Кран консольный передвижной грузоподъемность 5 тонн




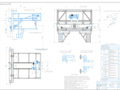
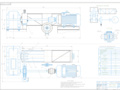
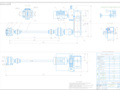
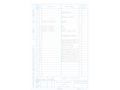
- Добавлен: 25.10.2022
- Размер: 2 MB
- Закачек: 1
Описание
Состав проекта
![]() |
![]() ![]() ![]() ![]() |
![]() ![]() |
![]() ![]() |
![]() ![]() |
![]() ![]() |
![]() ![]() ![]() |
![]() ![]() ![]() |
![]() ![]() ![]() ![]() |
![]() ![]() |
![]() ![]() ![]() ![]() |
![]() ![]() |
![]() ![]() |
![]() ![]() ![]() |
![]() ![]() |
![]() ![]() |
![]() ![]() |
![]() ![]() |
![]() ![]() ![]() ![]() |
![]() ![]() ![]() ![]() |
![]() ![]() |
![]() ![]() ![]() ![]() |
Дополнительная информация
ЛИСТ3 МЕХАНИЗМ подъема-доделка2.dwg

должны быть выполнены в соответствии с ОСТ 24.090.63.
Предварительное покрытие наружных поверхностей металлоконструкций и механизмов -
грунтовка ГФ - 0119 ГОСТ 23343 в один слой.
Окончательное покрытие должно производиться потребителем после монтажа крана
эмалью ПФ - 115 ГОСТ 6465 в два слоя. Класс покрытия по ГОСТ 9.032.
Кинематическая схема привода
Техническая характеристика
Группа классификации
Технические требования
Реферат.docx
КОНСОЛЬНЫЙ КРАН МЕХАНИЗМ ПОДЪЕМА МЕХАНИЗМ ПЕРЕДВИЖЕНИЯ ТЕЛЕЖКА ТЕХНИКА БЕЗОПАСНОСТИ
Объект исследования – консольный передвижной кран.
Цель курсового проекта – спроектировать консольный передвижной кран.
В процессе работы был произведен выбор подвески каната крана. Также был произведен расчет и выбран электродвигатель редуктор проведен выбор муфт и механизма тормоза крана. В результате расчетов разработана компоновочная схема механизма подъема.
В расчетной части проведен расчет механизма передвижения тележки с последующим выбором колесных установок рельса проведен расчет и выбор электродвигателя и редуктора муфт и тормозного механизма тележки. Также был проведен расчет механизма передвижения крана и расчет на прочность элементов барабана.
Были рассмотрены устройства безопасности и приведены основные мероприятия по технике безопасности при работе с консольным передвижным краном.
Студент подтверждает что приведенный в пояснительной записке материал правильно и объективно отражает состояние рассматриваемого вопроса все заимствованные из литературных и других источников теоретические и методологические положения и концепции сопровождаются ссылками на их авторов.
ФЛЕЙТО готово.doc
Расчет механизма подъема ..8
1 Исходные данные . 8
2 Выбор крюковой подвески . . ..9
4 Определение размеров барабана . ..11
5 Расчет и выбор двигателя . 15
6 Расчет и выбор редуктора .. . ..17
8 Выбор тормоза .. .22
9 Расчет параметров неустановившегося движения .24
10 Компоновка механизма подъема 27
Расчет механизма передвижения тележки .. 28
1 Исходные данные ..28
2 Выбор колес и колесных установок 28
4 Сопротивление передвижению тележки .. 31
5 Расчет и выбор электродвигателя . 32
6 Расчет и выбор редуктора . .34
7 Выбор муфт .. ..36
9 Компоновка механизма передвижения тележки 48
Расчет механизма передвижения крана . .49
1 Исходные данные ..49
2 Определение сопротивлений передвижению крана .. 50
3 Расчет и выбор электродвигателя 51
4 Расчет и выбор редуктора . 53
7 Компоновка механизма передвижения крана .66
Расчет на прочность элементов установки барабана . 67
1 Толщина цилиндрической стенки .. .67
2 Устойчивость цилиндрической стенки барабана ..68
3 Крепление каната к барабану ..69
4 Расчет болтов соединяющих зубчатый венец с барабаном 70
5 Расчет оси барабана . 73
6 Расчет подшипников на статическую грузоподъемность 75
Разработка металлоконструкции грузоподъемного крана 77
Устройства безопасности 78
Мероприятия по технике безопасности ..79
Список используемых источников 83
В создании материально-технической базы значительная роль отводится подъёмно-транспортным механизмам перед которым поставлена задача широкого внедрения во всех областях народного хозяйства комплексной механизации и автоматизации производственных процессов ликвидации ручных погрузочно-разгрузочных работ и исключение ручного труда при выполнении основных и вспомогательных производственных операций.
Современные технологические и автоматизированные линии погрузочно-разгрузочных операций связаны с применением разнообразных грузоподъёмных машин и механизмов обеспечивающих непрерывность и рентабельность производственных процессов.
Правильный выбор грузоподъёмного оборудования является основным фактором нормальной работы и высокой эффективности производства. Нельзя обеспечить устойчивый режим на современном этапе его интенсификации без согласований и безотказной работы современных средств механизации. Усиленно осуществляется переход от применения отдельных видов подъёмно-транспортной техники и внедрению высокопроизводственных комплексов. Создаются принципиально новые механизмы грузоподъёмных машин для комплексной механизации погрузочно-разгрузочных работ.
Созданы электро- и автопогрузчики различные разгрузочные машины а также различные подъёмные средства и лифты которые позволили осуществлять комплексную механизацию на многих предприятиях.
Техническое задание было выдано на кафедре «Механизация и автоматизация дорожно-строительного комплекса». На основании этого задания был разработан курсовой проект на тему «Спроектировать консольный передвижной кран». В ходе разработки проекта были выполнены пояснительная записка чертежи (общий вид крана сборочный чертёж крюковой подвески общий вид механизма передвижения тележки а также чертёж общего вида механизма подъема). Цель проекта – углубление и закрепление знаний по дисциплине «Подъемно-транспортные машины».
НАЗНАЧЕНИЕ ОБЛАСТЬ ПРИМЕНЕНИЯ И ТЕХНИЧЕСКАЯ ХАРАКТЕРИСТИКА КРАНА
Большое применение в промышленности имеют передвижные консольные настенные краны передвигающиеся по рельсам укрепленным вдоль стены здания. Для изменения вылета стрелы эти краны обычно снабжаются тележкой или электроталью передвигающейся по горизонтальной стреле а в некоторых конструкциях стрела имеет еще дополнительную возможность поворота относительно вертикальной оси что облегчает управление краном. Краны этого типа обслуживают площадь расположенную вдоль подкранового рельса и широко применяются в сборочных и механообрабатывающих цехах для передачи изделия с одной операции на другую. На рисунке 1.1 представлена схема настенного консольного передвижного крана.
-концевая балка; 2-кабина управления; 3-нижний горизонтальный ролик; 4-рельсовый путь крана; 5-верхний горизонтальный ролик; 6-консоль крана; 7-тележка; 8-рельсовый путь тележки; 9-опорные ходовые колеса
Рисунок 1.1 - Схема настенного консольного передвижного крана
Опорно-ходовым устройством консольного непередвижного крана является концевая балка 1 которая передвигается на двух двухребордных колесах 9 по рельсу 4. Две пары верхних 5 и нижних 3 горизонтальных роликов удерживают кран от опрокидывания. Тележка 7 передвигается по рельсовому пути 8 расположенному на консоли крана 5. Краны оборудован кабиной управления 2.
масса поднимаемого груза - Q = 5000 кг;
высота подъёма груза - Н = 8 м;
скорость передвижения тележки т=02 мс;
скорость подъёма груза г=013 мс;
скорость передвижения крана к=10 мс.
