Консольный передвижной кран со спецзахватом и приспособлением для высвобождения груза 1 т




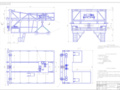
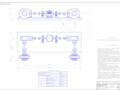


- Добавлен: 25.10.2022
- Размер: 3 MB
- Закачек: 1
Описание
Состав проекта
![]() |
![]() ![]() |
![]() ![]() |
![]() ![]() ![]() ![]() |
![]() ![]() ![]() ![]() |
![]() ![]() ![]() ![]() |
![]() ![]() |
![]() ![]() |
![]() |
![]() ![]() |
![]() ![]() |
![]() ![]() |
![]() ![]() |
![]() |
![]() ![]() |
![]() ![]() |
![]() ![]() |
![]() |
![]() ![]() |
![]() |
![]() |
![]() |
![]() |
![]() |
![]() |
![]() ![]() ![]() |
![]() ![]() ![]() |
![]() ![]() |
![]() ![]() |
![]() ![]() |
![]() ![]() ![]() ![]() |
![]() ![]() ![]() ![]() |
![]() ![]() ![]() ![]() |
![]() ![]() |
![]() ![]() ![]() ![]() |
![]() ![]() ![]() |
Дополнительная информация
СБ2.dwg

ПензГУ1.3-08.190205.102СБ2
Механизм передвижения
Сборку механизма передвижения производить на кране
установленном на все колеса
а) осевой ход для плавающих валов 5-10 ммсм. поз.6.
в) вертикальная плоскость симметрии каждого кодового колеса
не должна смещаться от вертикальной плоскости симметрии
смещение на каждой стороне крана
должно быть в одну сторону.
г) отклонение геомертических осей ходовых колес от общей
горизонтальной плоскости должно быть не более 3 мм.
д) отклонение торцевой плоскости каждого ходового колеса от
вертикальной плоскости параллельной оси подкранового рельса
не должно превышать 1 мм на 1000 мм в любом направлении.
е) разность диагоналей
измеренная по осям ходовых колес
отверстие для сливной трубки редуктора выполнить со
стороны входного вала.
Толщина регулировочных прокладок под редукторы
электродвигатели и тормоза определяется по месту при
установе и выверке механизма передвижения. Разрешается
ставить только одну регулировочную прокладку.
Кожухи на зубчатые муфты должны открываться в сторону
подкладок и сухарей производить
катетом 4 мм электродом Э42
После сборки на заводе мехинизм передвижения крана без
груза обкатать при номинальном числе оборотов заказанного
электродвигателя. Для этого приводную сторону крана
приподнять и опереть на подкладки
установленные в местах -
соединения главных торцевых балок.
Скорость передвижения
Продолжительность включения
Техническая характеристика
Технические требования
ВО.dwg

Грузоподъёмность 10 кН.
Вылет крюка: наибольший 5.5 м
Высота подъёма груза 9 м
Скорость: подъёма груза 8 ммин
передвижения крана 37 ммин
передвижения тележки 19 ммин
Отклонение ходового рельса не более 0
Обеспечить уклон ходового пути не более 0
ПензГУ1.3-08.190205.102 ВО
*Размер для справок.
Неуказанные предельные отклонения размеров: отверстий
Наличие трещин металлоконструкции не допускается.
Проскальзывание ходовых колёс крана и тележки не допускается.
Металлические покрытия красить маслостойкой эмалью ПФ-113
Технические требования
СП2.dwg

Механизм передвижения
ПензГУ1.3-08.190205.102СБ2
Электродвигатель МТF-116-4
ПензГУ1.3-08.190205.102СБ8
ПензГУ1.3-08.190205.102СБ9
ПЗ.doc
Ключевые слова: кран консольный механизм подъёма приспособление для высвобождения груза канат вылет высота подъёма.
В настоящем курсовом проекте приведены расчёты по проектированию консольный передвижной кран и приспособления для высвобождения груза специального грузозахвата. Проект состоит из пояснительной записки и листов графической работы.
Записка содержит титульный лист реферат содержание работы введение 2 основных раздела заключение. Записка выполнена на 49 листах содержит 129 формул 13 таблиц.
Графический материал изложен на 4 листах формата А1 и содержит: на I листе общий вид крана на II листе сборочный чертёж тележки на III листе сборочный чертёж механизма передвижения крана на IV листе сборочный чертёж специального захвата с приспособлением для высвобождения груза.
Раздел I Проектный расчёт крана 6
Предварительные расчёты . ..-
1 Механизм подъёма -
1.1 Выбор двигателя -
1.2 Расчёт редуктора 9
1.3 Выбор тормоза ..24
2 Механизм передвижения крана .. .25
2.1 Выбор кинематической схемы -
2.2 Выбор электродвигателя 26
2.3 Выбор редуктора .. 27
2.4 Выбор тормоза .28
Уточняющие расчёты 30
1 Проверка механизма подъёма .-
1.1 Проверка редуктора ..-
1.2 Проверка по времени пуска .31
1.3 Проверка по времени торможения 33
2 Проверка механизма передвижения крана .. 34
2.1 Проверка по времени пуска 36
2.2 Проверка по времени торможения ..37
Раздел II Техническое предложение и расчёт специального захвата .. .39
Патентно – информационный поиск ..-
Описание предлагаемой конструкции ..45
Расчёт захвата и приспособления для высвобождения груза 46
Список использованной литературы. ..49
В современной промышленности на ряде производств встаёт проблема автоматизации работы кранового оборудования например литейные комбинаты объекты крупномасштабного строительства и.т.д. Подъёмная техника может иметь полную (что редко встречается) автоматизацию или частичную. К последней можно отнести возможность специального захвата высвобождать перемещаемый груз после того как он оказался на месте разгрузки.
Возможность автоматического высвобождения груза в ряде случаев является необходимым условием для работы к примеру можно отнести большую часть металлургических кранов; объекты преобразования ядерной энергии (атомные реакторы); скоростная перегрузка в портах. Все эти случаи объединяет либо вредные условия для нахождения человека либо связано с высокой требуемой скоростью перегрузочных работ [1-11].
В настоящем курсовом проекте будет рассмотрен случай высвобождения листового материала что часто требуется при строительстве и транспортных узлах (порты вокзалы).
