Детали машин




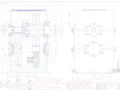
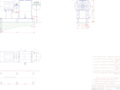
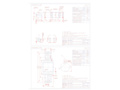
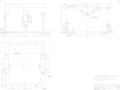
- Добавлен: 24.01.2023
- Размер: 2 MB
- Закачек: 0
Описание
Состав проекта
![]() |
![]() |
![]() ![]() ![]() |
![]() |
![]() ![]() ![]() ![]() |
![]() ![]() ![]() ![]() |
![]() ![]() ![]() |
![]() ![]() ![]() ![]() |
![]() ![]() ![]() ![]() |
![]() ![]() ![]() |
![]() ![]() ![]() ![]() |
Дополнительная информация
пояснительная записка.doc
Тяговая сила цепи Ft = 600 даН = 6 кН.
Скорость движения грузовой цепи v = 085 мс.
Шаг грузовой цепи p = 125 мм.
Число зубьев звездочки z =7.
Тип редуктора – соосный вертикальный цилиндрический.
Передача привода – нет.
Выбор электродвигателя.
1.Требуемая мощность на выходе.
2 КПД всего привода.
где hмс = 098 – КПД соединительной муфты;
hз(бс) = 097 – КПД закрытой зубчатой передачи (быстроходной ступени);
hз(тс) = 097 – КПД закрытой зубчатой передачи (тихоходной ступени);
hпк = 099 – КПД учитывающий потери пары подшипников качения ;
3 Требуемая мощность электродвигателя.
4 Частота вращения приводного вала.
Здесь диаметр делительной окружности звездочки определяется следующим образом:
5 Подбор электродвигателя.
Следуя справочным данным выбираем электродвигатель 132S6 с синхронной частотой вращения nc = 1000 обмин. для которого номинальная мощность Рдв = 55 кВт (допускаем перегрузку в 55%) асинхронная частота вращения nдв = 965 обмин.
6 Передаточное число привода.
где частные передаточные отношения отдельных передач
uр – передаточное отношение редуктора.
nв – частота вращения выходного вала:
В итоге u=965582»16.
7 Разбивка передаточного числа редуктора по ступеням.
Для двухступенчатого соосного редуктора.
Передаточное число быстроходной ступени:
Передаточное число тихоходной ступени:
Кинематический расчет.
Быстроходный вал редуктора:
мощность P1=Pдв×hмс×hпк=5500×098×099=53361 Вт.
частота вращения n1= nдв=965 обмин.
угловая скорость w1=p×n130=p×96530=101 c-1.
крутящий момент T1=P1w1=53361101=528 Н×м.
Промежуточный вал редуктора:
мощность P2=P1×hб×hпк=53361×097×099=51243 Вт.
частота вращения n2= n1uб=9654=24125 обмин.
угловая скорость w2=p×n230=p×2412530=2525 c-1.
крутящий момент T2=P2w2=512432525=2029 Н×м.
Тихоходный вал редуктора:
мощность P3=P2×hт×hпк=51243×097×099=49209 Вт.
частота вращения n3= n2uт=241254=603 обмин.
угловая скорость w3=p×n330=p×60330=63 c-1.
крутящий момент T3=P3w3=4920963=7811 Н×м.
мощность P4=P3×hмс×hпк=49209×098×099=47743 Вт.
частота вращения n4= n3=603 обмин.
угловая скорость w4=w3=63 c-1.
крутящий момент T4=P4w4=4774363=7578 Н×м
Расчет цилиндрической зубчатой передачи (быстроходная ступень).
Т2 = 2029 Н×м — вращающий момент на колесе;
n2Т = 24125 обмин — частота вращения колеса;
u = 4— передаточное число;
1. Материалы колеса и шестерни.
В качестве материала для цилиндрического колеса применяем ст.40Х. Применяем т.о. колеса – улучшение твердость сердцевины НВ 269 302 твердость поверхности НВ 269 302.
Механические свойства: sT = 750 МПа.
В качестве материала для шестерни используем ст.40Х. Применяем т.о. шестерни – улучшение твердость сердцевины НВ 269 302 твердость поверхности НВ 269 302.
Механические свойства: sТ = 750 МПа.
2. Допускаемые напряжения.
Вычисляем допускаемые контактные напряжения.
допускаемые контактные напряжения:
[s]H = 18+67 = 18×2855+67=5809 МПа;
допускаемые напряжения на изгиб:
[s]F = 103 = 103×2855=29407 МПа;
предельные допускаемые напряжения:
3 Межосевое расстояние:
где Ka – коэффициент межосевого расстояния; Ка = 4300 – для косозубых колес;
ya – коэффициент ширины венца по межосевому расстоянию: т.к. колеса в зацеплении расположены несимметрично относительно опор то ya = 0315.
Коэффициент концентрации нагрузки для прирабатывающихся колес при постоянном режиме КHb = 1.
Эквивалентный момент на колесе ТНЕ2 = КНдТ2
где — коэффициент долговечности.
Здесь: КНЕ — коэффициент эквивалентности зависящий от режима нагружения (при постоянном режиме нагружения КНЕ=1);
NHG=()3=2327117638 — базовое число циклов нагружений.
В итоге коэффициент циклов .
Следовательно эквивалентный момент на колесе ТНЕ2 = Т2 = 2029 Н.
Межосевое расстояние в итоге:
Принимаем стандартное значение межосевого расстояния aw=125мм.
4 Предварительные основные размеры колеса.
- делительный диаметр:
где yа – коэффициент ширины колеса yа=0315.
принимаем стандартное значение b2 = 63м.
где коэффициент Km принимают для косозубых колес: Km =58.
ТFE=КFдТ2—эквивалентный момент на колесе
где — коэффициент долговечности. Здесь NFG=4×106— базовое число циклов. При N³108 принимаем KFд=10.
Т.о. эквивалентный момент на колесе ТFE=Т2=2029 Н.
Модуль принимает значение:
Принимаем модуль передачи равным m = 10 мм.
6 Суммарное число зубьев и угол наклона.
Минимальный угол наклона зубьев косозубых колес
Суммарное число зубьев
zS=2×125×cos 318° 1 = 249
Определяем действительное значение угла
b = arccos (zSm 2aw).
b = arccos (249×1 2×125) = 513°.
7 Число зубьев шестерни и колеса.
Число зубьев шестерни
Для косозубых колес z1m
z1 = 249(4+l) = 50 ³ z1min.
Число зубьев колеса: z2 = zS - z1 = 249 – 50 = 199.
8 Фактическое передаточное число
Фактическое передаточное число uф= z2 z1 = 199 50 = 398.
Допускаемое отклонение от заданного передаточного числа 4%.
Делительные диаметры d:
шестерни d1 =z1mcosb = 50×1 cos 513° = 502 мм;
колеса d2 =2aw- d1 = 2×125 – 502 = 1998 мм.;
Диаметры окружностей вершин da и впадин df зубьев:
10 Размеры заготовок колес.
Чтобы получить при термической обработке принятые для расчета механические характеристики материала колес требуется чтобы размеры заготовок колес не превышали предельно допустимых значений: Dзаг Dпред; Сзаг Sзаг Sпред;
Значения Dзаг Sзаг Сзаг (мм) вычисляют по формулам:
для цилиндрической шестерни Dзаг=dа+6 мм = 522 + 6 = 582 мм 200 мм;
Для колеса с выточками принимают меньшее из значений Сзаг= 05b2 = 05×63= 315мм. 125 мм; и Sзаг=8m =8мм.
11 Силы в зацеплении
-окружная Ft=2T2d2 = 2×2029 01998 = 2031 Н;
-радиальная Fr=Fttgacosb = 2031×0364 cos 513° = 7423 Н.
(для стандартного угла a=20° tga=0364);
-осевая Fa = Fttgb = 2031×tg 513° = 1823 Н.
12 Проверка зубьев колес по напряжениям изгиба.
Расчетное напряжение изгиба в зубьях колеса:
sF2=KFaKFbKFvYbYF2FtE(b2m) [s]F2
Для колес с b>0° принимают для 9-ой степени точности KFa=1.
Степень точности передачи принимаем в зависимости от окружной скорости колеса (мс) степень точности 9-ая.
Коэффициент концентрации нагрузки KFb принимают для прирабатывающихся колес при постоянной нагрузке KFb=1.
Коэффициент динамической нагрузки принимают согласно окружной скорости КFv = 107. Коэффициент Yb вычисляют по формуле Yb=1—b°140 = 096. Коэффициент формы зуба YF2 = 36 YF1 = 365.
FtE = KFдFt — эквивалентная окружная сила. Коэффициент долговечности KFд = 1. Т.е. FtE= Ft = 2031 Н.
sF2=1×1×107×096×36×2031(0063×0001) = 1192 МПа 29407 МПа.
Расчетное напряжение в зубьях шестерни:
sF1=sF2YF1 YF2 [s]F1
sF1=1192×365 36 = 1209 29407 МПа.
13 Проверка зубьев колес по контактным напряжениям.
Расчетное контактное напряжение
где для косозубых колес КНa = 11; КН= 27×105; КНb = 1; KHv = 103.
Расчет цилиндрической зубчатой передачи (тихоходная ступень).
Т2 = 7811 Н×м — вращающий момент на колесе;
n2Т = 603 обмин — частота вращения колеса;
u = 4 — передаточное число;
В качестве материала для цилиндрического колеса применяем ст.40Х. Применяем т.о. шестерни – улучшение и закалка ТВЧ твердость сердцевины НВ 269 302 твердость поверхности НRC 45 50.
В качестве материала для шестерни используем ст.40Х. Применяем т.о. шестерни – улучшение и закалка ТВЧ твердость сердцевины НВ 269 302 твердость поверхности НRC 45 50.
допускаемые контактные напряжения: [s]H = 14 + 170 = 835 МПа
допускаемые напряжения на изгиб: [s]F = 370 МПа;
NHG – базовое число циклов нагружений.
Следовательно эквивалентный момент на колесе ТНЕ2 = Т2 = 7811 Н.
Принимаем стандартное значение межосевого расстояния равное значению межосевого расстояния быстроходной ступени aw=125 мм.
принимаем стандартное значение b2 = 63 мм.
Т.о. эквивалентный момент на колесе ТFE=Т2=19736.
Принимаем модуль равным m = 2мм.
zS=2×125×cos638° 2 = 124
b = arccos (124×2 2×125) = 725°.
z1 = 124(4+l) = 25 ³ z1min.
Число зубьев колеса: z2 = zS - z1 = 124 – 25 = 99.
Фактическое передаточное число uф= z2 z1 = 99 25 = 396.
Отклонение от заданного передаточного отношения не превышает допускаемых 4%.
шестерни d1 =z1mcosb = 25×2 cos 725° = 504 мм;
колеса d2 =2aw- d1 = 2×125 – 504 = 1996 мм.;
для цилиндрической шестерни Dзаг=dа+6 мм = 504 + 6 = 564 мм 200 мм;
Для колеса с выточками принимают меньшее из значений Сзаг= 05b2 = 05×63 = 315 мм. 125 мм; и Sзаг=8m = 16мм.
-окружная Ft=2T2d2 = 2×7811 01996 = 78267 Н;
-радиальная Fr=Fttgacosb = 78267×0364 cos 725° = 28719 Н.
-осевая Fa = Fttgb = 78267×tg725° = 9957 Н.
Коэффициент динамической нагрузки принимают согласно окружной скорости КFv = 101 Коэффициент Yb вычисляют по формуле Yb=1—b°140= =0948. Коэффициент формы зуба YF2 = 36 YF1 = 39.
FtE = KFдFt — эквивалентная окружная сила. Коэффициент долговечности KFд = 1. Т.е. FtE= Ft = 78267 Н.
sF2=1×1×101×0948×36×78267(0063×0002) = 2141 МПа 370 МПа.
sF1=2141×39 36 = 232 370 МПа.
где для косозубых колес КНa = 11; КН= 27×105; КНb = 1; KHv = 101.
Диаметры различных участков валов редуктора определяем следующим образом:
Диаметр d выходного конца:
d ³ (7 8) 3ТБ = (7 8) 3528 = 2626 30 мм.
Согласуя диаметр выходного конца быстроходного вала редуктора с диаметром выходного конца вала электродвигателя принимаем d = 30 мм.
Диаметр вала под подшипник dп ³ d + 2t ³ 344 мм
где высота буртика t = 22 мм;
Принимаем dп = 35 мм.
Диаметр dбп ³ dп + 3r ³ 425 мм.
где координата фаски подшипника r = 25 мм;
Принимаем dбп = 42 мм.
Диаметр dк: dк ³ (6 7) 3ТПр = (6 7) 32029 = 3525 4113 мм.
Принимаем dк = 40 мм.
Диаметр dбк: dбк ³ dк + 3f = 436 мм.
где размер фаски f = 12 мм;
Принимаем dбк = 45 мм.
Диаметр dбп: dбп ³ dп + 3r = 425 мм.
Принимаем dбп = 45 мм.
Диаметр вала под подшипник dп = dk – 3r = 325 мм
d ³ (5 6) 3ТТ = (5 6) 37811 = 46 55 мм.
Принимаем d = 50 мм.
Диаметр вала под подшипник dп ³ d + 2t ³ 556 мм
где высота буртика t = 28 мм;
Принимаем dп = 55 мм.
Диаметр dбп ³ dп + 3r ³ 64 мм.
