Технологический процесс на сборку планетарного редуктора


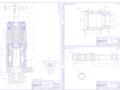
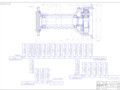
- Добавлен: 25.10.2022
- Размер: 1012 KB
- Закачек: 0
Описание
Состав проекта
![]() |
![]() ![]() ![]() |
![]() ![]() |
![]() |
![]() ![]() ![]() ![]() |
![]() |
![]() |
![]() ![]() |
![]() ![]() ![]() ![]() |
![]() ![]() |
Дополнительная информация
записка.docx
2 Технические условия на сборку
Технологическая часть
1 Обоснование типа производства
2 Определение числа сборочных единиц и составление комплектовочной карты
3 Обоснование выбранных видов соединений
4 Выбор методов обеспечения точности сборки
5 Технологические инструкции
6 Технологическая схема сборки
7 Определение состава содержания и последовательности операций сборки
8 Расчет норм времени
9 Требования безопасности противопожарные мероприятия и охрана окружающей среды
10 Утилизация и переработка отходов использование вторичных ресурсов
Конструкторская часть
1 Анализ существующих конструкций приспособления
2 Назначение и устройство приспособления
3 Принцип действия приспособления
4 Расчет приспособления
5 Технико-экономическое обоснование конструкции приспособления
Список использованной литературы
В сфере технического сервиса на перспективу поставлены задачи по повышению качества ремонта и технического обслуживания машин. Решение
этих задач возложено на сеть ремонтнообслуживающих предприятий: ремонтные заводы специализированные мастерские и цехи по капитальному ремонту машин (шасси) сборочных единиц и осстановления изношенных деталей мастерские и станции по текущему ремонту и техническому обслуживанию техники. Одним из условий решения поставленной задачи является строгое соблюдение на ремонтных предприятиях технологической дисциплины. Уровень технологической дисциплины закладывается в нормативно-технической документации (НТД). Она является основой технологической подготовки производства. Разработка НТД возлагается на инженерно-техническую службу ремонтного производства. К технологической документации относятся комплекты технологических документов на технологические процессы изготовления восстановления и дефектации деталей; ремонта разборки (сборки) обкатки сборочной единицы (машины).А так же требуются специалисты которые могли бы качественно выполнять все операции.
Подготовкой специалистов для этого занимаются множество учебных заведений. Одним из таких учебных заведений является «Гомельский государственный дорожно-строительный колледж им. Ленинского комсомола Беларуси» где в соответствии с учебным планом изучается дисциплина «Ремонт дорожных машин автомобилей и тракторов». В конце изучения дисциплины выполняется курсовой проект который позволяет закрепить теоритические знания. В настоящем курсовом проекте разрабатывается «Проект разработки технологического процесса на сборку планетарного редуктора вилочного погрузчика АМКОДОР-451А»
1Характеристика объекта сборки
Вилочный погрузчик Амкадор - 451А - универсальное подъёмно-транспортное средство с гидромеханическим приводом. Он предназначен для погрузочно-разгрузочных операций и перевозок грузов на близкие расстояния на установленных поддонах или в другой таре. Технические характеристики Вилочный погрузчик Амкадор - 451А расположены в таблице 1.
Таблица 1 - Технические характеристики погрузчика Амкадор - 451А
Свободная высота подъемамм
Скорость передвижения впередназад кмч
Габаритные размеры погрузчика:
строительная высота мм
Радиус поворота внешний мм
Расстояние от передней спинки вил до оси переднего моста мм
Собственная масса кг
Двигатель погрузчика
Автопогрузчик вилочный АМКОДОР - 451А спроектирован для движения по ровным дорогам с твёрдым и гладким покрытием. Он удобен для работы на базах складах заводских дворах станциях железных дорог в аэропортах речных и морских портах при температуре воздуха от -20С до +40С.
Место водителя автопогрузчика Амкодор - 451А оборудовано в соответствии с эргономическими показателями причём командные рычаги и кнопки управления расположены непосредственно возле водителя.
Тормозная педаль и педаль ускорения - автомобильного расположения.
Сиденье с пружинной подвеской с амортизатором регулируется в горизонтальной плоскости по продольной оси погрузчика и в зависимости от веса водителя.