РАСЧЕТ МЕХАНИЗМА ПОДЪЕМА
скорость подъема груза ;
Группа классификации механизма М3 в соответствии с ИСО43011-86 в соответствии с ГОСТ 25835-83 - 4М.
На рисунке 2.1 приведена кинематическая схема механизма подъема груза.
Рисунок 2.1 – Кинематическая схема механизма
На рисунке 1 – электродвигатель; 2 – муфта; 3 – промежуточный вал; 4 – муфта; 5 – тормоз; 6 – редуктор; 7 – барабан.
По таблице 2.1 1 c.22 выбираем полиспаст в зависимости от грузоподъемности. Характеристику полиспаста занесем в таблицу 2.1:
Таблица 2.1 – Характеристика полиспаста
Характер навивки каната на барабан
Кратность полиспаста
Схема запасовки каната приведена на рисунке 2.2.
Рисунок 2.2 – Кинематическая схема запасовки каната
2 Выбор крюковой подвески
Выбор крюковой подвески осуществляем с учетом выполнения 2-х условий:
– грузоподъемность крюковой подвески не должна быть меньше заданной грузоподъемности: ;
– режим работы крюковой подвески должен соответствовать режиму работы механизма. Т.к. по ГОСТ 25835-83 группа режима работы 3К то в соответствии с табл.1.5 1 c.14 по правилам ГГТН – группа классификации механизма – М3.
Выбираем крюковую подвеску по ОСТ 24.191.08-81 типоразмера 2-10-406.
крюковая подвеска состоит из: двух блоков 1 траверсы 2 грузового крюка 3 и упорного подшипника 4. Конструктивная схема крюковой подвески показана на рисунке 2.3.
Рисунок 2.3 – конструктивная схема крюковой подвески
Наибольшее натяжение ветви каната определяем по формуле 1.3 2 c.11:
где - КПД полиспаста;
- кратность полиспаста
- число ветвей каната навиваемых на барабан.
Коэффициент полезного действия полиспаста определим по формуле 2.2:
Здесь - КПД блока на подшипниках качения.
Канат выберем исходя из условия:
произведение максимального статического усилия в канате на коэффициент использования каната не должно превышать разрывного усилия каната в целом указанного в таблице ГОСТа:
где - разрывное усилие каната в целом Н; - коэффициент использования каната назначаемый ГГТН. Значение принимаем по таблице 2 3 c.45 =56.
Выбираем по ГОСТ 2688-80 канат двойной свивки типа ЛК-Р 6х19(1+6+66)+1о.с. - с диаметром 130 мм. Канат грузовой (Г) первой марки (1) из проволоки без покрытия (-) правой крестовой свивки (-) нераскручивающийся (Н) обозначается: 13-Г-I-H-ГОСТ 2688-80
Определим соотношение между диаметром выбранного каната и диаметром блока крюковой подвески по формуле (2.4):
где - диаметр блока измеряемый по средней линии навитого каната (); - диаметр каната; - коэффициент регламентируемый нормами ГГТН и зависящий от типа машины и режима работы принимаем по табл.2.4 1 с.25
В соответствии с рядом предпочтительных чисел принимаем диаметр блока по высоте реборды .
4 Определение размеров барабана
Согласно рекомендациям по определению размеров барабана указанных в 1 c.29:
Согласно значениям нормального ряда диаметров принимаем . Так как диаметр барабана измеряется по средней линии навитого каната то диаметр барабана по дну канавок:
На рисунке 2.4 представлена схема к определению размеров барабана.
Рисунок 2.4 – Определение размеров барабана
Определим шаг нарезки:
Толщина стенки литого чугунного барабана:
Для уменьшения металлоемкости барабана принимаем толщину его стенки .
Принимаем в качестве материала барабана чугун марки СЧ 15 ( []=130 МПа) найдем напряжения сжатия в стенке барабана:
где – усилие в канате Н;
[]=130 – допускаемое напряжение сжатия для материала барабана МПа
Действующие напряжения меньше допускаемых поэтому выбранная толщина стенки обеспечивает требуемую прочность.
Длина барабана при сдвоенном полиспасте и намотке обеих ветвей каната на один барабан определяется по формуле:
где – длина рабочей части барабана м;
– длина части барабана на которой размещаются разгружающие витки м;
– гладкая часть барабана м;
– длина свободной (не нарезанной) части барабана м;
– длина части барабана для размещения запасных и закрепляющих витков каната.
Длина рабочей части барабана:
где – высота подъема м;
– кратность полиспаста;
– диаметр барабана м;
Длина части барабана на которой размещаются разгружающие витки:
Определяем длину гладкой части барабана:
Определяем длину части барабана для закрепления запасных и закрепляющих витков каната:
Приняв расстояние между правой и левой нарезками на барабане (длина не нарезанной части) равными расстоянию между ручьями блоков в крюковой обойме найдем полную длину барабана по формуле (2.10):
При расчете длины барабана должно выполняться условие:
Данное условие выполняется оставляем ранее выбранный размер.
Определяем частоту вращения барабана:
где – скорость подъема груза мс;
– диаметр барабана м
Определяем требуемую угловую скорость барабана:
где – частота вращения барабана обмин
5 Расчет и выбор двигателя
Выбор электродвигателя производится в зависимости от рода тока и номинального напряжения номинальной мощности и частоты вращения вида естественной характеристики двигателя и его конструктивного исполнения.
В кранах общего назначения применяются специальные крановые и металлургические двигатели постоянного тока серии Д крановые и металлургические асинхронные двигатели переменного тока с фазным ротором серии МТF и МТН а также крановые и металлургические двигатели с короткозамкнутым ротором серии МТКF и МТКН а в приводах малой мощности – асинхронные двигатели единой серии 4А с короткозамкнутым ротором.
Типоразмер двигателя подбирается по максимальной статической мощности :
где G – вес номинального груза и крюковой подвески кН; V – скорость подъема груза мс; – кпд механизма в предварительных расчетах можно принять = 080 085.
Номинальная мощность двигателя может быть принята на 20 30 % меньше максимальной статической мощности т. е.
Это обусловлено тем что эквивалентная мощность развиваемая двигателем при работе с грузами разного веса и зависящая от использования механизма по грузоподъемности всегда меньше . При работе с грузами номинального веса крановые двигатели обладают необходимой перегрузочной способностью достаточной чтобы выдержать кратковременную перегрузку.
С учетом проведенных расчетов выбираем крановый электродвигатель с фазным ротором МТF 311-8 4 c.45 имеющим для группы классификации механизма М6 номинальную мощность ; частоту вращения обмин; угловую скорость ; Момент инерции ротора ; максимальный пусковой момент двигателя и массой 170 кг. Габаритная схема электродвигателя представлена на рисунке 2.5.
Рисунок 2.5 - Габаритная схема электродвигателя MTF 311-8
Основные габаритные и установочные размеры представлены в таблице 2.2
Таблица 2.2 - Основные габаритные и установочные размеры
6 Расчет и выбор редуктора
Типоразмер редуктора подбирается по требуемому передаточному числу и передаваемой мощности.
Требуемое передаточное число определяется из выражения:
где - число оборотов выбранного электродвигателя ; - число оборотов барабана .
Допустимая мощность для выбранного редуктора на быстроходном валу должна быть не менее номинальной мощности двигателя или . Иногда заводы-изготовители редукторов указывают допустимую частоту вращения быстроходного вала. В таком случае эта частота должна быть не меньше частоты вращения двигателя .
Согласно вышеуказанным рекомендациям выбираем редуктор с учетом передаточного числа и мощности 6 с.218 цилиндрический двухступенчатый горизонтальный крановый имеющий тихоходный вал с зубчатым венцом типоразмера Ц2-500 с передаточным числом и мощностью на быстроходном валу для группы классификации механизма М3 - .редуктора 315 кг 6 с.218. Габаритная схема редуктора Ц2-500 показана на рисунке 2.6.
