Инструментальное обеспечение автоматизированного производства




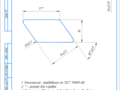
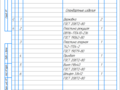
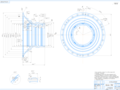
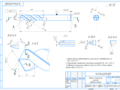
- Добавлен: 24.01.2023
- Размер: 14 MB
- Закачек: 0
Описание
Инструментальное обеспечение автоматизированного производства
Состав проекта
![]() |
![]() |
![]() |
![]() ![]() ![]() ![]() |
![]() ![]() ![]() ![]() |
![]() ![]() ![]() ![]() |
![]() ![]() ![]() ![]() |
![]() |
![]() |
![]() ![]() ![]() ![]() |
![]() |
![]() |
![]() |
![]() ![]() ![]() ![]() |
![]() |
![]() |
![]() ![]() ![]() ![]() |
![]() |
![]() |
![]() ![]() ![]() ![]() |
![]() ![]() ![]() ![]() |
![]() |
![]() |
![]() ![]() ![]() |
![]() ![]() ![]() |
![]() ![]() ![]() |
![]() ![]() |
Дополнительная информация
Пластина.cdw

* - размер для справок
Пластину подвергнуть виброабразивной обработке
Деталь.cdw

Заготовка - штамповка.
Термообработать деталь для снятия напряжения после
механической обработки по технологии главного металурга.
Маркировать электромеханическим способом порядковый номер
номер первого и номер второго отверстия.
Общие требования к изготовлению по ОСТ1 00450-82.
* Размер для справок.
Державка.cdw

Неуказанные предельные отклонения линейных и угловых размеров
Сталь 50ХГ ГОСТ 14959-79
Резец контурный левый.cdw

Неуказанные предельные отклонения размеров отверстий Н14
Термообработка до HRC 40 42.
Материал режущей части ВК8 по ГОСТ 19068-80.
Материал державки Сталь 50ХГ по ГОСТ 14959-79.
Маркировать: 2101-0638.
Фреза концевая.cdw

Неуказанные предельные отклонения размеров отверстий H14
Центровые отверстия выполняются по ГОСТ 14034-74 формы В.
Сверло.cdw

Неуказанные предельные отклонения размеров H14
Обратная конусность рабочей части на 100 мм длины сверла
должна быть 0.1-0.2 мм
резцедержатель с цил хвостовиком.cdw

Неуказанные предельные отклонения размеров отверстий Н14
- размер для справок.
Патрон цанговый.cdw

Шлицевая головка прижимной гайки по ГОСТ 11871-88 под ключ
Хвостовик по ГОСТ 25827-93
Основные размеры по ГОСТ 26539-85
Оребования к изготовлению по ТУ2 035-490-76
Спецификация 2.spw

Пояснилка с формулами 2.docx
Операция 55 – сверлильная (рис. 6). Обработка производится на сверлильно-фрезерно-расточном станке 400V. В этой операции присутствуют следующие переходы: сверление зенкерование.
Для достижения максимальной производительности мной выбрано спиральное цельное твердосплавное сверло мм короткой серии ГОСТ 17277-71. Небольшая длина сверла ввиду короткой серии придает ему повышенную жесткость. Сверло представлено на рисунке 7.
Рис. 7. Сверло спиральное цельное твердосплавное ГОСТ 17277-71.
2.1. Назначение режима резания при сверлении.
Материал детали – жаропрочная сталь ХН73МБТЮ-ВД.
Вид обработки - сверление.
Сверло. Материал режущей части ВК10М ГОСТ 3882-74.
Геометрические параметры: глубина резания t=6.1 мм;
диаметр сверла d=9 мм.
Геометрические параметры режущей части сверла: передний угол задний угол угол подъема винтовой линии угол при вершине .
Назначим режим резания:
подача: S0 =006 ммоб;
скорочть резания: v =9.5 ммин;
частота вращения: n =380 обмин;
осевая сила: P0 =2000 H;
крутящий момент: Мкр =510 Нсм
мощность резания: Nэ =0.2 КВт (табл. 90 [6]).