где координата фаски подшипника r = 3 мм;
Принимаем dбп = 64 мм.
Диаметр dк ³ dбп = 64 мм.
2 Конструктивные размеры зубчатых колес.
2.1 Быстроходная ступень
Цилиндрическая шестерня выполняется за одно целое с валом. Ее размеры: d1 = 502 мм; da1 = 522 мм; b1 = 67 мм.
Цилиндрическое зубчатое колесо кованое. Его размеры:
d2 = 1998 мм; da2 = 2018 мм; b2 = 63 мм.
Диаметр ступицы колеса: dст = 15*d + 10 мм = 15* 40 + 10мм = 70 мм.
Длина ступицы колеса: lст = (12 15)*d = (12 15)* 40 = 48 60 мм.
принимаем lст = 63 мм.
Толщина обода: d = (25 4)*m = (25 4)*1 мм = 25 4 мм.
Толщина диска: С = 03*b2 = 03*63 мм = 189 мм. Принимаем С = 18 мм.
Диаметр центровой окружности: Dотв = (Dо + dст) * 05
Do = da2 – [2d + 2(24m + 2m)] = 2018 – [2*4 + 2(24*1 + 2*1)] = 185 мм.
Dотв = (185 + 70) * 05 = 1275 мм.
Диаметр отверстий в колесе:
dотв » (Do - dст) = (185 - 70) = 2875 мм.
принимаем dотв = 30 мм.
2.2 Тихоходная ступень
Цилиндрическая шестерня выполняется за одно целое с валом. Ее размеры: d1 = 504 мм; da1 = 544 мм; b1 = 67 мм.
d2 = 1996 мм; da2 = 2036 мм; b2 = 63 мм.
Диаметр ступицы колеса: dст = 15*d + 10 мм = 15*64 + 10мм = 106 мм.
Длина ступицы колеса: lст = (12 15)*d = (12 15)*64 = 768 96 мм.
принимаем lст = 83 мм.
Толщина обода: d = (25 4)*m = (25 4)*2 мм = 5 8 мм.
Do = da2 – [2d + 2(24m + 2m)] = 2036 – [2*8 + 2(24*2 + 2*2)] = 170 мм.
Dотв = (170 + 106) * 05 = 138 мм.
dотв » (Do - dст) = (170 - 106) = 16 мм.
принимаем dотв = 16 мм.
Для передачи момента с вала электродвигателя на быстроходный вал редуктора используем упругую втулочно-пальцевую муфту.
1 Быстроходная ступень
По ГОСТ 21424-75 для посадочного диаметра d=30 мм применяем муфту со следующими параметрами:
Передаваемый вращающий момент не более T= 125 Н×м (в нашем случае 528 Н×м).
Угловая скорость не более 480 с-1. (в нашем случае 101 с-1)
Длины отверстий: lкон =38 мм.
Габаритные размеры: L =121 мм; D=120 мм; d0=28 мм.
Смещение осей валов не более: радиальное Dr=03; угловое Dg=1°30.
Зазор между полумуфтами С=3 5мм.
Остальные параметры муфты рассчитываются по следующим соотношениям: B»025D=30мм; b»05B=15мм; D0=D-(15 16)d0=78мм; dст=16d=48 мм.
Размеры втулок и пальцев:
диаметр пальца dп =14мм.
длина пальца lп=33мм.
резьба выходного конца пальца d0 М10.
количество пальцев z=6.
диаметр втулки упругой dв =27мм.
длина втулки упругой lв=28мм.
Пальцы муфты изготовленные из стали 45 рассчитываем на изгиб:
Упругие элементы муфты проверяют на смятие в предположении равномерного распределения нагрузки между пальцами:
Выбранная муфта подходит.
Консольная нагрузка от муфты: Fм50T1 125T1= 3633 9083 Н. Принимаем значение Fм=650 Н.
2 Тихоходная ступень
По ГОСТ 21424-75 для посадочного диаметра d=50 мм применяем муфту со следующими параметрами:
Передаваемый вращающий момент не более T= 810 Н×м (в нашем случае 7811 Н×м).
Угловая скорость не более 315 с-1. (в нашем случае 63 с-1)
Длины отверстий: lкон =56 мм.
Габаритные размеры: L =170 мм; D=190 мм; d0=36 мм.
Смещение осей валов не более: радиальное Dr=04; угловое Dg=1°.
Остальные параметры муфты рассчитываются по следующим соотношениям: B»025D=475мм; b»05B=2375мм; D0=D-(15 16)d0=136мм; dст=16d=80 мм.
диаметр пальца dп =18мм.
длина пальца lп=42мм.
резьба выходного конца пальца d0 М12.
количество пальцев z=8.
диаметр втулки упругой dв =35мм.
длина втулки упругой lв=36мм.
Консольная нагрузка от муфты: Fм200T2=5590 Н.
Шпонки призматические со скругленными торцами. Материал - сталь 45 термообработка – нормализация. Напряжения смятия и условия прочности:
Допускаемые напряжения смятия:
-при стальной ступице: [sсм] = 100 120 МПа.
-при чугунной ступице: [sсм] = 60 80 МПа.
Диаметр вала под полумуфту 30 мм.
Сечение шпонки bh = 87 мм.
Глубина паза t1 = 4 мм.
Длина шпонки l = 50 мм.
т.к. материал полумуфты – чугун.
Условие прочности выполняется.
2 Промежуточный вал.
Диаметр вала под цилиндрическое колесо 40 мм.
Сечение шпонки bh = 128 мм.
Глубина паза t1 = 5 мм.
Длина шпонки l = 56 мм.
т.к. материал цилиндрического колеса – сталь.
Диаметр вала под цилиндрическое колесо 64 мм.
Сечение шпонки bh = 1811 мм.
Глубина паза t1 = 7 мм.
Длина шпонки l = 76 мм.
Диаметр вала под звездочку 50 мм.
Сечение шпонки bh = 149 мм.
Глубина паза t1 = 55 мм.
Условие прочности не выполняется. Ставим вторую шпонку из расчета симметричности распределения нагрузки имеем sсм= ×165=72МПа - нагрузка воспринимаемая одной шпонкой. Таким образом sсм»[sсм] т.е. условие выполняется.
Проверочный расчет подшипников.
Силы в зацеплении: Ft = 2031 Н Fr = 7423 Н. Fa= 1823 Н.
Консольная сила от муфты: Fм=650 Н.
Частота вращения вала n = 1390 обмин.
Расстояния: lб = 120 мм lм = 60 мм
Приемлемая долговечность подшипников Lh = 20000 часов.
1.1 Определение опорных реакций.
В вертикальной плоскости:
SY =0 RDy – Fr +RBy = 0;
2 – 9501 + 5181 = 0.
В горизонтальной плоскости:
765–2603+1765+750=0.
1.2 Определение суммарных реакций опор.
1.3 Выбор типа подшипника
Тип подшипника выбираем в соответствии с установившейся практикой проектирования и эксплуатации машин.
Для быстроходного вала dп = 45 мм. принимаем наиболее дешевый шарикоподшипник радиальный однорядный № 209 легкой серии с параметрами: d = 45 мм D = 85 мм В = 19 мм r = 2 мм; грузоподъемность: Cr = 257 кН Cor = 181 кН .
1.4 Выбор коэффициентов
Первоначально задаемся коэффициентами:
Кк – коэффициент учитывающий вращение колец; при вращении внутреннего кольца Кк = 1.
Ks – коэффициент безопасности при кратковременной перегрузке Ks =12.
KT – температурный коэффициент KT =1.
1.5 Определение осевых составляющих реакций:
Отношение осевой нагрузки подшипника Ra=Fa к статической грузоподъемности: RaC0 = 194318100 = 001. По табличным данным определяем e=018.
Отношение осевой нагрузки к радиальной:
Для опоры D: RaKкRD=1943(1×17313)= 0112.
Т.к. RaKкRD e X=1; Y=0.
Для опоры B: RaKкRB=1943(1×5473)= 0355.
Т.к. RaKкRB > e X=056; Y= 249.
1.6 Определение эквивалентной нагрузки.
где R – радиальная нагрузка действующая на опору Н.
Fa – осевая нагрузка действующая на опору Н.
X – коэффициент радиальной нагрузки.
Y – коэффициент осевой нагрузки;
Для опоры D: RE = 1·1·17313·12·1= 207756 Н.
Для опоры B: RE = (1·056·5473+249·1943)·12·1= 948 Н.
1.7 Расчетная долговечность в часах для более нагруженной опоры D.
Полученный вариант устраивает.
Силы в цилиндрическом зацеплении быстроходной ступени: Ft2 = 2603 Н Fr2 = 9501 Н Fa2= 1943 Н.
Силы в цилиндрическом зацеплении тихоходной ступени: Ft1 = 130832 Н Fr1 = 48299 Н. Fa1= 22129 Н.
Частота вращения вала n = 1672 обмин.
Расстояния: l1 = 60 мм l2 = 150 мм l3 = 120мм.
2.1 Определение опорных реакций.
Вертикальная плоскость.
В вертикальной плоскости имеем
SY =0 RDy + Fr2 – Fr1 +RAy = 0;
205 + 9501 – 48299 +5593 = 0.
Горизонтальная плоскость.
В горизонтальной плоскости имеем:
579 + 26034 – 130832 + 7221 = 0.
2.2 Определение суммарных реакций опор.
Дальнейший расчет для более нагруженной опоры D.
2.3 Выбор типа подшипника
Для опор промежуточного вала dп = 45 мм. принимаем наиболее дешевый шарикоподшипник радиальный однорядный № 209 легкой серии с параметрами: d = 45 мм D = 85 мм В = 19 мм r = 2 мм; грузоподъемность: Cr = 257 кН Cor = 181 кН .
2.4 Выбор коэффициентов
2.5 Определение осевых составляющих реакций:
Отношение осевой нагрузки подшипника Ra=Fa1+Fa2 к статической грузоподъемности: RaC0=2407218100=013. По табличным данным определяем e=019.
RaKкRD=24072(1×103074)= 0234.
Т.к. RaKкRB > e X=056; Y=23.
2.6 Определяем эквивалентную нагрузку.
RE = (1·056·103074+23·24072)·12·1= 135705 Н.
2.7 Расчетная долговечность в часах.
Полученный вариант недостаточен используем конические однорядные роликоподшипники №7308 со следующими параметрами: d = 45 мм D = 100 мм Tma r1 = 08 мм; грузоподъемность: Cr = 761 кН Cor = 593 кН . Схема установки – «врастяжку». Фактор нагрузки: e=029.
1.5 Находим осевые составляющие реакций.
SA=083×e×RA=083×029×9134=220;
SD=083×e×RD=083×029×103074=2481;
Т.к. SA SD и Ra=24072 Н > SD – SA = 2261 Н то
FaA = SA =220; FaD = Ra+SD = 48882;
При принимаем X=1; Y=0.
При принимаем X=04; Y=209.
1.6 Определяем эквивалентную нагрузку.
Опора A: RE = 9134·12·1= 1096 Н.
Опора D: RE = (1·04·103074+209·24072)·12·1= 109848 Н.
Силы в цилиндрическом зацеплении тихоходной ступени: Ft2 = 130832 Н Fr2 = 48299 Н. Fa2= 22129 Н.
Частота вращения вала n = 322 обмин.
Консольная сила от муфты: Fм= 8885 Н.
Расстояния: lц = 80 мм lб = 180 мм.
3.1 Определяем опорные реакции.
SY =0 Fцy – RGy – Fr2 +REy = 0;
8938 – 1346 – 2340 + 22644 = 0.
993 – 2217 – 45195 + 36372 = 0.
3.2 Определяем суммарные реакции опор.
Как видно опора E является более нагруженной поэтому по ней ведем дальнейшие расчеты.
3.3 Выбор типа подшипника
Для опор промежуточного вала dп = 75 мм применяем компактные конические однорядные роликоподшипники легкой серии №7215 со следующими параметрами: d = 75 мм D = 130 мм Tma r1 = 08 мм; грузоподъемность: Cr = 976 кН Cor = 845 кН . Схема установки – «врастяжку». Фактор нагрузки: e=039.
SE=083×e×RE=083×041×42845=1458;
SG=083×e×RG=083×041×32235=1097;
Т.к. SE SG и Ra=15254Н > 0 Н то
FaE = SE =1458; FaG = Ra+SE = 29834;
При принимаем X=04; Y=145.
Опора E: RE = 42845·12·1= 51414 Н.
Опора G: RG = (1·04·32235+188·29834)·12·1= 82778 Н.
для роликоподшипников параметр a23 = 07
Проверочный расчет валов на прочность.
Проверочный расчет проводится для проверки прочности в опасном сечении в зависимости от направления и величины действующих на него нагрузок. Напряжение изгиба изменяется по симметричному циклу а касательные напряжения кручения по пульсирующему.
1.1 Выбор материала вала
Для изготовления быстроходного вала выбрали материал сталь 40Х твердость не менее 200НВ; s-1 = 320 МПа и t-1 = 200МПа – пределы выносливости при симметричном цикле изгиба и кручения.
1.2 Строим расчетную схему вала.
Из предыдущих разделов имеем
Силы в зацеплении: Ft = 15124 Н Fr = 5555 Н. Fa= 2034 Н.
Консольная сила от муфты: Fм=500 Н.
Реакции: RDy = 2264 Н RBy =3291 Н .
Расстояния: lб = 100 мм lм = 40 мм
1.3 Определим величину изгибающих моментов в характерных сечениях А B С D.
