Редуктор ПК-2202 технологический процесс




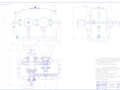
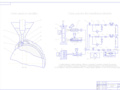
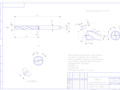
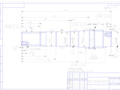
- Добавлен: 25.10.2022
- Размер: 1 MB
- Закачек: 0
Описание
Состав проекта
![]() |
![]() |
![]() |
![]() ![]() |
![]() ![]() |
![]() ![]() ![]() ![]() |
![]() ![]() ![]() ![]() |
![]() |
![]() ![]() ![]() ![]() |
![]() ![]() ![]() ![]() |
![]() ![]() ![]() ![]() |
![]() ![]() |
![]() ![]() |
![]() ![]() ![]() ![]() |
![]() ![]() |
![]() ![]() |
![]() |
![]() ![]() |
![]() ![]() ![]() ![]() |
![]() |
![]() ![]() ![]() |
![]() ![]() ![]() |
![]() ![]() ![]() |
Дополнительная информация
восстановление.dwg

-аппарат для наплавления; 8-горелка; 9-вращатель; 10-воздуховод (вытяжка); 11-восстанавливаемая деталь;
-стол сварщика; 13-фильтр-масловлагоотделитель; 14-камера струйной обработки; 15-стол; 16-печь для сушки порошка.
Схема процесса наплавки
Схема участка восстановления деталей
Редуктор.dwg

Вращающий момент на тихоходном валу
Частота вращения тихоходного вала
Общее передаточное число 22.9
Коэфициент полезного действия 0
Технические требования:
Необработанные поверхности литых деталей
находящихся в масленной ванне красить
маслостойкой краской.
Наружные поверхности корпуса красить
серойэмалью ПФ-15 ГОСТ 6465-76
Плоскость разъёма покрыть тонким слоем
герметика УТ-34 ГОСТ 24285-80 при
окончательной сборке.
резец.dwg

Материал стержня: сталь 45 ГОСТ 1050-88
Пластину паять припоем Л63 ГОСТ 15527-70
Маркировать: материал режущей части
Общие допуски по ГОСТ30893.1: +
сверло.dwg

так и без кондуктора.
Сверла изготавливаются шлифованием из гладких цилиндрических
стержней твердого сплава ВК6М и ВК60М (по ГОСТ 3882-74)
Маркировать РГКРИПТ 120101.4115.004
Общие допуски по ГОСТ30893.1: +
Геометрия режущей части (5:1)
Заготовка.dwg

Недопускается наличие выемок
Качество поверхности поковки должно соответствовать
ГОСТ977-88 для поковок 1-го класса точности
Вал ПК-2202.dwg

Технология 1.dwg

035-2317-1028 ГОСТ 4010-77
=53 С подрезкой торца
Фрезеровать 14 шлицев 47х3
Сверлить два отверстия
2301-0189 ГОСТ10903-77
Нарезать резьбу М8-7Н в двух отверстиях
Шлиовать поверхность
Карта технологического процесса.
Обозначение документа
Код заготов. Профиль и разм.
Сталь 40Х ГОСТ 14637-89.
наименование операци
Код и наименование оборудования
Заготовительная - поковка
Фрезерно-центровальная
Установить заготовку
Предъявить деталь ОТК
Патрон 37 кулачковый ГОСТ 2675-80
Подрезать торец начисто
Резец подрезной РО-742
Перевернуть заготовку
Резец проходной РО-746
Притупить острые кромки
Метчик М8-7Н 2620-1225 ГОСТ 3266-81
Круг шлифовальный 1-600х63х305 24А 40 СТ 25К ГОСТ 2424-80
Моя ЗАПИСКА.doc
Однако под «технологией машиностроения» принято понимать научную дисциплину изучающую преимущественно процессы механической обработки деталей и сборки машин и попутно затрагивающую вопросы выбора заготовок и методы их изготовления. Это объясняется тем что в машиностроении заданные формы деталей с требуемой точностью и качеством их поверхностей достигаются в основном путем механической обработки так как другие способы обработки не всегда могут обеспечить выполнение этих технических требований. В процессе механической обработки деталей машин возникает наибольшее число проблемных вопросов связанных с необходимостью выполнения технических требований поставленных конструкторами перед производством. Процесс механической обработки связан с эксплуатацией сложного оборудования — металлорежущих станков; трудоемкость и себестоимость механической обработки больше чем на других этапах процесса изготовления машин.
Эти обстоятельства объясняют развитие «технологии машиностроения» как научной дисциплины в первую очередь в направлении изучения вопросов технологии механической обработки и сборки в наибольшей мере влияющих на производительную деятельность предприятия.
