Проектирование технологического процесса восстановления шкива коленчатого вала




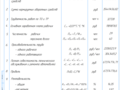
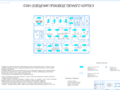
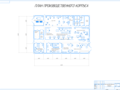
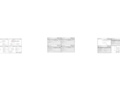
- Добавлен: 04.11.2022
- Размер: 704 KB
- Закачек: 2
Описание
Состав проекта
![]() |
![]() |
![]() ![]() ![]() |
![]() ![]() ![]() |
![]() ![]() ![]() |
![]() ![]() ![]() ![]() |
![]() ![]() ![]() ![]() |
![]() ![]() ![]() |
Дополнительная информация
Диплом ПЗ.doc
ОРГАНИЗАЦИОННО-ТЕХНОЛОГИЧЕСКАЯ ЧАСТЬ
Определение трудоемкости капитального ремонта восстанавливаемого объекта . . . . . . . . . . . . . . . . .. . . . . . . . . . . . . . . . . . . . . . . . . . . . . . .
Линейный график согласования ремонтных работ. . . . . . . . . . . . . . .
Расчет годовой программы предприятия. . . . . . . . . . . . . . . . . . . . . .
Годовая трудоемкость основных работ . . . . . . . . . . . . . . . . . . . . . .
Трудоемкость сопутствующих работ . . . . . . . . . . . . . . . . . . . . . . . .
Распределение трудоемкости по отделениям (участкам)
Предприятия. . . . . . . . . . . . . . . . . . . . . . . . . . . . . . . . . . . . . . . . . . .
Режим работы предприятия и годовые фонды времени. . . . . . . . . . . .
Расчет и подбор технологического оборудования. . . . . . . . . . . . .
Расчет площадей ремонтного предприятия. . . . . . . . . . . . . . . . . . . .
Расчет площадей вспомогательных помещений. . . . . . . . . . . . . . . . . . . . . . .
Компоновка производственного корпуса. . . . . . . . . . . . . . . . . . . . . . . . . . . . .
Определение габаритов здания. . . . . . . . . . . . . . . . . . . . . . . . . . . . . . . .
Компоновка подразделений производственного корпуса. . . . . . . . . . . . . .
Назначение конструктивные особенности и условия работы детали в узле. . . . .
Технические условия на контроль-сортировку. . . . . . . . . . . . . . . . . . . . . . . .
Обоснование маршрута восстановления. . . . . . . . . . . . . . . . . . . . . . . . . . . .
Установление технологической последовательности операций. . . . . . . . . . . . .
Расчет режимов механической обработки и техническое нормирование операций
восстановления . . . . . . . . . . . . . . . . . . . . . . . . . . . . . . . . . . . . . . . . . .
Проектирование станочного приспособления. . . . . . . . . . . . . . . . . . . . . . . . .
ОХРАНА ТРУДА И ПРОИЗВОДСТВЕННАЯ САНИТАРИЯ . . . . . . . . . . . . . . . . . . . . .
Расчет отопления производственного корпуса АРП. . . . . . . . . . . . . . . . . . .
Расчет вентиляции производственного корпуса . . . . . . . . . . . . . . . . . . . . . .
Расчет освещения производственных помещений. . . . . . . . . . . . . . . . . . . . . .
Расчет естественного освещения. . . . . . . . . . . . . . . . . . . . . . . . . . . . . . .
Расчет искусственного освещения. . . . . . . . . . . . . . . . . . . . . . . . . . . . . . .
Производственный шум. . . . . . . . . . . . . . . . . . . . . . . . . . . . . . . . . . . . . . .
Аттестация рабочих мест по условиям труда в производственном участке. . . . .
Оценка технического и организационного уровня рабочего места. . . . . . . . . . . .
Оградительные устройства. . . . . . . . . . . . . . . . . . . . . . . . . . . . . . . . . . . .
Пожаровзрывобезопасность. . . . . . . . . . . . . . . . . . . . . . . . . . . . . . . . . . . .
Анализ условий возникновений пожара. . . . . . . . . . . . . . . . . . . . . . . . . . . . .
Анализ путей распространения пожара . . . . . . . . . . . . . . . . . . . . . . . . . . . .
Анализ мероприятий по ограничению распространения пожара. . . . . . . . . . . . . .
Мероприятия по защите окружающей среды . . . . . . . . . . . . . . . . . . . . . . . . .
ТЕХНИКО-ЭКОНОМИЧЕСКАЯ ОЦЕНКА ПРОЕКТА
Полная себестоимость обслуживания и текущего ремонта автомобилей. . . . . .
Фонд заработной платы ремонтно-обслуживающих рабочих зоны ТО и ТР. . . . .
Затраты на запасные части. . . . . . . . . . . . . . . . . . . . . . . . . . . . . . . . . . . .
Затраты на основные материалы. . . . . . . . . . . . . . . . . . . . . . . . . . . . . . . . .
Расходы по обслуживанию и управлению производством (накладные расходы) . . .
Прибыль предприятия. . . . . . . . . . . . . . . . . . . . . . . . . . . . . . . . . . . . . . . . .
Потребность в нормированных оборотных средствах. . . . . . . . . . . . . . . . . . .
Рентабельность предприятия. . . . . . . . . . . . . . . . . . . . . . . . . . . . . . . . . . . .
Расчет нормируемых оборотных средств. . . . . . . . . . . . . . . . . . . . . . . . . . . .
Производительность труда. . . . . . . . . . . . . . . . . . . . . . . . . . . . . . . . . . . . .
Показатели использования производственных фондов. . . . . . . . . . . . . . . . . . . .
Основные технико-экономические показатели зоны ТО и ТР. . . . . . . . . . . . . . .
РАЗРАБОТКА ПЛАНА-КОНСПЕКТА КОМБИНИРОВАННОГО УРОКА С ЭЛЕМЕНТАМИ ИГРЫ . . . . .
Заключение . . . . . . . . . . . . . . . . . . . . . . . . . . . . . . . . . . . . . . . . . . . . . . .
Перечень ссылок. . . . . . . . . . . . . . . . . . . . . . . . . . . . . . . . . . . . . . . . . . . .
Приложение. . . . . . . . . . . . . . . . . . . . . . . . . . . . . . . . . . . . . . . . . . . . . . .
Важнейшей характеристикой в качестве и надёжности машин являются затраты на их эксплуатацию и ремонт т.е. затраты на поддержание и восстановление их работоспособности и ресурса в процессе применение. В технической литературе указывается что затраты труда и средств на техническое обслуживание в 5-10 раз и более превышают соответствующие затраты их изготовления.
Основными задачами машиностроения на данный момент являются повышение надёжности и долговечности машин снижение себестоимости их производства. Это требует дальнейшего совершенствования технологии машиностроения применения средств автоматизации и комплексной механизации технологических процессов современных высоко-производственных методов обработки деталей и сборки машин. Технология производства и дорожных машин должно базироваться на современных достижениях науки и техники.
С целью ускорения технологической подготовки производства широко используют типовые технологические процессы что значительно снижает затраты на проектирование позволяет применять автоматические переналаживания машин участки и технологическую оснастку. Основное внимание следует уделить достижению заданных качественных характеристик изделия при выполнении ремонтов.
ОПРЕДЕЛЕНИЕ ТРУДОЕМКОСТИ КАПИТАЛЬНОГО РЕМОНТА ВОССТАНАВЛИВАЕМОГО ОБЪЕКТА
Расчет предприятия ведется по укрупненным показателям поэтому трудоемкость восстановления ремонтируемого объекта рассчитывают опираясь на эталонную трудоемкость.
За эталонную принята трудоемкость восстановления двигателей автомобиля с годовой программой 728 единиц.
Для силового агрегата
Трудоемкость восстановления заданного объекта ремонта составит:
3*11*1009=8073 чел·ч
где КА – коэффициент учитывающий изменение трудоемкости восстановления в зависимости от типа объекта ремонта (Табл. 12);
КП – коэффициент учитывающий изменение трудоемкости восстановления в зависимости от годовой программы предприятия.
ЛИНЕЙНЫЙ ГРАФИК СОГЛАСОВАНИЯ РЕМОНТНЫХ РАБОТ
Такт ремонта означает время через которое на предприятие должно поступить или выйти из ремонта очередное изделие.
Общий такт ремонта рассчитывают по формуле
где ФП – годовой фонд времени предприятия ФП =2034ч;
N – программа ремонтного предприятия N=800 ед·год.
Длительность производственного цикла ремонта изделия характеризует совершенство организации производственного процесса на проектируемом предприятии и означает продолжительность пребывания изделия в ремонте.
Длительность цикла ремонта изделия наиболее точно определяется графическим путем т. е. построением линейного графика согласования ремонтных работ. Исходные данные для построения графика:
последовательный перечень работ (операций) составляющий технологический процесс ремонта изделия с указанием нормы времени (трудоемкости) и разряда по каждой работе.
общий такт ремонта изделия.
Построение линейного графика согласования операций ремонта изделия выполняют в такой последовательности.
На листе вычерчивают специальную форму в которую пользуясь справочными данными заносят номера рабочих мест наименование операций (работ) в соответствии с принятой технологией ремонта машин разряды работ и их трудоемкость.
Расчетную численность рабочих по каждому рабочему месту определяют по формуле
где Тр — трудоемкость работ на определенном рабочем месте чел.-ч.
Рабочие места комплектуют в посты. Так как численность рабочих по каждой укрупненной операции при расчете как правило не будет целым числом принятое количество их определяют комплектованием рабочих мест в посты по признаку сходности выполняемых операций близких по разряду до наиболее полной загрузки рабочего.
При этом надо иметь в виду что недогрузка допускается до 5% а перегрузка — до 15%.
Загрузка рабочего на каждом посту составит;
где Рпр — принятое число рабочих на посту.
Для операций (работ) где численность рабочих больше двух — четырех человек рассчитывают число рабочих мест так как одновременная работа такого количества рабочих на одном рабочем месте технологически неосуществима или затруднена.
Число рабочих мест рассчитывают по формуле
где Ро — число исполнителей на одном рабочем месте (плотность выполнения работ).
При формировании рабочих мест необходимо стремиться к получению их минимального числа. Это можно достигнуть увеличением числа исполнителей на одном рабочем месте до определенного предела а также более равномерным распределением работ по сменам.
Число исполнителей на одном рабочем месте устанавливают из характера и удобства выполнения работы несколькими исполнителями массы и габаритов изделий. Так например для разборки и сборки машины на одном рабочем месте рекомендуется иметь два — четыре человека.
Данные по формированию рабочих мест заносят в соответствующие графы таблицы линейного графика согласования операций.
Продолжительность выполнения операций (работ) по каждому рабочему месту определяют по формуле:
где Кз – коэффициент учитывающий загрузку рабочих на рабочем месте (Кз = Зр100).
Продолжительность каждой операции в принятом масштабе откладывают на графике в виде отрезков прямой около которой цифрой указывают номер рабочего выполняющего данную работу.
В случае наличия нескольких исполнителей на одном рабочем месте продолжительность выполняемой работы изображают параллельными линиями число которых равно численности исполнителей. При недостаточной загрузке рабочего на одном виде и догрузке его другим видом работ связь между указанными работами на графике показывают вертикальной пунктирной линией. При построении графика нужно стремиться к тому чтобы продолжительность работы выполняемой каждым рабочим равнялась продолжительности такта ремонта; очередная работа начиналась после того как будет закончена предыдущая технологически ей предшествующая; работы выполнялись максимально возможно параллельно; соблюдались разряды выполняемых одним рабочим работ.
Сегодня практически отсутствует опыт передовых специализированных организации по ремонту автомобилей на который можно было бы базироваться поэтому распределение трудоемкости по видам операций рекомендуется производить на основе уже имеющихся справочных данных в литературе и данных приведенных таблицах Приложения. В учебных целях допускается в проекте производить распределение трудоемкости работ для заданного объекта ремонта самим проектантом согласуя конечные результаты с руководителем придерживаясь нижеизложенных положений.
В начале в соответствии с разработанным производственным процессом необходимо произвести укрупненное деление трудоемкости Тосн по агрегатам и составным частям автомобиля в пропорции и соответствии имеющихся коэффициентов приведения капитального ремонта агрегатов к капитальному ремонту полнокомплектного автомобиля Приложение . Затем необходимо трудоемкость каждого агрегата и составной части автомобиля в зависимости от конструктивных особенностей распределить в процентах по видам и последовательности выполнения работ примерно в соотношении:
-Разборочно-моечные - 8-145%
-Контрольно-сортировочные .-18-27%
-Ремонтно-восстановительные -58-62%
-Обезжиривающие и окрасочные -0.02-5%
-Сборочно-испытательные .-25%.
В зависимости от сложности виды производимых работ разбиваются на более мелкие составляющие до вычленения рабочих мест по специальности и квалификации. Затем разбивку трудоемкости агрегатов и составных частей необходимо объединить в общую трудоемкость производственного процесса ремонта заданного объекта. Этот процесс очень важен и требует от проектанта не только знания производственного процесса ремонта но и сочетания этих знаний с опытом приобретенным при прохождении производственных практик.
Процентная разбивка трудоемкости разборки и сборки узлов основных агрегатов автомобилей приведена в Таблице. Распределение трудоемкости по производственным участкам авторемонтного предприятия в процентном соотношении приведена в Приложении.
В графах под общим наименованием "Число рабочих" в соответствии с трудоемкостью производственной операции рассчитывается по формуле и указываются количество принятых рабочих. На этом этапе формируются из рабочих мест посты ( разборки сборки дефектовки и т.д.) обосновывается их сменность. Кроме того на этом этапе так же формируется список основного производственного оборудования и механизированного инструмента для выполнения операций который приводится в расчетно-пояснительной записке. Особенностью этой части работы является возможность и необходимость организации работ с наибольшей загруженностью оборудования и обслуживания одним человеком нескольких недогруженных станков и другого оборудования. Для участков годовой объем работ которых выражается не в человеко-часах а в станко-часах и специфика технологического процесса предусматривает использование оборудования не требующего постоянного и активного участия рабочих (термические гальванические) и появляется возможность одному рабочему обслуживать несколько термических печей гальванических ванн.
После проделанных расчетов переходим к наиболее важной части работы - построению самого графика ремонтного цикла. На этом этапе должены задаться целью - минимизировать продолжительность пребывания объекта в ремонте и для этого возможно большее число работ необходимо выполнять параллельно с учетом технологической возможности. Например дефектацию необходимо производить после мойки а работы по ремонту деталей должны начаться только после дефектации и т.д.
В случаях выполнения ремонта узлов снятых при предварительной разборке например топливная аппаратура электрооборудование необходимо предусмотреть проведение всего комплекса ремонтных работ на участке в том числе и дефектовку с комплектовкой. Соответственно исполнителем работ необходимо назначать квалифицированного рабочего.
Продолжительность каждой операции в принятом масштабе откладывают на графике в виде отрезков прямой около которой цифрой указывается номер рабочего выполняющего указанную часть работ производственного процесса. Длинна отрезка должна приближаться и соответствовать величине такта производства рассчитанного по формуле . В случаях когда трудоемкость работ выделенных в пунктах производственного процесса превышает действительный фонд времени рабочего соответствующей специальности необходимо увеличить количество исполнителей а на графике в этом случае изображается дополнительная параллельная линия с указанием последующего номера рабочего этих работах. При недостаточной загрузке рабочего на одном рабочем месте и догрузке его на другом виде работ связь между указанными работами показывается вертикальной пунктирной линией.
Если организация рабочих мест предусматривает несколько одинаковых рабочих мест то продолжительность выполнения на первом рабочем месте показывают сплошной линией а последующих пунктирной.
