорный
Дроссель 1.cdw

МУ 2008.2.doc
Севастопольский национальный технический университет
Методические указания
к выполнению практических занятий
по дисциплинам «Производственные процессы и
оборудование объектов автоматизации» и «Типовые
технологические объекты и процессы производства»
для студентов направления 6.0925 «Автоматизация и
компьютерно-интегрированные технологии» всех форм обучения
Методические указания к выполнению практических занятий по дисциплинам «Производственные процессы и оборудование объектов автоматизации» и «Типовые технологические объекты и процессы производства» для студентов направления 6.0925 «Автоматизация и компьютерно-интегрированные технологии» всех форм обученияА.В. Троценко. – Севастополь: Издательство СевНТУ 2008. – 32 с.
Целью методических указаний является оказание помощи студентам при выполнении практических занятий.
Методические указания рассмотрены и утверждены на заседании кафедры «Технология машиностроения» 2008 г протокол № 9 от 29.01.08.
Допущено учебно-методическим центром и научно-методическим советом СевНТУ в качестве методических указаний.
Рецензент: Карлов А.Г. доцент кафедры «Автоматизация технологических процессов и производств» канд. техн. наук.
Ответственный за выпуск: Ю.К. Новоселов зав. кафедрой «Технология машиностроения» доктор техн. наук профессор.
Практическое занятие № 1
Определение типа производства .4
Практическое занятие № 2
Обоснование способа получения исходной заготовки ..7
Практическое занятие № 3
Определение припусков на механическую обработку . 13
Практическое занятие № 4
Анализ схем базирования детали 20
Практическое занятие № 5
Определение погрешности механической обработки 23
Библиографический список . 31
ПРАКТИЧЕСКОЕ ЗАНЯТИЕ № 1
ОПРЕДЕЛЕНИЕ ТИПА ПРОИЗВОДСТВА
Цель занятия. Изучить методику определения и анализа типа
машиностроительного производства.
1.Краткие теоретические сведения
Для предварительного определения типа производства на первоначальной стадии проектирования используют расчетное значение такта выпуска изделий определяемое по формуле
где - действительный годовой фонд времени при работе в одну смену час; m – количество смен работы; N – годовая программа выпуска изделий.
Принято считать что при
– массовое производство;
30 – крупносерийное производство;
60 – среднесерийное производство;
> 60 – мелкосерийное и единичное производство.
Окончательное решение о типе производства принимается на основании расчета коэффициента закрепления операции после составления маршрутной технологии и закрепления операций за оборудованием.
Значение принимается для планового периода равного одному месяцу и определяется по формуле:
где O – число различных операций; P – число рабочих мест на которых выполняются различные операции.
В зависимости от значения принимают
> 4 – при массовом производстве;
10 – при крупносерийном производстве;
20 – при среднесерийном производстве;
40 – при мелкосерийном производстве.
При единичном производстве не регламентируется.
Если задана годовая программа выпуска изделий то необходимо установить соотношение между трудоемкостью выполнения операций и производительностью рабочих мест предназначенных для проведения данного технологического процесса при условии загрузки оборудования в соответствии с нормативными коэффициентами.
Располагая штучным штучно-калькуляционным временем на выполнение каждой операции определяем количество станков
где - нормативный коэффициент загрузки оборудования который принимают равным для мелкосерийного производства – 08 - 09; среднесерийного – 075 - 085; крупносерийного и массового – 065 - 075.
Устанавливают число рабочих мест P округляя до ближайшего большего целого числа полученное значение количества станков . По каждой операции вычисляют значение фактического коэффициента загрузки рабочего места
Количество операций выполняемых на рабочем месте определяют по формуле
Подсчитывают суммарные значения O и P для всех операций определяют и устанавливают тип производства.
2. Порядок выполнения работы
В зависимости от заданной годовой программы выпуска деталей рассчитать такт
выпуска и произвести предварительный выбор типа производства.
Задаться нормативным коэффициентом загрузки оборудования.
Составить маршрутную технологию изготовления детали.
Рассчитать или определить по справочным таблицам штучное штучно-калькуляционное время затраченное на каждую операцию.
Рассчитать коэффициент закрепления операции и определить тип производства.
3. Пример выполнения работы
Определить тип производства детали технологический процесс изготовления которой состоит из трёх операций: токарной t= 24мин протяжной t=1мин зубофрезерной t= 8мин. Годовая программа выпуска N = 60000шт. Действительный годовой фонд рабочего времени Fg = 2015 час. Количество смен m = 2.
Такт выпуска деталей мин.
По предварительному расчёту производство массовое. Принимаем з.н = 07.
Расчётное количество станков составит: для первой операции – 085 второй - 035 третьей - 283.
Принимаем количество станков по операциям: первой-1 второй -1 третьей -3.Фактический коэффициент загрузки оборудования: для первой операции - 085 второй - 035 третьей -094.Количество операций выполняемых на рабочих местах соответственно 121.
Коэффициент закрепления операций
Производство будет массовым.
4. Задание к практической работе
Технологический процесс обработки стального валика в соответствии с лабораторной работой №1. Нормирование операций в соответствии с лабораторной работой №2. Годовая программа выпуска согласно таблицы 1.
Таблица 1 - Годовая программа выпуска
5. Содержание отчёта
Название цель работы.
По заданной программе выпуска определить тип производства.
6. Контрольные вопросы
Как предварительно определяется тип производства.
Методика определения типа производства по коэффициенту закрепления операции.
Дать характеристику единичного и массового типов производства.
Дать характеристику серийного производства.
ПРАКТИЧЕСКОЕ ЗАНЯТИЕ № 2
ОБОСНОВАНИЕ СПОСОБА ПОЛУЧЕНИЯ ИСХОДНОЙ ЗАГОТОВКИ
Цель занятия. Изучить методику теоретического обоснования способа получения заготовок в машиностроительном производстве.
1. Краткие теоретические сведения
Выбор способа получения заготовок в значительной степени определяется типом производства и программой выпуска а также техническими возможностями заготовительных цехов предприятия и возможностями получения прогрессивных заготовок от специализированных предприятий.
Важнейшим фактором определяющим выбор способа получения заготовок является технологические свойства материала (жидкотекучесть способность к пластической деформации свариваемость). Например если деталь изготавливается из серого чугуна то заготовку можно получить только литьем т.к. чугун нельзя обрабатывать давлением и он практически не сваривается. В то же время литые заготовки требуют дополнительной обработки для стабилизации формы и размеров (естественное старение низкотемпературный отжиг и др.).
Необходимо использовать метод получения заготовки который обеспечивает максимальное приближение к готовой детали. Однако при этом в заготовительном производстве увеличиваются расходы на технологическое оборудование и оснастку. Поэтому при выборе следует проводить технико-экономический анализ двух видов производства – заготовительного и механообрабатывающего.
При выборе способа получения заготовок возможны варианты которые по техническим параметрам равноценны. На первом этапе выбора осуществляют предварительную оценку вариантов по основным признакам эффективности
) Коэффициент использования материала
где и - соответственно масса детали и заготовки кг.
Чем больше значение тем при прочих равных условиях технологичнее конструкция заготовки и меньше её себестоимость.
) Снижение материалоемкости
где и - соответственно масса заготовки при базовом и новом вариантах кг; N - годовой объем выпуска деталей шт.
) Трудоемкость изготовления детали
где и - трудоемкость изготовления детали (нчас) или норма штучного времени (мин) соответственно при новом и базовом вариантах.
) Стоимость заготовки и её черновой обработки:
для литой заготовки
где - стоимость основных материалов - стоимость материала заготовки грнкг; - масса отходов на одну деталь кг ; - стоимость отходов грнкг; - стоимость соответственно черновой обработки заготовки кузнечных штамповочных или литейных работ (4)
B - часовая зарплата основных рабочих с учетом коэффициента выполнения норм премий дополнительной зарплаты и отчислений по социальному страхованию грнчас; - штучное время на выполнение соответствующих работ мин.; g - накладные расходы соответствующих цехов %; - стоимость соответственно штампа и формовочной оснастки грн; n - количество заготовок изготовляемых с применением штампа или формовочной оснастки.
Если в стоимость материала заготовки включить расходы связанные с её получением то стоимость заготовки и черновой обработки можно представить в виде
где - приведенная стоимость материала заготовки грн.
Окончательный вывод о целесообразности того или иного варианта получения заготовки делают после сравнения суммарных приведенных затрат рассчитываемых по формуле
где - нормативный коэффициент эффективности равный 015; К - годовые капитальные вложения грн.
Вариант для которого будет меньше считается наиболее целесообразным. При отсутствии дополнительных капитальных вложений определяют экономию по себестоимости
где и - стоимость изготовления деталей из заготовок базового и нового вариантов.
В зависимости от материала детали её формы размеров основных технических характеристик и объема выпуска установить равноценные варианты получения заготовки.
Произвести предварительную оценку эффективности технически равноценных методов получения заготовок по коэффициенту использования материала снижению материалоемкости и трудоемкости изготовления.
Оценить стоимость заготовки и её черновой обработки для каждого из сравниваемых вариантов.
Определить суммарные приведенные затраты для каждого варианта.
Определить экономический эффект для наиболее целесообразного варианта получения заготовки.
3. Задание на практическую работу
Задача 1. Заготовку втулки (рисунок 1) изготовляют из углеродистой стали различными способами (таблица 1).детали 108 кг. Рассчитать технико-экономические показатели различных вариантов получения заготовки при годовом объеме выпуска деталей 5000Экономические показатели вариантов приняты условно. Стоимость материалов заготовки принята с учетом расходов связанных с её получением. Стоимость отходов 80 копкг. Часовая тарифная ставка токаря 36 грн. Накладные расходы механического цеха 100%.
Рисунок 1 – Эскиз втулки
Таблица 1 – Исходные данные
Методы получения заготовок
материала заготовки грнкг
Задача 2. Полый вал (рисунок 2) из углеродистой стали изготовляют различными способами (таблица 2).вала 12 кг. Рассчитать технико-экономические показатели и выбрать наиболее целесообразный способ получения заготовки при годовом объеме выпуска деталей 3000Остальные экономические показатели согласно задачи 1.
Рисунок 2 – Эскиз полого вала
Таблица 2 – Исходные данные
Трудоемкость черновой обработки мин
Приведенная стоимость материала заготовки грнкг
4. Содержание отчета
Название цель работы исходные данные.
В соответствии с условиями задачи 1 или 2 рассчитать основные показатели
эффективности заданного способа получения заготовки.
Представьте эскиз заготовки.
5. Контрольные вопросы
Охарактеризуйте способы получения исходных заготовок в машиностроительном производстве.
Приведите основные признаки эффективности способа получения заготовки.
Приведите основные технические характеристики детали и производства определяющие способ получения заготовки.
Определите суммарные приведенные затраты и экономический эффект для наиболее целесообразного варианта получения заготовки.
ПРАКТИЧЕСКОЕ ЗАНЯТИЕ № 3
ОПРЕДЕЛЕНИЕ ПРИПУСКОВ НА МЕХАНИЧЕСКУЮ ОБРАБОТКУ
Цель занятия. Изучить последовательность определения общих и операционных припусков при механической обработке деталей в машиностроительном производстве.
Припуском называют слой материала удаляемый в процессе механической обработки заготовки для достижения
заданного качества обрабатываемой поверхности. Различают припуски операционные и общий.
Операционный припуск – это слой материала удаляемый с заготовки при выполнении одной технологической операции.
Общий припуск – это слой материала удаляемый с исходной заготовки для получения готовой детали с заданными чертежом параметрами качества.
Общий номинальный припуск z ном определяется разностью номинальных размеров исходной заготовки Д и.з. и готовой детали Д д. и равен сумме номинальных припусков z i ном на отдельные операции
где n – общее количество операций обработки детали.
Определение общих припусков расчетно-аналитическим методом базируется на расчёте минимальных операционных припусков каждый из которых содержит составляющие обусловленные соответствующими погрешностями обработки (рис.1).
Рисунок 1 – Составляющие минимального операционного припуска
Расчётные формулы для определения минимального операционного припуска на обработку:
поверхностей вращения 2 z i min и их торцов z i min
плоских поверхностей
где: R z i – погрешность установки возникающая на выполняемой операции.
Значения составляющих минимального припуска приведены в справочной литературе.
После определения минимальных припусков устанавливают размеры максимальных операционных припусков которые обусловлены операционными допусками на получаемые размеры и методом достижения точности механической обработки.
При работе на предварительно настроенных станках по методу автоматического получения размеров за один проход при превалирующем влиянии на погрешность обработки упругих деформаций технологической системы схема расположения операционных припусков для чернового и чистового точения вала представлена на рис.2а.
где i-1 и i - соответственно допуски для предшествующей и выполняемой операции.
Размер исходной заготовки определяем по формуле для вала
где Д д.m ЕI и.з. – нижнее отклонение исходной заготовки часть допуска в металл.
При работе по методу пробных ходов и промеров схема расположения припусков и допусков представлена на рис. 2б. При этом
После округления операционных размеров в большую (для вала) сторону производим перерасчёт номинальных и максимальных припусков которые используем для определения режимов резания выбора технологической оснастки металлорежущего инструмента и оборудования.
Ознакомиться с чертежом детали.
Определить поверхность на которую необходимо
Установить последовательность обработки
выбранной поверхности (составить маршрутную технологию).
Произвести расчет операционных припусков и составить схему расположения припусков и допусков для обработки по методу пробных ходов и автоматического получения размеров.
Рисунок 2 – Схема расположения припусков и допусков на
токарную обработку вала: а) по методу автоматического получения размеров; б) по методу пробных ходов и промеров
Определить диаметр исходной заготовки и фактические припуски для первой операции.
Определить операционные припуски и размеры стального вала Д = 45h8 1 = 39 мкм L = 100 мм R z = 32 мкм при черновом и чистовом точении. Исходная заготовка – прокат обычной точности. По справочным данным: ES = 04 мм EI = -07 мм R z = 150 мкм Т = 250 мкм. Погрешность формы: удельная кривизна Δ к = 012 мкммм; общая кривизна заготовки обрабатываемой в центрах
Погрешность установки: смещение оси заготовки в результате погрешности зацентровки
где з – допуск на диаметр базовой поверхности заготовки использованной для центрирования мм; з = 11 мм.