Шасси – прочная хорошо оформленная цельносварная конструкция из стальных профилей и листов. Надёжное крепление всех агрегатов. Беспроблемное обслуживание всех систем. Эргономичность — регулируемое сиденье рациональное расположение командных рычагов педалей и приборов.
Редуктор планетарный (Рисунок 1) 451.16.40.000 установлен в ведущем мосту вилочного погрузчика АМКОДОР-451А.Предназначен для передачи крутящего момента с целью его увеличения.
Рисунок 1 – Планетарный редуктор вилочного погрузчика АМКОДОР-451А
– водило; 2 - полуось; 3 - фланец; 4 - сухарь; 56 – кольцо регулировочное; 7 - ось; 8 – шайба стопорная; 9 - шайба; 10 - картер; 11 - стержень; 12 - маслоотбойник; 13 – пылеотражатель; 14 – шестерня коронная; 15 - сателлит; 16 - болт; 17 - болт; 18 - шайба; 19 - манжета; 20 - шарик; 21 - кольцо; 22 - подшипник; 23 - подшипник.
После разборки и мойки определяют пригодность деталей для дальнейшего использования или ремонта. Наружным осмотром выявляют внешние дефекты: трещины вмятины задиры забоины. С помощью измерительного инструмента определяют размеры и форму детали; результаты замеров сравнивают с величинами предельных износов приведенными в технологических картах на ремонт и заносят в дефектовочную ведомость.
При сборке выполняют следующие операции: сборку резьбовых соединений соединений с подшипниками качения.
При сборке резьбовых соединений применяют болты шпильки с гайками и крепежные винты. Затяжка гаек - ответственная операция так как ослабление резьбового соединения нарушает крепление частей автопогрузчика и ведет к поломке машины. При сборке агрегата или детали с несколькими болтами (шпильками) гайки затягивают постепенно и в определенной последовательности вначале примерно на одну треть затяжки затем - на две трети и наконец полностью. Длина стандартных гаечных ключей рассчитана таким образом чтобы создать в резьбовом соединении необходимый момент затяжки или использую наборы ключей с трещетками.
Величины максимальных моментов затяжки соединений указаны в таблице 1.
Таблица 1 - Максимальные моменты затяжки соединений Нм
Класс прочности по ГОСТ 1759-70
Во избежание отвинчивания гаек устанавливают пружинные шайбы контргайки шплинты отгибные шайбы. Для повышения производительности труда применяют электрические или пневматические гайковерты. Чтобы можно было использовать механизированный инструмент при сборке-разборке на крепежных винтах выполняют крестовые шлицы.
Особое внимание следует уделять качеству затяжки резьбовых соединений крепления колес.
Момент затяжки гаек крепления колес к ступицам – 100 – 125 Нм.
Бывшие в употреблении уплотнительные прокладки разрешается устанавливать на машине при условии их полной годности.
Детали имеющие забитую или сорванную более двух ниток резьбу подлежат замене. Для деталей сборочных единиц гидросистемы срыв резьбы допускается не более одной нитки.
Размеры «под ключ» болтов и гаек должны соответствовать стандартам. Нельзя устанавливать болты и гайки со смятыми ребрами граней а также зарубками от зубила.
Детали с изношенными подшипниками и уплотнениями заменяют новыми.
В большинстве случаев причиной всех отказов является не герметичность соединений трубопроводов и стыков картеров утечки масла попадания воздуха в гидросистему ГМП. Для предотвращения появления неисправностей необходимо своевременно заменять фильтрующие элементы фильтров гидросистемы ГМП промывать фильтрующую сетку поддона картера ГМП в соответствии с периодичностью проведения ТО производить замену рабочих жидкостей масел .
1 Обоснования типа производства
После изучения служебного назначение изделия его сборочные и рабочие чертежи а также программу выпуска выбираем тип производства.
Таблица 2 – Выбор типа производства
Количество отработанных деталей одного наименования в год шт
Тяжелые (масса свыше 500 кг)
Средние (масса от 30 до 500 кг)
Легкие (масса до 30 кг)
Так как годовая программа выпуска управляемого моста равна N=800и масса составляет 700 кг выбираем тип производства крупносерийный.
После изучения сборочных чертежей и технологического анализа конструкции устанавливаем базовые детали количество сборочных единиц и порядок комплектования узлов и изделий в процессе сборки.