В целом этот этап работы требует от исполнителя глубокого осмысления каждого пункта производственного процесса творческого подхода к организации выполнения работ каждой операции. У проектанта должно сформироваться четкое представление об организации производимых работ оснащенности исполнителя оборудованием приспособлениями оснасткой инструментом.
Нетрудно понять что физический смысл этой работы заключатся в стремлении правильно рассчитать и уменьшить время пребывания объекта в ремонте и равномерно распределить работы по ремонту единицы изделия на общее количество основных производственных рабочих соблюдая при этом технологическое время производимых работ и смысловую последовательность выполнения операции.
Действительно в этом случае если каждый рабочий выполнит свою часть возложенной на него работы за время равное такту производства то в результате должен завершится ремонт одного объекта из общего количества находящихся в процессе ремонта предоставив при этом возможность принять на ремонт следующий объект. Не трудно понять что чем больше программа ремонта тем меньшее количество технологических операций возлагается на одного рабочего предоставляется экономическая и технологическая возможность применения высокопроизводительного оборудования приспособлений и инструментов. В наибольшей степени это можно отнести в настоящем к возможностям организации ремонта силовых агрегатов автомобиля так как эксплуатационные требования по экологической безопасности заметно ужесточаются и вызывает необходимость ремонта на специализированных предприятиях.
Сокращение ремонтного цикла объекта ремонта должно производиться путем осмысленного планирования и соответствия последовательности выполнения работ в технологии ремонта. Зачастую в технологии ремонта заложены физико-химические процессы происходящие без постоянного и непосредственного участия рабочего например очистка в моечной машине нагрев в печи гальваника сушка после окраски применения клеящих составов обкатка и т. д. Поэтому проектанту необходимо учесть технологическое время работы некоторой части оборудования без постоянного и непосредственного участия рабочего. В это время рабочий должен выполнять подготовительные и прочие работы с предыдущим или последующим объектом ремонта. На ГРЦ этот процесс будем изображать в виде прерывистой линии где сплошной показывается время рабочего затраченного на выполнение технологических работ. В сумме время участия рабочего на данной операции должно соответствовать по величине такту ремонта.
Разнообразие моделей автомобилей и его модификаций в одном классе направляет разработчика на использование подходов характерных для индивидуального и мелкосерийного ремонта автомобилей что соответственно отражается на графике ремонтного цикла в виде недостаточного количества заделов по готовым (отремонтированным) сложным агрегатам и узлам и даже запасным частям. В итоге это обстоятельство не позволяет уложиться по длительности работ в расчетный такт производства и тем самым удлиняет время пребывания объекта в ремонте. Действительно сборка автомобиля не может быть завершена пока не отремонтированы все его агрегаты. Агрегат с наибольшей трудоемкостью и продолжительностью ремонта определяет продолжительность ремонта. У легковых автомобилей таким агрегатом является кузов. Объем работ по его ремонту составляет более 40% от общего объема работ по ремонту автомобиля в целом. Трудоемкость и продолжительность ремонта рамы грузового автомобиля меньше трудоемкости и продолжительности ремонта других более сложных агрегатов - кабины двигателя. Эти и другие подобные технологические особенности ремонта автомобилей его агрегатов должны быть отражены в графике ремонтного цикла. Приводится график технологического цикла ремонта автомобиля отражающий эти особенности.
Получить наибольшее приближение ГРЦ к реальному процессу позволяет узловая детализация технологического процесса ремонта. Для этого при построении последовательности операций технологического процесса на листе необходимо выделить процессы ремонта агрегатов узлов в отдельные группы ранжируя их по мере последовательности выполнения разборки. В результате на ГРЦ можно будет различить работу по отделениям постам и каждого исполнителя.
При достаточном дроблении технологии на элементарные операции ремонта упрощается последующая работа по размещению исполнителей по рабочим местам и выбор соответствующего оборудования приспособлений и размещения его при планировке производственного крпуса.
Иногда могут встречаться ситуации когда продолжительность работы меньше такта. При этом для загрузки рабочего необходимо в последующих работах отыскать такую которая догружала бы рабочего до полного такта.
Для уменьшения продолжительности цикла производства целесообразно возможно большее число работ выполнять параллельно с учетом технологической возможности. Так например работы по ремонту сборочных единиц и восстановлению отдельных деталей должны начинаться только после дефектации. Окончание моечных работ необходимо планировать на один-два часа позже разборочных дефектацию — на один-два часа после мойки. Нельзя начинать сборку двигателя и заднего моста не закончив ремонт блока и корпуса заднего моста и т. д.
Отрезки на графике определяющие все эти виды работ соответствуют технологическому времени.
По графику определяют длительность цикла отражающего только технологическое время (tтех). Общая продолжительность цикла производства с учетом времени на контроль транспортирование комплектование перед сборкой и межоперационное время составит:
Устанавливают главный параметр производства — фронт ремонта т. е. число изделий одновременно находящихся в ремонте. Его определяют по формуле
РАСЧЕТ ГОДОВОЙ ПРОГРАММЫ ПРЕДПРИЯТИЯ
Годовая трудоемкость основных работ
где T – трудоемкость ремонта одного объектаТ=8073 чел×ч; N – годовая программа предприятияN=800 ед·год.
Если по заданию кроме выполнения основных работ предусмотрено выполнение дополнительных работ по текущему ремонту автомобилей либо отдельных агрегатов расчет годовой трудоемкости Тдоп ведется аналогично основной трудоемкости.
Трудоемкость сопутствующих работ составит
а) Ремонт оборудования мастерской
б) Ремонт и изготовление инструментов и приспособлений
Тпроч = 01× Тосн чел·ч.
Распределение трудоемкости по отделениям (участкам) предприятия.
Предприятие по ремонту автомобильного транспорта в основном имеют в своем составе следующие отделения (участки) (на примере предприятия по ремонту грузовых автомобилей):
Контрольно-сортировочное и комплектовочное;
Ремонта электрооборудования;
Ремонта пневмо- и гидросистем;
Слесарно-механическое;
Сварочно-наплавочное;
Регулировки и испытания;
Данные зоны относятся к производственным. Помимо этого обязательно предусматриваются вспомогательные помещения: складские санитарно-бытовые ремонта собственного оборудования и пр.
Основную трудоемкость Тосн распределяют по отделениям предприятия. Полученные данные заносят в табл. 1.
Процентное распределение трудоемкости по отделениям принимаются в соответствии с соотношением принятым при построении графика ремонтного цикла. При распределении по отделениям проценты работ выполняемых в одном отделении (например разборочно-моечное отделение объединяет работы по подразборке мойке разборке узлов и др.) суммируются.
Сопутствующие работы по ремонту оборудования ремонту и изготовлению инструментов и прочие неучтённые работы распределяются по определённым отделениям предприятия по соотношениям приведенным в методических указаниях (табл 1).
Общая трудоемкость по каждому отделению Т отд (в чел×ч) определится суммированием основной дополнительной и сопутствующей трудоемкостей для этого отделения.
РЕЖИМ РАБОТЫ ПРЕДПРИЯТИЯ И ГОДОВЫЕ ФОНДЫ ВРЕМЕНИ
Режим работы предприятия характеризуется количеством рабочих дней в году количеством смен в сутки продолжительностью смены и рабочей недели в часах.
Законодательством Украины предусмотрена пятидневная рабочая неделя и шесть официальных праздничных дней в году. Количество рабочих дней в году составляет:
где Дк – количество календарных дней в году принимается Дк = 365;
Дв – количество выходных дней в году принимается Дв = 104 (при пятидневной рабочей неделе);
Дп – количество праздничных дней в году Дп = 6
Количество смен в сутки для различных отделений мастерских обычно неодинаково. Механическое испытательное гальваническое отделения должны работать в 2 смены а в остальных отделениях допускается работа в одну смену. Однако в учебных целях и ввиду относительно небольших программ проектируемых предприятий принимается для всех отделений предприятия односменный режим работы.
Годовые фонды рабочего времени подразделяются на номинальные и действительные.
Действительный фонд времени рабочего определяется фактическим временем отработанным рабочим в течение года с учетом различных потерь (отпуска болезни командировки выполнения общественных обязанностей).
Номинальный фонд времени рабочего рассчитывается без учета указанных потерь. Номинальный годовой фонд времени одного рабочего (Фн) определяется по формуле:
5 * 8 - 6 * 1 = 2034 ч
5 * 72 - 6 * 1 = 1830 ч
где tсм – продолжительность рабочей смены ч;
tсм – сокращение рабочей смены в предпраздничные дни tсм = 1 ч.
Дпп – количество предпраздничных дней в году Дпп=Дп.
Действительный годовой фонд времени одного рабочего (Фд)
где Дот – продолжительность отпуска рабочего дни.
Законодательством предусмотрен отпуск в количестве:
дня – для кузнецов мотористов гальваников сварщиков медников маляров аккумуляторщиков;
дней – для прочих профессий.
р – коэффициент учитывающий потери рабочего времени по уважительным причинам
Расчет численности производственных рабочих ИТР МОП.
Количество производственных рабочих подразделяется на списочное и явочное. Списочное количество определяется по отделениям предприятия по формуле:
где Тотд – трудоемкость работ по отделению (табл. 2) чел·ч;
Фд – действительный годовой фонд времени рабочего ч.
Явочное количество:
где Фн – номинальный годовой фонд времени рабочего ч.
Полученные значения Ряв округляются до целых Рпр.
При этом загрузка рабочего ) должна лежать в пределах от 95% до 115%.
Результаты расчетов заносятся в таблицу 1.
При невозможности округления до целого числа численности рабочих в пределах одного отделения объединяются рабочих разных отделений по сродности выполняемых работ разряду работ близости расположения отделений суммарной загруженности рабочего.
РАСЧЕТ И ПОДБОР ТЕХНОЛОГИЧЕСКОГО ОБОРУДОВАНИЯ
В проекте даются примеры расчетов основного оборудования ремонтного предприятия. К основному относятся оборудования на котором выполняются наиболее сложные технологические операции ремонта машин. Это моечные машины металлорежущие станки разборочно-сборочные конвейеры обкаточно-испытательные стенды.
Остальное технологическое оборудование подбирают по типовой технологий ремонта машин исходя из полученного количества производственных рабочих установленных рабочих мест постов.
Количество моечных машин периодического действия (для мойки агрегатов) определяется по формуле:
где Q - масса агрегатов подлежащих мойке за год (или 30 от массы машины);
t - время мойки агрегатов (деталей). Ориентировочно 05ч.;
Фдо - действительный фонд времени оборудования (моечной машины);
g - масса одной загрузки кг принимается по технической характеристике машины для мойки;
ha- коэффициент загрузки моечной машины по массе зависящий от конфигурации и габаритных размеров равный 06-08;
ht - коэффициент использования машины во времени. Количество моечных машин конвейерного типа (для мойки деталей)
где g1 - производительность моечной машины кгчас принимается по технической характеристике моечной машины.
Общая масса деталей подлежащих мойке определяется из выражения:
Q = 0.6*1000*3300 = 1980000
где - коэффициент учитывающий долю массы деталей подлежащих мойке = 04÷06 - для тракторов автомобилей
Q - мacca машины кг (приложение 7)
N - годовая программа ремонта (единиц шт.).
Количество выварочных ванн для выварки корпусных деталей (блоков жюпусов задних мостов КПП.) определяется из выражения:
Qв - масса деталей подлежащих выварке в расчетах Qв принимается 15 от массы машины или 40 % от массы двигателя.
Согласно технологическому процессу подбирается остальное оборудование моечного отделения. Количество металлорежущих станков определяется из выражения:
Scm=167080*1.11689*09=45
где Тап - годовая трудоемкость станочных работ.
γ - коэффициент неравномерности загрузки предприятия (γ = 10÷13)
- коэффициент использования станочного оборудования равный: 085÷090
Для специализированных ремонтных предприятий механическое отделение планируют на двусменную работу.
Количество испытательных стендов для специализированных ремонтных
предприятий определяется из выражения:
где об - общий такт ремонта ч.
При SИ ≤ 2 принимают два стенда один для обкатки и испытания основного двигателя и один для пускового.
При SИ ≥ 2 работу испытательного участка принимают в две смены.
Количество сварочных аппаратов рассчитывается по формуле:
где Тсв – трудоемкость сварочных работ.
С – количества смен.
Полученное по расчету и принятое оборудование сводится в таблицу.
Расчет площадей ремонтного предприятия
Расчет производственных помещений
В ходе выполнения проекта расчет производственных площадей производится в два этапа: вначале рассчитывается по удельным площадям на одного производственного рабочего затем проверяются полученные значения расчетом по площади занимаемой оборудованием и ремонтными агрегатами.
По количеству производственных рабочих площади отделений рассчитываются по формуле:
где: Рпр - принятое количество человек в отделении
fyд - удельная площадь на одного производственного рабочего.
Площадь рассчитывается для каждого отделения. В случае когда на один рабочий задействован на нескольких отделениях необходимо читывать его для каждого из отделении.
Расчет по площади занимаемой оборудованием ведется по формуле:
где Fоб - суммарная площадь занимаемая оборудованием м2;
кпр- коэффициент учитывающий площадь необходимых рабочих проездов. Площадь отделения принимается по максимальной из полученных величин.
Результаты всех расчетов сведены в таблицу 3.
Наименование отделения
Номер на технологической планировке
Принятое количество рабочих в отделении Рпр
Удельная площадь на одного производственного fуд
Контрольно-сортировочное и комплектовочное
Ремонта топливных систем
Ремонта электрооборудования
Слесарно-механическое
Медницко-радиаторное
Сварочно-наплавочное
Восстановления узлов и агрегатов
Регулировки и испытания
Расчет площадей вспомогательных помещений.
К вспомогательным помещениям относятся помещения напрямую не связанные с технологическим процессом ремонта однако находящиеся 5 производственном корпусе: склады ОГМ лаборатории культурно-бытовые и другие помещения.
Расчет их площадей обычно ведется по аналогии с производственными помещениями. Однако с целью упрощения расчетной части проекта на основании эмпирических данных площадь вспомогательных помещений принимается в размере 25% от производственных. В данном расчете окончательная площадь производственного корпуса составит 2900 м2.
КОМПОНОВКА ПРОИЗВОДСТВЕННОГО КОРПУСА
В соответствии с разработанной схемой производственного процесса капитального ремонта выбрать схему технологического процесса;
В соответствии с выбранной схемой технологического процесса определится с взаиморасположением производственных участков и зон;
В соответствии с габаритными размерами ремонтируемых объектов подъемно-транспортным оборудованием строительными нормами и правилами (СНИП) определить предварительно производственные пощади и общие размеры производственного корпуса;
Определившись с предварительной компоновкой производственного корпуса нанести разработанный вариант грузопотока и проверить его на наличие противотоков. (В случае наличия большого числа противотоков и перекрещивающихся грузопотоков - разработать новую схему).
1 ОБЩИН ПОЛОЖЕНИЯ. Перед разработкой компоновочного плана производственного корпуса на выбранном участке застройки предприятия намечают предварительную схему производственного потока. На нее наносят взаимное расположение всех намечаемых к строительству
объектов предприятия складов рем. фонда металла заготовок и готовой продукции котельной служебно-бытовых помещений подъездных путей и других объектов. (Создается компоновочный план производственного корпуса).
Как правило при проектировании авторемонтных предприятий все производственные и вспомогательные подразделения располагают в одном корпусе. По общей площади выбирают форму здания в плане. При этом стремятся чтобы периметр стен был возможно наименьшим при одной и гой же площади здания: это сведет к минимуму затрат на строительство.