Сложность процесса и физической природы явлений связанных с механической обработкой вызвала трудность изучения всего комплекса вопросов в пределах одной технологической дисциплины и обусловила образование нескольких таких дисциплин. Так явления происходящие при снятии слоев металла режущим и абразивным инструментом изучаются в дисциплине «Учение о резании металлов»; изучение конструкций режущих инструментов и материалов для их изготовления относится к дисциплине «Режущие инструменты».
Эти специализированные технологические дисциплины сформировались раньше чем комплексная дисциплина «Технология машиностроения».
В «Технологии машиностроения» комплексно изучаются вопросы взаимодействия станка приспособления режущего инструмента и обрабатываемой детали; пути построения наиболее рациональных т. е. наиболее производительных и экономичных технологических процессов обработки деталей машин включая выбор оборудования и технологической оснастки; методы рационального построения технологических процессов сборки машин. Таким образом научная дисциплина «Технология машиностроения» изучает основы и методы производства машин являющиеся общими для различных отраслей машиностроения.
Таким образом научная дисциплина «Технология машиностроения» изучает основы и методы производства машин являющиеся общими для различных отраслей машиностроения.
Начало формирования этой дисциплины относится к тридцатым годам нашего столетия. Развитие технологии механической обработки и сборки и ее направленность обусловливаются стоящими перед машиностроительной промышленностью задачами совершенствования технологических процессов изыскания и изучения новых методов производства дальнейшего развития и внедрения комплексной механизации и автоматизации производственных процессов на базе достижений науки и техники обеспечивающих наиболее высокую производительность труда при надлежащем качестве и наименьшей себестоимости выпускаемой продукции.
1 Характеристика детали
Деталь ПК-2202 300005 является валом редуктора фронтального погрузчика ПК-2202 и служит для передачи крутящего момента от первичного вала к выходному валу редуктора. Вал редуктора изготовлен из Ст40Х ГОСТ 14637-89. Вал имеет длину 292 мм и максимальный диаметр 65 мм. Вал состоит из двух шлицевых частей двух опорных частей на которые одеваются подшипники. На концах вала имеются резьбовые отверстия 67х18.
Рисунок 1-Вал заднего хода
2 Физико-механические свойства материала детали
Таблица 1 – Общая характеристика
Сталь конструкционная легированная.Хромистая
Сталь 45Хсталь 38ХАсталь 40ХНсталь 40ХСсталь 40ХФАсталь 40ХГТР
AISI 5135AISI 5135 HAISI 5140AISI 5140 H
оси валы вал-шестерни плунжеры штоки коленчатые и кулачковые валы кольца шпиндели оправки рейки губчатые венцы болты полуоси втулки и другие улучшаемые детали повышенной прочности.
Химический состав в % материала Ст40Х
Таблица 2 – Химический состав стали 40Х
Технологические свойства
Таблица 3 – Технологические свойства стали 40Х
Начала 1250 конца 800. Сечения до 350 мм охлаждаются на воздухе.
трудносвариваемая. Способы сварки: РДС ЭШС. Необходимы подогрев и последующая термообработка. КТС - необходима последующая термообработка.
Обрабатываемость резанием
В горячекатаном состоянии при НВ 163-168 в= 610 МПа K тв.спл. = 0.20 K б.ст. = 0.95.
Склонность к отпускной способности
Флокеночувствительность
Физические свойства стали 40Х
Таблица 4 – Физические свойства стали 40Х
Температура испытания °С
Модуль нормальной упругостиE ГПа
Модуль упругости при сдвиге кручениемG ГПа
Коэффициент тепло-проводностиlВт(м ·°С)
Уд. электросопротивление (R 10 9 Ом·м)
Коэффициент линейного расширения (a 10-6 1°С)
Удельная теплоемкость (С Дж(кг · °С))
Температура критических точек
Таблица 5 – Температура критических точек
3.1 Качественная оценка
Форма детали является правильной геометрической является телом вращения. Значение шероховатостей поверхностей (Ra 25) соответствует классам точности их размеров и методам обработки этих поверхностей.
Для обработки детали достаточно использовать токарную сверлильную и фрезерную операции. Деталь обладает достаточно большой жесткостью что обеспечивает высокую точность при токарных операциях. Деталь не имеет сложных конструктивных элементов для ее обработки требуется минимальный набор инструментов и приспособлений. Имеется свободный отвод и подвод режущего и мерительного инструмента к обрабатываемым поверхностям. Многообразие размеров сведено к минимуму.