Назначим период стойкости:
T=15мин (табл.30 [1])
2.2 Расчет опасного сечения сверла.
Силу резания уточняем с помощью программы Расчет режимов резания МГТУ Станкин. Расчет представлен на рисунке 8.
Рис. 8. Расчет режимов резания при сверлении
Момент резания находится по формуле:
С помощью САПР Solid Works находим полярный момент сопротивления опасного сечения . Расчет сечения показан на рисунке 9.
Рис. 9. Характеристика опасного сечения сверла.
Полярный момент сопротивления :
Действующие касательные напряжения находим по формуле:
где М – момент резания
Wp – полярный момент сопротивления.
Предел прочности материала ВК10М Предел прочности на кручение примерно равен:
Так как значит условие прочности соблюдается.
Делаем вывод что инструмент можно эксплуатировать.
3. Расчет конструкции и геометрических параметров режущей части фрезы для операции 70.
Операция 70 – фрезерная (рис. 10). Обработка производится на сверлильно-фрезерно-расточном станке 400V.
Рис. 10. Операция 70.
В операции 55 для фрезерования пазов применим фрезу с диаметром рабочей части 9 мм. Фреза изготавливается целиком из твердого сплава ВК8 ГОСТ 3882-74 т.к. размещение СМП не возможно а применение напайных пластин не целесообразно. Фреза представлена на рисунке 11.
Рис. 11. Фреза концевая твердосплавная ГОСТ 18372-73
3.1. Назначение режима резания при фрезеровании.
Фреза цельная из материала ВК10М ГОСТ 3882-74.
Геометрические параметры:
глубина резания t=2 мм;
диаметр фрезы d=9 мм;
число зубьев фрезы z=4.
Геометрические параметры режущей части: передний угол вспомогательный передний угол задний угол вспомогательный задний угол угол подъема винтовой линии .
Для обработки концевой фрезой предварительно назначаем подачу на зуб Sz=002 – 0.03 ммзуб. (табл.136 [6])
Принимаем Sz=0.25 ммзуб.
Для фрезы скорость резания вычисляется по формуле:
Назначаем период стойкости: T=60 мин (табл. 40 [1]).
Ширина фрезерования равна диаметру фрезы d=В=9мм.
3.2. Расчет опасного сечения фрезы.
Силу резания определяем с помощью программы Расчет режимов резания МГТУ Станкин. Расчет представлен на рисунке 12.
Рис. 12. Расчет режимов резания при фрезеровании.
Составляющая силы резания:
Момент резания находится по формуле (16):
С помощью САПР Solid Works находим полярный момент сопротивления опасного сечения . Расчет сечения показан на рисунке 13.
Рис. 13. Характеристика опасного сечения фрезы.
Полярный момент сопротивления
Действующие касательные напряжения находим по формуле (17):
где М – момент резания Wp – полярный момент сопротивления (находится по формуле (18)).
Выбор вспомогательного инструмента для режущего инструмента используемого на операциях 10 55 70.
Эффективность работы станков с ЧПУ повышение их производительности в значительной мере зависит от технического уровня вспомогательного инструмента (с. 281 [2])..
Конструкция вспомогательного инструмента для станков с ЧПУ определяется его основными элементами: присоединительными поверхностями для крепления его на станке и для крепления режущего инструмента. Устройства осуществляющие автоматическую смену инструмента и его крепление на станках определяют конструкцию хвостовика. Для получения размеров деталей без пробных проходов в соответствии с программой необходимо введение в конструкцию вспомогательного инструмента устройств обеспечивающих регулирование положения режущих кромок. Эти обстоятельства привели к появлению разнообразных проводников (адаптеров) у которых хвостовик сконструирован для конкретного станка а передняя зажимная часть для инструмента со стандартными присоединительными поверхностями которые образуют комплект вспомогательного инструмента состоящий из резцедержателей патронов оправок и втулок различных конструкций предназначенных для крепления режущего инструмента (с. 282 [2]).
Режущие инструменты могут устанавливаться непосредственно в резцедержатель станка токарной группы либо через промежуточный вспомогательный инструмент (переходные оправки и втулки). Эти элементы в свою очередь крепятся в позициях револьверной головки с помощью специальных устройств различных конструкций.