Обычно здания ремонтных предприятий проектируют прямоугольной формы. Соотношение между длиной и шириной здания во многом определяется номенклатурой ремонтируемых объектов производственной программой и выбранной схемой технологического процесса (обычно соотношение длины здания к его ширине принимают равным 15). На специализированных предприятиях по ремонту автомобилей факторов или их агрегатов в зависимости от пути движения рамы машины или базовой детали (предприятия по ремонту агрегатов) принимают следующие варианты схем технологического процесса: прямоточную Г-образную и П - образную.
Прямоточная схема технологического процесса отличается простотой. При прямом потоке удобны организация конвейерных линий и последовательное расположение производственных и вспомогательных подразделений по ходу технологического процесса. При такой схеме наиболее тяжелые и громоздкие детали (рамы кузова) движутся по прямому пути на этой же линии располагают разборочно-моечные комплектовочные и сборочные участки. Участки по ремонту кузовов и тугих агрегатов располагают с одной стороны потока а участки по восстановлению и изготовлению деталей - с другой стороны. Недостаток этой схемы состоит в том что при полнокомплектном ремонте машин .aero суммарные площади основных групп производственных подразделений разборочно-моечных кузовных по восстановлению и изготовлению деталей и других не соответствуют между собой.
В этом случае приходится отдельные производственные участки переносить из одной группы в другую. Кроме того при прямоточной схеме затруднена изоляция разборочно-сборочных работ от других участков.
Г - образная или П - образная схема технологического процесса позволяет изолировать разборочно-моечные отделения (участки) от других производственных участков более рационально расположить отдельные группы производственных участков и сократить пути транспортирования грузов. Недостатки этих схем: непрямолинейное перемещение конвейера а также затрудненное размещение отдельных подразделений.
При П - образном потоке производственные отделения (участки) охватывают разборочно-моечные и сборочные участки.
Размещение основных служб по П - образной схеме потока целесообразно и большом объеме производства когда оправдывают себя удлиненные пиши разборки и сборки.
ОПРЕДЕЛЕНИЕ ГАБАРИТОВ ЗДАНИЯ.
По общей площади после бора схемы определяют габариты производственного корпуса. Основой ли определения длины и ширины корпуса служат длина поточных линий разборки и сборки шаг колонн размеры и расположение площадки под строительство. В соответствии с положениями по унификации и габаритными схемами разработанными и утвержденными ДСТУ для производственных зданий промышленных предприятий габаритную схему производственного корпуса выбирают в зависимости от подъемно-транспортного оборудования и вида ремонтируемых объектов.
Окончательно габариты корпуса определяют исходя из максимальных размеров ремонтируемых объектов принятого технологического и санитарно-технического оборудования. В каждом конкретном случае ширина и высота должны быть обоснованы расчетом по вертикальному разрезу здания.
Размеры въездных и выездных ворот для ремонтных предприятий качают в зависимости от габаритов ремонтируемых объектов. Ширину ворот принимают на 06 м больше ширины ремонтируемого объекта а высоту - на 02 м больше высоты объекта.
Для определения длины производственного корпуса его суммарную расчетную площадь увеличивают на 10 15% чтобы учесть магистральные межцеховые проезды предназначенные для перевозок грузов механизированным транспортом (электрокары электропогрузчики и др.).
КОМПОНОВКА ПОДРАЗДЕЛЕНИЙ ПРОИЗВОДСТВЕННОГО КОРПУСА.
Участки на плане производственного корпуса разметают так чтобы ремонтируемые агрегаты и отдельные громоздкие делили можно было перемещать по наикратчайшему пути а взаимосвязь разборочно-сборочных участков и участков по восстановлению деталей соответствовала ходу технологического процесса и направлению основного грузопотока.
Участки где требуется большое количество воды лучше концентрировать в одном месте.
Согласно противопожарным требованиям огнеопасные (тепловые) участки (сварочный кузнечный и т. д.) рекомендуется располагать группами у наружных стен и изолировать от других помещении огнестойкими стенами.
За основу компоновки подразделений принимают соответствие между схемой технологического процесса ремонта объекта и транспортированием внутрипроизводственных грузов. Направление грузопотока должно совпадать с ходом технологического процесса. Поэтому из анализа действующих ремонтных предприятий аналогичных проектируемому по профилю выявляют откуда в какие подразделения и с какой общей массой необходимо перемещать грузы в процессе ремонта. Часто значения массы транспортируемых грузов выражают в процентах от общей массы ремонтируемого объекта и составляют таблицу распределения грузов по подразделениям предприятия.
Затем строят схему грузопотока в виде соответствующих линий выражающих направление перемещения грузов и их массу изображаемую толщиной этих линий в определенном масштабе.
Для построения графиков грузопотоков выбирают машину той марки по которой объем ремонтных работ в наиболее загруженном месяце максимальный. Линии (или полосы) грузовых потоков показывают движение грузов а их ширина изображает массу в соответствующем масштабе.ширины полосы может быть принят равным 100 200 кгмм.
Ширину полос по участкам берут в процентной отношении от ширины полосы полной массы машины (агрегата) или в принятом масштабе откладывают полосы соответствующие массам грузов поступающих на участки.
Распределение грузопотоков по отделениям предприятия приведено в табл.
Между собой полосы соединяют в соответствии с принятой схемой технологического процесса ремонта объекта; направление движения грузов указывают стрелками. Для выявления лучшего варианта составляют несколько схем грузопотоков и анализируют их. На полосах указываю массу перемещаемых грузов или процент общей массы объекта ремонта.
Подразделения производственного корпуса размещают так чтобы основная масса агрегатов громоздких деталей и других грузов транспортировалась по наикратчайшему пути. Для выявления лучшего варианта составляют несколько схем грузопотока и анализируют их. Оптимальным вариантом компоновки производственного корпуса считают такой в котором достигнуты прямоточность производственного процесса перемещение грузов по кратчайшему пути с наименьшим числом оборотных и перекрещивающихся грузопотоков.
При компоновке трудно обеспечить совпадение расчетных площадей с принятыми поэтому допускается их расхождение в пределах ± 15%.
При вычерчивании компоновочного плана здания с помощью принятых условных обозначений показывают: габаритные размеры зданий ширину пролета и шаг колонн маркировку сетки колонн стены перегородки или границы между участками подъемно-транспортные средства дверные и оконные проемы а также линию основного потока т. е. проведения разборочно-сборочных работ с объектами ремонта и рабочими местами находящимися на линии.
В правом углу листа показывают направление господствующих ветров по отношению к которому производственный корпус располагают так чтобы пожароопасные участки и участки с вредными выделениями находились с подветренной стороны.
Все элементы зданий изображают в соответствии с принятыми условными обозначениями.
При любой схеме потока испытательную станцию целесообразно размещать рядом с отделением сборки двигателей а инструментального паточную кладовую - недалеко от слесарно-механического отделения. Контрольно-сортировочное отделение склад запасных частей и материалов и комплектовочное отделение также следует располагать в одном месте. Аналогично компонуют и другие взаимосвязанные подразделения.
Производственные подразделения предприятия не рекомендуется разделять перегородками если это не оговорено правилами техники безопасности и пожарной безопасности. В здании корпуса рекомендуется предусматривать несколько взаимно перпендикулярных магистральных проездов причем желательно иметь их сквозными. Количество и расположение магистральных проездов определяются размерами и компоновкой корпуса а также технологическими связями с подразделениями предприятия. На проездах не должны размещаться перегрузочные платформы на рельсовом пути - тележки и другие транспортные устройства для транспортирования громоздких и тяжелых деталей. Ширину магистральных проездов устанавливают в зависимости ч вида и количества механизированного транспорта. На ремонтных предприятиях где имеется до 5 транспортных единиц (электрокары электропогрузчики) принимают магистральные проезды с односторонним движением шириной 30 35 м.
Производственные корпуса специализированных предприятий обычно проектируют одноэтажными многопролетными но часто административно-бытовые помещения располагают в специальных пристройках в несколько этажей. Иногда эти помещения размещают на втором этаже производственного корпуса.
НАЗНАЧЕНИЕ КОНСТРУКТИВНЫЕ ОСОБЕННОСТИ И УСЛОВИЯ РАБОТЫ ДЕТАЛИ В УЗЛЕ
Шкив коленчатого вала предназначен для передачи крутящего момента от коленчатого вала к генератору и водяному насосу с вентилятором при помощи первого ремня и к насосу гидроусилителя и водяному насосу с вентилятором при помощи второго ремня. Для этого на шкиве имеется два ручья для двух ремней.
Для передачи крутящего момента от коленчатого вала к шкиву имеется элемент шпоночного соединения в виде продольного паза длинной 84мм и глубиной 26мм.
Диаметр посадочного отверстия на шейку коленчатого вала 46 +0027 мм.
Шкив основное время работы находится под действием инерционных нагрузок и нагрузки от натяжения приводных ремней.
ТЕХНИЧЕСКИЕ УСЛОВИЯ НА КОНТРОЛЬ-СОРТИРОВКУ
Деталь: Шкив коленчатого вала
Обломы и трещины кроме указанных в п. 2
Способ установления дефекта и измерительные инструменты
допустимый для ремонта
Обломы и тещины на краях бортов
Риски задиры или износ шейки под сальник
не более 50 по длине окруж1ности
Ремонтировать. Наплавка. Браковать при обломах и трещинах более 50мм по длине окружности
Износ отверстия под шейку коленчатого вала
Скоба 6180 мм или штангенциркуль
80при отсутствии рисок и задиров
менее 61180 или при наличии рисок и задиров
Ремонтирова1ть. Шлифование «как чисто» до размера 6180мм. При размере менее 6180мм вибродуговая наплавка постановка втулки или металлизация.
Износ паза под шпонку
или нутромер индикаторный 35-50 мм
Ремонтировать. Вибродуговая наплавка
Износ рабочих поверхностей канавок1 шкива
Ремонтировать. Изготовление паза под шпонку номинального размера под углом 1180° к старому.
Износ рабочих поверхностей канавок шкива
Контроль по роликам 20мм. Штангенциркуль
Браковать при размере менее 20365мм
ОБОСНОВАНИЕ МАРШРУТА ВОССТАНОВЛЕНИЯ
Проведенными исследованиями деталей поступающих в капитальный ремонт нами выявлено что наиболее часто встречающимися в действительном сочетании являются:
а) риски задиры и износ шейки коленчатого вала под сальник;
б) износ отверстия под шейку коленчатого вала;
в) износ паза под шпонку.
Такие сочетания дефектов очень характерны для деталей этого вида и класса.
Выбор способа восстановления
Определив наиболее характерные дефекты окончательно выбираем рациональный способ для каждого из принятых дефектов.
Для восстановления шейки под сальник выбираем способ ремонтных размеров. В качестве механической обработки принимаем шлифование «как чисто». При этом способе ремонта восстанавливается правильность геометрической формы и шероховатость поверхности детали. Восстановление деталей под ремонтный размер является широко распространенным и общедоступным способом и наиболее дешевым по сравнению с другими способами.
Для восстановления отверстия под шейку коленчатого вала выбираем способ вибродуговой наплавки. Преимуществами вибродуговой наплавки в жидкости являются отсутствие нагрева и деформации детали незначительная величина зоны термического влияния меньшее выгорание углерода по сравнению с наплавкой в атмосфере воздуха или его потоке. Механической обработкой наплавленной поверхности является шлифование: первоначально грубое (обдирочное) затем чистовое под требуемый размер.
Паз под шпонку восстанавливается одновременно отверстием под шейку коленчатого вала. Так что паз в принципе придётся не восстанавливать а изготавливать заново. Изготавливать шпоночный паз будем протягиванием. Разработаем технологический процесс восстановления. Он будет состоять из следующих операций:
Операция 05 – слесарная: зачистка установочной базы очистка от жировых пятен и т.д.;
Операция 10 – шлифовальная: шлифовка шейки под сальник до устранения следов износа (до 6180мм);
Операция 15 – наплавочная: наплавить отверстие под шейку коленчатого вала до 42мм;
Операция 20 – токарная: обточка наплавленного отверстия до 46+0027мм;
Операция 25 – протяжная: протяжка шпоночного паза 6+00656+0015 мм;
Операция 30 – слесарная: очистка шкива;
Операция 35 – контрольная: контроль размеров 62 – 020 46 +0027 6 +0065 +0015
УСТАНОВЛЕНИЕ ТЕХНОЛОГИЧЕСКОЙ ПОСЛЕДОВАТЕЛЬНОСТИ ОПЕРАЦИЙ
С целью обеспечения выполнения технологического процесса ремонта детали нам необходимо обеспечить оборудованием соответствующий участок (это может быть линия централизованного восстановления шкивов коленчатого вала или что ни будь другое).
Операции 05 и 30 – слесарные: для выполнения этих операций нам необходимо иметь верстак слесарный напильник круглый ветошь бачок с бензином металлическая щетка.
Операция 10 – шлифовальная. Для шлифования наружного диаметра выбираем круглошлифовальный станок мод. 3М161.
Установка шкива осуществляется в трехкулачковом патроне в разжим с базированием по торцу. Шлифование производится шлифовальным кругом ПП 1502540 марки Э46СМ1К5 35мс 2кл. ГОСТ 2424–83.
В качестве измерительного инструмента используем калибр скобы на 6180 ГОСТ 2216–84.
Операция 15 – наплавочная. Восстановление посадочного отверстия под шейку коленчатого вала производится вибродуговой наплавкой на установке 4АНН–1–6НИИАТ в потоке воздуха до 49мм плотным круговым швом проволокой 16мм Св–15ГСТЮЦ ГОСТ 10543–75.
В качестве источников питания дуги применяют агрегат типа АНД 1500750 в комплект которого входят: наплавочная головка УАНЖ–6 конструкции НИИАТ токарный станок мод. 16К50П т.к. он обеспечивает число оборотов от 25 до 800 обмин.
Операция 20 – токарная. Для выполнения данной операции выбираем токарно–винторезный станок мод.16К25 предназначенный для выполнения различных токарных работ. Благодаря своей высокой быстроходности (1600 мин –1) и мощности (10 кВт) станок позволяет выполнить работы быстро и в полном объеме с использованием режущих инструментов оснащенных пластинками из твердых сплавов. Установка детали осуществляется в трехкулачковом патроне в разжим с базированием по торцу. Выбираем расточной резец для обработки сквозных отверстий с пластинкой из твердого сплава ВК6 позволяющий получить требуемую шероховатость и обеспечить нужную точность обработки.
В качестве измерительного инструмента выбираем штангенциркуль ШЦ–I ГОСТ 166–80.
Операция 25 – протяжная. Для выполнения данной операции выбираем протяжной станок для внутреннего протягивания мод.7505.
Операция 30 – контрольная. Здесь необходим стол ОТК и измерительные инструменты:
–штангенциркуль ШЦ–I ГОСТ 166–80
–скобы на 6180 ГОСТ 2216–84
РАСЧЕТ РЕЖИМОВ МЕХАНИЧЕСКОЙ ОБРАБОТКИ И ТЕХНИЧЕСКОЕ НОРМИРОВАНИЕ ОПЕРАЦИЙ ВОССТАНОВЛЕНИЯ
Операция 10 – шлифовальная.
Поперечную подачу (глубину шлифования) определяем из табл.IV.3.88[4]
Продольная подача на один оборот обрабатываемой детали принимается в долях ширины шлифовального круга стр.367 [4]
S = b×B = 0.45×25 = 11.25 ммоб.)
где B=25мм – ширина шлифовального круга;
b=045 – коэф. определяющий долю ширины шлифовального круга; принимается из табл. IV.3.90[4].
Скорость вращения обрабатываемой детали определяется по эмпирической формуле стр.367 [4]
где CV = 024 – величина зависящая от обрабатываемого материала;
d – диаметр обрабатываемой поверхности;
T – стойкость шлифовального круга;
t – глубина шлифования;
b – коэф. продольной подачи.