Раздел I Проектный расчёт крана [1-9]
Предварительные расчёты
Выбор двигателя выполняется после выбора ряда элементов механизма.
Выбираем полиспаст исходя из грузоподъёмности. По рекомендации [1] принимаем одинарный полиспаст с кратностью u=4 согласно практическому опыту эксплуатации грузоподъёмных машин (ГПМ).
Выбор крюковой подвески крана выполняем в соответствии с типом груза перемещаемого краном. В настоящем случае кран на колонке с грузоподъёмностью 10 т и работающий в крытом цеху для данной машины подойдёт подвеска с однорогим крюком. Выбираем тип подвески 2 подвески с однорогим крюком по ОСТ24.191.08-81. Группа режима 2К соответствует среднему режиму работы.
Выбранная крюковая подвеска соответствует всем условиям выбора:
Грузоподъёмность подвески больше требуемой;
Режим работы подвески соответствует режиму работы механизма.
Выбираем канат исходя из условий (2) и (3). Материал для каната согласно ГОСТ7372-79 принимаем В1. Рассчитаем максимальное статическое усилие в канате Smax по формуле (1).
Где G – вес номинального груза и крюковой подвески G = 10000Н;
Zк.б. – число ветвей каната навиваемых на барабан Zк.б. = 1;
u – кратность полиспаста u = 3;
п – к.п.д. полиспаста п = 099;
н.бл. – к.п.д. направляющих блоков п = 098.
Где Sразр – разрывное усилие каната в целом Н;
kзап – коэффициент запаса прочности каната;
Значение коэффициента запаса принимаем исходя из таблицы 1
Таблица 1. Коэффициент прочности каната
Группа режима работы по ГОСТ25835-83
Коэффициент запаса прочности каната
Где Dбл – диаметр блока измеряемый по средней линии навитого каната мм;
dк – диаметр каната мм;
е – коэффициент регламентируемый нормами Ростехнадзора зависит от типа машины и режима работы; величина е обратно пропоциональна степени изгиба каната на блоке.
Коэффициент е выбираем из таблицы 2
Таблица 2. Коэффициент е
Группа режима работы
ГПМ всех типов за исключением стреловых кранов электроталей и лебёдок
Лебёдки для подъёма грузов и электротали
Принимаем канат двойной свивки типа ЛК-Р конструкции 6х19 (1+6+66)+1 о.с. по ГОСТ2688-80
Расчётная площадь сечения мм2
Масса 1000 м смазанного каната кг
Маркировочная группа МПа
Разрывное усилие кН не менее
Условиия (2) и (3) выполняются оставляем канат ЛК-Р 6х19 (1+6+66)+1 о.с. ГОСТ2688-80 параметры каната в таблице 3 [2].
Перед тем как выбрать двигатель выполним расчёт или выбор барабана.
Определяем основные размеры сборочной единицы «установка барабана» приведём изображение его привода. Так как в настоящем случае имеется простейший одинарный полиспаст то барабан выбираем с гладкими стенками одинарный.
Рассчитаем размеры барабана.
Уточняем из стандартного ряда и принимаем Dб = 400 мм.
Диаметр максимальной окружности описываемой крайней точкой установки барабана Dmax определяем предварительно по формуле
Принимаем Dmax = 500 мм.
Длина участка барабана с витками lн
Где zр – число рабочих витков;
zнепр – число неприкосновенных витков zр = 15;
Предварительно принимаем величины lпер = 7 мм и lр = 10 мм. Точных формул для расчёта этих параметров нет.
Тогда длина барабана
Высота оси барабана относительно основания внешней опоры принимаем
Таким образом были найдены приближённые геометрические параметры барабана.
Выбираем электродвигатель исходя из требуемой статической мощности. Максимальная статическая мощность Nст.max которую должен иметь механизм в период установившегося движения при подъёме номинального груза равна
Где пр – предварительное значение к.п.д. механизма пр = 08 085.
Так как группа режима работы крана (а значит и механизма подъёма) 4К то выбираем двигатель серии МТН отличающийся от других серий более высоким классом нагревостойкости следовательно могут переносить перегрузки более длительного характера. Двигатели серии МТН могут использоваться при высокой интенсивности работы механизма [3].
При выборе электродвигателя следует руководствоваться двумя условиями:
Относительная продолжительность включения (ПВ) двигателя должна соответствовать относительной продолжительности включения электрооборудования;
Номинальная мощность выбираемого двигателя может быть меньше максимальной статической мощности:
Предварительно выбираем двигатель МТН 112-6 его параметры занесены в таблицу 4.
Таблица 4. Параметры двигателя
Момент инерции ротора
1.2 Расчёт редуктора
Для начала расчёта редуктора рассчитаем требуемую частоту вращения барабана и необходимое передаточное отношение между двигателем и барабаном.
Частота вращения барабана:
Требуемое передаточное отношение редуктора:
При таком значении передаточного отношения применяются редукторы трёхступенчатые имеющие значительные массу и размеры или редукторы с червячной передачей которые сложнее в изготовлении и имеют меньший ресурс работы однако они значительно легче и компактнее цилиндрических. Спроектируем редуктор с червячной передачей а также в конструкцию которого входит цилиндрическая передача.
Распределяем передаточные соотношения между передачами следующим образом так что червячная передача uч=30 цилиндрическая uц=318.
Рассчитаем параметры червячной передачи. Определяем исходные данные.
Т1-вращающий момент на валу червяка Нм;
Т2-вращающий момент на валу колеса Нм;
u-передаточное число u=30;
n1-частота вращения червяка мин-1;
n2-частота вращения колеса мин-1;
[Н]-допускаемое контактное напряжение МПа;
[F]-допускаемое напряжение изгиба МПа.
Моменты Т1 Т2 определяем по формуле (16)
Где Р – мощность на валу кВт;
n – частота вращения вала мин-1.
Мощность по формуле (17)
– к.п.д. предыдущей передачи.
u – передаточное число предыдущей передачи.
Для выбора материала потребуется вычислить предварительное значение скорости скольжения
Коэффициент учитывающий интенсивность изнашивания материала Сv=133.
Коэффициенты долговечности (21)
Где NHE2 NFE2 – эквивалентное число циклов нагружения зуба колеса.
В качестве материала принимаем бронзу Бр 06Ц6С3. Проверим правильность выбора и вычислим значения [Н] и [F].
