Технологический процесс сборки рабочего тормозного гидроцилиндра




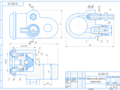
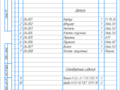
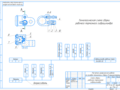
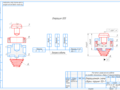
- Добавлен: 24.01.2023
- Размер: 664 KB
- Закачек: 2
Описание
Технологический процесс сборки рабочего тормозного гидроцилиндра
Состав проекта
![]() |
![]() ![]() ![]() ![]() |
![]() ![]() ![]() |
![]() ![]() ![]() |
![]() ![]() ![]() ![]() |
![]() ![]() ![]() ![]() |
![]() ![]() ![]() |
![]() ![]() ![]() |
![]() ![]() ![]() |
![]() ![]() ![]() ![]() |
![]() ![]() ![]() ![]() |
Дополнительная информация
Сборка.cdw

ТП.docx
Наименование и содержание операции
Эскизы базовой и устанавливаемой деталей
Запрессовать вилку в поршень.
Установить манжету на поршень.
Установить пружину на поршень.
Сборка гидроцилиндра.
Установить поршень в корпус.
Установить на корпус защитный колпак.
Наживить и завернуть штуцер и клапан.
Операционная карта.DOC
Код наименование операции
Обозначение документа
Код наименование оборудования
Пресс пневматический 7880-4350
Наименование детали сб. единицы материала
Масло индустриальное И-30А ГОСТ 20799-75
Установить детали 5 и 7 в приспособление
Приспособление специальное
Сопрягаемые поверхности вилки ∅8 смазать
Кисть плоская КП35 ГОСТ 10597-87
Запрессовать вилку в поршень
Пресс пневматический 7800-4350
Собрать детали 5 6 и 9 согласно чертежа
Отвертка 7810-1031 3В 1 Н12Х ГОСТ 17199-88
ГОСТ 3.1407–86 Форма 3
Схема сборки1.cdw

рабочего тормозного гидроцилиндра
Схема сборки рабочего
тормозного гидроцилиндра
БГТУ им. В.Г. Шухова
Гидроцилиндр рабочий торм.
Спецификация.spw

технологии сборки в машиностроении
Гидроцилиндр рабочий
БГТУ им. В.Г. Шухова
Пояснительная записка
Мaнжета 1.1-22 х 31 1 ГОСТ 8752-79
Шайба Н.1.12 М3 ГОСТ 11371-78
Титульный лист.docx
Белгородский Государственный Технологический Университет им. В.Г. Шухова
Кафедра Технологии Машиностроения
Расчетно-графическая работа
по основам технологии сборки
Тема: технологический процесс сборки рабочего тормозного гидроцилиндра
Принял: д.т.н. проф. Шрубченко И. В.
Записка.docx
- сборочный чертеж рабочего тормозного гидроцилиндра 04.000 СБ;
- программа выпуска изделия – 5000 штук в год;
- спецификация деталей.
Назначение и конструкция изделия
Опишем назначение и конструкцию рабочего тормозного гидроцилиндра. Гидроцилиндр рабочий тормозной 04.000 СБ является сборочной единицей тормозной системы транспортного средства и предназначен для перемещения тормозных колодок тормозов барабанного типа.
При нажатии на тормозную педаль тормозная жидкость под давлением из главного тормозного цилиндра поступает через штуцер 2 устанавливаемый в корпус посредством резьбового отверстия М12х15 и ниппель 3 в рабочий тормозной гидроцилиндр. Для удаления воздуха служит регулируемый спускной клапан 4 регулировка которого происходит перемещением по резьбовой поверхности М10х125. Под давлением тормозной жидкости поршень 5 расположенный в корпусе 1 перемещается и тем самым перемещает тормозные колодки передавая рабочее усилие через вилку 7. При прекращении нажатия на педаль тормозные колодки под действием пружин сходятся возвращая поршень 5 в первоначальное положение. При этом жидкость возвращается в главный тормозной цилиндр. Для обеспечения защиты от перекрытия выходного отверстия штуцера 2 поршень 5 подпирается пружиной 6.