Значения коэф. CV и показателей степени k m xv yv приводятся в табл. IV.3.92 – IV.3.94 [4]
При этой скорости число оборотов детали равно стр.370 [4]
Определим мощность необходимую на шлифование по формуле стр. 370[4]
Основное время определяется по следующей формуле стр. 370 [4].
При поперечной подаче на двойной ход стола
где – длина хода стола;
h = 008мм – припуск на обработку;
t – поперечная подача;
К = 15 – коэф. зависящий от точности шлифования и износа круга.
Определяем подготовительно–заключительное время в таблице IV.3.9 [4]
Определяем вспомогательное время стр.370[4]
tВ= tС.У+ tВ.П.=034+025=059мин.
а) вспомогательное время на установку и снятие детали по таблице в таблице IV.3.58 4]
б) вспомогательное время связанное с обработкой одной поверхности по таблице IV.3.97 [4]
Определяем оперативное время стр.370[4]
tОП = tО+ tВ=038+059=097мин.
Время обслуживания рабочего места и на естественные надобности исполнителя определяем по табл. IV.3.62 [4]
tо.р.м.=007× tОП=007×097=007мин.)
Определяем норму штучного времени стр. 370[4]
Tш.т.= tОП + tо.р.м = 097 + 007 = 104мин » 11мин.
Операция 15 – наплавочная.
Наплавить отверстие. Наплавка ведется в один слой толщиной t = 15мм длина наплавки равна 80мм и диаметр наплавляемого отверстия (после наплавки) 43мм. Диаметр электродной проволоки выбираем равной 16мм.
Плотность тока согласно рис. IV.3.3[4] принимаем DA = 85 Амм2 коэффициент наплавки aн = 75 гА×ч.
Сила сварочного тока стр.313[4]
I = 0785×d2× DA =0785×162×85=170 А.
Масса расплавленного металла стр.314 [4]
Gр.м. = I×aн = 170×7560= 2125 гмин.
Скорость подачи электродной проволоки определяется по эмпирической формуле стр.314 [4]
где: b =755 – плотность расплавленного метала.
Скорость наплавки определяется по эмпирической формуле стр.314 [4]
где K – коэф. перехода метала на наплавленную поверхность;
a – коэф. неполноты наплавленного слоя;
t – толщина наплавленного слоя;
S = 2×d = 32 – подача на один оборот детали (шаг наплавки).
Значения коэф. K и a приводятся в табл. IV.3.7 [4].
Частота вращения стр.314 [4]
Основное время определяется по следующей формуле стр. 316 [4]
для наплавки тел вращения
где: – длина хода стола;
– количество слоев наплавки;
Определяем подготовительно–заключительное время в таб. IV.3.8 [4]
Определяем вспомогательное время таб. IV.3.9 [4]
Определяем оперативное время стр.316[4]
tОП = tО+ tВ=862+038=9 мин.
Время обслуживания рабочего места и на естественные надобности исполнителя определяем стр.316 [4]
tо.р.м.=015× tОП=9×097=997 мин.
Определяем норму штучного времени стр. 370 [4]
Tш.т.= tОП + tо.р.м = 9 + 997 = 1897 мин » 19 мин.
Операция 20 – токарная.
Переход 1: черновое растачивание.
Глубину резания определяем исходя из того чтобы весь припуск снять за один проход
Подача выбираем по нормативам согласно табл. IV.3.47– IV.3.53 [4]
Скорость резания определяется по эмпирической формуле стр.342 [4]
где CV = 68 – коэф. зависящий от условий работы;
К = 12 – поправочный коэф. характериз. конкретные условия работы;
t – глубина резания;
Значения коэф. CV и показателей степени приводятся в табл. IV.3.54 – IV.3.55 [4].
При этой скорости число оборотов детали равно стр.342 [4]
Расчетная длинна прохода по формуле стр. 342[4]
L = l + l1 + l2 = 80+2+2=84 мм.
l2 =2мм – длина перебега.
Основное время определяется по следующей формуле стр. 370 [4]
где: – число проходов.
Определяем подготовительно – заключительное время в таблице IV.3.57 [4]
Определяем вспомогательное время стр.341[4]
tВ= tС.У+ tВ.П.=034+025=059 мин.
б) вспомогательное время связанное с обработкой одной поверхности по таблице IV.3.59 [4]
tОП = tО+ tВ=021+059=08 мин.
tо.р.м.=007× tОП=007×08=006 мин.
Tш.т.= tОП + tо.р.м = 08 + 006 = 086мин » 1мин.
Переход 2: чистовое растачивание.
где CV = 77 – коэф. зависящий от условий работы;
где – число проходов.
а) вспомогательное время на установку и снятие детали по таблице в таблице IV.3.58 [4]
tОП = tО+ tВ=074+059=133 мин.
tо.р.м.=007× tОП=007×133=009 мин.
Tш.т.= tОП + tо.р.м = 133 + 009 = 142мин » 15 мин.
ПРОЕКТИРОВАНИЕ СТАНОЧНОГО ПРИСПОСОБЛЕНИЯ
Проектируемое приспособление предназначено для установки и закрепления шкива коленчатого вала при выполнении операций технологического процесса восстановления шкива двигателя автомобиля УРАЛ-4320
Приспособление (рис.1) применяется при фрезеровании плоскости и предназначено для базирования детали (рис.2). Деталь базируется внешней цилиндрической поверхностью (двойная направляющая база: опорные точки 1 2 3 4) плоскостью (опорная база: опорная точка 5) и закрепляется двумя силами одновременно. После зажима заготовка фиксируется скрытой базой (опорная точка 6).
Рис. 1 - Схема приспособления
Рис. 2 - Схема базирования детали
В приспособлении деталь двойной направляющей базой устанавливается в призмы 1 опорной базой – на опорный элемент 2. Во время движения штока 3 клин 4 перемещается вверх а толкатель 5 влево. Толкатель 5 при помощи двух рычагов 6 связан кинематически с ползунами 7 на которых закреплены призмы 1. Таким образом осуществляется одновременное перемещение двух призм к детали ее центрирование и закрепление. Раскрепление осуществляется за счет сжимания пружин 8.
В проектируемом приспособлении целесообразно использовать пневматический привод прямого действия с пневмоцилиндром двухстороннего действия вместо механического по соображениям: компактность простота большее зажимное усилие сокращение вспомогательного времени надежность.
ОХРАНА ТРУДА И ПРОИЗВОДСТВЕННАЯ САНИТАРИЯ
Создание безопасных условий труда в производственных помещениях АРП требует предусматривать создание местного отсоса вредных газов и пыли проточно – вытяжную вентиляцию тепловые завесы.
Уровень низкочастотных шумов на АРП не должен превышать 90 дб. Движущиеся части технологического оборудования необходимо ограждать кожухами.
Температура воздуха в производственных помещениях должна быть не менее 16 *С при относительной влажности 75 – 80 %. Скорость движения воздуха вызванная вентиляцией не должна превышать 0.3 мс.
Для защиты рабочих от поражения электрическим током корпуса оборудования имеющие электропривод обязательно заземляются.
Переносное освещение используемое на АРП должно питаться от понижающего трансформатора на 36 В а подсветка смотровых канав не более 12В.
РАСЧЕТ ОТОПЛЕНИЯ ПРОИЗВОДСТВЕННОГО КОРПУСА АРП
Для производственного корпуса зоны ТО и ТР проектируется водяное отопление расчет которого ведется по укрупненным показателям и сводится к определению годового расхода топлива количества отопительных приборов и выбору котла.
Расчет годового расхода топлива:
Gут (кг) условного топлива необходимого для обогрева АРП в течении года
Gут=44928*778=3495398 кг
Vн – объем здания по наружному обмеру м3
g – годовая норма расхода топлива кгм3
По установленным нормам на отопление станций технического обслуживания g=778 кгм3.
Более точно годовой расход условного топлива Gу.т.(кг) находят по формуле:
Gу.т.=24dQм(tв-tср)*1157000 э*(tв-tм)
Gу.т.=24*180*4178304*(18-15)*1157000*06(18-15)=1317956 кг
где d – число дней отопительного сезона
Qм – максимальный часовой расход тепла для отопления и вентиляции помещения кДжч
tв – внутренняя температура помещения
tср – средняя за отопительный сезон температура наружного воздуха
э –к.п.д. котельной установки (э=0.6)
tм – минимальная наружная температура во время отопительного периода
Максимальный часовой расход тепла Qм (кДжч) необходимый для отопления и вентиляции помещения определяется по формуле:
Qм= Vн(go+gв) *(tв-tм)
Qм= 44928*(22+09)*(18-15)=4178304 кДжч
где Vн – объем здания по наружнему обмеру
go и gв - удельный расход тепла на отопление и вентиляцию при разнице внутренней и наружней температур в 1 0С
(go =1.9 – 2.3кДжч*м3*0 Сgв=0.62 – 1.04 кДжч*м3*0 С)
Годовой расход натурального топлива Gн.т. (Т) подсчитывают пользуясь выражением
Gн.т. = Gу.р.* н 1000
Gн.т. = 13179564*021000=2635 Т
где н – коэффициент перевода условного топлива в натуральное.
Для большинства цехов и отделений tв=15-16 0 С для механического отделения а также для отделения по ремонту топливной аппаратуры гидравлики и электрооборудования tв=20 0 С.
Значения tм и tср число дней отопительного сезона берут из справочников (климатограмм для данной местности).
Площадь нагревательных приборов (Fн ) определяют по формуле:
Fн=417830431*(80-18)=21739 м2
где Кн – коэффициент теплоотдачи равный для ребристых труб 3.1 кДжч*м3* 0С;
tср – средняя расчетная температура воды в приборе
( примерно – 80 0С );
tв – внутренняя температура помещений 0С.
Количество нагревательных приборов определяется из выражения:
где F1 – поверхность нагрева одного нагревательного прибора м2 для ребристых труб F1=4м2.
Количество нагревательных приборов на участке (отделении) уч находится пропорционально объему участков по отношению к общему объему здания из выражения:
где Vу - объем участка м3 ;
Vv – общий объем здания м3;
Поверхность нагрева котла Fк (м2) определяют по формуле
где Кк – коэффициент учитывающий теплопотери котла и трубопроводов (Кк=1.1 – 1.2);
К0 – теплоотдача 1 м2 поверхности котла Джч*м2.
Тип и марку котла подбираем по справочнику.
РАСЧЕТ ВЕНТИЛЯЦИИ ПРОИЗВОДСТВЕННОГО КОРПУСА
Для жизнедеятельности человека большое значение имеет качество воздуха. От него зависит самочувствие работоспособность и в конечном счёте здоровье человека. Качество воздуха определяется его химическим составом физическими свойствами а также наличием в нём посторонних частиц.
Воздух рабочей зоны редко имеет требуемый химический состав так как многие технологические процессы сопровождаются выделением в воздух производственных помещений вредных веществ - паров газов твердых и жидких частиц. Влияние этих и других вредных веществ может пагубно сказаться на здоровье работающих. С целью снижения (ликвидации) содержания вредных веществ в воздухе производственных помещений разрабатывается вентиляция – организованный воздухообмен. Вентиляция достигается удалением загрязненного или нагретого воздуха из помещения.
Задачей вентиляции является обеспечение чистоты воздуха и заданных метеорологических условий в производственных помещениях.
По способу перемещения воздуха вентиляция бывает с естественным побуждением (естественной) и с механическим (механической). Возможно также сочетание естественной и механической вентиляции (смешанная вентиляция).
В зависимости от того для чего служит система вентиляции— для подачи (притока) или удаления (вытяжки) воздуха из помещения или (и) для того и другого одновременно она называется приточной вытяжной или приточно-вытяжной.
По месту действия вентиляция бывает общеобменной и местной. Действие общеобменной вентиляции основано па разбавлении загрязненного нагретого влажного воздуха помещения свежим воздухом до предельно допустимых норм. Эту систему вентиляции наиболее часто применяют в случаях когда вредные вещества теплота влага выделяются равномерно по всему помещению. При такой вентиляции обеспечивается поддержание необходимых параметров воздушной среды во всем объёме помещения..
Требования к воздуху рабочей зоны на территории Украины регламентированы следующими документами:
-ГОСТ 12.1.005-88. ССБТ. Общие санитарно-гигиенические требования к воздуху рабочей зоны.
-ДСН 3.6.042-99 «Сан-СНиП 2.04.05-91. Отопление вентиляция и кондиционирование.
Естественная вентиляция. По нормам промышленного строительства все помещения должны иметь сквозное естественное проветривание. Площадь критического сечения фрамуг или форточек берется в размере 2 – 4 % от площади пола.
Искусственная вентиляция. Искусственная вентиляция должна применяться в помещениях где часовая кратность воздухообмена установлена более трех (медницкий кузнечно-сварочный ремонта топливной аппаратуры моечный ремонта электрооборудования).
В зависимости от характера производственного процесса выбирают вид вентиляции. При этом руководствуются следующими положениями: общеобменную механическую вентиляцию проектируют в помещениях без выделения пыли газов паров и др.общеобменная вентиляция может быть проточной и вытяжной..
Принимаем значение часовой кратности воздухообмена (к) и рассчитываем величину воздухообмена Lв м3ч по формуле:
Lв=44928*4=179712 м3ч
где Vп – объем помещения м3;
К = 4-6 – часовая кратность воздухообмена.
После определения количества воздуха сравниваем полученные данные с установленными нормами.
Так в производственных помещениях с объемом на одного работающего менее 20 м3 следует проектировать подачу наружного воздуха в количестве не менее 30 м3ч на каждого работающего а в помещениях с объемом на каждого работающего более 20 м3 – не менее 20 м3ч. Если объем помещения на каждого работающего более 40м3 то предусматривается только естественная вентиляция. Так как в нашем случае объем помещения производственного корпуса на каждого работающего составляет 100 м3 то нет необходимости в расчете искусственной вентиляции и предусматривается только естественная вентиляция.
Местная вентиляция. При проектировании местной (локализующей) вентиляции выбирают ее тип (зонт вытяжной шкаф бортовой отсос) исходя из особенностей источника вредных выделений и обслуживания рабочего места.
При проектировании вытяжного зонта приводится схема его размещения над рабочим местом и указываются следующие размеры:
Н – расстояние от поверхности рабочего места до приемной части зонта равное 0.5 – 0.8 м;
h – длина оборудования м;
А – длина приемной части зонта м;
Определяем часовой объем вытяжки (Lз м3ч) загрязненного воздуха через зонт по формуле:
Lз =07*32*3600=8064
где з – средняя скорость воздуха в приемной части зонта мс;
F – площадь приемной части зонта м2.
. Площадь приемной части зонта:
F=(0.8H+h)*(0.8H+b)
F=(08*07+15)*(08*07+1)=321
где b – ширина оборудования м..
По рассчитанной модели выбирают номер тип напор и К.П.Д. вентилятора зонта и определяют мощность электродвигателя для его привода.
Рис 1. Схема вытяжного зонта над рабочим местом
-зонт 2-оборудование
Определение выделения избыточного тепла в цехе
Теплоотдача от оборудования.
- мощность электродвигателей Nуст - 480 кВт
- коэффициент загрузки α = 08
Q1 = 860*0.8*480(1-0.7)0.7 = 1415315 ккалчас;
Тепловыделение от людей.
По тяжести труда работам в термическом цехе присвоена категория IIa
следовательно тепловыделения одного человека находятся в пределах
0-200 ккалчас. Примем 175.
Тепловыделения от солнечной радиации
Тепловая энергия солнечных лучей поступает в помещение через остекленные поверхности - окна. Таким образом она зависит от площади остекления:
Aocm - коэф. учитывающий загрязнение стекол = 075;
Focm - площадь остекленных поверхностей в помещении;
qocm = 150 ккалм2 час;
Общие тепловыделения составляют:
Расход приточного воздуха
G = Q0.24(tyx - tnp)
где: Qизб – теплоизбытки в помещении ккалч;
tyx и tnp - температура удаляемого и приточного воздуха С.