Заготовка после черновой обработки: погрешность по поле допуска 2 = 160 мкм; R z = 20 мкм; Т = 30 мкм; погрешность формы с уточнением 006 будет равна ρ к2 = 006. 6 = 036 мкм = 0; погрешность установки обусловленная биением y2 = 100 мкм.
Расчет припусков и операционных размеров производим в направлении от готовой детали к исходной заготовке.
Номинальный припуск
Максимальный припуск при обработке по методу пробных ходов и промеров
по методу автоматического получения размеров
Номинальный операционный размер для чистового точения согласно рис. 2а
Диаметр исходной заготовки
По сортаменту на прокат уточняем диаметр исходной заготовки При этом фактические размеры припуска на
4. Задание к выполнению работы
Определить операционные припуски и размеры
детали и исходной заготовки. Деталь – вал заготовка – прокат обычной точности. Обработка – черновое и чистовое точение цилиндрической поверхности на предварительно настроенных станках по методу автоматического получения размеров. Исходные данные – см. таблицу 1.
Составить схему расположения припусков и допусков.
5. Содержание отчета
Расчет припусков и размеров исходной заготовки.
Схема расположения припусков и допусков по
методу автоматического получения размеров на настроенных станках.
Таблица 1 – Исходные данные мм
Дать понятия припуска операционного общего минимального номинального и максимального припусков.
Охарактеризуйте на примерах составляющие минимального припуска заготовки.
Опишите схемы расположения припусков и допусков при обработке по методу пробных ходов и методу автоматического получения размеров.
Пример расчёта размера исходной заготовки.
ПРАКТИЧЕСКОЕ ЗАНЯТИЕ № 4
АНАЛИЗ СХЕМ БАЗИРОВАНИЯ ДЕТАЛИ
Цель занятия. Изучить схемы базирования заготовок на металлорежущем оборудовании в машиностроительном производстве.
Для работы каждой машины в соответствии со служебным назначением необходимо обеспечить определенное взаимное расположение ее деталей и узлов. При обработке на станках заготовки также должны быть правильно ориентированы относительно механизмов и узлов определяющих траектории движения подачи обрабатывающих инструментов.
Задачи взаимной ориентации деталей в сборочной единице или изделии и заготовки на технологическом оборудовании при их изготовлении решаются базированием.
Базирование – это придание детали или заготовке требуемого положения относительно выбранной системы координат.
Для выполнения технологической операции требуется не только осуществить базирование обрабатываемой заготовки но и обеспечить ее неподвижность на весь период обработки. Таким образом необходимо решить две задачи: ориентировку заготовки осуществляемую базированием и создание ее неподвижности достигаемое закреплением. Эти две задачи решаются теоретически одинаковыми методами – посредством наложения определенных связей на возможные перемещения заготовки в пространстве. Связями называются ограничения накладываемые на движения точек твердого тела. В реальных условиях позиционные (геометрические) связи заменяют контактом поверхностей по средством опорных точек число которых должно быть равно числу связей и не превышать 6.
На схеме базирования все опорные точки изображают условными знаками и нумеруют порядковыми номерами начиная с базы на которой располагается наибольшее количество опорных точек.
Схему расположения опорных точек на базах заготовки или изделия называют схемой базирования. В зависимости от того какие технологические задачи решаются в процессе обработки при базировании заготовки в приспособлении или на станке может быть использована одна две или три базы имеющие на себе в общей сложности три четыре пять или шесть опорных точек. Число проекций заготовки или изделия на схеме базирования должно быть достаточным для четкого представления о размещении опорных точек.
В тех случаях когда закрепление заготовки совмещается с опорой (что бывает при использовании для закрепления заготовки кулачкового патрона или разжимной оправки) на операционных эскизах можно указать не только опорные точки на базах но и направление усилий зажима.
Установка заготовки характеризуется выбором рациональной схемы базирования и действием сил закрепления. Обеспечивается это путем применения различных по конструкции механических пневматических электрических вакуумных и других зажимных устройств основанных на использовании сил трения в местах контакта зажимных элементов и заготовки.
Базирование необходимо для всех стадий создания изделия: конструирования изготовления и измерения. Базы разделяют по назначению на три вида: конструкторские технологические и измерительные.
Группу конструкторских баз составляют основные и вспомогательные базы. Это подразделение конструкторских баз действительно как для изображения изделия на чертеже так и изготовленного изделия. Необходимость такого подразделения вытекает из различия роли основных и вспомогательных баз и важности учета этого при выборе конструктивных форм поверхностей деталей задании их относительного положения простановки размеров разработки норм точности и т.д.
Конструкторская – база используемая для определения положения детали или сборочной единицы в изделии. Конструкторские базы подразделяют на основные и вспомогательные.
Технологические базы – это те базы которые используются для определения положения заготовки или изделия в процессе изготовления или ремонта.
Измерительная база – база используемая для определения относительного положения заготовки или изделия и средств измерения.
Установочная база – лишающая заготовку или изделие трех степеней свободы – перемещения вдоль одной координатной оси и поворотов вокруг двух других осей.
Направляющая база – лишающая заготовку двух степеней свободы – перемещения вдоль одной координатной оси и поворота вокруг другой.
Опорная база – лишающая заготовку или изделие одной степени свободы – перемещения вдоль одной координатной оси или поворота вокруг оси.
Двойная направляющая база– лишающая заготовку или изделие четырех степеней свободы – перемещений вдоль двух координатных осей и поворотов вокруг этих осей.
Двойная опорная база – лишающая заготовку или изделие двух степеней свободы – перемещений вдоль координатных осей.
Явная база – база заготовки или изделия в виде реальной поверхности разметочной риски или точки пересечения рисок.
Скрытая база – условные точки символизирующие связи заготовки с избранной системой координат.
Теоретическая схема базирования может служить заданием для разработчика приспособления (рисунок 1).
Рисунок 1 - Схема базирования детали
Схема базирования а) предполагает использование явной базы отверстия что обеспечивается жесткой цилиндрической оправкой с гайкой. Схема базирования б) предполагает беззазорное базирование с помощью разжимной конусной или цилиндрической с прессовой посадкой оправки.
Разработать маршрутный техпроцесс изготовления детали.
Составить теоретические схемы базирования для каждой операции техпроцесса и привести наименования баз согласно классификации.
3. Содержание отчета
Наименование цель работы.
Схемы базирования для каждой операции технологического процесса.
4. Контрольные вопросы
Характеристика позиционных связей и базирования детали.
Примеры базирования при фрезеровании плоской заготовки.
Классификация баз по числу лишаемых степеней свободы.
Примеры реализации двойной направляющей и двойной опорной баз.
Классификация баз по характеру проявления.
Классификация баз по назначению и области применения.
Основные принципы базирования в технологии машиностроения.
Изобразить теоретическую схему базирования детали на технологической операции.
ПРАКТИЧЕСКОЕ ЗАНЯТИЕ № 5
ОПРЕДЕЛЕНИЕ ПОГРЕШНОСТИ МЕХАНИЧЕСКОЙ ОБРАБОТКИ
Цель занятия. Изучить методику определения систематической и случайной составляющих погрешности механической обработки деталей на универсальном оборудовании и станках с ЧПУ.
Процесс механической обработки заготовок на металлорежущих станках сопровождается погрешностями вызываемыми различными
причинами систематического и случайного характера. Соответственно погрешности возникающие вследствие этих причин делятся на систематические и случайные.
Систематическая погрешность – составляющая погрешности остающаяся постоянной или закономерно изменяющаяся для всех заготовок рассматриваемой партии.
Основными причинами возникновения систематической погрешности являются:
- геометрическая погрешность станка ;
- износ режущего инструмента ;
- температурные деформации технологической системы .
Погрешность обработки обусловленную геометрической погрешностью станка можно определить в первом приближении по формуле
где с – удельное отклонение от параллельности относительного перемещения заготовки и режущего инструмента мкммм; l – длина обрабатываемой поверхности мм.
Погрешность обусловленную износом режущего инструмента определяют по формуле
где U0 - удельный износ инструмента мкмкм; L – длина пути резания км; Lдоп - дополнительный путь резания учитывающий начальный период более интенсивного износа км. Обычно принимают Lдоп = 1 км.
При фрезеровании в связи с прерывистым характером процесса резания удельный износ больше чем при точении
где В - ширина фрезерования мм.
Длина пути резания при токарной обработке партии заготовок
где D – диаметр обрабатываемой поверхности мм; n – число заготовок в партии; S – продольная подача ммоб.
Длина пути резания при торцовом фрезеровании
где SZ – подача фрезы ммзуб; Z – число зубьев фрезы.
Температурные деформации технологической системы при лезвийной обработке упрощенно могут быть приняты равными 15 % от суммарной погрешности.
Общая систематическая погрешность определяется алгебраической суммой составляющих
При обработке тел вращения составляющие погрешности должны быть удвоены.
Случайная погрешность – составляющая погрешности которая для различных заготовок рассматриваемой партии изменяется случайным образом не подчиняясь никакой закономерности.
Случайная погрешность обусловлена совокупностью многих причин случайного характера проявляющих свое действие независимо друг от друга и приводящих к рассеиванию размеров.
Поскольку законы распределения большинства составляющих случайной погрешности неизвестны для создания некоторой гарантии точности принимают условно распределение соответствующее закону Симпсона. Тогда случайная погрешность определяется выражением
Рассмотрим составляющие случайной погрешности.
- погрешность рассеяния размеров связанная с видом обработки и обусловленная нестационарностью процесса резания и податливости технологической системы. Статистические значения как правило приведены в справочной литературе. Составляющую рассеяния размеров обусловленную колебанием упругих деформаций технологической системы вследствие нестабильности составляющей силы резания Ру и податливости системы при обработке можно определить по формуле
где Wma Pyma у – погрешность установки заготовок
где б – погрешность базирования обусловленная несовпадением конструкторской и технологической баз а также особенностями формы опорных поверхностей заготовки и установочных элементов приспособления; з – погрешность закрепления заготовки в приспособлении; n – погрешность приспособления; - погрешность настройки универсального станка определяемая по формуле
где - погрешность регулирования положения режущего инструмента и элементов станка; - погрешность измерения пробных заготовок; - поле рассеяния среднего арифметического размера пробных заготовок (поле смещения центра группирования)
где m – число пробных заготовок.
При обработке на станках с ЧПУ дополнительно возникают погрешности подготовки программы и ее воспроизведения которые в свою очередь определяются погрешностями программирования интерполяции привода перемещения и позиционирования элементов станка. Вместе с тем при работе с корректором из расчета общей погрешности может быть исключена систематическая погрешность обусловленная износом инструмента а также составляющая рассеяния размеров из-за погрешности регулирования . Кроме того в связи с более жесткой конструкцией податливость станков с ЧПУ может быть принята в 2 - 4 раза меньше чем у аналогичных универсальных станков.
Суммарная погрешность механической обработки на металлорежущих станках равна сумме систематической и случайной составляющих
Полученное значение суммарной погрешности должно удовлетворять требованию
где TD – допуск размера обрабатываемой поверхности.
Ознакомиться с условиями базирования и обработки заготовок на
Произвести анализ составляющих общей погрешности обработки.
Произвести расчет суммарной погрешности.
Сравнить полученное значение с допуском на размер выполняемый на данной операции.
Определить процентное содержание каждой составляющей в суммарной погрешности.
Определить суммарную погрешность токарной обработки вала из стали 45. Размеры вала: диаметр 35h11 длина 200 мм. Обработка проводится в центрах на токарно-револьверном станке. На предшествующей операции вал обработан черновым точением по IT14. Партия деталей п = 50 штук. Число пробных деталей т= 4. Условия обработки: резец с пластиной из твердого сплава Т15К6 минимальный припуск 05 мм на сторону подача 03 ммоб скорость резания 130 ммин податливость элементов станка (2—25)10-2 мкмН. Для сплава Т15К6 удельный износ принимаем U0= 6 мкмкм.
Определим погрешность обработки обусловленную геометрической погрешностью станка . Для токарных станков нормальной точности принимаем с = 007 мкммм.
При длине обработки L = 200 мм = 007 · 200 = 14 мкм.
Определим погрешность обусловленную износом резца. Длина пути резания
Определим составляющую рассеяния размера обусловленную колебаниями деформаций технологической системы. Максимальную податливость система имеет при расположении резца посередине вала. При этом
где Wma Wmax заг — максимальная податливость заготовки:
где Е — модуль упругости материала заготовки Е = 2 · 1011 Па; J — момент инерции поперечного сечения; J = 005 D4 м4.
Определим наибольшую и наименьшую составляющие силы резания. Поскольку предварительно заготовка обработана с допуском IT 14 колебание припуска будет равно IT 14 что для заданного диаметра составит 03 мм. Тогда
Для заданного диаметрального размера 2Δ = 121 мкм.
При обработке в центрах погрешность установки равна 0.
Определим погрешность настройки станка на размер. Погрешность измерения принимаем равной 15% допуска на размер:
Погрешность регулирования принимаем равной Δр = 20 мкм. Тогда
Определим случайную составляющую погрешности обработки
Погрешность от температурных деформаций учтем введением коэффициента К = 115 (15% от суммарной погрешности). Таким образом суммарная погрешность обработки
Полученное значение удовлетворяет требованию
ΔΣ TD (1435 мкм 160 мкм).
Определить суммарную погрешность токарной обработки вала из стали 45. Условия обработки: минимальный припуск 05 мм; подача 03 ммоб; скорость резания 130 ммин. Размеры вала и остальные условия обработки согласно таблицы 1.
Таблица 1 — Исходные данные для расчета суммарной погрешности
Допуск на предшеств. операции
закрепления заготовки
Продолжение таблицы 1
Результаты расчёта систематической и случайной составляющих погрешности механической обработки детали.
Расчет суммарной погрешности механической обработки.
Охарактеризуйте комплекс систематических составляющих погрешности механической обработки.
Состав случайных составляющих погрешности обработки детали на станках с ЧПУ.
Оцените процентное соотношение каждой составляющей в суммарной погрешности.
Наметьте пути снижения суммарной погрешности.
Библиографический список
Маталин А.А. Технология машиностроения: учебник А.А. Маталин. — Л.: Машиностроение 1985. — 496с.