В горизонтальной плоскости.
В вертикальной плоскости.
справа: MСx = RBy·lб = 3291·50=165
1.4 Крутящий момент в сечениях вала.
Строим эпюру крутящих моментов.
1.5 Определение опасного сечения
Как видно из эпюр изгибающих моментов опасным сечением вала является сечение С. Определяем суммарный изгибающий момент в сечении С.
1.6 Осевой момент сопротивления сечения С.
1.7 Полярный момент сопротивления сечения С.
1.8 Амплитуда симметричного цикла по изгибу.
1.9 Амплитуда касательных напряжений:
1.10 Среднее напряжение цикла при изгибе
sm = 0 tm = ta = 088 Нмм2.
1.11 Принимаем коэффициенты
концентрации напряжений: Ks = 19; Kt = 16;
масштабных факторов: Еs = 085; Еt = 073;
коэффициенты учитывающие влияние среднего напряжения цикла на усталостную прочность: ys = 01 yt= 05.
1.12 Определяем коэффициенты запаса прочности вала в сечении С по напряжениям изгиба
1.13 Определяем коэффициенты запаса прочности вала в сечении С по напряжениям кручения
1.14 Расчетный коэффициент запаса прочности :
Сопротивление усталости обеспечивается.
2.1 Выбор материала вала
2.2 Строим расчетную схему вала.
Силы в цилиндрическом зацеплении быстроходной ступени: Ft2 = 15124 Н Fr2 = 5555 Н. Fa2 = 2034 Н.
Силы в цилиндрическом зацеплении тихоходной ступени: Ft1 = 45195 Н Fr1 = 1714 Н. Fa1= 1322 Н.
Реакции: RDy = 8035 Н RAy =355 Н .
Расстояния: l1 = 50 мм l2 = 70 мм l3 = 90мм
2.3 Определим величину изгибающих моментов в характерных сечениях А B С D.
MBx1 = RDy·(l1+l2) + Fа1·d1 – Fr1·l2 =
= 8035·120·10-3+·1322·573·10-3–1714·70·10-3= 143 Н·м;
MBx2 = RDy·(l1+l2) + Fа1·d1 – Fr1·l2 +Fа2·d2 =
=8035·120·10-3+·1322·573·10-3–1714·70·10-3+·2034·1735·10-3=32 Н·м;
2.4 Крутящий момент в сечениях вала.
2.5 Определение опасного сечения
2.6 Осевой момент сопротивления сечения С.
2.7 Полярный момент сопротивления сечения С.
2.8 Амплитуда симметричного цикла по изгибу.
2.9 Амплитуда касательных напряжений:
2.10 Среднее напряжение цикла при изгибе
sm = 0 tm = ta = 178 Нмм2.
2.11 Принимаем коэффициенты
масштабных факторов: Еs = 0785; Еt = 0685;
2.12 Определяем коэффициенты запаса прочности вала в сечении С по напряжениям изгиба
2.13 Определяем коэффициенты запаса прочности вала в сечении С по напряжениям кручения
2.14 Расчетный коэффициент запаса прочности :
3.1 Выбор материала вала
Для изготовления тихоходного вала выбрали материал сталь 40Х твердость не менее 200НВ; s-1 = 320 МПа и t-1 = 200МПа – пределы выносливости при симметричном цикле изгиба и кручения.
3.2 Строим расчетную схему вала.
Силы в цилиндрическом зацеплении: Ft2=45195 Н; Fr2=1714 Н; Fa2=1322 Н.
Консольная нагрузка от цепной передачи Fц=357876 Н. Проекции на оси соответственно: Fцy=Fцs Fц
Реакции: REy = 22644 Н RGy =2340 Н REx = 36372 Н RGx =2217 Н.
3.3 Определим величину изгибающих моментов в характерных сечениях E F G H.
MFx2 = Fцy·(lц+lб)–RGy·lб+Fa2·d2 =
= 178938·170·10-3 – 2340·90·10-3+1322··1667·10-3=2038 Н·м;
3.4 Крутящий момент в сечениях вала.
3.5 Определение опасного сечения
Как видно из эпюр изгибающих моментов опасным сечением вала является сечение F. Определяем суммарный изгибающий момент в сечении F.
3.6 Осевой момент сопротивления сечения F.
3.7 Полярный момент сопротивления сечения F.
3.8 Амплитуда симметричного цикла по изгибу.
3.9 Амплитуда касательных напряжений:
3.10 Среднее напряжение цикла при изгибе
sm = 0 tm = ta = 64 Нмм2.
3.11 Принимаем коэффициенты
масштабных факторов: Еs = 081; Еt = 07;
3.12 Определяем коэффициенты запаса прочности вала в сечении F по напряжениям изгиба
3.13 Определяем коэффициенты запаса прочности вала в сечении F по напряжениям кручения
3.14 Расчетный коэффициент запаса прочности :
Смазывания зубчатого зацепления и подшипников качения производится маслом заливаемым внутрь корпуса редуктора до уровня обеспечивающего погружение зубчатого колеса примерно на 10 мм. Объем масляной ванны определяется из расчета 025 дм3 на 1 кВт передаваемой мощности:
V = 025 · 4 = 1 дм3 = 1 л.
Устанавливаем вязкость масла. При контактных напряжениях sH = 693 МПа и скорости v = 25 мс рекомендуемая кинематическая вязкость масла должна быть примерно равна 50 · 10-6 м2с.
Выбираем масло индустриальное И – 50А с кинематической вязкостью (47 55) · 10-6 м2с по ГОСТ 20799-75.
Посадки зубчатого колеса и подшипников.
Посадки назначают в соответствии с ГОСТ 25347 – 82.
-посадка полумуфты на ведущий вал: ;
-посадка зубчатого колеса на вал: ;
-посадка звездочки цепной передачи на ведомый вал: ;
-посадка подшипников качения:
отклонение отверстия Н7;
- посадка распорных колец: .
- посадка шпоночных соединений: .
- посадка крышек подшипниковых узлов: .
Сборка редуктора осуществляется в следующей последовательности:
Установить корпус редуктора на стенд (посредством кран-балки или вручную).
Вручную установить в гнезда редуктора предварительно собранный быстроходный вал (т.е. на валу запрессованы подшипники).
Вручную установить в гнезда редуктора предварительно собранный промежуточный вал (т.е. на вал запрессованы подшипники посредством шпонки зафиксировано цилиндрическое колесо). На этом этапе предполагается организация конического зацепления.
Вручную установить в гнезда редуктора предварительно собранный тихоходный вал (т.е. на валу посредством шпонки зафиксировано зубчатое колесо одеты втулки и запрессованы подшипники). На этом этапе предполагается организация зубчатого зацепления.
Установить крышку редуктора с помощью кран-балки.
Разметить 2 отверстия под штифты (линейка штангенциркуль).
Просверлить 2 отверстия под штифты (электродрель).
Заштифтовать (молоток).
Закрепить смотровое окошко.
Установить две глухие крышки подшипников.
Установить две сквозные крышки подшипников в сборе (т.е. в крышки вмонтированы манжеты).
Установить шпонку под полумуфту (молоток).
Установить шпонку под звездочку (молоток).
Далее следует проверить вращение колеса от руки проконтролировать биение выходного вала. Также следует контролировать болтовые соединения в момент затяжки. Осуществить контроль герметичности.
Дунаев П.Ф. Леликов О.П. Детали машин. Курсовое проектирование: Учебное пособие для ВУЗов.– М.: Высшая школа 1984.
Куклин Н.Г. Куклина Г.С. Детали машин: Учебник для ВТУЗов – М.: Высшая школа 1999.
Устюгов И.И. Детали машин: Учебное пособие для учащихся ВТУЗов. – 2-е изд. перераб. и доп.– М.: Высшая школа 1981.
Чернавский С.А. Боков К.Н. Чернин И.М. и др. Курсовое проектирование деталей машин: Учебное пособие для учащихся машиностроительных специальностей.– 2-е изд. перераб. и доп.– М.: Машиностроение 1988.
Исходные данные для проектирования.2
Выбор электродвигателя.3
Кинематический расчет.5
Расчет цилиндрической зубчатой передачи (быстроходная ступень).6
Расчет цилиндрической зубчатой передачи (тихоходная ступень).12
Проверочный расчет подшипников.26
Проверочный расчет валов на прочность.36
Посадки зубчатого колеса и подшипников.49
_деталировка.dwg

Данные для контроля зубчатого венца выбирают по ГОСТ 1643-81
Коэффициент смещения
разноименных профилей
взаимного положения
Направление линии зуба
Данные для контроля зубчатого венца
выбирают по ГОСТ 1643-81
Сталь 40Х ГОСТ 4543-71
ДМ ПК 01.05.00.00.03.СБ
_привод.dwg

Внутреннюю стенку необработанной части корпуса и крышки покрасить маслостойкой краской
а снаружи - серой нитроэмалью. 2. Перед окончательной сборкой стыки фланцев корпуса покрыть пастой "Герметик". 3. В редуктор залитбь 3 л. масла марки И-30А.
* Размер обеспечивает инструмент.
Данные для контроля зубчатого венца выбирают по ГОСТ 1643-81
Внутреннюю стенку необработанной части корпуса и крышек покрасить маслостойкой краской
а снаружи - серой нитроэмалью.
Перед окончательной сборкой стыки
фланцев корпуса покрыть пастой "Герметик
План размещения отверстий под фундаментные болты
Осевое смещение валов до 2 мм.
Радиальное смещение валов до 2 мм.
Перекос валов до 1 градуса.
Техническая характеристика
Окружная сила на тяговых звездочках
Скорость движения тяговой цепи
Частота вращения приводного вала
Общее передаточное число привода
Мощность электродвигателя
Частота вращения электродвигателя
ДМ.ПК.01.05.00.00.00.СБ
_пояснительная записка.doc
Тяговая сила цепи Ft = 600 даН = 6 кН.
Скорость движения грузовой цепи v = 085 мс.
Шаг грузовой цепи p = 125 мм.
Число зубьев звездочки z =7.
Тип редуктора – соосный вертикальный цилиндрический.
Передача привода – нет.
Выбор электродвигателя.
1.Требуемая мощность на выходе.
2 КПД всего привода.
где hмс = 098 – КПД соединительной муфты;
hз(бс) = 097 – КПД закрытой зубчатой передачи (быстроходной ступени);
hз(тс) = 097 – КПД закрытой зубчатой передачи (тихоходной ступени);
hпк = 099 – КПД учитывающий потери пары подшипников качения ;
3 Требуемая мощность электродвигателя.
4 Частота вращения приводного вала.
Здесь диаметр делительной окружности звездочки определяется следующим образом:
5 Подбор электродвигателя.
Следуя справочным данным выбираем электродвигатель 132S6 с синхронной частотой вращения nc = 1000 обмин. для которого номинальная мощность Рдв = 55 кВт (допускаем перегрузку в 55%) асинхронная частота вращения nдв = 965 обмин.
6 Передаточное число привода.
где частные передаточные отношения отдельных передач
uр – передаточное отношение редуктора.
nв – частота вращения выходного вала:
В итоге u=965582»16.
7 Разбивка передаточного числа редуктора по ступеням.
Для двухступенчатого соосного редуктора.
Передаточное число быстроходной ступени:
Передаточное число тихоходной ступени:
Кинематический расчет.
Быстроходный вал редуктора:
мощность P1=Pдв×hмс×hпк=5500×098×099=53361 Вт.
частота вращения n1= nдв=965 обмин.
угловая скорость w1=p×n130=p×96530=101 c-1.
крутящий момент T1=P1w1=53361101=528 Н×м.
Промежуточный вал редуктора:
мощность P2=P1×hб×hпк=53361×097×099=51243 Вт.
частота вращения n2= n1uб=9654=24125 обмин.
угловая скорость w2=p×n230=p×2412530=2525 c-1.
крутящий момент T2=P2w2=512432525=2029 Н×м.
Тихоходный вал редуктора:
мощность P3=P2×hт×hпк=51243×097×099=49209 Вт.
частота вращения n3= n2uт=241254=603 обмин.
угловая скорость w3=p×n330=p×60330=63 c-1.
крутящий момент T3=P3w3=4920963=7811 Н×м.
мощность P4=P3×hмс×hпк=49209×098×099=47743 Вт.
частота вращения n4= n3=603 обмин.
угловая скорость w4=w3=63 c-1.
крутящий момент T4=P4w4=4774363=7578 Н×м
Расчет цилиндрической зубчатой передачи (быстроходная ступень).
Т2 = 2029 Н×м — вращающий момент на колесе;
n2Т = 24125 обмин — частота вращения колеса;
u = 4— передаточное число;
1. Материалы колеса и шестерни.
В качестве материала для цилиндрического колеса применяем ст.40Х. Применяем т.о. колеса – улучшение твердость сердцевины НВ 269 302 твердость поверхности НВ 269 302.
Механические свойства: sT = 750 МПа.
В качестве материала для шестерни используем ст.40Х. Применяем т.о. шестерни – улучшение твердость сердцевины НВ 269 302 твердость поверхности НВ 269 302.
Механические свойства: sТ = 750 МПа.
2. Допускаемые напряжения.
Вычисляем допускаемые контактные напряжения.