Рисунок 2.6 - Габаритная схема редуктора Ц2-500
Основные размеры редуктора представлены в таблице 2.3.
Таблица 2.3 - Основные размеры редуктора
Фактическая частота вращения барабана:
где – частота вращения электродвигателя обмин;
– передаточное число редуктора
Определяем фактическую скорость подъема груза которая не должна отличаться от заданной более чем на 10%:
где – диаметр барабана м;
– фактическая частота вращения барабана обмин;
– кратность полиспаста
Эта скорость отличается от заданной менее чем на 10% что допустимо.
В агрегатированных системах для соединения валов электродвигателей с быстроходными валами редукторов и их тихоходных валов с барабанами ходовыми колесами и другими сборочными единицами используют различные муфты. В таких соединениях муфты должны обеспечить не только передачу заданного крутящего момента но и иметь возможность компенсировать различного рода смещения геометрических осей соединяемых валов.
Момент статического сопротивления на валу двигателя в период пуска с учетом того что на барабан навиваются две ветви каната:
где – усилие в канате набегающем на барабан Н;
– передаточное число редуктора;
– КПД барабана 7 с.23 ;
– КПД привода барабана 7 с.127;
– число ветвей каната закрепленных на барабане;
-при опускании груза:
Момент передаваемый муфтой принимается равным моменту статических сопротивлений:
Номинальный момент на валу двигателя:
где -мощность электродвигателя кВт;
– частота вращения электродвигателя обмин
Расчетный момент для выбора зубчатой муфты:
где - коэффициент учитывающий степень ответственности механизма 7 с.42;
- коэффициент учитывающий режим работы механизма 7 с.42
Из 7 с.339 выберем ближайшую по требуемому крутящему моменту зубчатую муфту №1 с тормозным шкивом диаметром Dт=200мм шириной с Bт=95 мм и наибольшим передаваемым крутящим моментом 700 Нм. Момент инерции муфты Iм=01 кгм2.муфты 13 кг. На рисунке 3.7 представлена габаритная схема муфты типа МЗ с тормозным шкивом.
Рисунок 2.7 - Габаритная схема зубчатой муфты с тормозным шкивом
Так как в механизме присутствует промежуточный вал выбираем по ГОСТ 5006-83 зубчатую муфту с промежуточным валом (МЗП) №4 с наибольшим передаваемым крутящим моментом 4000 Нм и моментом инерции муфты . На рисунке 2.7 представлена габаритная схема зубчатой муфты с промежуточным валом. Основные размеры муфты типа МЗП представлены в таблице 2.4.
Расчет муфты соединяющей редуктор с барабаном не проводят т.к. конец тихоходного вала редуктора выполнен в виде зубчатого венца.
Таблица 2.4 – основные размеры муфты МЗП
В грузоподъемных механизмах для остановки груза и удержания его в подвешенном состоянии применяются тормоза. Тормоза обеспечивают не только удержание груза на определенной высоте но и остановку механизма и регулирование его скорости. По назначению тормоза разделяют на стопорные (для остановки груза) и спускные (для ограничения скорости спуска груза); по принципу действия – на автоматические и управляемые. Первые автоматически включаются в аварийной ситуации или при выключении двигателя соответствующего механизма. Управляемые тормоза замыкаются и размыкаются при воздействии оператора на органы управления тормоза.
Согласно правилам Госгортехнадзора механизмы подъема груза и изменения вылета стрелы должны оборудоваться нормально замкнутыми тормозами с автоматическим управлением. На механизмах передвижения и поворота устанавливают также нормально замкнутые или комбинированные тормоза. В механизмах поворота башенных и портальных кранов разрешается установка нормально разомкнутого тормоза.
Типоразмер тормоза выбирают по каталогу в зависимости от расчетного тормозного момента:
где – каталожное значение тормозного момента Нм; – расчетный крутящий момент на валу тормоза Нм определяемый из условия:
где – коэффициент запаса торможения.
Согласно правилам ГГТН тормоз механизма подъема груза должен обеспечивать тормозной момент с коэффициентом запаса торможения не менее 15 и не более 25; примем =15. – статический крутящий момент при торможении создаваемый весом номинального груза на валу на котором устанавливается тормоз определяемый из выражения:
где – вес поднимаемого груза Н;
– диаметр барабана по средней линии навивки каната м;
– кпд механизма подсчитанный по максимальным значениям кпд отдельных участков кинематической схемы ;
– передаточное число механизма .
Выбираем тормоз ТКТГ-300 с тормозным моментом 800 Н·м диаметром тормозного шкива .тормоза 100 кг 7 с.341. Регулировкой можно получить требуемый тормозной момент .
На рисунке 2.8 представлена габаритная схема двухколодочного тормоза с электрогидравлическим толкателем (ТКГ).
Рисунок 2.8 - Габаритная схема тормоза типа ТКТГ
Основные размеры тормоза типа ТКТГ-300 представлены в таблице 2.5
Таблица 2.5 - основные размеры тормоза типа ТКТГ-300
9 Расчет параметров неустановившегося движения
– среднепусковой момент двигателя Нм;
– момент статический при подъеме Нм;
– момент статический при торможении Нм;
– момент тормозной Нм;
– номинальная угловая скорость двигателя с-1;
– момент инерции ротора кгм2;
– момент инерции зубчатой муфты кгм2;
– момент инерции зубчатой муфты с тормозным шкивом кгм2.
Момент инерции вращающихся масс:
где – момент инерции ротора кгм2;
и – моменты инерции муфт кгм2
Параметр uв приведения направления движения полиспаста к валу двигателя:
Момент инерции поступательных и вращательных масс приведенных к быстроходному валу:
где - момент инерции вращающихся масс кг·м2;
- параметр приведения направления движения полиспаста к валу двигателя м
Расчет времени неустановившегося движения ускорения и перемещения .
Определяем фактическое время разгона при подъеме груза:
где - момент инерции всех движущихся масс кгм2;
- среднепусковой момент двигателя Н·м;
- момент статический при подъеме Н·м
- номинальная угловая скорость двигателя с-1
Время разгона при опускании груза:
Время торможения при опускании груза:
Время торможения при подъеме крюковой подвески без груза:
где – тормозной момент Н·м
Расчетные значения ускорения и пути перемещения определяются соответственно по формулам и где =013 мс – заданная скорость подъема груза.
Расчетные значения ускорения и перемещения представлены в таблице 2.6.
Таблица 2.6 – Расчетные значения ускорения и пути перемещения
Разгон при подъеме груза
Разгон при опускании груза
Торможение при опускании груза
Торможение при подъеме подвески без груза
10 Компоновка механизма подъема
На основании проведенных расчетов и выбранных комплектующих элементов для механизма подъема груза производим компоновку. На рисунке 2.9 приведена компоновка механизма подъема на этом рисунке: 1 – электродвигатель; 2 – зубчатая муфта; 3 – зубчатая муфта с тормозным шкивом; 4 – тормоз; 5 – редуктор; 6 – барабан.
Рисунок 2.9 – Компоновка механизма подъема
РАСЧЕТ МЕХАНИЗМА ПЕРЕДВИЖЕНИЯ ТЕЛЕЖКИ
– грузоподъемность кг;
– скорость передвижения тележки мc;
Группа классификации механизма М3 в соответствии с ИСО43011-86 в соответствии с ГОСТ 25835 – 4М.
Выбранная кинематическая схема механизма передвижения тележки с центральным приводом и тихоходным трансмиссионным валом показана на рисунке 3.1. Механизм имеет привод к валу ходового колеса – 1 от электродвигателя - 8 переменного тока через вертикальный цилиндрический редуктор – 5 типа ВК широко применяемый в механизмах передвижения крановых тележек. Двухколодочный тормоз с электрогидравлическим одноштоковым гидротолкателем – 7 установлен на валу двигателя. В механизме используются три типа муфт: упругая втулочно-пальцевая муфта с тормозным шкивом – 6 зубчатая муфта – 2 с промежуточным валом – 3 и зубчатая – 4.