В качестве уплотнения на поршень 5 устанавливается резиновая манжета 9 ГОСТ 14896-84. Чтобы предотвратить попадание в цилиндр загрязняющих веществ и прочих нежелательных факторов на корпус ставится защитный колпак 8 изготовленный из резины. Для обеспечения плотного соединения штуцера 2 с ниппелем 3 и ниппеля с корпусом 1 предусмотрена установка шайб ГОСТ 11371-78 изготовленных из сплава М3.
Основные конструкторские базы изделия: посадочная и опорная плоскости расположенные перпендикулярно друг к другу и отверстие диаметром 13 мм предназначенные для установки цилиндра на опорном щите тормозного механизма.
Вспомогательные базы изделия – поверхность паза вилки и ее торец предназначенные для установки тормозных колодок.
Тип производства и организационная форма сборки
Требуется определить тип производства и организационную форму сборки рабочего тормозного гидроцилиндра 04.000 СБ с программой выпуска Nг=5000 шт.
Рассчитанная в КОМПАС 3D V10 масса изделия составляет m=061 кг. По таблице 3 [1] находим что для изделий массой 1кг. с годовой программой выпуска от 1500 до 100000 штук производство будет являться среднесерийным.
Рассчитаем объем партии. Для бесперебойной работы сборочного цеха запас готовых изделий должен быть обеспечен на 18 дней тогда размер партии:
В формуле (1) a – периодичность запуска в днях N – годовая программа выпуска в штуках.
Далее по таблице 60 [1] исходя из типа производства объема партии и того что в изделии можно выделить две сборочные единицы (поршень в сборе и штуцер в сборе) принимаем подвижную форму сборки с расчленением работ и регламентированным тактом их выполнения.
Анализ чертежа и технических условий
Выполним анализ чертежа и технических условий рабочего тормозного гидроцилиндра 04.000 СБ.
Сборочный чертеж рабочего тормозного гидроцилиндра 04.000 СБ содержит достаточное количество видов разрезов и сечений дающих полное представление о конструкции изделия. Чертеж выполнен в соответствии с ЕСКД. Чтобы проверить достаточность и правильность простановки размеров и назначения технических требований выделим в изделии все замыкающие звенья:
а) точность размера между посадочной плоскостью (основная база) и осью паза вилки (вспомогательная база);
б) минимальный вылет вилки от опорной плоскости;
в) параллельность оси паза вилки и посадочной плоскости;
г) точность размера между осями паза вилки и посадочного отверстия в вертикальной плоскости;
д) подвижное соединение поршня и корпуса;
е) неподвижное соединение в сочленении вилка – поршень;
ж) требуемое усилие затяжки штуцера и спускного клапана.
Для замыкающих звеньев а) б) в) необходимо выявить размерные цепи (рис. 1).
Рис. 1. Размерные цепи: А – определяющая минимальный вылет вилки от опорной плоскости Б – определяющая точность размера между посадочной плоскостью и осью паза вилки; α – определяющая параллельность оси вилки и посадочной плоскости.
На присоединительный размер между посадочной плоскостью и осью паза вилки не указан допуск. Чтобы назначить этот допуск решим размерную цепь Б где Б1 Б2 Б3 -увеличивающие звенья.
По чертежам изделий составляем таблицу 1 с данными для расчета:
Расчетные данные для размерной цепи Б Таблица 1
Координаты середины допуска
Сущность допустимого отклонения
Допуск на расстояние между осью вилки и осью паза вилки
Допуск на расстояние от оси отверстия под вилку до оси отверстия
Допуск на расстояние между осью паза вилки и осью поршня
Определим номинальный размер замыкающего звена:
Определим максимальный и минимальный размер замыкающего звена:
Найдем верхнее и нижнее предельные отклонения:
Таким образом расстояние между осью паза вилки и посадочной плоскостью составляет мм.
Так как на сборочном чертеже не указана посадка для сочленения вилка-поршень выберем посадку для обеспечения неподвижного соединения вилки и поршня. По [4 с.340] выбираем посадку Hs - «прессовые средние». Характеризуется умеренным натягом обеспечивает передачу нагрузок средней величины без дополнительного крепления. Принимаем из данной группы посадку средней точности-H7s6 предельные значения натяга: Nmin=0008 мм Nmax=0032 мм.
Аналогично назначаем остальные допуски и посадки и вносим соответствующие изменения на чертеж.
Анализ технологичности конструкции изделия
Необходимо выполнить анализ и предложить мероприятия по улучшению технологичности конструкции рабочего тормозного гидроцилиндра 04.000 .
