Проектирование коробки скоростей горизонтально-фрезерного станка



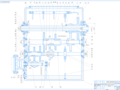

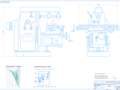
- Добавлен: 25.01.2023
- Размер: 354 KB
- Закачек: 0
Описание
Состав проекта
![]() |
![]() ![]() ![]() |
![]() ![]() ![]() ![]() |
![]() ![]() ![]() ![]() |
![]() ![]() ![]() ![]() |
Дополнительная информация
ПЗ.docx
Определение основных кинематических параметров 5
Разработка кинематической схемы и структурного графика коробки скоростей 8
Режимы резания. Мощность. Выбор электродвигателя ..12
Предварительный расчет коробки скоростей 17
Расчет валов на прочность ..21
Выбор подшипников 26
Расчет шлицевых соединений 27
Расчет шпоночных соединений ..29
Система управления ..31
Конструирование корпуса .. 32
Библиографический список .. . 34
Перечень листов графической части 35
Станок: горизонтально-фрезерный
Минимальное число оборотов шпинделя nmin=315 обмин
Максимальное число оборотов шпинделя nmax=1600 обмин
Предварительная мощность главного привода N=75кВт
Число скоростей: Zn=18
Вид выполняемой работы:
Фрезерование плоской поверхности
Материал - сталь (поковка) 40Х
Спроектировать коробку скоростей для горизонтально-фрезерного станка
Работа над проектом по курсу «Станки и инструменты» требует применения и способствует закреплению знаний полученных при изучении общепрофессиональных дисциплин: технологические процессы в машиностроении сопротивление материалов теория механизмов и машин детали машин и основы конструирования а также специальных дисциплин: резание материалов режущий инструмент технология машиностроения и курса «Металлорежущие станки» который является основой проекта.
В ходе курсового проекта решаются задачи разработки основного узла металлорежущего станка с учетом ряда требований:
) обеспечение технологических характеристик станка обусловленных заданием;
) разработка рациональной схемы механизма привода главного движения и системы управления величиной и направлением скоростей;
) разработка компактной и надежной конструкции узлов привода главного движения в совокупности с элементами систем управления и смазки;
) обеспечение технологичности изготовления деталей и сборки проектируемых узлов;
) обоснование принятых решений методом сопоставлений и выполнения поверочных расчетов логичного и грамотного изложения соответствующих материалов в расчетно-пояснительной записке.
Удовлетворение этих требований возможно при рассмотрении и анализе вариантов и на стадии разработки схем и общей компоновки разрабатываемых узлов т.е. творческого подхода к работе.
Целью курсового проекта является проектирование коробки скоростей для горизонтально-фрезерного станка.
Определение основных кинематических параметров
Число ступеней скоростей коробки Zn = 18.
Каждое следующее значение частоты вращения отличается от предыдущего на множитель. Вычислим знаменатель геометрического ряда:
где z – количество скоростей
- максимальное число оборотов шпинделя
- минимальное число оборотов шпинделя.
Принимаем - наиболее близкое из стандартизованных значений.
Примем частоты вращения для каждой передачи коробки скоростей.
Определим погрешность чисел оборотов
Допустимая погрешность = +10 ( -1) = +10 (126-1) = +26%
Вывод: все рассчитанные числа оборотов находятся в допустимых пределах.
Разработка кинематической схемы и структурного графика коробки скоростей
Разработка структурного графика коробки скоростей
Zn = 18 – число ступеней кратное числу ступеней 2 и 3.
Выбираем множительную структурную сетку коробки скоростей.
Возможные варианты:
Из всех возможных конструктивных и кинематических вариантов коробки скоростей наиболее выгодным является тот который обеспечивает простоту конструкции наименьшее количество групп и передач малые габариты а также наименьший вес. Выбираем схему 3х3х2. Z = 18 = 3(1)3(3)2(9)
Рисунок 1. Структурная сетка для коробки на Z = 3х3х2=18 скоростей
Из структурной сетки получаем следующие соотношения для передаточных чисел:
Построение графика чисел оборотов
Для построения графика чисел оборотов необходимо в каждом из соотношений выбрать одно передаточное число.
Выбор должен производиться так чтобы его значения не выходили за допускаемые пределы
Рисунок 2. График чисел оборотов
Определение чисел зубьев передач
Условие соблюдается.
Определение чисел зубьев зубчатых передач
Принимаем . [6 с.92 т.5]
Режимы резания. Мощность. Выбор электродвигателя
Выбор электродвигателя
Двигатель заданной мощности подбирается так чтобы частота его вращения была близка максимальной частоте вращения шпинделя.
