Проектирование редуктора




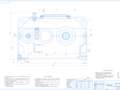

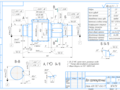
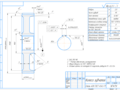
- Добавлен: 04.11.2022
- Размер: 1 MB
- Закачек: 0
Описание
Курсовой проект - Проектирование редуктора
Состав проекта
![]() |
![]() |
![]() ![]() ![]() ![]() |
![]() |
![]() ![]() ![]() ![]() |
![]() |
![]() |
![]() ![]() ![]() ![]() |
![]() ![]() ![]() ![]() |
![]() |
![]() ![]() ![]() |
![]() |
Дополнительная информация
Колесо зубчатое.cdw

Нормальный исходный контур
Коэффициент смещения
Сталь 40Х ГОСТ 4543-71
* Размер обеспечить инструментом.
Общие допуски по ГОСТ 30893.2-mK.
Острые кромки по контурам Б скруглить радиусом R = 0
Вал.cdw

Нормальный исходный контур
Коэффициент смещения
Сталь 40Х ГОСТ 4543-71
* Размер обеспечивается инструментом.
Общие допуски по ГОСТ 30893.1-mK.
Спецификация_Редуктор.spw

Кольцо маслозащитное
Втулка дистанционная
Кольцо маслоотражательное
Кольцо дистанционное
Редуктор_СБ.cdw

Техническая характеристика
Вращающий момент на тихоходном валу
Частота вращения тихоходного вала
Общее передаточное число 18
Степень точности изготовления зубчатых передач 8-А
Коэффициент полезного действия редуктора 0
Параметры зацепления
Технические требования
Необработанные поверхности литых деталей
красить маслостойкой красной эмалью НЦ-5123
Наружные поверхности корпуса красить серой эмалью
Плоскость разъема покрыть тонким слоем герметика УТ-34ГОСТ
285-80 при окончательной сборке.
Валы должны проворачиваться от руки плавно
Залить в редуктор масло И-Г-А-32 ГОСТ 20799-88 в количестве
Редуктор обкатать при частоте вращения входного вала 1455
обмин в течении трех часов. После обкатки масло слить.
Контроливать наличие стружки.
Сборку соединений с натягом выполнять с нагревом
охватывающей детали.
Полости К и Л заполнить смазкой ЦИАНТИМ-201 ГОСТ 6267-74
* Размер для справок
ПЗ по ДМиОКмояверсия.doc
Выбор оптимального варианта компоновки
Геометрический расчет передач редуктора 9
Кинематический расчет редуктора 11
Статическое исследование редуктора 11
Конструирование валов редуктора 14
Предварительный подбор подшипников 16
Проверка зубьев на прочность 17
Проверочный расчет промежуточного вала 26
Проверочный расчет подшипников промежуточного вала 30
Расчет на усталостную прочность 31
Конструирование элементов редуктора .. 35
Манжетные уплотнения 39
Выбор смазочного материала 39
Список использованной литературы 40
Привод грузоподъемной машины состоит из электродвигателя муфты редуктора и лебедки.
При помощи муфты передается вращающий момент от электродвигателя на быстроходную ступень редуктора. В данном варианте редуктор двухступенчатый развернутой схемы. Редуктор повышает вращающий момент который мы получаем на выходе при этом приводится в движение лебедка. Выходной конец вала соединен с лебедкой при помощи муфты. Лебедка состоит из каната навиваемого на барабан. С помощью нее мы можем поднимать и перемещать различные грузы.
ПРОЕКТИРОВАНИЕ ПРИВОДА ЛЕБЕДКИ
1. Диаметр грузового каната
Диаметр каната определяется исходя из условия прочности с учетом коэффициента безопасности устанавливаемого для каждой категории режима (ГОСТ 21354–87) по нормам ГОСГОРТЕХНадзора.
В упрощенных расчетах для легкого (4) и средних (2 и 3) режимов диаметр каната dк можно определить по формуле
Диаметр грузового барабана лебедки (мм) предварительно назначаем из условия:
D³dк·(e – 1)= 768·(18 – 1) = 13056 мм
где е – коэффициент диаметра барабана выбираемый в соответствии с нормами ГОСГОРТЕХНадзора; принимаем е = 18 [1].