Температуру наружного воздуха в теплый период года принимают равной средней температуре самого жаркого месяца в 13 ч. Допустимое значение параметра воздуха в производственных помещениях для категории работ средней тяжести (IIа) – не более чем на 3 С выше температуры наружного воздуха но не более 28 С.
Объем воздуха (м3 ч) отсасываемого от каждой оборудования от которого выделяется значительное количество тепла: L1 = F*v*3600
где F - площадь сечения трубы местного отсоса – 05024 м2;
v - скорость движения удаляемого воздуха в этом отверстии – 7 мс;
L1 = 05024×7×3600 = 12 660(м3 ч);
Общий объем воздуха удаляемый местной вытяжкой составляет:
РАСЧЕТ ОСВЕЩЕНИЯ ПРОИЗВОДСТВЕННЫХ ПОМЕЩЕНИЙ.
Одним из основных вопросов охраны труда является организация рационального освещения производственных помещений и рабочих мест.
Правильно спроектированное и выполненное производственное освещение улучшает условия зрительной работы снижает утомляемость способствует повышению производительности труда благотворно влияет на производственную среду оказывает положительное психологическое воздействие на рабочего повышает безопасность труда и снижает травматизм.
Значение освещения в процессе жизнедеятельности и особенно в производственной деятельности велико. При неудовлетворительном освещении зрительная способность глаз снижается и могут появиться такие заболевания как близорукость резь в глазах катаракта нистагм (профессиональное заболевание). Правильно выполненная система освещения имеет большое значение в снижении производственного травматизма уменьшая потенциальную опасность многих производственных факторов; создаёт нормальные условия для работы органам зрения и повышает общую работоспособность организма. Освещение можно назвать рациональным если оно является экономичным и учитывает свойства и способности глаз работников.
В зависимости от источника света освещение может быть естественным (создаётся солнечным диском и диффузным светом небосвода) искусственным (создаётся электрическими лампами) и совмещённым (естественное и искусственное одновременно).
Решение вопроса рационального освещения производственных помещений и рабочих мест улучшает условия зрительной работы ослабляет зрительное и нервное утомление способствует повышению внимания и улучшению координационной деятельности. Хорошее освещение усиливает деятельность дыхательных органов способствуя увеличению поглощения кислорода.
Напряжённая зрительная работа вследствие нерационального освещения может явиться причиной функциональных нарушений в зрительном анализаторе и привести к расстройству зрения а в тяжёлых случаях и к полной его потере.
Для освещения производственных помещений используется освещение трёх видов: естественное обусловленное энергией Солнца и рассеянного света небосвода; искусственное осуществляемое электрическими лампами и смешанное т. е. сочетание естественного и искусственного освещения.
Естественное освещение характеризуется тем что меняется в широких пределах в зависимости от времени дня времени года характера области и ряда других факторов.
Искусственное освещение по функциональному назначению подразделяется на следующие виды: рабочее аварийное эвакуационное и охранное.
Рабочее освещение обеспечивает минимально необходимые осветительные условия при нормальном режиме работы осветительных установок.
Аварийное освещение обеспечивает минимально необходимые осветительные условия для продолжения работы при временном выходе из строя рабочего освещения.
Эвакуационное освещение служит для эвакуации людей из помещений при авариях рабочего освещения в местах опасных для прохода людей на лестницах и по основным проходам производственных помещений.
Охранное освещение (при отсутствии специальных технических средств охраны) должно предусматриваться вдоль границ территорий охраняемых в ночное время.
Искусственное рабочее освещение промышленных предприятий осуществляется с помощью двух систем: Общего освещения и комбинированного освещения т.е. совокупности местного и общего освещения.
Проектирование освещения ведется в соответствии со строительными нормами и правилами.
При проектировании расчете освещения производственных помещений необходимо учитывать следующие основные требования:
- освещение должно быть достаточным чтобы рабочий мог легко и быстро оперировать с объектами работы;
- освещение не должно вызывать резких теней и сменяющихся бликов;
- устройство освещения должно выполняться с учетом характера производства.
Большое значение для создания нормальных зрительных условий имеет расположение источников света относительно рабочего места.
Расчет естественного освещения. При проектировании новых АРП расчет естественного освещения цехов и участков сводится к определению размеров окон и их количества для каждого отделения или всего помещения.
Выбираем тип естественного освещения с учетом расположения участков в здании: затенения окон зданиями и сооружениями расположенными рядом высоты помещений размеров производственного корпуса и др.
Учитывая частичное затенение окон проектируемого помещения рядом стоящими зданиями а также для отделений расположенных в центральной части здания выбираем комбинированное освещение (через световые фонари на крыше и через окна).
Рассчитываем суммарную площадь световых проемов согласно выбранному типу освещения по следующей формуле:
Sб=Sп*еср*0 1000 rзК
где Sб – суммарная площадь окон и фонарей м2;
Sп - площадь пола помещения м2;
еср – нормированное среднее значение е при комбинированном освещении
– общий коэффициент светопропускания 0 = 0.6;
rз – коэффициент учитывающий влияние отраженного света rз =2.4;
– световая характеристика окна 0 =10.0
К – коэффициент учитывающий затенение окон противостоящими зданиями К=1
Sб=Sп*еср*0 1000 rзК=36*24*12*20100*035*17*1=3485
После выбора типа естественного освещения и определения суммарной площади световых проемов необходимо для боковых проемов рассчитать высоту окон и их количество.
Расчет высоты окна h0 ведется по формуле
где hпод – расстояние от пола до подоконника равное 0.6 – 1.2 м;
hнад – размер надоконного пространства равный 0.3 – 0.5 м;
Н – высота стен здания Н=52 м.
h0=Н-(hпод+hнад)=52 –(02+08)=42
Рис.2 Схема к определению размеров А и Б:
А- расстояние между проектируемым 2 и противостоящим зданием М;
Б - высота расположения карниза над подоконником
Рис. 3 Схема для определения размеров окна 1-зонт 2-оборудование
Принимаем ближайшее стандартное значение h0 =2500 мм. Ширину окна выбираем в зависимости от его высоты и конструктивных размеров помещения и принимаем равной 1555 мм.
Число окон в помещении исходя из выбранных размеров определяем по формуле:
пок=3485387=9005 м2
где Sок – площадь одного окна м2 Sок=387 м2
Σ Sф – суммарная площадь остекления фонарей Σ Sф = hф* Lф здесь hф – высота остекления фонарей характеризующаяся расстоянием между нижней кромкой остекления начиная от рабочей плоскости оборудования и верхней кромкой остекления определяемой линией О – О (рис 2) проходящей через верхнюю точку О оборудования расположенного на расстоянии 4h от оси здания и через
точку d нижней части фонаря.
hф=в2*tgα=62*tg35=3*074=22
Длину фонаря выберем Lф=24 м
Тогда суммарная площадь остекления фонарей
Σ Sф = hф* Lф=22*12=264 м2.
Рис. 4 Схема к определению размеров фонаря
Расчет искусственного освещения. Искусственное освещение – освещение помещения электрическими лампами различных конструкций обеспечивающих достаточную предусмотренную нормами освещенность рабочих мест. Искусственное освещение может быть общим местным комбинированным и специальным. При проектировании АРП выбирается напряжение осветительной сети. Согласно правилам эксплуатации и установок в осветительных сетях для местного освещения и ручных переносных ламп применяется напряжение 12 и 36 В и для общего освещения 380220 В.
Расчет искусственного освещения будем проводить по световому потоку который сводится к определению необходимого светового потока освещения участка или отделения и мощности ламп.
Расчет ведем в следующей последовательности:
Выбираем значение освещенности Е и систему освещения в зависимости от характера работ на участке или отделении.
При этом учитывая что система освещения может быть :
- общей – обязательна для всех производственных и бытовых помещений;.
- местной – на рабочих местах;
- комбинированной то есть сочетать в себе общее и местное освещение.
Подбираем тип светильника в соответствии с характером выполняемых работ.
Выбираем и чертим схему размещения светильников по участку или отделению в зависимости от расположения оборудования и с учетом максимальной освещенности рабочих мест (рис.3). Целесообразнее всего выбрать размещение светильников шахматное по квадрату т.к. помещение имеет фермы колонны и другие устройства
Вычерчиваем схему (рис. 4) и рассчитываем высоту подвеса светильника по формуле:
где Н – высота помещения м;
hр – рабочая высота оборудования м;
hс – расстояние от светильника до потолка равное (0.2-0.25м).
Нп=Н-(hр+hс)=52-(12+025)=275
Рис. 5 Схема к определению высоты светильника
Положение светильников выбираем многорядное.
Вначале выбираем отношение LНп в зависимости от принятого типа светильника и схемы их размещения LНп =1.3и определяем расстояние между светильниками Lсв =3.25*1.3=4.23м. Затем пользуясь схемой размещения светильников подсчитываем количество ламп в отделении или цехе при этом световой поток излучаемый каждой лампой находим по формуле:
Рис.6 Схемы размещения светильников
Коэффициент использования осветительной установки
Световые и электрические параметры ламп накаливания (ГОСТ 2239-70)
и люминесцентных ламп (ГОСТ 6825-74).
Люминесцентные лампы
световая отдача лмВт
Из табл. 2.2 по световому потоку выбираем лампы ЛБ 80 световой поток 5220 лм световая отдача 653 лмВт; количество ламп в светильнике = 4.
Световой поток выбранного светильника
Ф1 = 5220*4 = 20880 лм;
Освещённость на рабочем месте цеха:
Ен - необходимая по нормам освещенность лк;
Ф1 – световой поток выбранного светильника лм;
Фо – расчётный световой поток светильника лм.
Е = 180*20880 19874 = 189 лк;
Электрическую мощность всей светильной установки
P1 – мощность выбранной лампы Вт;
N – количество светильников;
n – количество ламп в светильнике.
P = 80*7*4 = 2240 Вт.
Для контроля показаний датчиков на шкафах управления и контроля данных шкал блоков ротаметров предлагаю:
- установить над шкафами управления и над блоками ротаметров светильники местного освещения типа ВЗГ.
- в качестве осветительного элемента использовать лампы накаливания В-25
мощность 25 Вт световой поток 220 лм светоотдача 88 Втлм.
Для определения необходимо рассчитать показания помещения
=36*2442*(36+24)=342
где а-ширина помещения м2
в-длина помещения м2
Выбранный тип светильника:
Люминесцентный с диффузным отражателем
Рис.7 Эскизный чертеж светильника
Светораспределение-прямого света косинусное
Коэффициент усиления-30
Мощность лампы Вт-2х402х80
Защитный угол-15 в поперечной плоскости
Наименьшая высота подвеса-3
ПРОИЗВОДСТВЕННЫЙ ШУМ
Все производственные процессы сопровождаются шумом. Шумом называется - сочетание звуков различной частоты и интенсивности.
Шумом является всякий нежелательный для человека звук. В качестве звука мы воспринимаем упругие колебания распространяющиеся волнообразно в твердой жидкой или газообразной среде. Звуковые волны возникают при нарушении стационарного состояния среды вследствие воздействия на нее какой-либо возмущающей силы. Частицы среды при этом начинают колебаться относительно положения равновесия причем скорость таких колебаний (колебательная скорость v) значительно меньше скорости распространения волны (скорости звука с)
В природе и тем более в работающих машинах механизмах а так же в различных динамических процессах одновременно возникают звуки разной частоты и интенсивности. Такая хаотическая совокупность звуков различной частоты беспорядочно меняющихся по времени называется шумом. В обыденной жизни шумом считается совокупность посторонних звуков мешающих правильно воспринимать речь препятствующих работе и отдыху.
Известно что ряд таких серьезных заболеваний как гипертоническая и язвенная болезни неврозы в ряде случаев желудочно-кишечные и кожные заболевания связаны с перенапряжением нервной системы в процессе труда и отдыха.
Сильный шум вредно отражается на здоровье и работоспособности людей. Человек работая при шуме привыкает к нему но продолжительное действие сильного шума вызывает общее утомление может привести к ухудшению слуха а иногда и к глухоте.
Для уменьшения уровней шума применяются технические строительно-акустические и организационные мероприятия а также средства индивидуальной защиты (ГОСТ 12.4.051-87 - Средства индивидуальной защиты органа слуха).
К этим мерам относятся :
Подавление шума в источниках
а) замена ударных взаимодействий деталей безударными;
б) замена возвратно-поступательных движений вращательными;
в) заменять зубчатые и цепные передачи клиноременными или зубчато-ременными;
г.) применять принудительное смазывание трущихся поверхностей;
д.) применение глушителей шума звукоизолирующих кожухов
Предупреждение распространения шума - звукоизоляция и звукопоглощение.
При звукоизоляции уменьшается уровень шума который распространяется за счет колебания преграды. Для звукоизоляции применяются плотные жесткие массивные перегородки. При этом ослабление зависит от массы перегородки а не от ее материала. Большее ослабление достигается при слоистых перегородках с воздушными промежутками между слоями.
При звукопоглощении звук ослабляется за счет поглощения звуковой энергии в порах материала перегородки (войлок вата пемза). Наряду с пористыми материалами для звукопоглощения применяются специальные мастики которыми покрываются перегородки и отдельные части машин.
Строительные и организационные меры :
а) увеличение расстояния от источника шума - концентрация цехов с большим уровнем шума и удаление их от других производственных помещений.
Так как интенсивность шума в помещениях зависит не только от прямого но и от отраженного звука который может быть уменьшен за счет увеличения площади звукопоглощения помещения т.е. необходимо применять:
б) покрытие внутренних поверхностей помещения звукопоглощающими облицовками;
в) размещение в помещениях штучных звукопоглощателей (объемные тела заполненные звукопоглощающим материалом и подвешенные к потолку);
г) закрытие машин звукоизоляционными кожухами;
д) устройство экранов (с покрытием их звукоизолирующими материалами) между машиной и рабочим местом;
е) устройство звукоизолированных машин;
В данном производственном корпусе при выполнении соответствующих работ свойственных для данного производства необходимо выполнить ряд мероприятий для снижения уровня шума:
- покрыть внутренние поверхности помещения звукопоглощающими облицовками;
- для звукопоглощения применять специальные мастики которыми покрываются перегородки.
Действие его на организм человека связано главным образом с применением нового высокопроизводительного оборудования с механизацией и автоматизацией трудовых процессов: переходом на большие скорости при эксплуатации различных станков и агрегатов. Источниками шума могут быть двигатели насосы компрессоры турбины пневматические и электрические инструменты молоты дробилки станки центрифуги бункеры и прочие установки имеющие движущиеся детали.
Нормируемыми параметрами шума являются уровни звукового давления; октавных полосах со среднегеометрическими частотами
125 250 500 1000 2000 4000 и 8000 Гц
и эквивалентный (по энергии) уровень звука в децибелах (шкала А).
Допустимые уровни шума на рабочих местах не превышают соответственно 110 94 87 81 78 75 73 дБ а по шкале А — 80 дБ. Действие шума на организм человека. Шум - действует в целом на нервную систему человека как общий биологический раздражитель и замедляет ответные реакции снижает внимание что влечет за собой частый травматизм. Наблюдается учащенность пульса дыхания повышение кровеносного давления бессонница понижение работоспособности. Характерны специфические влияния шума на органы слуха приводящие к снижению слуха до полной глухоты.