Для установки контурного левого резеца с механическим креплением многогранной пластины с углом в плане 93º ГОСТ 20872-80 выбираю резцедержатель с циллиндрическим хвостовиком с открытым пазом. При выборе резцедержателя необходимо учитывать расположение револьверной головки относительно обрабатываемой детали и вида резца (правый или левый). Выбираем левое исполнение резцедержателя. Резцедержатель представлен на рисунке 14.
Рис. 14. Резцедержатель.
Для установки резца на необходимой высоте служит прокладка 4. Крепление резца осуществляется с помощью винтов 3 и прижимной планки 2 удерживаемой на креплении 5.
Крепление резцедержателя в револьверной головке представленно на рисунке 15.
Рис. 15. Крепление резцедержателя в револьверной головке
Крепление инструмента в револьверной головке производится при помощи клина имеющего рифление но смещенного относительно рифленого хвостовика. В результате опорная поверхность вспомогательного инструмента прижимается к револьверной головке станка с усилием в несколько тонн. Жесткость такого соединения увеличивается до 3 раз по сравнению с жесткостью хвостовика без рифления.
Для крепления концевой фрезы и сверла на станке с ЧПУ на операциях 55 и 70 будет использоваться патрон цанговый (рисунок 16). Используем соединение конических поверхностей с конусностью 7:24 по ГОСТ 25827-93. Такой конус не является самотормозящимся и позволяет легко извлекать оправку из шпинделя станка.
Рис. 16. Патрон цанговый используемый для крепления сверла и фрезы.
– корпус 2 – гайка шлицевая 3 – цанга.
Инструмент в нашем случае сверло или концевая фреза устанавливается в разрезную цангу 3 которая имеет 8 прорезей с двух сторон. Цанга в корпусе 1 крепится за счет шлицевой гайки 2. Гайка и цанга сопрягаются по конической поверхности поэтому при завинчивание гайки цанга сжимается обеспечивая надежное закрепление инструмента.
Конус хвостовика патрона не является самотормозящимся и позволяет легко извлекать оправку из шпинделя станка с ЧПУ 400V. Крутящий момент со шпинделя передается с помощью торцовых шпонок. Оправка удерживается в шпинделе с помощью тяги и тарельчатых пружин или затягивается винтом. Движение передается тяге или винту от гидроцилиндра или электродвигателя.[4]
В ходе работы был произведен анализ базового технологического маршрута изготовления детали «Носок ТВД» и предложен более рациональный маршрут обработки с использованием современного мехатронного станочного оборудования. Для обработки большинства операций были выбраны два станка: токарный станок с ЧПУ Mori Seiki NL1500S и Станок сверлильно-фрезерно-расточный 400V. Повышение стоимости станочного оборудования взамен старого объясняется сокращением времени затраченного на производство детали и загрузкой станков другими задачами.
Из предложенного маршрута обработки для курсовой работы я выбрал операции 10 55 и 70 содержащие следующие виды обработок: точение контурное сверление и фрезерование. Для которых спроектировал режущий инструмент и подобрал инструментальную оснастку.
Операция 10 выполняется на токарном станке Mori Seiki NL1500S. Для достижения максимальной производительности мной был выбран контурный левый резец с механическим креплением многогранной пластины с углом в плане 93º ГОСТ 20872-80 которым можно обработать большинство поверхностей за один переход. Применение МНП гарантирует оптимальность и постоянство геометрических параметров необходимую точность ликвидировало необходимость переточки резца. Данная режущая пластина обеспечивает также стружколомание. В ходе проверочных расчетов я убедился что резец удовлетворяет требованиям к прочности и жесткости а следовательно гарантирует нам необходимую точность детали. Для установки резеца на станок с учетом расположения револьверной головки относительно обрабатываемой детали и вида резца (в моем случае - левый) выбираю резцедержатель с циллиндрическим хвостовиком с открытым пазом левого исполнения.
