Модернизация электропогрузчика с шарнирно-сочлененным грузоподъемником




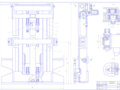
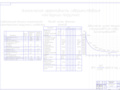
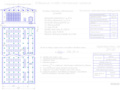
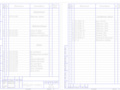
- Добавлен: 25.10.2022
- Размер: 6 MB
- Закачек: 0
Описание
Состав проекта
![]() |
![]() |
![]() ![]() ![]() ![]() |
![]() |
![]() ![]() ![]() |
![]() ![]() ![]() |
![]() ![]() ![]() |
![]() ![]() ![]() |
![]() ![]() ![]() |
![]() ![]() ![]() |
![]() ![]() ![]() |
![]() ![]() ![]() |
![]() ![]() ![]() |
![]() ![]() ![]() |
![]() ![]() ![]() ![]() |
![]() ![]() ![]() ![]() |
![]() ![]() ![]() ![]() |
![]() ![]() ![]() ![]() |
![]() ![]() ![]() ![]() |
![]() ![]() ![]() ![]() |
![]() ![]() ![]() ![]() |
![]() |
![]() ![]() ![]() ![]() |
![]() |
![]() ![]() ![]() |
![]() ![]() ![]() |
![]() ![]() ![]() |
![]() ![]() ![]() |
![]() ![]() ![]() |
![]() ![]() ![]() ![]() |
![]() ![]() ![]() ![]() |
![]() ![]() ![]() ![]() |
![]() ![]() ![]() ![]() |
![]() ![]() ![]() ![]() |
![]() ![]() ![]() ![]() |
![]() ![]() ![]() ![]() |
![]() |
![]() ![]() ![]() |
![]() ![]() ![]() |
![]() ![]() ![]() |
![]() ![]() |
![]() ![]() ![]() |
![]() ![]() ![]() |
![]() ![]() ![]() |
![]() ![]() ![]() |
![]() ![]() ![]() |
![]() ![]() ![]() |
![]() ![]() ![]() |
![]() ![]() ![]() |
![]() ![]() ![]() |
![]() ![]() ![]() |
Дополнительная информация
Освещение склада_v15.cdw

Расчетная освещенность Е
Количество светильников N=84 шт.
Тип светильников ВЗГ
Световой поток лампы Ф
Мощность лампы Рл=80 Вт.
Мощность светильной установки Ру=3
Основные параметры осветительной
световой поток каждой из ламп;
Е - нормируемая минимальная освещенность
k - коэффициент запаса;
S - освещаемая площадь
характеризующий неравномерность освещения;
N - число светильников
которое намечается еще до расчета;
- коэффициент использования светового потока в долях единицы;
- коэффициент затенения
может вводиться в помещениях с фиксированным
положением работающего и приниматься равным 0
Характеристики лампы
Огнетушащая способность притушении
модельного очага пожара
Продолжительность подачи огнетушащего
Разработка электропогрузчика для работы
в складе с поворотным грузоподъемником
Освещение склада стеллажного хранения
Схема расположения светильников в складе
Расчет по методу коэффициента использования светового потока:
Рабочее напряжение в лампе
Минимальная t зажигания
Средняя продолжительность горения
Технические характеристики огнетушителя ОВП-4
Масса огнетушащего вещества
Длина струи огнетушащего вещества
Диапозон рабочих температур
Колличество перезарядки в году
Масса огнетушителя полная
Технология.dwg
Торцевать справа "как чисто
Cверлить центровое отверстие справа по условию эскиза
-Размеры для справок
Общие допуски по ГОСТ 30893.1
Сталь 40Х ГОСТ 1050-88
Установ Б (торцевание заготовки)
Переустановить заготовку
Торцевать справа в размер 1
Установ Д (точение получистовое).
Точить получисто в размер 1 на длине
Точить фаску в размер
Установ В (черновое точение)
Точить начерно в размер 1 на длине 2
Центровое отверстие В6.3
Установ Г (точение черновое
Точить начерно в размер 3 на длине 12
Точить начерно в размер 6 на длине 9.
Точить начерно в размер 2 на длине 7.
Точить получисто в размер 5 на длине 9.
Точить получисто в размер 4 на длине 8.
Точить получисто в размер 1 на длине 10 и
обеспечивая допуск перпендикулярности упорного бортика.
Установ Ж (предварительное и чистое шлифование)
Шлифовать предварительно размер 1 на длине 6
Шлифовать предварительно размер 3 на длине 5
Шлифовать чисто в размер 2 на длине 6
Шлифовать чисто в размер 4 на длине 5
Точить канавку В под резьбу.
Точить канавку А под выход
шлифовального круга.
Установ Е (шлифование предварительное и чистое)
Шлифовать предварительно в размер 1 на длине 3.
Шлифовать на чисто в размер 2 на длине 3.
*- размеры для справок.
Общие допуски по ГОСТ 30893
Модернизация погрузчика с
шарнирно-сочленённым
Технология изготовления оси ведущего колеса
Операционные эскизы по изготовлению детали
экономика(внесение штабелера).dwg
Энергия аккумуляторной
Обслуживающий персоонал
Экономическая эффективность совершенствования
конструкции погрузчика.
Сравнительная технико-экономическая
характеристика погрузчика и штабелера.
Расчёт чистых денежных
Зависимость чистой текущей
стоимости(NPV) от ставки
дисконтирования(HR).
-зарядные устройства
Модернизация погрузчика с
шарнирно-сочленённым
Гидросхема.dwg
Клапан предохранительный с перелевным золотником
Цилиндр поворота грузоподъемника
Распределитель PVG 32
Модернизация погрузчика с
шарнирно-сочленённым
Освещение склада.dwg
Расчетная освещенность Е
Количество светильников N=84 шт.
Тип светильников ВЗГ
Световой поток лампы Ф
Мощность лампы Рл=80 Вт.
Мощность светильной установки Ру=3
Основные параметры осветительной
световой поток каждой из ламп;
Е - нормируемая минимальная освещенность
k - коэффициент запаса;
S - освещаемая площадь
характеризующий неравномерность освещения;
N - число светильников
которое намечается еще до расчета;
- коэффициент использования светового потока в долях единицы;
- коэффициент затенения
может вводиться в помещениях с фиксированным
положением работающего и приниматься равным 0
Характеристики лампы
Огнетушащая способность притушении
модельного очага пожара
Продолжительность подачи огнетушащего
Разработка электропогрузчика для работы
в складе с поворотным грузоподъемником
Освещение склада стеллажного хранения
Схема расположения светильников в складе
Расчет по методу коэффициента использования светового потока:
Рабочее напряжение в лампе
Минимальная t зажигания
Средняя продолжительность горения
Технические характеристики огнетушителя ОВП-4
Масса огнетушащего вещества
Длина струи огнетушащего вещества
Диапозон рабочих температур
Колличество перезарядки в году
Масса огнетушителя полная
механизм поворота.dwg
Перед сборкой все детали прмыть и высушить.
На трущихся и сопряжаемых поверхностях деталей
не допускается наличае рисок
механических повреждений.
Скручивание уплотнений при монтаже не допускается.
При испытании рейка поз.6 с поршнями поз.3 должны
перемещаться на всей длине хода в обе стороны плавно
без вибраций при давлении масла не более 0.5 мПа.
Испытать на герметичность давлением 25 мПа в
течение 30 с маслом М-12 ВуТУ38-001-248-76 при температуре
масла 35 С -15 С в двух крайних положениях рейки.
Утечки через уплотнения не допостимы.
Отверстия для подвода жидкости заглушить пробками.
После испытаний масло слить
гидроцилиндра свыше суток
все обработанные и не окрашенные
наружные поверхности покрыть тонким слоем смазкисм.табл.
Модернизация погрузчика с
шарнирно-сочленённым
общ вид.dwg
шарнирно-сочленённым
Расстояние от центра тяжести
Скорость передвижения
Технические характеристики электропогрузчика
Гидросхема.cdw