Однако источниками шума бывают и системы вентиляции после приведенного перерасчета производительность вентиляции увеличилась на 30% при подобном увеличении притока воздуха в системе вентиляции может генерироваться «добавочный» уровень шума. Что может негативно сказаться на общем уровне шума в помещении. Для борьбы с шумом вентиляционных систем используют несколько способов:
-установка вентилятора на виброизолирован мое основание;
- применение эластичной вставки;
- использование глушителей шума:
Как правило максимальный эффект достигается путем комплексного применения указанных способов однако это сопряжено с определенными экономическими затратами. Наиболее дешевым является установка штучных звукопо глотителей. Штучный звукопоглотитель. Расчет необходимого числа штучных звукопоглотшелей. Количество штучных звкопоголатителей определяется по следующей
Ащ - требуемая эквивалентная площадь поглощения зависящая от величины AL = 2дБ определяется по номограмме предположили что увеличение производительности вентиляции повлечет за собой увеличение шума выше нормированного на 2 дБа
Аш - эквивалентная площадь поглощения одним звукопоглотителем =21 м2. таблица 4.26 источника 3.
Таким образом в помещении следует установить 4 звукопоглотителя.
АТТЕСТАЦИЯ РАБОЧИХ МЕСТ ПО УСЛОВИЯМ ТРУДА
В ПРОИЗВОДСТВЕННОМ УЧАСТКЕ
Аттестация рабочих мест по условиям труда (далееаттестация) проводится на предприятиях и в организациях независимо от форм собственности и хозяйствования где технологический процесс используемые оборудование сырье и материалы являются потенциальными источниками вредных и опасных производственных факторов которые могут неблагоприятно влиять на состояние здоровья работающих и их потомство в настоящем и будущем.
Основная цель аттестации состоит в регулировании отношений между собственником или уполномоченным им органом и работниками в области реализации прав на здоровые и безопасные условия труда льготное пенсионное обеспечение льготы и компенсации за работу в неблагоприятных условиях. Аттестация рабочих мест предусматривает:
- установление факторов и причин возникновения неблагоприятных условий труда;
- санитарно-гигиеническое исследование факторов производственной сферы тяжести и напряженности трудового процесса на рабочем месте;
- комплексную оценку факторов производственной среды и характера труда на соответствие их характеристик стандартам безопасности труда строительным и санитарным нормам и правилам;
- установление степени вредности и опасности труда и его характера по гигиенической классификации.
- обоснование отнесения рабочего места к категории с вредными (особо
вредными) тяжелыми (особо тяжелыми) условиями тру да;
- определение (подтверждение) права работников на льготное пенсионное обеспечение за работу в неблагоприятных условиях;
- составление перечня рабочих мест производств профессий и должностей с льготным пенсионным обеспечением работников;
- анализ реализации технических и организационных мероприятий направленных на оптимизацию уровня гигиены характера и безопасности труда.
Для организации и проведения работы по аттестации руководитель предприятия издает приказ в котором:
- указываются основание и задачи аттестации;
- утверждаются состав председатель и секретарь постоянно действующей аттестационной комиссии определяются ее полномочия при необходимости определяется состав цеховых (структурных) аттестационных комиссий;
- устанавливаются сроки и графики проведения подготовительных работ в структурных подразделениях предприятия;
- определяется взаимодействие с заинтересованными государственными органами и общественными организациями (экспертизой условий труда санитарно-эпидемиологической службой);
- определяются проектные научно-исследовательские учреждения для научно-технической оценки условий труда и участия в разработке мероприятий по устранению вредных производственных факторов.
В состав аттестационной комиссии рекомендуется включать главных специалистов работников отделов кадров труда и заработной платы охраны труда органов охраны здоровья предприятия представителей общественных организаций и других.
Изучение факторов производственной среды и трудового процесса
В ходе изучения необходимо определить:
- характерные для конкретного рабочего места производственные факторы подлежащие лабораторным исследованиям;
- нормативные значения (ПДК ПДУ) параметров факторов производственной
среды и трудового процесса используя систему стандартов безопасности труда санитарные нормы и правила другие нормативы;
- фактические значения параметров факторов производственной среды путем лабораторных исследований или путем расчетов.
Лабораторные и инструментальные исследования проводятся в соответствии с положением ГОСТ 1.25-76 «ГСС Метрологическое обеспечение. Основные положения» ГОСТ 12.0.005-84 «ССБТ Метрологическое обеспечение в области безопасности труда. Основные положения» стандартов Государственной системы обеспечения единства замеров (ГСИ) системы стандартов безопасности труда (ССБТ) методических указаний утвержденных Министерством здравоохранения.
Приборы и устройства для измерения должны соответствовать метрологическим требованиям и поверке в установленные сроки.
Оценка результатов лабораторных исследований инструментальных замеров проводится путем сопоставления фактически определенного значения с нормативными (регламентированными). При этом шум и вибрация оцениваются по эквивалентному уровню. Степень вредности и опасности каждого фактора производственной среды и трудового процесса только III класса определяются по критериям установленным Гигиенической классификацией труда № 4137-86 (приложение 3).
При наличии в воздухе рабочей зоны двух и болей вредных веществ разнонаправленного действия каждое из вредных веществ необходимо считать самостоятельным фактором подлежащим количественной оценке.
При наличии в воздухе рабочей зоны двух и более вредных веществ однонаправленного действия отношение фактических концентраций каждого из них к установленным для них ПДК суммируется. Если сумма отношений превышает единицу то степень вредности данной группы вещества определяется исходя из величины этого превышения с учетом класса опасности наиболее токсичного вещества группы а вся группа оценивается как одно вещество.
Концентрация вредных веществ однонаправленного действия определяется по ГОСТ 12.1.005-88.
Оценка условий труда при наличии двух и более вредных и опасных
производственных факторов производится по наиболее высокому классу и степени.
Оценка технического и организационного уровня рабочего места
Оценка технического уровня рабочего места проводится путем анализа:
- соответствия технологического процесса зданий и сооружений проектам оборудования - нормативно-технической документации характеру и объёму выполняемых работ оптимальности технологических режимов;
- технологической оснащенности рабочего места (наличия технологической оснастки и инструмента контрольно-измерительных приборов и их технического состояния обеспеченности рабочих мест подъемно-транспортными средствами);
- соответствия технологического процесса оборудования оснастки инструмента и средств контроля требованиям стандартов безопасности и нормам охраны труда;
- влияния технологического процесса происходящего на других рабочих
При оценке организационного уровня рабочего места анализируются:
- рациональная планировка (соответствие площади занятой рабочим местом нормам технологического проектирования и рационального размещения оборудования и оснастки) а также соответствие их стандартам безопасности санитарным нормам и правилам;
- обеспеченность работающих спецодеждой и спецобувью средствами индивидуальной и коллективной защиты и их соответствие стандартам безопасности труда и установленным нормам;
- организация работы защиты сооружений построек контрольных приборов.
На основе комплексной оценки рабочее место относится к одному из видов условий труда:
- с особо вредными и особо тяжелыми условиями труда;
- с вредными и тяжелыми условиями труда;
- с вредными условиями труда и заносятся в раздел III Карты.
По результатам аттестации определяются неотложные меры по улучшению
условий и труда не требующие для их разработки и внедрения привлечения посторонних организаций и специалистов.
Также по результатам аттестации составляются перечни:
- рабочих мест производств работ профессий и должностей работникам которых подтверждено право на льготы и компенсации предусмотренные законодательством;
- рабочих мест производств работ профессий и должностей работникам которых рекомендуется устанавливать льготы и компенсации за счет средств предприятия согласно ст. 26 Закона Украины «О предприятии» и ст. 13 Закона Украины «О пенсионном обеспечении»;
- рабочих мест с неблагоприятными условиями труда на которых необходимо осуществлять первоочередные мероприятия по их улучшению.
Оградительные устройства
Оградительные устройства (ограждения) предназначены для изоляции опасных зон т.е. предупреждения случайного проникновения человека в опасную зону; к движущимся или вращающимся деталям передаточным устройствам приспособлениям и инструментам машин механизмов и станков неизолированным токоведущим частям движущимся стреловым кранам кран-балкам мостовым или козловым кранам перемещающим поднятые грузы и др.
Кроме того они могут служить для предотвращения поражения обслуживающего персонала отлетающими частями режущих инструментов обрабатываемых заготовок стружки искр брызг расплавленного металла охлаждающей жидкости от попадания в открытые смотровые колодцы емкости от падения с высоты и т. п.
Оградительное устройство может одновременно выполнять роль паро- газо-и пылеприемника предотвращать запыленность и загазованность рабочих мест. исключать воздействие тепловых и электромагнитных излучений на рабочих местах в отдельных случаях снижать шум и т. д. Такие ограждения называют комбинированными или совмещенными (например ограждения фрез круглых пил ножевых валов головок сверл заточных и шлифовальных кругов служат одновременно приемниками пыли стружки и т. п.).
Пожаровзрывобезопасность.
Пожарная безопасность предусматривает такое состояние объекта при котором исключалось бы возникновение пожара а в случае его возникновения предотвращалось бы воздействие на людей опасных факторов пожара и обеспечивалась защита материальных ценностей.
Пожарная безопасность обеспечивается системами предотвращения пожара и пожарной защиты включающими комплекс организационных мероприятий и технических средств. На машиностроительных предприятиях имеются внЬвь разрабатываются и внедряются различные виды производственного оборудования новые технологические процессы. При недостаточном внимании к их особенностям они могут стать источником пожара или взрыва. Предотвратить это можно зная пожаро- и взрывоопасные особенности оборудований свойства материалов и их изменение в технологическом процессе. Современная пожарная защита имеет на вооружении системы быстрого обнаружения пожара совершенную технику и эффективные средства тушения своевременное и квалифицированное использование которых дает возможность ликвидировать пожар в самом начале его возникновения.
Анализ условий возникновения пожара
Возникновение пожара вероятно при наличии функционально обусловленной или вследствие аварии или нарушения правил пожарной безопасности горючей среды и при появлении в этой среде источника зажигания способного зажечь эту среду. К горючим средам относятся:
-горючие материалы легковоспламеняющиеся и горючие жидкости и их пары горючие дисперсные среды (пыли) горючие газы.
-применяемые или обращающиеся в функциональном (технологическом) процессе;
-строительные конструкции их облицовка и отделка а также элементы инженерного оборудования объектов (трубопроводы воздуховоды кабели и т.п.) выполненные из или с применением горючих материалов.
К основным источникам зажигания относятся:
-бытовые источники огня (спички зажигалки свечи сигареты и др.):
-аварийный режим работы электротехнических изделий;
-технологические процессы связанные с применением или образованием источников повышенных температур открытого огня и пламени;
-разряды статического или атмосферного электричества.
Анализ путей распространения пожара
Для выполнения дипломной работы следует рассмотреть возможные варианты развития пожара.
В зависимости от характеристик конструктивной пожарной опасности здания (огнестойкости здания) и функциональной пожарной опасности технологического процесса распространение пожара происходит
- по сгораемым веществам и материалам находящимся в помещении в виде линейного распространения горения;
- по технологическому оборудованию и конструкциям;
- в результате взрыва;
- вследствие лучистого и конвективного тепломассообмена между источником горения и другим пространством.
- при переходе пламени и продуктов горения через дверные проемы люки оконные и технологические проемы между помещениями;
- по коммуникациям шахтам;
- в результате достижения пределов огнестойкости ограждающими и несущими конструкциями;
- по распространяющим горение строительным
- конструкциям и содержащимся в них пустотам;
- по местам некачественной заделки стыков и трещинам;
- по проемам в наружных стенах и фасаду здания. Между зданиям
- в результате теплового излучения пламени горящего здания;
- в результате переброса на значительные расстояния искр и горящих
конструктивных элементов.
Формальные характеристики пожарной опасности объекта.
Все производства по пожарной опасности согласно НАПБ Б.07.005-86 (ОНТП 24-86).подразделяются на пять категорий которые условно обозначаются начальными буквами алфавита: АБВГ и Д
По взрывопожароопасности термическому участку присваивается категория В потому что:
- помещение не относится к категории А так как в процессе не учувствуют вещества с температурой меньше 28 градусов в количестве достаточном для образования взрывоопасной смеси с избыточным давлением больще j кПа.
- помещение не относится к категории Б так как в процессе не учавствуют вещества с температурой воспламенения более 28 градусов в количестве
достаточном для образования взрывоопасной смеси с избыточным давлением больше 5 кПа. Помещение относится к помещениям категории В так как в технологическом процессе участвуют вещества способные возгораться (масло И - 12)
Классы взрывопожароопасных зон Взрывопожароопасная зона - помещение или пространство в помещении либо вокруг наружной установки в котором имеются или могут образоваться взрывопожароопасные смеси.
При проведении экспертизы следует руководствоваться требованиями ПУЭ -86* п7.3 и 7.4. В результате было определено что возле каждой единицы оборудования где используется масло имеет место зона П-На.
Данная пожароопасная зона определяет следующие требования к оболочке электрооборудования - степень защиты электрооборудования должна быть не меньше IP – 54
Анализ мероприятий по ограничению распространения пожара
На предприятии разработаны и внедрены следующие мероприятия направленные на ограничение распространения пожара:
-предотвращением распространения горения в технологическом оборудовании и коммуникациях;
-ограничением применения сгораемых веществ и материалов в технологических процессах;
-применением не распространяющих горение строительных материалов и конструкций;
-разделением различных по пожарной опасности процессов;
-ограничением размеров зданий и пожарных отсеков;
-повышением пределов огнестойкости и снижением горючести ограждающих и несущих строительных конструкций;
-использованием противопожарных преград; защитой проемов устройством преград в коммуникациях заделкой стыков;
-использованием первичных автоматических и привозных средств пожаротушения а также систем обнаружения и сигнализации о пожаре;
-устройством противопожарных разрывов и преград между зданиями;
-использованием противопожарного водопровода;
обеспечением доступа пожарных к возможным очагам пожара.
Анализ путей эвакуации.
Для обеспечения при пожаре безопасной эвакуации людей находящихся зданиях производственного вспомогательного и другого назначения предусматриваются эвакуационные выходы. Они должны обеспечивать безопасный выход людей наружу кратчайшим путем в минимальное время. Эвакуационными считаются выходы если они ведут из помещения первого этажа наружу непосредственно или через коридор вестибюль лестничную клетку; из помещений любого этажа кроме первого в коридор или проход ведущий к лестничной клетке или в лестничную клетку имеющую самостоятельный выход наружу или через вестибюль; из помещения в соседние помещения в том же этаже обеспеченные выходами наружу и не содержащие производств категории А и Б.
Материал полов и облицовка стен и потолка
Двери в противопожарных стенах
Размеры путей эвакуации
Перепад высот на пути эвакуации
см если есть то не менее 45
Расстояние от наиболее удаленного рабочего места до ближайшего эвакуационного входа
Двери на путях эвакуации открываются в сторону
При проведении экспертизы путей эвакуации руководствовались требованиями Следующих нормативных актов:
СНиП 2.0102-85 п.п1.8 3.2-3.4 3.17 3.18 4.1-4.28;
СНиП 2.09.02-85 п.п2.11-2.15 2.22-2.40 2.57-2.59;
«ППБ в Украине» п.4.3.
Результаты экспертизы сведены в таблицу.
Результаты экспертизы эвакуационных путей и выходов
Исходя из принципов Гигиенической классификации условия труда подраспределяют на 3 класса:
класс — оптимальные условия труда — такие условия при
которых сохраняется не только здоровье работающих а создаются
предпосылки для поддерживания высокого уровня работоспособности
класс — допустимые условия труда — характеризуются такими
уровнями факторов производственной среды и трудового процесса которые не превышают установленных гигиенических нормативов для рабочих местах а возможные изменения функционального состояния организма восстанавливаются за время регламентированного отдыха или до начала следующей смены и не оказывают неблагоприятного влияния на состояние здоровья работающих и их потомство в ближайшем и отдаленном периодах.
