Мостовой кран грузоподъемность 40/8 т




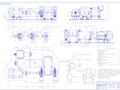
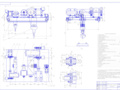
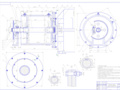
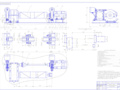
- Добавлен: 25.10.2022
- Размер: 8 MB
- Закачек: 2
Описание
Состав проекта
![]() |
![]() |
![]() ![]() ![]() |
![]() ![]() ![]() |
![]() |
![]() ![]() |
![]() ![]() |
![]() ![]() |
![]() ![]() |
![]() ![]() |
![]() ![]() |
![]() ![]() |
![]() ![]() |
![]() ![]() |
![]() ![]() |
![]() ![]() |
![]() ![]() |
![]() ![]() |
![]() ![]() |
![]() ![]() |
![]() ![]() |
![]() ![]() |
![]() ![]() |
![]() ![]() |
![]() ![]() |
![]() ![]() |
![]() ![]() |
![]() ![]() |
![]() ![]() |
![]() ![]() |
![]() ![]() |
![]() ![]() |
![]() ![]() |
![]() ![]() |
![]() ![]() |
![]() ![]() |
![]() ![]() |
![]() ![]() |
![]() ![]() |
![]() ![]() |
![]() ![]() |
![]() ![]() |
![]() ![]() |
![]() ![]() |
![]() ![]() |
![]() ![]() |
![]() ![]() |
![]() ![]() |
![]() ![]() |
![]() ![]() |
![]() ![]() |
![]() ![]() |
![]() ![]() |
![]() ![]() |
![]() ![]() |
![]() ![]() |
![]() ![]() |
![]() ![]() |
![]() ![]() |
![]() |
![]() ![]() ![]() ![]() |
![]() ![]() ![]() ![]() |
![]() ![]() ![]() ![]() |
![]() ![]() ![]() ![]() |
![]() ![]() ![]() ![]() |
![]() ![]() ![]() ![]() |
![]() ![]() ![]() ![]() |
![]() ![]() ![]() ![]() |
![]() ![]() ![]() ![]() |
![]() ![]() ![]() ![]() |
![]() ![]() ![]() ![]() |
![]() ![]() ![]() ![]() |
![]() ![]() ![]() ![]() |
![]() ![]() ![]() ![]() |
![]() ![]() ![]() ![]() |
![]() ![]() ![]() ![]() |
![]() ![]() ![]() ![]() |
![]() ![]() ![]() ![]() |
![]() ![]() ![]() ![]() |
![]() ![]() ![]() |
![]() ![]() ![]() ![]() |
![]() ![]() ![]() ![]() |
![]() ![]() ![]() ![]() |
![]() ![]() ![]() ![]() |
![]() ![]() ![]() ![]() |
![]() ![]() ![]() ![]() |
![]() ![]() ![]() ![]() |
Дополнительная информация
Вал-шестерня.dwg

Ребро жесткости.dwg

КрышкаПодш2.dwg

Ребро.dwg

Вал.dwg

План цеха.dwg

Тележка крана.dwg

СпецификацияВсПод.dwg

СпецификацияГлПод2.dwg

СпецификацияОбщий вид.dwg

Механизм подъема.dwg

СпецификацияГлПод.dwg

Общий вид.dwg

Установка кабельного барабана.dwg

СпецификацияУстБар.dwg

СпецификацияКрПодТорм.dwg

Механизм вспомагательного подъема.dwg

СпецификацияУстБар2.dwg

КрышкаПодш1.dwg

СпецификацияКабБар.dwg

СпецификацияПланЦеха.dwg

СпецификацияКабБар2.dwg

Установка барабана.dwg

Опора тормоза.dwg

Кронштейн под тормоз.dwg

СпецификацияТележка.dwg

СпецификацияВсПод2.dwg