Клапан предохранительный с перелевным золотником
Цилиндр поворота грузоподъемника
Распределитель PVG 32
Модернизация погрузчика с
шарнирно-сочленённым
общ вид.cdw

шарнирно-сочленённым
Расстояние от центра тяжести
Скорость передвижения
Технические характеристики электропогрузчика
экономика(внесение штабелера).cdw

Энергия аккумуляторной
Обслуживающий персоонал
Экономическая эффективность совершенствования
конструкции погрузчика.
Сравнительная технико-экономическая
характеристика погрузчика и штабелера.
Расчёт чистых денежных
Зависимость чистой текущей
стоимости(NPV) от ставки
дисконтирования(HR).
-зарядные устройства
Модернизация погрузчика с
шарнирно-сочленённым
механизм поворота.cdw

Перед сборкой все детали прмыть и высушить.
На трущихся и сопряжаемых поверхностях деталей
не допускается наличае рисок
механических повреждений.
Скручивание уплотнений при монтаже не допускается.
При испытании рейка поз.6 с поршнями поз.3 должны
перемещаться на всей длине хода в обе стороны плавно
без вибраций при давлении масла не более 0.5 мПа.
Испытать на герметичность давлением 25 мПа в
течение 30 с маслом М-12 ВуТУ38-001-248-76 при температуре
масла 35 С -15 С в двух крайних положениях рейки.
Утечки через уплотнения не допостимы.
Отверстия для подвода жидкости заглушить пробками.
После испытаний масло слить
гидроцилиндра свыше суток
все обработанные и не окрашенные
наружные поверхности покрыть тонким слоем смазкисм.табл.
Модернизация погрузчика с
шарнирно-сочленённым
ведущее колесо.cdw

поворотный грузоподъемник.cdw

организация работ (дораб).cdw

Грузоподъемник.spw

2.Ведущее колесо.dwg
Промежуточная шестерня
Уплотнение войлочное
1.общ.вид.dwg
шарнирно-сочленённым
Поворотный грузоподъемник
Шарнирное соединение
Повоторный грузоподъемник.dwg
Гидроцилиндр наклона
Шарнирное соединение
Механизм поворота.spw

2.Ведущее колесо.spw

Промежуточная шестерня
Уплотнение войлочное
1.общ.вид.cdw

шарнирно-сочленённым
Поворотный грузоподъемник
Шарнирное соединение
Повоторный грузоподъемник.spw

Гидроцилиндр наклона
Шарнирное соединение
Освещение склада_v5.11.cdw

Расчетная освещенность Е
Количество светильников N=84 шт.
Тип светильников ВЗГ
Световой поток лампы Ф
Мощность лампы Рл=80 Вт.
Мощность светильной установки Ру=3
Основные параметры осветительной
световой поток каждой из ламп;
Е - нормируемая минимальная освещенность
k - коэффициент запаса;
S - освещаемая площадь
характеризующий неравномерность освещения;
N - число светильников
которое намечается еще до расчета;
- коэффициент использования светового потока в долях единицы;
- коэффициент затенения
может вводиться в помещениях с фиксированным
положением работающего и приниматься равным 0
Характеристики лампы
Огнетушащая способность притушении
модельного очага пожара
Продолжительность подачи огнетушащего
Разработка электропогрузчика для работы
в складе с поворотным грузоподъемником
Освещение склада стеллажного хранения
Схема расположения светильников в складе
Расчет по методу коэффициента использования светового потока:
Рабочее напряжение в лампе
Минимальная t зажигания
Средняя продолжительность горения
Технические характеристики огнетушителя ОВП-4
Масса огнетушащего вещества
Длина струи огнетушащего вещества
Диапозон рабочих температур
Колличество перезарядки в году
Масса огнетушителя полная
грузоподъемник_3храмный.cdw