Принимаем диаметр барабана равным Dб = 150 мм.
3. Частота вращения барабана
Частота вращения барабана (мин-1) вычисляется по формуле:
4. Подбор электродвигателя
Мощность необходимая для привода барабана:
Определение потребной мощности электродвигателя:
Определение КПД привода:
= 099 – КПД подшипника
=098– КПД зацепления
= 096 – КПД барабана
Окончательно принимаем
Определение общего передаточного отношения механизма.
По техническим данным двигателей серии АИР подсчитаем передаточное отношение.
По значениям данной таблицы выберем двигатель типа 112М4 со значением i = 1813 и n = 1455 обмин.
5. Момент на барабане лебедки
6. Момент на зубчатом колесе тихоходной ступени
7. Допускаемые контактные напряжения
Для передачи тихоходной ступени
Принимаем [sH]T = 630 МПа
Для передачи быстроходной ступени
Принимаем [sH]Б = 550 МПа.
8. Коэффициенты относительной ширины колес
Для редуктора по схеме 20:
–тихоходная передача ;
–быстроходная передача
Принимаем ybaБ = 032.
9. Эквивалентное время работы
Эквивалентное время работы LhЕ назначают с учетом категории режима работы:
– определяем коэффициент mH = 018 (для режима работы – III);
– находим LhЕ по формуле:
где Lh – заданный срок службы час.
10. Коды передач редуктора
Код передачи соответствует принятому в программе компьютера обозначению:
– прямозубая передача– 1;
– косозубая передача– 2;
– шевронная передача– 3.
В нашем случае редуктор по схеме 20 первая ступень (быстроходная передача) – косозубая вторая ступень (тихоходная ступень) – косозубая. Соответственно записываем 2 и 2.
11. Код схемы редуктора
Код схемы редуктора указывается в задании. В соответствии с ним заносим 21.
Кочкуров МХС-317 PEДУKTOP 20
MOM= 485. SIG1= 550. PSI1= .32 L1=2 CH=1455.
I= 18.13 SIG2= 630. PSI2= .35 L2=2 TE= 1800.
AW B Z1 Z2 U MOD D1 D2 X BETA
KOC 95.0 32.6 19 73 3.84 2.00 39.24 150.76 14.437
KOC 140.0 55.4 19 90 4.74 2.50 48.81 231.19 13.291
ПOДШИПHИKИ I ШAPИKOBЫE PAДИAЛЬHЫE I POЛИKOBЫE KOHИЧECKИE I
KAЧEHИЯ I TИП 0000 I TИП 7000 I
BAЛ 1 I C1= 8.03 C2= 5.41 I C1= 6.71 C2= 7.20 I
BAЛ 2 I C1= 9.70 C2= 17.25 I C1= 8.48 C2= 16.63 I
BAЛ 3 I C1= 32.33 C2= 7.49 I C1= 29.76 C2= 20.37 I
KOC 100.0 36.1 18 79 4.39 2.00 37.11 162.89 14.070
KOC 140.0 51.7 21 88 4.19 2.50 53.94 226.06 13.291
BAЛ 1 I C1= 8.24 C2= 5.63 I C1= 6.89 C2= 7.43 I
BAЛ 2 I C1= 9.37 C2= 17.07 I C1= 8.22 C2= 16.41 I
BAЛ 3 I C1= 32.65 C2= 7.51 I C1= 30.05 C2= 20.55 I
KOC 105.0 40.4 17 85 5.00 2.00 35.00 175.00 13.729
KOC 135.0 54.0 22 83 3.77 2.50 56.57 213.43 13.536
BAЛ 1 I C1= 8.57 C2= 5.86 I C1= 7.16 C2= 7.73 I
BAЛ 2 I C1= 9.38 C2= 17.47 I C1= 8.26 C2= 16.77 I
BAЛ 3 I C1= 34.30 C2= 7.91 I C1= 31.57 C2= 21.62 I
KOC 115.0 40.5 17 95 5.59 2.00 34.91 195.09 13.116
KOC 135.0 48.1 25 80 3.20 2.50 64.29 205.71 13.536
BAЛ 1 I C1= 8.60 C2= 5.82 I C1= 7.19 C2= 7.69 I