Количество сборочных единиц равно пяти:
Комплектная схема сборки полуоси: к полуоси крепятся манжета маслоотбойник наружные кольца подшипника.
Комплектная схема сборки водила: к водилу крепятся подшипник шайбы сателлиты ось сателлитов.
После монтажа сборочных единиц осуществляется общая сборка редуктора планетарного. Базовой деталью сборка редуктора планетарного является корпус который устанавливается на стенде. Сборка осуществляется в технологической последовательности и доукомплектовывается деталями не вошедшими в сборочные единицы.
После технологического анализа сборочных чертежей собираемого изделия в данном подразделе определяем число сборочных единиц и составляем комплектовочную карту. Оформленная комплектовочная карта приведена в приложении А.
Все соединения в планетарном редукторе вилочного погрузчика Амкодор-451А можно классифицировать следующим образом:
По конструкции условиям эксплуатации и возможности демонтажа:
1неподвижные разъемные (резьбовые шпоночные и шлицевые штифтовые конические);
2подвижные разъемные (цилиндрические с зазором например валы-подшипники скольжения плунжеры-втулки зубья колес);
По виду контакта сопрягающихся поверхностей деталей:
1 соединения с непосредственным контактом по поверхности сопряжения (общим местным линейным точечным);
2 соединения с контактом по поверхности сопряжения через промежуточный слой материала;
1соединения осуществляемые установкой сопрягаемых деталей по охватывающим (охватываемым) поверхностям или по установочным элементам сборочных приспособлений (соединения с гарантированным зазором );
2соединения выполняемые упругим деформированием соединяемых или соединительных деталей (прессовые постановка упругих стопорных колец разрезных шайб защелок и т. п.);
3разъемные соединения осуществляемые различными крепежными и фиксирующими деталями (резьбовые детали клинья цилиндрические и конические штифты);
Процесс комплектования сопровождается оформлением комплектовочной карты (КК) ГОСТ 3.1105-84 форма 7 7а. [8].
Комплектовочная карта применяется как сводный документ для указания сведений о комплектующих частях изделия (сборочной единицы) вспомогательном материале идущем на изготовление изделия. В процессах предусматривающих применение материалов расход которых не отражен в других документах составление КК является обязательным. КК составляется на весь процесс разработанный на маршрутной карте (МК).
Обоснование выбора соединений проводим с позицией конструктивных особенностей деталей затрат на соединение сопрягаемых деталей расходов на обслуживание и ремонт [910]. При выборе способа соединения учитываем условия работы изделия обеспечение необходимой его надёжности технологии обработки и сборки условия эксплуатации включая необходимые разборку ремонт и сборку соединения а также затраты на изготовление и эксплуатацию в течение заданного срока службы изделия.
Классифицирование и обоснование видов соединений сопрягаемых деталей можно представить в табличной форме (таблица 3).
Таблица 3 - Обоснование видов соединений
Неподвижное разъёмные:
Шестерня коронная с картером
Стопорная шайба в соединении фланца с полуосью
Подвижные разъёмные:
Подшипник роликовый радиальный с сателлитами
Подвижное неразъёмное
Подшипник роликовый радиально-упорный с картером
Подшипник роликовый радиально-упорный с полуосью
Подшипник роликовый радиальный с водилом
Выполняемые упругим деформированием соединяемых деталей
Кольцо регулировочное в соединении фланца с полуосью
Шайба в соединении оси с водилом
Требуемая точность сборки изделий достигается следующими методами (ГОСТ 16.319-83) [11]:
-метод групповой взаимозаменяемости (селективный метод) при котором требуемая точность сборки достигается путём соединения деталей принадлежащий к одной из размерных групп на которые они предварительно рассортированы. В пределах каждой группы требуемая точность достигается методом полной взаимозаменяемости.
Таблица 4 –Метод обеспечения точности сборки
Наименование сопряжения
Номер (по каталогу) и наименование
сопряженных деталей (узлов)
Выбранный метод сборки и его обоснование
деталь (узeл) посадочная поверхность
Деталь (узeл) посадочная поверхность
Посадка подшипников на полуось
подшипник 7516 – диаметр полуоси
Метод групповой взаимозаменяемости
Посадка сателлитов на ось
сателлиты – на диаметр оси
Посадка фланца на полуось
Фланец- на диаметр полуоси
Планетарный редуктор состоит из солнечной шестерни трех сателлитов водила трех роликовых подшипников установленных на оси сателлитов. Сателлиты входят в зацепление с коронной шестерней неподвижно соединенной с картером.