Рисунок 3.1 - Кинематическая схема механизма передвижения тележки
2 Выбор колес и колесных установок
Число ходовых колес тележек зависит от грузоподъемности крана. При
грузоподъемности до 16 т. предварительно можно принять четыре колеса а при большей грузоподъемности – восемь.
Типоразмер колес определяется их диаметром который выбирается по табл. 3.1 2 c.53 в зависимости от максимальной статической нагрузки приходящейся на одно колесо:
где – максимальная статическая нагрузка на одно колесо; –допускаемая нагрузка на одно колесо.
определяется из условия того что нагрузка на ходовые колеса от веса поднимаемого груза веса тележки а также узлов и агрегатов смонтированных на ней распределяется равномерно на все опоры:
где – коэффициент неравномерности ; – грузоподъемность крана; – вес тележки ( определим по табл.3.2 2 c.53); – вес грузозахватной подвески; – количество ходовых колес.
Согласно таблице 3.1 2 c.53 принимаем диаметр колеса . По ОСТ 24.090.09-75 принимаем для приводных колес установку типа – К2РП для ведомых колес установку типа – К2РН. Схемы колес приведены на рисунках 3.2 и 3.3 соответственно. Параметры колесных установок занесем в таблицу 3.1.
Рисунок 3.2 – Колесо приводное К2РП
Рисунок 3.3 – Колесо неприводное К2РН
Таблица 3.1 – Размеры крановых колес на угловых буксах
Продолжение таблицы 3.1
В качестве подтележечных и подкрановых рельсов можно использовать рельсы как с выпуклой головкой (типы Р и КР) так и плоские. Типоразмер рельса определяем по таблице 2.11 1 c.39 в зависимости от максимальной статической нагрузки на колесо таковым является типоразмер рельса с выпуклой головкой Р24 ГОСТ 6368-82. Поперечное сечение рельса представлено на рисунке 3.4 основные размеры сведены в таблицу 3.2.
Рисунок 3.4 – Поперечное сечение рельса типа Р24
Таблица 3.2 – Основные данные железнодорожных рельсов узкой и широкой колеи
4 Определение сопротивления передвижению тележки
Сопротивление передвижению тележки с номинальным грузом приведенное к ободу ходового колеса:
где – масса номинального груза кг;
– масса тележки кг;
– коэффициент трения качения ходовых колес по рельсам с плоской головкой 7 с.33 м;
- коэффициент трения в подшипниках качения ходовых колес (подшипники конические) 1 с.33;
– диаметр ходового колеса м;
. Принимаем – диаметр цапфы;
– коэффициент учитывающий сопротивление трения реборд ходовых колес и торцов ступиц колеса.
Сопротивление передвижению тележки без груза:
5 Расчет и выбор электродвигателя
Выбор электродвигателя для механизма передвижения крановых тележек производят по статической мощности при которой обеспечивается надлежащий запас сцепления ходового колеса с рельсом исключающий возможность буксования при передвижении тележки без груза в процессе пуска.
Определим статическую мощность электродвигателя:
где - скорость передвижения тележки мc;
- КПД механизма 7 с.23;
- сопротивление передвижению тележки H.
Номинальная мощность электродвигателя принимается равной или несколько большей статической мощности. С учетом этих указаний из 4 с.45 выбираем крановый электродвигатель с фазным ротором MTF 011-6 4 с.45 имеющим для группы классификации механизма М3 номинальную мощность ; частоту вращения ; момент инерции ротора ; максимальный пусковой момент двигателя и массой 65 кг. На рисунке 3.5 показана габаритная схема электродвигателя MTF 011-6.
Номинальный момент двигателя:
где – номинальная мощность электродвигателя кВт;
– частота вращения обмин.
Рисунок 3.5 - Габаритная схема электродвигателя MTF 011-6
Основные габаритные и установочные размеры представлены в таблице 3.3.
Таблица 3.3 - Основные габаритные и установочные размеры
Частота вращения ходового колеса:
Требуемое передаточное число привода:
В соответствии со стандартным рядом принимаем передаточное число привода .
Расчетная мощность редуктора:
где - статическая мощность электродвигателя кВт;
– коэффициент учитывающий условия работы редуктора 7 с.40
Исходя из этой мощности и требуемого передаточного числа выбираем для группы классификации механизма М3 редуктор типа ВК-400 7 с.331 номинальная передаваемая мощность которого частоту вращения и передаточным числом . Габаритная схема редуктора ВК-400 представлена на рисунке 2.6.
Рисунок 3.6 - Габаритная схема редуктора ВК-400
Основные размеры редуктора представлены в таблице 3.4.
Таблица 3.4 - Основные размеры редуктора
Всего в данном механизме передвижения тележки исходя из выбранной кинематической схемы используется три муфты одна из которых упругая втулочно-пальцевая с тормозным шкивом установленная на быстроходном валу редуктора и две зубчатые муфты одна из которых с промежуточным валом установленные на тихоходном валу.
Муфта соединяющая электродвигатель с редуктором:
Номинальный момент передаваемый муфтой электродвигателя:
где – сопротивление передвижению тележки с номинальным грузом Н;
Расчетный момент для выбора муфты:
где – коэффициент учитывающий степень ответственности механизма 7 с.42;
– коэффициент учитывающий режим работы механизма 7 с.42
Выбираем упругую втулочно-пальцевую муфту с крутящим моментом 250 Нм. Диаметр муфты момент инерции и масса 135 кг. Габаритная схема упругой втулочно-пальцевой муфты с тормозным шкивом показана на рисунке 3.7.
Рисунок 3.7 - Габаритная схема упругой втулочно-пальцевой муфты с тормозным шкивом
Основные размеры муфты представлены в таблице 3.5.
Таблица 3.5 - Основные размеры муфты
Муфты соединяющие редуктор с колесами:
Номинальный момент на тихоходном валу редуктора:
Расчетный момент для выбора муфт:
Выбираем по ГОСТ 5006-83 зубчатую муфту №2 с наибольшим передаваемым крутящим моментом 1600 Нм и моментом инерции муфты и массой 92 кг. Габаритная схема зубчатой муфты представлена на рисунке 3.8.
Рисунок 3.8 - Габаритная схема зубчатой муфты
Основные размеры муфты представлены в таблице 3.6
Таблица 3.6 - Основные размеры муфты
Также выбираем по ГОСТ 5006-55 зубчатую муфту с промежуточным валом №1 для передачи крутящего момента между колесами с наибольшим передаваемым крутящим моментом 710 Нм и моментом инерции муфты и массой 205 кг.
Габаритная схема зубчатой муфты с промежуточным валом представлена на рисунке 3.9.
Рисунок 3.9 - Габаритная схема зубчатой муфты с промежуточным валом
Основные размеры муфты МЗП представлены в таблице 3.7
Таблица 3.7 - Основные размеры муфты МЗП
Фактическая скорость передвижения тележки:
отличается от заданного значения 02 мс менее чем на 10% что допустимо.