Проектирование технологии автоматизированного машиностроения Ред. Ю.М. Соломенцев. — М.: Высш. шк. 1999. — 415с.
Справочник технолога-машиностроителя: В 2 т. Под ред. А.Г. Косиловой Р.К. Мещерякова. — М.: Машиностроение 1990. — 924с.
Сборник задач и упражнений по технологии машиностроения: учеб. пособие В.И. Аверченко и др. под общ. ред. О.А. Горленко. — М.: Машиностроение 1988. — 192с.
Заказ № от « » 2008. Тираж экз
Конт.раб1.doc
Кафедра Технологии машиностроения
Дисциплина: Международная техническая экспертиза технологических систем
Специальность: Металлорежущие станки и системы
на контрольную работу студента
(фамилия имя отчество)
Тема работы: Определение погрешности механической обработки детали и экспертизы точности станка
Исходные данные к работе:
Обрабатываемая деталь -
Число деталей в серии - Число пробных деталей -
Содержание расчетно-пояснительной записки:
1. Маршрутный техпроцесс изготовления детали.
2. Разработка технологической операции. Операция -
3. Анализ составляющих погрешности механической обработки детали.
Международ. экспертиза.docx
СЕВАСТОПОЛЬСКИЙ НАЦИОНАЛЬНЫЙ ТЕХНИЧЕСКИЙ УНИВЕРСИТЕТ
По дисциплине: Международная техническая экспертиза технологических машин и систем
Тема работы: Разработать методику определения составляющих погрешности механической обработки детали – дроссель
Маршрутный ТП изготовления -дроссель . 5
Разработка технологической операции (токарной) ..6
Анализ составляющих погрешности геометрической точности и жесткости 8
Методика и схемы экспертизы геометрической точности и жесткости токарного станка 12
Научно техническая экспертиза представляет собой вид деятельности состоящий в организационном материальном информационном обеспечении и непосредственном проведении профессиональных исследований и оценок объектов имеющих научное или техническое содержание по согласованным критериям отражающих специфику этих объектов.
Разновидности технической экспертизы:
- предварительная. Проводится для выяснения соответствия формальных признаков экспертизы установленным нормами правилам технологической и экологической безопасности требований стандартов и отраслевых нормативов.
- первичная. Предусматривает реализацию всех необходимых мер связанных с подготовкой обоснованных заключений по исследуемым объектам и предусмотренных законодательством. Повторная экспертиза может проводиться или в случае установленных нарушений требований и правил проведения экспертизы или по требованию заказчика экспертизы или автора разработки.
- дополнительная. Производится применительно к объектам в отношении к которым открылись новые технические обстоятельства.
- контрольная. Осуществляется по инициативе заказчика для проверки заключений первичной экспертизы ил по инициативе юридических или физических лиц не согласных с проведением экспертизы.
Техническая экспертиза может иметь статус государственной общественной или специализированной. Государственная экспертиза проводится органы государственной власти или управления а также предприятием или организацией по поручению госорганов. Общественная экспертиза проводится в соответствии с общественным контролем. Специализированная экспертиза проводится по инициативе юридических и физических лиц заинтересованных в экспертных заключениях по частным прошениям.
Материалы и заключения технической экспертизы представляют собой научно-техническую продукцию право собственности которая принадлежит заказчику.
МАРШРУТНЫЙ ТЕХНОЛОГИЧКИЙ ПРОЦЕСС ИЗГОТОВЛЕНИЯ ДЕТАЛИ-ДРОССЕЛЬ
Маршрутный технологический процесс
5 Заготовительная. Отрезаем пруток заданного диаметра и на заданную длину.
0 Транспортная. Транспортируем заготовку к токарному станку .
5 Токарная. Производим обработку на станке с ЧПУ 16К20Ф3 и производим обработку поверхностей .
0 Фрезерная . Фрезируем паз.
5 Слесарная. Убираем с поверхности детали заусенцы.
0 Моечная. В моечной ванне смываем с детали СОЖ .
5 Контрольная. С помощью микрометра контролируем размеры детали.
РАЗРАБОТКА ТЕХНОЛОГИЧЕСКОЙ ОПЕРАЦИИ (ТОКАРНОЙ)
Все операции производим при закреплении заготовки в трех кулачковом патроне.
Расчет режимов резания.[8]
- требуемая шероховатость поверхности 63.
- длина обрабатываемой поверхности:
- материал режущей части резца - твердый сплав ВК8
Скорость резания определяется по формуле:
где t- глубина резания мм
V- скорость резания ммин
Kv Cv x y m- коэффициенты эмпирической формулы.
Общий поправочный коэффициент по скорости резания:
Коэффициент на обрабатываемый материал Kmv=11
Коэффициент на инструментальный материал Kиv =09
Коэффициент учитывающий глубину резания Kпv =1
Число оборотов шпинделя:
где D – диаметр обрабатываемой поверхности
Принимаем ближайшее имеющееся на станке значение
числа оборотов n=530 обмин
При этом условии фактическая скорость резания составит:
Сила резания при точении определяется по формуле:
где Kp Cp x y n- поправочные коэффициенты
АНАЛИЗ СОСТАВЛЯЮЩИХ ПОГРЕШНОСТИ МЕХАНИЧЕСКОЙ ОБРАБОТКИ ДЕТАЛИ.
Допуск на проект. операцию
Определяем погрешность обработки обусловленную геометрической погрешностью станка для токарных станков норма точности с=0.07 мкмкм:
Δст=с*l=0.07*200=14 мкм.
Погрешность обусловленная износом резца:
Погрешность обусловленная рассеиванием размеров из-за колебаний деформации технологической системы.
где Е-модуль упругости материала заготовки
Колебание припуска 03мм
Для заданного диаметра размера.
Определим погрешность настройки станка на размер. Погрешность размера Δрег=20 мкм погрешность измерений принимаем равной 15% допуска на размер.
Определяем случайную составляющую погрешности обработки.
Погрешность температуры примем с введением коэффициента кт=1.15 тогда суммарная погрешность:
Полученное значение удовлетворяет требованию
Определим соотношение составляющих погрешностей:
МЕТОДИКА И СХЕМЫ ЭКСПЕРТИЗЫ ГЕОМЕТРИЧЕСКОЙ ТОЧНОСТИ И ЖЁСТКОСТИ ТОКАРНОГО СТАНКА.
Проверка Радиального Биения Центрирующей Шейки Шпинделя Станка (Рис. 1)
При проверке индикатор устанавливается так (Рис. 1) чтобы его зрительный наконечник касался поверхности шейки вращающегося шпинделя и был перпендикулярен к образующей. Допускаемое радиальное биение 001 мм.
Проверка Перпендикулярности Торцевой Поверхности Фланца (Буртика) Шпинделя Оси Его Вращения (Рис. 2)
Индикатор устанавливается так (Рис. 2) чтобы мерительный наконечник касался торцевой поверхности фланца (буртика) шпинделя у его периферии и был перпендикулярен этой поверхности. Шпиндель приводится во вращение и фиксируется торцевое биение поверхности фланца (буртика).
Проверка Осевого Биения Шпинделя
В коническое отверстие шпинделя вставляется короткая оправка торцевая поверхность которой перпендикулярна ее оси. Индикатор устанавливается так (Рис. 3) чтобы его мерительный наконечник касался торца оправки у ее оси. Шпиндель приводится во вращение. Проверка производится при отсутствии осевого люфта шпинделя в подшипниках. Допускаемое осевое биение 001.
Проверка Радиального Биения Оси Конического Отверстия Шпинделя (Рис. 4)
В коническое отверстие шпинделя плотно вставляется цилиндрическая оправка с длиной цилиндрической части 310-330 мм. Мерительный наконечник индикатора установленный в радиальном направлении к оправке касается опоры (Рис. 4). Шпиндель приводится во вращение. Производится проверка биения оправки у конца шпинделя на расстоянии 300 мм от конца.
Допустимые биения шпинделя 001 мм: на расстоянии 300 мм от конца – 002 мм.
В контрольной работе рассмотрены вопросы по нахождению и выявлению систематических погрешностей влияющих на обработку детали. Можно сделать вывод что изготовленное таким образом изделие должно обладать такими свойствами которые будут удовлетворять определенным потребностям. Совокупность свойств изделия определяют его функциональное назначение и качество. При экспертизе технологических систем и выявлении технологических связей необходимо проанализировать совокупность причин определяющих погрешность механической обработки деталей на технологических операциях что и было сделано в данной контрольной работе.
Библиографический список.
Косилова А.Г. Мещеряков Р.К. Справочник технолога-машиностроителя-М.:Машиностроение1985.
Допуски и посадки: Справочник. В 2-х ч. Под ред. В.Д. Мягкова. Л.: Машиностроение. 1983.
Горбацевич А.Ф. Курсовое проектирование по технологии машиностроения - Минск: Вышейшая школа 1983.
Наладки станков с программным управлением. - Учебное пособие. М.: Высшая школа 1976.
Проектирование технологических процессов механической обработки в машиностроении Под ред. В.В. Бабук – Минск: Вышейшая школа 1987.- 255с.
Станки с ЧПУ Под ред. В.А. Лещенко. - М.: Машиностроение 1979.
Технология машиностроения. - (спецчасть). - М.: Машиностроение -1986. их конструкции и принципов работы.
Общемашиностроительные нормативы времени вспомогательного на обслуживание рабочего места и подготовительно-заключительного для технического нормирования станочных работ. Серийное производство. – М.. Машиностроение 1974.-422с.
МУ Эк 09 нов_брош.doc
Севастопольский национальный технический университет
МЕТОДИЧЕСКИЕ УКАЗАНИЯ
к выполнению практических занятий
по дисциплине «Международная техническая экспертиза технологических процессов машин и систем» для студентов всех форм обучения по специальности «Металлорежущие станки и системы»
Методические указания к выполнению практических занятий по дисциплине «Международная техническая экспертиза технологических процессов машин и систем» для студентов специальности 7.09.0203 «Металлорежущие станки и системы» всех форм обучения Сост. А.В. Троценко.- Севастополь СевНТУ 2009 - 33 с.
Целью настоящих методических указаний является обеспечение возможности выполнения практических занятий по курсу. Методические указания составлены в соответствии с требованиями программы дисциплины «Международная техническая экспертиза технологических процессов машин и систем» для студентов специальности 7.09.0203 всех форм обучения.
Методические указания утверждены на заседании кафедры «Технология машиностроения» 2009 г. Протокол № .
Рецензент: Братан С.М. доктор техн. наук профессор кафедры ТМ.
Ответственный за выпуск: Братан С.М. докт. техн. наук профессор зав. кафедрой ТМ.
Рекомендованы в качестве учебного пособия научно-методическим центром СевНТУ.
Практическое занятие № 1
Определение погрешности механической обработки деталей на
металлорежущем станке 3
Практическое занятие № 2
Аккредитация органов по сертификации и испытательных лабораторий10
Практическое занятие № 3
Аттестация экспертов (аудиторов) в системе УкрСЕПРО13
Практическое занятие № 4
Оценка деятельности территориального центра по стандартизации метрологии и сертификации 16
Библиографический список 19
Приложения А БВГДЕЖЗИКЛМН 20
ПРАКТИЧЕСКОЕ ЗАНЯТИЕ № 1
ОПРЕДЕЛЕНИЕ ПОГРЕШНОСТИ МЕХАНИЧЕСКОЙ ОБРАБОТКИ ДЕТАЛЕЙ НА МЕТАЛЛОРЕЖУЩЕМ СТАНКЕ
1. Краткие теоретические сведения
Процесс механической обработки заготовок на металлорежущих станках сопровождается погрешностями вызываемыми различными причинами систематического и случайного характера. Соответственно погрешности возникающие вследствие этих причин делятся на систематические и случайные.
Систематическая погрешность – составляющая погрешности остающаяся постоянной или закономерно изменяющаяся для всех заготовок рассматриваемой партии.
Основными причинами возникновения систематической погрешности являются:
- геометрическая погрешность станка ;
- износ режущего инструмента ;
- температурные деформации технологической системы .
Погрешность обработки обусловленную геометрической погрешностью станка можно определить в первом приближении по формуле
где с – удельное отклонение от параллельности относительного перемещения заготовки и режущего инструмента мкммм; l – длина обрабатываемой поверхности мм.
Погрешность обусловленную износом режущего инструмента определяют по формуле
где U0 - удельный износ инструмента мкмкм; L – длина пути резания км; Lдоп - дополнительный путь резания учитывающий начальный период более интенсивного износа км. Обычно принимают Lдоп = 1 км.
При фрезеровании в связи с прерывистым характером процесса резания удельный износ больше чем при точении
где В - ширина фрезерования мм.
Длина пути резания при токарной обработке партии заготовок
где D – диаметр обрабатываемой поверхности мм; n – число заготовок в партии; S – продольная подача ммоб.
Длина пути резания при торцовом фрезеровании
где SZ – подача фрезы ммзуб; Z – число зубьев фрезы.
Температурные деформации технологической системы при лезвийной обработке упрощенно могут быть приняты равными 15 % от суммарной погрешности.
Общая систематическая погрешность определяется алгебраической суммой составляющих
При обработке тел вращения составляющие погрешности должны быть удвоены.
Случайная погрешность – составляющая погрешности которая для различных заготовок рассматриваемой партии изменяется случайным образом не подчиняясь никакой закономерности.
Случайная погрешность обусловлена совокупностью многих причин случайного характера проявляющих свое действие независимо друг от друга и приводящих к рассеиванию размеров.
Поскольку законы распределения большинства составляющих случайной погрешности неизвестны для создания некоторой гарантии точности принимают условно распределение соответствующее закону Симпсона. Тогда случайная погрешность определяется выражением
Рассмотрим составляющие случайной погрешности.
- погрешность рассеяния размеров связанная с видом обработки и обусловленная нестационарностью процесса резания и податливости технологической системы. Статистические значения как правило приведены в справочной литературе. Составляющую рассеяния размеров
обусловленную колебанием упругих деформаций технологической системы вследствие нестабильности составляющей силы резания Ру и податливости системы при обработке можно определить по формуле
где Wma Pyma у – погрешность установки заготовок
где б – погрешность базирования обусловленная несовпадением конструкторской и технологической баз а также особенностями формы опорных поверхностей заготовки и установочных элементов приспособления; з – погрешность закрепления заготовки в приспособлении; n – погрешность приспособления; - погрешность настройки универсального станка определяемая по формуле
где - погрешность регулирования положения режущего инструмента и элементов станка; - погрешность измерения пробных заготовок; - поле рассеяния среднего арифметического размера пробных заготовок (поле смещения центра группирования)
где m – число пробных заготовок.
