Стационарный кран на поворотной колонне с переменным вылетом г/п 1 тонна




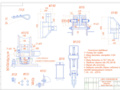
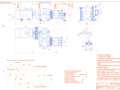
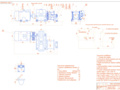
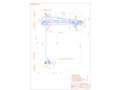
- Добавлен: 25.10.2022
- Размер: 2 MB
- Закачек: 1
Описание
Состав проекта
![]() |
![]() |
![]() ![]() ![]() ![]() |
![]() ![]() ![]() ![]() |
![]() ![]() ![]() ![]() |
![]() ![]() ![]() ![]() |
![]() ![]() ![]() ![]() |
![]() |
![]() ![]() ![]() |
![]() ![]() ![]() |
![]() ![]() ![]() |
Дополнительная информация
ryirsrss_2.1ryirsrrrrerrrrer.dwg

Механизм передвижения грузовой тележки. Сборочный чертеж.
СДМ2-13.03.00.000 СБ
Тормоз условно не показан.
Схема расположения болтов крепления элементов механизма к раме.
Ось электродвигателя
Ось входного вала редуктора
Ось выходного вала редуктора
Технические требования 1. Размеры для справок. 2. Несоосность валов устранить при помощи регулировочных прокладок. 3. Перед окончательной сборокой проверить барабан. 4. Отрегулировать тормоз на расчетный тормозной момент. 5. В опоры подшипников заложить смазку - солидол марки "С" ГОСТ 4366-76. 6.Все резьбовые поверхности покрыть тонким слоем солидола марки "С" ГОСТ 4366-76. 7. После сборки привод обкатать без нагрузки. 8. В редуктор залить масло индустриальное И-40А ГОСТ 20799-75 в количестве 1.2 1.5 л.
Техническая характеристика 1. Скорость передвижения тележки
ммин 24 2. Режим работы тяжелый (М7) 3. Перемещение тележки (вылет)
м 4.5 4. Тормозной момент
Нм 6.8 5. Диаметр каната
мм 8.3 6. Мощность двигателя
кВт 1.2 7.Передаточное число редуктора 25
ryirsrss_1.1.dwg

Николаевич Бежик А.А.
Кран на колонне поворотный Чертеж общего вида
т 1 2. Вылет (наибольший)
м 4.5 3. Высота подъема груза
м 5 4. Скорость подъема груза
ммин 10 5. Скорость передвижения тележки
ммин 24 6. Скорость поворота
ryirsrss_1.3ryirrsrr-rssrr.dwg

СДМ2-13.02.00.000 СБ
Тормоз условно не показан
Ось электродвигателя
Ось входного вала редуктора
Схема расположения болтов крепления элементов механизма к раме.
Ось выходного вала редуктора
Техническая характеристика 1. Грузоподъемность
т 1 2. Режим работы тяжелый (М7) 3. Скорость подъема
ммин 10 4. Высота подъема
м 5 5. Диаметр каната
мм 8.3 6. Мощность двигателя
кВт 1.7 7.Передаточное число редуктора 32.42
Технические требования 1. Размеры для справок. 2. Несоосность валов устранить при помощи регулировочных прокладок. 3. Перед окончательной сборокой проверить барабан. 4. Отрегулировать тормоз на расчетный тормозной момент. 5. В опоры подшипников заложить смазку - солидол марки "С" ГОСТ 4366-76. 6.Все резьбовые поверхности покрыть тонким слоем солидола марки "С" ГОСТ 4366-76. 7. После сборки привод обкатать без нагрузки. 8. В редуктор залить масло индустриальное И-40А ГОСТ 20799-75 в количестве 1.2 1.5 л.
r2.dwg

СДМ2-91.00.00.000 ВО
d-10x100H7f7x110H10a11x16H9d11
Технические требования: 1.* Размеры для справок. 2. Сварку выполнять электродом Э-50А ГОСТ 9467-75. 3. Сварку выполнять по ГОСТ 5264-80. 4. Твердость сварного шва 290 300 HB. 5. Сварные швы зачистить. 6. Проверить качество сварных соединений одним из методов неразрушающего контроля. 7. H14 ; h14 ; ±0.5IT14.
СДМ2-13.00.00.000 ВО
srssrr_4.1rrsrr.dwg

Металлоконструкция стрелы Сборочный чертеж
Технические требования: 1.* Размеры для справок. 2. Сварку выполнять электродом Э-50А ГОСТ9467-75. 3. Сварку выполнять по ГОСТ 5264-80. 4. Твердость сварного шва 290 300 HB. 5. Сварные швы зачистить. 6. Проверить качество сварных соединений одним из методов неразрушающего контроля. 7. H14 ; h14 ; ±0.5IT14.
СПЕЦИФИКАЦИЯ 1.doc
М16х15-6gх70.58(S24)
М18х15-6gх70.58(S27)
Механизм подъема груза
СДМ2-91.03.00.000 СБ
М10х125-6gх80.58(S16)
Механизм передвижения тележки
СДМ2-91.00.00.000 ВО
Кран поворотный на колонне
M22 х15-6gх120.58(S34)
Манжета 1.1-85 х110-1
Редуктор цилиндрический
Редуктор червячный Ч-80
Выключатель конечный 211
Канат-8.3-Г-1-Н-1764
Канат-8.3-Г-1-Н-1568
Масло индустриальное
Уголок №5 ГОСТ 8509-86
Уголок №2.5 ГОСТ 8509-86
Уголок №3.5 ГОСТ 8509-86
Швеллер №24ГОСТ 8240-89
Записка_моя!!!.doc
Целью данного курсового проекта является разработка полноповоротного крана на колонне с переменным вылетом. Краны данного типа широко применяются на различных складах в производственных цехах ремонтных мастерских и пр. Удобство монтажа и простота в обслуживании делают данный тип кранов весьма популярным. Краны выполняют преимущественно с крюковыми или со специальными захватами.
В зависимости от типа поворота данные краны делятся на полно- и неполноповоротные с ручным и механическим поворотом следует отметить что ручной поворот в последнее время применяется крайне редко. Грузовые тележки которые достаточно часто применяют в конструкции крана бывают самоходными или с канатным приводом. При применении канатного привода в механизме изменения вылета конструкция стрелы и тележки выполняется облегченной.