Материал удовлетворяет предъявляемым требованиям
Исходные данные для расчёта червячной передачи
Число витков червяка выбираем из таблицы 5.
Таблица 5. Число витков червяка
Число зубьев червячного колеса
Предварительное значение межосевого расстояния
Где K' – предварительное значение коэффициента концентрации нагрузки.
Где K° –теоретическое значение коэффициента концентрации нагрузки.
Уточняем из стандартного ряда получаем значение мм.
Значение найдём по формуле (I.1.28)
Коэффициент смещения при нарезке
x>1 принимаем значение z2=62 тогда
>x>-1. Проверим значение передаточного отношения
Углы подъёма витков червяка
На делительном диаметре
На начальном диаметре
Уточняем расчётные параметры передачи путём проверочного расчёта
Коэффициент нагрузки
Коэффициент концентрации нагрузки
Где – коэффициент деформации червяка =171.
Окружная скорость червячного колеса
По табличным значениям принимаем .
Окружная скорость на начальном диаметре червяка
Скорость скольжения в зацеплении
Проверяем и уточняем значение допустимой контактной прочности по условию
Принимаем материал Бр А9Ж4 в=500 МПа т=200 МПа.
Расчётное контактное напряжение
Оставляем рассчитанные параметры за окончательные.
Геометрические размеры передачи
Делительный диаметр (I.1.39)
Диаметр вершин витков (I.1.40)
Диаметр впадин витков (I.1.41)
Длина нарезанной части червя (I.1.42)
Делительный диаметр мм
Определение напряжений изгиба в зубьях червячного колеса
Где - коэффициент нагрузки ;
- коэффициент формы зуба для червячного колеса.
Коэффициент полезного действия передачи
Где φ – угол трения φ=13°.
Значение кпд довольно высокое проверку на нагрев проводить нет смысла.
Определение сил в зацеплении
Окружная сила на колесе
Окружная сила на червяке
Радиальная сила раздвигающая червяк и колесо
Рассчитаем цилиндрическую передачу.
Для расчета передачи потребуются следующие данные:
Т1 – вращающий момент на шестерне Т1=032 кНм;
Т2 – вращающий момент на колесе Т2=46 кНм;
n2 – частота вращения колеса n2=294 мин-1;
u – передаточное число u=318;
[Н] – допускаемое контактное напряжение МПа;
[F]1 – допускаемое напряжение изгиба зубьев шестерни МПа;
[F]2 – допускаемое напряжение изгиба зубьев колеса МПа.
Выбираем материал для колеса и шестерни откуда возьмём прочностные характеристики. Принимаем Сталь 45 ГОСТ1050-88 её характеристики приведены в таблице 6.
Таблица 6. Характеристики Сталь 45.
Предел прочности в МПа
Предел текучести т МПа
Допускаемые контактные напряжения
zR – коэффициент учитывающий шероховатость рабочих поверхностей зубьев zR=09;
zV – коэффициент учитывающий влияние скорости zV=1;
zN – коэффициент долговечности учитывающий режим нагружений и требуемый ресурс передачи;
sH – коэффициент запаса контактной прочности sH=12.
Nк – требуемый ресурс рассчитываемого зубчатого колеса в циклах.
Где с – число вхождений в зацепление одного зуба рассчитываемого колеса за один оборот с=1;
n – частота вращения рассчитываемого колеса мин-1;
Lh – требуемый ресурс передачи ч.
Где Lr – срок службы передачи Lr=10 лет;
Кгод – коэффициент использования передачи в течение года Кгод=075;
Ксут – коэффициент использования передачи в течение суток Ксут=065.
Из двух значений принимаем наименьшее [н]=833 МПа.
Допускаемые напряжения изгиба зубьев
yN – коэффициент долговечности;
sF – коэффициент запаса изгибной прочности sF=17.
Где mF – показатель степени кривой усталости mF=6.
Итак были найдены исходные данные для расчёта цилиндрической передачи:
Определение предварительного значения межосевого расстояния
Где К – коэффициент учитывающий твёрдость поверхности зубьев К=10;
± – знак учитывающий тип зацепления «+» при внешнем зацеплении;
Уточнение найденного значения межосевого расстояния
Где Ка – коэффициент учитывающий тип зубьев Ка=450;
ba – коэффициент ширины зубчатого колеса ba=04;
КН – коэффициент нагрузки.
Где КНV – коэффициент учитывающий внутреннюю динамическую нагрузку зависит от окружной скорости V и качества поверхности;
КН – коэффициент учитывающий неравномерность распределения нагрузки по длине контактных линий определяется по номограммам;
КНα – коэффициент учитывающий неравномерность распределения нагрузки между одновременно зацепляющимися парами зубьев в связи с погрешностью изготовления шестерни и колеса.
Тогда при точности 7 КНV=104.
Находим приближённое значение КН=105.
Где nст – степень точности передачи nст=7.
Принимаем по стандартному ряду чисел значение межосевого расстояния aw=250мм.
Округляем значения ширины b1 =120 мм; b2=100 мм
Определение нормального модуля зубьев. Значение модуля должно быть в пределах mmin≤m≤mmax.
Где Кm =2600 – для косозубых передач;
КF – коэффициент нагрузки принимаемый равным КН.
Из стандартного ряда чисел выбираем значение нормального модуля mn=50 мм.
Расчёт количества зубьев. Суммарное количество зубьев на шестерни и венце
Число зубьев шестерни
Тогда для колеса получаем количество зубьев z2.
Итак z1=24 зуба z2=76 зуба.
Фактическое передаточное отношение
Подсчитаем отклонение от требуемого передаточного отношения
Проверочный расчёт на контактную выносливость
Проверочный расчёт на выносливость при изгибе
Где КF – коэффициент нагрузки;
yFS – коэффициент учитывающий форму зуба и концентрацию напряжений;
y – коэффициент учитывающий наклон зуба;
y – коэффициент учитывающий перекрытие зубьев.
Где КFV – коэффициент учитывающий внутреннюю динамическую нагрузку в передаче;
КF – коэффициент учитывающий неравномерность распределения нагрузке по длине контактных линий;
КFα – коэффициент учитывающий неравномерность распределения нагрузки между одновременно зацепляющимися парами зубьев в связи с погрешностями изготовления шестерни и венца КFα=КHα=112.