Для сборочной единицы при анализе технологичности конструкции изделия (ТКИ) могут быть рассмотрены следующие группы показателей:
)Технологическая рациональность конструкции изделия;
)Преемственности конструкции изделия;
)Ресурсоемкости изделия;
)Производственный ТКИ;
)Эксплуатационный ТКИ;
Для технологической рациональности конструкции изделия определим коэффициент сборности
где Е - число сборочных единиц в изделии Д - количество деталей в изделии не вошедших ни в одну из сборочных единиц. В соответствии со спецификацией в изделии не выделены отдельные сборочные единицы следовательно Е=0 таким образом для базового варианта Ксб=0.
Чтобы повысить коэффициент сборности выделим в данном изделии сборочную единицу - поршень в сборе (поршень (5) вилка (7) пружина (6) и манжета (9)).
Тогда число сборочных единиц Е=1 а число деталей Д=7.
Дальнейшее увеличение коэффициента невозможно конструктивно.
В группе показателей преемственности конструкции изделия определим коэффициент применяемости унифицированных составных частей:
В соответствии со спецификацией число унифицированных деталей равно 2(шайба ГОСТ 11371-78 поз. 10 – 2 шт.) Значит для первого варианта:
Для второго варианта при выделении в конструкции сборочной единицы:
Определим коэффициент применения стандартных деталей.
В соответствии со спецификацией число стандартных деталей равно 3(шайба ГОСТ 11371-78 поз. 10 – 2манжета ГОСТ 14896-84 поз. 9 – 1 шт.). Для базового варианта:
Для второго варианта:
В целом конструкция изделия является технологичной она не требует применения специальных методов приемов средств технологического оснащения.
Выбор метода обеспечения точности сборки
В соответствии с пунктом 4 в изделии выявлены все замыкающие звенья. Произведем выбор метода обеспечения точности на примере размерной цепи А (рис.1). Вылет паза вилки относительно опорной плоскости должен быть равен . Выясним обеспечивается ли требуемая точность размера по методу полной взаимозаменяемости. Для этого решим размерную цепь А.
В рассматриваемой размерной цепи: А- замыкающее звено; А1 А2А4 - увеличивающие звенья.
Расчетные данные для размерной цепи А Таблица 2
Допуск на высоту головки вилки
Допуск на высоту поршня
Допуск на длину пружины
Допуск на толщину стенки корпуса
Определим максимальный и минимальный размер замыкающего звена
В результате решения размерной цепи получили присоединительный размер . Полученная величина допуска не выходит за пределы заданного следовательно метод полной взаимозаменяемости обеспечивает заданную точность.
Установление порядка комплектования изделия и составление технологической схемы сборки
В ходе анализа размерных цепей а также анализа технологичности конструкции изделия были выявлены все замыкающие звенья и выделены отдельные сборочные единицы.
Сборку гидроцилиндра можно вести по двум вариантам. Первый вариант – сборка изделия из стандартных неразъемных изделий (рис. 2а). Второй вариант - когда в изделии выделяются две сборочные единицы: поршень в сборе (поршень (5) вилка (7) пружина (6) и манжета (9)); штуцер в сборе (штуцер (2) ниппель (3) и две шайбы (10)) (рис. 2б). Базовой деталью при сборке будет корпус.
Рис. 2. Варианты схем сборки рабочего тормозного гидроцилиндра:
а) без выделения сборочных единиц;
б) с выделением одной сборочной единицы.
Анализ вариантов схем сборки
Анализируя приведенные выше варианты сборки можно сделать следующее заключение. Наиболее рационален второй вариант сборки так как в нем выделена сборочная единица сборка которой может осуществляться параллельно тем самым сокращается общее время на сборку. Так же в пользу второго варианта говорит и анализ технологичности конструкции изделия. Окончательно принимаем вариант сборки показанный на рисунке 2 (б).
Разработка технологического маршрута сборки
Необходимо разработать маршрут сборки рабочего тормозного гидроцилиндра 04.000 СБ.
Маршрут будет содержать две операции: сборку поршня и сборку тормозного гидроцилиндра. Такой порядок выполнения операций по сборке обусловлен выбранной схемой сборки – то есть в первую очередь необходимо собрать сборочную единицу 1СБ-1 (операция 005) так как она устанавливается на последующей операции. Основными сборочными работами при сборке рабочего тормозного гидроцилиндра 04.000 СБ являются: запрессовка вилки в поршень установка поршня в корпус установка защитного колпака затяжка клапана и штуцера.