Опорные части крана - опорные узлы колонны воспринимающие различные нагрузки проектируются с учетом места расположения крана. Так колонна крана может быть с закреплением как в нижней так и в верхней части может применяться закрепление только в одной нижней части что значительно увеличивает размеры опорного узла.
По результатам расчетов всех механизмов и металлоконструкции крана выполняется графическая часть проекта в которой приводятся все основные схемы и механизмы крана.
Обзор литературных и патентных источников
Кран состоит из следующих основных частей (рис. 1): стационарной колонны 1 поворотной колонны 2 рамы фундамента 3 механизма поворота 4 механизма передвижения 5 механизма подъема (электрической тали ТВ-2) 6.
Стационарная колонна (рис.2) представляет собой трубу 1 на верхнюю часть которой через сферический радиальный и упорный подшипники опирается траверса 2. На траверсе закреплен токосъемник 3 (щеткодержатели расположены на поворотной колонне). Своей нижней частью колонна смонтирована на раме фундамента (в верхнем поясе на конической в нижнем — на цилиндрической поверхности) и прикреплена к ней при помощи фланца 4 и болтов. Поворотная колонна закреплена на стационарной при помощи опор 5 и 6 надетых на цапфы траверсы.
Конструкция поворотной колонны изображена на рис. 4. К трубе 1 приварены швеллеры 2 используемые в качестве стрелы. С противоположной стороны на колонне расположена площадка 3 на которой установлен механизм передвижения. Механизм поворота расположен на площадке 4.
Фундаментная рама сварена из восьми крестообразно расположенных швеллеров № 30 и усилена верхним горизонтальным листом и диафрагмами. Механизм поворота (рис. 5) расположен на поворотной части крана и состоит из червячного редуктора 1 соединенного с электродвигателем 2 втулочно-пальцевой муфтой 3 и колодочного электромагнитного тормоза 4 На выходном валу редуктора закреплена шестерня 5 входящая в зацепление с зубчатым венцом жестко скрепленным с фундаментной рамой.
В редукторе (рис. 3) крутящий момент от электродвигателя через червяк 1 передается на червячное колесо 2 которое свободно вращается на вертикальном валу 3. К. колесу на шлицах прикреплены ведущие диски фрикционной предохранительной муфты а ее ведомые диски при
помощи шлицев соединены с втулкой 4. Эта втулка также на шлицах сидит на валу 3. Прижатие дисков осуществляется пружинами 5 усилие которых можно регулировать при помощи гаек 6.
Механизм передвижения состоит из барабана установленного на выходном валу червячного редуктора типа РЧ электродвигателя и колодочного электромагнитного тормоза. Редуктор соединен с двигателем втулочно-пальцевой муфтой.
Энергоснабжение крана производится от сети переменного тока напряжением 380 В. В связи с тем что все электрооборудование расположено на вращающейся части крана для подачи к нему питания установлен кольцевой токосъемник с тремя кольцами.
Для привода всех механизмов применены короткозамкнутые двигатели кнопочное управление которыми осуществляется с помощью реверсивных магнитных пускателей.
Рис. 1. Общий вид поворотного крана
Рис.2.Стационарная колонна
Рис.3.Червячный редуктор
Рис.4.Поворотная колонна
Рис.5.Механизм поворота
Таблица № 1-Основные параметры крана.
Грузоподъемность крана т
Максимальный вылет м
Скорость подъема груза ммин
Скорость передвижения тележки ммин
Скорость поворота крана обмин
Высота подъема груза м
На основании приведенных в данных ведется дальнейший расчет всех механизмов и металлоконструкции крана.
Расчет механизма подъема груза
Расчет ведем в соответствии с методикой изложенной в литературе [1].
Механизм подъёма груза предназначен для перемещения груза в вертикальном направлении. Он проектируется в зависимости от грузоподъёмности высоты подъема груза и максимального вылета с учетом режима работы крана. Режим работы крана – тяжелый М7.
Привод механизма подъёма и опускания груза включает в себя лебёдку механизма подъёма. Крутящий момент создаваемый электродвигателем передаётся на редуктор через муфту. Редуктор предназначен для уменьшения числа оборотов и увеличения крутящего момента на барабане.
Рисунок 1- Кинематическая схема механизма подъема груза.
Барабан предназначен для преобразования вращательного движения привода в поступательное движение каната.
Усилие в канате набегающем на барабан H:
где: Q-номинальная грузоподъемность крана кг;
z - число полиспастов в системе;
u – кратность полиспаста;
h0 – общий КПД полиспаста и обводных блоков;
где п – КПД полиспаста;
об – КПД обводных блоков;
где бл – КПД блока в соответствии с [табл. 2.1] бл=0.97;
Рисунок 2-Схема запасовки грузового каната.
где z – число обводных блоков;
Расчетное разрывное усилие в канате при максимальной нагрузке на канат:
где k – коэффициент запаса прочности для тяжелого режима работы
Выбираем по ГОСТ 2688– 80 канат двойной свивки типа ЛК-Р конструкции 6х19 (1+6+66)+1о.с. диаметром dk=8.3 мм имеющий при маркировочной группе проволок 1764 МПа разрывное усилие F=38150 Н.
Обозначение каната [1.с.277]
Канат – 8.3 – Г – 1 – Н – 1764 ГОСТ 2688-80.
Фактический коэффициент запаса прочности:
kф=FкFб=381505285=7.22>=7.1. (2.5)
Требуемый диаметр барабана по средней линии навитого стального каната мм:
где: d – диаметр каната мм;
h1 – коэффициент зависящий от типа машины привода механизма и режима работы машины механизма принимается 22.4 [2 прил. 6].
Принимаем диаметр барабана Dб=200 мм.
Диаметр блока по средней линии мм:
где: h1 – коэффициент зависящий от типа машины привода механизма и режима работы машины механизма принимается 25.