Где α – коэффициент торцевого перекрытия
Проверки на контактную прочность и изгиб подтверждают правильность проведения расчёта.
Определение геометрических параметров передачи
Делительный диаметр колёс
Диаметр вершин зубьев
Диаметр впадин зубьев
Определение сил в зацеплении необходимых для расчёта валов и подшипников
Так как подшипник предварительно выбран то проводим проверочный расчёт с целью определения ресурса выбранного подшипника для заданных условий эксплуатации и сравнения его с требуемым Lh.тр=15000 ч.
Где n – частота вращения кольца мин-1;
L – ресурс подшипника млн. оборотов.
Где а1 – коэффициент долговечности а1=1;
а23 – коэффициент учитывающий качество металла деталей подшипника и условия эксплуатации а23=07;
Р – показатель степени Р=3;
ΣСr – динамическая радиальная грузоподъёмность Н;
Рr – эквивалентная динамическая радиальная нагрузка Н.
V – коэффициент вращения V=12;
k – коэффициент безопасности учитывающий характер нагрузки k=14;
kт – коэффициент учитывающий температуру подшипникового узла kт=1.
Выбираем в качестве опор для червячной передачи подшипники роликовые конические а для шестерни цилиндрической передачи подшипники радиально – упорные. Расчётные схемы приведены в источнике [].
Определяем силу FА для вала с червяком и зубчатым колесом. Расположим колесо относительно червяка таким образом чтобы возникающие осевые усилия гасили друг дружку тогда
FА=Fач – Fак=69677 – 1941=67736 Н.
Радиальные силы Frч=25360 Н Faк=2066.
Предварительно принимаем подшипник 2007109 Сor=34900 Н Сr=44000 Н.
Запишем уравнение статического равновесия
Будем считать что первая опора (слева) будет располагаться вверху. Принимаем Fa1=S1 тогда
Найдём значение отношения
По таблице находим X=056; Y=10 для 1 опоры X=056; Y=10 для 2.
Так как данный подшипник не удовлетворяет условию по динамической грузоподъёмности то применим подшипник 2007120 Сor=120000 Н Сr=132000 Н а в узле применим сдвоенный подшипник.
Проверяем по статической грузоподъёмности X0=10; Y0=044ctg12=375.
значение нагрузки во II опоре превышает допустимые значения. Применим два конических подшипника. На валу с червячным колесом применим аналогичные подшипниковые узлы так как на этот вал действуют примерно такие же по значению нагрузки.
Рассчитаем подшипниковый узел на цилиндрической шестерне. Так как при работе цилиндрической передачи появляются осевые силы то применим радиально – упорные подшипники. Массой вала и шестерни будем пренебрегать. Осевая сила FA=1941 Н радиальная сила Fr=2066 Н согласно расчёту передачи. Предварительно выбираем узел со сдвоенным подшипником лёгкой серии 36204 Cor=831 кН Cr=157 кН. Рассчитаем значение е' для каждой из опор. Будем считать что первая опора справа.
Принимаем Fa1=S1 тогда
По таблице находим X=1; Y=0 для 1 опоры X=045; Y=1 для 2.
Проверяем по статической грузоподъёмности
X0=05; Y0=ctg12=047.
CorΣ=2Cor=2831=1662.
Проверка подшипникового узла показывает правильность выбранного номера оставляем радиально – упорный подшипник лёгкой серии 36204.
Рассчитаем толщину стенок редуктора по формуле (82).
Коэффициент полезного действия редуктора
Выбираем тормоз. Тормоз выбирается исходя из условия необходимого тормозного момента (или расчётного тормозного момента) Тт.р.
Где kт – коэффициент запаса торможения kт =20;
Тст.т – статический крутящий момент при торможении создаваемый весом номинального груза на валу на котором устанавливается тормоз.
uмех – полное передаточное число механизма включая передаточное число полиспаста.
Выбираем тип тормоза – тормоз марки ТКП. Характеристики узла приведены в таблице 7.
Таблица 7. Тормозные моменты тормоза ТКП 400 Нм.
Катушка параллельного возбуждения
Катушка последовательного возбуждения
Выбираем ТКП-400 так как он удовлетворяет всем требованиям Тт.тр.=1200 при ПВ=40% с катушкой параллельного возбуждения.
Выбираем муфту втулочно – пальчиковую с тормозным шкивом диаметром 400 мм ГОСТ 5006 – 55.
Таким образом был выполнен предварительный расчёт механизма подъёма крана на неподвижной колонке. Были выбраны основные элементы механизма: крюковая подвеска канат электродвигатель рассчитан редуктор.
2 Механизм передвижения крана
2.1 Выбор кинематической схемы
Для перемещения крана спроектируем механизм. Механизмы передвижения настенного крана как правило имеют центральный привод с тихоходным трансмиссионным валом. Выбираем кинематическую схему механизма которая представлена на рисунке 1.
Рисунок 1 Кинематическая схема механизма передвижения
2.2 Выбор электродвигателя
Выбор электродвигателя зависит от сопротивления которое приходится преодолевать при работе механизма передвижения.
Момент сопротивления (Н*м) и силу сопротивления (Н) действующие на ходовом колесе с учётом коэффициента трения реборд можно определить по следующим выражениям:
По таблицам принимаем:
m =04; Dх.к = 250мм; d = 63мм; f = 002; К=2 – коэффициент режима;
Вес тележки Gт равен
Подставив числа получим
Сила инерции поступательно движущихся масс (груза и тележки)
где d = 125 - коэффициент учитывающий инерцию вращающихся частей механизма (при скорости передвижения менее 1 мс принимать d = 125; если скорость передвижения больше 1 мс d = 115);
mпост - масса поступательно движущегося объекта ( mгр + mт ). В этой формуле mгр mт – масса груза и тележки соответственно кг;
а - ускорение при разгоне мс2.
Значение ускорения а предварительно можно принять равным (05 10)[a] где [a] - допускаемое ускорение мс2. После подстановки чисел получим:
Без учета ветровой нагрузки и нагрузки от уклона пути
Необходимая пусковая мощность двигателя с учетом коэффициента пусковой перегрузки равного 15 для одного двигателя в механизме передвижения
Выбираем двигатель MTKF 012-6 Рдв = 06 кВт; nдв = 835 мин-1;
Jдв = 0022 кг*м2; Тmax = 67 Нм.