Технология.cdw

Торцевать справа "как чисто
Cверлить центровое отверстие справа по условию эскиза
-Размеры для справок
Общие допуски по ГОСТ 30893.1
Сталь 40Х ГОСТ 1050-88
Установ Б (торцевание заготовки)
Переустановить заготовку
Торцевать справа в размер 1
Установ Д (точение получистовое).
Точить получисто в размер 1 на длине 3.
Точить фаску в размер 2.
Установ В (черновое точение)
Точить начерно в размер 1 на длине 2
Центровое отверстие В6.3
Установ Г (точение черновое и получистовое)
Точить начерно в размер 3 на длине 12
Точить начерно в размер 6 на длине 9.
Точить начерно в размер 2 на длине 7.
Точить получисто в размер 5 на длине 9.
Точить получисто в размер 4 на длине 8.
Точить получисто в размер 1 на длине 10 и
обеспечивая допуск перпендикулярности упорного бортика.
Установ Ж (предварительное и чистое шлифование)
Шлифовать предварительно размер 1 на длине 6
Шлифовать предварительно размер 3 на длине 5
Шлифовать чисто в размер 2 на длине 6
Шлифовать чисто в размер 4 на длине 5
Точить канавку В под резьбу.
Точить канавку А под выход
шлифовального круга.
Установ Е (шлифование предварительное и чистое)
Шлифовать предварительно в размер 1 на длине 3.
Шлифовать на чисто в размер 2 на длине 3.
*- размеры для справок.
Общие допуски по ГОСТ 30893
Модернизация погрузчика с
шарнирно-сочленённым
Технология изготовления оси ведущего колеса
Операционные эскизы по изготовлению детали
9. БЖД(стр 121-131).docx
1.1 Электропогрузчик (Рис.3.1) представляет собой самоходную четырехопорную машину.
Техническая характеристика.
расстояние от центра тяжести груза до спинки вил Lq
скорость передвижения
габаритные размеры: длина с вилами
шины массивные: передние
Корпус представляет собой несущую конструкцию состоящую из рамы капота отсека противовеса.
Электропогрузчик — передвижная машина на колесном ходу оборудованный грузоподъемным устройством все механизмы которого приводятся в действие от электродвигателя получающего энергию от аккумуляторной батареи. Он предназначен для выполнения погрузочно-разгрузочных работ в складских помещениях.
1.2 Для приемки погрузчика поступившего с завода-изготовителя организация получившая электропогрузчик выделяет инженерно-технического работника который проверяет техническое состояние и комплектность электропогрузчика в соответствии с упаковочной ведомостью; проводит внешний осмотр удостоверяется что запасные части инструменты и эксплуатационная документация прилагаются сверяет заводские номера агрегатов и деталей с номерами проставленными в паспорте; контролирует состояние аккумуляторной батареи. После этого составляют приемо-технический акт регистрируют электропогрузчик в приобретшей его организации и присваивают ему инвентарный номер. Так же оформляют машину при передаче ее другому владельцу.
Для управления электропогрузчиками назначают машинистов окончивших профессионально-технические учебные заведения курсы или школы на предприятиях и имеющих удостоверения о профессиональной подготовке. Во время работы машинисты и обслуживающий персонал машины должны иметь эти удостоверения при себе. Кроме того эти лица должны иметь допуск к работе оформленный приказом по предприятию.
Перед началом работы машинист получив наряд-задание осматривает машину и удостоверяется в исправности ее проводит ежедневное обслуживание. Во время работы машинист соблюдает правила безопасной работы: останавливает машину при обнаружении повреждения и устраняет неисправность; во время перерыва в работе (обед отдых) опускает груз на землю устанавливает машину в положение исключающее ее самопроизвольное движение выключает двигатель отключает энергопитание. По окончании работы машинист освобождает машину от груза и переводит ее в транспортное положение оформляет наряд-задание. На стоянку погрузчик ставят так чтобы к нему не было доступа посторонним лицам и он не мешал работе других машин и механизмов.
1.3 При эксплуатации электропогрузчика на водителя могут воздействоватьопасныеивредныефакторы:
- движущиеся машины и механизмы перевозимые грузы;
- повышенная загазованность и запыленность воздуха рабочей зоны;
- повышенная или пониженная температура поверхностей оборудования и материалов;
- повышенное давление в шинах колес;
- повышенная или пониженная влажность воздуха рабочей зоны;
-вредные вещества (кислоты щелочи и другие);
-опасность поражения электрическим током;
-повышенные уровни шума и вибрации на рабочем месте водителя;
- повышенная или пониженная температура воздуха рабочей зоны;
- недостаточная освещенность рабочего места.
Выполняя разнообразные технологические операции по погрузке-выгрузке транспортных средств транспортировке и штабелированию грузов операторам часто необходимо использовать предельные возможности погрузчиков по грузоподъемности высоте подъема груза и устойчивости что в сочетании с неблагоприятными и случайными факторами возникающими в процессе выполнения работ может приводить к авариям.
Опасные с точки зрения потери устойчивости погрузчиков ситуации возникают:
- при подъеме груза в сочетании с боковым смещением груза;
- при кантовании груза поворотным захватом центр тяжести которого смещен относительно продольной оси вращения захвата;
- при подъеме груза и отклонении вперед грузоподъемника;
- при использовании удлинителей вил захватов типа «пантограф» захватов с боковым смещением каретки и т.д.
Для рассматриваемого электропогрузчика главной опасностью является опрокидывание т.к штабелирование и позиционирование грузов совершается на высоте до 6.5 метров. Во избежание опрокидываний необходимо соблюдать правила техники безопасности при работе на электропогрузчике а главное не допускать перегруза.
1.4 Общие сведения и нормы освещённости
Устройство освещения складов должно обеспечивать нормы освещенности и показатели качества освещения бесперебойность действия освещения удобство обслуживания и управления. Различают два вида освещения: естественное и искусственное. Естественное освещение осуществляется через специальные проемы и фонари в наружных стенах искусственное создается с помощью осветительных приборов. Отсутствие или недостаток естественного освещения в складских помещениях связано со строительством многопролетных одноэтажных зданий большой ширины и безоконных и бесфонарных сооружений. Как правило в складских помещениях планируется смешанное освещение при котором недостаточное по нормам естественное освещение дополняется искусственным. В бесфонарных и безоконных зданиях используется только искусственное освещение.
Согласно СНиП 23.05-95 склады оборудуют рабочим аварийным и охранным освещением причем устройство дежурного освещения в складских помещениях не допускается. Электроосвещение складов выполняют в соответствии с требованиями ПУЭ – Правилами устройства электроустановок СНиП 23.05-95 «Естественное и искусственное освещение» ГОСТ 50571.8–94 «Электроустановки зданий. Требования по обеспечению безопасности» НПБ 249-97 «Светильники. Требования пожарной безопасности. Методы испытаний».
Рабочее освещение обеспечивает нормируемые осветительные условия (освещенность качество освещения) в помещениях и в местах производства работ вне зданий. В складских зданиях применяется как правило общее освещение; в этом случае светильники размещаются в верхней зоне помещения равномерно (общее равномерное освещение) или применительно к расположению хранимых товаров материалов оборудования (общее локализованное освещение). Последнее применяют при стеллажном хранении. Для питания светильников общего освещения согласно ПУЭ используется напряжение переменного тока не выше 220 В. При общем освещении светильники устанавливают непосредственно на поверхности потолка или подвешивают к нему на фермах стенах и колоннах.
Устройство рабочего электрического освещения обязательно для всех складских помещений независимо от устройства других видов освещения. Для помещений имеющих зоны с разными условиями естественного освещения и разными режимами работы необходимо чтобы и управление освещением таких зон было выполнено раздельным.