Длина каната навиваемого на барабан
где: Н – высота подъема груза м;
Uп – кратность полиспаста;
Dб – диаметр барабана по средней линии навитого каната м;
z1 – число запасных ( неиспользуемых ) витков на барабане до места
крепления (z1=15 2);
z2 – число витков каната находящихся под зажимным устройством на
Рабочая длина барабана м:
где: Lк – длина каната навиваемого на барабан м;
t – шаг витка t = 0.010 [табл.2.8];
m – число слоев навивки;
dк – диаметр каната м;
Dk – диаметр барабана м;
j - коэффициент не плотности навивки;
Толщина стенки литого чугунного барабана должна быть мм:
где Dб.д – диаметр барабана по дну канавки;
В качестве материала барабана примем сталь марки 20Х (dтек=400 МПа
Статическая мощность двигателя при h = 085 кВт:
где: Q – номинальная грузоподъемность кг;
vг – скорость подъема груза мс;
Номинальная мощность двигателя принимается равной или несколько меньше статической мощности. Выбираем крановый электродвигатель с фазным ротором MTF –012– 6 имеющий при ПВ=60% номинальную мощность Рдв= 1.97 кВт частоту вращения n=920 обмин. момент инерции ротора Ip=0029 кгм2 и массу m=58 кг.
Частота вращения барабана обмин:
где: Uп – кратность полиспаста;
Dрасч – расчетный диаметр барабана м.
Общее передаточное число привода механизма:
Расчетная мощность редуктора кВт:
где:kp-коэффициент условий работы равный 1.7 [табл 1.34];
Выбираем редуктор цилиндрический двухступенчатый горизонтальный крановый типоразмера Ц2 –250 с передаточным числом
Uр =32.42 и мощностью на быстроходном валу при тяжелом режиме работы Рр =3.6 кВт [табл.III.4.2 с.318].
Момент статического сопротивления на валу двигателя в период пуска Нм:
где z – число полиспастов в системе;
Dб – диаметр барабана м;
Uред – передаточное число редуктора;
б и пр – КПД барабана и привода (ориентировочно б=0.96 пр=0.96) [табл.1.18 с.23; табл.5.1 с.127].
Номинальный момент передаваемый муфтой принимается равным моменту статических сопротивлений:
Тмном=Тс=20.1 (Нм)..
Номинальный момент на валу двигателя (Нм):
где Рдв – мощность двигателя кВт;
nдв – частота вращения двигателя обмин;
Расчетный момент для выбора соединительной муфты Нм :
где к1 – коэффициент учитывающий степень ответственности механизма и режим работы принимается 4 [табл.1.35 с.42].
Выбираем ближайшую по требуемому крутящему моменту упругую втулочно–пальцевую муфту с тормозным шкивом диаметром Dт=200 мм и наибольшим передаваемым крутящим моментом 125 Нм. момент инерции ротора муфты Iм=0.06 кгм2. [3табл. 13.3.1].
Момент инерции ротора двигателя и муфты кгм2
I=Iр+Iм=0.029+0.06=0.089 (кгм2). (2.18)
Средний пусковой момент двигателя Нм:
ymin- минимальная кратность пускового момента электродвигателя:
Тмах- максимальный пусковой момент двигателя Нм
Тном- номинальный момент двигателя Нм
Время пуска при подъеме груза с:
где Тср.п – средний пусковой момент двигателя Нм;
Тс – момент статического сопротивления соответственно на валу двигателя при пуске Нм;
d-коэффициент учитывающий влияние вращающихся масс привода (кроме двигателя и муфты) равен 1.1 1.25;
Фактическая частота вращения барабана по формуле:
Фактическая скорость подъема груза:
где: uп – кратность полиспаста
Dрасч- расчетный диаметр барабана м
Ускорение при пуске:
Рисунок 3- Усредненный график загрузки механизма подъема [рис.1.1 с16].
Из графика усредненной загрузки механизма определим моменты развиваемые двигателем и время его пуска при подъеме и опускании груза в различные периоды работы механизма.Согласно графику за время цикла (подъем и опускание груза) механизм будет работать с номинальным грузом
7 Q=7000 кг – 4 разa;
17Q=1700 кг – 1 раз;
05Q=500 кг – 3 раза.
Таблица № 2 – Моменты развиваемые двигателем и время его пуска
Наименование показателя
Результаты расчета при массе
поднимаемого груза кг
Натяжение каната у барабана при подъеме груза
Момент при подъеме груза
Время пуска при подъеме
Натяжение каната у барабана при опускании груза
Момент при опускании груза
Время пуска при опускании
Средняя высота подъема груза составляет 0.5 0.8 номинальной высоты Н=5м. Примем Нср=0.7·Н=0.7·5=3.5 (м).
Время установившегося движения:
Сумма времени пуска при подъеме и опускании груза за цикл работы механизма:
Общее время включений двигателя за цикл :
Среднеквадратичный момент:
где: tп – общее время пуска механизма в разные периоды работы с различной нагрузкой с;
Т2сty – сумма произведений квадрата моментов статических сопротивлений движению при данной нагрузке на время установившегося движения при этой нагрузке;
t – общее время включения электродвигателя за цикл с.
Среднеквадратическая мощность двигателя кВт:
где: Тср – среднеквадратичный момент преодолеваемый электродвигателем.
Во избежание перегрева электродвигателя необходимо чтобы
развиваемая двигателем среднеквадратичная мощность удовлетворяла условию Рср Рном – условие соблюдается.
Расчет и выбор тормоза.
Момент статического сопротивления на валу двигателя при торможении механизма:
где: hт – КПД привода от вала барабана до тормозного вала 0.96;
U – общее передаточное число между тормозным валом и валом барабана;
Необходимый по нормам тормозной момент развиваемый тормозом выбираем из условия:
где кт – коэффициент запаса торможения для тяжелого режима кт=2.0 [табл.2.9].
Подбираем тормоз ТКТ – 200 со следующими параметрами: тормозной момент 40 Н·м диаметр тормозного шкива Dт=200 мм [табл.2.9с.342].
Расчет механизма передвижения грузовой
Расчет ведем в соответствии с рекомендациями литературы [1].
Расчет механизма передвижения тележки заключается в подборе и расчете ходовых колес определении сопротивлений передвижению выбора двигателя редуктора муфты и тормоза.
Рассчитываем подвесную тележку с канатным приводом.
Рекомендуемый диаметр ходовых колес для грузоподъемности 125 т равен 200мм. Принимаем Dк=200 мм.
Коэффициент трения качения ходовых колес по рельсам с плоской головкой m=0.0003 м.
Коэффициент трения в подшипниках качения ходовых колес f=0.015.
Диаметр вала цапфы ходового колеса:
dк=(0.2 0.25)Dк ;мм (3.1)
dк=(0.2 0.25)200=(40 50) мм.