3.2 Количественная оценка
Количественная оценка определяет рациональное использование материала заготовки. И выражена коэффициентом использования материала.
где - масса готовой детали кг
Масса готовой детали равна 4 кг длина детали составляет 292 мм а максимальный диаметр 65 мм. В качестве заготовки используется круг диаметром 65мм.
Где V-объём заготовки
-плотность материала
Так как коэффициент использования меньше 07 то целесообразным будет выбор другой заготовки.
Взяв заготовку сделанную методом поковки коэффициент использования материала увеличится.
Рисунок 2 - Заготовка вала
Объём заготовки изготовленной методом поковки V=00005767 м
Так как коэффициент использования больше 07 то использование такой заготовки будет целесообразным.
4 Определение типа производства
Тип производства зависит от двух факторов а именно: заданной программы и трудоемкости изготовления изделия. Тип производства определяют с помощью коэффициента серийности:
где tB - такт выпуска изделия миншт;
Tшт - среднее штучное временя по операциям действующего производства.
Величина такта выпуска рассчитывается по формуле:
где FД - действительный годовой фонд времени работы оборудования чсм (FД =2070 чсм по таблице 3 и 5 [1]);
N - годовая программа выпуска деталей(N=800 шт).
Подставим в формулу (2) числовые результаты:
Формула для расчета среднего штучного времени имеет следующий вид:
Определим коэффициентом серийности по формуле (3):
Так как коэффициент серийности находится в пределах от 10 до 20 то типа производства – среднесерийное [1].
5 Выбор варианта заготовки и ее технико-экономическое
Метод выполнения заготовок для деталей машин определяется назначением и конструкцией детали материалом техническими требованиями масштабом и серийностью выпуска а также экономичностью изготовления. Выбрать заготовку - значит установить способ ее получения.
Получение заготовки с помощью сортового проката применяется преимущественно для крупносерийного производства так как этот способ является очень производительным производительность находится в пределах 300-400 штчас. При данном способе меньше отходов металла однако для конкретного случая этот способ получения заготовок не подходит в следствии того что производство является среднесерийным с объемом выпуска 800 штук в год. Оборудование предназначенное для получения данного вида заготовок будет простаивать большую часть времени.
Получение заготовки литьем имеет много преимуществ таких как возможность получения сложной конфигурации детали возможность получение точности заготовки с минимальной последующей обработкой. Но данный метод рентабельно применять при массовом и крупносерийном производстве где число деталей более 2000 штук.
Получение заготовки методом поковки является наиболее подходящим способом для ее производства. Данный вид не требует специального оборудования такого как печи для плавки металла. Существенным преимуществом данного способа является наименьшее количество отходов материала.
Затраты на изготовление заготовки из сортового проката определяются по следующей формуле:
где Q - масса заготовки кг (Q=721 кг);
S - цена 1 кг материала заготовки руб (S=226 руб);
q - масса готовой детали кг (q=4 кг);
Sотх - цена 1 т отходов руб (Sотх=8000 руб).
Подставим значения в формулу (4):
Стоимость получения заготовок методом поковки определяем по формуле:
где С1 – базовая стоимость 1 тонны заготовок руб;
- коэффициенты зависящие от класса точности группы сложности массы марки материала и объема производства заготовок (принимаем по справочным данным приведенным в [1] - для поковок из черных металлов 2 класса точности; - для поковок второй группы сложности; - для поковок из стали имеющей вес в пределах от 3 до 8 кг; -для углеродистой стали; - для 3-его класса серийности поковок из стали).
Стоимость применения заготовок полученных поковкой значительно меньше стоимости применения заготовок из проката следовательно целесообразно изменить вид заготовки для уменьшения себестоимости работ по изготовлению детали.
6 Анализ базового технологического процесса
Заготовкой для вала редуктора является прокат круглого сечения что является целесообразно для применения его при данном типе производства. Деталь является технологичной имеет простую форму.
Заготовка удовлетворяет всем техническим требованиям указанным на чертеже.
Существенным недостатком технологического процесса является то что обработка детали осуществляется на устаревшем оборудовании с использованием несовершенных инструментов что вызывает снижение производительности и приводит к большому проценту брака.
Так как деталь не является сложной для контроля ее качества требуется небольшое число приспособлений и инструмента.
Одним из недостатков технологического процесса является трудоёмкость изготовления детали. Устранением этого недостатка является упрощение технологического процесса (выбор другой заготовки).
7 Выбор технологических баз
В качестве размерной базы во время обработки детали точение используют левый торец винта. В качестве поверхности воспринимающей зажимные силы принимают головку винта.
8 Выбор технологического оборудования приспособлений регулирующего и измерительного инструмента.