Аварийное освещение подразделяется на освещение безопасности и эвакуационное. Освещение безопасности предназначено для создания осветительных условий необходимых для продолжения работы персонала в помещениях и на местах производства открытых работ при отключении рабочего освещения. По рекомендациям РАМН разработанным на основании требований ПУЭ и СНиП 23.05-95 (Суворов Т.А. Освещение на производстве. Эколого-гигиеническая оценка и контроль. РАМН 1998) освещение безопасности должно создавать минимальную освещенность на рабочих местах не менее 5% нормируемой рабочей освещенности но не меньше 2 лк внутри помещений и не меньше 1 лк для территорий предприятий.
Эвакуационное освещение предназначено для создания необходимых осветительных условий для эвакуации людей из помещений или мест производства наружных работ при аварийном отключении рабочего освещения. Эвакуационное освещение согласно требованиям СНиП 23.05-95 переключаемое на источник не используемый при нормальном режиме для питания рабочего освещения является обязательным для помещений без естественного освещения и должно обеспечивать минимальную освещенность на полу основных проходов (или на земле) и на ступенях лестниц 05 лк – в помещениях и 02 лк – на открытых территориях.
Для рабочего освещения освещения безопасности и эвакуационного освещения не допускается применение общих групповых щитков а также установка аппаратов управления рабочим освещением освещением безопасности и эвакуационным освещением в общих шкафах.
Светильники аварийного освещения могут быть горящими включенными одновременно с основными светильниками нормального освещения и не горящими автоматически включающимися при отключении нормального освещения. Устанавливать их рекомендуется по возможности в удалении от оконных проемов. Для аварийного освещения в складах используются только лампы накаливания.
При наличии в одном помещении рабочих и вспомогательных зон следует предусматривать локальное общее освещение рабочих зон и менее интенсивное освещение вспомогательных зон относя их к соответствующему разряду освещенности.
Нормы освещенности для складов устанавливаются в соответствии со СНиП 23.05-95:
– для закрытых складов при напольном хранении (разряд зрительной работы VШб) минимальный уровень освещенности 75 лк с газоразрядными лампами 50 лк – с лампами накаливания (по СНиП 11-4-79 этот показатель был ниже – 50 и 30 лк соответственно);
– для стеллажного хранения (разряд зрительной работы VI-1) – 200 лк с газоразрядными лампами 100 лк – с лампами накаливания.
Минимальный уровень освещенности при производстве грубых работ (по рекомендациям РАМН в соответствии с требованиями СНиП 23.05-95) при общем освещении составляет 200 лк с газоразрядными лампами и 100 лк с лампами накаливания. Этот показатель может быть использован для нормирования уровня освещенности при проведении погрузочно-разгрузочных и транспортно-складских (ПРТС) работ на складах.
Для создания освещенности 100 лк в зоне проведения ПРТС работ при необходимости освещения высоко расположенных вертикальных поверхностей (при освещенности всей площади складирования 50 лк) необходимо раздельное управление освещением этих зон. Большое значение для достижения нужного уровня и качества освещения имеет выбор типа светильников (например прямого или рассеянного света одностороннего распределения света с увеличенным световым потоком и т. п.) а также их рациональное расположение и установка.
Выбор источников света. Осветительные приборы
Для освещения складских помещений как правило применяют лампы накаливания. В неотапливаемых складах сырых пожаро- и взрывоопасных помещениях а также для аварийного освещения следует использовать только лампы накаливания. В отапливаемых складских помещениях с нормальными условиями среды допускается применение люминесцентных ламп но при этом необходимо соблюдать следующие условия: температура окружающей среды помещения должна быть не ниже +5 °С напряжение питания осветительных приборов – не менее 90% номинального. Следует также учитывать конструктивные возможности здания для крепления светильников люминесцентного освещения высоту установки доступ для обслуживания и т. д. В основном люминесцентное освещение используют в лабораториях весовых административных помещениях диспетчерских с постоянным пребыванием людей.
Дуговые ртутные лампы (ДРЛ) могут использоваться для освещения территорий складов (особенно в прожекторах) но применение их для аварийного и охранного освещения не допускается.
Конструкция светильников должна обеспечивать надежную защиту всех их частей от вредных воздействий окружающей среды электро- пожаро- и взрывобезопасность надежность долговечность стабильность светотехнических характеристик. Светильники должны соответствовать требованиям ГОСТ 14254–96 «Изделия электротехнические. Оболочки. Степени защиты» ГОСТ 15597–82 «Светильники для производственных зданий. Общие технические условия» ПУЭ и НПБ 249-97. Допустимая степень защиты светильников в зависимости от класса пожаро- и взрывоопасной зоны по ГОСТ 14254–96 ГОСТ Р 51330.0–99 «Электрооборудование взрывозащищенное. Общие требования» приведена в табл. 1 и 2.
Для увеличения высоты складирования товаров светильники целесообразно размещать над свободными от штабелей и стеллажей участками площади.Не допускается устройство в штабелях ниш для электросветильников; осветительная сеть должна быть смонтирована так чтобы светильники не соприкасались со сгораемыми конструкциями зданий и горючими материалами.
Защита осветительных сетей. Электропроводка
Согласно ПУЭ осветительные сети защищаются от токов короткого замыкания во всех случаях. Номинальные токи аппаратов защиты должны быть не менее расчетных токов защищаемых участков и не должны отключать электроустановку при включении ламп. В качестве аппаратов защиты применяются плавкие предохранители автоматические выключатели с регулируемыми нерегулируемыми и мгновенно действующими расцепителями. Они монтируются в щитках и шкафах которые устанавливают в специальных помещениях. Способы выполнения осветительных сетей должны соответствовать требованиям надежности долговечности пожарной безопасности.
Сечение проводов и кабелей следует рассчитывать исходя из условий нагрева (длительно допустимой токовой нагрузки) допустимой потери напряжения и механической прочности. Сечение заземляющих и нулевых защитных проводников надо выбирать с соблюдением требований ПУЭ. Электропроводка должна быть выполнена открытой или скрытой и иметь исполнение и степень защиты с учетом требований ПУЭ. Изоляцию проводов независимо от вида электропроводки необходимо рассчитывать на напряжение не ниже 500 В (при напряжении сети 380 220 В). Места соединения и ответвления жил проводов и кабелей а также соответствующие зажимы должны иметь изоляцию равноценную изоляции жил целых мест этих проводов и кабелей. Соединения проводов и кабелей и их ответвления выполняют с помощью соединительных и ответвительных коробок изготовленных из несгораемого материала а металлические коробки должны иметь внутри надежную изолирующую прокладку.
1.5 Техника безопасности при обслуживании электропогрузчика.
Инструкция содержит основные требования по технике безопасности для слесарей ремонтных работ работающих по ремонту техники с применением механизированного электрического инструмента а также использующих станочное оборудование для сверлильных заточных и других работ применяющих различные приспособления и механизмы.
К выполнению слесарных работ допускаются лица прошедшие медицинское освидетельствование имеющие соответствующее квалификационное удостоверение или прошедшие специальное обучение по утвержденной программе с проверкой знаний в квалификационной комиссии и получившие права (допуск).
До проведения ремонтных работ вновь принятые слесари а также машинисты водители автомобилей и рабочие других профессий принимающие участие в ремонте закрепленных за ними машин и оборудования обязаны получить от непосредственного руководителя работ инструктаж на рабочем месте о способах безопасного выполнения слесарных работ.
Выполнять работы на сверлильных и других металлообрабатывающих и заточных станках с пневмо-и электроинструментом а также работы связанные со строповкой подъемом и перемещением грузов грузоподъемными механизмами управляемыми с пола разрешается только лицам не моложе 18 лет прошедшим дополнительное обучение и инструктаж по безопасным методам выполнения этих работ.[16]
2 Расчет освещения склада