Максимально допустимое ускорение тележки при пуске:
где – общее число ходовых колес;
- число приводных колес;
– коэффициент сцепления ходовых колес с рельсами (при работе в помещении) 7 с.33;
– коэффициент запаса сцепления 7 с.32;
– коэффициент трения в конических подшипниках опор вала ходового колеса;
– диаметр цапфы вала м;
– коэффициент учитывающий сопротивление трения реборд ходовых колес и торцов ступиц колеса 7 с.23;
– коэффициент трения качения ходовых колес по рельсам с выпуклой головкой;
– диаметр ходового колеса м
Наименьшее допускаемое время пуска:
Средний пусковой момент электродвигателя:
min=11..14 – минимальная кратность пускового момента электродвигателя принимаем min=11
Момент статических сопротивлений при работе крана без груза:
где – сопротивление передвижению тележки без груза Н;
Суммарный момент инерции вращающихся масс:
где– момент инерции ротора электродвигателя кгм2;
– момент инерции муфты на быстроходном валу кгм2;
Фактическое время пуска механизма передвижения без груза:
где – коэффициент учитывающий влияние вращающихся масс привода механизма (кроме ротора двигателя и муфт) 7 с.25;
– суммарный момент инерции вращающихся масс кгм2;
– число оборотов электродвигателя обмин;
– средний пусковой момент электродвигателя Нм;
– момент статических сопротивлений при работе крана без груза Нм;
– фактическая скорость передвижения тележки мc;
Фактическое ускорение крана без груза при пуске:
где– фактическая скорость передвижения мс;
- фактическое время пуска механизма передвижения без груза c;
– максимально допустимое ускорение тележки мc2
условие выполняется или 0265 мс2 0652 мс2.
Проверяем фактический запас сцепления. Для этого найдем суммарную нагрузку на приводные колеса без груза:
– число приводных колес;
Найдем фактический коэффициент запаса сцепления:
где– суммарная нагрузка на приводные колеса Н;
– полное сопротивление передвижению без груза Н;
– коэффициент сцепления ходовых колес с рельсами;
– общее число ходовых колес;
– коэффициент трения в подшипниках опор вала ходового колеса (для конических).
Максимальное допустимое замедление тележки при торможении:
где – коэффициент сцепления ходовых колес с рельсами (при работе в помещении);
– коэффициент запаса сцепления;
– коэффициент трения в подшипниках опор вала ходового колеса (для конических);
– коэффициент трения качения ходовых колес по рельсам с выпуклой головкой м
Время торможения тележки без груза:
где=0668 – максимальное допустимое замедление тележки при торможении мс2;
=022 – фактическая скорость передвижения тележки мс
Сопротивление при торможении тележки без груза:
где– масса тележки кг;
– коэффициент трения в подшипниках опор вала ходового колеса (для конических)
Момент статических сопротивлений на тормозном валу при торможении тележки:
где – сопротивление при торможении тележки без груза Н;
Момент сил инерции при торможении тележки без груза:
где – коэффициент учитывающий влияние вращающихся масс привода механизма (кроме ротора электродвигателя и муфт быстроходного вала);
– фактическая скорость передвижения тележки мс;
– время торможения тележки без груза c
Расчетный тормозной момент на валу тормоза:
где=2804 – момент сил инерции при торможении тележки без груза Нм;
=0392 – момент статических сопротивлений на тормозном валу при торможении тележки Нм
Выбираем тормоз ТКГ-200 с тормозным моментом 250 Нм диаметром тормозного шкива мм 7 с.341.тормоза 38 кг. Регулировкой можно получить требуемый тормозной момент =27648 Н·м. На рисунке 3.10 представлена габаритная схема двухколодочного тормоза с электрогидравлическим толкателем (ТКГ).
Рисунок 3.10 – Габаритная схема тормоза типа ТКГ
Основные размеры тормоза типа ТКГ-200 представлены в таблице 3.8.
Таблица 3.8 - Основные размеры тормоза типа ТКГ-200
Минимальная длина пути торможения:
где - фактическая скорость передвижения тележки мс;
– коэффициент торможения 7 с.31
Фактическая длина пути торможения:
где- время торможения тележки без груза
Условие выполняется или 004>0032 м.
9 Компоновка механизма передвижения тележки
На основе рассчитанных параметров и выбранных элементов механизма передвижения тележки производим компоновку всех его составных частей их взаимное расположение в масштабе представлено на рисунке 3.11.
На этом рисунке: 1 – ходовое колесо; 2 – муфта зубчатая с промежуточным валом; 3 – промежуточный вал; 4 – муфта зубчатая; 5 – редуктор; 6 – муфта упругая втулочно-пальцевая с тормозным шкивом; 7 – тормоз; 8 – электродвигатель.
Рисунок 3.11 – Компоновка механизма передвижения тележки
РАСЧЕТ МЕХАНИЗМА ПЕРЕДВИЖЕНИЯ КРАНА
- грузоподъемность кг;
- скорость передвижения крана мс;
Группа классификации механизма М3 в соответствии с ИСО43011-86 в соответствии с ГОСТ 25835 - 4М.
Механизмы передвижения кранов на рельсовом ходу делятся на центральные и раздельные. Центральные в свою очередь делятся на механизмы с тихоходным трансмиссионным валом быстроходным и среднеходовым. Раздельный механизм устанавливается отдельно на каждое приводное колесо. Выберем механизм передвижения крана с раздельным приводом габаритная схема приведена на рисунке 4.1.
Рисунок 4.1 – Габаритная схема механизма передвижения крана с раздельным приводом
На этой схеме 1 – ходовое колесо; 2 – муфта зубчатая; 3 – редуктор; 4 – тормоз; 5 – упругая втулочно-пальцевая муфта; 6 – электродвигатель.
Механизм имеет привод к валу ходового колеса - 1 от электродвигателя - 6 переменного тока через вертикальный цилиндрический редуктор - 3 типа ВК широко применяемый в механизмах передвижения кранов. Двухколодочный электрогидравлический тормоз - 4 с одноштоковым гидротолкателем установлен на валу двигателя. В механизме используются два типа муфт: упругая втулочно-пальцевая муфта с тормозным шкивом – 5 и зубчатая муфта – 2.
2 Определение сопротивлений движению крана
Согласно рекомендациям 7 с.13 по определению ориентировочной массы масса данного крана будет равна:
где- масса номинального груза т;
Сопротивление передвижению крана с номинальным грузом приведенное к ободу ходового колеса:
– коэффициент трения в подшипниках качения ходовых колес (подшипники конические) 7 с.33;
– диаметр ходового колеса м 7 с.33;
– коэффициент учитывающий сопротивление трения реборд ходовых колес и торцов ступиц колеса 7 с.33
Сопротивление передвижению крана без груза:
3 Расчет и выбор электродвигателя
Статическая мощность электродвигателя:
где -скорость передвижения крана мс;
КПД механизма 7 с.23;
- сопротивление передвижению крана Н
Поскольку в приводе механизма передвижения должно быть установлено два одинаковых электродвигателя на каждый из них приходится т.е. 143..172 кВт. Примем статическую мощность электродвигателя .
Номинальная мощность электродвигателя принимается равной или несколько большей статической мощности. С учетом этих указаний из 4 с.45 выбираем крановый электродвигатель с фазным ротором MTF 012-6 имеющим для группы классификации механизма М3 номинальную мощность ; частоту вращения ; Момент инерции ротора ; максимальный пусковой момент двигателя и массой 58 кг. На рисунке 4.2 показана габаритная схема электродвигателя MTF 012-6.
Рисунок 4.2 – Габаритная схема электродвигателя MTF 012-6
Основные габаритные и установочные размеры представлены в таблице 4.1.
Таблица 4.1 – Основные габаритные и установочные размеры
Номинальный момент электродвигателя:
– частота вращения обмин
4 Расчет и выбор редуктора
В соответствии со стандартным рядом принимаем передаточное число привода округляя его в меньшую сторону .
где- статическая мощность электродвигателя кВт;
Исходя из этой мощности и требуемого передаточного числа выбираем для группы классификации механизма М3 редуктор типа ВК-400 5 с.426 имеющий номинальную мощность Nр=44 кВт частоту вращения nр=750 обмин и передаточным числом ip=28. Габаритная схема редуктора ВК-400 представлена на рисунке 4.3.
Рисунок 4.3 - Габаритная схема редуктора ВК-400 и его размеры
Основные размеры редуктора представлены в таблице 4.2.