Общее сопротивление преодолеваемое тяговым канатом грузовой тележки Н:
где Wтр – сопротивление от трения;
Wукл – сопротивление от уклона рельсового пути;
Wтр – сопротивление от ветровой нагрузки;
Wц – сопротивление создаваемое массой груза и тележкой при повороте;
Wн – сопротивление от разности натяжений ветвей грузового каната;
Wпр – сопротивление от провисания холостой ветви.
Сопротивление от трения:
где кр – коэффициент учитывающий трение реборд о рельсы; кр=2.2 [с.33];
Gт – масса грузовой тележки кг;
Q – грузоподъемность крана кг;
m – коэффициент трения качения ходовых колес м;
f – коэффициент трения в подшипниках качения ходовых колес;
Сопротивление от уклона рельсового пути:
Сопротивление от ветровой нагрузки:
где р – распределенная ветровая нагрузка;
А – наветреваемая площадь; Ател1м2 и Агр2.8м2 [табл. 1.16];
где q – динамическое давление ветра принимают q = 125 Па [с.21];
к – коэффициент учитывающий изменение динамического давления по высоте равен 1 т.к Н = 5 м [с.21];
с – коэффициент аэродинамической силы с = 1.2 и с = 1.4 (для груза и тележки соответственно) [1.с.21];
n – коэффициент перегрузки n = 1 [с.21];
Сопротивление создаваемое массой груза и тележкой при повороте:
где:n-скорость поворота платформы с-1;
R=L-максимальный вылет м;
Сопротивление от разности натяжений ветвей грузового полиспаста:
где:z=U+2 – количество ветвей каната в системе грузового полиспаста;
Сопротивление от провисания холостой ветви:
где: qk – погонная масса каната 0.256 кгм;
Общее сопротивление:
Wпер=824+332+448+94.2=1698.2(Н).
Усилие в канате набегающего на барабан:
z – число обводных блоков;
Расчетное разрывное усилие в канате:
Принимаем канат по ГОСТ 2688 – 80 двойной свивки типа ЛК-Р конструкции 6х19 (1+6+66)+1 о.с диаметром dk=8.3 мм имеющий при маркировочной группе проволок 1568 МПа разрывное усилие F=34800 Н.
Канат – 8.3 – Г – 1 – Н – 1568 ГОСТ 2688-80.
Требуемый диаметр барабана по средней линии навитого стального канатамм:
где: h1 – коэффициент зависящий от типа машины привода механизма и режима работы машины механизма принимается 25 [2 прил. 6].
Длина каната навиваемого на барабан:
где: Dб – диаметр барабана по средней линии навитого каната;
L – максимальный вылет м;
Толщина стенки литого барабана мм:
Статическая мощность привода при h = 085 кВт:
где Wпер – общее сопротивление Н;
vпер – скорость передвижения грузовой тележки мс;
Выбираем крановый электродвигатель с фазным ротором MTF – 011 – 6 имеющий при ПВ=60% номинальную мощность Рном= 1.2 кВт и частоту вращения n=910 обмин. момент инерции ротора Ip=0021 кгм2 масса двигателя m=51 кг.[табл.III.3.5].
Выбираем редуктор цилиндрический двухступенчатый горизонтальный крановый типоразмера 2Ц2 –125Н с передаточным числом
Uр =25 и мощностью на быстроходном валу при тяжелом режиме работы Рр=1.2кВт .[ табл.III.4.2].
Момент статического сопротивления на валу двигателя в период пуска:; (3.19)
де z – число полиспастов в системе;
б и пр – КПД барабана и привода (ориентировочно б=0.96 пр=0.85) [с.23табл.1.18 с.127 табл.5.1].
Номинальный момент передаваемый муфтой принимается равным моменту статических сопротивлений: Тмном=Тс=9.4 Нм.
Номинальный момент на валу двигателя Нм:
где: к1 – коэффициент учитывающий степень ответственности механизма (к1=1.4) [с.42табл.1.35].
к2 – коэффициент учитывающий режим работы механизма (к2=1.3) [с.42табл.1.35].
Выбираем ближайшую по требуемому крутящему моменту упругую втулочно–пальцевую муфту с тормозным шкивом диаметром Dт=120 мм наибольшим передаваемым крутящим моментом 63 Нм. момент инерции муфты Iм=0.04 кгм2. [3табл.13.3.1].
Момент инерции ротора и муфты кгм2 :
I=Iр+Iм=0.021+0.04 =0.061(кгм2).
Средний пусковой момент двигателя :
Фактическое время пуска при передвижении тележки:
Тс – момент статического сопротивления соответственно на валу двигателя при пуске
Фактическая скорость подъема груза:
где: hт – КПД привода от вала барабана до тормозного вала;
U – общее передаточное число между тормозным валом и валом барабана.
Необходимый тормозной момент развиваемый тормозом выбираем из условия.;
где: кт – коэффициент запаса торможения (для тяжелого режима кт=2.0).
Выбираем тормоз ТКТ –100100 со следующими параметрами: тормозной момент 20 Н·м диаметр тормозного шкива Dт=120 мм [табл.III.5.11].
Расчет механизма поворота крана
Расчет механизма поворота крана ведем в соответствии с рекомендациями литературы [1] [4].
1 Определение опорных реакций и выбор подшипников.
Для определения реакций в опорах крана составим расчетную схему на которой покажем все усилия действующие на него и составим уравнения статики из которых определим все неизвестные величины.
Рисунок 5 – Расчетная схема для определения реакций в опорах.
Для определения верхней горизонтальной реакции составим уравнение суммы моментов сил относительно точки А:
ΣМа=0: -Rb(H+1)-M1+2-( Σп+Σт)0.5g+mстg0.5L+(mт+Q)g·L+Fст.в.гр·H+ +Fст.в.кр·0.5(H+1)+F1+2·cos45°·0.5+ F1+2·cos45°·4.5=0; (4.1)
где: H-высота подъема груза м;
M1+2 – момент от приведения сил разности натяжения к центру барабана Нм;
Σп+Σт – масса механизма подъема груза и передвижения тележки кг;
mст – масса стрелы кг;
mт – масса тележки кг;
Q – грузоподъемность кг;
Fст.в.гр и Fст.в.кр – ветровая нагрузка действующая на груз и кран соответственно Н;
F1+2 – усилие действующее на кран от разности натяжений ветвей каната механизма подъема груза Н.
f – коэффициент трения0.13;
α – угол навивки каната на барабан (3.5 оборота).