допускаемые контактные напряжения:
[s]H = 18+67 = 18×2855+67=5809 МПа;
допускаемые напряжения на изгиб:
[s]F = 103 = 103×2855=29407 МПа;
предельные допускаемые напряжения:
3 Межосевое расстояние:
где Ka – коэффициент межосевого расстояния; Ка = 4300 – для косозубых колес;
ya – коэффициент ширины венца по межосевому расстоянию: т.к. колеса в зацеплении расположены несимметрично относительно опор то ya = 0315.
Коэффициент концентрации нагрузки для прирабатывающихся колес при постоянном режиме КHb = 1.
Эквивалентный момент на колесе ТНЕ2 = КНдТ2
где — коэффициент долговечности.
Здесь: КНЕ — коэффициент эквивалентности зависящий от режима нагружения (при постоянном режиме нагружения КНЕ=1);
NHG=()3=2327117638 — базовое число циклов нагружений.
В итоге коэффициент циклов .
Следовательно эквивалентный момент на колесе ТНЕ2 = Т2 = 2029 Н.
Межосевое расстояние в итоге:
Принимаем стандартное значение межосевого расстояния aw=125мм.
4 Предварительные основные размеры колеса.
- делительный диаметр:
где yа – коэффициент ширины колеса yа=0315.
принимаем стандартное значение b2 = 63м.
где коэффициент Km принимают для косозубых колес: Km =58.
ТFE=КFдТ2—эквивалентный момент на колесе
где — коэффициент долговечности. Здесь NFG=4×106— базовое число циклов. При N³108 принимаем KFд=10.
Т.о. эквивалентный момент на колесе ТFE=Т2=2029 Н.
Модуль принимает значение:
Принимаем модуль передачи равным m = 10 мм.
6 Суммарное число зубьев и угол наклона.
Минимальный угол наклона зубьев косозубых колес
Суммарное число зубьев
zS=2×125×cos 318° 1 = 249
Определяем действительное значение угла
b = arccos (zSm 2aw).
b = arccos (249×1 2×125) = 513°.
7 Число зубьев шестерни и колеса.
Число зубьев шестерни
Для косозубых колес z1m
z1 = 249(4+l) = 50 ³ z1min.
Число зубьев колеса: z2 = zS - z1 = 249 – 50 = 199.
8 Фактическое передаточное число
Фактическое передаточное число uф= z2 z1 = 199 50 = 398.
Допускаемое отклонение от заданного передаточного числа 4%.
Делительные диаметры d:
шестерни d1 =z1mcosb = 50×1 cos 513° = 502 мм;
колеса d2 =2aw- d1 = 2×125 – 502 = 1998 мм.;
Диаметры окружностей вершин da и впадин df зубьев:
10 Размеры заготовок колес.
Чтобы получить при термической обработке принятые для расчета механические характеристики материала колес требуется чтобы размеры заготовок колес не превышали предельно допустимых значений: Dзаг Dпред; Сзаг Sзаг Sпред;
Значения Dзаг Sзаг Сзаг (мм) вычисляют по формулам:
для цилиндрической шестерни Dзаг=dа+6 мм = 522 + 6 = 582 мм 200 мм;
Для колеса с выточками принимают меньшее из значений Сзаг= 05b2 = 05×63= 315мм. 125 мм; и Sзаг=8m =8мм.
11 Силы в зацеплении
-окружная Ft=2T2d2 = 2×2029 01998 = 2031 Н;
-радиальная Fr=Fttgacosb = 2031×0364 cos 513° = 7423 Н.
(для стандартного угла a=20° tga=0364);
-осевая Fa = Fttgb = 2031×tg 513° = 1823 Н.
12 Проверка зубьев колес по напряжениям изгиба.
Расчетное напряжение изгиба в зубьях колеса:
sF2=KFaKFbKFvYbYF2FtE(b2m) [s]F2
Для колес с b>0° принимают для 9-ой степени точности KFa=1.
Степень точности передачи принимаем в зависимости от окружной скорости колеса (мс) степень точности 9-ая.
Коэффициент концентрации нагрузки KFb принимают для прирабатывающихся колес при постоянной нагрузке KFb=1.
Коэффициент динамической нагрузки принимают согласно окружной скорости КFv = 107. Коэффициент Yb вычисляют по формуле Yb=1—b°140 = 096. Коэффициент формы зуба YF2 = 36 YF1 = 365.
FtE = KFдFt — эквивалентная окружная сила. Коэффициент долговечности KFд = 1. Т.е. FtE= Ft = 2031 Н.
sF2=1×1×107×096×36×2031(0063×0001) = 1192 МПа 29407 МПа.
Расчетное напряжение в зубьях шестерни:
sF1=sF2YF1 YF2 [s]F1
sF1=1192×365 36 = 1209 29407 МПа.
13 Проверка зубьев колес по контактным напряжениям.
Расчетное контактное напряжение
где для косозубых колес КНa = 11; КН= 27×105; КНb = 1; KHv = 103.
Расчет цилиндрической зубчатой передачи (тихоходная ступень).
Т2 = 7811 Н×м — вращающий момент на колесе;
n2Т = 603 обмин — частота вращения колеса;
u = 4 — передаточное число;
В качестве материала для цилиндрического колеса применяем ст.40Х. Применяем т.о. шестерни – улучшение и закалка ТВЧ твердость сердцевины НВ 269 302 твердость поверхности НRC 45 50.
В качестве материала для шестерни используем ст.40Х. Применяем т.о. шестерни – улучшение и закалка ТВЧ твердость сердцевины НВ 269 302 твердость поверхности НRC 45 50.
допускаемые контактные напряжения: [s]H = 14 + 170 = 835 МПа
допускаемые напряжения на изгиб: [s]F = 370 МПа;
NHG – базовое число циклов нагружений.
Следовательно эквивалентный момент на колесе ТНЕ2 = Т2 = 7811 Н.
Принимаем стандартное значение межосевого расстояния равное значению межосевого расстояния быстроходной ступени aw=125 мм.
принимаем стандартное значение b2 = 63 мм.
Т.о. эквивалентный момент на колесе ТFE=Т2=19736.
Принимаем модуль равным m = 2мм.
zS=2×125×cos638° 2 = 124
b = arccos (124×2 2×125) = 725°.
z1 = 124(4+l) = 25 ³ z1min.
Число зубьев колеса: z2 = zS - z1 = 124 – 25 = 99.
Фактическое передаточное число uф= z2 z1 = 99 25 = 396.
Отклонение от заданного передаточного отношения не превышает допускаемых 4%.
шестерни d1 =z1mcosb = 25×2 cos 725° = 504 мм;
колеса d2 =2aw- d1 = 2×125 – 504 = 1996 мм.;
для цилиндрической шестерни Dзаг=dа+6 мм = 504 + 6 = 564 мм 200 мм;
Для колеса с выточками принимают меньшее из значений Сзаг= 05b2 = 05×63 = 315 мм. 125 мм; и Sзаг=8m = 16мм.
-окружная Ft=2T2d2 = 2×7811 01996 = 78267 Н;
-радиальная Fr=Fttgacosb = 78267×0364 cos 725° = 28719 Н.
-осевая Fa = Fttgb = 78267×tg725° = 9957 Н.
Коэффициент динамической нагрузки принимают согласно окружной скорости КFv = 101 Коэффициент Yb вычисляют по формуле Yb=1—b°140= =0948. Коэффициент формы зуба YF2 = 36 YF1 = 39.
FtE = KFдFt — эквивалентная окружная сила. Коэффициент долговечности KFд = 1. Т.е. FtE= Ft = 78267 Н.
sF2=1×1×101×0948×36×78267(0063×0002) = 2141 МПа 370 МПа.
sF1=2141×39 36 = 232 370 МПа.
где для косозубых колес КНa = 11; КН= 27×105; КНb = 1; KHv = 101.
Диаметры различных участков валов редуктора определяем следующим образом:
Диаметр d выходного конца:
d ³ (7 8) 3ТБ = (7 8) 3528 = 2626 30 мм.
Принимаем d = 26 мм.
Диаметр вала под подшипник dп ³ d + 2t ³ 304 мм
где высота буртика t = 22 мм;
Принимаем dп = 30 мм.
Диаметр dбп ³ dп + 3r ³ 425 мм.
где координата фаски подшипника r = 2 мм;
Принимаем dбп = 35 мм.
Диаметр dк: dк ³ (6 7) 3ТПр = (6 7) 32029 = 3525 4113 мм.
Принимаем dк = 35 мм.
Диаметр dбк: dбк ³ dк + 3f = 386 мм.
где размер фаски f = 12 мм;
Принимаем dбк = 38 мм.
Диаметр dбп: dбп ³ dп + 3r = 36 мм.
Диаметр вала под подшипник dп = dk – 3r = 275 мм
где координата фаски подшипника r = 25 мм;
d ³ (5 6) 3ТТ = (5 6) 37811 = 46 55 мм.
Принимаем d = 45 мм.
Диаметр вала под подшипник dп ³ d + 2t ³ 506 мм
где высота буртика t = 28 мм;
Принимаем dп = 50 мм.
Диаметр dбп ³ dп + 3r ³ 59 мм.
где координата фаски подшипника r = 3 мм;
Принимаем dбп = 60 мм.
Диаметр dк ³ dбп = 60 мм.
2 Конструктивные размеры зубчатых колес.
2.1 Быстроходная ступень
Цилиндрическая шестерня выполняется за одно целое с валом. Ее размеры: d1 = 502 мм; da1 = 522 мм; b1 = 67 мм.
Цилиндрическое зубчатое колесо кованое. Его размеры:
d2 = 1998 мм; da2 = 2018 мм; b2 = 63 мм.
Диаметр ступицы колеса: dст = 15*d + 10 мм = 15* 40 + 10мм = 70 мм.
Длина ступицы колеса: lст = (12 15)*d = (12 15)* 40 = 48 60 мм.
принимаем lст = 63 мм.
Толщина обода: d = (25 4)*m = (25 4)*1 мм = 25 4 мм.
Толщина диска: С = 03*b2 = 03*63 мм = 189 мм. Принимаем С = 18 мм.
Диаметр центровой окружности: Dотв = (Dо + dст) * 05
Do = da2 – [2d + 2(24m + 2m)] = 2018 – [2*4 + 2(24*1 + 2*1)] = 185 мм.
Dотв = (185 + 70) * 05 = 1275 мм.
Диаметр отверстий в колесе:
dотв » (Do - dст) = (185 - 70) = 2875 мм.
принимаем dотв = 30 мм.
2.2 Тихоходная ступень
Цилиндрическая шестерня выполняется за одно целое с валом. Ее размеры: d1 = 504 мм; da1 = 544 мм; b1 = 67 мм.
d2 = 1996 мм; da2 = 2036 мм; b2 = 63 мм.
Диаметр ступицы колеса: dст = 15*d + 10 мм = 15*64 + 10мм = 106 мм.
Длина ступицы колеса: lст = (12 15)*d = (12 15)*64 = 768 96 мм.
принимаем lст = 83 мм.
Толщина обода: d = (25 4)*m = (25 4)*2 мм = 5 8 мм.
Do = da2 – [2d + 2(24m + 2m)] = 2036 – [2*8 + 2(24*2 + 2*2)] = 170 мм.
Dотв = (170 + 106) * 05 = 138 мм.
dотв » (Do - dст) = (170 - 106) = 16 мм.
принимаем dотв = 16 мм.
Для передачи момента с вала электродвигателя на быстроходный вал редуктора используем упругую втулочно-пальцевую муфту.
1 Быстроходная ступень
По ГОСТ 21424-75 для посадочного диаметра d=26 мм применяем муфту со следующими параметрами:
Передаваемый вращающий момент не более T= 125 Н×м (в нашем случае 528 Н×м).
Угловая скорость не более 480 с-1. (в нашем случае 101 с-1)
Длины отверстий: lкон =26 мм.
Габаритные размеры: L =89 мм; D=120 мм; d0=28 мм.
Смещение осей валов не более: радиальное Dr=03; угловое Dg=1°30.
Зазор между полумуфтами С=3 5мм.
Остальные параметры муфты рассчитываются по следующим соотношениям: B»025D=30мм; b»05B=15мм; D0=D-(15 16)d0=78мм; dст=16d=40 мм.
Размеры втулок и пальцев:
диаметр пальца dп =14мм.
длина пальца lп=33мм.
резьба выходного конца пальца d0 М10.
количество пальцев z=6.
диаметр втулки упругой dв =27мм.
длина втулки упругой lв=28мм.
Пальцы муфты изготовленные из стали 45 рассчитываем на изгиб:
Упругие элементы муфты проверяют на смятие в предположении равномерного распределения нагрузки между пальцами:
Выбранная муфта подходит.
Консольная нагрузка от муфты: Fм50T1 125T1= 3633 9083 Н. Принимаем значение Fм=650 Н.
2 Тихоходная ступень
По ГОСТ 21424-75 для посадочного диаметра d=45 мм применяем муфту со следующими параметрами:
Передаваемый вращающий момент не более T= 810 Н×м (в нашем случае 7811 Н×м).
Угловая скорость не более 315 с-1. (в нашем случае 63 с-1)
Длины отверстий: lкон =56 мм.
Габаритные размеры: L =170 мм; D=190 мм; d0=36 мм.
Смещение осей валов не более: радиальное Dr=04; угловое Dg=1°.
Остальные параметры муфты рассчитываются по следующим соотношениям: B»025D=475мм; b»05B=2375мм; D0=D-(15 16)d0=136мм; dст=16d=80 мм.
диаметр пальца dп =18мм.