Операции 55 и 70 производится на сверлильно-фрезерно-расточном станке 400V. Для достижения необходимой жесткости и прочности назначаю инструмент: сверло спиральное цельное твердосплавное ГОСТ 17277-71 и фреза концевая твердосплавная ГОСТ 18372-73. Инструмент был выбран по возможности меньшей длины для повышения жесткости. Для установки инструмента на станок будет использоваться патрон цанговый с конусом хвостовика 7:24. Такой конус не является самотормозящимся и позволяет легко извлекать оправку из шпинделя станка что важно для автоматизированного производства.
Справочник технолога – машиностроителя. В 2-х т. Под ред. А.Г. Косиловой и Р.К. Мещерякова. - 4-е изд. перераб. и доп. – М.: Машиностроение 1985. 496 с. ил.
Оснастка для станков с ЧПУ. Справочник Ю.А. Кузнецов А.Р. Маслов А.Н. Байков. – М.: Машиностроение 1983. - 359 с.: ил.
Сборник задач и примеров по резанию металлов и режущему инструменту Н.А. Нефедов Осипов К.А. – 5-е изд. перераб. и доп. – М.: Машиностроение 1990. 448 с. ил.
Справочник инструментальщика И.А. Ординарцев Г.В. Филиппов А.Н. Шевченко и др.; Под общ. ред. И.А. Ординарцева. – Л.: Машиностроение. Ленингр. отд-ние 1987. – 846 с. ил.
Расчет режимов резания при механической обработке. Методические указания к курсовой работе по дисциплине «Физические основы рабочих процессов» для специальности «Мехатроника».
Режимы резания труднообрабатываемых материалов: Справочник Я. Л. Гуревич М. В. Горохов В. И. Захаров и др. 2-е изд. перераб. и доп.-М.: Машиномтроение 1986 240 с. ил.
ГОСТ 17274-71. Сверла спиральные цельные твердосплавные. Короткая серия.
ГОСТ 20872-80. Резцы токарные сборные для контурного точения с механическим креплением многогранных твердосплавных пластин. Конструкция и размеры.
ГОСТ 19062-80. Пластины режущие сменные многогранные твердосплавные параллелограммной формы с углом 55 град. и стружколомающими канавками на одной стороне. Конструкция и размеры.
ГОСТ 19079-80. Пластины опорные сменные многогранные твердосплавные параллелограммной формы. Конструкция и размеры.
ГОСТ 18372-73 Фрезы концевые твердосплавные. Технические условия.
ГОСТ 14959-79. Углеродистые стали. Марки.
ГОСТ 3882-74. Сплавы твердые спеченные. Марки.
ГОСТ 25827-93. Хвостовики инструмента с конусом 7:24. Размеры.
ГОСТ 24900-81. Хвостовики державок цилиндрические для токарных станков с программным управлением. Основные размеры.
Анализ конструкции обрабатываемой деталей. Уточнение маршрутной и операционной технологии изготовления деталей
1.Анализ конструкции детали
2.Базовый технологический маршрут
3.Разработка предложений по изменению маршрутной технологии изготовления детали
4.Описание используемых станков с ЧПУ
Подбор режущего инструмента для операций точение фрезерование и сверление
1.Расчет конструкции и геометрических параметров режущей части контурного резца для операции 10
1.1. Расчет режимов резания
1.2. Расчет на прочность винта крепления
1.3. Расчет размеров державки резца
1.4. Проверка державки на прочность и жесткость
2.Расчет конструкции и геометрических параметров режущей части сверла для операции 55
2.1.Назначение режима резания при сверлении
2.2. Расчет опасного сечения сверла
3.Расчет конструкции и геометрических параметров режущей части фрезы для операции 70
3.1. Назначение режима резания при фрезеровании
3.2. Расчет опасного сечения фрезы
Выбор вспомогательного инструмента для режущего инструмента используемого на операциях 10 55 70
титульный лист.doc
Государственное образовательное учреждение высшего профессионального образования
Уфимский государственный авиационный технический университет.
Кафедра мехатронных станочных систем.