Для создания благоприятны и безопасных условий труда для работы электропогрузчика огромное значение имеет достаточная
освещенность рабочей площади правильное направление света отсутствие резких теней и бликов. Недостаточное или нерациональное освещение не только затрудняет работу но и ведет к снижению производительности труда но может явиться причиной травматизма.
Ширина склада – 26 м
Высота склада – 10 м
Площадь склада – 1196 м2.
Для складов с общим освещением при высоте помещения 10м выбираем дуговые ртутные люминесцентные лампы ДРЛ. Этим лампам соответствует светильник ВЗГ.
Для зрительной работы необходима освещённость Енорм=30лк.
Определяем расстояние между светильниками:
где: =1.6 величина зависящая от кривой распределения светильника;
- расчётная высота подвеса светильников м.
где: Н- высота помещения 10 м;
hc- расстояние от светильников до перекрытия 05 м;
hn- высота рабочей поверхности над полом 0 м.
Исходя из размеров склада принимаем: L=95 м.
Определим расстояние от крайнего светильника до стены
hp=(015-045)h=(015-045)51=08-23 м; (9.4.3.)
Определим необходимое число светильников:
принимаем количество светильников по длине склада: 12 шт
принимаем количество светильников по ширине склада: 7 шт
Определим необходимое значение светового потока:
где: Ен - нормируемая освещённость: Ен=30 лк;
S- освещаемая площадь S=1196 м2;
кз – коэффициент запаса: кз =15;
z- коэффициент неравномерности освещения для ламп ДРЛ z=11;
N- число светильников N=84;
- зависит от типа светильника индекса помещения i коэффициента отражения (пола и стен) и других условий освещённости принимаем =065.
- расчетная высота подвески светильника над рабочей поверхностью м;
По рассчитанному световому потоку выбираем лампу ДРЛ-80.
Определим расчётную освещённость:
где: Фл- - световой поток лампы Фл-=3200 лм.
Определяем мощность осветительной установки:
где: Pл- -мощность лампы Рл=80В
Для обеспечения безопасности в складском помещении при работе погрузчика необходимо выполнять все вышеперечисленные требования безопасности и охраны труда персонала. При выполнении всех норм шансы происшествий и несчастных случаев резко сокращаются.
Безопасность жизнедеятельности: Учебник для вузов Занько Н.Г Малаян К.Р. Русак О. Н. - 12 издание пер. и доп. – СПб.: Лань 2008 . – 672 с.: ил.
Б.С. Мастрюков Опасные ситуации техногенного характера и защита от них. Учебник для вузов Б.С. Мастрюков.- М.: Академия 2009. – 320 с.: ил.
Б.С. Мастрюков Безопасность в чрезвычайных ситуациях. – Изд. 5-е перераб.- М.: Академия 2008.- 334 с.: ил.
Человеческий фактор в обеспечении безопасности и охраны труда: Учебное пособие П.П. Кукин Н.Л. Пономарев В.М. Попов Н.И. Сердюк.— М.: Высшая школа 2008.— 317 с.: ил.
В.А. Акимов. Безопасность жизнедеятельности. Безопасность в чрезвычайных ситуациях природного и техногенного характера: Учебное пособие В.А. Акимов Ю.Л. Воробьев М.И. Фалеев и др. Издание 2-е переработанное — М.: Высшая школа 2007. — 592 с: ил.
1. обзор существующих конструкций(стр 6-13).doc
Машины напольного безрельсового транспорта (МНБТ) получили широкое распространение в промышленности на железнодорожном транспорте и в иных отраслях для работы в крупнотоннажных контейнерах крытых вагонах автомобилях складах судах благодаря отличной маневренности высоким эксплуатационным показателям. Они требуют относительно небольших капиталовложений при малых сроках окупаемости.
МНБТ относятся к погрузочно-разгрузочным машинам циклического действия и производят следующие операции: захват груза его подъем и опускание транспортирование освобождение груза с захвата. Некоторые операции могут совмещаться полностью или частично. Возможность совмещения операций — важный фактор повышения производительности перегрузочных работ зависящий от квалификации водителя и маневренности машины.
Захват тарно-штучных сыпучих грузов производится погрузчиками без применения питателей или других дополнительных загрузочных приспособлений необходимых для функционирования машин непрерывного транспорта (конвейеров) и как правило без ручного труда рабочих-стропальщиковтакелажников.
В отличие от рельсовых пневмоколесных гусеничных кранов погрузчики способны перемещаться с грузом на значительные расстояния и обслуживать большие складские и производственные площади. Возможность использования разнообразной номенклатуры быстро заменяемых грузозахватных приспособлений в сочетании с высокой мобильностью автономностью привода (в большинстве случаев) и отсутствием привязки к ограниченному месту МНБТ получает свойство универсальности.
В основании классификации МНБТ положены конструктивные исполнения машин и сферы применения при выполнении перегрузочных работ.
Универсальные автопогрузчики с приводом от моторов внутреннего сгорания используют для работы на открытых площадках либо в хорошо вентилируемых помещениях с расстоянием транспортировки грузов до 200 м.
Универсальные электропогрузчики с приводом от аккумуляторных батарей используют преимущественно для перегрузочных работ в крытых помещениях с расстоянием транспортировки до 100-120 м.
Погрузчики с фронтальным выдвижным грузоподъемником (электро-штабелеры) применяют для складских работ они более маневренны но уступают по скоростным характеристикам и проходимости универсальным погрузчикам рабочее плечо до 50 м высота подъема груза 6-8 м а в специальных исполнений 15-20.
Погрузчики с боковым выдвижным грузоподъемником перегружают многотонные контейнеры крупногабаритные грузы (пиломатериалы прокат железобетонные изделия и др.). Бывают с приводом от аккумуляторных батарей малой грузоподъемности и от двигателей внутреннего сгорания крупной грузоподъемности до 40-60 т. Длина транспортировки зависит от вида привода и грузоподъемности и может доходить до 1000 м и больше.
Электротележки бывают с подъемной платформой или вилами с опрокидывающимся кузовом или ковшом со статичной платформой используются для перемещения грузов на расстояние 100 м и больше.
Тягачи характеризуются величиной тягового усилия от 0250 до 5000 кН и выше используются для транспортировки грузов на тележках или сцепках на расстояния 100-1000 м. Производятся электро- и автотягачи последние имеют более высокие тяговые и скоростные качества.
Портальные погрузчики (контейнеровозы) используют для перегрузки и транспортировки крупнотоннажных контейнеров и других длинномерных грузов. Расстояние транспортировки до 500-1000 м высоты штабелирования 45-7 м в зависимости от двух- или трехъярусной установки контейнеров.
Специальные погрузчики используют для транспортировки рулонов металла расплавленного металла или шлака в ковшах т.е. выполнения технологических операций на производстве. Для них характерно применение специальных приспособлений в виде одно или двухстержневого раздвижного хобота большая грузоподъемность до 100-150 т. Разновидностью специальных машин являются тележки для транспортировки расплавленных металлов подъема и установки штампов.
Кроме основных типов электропогрузчиков электроштабелеров электротележек и электротягачей где управление выполняется водителем с пульта сидя имеется большое количество конструкций мало
габаритных машин для работы в узких проездах и стесненных условиях с дышловым управлением рядом идущим оператором. В последние годы получают распространение электроштабелеры для комплектования грузов у которых пульт управления вместе с оператором и захватным устройством перемещаются в вертикальном направлении по грузоподъемнику. Такие погрузчики используют для обслуживания складов со стеллажным хранением груза в ячейках. Известны исполнения машин с перемещением грузозахватного устройства в трех взаимно перпендикулярных направлениях что улучшает степень обслуживания стеллажных складов.
Машины в зависимости от типа силовой установки делятся на авто - и электропогрузчи. Тип силовой установки в большой степени определяет технические характеристики машин и области их применения. Из-за ограниченной энергоемкости аккумуляторных батарей электропогрузчики имеют невысокие скорости подъема и передвижения и предназначаются основном для работы на площадках с ровным асфальтовым или бетонным покрытием. Импульсные схемы управления тяговыми двигателями улучшают ходовые качества электропогрузчиков увеличивают величину и длину преодолеваемых уклонов и способствуют сохранению энергоемкости аккумуляторной батареи.