длина пальца lп=42мм.
резьба выходного конца пальца d0 М12.
количество пальцев z=8.
диаметр втулки упругой dв =35мм.
длина втулки упругой lв=36мм.
Консольная нагрузка от муфты: Fм200T2=5590 Н.
Шпонки призматические со скругленными торцами. Материал - сталь 45 термообработка – нормализация. Напряжения смятия и условия прочности:
Допускаемые напряжения смятия:
-при стальной ступице: [sсм] = 100 120 МПа.
-при чугунной ступице: [sсм] = 60 80 МПа.
Диаметр вала под полумуфту 26 мм.
Сечение шпонки bh = 87 мм.
Глубина паза t1 = 4 мм.
Длина шпонки l = 50 мм.
т.к. материал полумуфты – чугун.
Условие прочности выполняется.
2 Промежуточный вал.
Диаметр вала под цилиндрическое колесо 35 мм.
Сечение шпонки bh = 108 мм.
Глубина паза t1 = 5 мм.
Длина шпонки l = 56 мм.
т.к. материал цилиндрического колеса – сталь.
Диаметр вала под цилиндрическое колесо 60 мм.
Сечение шпонки bh = 1811 мм.
Глубина паза t1 = 7 мм.
Длина шпонки l = 76 мм.
Диаметр вала под полумуфту 45 мм.
Сечение шпонки bh = 149 мм.
Глубина паза t1 = 55 мм.
Условие прочности не выполняется. Ставим вторую шпонку из расчета симметричности распределения нагрузки имеем sсм= ×121=605МПа - нагрузка воспринимаемая одной шпонкой. Таким образом sсм»[sсм] т.е. условие выполняется.
Проверочный расчет подшипников.
Силы в зацеплении: Ft = 2031 Н Fr = 7423 Н. Fa= 1823 Н.
Консольная сила от муфты: Fм=650 Н.
Частота вращения вала n = 965 обмин.
Расстояния: lб = 120 мм lм = 60 мм
Приемлемая долговечность подшипников Lh = 20000 часов.
1.1 Определение опорных реакций.
В вертикальной плоскости:
SY =0 RDy – Fr +RBy = 0;
3 – 7423 + 4093 = 0.
В горизонтальной плоскости:
615–7423-60385+650=0.
1.2 Определение суммарных реакций опор.
1.3 Выбор типа подшипника
Тип подшипника выбираем в соответствии с установившейся практикой проектирования и эксплуатации машин.
Для быстроходного вала dп = 30 мм. принимаем наиболее дешевый шарикоподшипник радиальный однорядный № 206 легкой серии с параметрами: d = 30 мм D = 62 мм В = 16 мм r = 15 мм; грузоподъемность: Cr = 153 кН Cor = 102 кН .
1.4 Выбор коэффициентов
Первоначально задаемся коэффициентами:
Кк – коэффициент учитывающий вращение колец; при вращении внутреннего кольца Кк = 1.
Ks – коэффициент безопасности при кратковременной перегрузке Ks =12.
KT – температурный коэффициент KT =1.
1.5 Определение осевых составляющих реакций:
Отношение осевой нагрузки подшипника Ra=Fa к статической грузоподъемности: RaC0 = 182310200 = 0018. По табличным данным определяем e=02.
Отношение осевой нагрузки к радиальной:
Для опоры D: RaKкRD=1823(1×7717)= 024.
Т.к. RaKкRD > e X=056; Y=22.
Для опоры B: RaKкRB=1823(1×7295)= 025.
Т.к. RaKкRB > e X=056; Y= 22.
1.6 Определение эквивалентной нагрузки.
где R – радиальная нагрузка действующая на опору Н.
Fa – осевая нагрузка действующая на опору Н.
X – коэффициент радиальной нагрузки.
Y – коэффициент осевой нагрузки;
Для опоры D: RE = (1·056·7717+22·1823)·12·1= 1000 Н.
Для опоры B: RE = (1·056·7295+22·1823)·12·1= 9715 Н.
1.7 Расчетная долговечность в часах для более нагруженной опоры D.
Полученный вариант устраивает.
Силы в цилиндрическом зацеплении быстроходной ступени: Ft2 = 2031 Н Fr2 = 7423 Н. Fa2= 1823 Н.
Силы в цилиндрическом зацеплении тихоходной ступени: Ft1 = 78267 Н Fr1 = 28719 Н. Fa1= 9957 Н.
Частота вращения вала n = 24125 обмин.
Расстояния: l1 = 60 мм l2 = 150 мм l3 = 120мм.
2.1 Определение опорных реакций.
Вертикальная плоскость.
В вертикальной плоскости имеем
SY =0 RDy + Fr2 – Fr1 +RAy = 0;
486 + 7423 – 28719 +181 = 0.
Горизонтальная плоскость.
В горизонтальной плоскости имеем:
651 + 2031 – 78267 + 1306 = 0.
2.2 Определение суммарных реакций опор.
Дальнейший расчет для более нагруженной опоры D.
2.3 Выбор типа подшипника
Для быстроходного вала dп = 35 мм. принимаем конические однорядные роликоподшипники №7306 со следующими параметрами: d = 30 мм D = 72 мм Tma r1 = 08 мм; грузоподъемность: Cr = 400 кН Cor = 299 кН . Схема установки – «врастяжку». Фактор нагрузки: e=034.
2.4 Находим осевые составляющие реакций.
SA=083×e×RA=083×034×2232=63;
SD=083×e×RD=083×034×59909=16906;
Т.к. SA SD и Ra=1178 Н SD – SA = 16276 Н то
FaD = SD =16906; FaA = FaD-Ra = 5126;
При принимаем X=04; Y=178.
При принимаем X=1; Y=0.
2.5 Определяем эквивалентную нагрузку.
Опора A: RE = (1·04·2232+178·5126)·12·1= 1202 Н.
Опора D: RE = 59909·12·1= 7189 Н.
2.6 Расчетная долговечность в часах для более нагруженной опоры D.
Силы в цилиндрическом зацеплении тихоходной ступени: Ft2 = 78267 Н Fr2 = 28719 Н. Fa2=9957 Н.
Частота вращения вала n = 603 обмин.
Консольная сила от муфты: Fм= 5590 Н.
Расстояния: lц = 80 мм lб = 180 мм.
3.1 Определяем опорные реакции.
SY =0 RGy – Fr2 +REy = 0;
39 – 28719 + 1988 = 0.
-5590 + 119878 – 78267 + 14289 = 0.
3.2 Определяем суммарные реакции опор.
Как видно опора G является более нагруженной поэтому по ней ведем дальнейшие расчеты.
3.3 Выбор типа подшипника
Для опор промежуточного вала dп = 50 мм применяем компактные конические однорядные роликоподшипники легкой серии №7210 со следующими параметрами: d = 50 мм D = 90 мм Tma r1 = 08 мм; грузоподъемность: Cr = 529 кН Cor = 406 кН . Схема установки – «врастяжку». Фактор нагрузки: e=037.
1.5 Находим осевые составляющие реакций.
SE=083×e×RE=083×037×24482=7518;
SG=083×e×RG=083×037×120203=36914;
Т.к. SE SG и Ra=9957 Н > 0 Н то
FaE = SE =7518; FaG = Ra+SE = 17475;
1.6 Определяем эквивалентную нагрузку.
Опора E: RE = 24482·12·1= 29378 Н.
Опора G: RG = 120203·12·1= 144244 Н.
1.7 Расчетная долговечность в часах для более нагруженной опоры G.
Проверочный расчет валов на прочность.
Проверочный расчет проводится для проверки прочности в опасном сечении в зависимости от направления и величины действующих на него нагрузок. Напряжение изгиба изменяется по симметричному циклу а касательные напряжения кручения по пульсирующему.
1.1 Выбор материала вала
Для изготовления быстроходного вала выбрали материал сталь 40Х твердость не менее 200НВ; s-1 = 320 МПа и t-1 = 200МПа – пределы выносливости при симметричном цикле изгиба и кручения.
1.2 Строим расчетную схему вала.
Из предыдущих разделов имеем
Силы в зацеплении: Ft = 15124 Н Fr = 5555 Н. Fa= 2034 Н.
Консольная сила от муфты: Fм=500 Н.
Реакции: RDy = 4093 Н RBy =333 Н .
Расстояния: lб = 100 мм lм = 40 мм
1.3 Определим величину изгибающих моментов в характерных сечениях А B С D.
В горизонтальной плоскости.
В вертикальной плоскости.
справа: MСx = RBy·lб = 3291·50=165
1.4 Крутящий момент в сечениях вала.
Строим эпюру крутящих моментов.
1.5 Определение опасного сечения
Как видно из эпюр изгибающих моментов опасным сечением вала является сечение С. Определяем суммарный изгибающий момент в сечении С.
1.6 Осевой момент сопротивления сечения С.
1.7 Полярный момент сопротивления сечения С.
1.8 Амплитуда симметричного цикла по изгибу.
1.9 Амплитуда касательных напряжений:
1.10 Среднее напряжение цикла при изгибе
sm = 0 tm = ta = 088 Нмм2.
1.11 Принимаем коэффициенты
концентрации напряжений: Ks = 19; Kt = 16;
масштабных факторов: Еs = 085; Еt = 073;
коэффициенты учитывающие влияние среднего напряжения цикла на усталостную прочность: ys = 01 yt= 05.
1.12 Определяем коэффициенты запаса прочности вала в сечении С по напряжениям изгиба
1.13 Определяем коэффициенты запаса прочности вала в сечении С по напряжениям кручения
1.14 Расчетный коэффициент запаса прочности :
Сопротивление усталости обеспечивается.
2.1 Выбор материала вала
2.2 Строим расчетную схему вала.
Силы в цилиндрическом зацеплении быстроходной ступени: Ft2 = 15124 Н Fr2 = 5555 Н. Fa2 = 2034 Н.
Силы в цилиндрическом зацеплении тихоходной ступени: Ft1 = 45195 Н Fr1 = 1714 Н. Fa1= 1322 Н.
Реакции: RDy = 8035 Н RAy =355 Н .
Расстояния: l1 = 50 мм l2 = 70 мм l3 = 90мм
2.3 Определим величину изгибающих моментов в характерных сечениях А B С D.
MBx1 = RDy·(l1+l2) + Fа1·d1 – Fr1·l2 =
= 8035·120·10-3+·1322·573·10-3–1714·70·10-3= 143 Н·м;
MBx2 = RDy·(l1+l2) + Fа1·d1 – Fr1·l2 +Fа2·d2 =
=8035·120·10-3+·1322·573·10-3–1714·70·10-3+·2034·1735·10-3=32 Н·м;
2.4 Крутящий момент в сечениях вала.
2.5 Определение опасного сечения
2.6 Осевой момент сопротивления сечения С.
2.7 Полярный момент сопротивления сечения С.
2.8 Амплитуда симметричного цикла по изгибу.
2.9 Амплитуда касательных напряжений:
2.10 Среднее напряжение цикла при изгибе
sm = 0 tm = ta = 178 Нмм2.
2.11 Принимаем коэффициенты
масштабных факторов: Еs = 0785; Еt = 0685;
2.12 Определяем коэффициенты запаса прочности вала в сечении С по напряжениям изгиба
2.13 Определяем коэффициенты запаса прочности вала в сечении С по напряжениям кручения
2.14 Расчетный коэффициент запаса прочности :
3.1 Выбор материала вала
Для изготовления тихоходного вала выбрали материал сталь 40Х твердость не менее 200НВ; s-1 = 320 МПа и t-1 = 200МПа – пределы выносливости при симметричном цикле изгиба и кручения.
3.2 Строим расчетную схему вала.
Силы в цилиндрическом зацеплении: Ft2=45195 Н; Fr2=1714 Н; Fa2=1322 Н.
Консольная нагрузка от цепной передачи Fц=357876 Н. Проекции на оси соответственно: Fцy=Fцs Fц
Реакции: REy = 22644 Н RGy =2340 Н REx = 36372 Н RGx =2217 Н.
3.3 Определим величину изгибающих моментов в характерных сечениях E F G H.
MFx2 = Fцy·(lц+lб)–RGy·lб+Fa2·d2 =
= 178938·170·10-3 – 2340·90·10-3+1322··1667·10-3=2038 Н·м;
3.4 Крутящий момент в сечениях вала.
3.5 Определение опасного сечения
Как видно из эпюр изгибающих моментов опасным сечением вала является сечение F. Определяем суммарный изгибающий момент в сечении F.
3.6 Осевой момент сопротивления сечения F.
3.7 Полярный момент сопротивления сечения F.
3.8 Амплитуда симметричного цикла по изгибу.
3.9 Амплитуда касательных напряжений:
3.10 Среднее напряжение цикла при изгибе
sm = 0 tm = ta = 64 Нмм2.
3.11 Принимаем коэффициенты
масштабных факторов: Еs = 081; Еt = 07;
3.12 Определяем коэффициенты запаса прочности вала в сечении F по напряжениям изгиба
3.13 Определяем коэффициенты запаса прочности вала в сечении F по напряжениям кручения
3.14 Расчетный коэффициент запаса прочности :
Смазывания зубчатого зацепления и подшипников качения производится маслом заливаемым внутрь корпуса редуктора до уровня обеспечивающего погружение зубчатого колеса примерно на 10 мм. Объем масляной ванны определяется из расчета 025 дм3 на 1 кВт передаваемой мощности:
V = 025 · 4 = 1 дм3 = 1 л.