Технологическое оборудование приспособления регулирующий и измерительный инструмент применяемый для производства детали вал редуктора представлены в таблице 4.
Таблица 4 – Перечень технологического оборудования приспособлений инструментов
Приспособления инструмент
токарно-винторезный станок 1К62;
резец 1820-0552 ГОСТ 18869-73
резец 2100-0552 ГОСТ 18869-73
резец 1700-0402 ГОСТ 18869-73
резец 1128-02115 ГОСТ 18869-73
токарно-винторезный станок 1К62; ГОСТ 19257-73
Фрезерный станок МР-73; ГОСТ 18101-85
Расчет припусков на механическую обработку
Заготовка представляет собой поковку массой 449 кг. Технологический процесс обработки вала 50К6() состоит из двух операций: чернового чистового растачивания выполняемых при одной установке детали
Расчет припусков произведем двумя методами: для размера 50К6() рассчитаем припуски аналитическим методом а для остальных размеров - опытно статическим.
Аналитический метод определения припусков базируется на анализе производственной погрешности возникающей при конкретных условиях обработки заготовки.
Минимальный припуск при обработке поверхности вала определяется по формуле:
где Rz - высота неровности профиля мкм;
ρ - суммарное отклонение расположения поверхностей мкм;
ei - погрешность установки заготовки мкм (при установке в самоцентрирующихся патронах e=0).
Результаты расчетов и исходные данные сводим в таблицу 5.
Подставим числовые значения в формулу (6):
Минимальный максимальный а так же расчетный диаметр определим по формулам:
dp – расчетный диаметр мм;
– допуск на размер мм;
zmin – расчетный припуск мм.
Подставим числовые значения в формулы (7) (8) (9):
Минимальный и максимальный припуск определяется по формулам:
Подставим числовые значения в формулы (10) (11):
Для определения правильности расчетов произведем проверку соблюдения условия:
Таблица 5 – Расчет припусков на механическую обработку
Элементы припуска мкм
На рисунке 4 представлена схема расположения припусков и допусков для размера 50k6.
Рисунок 4 – Схема расположения припусков и допусков для размера 50k6
Для остальных размеров припуски определяются опытно-статическим методом путем выбора стандартных значений припуска для каждой поверхности по таблицам [2]. Результаты занесем в таблицу 6.
Таблица 6 – Значения припусков
Вид окончательной обработки
Расчет режимов резания
Операция 005. Фрезерно-центровальная.
Оборудование: Фрезерный станок МР-73; Фреза Д-200.
Переход 1: Фрезеровать торцы
Глубина резания: t=25 мм
Скорость резания: при фрезеровании скорость резания определяется по формуле:
где K1 – коэффициент зависящий от материала (K1=09);
К2 – коэффициент зависящий от стойкости и марки твердого сплава (К2=14);
К3 – коэффициент зависящий от вида обработки (К3=105).
Vтабл – стандартная скорость резания (Vтабл=90 ммин).
Подставим числовые значения в формулу (9):
Частота вращения определяется по формуле:
Принимаем частоту вращения nст=600 мин-1.
Уточним скорость резания по принятой частоте вращения:
Переход 2: сверлить отверстие 63 мм.
Сверло 63 2317-0020 ГОСТ 14952-75
Глубина резания: t=20 мм
Охлаждение: эмульсия.
Подача: при сверлении отверстия выбирают максимальную подачу допустимую по прочности сверла: S=04 мм.
Скорость резания: скорость резания при сверлении определяется по формуле:
где T – значение периода стойкости инструмента (T=60);
KV – общий поправочный коэффициент на скорость резания учитывающий фактические условия резания определяется по формуле:
где KMV - поправочный коэффициент учитывающий материал резания (KMV=1);
KUV - поправочный коэффициент учитывающий влияние материала режущей части инструмента (KUV=083);
KLV – поправочный коэффициент учитывающий изменение скорости от глубины сверления (KLV=1).
Значения коэффициента CV и показатели степени равны: CV=98; q=04; Y=05; m=02.
Подставим числовые значения в формулу (14):
Подставим числовые значения в формулу (13):
Предъявить деталь ОТК.
Операция 005-01. Токарная.
Оборудование: токарно-винторезный станок 1К62; резец РО-742
Переход 1: Подрезать торец начисто.
Скорость резания: при точении скорость резания определяется по формуле:
К2 – коэффициент зависящий от стойкости и марки твердого сплава (К2=14)
Принимаем частоту вращения nст=1500 мин-1.
Переход 3: Перевернуть заготовку.
Переход 4: Подрезать торец начисто.
Переход 5: сверлить отверстие 63 мм.