Подставив значения получим:
Для определения нижней горизонтальной реакции составим уравнение суммы проекций всех сил на горизонтальную ось:
Rax=9577-1390-700-500=7(кН).
Для определения верхней вертикальной реакции составим уравнение суммы проекций всех сил на вертикальную ось:
Ray+ F1+2·cos45°-( Σп+Σт)g- mстg-(mт+Q)g=0; (4.3)
Ray=(1055+85+207+282)9.8-1390=14.6 (кН).
Построим эпюры продольных поперечных сил и изгибающих моментов действующих на колонну крана:
Рисунок 6 - Эпюры продольных поперечных сил и изгибающих моментов.
М1=(mт+Q)g·L=1055·9.8·4=46.6 (кНм);
М2= mстg0.5L=85·9.8·0.5·4=1.87 (кНм);
М3=( Σп+Σт)0.5g=(207+282)·9.8·0.5=2.4 (кНм);
М4= F1+2·cos45°·0.5=1968·0.7·0.5=0.7 (кНм);
М*=М1+М2+М4-М3=46.8 (кНм);
N*=( mт+Q+mст+ Σп+Σт)g- F1+2·cos45°=14.6 (кН).
Приняв в качестве материала колонны сталь марки 09Г2С (пр=420 МПа тек=220 МПа) определим максимальный диаметр в наиболее опасном сечении:
Приняв максимальный изгибающий момент 37.2 кНм и продольное усилие 14.6 кН получим расчетный диаметр d=100 мм. Далее проектируем колонну с учетом особенностей крепления всех механизмов и конструкций опорных узлов.
Подбираем подшипники:
- для верхней опоры воспринимающей радиальные усилия выбираем шариковый радиальный однорядный подшипник 1000815 ГОСТ 8338 с посадочным диаметром 75 мм и статической грузоподъемностью 12.5 кН;
- для нижней опоры воспринимающей осевые усилия выбираем шарикоы упорный однорядный подшипник 28211 ГОСТ 7872 с посадочным диаметром 55 мм и статической грузоподъемностью 50 кН.
2 Расчет привода механизма поворота.
Рисунок 7 – Кинематическая схема привода механизма поворота.
Определим момент сопротивления вращению крана от сил трения в опорах:
Ттр=Тах+Тау+Тв ; (4.5)
d-средний диаметр подшипника м;
f-коэффициент трения между внутренним кольцом подшипника и колонной равен 0.015 [1].
Подставив последовательно значения для всех реакций опор получим:
Тах=7000·(0.09+0.65)2·0.015=8.14(Hм);
Тау=14600·(0.055+0.090)2·0.015=12.9(Нм);
Тв=9577·(0.09+0.65)2·0.015=11.13(Нм).
Суммарное сопротивление трению:
ΣТ=8.14+12.9+11.13=32.17(Нм).
с – коэффициент аэродинамической силы с = 1.2 и с = 1.4 (для груза и стрелы соответственно) [1.с.21];
Fстр=рстр·А·кспл; (4.7)
где:А-площадь стрелы и груза соответственном2;
кспл - коэффициент сплошности металлоконструкции стрелы принимаем 0.3.
Момент сопротивления от ветровой нагрузки:
Твет= Fстр·0.5·L+ Fгр·L; (4.9)
Подставив все значения получим:
Твет=175·(0.7+5.0)2·0.3·0.5·4+500·4=2457 (Нм).
Определим момент сил инерции:
где: J=γ Jпч– момент инерции относительно оси поворота вращающихся частей крана т·м2;
γ=1.2 1.4 – коэффициент учета инерции вращающихся частей;
= [а]L – угловое ускорение радс2;
[а] – допускаемое ускорение равное 0.10 м с2; [4табл 2.16]
=1.3 1.4 – коэффициент приведения геометрических радиусов к радиусам инерции;
xi – расстояние от вращающейся части до оси поворота м.
Тин=·γ··Σ mi·xi2=0.037·(207·0.52+288·0.52+85·(0.5·4.5)2+(55+1000) · ·4.52)=811 (Нм).
Таким образом момент сопротивления повороту крана действующий в период разгона будет равен:
Т= Тин+ Твет+ Ттр=811+2457+32.17=3300 (Нм).
Статический момент сопротивления:
Тст=Твет+ Ттр=2457+32.17=2489.17 (Нм).
Необходимая статическая мощность двигателя:
где: n – частота вращения кранаобмин;
=0.5 0.75 – КПД механизма [ 1табл 1.18].
Выбираем червячный редуктор Ч-80 с передаточным числом Uред=80 КПД-0.53 и масса – 20 кг.
Необходимое передаточное число зубчатой пары (шестерня-зубчатый венец):
Uз.п.=U Uред=36480=4.6.Принимаем 5.
Фактическая скорость вращения тогда будет равна:
Это составляет расхождение с номинальной частотой вращения 9%.
Определим расчетный момент для выбора муфты:
Выбираем ближайшую по требуемому крутящему моменту упругую втулочно–пальцевую муфту с тормозным шкивом диаметром Dт=100мм наибольшим передаваемым крутящим моментом 63 Нм. момент инерции муфты Iм=0.035 кгм2. [3табл.13.3.1].
Момент инерции вращающихся частей:
Iвр=Σ mi·xi2= Тин ·γ·=8110022·1.3·1.3=21917(кгм2).
Момент сил инерции при пуске на валу двигателя :
где : t =[]3·nпов – время поворота с;
[] – наибольший допускаемый угол поворота поворотной части при пуске равен 30° [1табл1.24 ];
Момент сопротивления на валу двигателя при пуске:
Тпуск=Тин+ТсU·=8.13+2489.17400·0.5=20.58(нМ).
Требуемая мощность двигателя при пуске:
условие : Pдв≥k Pпуск
где k=0.35 0.5 – коэффициент учитывающий допустимую перегрузку в момент пуска;
2≥0.95 –выполняется.
Момент сил инерции при торможении:
принимай что время пуска равно времени торможения:
Момент сопротивления на валу тормоза:
Тт=Тин.т-Тс.т= Тин.т-(Ттр-Тв)U ; (4.16)
Тт=3.23-(32.17-2457)·0.5400=6.3 (нМ).
Выбираем тормоз ТКТ –100100 со следующими параметрами: тормозной момент 20 Н·м диаметр тормозного шкива Dт=100мм [табл.III.5.11].
3 Расчет зубчатой передачи.