Кроме того сопрягаемые поверхности должны быть предварительно смазаны. Необходимо проведение работ по проверке правильности выполнения соединений: проверка легкости перемещения поршня; параллельности оси вилки относительно посадочной плоскости; неразъемного соединения вилка-поршень; достаточного вылета вилки относительно опорной плоскости.
Так как организационной формой сборки является подвижная форма то объект сборки будет последовательно перемещаться по сборочным постам. Следовательно результатом каждой операции должно быть изделие с зафиксированным положением составных частей чтобы при транспортировке изделие не могло самопроизвольно разобраться.
Составим технологический маршрут сборки гидроцилиндра который будет включать только работы по выполнению соединений (табл. 3).
Назначение технологических баз
Необходимо выбрать технологические базы для операции 005.
В глухое отверстие поршня диаметром 8 мм устанавливается вилка. Торцевую поверхность поршня назначим установочной базой для всей сборочной единицы. Наружная цилиндрическая поверхность поршня является двойной направляющей технологической базой. У вилки наружная цилиндрическая поверхность головки также будет являться двойной направляющей технологической базой. Так как по конструкции изделия торцы поршня и головки вилки должны лежать в одной плоскости то опорной базой для поршня будет торец для вилки – нижний торец ее головки. Схема базирования представлена на рисунке 3.
Поверхность А является и технологической и измерительной базой. Следовательно погрешность базирования для выдерживаемого при запрессовке размера будет устранена.
Рис. 3. Схема базирования при сборке корпуса с поршнем и защитным колпаком.
Аналогично назначаем технологические базы для остальных сборочных операций и вносим в таблицу 3.
Для операции 005 требуется выбрать необходимое оборудование. Исходные данные: длина стержня вилки – 11 мм тип производства – среднесерийный посадка вилки в поршень .
Необходимо выполнить запрессовку вилки. Посадка вилка-поршень выполняется с натягом натяг имеет величину 0008-0032 мм. Для запрессовки вилки в поршень будем использовать пневматический пресс 7800-4350 с номинальным усилием прессования 176 кН. Аналогично выбираем оборудование и средства для других операций. Для завинчивания штуцера выбираем гаечный торцовый не механизированный ключ (для присоединительных квадратов со стороной 63-24 мм) 7813 – ГОСТ 19733-74. Для завинчивания клапана выберем ключ гаечный с открытым зевом односторонний (размер зева от 32 до 85 мм) 7811 – ГОСТ 2841-80.
Определение режимов работы сборочного оборудования
На операции 005 для запрессовки вилки будем использовать пневматический пресс. Необходимо определить требуемое усилие запрессовки.
где f – коэффициент трения при запрессовке (f=01-015) d – номинальный диаметр сопряжения (d=8 мм) L – длина запрессовки (L=11 мм) p – давление на контактной поверхности.
где – максимальный натяг ();
Е1 и Е2 – модули упругости материалов охватываемой и охватывающей деталей (Е1=2*10 5 МПа (сталь) Е2=07*10 5 (алюминий)) и - коэффициенты Пуассона соответственно для тех же материалов ( ); d2 – диаметр наружной поверхности охватывающей детали (d2=30 мм); d1 – диаметр центрального отверстия охватываемой детали (d1=0).
и с учетом коэффициента запаса:
Из расчетов видим что выбранный пневматический пресс способен обеспечить заданное усилие запрессовки.
Проверка качества сборки соединений
При запрессовке вилки в поршень происходит уменьшение зазора между поверхностью поршня и отверстия в корпусе. В этом случае возможен брак результатом которого может стать невозможность сборки изделия. Рассчитаем величину уменьшения этого зазора по [3 с.229]. Величина увеличения диаметра поршня составит:
где p – удельное давление на поверхности контакта (p=147 МПа) d – диаметр отверстия в поршне (d=8 мм) D – наружный диаметр поршня (D=30 мм) E2 – модуль упругости материала поршня (Е2=07*10 5(алюминий)).