Водило соединено болтами с фланцем установленным на полуоси. Крутящий момент от дифференциала передается солнечной вал-шестерней на сателлиты которые вращаясь вокруг своих осей одновременно вращаются вместе с водилом относительно неподвижной коронной шестерни в результате чего крутящий момент от водила передается через полуось на фланец колеса. Регулировка зазора подшипников полуоси осуществляется подбором регулировочных прокладок.
Тормоз выполняет функции рабочего торможения посредством блокировки полуоси.
Многодисковые тормоза используемые в конструкции моста постоянно разомкнутого типа. Замыкание тормоза происходит под действием гидравлического давления размыкание - под действием пружин.
Под действием рабочей жидкости поршень сжимает пакет состоящий из стальных дисков и фрикционных дисков перемещающихся на шлицах втулки которая входит в зацепление с солнечной вал-шестерней.
Рабочая жидкость подводится через штуцер по каналам в опоре под-шипника в рабочую полость.
При разработке технологического процесса сборки учитываем рациональную последовательность сборки. В связи с этим производим расчленение объекта сборки на сборочные единицы первого порядка и выявлены базовые детали и сборочной единицы.
Расчленение допускает возможность параллельного выполнения узловой и общей сборки осуществление специализации сборщиков с применением высокопроизводительного оборудования и приспособлений одновременное выполнение нескольких технологических переходов в одной операции механизация слесарно-сборочных работ рациональный подбор транспортных средств. Это сокращает трудоёмкость сборки.
После подробного изучения объекта сборки составляем технологическую схему сборки управляемого моста на основе которой будет разрабатываться технологический процесс узловой и общей сборки.
Достоинства технологических схем в том что они:
-исключают возможность пропуска какой-либо детали при комплектовании;
-позволяют вести дальнейшее проектирование сборки несколькими технологами параллельно чем ускоряют проектирование процесса;
-позволяют выбрать наиболее эффективную для всех узлов организационную форму сборки.
Часто прибегают к схемам которые позволяют рассчитывать время подачи на линию сборки тех или иных сборочных единиц чтобы выдержать непрерывность сборочного процесса.
7 Определение состава содержания и последовательности операций сборки
Состав содержание и последовательность сборки уже предопределены при разработке технологической схемы сборки. Разработка маршрута сборки изделия начинается с определения порядка сборки его отдельных сборочных единиц.
Разрабатывая порядок и содержание операций сборки сборочных единиц и изделия из сборочных единиц целесообразно учитывать следующее:
на каждом рабочем месте должна выполняться однородная по своему характеру технологически законченная операция. Это позволит сборщику лучше специализироваться применять производительное технологическое оснащение и добиваться высокой эффективности;
возможность совмещения данной операции с другой целиком или с несколькими другими разделив ее на части;
возможность более рациональной последовательности операций;
возможность совмещения данной технологической операции с контрольной;
возможность упрощения сложной операции выделив часть ее в самостоятельную операцию;
возможность данную операцию требующую пригоночных работ выполнять в механоо6рабатывающем а не в сборочном цехе и тем сократить затраты на ее выполнение;
Содержание операций оформлены в комплектовочной карте(Приложение).
8 Расчёт норм времени
Сборочные ра6оты - это преимущественно ручные операции. Сложность сборочных работ состоит в том что сборка осуществляется из деталей имеющих различную точность размеров. Эта требует подготовки деталей к сборке т.е. выполнения ряда слесарных работ например притирки пригонки и т.д. Основными факторами влияющими на продолжительность выполнения сборочных работ являются конструктивная сложность узлов и деталей их вес и взаимное расположение способ соединения.
При нормировании сборочных работ пользуются общемашиностроительными нормативами времени на слесарно-сборочные работы для различных типов производств.
Под технически обоснованной нормой времени понимают время необходимое для выполнения заданного объема работы (операции) при определенных организационно-технических условиях и наиболее эффективном использовании всех средств производства.