Таблица 4.2 - Основные размеры редуктора
где – сопротивление передвижению крана с номинальным грузом Н;
Выбираем упругую втулочно-пальцевую муфту с крутящим моментом 250 Нм. Диаметр муфты момент инерции и масса 135 кг. Габаритная схема упругой втулочно-пальцевой муфты с тормозным шкивом показана на рисунке 4.4.
Рисунок 4.4 - Габаритная схема упругой втулочно-пальцевой муфты с тормозным шкивом
Основные размеры муфты представлены в таблице 4.3
Таблица 4.3 - Основные размеры муфты
Муфты соединяющие редуктор с колесом:
Выбираем по ГОСТ 5006 – 83 зубчатую муфту №2 с наибольшим передаваемым крутящим моментом 1600 Нм и моментом инерции муфты и массой 92 кг. Габаритная схема зубчатой муфты представлена на рисунке 4.5.
Рисунок 4.5 - Габаритная схема муфты типа МЗ
Основные размеры муфты представлены в таблице 4.4.
Таблица 4.4 - Основные размеры муфты
Фактическая скорость передвижения крана:
отличается от заданного значения 10 мс менее чем на 10% что допустимо.
Максимально допустимое ускорение крана при пуске:
– коэффициент трения качения ходовых колес по рельсам с плоской головкой м;
min=11..14 - минимальная кратность пускового момента электродвигателя примем min=13
Т.к. в механизме используется два электродвигателя средний пусковой момент следует умножить на два: .
где- сопротивление передвижению тележки без груза Н;
где – момент инерции ротора электродвигателя кгм2;
Фактическое время пуска механизма передвижения крана без груза:
- момент статических сопротивлений при работе крана без груза Нм;
– фактическая скорость передвижения крана мc;
где – фактическая скорость передвижения крана мс;
– фактическое время пуска механизма без груза c;
– максимально допустимое ускорение крана м
Условие выполняется aФamax или 0119 мс20487 мс2.
- фактическое ускорение крана без груза мс2;
Максимальное допустимое замедление крана при торможении:
– коэффициент сцепления ходовых колес с рельсами (при работе в помещении);
– коэффициент трения качения ходовых колес по рельсам с плоской головкой м
Время торможения крана без груза:
где – максимальное допустимое замедление крана при торможении мс2;
– фактическая скорость передвижения крана мс
Сопротивление при торможении крана без груза:
где – масса крана кг;
Момент статических сопротивлений на тормозном валу при торможении крана:
– передаточное число редуктора.
Момент сил инерции при торможении крана без груза:
где – коэффициент учитывающий влияние вращающихся масс привода механизма (кроме ротора двигателя и муфт);
– число оборотов двигателя обмин;
– фактическая скорость передвижения крана мс;
– время торможения крана без груза c
где – момент инерции при торможении крана без груза Нм;
– момент статических сопротивлений на тормозном валу при торможении крана Нм
Так как в данном механизме используется два тормоза расчетный тормозной момент для выбора тормоза будет равен:
Выбираем тормоз ТКГ-200 с тормозным моментом 250 Нм диаметром тормозного шкива 7 с.341.тормоза 38 кг. Регулировкой можно получить требуемый тормозной момент . На рисунке 4.6 представлена габаритная схема тормоза типа ТКГ.
Рисунок 4.6 - Габаритная схема тормоза типа ТКГ
Основные размеры тормоза типа ТКГ-200 представлены в таблице 4.5
Таблица 4.5 - Основные размеры тормоза типа ТКГ-200
– коэффициент по 7 с.31
Фактическая длина пути:
где – время торможения крана без груза c;
– фактическая скорость передвижения крана мc
Условие выполняется или 276 м>0735 м.
7 Компоновка механизма передвижения крана
На основе рассчитанных параметров и выбранных элементов механизма передвижения крана производим компоновку всех его составных частей их взаимное расположение в масштабе представлено на рисунке 3.7.
На консольных кранах механизм передвижения с раздельным приводом имеет по одному приводу с двух сторон в нижней части крана. Ходовое колесо - 1 связано с тихоходным валом редуктора - 3 через зубчатую муфту - 2. Первый вал редуктора связан с выходным валом двигателя - 6 упругой втулочно-пальцевой муфтой - 5 половина этой муфты укрепленная на валу редуктора одновременно служит тормозным шкивом на котором находится тормоз - 4.
Рисунок 4.7 – Компоновка механизма передвижения крана
Расчет на прочность элементов установки барабана
1 Толщина цилиндрической стенки
Принимаем в качестве материала барабана чугун марки СЧ 15 ([]сж=130 МПа ).
Определяем приближенное значение толщины стенки барабана:
t=0015 - шаг нарезки м;
[]сж=130 - допускаемое напряжение сжатия для материала барабана МПа
Уточним полученное значение для этого определим коэффициент влияния деформации стенки барабана и каната:
гдеЕк=88260 – модуль упругости каната МПа;
Еб – модуль упругости стенки барабана для чугунных барабанов Еб=98000 МПа;
Fк=6100 – площадь сечения всех проволок каната мм2;
t=0015 - шаг нарезки м
С учетом уточнений толщина цилиндрической стенки барабана:
Учитывая что стенка барабана в процессе эксплуатации изнашивается принимаем =10 мм.
2 Устойчивость цилиндрической стенки барабана
Для определения необходимости проверки устойчивости подсчитываем номинальное напряжение сжатия в стенке барабана:
При этих параметрах из 9 с.94 следует что проверку необходимо производить если отношение . Для проектируемого барабана . Следовательно проверки устойчивости стенки барабана не требуется.
3 Крепление каната к барабану
Наибольшее применение находит крепление каната планками прижимающими канат к барабану. При этом канат из крайней канавки барабана переводят сразу в третью для чего частично вырубают выступы нарезки которые разделяют канавки. Среднюю же канавку используют для установки крепежных болтов и шпилек. На рисунке 5.1 показана схема крепления каната на барабане прижимными планками.
Рисунок 5.1 - Схема крепления каната на барабане прижимными планками
Применяя способ крепления прижимными планками с трапециевидными пазами прижимающими два соседних витка определим суммарное усилие растяжения болтов:
где f=010..012 – коэффициент трения между канатом и
барабаном принимаем f=010;
γ=40 – угол наклона боковой грани трапециевидного выреза в
α=4 – угол обхвата барабана неприкосновенными витками;
е – основание натурального логарифма
Используя нормализованные планки ПО «Сибтяжмаш» для диаметра каната 13 мм задаемся диаметром болта М12 по диаметру отверстия в планке. Тогда необходимое число болтов выполненных из стали ВСт3сп (тек=230 МПа):
где k≥15 –коэффициент запаса надежности крепления каната к
барабану примем k=15;
- приведенный коэффициент трения между канатом и поверхностью планки где f =01 – коэффициент трения между канатом и барабаном γ=400 – угол наклона боковой грани трапециевидного выреза в планке к вертикали ;
- допускаемое напряжение растяжения болта;
d=0012 – диаметр одного болта м;
l=0045 – расстояние от дна канавки на барабане до верхней плоскости прижимной планки м
принимаем число крепежных болтов z=6.
4 Расчет болтов соединяющих зубчатый венец с барабаном
Соединение осуществляем болтами для отверстий из под развертки по ГОСТ 7817-80 материал болтов – сталь 45 предел текучести материала т=353 МПа. Болты устанавливаем на диаметре окружности Dокр=285 мм. . На рисунке 6.2 показана схема соединения зубчатого венца с барабаном.
