Проектирование коробки скоростей для станка мод. 262



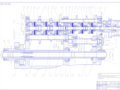
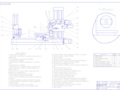
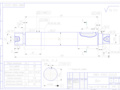
- Добавлен: 25.10.2022
- Размер: 5 MB
- Закачек: 0
Узнать, как скачать этот материал
Подписаться на ежедневные обновления каталога:
Описание
Проектирование коробки скоростей для станка мод. 262
Состав проекта
![]() |
![]() |
![]() ![]() ![]() ![]() |
![]() ![]() ![]() ![]() |
![]() ![]() ![]() ![]() |
![]() |
![]() |
![]() ![]() |
![]() ![]() |
![]() ![]() ![]() |
![]() ![]() |
Дополнительная информация
Контент чертежей
Готовая коробка.dwg

Общий вид станка.dwg

Тихоходный вал.dwg

Рекомендуемые чертежи
Свободное скачивание на сегодня
Обновление через: 8 часов 55 минут
Другие проекты
- 07.07.2023