Устанавливаем вязкость масла. При контактных напряжениях sH = 693 МПа и скорости v = 25 мс рекомендуемая кинематическая вязкость масла должна быть примерно равна 50 · 10-6 м2с.
Выбираем масло индустриальное И – 50А с кинематической вязкостью (47 55) · 10-6 м2с по ГОСТ 20799-75.
Посадки зубчатого колеса и подшипников.
Посадки назначают в соответствии с ГОСТ 25347 – 82.
-посадка полумуфты на ведущий вал: ;
-посадка зубчатого колеса на вал: ;
-посадка звездочки цепной передачи на ведомый вал: ;
-посадка подшипников качения:
отклонение отверстия Н7;
- посадка распорных колец: .
- посадка шпоночных соединений: .
- посадка крышек подшипниковых узлов: .
Сборка редуктора осуществляется в следующей последовательности:
Установить корпус редуктора на стенд (посредством кран-балки или вручную).
Вручную установить в гнезда редуктора предварительно собранный быстроходный вал (т.е. на валу запрессованы подшипники).
Вручную установить в гнезда редуктора предварительно собранный промежуточный вал (т.е. на вал запрессованы подшипники посредством шпонки зафиксировано цилиндрическое колесо). На этом этапе предполагается организация конического зацепления.
Вручную установить в гнезда редуктора предварительно собранный тихоходный вал (т.е. на валу посредством шпонки зафиксировано зубчатое колесо одеты втулки и запрессованы подшипники). На этом этапе предполагается организация зубчатого зацепления.
Установить крышку редуктора с помощью кран-балки.
Разметить 2 отверстия под штифты (линейка штангенциркуль).
Просверлить 2 отверстия под штифты (электродрель).
Заштифтовать (молоток).
Закрепить смотровое окошко.
Установить две глухие крышки подшипников.
Установить две сквозные крышки подшипников в сборе (т.е. в крышки вмонтированы манжеты).
Установить шпонку под полумуфту (молоток).
Установить шпонку под звездочку (молоток).
Далее следует проверить вращение колеса от руки проконтролировать биение выходного вала. Также следует контролировать болтовые соединения в момент затяжки. Осуществить контроль герметичности.
Дунаев П.Ф. Леликов О.П. Детали машин. Курсовое проектирование: Учебное пособие для ВУЗов.– М.: Высшая школа 1984.
Куклин Н.Г. Куклина Г.С. Детали машин: Учебник для ВТУЗов – М.: Высшая школа 1999.
Устюгов И.И. Детали машин: Учебное пособие для учащихся ВТУЗов. – 2-е изд. перераб. и доп.– М.: Высшая школа 1981.
Чернавский С.А. Боков К.Н. Чернин И.М. и др. Курсовое проектирование деталей машин: Учебное пособие для учащихся машиностроительных специальностей.– 2-е изд. перераб. и доп.– М.: Машиностроение 1988.
Исходные данные для проектирования.2
Выбор электродвигателя.3
Кинематический расчет.5
Расчет цилиндрической зубчатой передачи (быстроходная ступень).6
Расчет цилиндрической зубчатой передачи (тихоходная ступень).12
Проверочный расчет подшипников.26
Проверочный расчет валов на прочность.36
Посадки зубчатого колеса и подшипников.49
_рама.dwg

Внутреннюю стенку необработанной части корпуса и крышки покрасить маслостойкой краской
а снаружи - серой нитроэмалью. 2. Перед окончательной сборкой стыки фланцев корпуса покрыть пастой "Герметик". 3. В редуктор залитбь 3 л. масла марки И-30А.
* Размер обеспечивает инструмент.
Данные для контроля зубчатого венца выбирают по ГОСТ 1643-81
Внутреннюю стенку необработанной части корпуса и крышек покрасить маслостойкой краской
а снаружи - серой нитроэмалью.
Перед окончательной сборкой стыки
фланцев корпуса покрыть пастой "Герметик
План размещения отверстий под фундаментные болты
Сварные швы по ГОСТ 5264-80.
Электроды типа Э42 ГОСТ 9467-80.
После сварки провести рихтовку и отжиг.
Обработку поверхностей платиков и
сверление отверстий производить после
Неуказанные предельные отклонения
Отклонение размеров диагонали между
осями двух любых отверстий группы Б и В
ДМ ПК 01.05.03.00.00.СБ
_корпус.dwg

Внутреннюю стенку необработанной части корпуса и крышки покрасить маслостойкой краской
а снаружи - серой нитроэмалью. 2. Перед окончательной сборкой стыки фланцев корпуса покрыть пастой "Герметик". 3. В редуктор залитбь 3 л. масла марки И-30А.
* Размер обеспечивает инструмент.
Данные для контроля зубчатого венца выбирают по ГОСТ 1643-81
Неуказанные предельные отклонения
размеров: отверстий- валов-
Перекос осей отверстий AB и CD до
ДМ.ПК.01.08.00.00.00.СБ
Перекос осей отверстий AB до
ДМ.ПК.01.05.00.00.00.СБ
пояснительная записка.doc
Тяговая сила цепи Ft = 600 даН = 6 кН.
Скорость движения грузовой цепи v = 085 мс.
Шаг грузовой цепи p = 125 мм.
Число зубьев звездочки z =7.
Тип редуктора – соосный вертикальный цилиндрический.
Передача привода – нет.
Выбор электродвигателя.
1.Требуемая мощность на выходе.
2 КПД всего привода.
где hмс = 098 – КПД соединительной муфты;
hз(бс) = 097 – КПД закрытой зубчатой передачи (быстроходной ступени);
hз(тс) = 097 – КПД закрытой зубчатой передачи (тихоходной ступени);
hпк = 099 – КПД учитывающий потери пары подшипников качения ;
3 Требуемая мощность электродвигателя.
4 Частота вращения приводного вала.
Здесь диаметр делительной окружности звездочки определяется следующим образом:
5 Подбор электродвигателя.
Следуя справочным данным выбираем электродвигатель 132S6 с синхронной частотой вращения nc = 1000 обмин. для которого номинальная мощность Рдв = 55 кВт (допускаем перегрузку в 55%) асинхронная частота вращения nдв = 965 обмин.
6 Передаточное число привода.
где частные передаточные отношения отдельных передач
uр – передаточное отношение редуктора.
nв – частота вращения выходного вала:
В итоге u=965582»16.
7 Разбивка передаточного числа редуктора по ступеням.
Для двухступенчатого соосного редуктора.
Передаточное число быстроходной ступени:
Передаточное число тихоходной ступени:
Кинематический расчет.
Быстроходный вал редуктора:
мощность P1=Pдв×hмс×hпк=5500×098×099=53361 Вт.
частота вращения n1= nдв=965 обмин.
угловая скорость w1=p×n130=p×96530=101 c-1.
крутящий момент T1=P1w1=53361101=528 Н×м.
Промежуточный вал редуктора:
мощность P2=P1×hб×hпк=53361×097×099=51243 Вт.
частота вращения n2= n1uб=9654=24125 обмин.
угловая скорость w2=p×n230=p×2412530=2525 c-1.
крутящий момент T2=P2w2=512432525=2029 Н×м.
Тихоходный вал редуктора:
мощность P3=P2×hт×hпк=51243×097×099=49209 Вт.
частота вращения n3= n2uт=241254=603 обмин.
угловая скорость w3=p×n330=p×60330=63 c-1.
крутящий момент T3=P3w3=4920963=7811 Н×м.
мощность P4=P3×hмс×hпк=49209×098×099=47743 Вт.
частота вращения n4= n3=603 обмин.
угловая скорость w4=w3=63 c-1.
крутящий момент T4=P4w4=4774363=7578 Н×м
Расчет цилиндрической зубчатой передачи (быстроходная ступень).
Т2 = 2029 Н×м — вращающий момент на колесе;
n2Т = 24125 обмин — частота вращения колеса;
u = 4— передаточное число;
1. Материалы колеса и шестерни.
В качестве материала для цилиндрического колеса применяем ст.40Х. Применяем т.о. колеса – улучшение твердость сердцевины НВ 269 302 твердость поверхности НВ 269 302.
Механические свойства: sT = 750 МПа.
В качестве материала для шестерни используем ст.40Х. Применяем т.о. шестерни – улучшение твердость сердцевины НВ 269 302 твердость поверхности НВ 269 302.
Механические свойства: sТ = 750 МПа.
2. Допускаемые напряжения.
Вычисляем допускаемые контактные напряжения.
допускаемые контактные напряжения:
[s]H = 18+67 = 18×2855+67=5809 МПа;
допускаемые напряжения на изгиб:
[s]F = 103 = 103×2855=29407 МПа;
предельные допускаемые напряжения:
3 Межосевое расстояние:
где Ka – коэффициент межосевого расстояния; Ка = 4300 – для косозубых колес;
ya – коэффициент ширины венца по межосевому расстоянию: т.к. колеса в зацеплении расположены несимметрично относительно опор то ya = 0315.
Коэффициент концентрации нагрузки для прирабатывающихся колес при постоянном режиме КHb = 1.
Эквивалентный момент на колесе ТНЕ2 = КНдТ2
где — коэффициент долговечности.
Здесь: КНЕ — коэффициент эквивалентности зависящий от режима нагружения (при постоянном режиме нагружения КНЕ=1);
NHG=()3=2327117638 — базовое число циклов нагружений.
В итоге коэффициент циклов .
Следовательно эквивалентный момент на колесе ТНЕ2 = Т2 = 2029 Н.
Межосевое расстояние в итоге:
Принимаем стандартное значение межосевого расстояния aw=125мм.
4 Предварительные основные размеры колеса.
- делительный диаметр:
где yа – коэффициент ширины колеса yа=0315.
принимаем стандартное значение b2 = 63м.
где коэффициент Km принимают для косозубых колес: Km =58.
ТFE=КFдТ2—эквивалентный момент на колесе
где — коэффициент долговечности. Здесь NFG=4×106— базовое число циклов. При N³108 принимаем KFд=10.
Т.о. эквивалентный момент на колесе ТFE=Т2=2029 Н.
Модуль принимает значение:
Принимаем модуль передачи равным m = 10 мм.
6 Суммарное число зубьев и угол наклона.
Минимальный угол наклона зубьев косозубых колес
Суммарное число зубьев
zS=2×125×cos 318° 1 = 249
Определяем действительное значение угла
b = arccos (zSm 2aw).
b = arccos (249×1 2×125) = 513°.
7 Число зубьев шестерни и колеса.
Число зубьев шестерни
Для косозубых колес z1m
z1 = 249(4+l) = 50 ³ z1min.
Число зубьев колеса: z2 = zS - z1 = 249 – 50 = 199.
8 Фактическое передаточное число
Фактическое передаточное число uф= z2 z1 = 199 50 = 398.
Допускаемое отклонение от заданного передаточного числа 4%.
Делительные диаметры d:
шестерни d1 =z1mcosb = 50×1 cos 513° = 502 мм;
колеса d2 =2aw- d1 = 2×125 – 502 = 1998 мм.;
Диаметры окружностей вершин da и впадин df зубьев:
10 Размеры заготовок колес.
Чтобы получить при термической обработке принятые для расчета механические характеристики материала колес требуется чтобы размеры заготовок колес не превышали предельно допустимых значений: Dзаг Dпред; Сзаг Sзаг Sпред;
Значения Dзаг Sзаг Сзаг (мм) вычисляют по формулам:
для цилиндрической шестерни Dзаг=dа+6 мм = 522 + 6 = 582 мм 200 мм;
Для колеса с выточками принимают меньшее из значений Сзаг= 05b2 = 05×63= 315мм. 125 мм; и Sзаг=8m =8мм.
11 Силы в зацеплении
-окружная Ft=2T2d2 = 2×2029 01998 = 2031 Н;
-радиальная Fr=Fttgacosb = 2031×0364 cos 513° = 7423 Н.
(для стандартного угла a=20° tga=0364);
-осевая Fa = Fttgb = 2031×tg 513° = 1823 Н.
12 Проверка зубьев колес по напряжениям изгиба.
Расчетное напряжение изгиба в зубьях колеса:
sF2=KFaKFbKFvYbYF2FtE(b2m) [s]F2
Для колес с b>0° принимают для 9-ой степени точности KFa=1.
Степень точности передачи принимаем в зависимости от окружной скорости колеса (мс) степень точности 9-ая.
Коэффициент концентрации нагрузки KFb принимают для прирабатывающихся колес при постоянной нагрузке KFb=1.
Коэффициент динамической нагрузки принимают согласно окружной скорости КFv = 107. Коэффициент Yb вычисляют по формуле Yb=1—b°140 = 096. Коэффициент формы зуба YF2 = 36 YF1 = 365.
FtE = KFдFt — эквивалентная окружная сила. Коэффициент долговечности KFд = 1. Т.е. FtE= Ft = 2031 Н.
sF2=1×1×107×096×36×2031(0063×0001) = 1192 МПа 29407 МПа.
Расчетное напряжение в зубьях шестерни:
sF1=sF2YF1 YF2 [s]F1
sF1=1192×365 36 = 1209 29407 МПа.
13 Проверка зубьев колес по контактным напряжениям.
Расчетное контактное напряжение
где для косозубых колес КНa = 11; КН= 27×105; КНb = 1; KHv = 103.
Расчет цилиндрической зубчатой передачи (тихоходная ступень).