Операция 010 Токарная
Оборудование: токарно-винторезный станок 1К62;
Переход 1: точить поверхность 58 мм на расстояние L=219 мм. Чистовое точение.
Глубина резания: t=35 мм
Скорость резания: при точении скорость резания определяется по формуле (9):
К3 – коэффициент зависящий от вида обработки (К3=104).
Частота вращения определяется по формуле (10):
Уточним скорость резания по принятой частоте вращения (11):
Переход 2: точить поверхность 53 мм на расстояние L=183 мм. Чистовое точение.
Принимаем частоту вращения nст=700 мин-1.
Переход 3: точить поверхность 50 мм на расстояние L=111 мм. Чистовое точение.
Переход 4: Притупить острые кромки
Перевернуть деталь предъявить ОТК.
Операция 015 Токарная
Переход 1: точить поверхность 63 мм на расстояние L=53 мм. Чистовое точение.
Глубина резания: t=1 мм
Переход 2: точить поверхность 50 мм с подрезанием торца
Глубина резания: t=2 мм
Переход 3: Притупить острые кромки
Операция 020. Термическая
Операция 025. Токарная
Переход 1: Зачистка центровых отверстий
Переход 2: Перевернуть деталь
Переход 3: Зачистка центровых отверстий
Операция 030. Токарная
Переход 1: точить поверхность 475 мм на расстояние L=112 мм.
Принимаем частоту вращения nст=800 мин-1.
Переход 2: точить поверхность 485 мм на расстояние L=46 мм.
Глубина резания: t=23 мм
Переход 3: точить поверхность 505 мм на расстояние L=26 мм.
Глубина резания: t=13 мм
Переход 4: точить поверхность 555 мм на расстояние L=36 мм.
Переход 5: точить фаску на 475 мм.
Глубина резания: t=3 мм
К2 – коэффициент зависящий от стойкости и марки твердого сплава (К2=15);
Переход 6: точить фаску на 485 мм.
Переход 7: точить фаску на 65 мм.
Остальные режимы резания рассчитываются аналогично.
Таблица 12 – Режимы резания.
Скорость главного движения
Техническое нормирование
Технические нормы времени в условиях массового и серийного производства устанавливаются расчетно-аналитическим методом. При массовом и серийном производстве определяется норма штучного времени:
где Т0 – основное (технологическое) время мин;
ТВ – вспомогательное время мин (ТВ=40 мин по [2]);
Тобсл – время обслуживания рабочего места мин (Тобсл=45 мин по [2]);
Тотд – время перерыва на отдых и естественные потребности мин (Тотд=60 мин по [2]).
Основное время определяется по формуле:
где L – расчетная длина обработки мм;
n – частота вращения заготовки обмин;
s – подача инструмента за один оборот мм.
Подставим числовые значения в формулу (19):
Оставшееся время рассчитываем аналогично а полученные результаты заносим в таблицу 7.
Определим общее основное время обработки детали сложив время обработки на каждом переходе:
Подставим числовые значения в формулу (18):
Таблица 7 – Расчет основного времени на обработку детали
Восстановление детали
Эффективное использование машин и оборудования обеспечивается высоким уровнем их технического обслуживания и ремонта наличием необходимого числа запасных частей. Сбалансированное обеспечение запасными частями ремонтных предприятий и сферы эксплуатации машин и оборудования как показывают технико-экономические расчеты целесообразно осуществлять с учетом периодического возобновления работоспособности деталей восстановленных современными способами.
Восстановление деталей машин обеспечивает экономию высококачественного металла топлива энергетических и трудовых ресурсов а также рациональное использование природных ресурсов и охрану окружающей среды. Для восстановления работоспособности изношенных деталей требуется в 5 - 8 раз меньше технологических операций по сравнению с изготовлением новых деталей. Ежегодный экономический эффект от восстановления деталей составляет более 300 млн. руб.
Образование и развитие неисправностей в машине объясняется действием объективно существующих закономерностей. Неисправности машин появляются в результате постоянного или внезапного снижения физико-механических свойств материала деталей их истирания деформирования смятия коррозии старения перераспределения остаточных напряжений и других причин вызывающих разрушение деталей. В большинстве случаев происходят изменения в сопряжениях — нарушения заданных зазоров в подвижных соединениях или натягов в неподвижных. Практически любая неисправность является следствием изменения состава структуры или механических свойств материала конструктивных размеров деталей и состояния их поверхностей.
Появление неисправностей обусловлено конструктивными технологическими и эксплуатационными факторами.