Пояснительная записка
к курсовой работе по дисциплине
Инструментальное обеспечение мехатронных систем
Пояснилка с формулами.docx
Дальнейшее направление развития обработки металлов резанием: интенсификация процессов резания освоение обработки новых материалов повышение точности и качества обработки применение упрочняющих процессов автоматизации и механизации обработки. Также важную роль в обеспечении процесса механической обработки играет инструментальная подготовка производства так как от эффективности точности и работоспособности инструмента во многом зависит качество и эффективность всего процесса.
На сегодняшний день актуальной задачей является: определение путей совершенствования режущих инструментов выявление наиболее рациональных материалов используемых для производства режущих инструментов изучение свойств и качеств инструментальных материалов.
Одним из главных элементов любого машиностроительного производства вообще а автоматизированного в особенности является инструментальная оснастка обеспечивающая надежность функционирования каждого отдельного станка и производственной системы в целом качество продукции и производительность. Роль инструментальной оснастки в условиях высокоавтоматизированного гибкого производства возросла так что способна определять конструкцию и схему построения отдельных станков и систем (инструментальные магазины их запасные комплекты манипуляторы для замены инструментов автоматические инструментальные склады и транспортеры системы компенсации износа инструмента и т. д.). В последние годы конструкция инструментов претерпевает принципиальные изменения (стр. 3 [4]).
Основные отличительные особенности конструкций современных инструментов можно свести к следующим направлениям:
- использование в качестве режущих элементов механически закрепляемых многогранных неперетачиваемых пластин (МНП) различных режущих материалов (твердых сплавов режущей керамики синтетических сверхтвердых материалов);
- применение малоразмерных твердосплавных инструментов что позволило использовать их для резьбонарезающих мелкомодульных зубонарезающих и других инструментов;
- использование при изготовлении инструментов синтетических сверхтвердых материалов (СТМ);
- применение одно- и многослойных покрытий наносимых на твердые сплавы и быстрорежущие инструментальные стали;
- использование подвода СОЖ под высоким давлением непосредственно в зону резания;
- повышение точности исполнительных размеров формы и взаимного расположения как рабочих так и крепежных поверхностей и режущих элементов;
- разработка различных модульных систем инструментов в целях повышения универсальности инструментов автоматического производства и расширения спектра технологических задач (стр. 4 [4]).
В курсовой работе мной спроектирован режущий инструмент и инструментальная оснастка для операций включающих такие переходы как точение сверление и фрезерование обработки детали «Носок ТВД».
Анализ конструкции обрабатываемой деталей. Уточнение маршрутной и операционной технологии изготовления деталей.
1. Анализ конструкции детали.
Деталь называется «Носок ТВД» первоначально предложенный состав материала стали очень сложный и содержит много компонентов что свидетельствует о том что деталь ответственная и имеет важное значение в сборке готовой конструкции или узла.
Масса заготовки 27кг заготовка - отливка.
Материал детали: жаропрочная сталь ХН73МБТЮ-ВД (ЭИ698-ВД) ГОСТ 22411-77 относится к труднообрабатываемым материалам МПа.
Процентное содержание элементов:
Назначение сплава ХН73МБТЮ ГОСТ 22411-77 : изготовление деталей авиационной техники (лопаток газовых турбин термообработанных и обточеных штамповок дисков дефлекторов лабиринтов и носков) с рабочей температурой до +750 °C; крепежных и других деталей работающих при температуре до 750-800 °С.
Габаритные размеры: Dma Dmin= мм а наименьший диаметр который необходимо обработать составляет 3мм. Деталь выполняется по седьмому и восьмому квалитету точности. Шероховатость точных поверхностей Ra=04мкм остальных Ra=1.6мкм. Суммарная погрешность формы и расположения оценивается торцевым биением равным 002мкм допуском перпендикулярности равным 002мкм и позиционным допуском отверстий равным 005мкм.
В детали имеется множество отверстий симметричных и асимметричных относительно осей ряд канавок пазов резьб на наружной и
внутренней поверхностях что усложняет обработку.
2. Базовый технологический маршрут.
Рассмотрим базовую маршрутную технологию изготовления детали. Базовый технологический маршрут представлен в таблице 1.1.
Базовый технологический маршрут.