Частота вращения ходовых колес определяется по формуле
Передаточное число редуктора
Момент на выходном валу редуктора
Типоразмер выбирается по эквивалентному моменту (Креж=084)
Выбираем редуктор ЦЗвк-200 uр = 124; Тн = 300 Нм.
Принимаем величину допускаемого замедления равным 015 мс2.
Момент сил инерции приведённый к валу электродвигателя
Предварительно принимаем диаметр тормозного шкива Dт равным 100 мм. Тормозной шкив изготовлен совместно с втулочно-пальцевой полумуфтой и ее момент инерции Jм равен 004 кг*м2. При торможении
Момент сил сопротивления передвижению при торможении
Направление момент Тст совпадает направлением момента тормоза и необходимый тормозной момент
Выбираем тормоз ТКТ-100 диаметр тормозного шкива Dт = 100 мм; Тт до 20 Нм.
При расчетном тормозном моменте должен обеспечиваться достаточный запас сцепления колёс с рельсами.
Сила инерции при торможении тележки с грузом;
Максимальное усилие на колесо для тележки мостового крана
Усилие сцепления на ободе приводных колёс
где f0 – коэффициент сцепления колёс с рельсами (f0 = 02).
Запас сцепления достаточный так как наименьшая допускаемая величина b равна 12 14.
1 Проверка механизма подъёма
1.1 Проверка редуктора
Проверяем условия касающиеся прочности долговечности и кинематики редуктора.
Первое условие – расчётный эквивалентный момент на тихоходном валу редуктора Тр.э. не должен превышать номинальный крутящий момент на тихоходном валу Тр.н.
Где kд – коэффициент долговечности;
Тр – расчётный крутящий момент на тихоходном валу при подъёме номинального груза.
Где kQ – коэффициент переменности нагрузки;
kt – коэффициент срока службы.
Где k – коэффициент нагружения k=02.
Где zp – суммарное число циклов контактных напряжений зуба шестерни тихоходной ступени редуктора;
z0 – базовое число циклов контактных напряжений z0 =125106.
Где zТ – число циклов нагружения на тихоходном валу редуктора;
uТ – передаточное число тихоходной ступени редуктора принимаем uТ=30.
Где nТ – частота вращения тихоходного вала редуктора;
tмаш – машинное время работы механизма tмаш=20000 ч.
Второе условие – передаточное число редуктора up не должно отличаться от требуемого передаточного числа более чем на ±15%.
Фактическое передаточное число редуктора
Итак спроектированный редуктор удовлетворяет всем условиям выбора и характеристикам.
Проверка скорости подъёма. Рассчитаем фактическое значение скорости подъёма груза для чего воспользуемся формулой (14).
Где nф – фактическая частота вращения барабана мин-1.
Отклонение требуемой скорости подъёма от фактической
Отклонение фактической скорости подъёма груза от требуемой составляет 1% что меньше 5% редуктор спроектирован правильно.
1.2 Проверка по времени пуска
Двигатель должен разгонять механизм за достаточно короткое время иначе уменьшится производительность крана. С другой стороны если оно будет слишком мало то разгон будет сопровождаться большим ускорением что скажется на прочности элементов устойчивости грузов и т. д. Время разгона механизма подъёма принимают 1 4 с. Для механизма подъёма груза наибольшее время затрачивается при разгоне на подъём
Где дв – угловая скорость двигателя дв=979 с-1;
Jмех.р – приведённый к валу двигателя момент инерции при разгоне всех движущихся частей механизма включая поступательно движущиеся массы кгм2;
Тп.ср – среднепусковой момент двигателя Нм;
Тст.р – момент статических сопротивлений при разгоне приведённый к валу двигателя Нм.
Где п.ср – кратность среднепускового момента двигателя п.ср=22;
Тдв.н – номинальный момент двигателя Тдв.н=315 Нм.
Где Jвр – момент инерции при разгоне всех вращающихся частей механизма приведённый к валу двигателя;
Jпост.р – момент инерции при разгоне поступательно движущихся частей механизма и груза приведённый к валу двигателя.
Где γ – коэффициент учёта инерции вращающихся масс расположенных на II III и последующих валах механизма γ=11 12;
J1 – момент инерции вращающихся масс расположенных на первом валу равный сумме моментов инерции якоря двигателя Jр.дв=0056 кгм2 муфты Jм=90 кгм2 и т. д.
Где Dб – диаметр барабана по оси навиваемого каната Dб=04 м;
uмех – полное передаточное число механизма включая полиспаст uмех=2853.
Проверка по времени показывает удовлетворительный результат.
После выполненной проверки необходимо проверить величину ускорения
Допустимое ускорение [а]=02. Таким образом фактическое ускорение груза при подъёме не превышает допустимой величины.
1.3 Проверка по времени торможения
Наиболее неблагоприятным случаем торможения является опускание груза.
Найдём фактическое время торможения
Где m1т – приведённая к грузу при торможении масса вращающихся частей;
m2 – масса груза и крюковой подвески m2=7116 кг;
Vгр0 – скорость груза к моменту начала торможения;
Рт – сила тормоза вызванная действием тормозного момента и приведённая к грузу;
G – вес груза включая вес крюковой подвески G=71160 Н.
Где V – скорость опускания груза мс;
а0 – ускорение опускания груза когда двигатель выключен а тормоз ещё не сработал мс2;
tср – время срабатывания тормоза tср=003 с.
Где Тт – расчётный тормозной момент Тт=88 Нм.
Полное время торможения
Путь опускания груза за время срабатывания тормоза
Полный путь торможения
Нормальным зазором (допустимый тормозной путь) составляет 02 м. Проверка подтверждает возможность работы механизма при выбранных характеристиках конструктивных элементов.
2 Проверка механизма передвижения крана
Первое условие – расчётный эквивалентный момент на тихоходном валу редуктора Тр.э. не должен превышать номинальный крутящий момент на тихоходном валу Тр.н. по паспорту редуктора
Третье условие – частота вращения быстроходного вала редуктора должна быть не меньше частоты вращения двигателя. Так как производитель редуктора не указывает максимальную частоту вращения быстроходного вала то принимаем что третье условие выполняется. Оставляем в конструкции механизма поворота выбранный редуктор.