BAЛ 2 I C1= 9.10 C2= 17.29 I C1= 8.05 C2= 16.57 I
BAЛ 3 I C1= 35.34 C2= 8.14 I C1= 32.52 C2= 22.27 I
KOC 125.0 45.6 13 84 6.46 2.50 33.51 216.49 14.070
KOC 135.0 47.7 27 78 2.89 2.50 69.43 200.57 13.536
BAЛ 1 I C1= 8.68 C2= 6.34 I C1= 7.25 C2= 8.10 I
BAЛ 2 I C1= 8.73 C2= 17.28 I C1= 7.76 C2= 16.47 I
BAЛ 3 I C1= 35.79 C2= 8.19 I C1= 32.94 C2= 22.54 I
KOC 135.0 46.1 13 92 7.08 2.50 33.43 236.57 13.536
KOC 130.0 48.0 29 72 2.48 2.50 74.65 185.35 13.795
BAЛ 1 I C1= 8.94 C2= 6.40 I C1= 7.47 C2= 8.25 I
BAЛ 2 I C1= 8.90 C2= 17.86 I C1= 7.94 C2= 17.04 I
BAЛ 3 I C1= 38.70 C2= 8.92 I C1= 35.62 C2= 24.43 I
PACЧET REDUCE ЗAKOHЧEH
ВЫБОР ОПТИМАЛЬНОГО ВАРИАНТА КОМПОНОВКИ РЕДУКТОРА
Выбор оптимального варианта компоновки редуктора осуществляется по 2 критериям:
)по минимальному объему корпуса;
)по минимальной массе зубчатых колес.
Выбор производится из нескольких вариантов компоновки рассчитанных с использованием программы ATILLA.
Программа ATILLA предназначена для:
выбора оптимального варианта распределения передаточного отношения между ступенями двухступенчатого редуктора;
определения основных геометрических размеров передач;
предварительного подбора подшипников качения.
Программа не выдает единого оптимального решения. Она рассчитывает некоторое множество решений полученных при различных вариантах распределения общего передаточного отношения по ступеням передачи.
На рис. 1.1. приведены основные размеры зубчатых передач редуктора по схеме 21 с шевронной быстроходной передачей и выделены размеры A B и L определяемые для каждого из содержащихся в распечатке варианта по следующим формулам:
B = bwБ + bwТ + 3×a;
L = 05×(da2Б + da2Т) + awБ + awТ + (3 4)×a;
где da2ma a – зазор между корпусом и вращающимися деталями передач (колесами) (мм) определяемый по формул:
Проведем расчеты массы и объема для различных вариантов компоновки. Результаты расчетов сведем в таблицу и по ним построим графики изменения объема (V) и массы (m) редуктора по вариантам.
По критериям оптимизации – минимальные масса и объем - выбираем 4-й вариант.
ГЕОМЕТРИЧЕСКИЙ РАСЧЕТ ПЕРЕДАЧ РЕДУКТОРА
1. Быстроходная передача
– делительный диаметр:
Коэффициент торцового перекрытия для косозубых передач:
Коэффициент осевого перекрытия:
Суммарный коэффициент перекрытия:
2. Тихоходная передача
КИНЕМАТИЧЕСКИЙ РАСЧЕТ РЕДУКТОРА
1. Определение частот вращения валов
частота вращения быстроходного вала
nI = n1Б = 1455 мин-1;
частота вращения промежуточного вала
nII = n1Т = n2Б = n1Б uБ = 1455 559 = 2603 мин-1
частота вращения тихоходного вала
nIII = n2Т = n1Б (uБ × uТ) = 1455 (559×320) = 813 мин-1
2. Определение окружных скоростей в зацеплении
быстроходной ступени
V = p × d1Б × n1Б (6×104) = p × 34911 × 1455 (6×104) = 266 мс
По величине окружной скорости назначаем степень точности передачи – 8.