К конструктивным факторам относятся: расчетные нагрузки скорости относительного перемещения давления материалы их физико-механические характеристики и структура конструктивное исполнение деталей и сборочных единиц форма и величина зазоров или натягов в сопряжениях макрогеометрия шероховатость и твердость поверхностей условия смазывания и охлаждения деталей. Технологическими факторами являются приемы способы точность и стабильность получения заготовок виды механической термической упрочняющей и финишной обработки при изготовлении деталей правильность сборки регулирования приработки и испытания узлов агрегатов и машин.
При восстановлении валов чаще всего применяется восстановление геометрии вала и изношенного слоя посредствам наплавки материала.
Процесс восстановления деталей состоит из следующих этапов:
) Приемка деталей. Приемка деталей на восстановление зависит от масштабов ремонтного производства и места выполнения работ. На ремонтных предприятиях детали восстанавливают партиями поступившими со склада деталей ожидающих ремонта в соответствии с заключением по результатам дефектации.
На централизованное восстановление принимают детали только определенной номенклатуры утвержденной в установленном порядке.
Детали сдаваемые на восстановление очищают от загрязнений до такого состояния чтобы их можно было осмотреть и выявить дефекты. Сборочные единицы поступают полнокомплектными.
) Очистка деталей. Очистка деталей от загрязнений является специфической операцией ремонтного производства. От качества и полноты проведения этой операции зависят культура производства производительность труда рабочих-ремонтников эффективность использования оборудования и в конечном итоге долговечность работы отремонтированных изделий. Если не удалить грязь на постах мойки то она разносится по цехам и попадая на постах сборки в трущиеся сопряжения вызывает их интенсивное изнашивание. Наличие жировых и других загрязнений на деталях подлежащих окраске или покрытию гальваническими и химическими способами приводит к шелушению и отслаиванию этих покрытий в процессе эксплуатации. Загрязнения на деталях восстанавливаемых наплавкой вызывают образование в наплавленном металле пор и раковин.
Организация и технология моечно-очистных работ зависит от типа предприятия его производственной программы вида загрязнений подлежащих удалению объекта мойки. Опыт работы ремонтных предприятий показывает что наиболее рациональной формой организации моечно-очистных работ является многостадийная мойка с использованием специальных способов очистки ответственных деталей.
) Дефектация деталей. Дефектацию деталей проводят с целью определить их техническое состояние: деформацию и износ поверхностей целость материала изменение свойств и характеристик рабочих поверхностей сохранность формы. Дефектацию деталей осуществляют в соответствии с таблицами дефектации технических условий или требований на ремонт машин.
Процесс дефектации в значительной мере определяет качество восстановленных деталей. При дефектации выполняют следующие операции. Вначале внешним осмотром невооруженным глазом или с применением лупы проверкой на ощупь простукиванием выявляют следующие повреждения деталей: трещины забоины риски обломы пробоины вмятины задиры коррозию ослабление плотности посадки.
Далее используя универсальный и специальный измерительный инструмент определяют геометрические параметры деталей. Для обнаружения скрытых дефектов проверки на герметичность упругость контроля взаимного положения элементов деталей используют специальные приборы и приспособления.
) Процесс восстановления. Наплавка по сравнению с другими способами восстановления дает возможность получать на поверхности деталей слой необходимой толщины и нужного химического состава высокой твердости и износостойкости.
- наплавляемая деталь; 2 - оболочка жидкого флюса; 3 - эластичная оболочка; 4 - бункер с флюсом; 5 - мундштук; 6 - электрод; 7 - электрическая дуга; 8 - шлаковая корка; 9 - наплавленный металл; а - смещение с зенита.
Рисунок 6 – Схема наплавки
Автоматическая наплавка под слоем флюса. При такой наплавке в зону горения дуги (рисунок 6) подают сыпучий флюс состоящий из отдельных мелких крупиц (зерен). Под воздействием высокой температуры часть флюса плавится образуя вокруг дуги эластичную оболочку которая надежно защищает расплавленный металл от действия кислорода и азота. После того как дуга переместилась жидкий металл твердеет вместе с флюсом образуя на наплавленной поверхности ломкую шлаковую корку. Флюс который не расплавился может быть снова использован. Наплавку под слоем флюса применяют для восстановления многих деталей тракторов автомобилей и сельскохозяйственных машин.
Автоматическая наплавка эффективна в тех случаях когда нужно наплавить слой толщиной более 3 мм (например при выполнении наплавки на деталях ходовой части тракторов и сельскохозяйственных машин - катках цапфах роликах осях и т. д.) глубокое проплавление нежелательно так как оно увеличивает деформацию детали. Главным фактором влияющим на глубину проплавления является сила тока:
где h - глубина проплавления мм;
кн - скорость наплавки мммин;
Влияние на глубину проплавления оказывает относительное размещение электрода и детали. В практике применяют наплавку углом вперед при которой глубина проплавления меньше чем при наплавлении углом назад. Глубина проплавления также уменьшается с увеличение вылета электрода.