Рисунок 5.2 - Схема соединения зубчатого венца с барабаном
Окружное перерезывающее усилие действующее на все болты:
DБ=0320– диаметр барабана м;
Dокр=0285 – диаметр окружности на которой устанавливаются
болты соединяющие зубчатый венец с барабаном м
Допускаемое напряжение среза болта:
гдет=353 - предел текучести материала МПа;
k1 – коэффициент безопасности для механизма подъема крана работающих с крюком k1=13 9 с.97;
k2 – коэффициент нагрузки для группы классификации М6 k2=11 9 с.97
Задаваясь числом болтов mб=6 определим их диаметр:
гдеPокр – усилие действующее на окружности установки болтов Н;
m’б – расчетное число болтов m’б=075mб;
mб – число установленных болтов;
[] – допускаемое напряжение среза болта МПа
Принимаем диаметр болта d=10 мм.
Определим напряжение смятия:
гдеb=0028 – расчетная длина болта м
Прочность болтов на смятие обеспечена так как допускаемые напряжения смятия болтов выполненных из стали 45 [см]=280 МПа.
5 Расчет оси барабана
При выбранном типе полиспаста положение равнодействующей натяжений каната относительно опор оси остается неизменным эта равнодействующая: .
Нагрузка на опору А оси при положении равнодействующей показанной на рисунке 6.1:
Нагрузка на опору В:
Нагрузка на ступицу D барабана (равнодействующую этой нагрузки полагаем приложенной в середине ступицы):
Нагрузка на ступицу C:
Определим изгибающие моменты:
Принимаем в качестве материала оси сталь 45. Предел прочности В=598 МПа предел выносливости -1=257 МПа.
Определим допускаемые напряжения при симметричном цикле:
где k0 – коэффициент учитывающий конструкцию детали (для валов осей и цапф k0=2..28 9 с.97) примем k0=25;
-1=257 - предел выносливости МПа;
[n] – допускаемый коэффициент запаса прочности для группы классификации М6 [n]=16
На рисунке 5.3 показана расчетная схема оси барабана в масштабе.
Рисунок 5.3 - Расчетная схема оси барабана
Предварительно диаметр оси под правой ступицей (здесь действует наибольший момент) определяем по формуле:
принимаем диаметр оси dD=55 мм.
Диаметр оси под левой ступицей определяем по формуле:
Принимаем диаметр оси dС=65 мм.
6 Расчет подшипников на статическую грузоподъемность
На статическую грузоподъемность проверяют подшипники работающие при малых частотах вращения. Подбор подшипников выполняют для обеих опор вала. Выбираем подшипник шариковый радиальный сферический двухрядный по ГОСТ 28428-90.
Для диаметра оси в опоре А (см. рисунок 6.2) d=55 мм предварительно выбираем подшипник №1211 для него значение базовой статической радиальной грузоподъемности равно COr=10300 Н. Для диаметра оси в опоре В d=65 мм выбираем подшипник №1213 для него это значение равно COr=13000 Н.
При расчете на статическую грузоподъемность проверяют не будет ли радиальная Fr нагрузка на подшипник превосходить статическую грузоподъемность указанную в каталоге:
Найдем радиальные силы в точках А и В:
где RA=13652 - нагрузка на опору А Н;
где RВ=12664 - нагрузка на опору В Н;
Выбранные ранее подшипники удовлетворяют условию по формуле (6.20) оставляем Подшипник 1211 ГОСТ 28428-90 для опоры А и Подшипник 1213 ГОСТ 28428-90 для опоры В.
РАЗРАБОТКА МЕТАЛЛОКОНСТРУКЦИИ ГРУЗОПОДЪЁМНОГО КРАНА
Подбираем профиль металлоконструкции по моменту сопротивления (относительно оси x):
где момент сопротивления;
изгибающий момент Н·м;
допускаемое напряжение МПа;
Обычно материал профиля изготовляются из: Сталь 3
Определяем допускаемое напряжение:
где предел текучести;
коэффициент запаса прочности .
Подбираем профиль по ГОСТ 8240-89 №50 (двутавр).
УСТРОЙСТВА БЕЗОПАСНОСТИ
Для ограничения высоты подъема выбираем рычажный конечный выключатель КУ 703.
Контактные системы удерживаются в замкнутом положении грузом 1 при переходе крюка за допустимый предел высоты крюковая подвеска упирается в груз 1 и приподнимает его. Контргруз немедленно размыкает контактную систему.
Для ограничения массы поднимаемого груза выбираем ограничитель грузоподъемности с восприятием натяжения грузового каната. Он ограничивает подъем когда масса поднимаемого груза на 10 % превышает грузоподъемность равную 125 т.
При подъеме груза превышающего грузоподъемность хвостовой конец через рычаг действует на контактную систему.
МЕРОПРИЯТИЯ ПО ТЕХНИКЕ БЕЗОПАСНОСТИ
Требования безопасного выполнения работ по перемещению грузов кранами содержатся в п. 413 Правил безопасной эксплуатации грузоподъемных кранов [10].
Так погрузочно-разгрузочные работы и складирование грузов на базах складах площадках должны выполняться по технологическим картам разработанным с учетом требований нормативных документов и утвержденным в установленном порядке. Не разрешается опускать груз на автомашину а также поднимать груз при нахождении людей в кузове или кабине автомашины. В местах постоянной погрузки и разгрузки автомашин и полувагонов должны быть установлены эстакады или навесные площадки для стропальщиков. Погрузка и разгрузка полувагонов крюковыми кранами должны производиться под руководством лица ответственного за безопасное производство работ и по технологии утвержденной производителем работ в которой должны быть определены места нахождения стропальщиков при перемещении грузов а также возможность выхода их на эстакады и навесные площадки. Нахождение людей в полувагонах при подъеме и опускании грузов краном не допускается.
Перемещение груза не должно производиться при нахождении под ним людей. Стропальщик может находиться возле груза во время его подъема или опускания если груз поднят на высоту не более 1000 мм от уровня площадки.
Строповка грузов должна производиться в соответствии со схемами строповки. Для строповки предназначенного к подъему груза должны применяться стропы соответствующие массе и характеру поднимаемого груза с учетом числа ветвей и угла их наклона; стропы общего назначения следует подбирать так чтобы угол между их ветвями не превышал 90°.
Перемещение мелкоштучных грузов должно производиться в специально для этого предназначенной таре при этом должна исключаться возможность выпадения отдельных грузов. Подъем кирпича на поддонах без ограждения разрешен при погрузке и разгрузке (на землю) транспортных средств.
Перемещение груза масса которого неизвестна должно производиться только после определения его фактической массы.
Груз или грузозахватное приспособление при горизонтальном перемещении должны быть предварительно подняты на 500 мм выше встречающихся на пути предметов.
При перемещении стрелового самоходного крана с грузом положение стрелы и нагрузка на кран должны устанавливаться в соответствии с руководством по эксплуатации крана.
Опускать перемещаемый груз разрешается лишь на предназначенное для этого место где исключена возможность падения опрокидывания или сползания устанавливаемого груза. На место установки груза должны быть предварительно уложены подкладки соответствующей прочности для того чтобы стропы могли быть легко и без повреждения извлечены из-под груза. Устанавливать груз в местах для этого не предназначенных не разрешается. Укладку и разборку груза следует производить равномерно не нарушая установленных для складирования груза габаритов и не загромождая проходов. Укладка груза в полувагоны на платформы должна производиться в соответствии с установленными нормами по согласованию с грузополучателем. Погрузка груза в автомашины и другие транспортные средства должна осуществляться таким образом чтобы была обеспечена удобная и безопасная строповка его при разгрузке. Погрузка и разгрузка полувагонов платформ автомашин и других транспортных средств должны выполняться без нарушения их равновесия.
Не допускается нахождение людей и проведение каких-либо работ в пределах перемещения грузов кранами оснащенными грейфером или магнитом. Подсобные рабочие обслуживающие такие краны могут допускаться к выполнению своих обязанностей только во время перерывов в работе кранов и после того как грейфер или магнит будут опущены на землю. Места производства работ такими кранами должны быть ограждены и обозначены предупредительными знаками.