V = p × d1Т × n1Т (6×104) = p × 64286 × 2603 (6×104) = 088 мс
СТАТИЧЕСКОЕ ИССЛЕДОВАНИЕ РЕДУКТОРА
1. Моменты на валах и колесах редуктора
Момент на хвостовике быстроходного вала Нм
Момент на шестерне быстроходной передачи
Момент на колесе быстроходной передачи
Момент на шестерне тихоходной передачи редуктора
2. Составляющие полного усилия в зацеплениях быстроходной
и тихоходной передач
Окружная сила на шестерне быстроходной передачи Н
Радиальная сила на шестерне быстроходной передачи Н
Осевая сила на шестерне быстроходной передачи Н
Усилия действующие на колесо быстроходной передачи Н:
Окружная радиальная и осевая силы на шестерне тихоходной передачи Н:
Усилия действующие на колесо тихоходной передачи Н:
КОНСТРУИРОВАНИЕ ВАЛОВ РЕДУКТОРА
диаметр входного конца ведущего вала
Так как быстроходный вал приводится во вращение электродвигателем через стандартную муфту то необходимо согласовать выходной конец вала с валов электродвигателя т.е.
dБ = (08 – 10)×d1эл.дв. = (08 – 12)× 28 = 224 – 336 мм
Окончательно из двух условий диаметр входного конца вала принимаем dБ = 28 мм.
диаметр вала под подшипник и уплотнение
dП = dБ+2×tцил. = 28 + 2·35 = 35 мм;
принимаем dП = 35 мм;
где tцил. – высота заплечника (буртика); определяется по величине dБ;
диаметр буртика под подшипник (равный посадочному диаметру под колесо dK)
dБП = dK = dП + 32×r = 35 + 32·25 = 43 мм;
принимаем dБП = dK = 45 мм;
где r – координата фаски; определяется по таблице от величины dП;
длина посадочного участка
LМБ = 15 · d = 15 ·28 = 42 мм;
длина промежуточного участка
LКБ = (1 14) · dП = (1 14) ·35 = 35 49 мм;
принимаем LКБ = 40 мм;
для промежуточного вала диаметр в месте установки зубчатых колес
принимаем dK = 45 мм;
диаметр вала под подшипник
dП = dК - 3×r = 45 - 3·3 = 36 мм;
принимаем dП = 35 мм.
диаметр буртика для упора кольца подшипника
dБП = dП + 3 × r = 35 + 3× 25 = 425;
принимаем dБП = 42 мм.
диаметр буртика для упора колеса
dБК = dК + 3 × f = 45 + 3× 16 = 498;
принимаем dБК = 50 мм.
диаметр входного конца ведомого вала
принимаем dТ = 40 мм;
dП = dТ + 2×tцил. = 40 + 2·4 = 48 мм;
принимаем dП = 50 мм;
dБП = dK = dП + 32×r = 50 + 32·35 = 612 мм;
принимаем dБП = dK = 63 мм;
где r – координата фаски; определяется по таблице в зависимости от величины dП;
LМТ = 15 · dТ = 15 · 40= 60 мм;
LКТ = (08 12) · dП = (08 12) · 50 = 40 60 мм;
принимаем LКТ = 50 мм.
ПРЕДВАРИТЕЛЬНЫЙ ПОДБОР ПОДШИПНИКОВ
Быстроходный и промежуточный валы. По диаметру dП = 35 мм назначаем – шариковые радиальные подшипники легкой серии № 207 (С = 255 кН; С0 = 137 кН) ГОСТ 8338-75.
Тихоходный вал. По диаметру dП = 50 мм назначаем – шариковые радиальные подшипники легкой серии № 210 (С = 351 кН; С0 = 198 кН) ГОСТ 8338-75.