Для наплавки под слоем флюса применяют устанавливаемые на токарных станках или специальных установках головки типов А 580 ОКС-Ю31Б ОКС-1252М.
Качество наплавленного металла и его износостойкость зависят от марки электродной проволоки флюса и режима наgлавки.
Для наплавки низкоуглеродистых и низколегированных сталей используют проволоку из низкоуглеродистых (Св-08 Св-08А) марганцовистых (Св-08Г Св-08ГА) и кремний-марганцовистых (Св-08ГС Св-08Г2С Св-12ГС) сталей.
Стали с большим содержанием углерода наплавляют проволокой Нп-65Г Нп-80 Нп-ЗОХГСА Нп-40Х13 (ГОСТ 10543—82). Флюсы подразделяют на плавленые керамические и флюсы-смеси.
Плавленые флюсы АН-348А АН-60 ОСУ-45 АН-20 АН-28 содержат стабилизирующие и шлакообразующие элементы но в состав этих флюсов не входят легирующие добавки что не способствует повышению прочности и износостойкости наплавленного металла.
Керамические флюсы АНК-18 АНК-19 ЖСН-1 кроме стабилизирующих и шлакообразующих элементов содержат легирующие добавки — ферросплавы которые при наплавке малоуглеродистой проволокой обеспечивают высокую твердость и износостойкость наплавленного металла.
Флюсы-смеси состоят из флюса АН-348А с добавлением феррохрома ферромарганца и графита. Смесь расстилают слоем 15—20 мм на листе сушат 15—25 мин при температуре 100—120 °С а затем просеивают через сито № 16 и высушивают при температуре 150—200 °С в течение 3—4 ч. Смешивая агломерат с флюсом в необходимом соотношении получают легирующий флюс применение которого позволяет получать наплавленный слой однородного химического состава высокой твердости и износостойкости.
При наплавке могут возникнуть такие дефекты:
- неравномерность ширины и высоты наплавленного валика из-за износа мундштука или подающих роликов;
- чрезмерного вылета электрода;
- наплыв металла вследствие чрезмерной силы сварочного тока или недостаточного смещения электродов из зенита;
- поры в наплавленном металле из-за повышенной влажности флюса (его необходимо просушить в течение 1—15 ч при температуре 250— 300 °С); неустойчивая дуга как следствие ненадежного контакта.
На качество восстановления значительно влияет режим наплавки.
В качестве источников питания дуги используют преобразователи ПСГ-500 выпрямители ВС-300 ВДУ-504 ВС-600 ВДГ-301 с жесткой внешней характеристикой.
Твердость и относительная износостойкость наплавленного металла в зависимости от марки электродной проволоки и флюса приведены в таблице 8.
Таблица 8 - Твердость и относительная износостойкость наплавленного металла в зависимости от марок электродной проволоки и флюса
Твердость покрытия HRC
) Контроль качества восстановления. Качество восстановления деталей оценивают степенью соответствия полученных физико-механических свойств и геометрических параметров заданным техническими условиями на восстановление детали и ремонтным чертежом аналогичным свойствам и параметрам.
При восстановлении деталей выполняют летучий промежуточный и окончательный контроль. Летучий контроль проводят выборочно как на отдельных операциях технологического процесса так и на готовых деталях. Промежуточный контроль выполняют пооперационно и по сгруппированным операциям. Проверку как правило осуществляют непосредственные исполнители работ а также мастера бригадиры руководители подразделений. Периодически промежуточный контроль проводят работники ОТК предприятия. Окончательный контроль всех восстановленных деталей проводят работники ОТК предприятия.
При обработке резанием проверяют соответствие размеров формы взаимного расположения обработанных поверхностей и их шероховатость требованиям ремонтных чертежей или технических условий. Для этой цели используют универсальные измерительные инструменты предельные калибры приспособления и приборы профилометры.
Периодически проверяют состояние технологического оборудования приспособлений режущего и измерительного инструмента на рабочих местах а также режимы обработки (скорость резания подачи припуск на обработку).
При контроле шейки валов и отверстия измеряют в нескольких плоскостях и сечениях. Шлицевые части валов и шлицевые ступицы контролируют по наружному и внутреннему диаметрам шлицев толщине каждого зуба (ширине впадины) универсальными средствами измерения комплексными калибрами или новыми сопрягаемыми деталями. Резьбовые части валов и отверстия проверяют калибром-кольцом и калибром-пробкой на всей длине резьбы взаимное расположение поверхностей — специальными приборами и приспособлениями с индикаторами.