Параметры передач принимаем исходя из конструктивных соображений.
Определяем фактическое значение передаточного числа механизма
Определяем фактическую частоту вращения крана
Определяем фактическое значение кпд механизма
Фактическое значение требуемой мощности двигателя
Запас по мощности составляет 136.
2.1 Проверка по времени пуска
Номинальный момент электродвигателя
Наименьший коэффициент пусковой перегрузки ymin обычно принимается равным 11 12 наибольший определяется по формуле
где Тmax – максимальный момент электродвигателя.
Средний коэффициент пусковой перегрузки
Тогда средний пусковой момент
Значение момента инерции механизма при разгоне Jмех.р определяется по формуле
Jмех.р = Jвр + Jпост.
где Jвр – момент инерции при разгоне вращающихся масс привода определяется по формуле
Момент инерции поступательно движущихся масс приведенный к валу двигателя определяется по формуле
Здесь Нм – момент сил сопротивления движению приведенный к валу двигателя.
Время пуска двигателя
Среднее ускорение соответствующее этому времени пуска
Это ускорение не превышает допустимое значение.
Время на разгон механизма несколько заниженное однако для крана настенного это допустимо.
2.2 Проверка по времени торможения
Сущность проверки состоит в вычислении времени торможения и сравнения его со временем разгона.
Формула во многом аналогична проверке на время разгона
Где Jмех.т – момент инерции всех движущихся масс механизма приведённые к первому валу кгм2;
Время торможения очень мало что приведёт к перегрузке механизма отрегулируем тормозной момент таким образом чтобы время торможения стало около 1 2 с.
Таким образом выполнили проверочный расчёт механизма поворота. Также было уточнено значение тормозного момента.
Выбор типоразмера муфты производится по максимальному моменту передаваемому данной муфтой по ГОСТ 5006-83.
Муфта втулочно-пальцевая соединяющая вал электродвигателя с промежуточным валом.
Наибольший передаваемый момент 500 Нм
Муфта зубчатая с тормозными шкивами соединяющая промежуточный вал с входным валом редуктора.
Наибольший передаваемый момент 700 Нм
Муфта зубчатая соединяющая выходной вал редуктора с осью ведущих колес (4 муфты).
Наибольший передаваемый момент 119Нм
Раздел II Техническое предложение и расчёт специального захвата [9-11]
Патентно – информационный поиск
Патентно – информационный поиск выполним в следующей последовательности: информационный поиск затем патентный поиск.
Задача перед информационным и патентным поиском заключается в поиске аналогов приспособлений имеющих приспособления для высвобождения груза.
Выполним информационный поиск.
При производстве стропальных работ могут применяться закладные пальцы что сокращает время зачаливания и повышает удобство эксплуатации.
С целью повышения производительности и безопасности производства строповочных работ применяется дистанционная или автоматическая зацепка и отцепка захватных органов стропов. В простых устройствах этого типа захватывающий орган (крюк) поворачивается с помощью рычага или канатика при ослабленных стропах. Несколько сложнее конструкция крюкового захвата с дистанционной расстроповкой технологического оборудования строительных конструкций и других грузов представленная на рисунок 2.
Перекрытый постоянно рогом крюка 1 зев под действием пружины 2 раскрывается при повороте рукоятки 3 натяжением расcтроповочного шнура 4. Скоба 5 на обойме 6 обеспечивает оптимальный угол между расстроповочным шнуром и рукоятью при её горизонтальном положении [9].
Более эффективны в работе строповые ГУ с электромагнитным и пневматическим приводами дистанционного управления и расстроповкой из кабины управления крана которые в большей мере обеспечивают производительность и безопасность такелажных и монтажных работ.
Применение дистанционной и автоматической зацепки и отцепки крюков стропов повышает производительность кранового оборудования и трудастропальщиков и обеспечивает безопасность производства строповочных работ. В простых устройствах этого типа крюк поворачивается с помощью рычага или канатика при ослабленных стропах. Мосоргстроем разработано и широко применяется при строительстве крупнопанельных зданий универсальное строповое ГУ. с дистанционным отцеплением крюков. Наличие колец обеспечивает поворот относительно вертикальной оси обоймы в пределах 120° Грузоподъемность устройства 10т масса 195 кг.
Для строповки и дистанционной расстроповки строительных конструкций технологического оборудования и других грузов применяется ГУ ЗСП-ЗА. На консоли рычага жестко связанного с крюком имеются отверстия и для закрепления деталей. Один конец рукоятки выполненный в виде вилки охватывает рычаг а другой кольцом соединяется с расстроповочным шнуром. Рукоять может поворачиваться на рычаге вокруг оси отверстия на 135° при этом фиксатор входя в зацепленный с любым из четырех пазов на рычаге надежно фиксирует ее положение. В верхней части ГУ вставлен палец для соединения его со стропом грузоподъемного механизма. Зёв перекрывается рогом крюка и под действием пружины постоянно замкнут. Он раскрывается при повороте рукояти непосредственно рукой или натяжением расстроповочного шнура. Скоба на обойме обеспечивает оптимальный угол между рас строповочным шнуром и рукоятью при ее горизонтальном положении [10].
Груз стропят непосредственно зацепляя крюком за монтажные петли или с помощью дополнительных кольцевых стропов обвязкой на «удав». Перед подъемом груза рукоять устанавливают так чтобы при дистанционном раскрытии ГУ угол между натянутым расстроповочным шнуром и рукоятью достигал 90°. Когда соблюдение этого условия невозможно рукоять устанавливают в горизонтальное положение а расстроповочный шнур пропускают через скобу. Для изменения положения рукояти ее оттягивают до выхода фиксатор из зацепления с пазом на рычаге крюка устанавливают в требуемое положение и фиксируют.
Дистанционную расстроповку производят натяжением расстроповочного шнура после снятия нагрузки с крюка. Когда в дистанционной расстроповке нет необходимости рукоять можно установить в крайнее нижнее положение. Грузоподъемность ГУ 3 т габаритные размеры 70х200х320 мм масса 75 кг.