Принимаем электродвигатель АИР 132М4 ТУ16-525.564-84. [4 с.459 т.24.9]
Для фрезерования плоской поверхности
Принимаем цилиндрическую фрезу:
Материал фрезы ВК 6.
Определяем величину подачи на 1 зуб (1 страница 283 таблица 34)
Рассчитаем скорость резания Uммин (1 страница 282)
Значение и показателей степени выбираем по таблице (1 страница 286 таблица 39)
Определим общий поправочный коэффициент на скорость резания (1 страница 282)
коэффициент учитывающий качество обрабатываемого материала (1 страница 261 таблица 1);
коэффициент учитывающий состояние поверхности заготовки (1 страница 263 таблица 5);
коэффициент учитывающий материал инструмента (1 страница 263 таблица 6).
Рассчитаем силу резания
Значение и показатели степени:
Определим мощность резания (эффективную)
АИР 132М4 ТУ16-525.564-84.
Предварительный расчет коробки скоростей
Расчет крутящих моментов.
По нижним точкам на каждом валу структурного графика (исключая шпиндель) рассчитываю крутящие моменты по формуле:
где Ni и ni – соответственно номинальная мощность и расчетная частота вращения i-го вала.
Номинальная мощность:
где Nдв– мощность электродвигателя кВт;
i – КПД кинематической цепи от двигателя до расчетного вала (равен произведению КПД всех зубчатых и КПД подшипников в опорах валов).
Расчет первого вала:
Расчет второго вала:
Расчет третьего вала:
Расчет вала шпинделя:
Ориентировочно только из расчёта на кручение так как пока еще нет данных о расстояниях между опорами и размещений зубчатых колёс определяются диаметры валов по формуле:
где – допускаемое напряжение кручения МПа.
Для валов изготовляемых из углеродистых сталей марок 35 40 45 40Х = 250-320 кгсм2 - при расчете диаметра вала в месте установки зубчатого колеса.
Расчет диаметра первого вала:
Округляя диаметр до стандартного получаю:
Расчет диаметра второго вала:
Расчет диаметра третьего вала:
Расчет геометрических параметров зубчатых зацеплений
Расчет модуля зубьев по напряжениям изгиба
где φ=8 - относительная ширина венцов;
- коэффициент учитывающий характер нагрузки;
- коэффициент формы зубьев. [4 с.25 т.7]
Допускаемое напряжение изгиба при стали и термообработки 40Х-М48 и модуле до 6: . [4 с.22 т.5]
Коэффициент формы зубьев: у=0106
Принимаем модуль для первой группы: m=3 мм
Ширина колес:B=24 мм
Коэффициент формы зубьев: у=0100
Принимаем модуль для второй группы: m=3мм
Принимаем модуль для первой группы: m=4
Расчет диаметров колес
Делительный диаметр:
Расчет межосевых расстояний
Расчет валов на прочность
Рисунок 3. Эпюры изгибающих и крутящих моментов
где - крутящий момент третьего вала;
- модуль зубчатого колеса;
- число зубьев зубчатого колеса.
где - угол зацепления.
Реакции опор в горизонтальной плоскости:
Изгибающие моменты в горизонтальной плоскости:
Реакции опор в вертикальной плоскости:
Изгибающие моменты в вертикальной плоскости:
Суммарные изгибающие моменты:
Вычислим геометрические характеристики опасных сечений вала.
Наиболее нагруженным является сечение С.
Момент сопротивления изгибу вала со шпонкой 16×10×55:
где - диаметр третьего вала;
Момент сопротивления кручению:
Напряжение кручения:
Коэффициент запаса прочности для вала из стали 45:
Общий коэффициент запаса прочности:
где - минимально допустимое значение общего коэффициента запаса по текучести. [2 с.166]
Вывод: статическая прочность обеспечена.
Подбор подшипников производится определением ресурса работы подшипника будем считать подшипник подходящим если его ресурс будет 15000ч. и выше
Расчет ведем для второй более нагруженной опоры.
Для третьего вала предварительно принимаем подшипники шариковые радиальные однорядные 210 ГОСТ 8338-75 из таблицы 24.10 (5)
Определим эквивалентную динамическую радиальную нагрузку по формуле:
Значение коэффициента безопасности принимают по таблице 7.4.