При сварке и наплавке проверяют качество швов толщину наплавленного металла обрабатываемость плотность наплавленного металла и его твердость а также режим наплавки. Наплывы подрезы трещины кратеры непровары поры раковины шлаковые включения выявляют при осмотре невооруженным глазом и через лупу. Ответственные детали после предварительной обработки подвергают магнитной или ультрафиолетовой дефектоскопии.
Герметичность контролируют керосином или воздухом при определенном давлении а при необходимости — гидравлическим методом на специальных стендах. Твердость наплавленного металла определяют с использованием твердомеров.
Гальванические покрытия контролируют по внешнему виду осажденного металла. При осмотре может быть использована лупа. При контроле выявляют трещины поры отслоение осадка от основного металла дендритные наросты пятна пригар. Прочность сцепления осадка с основным металлом проверяют методом нанесения на поверхность осадка острым шабером перекрещивающихся царапин глубиной до основного металла и через лупу осматривают места царапин. Отслоение осадка в этих местах свидетельствует о плохой сцепляемости. В отдельных случаях сцепляемость проверяют на специальных образцах.
Твердость гальванических покрытий контролируют на приборе типа ПМТ-3 или с помощью твердомера Виккерса. В гальванических цехах систематически контролируют состав электролитов оборудование режим процесса качество подготовительных операций.
На термических участках контролируются режимы термообработки и твердость обработанных поверхностей с помощью твердомеров.
Для обеспечения высокой надежности контрольно-измерительных операций все измерительные приборы и инструмент должны периодически подвергаться проверке через установленные промежутки времени гарантирующие поддержание их точности в заданных пределах. Все приборы и инструмент должны быть обеспечены инструктивной документацией по правилам пользования.
В ходе выполнения курсового проекта было рассчитано и обосновано применение новой заготовки получаемой методом поковки. В связи с изменением заготовки был изменен технологический процесс вследствие чего сократилось время на обработку детали с 345 минут до 267 минут.
Благодаря тому что был изменен вид заготовки на более экономически выгодный и сократилось время изготовления детали удалось снизить себестоимость получения детали что благоприятно скажется на всем процессе производства и позволит экономить производственные мощности продляя тем самым ресурс оборудования.
Так же были рассчитаны режимы резания для каждой операции и каждого перехода. Режимы резания являются современными и производительными что так же позволяет снизить себестоимость изготовления детали.
В ходе расчетов были усовершенствованы режимы резания была увеличена скорость резания до значения 116 и 127 ммин что позволило так же сократить процесс обработки детали.
Вследствие изменения заготовки были изменены припуски на обработку которые после проведения расчетов составили всего 09 мм что значительно снизило время а так же количество материала идущего в отход.
ТЕХНИЧЕСКИЕ ХАРАКТЕРИСТИКИ 1К62
Наибольший диаметр обрабатываемой заготовки мм:
Наибольшая длина обрабатываемой заготовки мм
Размер внутреннего конуса в шпинделе
Диаметр цилиндрического отверстия в шпинделе
Число ступеней частот вращения шпинделя
Частота вращения шпинделя
Число ступеней рабочих подач:
Рабочие подачи ммоб:
Число нарезаемых резьб:
- архимедовой спирали
Шаг нарезаемой резьбы:
" 716" 8; 10 и 12 мм
Быстрые установочные перемещения суппорта ммин:
Размер внутреннего конуса в задней бабке
Наибольшее перемещение пиноли задней бабки мм
Поперечное смещение корпуса задней бабки мм
Наибольшее сечение резца
Давление воздуха МПа
Питание от электросети напряжением
Мощность электродвигателя главного привода кВт
Габаритные размеры станка мм:
Масса станкакг при длине обработки:
Список использованных источников
Горбацевич А.Ф. Курсовое проектирование по технологии машиностроения. Минск «Высшая школа» 1975 г.
Косилова А.Г. и Мещерякова Р.К. Справочник технолога машиностроителя. Том 1 и том 2 -М.: Машиностроение 1985.
Маталин А.А. Технология машиностроения.-М.: Машиностроение 1985 -496 с.
Балакшин Б.С. Технология машиностроения и конструкционных материалов.-М: Машиностроение 1969
Коренев А.П. Технологические процессы получения заготовок в машиностроительном производстве.
аннотация.doc
Графическая часть курсового проекта представлена на 3 листах формата А1:
- заготовка вал редуктора сверло резец;
- технологический процесс;
- редуктор восстановление детали;
Рекомендуемые чертежи
- 24.01.2023