Т2 = 7811 Н×м — вращающий момент на колесе;
n2Т = 603 обмин — частота вращения колеса;
u = 4 — передаточное число;
В качестве материала для цилиндрического колеса применяем ст.40Х. Применяем т.о. шестерни – улучшение и закалка ТВЧ твердость сердцевины НВ 269 302 твердость поверхности НRC 45 50.
В качестве материала для шестерни используем ст.40Х. Применяем т.о. шестерни – улучшение и закалка ТВЧ твердость сердцевины НВ 269 302 твердость поверхности НRC 45 50.
допускаемые контактные напряжения: [s]H = 14 + 170 = 835 МПа
допускаемые напряжения на изгиб: [s]F = 370 МПа;
NHG – базовое число циклов нагружений.
Следовательно эквивалентный момент на колесе ТНЕ2 = Т2 = 7811 Н.
Принимаем стандартное значение межосевого расстояния равное значению межосевого расстояния быстроходной ступени aw=125 мм.
принимаем стандартное значение b2 = 63 мм.
Т.о. эквивалентный момент на колесе ТFE=Т2=19736.
Принимаем модуль равным m = 2мм.
zS=2×125×cos638° 2 = 124
b = arccos (124×2 2×125) = 725°.
z1 = 124(4+l) = 25 ³ z1min.
Число зубьев колеса: z2 = zS - z1 = 124 – 25 = 99.
Фактическое передаточное число uф= z2 z1 = 99 25 = 396.
Отклонение от заданного передаточного отношения не превышает допускаемых 4%.
шестерни d1 =z1mcosb = 25×2 cos 725° = 504 мм;
колеса d2 =2aw- d1 = 2×125 – 504 = 1996 мм.;
для цилиндрической шестерни Dзаг=dа+6 мм = 504 + 6 = 564 мм 200 мм;
Для колеса с выточками принимают меньшее из значений Сзаг= 05b2 = 05×63 = 315 мм. 125 мм; и Sзаг=8m = 16мм.
-окружная Ft=2T2d2 = 2×7811 01996 = 78267 Н;
-радиальная Fr=Fttgacosb = 78267×0364 cos 725° = 28719 Н.
-осевая Fa = Fttgb = 78267×tg725° = 9957 Н.
Коэффициент динамической нагрузки принимают согласно окружной скорости КFv = 101 Коэффициент Yb вычисляют по формуле Yb=1—b°140= =0948. Коэффициент формы зуба YF2 = 36 YF1 = 39.
FtE = KFдFt — эквивалентная окружная сила. Коэффициент долговечности KFд = 1. Т.е. FtE= Ft = 78267 Н.
sF2=1×1×101×0948×36×78267(0063×0002) = 2141 МПа 370 МПа.
sF1=2141×39 36 = 232 370 МПа.
где для косозубых колес КНa = 11; КН= 27×105; КНb = 1; KHv = 101.
Диаметры различных участков валов редуктора определяем следующим образом:
Диаметр d выходного конца:
d ³ (7 8) 3ТБ = (7 8) 3528 = 2626 30 мм.
Согласуя диаметр выходного конца быстроходного вала редуктора с диаметром выходного конца вала электродвигателя принимаем d = 30 мм.
Диаметр вала под подшипник dп ³ d + 2t ³ 344 мм
где высота буртика t = 22 мм;
Принимаем dп = 35 мм.
Диаметр dбп ³ dп + 3r ³ 425 мм.
где координата фаски подшипника r = 25 мм;
Принимаем dбп = 42 мм.
Диаметр dк: dк ³ (6 7) 3ТПр = (6 7) 32029 = 3525 4113 мм.
Принимаем dк = 40 мм.
Диаметр dбк: dбк ³ dк + 3f = 436 мм.
где размер фаски f = 12 мм;
Принимаем dбк = 45 мм.
Диаметр dбп: dбп ³ dп + 3r = 425 мм.
Принимаем dбп = 45 мм.
Диаметр вала под подшипник dп = dk – 3r = 325 мм
d ³ (5 6) 3ТТ = (5 6) 37811 = 46 55 мм.
Принимаем d = 50 мм.
Диаметр вала под подшипник dп ³ d + 2t ³ 556 мм
где высота буртика t = 28 мм;
Принимаем dп = 55 мм.
Диаметр dбп ³ dп + 3r ³ 64 мм.
где координата фаски подшипника r = 3 мм;
Принимаем dбп = 64 мм.
Диаметр dк ³ dбп = 64 мм.
2 Конструктивные размеры зубчатых колес.
2.1 Быстроходная ступень
Цилиндрическая шестерня выполняется за одно целое с валом. Ее размеры: d1 = 502 мм; da1 = 522 мм; b1 = 67 мм.
Цилиндрическое зубчатое колесо кованое. Его размеры:
d2 = 1998 мм; da2 = 2018 мм; b2 = 63 мм.
Диаметр ступицы колеса: dст = 15*d + 10 мм = 15* 40 + 10мм = 70 мм.
Длина ступицы колеса: lст = (12 15)*d = (12 15)* 40 = 48 60 мм.
принимаем lст = 63 мм.
Толщина обода: d = (25 4)*m = (25 4)*1 мм = 25 4 мм.
Толщина диска: С = 03*b2 = 03*63 мм = 189 мм. Принимаем С = 18 мм.
Диаметр центровой окружности: Dотв = (Dо + dст) * 05
Do = da2 – [2d + 2(24m + 2m)] = 2018 – [2*4 + 2(24*1 + 2*1)] = 185 мм.
Dотв = (185 + 70) * 05 = 1275 мм.
Диаметр отверстий в колесе:
dотв » (Do - dст) = (185 - 70) = 2875 мм.
принимаем dотв = 30 мм.
2.2 Тихоходная ступень
Цилиндрическая шестерня выполняется за одно целое с валом. Ее размеры: d1 = 504 мм; da1 = 544 мм; b1 = 67 мм.
d2 = 1996 мм; da2 = 2036 мм; b2 = 63 мм.
Диаметр ступицы колеса: dст = 15*d + 10 мм = 15*64 + 10мм = 106 мм.
Длина ступицы колеса: lст = (12 15)*d = (12 15)*64 = 768 96 мм.
принимаем lст = 83 мм.
Толщина обода: d = (25 4)*m = (25 4)*2 мм = 5 8 мм.
Do = da2 – [2d + 2(24m + 2m)] = 2036 – [2*8 + 2(24*2 + 2*2)] = 170 мм.
Dотв = (170 + 106) * 05 = 138 мм.
dотв » (Do - dст) = (170 - 106) = 16 мм.
принимаем dотв = 16 мм.
Для передачи момента с вала электродвигателя на быстроходный вал редуктора используем упругую втулочно-пальцевую муфту.
1 Быстроходная ступень
По ГОСТ 21424-75 для посадочного диаметра d=30 мм применяем муфту со следующими параметрами:
Передаваемый вращающий момент не более T= 125 Н×м (в нашем случае 528 Н×м).
Угловая скорость не более 480 с-1. (в нашем случае 101 с-1)
Длины отверстий: lкон =38 мм.
Габаритные размеры: L =121 мм; D=120 мм; d0=28 мм.
Смещение осей валов не более: радиальное Dr=03; угловое Dg=1°30.
Зазор между полумуфтами С=3 5мм.
Остальные параметры муфты рассчитываются по следующим соотношениям: B»025D=30мм; b»05B=15мм; D0=D-(15 16)d0=78мм; dст=16d=48 мм.
Размеры втулок и пальцев:
диаметр пальца dп =14мм.
длина пальца lп=33мм.
резьба выходного конца пальца d0 М10.
количество пальцев z=6.
диаметр втулки упругой dв =27мм.
длина втулки упругой lв=28мм.
Пальцы муфты изготовленные из стали 45 рассчитываем на изгиб:
Упругие элементы муфты проверяют на смятие в предположении равномерного распределения нагрузки между пальцами:
Выбранная муфта подходит.
Консольная нагрузка от муфты: Fм50T1 125T1= 3633 9083 Н. Принимаем значение Fм=650 Н.
2 Тихоходная ступень
По ГОСТ 21424-75 для посадочного диаметра d=50 мм применяем муфту со следующими параметрами:
Передаваемый вращающий момент не более T= 810 Н×м (в нашем случае 7811 Н×м).
Угловая скорость не более 315 с-1. (в нашем случае 63 с-1)
Длины отверстий: lкон =56 мм.
Габаритные размеры: L =170 мм; D=190 мм; d0=36 мм.
Смещение осей валов не более: радиальное Dr=04; угловое Dg=1°.
Остальные параметры муфты рассчитываются по следующим соотношениям: B»025D=475мм; b»05B=2375мм; D0=D-(15 16)d0=136мм; dст=16d=80 мм.
диаметр пальца dп =18мм.
длина пальца lп=42мм.
резьба выходного конца пальца d0 М12.
количество пальцев z=8.
диаметр втулки упругой dв =35мм.
длина втулки упругой lв=36мм.
Консольная нагрузка от муфты: Fм200T2=5590 Н.
Шпонки призматические со скругленными торцами. Материал - сталь 45 термообработка – нормализация. Напряжения смятия и условия прочности:
Допускаемые напряжения смятия:
-при стальной ступице: [sсм] = 100 120 МПа.
-при чугунной ступице: [sсм] = 60 80 МПа.
Диаметр вала под полумуфту 30 мм.
Сечение шпонки bh = 87 мм.
Глубина паза t1 = 4 мм.
Длина шпонки l = 50 мм.
т.к. материал полумуфты – чугун.
Условие прочности выполняется.
2 Промежуточный вал.
Диаметр вала под цилиндрическое колесо 40 мм.
Сечение шпонки bh = 128 мм.
Глубина паза t1 = 5 мм.
Длина шпонки l = 56 мм.
т.к. материал цилиндрического колеса – сталь.
Диаметр вала под цилиндрическое колесо 64 мм.
Сечение шпонки bh = 1811 мм.
Глубина паза t1 = 7 мм.
Длина шпонки l = 76 мм.
Диаметр вала под звездочку 50 мм.
Сечение шпонки bh = 149 мм.
Глубина паза t1 = 55 мм.
Условие прочности не выполняется. Ставим вторую шпонку из расчета симметричности распределения нагрузки имеем sсм= ×165=72МПа - нагрузка воспринимаемая одной шпонкой. Таким образом sсм»[sсм] т.е. условие выполняется.
Проверочный расчет подшипников.
Силы в зацеплении: Ft = 2031 Н Fr = 7423 Н. Fa= 1823 Н.
Консольная сила от муфты: Fм=650 Н.
Частота вращения вала n = 965 обмин.
Расстояния: lб = 120 мм lм = 60 мм
Приемлемая долговечность подшипников Lh = 20000 часов.
1.1 Определение опорных реакций.
В вертикальной плоскости:
SY =0 RDy – Fr +RBy = 0;
3 – 7423 + 4093 = 0.
В горизонтальной плоскости:
615–7423-60385+650=0.
1.2 Определение суммарных реакций опор.
1.3 Выбор типа подшипника
Тип подшипника выбираем в соответствии с установившейся практикой проектирования и эксплуатации машин.
Для быстроходного вала dп = 35 мм. принимаем наиболее дешевый шарикоподшипник радиальный однорядный № 207 легкой серии с параметрами: d = 35 мм D = 72 мм В = 17 мм r = 2 мм; грузоподъемность: Cr = 201 кН Cor = 139 кН .
1.4 Выбор коэффициентов
Первоначально задаемся коэффициентами:
Кк – коэффициент учитывающий вращение колец; при вращении внутреннего кольца Кк = 1.
Ks – коэффициент безопасности при кратковременной перегрузке Ks =12.
KT – температурный коэффициент KT =1.
1.5 Определение осевых составляющих реакций:
Отношение осевой нагрузки подшипника Ra=Fa к статической грузоподъемности: RaC0 = 182313900 = 0013. По табличным данным определяем e=019.
Отношение осевой нагрузки к радиальной:
Для опоры D: RaKкRD=1823(1×7717)= 024.
Т.к. RaKкRD > e X=056; Y=23.
Для опоры B: RaKкRB=1823(1×7295)= 025.
Т.к. RaKкRB > e X=056; Y= 23.
1.6 Определение эквивалентной нагрузки.
где R – радиальная нагрузка действующая на опору Н.
Fa – осевая нагрузка действующая на опору Н.
X – коэффициент радиальной нагрузки.
Y – коэффициент осевой нагрузки;
Для опоры D: RE = (1·056·7717+23·1823)·12·1= 10217 Н.
Для опоры B: RE = (1·056·7295+23·1823)·12·1= 9934 Н.
1.7 Расчетная долговечность в часах для более нагруженной опоры D.
Полученный вариант устраивает.
Силы в цилиндрическом зацеплении быстроходной ступени: Ft2 = 2031 Н Fr2 = 7423 Н. Fa2= 1823 Н.
Силы в цилиндрическом зацеплении тихоходной ступени: Ft1 = 78267 Н Fr1 = 28719 Н. Fa1= 9957 Н.
Частота вращения вала n = 24125 обмин.
Расстояния: l1 = 60 мм l2 = 150 мм l3 = 120мм.
2.1 Определение опорных реакций.
Вертикальная плоскость.
В вертикальной плоскости имеем
SY =0 RDy + Fr2 – Fr1 +RAy = 0;
486 + 7423 – 28719 +181 = 0.
Горизонтальная плоскость.
