Технологический процесс ремонта гидроцилиндра экскаватора – погрузчика ДЭМ-114



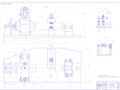
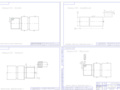
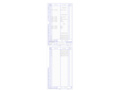
- Добавлен: 25.10.2022
- Размер: 1 MB
- Закачек: 2
Узнать, как скачать этот материал
Подписаться на ежедневные обновления каталога:
Описание
Технологический процесс ремонта гидроцилиндра экскаватора – погрузчика ДЭМ-114
Состав проекта
![]() |
![]() ![]() ![]() |
![]() ![]() |
![]() ![]() ![]() |
![]() ![]() ![]() |
![]() ![]() ![]() |
![]() ![]() ![]() |
![]() ![]() ![]() ![]() |
![]() ![]() ![]() ![]() |
![]() ![]() |
![]() ![]() ![]() ![]() |
![]() ![]() ![]() |
![]() ![]() |
![]() ![]() |
![]() ![]() ![]() |
![]() ![]() ![]() |
Дополнительная информация
Контент чертежей
Prisposoblenie1.dwg

Spetsifikatsia_Prisposoblenie_dlya_sverlenia__SDM.dwg

Лист №2 - Эскизы операционные.dwg

Рекомендуемые чертежи
- 24.01.2023
- 24.05.2016
- 13.12.2022
Свободное скачивание на сегодня
Обновление через: 17 часов 18 минут