Автопогрузчики в сравнении с идентичными по грузоподъемности электропогрузчиками имеют повышенные скорости подъема в 2-25 и передвижения в 2-5 раз. Они предназначены для работы в более тяжелых дорожных условиях и имеют меньше ограничений в отношении проходимости. Использование в механизмах передвижения гидромуфт гидротрансформаторов гидродвигателей и дизель-электрического привода существенно улучшает тяговые характеристики машин и условия работы водителя. Сфера применения автопогрузчиков ограничивается вредными действиями выхлопных газов что практически не позволяет использовать их в закрытых плохо вентилируемых помещениях. Чтобы уменьшить этот недостаток ведутся большие исследовательские и конструкторские работы по использованию нейтрализаторов выхлопных газов способствующих уменьшению содержания вредных примесей в продуктах выхлопа и установках двигателей работающих на сжиженном газе. Для работы на автопогрузчиках требуется более высокая квалификация водителя и обслуживающего персонала так как они сложны в управлении и чаще требуют ремонта двигателя чем электропогрузчики.
Для механизации работ на складах применяют электропогрузчики с кабельным питанием от электрической сети они не ограничены энергоемкостью но радиус транспортировки груза определяется длиной питающего кабеля (обычно в пределах 25—50 м). Кабель ухудшает маневренные качества электропогрузчиков и это сужает сферы их применения при перегрузочных работах. Особенно эффективны машины напольного безрельсового транспорта при массовых пакетных и контейнерных перевозках их также легко приспособить для перегрузки различных штучных и насыпных грузов оснастив сменными грузозахватными приспособлениями.
Электропогрузчики — передвижные машины на колесном ходу оборудованные грузоподъемным устройством все механизмы которого приводятся в действие от электродвигателя получающего энергию от аккумуляторной батареи. Они предназначены для выполнения погрузочно-разгрузочных работ в железнодорожных вагонах контейнерах автофургонах морских и речных судах применяются для штабелирования тарно-штучных грузов в крытых складах а также для внутрицеховой транспортировки и обслуживания станочных и сборочных линий комплектовочных складов и др.
Электропогрузчики могут работать в помещениях или на открытых площадках при температуре от —40 до + 40°С и высоте над уровнем моря не более 1200 м. Они не предназначены для работы в пожароопасных содержащих активные химические газы пары и пыль средах. Для таких условий выпускают погрузчики специального исполнения. Электропогрузчики изготовляются в климатическом исполнении У и Т категории II по ГОСТ 15150—69. Электропогрузчики могут работать только на твердом гладком основании с уклонами не более 1:10.
Основанием пола в складах обычно служит утрамбованный грунт усиленный щебнем или шлаком. На основание укладывается подстилающий слой толщиной 150—200 мм из щебня гравия или бетона на цементном растворе с заполнителями небольшой крупности. Покрытие пола рекомендуется асфальтовое или асфальтобетонное состоящее из смеси асфальтовой мастики со щебнем крупностью фракций до 10—12 мм. Полы с асфальтовым покрытием допускают нагрузку до 25 — 30 кНм2 с асфальтобетонным до 30—35 кНм2.
Для въезда погрузчиков в склад с прилегающих к нему площадок или автопроезда (и в обратном направлении) применяются наклонные дорожки (пандусы) обеспечивающие уклон не более 1:10. Для въезда погрузчиков в крытые вагоны и выезда из них в склад (или на рампу) применяются простейшие переносные мостики в виде стального рифленого листа прямоугольной формы толщиной 7—8 мм. При высоте пола склада над уровнем головки рельса 1200 мм длина мостика в направлении склад—вагон достаточна 800 мм. Ширина листа должна быть около 1200 мм. Снизу к листу приваривают два зацепа для закрепления мостика за дверную рейку нагона. При высоте пола склада 1100 мм над уровнем головки рельса устанавливают мостики длиной около 2000 мм для обеспечения их наклона не круче 1:10. Для въезда в кузов автомобиля и выезда из него электропогрузчиков применяют встроенные выравнивающие мостики длиной 2—3 м в связи с тем что высота пола кузовов автомобилей и прицепов различных моделей над дорогой составляет от 1150 до 1400 мм. Высота пола крупнотоннажных контейнеров находящихся на автополуприцепах над тем же уровнем может достигать 1600—1700 мм.[18]
Все крупнотоннажные контейнеры допускают заезд и работу внутри них вилочных погрузчиков. Среднетоннажные универсальные контейнеры также допускают применение внутри них электропогрузчиков.
У электропогрузчиков общего назначения грузоподъемный механизм расположен впереди машины вне опорного контура и предназначен для перемещения груза в вертикальной плоскости. Для удобства захвата транспортировки и укладки груза рама грузоподъемника при помощи механизма наклона отклоняется вперед на 3° и назад на 10°. По конструкции рамы грузоподъемники делятся на простые (однорамные) телескопические (двухрамные) и двойные телескопические (трехрамные).
Для работы в низких помещениях используют погрузчики у которых конструкция грузоподъемника позволяет поднимать груз без увеличения габарита по высоте (грузоподъемник со свободной высотой подъема). Обычно машины им оснащают по специальному заказу. Отличительная особенность такой конструкции — телескопический гидроцилиндр: сначала вилы поднимает подвижный цилиндр с двукратным полиспастом а потом каретку и внутреннюю раму поднимает плунжер гидроцилиндра. Рабочее давление в гидросистеме 18 МПа (есть варианты с давлением до 23 МПа). Привод гидросистемы обеспечивает работу гидроцилиндров механизмов подъема наклона и поворота грузоподъемника или каретки а также гидроусилителя руля.
Номинальные скорости электропогрузчиков обеспечиваются при температуре масла в гидросистеме и смазки в картерах ведущих колес в пределах от 10 до 35°С и температуре электролита в аккумуляторах от 15 до 35°С.
Конструкция грузоподъемника дает возможность устанавливать на нем различные сменные грузозахватные устройства что значительно расширяет область применения электропогрузчиков делает их универсальными. Однако следует учитывать что грузоподъемность и устойчивость универсальных электропогрузчиков снижается с удалением центра тяжести массы груза от оси передних колес. Для обеспечения продольной устойчивости сзади погрузчика устанавливается противовес.
Маневренные качества электропогрузчиков определяющие область их применения зависят от многих факторов. Наиболее важные из них — размеры машины и минимальный радиус поворота. На маневренные качества влияет и принципиальная схема компоновки узлов погрузчика особенно конструкция ходовой части. При большом многообразии ее конструктивных решений можно выделить следующие схемы:
трехопорные — ходовая часть опирается на грунт в трех точках. Заднее колесо может быть и ведущим и управляемым однако чаще ведущими служат передние колеса с индивидуальным приводом;
четырехопорные — ходовая часть опирается на грунт (дорогу) в четырех точках. Передние колеса ведущие а задние управляемые. Вариантов исполнения четырехопорной схемы два: с подрессориванием заднего моста или жестким креплением его к раме для обеспечения сцепления обоих ведущих колес с дорогой и с горизонтальным шарнирным соединением заднего моста с рамой.
Каждая из этих схем обладает своими достоинствами и недостатками. Трехопорные схемы обеспечивают достаточное сцепление ведущих колес с покрытием пути и позволяют получить более высокую маневренность но несколько снижают поперечную устойчивость машины по сравнению с четырехопорными.
Трехопорные электропогрузчики сочетают высокую маневренность и малую собственную массу. Это позволяет применять их при загрузке крытых железнодорожных вагонов контейнеров автомашин и для работы в стесненных условиях складов и цехов промышленных предприятий.
Все электропогрузчики повышенной маневренности выпускаемые в настоящее время унифицированы по узлам и по конструктивному исполнению. Модели отличаются габаритными размерами некоторыми узлами электрооборудования гидропривода и конструкцией грузоподъемника. Электропогрузчики ЭП-0805 ЭП-1205 отличаются от электропогрузчиков ЭП-0803 и ЭП-1203 только конструкцией каретки грузоподъемника и имеют дополнительно натяжное устройство и третью секцию гидрораспределителя.[17]