Наименование операции
Оборудование модель станка
Контроль ультрозвуком
Слесарная(случайная)
Сдача на участок сборки
3. Разработка предложений по изменению маршрутной технологии изготовления детали.
В ходе анализа маршрута обработки по базовому технологическому процессу были введены следующие коррективы.
Максимально сконцентрированы операции. Объединены операции выполняемые на одних и тех же поверхностях с целью выполнить максимальное количество операций за одну установку т.е. повысить производительность. Объединены операции с учетом обработки на контр-шпинделе исключены операции по доводке режущих кромок инструментов ввиду использования неперетачиваемых твердосплавных пластин с одно- и многослойными покрытиями. Подробно это можно увидеть в таблице 1.2.
Предлагаемый маршрут обработки.
Комбинированная операция:
Притирочная(случайная)
4. Описание используемых станков с ЧПУ.
Для обработки большинства операций были выбраны два станка: токарный станок с ЧПУ Mori Seiki NL1500S и Станок сверлильно-фрезерно-расточный 400V.
Описание Токарного станка с ЧПУ модели Mori Seiki NL1500S:
Станок многоцелевой токарный патронно-центровой с ЧПУ Mori Seiki NL1500S предназначен для выполнения разнообразных токарных работ при обработке деталей различной сложности в условиях единичного и серийного производства. Вид и компановка станка представлены на рисунке 2.
Станина станка представляет собой жесткую и прочную конструкцию. Наклонное расположение станины обеспечивает свободный сход стружки и доступ в зону резания.
На суппорте станка установлена револьверная головка дискового типа с закрепленным на ней инструментом. Станок имеет контр-шпиндель.
Имеется возможность оснащения различными токарными патронами и различными револьверными головками с приводным инструментом.
Рис. 2. Вид и компоновка станка MORI SEIKI NL1500S
На рисунке 2 показаны важнейшие узлы станка:
- шпиндельная головка
– револьверная головка
– головка контр-шпинделя
Технические характеристики станка MORI SEIKI NL1500S приведены в таблице 1.3.
Технические характеристики станка MORI SEIKI NL1500S.
Макс. вращения над станиной (при закрытой фронтальной двери)
Макс. вращения над поперечными салазками
Макс. длина обработки
Перемещение по оси Х
Перемещение по оси Z
Перемещение по оси Y
Макс. скорость шпинделя и контршпинделя
Револьверная головка
Количество инструментов (все приводные)
Макс. скорость на приводных инструментах
Габариты и массса станка
Описание станка 400V:
Станок сверлильно-фрезерно-расточный с автоматической сменой инструмента (АСИ) и числовым программным управлением (ЧПУ) модели 400V предназначен для комплексной обработки деталей из различных конструкционных материалов в условиях единичного мелкосерийного и серийного производства. Выполняет операции сверления зенкерования развертывания получистового и чистового растачивания отверстий нарезания резьбы метчиками и фрезами фрезерования. Область применения: машиностроительные предприятия различных отраслей промышленности.
Возможно оснащение станка поворотным столом для четырехкоординатной обработки. Также возможно оснащение щупами для измерения детали и инструмента.
Технические характеристики станка 400V приведены в таблице 1.4.
Технические характеристики станка 400V.
Размер рабочей поверхности стола мм
Наибольшее расстояние от торца шпинделя до стола мм
Наибольшая масса обрабатываемой детали кг
Пределы частот вращения шпинделя обмин
Номинальный крутящий момент на шпинделе Нм
продольное перемещение стола (Х)
поперечное перемещение колонны (Y)
вертикальное перемещение шпиндельной бабки (Z)
Точность позиционирования мм
Мощность двигателя главного привода кВт
Номинальная частота вращения обмин
Максимальная частота вращения обмин
Габаритные размеры мм
Подбор режущего инструмента для операций точение фрезерование и сверление.
Из предложенного маршрута обработки выбираем операции 10 55 и 70 содержащие следующие виды обработок: точение контурное сверление и фрезерование соответственно. Для которых спроектируем режущий инструмент и подберем инструментальную оснастку.
1. Расчет конструкции и геометрических параметров режущей части контурного резца для операции 10.