Значение температурного коэффициента принимают в зависимости от рабочей температуры: при
Подставим все значение коэффициентов и величин в выражение:
Определим расчетный ресурс L10h подшипника ч:
Вывод: так как расчетный ресурс больше требуемого то подшипник легкой серии 210 ГОСТ 8338-75.
Расчет шлицевых соединений
Боковые поверхности зубьев шлицевого соединения работают на смятие а основание их на изгиб и на срез.
Решающее значение имеет расчет на смятие.
где - коэффициент учитывающий неравномерность распределения нагрузки между шлицами: = 07 08; = 075.
Поверхность всех боковых поверхностей зубьев вала:
- наружный диаметр шлицев
- внутренний диаметр шлицев
- рабочая длина шлица
- допускаемое напряжение на смятие рабочих поверхностей. Для подвижного соединения =10 20 МПа.
Первый вал – шлицевый вал 6×26×32.
Второй вал – шлицевый вал 8×36×42.
Третий вал – шлицевый вал 8×42×48.
Вывод: валы обладают требуемой прочностью.
Расчет шпоночных соединений
При расчете принимают нагружение шпонки по длине равномерно.
Расчет шпонок на смятие и на срез.
Условие прочности на смятие:
- выступ шпонки от шпоночного паза.
=225 МПа - допускаемое напряжение на смятие для стали 45.
Условие прочности на срез:
– допускаемое напряжение на срез для стали 45.
Шпонка призматическая 16×10×55 на третьем валу.
Шпонка призматическая 20×12×140 на шпинделе.
Вывод: все шпонки обладают требуемой прочностью.
В коробке скоростей применяется смазка поливанием. Поливание применяется для зубчатых передач работающих с любыми окружными скоростями.
Смазочная жидкость нагнетается из ванны плунжерным насосом в коллектор. Затем по трубкам распределяется к трущимся поверхностям. Насос приводится в действие от эксцентрика расположенного на одном из валов коробки.
Производительность насоса определяется в предположении что всё количество тепла выделяемое при трении отводится маслом циркулирующем в смазочной системе.
где – мощность электродвигателя
– КПД коробки скоростей.
где коэффициент К = 1
Примем насос плунжерный 25 МН 3030-61.
Qном = 025 лмин при .
что меньше требуемой Q = 154 лмин.
Плунжерный насос не обеспечивает выбранную производительность для этого в эксцентрике сделаем эксцентриситет с двух сторон и получим производительность Q = 0792=158 лмин которая удовлетворяет расчетной производительности.
Механизмы для осевого передвижения зубчатых колёс конструируют по принципиальным схемам.
В первой схеме зубчатые колеса будем перемещать по валу рычагом установленным на одной оси с рукояткой управления. Этот способ наиболее простой но недостаток его в том что происходит смещение с оси вала переводного камня находящегося в пазу перемещаемых колес вследствие поворота конца рычага описывающего дугу радиусом R.
Для уменьшения смещения камня радиус рычага принимают равным
Желательно чтобы отклонение камня от оси вала было . Если не удаётся выдержать это соотношение то применяют механизмы выполненные по второй схеме. В этом случае деталь (зубчатое колесо) перемещают вилкой расположенной на направляющей скалке и приводимой в движение рычагом с зубчатым венцом сцепляющимся с рейкой. В механизмах выполненных по второй схеме зубчатые колёса (муфты) обычно перемещают вилками.
Связь рычага с вилкой осуществляют разными способами. Наиболее простое и дешёвое исполнение где в паз вилки входит цилиндрический штифт рычага. Недостаток этого варианта в том что контакт штифта с пазом вилки в лучшем случае происходит по линии: при частых переключениях штифт быстро изнашивается. Поэтому чаще всего рычаг снабжают переводным камнем по одному из вариантов. При необходимости перемещения на большую длину применяют зубчато-реечное зацепление. Для уменьшения трения в блоки колёс встраивают подшипники качения.
Вилки перемещаются по направляющим скалкам которые чаще всего выполняют одного диаметра с полем допуска h6 по всей длине. Отверстие в корпусе для скалки изготовляют с полем допуска H7 а отверстие в вилке Е9.
В каждом из положений механизм переключения должен быть зафиксирован. Для этого достаточно зафиксировать оду из перемещающихся деталей этого механизма. Часто фиксирующее устройство располагают в рукоятке управления. Наиболее распространённый вариант фиксирования механизма шариком и пружиной заходящими в гнездо с углом при вершине . Засверловку под шарик делают в стальных пластинах или непосредственно на поверхности стенки корпуса. Желательно применять износостойкие привёртные стальные шайбы или планки чтобы уменьшить износ шариком между гнёздами. Расстояние между краями гнёзд должно быть не менее 1 2 мм. Для повышения возможности фиксирования радиус расположения фиксаторных гнёзд должен быть по возможности большим.