При обработке на станках с ЧПУ дополнительно возникают погрешности подготовки программы и ее воспроизведения которые в свою очередь определяются погрешностями программирования интерполяции привода перемещения и позиционирования элементов станка. Вместе с тем при работе с корректором из расчета общей погрешности может быть исключена систематическая погрешность обусловленная износом инструмента а также составляющая рассеяния размеров из-за погрешности регулирования . Кроме того в связи с более жесткой конструкцией податливость станков с ЧПУ может быть принята в 2 - 4 раза меньше чем у аналогичных универсальных станков.
Суммарная погрешность механической обработки на металлорежущих станках равна сумме систематической и случайной составляющих
Полученное значение суммарной погрешности должно удовлетворять требованию
где TD – допуск размера обрабатываемой поверхности.
2. Порядок выполнения работы
2.1. Ознакомиться с условиями базирования и обработки заготовок на данной операции.
2.2. Произвести анализ составляющих общей погрешности обработки.
2.3. Произвести расчет суммарной погрешности.
2.4. Сравнить полученное значение с допуском на размер выполняемый на данной операции.
2.5. Определить процентное содержание каждой составляющей в суммарной погрешности.
3. Пример выполнения работы
Определить суммарную погрешность токарной обработки вала из стали 45. Размеры вала: диаметр 35h11 длина 200 мм. Обработка проводится в центрах на токарно-револьверном станке. На предшествующей операции вал обработан черновым точением по IT14. Партия деталей n = 50 штук. Число пробных деталей m = 4. Условия обработки: резец с пластиной из твердого сплава Т15К6 минимальный припуск 05 мм на сторону подача 03 ммоб скорость резания 130 ммин податливость элементов станка (2—25)10-2 мкмН. Для сплава Т15К6 удельный износ принимаем U0= 6 мкмкм.
Определим погрешность обработки обусловленную геометрической погрешностью станка . Для токарных станков нормальной точности принимаем с = 007 мкммм.
При длине обработки L = 200 мм = 007 · 200 = 14 мкм.
Определим погрешность обусловленную износом резца. Длина пути резания
Определим составляющую рассеяния размера обусловленную колебаниями деформаций технологической системы. Максимальную податливость система имеет при расположении резца посередине вала. При этом
где Wma Wmax заг — максимальная податливость заготовки:
где Е — модуль упругости материала заготовки Е = 2 · 1011 Па; J — момент инерции поперечного сечения; J = 005 D4 м4.
Определим наибольшую и наименьшую составляющие силы резания. Поскольку предварительно заготовка обработана с допуском IT 14 колебание припуска будет равно IT 14 что для заданного диаметра составит 03 мм. Тогда
Для заданного диаметрального размера 2Δ = 121 мкм.
При обработке в центрах погрешность установки равна 0.
Определим погрешность настройки станка на размер. Погрешность измерения принимаем равной 15% допуска на размер:
Погрешность регулирования принимаем равной Δр = 20 мкм. Тогда
Определим случайную составляющую погрешности обработки
Погрешность от температурных деформаций учтем введением коэффициента К = 115 (15% от суммарной погрешности). Таким образом суммарная погрешность обработки
Полученное значение удовлетворяет требованию
ΔΣ TD (1435 мкм 160 мкм).
4. Задание к выполнению работы
Определить суммарную погрешность токарной обработки вала из стали 45. Условия обработки: минимальный припуск 05 мм; подача 03 ммоб; скорость резания 130 ммин. Размеры вала и остальные условия обработки согласно таблицы 1.
Таблица 1 — Исходные данные
Допуск на предшеств. операции
закрепления заготовки
5. Содержание отчета
5.1. Название цель работы исходные данные.
5.2. Результаты расчёта систематической и случайной составляющих погрешности механической обработки детали.
5.3. Расчет суммарной погрешности механической обработки.
5.4. Выводы по работе.
6. Контрольные вопросы
6.1. Охарактеризуйте комплекс систематических составляющих погрешности механической обработки.
6.2. Состав случайных составляющих погрешности обработки детали на станках с ЧПУ.
6.4. Оцените процентное соотношение каждой составляющей в суммарной погрешности.
6.5. Наметьте пути снижения суммарной погрешности.
ПРАКТИЧЕСКОЕ ЗАНЯТИЕ № 2
АККРЕДИТАЦИЯ ОРГАНОВ ПО СЕРТИФИКАЦИИ И
ИСПЫТАТЕЛЬНЫХ ЛАБОРАТОРИЙ
Цель работы. Освоить порядок оформления документов по аккредитации организаций.
Аккредитация – это официальное признание того что орган по сертификации (ОС) правомочен осуществлять конкретные испытания или конкретные типы испытаний.
Основными целями аккредитации являются:
-повышение качества работы и укрепление доверия к ОС со стороны заявителя государства других заинтересованных структур;
-обеспечение конкурентоспособности продукции и услуг на внутреннем и внешнем рынках;
-признание результатов испытаний и сертификатов соответствия на национальном европейском и мировом уровнях.
Типовая структура системы аккредитации представлена на рисунке 1.
Аккредитация как и сертификация проводится в законодательно регулируемой и нерегулируемой областях. Госстандарт в пределах его компетенции выполняет функции органа по аккредитации разрабатывает общие процедуры общие требования к объектам аккредитации и экспертам к необходимым документам.
Совет по аккредитации
Органы по аккредитации
В обязательной сфере
В добровольной сфере
Испытательные лаборатории измерительные лаборатории ОС метрологические службы организации подготовки экспертов контролирующие организации
Объекты аккредитации
Юридические лица отвечающие требованиям
Испытательные лаборатории ОС организации подготовки экспертов контролирующие организации
Испытательные лаборатории ОС организации подготовки экспертов
Рисунок 1 – Типовая структура системы аккредитации
Организации претендующей на аккредитацию необходимо в орган по аккредитации направить в следующие документы:
- заявку по установленной форме (Приложение А);
- справку о деятельности организации;
-анкету - вопросник с ответами которая высылается органом по аккредитации при подготовке заявки;
-проект «Положения об ОС» (Приложение Б);
-проект документа «Порядок сертификации» (Приложение В);
-проект «Руководства по качеству»;
-проект приказа о создании ОС;
-сведения об экспертах или аудиторах;
-перечень организаций взаимодействующих с ОС;
-копию Устава организации;
-проект документа «Области аккредитации».
Оформление решения по аккредитации организации включает следующие операции:
-проверка результатов экспертизы;
-утверждение «Положения об ОС» и «Порядка сертификации»;
-оформление аттестата аккредитации при положительном решении;
-заключение Соглашения между ОС и органом по аккредитации;
-занесение в Реестр Системы.
Аккредитация испытательной лаборатории (ИЛ) – официальное признание технической компетенции и независимости лаборатории от разработчиков производителей и потребителей продукции или только ее технической компетенции.
Аккредитованной может быть любая лаборатория которая изъявила желание пройти аккредитацию независимо от ее отраслевой подчиненности и формы собственности.
Основной функцией ИЛ является проведение испытаний в закрепленной области аккредитации. Лаборатория должна осуществлять свою деятельность соответственно «Положению об ИЛ» (Приложение Г).
Для аккредитации ИЛ в Системе необходимо в орган по аккредитации подать заявку по специальной форме (Приложение Д) области аккредитации ИЛ и другие необходимые документы. После проверки ИЛ орган по аккредитации составляет акт проверки ИЛ (Приложение Е) и выдает аттестат аккредитации.
2.1. Составить заявку на аккредитацию конкретного органа по сертификации продукции или услуги и испытательной лаборатории в области машиностроения.
2.2. Разработать проект документа «Положение об испытательной лаборатории».
2.3. Составить «Соглашение» с Госстандартом Украины и органом по аккредитации».
2.4. От лица Госстандарта Украины или органа по аккредитации принять решение по заявке на проведение аккредитации составить акт проверки и оформить аттестат аккредитации.
2.5. Составить отчет.
3. Содержание отчета
В отчете необходимо указать цель работы представить оформленные документы по аккредитации конкретной испытательной лаборатории продукции или органа по сертификации оформить документы по соглашениям и решениям органов по аккредитации.
4. Контрольные вопросы
4.1. Основные цели и задачи аккредитации.
4.2. Типовая структура системы аккредитации.
4.3. Роль Госстандарта в системе аккредитации организаций.
4.4. Типовая схема организации органа по аккредитации.
4.5. Перечень и характеристика документов по аккредитации органов по сертификации продукции и услуг.
4.6. Аккредитация испытательных лабораторий.
4.7. Квалификация персонала и оснащение лаборатории.
4.8. Перечень документов которыми должна располагать лаборатория претендующая на аккредитацию.
ПРАКТИЧЕСКОЕ ЗАНЯТИЕ № 3
АТТЕСТАЦИЯ ЭКСПЕРТОВ (АУДИТОРОВ) В СИСТЕМЕ УКРСЕПРО
Цель работы. Освоить порядок подготовки и аттестации аудиторов в национальной Системе УкрСЕПРО.
1.Краткие теоретические сведения
Аудитор по сертификации – лицо которое имеет соответствующую квалификацию теоретическую и практическую подготовку необходимую для проведения одного или нескольких видов работ по сертификации в Системе аттестованный в установленном порядке и занесенный в Реестр Системы.
Официально признанными в Системе аудиторами могут быть специалисты разных областей науки техники промышленности сферы услуг и других видов деятельности которые отвечают требованиям стандартов признают и выполняют требования Системы. Аудиторов аттестуют на право проведения:
-сертификации систем качества;
-аттестации производства;
-сертификации продукции и услуг;
-аккредитации испытательных лабораторий (центров).
Кандидат в аудиторы должен иметь: законченное высшее техническое или экономическое образование минимум 4 года стажа практической работы в области управления качеством специальное образование на курсах подготовки экспертов в Системе сертификации не менее 2 стажировок по проверкам систем качества свободно владеть устно и письменно государственным языком.
Аудитор должен владеть знаниями в обязательном объеме в таких направлениях:
-государственные и межгосударственные стандарты другие нормативные документы на соответствие требованиям которых проводится сертификация аттестация аккредитация;
-основополагающие документы Системы;
- методы проведения проверок (исследования опрашивания оценивания) составления отчетов;
-руководство проверками (планирование организация контроль);
-экономические и правовые основы ведения работ по сертификации аттестации и аккредитации;
-организация производства и контроля;
-международные и европейские системы сертификации и аккредитации.
Теоретическую подготовку кандидатов проводят учебные учреждения которые получили разрешение Национального органа по сертификации на проведение такой деятельности. Теоретическая подготовка осуществляется с отрывом кандидата от производства по учебным планам и программам утвержденных Национальным органом по сертификации.
По окончании курса теоретической подготовки кандидат сдает экзамен и в случае удовлетворительной оценки получает удостоверение (Приложение Ж).
Аттестацию аудиторов осуществляет постоянно действующая аттестационная комиссия Национального органа по сертификации. Комиссия создается и утверждается приказом Председателя Госстандарта Украины сроком на один год из числа ведущих сотрудников Национального органа по сертификации и высококвалифицированных специалистов из разных видов деятельности.
Процесс аттестации аудиторов состоит из таких основных этапов:
-рассмотрение заявки кандидатов и анализ представленных документов;
-проверка и оценка кандидата;
-оформление результатов аттестации;
-выдача сертификата аудитора.
Кандидат который претендует на аттестацию должен подать заявку в Национальный орган сертификации по специальной форме (Приложение З).
Национальный орган в месячный срок рассматривает заявку проверяют комплектность представленных документов и в случае положительных результатов рассмотрения документов включает кандидата в аудиторы в график аттестации и информирует его об этом (Приложение И).
По результатам проверки и оценки кандидата аттестационная комиссия принимает решения об утверждении или отклонении его кандидатуры. Решения принимается большинством голосов. Решения аттестационной комиссии оформляются протоколом (Приложение К). Кандидат кандидатура которого была отклонена имеет право на повторную аттестацию через срок который устанавливает аттестационная комиссия.
В случае положительного решения Национальный орган оформляет и выдает кандидату сертификат аудитора (Приложение Л). Сертификат аудитора регистрируется в Реестре Системы. Срок действия сертификата аудитора – три года. Для продолжения действия аттестации аудитор за шесть месяцев до окончания срока действия сертификата подает в Национальный орган по сертификации заявку (Приложение З). В случае получения сертификата аудитор подписывает «Кодекс поведения аудиторов» (Приложение М).
Аттестованный в Системе аудитор обязан ежегодно до 31 декабря предоставлять Национальному органу по сертификации отчет о своей деятельности в Системе как аудитор (Приложение Н).
2.1. Составить заявку на аттестацию аудитора.
2.2. Оформить документы необходимые для подачи
заявки на аттестацию.
2.3. Составить проект программы теоретической подготовки кандидатов в аудиторы.
2.4. Составить протокол решения аттестационной комиссии.
2.5. Оформить сертификат аудитора.
2.6. Составить отчет о деятельности аудитора Системы.
2.7. Составить отчет по работе.
В отчете необходимо указать цель работы представить оформленные документы по аттестации аудиторов оформить документы по заявлениям и принятию решения об аттестации.
4.1. Виды работ на проведение которых аттестуется
4.2. Основные требования к аудиторам.
4.3. Функции права и обязанности аудиторов.
4.4. Порядок подготовки кандидатов в аудиторы.
4.5. Порядок проведения аттестации аудиторов.
ПРАКТИЧЕСКОЕ ЗАНЯТИЕ № 4
ОЦЕНКА ДЕЯТЕЛЬНОСТИ ТЕРРИТОРИАЛЬНОГО ЦЕНТРА ПО СТАНДАРТИЗАЦИИ МЕТРОЛОГИИ И СЕРТИФИКАЦИИ
Цель работы. Изучение критериев оценки деятельности территориальных центров по стандартизации метрологии и сертификации продукции.