ПРОВЕРКА ЗУБЬЕВ НА ПРОЧНОСТЬ
Сталь 40Х ГОСТ 4543-71
Термообработка – закалка ТВЧ
Твердость поверхности 45 55 HRC
Сталь 45 ГОСТ 1050-88
Термообработка – улучшение
Твердость 192 240 HB
1 Расчет допускаемых контактных напряжений
Коэффициент безопасности
sHlim 1 = 17HRC + 200 = 17×50 +200 = 1050 МПа
Коэффициент долговечности
- базовое число циклов пр. усталости
По рисунку 8.40 [1]
Время работы tS = 10000 часов
Число циклов нагружения за срок работы
Эквивалентное число нагружений
Допускаемое контактное напряжение
SH = 11 при однородной структуре зуба
sHlim 2 = 2HB + 70 = 2×210 +70 = 490 МПа
Допускаемое контактное напряжение передачи
2. Расчет допускаемых изгибных напряжений
где - предел выносливости при изгибе
YN - коэффициент долговечности
YA - коэффициент учитывающий характер приложения нагрузки
SF - коэффициент безопасности
SF = 175 (улучшение)
YA = 1 (нереверсивная нагрузка)
sF lim1 = 18HB1 = 18 × 270 = 486 МПа
где NFG - базовое число циклов
NFE - эквивалентное число циклов нагружения
Эквивалентное число циклов нагружения
Допускаемое изгибное напряжение для шестерни
sF lim2 = 18HB2 = 18 × 210 = 378 МПа
Допускаемое изгибное напряжение для колеса
3. Расчет прочности зубьев по контактным напряжениям
Контактное напряжение в передаче
По степени точности 8 [1] скорости передачи
определим коэффициент учитывающий распределение нагрузки между зубьями
Коэффициент динамичности
Коэффициент перекрытия
Приведенный модуль упругости зубчатой пары
Тогда коэффициент повышения прочности
Найдем коэффициент концентрации нагрузки (KHb) по длине контактных линий
Условие прочности выполнено.
4. Расчет прочности зубьев по изгибным напряжениям
Коэффициенты нагрузки
Коэффициент нагрузки при изгибе:
Коэффициент формы зуба
Коэффициент учитывающий наклон зуба
Коэффициент торцевого перекрытия
sF2 = 1386 × 375 390 = 1333 МПа.
Условие прочности выполняется.
Проверочный расчет промежуточного вала
Расчетная схема промежуточного вала представляет собой двухопорную балку нагруженную силами возникающими в зацеплении от шестерни тихоходной ступени и на колесе быстроходной ступени.
Эпюры изгибающих моментов строят в двух взаимно перпендикулярных плоскостях. Для построения эпюры суммарного изгибающего момента используется зависимость где Mz и My – изгибающие моменты в сечении по плоскостям.
Реакции в опорах определяют из условия равновесия вала составляя уравнения статики Правильность определения реакций проверяют с помощью уравнения .
Суммарные реакции в опорах:
Внутренние изгибающие моменты в поперечных сечениях на каждом участке вала определяют методом сечений составляя уравнения равновесия .
I: 0 х1 а; МZ = RAy×
при МZ = RAy×a = -601·41 = -246 Н·м;
II: 0 х2 b; МZ = RAy×(a +
МZ = RAy×a+Fa2Б·d2Б2 = -601·41+359·195.0892 = 104 Н·м;
МZ =RAy×(a+b) - Fr2Б b+Fa2Б·d2Б2 =
= -601·(41 + 56)-548·56+359·195.0892 = -540 Н·м;
III: 0 х3 c; МZ = RBy×
при МZ = RBy с = -497·50 = -249 Н·м.
I: 0 х1 а; Мy = RAz×
при Мy = RAz×a = -2551 · 41 = -1046 Н·м;
II: 0 х2 b; Мy = RBz×(c+
Мy = RBz×c = -3314 · 50 = -1657 Н·м;
Мy = RBz×(b+c) + Ft1Т×b = -3314·(56+50) + 4404·56 = -1046 Н·м;
III: 0 х3 c; Мy = RBz
при МZ = RBz c = -3314 · 50 = -165.7 Н·м.
Опасное сечение в сечении С:
Mma Tmax = 126.0 Н·м
Проверочный расчет подшипников промежуточного вала
По ГОСТ 8338-75 выбрали подшипник 207.
Статическая грузоподъемность:
=3 – для шариковых подшипников
КБ = 13 – коэффициент динамической грузоподъемности
КТ = 1 – температурный коэффициент
V = 1 – коэффициент вращения кольца
Х = 1 – коэффициент радиальной нагрузки
Y = 0 – коэффициент осевой нагрузки.
Fa = FaT – FaБ = 1026 - 359 = 667 (осевая сила).
Так как Lh > Lhe = 1800 час (эквивалентное время работы с учетом режима работы) то данный подшипник подходит
Расчет на усталостную прочность
где запас сопротивления усталости только по изгибу;
– запас сопротивления усталости только по кручению;
и – амплитуды переменных составляющих циклов напряжений;
и – постоянные составляющие
и - коэффициенты корректирующие влияние постоянной составляющей цикла напряжений на сопротивление усталости;
Значения и зависят от механических характеристик материала.
Для легированных сталей =015; =01.