класс — вредные и опасные условия труда — характеризуются I наличием вредных производственных факторов которые превышают гигиенически нормативы и способны вызвать неблагоприятное влияние на организм работающего и (или) его потомство.
Вредные условия труда по степени превышения гигиеничен нормативов подразделяются на четыре ступени (3.1—3.3). при этом создав высокий риск возникновения тяжелых форм острых профессиональных поражений; отравлений увечий угрозу для жизни.
Определение общей оценки условий труда базируется на дифференцированном анализе определения условий труда для отдельных факторов производственной среды и трудового промесса. Фактор производственной среды включают: параметры микроклимата; содержание вредных веществ в воздухе рабочей зоны; уровень шума вибрации инфро-и ультразвука освещенности и т. д. Адекватная оценка конкретных условий и характера труда будет содействовать обоснованной разработке и внедрению комплекса мероприятий и технических средств по профилактике производственного травматизма и профессиональных заболеваний в частности за счет улучшения.
МЕРОПРИЯТИЯ ПО ЗАЩИТЕ ОКРУЖАЮЩЕЙ СРЕДЫ
АРП должны проектироваться соблюдая требования «Санитарных норм проектирования промышленных предприятий» и «Указаний по расчету рассеивания в атмосферу вредных веществ содержащихся в выбросах предприятий» поскольку они являются источниками рассеивания в атмосфере вентиляционных и технологических выбросов (окислов азота окиси углерода альдегидов и др.). Для каждого источника установлены предельно допустимые концентрации выброса вредных веществ в атмосферу.
Мероприятия по защите атмосферного воздуха на АРП должны рассматриваться как составная часть общего плана по охране окружающей среды и разрабатываться в две стадии: определение необходимости осуществления мероприятий по снижению выбросов и уровня загрязнения воздуха; конкретизация содержания мероприятий обеспечивающих требования государственных стандартов.
Охрана водоемов и почв от загрязнений сточными водами на территории АРП предполагает устройство твердого покрытия проездов и стоянок автомобилей озеленение свободных от застройки площадей очистку дождевых вод сточных вод при мойке автомобилей на открытых площадках и эстакадах с устройством оборотного водоснабжения.
По санитарным нормам (СНиП 11-93 - 74) концентрация загрязнений в воде подаваемой для мойки автомобилей системами оборотного водоснабжения после ее очистки не должна превышать: взвешенных веществ - 70 мгл при мойке грузовых 40 мгл - легковых автомобилей и автобусов; нефтепродуктов - соответственно 40 и 15 мгл тетраэтилсвинца - 0001 мгл.
При сливе сточных вод в канализационные коллекторы в них должно быть не более 025 075 мгл взвешенных веществ и 005 03 мгл нефтепродуктов а наличие тетраэтилсвинца не допускается.
В средних и крупных АРП предусматривают оборотное водоснабжение для мойки автомобилей устройство локальных очистных сооружений для очистки производственных стоков от постов
Полная себестоимость обслуживания и текущего ремонта автомобилей
Себестоимостью называются затраты на производство и реализацию продукции которая определяется из выражения:
Сn = Cосн + Сдоп. + Ссоц + Cз.ч + См + Но + Нц + Нз
Сn =11898765 +88050861 +46005384996 +24000000+16000000 +416456775 +2379753+345064185 =673747747096 руб
где Сn - полная себестоимость обслуживания и ремонта автомобилей руб.
Cосн основная заработная плата ремонтно-обслуживающих рабочих руб;
Сдоп - дополнительная заработная плата ремонтно-обслуживающих рабочих руб;
Ссоц - отчисления на социальное страхование руб.
Cз.ч - затраты на запасные части руб.
См - затраты на материалы руб;
Но - расходы на содержание и эксплуатацию оборудования руб;
Нц - цеховые расходы руб.
Нз - общепроизводственные расходы руб;
Исчисление всех затрат на производство и реализацию единицы продукции называется калькуляцией себестоимости и определятся по формуле:
Сп=Сп’N=673747747096800=8421847 руб
Фонд заработной платы ремонтно-обслуживающих рабочих зоны ТО и ТР
Фонд заработной платы включают в себя основной и дополнительный фонд зарплаты. К основной заработной плате относятся все виды платы за время работы (платы по сдельным расценкам или тарифным ставкам оплата за работу в ночное время доплаты за руководство бригадой доплаты за сверхурочные и праздничные дни и др. виды оплат и премий) в рабочее время.
К дополнительной заработной плате относятся две выплаты за все отработанное время: оплаты отпусков оплаты за выполнение государственных и общественных обязанностей и др. Размер дополнительной зарплаты рассчитывается в процентах от основной зарплаты для различных категорий рабочих и зависит от продолжительности отпуска.
Основная годовая заработная плата ремонтно-обслуживающих рабочих
Сосн=001·Тн·Сг·Кт=001*793251*10000*15=11898765 руб
гдеТн - плановая годовая норма времени на выполнение всего объема работ численно равная величине общей трудоемкости работ технического обслуживания и ремонта подвижного состава СТО (Тобщ.)
Сг - часовая ставка рабочих исчисленная по среднему разряду методом интерполяции копчас.
Кт - коэффициент учитывающий доплату к основной заработной плате за руководство бригадой обучение учеников за сверхурочные и др. работы (Кт =13-15ч.)
Дополнительная заработная плата.
Сдоп.= 0074*Сосн =0074*11898765=88050861 руб
где: 0074 - коэффициент учитывающий дополнительную заработную плату в размере 74% от основной заработной платы.
Общий фонд заработной платы.
Спр=Сосн.+Сдоп=11898765 + 88050861 = 1277927361 руб
Отчисление на социальное страхование в размере 36% от фонда зарплаты
Ссоц.= 036*·Спр.=036*1277927361 = 46005384996 руб
Среднемесячная заработная плата одного производственного рабочего
Сср=Спр12*Pпр =1277927361 12*29=3672205 руб
Результаты расчетов количества работающих (берутся из технологической части) и фонд заработной платы заносятся в таблицу
Затраты на запасные части
Затраты на запасные части рассчитывают из установления норм расхода (коэффициента замены) действующих прейскуратных цен и плановых расходов за доставку их на склад потребителя.
Сз.ч. =С'з..ч. N=30000*800=24000000 руб
где С'з.ч. - норма расхода запасных частей на единицу данного вида ремонтируемого объекта руб.
N - годовая программа данного вида объектов шт.
Для смешанных СТО годовая программа рассчитывается в приведенных ремонтах.
Затраты на основные материалы
- рассчитываются на основе норм расхода отпускных цен и транспортно-заготовительных расходов
См=С'м.N=20000*800=16000000 руб
где С'м - норма расхода основных ремонтных материалов на единицу данного вида ремонтных объектов руб.
Сводный план по заработной плате
Категория работающих
месячная зарплата одного рабочего
Производственные рабочие
Вспомогательные рабочие
Расходы по обслуживанию и управлению производством (накладные расходы).
Общие накладные расходы по обслуживанию производства и управлению (Н) состоят из трех разделов:
а) Расходы на содержание и эксплуатацию оборудования (Ho) (материалы топливо энергия заработная плата и оплата услуг по содержании оборудовании и рабочих мест; текущие ремонты производственного оборудования транспортных средств и ценных инструментов расходы связанные с перемещением материалов полуфабрикатов топлива и готовой продукции; автоматизация производственного оборудования транспортных средств и ценных инструментов; возмещение износа малоценных и быстроизнашивающихся инструментов расходы по их восстановлению; прочие расходы.
б) Цеховые расходы (Hц) (затраты связанные с содержанием персонала текущего ремонта и амортизации зданий сооружений и дорогостоящего инвентаря расходы по охране труда и техники безопасности; стоимость износа и возмещения малостоящего инвентаря; расходы по испытаниям опытам исследованиям рационализации производства).
в) Общепроизводственные расходы (Hз) включающие в себя административно-управленческие и общехозяйственные расходы. Административно-управленческие расходы заработная плата работников управления зоны ТО и ТР СТО расходы по командировкам канцелярские расхода и прочие управленческие расходы. Общехозяйственные расходы - содержание и текущий ремонт зданий сооружений и инвентаря общепроизводственного назначения (помимо цеховых) содержание складов амортизация основных фондов расходы по охране труда и др. В дипломном проекте пользуется укрупненными нормами накладных расходов в % к основной зарплате основных производственных рабочих (Сосн.).
- расходы на содержание и эксплуатацию оборудования
Ho = (033 037)Сoсн.=035*11898765= 416456775 руб
- цеховые расходы Hц = (011 025)· Сoсн. руб
Hц =02*11898765=2379753 руб
- общепроизводственные расходы
Hз= (025 029)·Сoсн=029*11898765=345064185 руб
- накладные расходы
H = Ho + Hц + Hз =416456775 +2379753 +345064185 =1106585145 руб
Прибыль от основной деятельности зоны ТО и ТР СТО (П) определяется как разность отпускной (оптовой) цены на обслуживание (Оц) и полной себестоимости единицы продукции (Сп) помноженное на годовую программу (N)
П = (Оц - Сп) ·N=(92640317-8421847)*800=67374776 руб
Принимаем Оц=11*8421847 руб
Прибыль от дополнительной деятельности предприятия (Пд) определяется с учетом прибыли полученной от выполнения дополнительных работ входящих в состав товарной продукции. В дипломном проекте балансовую прибыль можно определить следующим образом:
Пд=(11·Оц-Сп)N=(11*92640317-8421847)*800=1414870296 руб.
где: 11 - коэффициент учитывающий доходы от дополнительной работы.
Расчеты себестоимости прибыли и рентабельности продукции сводятся в таблицу
Сводная таблица себестоимости прибыли и рентабельности продукции
Условные обозначения
Основная зароботная плата
Дополнительная заработная плата
Отчисление на социальное страхование
Расходы на содержание оборудования
Общепроизводственные расходы
Полная себестоимость
Рентабельность производства ТО и ТР
Рентабельность продукции определяется как отношение прибыли к полной себестоимости
R=ПСп 100%=67374776673747747096*100%=11
Потребность в нормированных оборотных средствах
К нормируемым средствам СТО относятся
Производственные запасы (основные и вспомогательные материалы запасные части топливо малоценные и быстроизнашивающиеся инструменты).
Незавершенные производства и полуфабрикаты собственной выработки.
Расходы будущих периодов.
Сумма нормируемых оборотных средств определяется согласно таблицы
Рентабельность предприятия
Рентабельность исчисляется как общая так и расчетная. Общая рентабельность (Rобщ.) определяется отношением всей суммы полученной предприятием прибыли к сумме основных фондов и нормируемых оборотных средств (Фн.об.)
Rобщ =(Пб(Фосн.+Фн.об.))*100%
Rобщ =(1414870296(90720000+99919315))*100=1405%
Расчет нормируемых оборотных средств
Годовая сумма расходов
Среднедневное потребление
Сумма нормируемых оборотных средств
Вспомогательные материалы
Малоценные и быстроизнашивающиеся
Стоимость основных производственных фондов ремонтного предприятия определяется:
Фосн.=Сзд+Соб.+Сп.и.= 51840000 +25920000 +12960000 =90720000 руб
где Сзд и Соб. - соответственно стоимости производственного задания и установленного оборудования в руб.
Сп.и. - стоимость приборов приспособлений инструмента инвентаря штучная и оптовая цена которых превышает 1500 руб. и срок службы которых не менее одного года. Стоимость основных производственных фондов ориентировочно рассчитывается следующий образом стоимость производственного здания по формуле:
Сзд.=С'зд..S=60000*864=51840000 руб
где S - площадь производственного здания м2.
С'зд.- средняя стоимость строительно-монтажных работ отнесенная к 1 м2 производственной площади ремонтного предприятия руб.
Для СТО в учебных целях можно принять Сзд=60000руб.м2.
Стоимость установленного оборудования (Соб.) приборов приспособлений инструмента (Сп.и.) инвентаря определяется по уравнению:
Соб.= С'об..S=30000*864=25920000 руб.
С п.и.= С'п.и..S=15000*864=12960000 руб
где С'об. и С'п.и.- соответственно стоимость оборудования и приборов приспособление инструмента инвентаря отнесенная к 1 м2 производственной площади руб.м2
Плата за производственные фонды составляет 3% от их стоимости.
В дипломном проекте фиксированные платежи и платежи процентов за банковские кредиты принимаются равными нулю следовательно расчетная рентабельность определяется по формуле:
Ррасч=((П-003(Фосн +Фн.об.))(Фосн +Фн.об.))100%
Ррасч=((67374776-003(90720000 +99919315))( 90720000 +99919315)*093)*100=397 %
Результаты расчетов сводим в таблицу
Рентабельность предприятия
Стоимость основных производственных фондов руб.
Стоимость нормируемых оборотных средств руб.
Общая сумма прибыли руб.
Общая рентабельность %
Расчетная рентабельность %
Производительность труда
Производительность труда по зоне ТО и ТР определяется в гривнах валовой продукции приходящихся на одного производственного рабочего и работающего;
где В-выпуск валовой продукции
В=Сп+П+Пд=673747747+67374776+1414870296 =8826095526 руб
а) производственного рабочего:
Ппр=ВРпр=882609552629= 30434812 рубчел
Ппр=ВРраб=8826095526 40= 22065239 рубчел
Показатели использования производственных фондов
Коэффициент фондоотдачи (Фо) оценивает использование основных производственных фондов определяется из выражения
Фо =ВФосн =8826095526 90720000 =097
Фв=9072000029=31282758 рубчел
где Фе-коэффициент фондоемкости
Фв-коэффициент фондовооруженности
Коэффициент оборачиваемости (Kоб.) оценивает использование оборотных средств определяется по формуле
Kоб =ВФн.об =8826095526 99919315=88
Тоб=360Коб=36088=409 дней
где Тоб-переодичность
Показатели зоны ТО и ТР
Значения показателей
Стоимость основных производственных средств
Общая трудоемкость работ по ремонту и тех обслуживанию автомобилей
Основная заработная плата
Численность персонала всегов том числе рабочих
Производительность труда:
Полная себестоимость технического обслуживания и ремонта автомобилей
Коэффициент фондоотдачи
Коэффициент оборачиваемости
Основные технико-экономические показатели зоны ТО и ТР
РАЗРАБОТКА ПЛАНА-КОНСПЕКТА КОМБИНИРОВАННОГО УРОКА С ЭЛЕМЕНТАМИ ИГРЫ
Тема: . Проектирование технологического процесса восстановления шкива коленчатого вала автомобиля Урал-4320
– развить умения в разработке технологических карт у учащихся в соответствии с существующим технологическим процессам.
– развитие умений позволяющих читать а так же пользоваться технологическими картами на производстве .
– воспитание ответственности к порученному делу.
– воспитать чувства коллективной ответственности и взаимной помощи .
– установить уровень знаний по теме «Проектирование технологического процесса восстановления шкива коленчатого вала автомобиля Урал-4320»
– систематизировать изученный материал по раннее пройденным а так же по теме проводимого занятия
Словесные ( дискуссия рассказ )
Практические ( лабораторная работа )
Межпредметные связи:
«Основы конструкции автомобиля »
« Технология конструкционных материалов »
Внутрипредметные связи:
«Технологии машиностроения »
Материально-техническое обеспечение:
Компьютер и измерительные приборы .
Дидактическое оснащение урока:
План конспект методические указания проведения урока
Тип урока: комбинированный урок с элементами игры
I. Организационный момент
Добрый день. Начнем с проверки присутствующих на занятии учащихся а также с подготовки всех к проведению занятия.
II. Актуализация опорных знаний
А теперь давайте преступим к занятию. Сейчас мыс вами проведем устный опрос по ранее пройденным темам .