Норма калькуляционного времени на сборочные работы Тк мин:
для массового и крупносерийного производства (штучное время)
Тк=Кс · Тт · n ·Ку · Кдз мин
где Тк – норма калькуляционного времени мин;
Кс – поправочный коэффициент на норму калькуляционного времени зависящий от сложности собираемого узла или агрегата машины;
Тт – табличное время выполнения перехода (приема) работ указанное в таблицах;
n – количество деталей на узел т.е одноименных переходов (приемов) работы ;
Ку – коэффициент учитывающий условия работы исполнителя ;
Кдз – коэффициент учитывающий затрудненный доступ исполнителя к деталям при выполнении им сборочных работ Кдз = 15 .
Таблица 4 - Нормировочная карта на сборку
Переход (прием) работы
Нормо-образующие факторы
планетарного редуктора на стенд
Одна крепежная деталь
Запрессовать подшипник в корпус
Диаметр подшипника 85
Установить шестерню коронную в корпус
Исследовательский метод
Диаметр подшипника 50
Установить кольцо регулировочное
кольцо регулировочное
Установить сухарь на полуось
Окончание таблицы 4 - Нормировочная карта на сборку
Закрепить корпус с фланцем болтом
Установить фланец на шлицы полуоси
кольцо в сопряжении фланца с полуосью
Установить шарик в паз на фланце
водило в сборе на фланец
Одеть стопорную шайбу на болт
Закрепить болтом водило с полуосью
Вставить стержень в корпус
Тк=15 · 403 ·2·10·15=18 мин.
10.1Требования безопасности.
Несчастные случаи на производстве чаще всего происходят в результате пренебрежительного отношения к правилам техники безопасности как со стороны отдельных руководителей предприятий так и со стороны рабочих.
Основную роль в борьбе с травматизмом играет обеспечение безопасных условий труда (при организации участков установке оборудования и т. д.) и наряду с ними — пропаганда техники безопасности инструктаж и обучение безопасным методам ведения работ.
Для вновь поступающих на предприятие рабочих должен обязательно проводиться вводный инструктаж ответственным лицом по технике оборудования организацией рабочего места безопасными приемами работы устройством и применением защитных приспособлений.
Для возобновления знаний по технике безопасности периодически проводится повторный инструктаж.
Участки на которых производится восстановление изношенных деталей различными методами должны быть оборудованы с соблюдением правил по технике безопасности и промсанитарии. Помещения в которых размещаются наплавочные участки должны быть построены из огнестойких материалов. Деревянные помещения должны быть оштукатурены или окрашены огнестойкой краской. Наплавочные посты должны располагаться в отдельных кабинах или ограждаться ширмами. Стены кабин окрашиваются в светло-серый цвет. Проходы между оборудованием участка и рабочими местами должны быть шириной не менее 1 м.
Помещения должны иметь общеобменную вентиляцию а рабочие места (наплавочные посты) — местную вытяжную вентиляцию достаточной производительности.
10.2 Противопожарные мероприятия.
В связи с тем что пожар на предприятии может нанести большой материальный ущерб (включая гибель людей) важное значение имеют противопожарные мероприятия. Одно из ведущих мест по обеспечению пожарной безопасности занимает профилактика. Руководители обязаны организовать: проведение на объектах противопожарного инструктажа; добровольную пожарную дружину и пожарно-техническую комиссию; периодические проверки состояния пожарной безопасности участка наличия и исправности технических средств борьбы с пожарами.
Во избежание пожаров необходимо осуществлять надзор за пожарными устройствами и производственным оборудованием. На участке не разрешается хранить порожнюю тару из-под топлива и смазочных материалов. В помещении необходимо проводить тщательную уборку после окончания работ каждой смены разлитое масло и топливо убирать при помощи песка собирать использованные обтирочные материалы после окончания работы выносить их в отведенное и безопасное в пожарном отношении место. Участок должен быть в полном объеме оборудован средствами первичного пожаротушения: ведрами топорами баграми ящиком с песком огнетушителями ОП-5 ОП-10. На видном месте должна быть закреплена табличка с телефоном аварийной пожарной службы.
10.3 Мероприятия по охране окружающей среды
При проведении сборочных работ агрегатов нужно уделять особое внимание утилизации технических жидкостей применяемых в собираемых или разбираемых агрегатах. При лояльном отношении к этому вопросу то эти жидкости (дизельное топливо масло бензин) могут попасть в почву и водоемы и нанести существенный вред окружающей среде.