Территориальный орган (центр) по стандартизации метрологии и сертификации (ЦСМС) является государственным учреждением с правом ведения хозяйственной деятельности и руководствуется в своей работе Конституцией и иными законодательными актами постановлениями и распоряжениями Правительства приказами и распоряжениями Госстандарта.
Территориальный орган имеет право проводить работы и оказывать услуги в области стандартизации метрологии и сертификации в соответствии с действующим законодательством на некоммерческой основе и не преследует извлечения прибыли в качестве основной цели своей деятельности. Госстандарт устанавливает численность государственных инспекторов и расходы на их содержание назначает на контрактной основе руководителя органа утверждает других должностных лиц. Руководитель утверждает штатное расписание структуру и положения о входящих в состав органа подразделений.
В составе ЦСМС аккредитуется орган по сертификации который должен выполнять работы в соответствии с областью аккредитации и включать несколько направлений деятельности.
Государственный надзор ЦСМС и контроль его деятельности проводит Госстандарт им же устанавливается отчетность по госнадзору. С целью оценки результативности госнадзора разработана система критериев позволяющая осуществлять анализ деятельности по направлениям и дать предложения по ее совершенствованию.
Рассмотрим пример расчета критериев. Исходные данные представлены в таблице 1.
Расчет критериев проводится по формулам:
Применяемость запрещения реализации продукции
Воздействие госнадзора на деятельность предприятий по соблюдению обязательных требований стандартов
Таблица 1 – Критерии оценки деятельности ЦСМС
Наименование показателя
Суммарный объем проверенной продукции в том числе сертифицированной у.е.
Суммарный объем запрещенной к реализации продукции у.е.
Общее количество предприятий на которых проведено соблюдение требований стандартов
Количество предприятий продукция которых не соответствовала требованиям стандартов
Количество предприятий на которых проверено соблюдение правил сертификации
Количество предприятий на которых выявлены нарушения правил сертификации
Количество повторно проверенных предприятий
Количество предприятий продукция которых соответствовала требованиям стандартов и правил сертификации при проведении повторных проверок
Количество предприятий на которых реализация продукции запрещена
Количество проверенных предприятий к которым применены штрафы за отчетный период
Общее количество проверенных предприятий на которых выявлены нарушения требований стандартов и правил сертификации
Общее количество проверок проведенных госинспекторами
Количество инспекторов по надзору за государственными стандартами
Суммарный объем штрафов примененных к предприятиям и должностным лицам у.е.
Суммарный объем бюджетных ассигнований на проведение проверок предприятий у.е.
Воздействие госнадзора на деятельность предприятий по соблюдению правил сертификации
Результативность госнадзора на деятельность предприятий
Использование запретов реализации выпуска продукции
Использование штрафов
Интенсивность деятельности по госнадзору
Анализ критериев показывает что на проверяемых предприятиях правила сертификации нарушаются в 2 раза чаще чем требования стандартов (783 и 384). При проведении повторных проверок нарушения выявленные при первичных проверках в 833% устраняются. На одного госинспектора приходится 7 проверок в квартал сумма штрафов поступающих в госбюджет в 46 раз больше объема бюджетного финансирования.
2.1. Рассчитать критерий интенсивности
деятельности по госнадзору территориальному органу. Количество проверок равно –350; количество инспекторов – 30.
2.2. Составить отчет.
В отчете необходимо представить цель работы
перечень критериев организации деятельности органов по сертификации производственную деятельность органов выводы по работе.
4.1. Охарактеризуйте деятельность ЦСМС.
4.2. Основной состав территориального органа по сертификации продукции и услуг.
4.3. Перечислите и охарактеризуйте критерии оценки деятельности ЦСМС.
4.4. Произведите расчет основных показателей деятельности ЦСМС.
БИБЛИОГРАФИЧЕСКИЙ СПИСОК
Маталин А.А. Технология машиностроения: учебник А.А. Маталин — Л.: Машиностроение 1985. — 496с.
Проектирование технологии автоматизированного машиностроения Ред. Ю.М. Соломенцев. — М.: Высш. шк. 1999. — 415с.
Справочник технолога-машиностроителя Под ред. А.Г. Косиловой Р.К. Мещерякова. В 2-х т. — М.: Машиностроение 1990. — 924с.
Система сертификации УкрСЕПРО. Комплекс государственных
Сертификация и аккредитация. Система международных стандартов ISO и европейских EN 2000.
председателю ГОССТАНДАРТА УКРАИНЫ
(ОРГАНА АККРЕДИТАЦИИ)
на аккредитацию органа по сертификации
(название организации-заявителя)
просит произвести его (ее) аккредитацию как органа по сертификации.
(адрес телефон телекс факс номер расчетного счета)
(фамилия имя отчество руководителя)
(должность фамилия имя отчество работника отвечающего за связь с Госстандартом)
Название продукции и показателей которые подлежат сертификации.
Код ОКП (класс подкласс
группа подгруппа вид)
Заявитель обязуется:
а) отвечать требованиям предъявляемым к органу по сертификации;
б) оплатить все расходы связанные с проведением работ по аккредитации независимо от их результатов.
Приложения: Перечень документов в соответствии с ДСТУ 3411 - 96.
(подпись инициалы фамилия)
Руководитель территориального органа Госстандарта
ПОЛОЖЕНИЕ ОБ ОРГАНЕ ПО СЕРТИФИКАЦИИ
Б.1. ТРЕБОВАНИЯ К СОДЕРЖАНИЮ
Положение об органе по сертификации " должно устанавливать:
- область аккредитации;
- краткое описание юридического статуса органа по сертификации;
- функции органа по сертификации его права обязанности и ответственность которые вытекают из правил Системы сертификации УкрСЕПРО и соглашения с Госстандартом;
- сведения об организации деятельности органа по сертификации которые включают организационную схему которая отображает подчиненность ответственность и распределение обязанностей персонала;
- квалификацию практический опыт работы и полномочия персонала органа по сертификации как штатного так и внештатного;
- перечень органов по сертификации системы качества испытательных лабораторий организаций которые взаимодействуют с органом по сертификации.
При необходимости положение может содержать другие аспекты которые регламентируют деятельность органа исходя из специфики области его аккредитации.
Б.2. ФОРМА ТИТУЛЬНОГО ЛИСТА
Cистема сертификации УкрСЕПРО
Председатель Госстандарта Украины
М.П. (подпись инициалы фамилия)
ПОЛОЖЕНИЕ ОБ ОРГАНЕ ПО
(название органа по сертификации)
Руководитель органа управления Госстандарта Украины
(подпись инициалы фамилия) “ ” 200__ г.
“ПОРЯДОК СЕРТИФИКАЦИИ ”
В.1. ТРЕБОВАНИЯ К СОДЕРЖАНИЮ
“Порядком сертификации ” должны устанавливаться:
- перечень продукции которая сертифицируется и состав нормативных документов на соответствие которым проводится сертификация относительно области аккредитации;
- перечень органов по сертификации систем качества испытательных лабораторий организаций которые взаимодействуют с органом по сертификации;
- перечень предприятий продукция которых сертифицируется органом по сертификации;
- порядок подготовки и проведения сертификации конкретной продукции схемы (модели) сертификации правила выдачи сертификата соответствия и применения знака соответствия;
- порядок проведения анализа предоставленной документации;
- порядок идентификации продукции отбора и испытаний образцов
- перечень нормативных документов на методы испытаний;
- порядок обследования и аттестации производства;
- сведения относительно процедуры оценивания результатов испытания продукции которая сертифицируется;
- порядок оформления и регистрации сертификатов соответствия и аттестатов производств;
- порядок признания сертификатов на продукцию иностранного производства;
- порядок проведения технического надзора прекращения действия и отмены сертификатов и лицензионных соглашений;
- порядок предоставления новой лицензии (вместо той что утратила силу);
- информационное обеспечение организаций которые взаимодействуют с органом по сертификации продукции;
- порядок представления и рассмотрения апелляций.
В.2. ФОРМА ТИТУЛЬНОГО ЛИСТА
Система сертификации УкрСЕПРО
(подпись инициалы фамилия) “ ” 200 г.
ПОРЯДОК СЕРТИФИКАЦИИ
ТРЕБОВАНИЯ К СОДЕРЖАНИЮ И ОФОРМЛЕНИЮ «ПОЛОЖЕНИЯ ОБ ИСПЫТАТЕЛЬНОЙ ЛАБОРАТОРИИ»
Г.1. ТРЕБОВАНИЯ К СОДЕРЖАНИЮ "ПОЛОЖЕНИЯ
Положение об испытательной лаборатории (центра) может устанавливать:
- описание юридического статуса испытательной лаборатории;
- функции испытательной лаборатории которые она выполняет в Системе ее права обязанности и ответственность;
- организационную структуру испытательной лаборатории с описанием схемы управления подчиненности и функций сведения про его персонал;
- сведения об испытательном оснащении средствах измерительной техники и помещение испытательной лаборатории;
- взаимодействие с другими подразделами и организациями. За необходимости этот документ может содержать другие положения которые регламентируют деятельность лаборатории исходя из специфики области ее аккредитации.
Г.2. ФОРМА ТИТУЛЬНОГО ЛИСТА "ПОЛОЖЕНИЯ
Об испытательной лаборатории (центра)
аккредитованную Госстандартом Украины
(записать аккредитацию на техническую компетентность и независимость или только на техническую компетентность)
Начальник Соответствующего функционального Управления Госстандарта Украины
(подпись инициалы фамилия)
Руководитель лаборатории (центра)
Председателю Госстандарта Украины
(руководителю органа аккредитации)
(название лаборатории)
- отвечать требованиям аккредитованной испытательной лаборатории;
- возместить все затраты связанные с проведением работ по аккредитации независимо от их результатов.
- проект "Положения об аккредитованной испытательной лаборатории";
- паспорт испытательной лаборатории;
- руководство по качеству испытательной лаборатории;
- заполненная опросная анкета;
- проект области аккредитации испытательной лаборатории.
(подпись инициалы фамилия руководителя)
(подпись инициалы фамилия главного бухгалтера)
Руководитель территориального органа
Форма акта проверки испытательной лаборатории
АКТ ПРОВЕРКИ ИСПЫТАТЕЛЬНОЙ ЛАБОРАТОРИИ
( название испытательной лаборатории)
(название номер и дата документа о проведении проверки)
(место работы должность инициалы фамилия)
(название испытательной лаборатории)
(название организации в составе которой функционирует испытательная лаборатория)
Проверкой установлено (приводятся результаты проверки по разделам):
Статус организационная структура административное устройство финансовое положение система оплаты работы служащих.
Оснащение методов испытания и их состояние.
Обеспечение нормативной и методической документацией их перечень и сбережение.
Квалификация и образованность персонала состояние роботы по повышению квалификации которая проводится.
Состояние производственных помещений.
Наличие и эффективность функционирования системы обеспечения качества испытаний.
(дополнительные характеристики лаборатории)
Предложения и рекомендации.
(рекомендации комиссии по аккредитации лаборатории и уточнения в случае необходимости виды аккредитации)
Проект “Положения об аккредитованной испытательной лаборатории».
Паспорт испытательной лаборатории.
Показатели качества.
Проект области аккредитации испытательной лаборатории.
Протоколы заседания комиссии.
Протоколы испытаний которые проведены во время проверки.
Форма удостоверения о теоретической подготовке
(фамилия имя отчество)
(вид работ в области сертификации)
(название учебного учреждения)
М.П. (подпись) (инициалы фамилия)
(подпись) (инициалы фамилия)
Форма заявки на аттестацию (от кандидата которого
направляет организация или предприятие)
Председателю Национального
органа по сертификации
на аттестацию аудитора
сертификации УкрСЕПРО в
(название организации)
ОБЯЗУЕТСЯ ОПЛАТИТЬ ВСЕ ЗАТРАТЫ СВЯЗАННЫЕ С ПРОВЕДЕНИЕМ АТТЕСТАЦИИ И ЭКСПЕРТИЗЫ ДОКУМЕНТОВ НЕЗАВИСИМО ОТ ИХ РЕЗУЛЬТАТОВ.
Приложение: (в соответствии с нормативными документами)
(подпись) (инициалы фамилия)
Форма вывода о целесообразности и форме проведения проверки и
оценки кандидата аттестационной комиссией
о целесообразности и форме проведения проверки
и оценки кандидата аттестационной комиссией
На основании изучения заявки кандидата в аудиторы в
(перечень документов)
провести проверку и оценку кандидата
(обоснования вывода)
(должность) (подпись) (инициалы фамилия)
Форма протокола решения аттестационной
комиссии по проверке и оценке знаний кандидата
решения аттестационной комиссии по проверке
и оценке знаний кандидата в аудиторы
Аттестационная комиссия в составе:
(фамилия инициалы должность)
Форма сертификата аудитора
ГОСУДАРСТВЕННЫЙ КОМИТЕТ
СТАНДАРТИЗАЦИИ МЕТРОЛОГИИ И СЕРТИФИКАЦИИ УКРАИНЫ
(ГОССТАНДАРТ УКРАИНЫ)
Зарегистрированный в Реестре Системы сертификации УкрСЕПРО
Этот сертификат заверяет что
Форма кодекса поведения аудитора
КОДЕКС ПОВЕДЕНИЯ АУДИТОРА
принимаю на себя обязательства и ответственность за следующее:
-действовать достойно и неумолимо по отношению к нанимателю (органу по сертификации аккредитации) и предприятию (организации) представляющей объект проверки;
- не распространять информацию которая порочит и наносит вред репутации или интересам нанимателя и предприятия (организации) представляющей объект проверки;
-в случаи привлечения к выполнению работ по сертификации (аккредитации) перед заключением договора извещать о наличии деловых связей с предприятием (при наличии таковых) представляющим объект проверки;
- не принимать материального вознаграждения (комисcионных) от предприятия (организации) представляющей объект проверки и других заинтересованных сторон;
-сохранять конфиденциальность информации полученной во время выполнения работ по проверке предприятия (организации);
-во всех случаях придерживаться этических норм.