Вопросы для фронтального опроса:
Какая отрасль отвечает за изготовление орудий труда и рабочих машин?
Что называется действительным размером?
Дайте определение термину технологический процесс?
Что больше масса заготовки или масса детали?
Как называется деталь с которой мы сегодня будем работать?
Дайте определение понятию технологическая операция?
На каком станке выполняется операция точение?
Каким способом изготавливается шкив коленчатого вала?
Из какого материала изготавливается шкив коленчатого вала?
Расшифруйте аббревиатуру ЧПУ?
Вопросы для индивидуального опроса:
Дайте понятие определению производственный процесс? Какие стадии производства он охватывает ?
Назовите все нормы времени при выполнении технологических операций?
III. Новые понятия и способы действий
На сегодняшнем занятии мы с вами будем изучать «Технологический процесс восстановления шкива коленчатого вала автомобиля Урал-4320»
Прежде чем перейти к изучению нового материала ознакомимся с планом на сегодняшний урок.
Назначение конструктивные особенности и условия работы детали в узле .
Технологические условия на контроль-сортировку.
Обоснование маршрута восстановления .
Установление технологической последовательности операции.
Расчет режимов механической обработки и техническое нормирование операции восстановления.
Изучение нового материала
На сегодняшнем уроке мы с вами рассмотрим шкив коленчатого вала автомобиля Урал-4320. Познакомимся с наиболее часто встречающимися неисправностями этой детали . Проведем анализ этих неисправностей найдем пути восстановления этой детали и рассчитаем нормы времени при ремонтно восстановительных работ.
Давайте выясним для чего предназначен шкив коленчатого вала какие он имеет конструктивные особенности а так же в каких условиях от работает.
не более 50 по длине окружности
менее 6180 или при наличии рисок и задиров
Ремонтировать. Шлифование «как чисто» до размера 6180мм. При размере менее 6180мм вибродуговая наплавка постановка втулки или металлизация.
Ремонтировать. Изготовление паза под шпонку номинального размера под углом 180° к старому.
1 Выбор способа восстановления
Паз под шпонку восстанавливается одновременно отверстием под шейку коленчатого вала. Так что паз в принципе придётся не восстанавливать а изготавливать заново. Изготавливать шпоночный паз будем протягиванием.
Разработаем технологический процесс восстановления. Он будет состоять из следующих операций:
Операция 35 – контрольная: контроль размеров
Операция 20 – токарная. Для выполнения данной операции выбираем токарно–винторезный станок мод.16К25 предназначенный для выполнения различных токарных работ. Благодаря своей высокой быстроходности (1600 мин –1) и мощности (10 кВт) станок позволяет выполнить работы быстро и в полном объеме с использованием режущих инструментов оснащенных пластинками из твердых сплавов.
Установка детали осуществляется в трехкулачковом патроне в разжим с базированием по торцу.
Выбираем расточной резец для обработки сквозных отверстий с пластинкой из твердого сплава ВК6 позволяющий получить требуемую шероховатость и обеспечить нужную точность обработки.
штангенциркуль ШЦ–I ГОСТ 166–80 скобы на 6180 ГОСТ 2216–845 РАСЧЕТ РЕЖИМОВ МЕХАНИЧЕСКОЙ ОБРАБОТКИ И ТЕХНИЧЕСКОЕ НОРМИРОВАНИЕ ОПЕРАЦИЙ ВОССТАНОВЛЕНИЯ
S = b×B = 0.45×25 = 11.25 ммоб.
tо.р.м.=007× tОП=007×097=007мин.
Tш.т.= tОП + tо.р.м = 9 + 997 = 1897 мин » 19 мин.(5.19)
tВ= tС.У+ tВ.П.=034+025=059 мин.(5.24)
Время занятия подходит к концу поэтому прошу вас сдать выполненные вами работы о результатах я сообщу вам на следующем занятии
Домашним заданием будет закрепление написанного вами конспекта а также подготовка доклада на темы которые были выданы вам раннее. Всем хорошего дня до свидания.
В ходе выполнения данного дипломного проекта по разработке технологического процесса ремонта крестовины дифференциала заднего моста автомобиля Урал-4320 были спроектированы: маршрут ремонта крестовины дифференциала заднего моста позволяющий получить восстановленную деталь качественной и с минимальными затратами времени а также произведен расчет режимов резания позволяющий определить их оптимальные значения.
Также при выполнении дипломного проекта было спроектировано авторемонтное предприятие со всеми необходимыми условиями и нормами охраны труда. Расчеты полученные в ходе разработки проекта показали что создание подобного рода авторемонтных предприятий положительно скажется на сфере ремонта подобных видов грузового транспорта. Данный вывод можно сделать опираясь на результаты расчетов технико-экономических показателей.
В дидактическом разделе был разработан комбинированный урок на тему «Восстановление крестовины дифференциала заднего моста автомобиля Урал-4320» с применением проблемного обучения и использованием фрагмента рабочей тетради для проведения необходимых расчётов
Зеленков Г. И. Коляссинский Б.С. Проектирование предприятий по ремонту доржно -строительных машин М.: И д-во "Высш. школа" 1971г с 240.
Проектирование авторемонтных предприятий: Учебное пособие Дехтеринский Л.В. Абелевич Л.А. и др.; -М.; Транспорт 1981 с 218.
Лудченко О.А. Техн - К.: Знаня- Пресс 2003. – 511с.
Карагодин В.И. Ремонт автомобилей и двигателей: Учеб. для студ. сред. проф. учеб. заведений В.И. Карагодин Н .Н. Митрохин.-2-е изд.стер.- М.: Издательский центр Академия>> 2003.-496с.
Проектирование авторемонтных предприятий. Справочник инженера – механика. Верещак Ф. П. Абелевич Л. А. М: “Транспорт” 1973 с 328.
Ремонт дорожных машин автомобилей и тракторов: Учебник для студ. Учреждений сред. Проф. образования Б.С. Васильев Б.П. Долгополов Г.Н.Доценко и др.; Под ред. В.А. Зорина. – 3-е изд. стер.- М.: Издательский центр “Академия” 2003.- 512с.
Шадричев В.А. Основы технологии автостроения и ремонт автомобилей. Учебник для ву ов. Л. "Машиностроение" (Ленингр. отд-ние) 1976.-500с.
Верещак Ф. П. Абелевич Л. А. "Проектирование авторемонтных предприятий. Справочник инженера- механика. М: И д-во "Транспорт 1973 с 328.
Канарчук В.Е. Чиргинец А.Д. Техническое обслуживание ремонт и хранение автотранспортных средств: Учебник: В 3 кн. – Кн. 3. Ремонт автотранспортных средств. – Киев: Вища школа 1992.– 496с.
Шадричев В.А. Основы технологии автостроения и ремонт автомобилей. – Л.: Машиностроение 1976.– 560с.
Справочник технолога авторемонтного производства. Под ред. Г.А. Малышева. – М.: Машиностроение 1977.– 432с.
Обработка металлов резанием: Справочник технолога Под ред. А.А. Панова. – М.: Машиностроение 1988.– 736с.
Двигатели УРАЛ-4320 Руководство по капитальному ремонту РК 238 УССР 53000–192–90. Ч. 1 2. – Минавтотранспорт УССР ТПО Авторемонт 1990.– 142с.
Гжиров Р.Л. Краткий справочник конструктора. – Л.: Машиностроение 1983.– 464с.
Корпус..cdw
распределительного валов
Отделение восстановления базовых деталей
со слесарно-механическим участком
Сварочно-наплавочный
полимерный-гальванический и
Ремонт электрооб-я и
топливной аппаратуры
План производственного
Участок испытания и регулировки
Ремонт головки и блока цилиндров
Слесарно-механический участок
Разборочно-моечный участок
ПЛАН ПРОИЗВОДСТВЕННОГО КОРПУСА
Освещение.cdw

распределительного валов
Отделение восстановления базовых деталей
со слесарно-механическим участком
Сварочно-наплавочный
полимерный-гальванический и
Ремонт электрооб-я и
топливной аппаратуры
световой поток 715 лм
Светильник с 4 лампами ЛБ-80
световой поток 5220 лм
Светильник с 2 лампами ЛБ-80
Освещеность на рабочем месте должна соответствовать зрительным условиям труда согласно гигиеническим нормам
Необходимо обеспечить достаточно равномерное распределение яркости на рабочей поверхности
окружающего пространвства
На рабочей поверхности должны отсутствовать резкие тени. При естественном освещении должны предусматриваться
солнцезащитные устройства (жалюзи
светорассеивающие стеклоблоки)
предотвращающие проникновение в
помещение прямых солнечных лучей
которые создают резкие тени.
В поле зрения должны отсутствовать прямая и отраженная блескость
Величина освещенности должна быть постоянной во времени. Постоянство освещенности во времени достигается
стабилизацией питающего напряжения.
Следует выбирать оптимальную направленност светового потока
что позволяет в одних случаях рассмотреть
внутренние поверхности детали
в других-различить рельефность элементов рабочей поверхности.
Осветительная установка не должна бытьисточником дополнительных опасностьей и вредностей.
Установка должна быть удобной
надежной и простой в эксплуатации. Работы
выполняемые в сборочном цехе
относятся к характеру зрительных работ средней точности. Наименьший размер объекта различения от 0
*Размеры для справок
Расстояние между светильниками
возможно изменить не более 10%
Контроль за осветительными
приборами 1 раз в 6 месяцев
Участок испытания и регулировки
Ремонт головки и блока цилиндров
Слесарно-механический участок
Разборочно-моечный участок
ПЛАН ОСВЕЩЕНИЯ ПРОИЗВОДСТВЕННОГО КОРПУСА
Условные обозначения:
ТЕХНИЧЕСКИЕ ТРЕБОВАНИЯ:
Экономика..cdw

Численность: рабочих
Производительность труда
- одного работающего
Полная себестоимость технического
обслуживания и ремонта автомобилей
Технико-экономические
Ведомость эскизного проекта
ТЕХНИКО-ЭКОНОМИЧЕСКИЕ ПОКАЗАТЕЛИ СТО
Показатели зоны ТО и ТР
Сумма нормируемых оборотных средств
Трудоемкость работ по ТО и ТР
Основная заработная плата рабочих
Коэффициент фондоотдачи
Коэффициент оборачиваемости
Содержание.doc
ОРГАНИЗАЦИОННО-ТЕХНОЛОГИЧЕСКАЯ ЧАСТЬ
Определение трудоемкости капитального ремонта восстанавливаемого объекта . . . . . . . . . . . . . . . . .. . . . . . . . . . . . . . . . . . . . . . . . . . . . . . .
Линейный график согласования ремонтных работ. . . . . . . . . . . . . . .
Расчет годовой программы предприятия. . . . . . . . . . . . . . . . . . . . . .
Годовая трудоемкость основных работ . . . . . . . . . . . . . . . . . . . . . .
Трудоемкость сопутствующих работ . . . . . . . . . . . . . . . . . . . . . . . .
Распределение трудоемкости по отделениям (участкам)
Предприятия. . . . . . . . . . . . . . . . . . . . . . . . . . . . . . . . . . . . . . . . . . .
Режим работы предприятия и годовые фонды времени. . . . . . . . . . . .
Расчет и подбор технологического оборудования. . . . . . . . . . . . .
Расчет площадей ремонтного предприятия. . . . . . . . . . . . . . . . . . . .
Расчет площадей вспомогательных помещений. . . . . . . . . . . . . . . . . . . . . . .
Компоновка производственного корпуса. . . . . . . . . . . . . . . . . . . . . . . . . . . . .
Определение габаритов здания. . . . . . . . . . . . . . . . . . . . . . . . . . . . . . . .
Компоновка подразделений производственного корпуса. . . . . . . . . . . . . .
Назначение конструктивные особенности и условия работы детали в узле. . . . .
Технические условия на контроль-сортировку. . . . . . . . . . . . . . . . . . . . . . . .
Обоснование маршрута восстановления. . . . . . . . . . . . . . . . . . . . . . . . . . . .
Установление технологической последовательности операций. . . . . . . . . . . . .
Расчет режимов механической обработки и техническое нормирование операций
восстановления . . . . . . . . . . . . . . . . . . . . . . . . . . . . . . . . . . . . . . . . . .
Проектирование станочного приспособления. . . . . . . . . . . . . . . . . . . . . . . . .
ОХРАНА ТРУДА И ПРОИЗВОДСТВЕННАЯ САНИТАРИЯ . . . . . . . . . . . . . . . . . . . . .
Расчет отопления производственного корпуса АРП. . . . . . . . . . . . . . . . . . .
Расчет вентиляции производственного корпуса . . . . . . . . . . . . . . . . . . . . . .
Расчет освещения производственных помещений. . . . . . . . . . . . . . . . . . . . . .
Расчет естественного освещения. . . . . . . . . . . . . . . . . . . . . . . . . . . . . . .
Расчет искусственного освещения. . . . . . . . . . . . . . . . . . . . . . . . . . . . . . .
Производственный шум. . . . . . . . . . . . . . . . . . . . . . . . . . . . . . . . . . . . . . .
Аттестация рабочих мест по условиям труда в производственном участке. . . . .
Оценка технического и организационного уровня рабочего места. . . . . . . . . . . .
Оградительные устройства. . . . . . . . . . . . . . . . . . . . . . . . . . . . . . . . . . . .
Пожаровзрывобезопасность. . . . . . . . . . . . . . . . . . . . . . . . . . . . . . . . . . . .
Анализ условий возникновений пожара. . . . . . . . . . . . . . . . . . . . . . . . . . . . .
Анализ путей распространения пожара . . . . . . . . . . . . . . . . . . . . . . . . . . . .
Анализ мероприятий по ограничению распространения пожара. . . . . . . . . . . . . .
Мероприятия по защите окружающей среды . . . . . . . . . . . . . . . . . . . . . . . . .
ТЕХНИКО-ЭКОНОМИЧЕСКАЯ ОЦЕНКА ПРОЕКТА
Полная себестоимость обслуживания и текущего ремонта автомобилей. . . . . .
Фонд заработной платы ремонтно-обслуживающих рабочих зоны ТО и ТР. . . . .
Затраты на запасные части. . . . . . . . . . . . . . . . . . . . . . . . . . . . . . . . . . . .
Затраты на основные материалы. . . . . . . . . . . . . . . . . . . . . . . . . . . . . . . . .
Расходы по обслуживанию и управлению производством (накладные расходы) . . .
Прибыль предприятия. . . . . . . . . . . . . . . . . . . . . . . . . . . . . . . . . . . . . . . . .
Потребность в нормированных оборотных средствах. . . . . . . . . . . . . . . . . . .
Рентабельность предприятия. . . . . . . . . . . . . . . . . . . . . . . . . . . . . . . . . . . .
Расчет нормируемых оборотных средств. . . . . . . . . . . . . . . . . . . . . . . . . . . .
Производительность труда. . . . . . . . . . . . . . . . . . . . . . . . . . . . . . . . . . . . .
Показатели использования производственных фондов. . . . . . . . . . . . . . . . . . . .
Основные технико-экономические показатели зоны ТО и ТР. . . . . . . . . . . . . . .
РАЗРАБОТКА ПЛАНА-КОНСПЕКТА КОМБИНИРОВАННОГО УРОКА С ЭЛЕМЕНТАМИ ИГРЫ . . . . .
Заключение . . . . . . . . . . . . . . . . . . . . . . . . . . . . . . . . . . . . . . . . . . . . . . .
Перечень ссылок. . . . . . . . . . . . . . . . . . . . . . . . . . . . . . . . . . . . . . . . . . . .
Приложение. . . . . . . . . . . . . . . . . . . . . . . . . . . . . . . . . . . . . . . . . . . . . . .
Рекомендуемые чертежи
- 24.01.2020