РГР по метрологии, стандартизации и сертификации




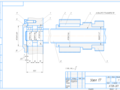

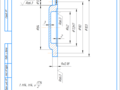
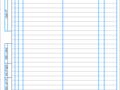
- Добавлен: 24.01.2023
- Размер: 341 KB
- Закачек: 0
Описание
РГР по метрологии, стандартизации и сертификации
Состав проекта
![]() |
![]() |
![]() |
![]() ![]() ![]() ![]() |
![]() ![]() ![]() ![]() |
![]() ![]() ![]() ![]() |
![]() |
![]() ![]() ![]() |
![]() ![]() ![]() ![]() |
![]() |
![]() ![]() ![]() |
![]() |
Дополнительная информация
Узел_17.cdw

Крышка_подшипника.cdw

Спецификация.spw

Колесо зубчатое ведомое
Подшипник 6-306 ГОСТ 8338-75
РГР-МСС.doc
Зачастую это проявлялось в некоторой небрежности при размерной отработке чертежей изделий в части обоснованного назначения технических требований к изготовлению деталей и сборки узлов и соединений.
Между тем именно разработка чертежей и технологической документации связанная с выбором необходимой точности поверхностей и шероховатости обоснованием посадок с учётом технологических особенностей обработки выбором контрольно-измерительных средств расчетом размерных цепей и особенно с обоснованным нормированием отклонений формы и расположения в первую очередь формирует качественные показатели машиностроительных изделий.
Большое значение для развития машиностроения имеет организация производства машин и других изделий на основе взаимозаменяемости создание и применение надежных средств технических измерений и контроля деталей.
Наиболее широко применяется полная взаимозаменяемость которая обеспечивает возможность беспригонной сборки любых независимо одна от другой изготовленных деталей в сборочные единицы а последних – в изделие. Взаимозаменяемыми могут быть как отдельные детали так и сборочные узлы и изделия в целом.
При полной взаимозаменяемости сборку выполняют без доработки деталей и сборочных единиц.
ДОПУСКИ И ПОСАДКИ ГЛАДКИХ ЦИЛИНДРИЧЕСКИХ СОЕДИНЕНИЙ
1 Выбор системы назначение посадок
Выбор системы отверстия или вала для той или другой посадки определяется конструктивными технологическими и экономическими соображениями.
В большинстве случаев отдается преимущество системе отверстия так как она обуславливает значительное уменьшение номенклатуры резального и измерительного инструмента вследствие чего есть более экономичной чем система вала.
Однако в некоторых случаях более преобладает система вала: если детали (валы осы тяги) могут быть изготовлены с точных холоднотянутых прутков без обработки резанием внешних поверхностей если на одном вале чередуются соединения с одинаковыми номинальными диаметрами но с разными посадками.
Важно также правильно выбрать допуски сопряженных размеров соединения так как от этого зависят с одного стороны качество и долговечность а с другого – стоимость и производительность деталей (стоимость – с уменьшением допусков стоимость обработки увеличивается; производительность – от допусков зависят возможности применения целесообразной технологии обработки и сборки деталей а также использование соответствующего оснащения).
2 Назначение и расчет посадки с натягом подшипников качения
Рассчитываем посадку с натягом при сборке соединения при запрессовке зубчатого колеса на вал и нагрузку осевой силой и крутящим моментом.
Исходные данные для расчета:
D1 = 0.048 мEA = EB = 2.06·1011 Па
D2 = 0.080 м Т = 87 Н·м
L = 0.045 м И = 3.14·108 Па
f = 0.14 ТВ = 3.14·108 Па
Определяем наименьшее удельное давление на поверхностях которые сопрягаются:
где f = 0.14 – коэффициент трения на поверхностях которые сопрягаются при сборке под прессом при нормальной температуре.
Находим наибольшее удельное давление на поверхностях которые сопрягаются:
Для дальнейшего расчета принимаем меньшее из двух значений:
Pmax = PmaxА = 498·106 Па.