(дата) (подпись) (инициалы фамилия)
Форма отчета аудитора
о деятельности аудитора Системы сертификации УкрСЕПРО за 200_ год
(сертификат аудитора зарегистрированный в Реестре Системы УкрСЕПРО)
Сообщаю что в 200_ г. я принимал участие как аудитор Системы сертификации УкрСЕПРО в таких проверках:
EXPERTIZA_113.doc
Севастопольский национальный технический университет
МЕТОДИЧЕСКИЕ УКАЗАНИЯ
к выполнению лабораторных работ по дисциплинам:
«Техническая экспертиза технологических процессов машин и систем» и «Эксплуатация и обслуживание машин»
для студентов специальностей 7.09.0203 «Металлорежущие станки и системы» и 7.09.0202 «Технология машиностроения» всех форм обучения
Методические указания к выполнению лабораторных работ по дисциплинам: «Техническая экспертиза технологических процессов машин и систем» и «Эксплуатация и обслуживание машин» для студентов специальностей 7.09.0203 «Металлорежущие станки и системы» и 7.09.0202 «Технология машиностроения» всех форм обучения Сост. А.В. Троценко И.В. Крылов.- Севастополь Изд-во СевНТУ 2002. - 41с.
Целью настоящих методических указаний является обеспечение возможности выполнения лабораторных работ по курсам. Методические указания составлены в соответствии с требованиями программ дисциплин «Техническая экспертиза технологических процессов машин и систем» и «Эксплуатация и обслуживание машин» для студентов специальностей 7.09.0203 «Металлорежущие станки и системы» и 7.09.0202 «Технология машиностроения» всех форм обучения.
Методические указания утверждены на заседании кафедры Машиностроения и транспорта 11.10.2002 г. протокол № 3.
Рецензент: Сопин П. К. канд. техн. наук доцент кафедры МАШ и Т.
Ответственный за выпуск: Торлин В.Н. докт. техн. наук профессор зав. кафедрой МАШ и Т
Допущено учебно-методическим центром и научно-методическим советом СевНТУ в качестве методических указаний.
ЛАБОРАТОРНАЯ РАБОТА № 1
«Экспертиза геометрической точности фрезерных
консольных станков с горизонтальным шпинделем
классов точности Н и П»
Последовательность экспертизы геометрической точности станка
Порядок выполнения работы
ЛАБОРАТОРНАЯ РАБОТА № 2
«Экспертиза геометрической точности и жесткости
вертикально – сверлильных станков классов
Методика экспертизы жесткости станка
ЛАБОРАТОРНАЯ РАБОТА № 3
«Экспертиза точности позиционирования рабочих органов металлорежущего станка с ЧПУ (типа «обрабатывающий центр»)»
Последовательность экспертизы точности позиционирования
Пример оценки результатов экспертизы точности позиционирования
ЛАБОРАТОРНАЯ РАБОТА № 4
«Определение жесткости фрезерных консольных станков с горизонтальным шпинделем классов точности Н и П»
Методика определения жесткости фрезерного станка
ЛАБОРАТОРНАЯ РАБОТА № 5
«Экспертиза геометрической точности токарно–револьверного станка с ЧПУ мод. 1В340Ф30 класса точности П»
БИБЛИОГРАФИЧЕСКИЙ СПИСОК
ЭКСПЕРТИЗА ГЕОМЕТРИЧЕСКОЙ ТОЧНОСТИ ФРЕЗЕРНЫХ
КОНСОЛЬНЫХ СТАНКОВ С ГОРИЗОНТАЛЬНЫМ ШПИНДЕЛЕМ КЛАССОВ ТОЧНОСТИ Н И П
Цель работы. Освоение методики определения показателей геометрической точности фрезерного станка.
В результате выполнения лабораторной работы студент должен знать:
а) нормы точности металлорежущих станков различного класса точности;
б) нормы точности конкретного фрезерного станка;
в) общие требования к определению геометрической точности станков согласно ГОСТ 8 - 82;
г) номенклатуру и основные характеристики оснастки и средств измерений согласно ГОСТ 17734 - 76;
д) последовательность и содержание работ по проверке геометрической точности станка.
Студент должен уметь:
а) устанавливать на станок специальные оправки;
б) устанавливать на станок средства измерения;
в) реализовывать методы экспертизы геометрической точности фрезерного станка;
г) производить обработку результатов измерений и формулировать выводы по результатам экспертизы.
В настоящей лабораторной работе реализуются схемы и способы измерений следующих геометрических параметров:
-геометрических форм и относительного положения поверхностей используемых для базирования заготовки и инструмента;
-траекторий перемещения рабочих органов станка;
-положения осей вращения и траекторий перемещений рабочих органов несущих заготовку и инструмент относительно друг друга и баз.
Методы и средства экспертизы геометрической точности фрезерных станков соответствуют требованиям ГОСТ 22267 - 76 ГОСТ 17734 - 88 и рекомендациям ИСО Р 230 - 74.
Относительное положение и перемещение узлов станка при измерении должно воспроизводить их положение и перемещение при обработке заготовки. Показывающие измерительные приборы должны устанавливаться как правило на место рабочего инструмента а применяемые для измерения поверочные линейки угольники и т. п. – на место обрабатываемой заготовки.
Погрешность измерения не должна превышать 20 % от допуска измеряемой величины.
Номенклатура средств измерения и предъявляемые к ним основные технические требования приведены в Приложении А. Нормы точности станков не должны превышать значений указанных в Приложении Б.
ПОСЛЕДОВАТЕЛЬНОСТЬ ЭКСПЕРТИЗЫ ГЕОМЕТРИЧЕСКОЙ ТОЧНОСТИ СТАНКА
1. Прямолинейность рабочей поверхности стола в продольном и поперечном сечениях.
Для измерений используют метод 3 раздел 4 по ГОСТ 22267 - 76 – с помощью поверочной линейки и показывающего прибора. Измерения проводят в отдельных сечениях рабочей поверхности стола – в двух продольных и трех поперечных. Схема расположения проверяемых сечений представлена на рисунке 1.
Рисунок 1 – Схема расположения проверяемых сечений
Стол должен быть установлен в среднее положение. Схема измерений указана на рисунке 2.
Рисунок 2 – Схема измерений
На рабочую поверхность стола 1 в двух точках заданного сечения устанавливают две опоры 2 на которые рабочей поверхностью кладут поверочную линейку 3 так чтобы расстояния от проверяемой поверхности до рабочей поверхности линейки у ее концов были равны.
Показывающий прибор 4 (индикатор часового типа с магнитной стойкой) устанавливают на проверяемую поверхность так чтобы его измерительный наконечник касался рабочей поверхности линейки и был перпендикулярен ей.
Показывающий прибор перемещают по поверяемой поверхности вдоль линейки.
Выпуклость рабочей поверхности стола не допускается. Отклонение от прямолинейности равно наибольшей алгебраической разности показаний прибора 4 во всех сечениях.
2. Параллельность боковой поверхности направляющего паза стола траектории его продольного перемещения.
Измерения проводят в соответствии со схемой указанной на рисунке 3.
Рисунок 3 – Схема измерений
Рабочий стол перемещают в крайнее левое положение. Показывающий прибор 2 устанавливают неподвижно. Измерительный наконечник прибора вводят в соприкосновение с боковой поверхностью центрального паза стола. Стол перемещают в продольном направлении на всю длину хода. Отклонение от параллельности равно наибольшей алгебраической разности показаний прибора 2 на всей длине перемещения для двух боковых поверхностей паза.
3. Перпендикулярность поперечного перемещения стола к направлению его продольного перемещения.
Для измерения используют метод 1 раздел 8 по ГОСТ 22267 - 76 – с помощью поверочного угольника с углом 90 0 и показывающего прибора.
Схема измерений указана на рисунке 4.
Рисунок 4 – Схема измерений
Поверочный угольник 2 устанавливают на середину рабочей поверхности стола 1 таким образом чтобы одна из его рабочих поверхностей была параллельна продольному перемещению стола (показания прибора 3 измерительный наконечник которого касается этой поверхности должны быть одинаковыми в крайних точках хода). Затем показывающий прибор 3 устанавливают неподвижно таким образом чтобы его измерительный наконечник касался другой рабочей поверхности угольника и был перпе6ндикулярен ей. Стол перемещают в поперечном направлении на заданную длину. Отклонение от перпендикулярности равно наибольшей алгебраической разности показаний прибора на всей длине перемещения.
4. Параллельность траекторий продольного и поперечного перемещений стола относительно его рабочей поверхности.
Для измерений используют метод 1 б раздел 6 по ГОСТ 22267 - 76 – с помощью показывающего прибора и плоскопараллельной концевой меры длины.
Схема измерений указана на рисунке 5.
Рисунок 5 – Схема измерений
Концевую меру длины 2 устанавливают на рабочей поверхности стола 1. Показывающий прибор 3 устанавливают неподвижно вне рабочего стола так чтобы измерительный наконечник касался рабочей поверхности концевой меры и был перпендикулярен ей. Стол перемещают в продольном (поперечном) направлении шагами на заданную длину L (длина шага равна 02 L).
Отклонение от параллельности равно наибольшей алгебраической разности показаний прибора на всей длине продольного (поперечного) перемещения.
5. Осевое биение шпинделя
Для измерений используют метод 1 раздел 17 по ГОСТ 22267 - 76 – с помощью оправки с шариком и показывающего прибора.
Схема измерений указана на рисунке 6.
Рисунок 6 – Схема измерений
Оправку с шариком 1 устанавливают в шпиндель 2 станка так чтобы ее ось совпадала с осью вращения. Показывающий прибор устанавливают неподвижно таким образом чтобы его измерительный наконечник касался центра оправки в направлении оси вращения. Шпиндель поворачивают не менее чем на два оборота. Осевое биение равно наибольшей алгебраической разности показаний прибора.
6.Торцевое биение опорного торца шпинделя.
Для измерений используют метод 1 раздел 18 по ГОСТ 22267 - 76.
Схема измерений указана на рисунке 7.
Рисунок 7 – Схема измерений
На неподвижной части станка укрепляют показывающий прибор 1 так чтобы его измерительный наконечник касался торцевой поверхности шпинделя 2 у периферии. Возможно использование контрольной оправки. Шпиндель поворачивают не менее чем на два оборота. Торцевое биение определяют как наибольшую величину алгебраической разности показаний прибора в каждом его положении.
7. Радиальное биение наружной поверхности шпинделя.
Измерения следует проводить по методу 1 раздел 15 по ГОСТ 22267 - 76 – с помощью показывающего прибора. Схема измерения указана на рисунке 8.
Рисунок 8 – Схема измерений
На неподвижной части станка устанавливают показывающий прибор 1 так чтобы его измерительный наконечник касался проверяемой поверхности шпинделя 2 и был направлен к его оси перпендикулярно образующей. Возможно использование контрольной оправки 3.
Шпиндель 2 приводят в медленное вращение. Измерения проводят в двух поперечных сечениях. Измерения проводят четыре раза. После каждого измерения оправку поворачивают вокруг оси вращения на 90 0. Радиальное биение в каждом положении оправки равно наибольшей алгебраической разности показаний прибора в течение одного оборота.
Радиальное биение шпинделя равно среднему арифметическому результату четырех измерений.
8. Радиальное биение конического отверстия шпинделя.
Измерения следует проводить по методу 2 раздел 15 по ГОСТ 22267 - 76 – с помощью показывающего прибора и контрольной оправки. Схема измерений указана на рисунке 9.
В коническое отверстие шпинделя 3 устанавливают контрольную оправку 2 с цилиндрической рабочей поверхностью. На неподвижной части станка устанавливают прибор 1 так чтобы его измерительный наконечник касался цилиндрической поверхности оправки и был направлен к ее оси перпендикулярно образующей.
Рисунок 9 – Схема измерений
Шпиндель приводят во вращение. Радиальное биение оси шпинделя определяют как наибольшее значение алгебраической разности показаний прибора в двух положениях на расстоянии 150 мм.
9. Параллельность оси вращения шпинделя относительно рабочей поверхности стола.
Измерения следует проводить по методу 1 раздел 7 по ГОСТ 22267 - 76.
Стол устанавливают в среднее положение в продольном положении. Схема измерений указана на рисунке 10.
Рисунок 10 – Схема измерений
В шпиндель 1 устанавливают оправку 2 с цилиндрической рабочей поверхностью. На рабочую поверхность стола 3 устанавливают прибор 4 так чтобы его измерительный наконечник касался цилиндрической поверхности оправки и был перпендикулярен ее образующей. Измерения проводят в двух сечениях оправки отстоящих друг от друга на расстоянии L = 150 мм. Измерения повторяют после поворота шпинделя на 1800.
Отклонение от параллельности определяют как среднее значение двух алгебраических разностей показаний прибора полученных по одной а затем по другой образующим оправки. Отклонение свободного конца оправки вверх не допускается.
10.Параллельность направляющих консоли относительно оси вращения шпинделя в вертикальной и горизонтальной плоскостях.
Измерения следует проводить по методу 3 а) раздел 6 по ГОСТ 22267 - 76 в соответствии со схемой указанной на рисунке 11.
Рисунок 11 – Схема измерений
В отверстие шпинделя 1 устанавливают контрольную оправку 2 с цилиндрической поверхностью. На специальной державке 3 (допускается использовать серьгу станка) укрепляют показывающий прибор 4 так чтобы его измерительный наконечник касался цилиндрической поверхности оправки в вертикальной плоскости. Державку с прибором перемещают по направляющим консоли на длину l = 150 мм. Измерения проводят в начале и конце перемещения. Контрольную оправку поворачивают на 1800 и измерения повторяют. Затем измерения проводят в горизонтальной плоскости по схеме описанной выше.
Отклонение консоли вверх не допускается. Отклонение от параллельности направляющих консоли равно среднему арифметическому двух значений алгебраической разности показаний прибора полученных до и после поворота оправки.
11. Соосность отверстия серьги и горизонтального шпинделя в вертикальной и горизонтальной плоскостях.
Измерения следует проводить по методу 1 раздел 14 по ГОСТ 22267 - 76 – с помощью коленчатой оправки с показывающим прибором и контрольной оправки.
Измерения проводят в соответствии со схемой указанной на рисунке 12.
Рисунок 12 – Схема измерений
Контрольную оправку 1 устанавливают в отверстие серьги. В отверстие шпинделя 2 устанавливают коленчатую оправку 3 на которой закрепляют показывающий прибор 4 так чтобы его измерительный наконечник касался цилиндрической оправки 1 на расстоянии L = 300 мм от направляющих станины. Шпиндель станка поворачивают и измеряют разность показаний. Контрольную оправку 1 поворачивают на 1800 и повторяют измерения.