Из расчета видим что увеличение диаметра поршня после запрессовки в него вилки лежит в пределах допуска на его изготовление () следовательно фактический зазор будет находиться в пределах максимального и минимального зазоров посадки (Smin=20 мкм Smax=66 мкм).
Нормирование времени сборочных работ
Выполним нормирование времени для сборки рабочего тормозного гидроцилиндра в условиях среднесерийного производства. Перечень деталей входящих в сборочную единицу приведен в таблице 3.
Перечень деталей входящих в сборочную единицу
Манжета ГОСТ 14896-84
Нормирование времени на сборку рабочего тормозного гидроцилиндра
на продолжительность
Оперативное время мин
Взять вилку смазать поверхности вилки.
1. Установить поршень на стол пресса.
2. Установить вилку на поршень с оправкой.
3. Запрессовать вилку в поршень.
Взять манжету и инструмент.
1. Установить манжету в выточку.
2. Обжать манжету по всему диаметру для плотного прилегания.
3. Отложить инструмент.
1. Установить пружину в гнездо.
Вид покрытия – масло. Диаметр обработки – до 45 мм. Длина обработки – до 100 мм.
Длина запрессовывания – до 25 мм.детали до 1 кг.
Диаметр манжеты до 30 мм.
Диаметр пружины до 30 мм.
1. Установить поршень в отверстие корпуса.
Взять защитный колпак.
1. Установить колпак на выточку.
2. Обжать колпак по всему диаметру для плотного прилегания.
Взять ниппель и две шайбы и установить на штуцер.
1. Ввернуть штуцер на 2-3 нитки вручную.
2. Завернуть штуцер окончательно ключом.
Взять спускной клапан.
1. Ввернуть на 2-3 нитки вручную.
2. Завинтить клапан окончательно ключом.
Длина продвижения – до 25 мм.
Внутренний диаметр шайбы до 15 мм.
Наибольший размер – до 20 мм.
Диаметр резьбы – до 16 мм.
Длина ввертывания – до 15 мм.
Шаг резьбы – 125 мм.
Т=0022.+0020++0019=0061
Из таблицы 4 видно что трудоемкость операции 010 значительно отличается от операции 005 однако трудоемкость операции 005 кратна 010 (0857029=3) что также приемлемо.
Проектирование сборочных операций
Составим полную структуру записи для операции 005. Ключевые слова выбираем по ГОСТ 3.1703-79.
Операция будет содержать четыре перехода:
) установить детали 5 и 7 в приспособление;
) смазать сопрягаемые поверхности детали 7;
) запрессовать деталь 7 в деталь 5;
) собрать детали 5 6 и 9 выдерживая размер 2.
Рис. 4. Операционный эскиз для операции 005: а) для первого перехода; б) для третьего перехода; в) для четвертого перехода.
Окончательно назначаем оборудование для операции 005: для запрессовки вилки в поршень будет использоваться пневматический пресс развивающий усилие запрессовки не менее 7315 Н; в качестве вспомогательного инструмента при установке манжеты и пружины может быть использована отвертка; смазывание сопрягаемых поверхностей будет производиться маслом индустриальным И-30А ГОСТ 20799-75. Для операции 005 оперативное время составит 043 мин.
Эскиз сборочной единицы получаемой в результате выполнения операции 005 представлен на рисунке 4.
Разработка схем и выбор оборудования для контроля
В процессе сборки необходимо обеспечить и проконтролировать выполнение следующих параметров:
) размер между посадочной плоскостью и осью паза вилки мм;
) минимальный вылет вилки от опорной плоскости мм;
) параллельность оси паза вилки и посадочной плоскости 005 мм на 100 мм;
) зазор между поршнем и корпусом от 0 до 0034 мм;
) неподвижное соединение в сочленении вилка – поршень: натяг от 0008 до 0032 мм;
) требуемое усилие затяжки штуцера и спускного клапана.
Параметр 2 контролируется штангенинструментами. Точность измерения 001 мм на 100 мм длины.
Рис. 5. Схема контроля вылета вилки.
Параметр 3 контролируется приспособлением с индикаторами часового типа путем осевого перемещения изделия. Точность измерения 001 мм на 1 м длины. Параметр 4 контролируется щупом. Параметр 4 контролируется усилием запрессовки (7315 Н).
Рис. 6. Схема контроля параллельности оси вилки и посадочной плоскости.
Параметр 6 контролируется путем выбора крутящего момента для ключа.