Широко применяется устройство для автоматического освобождения крюка от одного концевого звена петли грузового стропа при снятии с него груза. Устройство монтируемое на стандартном однорогом крюке состоит из двух фигурных скоб. Скоба "верхним концом перекрывает зев крюка что исключает выпадение концевых звеньев стропа при рабочем положении. Щека скобы служит для сбрасывания звена стропа с крюка. Крюк освобождается от петли грузового стропа только при упоре пяты в груз. В этом случае крюк под действием силы тяжести скользит внутри обоймы и звено стропа сбрасывается с крюка. Отмеченные ранее недостатки штырьево – строповых захватов привели к тому что для дальнейшего улучшения управления ими были
Рисунок 3. Захват с электрическим управлением.
разработаны конструкции с дистанционным пневматическим и электрическим управлением (рисунок 3). Общая схема строповки груза показана на рисунке 3 а. Представленные на рисунке 3 б и в захваты грузоподъемностью 10 т идентичны и отличаются только приводом для вытягивания штыря. В конструкции привод рычажно-пневматический при давлении воздуха 3 aтм. В качестве пневмотолкателя использована тормозная камера автомобиля. Вес захвата 45 кГ.
В последнее время были разработаны новые конструкции штырьево – строповых захватов с управлением при помощи тормозных электромагнитов. Основное отличие этих захватов заключается в том что штырьевое устройство размещено в плоскости захвата что дает возможность лучше направлять штырь удлинив опорную втулку.
Такие захваты созданы для изделий (колонн балок ферм и др.) весом 10 и 20 т. В качестве привода для втягивания штыря применены электромагниты типа МПС-8100 работающие на переменном токе при напряжении 127 в; рабочий ход штока магнита 30 мм; передаточное число рычажной передачи 2:1; ход штыря 60 мм; развиваемое усилие для перемещения штыря до 100 кГ.
В захвате грузоподъемностью 10 т применен один электромагнит; в захвате грузоподъемностью 20 т — два электромагнита; штоки их связаны балансирной траверсой. Вес захвата грузоподъемностью 10 т — 85 кГ грузоподъемностью 20 т — 300 кГ.
Все штырьево – строповые захваты с пневматическим и электромагнитным приводом управляются дистанционно крановщиком из кабины крана. Для ликвидации недостатков присущих штырьевым захватам с ручным управлением были разработаны конструкции штырьевых захватов с применением электромеханического привода для перемещения штыря. Управлять приводом можно непосредственно с захвата что необходимо при надевании захвата на перегружаемое изделие и дистанционно из кабины крана что удобно при снятии захвата с изделия.
Захват подвешен на канатных тягах 2 к траверсе 1. Захват выполнен в виде корпуса состоящего из двух боковин 5 соединенных разрезной перемычкой 4. Перемычка выполнена из двух стержней входящих один в другой и соединенных болтами 3 что дает возможность меняя места крепления сдвигать или раздвигать боковины в зависимости от габаритов изделия. В нижней части боковин имеются отверстия снабженные фланцами 15 в которые входит штырь 10. К одной из боковин прикреплена площадка 7 на которой размещается привод штыря состоящий из связанного со штырем поводка — гайки 9 перемещающейся по винту 8 диаметром 40 мм вращаемый через зубчатую передачу 11 реверсивным электродвигателем 12. Крайние положения винта ограничиваются конечными выключателями 14. На площадке 7 размещена кнопочная станция 13 управления электродвигателем. Для электропитания и дистанционного управления используется кабель 6.
Захват может быть применен для оперирования с колоннами весом от 25 до 20 Т толщиной от 400 до 600 мм. Сменными деталями для колонн разных размеров являются штыри и фланцы [11].
Выполним патентный поиск.
Патентно – информационный поиск выполняется на тему: «Строповые грузозахватные устройства».
Наименование работы: «Захват грузоподъёмный строповый».
Перед работой ставятся следующие цели: поиск информации выявление патентной и научно – технической информации позволяющей исследовать технический уровень и тенденции развития захватов строповых с устройствами для высвобождения груза. Обоснование выбора направления при выполнении исследовательской части проекта.
Начало поиска: 01.05.2009
Окончание поиска: 19.06.2009
Определение классов рубрик МПК: B60R22 В66F9.
Глубина поиска: патентная документация опубликованная с 1960 года по настоящее время.
Перечень документов отобранных для анализа и приложения к настоящему отчёту представлен в таблице 1.
Таблица 1. Патентная документация
Страна выдачи вид охранного документа основной индекс МПК
Патентообладатель № заявки дата приоритета дата публикации
Название изобретения
Устройство для строповки изделий
Егорова Галина Борисовна
Поддоны для транспортировки груза и средство строповки груза
Устройство для транспортирования штучных грузов в автоматическом режиме
Система управления грузоподъёмным краном
Автоматический грузовой захват
Автоматический захват
Поиск проведён в соответствии с заданием и регламентом поиска.
Регламент поиска выполнен полностью в соответствии с заданием на проведение патентного исследования.
Поиск по теме: «Строповые грузозахватные устройства» проведён с ретроспективой 49 лет.
Для проведения поиска привлекались материалы из Пензенской областной библиотеки им. Лермонтова и библиотеки ПГУ.
Широта и глубина поиска являются достаточными.
В результате поиска для последующего анализа были отобраны рефераты патентов и описания изобретений (см. таблицу 1).
Заключение по патентно – информационному поиску
Согласно рассмотренным выше патентным документам проведём анализ направлений развития захватов лапчатых. Для этого проанализируем каждый патент.
2026255 C1. Разработка направлена на автоматизацию разгрузки крюка.
2003101057. Разработка направлена на возможность автоматической выгрузки поддонов.
2055012 C1. Разработка направлена на автоматическую перегрузку штучных грузов в цехах.
2007110865 А. Разработка направлена на компьютерное управление разгрузкой.
94009465 А1. Разработка направлена на автоматизацию разгрузки.
94018482 А1. Разработка направлена на повышение производительности.
Вцелом дальнейшее развитие строповых автоматических захватов будет направлено на расширение разнообразия перегружаемых грузов.
Описание предлагаемой конструкции
За основу предлагаемой конструкции принимаем специальный захват для транспортирования стальных листов с помощью самозажимных прихватов
Рисунок 4. Захват для перегрузки листов.
Предлагаемая конструкция состоит главным образом из крюка зажимной планки фиксирующего элемента дополнительного устройства предназначенное для ослабления зажима после чего при поднятии ГУ происходит высвобождение груза.