Отклонение от соосности определяют как полусумму алгебраической разности показаний при каждом измерении.
ПОРЯДОК ВЫПОЛНЕНИЯ РАБОТЫ
1. Ознакомиться с разделами 1 2 настоящих указаний.
2. Ознакомиться с инструкцией по эксплуатации фрезерного станка.
3. Ознакомиться с инструкциями по эксплуатации и основными харак-теристиками приборов и оснастки.
4. Подготовить станок приборы и оснастку для проведения экспертизы точности.
5.Провести экспертизу геометрической точности станка на соответствие нормам.
6.При отклонении параметров геометрической формы проверяемого станка от установленных норм оценить влияние измеренных параметров на точность корпусной детали заданной преподавателем.
7.Сформулировать рекомендации по снижению погрешности параметров геометрической точности конкретного станка.
В отчете необходимо указать последовательность действий при выполнении экспертизы точности станка составить таблицы измерений и сделать выводы по результатам экспертизы.
1. Характеристика геометрических параметров фрезерного станка.
2. Общие требования к определению геометрической точности станка.
3. Схемы и способы измерений геометрических параметров.
4. Порядок экспертизы показателей геометрической точности станка.
5.Влияние отклонений параметров геометрической формы проверяемого станка от установленных норм на точность корпусной детали.
6.Рекомендации по снижению погрешности параметров геометрической точности конкретного станка.
ЭКСПЕРТИЗА ГЕОМЕТРИЧЕСКОЙ ТОЧНОСТИ И ЖЕСТКОСТИ ВЕРТИКАЛЬНО-СВЕРЛИЛЬНЫХ СТАНКОВ КЛАССОВ
Цель работы. Освоение методики определения показателей геометрической точности и жесткости сверлильного станка.
б) нормы точности конкретного сверлильного станка;
г) номенклатуру и основные характеристики оснастки и средств измерений согласно ГОСТ 370 - 93;
д) последовательность и содержание работ по проверке геометрической точности и жесткости станка.
в) реализовывать методы экспертизы геометрической точности сверлильного станка;
г) реализовывать методы экспертизы жесткости сверлильного станка;
д) производить обработку результатов измерений и формулировать выводы по результатам экспертизы.
Методы и средства экспертизы геометрической точности сверлильных станков соответствуют требованиям ГОСТ 22267 - 76 ГОСТ 370 - 93 и рекомендациям ИСО Р 230 - 74.
Номенклатура средств измерения и предъявляемые к ним основные технические требования приведены в Приложении А. Нормы точности станков не должны превышать значений указанных в Приложении В.
1. Плоскостность рабочей поверхности стола.
Для измерений используют метод 3 раздел 4 по ГОСТ 22267 - 76 – с помощью поверочной линейки и показывающего прибора. Измерения проводят в отдельных сечениях рабочей поверхности стола – в трех продольных трех поперечных и двух диагональных. Схема расположения проверяемых сечений представлена на рисунке 13.
Стол должен быть установлен в среднее положение. Схема измерений в каждом сечении рабочей поверхности стола указана на рисунке 2.
Показывающий прибор 4 (индикатор часового типа с магнитной стойкой) устанавливают на проверяемую поверхность так чтобы его измерительный наконечник касался рабочей поверхности линейки и был пе6рпендикулярен ей. Показывающий прибор перемещают по поверяемой поверхности вдоль линейки.
Рисунок 13 – Схема расположения проверяемых сечений
Выпуклость рабочей поверхности стола не допускается. Отклонение от плоскостности равно наибольшей алгебраической разности показаний прибора во всех сечениях.
2. Перпендикулярность рабочей поверхности стола к оси вращения шпинделя.
а) в вертикальной плоскости симметрии станка;
б) в вертикальной плоскости перпендикулярной к плоскости симметрии станка.
Для измерений используют метод 1 раздел 10 по ГОСТ 22267 - 76 – с помощью коленчатой оправки и показывающего прибора. Измерения проводят в нижнем и верхнем положениях подъемного стола. Перед измерением стол и шпиндельная бабка должны быть закреплены. Шпиндельная бабка находится в среднем положении.
Измерения проводят в соответствии со схемой указанной на рисунке 14.
Коленчатую оправку 1 несущую на заданном плече длиной 1 показывающий прибор 2 устанавливают в шпиндель 3 станка. Прибор 2 закрепляют так чтобы его измерительный наконечник касался плоскопараллельной концевой меры длины устанавливаемой на столе 5. Шпиндель поворачивают на полный оборот. Фиксируют показания прибора через каждые 900. Отклонение от перпендикулярности на длине 21 равно наибольшей алгебраической разности показаний прибора в двух диаметрально расположенных точках.
3. Перпендикулярность траектории перемещения шпинделя рабочей поверхности стола.
Рисунок 14 – Схема измерений
Для измерений используют метод 1 б) раздел 9 по ГОСТ 22267 - 76. Схема измерений представлена на рисунке 15.
Рисунок 15 – Схема измерений
Перед измерением стол и шпиндельная бабка должны быть закреплены. На середине стола 1 устанавливают поверочный угольник 2 одной из своих рабочих поверхностей. При этом другая рабочая поверхность совпадает с направлением перемещения. Показывающий прибор 3 закрепляют на шпинделе 4 так чтобы измерительный наконечник касался рабочей поверхности угольника параллельной направлению перемещения и был перпендикулярен ей.
Шпиндель перемещают на длину 250 мм. Измерение проводят в двух взаимно перпендикулярных плоскостях.
Отклонение от перпендикулярности траектории перемещения равно наибольшей алгебраической разности показаний прибора на заданной длине хода.
4. Радиальное биение конуса шпинделя.
Измерения следует проводить по методу 2 раздел 15 по ГОСТ 22267 - 76. Схема измерений представлена на рисунке 16.
Рисунок 16 – Схема измерений
Показывающий прибор 1 устанавливают так чтобы его измерительный наконечник был перпендикулярен шпинделю 2 и проходил через ось вращения. Шпиндель приводят в медленное вращение. Измерения производят в двух поперечных сечениях и в двух точках вдоль оси шпинделя на расстоянии 250 мм. За радиальное биение принимают наибольший из результатов измерений.
5. Осевое биение шпинделя.
Измерения следует проводить по методу 1 раздел 17 по ГОСТ 22267 - 76. Схема измерений указана на рисунке 17.
Короткую оправку 1 с плоским торцом перпендикулярным ее оси устанавливают в шпиндель 2 так чтобы ее ось совпадала с осью вращения. Показывающий прибор 3 устанавливают так чтобы его измерительный наконечник касался центра оправки в направлении оси вращения. Шпиндель поворачивают не менее чем на два оборота. Осевое биение равно наибольшей алгебраической разности показаний прибора.
Рисунок 17 – Схема измерений
МЕТОДИКА ЭКСПЕРТИЗЫ ЖЕСТКОСТИ СТАНКА
Изменение положения оси нагруженного шпинделя к рабочей поверхности стола под действием осевой статической нагрузки проводят:
а) в вертикальной плоскости симметрии (рисунок 18 а);
б) в плоскости перпендикулярной к вертикальной плоскости симметрии проходящей через ось шпинделя (рисунок 18 б).
Рисунок 18 – Схема измерений
На шпинделе 1 станка устанавливают и закрепляют поперечину 2. На рабочем столе 3 закрепляют устройство 4 для создания нагружающей силы Р для измерения которой используют динамометр 5.
Два показывающих прибора 6 закрепляют на столе так чтобы их измерительные наконечники касались торца поперечины 2 на расстоянии L друг от друга.
Производят предварительную нагрузку системы и снимают нагрузку. Устанавливают шкалы показывающих приборов на 0 (натяг измерительного наконечника должен быть 05 – 1 мм). Между столом и шпинделем создают возрастающую нагрузку ступенями через пять делений шкалы индикатора динамометра до заданного значения силы Р. Одновременно при помощи показывающих приборов измеряют перемещение поперечины относительно стола.
Отклонение от перпендикулярности оси нагруженного шпинделя к рабочей поверхности стола определяют как разность показаний приборов. Относительное перемещение под нагрузкой шпинделя и стола определяют как алгебраическую полусумму показаний приборов.
В обратной последовательности производят разгрузку системы.
Проводят двукратные испытания. Наибольшее допускаемое перемещение определяют как среднее арифметическое результатов двух испытаний.
Строят графики зависимости «нагрузка – перемещение» для всей системы и определяют коэффициенты жесткости.
1. Ознакомиться с разделами 1 2 3 настоящих указаний.
2. Ознакомиться с инструкцией по эксплуатации сверлильного станка.
3. Ознакомиться с инструкциями по эксплуатации и основными характеристиками приборов и оснастки.
5.Провести экспертизу геометрической точности и жесткости станка на соответствие нормам.
8.Оценить влияние жесткости станка на точность обрабатываемой детали.
В отчете необходимо указать последовательность действий при выполнении экспертизы точности и жесткости станка составить таблицы измерений графики и сделать выводы по результатам экспертизы.
1. Характеристика геометрических параметров сверлильного станка.
5. Порядок экспертизы жесткости станка.
6. Рекомендации по снижению погрешности параметров геометрической точности конкретного станка.
7. Влияние жесткости станка на точность обрабатываемой детали.
ЛАБОРАТОРНАЯ РАБОТА №3
ЭКСПЕРТИЗА ТОЧНОСТИ ПОЗИЦИОНИРОВАНИЯ РАБОЧИХ ОРГАНОВ МЕТАЛЛОРЕЖУЩЕГО СТАНКА С ЧПУ (ТИПА «ОБРАБАТЫВАЮЩИЙ ЦЕНТР»)
Цель работы. Освоение методики определения показателей точности позиционирования рабочих органов станка с ЧПУ.
Методы экспертизы точности позиционирования соответствуют ГОСТ 27843 - 88.
Экспертизу следует проводить одним из методов:
– при помощи показывающего прибора и плоскопараллельных концевых мер длины;
– при помощи штриховой меры и микроскопа;
– при помощи лазер – интерферометра.
Общие требования к методам проверки – по ГОСТ 8 - 82. Измерения должны проводиться на холостом ходу станка с исключением влияния сил резания и массы изделия.
Номенклатура средств измерения и предъявляемые к ним основные технические требования приведены в Приложении А.
Число контрольных точек при экспертизе устанавливают равным 11 на длине до двух метров. В каждом заданном положении рабочего органа станка должны проводиться не менее 5 измерений (n min= 5).
Последовательность перемещений рабочего органа в заданные положения от исходного до конечного выполняют согласно рисунка 19.
Предпочтительным способом представления результатов проверки является графический.
При экспертизе определяют следующие показатели точности позиционирования:
а) точность двустороннего позиционирования А – это наибольшая разность между предельными значениями независимо от направления перемещения определяемая согласно формуле
где хj или хj - среднее одностороннее отклонение от заданного положения определяемое как среднее арифметическое отклонений от заданного положения определенных в положении Рj в серии n односторонних подходов в заданное положение
Рj – заданное или запрограммированное положение рабочего органа станка в которое он должен переместиться вдоль оси координат;
j – отличает заданное положение от других ;
Рij – положение рабочего органа станка при i - м подходе в j - е заданное положение.
Вместо обозначения х могут применяться другие обозначения соответствующие проверяемой координатной оси.
При позиционировании с подходом в положительном направлении применяют символ а в отрицательном - ;
Sj – среднее квадратичное отклонение от заданного положения определяемая из серии n подходов в заданное положение Pj по формуле
б) Повторяемость двустороннего позиционирования Rmax – это наибольшее значение повторяемости позиционирования в любом заданном положении определяют по формуле
Bj – зона нечувствительности – разность средних односторонних отклонений от заданного положения по выбранной оси координат при противоположных направлениях перемещения
в) максимальная зона нечувствительности Вmax – максимальное значение зоны нечувствительности Вj определяемое в любом заданном положении
Рисунок 19 – Цикл с возвратом шага
г) точность одностороннего позиционирования А и А;
д) повторяемость одностороннего позиционирования R и R
ПОСЛЕДОВАТЕЛЬНОСТЬ ЭКСПЕРТИЗЫ ТОЧНОСТИ
При экспертизе используется метод 1. Схема проверки указана на рисунке 20. Cтол 1 перемещают в крайнее правое положение.
На рабочую поверхность стола устанавливают и закрепляют опору 2 так чтобы его шлифованная поверхность была перпендикулярна поверхности стола и его продольному перемещению. Показывающий прибор 4 закрепляют неподвижно так чтобы его измерительный наконечник касался шлифовальной поверхности опоры 2 и был перпендикулярен ей. Стол перемещают на заданное расстояние L например 100 мм. К шлифованной поверхности опоры 2 притирают плоскопараллельную меру длины 3 с номинальным размером 100 мм и регистрируют показания прибора.
Меру убирают стол возвращают в нулевое положение и регистрируют показания прибора. Действия повторяют пять раз.
Рисунок 20 – Схема измерений
Затем стол перемещают на расстояние 190 мм. На стол устанавливают две меры длины с номинальными значениями 100 мм и 90 мм регистрируют показания прибора. Аналогичные измерения проводят для каждого из 11 положений рабочего стола. Испытания повторяют для поперечного перемещения стола.
1. Ознакомиться с разделами 12 настоящих указаний.
2. Ознакомиться с инструкцией по эксплуатации обрабатывающего центра.
3. Ознакомиться с инструкцией по эксплуатации приборов и оснастки.
4. Настроить схему измерений.
5. Провести проверку точности позиционирования при продольном перемещении рабочего стола.
6. Провести проверку точности позиционирования при поперечном перемещении рабочего стола.
ПРИМЕР ОЦЕНКИ РЕЗУЛЬТАТОВ ЭКСПЕРТИЗЫ ТОЧНОСТИ ПОЗИЦИОНИРОВАНИЯ
Результаты измерений и расчеты полученные при экспертизе точности позиционирования при перемещении рабочего органа станка в заданные положения приведены в диаграммах согласно рисунку 21. Допускается соединить диаграмму для обоих направлений перемещения в одну диаграмму.
