Кран балка подвесная грузоподъемность 0,5 т.




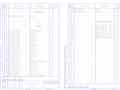
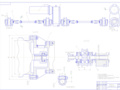
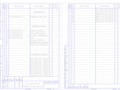
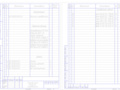
- Добавлен: 25.10.2022
- Размер: 2 MB
- Закачек: 1
Описание
Состав проекта
![]() |
![]() ![]() |
![]() |
![]() ![]() ![]() ![]() |
![]() ![]() ![]() ![]() |
![]() ![]() ![]() ![]() |
![]() ![]() ![]() ![]() |
![]() ![]() ![]() ![]() |
![]() ![]() ![]() ![]() |
![]() ![]() ![]() ![]() |
![]() ![]() ![]() ![]() |
![]() ![]() |
![]() ![]() |
![]() ![]() |
![]() ![]() |
![]() ![]() |
![]() ![]() |
![]() ![]() |
![]() ![]() ![]() |
Дополнительная информация
Спецификация 3.dwg

Спецификация 4.dwg

1 лист.dwg

3лист.dwg

2лист.dwg

4лист.dwg

Спецификация 2.dwg

Спецификация 1.dwg
