Курсовая работа по метрологии, стандартизации и сертификация. Вариант 54




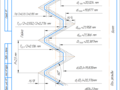
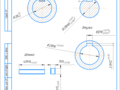
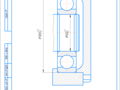
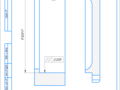
- Добавлен: 24.01.2023
- Размер: 462 KB
- Закачек: 1
Описание
Состав проекта
![]() |
![]() |
![]() |
![]() ![]() ![]() ![]() |
![]() ![]() ![]() ![]() |
![]() ![]() ![]() ![]() |
![]() ![]() ![]() |
![]() ![]() ![]() |
![]() ![]() ![]() ![]() |
![]() ![]() ![]() ![]() |
![]() ![]() ![]() |
![]() ![]() ![]() |
![]() ![]() ![]() ![]() |
![]() ![]() ![]() ![]() |
![]() ![]() ![]() |
![]() ![]() ![]() ![]() |
![]() ![]() ![]() |
![]() ![]() ![]() |
Дополнительная информация
Задание 3,2-вал.cdw

Задание 4 -шпоночное соединение.cdw

Задание 6 резьба.cdw

Задание 1,1-вал.CDW

Задание 2,1-вал.CDW

Задание 5,2-отверстие шлиц.cdw

Задание 5,1-сборочный шлицы.cdw

Задание 3,1-сборочный чертеж.CDW

Задание 2,2-отверстие.CDW

Задание 5,3-вал шлиц.cdw

Задание 1,2 втулка.cdw

Задание 3,3-крышка,корпус.CDW

Задание 1,3 соединение.cdw

Задание 2,3-соединение.CDW

Рекомендуемые чертежи
Свободное скачивание на сегодня
Другие проекты
- 23.08.2014