Четырехопорные электропогрузчики выпускаются грузоподъемностью 10; 15; 20 и 50 т соответственно моделей ЭП-103 (106); 02(04) ЭП-202(201) и ЭП-501.
7.технологиия(стр 88-107).docx
1. Анализ технологических требований к конструкции детали.
В конструкторской части был выполнен расчет основных параметров электропогрузчика с шарнирно-сочлененным грузоподъемником выполнен прочностной расчет оси ведущего колеса в программе APM Shaft. Заданием на дипломное проектирование в технологической части предложена разработка технологического процесса изготовления уникальной оси ведущего колеса т.к. изменяется вес конструкции грузоподъемника. Задание выполнено в следующей последовательности: выбор вида заготовки определение размеров заготовки составление маршрута изготовления детали разработка токарной и шлифовальной операций с составлением эскизов.
Ось редуктора приводного колеса 5-ти ступенчатая длиной 170 мм. Ось запрессовывается в редуктор и заваривается на ось надевают приводное колесо. Компоновочная схема оси изображена на рисунке 7.1.
Рисунок 7.1. Компоновочная схема оси приводного колеса
ступень оси под резьбу; 2. ступень оси под подшипник; 3. нерабочая ступень; 4. ступень под подшипник; 5. ступень под запрессовку в редуктор;
I. круглая шлицевая гайка; II. прокладка; III. роликовый подшипник;
IV. корпус редуктора.
Первая ступень длинной 18 мм и диаметром 36 мм имеет резьбу М36 с шагом витка 15 мм для навинчивания круглой шлицевой гайки для удержания подшипника. Согласно [6 c. 123] выбираем поле допуска 6g (предельные отклонения наружного диаметра резьбы для 6g составляют [6 c. 124] что соответствует квалитету вала 12. Также на данной ступени имеется канавка под резьбу фаска 16х45º.
Ось имеет две опоры в виде конических роликовых подшипников которые располагаются на 2 и 4 ступенях. Длины 2 и 4 ступени равны 22 мм а их диаметры 40 мм. Эти поверхности обрабатываются с допуском k6 и шероховатостью Ra=08 мкм. Имеются фаски для запрессовки подшипника 2х45º.
Третья ступень длиной 52 мм и диаметром 36 мм не рабочая. Специально не обрабатывается.
Пятая ступень длиной 56 мм и диаметром 48 мм служит для упора подшипника и для запрессовки в редуктор. Эта поверхность обрабатывается с допуском n6 и шероховатостью Ra=08. Имеет фаску 2х45º.
Материал заготовки сталь 40Х ГОСТ 1050-88. Твердость HB 260 285 термообработка - улучшение.
В качестве конструкционной базы выбираем поверхности 2 и 4 так как эти поверхности детали соприкасается с подшипником и определяет своё положение в сборочной единице.
Необходимо при изготовлении детали выдерживать допуски формы и расположения.
Допуск соосности расположения для поверхностей 2 и 4 составит:
Т=01 .В1 .ТТабл(7.1)
где В1- ширина поверхности под подшипник (В=22мм)
ТТабл = 3 [1 табл. 22.5]
Т=01 .22 .3=66мкм=00066 мм. Принимаем Т=001 мм.
Допуск цилиндричности: То = 05 · Т
Для поверхностей 2 и 4 . Т= 0016
То24 = 05 ·Т=05·0016=0008(7.2)
Допуск перпендикулярности упорного буртика под подшипник Т=0016 мм для диаметра d=40 мм.
2 Выбор вида окончательной финишной обработки
конструктивных элементов.
Дано: деталь ступенчатая ось = 164 мм max
- посадочные места под подшипники качения из требований к шероховатости и получения точности размера по квалитету 6 применяется шлифование чистовое;
Торцы вала подрезаются «начисто» а обработка нерабочих поверхностей вала – обтачивание черновое.
Таким образом назначаем:
Под резьбу M36x15-6g Rz 20 финишная обработка - получистовое точение.
Ra 08 финишная обработка - чистовое круглое
Rz 80 финишной обработки - черновое точение
Ra 08 финишная обработка – чистовое круглое
Выточить канавки под шлифовальный круг и резьбу с помощью канавочного резца резьбу нарезать резьбовым резцом.
3 Выбор способов установки на операциях по формированию контура.
Определяем средний диаметр заготовки по формуле [5]:
гдеn – число конструктивных элементов;
Определяем технологическую жёсткость по формуле [5]:
т.к. Кж>2 то деталь целесообразно обрабатывать в центрах.
1.1.Выбор вида и типоразмера центровых отверстий
Для обработки детали в центрах необходимо выбрать вид и типоразмер центровых отверстий. Выбранное центровое отверстие (рис. 2) является базой для многократного использования.
Рис. 2. Центровое отверстие
Тип В 63 ГОСТ 14034-74 в соответствии с [2 табл. 23 с. 171].
4 Выбор вида и размеров заготовки для детали.
В качестве заготовки для условия единичного производства наиболее рациональным является сортовой прокат круглого сечения обычной степени точности. Для максимального диаметра равного 48 мм диаметр заготовки составляет 52мм. Из сортамента выпускаемого круглого проката выбираем в качестве заготовки сталь горячекатаную круглую (ГОСТ 2590-71) обычной точности прокатки (В) .
z – припуск на торцевую обработку детали.
Согласно [5 стр. 586 табл.6] принимаем z = 2 мм.
5 Составление укрупнённого маршрута изготовления детали.
Отрезать от прутка приводной ножовкой штучную заготовку
Заготовку (сталь 40Х) подвергнуть термообработке – улучшению до HB 260 285.
Для формирования профиля вала применяем токарный станок 16К20.
Последовательно торцевать и сверлить центровые отверстия. За несколько установов выполнить токарную обработку заготовки точить фаски канавки на участках 1 и 4. Центровка производится свёрлами центровочными комбинированными диаметром 4 мм из быстрорежущей стали Р18.
При токарной обработке применяем проходные и отрезные резцы.
За несколько установов выполнить обработку шеек оси диаметром 40мм и 48мм с шероховатостью указанной на чертеже.
Произвести контроль размеров по чертежу.
6Разработка операций по формированию контура детали.
6.1 Расчёт числа переходов механической обработки числа стадий для
достижения точности конструктивного элемента.
Число переходов механической обработки [5]:
где коэффициент ужесточения точности [5]:
Выполним расчет числа стадий обработки по каждому конструкторскому элементу. Результаты сведены в таблице 7.1.
Расчет числа стадий обработки
Коэффициент ужесточения точности
Расчётное значение количества переходов
Принятое значение количества переходов
7 Определение квалитетов промежуточных размеров.
Квалететы промежуточных размеров в порядке выполнения механической обработки резаньем определяют с шагом вычисляем по убывающей арифметической прогрессии.
Расчет квалитетов промежуточных размеров заготовки выполняется в табличной форме (табл.7.2-7.5)
Назначение квалитетов по стадиям обработки для поверхности 36h7
Получистовое точение
Назначение квалитетов по стадиям обработки для поверхности 40k6
Шлифование предварительное
Назначение квалитетов по стадиям обработки для поверхности 36h14
Назначение квалитетов по стадиям обработки для поверхности 48n6
8 Расчёт промежуточных размеров заготовки.
Промежуточные размеры находим по формуле:
Zi – припуск на токарную обработку.
В качестве исходного размера принимают максимальный размер детали по данной поверхности.
Припуск 2Zi -выбираем из таблицы [5]
Расчёт промежуточных размеров по стадиям обработки
Расчёт промежуточных размеров
Характеристика размера
Точение получистовое
Проверка: Минимальный фактический диаметр заготовки составляет dзmin=52 - 1=51 мм.
Минимальный расчётный диаметр составляет dзрасч=5024 - 1=4924 мм.
dзmin=51 > dзрасч=4924 следовательно заготовка подходит.
9. Составление плана токарной обработки.
Расчёт выполним исходя из характеристик станка 16К20:
Мощность на шпинделе: 75 кВт;
Максимальный диаметр заготовки: 400 мм;
Максимальный диаметр закрепляемой детали в трёхкулачковом патроне: 190 мм;
Диаметр центрового отверстия в шпинделе станка для пропуска проката: 58 мм
Максимальная длина заготовки: 1400мм.
Частота вращения шпинделя: 125; 16; 20; 25; 315; 40; 56; 63; 80; 100; 125; 160; 200; 250; 315; 400; 500; 630; 860; 1000; 1250; 1600 мин-1.
Продольная подача суппорта резца Sпродол: 005; 006; 0075; 009; 01; 0125; 015; 0175; 02; 025; 03; 035; 04; 05; 06; 07; 08; 1; 12; 14; 16; 22; 28 ммоб.
Поперечная подача: Sпопер. = 05 Sпродол.
Глубину резания для технологического перехода рассчитываем по формуле:
и сравниваем полученное значение с предельно допустимым для данного диаметра:
-если то переход возможен
-если то переход невозможен.
Согласно [4] значение .
Выполним также анализ допустимой глубины резания исходя из ограничения по мощности резания.