Среднее отклонение от заданного положения
Зона нечувствительности
Повторяемость позиционирования
——— перемещение в положительном направлении
– – – – перемещение в отрицательном направлении
Точность двустороннего позиционирования А = 1801 мкм.
Повторяемость двустороннего позиционирования 1349 мкм.
Максимальная зона нечувствительности 448 мкм.
Точность одностороннего позиционирования 15.22 мкм:
Повторяемость одностороннего позиционирования1184 мкм
Средняя зона нечувствительности В =153 мкм.
Рисунок 21 – Диаграммы точности позиционирования
В отчете необходимо указать последовательность действий при выполнении экспертизы точности позиционирования станка составить таблицы измерений диаграммы и сделать выводы по результатам экспертизы.
1. Показатели точности позиционирования рабочих органов станка с ЧПУ
2. Общие требования к проверке точности позиционирования
3. Порядок обработки результатов измерений.
4. Анализ точности используемых методов экспертизы.
5. Анализ диаграмм при оценке точности позиционирования.
6. Порядок экспертизы показателей точности позиционирования
ОПРЕДЕЛЕНИЕ ЖЕСТКОСТИ ФРЕЗЕРНЫХ КОНСОЛЬНЫХ СТАНКОВ С ГОРИЗОНТАЛЬНЫМ ШПИНДЕЛЕМ КЛАССОВ ТОЧНОСТИ Н И П
Цель работы. Освоение методики определения перемещения под нагрузкой рабочего стола фрезерного станка относительно оправки закрепленной в шпинделе.
а) направление действия нагружающей силы;
б) конструкцию контрольной оправки и расположение точки приложения силы;
в) взаимное расположение рабочих органов станка при измерении;
г) последовательность и содержание действий по проверке жесткости станка.
а) устанавливать на станок специальную оправку;
б) устанавливать на станок средства измерения нагружения и оснастку;
в) реализовывать метод определения жесткости рабочих органов фрезерного станка;
Метод определения жесткости фрезерного станка соответствует ГОСТ 17734 - 88. Общие требования к проведению экспертизы металлорежущего станка по ГОСТ 8 - 82.
Жесткость горизонтально-фрезерного станка определяется жесткостью шпинделя серьги и стола с консолью. Значения допусков перемещения под нагрузкой стола должны соответствовать указанным в таблице 1.
Таблица 1 – Значения допусков
Класс точности станка
Направление действия нагружающей силы должно соответствовать указанному на рисунке 22.
Рисунок 22 – Направление действия силы
a = 400 – угол между проекцией нагружающей силы на горизонтальную плоскость и направлением продольной подачи стола;
b = 300 – угол между направлением нагружающей силы и ее проекцией на горизонтальную плоскость;
g = 340 – угол наклона части образующей диска оправки и ее оси;
h = 370 – угол между проекцией нагружающей силы на вертикальную плоскость и направлением продольной подачи стола.
Расположение точки приложения нагружающей силы по отношению к деталям станка должно соответствовать указанным на рисунке 23 и в таблице 2.
Рисунок 23 – Схема приложения нагружающей силы
Таблица 2 – Размеры определяющие взаимное расположение элементов станка и точки приложения нагружающей силы
Наименование размера
Расстояние 1 от оси шпинделя до рабочей поверхности стола
Расстояние 11 от вертикальных направляющих станины до точки приложения силы
Расстояние 12 от точки приложения силы до торца подшипника серьги
Диаметр D конусной части контрольной оправки
Диаметр d цилиндрической части контрольной оправки
МЕТОДИКА ОПРЕДЕЛЕНИЯ ЖЕСТКОСТИ ФРЕЗЕРНОГО СТАНКА
В отверстие шпинделя 1 станка устанавливают контрольную оправку 2 и закрепляют. На свободный конец оправки надевают серьгу 3 и закрепляют на консоли в заданном положении. Консоль устанавливают заподлицо с задней стенкой станины.
На рабочем столе закрепляют устройство для создания нагружающей силы Р для измерения которой используют динамометр. Показывающий прибор 4 закрепляют на столе так чтобы его измерительный наконечник касался торца диска оправки в точке расположенной у периферии в горизонтальной плоскости проходящей через ось оправки. Нагружающую силу прилагают к конусной части диска оправки и направляют через ось оправки направление силы определяют углами a b и g ( см. рисунок 22).
Производят предварительную нагрузку системы и снимают нагрузку. Устанавливают шкалу показывающего прибора на 0 (натяг измерительного наконечника должен быть 05 – 1 мм). Создают возрастающую нагрузку ступенями через пять делений шкалы индикатора динамометра до заданного значения силы Р. Одновременно при помощи показывающего прибора измеряют перемещение оправки относительно стола в направлении поперечной подачи.
Проводят двукратные испытания. Наибольшее допускаемое перемещение определяют как среднее арифметическое результатов двух испытаний. Строят графики зависимости «нагрузка – перемещение» для всей системы и определяют коэффициенты жесткости.
4. Подготовить станок приборы и оснастку для проведения экспертизы жесткости.
5.Провести экспертизу жесткости станка на соответствие нормам .
6.Оценить влияние жесткости станка на точность обрабатываемой детали.
В отчете необходимо указать последовательность действий при выполнении экспертизы жесткости станка составить таблицы измерений графики и сделать выводы по результатам экспертизы.
1. Характеристика жесткости элементов фрезерного станка.
2. Общие требования к определению жесткости элементов станка.
3. Схема и способ определения жесткости станка.
4. Конструкция контрольной оправки.
5. Порядок экспертизы коэффициентов жесткости элементов станка.
6. Влияние жесткости станка на точность обрабатываемой детали.
ЭКСПЕРТИЗА ГЕОМЕТРИЧЕСКОЙ ТОЧНОСТИ ТОКАРНО–РЕВОЛЬВЕРНОГО СТАНКА С ЧПУ МОД. 1В340Ф30 КЛАССА
Цель работы. Освоение методики определения показателей геометрической точности токарно-револьверного станка с ЧПУ.
б) нормы точности станка мод. 1В340Ф30;
в) общие требования к определению геометрической точности станков согласно ГОСТ 8 -82;
г) номенклатуру и основные характеристики оснастки и средств измерений согласно ГОСТ 17 - 70;
в) реализовывать методы экспертизы геометрической точности токарно-револьверного станка;
Методы и средства экспертизы геометрической точности фрезерных станков соответствуют требованиям ГОСТ 22267 - 76 и ГОСТ 17 - 70.
Относительное положение и перемещение узлов станка при измерении должно воспроизводить их положение и перемещение при обработке заготовки.
Номенклатура средств измерения и предъявляемые к ним основные технические требования приведены в Приложении А. Нормы точности станков не должны превышать значений указанных в Приложении Г.
1.Осевое биение шпинделя
Измерения проводят с помощью оправки с шариком и показывающего прибора.
2.Торцевое биение опорного торца шпинделя.
3. Радиальное биение наружной поверхности шпинделя.
Измерения следует проводить с помощью показывающего прибора. Схема измерения указана на рисунке 8.
4.Совпадение осей отверстий для резцедержателей в револьверной головке с осью шпинделя в вертикальной и горизонтальной плоскостях.
Схема измерений указана на рисунке 24.
Рисунок 24 – Схема измерений
В шпинделе 2 закрепляют показывающий прибор 1 так чтобы его измерительный наконечник был перпендикулярен в точке касания цилиндрической поверхности оправки 3 установленной в отверстие для инструмента в револьверной головке 4.
В каждой плоскости измерения производят по двум диаметрально противоположным образующим (шпиндель поворачивают на 1800. Расстояние L = 50 мм.
Отклонение определяют половиной алгебраической разности показаний прибора 1 в данной плоскости. Проверке подвергают все отверстия револьверной головки.
Примечание. При наличии поперечного перемещения револьверной головки предварительно выверяют оправку в горизонтальной плоскости относительно оси шпинделя.
5.Перпендикулярность к оси шпинделя боковых граней револьверной головки с вертикальной осью вращения.
Схема измерений указана на рисунке 25.
Рисунок 25 – Схема измерений
Показывающий прибор 1 устанавливают в шпинделе 2 так чтобы его измерительный наконечник был перпендикулярен в точке касания боковой грани револьверной головки 3 с вертикальной осью вращения.
Шпиндель с прибором поворачивают на 1800.
Отклонение определяют как алгебраическую разность показаний индикатора. Размер D0 = 150 мм.
6.Параллельность оси шпинделя направлению перемещения револьверного суппорта.
Схема измерений указана на рисунке 26.
Рисунок 26 – Схема измерений.
Показывающий прибор 2 закрепляют на револьверной головке 3 так чтобы его измерительный наконечник был перпендикулярен в точке касания цилиндрической поверхности оправки 4 закрепленной на шпинделе 1.
Револьверный суппорт перемещают на длину L = 110 мм. В каждой плоскости измерения производят по двум диаметрально противоположным образующим (шпиндель поворачивают на 1800).
В вертикальной плоскости свободный конец оправки может отклоняться только вверх в горизонтальной – только вперед в сторону инструмента. Отклонение определяют как среднюю арифметическую результатов измерений в данной плоскости.
7.Перпендикулярность к оси шпинделя направления перемещения револьверного суппорта.
Схема измерений указана на рисунке 27.
Рисунок 27 – Схема измерений.
Показывающий прибор 1 устанавливают на револьверном суппорте 3 так чтобы его измерительный наконечник был перпендикулярен в точке касания торцовой поверхности контрольного диска 4 закрепленного в шпинделе 2. Револьверный суппорт 3 перемещают от периферии диска 4 к центру так чтобы расстояние от точки начала отсчета до центра равнялось L = 100 мм.
Отклонение допускается только в сторону передней бабки при перемещении прибора к оси шпинделя. Отклонение определяют как среднюю арифметическую результатов двух измерений (при втором измерении шпиндель поворачивают на 1800).
8.Параллельность осей отверстий для инструмента в револьверной головке направлению ее продольного перемещения в вертикальной и горизонтальной плоскостях.
Схема измерений указана на рисунке 28.
Рисунок 28 - Схема измерений
Показывающий прибор 1 закрепляют вне проверяемого узла 2 так чтобы его измерительный наконечник был перпендикулярен в точке касания цилиндрической поверхности оправки 3 вставленной в отверстие револьверной головки 4.
Револьверной головке сообщают продольное перемещение на длину L = 110 мм. В каждой плоскости отклонение определяют как среднюю арифметическую результатов трех измерений. При последовательных измерениях положение оправки в револьверной головке меняют. Проверке подвергают все отверстия револьверной головки.
2. Ознакомиться с инструкцией по эксплуатации токарно-револьверного станка.
9.При отклонении параметров геометрической формы проверяемого станка от установленных норм оценить влияние измеренных параметров на точность цилиндрической ступенчатой детали заданной преподавателем.
6.Сформулировать рекомендации по снижению погрешности параметров геометрической точности конкретного станка.
1. Характеристика геометрических параметров токарно-револьверного станка.
5.Влияние отклонений параметров геометрической формы проверяемого станка от установленных норм на точность цилиндрической ступенчатой детали.
Фрезерный консольный станок 6Р81Г. Руководство по эксплуатации 6Р81Г.00.000 РЭ 1977. – 185 с.
ГОСТ 8 - 82. Станки металлорежущие. Общие требования к испытаниям на точность. Введ. 01.01.84. – М.: Изд. стандартов 1983. – 11 с.
ГОСТ 17734 - . Станки фрезерные консольные. Нормы точности и жесткости. Введ. 01.01.90. – М.: Изд. стандартов 1988. – 28 с.
ГОСТ 22267 - 76. Станки металлорежущие. Схемы и способы измерений геометрических параметров. Введ. 01.01.78. – М.: Изд. стандартов 1977. – 55 с.
Станок вертикально – сверлильный 1А135. Руководство по эксплуатации. 1А135.00.000 РЭ 1980. – 146 с.
ГОСТ 370 - 93. Станки вертикально – сверлильные. Основные размеры. Нормы точности жесткости. Введ. 01.01.95. – М.: Изд. стандартов 1994. – 21 с.
Станок 6906ВМФ2. Руководство по эксплуатации. 6906ВМФ2.00.000 РЭ 1977. – 243 с.
ГОСТ 27843 - 88. Станки металлорежущие. Методы проверки точности позиционирования. Введ. 01.01.90. – М.: Изд. стандартов 1988. – 19 с.
Проников А. С. Точность и надежность станков с ЧПУ.- М.: Машиностроение 1985. – 256 с.
Станок токарно-револьверный 1В340Ф30. Руководство по эксплуатации. 1В340Ф30.00.000 РЭ 1984. – 95 с.
ГОСТ 17 - 70. Станки токарно-револьверные. Нормы точности. Введ. 01.01.73. – М.: Изд. стандартов 1970. – 28 с.
Таблица А.1 – Номенклатура средств измерения используемых для экспертизы точности фрезерных и сверлильных станков
Наименование обозначение
Метрологические характеристики
Индикатор часового типа
Диапазон измерений +- 50 мкм
Индикатор рычажно-зубчатый
Диапазон измерений до 08 мм
Стойка магнитная для индикатора
Длина линейки 300 мм:
допуск прямолинейности рабочих поверхностей 25 мкм;
допуск параллельности рабочих поверхностей 4 мкм.
Длина линейки 600 – 1000 мм:
допуск прямолинейности 4 мкм;
допуск параллельности 6 мкм
Поверочный угольник с длиной плеч 300 300 мм
Допуск прямолинейности рабочих поверхностей 3 мкм;
Допуск перпендикулярности 5 мкм
Длина измерения 150 мм допуск круглости 12 мкм допуск прямолинейности образующих 25 мкм Допуск параллельности образующих 4 мкм Допуск торцевого биения 2 мкм на радиусе 50 мм
Набор плоскопараллельных мер длины
Диапазон от 05 до 100 мм;
Таблица Б.1 – Нормы точности геометрических параметров фрезерных станков
Пункт методических указаний
Допуск для станков класса точности мкм
Таблица В.1 – Нормы точности геометрических параметров вертикально – сверлильных станков
Таблица Г.1 – Нормы точности геометрических параметров
токарно-револьверного станка
Пункт метод. указаний
Рекомендуемые чертежи
- 24.01.2023
- 24.01.2023
- 15.09.2016
- 23.10.2015