и – пределы выносливости
и – масштабный фактор и фактор шероховатости поверхности; (рис. 15.5 и 15.6) [1]
и - эффективные коэффициенты концентрации напряжений при изгибе и кручении; (табл. 15.1) [1]
Так как S > [S] = 15 – условие выполняется.
При установке колес на валах необходимо обеспечить надежное закрепление колеса на валу передачу вращающего момента от колеса к валу или от вала к колесу решить вопросы связанные с осевым фиксированием колес на валах и при необходимости предусмотреть регулирование осевого положения колес.
Для передачи вращающего момента чаще всего применяют призматические шпонки. Стандарт предусматривает для каждого размера вала определенные размеры поперечного сечения шпонки. Длину шпонки выбирают из стандартного ряда. Длину ступицы назначают на 8 10 мм больше длины шпонки.
Проверочный расчет шпоночных соединений.
В большинстве случаев в редукторах для крепления колес на валах применяют призматические шпонки.
Проведем расчет на прочность:
[sсм] = 150 МПа – допускаемое напряжение смятия.
Так как выбранная шпонка стандартная т.е. условие прочности по касательным напряжениям должно выполняться поэтому расчет ведем по напряжениям смятия.
Напряжение смятия действующее на шпонку
- шпонка обеспечивает необходимую прочность.
)На быстроходной ступени
Шпонка обеспечивает необходимую прочность.
)На тихоходной ступени
) На конце тихоходного вала
КОНСТРУИРОВАНИЕ ЭЛЕМЕНТОВ РЕДУКТОРА
1. Конструирование корпуса
В проектируемом редукторе принята конструкция разъёмного корпуса состоящего из крышки и основания корпуса. Габаритные размеры корпуса определяются размерами расположенной в корпусе редукторной передачи и кинематической схемой редуктора.
Толщину стенки основания корпуса отвечающую требованиям технологии литья необходимой прочности и жесткости корпуса находим по формуле
Толщина стенки крышки корпуса 1 = 09· = 09·8 = 72 мм. Принимаем 1 = 8 мм.
При конструировании корпусных деталей следует отделять обрабатываемые поверхности от необрабатываемых. Обрабатываемые поверхности выполняем в виде платиков высота h которых равна
Для соединения корпуса и крышки по всему контуру плоскости разъема редуктора выполняют специальные фланцы. Размеры конструктивных элементов фланцев:
мм. Принимаем f = 4 мм.
мм. Принимаем b = 12 мм.
мм. Принимаем l = 16 мм.
На продольных сторонах редуктора фланцы корпуса располагаются внутрь от стенки корпуса а фланцы крышки снаружи. Диаметр прилива для закладной крышки рассчитываем по формуле
где D – наружный диаметр подшипника.
Быстроходный и промежуточный валы:
Принимаем DП = 150 мм.
Длину l подшипниковых гнезд определяем конструктивно.
Для соединения крышки с основанием используем винты с цилиндрической головкой и внутренним шестигранником размера
Принимаем винты М12.
Для фиксирования крышки относительно основания применяем два конических штифта с внутренней резьбой. Диаметр штифтов
dшт. = (07 08)d = (07 08)· 12= 84 96 мм
где d – диаметр крепежного винта. Принимаем dшт. = 10 мм.
Для подъема и транспортирования крышки корпуса и редуктора в сборе применяем проушины отливая их заодно с крышкой. Проушины выполнены в виде ребра с отверстием. Диаметр отверстия
d = 3·1 = 3·8 = 24 мм.
Диаметр крепления корпуса к плите[4]:
dф » 125*d = 125*12 = 15 мм
где d – диаметр винта крепления крышки и корпуса редуктора.
Принимаем dф = 14 мм.
Места крепления корпуса к плите располагаем на возможно большем (но в пределах габарита корпуса) расстоянии друг от друга и оформляем в виде ниш расположенных по углам корпуса (рис. 12.3).
Высоту ниши принимаем [4]:
h0 = 25 × (dф + d) = 25 × (14 + 8) = 55 мм.
Принимаем h0 = 60 мм.
Остальные размеры назначаем в соответствии с рекомендациями рис. 17.18 [4]:
×dф = 11×14 = 154 мм. Принимаем 15 мм.