Определяем коэффициенты СА и СВ:
Определяем предельные значения натягов:
Определяем величину поправки NR которая учитывает смятие микронеровностей поверхностей вала и втулки при сборке изделия:
где КА = КВ = 0.5 для стальной втулки и вала при сборке соединения под прессом при нормальной температуре. RZA = 10мкм RZB = 5 мкм - высота микронеровностей поверхностей втулки и вала по 7 квалитету (предполагается)
Определим минимальный и максимальный расчетные натяги:
Назначаем стандартную посадку в системе отверстия из рекомендованных ГОСТ 25347-82 посадок с натягом. Условием выбора стандартной посадки есть соотношение между расчетными и стандартными предельными натягами:
Назначаем посадку 48.
Рисунок 1 – Схема расположения полей допусков
Запас прочности соединения определяется разностью между расчетными и стандартными натягами.
Эксплуатационный запас прочности необходимый для избежания относительного сдвига деталей при возможных перегрузках:
Технологический запас прочности необходим для предотвращения разрушения деталей соединения при сборке вследствие отклонения режимов сборки от расчетных значений:
3 Обоснование посадок в гладких цилиндрических соединениях
Для гладких цилиндрических соединений заданного изделия в соответствии со служебным назначением устанавливаем следующие посадки:
–соединение “корпус – крышка подшипника ” 72 – посадка с зазором в системе отверстия характеризуется большим гарантированным зазором применяется для неподвижных грубоцентрированных соединений;
–соединение “вал - кольцо” 30 - посадка с зазором в системе отверстия.
НАЗНАЧЕНИЕ И ОБОСНОВАНИЕ ПОСАДОК ПОДШИПНИКОВ КАЧЕНИЯ
Исходные данные: шариковый радиальный однорядный подшипник 6-306 по ГОСТ 8338-75; диаметр внутреннего кольца d =30 мм. Вид нагружения наружного кольца – колебательное так как по условиям работы кольцо воспринимает ограниченным участком окружности дорожки качения равнодействующую от двух радиальных нагрузок (постоянной по направления и вращающейся) и передает ее соответствующему ограниченному участку посадочной поверхности. Нагружение внутреннего кольца – циркуляционное поскольку кольцо воспринимает радиальную нагрузку последовательно всей окружностью и передает ее всей посадочной поверхности вала.
Тип и номинальные размеры подшипников качения определяем по справочнику исходя из предоставленных уловных обозначений в спецификации сборочной единицы.
Колебательно нагруженные кольца имеют плотно подвижное соединение с сопрягаемой деталью (переходная посадка) а циркуляционно-нагруженные колеса имеют неподвижное соединение (посадка с натягом).
Согласно ГОСТ 8338-75 подобрали подшипник 6 класса точности №306 средней серии со следующими параметрами:
Диаметр внутреннего кольца d =30 мм;
Диаметр наружного кольца D =72 мм;
Ширина колец B =19 мм;
Радиус закругления фаски r =2 мм.
Рисунок 2 – Допуски формы и расположения посадочных мест подшипниковых узлов соединения.
РАСЧЕТ ПРЕДЕЛЬНЫХ РАЗМЕРОВ И ПОСТРОЕНИЕ СХЕМЫ РАСПОЛОЖЕНИЯ ПОЛЕЙ ДОПУСКОВ РЕЗЬБОВОГО СОЕДИНЕНИЯ.
Исходные данные: резьба метрическая с диаметром d=8мм с шагом P=125мм. Цилиндрическая резьба характеризуется следующими параметрами: наружный диаметр резьбы d=8мм; внутренний диаметр резьбы d1=6647мм; средний диаметр резьбы d2=7188мм; угол профиля резьбы; высота исходного треугольника резьбы H=108мм [1].
1 Эксплуатационные требования к резьбам зависят от их назначения. Требования надежности долговечности и свинчиваемости без подгонки независимо от изготовленных резьбовых деталей при сохранении эксплуатационных качеств соединений являются общими для всех резьб.
В заданном узле на резьбовое сопряжение не установлено дополнительных требований по точности поэтому назначаем средний класс точности. Для обеспечения подвижности сопряжения назначаем предпочтительную посадку M10 - 7H6h.