Попадая в водоемы они не только покрывают поверхность пленкой но и распространяются по всей толще воды отлагаются вместе с илом на дно. Наличие в 1 л воды 01 мг нефтепродуктов придает рыбе неустранимый впоследствии привкус нефти и специфический запах. При больших количествах нефтепродуктов в воде рыбы погибают. Присутствие нефтепродуктов в почве губительно действует на растения.
Чтобы предупредить загрязнение окружающей среды нефтепродуктами необходимо соблюдать следующие меры предосторожности. Нельзя мыть сельскохозяйственную технику дизельным топливом. Сливать отстой топлива из топливных баков и фильтров следует в приготовленную тару. При прокачке топлива во время удаления воздуха из системы питания нужно сливать топливо также в какую-либо емкость. Шланги гидросистемы прицепных орудий в местах присоединения должны быть оборудованы разрывными муфтами чтобы при случайном расцеплении орудия с трактором предотвратить утечку масла на почву.
На нефтескладах ремонтных мастерских машинных дворах пунктах технического обслуживания должен быть организован сбор отработанных нефтепродуктов. Для этого в специально отведенных местах с соответствующими указателями устанавливают резервуары или бочкообразную тару.
Для обеспечения чистоты производства современные методы очистки и утилизации материалов многие из которых перерабатываются и вторично используется. Например для недопущения загрязнения почв и рек сточными водами предусмотрена их очистка и дальнейшее использование. Вентиляция оснащается фильтрующими элементами улавливающими частицы пыли и вредные соединения. Использованную ветошь собирают и утилизируют в топках с другими негодными материалами не подлежащие обработке.
1Анализ существующих конструкций приспособления
Перед проектированием проанализировал конструкции существующих приспособлений для демонтажа и сборки резьбовых соединений. Данное приспособление уменьшает физическую нагрузку рабочего повышает производительность труда точности сборки-разборки улучшению условий и безопасности труда.
Аналогичные приспособления не имеют защиты резьбового соединения от перегрузки.
Защита резьбового соединения от перегрузки достигается тем что при превышении предельного значения крутящего момента шарики прижимаемые к наружному кулачку посредством пружин отжимаются позволяя наружному кулачку свободно вращаться в результате чего прекращается передача крутящего момента от приводного вала к валу с прорезями. Регулирование предельного крутящего момента осуществляется поворотом и соответствующим осевым смещением гайки с выполненным на ее торце скосом. Удобство механизма заякоривания в эксплуатации заключается в возможности фиксирования его на различных высотах вследствие нахождения удобных поверхностей для заякоривания на разных уровнях относительно резьбового соединения.
Приспособление для демонтажа и сборки резьбовых соединений предназначен для демонтажа и сборки резьбовых соединений крепящих головки цилиндров дизельных двигателей. Внешний вид представлен на рисунке 2.
Приспособление для демонтажа и сборки резьбовых соединений содержащее механизм заякоривания съемную рукоятку корпус и размещенный в нем редуктор выполненный в виде планетарной шариковой передачи имеющий приводной вал причем в корпусе закреплен наружный кулачок и размещены кинематически связанные с ним тела качения внутренний кулачок и вал с прорезями отличающееся тем что наружный кулачок соединен с корпусом посредством предохранительного устройства предельного момента механизм заякоривания имеет возможность перемещения вдоль оси устройства а на торце вала с прорезями выполнен шестигранник.
Рисунок 2 – Внешний вид приспособления
Приспособление для демонтажа и сборки резьбовых соединений работает следующим образом. Приспособление устанавливается так чтобы шестигранник 32 на торце вала с прорезями 5 вошел в зацепление с шестигранным отверстием отвинчиваемой или завинчиваемой гайки 33. С помощью винта 29 ползун 26 фиксируется на необходимой высоте осуществляя заякоривание корпуса 11 посредством механизма заякоривания 31 относительно отвинчиваемой или завинчиваемой гайки 33 винт 30 ограничивает возможное максимальное перемещение ползуна. При вращении приводного вала 1 с помощью съемной рукоятки 23 вращается составной внутренний кулачок 3 и беговая дорожка 4 по которой перемещаются тела качения 9. При этом тела качения 9 перемещаются также по волнообразной торцовой поверхности 8 наружного кулачка 7 и одновременно вдоль прорезей 6 вала с прорезями 5 заставляя его вращаться с замедлением. Таким образом с помощью планетарной шариковой передачи 10 на валу с прорезями 5 и на шестиграннике 32 увеличивается крутящий момент и происходит отвинчивание или завинчивание гайки 33. В случае перегрузки срабатывает предохранительное устройство предельного момента 34. При этом шарики 12 раздвигаются в радиальном направлении и наружный кулачок 7 проворачивается в корпусе и увеличения крутящего момента не происходит. Перемещением гайки 16 с выполненным на ее торце скосом 17 осуществляется регулирование предельного крутящего момента затяжки путем регулировки различных сил нажатия пластин 14 и 15 на пружины 13 и соответственно на шарики 12.