Оформление технологической документации
Комплектность технологических документов на единичные технологические процессы зависит от типа производства степени детализации описания технологических процессов и применяемых технологических методов изготовления и ремонта изделий и определяется разработчиком.
Выполним операционную карту и карту эскизов а также операционную схему сборки для операции 005.
Операция 005 представляет собой запрессовку вилки в отверстие поршня а также установку на него манжеты и пружины. Запись операции и переходов в ОК выполнена по ГОСТ 3.1407-86 для слесарно-сборочных работ.
В первой графе если перед номером строки стоит буква «К»- то в нее записываются комплектующие. Если перед номером строки стоит буква «М»- то записываются материалы. Если перед номером строки стоит буква «О»- то происходит описание операции или перехода. Если перед номером строки стоит буква «Т»- то записывается информация о технологическом оснащении. Если перед номером строки стоит буква «Р»- то записываются режимы.
В графе «Код наименование операции» записывается код детали – 1СБ-1 и наименование операции - сборка.
Во второй графе «Наименование детали сб. единицы материала» напротив строк К03-К06 указываются «поршень вилка манжета и пружина» соответственно. Напротив строки М07 - «масло индустриальное И-30А ГОСТ 20799-75». Напротив строки О 08 - «установить детали 5 и 7 в приспособление» в строке Т09 указывается приспособление - «приспособление специальное». Далее идет строка О 10 - «сопрягаемые поверхности смазать» в качестве оснащения в строке Т11 указывается «Кисть плоская КП35 ГОСТ 10597-87». В строке 0 12 - «Запрессовать вилку в поршень» оснащение – в строке Т13 «Пресс пневматический 7800-4350» в строке Р14 указывается усилие запрессовки 7315 Н. Далее в строке О 15 - «Собрать детали 5 6 и 9 согласно чертежа» и в строку Т16 заносим в качестве оснащения «Отвертка 7810-1031 3В 1 Н12Х ГОСТ 17199-88».
В третьей графе «Код обозначение» записываем код поршня вилки манжеты и пружины «поршень – 04.005 вилка – 04.007 манжета – 04.009 пружина – 04.006».
В графе ЕВ- код единицы величина массы длины допускается указывать единицы измерения в данную графу записываем «шт.» напротив строки масло индустриальное И-30А – «кг.».
В графе ЕН - единица нормирования на которую установлена норма расхода материала записываем «1».
В графе КИ - количество деталей или сборочных единиц при сборке изделия записываем напротив всех деталей «1».
В графе Нрасх.- норма расхода материала записываем напротив масла индустриального И-30А «0005»
В графе МИ- записываем массу изделия «061 кг».
В графе То- записываем оперативное время «029».
Лебедев Л.В. Шрубченко И.В. Погонин А.А. и др. «Разработка технологических процессов в машиностроении»: Учеб. пособие. - Белгород: Изд-во БГТУ им. В.Г. Шухова 2004. – 177 с.
Анурьев В.И. «Справочник конструктора-машиностроителя»: В 3-х т. Т. 1-3. - 5-е изд. перераб. и доп. - М.: Машиностроение 1979.
Новиков М.П. «Основы технологии сборки машин и механизмов» М.П. Новиков. – М.: Машиностроение 1980.
«Допуски и посадки»: Справочник В.Д. Мягков П. А. Палей А. Б. Романов В. А. Брагинский. - М.: Машиностроение 1982. - Ч. I 2.
«Общемашиностроительные нормативы времени на слесарную обработку деталей и слесарно-сборочные работы по сборке машин и приборов в условиях массового крупносерийного и среднесерийного типов производства». - М.: Машиностроение 1991. - 158 с.
Лебедев Л.В. «Единые правила оформления расчетно-графических работ и проектов студентами спец. 12.01.» - Белгород: Изд. БТИСМ 1993. - 32 с.
Схема сборки A3.cdw

рабочего тормозного гидроцилиндра
БГТУ им. В.Г. Шухова
Расчетно-графическая работа
по основам технологии сборки в машиностроении
Гидроцилиндр рабочий торм.
Операционная схема сборки.cdw

по основам технологии сборки в машиностроении
БГТУ им. В.Г. Шухова
Рекомендуемые чертежи
- 24.01.2023
Свободное скачивание на сегодня
Другие проекты
- 22.08.2014