× dф = 15×14 = 21 мм. Принимаем 21 мм.
×dф + d = 24×14 + 8= 416 мм. Принимаем 42 мм.
5×dф = 125×14 = 175 мм. Принимаем 18 мм.
r = 05×d = 05×8 = 4 мм.
h1 = 05×d = 05×8 = 4 мм.
Для подъема и транспортирования крышки корпуса и редуктора в сборе применяем проушины отливая их заодно с крышкой. Проушины выполнены в виде ребра с отверстием.
S = 25·1 = 25·8 = 20 мм.
При работе передачи масло постепенно загрязняют продукты изнашивания оно стареет – свойства его ухудшаются. Поэтому масло периодически меняют. Для слива масла в корпусе выполняют сливное отверстие закрываемое пробкой с конической резьбой.
Для заливки масла в редуктор и контроля правильности зацепления делают люк. Чтобы удобнее было заливать масло и наблюдать за зубчатыми колесами при сборке и эксплуатации размеры люка должны быть максимально возможными.
МАНЖЕТНЫЕ УПЛОТНЕНИЯ
Широко применяются при смазывании подшипников жидким маслом и при окружной скорости до 20 мс манжетные уплотнения. Манжета состоит из корпуса изготовленного из маслобензостойкой резины каркаса представляющего собой стальное кольцо Г-образного сечения и браслетной пружины. Каркас придает манжете жесткость и обеспечивает плотную посаду в корпусную деталь без дополнительного крепления. Браслетная пружина стягивает уплотняющую часть манжеты вследствие чего образуется рабочая кромка шириной b = 04 06 мм плотно охватывающая поверхность вала.
Манжету обычно устанавливают открытой стороной внутрь корпуса. К рабочей кромке манжеты в этом случае обеспечен хороший доступ смазочного масла.
Подбор манжеты проводим по диаметру вала под подшипник:
– для быстроходного вала dП = 35 мм – Манжета 1-35х58-1 ГОСТ 8752-79;
– для тихоходного вала dП = 50 мм – Манжета 1-50х70-1 ГОСТ 8752-79.
ВЫБОР СМАЗОЧНЫХ МАТЕРИАЛОВ
В данном редукторе используется картерная система смазывания т.е. корпус является резервуаром для масла. Масло заливается через верхний люк. Для слива масла в корпусе предусмотрено сливное отверстие закрываемое пробкой.
При работе передач продукты изнашивания постепенно загрязняют масло. С течением времени оно стареет свойства его ухудшаются. Браковочными признаками служат повышенное содержание воды и наличие механических примесей. Поэтому масло залитое в корпус периодически меняют.
В зависимости от контактного напряжения и окружной скорости колес определяем требуемую вязкость масла 34 мм2с. По вязкости определяем марку масла - масло индустриальное И-Г-А-32. Потребное количество масла V = 90 л.
Для наблюдения за уровнем масла в корпусе устанавливают маслоуказатели жезловые (щупы). Исполнение наклонного щупа вызывает некоторые технологические трудности при формовке корпуса и сверлении наклонного отверстия поэтому вертикальное исполнение предпочтительнее.
СПИСОК ИСПОЛЬЗОВАННОЙ ЛИТЕРАТУРЫ
Прокшин С.С. Беляев Б.А. Методические указания к курсовому проектированию по дисциплине «Детали машин и основы конструирования»: Уфимск. гос. авиац. техн. ун-т. – Уфа 2006. – 58 с.
Дунаев П.Ф. Леликов О.П. Конструирование узлов и деталей машин: учебное пособие. – 9-е изд. перераб. и доп. – М.: Академия 2006. – 496 с.
Анурьев В.И. Справочник конструктора-машиностроителя: в 3-х томах. Т.1-3 – 5-е изд. перераб. и доп. – М.: Машиностроение 1978.
Иванов М.Н. Детали машин: Учеб. для студентов вузов. – 6-е изд. перераб. – М.: Высш. шк. 2000 – 383 с. ил.
Эскизы стандартных изделий
Подшипник ГОСТ 8338-75
Обозначение подшипника
Манжета ГОСТ 8752-79
Винт М12х60-6gх 60.58
d = 10 мм;D = 16 мм;Н1 = 56 мм;h1 = 46 мм;
Рекомендуемые чертежи
- 24.01.2023