Принимаем число зубьев шестерни z1=20 тогда число зубьев на зубчатом венце:
Модуль зацепления для данной пары принимаем 5 мм тогда диаметры делительных окружностей будут соответственно равны:
d1= z1·m=20·5=100 (мм);
d2= z2·m=100·5=500 (мм).
Закрепление зубчатого колеса на выходном валу от редуктора осуществляем при помощи шлицевого соединения.
Расчет металлоконструкции стрелы
Расчет ведем в соответствии с рекомендациями изложенными в литературе [4][6].
При проектировании металлоконструкции стрелы поворотного крана на колонне составим расчетную схему металлоконструкции определим все силовые факторы действующие на нее определим усилия в стержнях подберем соответствующие профиля для раскосов стоек и поясов исходя из максимальных напряжений возникающих в сечении спроектируем конструкцию стрелы с обозначением всех соединений и соединительных элементов.
1 Выбор расчетной схемы и определение опорных реакций.
При выборе расчетной схемы будем руководствоваться следующими значениями: - максимальный вылет 5 м - грузоподъемность 1000 кг.
Рисунок 8 – Расчетная схема металлоконструкции стрелы.
Для определения опорных реакций составим уравнения статики:
Последовательно подставляя значения получим:
: Ra·0.7+(mт+Q)g·4=0; Ra=-40.7·(55+1000) ·9.81=-66.5(кН);
: (mт+Q)g·0.5+ Ra·0.7- Rby·5.1=0; Rby=15.1·((55+1000)· ·9.81·0.5+66.5·0.7)=10.35(кН).
2 Определение усилий в стержнях фермы.
При определении усилий в стержнях заменим нагрузку (mт+Q)g действующую на максимальном вылете распределенной по всей длине ездового пояса равной:
Рисунок 9 - Расчетная схема металлоконструкции стрелы.
Для определения усилий во всех стержнях воспользуемся методом моментной точки.
ΣМG=0; N10·cos8· 0.24-qd· 1.7-qd2· 3.4+Rby· 3.4-Ra· 0.7=0;
N10=10.24·cos8(3.45·1.7+1.73·3.4-10.35·3.4+66.5·0.7)=97(кН);
ΣF N10·cos8+N11+Rby-Ra=0;
N11= -97·0.99= -96(кН).
ΣМG=0; N6·cos8· 0.24-qd· 1.7-qd2· 3.4+Rby· 3.4-Ra· 0.7=0;
N6=10.24·cos8(3.45·1.7+1.73·3.4-10.35·3.4+66.5·0.7)=97(кН);
ΣМD=0; N7·0.47+qd2·1.7+Rb
N7=10.47(-1.73·1.7-66.5·0.47+10.35·1.7-66.5·0.23)=-68(кН);
N8=1cos16(68-97·0.99)= -29(кН).
ΣМE=0; N2·cos8·0.47-qd2·1.7+Rby·1. 7-Ra0.7=0;
N2=1cos8·0.47(1.73·1.7-10.35·1.7+66.5·0.7)=68.5(кН);
N4=1cos22(66.5-68.5·0.99)=-2(кН).
N5=11.7(-29·0.96·0.23+29·0.27·1.7)=4(кН);
ΣМD=0; N1·1.7+Ra·0.23+N4·s
N1=11.7(-66.5·0.23+2·0.37·1.7-2·0.93·0.23)= -8.5(кН).
N9=97·0.13-1.73=11(кН).
Таблица № 3 – Значение усилий в стержнях металлоконструкции.
3 Подбор сечения стержней.
Расчет элементов металлоконструкции ведем по наиболее нагруженным элементам (наибольшие усилия).
Так для стоек максимальное усилие Nmax=11 кН для раскосов Nmax= -29 кН для верхнего пояса Nmax=97 кН для ездового пояса Nmax= -96 кН.
В качестве материала для профиля стержней выбираем сталь марки Ст3пс5 (т=220 МПа). Расчет ведем по допускаемым напряжениям.
А – площадь поперечного сечения двух профилей образующих стержень м2;
n – коэффициент запаса равный 1.4 [4табл1.13].
для верхнего пояса :
где: γ – коэффициент продольного изгиба (выбирается в зависимости от гибкости) [6табл.2.13];
m – коэффициент условий работы при двухстороннем креплении к фасонке равен 1.
для ездового пояса :
В качестве проката для стоек выбираем уголок равнополочный № 2.5 площадь сечения равна 1.43 см2 для верхнего пояса-уголок равнополочный № 5 площадь сечения равна 3.89 см2 для раскосов-уголок равнополочный №3.5 площадь сечения равна 2.17 см2 для ездового пояса с учетом диаметра ходовых колес тележки 200 мм выбираем швеллер № 24 площадь сечения равна 30.6 см2. Толщину фасонки в соответствии с рекомендациями принимаем 10 мм.
Устройства безопасности
Для обеспечения безопасности работы грузоподъемные машины с машинным приводом оборудуют автоматически действующими приборами безопасности. Эти устройства обеспечивают выключение: механизма подъема груза и механизма подъема стрелы перед подходом грузозахватного органа и стрелы к упору механизма передвижения крана или тележки имеющих скорость передвижения 32 ммин и более при подходе их к упорам 1; механизма передвижения грузоподъемной машины при подходе ее к другой машине работающей с ней на одних рельсовых путях; механизма поворота (для неполноповоротных машин) при подходе поворотной части к ее крайним положениям; механизма выдвижения телескопической части; механизма подъема кабины.
Стреловые краны кроме перечисленных устройств имеют указатели вылета стрелы и грузоподъемности соответствующей этому вылету. Одна из конструкций такого указателя показана на рис. 39. Сбоку на стреле крана шарнирно подвешена массивная стрелка 2 конец которой при изменении вылета указывает на значения вылета и грузоподъемности нанесенные на шкале 1. Эта шкала видна крановщику. Его помощнику с рабочего места видна шкала 3 на которой также нанесены значения вылета и грузоподъемности.
Рис. 39. Указатель вылета стрелы
Рис. 40. Ограничитель высоты подъема подвески крановой тележки
По этой шкале передвигается указатель 4 жестко соединенный со стрелкой 2.
Все стреловые передвижные и башенные краны снабжают ограничителями грузоподъемности автоматически отключающими механизмы в случае подъема груза вес которого превышает грузоподъемность крана более чем на 10% для установленного вылета.