Конструирование корпуса
Корпусные детали серийно выпускающихся станков обычно получают отливкой из серого чугуна СЧ15-32. Модели и стержни должны легко извлекаться из форм и стержневых ящиков. Для этого на модели не должно быть подрезок – выступов и впадин расположенных перпендикулярно или наклонено к направлению извлечения. Поверхностям перпендикулярным к плоскости разъема придают формовочные уклоны.
Материал корпуса- чугун СЧ 15
Толщина стенки корпуса ≥ 13 х (Тк) 14
Округляем до оптимального значения и принимаем =16 мм.
В современных станках для подвижных блоков шестерен применяют шлицевые валы. Для посадки неподвижных колес и других деталей на валах применяют гладкие валы а на шпинделе только гладкие.
Валы в коробке скоростей изготовлены из стали 45 с закалкой. Вал шпинделя изготовлен из стали 45Х.
Муфта служит для соединения валов и передачи вращающего момента от одного вала к другому. Чаще всего применяют муфты с резиновыми упругими элементами (МУВП).
Работоспособность МУВП определяется прочностью пальцев и резиновых втулок. Проверочный расчёт резиновых втулок выполняют по условиям ограничения давления на поверхности их контакта с пальцами а самих пальцев— по условиям прочности на изгиб.
Нагрузка приходящаяся на один палец определяют по формуле
гдеD— диаметр окружности по которой расположены пальцы;
z— количество пальцев в муфте (обычно принимаютz= 4 8).
Условие прочности втулок муфты:
p = Fп(dпlв) ≤ [p]. Где [р]= (20 25) МПа p =2036
Условие прочности пальцев на изгиб:
= MW0= 13Fп(05 lв+ с)(dп3) ≤ []. Где []= (60 70) МПа =675
с— осевой зазор между полумуфтами.
При работе над курсовым проектом была получена коробка скоростей для токарно-обдирочного станка на 18 скоростей и диапазон регулирования от 20 до 1000 обмин. Данный диапазон позволяет использовать станок с данной коробкой скоростей в среднесерийном производстве в связи с достаточно большим диапазоном регулирования.
Проведённые проверочные расчёты показали надёжность коробки скоростей и наличие предела прочности механизмов.
Для облегчения изготовления привода применяется максимальное количество стандартных изделий. Например: шпонки винты болты шайбы и др.
Библиографический список
Анурьев В.И. Справочник конструктора – машиностроителя. в 3-х т: т.2 -М.: Машиностроение. 1978.
Дунаев П.Ф. Леликов О.П. Конструирование узлов и деталей машин. – М.: Высшая школа 206. – 496с.
Косилова А.Г. Справочник технолога-машиностроителя. В 2-х т. – М.: Машиностроение 1986. – 656с.
Кравченко Л.М. Металлорежущие станки: метод. указания к выполнению курсового проекта. Нижний Тагил: изд. НТИ(ф)УГТУ-УПИ 2009 70с.
Кравченко Л.М. Системы смазки маслоуказатели и уплотнения: метод. указания к выполнению курсового проекта. Нижний Тагил: изд. НТИ(ф)УГТУ-УПИ 2009 30с.
Проников А.С. Расчет и конструирование металлорежущих станков – М.: Высшая школа 1962. – 422с.
Пуш В.Э. Металлорежущие станки: Учебник для машиностроительных втузов – М.: «Машиностроение» 1985 - 256 с. ил.
Тепинкичиев В.К. Красниченко Л.В. Тихонов А.А. Колев Н.С. Металлорежущие станки – М.: Машиностроение 1972. – 464с.
Чернов Н. Н. Металлорежущие станки: Учебник для техникумов по специальности «Обработка металлов резаньем». – 4-е изд. перераб. и доп. – М.: Машиностроение 1988 - 416 с. ил.
Перечень листов графической части
Развертка коробки скоростей горизонтально-фрезерного станка
Свертка коробки скоростей горизонтально-фрезерного станка
горизонтально-фрезерного станка
1001-000.000.2014137-01 ВО
1 лист.cdw

горизонтально-фрезерного
2лист.cdw

3 лист.cdw

Мощность электродвигателя
Число ступеней оборотов шпинделя 18
Частота вращения шпинделя
Горизонтально-фрезерный
Кинематическая схема