Не допускается использование грейфера для подъема людей или выполнение работ для которых грейфер не предназначен.
По окончании работы или в перерыве груз не должен оставаться в подвешенном состоянии а выключатель подающий напряжение на главные троллеи или гибкий кабель должен быть отключен и заперт на замок. По окончании работы и во время перерывов в работе башенного портального козлового кранов и мостового перегружателя кабина управления должна быть заперта а кран укреплен всеми имеющимися на нем противоугонными устройствами с оформлением крановщиком соответствующей записи в вахтенном журнале.
Кантовка грузов кранами должна производиться с использованием специальных приспособлений (кантователей) и в специально отведенных местах. Выполнение такой работы разрешается только по заранее составленной технологии определяющей последовательность выполнения операции и указания по безопасному производству работ.
При работе мостовых кранов установленных в несколько ярусов должно выполняться условие проезда кранов верхнего яруса над кранами расположенными ниже только без груза с крюком поднятым в верхнее рабочее положение.
При подъеме груза он должен быть предварительно поднят на высоту не более 200–300 мм для проверки правильности строповки и надежности действия тормоза.
При подъеме груза установленного вблизи стены колонны штабеля железнодорожного вагона станка или другого оборудования не должно допускаться нахождение людей между поднимаемым грузом и указанными частями здания или оборудованием. Это требование должно также выполняться при опускании и перемещении груза [11].
В ходе курсового проекта был спроектирован консольный передвижной кран с тележкой. Были произведён проектировочный и проверочный расчеты всех механизмов крана: подъема передвижения тележки передвижения крана. Также рассчитали металлоконструкцию крана: подтележечную балку торцевую балку ферму. Графическая часть курсового проекта содержит 3 чертежа: общий вид крана сборочный чертеж механизма подъема и передвижения тележки.
СПИСОК ИСПОЛЬЗУЕМЫХ ИСТОЧНИКОВ
Марон Ф.Л. Справочник по расчетам механизмов подъемно-транспортных машин. - 2-е изд. перераб. и доп. - Мн.: Высш. шк. 1983.- 350 с. ил.
Гохберг М.М. Справочник по кранам в 2 т. Т.1 Характеристики материалов и нагрузок. Основы расчета кранов их приводов и металлических конструкций В.И. Брауде М.М. Гохберг И.Е. Звягин и др.; Под общ. Ред. М.М. Гохберга. - Л.: Машиностроение. Ленингр. Отд-ние 1988. - 536 с.: ил.
Гохберг М.М. Справочник по кранам в 2 т. Т.2 Характеристики конструктивные схемы кранов. Крановые механизмы их детали и узлы. Техническая эксплуатация кранов М.П. Александров М.М. Гохберг А.А. Ковин и др.; Под общ. Ред. М.М. Гохберга. - Л.: Машиностроение. Ленингр. Отд-ние 1988 - 559 с.: ил.
Правила устройства и безопасной эксплуатации грузоподъемных кранов. ПБ 10-382-00. Утверждены постановлением Госгортехнадзора России от 31.12.1999г. N 38.
Руденко Н.Ф Курсовое проектирование грузоподъемных машин. Руденко Н.Ф. Александров М.П. и Лысяков А.Г. Изд. 3-е переработанное и дополненное.-М. изд-во «Машиностроение» 1971 464 стр.
Крановое электрооборудование. Справочник под ред. канд. техн. наук А. А. Рабиновича.-М: 1979 239с. ил.
Расчеты крановых механизмов и их деталей. ВНИИПТМАШ. Издание 3-е переработанное и дополненное. М. «Машиностроение» 1971 496 стр. Додонов Б.П. Лифанов В. А. Грузоподъемные и транспортные устройства: Учебник для техникумов. - М.: Машиностроение 1984. - 136 с. ил.
Грузоподъемные машины: Учебник для вузов по специальности «Подъемно-транспортные машины и оборудование» М.П. Александров Л.Н. Колобов Н.А. Лобов и др.: - М.: Машиностроение 1986 - 400 с. ил.
Курсовое проектирование грузоподъемных машин: Учеб. пособие для студентов машиностр. спец. вузовС.А. Казак В.Е. Дусье Е.С. Кузнецов и др.; Под ред. С.А. Казака.-М.: Высш. шк. 1989.-319с.: ил.
Постановление МЧС РБ от 28.06.2012 № 37 «Об утверждении Правил устройства и безопасной эксплуатации грузоподъемных кранов» (Правила безопасной эксплуатации грузоподъемных кранов).
Правила по обеспечению промышленной безопасности грузоподъемных кранов утвержденных постановлением Министерства по чрезвычайным ситуациям Республики Беларусь от 22 декабря 2018 г. № 66
ЛИСТ1 Общий вид крана ДОДЕЛКА2.dwg

«Правилам устройства и безопасной эксплуатации грузоподъемных кранов» (ПБ 10-382-00)'
«Правилам устройства электроустановок» (ПУЭ) и комплекту конструкторской документации
Кран следует снабдить укрепленной на видном месте табличкой с указанием наименования
предприятия-изготовителя или его товарного знака
а также других сведений в
соответствии с нормативными документами.
Сварные соединения несущих и вспомогательных металлоконструкций кранов
должны быть выполнены в соответствии с ОСТ 24.090.63.
Предварительное покрытие наружных поверхностей металлоконструкций и механизмов -
грунтовка ГФ - 0119 ГОСТ 23343 в один слой.
Окончательное покрытие должно производиться потребителем после монтажа крана
эмалью ПФ - 115 ГОСТ 6465 в два слоя. Класс покрытия по ГОСТ 9.032.
Вылет крюка: наименьший
Высота подъема груза
Вылет крюка: наибольший
передвижения тележки
Техническая характеристика
Схема запасовки каната механизма подъема
Кинематическая схема привода
механизма передвижения тележки
механизма подъема крана
Механизм передвижения крана
Металлоконструкция крана
Технические требования
Кран ОВ СП.dwg

Механизм передвижения тележки
Титульный.doc
Белорусский национальный технический университет
Факультет транспортных коммуникаций
Кафедра «Механизация и автоматизация дорожно-строительного комплекса»
по дисциплине «Подъемно-транспортные машины»
На тему: «Спроектировать консольный передвижной кран»
ПОЯСНИТЕЛЬНАЯ ЗАПИСКА
Исполнитель: студент гр. 31402118
Руководитель: ст.пр. А.А. Бежик
МЕХ передв тележки СП.dwg

Муфта зубчатая ГОСТ50895-96
Муфта зубчатаяГОСТ50895-96
Подшипник №210 ГОСТ8338-75
Шпонка 20х16х90 ГОСТ23360-78
Шпонка 14х12х70 ГОСТ23360-78
Муфта упругаяГОСТ21424-93
Электродвигатель MTF-200
Шпонка 8х7х40 ГОСТ23360-78
ЛИСТ 2 Механизм передвиж тележки-доделка2.dwg

должны быть выполнены в соответствии с ОСТ 24.090.63.
Предварительное покрытие наружных поверхностей металлоконструкций и механизмов -
грунтовка ГФ - 0119 ГОСТ 23343 в один слой.
Окончательное покрытие должно производиться потребителем после монтажа крана
эмалью ПФ - 115 ГОСТ 6465 в два слоя. Класс покрытия по ГОСТ 9.032.
Техническая характеристика:
Механизм передвижения тележки
Группа классификации
Кинематическая схема привода передвижения тележки
Механизм передвижения
Технические требования
МЕХ подъема СП.dwg

Муфта зубчатаяГОСТ50895-96
Электродвигатель MTF311-8
Шпонка 14х9х70 ГОСТ23360-78
Шпонка 32х18х215 ГОСТ23360-78
Рекомендуемые чертежи
- 25.10.2022