Ограничитель высоты подъема устанавливаемый на кранах мостового типа показан на рис. 40. Рычаг конечного нормально-разомкнутого выключателя типа КУ установленного на тележке соединен тросом 1 с шарнирно закрепленным рычагом 2 на конце которого помещается груз 3. Благодаря этому грузу рычаг конечного выключателя удерживает контакты в замкнутом положении. При достижении крюковой подвеской 4 крайнего верхнего положения она поднимает рычаг 2 трос ослабляется и контакты конечного выключателя размыкаются выключая тем самым электродвигатель механизма подъема.
Рис. 41. Ограничитель высоты подъема подвески электротали
При конструировании ограничителей высоты подъема следует иметь в виду что конечный выключатель механизма подъема должен останавливать грузозахватный огран без груза на расстоянии не менее чем 50 мм до верхнего упора у электроталей и 200 мм у всех других грузоподъемных машин.
Отключение механизмов передвижения грузоподъемной машины или тележки а также механизмов поворота производится конечными выключателями нормально-замкнутого типа на рычаги которых воздействуют специальные линейки. На кранах мостового типа выключатели ограничивающие путь передвижения тележки устанавливают на мосту а отключающую линейку—на тележке (например линейка 5 на рис. 40). Для выключения механизмов передвижения мостовых кранов конечные выключатели устанавливают на мосту а отключающие линейки —на подкрановых балках. На кранах передвигающихся по наземным подкрановым путям конечные выключатели устанавливаются на металлоконструкции крана и отключаются линейками укрепленными на шпалах путей. Конечный выключатель механизма передвижения устанавливают таким образом чтобы отключение электродвигателя происходило на расстоянии до упора равном не менее половины пути торможения механизма. При установке ограничителей хода на механизме передвижения для предупреждения столкновения двух грузоподъемных машин работающих на одном пути указанное расстояние может быть уменьшено до 05 м. На рис. 42 показана одна из возможных конструктивных схем ограничителя грузоподъемности. На коротком плече рычага 1 закреплен блок грузового каната. Второе плечо соединено штоком с пружиной 2. При превышении допустимой нагрузки пружина сжимается и планка 3 нажимает на шток конечного выключателя 4.
Ограничитель грузового момента электрического типа пригоден для установки на всех кранах и состоит из трех частей: датчика усилий датчика угла поворота стрелы (корректирующего устройства) и релейного блока.
Рис. 44. Датчик усилий Рис. 45. Датчик угла наклона
Датчик усилий 1 устанавливают между растяжками соединяющими оголовок стрелы с подвижной обоймой полиспаста. Другая часть ограничителя — датчик 2 угла наклона стрелы устанавливают соосно с осью поворота стрелы; его вал связан со стрелой рычагом. Релейный блок 3 размещенный в кабине крановщика подает с выдержкой 2—3 сек команду в цепь управления краном.
Датчик усилий (рис. 44) представляет собой кольцевую пружину которая при помощи тяг включается в систему стрелоподъемных канатов. Кольцевая пружина соединяется с передаточным механизмом спиральной пружиной. Механизм преобразует линейное перемещение тяг в угловое и черезпружинную муфту вращает ось потенциометра. При увеличении натяжениястрелоподъемных канатов угол образованный растяжками стрелы увели-чивается. Пружинное кольцо деформируется и происходит перемещение движка потенциометра т. е. линейноеперемещение кольца преобразуется в электрический сигнал. Вал 1 датчика угла наклона стрелы (рис. 45) связан со стрелой рычагом.
Мероприятия по технике безопасности (с указанием ссылок на ТНПА)
Правила устройства и безопасной эксплуатации грузоподъемных кранов [2] (далее - Правила) разработаны в соответствии с Законом Республики Беларусь от 10 января 2000 года "О промышленной безопасности опасных производственных объектов" (Национальный реестр правовых актов Республики Беларусь 2000 г. № 8 2138) и обязательны для всех организаций независимо от их организационно-правовой формы и формы собственности а также для индивидуальных владельцев грузоподъемных кранов.
Правила устанавливают требования к проектированию устройству изготовлению реконструкции монтажу установке ремонту эксплуатации и диагностированию грузоподъемных кранов их узлов и механизмов включая приборы и устройства безопасности а также грузозахватных органов грузозахватных приспособлений и тары.
Правила распространяются на:
- краны всех типов включая мостовые краны-штабелеры с машинным приводом и краны-манипуляторы (далее - краны);
- грузовые электрические тележки передвигающиеся по надземным рельсовым путям совместно с кабиной управления (далее - краны);
- краны-экскаваторы используемые для работы только с крюком подвешенным на канате или электромагнитом (далее - краны);
- электрические тали;
- подъемники крановые;
- лебедки с машинным приводом предназначенные для подъема груза и (или) людей;
- грузозахватные органы;
- грузозахватные приспособления;
- тару за исключением специальной тары применяемой в металлургическом производстве а также в морских и речных портах требования к которой устанавливаются отраслевыми правилами и (или) нормами.
Машинист грузоподъемных кранов обязан:
- знать требования Правил;
- знать инструкцию для машинистов грузоподъемных кранов а также инструкцию завода-изготовителя по монтажу и эксплуатации крана;
- знать безопасные способы строповки зацепки грузов и складирования;
- контролировать работу стропальщика и отвечать за действия прикрепленного к нему для прохождения стажировки ученика а также за нарушения требований изложенных в Правилах должностной инструкции и инструкции завода-изготовителя по монтажу и эксплуатации крана;
- проверять наличие приборов и устройств безопасности на кране (конечных выключателей указателя грузоподъемности в зависимости от вылета стрелы сигнального прибора аварийного рубильника ограничителя грузоподъемности анемометра нулевой блокировки); проверять исправность съемных грузозахватных приспособлений и тары; сообщать о замеченных неисправностях железнодорожного пути ответственному за безопасное производство работ кранами;
- производить работы с использованием крана только по сигналу стропальщика. Если стропальщик дает сигнал действуя вопреки инструкции то машинист по такому сигналу не должен производить требуемый маневр крана. За повреждения причиненные действиями крана вследствие выполнения неправильно поданного сигнала несут ответственность как машинист так и стропальщик подавший неправильный сигнал. Обмен сигналами между стропальщиком и машинистом должен производиться по установленному в организации порядку. Сигнал "Стоп" крановщик обязан выполнять независимо от того кто его подает;
- определять по указателю грузоподъемности грузоподъемность крана для каждого вылета стрелы. При работе крана на уклоне а железнодорожного крана также по кривой когда указатель вылета не учитывает уклона вылет стрелы определять фактическим промером при этом замеряется горизонтальное расстояние от оси центральной колонны крана до центра свободно висящего крюка;
- перед подъемом груза предупредить стропальщика и всех находящихся около крана лиц о необходимости уйти из зоны поднимаемого груза и возможного опускания стрелы. Перемещение груза можно производить только при отсутствии людей в зоне работы крана.