2 В соответствии с выбранным характером резьбового соединения устанавливаем по стандарту предельные отклонения размеров и заносим их в таблицу.
Таблица 1 – Численные значения полей допусков для посадки 6H6g.
Рисунок 3 – Схема полей допусков резьбового соединения
Определяем предельные размеры. Вычисляем предельные значения диаметров наружной и внутренней резьбы. Заполняем табл. 4.
Таблица 2 - Численные значения предельных размеров для посадки 6H6g.
Численное значение мм
ОБОСНОВАНИЕ ДОПУСКОВ ФОРМЫ РАСПОЛОЖЕНИЯ И ШЕРОХОВАТОСТИ ПОВЕРХНОСТЕЙ ЗУБЧАТОГО КОЛЕСА И ВАЛА
Установим требования к точности заготовки для зубчатого колеса 2. Они зависят от принятого технологического процесса обработки и методов измерения колеса.
Основные технологические базы колеса:
)отверстие зубчатого колеса которое используется для монтажа колеса на вале в зависимости от степени точности зубчатого колеса избираем 6 степень точности отверстия 11 Н7;
)внешний цилиндр зубчатого колеса который используется для сверки заготовки на зуборезном станке и для контроля размеров зубьев.
Допуск цилиндричности 20 мкм .
Биение внешнего цилиндра заготовки рассчитываем по формуле:
где ТН – допуск на смещение исходного контура.
Допуск внешнего цилиндра заготовки рассчитываем по формуле:
Торцовое биение заготовки зубчатого колеса в зависимости от степени точности по норме контакта зубьев и величины делительного диаметра:
Шероховатость поверхностей зубьев назначаем в зависимости от степени точности Ra = 32 мкм.
Для нерабочих торцовых поверхностей зубчатых колес принимаем Ra = 64 мкм. Другие размеры предельные отклонения назначены с учетом требований ЕСКД на оформление рабочих чертежей.
Поля допусков поверхностей вала назначаем в соответствии с посадками подшипников качения.
Допуск формы и расположения посадочных поверхностей подшипников:
- допуск профиля продольного сечения
- допуск торцевого биения опорных торцевых поверхностей заплечиков вала
Т - допуск соосности посадочных поверхностей вала в подшипниковых узлах
Т = ТТ В10 = 4.02410 = 9.6
где ТТ = 4.0мм – табличное значение допуска соосности посадочных поверхностей вала для длины посадочного места в = 10мм;
В = 24мм – длина посадочного места подшипника;
В зависимости от класса точности подшипников устанавливаем допуск торцового биения 0.030 мм. Шероховатость поверхностей на валу которые сопрягаются с подшипниками Ra = 1.25 мкм шероховатость опорных торцев заплечиков Ra = 2.5 мкм.
В данной курсовой работе произведен анализ конструкции и служебного назначения узла редуктора. Составлены и обоснованы технологические требования предъявляемые к точности изготовления основных деталей и соединений данного редуктора. Назначены и обоснованы посадки всех гладких цилиндрических соединений а также резьбовых соединений.
Определены и выбраны и обоснованы измерительные средства для контроля зубчатого колеса и вала.
Разработаны: сборочный чертеж узла рабочий чертеж крышки зубчатого колеса.
Допуски и посадки: Справочник. В 2 ч.В.Д.Мягков М.А.Палей А.Б.Романов. – Г.: Машиностроение 1982. – ч.1 – 543с.
Допуски и посадки: Справочник. В 2 ч.В.Д.Мягков М.А.Палей А.Б.Романов. – Г.: Машиностроение 1983. – ч.2 – 448с.
СпецификацияУзел 17.spw

содержание.doc
1 Выбор системы назначение посадок5
2 Назначение и расчет посадки с натягом подшипников качения5
3 Обоснование посадок в гладких цилиндрических соединениях9
НАЗНАЧЕНИЕ И ОБОСНОВАНИЕ ПОСАДОК ПОДШИПНИКОВ КАЧЕНИЯ9
РАСЧЕТ ПРЕДЕЛЬНЫХ РАЗМЕРОВ И ПОСТРОЕНИЕ СХЕМЫ РАСПОЛОЖЕНИЯ ПОЛЕЙ ДОПУСКОВ РЕЗЬБОВОГО СОЕДИНЕНИЯ11
ОБОСНОВАНИЕ ДОПУСКОВ ФОРМЫ РАСПОЛОЖЕНИЯ И ШЕРОХОВАТОСТИ ПОВЕРХНОСТЕЙ ЗУБЧАТОГО КОЛЕСА И ВАЛА13
ПРИЛОЖЕНИЕ А (Сборочный чертеж)17
ПРИЛОЖЕНИЕ Б (Рабочий чертеж крышки подшипников)18