4 Расчёт приспособления
Расчет производим по формуле
где – cила затяжки в резьбе Н;
d2 – средний диаметр резьбы мм;
– угол подъёма град;
- приведённый угол трения.
где d1 – внутренний диаметр резьбы мм;
Условие выполняется прочность резьбы обеспечивается.
- уменьшение физической нагрузки на рабочего.
- сокращения времени на технологическую операцию.
- обеспечивается сохранность детали.
- обеспечивается правильное положение и надёжное закрепление детали при её извлечении.
- возможность применения рабочих низкой квалификации
В результате выполнения курсового проекта я научился разрабатывать технологические процессы на сборку деталей подбирать необходимое оборудование рассчитывать нормы времени что в дальнейшем поможет повысить производительность труда.
При выполнении курсового проекта по дисциплине «Ремонт дорожных машин автомобилей и тракторов» у меня сформировались навыки самостоятельной работы при решении профессиональных задач. Закрепил полученные теоретически знания и практические умения.
Получил знания и умения в вопросах конструирования и расчёта приспособления и основных его деталей.
Ремонт автомобилей. Курсовое проектирование: учеб. пособие С.А. Скепьян. – Минск : Новое знание; М.:ИНФРА-М 2011. – 235с.: ил. – (Среднее профессиональное образование).
Радионов Ю.В. Ремонт автомобилей. Техническое нормирование труда. – Пенза: ПГУАС 2005. – 200с.
Ремонт дорожных машин автомобилей и тракторов : учебник для студ. учреждений сред. проф. образования. Б. С. Васильев [и др.]; под общ. ред. В. А. Зорина. – 2-е изд.стер. - М. : Академия 2003. – 512 с. : ил.
Воловик ЕЛ. и др. К вопросу выбора способов восстановления деталей. - М.: ЦНИИТЭИ 1981 выпуск 1.-с.7-15.
Технологические режимы наплавки в углекислом газе типовых поверхностей изношенных деталей РТМ 70.0009.004-82 ВНПО "Ремдеталь". - М.: ГОСНИТИ 1984. -8с.
ГОСТ 3.1105-84. Формы и правила оформления документов общего назначения.
ГОСТ 2.604-68. ЕСКД. Чертежи ремонтные.
Спецификация приспособления.doc
КП-3.21.12.53.02.001
КП-3.21.12.53.02.005
КП-3.21.12.53.02.010
КП-3.21.12.53.02.003
КП-3.21.12.53.02.004
КП-3.21.12.53.02.006
КП-3.21.12.53.02.011
КП-3.21.12.53.02.013
КП-3.21.12.53.02.015
КП-3.21.12.53.02.016
КП-3.21.12.53.02.017
КП-3.21.12.53.02.018
КП-3.21.12.53.02.020
КП-3.21.12.53.02.021
ВинтM10-6gГОСТ11074-93
Пружина C.11.090.0100.A
Приспособления для монтажа демонтажа резьбовых соединений
редуктор планетарный сборочный чертёж.dwg

КП-3.21.12.50.01.00.000.СБ
Кольцо регулировочное
1.16.40.004-01 поз.6
М8х20.56. 7796-70 поз.16
2-115х145-1. 8752 поз.19
А75. 13940-86 поз.21
Смазать и запресовать
приспособление.dwg

Остальные технические требования по СТБ 1022-96
Сталь 45 ГОСТ1050-88
Сборка приспособления
Рекомендуемые чертежи
- 24.01.2023
- 24.01.2023