Указанные требования машинист должен выполнять также при подъеме и перемещении грейфера или грузоподъемного магнита; при погрузке и разгрузке вагонеток автомашин и прицепов к ним железнодорожных полувагонов и платформ убедиться в отсутствии людей на транспортных средствах; устанавливать крюк подъемного механизма над грузом так чтобы при подъеме груза исключалось косое натяжение грузового каната; при подъеме груза массой близкой к разрешенной грузоподъемности для данного вылета стрелы поднять его на высоту не более 200-300 мм чтобы убедиться в устойчивости крана и исправности действия тормозов после чего производить его подъем на нужную высоту; при подъеме стрелы следует следить чтобы она не поднималась выше положения соответствующего наименьшему рабочему вылету; при подъеме и опускании груза находящегося вблизи стены колонны штабеля железнодорожного вагона автомашины станка или другого оборудования предварительно убедиться в отсутствии людей между поднимаемым грузом и указанными частями здания транспортными средствами или оборудованием а также в невозможности задевания стрелой или поднимаемым грузом стен колонн вагона и других
препятствий. Укладка грузов в полувагоны на платформы и вагонетки а также снятие его должны производиться без нарушения равновесия полувагонов вагонеток и платформ и под наблюдением лица ответственного за безопасное производство работ кранами; перед подъемом груза из колодца канавы траншеи котлована и перед опусканием груза в них предварительно убедиться путем опускания порожнего (ненагруженного) крюка в том что при его низшем положении на барабане остается не менее 15 витка каната не считая витков находящихся под зажимным устройством; укладывать и разбирать грузы равномерно без нарушения установленных для складирования грузов габаритов; внимательно следить за канатами в случае спадания их с барабана или блоков образования петель или обнаружения повреждений канатов необходимо приостановить работу крана.
Машинист грузоподъемного крана несет ответственность за нарушения требований Правил; ему запрещается:
- устанавливать кран под действующей линией электропередачи любого напряжения. Устанавливать кран или производить перемещение груза на расстоянии ближе 30 м от крайнего провода линии электропередачи машинист может только при наличии наряда-допуска подписанного главным инженером или главным энергетиком организации являющейся владельцем крана. Работа крана в этом случае должна производиться под непосредственным руководством ответственного лица назначенного приказом по организации с указанием его фамилии в наряде-допуске;
- при наличии у крана двух механизмов подъема одновременная их работа. Крюк неработающего механизма должен быть всегда поднят в наивысшее положение;
- отключать приборы безопасности;
- производить подъем или опускание груза когда в зоне работы крана находятся люди;
- допускать к обвязке или зацепке грузов лиц не имеющих удостоверения стропальщика а также применять грузозахватные приспособления без бирок или клейм. Машинист в этих случаях должен прекратить работу краном и поставить в известность лицо ответственное за безопасное производство работ кранами;
- поднимать или кантовать груз масса которого превышает грузоподъемность крана для данного вылета стрелы. Если машинист не знает массы груза то он должен получить в письменном виде сведения о массе груза у лица ответственного за безопасное производство работ кранами;
- опускать стрелу с грузом до вылета при котором грузоподъемность крана будет меньше массы поднимаемого груза;
- производить резкое торможение при повороте стрелы с грузом;
- подтаскивать груз по земле рельсам и лагам крана при косом натяжении канатов а также передвигать железнодорожные вагоны платформы вагонетки или тележки при помощи крюка;
- поднимать крюком или грейфером груз засыпанный землей или примерзший к земле заложенный другими грузами укрепленный болтами
или залитый бетоном;
- освобождать краном защемленные грузом съемные грузозахватные приспособления;
- поднимать железобетонные изделия с поврежденными петлями неправильно обвязанный груз находящийся в неустойчивом положении подвешенный за рог двурогого крюка а также в таре заполненной выше бортов;
- укладывать груз на электрические кабели и трубопроводы а также на краю откоса или траншеи;
- поднимать груз с находящимися на нем людьми а также груз выравниваемый массой людей или поддерживаемый руками;
- передавать управление краном лицам не имеющим прав на управление краном а также допускать к самостоятельному управлению учеников и стажеров без своего наблюдения за ними;
- производить погрузку и разгрузку автомашин при нахождении людей в кабине;
- поднимать баллоны со сжатым или сжиженным газом не уложенные в специальные контейнеры.
Список использованных источников
А.В. Кузьмин Ф.Л. Марон .Справочник по расчетам механизмов подъемно– транспортных машин-Высшая школа 1983.-350с.
Правила устройства и безопасной эксплуатации грузоподъемных кранов-Мн.:2006.-123с.
А.Т. Скойбеда.Детали машин.Проектирование-Мн.:2001.-290с.
С.А.КазакВ.Е.Дусье и др.Курсовое проектирование грузоподъемныхмашин-Высш.шк.1989.-319с.
М.П. Александров М.М. Гохберг.Подъемно-транспортные машины:Атлас конструкций-М.:Машиностроение1987.-122с.
И.Н.ЖивейновГ.Н.КарасевИ.Ю.Цвей. Строительная механика и металлоконструкции строительных и дорожных машин: Учебник для вузов по специальности «Строительные и дорожные машины и оборудование». М.: Машиностроение 1988. – 280с.
титул.docx
Белорусский национальный технический университет
Кафедра: «Строительные и дорожные машины»
по предмету: «Подъемно-транспортные машины»
на тему: «Стационарный кран на поворотной колонне с переменным вылетом»
Обзор литературных и патентных источников ..
Расчет механизма подъёма груза .
Расчет механизма передвижения грузовой тележки
Расчет механизма поворота крана
Расчет металлоконструкции стрелы
Устройства безопасности
Мероприятия по технике безопасности
(с указанием ссылок на ТНПА) ..
Список использованных источников ..
Приложение А Спецификация