Расчёт захвата и приспособления для высвобождения груза
Рассматриваемое приспособление представляет собой крюк. Поэтому при проектировании воспользуемся методикой расчёта крюка однорогого. Помимо самого крюкового элемента приведём доводы по выбору безопасного размера осевого пальца.
Цель расчёта состоит в нахождении безопасного размера опасного сечения крюка и нахождение диаметра осевого пальца.
Определяем размеры опасного сечения крюка с помощью формул сопротивления материалов. Напряжения на изгиб в крюке возрастают пропорционально радиусу крюка поэтому усилие в крюке в разных сечениях
Где α – угол на котором находится рассматриваемое сечение.
Будем считать вес груза (исходя из задания) 10000 Н.
Отсюда видно что наиболее опасным будет сечение при α=90 град. Это сечение по центру крюка тогда усилие Р будет в том числе срезающей силой. Так как сталь на срез работает значительно хуже то расчёт на изгибную прочность опустим.
Допустимое напряжение на срез для стали 45 составляет 80 МПа с запасом 2.
Тогда требуемая площадь сечения
Принимаем сечение размерностью 70 х 20 мм А=70 х 20 =1400 мм2
Форма сечения аналогична форме сечения стандартного крюка.
Рассчитаем достаточное усилие для удержания стального листа с учётом возможного соскальзывания. Сила трения действующая на лист со стороны зажима
Допустимой силой трения в зажимных приспособлениях при 4 – х точках крепления считается 1000 Н. Запас составляет
Условие удержания груза выполняется.
Диаметр осевого пальца для взаимодействия подвижного элемента принимаем 40 мм так как максимальная нагрузка на срез не превышает критической для площади сечения пальца.
В результате выполненных расчётов получаем сечение размерностью 70 х 20 мм А=70 х 20 =1400 мм2 диаметр пальца осевого 40 мм.
Конструктивно приспособление для захвата выполнено в виде заклинивающего устройства (см. лист графической работы). Устройство для высвобождения груза представлено как размыкающее после соприкосновения груза с поверхностью на которую он был перегружен.
В курсовом проекте был выполнен расчёт крана на неподвижной колонне со спецзахватом для перегрузки стальных листов. В пределах работы рассчитаны механизм подъёма крана механизм передвижения крана. Проектный расчёт захвата выполнен в несколько этапов. Предложена конструкция захвата рассчитано опасное сечение выбраны диаметры элементов захвата.
В результате выполненного курсового проекта оформлена пояснительная записка и представлены 4 листа графической работы: 1 лист содержит вид общий крана консольного настенного 2 лист показывает сборочный чертёж тележки 3 лист содержит чертёж сборочный механизма передвижения крана на 4 листе – сборочный чертёж специального захвата с приспособлением для высвобождением груза.
Список использованной литературы
Руденко Н.Ф. Курсовое проектирование грузоподъёмных машин Н.Ф. Руденко – М: Машиностроение 1971 463 с.
Курсовое проектирование грузоподъёмных машин под. ред. С.А. Казака – М: Высшая школа 1989 318 с.
Пантелеев В.Ф. Расчёты деталей машин В.Ф. Пантелеев – Пенза: Пензенский государственный университет 1998 164 с.
Справочник по кранам. Том I под. ред. М.М. Гохберга – М: Машиностроение 1988 536 с.
Справочник по кранам. Том II под. ред. М.М. Гохберга – Л: Машиностроение 1988 559 с.
Атлас грузо – подъёмных машин под. ред. М.П. Александрова – М: МГТУ им. Баумана 1979 204 с.
Подъёмно - транспортные машины. Атлас конструкций. под. ред. М.П. Александрова Д.Н. Решетова – М: Машиностроение 1973 г.
Александров М.П. Грузоподъёмные машины М.П. Александров – М: МГТУ им. Баумана 2000.
Специальные грузоподъёмные машины. Под ред. д.т.н. Вершинского А.В. – Красноярск 2008.
Андреев А.Ф. Применение грузозахватных устройств для строительно – монтажных работ А.Ф. Андреев – М.: Стройиздат 1985.
Вайнсон А.А. Специализированные крановые грузозахваты для штучных грузов А.А. Вайнсон А.Ф. Андреев – М.: Машиностроение 1972.
СП.dwg

ПензГУ1.3-08.190205.102ВО
ПензГУ1.3-08.190205.102СБ1
ПензГУ1.3-08.190205.102СБ2
ПензГУ1.3-08.190205.102СБ3
Механизм передвижения
Захват с дистанционной
расстроповкой строительных
ПензГУ1.3-08.190205.102СБ4
СП3.dwg

Захват с дистанционной
расстроповкой строительных
ПензГУ1.3-08.190205.102СБ3
ПензГУ1.3-08.190205.102СБ
ПензГУ1.3-08.190205.102
Стержень направляющий
Шнур расстроповочный
СБ3.dwg

циентом трения о захват не менее 0
Технические характеристики
Усилие зажима рабочее
Тип размыкающего канатика
любой с линейным контактом
Масса одного захвата
ПензГУ1.3-08.190205.102СБ3
Захват с дистанционной
расстроповкой строительных
*Размер для справок.
Обеспечить усилие зажима не менее 1 кН.
Осевые элементы термически обработать.
Схема перемещения листового материала
Технические требования
СП1.dwg

СБ1.dwg

При сборке муфты приводной поз.3 и муфты зубчатых М3П1
подлежат контролю: зазаор между торцами полумуфты и втулки 2
Торцевое биение втулки не более 0
При сборке муфты зубчатой поз.14 подлежат контролю: зазор
между торцами втулок 5
биение втулок относительно друг друга
радиальное не более 0
мм и торцевое не более 0
Размеры без допусков являются справочными
контролю не подлежат.
При эксплуатации обеспечить коэффициент трения колеса о рельс 0
Монтировать в условиях крытого цеха.
ПензГУ1.3-08.190205.102СБ1
Характеристика тележки
ТЛ.doc
Пензенский государственный университет
Кафедра: «Транспортно – технологические машины и оборудование»
Расчётно – пояснительная записка к курсовому проекту
по дисциплине: «специальные краны»
ПензГУ1.3 – 08.19.02.05.102ПЗ
Принял: д.т.н. профессор