Операция 10 – токарная (рис. 3). Обработка производится на токарном станке с ЧПУ MORI SEIKI NL1500S. В этой операции присутствуют следующие переходы: точение продольное подрезка торцев точение конусной поверхности и растачивание отверстия.
Для достижения максимальной производительности мной выбран контурный левый резец с механическим креплением многогранной пластины с углом в плане 93º ГОСТ 20872-80 которым можно обработать большинство поверхностей за один переход. Резец представлен на рисунке 4.
Рис. 4. Контурный левый резец с механическим креплением многогранной твердосплавной пластины. ГОСТ 20872-80.
-державка 2- винт 3-прихват 4-штифт 5-режущая пластина 6-опорная пластина.
В качестве режущей части резца применяется сменная четырехгранная пластина 5 твердосплавная ГОСТ 19062-80. Материал режущей пластины - ВК8 ГОСТ 3882-74 (табл. 13 [6]). Сечение державки квадратное со стороной 25 мм (табл. 12 [1]) Установленный период стойкости резца: 25 мин – с твердосплавными пластинами.
1.1. Расчет режимов резания.
Расчет режимов резания будем вести по наиболее тяжелым условиям т.е. для чернового точения.
Выбираем глубину резания t=3 мм.
Подача S=050 060мм (табл. 20 [6]). Принимаем S=055мм.
Марка твердого сплава для режущей части – ВК8.
Геометрические параметры режущей части резца:
Главный угол в плане φ=930.
Вспомогательный угол в плане φ'=320.
Главный задний угол α=100.
Радиус при вершине резца R=1мм.
Скорость резания Vрез =46 ммин (табл. 44 [6]).
Составляющая силы резания :
Сp=5600; (с. 74 [6])
PZ=5600308505507546-015=5089 Н.
1.2. Расчет на прочность винта крепления.
На резец во время работы действует составляющая силы резания Pz на прихват со стороны режущей пластины действует сила Р (рис. 5).
Рис. 5. Схема действия сил.
-державка 2-винт 3-прижим 4-штифт 5-режущая пластина 6-опорная пластина.
Режущая пластина 5 стремиться повернуться под действием режущей силы вокруг кромки опорной пластины 6 следовательно зависимость между этими двумя силами будут описываться следующим уравнением:
где b – расстояние от кромки опорной пластины 6 до кромки режущей пластины 5 b=06 мм;
a – расстояние от кромки опорной пластины 6 до точки давления прихвата 3 на режущую пластину 5 a=843 мм.
Из приведенного уравнения (2) получаем:
Сила Р растягивает винт 2 крепления прихвата 3 следовательно создаваемое при этом напряжения растяжения должно быть меньше или равно допускаемому напряжения растяжения для материала винта 2.
Площадь поперечного сечения винта 2:
Где d – внутрений деаметр резьбы винта М8. d= 7.5.
Напряжение растяжения для опасного сечения винта:
Подставив известные данные получаем:
Делаем вывод что данный винт выдерживает необходимые нагрузки.
1.3. Расчет размеров державки резца.
Материал державки резца – углеродистая Сталь 50ХГ по ГОСТ 14959-79 с в = 980 МПа и допускаемым напряжением на изгиб из = 785 МПа. Форма сечения державки - квадратное.
Определим поперечное сечения державки резца.
где l – расстояние от вершины резца до рассматриваемого сечения (вылет резца). Принимаем l = 150 мм.
Значит принятое значение размера державки мм по ГОСТ 20872-80 выдержит изгибающие нагрузки.
1.4. Проверка державки на прочность и жесткость.
Максимальная нагрузка допускаемая прочностью резца:
Максимальная нагрузка допускаемая жесткостью резца:
где f – допускаемая стрела прогиба при черновом точении f=01 мм;
E – модуль упругости материала державки резца E = 210000 МПа;
J – осевой момент инерции квадратного сечения державки
Подставляем (8) в (7) и получаем:
Резец обладает достаточной прочностью и жесткостью т. к. :
793 Н >5089 Н 7631 Н.
Делаем вывод что условие прочности и жесткости выполняется резец можно эксплуатировать.
Рекомендуемые чертежи
- 24.01.2023
- 04.11.2022