В горизонтальной плоскости имеем:
651 + 2031 – 78267 + 1306 = 0.
2.2 Определение суммарных реакций опор.
Дальнейший расчет для более нагруженной опоры D.
2.3 Выбор типа подшипника
2.4 Выбор коэффициентов
2.5 Определение осевых составляющих реакций:
Отношение осевой нагрузки подшипника Ra=Fa1+Fa2 к статической грузоподъемности: RaC0=117813900=0085. По табличным данным определяем e=028.
RaKкRD=1178(1×59909)= 02.
Т.к. RaKкRD e X=1; Y=0.
2.6 Определяем эквивалентную нагрузку.
RE = 1·1·59909·12·1= 7189 Н.
2.7 Расчетная долговечность в часах.
Полученный вариант недостаточен используем конические однорядные роликоподшипники №7307 со следующими параметрами: d = 35 мм D = 80 мм Tma r1 = 08 мм; грузоподъемность: Cr = 481 кН Cor = 353 кН . Схема установки – «врастяжку». Фактор нагрузки: e=032.
1.5 Находим осевые составляющие реакций.
SA=083×e×RA=083×032×2232=593;
SD=083×e×RD=083×032×59909=15912;
Т.к. SA SD и Ra=1178 Н SD – SA = 15319 Н то
FaD = SD =15912; FaA = FaD-Ra = 4132;
При принимаем X=04; Y=188.
При принимаем X=1; Y=0.
1.6 Определяем эквивалентную нагрузку.
Опора A: RE = (1·04·2232+188·4132)·12·1= 10393 Н.
Опора D: RE = 59909·12·1= 7189 Н.
Силы в цилиндрическом зацеплении тихоходной ступени: Ft2 = 78267 Н Fr2 = 28719 Н. Fa2=9957 Н.
Частота вращения вала n = 603 обмин.
Консольная сила от муфты: Fм= 5590 Н.
Расстояния: lц = 80 мм lб = 180 мм.
3.1 Определяем опорные реакции.
SY =0 RGy – Fr2 +REy = 0;
39 – 28719 + 1988 = 0.
-5590 + 119878 – 78267 + 14289 = 0.
3.2 Определяем суммарные реакции опор.
Как видно опора G является более нагруженной поэтому по ней ведем дальнейшие расчеты.
3.3 Выбор типа подшипника
Для опор промежуточного вала dп = 55 мм применяем компактные конические однорядные роликоподшипники легкой серии №7211 со следующими параметрами: d = 55 мм D = 100 мм Tma r1 = 08 мм; грузоподъемность: Cr = 579 кН Cor = 461 кН . Схема установки – «врастяжку». Фактор нагрузки: e=041.
SE=083×e×RE=083×041×24482=8331;
SG=083×e×RG=083×041×120203=40905;
Т.к. SE SG и Ra=9957 Н > 0 Н то
FaE = SE =8331; FaG = Ra+SE = 18288;
Опора E: RE = 24482·12·1= 29378 Н.
Опора G: RG = 120203·12·1= 144244 Н.
1.7 Расчетная долговечность в часах для более нагруженной опоры G.
Проверочный расчет валов на прочность.
Проверочный расчет проводится для проверки прочности в опасном сечении в зависимости от направления и величины действующих на него нагрузок. Напряжение изгиба изменяется по симметричному циклу а касательные напряжения кручения по пульсирующему.
1.1 Выбор материала вала
Для изготовления быстроходного вала выбрали материал сталь 40Х твердость не менее 200НВ; s-1 = 320 МПа и t-1 = 200МПа – пределы выносливости при симметричном цикле изгиба и кручения.
1.2 Строим расчетную схему вала.
Из предыдущих разделов имеем
Силы в зацеплении: Ft = 15124 Н Fr = 5555 Н. Fa= 2034 Н.
Консольная сила от муфты: Fм=500 Н.
Реакции: RDy = 2264 Н RBy =3291 Н .
Расстояния: lб = 100 мм lм = 40 мм
1.3 Определим величину изгибающих моментов в характерных сечениях А B С D.
В горизонтальной плоскости.
В вертикальной плоскости.
справа: MСx = RBy·lб = 3291·50=165
1.4 Крутящий момент в сечениях вала.
Строим эпюру крутящих моментов.
1.5 Определение опасного сечения
Как видно из эпюр изгибающих моментов опасным сечением вала является сечение С. Определяем суммарный изгибающий момент в сечении С.
1.6 Осевой момент сопротивления сечения С.
1.7 Полярный момент сопротивления сечения С.
1.8 Амплитуда симметричного цикла по изгибу.
1.9 Амплитуда касательных напряжений:
1.10 Среднее напряжение цикла при изгибе
sm = 0 tm = ta = 088 Нмм2.
1.11 Принимаем коэффициенты
концентрации напряжений: Ks = 19; Kt = 16;
масштабных факторов: Еs = 085; Еt = 073;
коэффициенты учитывающие влияние среднего напряжения цикла на усталостную прочность: ys = 01 yt= 05.
1.12 Определяем коэффициенты запаса прочности вала в сечении С по напряжениям изгиба
1.13 Определяем коэффициенты запаса прочности вала в сечении С по напряжениям кручения
1.14 Расчетный коэффициент запаса прочности :
Сопротивление усталости обеспечивается.
2.1 Выбор материала вала
2.2 Строим расчетную схему вала.
Силы в цилиндрическом зацеплении быстроходной ступени: Ft2 = 15124 Н Fr2 = 5555 Н. Fa2 = 2034 Н.
Силы в цилиндрическом зацеплении тихоходной ступени: Ft1 = 45195 Н Fr1 = 1714 Н. Fa1= 1322 Н.
Реакции: RDy = 8035 Н RAy =355 Н .
Расстояния: l1 = 50 мм l2 = 70 мм l3 = 90мм
2.3 Определим величину изгибающих моментов в характерных сечениях А B С D.
MBx1 = RDy·(l1+l2) + Fа1·d1 – Fr1·l2 =
= 8035·120·10-3+·1322·573·10-3–1714·70·10-3= 143 Н·м;
MBx2 = RDy·(l1+l2) + Fа1·d1 – Fr1·l2 +Fа2·d2 =
=8035·120·10-3+·1322·573·10-3–1714·70·10-3+·2034·1735·10-3=32 Н·м;
2.4 Крутящий момент в сечениях вала.
2.5 Определение опасного сечения
2.6 Осевой момент сопротивления сечения С.
2.7 Полярный момент сопротивления сечения С.
2.8 Амплитуда симметричного цикла по изгибу.
2.9 Амплитуда касательных напряжений:
2.10 Среднее напряжение цикла при изгибе
sm = 0 tm = ta = 178 Нмм2.
2.11 Принимаем коэффициенты
масштабных факторов: Еs = 0785; Еt = 0685;
2.12 Определяем коэффициенты запаса прочности вала в сечении С по напряжениям изгиба
2.13 Определяем коэффициенты запаса прочности вала в сечении С по напряжениям кручения
2.14 Расчетный коэффициент запаса прочности :
3.1 Выбор материала вала
Для изготовления тихоходного вала выбрали материал сталь 40Х твердость не менее 200НВ; s-1 = 320 МПа и t-1 = 200МПа – пределы выносливости при симметричном цикле изгиба и кручения.
3.2 Строим расчетную схему вала.
Силы в цилиндрическом зацеплении: Ft2=45195 Н; Fr2=1714 Н; Fa2=1322 Н.
Консольная нагрузка от цепной передачи Fц=357876 Н. Проекции на оси соответственно: Fцy=Fцs Fц
Реакции: REy = 22644 Н RGy =2340 Н REx = 36372 Н RGx =2217 Н.
3.3 Определим величину изгибающих моментов в характерных сечениях E F G H.
MFx2 = Fцy·(lц+lб)–RGy·lб+Fa2·d2 =
= 178938·170·10-3 – 2340·90·10-3+1322··1667·10-3=2038 Н·м;
3.4 Крутящий момент в сечениях вала.
3.5 Определение опасного сечения
Как видно из эпюр изгибающих моментов опасным сечением вала является сечение F. Определяем суммарный изгибающий момент в сечении F.
3.6 Осевой момент сопротивления сечения F.
3.7 Полярный момент сопротивления сечения F.
3.8 Амплитуда симметричного цикла по изгибу.
3.9 Амплитуда касательных напряжений:
3.10 Среднее напряжение цикла при изгибе
sm = 0 tm = ta = 64 Нмм2.
3.11 Принимаем коэффициенты
масштабных факторов: Еs = 081; Еt = 07;
3.12 Определяем коэффициенты запаса прочности вала в сечении F по напряжениям изгиба
3.13 Определяем коэффициенты запаса прочности вала в сечении F по напряжениям кручения
3.14 Расчетный коэффициент запаса прочности :
Смазывания зубчатого зацепления и подшипников качения производится маслом заливаемым внутрь корпуса редуктора до уровня обеспечивающего погружение зубчатого колеса примерно на 10 мм. Объем масляной ванны определяется из расчета 025 дм3 на 1 кВт передаваемой мощности:
V = 025 · 4 = 1 дм3 = 1 л.
Устанавливаем вязкость масла. При контактных напряжениях sH = 693 МПа и скорости v = 25 мс рекомендуемая кинематическая вязкость масла должна быть примерно равна 50 · 10-6 м2с.
Выбираем масло индустриальное И – 50А с кинематической вязкостью (47 55) · 10-6 м2с по ГОСТ 20799-75.
Посадки зубчатого колеса и подшипников.
Посадки назначают в соответствии с ГОСТ 25347 – 82.
-посадка полумуфты на ведущий вал: ;
-посадка зубчатого колеса на вал: ;
-посадка звездочки цепной передачи на ведомый вал: ;
-посадка подшипников качения:
отклонение отверстия Н7;
- посадка распорных колец: .
- посадка шпоночных соединений: .
- посадка крышек подшипниковых узлов: .
Сборка редуктора осуществляется в следующей последовательности:
Установить корпус редуктора на стенд (посредством кран-балки или вручную).
Вручную установить в гнезда редуктора предварительно собранный быстроходный вал (т.е. на валу запрессованы подшипники).
Вручную установить в гнезда редуктора предварительно собранный промежуточный вал (т.е. на вал запрессованы подшипники посредством шпонки зафиксировано цилиндрическое колесо). На этом этапе предполагается организация конического зацепления.
Вручную установить в гнезда редуктора предварительно собранный тихоходный вал (т.е. на валу посредством шпонки зафиксировано зубчатое колесо одеты втулки и запрессованы подшипники). На этом этапе предполагается организация зубчатого зацепления.
Установить крышку редуктора с помощью кран-балки.
Разметить 2 отверстия под штифты (линейка штангенциркуль).
Просверлить 2 отверстия под штифты (электродрель).
Заштифтовать (молоток).
Закрепить смотровое окошко.
Установить две глухие крышки подшипников.
Установить две сквозные крышки подшипников в сборе (т.е. в крышки вмонтированы манжеты).
Установить шпонку под полумуфту (молоток).
Установить шпонку под звездочку (молоток).
Далее следует проверить вращение колеса от руки проконтролировать биение выходного вала. Также следует контролировать болтовые соединения в момент затяжки. Осуществить контроль герметичности.
Дунаев П.Ф. Леликов О.П. Детали машин. Курсовое проектирование: Учебное пособие для ВУЗов.– М.: Высшая школа 1984.
Куклин Н.Г. Куклина Г.С. Детали машин: Учебник для ВТУЗов – М.: Высшая школа 1999.
Устюгов И.И. Детали машин: Учебное пособие для учащихся ВТУЗов. – 2-е изд. перераб. и доп.– М.: Высшая школа 1981.
Чернавский С.А. Боков К.Н. Чернин И.М. и др. Курсовое проектирование деталей машин: Учебное пособие для учащихся машиностроительных специальностей.– 2-е изд. перераб. и доп.– М.: Машиностроение 1988.
Исходные данные для проектирования.2
Выбор электродвигателя.3
Кинематический расчет.5
Расчет цилиндрической зубчатой передачи (быстроходная ступень).6
Расчет цилиндрической зубчатой передачи (тихоходная ступень).12
Проверочный расчет подшипников.26
Проверочный расчет валов на прочность.36
Посадки зубчатого колеса и подшипников.49
_редуктор.dwg

Внутреннюю стенку необработанной части корпуса и крышки покрасить маслостойкой краской
а снаружи - серой нитроэмалью. 2. Перед окончательной сборкой стыки фланцев корпуса покрыть пастой "Герметик". 3. В редуктор залитбь 3 л. масла марки И-30А.
* Размер обеспечивает инструмент.
Данные для контроля зубчатого венца выбирают по ГОСТ 1643-81
Техническая характеристика.
Вращающий момент на тихоходном валу
Коэффициент полезного действия
Частота вращения тихоходного вала
Общее передаточное число
Степень точности изготовления передач
ДМ ПК 01.08.00.00.00.СБ
ДМ.ПК.01.08.00.00.00.СБ
Внутреннюю стенку необработанной части корпуса и крышек покрасить маслостойкой краской
а снаружи - серой нитроэмалью.
Перед окончательной сборкой стыки
фланцев корпуса покрыть пастой "Герметик
В редуктор залить 1л. масла марки И-50А
ДМ.ПК.01.05.00.00.00.СБ
Рекомендуемые чертежи
- 30.04.2023
- 04.06.2015
- 04.11.2015
Свободное скачивание на сегодня
- 24.01.2023