В нормах [4 стр.266 табл. 11] приведены ориентировочные значения мощности резания в соответствии с глубиной резания и подачей .
Так как KЖ=4 8 то принимаем [t]d=001·d
Установ А. Установить заготовку в универсальный самоцентрующийся трехкулачковый патрон и закрепить. Торцевать заготовку сверлить центровое отверстие.
Установ Б. Переустановить заготовку торцевать в размер 1. сверлить центровое отверстие.
Следовательно переход возможен.
Согласно [4 с. 266 табл. 11] выбираем подачу 03 ммоб согласно [7 с. 27 табл. 12] мощность 63 кВт.
Таким образом 1 технологический переход выполним до мм.
Установ Г (черновое точение)
Следовательно переход невозможен.
Следовательно переход возможет только при выполнении его в два прохода с глубиной резания t1=t2=295 мм.
Следовательно переход возможен. Согласно [4 с. 266 табл. 11] выбираем подачу 03 ммоб согласно [7 с. 27 табл. 12] мощность 63 кВт.
Таким образом 2 технологический переход выполним до мм.
Таким образом 3 технологический переход выполним до мм.
Установ Г (получистовое точение)
Точить получисто в размер 5 на длине 9.
Точить получисто в размер 4 на длине 8.
Точить получисто в размер 1 на длине 10.
Установить закрепить снять заготовку.
Точить получисто в размер 1 на длине 3.
Шлифовать предварительно в размер 1 на длине 3.
Шлифовать на чисто в размер 2 на длине 3.
Шлифовать предварительно размер 1 на длине 6.
Шлифовать предварительно размер 3 на длине 5.
Шлифовать чисто в размер 2 на длине 6.
Шлифовать чисто в размер 4 на длине 5.
10 Определение режимов резания.
Операция токарная 015
Определим скорость резания
где Cv - коэффициент скорости зависящий от значения величины подачи.
Согласно [4 табл.17 стр.269] для материала режущей части резца Т15К6 и подачи 03s07 принимаем Cv=350;
x y m - показатели степени.
Согласно [4 табл.17 стр.269] для материала режущей части резца Т15К6 и подачи 03s07 принимаем y=035; m=020;
Т – расчётная стойкость резца. Принимаем согласно [4 стр.268]
t – глубина резания;
-для чернового обтачивания принимаем значение глубины резания из пункта 8.7.
-для получистового обтачивания: .
-для чернового обтачивания принимаем значение подачи из пункта 8.7.
-для получистового обтачивания:
где Ks - коэффициент корректировки подачи. Согласно [4 стр.271] принимаем Ks = 08;
- табличное значение подачи. Согласно [4 табл.14 стр.268] принимаем .
ммоб. Принимаем s = 07 ммоб.
Kv – поправочный коэффициент
где - коэффициент учитывающий материал заготовки.
Согласно [4 табл.1 стр.261]
где КГ - коэффициент характеризующий группу стали по обрабатываемости.
Согласно [4 табл.2 стр.262] при =650мПа>550мПа принимаем Кг=10;
- временное сопротивление.
Согласно [4 табл.2 стр.262] принимаем =650мПа;
nv – показатель степени.
Согласно [4 табл.2 стр.262] при обработке резцами из твёрдого сплава принимаем nv=1.
– коэффициент учитывающий влияние состояния поверхности заготовки на скорость резания.
Согласно [4 табл.5 стр.263] при состоянии поверхности заготовки:
-прокат с коркой принимаем КПv=09;
-без корки принимаем КПv=1;
– коэффициент учитывающий качество материала инструмента.
Согласно [4 табл.6 стр.263] для марки инструментального материала Т15К6 принимаем КИv=1;
- коэффициент учитывающий главный угол в плане.
Согласно [4 табл.18 стр.271] при главном угле резца в плане φ=45 принимаем Кφv=1.
Определим частоту вращения:
Полученное значение принимаем согласно частоте вращения шпинделя.
Произведем расчет согласно описанной выше методике. Результаты расчета сведены в таблицу 7.7
Режимы токарной обработки
Диаметр поверхности мм
- Установ В (черновое обтачивание)
- Установ Г (черновое обтачивание)
- Установ Г (получистовое обтачивание)
- Установ Д (получистовое обтачивание)
11 Расчет режимов шлифования
Расчёт режимов шлифования выполним исходя из характеристик шлифовального станка 3А110В:
Наибольший диаметр и длина шлифуемой поверхности – мм;
Диаметр и толщина шлифовального круга – 600мм и 63мм;
Частота вращения детали – 63 400 (регулирование бесступенчатое);
Скорость продольного перемещения рабочего стола - 01 6 ммин (регулирование бесступенчатое);
Поперечная подача шлифовального круга – 00025 005 мм за 1 ход рабочего стола с шагом 00025 мм;
Дискретные значения подач шлифовального круга
Непрерывная подача шлифовального круга при врезном шлифовании – 01 2 мммин (00005 001 ммоб.);
Мощность электродвигателя привода шлифовального круга – 7кВт.
Согласно [4 табл.55 стр.301] назначаем следующий режим шлифования:
Скорость вращения шлифовального круга Vшл.кр. = 30мс;
Скорость вращения заготовки:
- для предварительного шлифования Vзаг = 12ммин;
- для окончательного шлифования Vзаг = 15ммин
Подача шлифовального круга:
- для предварительного шлифования s = (03 07) Вшл.кр. = (03 07)·63=189 441 ммоб.
Принимаем s = 20 ммоб;
- для окончательного шлифования s = (02 04) Вшл.кр. = (02 04)·63=126 255 ммоб.
Принимаем s = 14 ммоб;
Глубина шлифования:
- для предварительного шлифования мм;
- для окончательного шлифования мм.
Так как за один проход согласно [4 табл.55 стр.301] снимается:
- для предварительного шлифования мм то необходимое число рабочих ходов шлифовального круга:
- для окончательного шлифования мм то необходимое число рабочих ходов шлифовального круга:
Частота вращения заготовки
Частота вращения шлифовального круга
Проверка шлифовального станка по мощности:
где СN r x y q – поправочный коэффициент и показатели степени.
Принимаем согласно [6]:
СN= 265; r = 05; y = 055; q = 0 при поперечной подаче на двойной ход с использованием шлифовального круга с зернистостью 40 и твердостью СМ1 – С1.
Если условие N[N]= 7 кВт соблюдено то проверка выполняется.
Произведем расчет режимов шлифования а результаты сведем в таблицу 7.9.
- предварительное шлифование
- окончательное шлифование
12 Расчет режимов нарезания резьбы
Согласно [4с . 294] принимаем число черновых рабочих ходов 3 чистовых – 2.
Согласно [4 табл. 49] принимаем: Т=80 мин; Cv =233; y=05; m=05.
Согласно [4 табл. 49] sz=08 ммоб.
s – продольная подача (равна шагу резьбы 15 мм)
где Kcv – коэффициент учитывающий способ нарезания резьбы. Согласно [4 с. 297] принимаем Кcv=07
Для черновых проходов:
nрез.ч=1000·166314·36=1473 обмин
принимаем n=125 обмин.
В процессе выполнения задания разработан технический процесс изготовления оси приводного колеса. Процесс состоит из разных способов обработки заготовки: точения шлифования нарезание резьбы. Режимы токарной обработки спроектированы с учетом использования станка 16К20 а режимы шлифования определены для станка 3Б151.
2. анализ(стр 14-17).doc
1 Конструктивное исполнение ведущего моста
Электропогрузчики могут быть с жестким передним мостом с выдвижным передним мостом и поворотно-выдвижным мостом.
У серийно выпускаемых погрузчиков обычно передний мост крепится к корпусу неподвижно. В ряде погрузчиков имеет место устройство подвижного переднего моста относительно корпуса погрузчика. При выдвижении переднего моста грузоподъемник погрузчика наклоняется назад увеличивается колесная база и следовательно продольная устойчивость машины увеличивается нагрузка на заднее ведущее колесо улучшается сцепление колеса с опорной поверхностью. При уменьшении колесной базы погрузчика повышается его маневренность. Все это имеет важное значение для погрузчиков повышенной маневренности. Погрузчики с поворотно-выдвижным передним мостом имеют ограниченное маневрирование при захвате грузов и штабелировании.
Таким образом конструкция погрузчика с поворотным мостом имеет ряд преимуществ перед конструкцией с жестким мостом так например погрузчику с поворотным мостом требуется меньшая ширина проходов для проезда по складу что позволяет увеличить полезную площадь склада за счет уменьшения ширины проездов. Также у погрузчика с поворотным мостом уменьшается время цикла штабелирования груза за счет упрощения процесса погрузки груза в штабель. Поэтому целесообразно в разрабатываемом погрузчике использовать поворотный передний мост. Поворотное устройство для поворота моста по принципу действия схоже с поворотным устройством погрузчика ЭП-1008 (зубчатая рейка на гидроцилиндре обкатывает зубчатое колесо.).
Для передачи движения на ходовые колеса вилочных погрузчиков применяют устройства с механическим дифференциалом с гидростатической трансмиссией с электрическим дифференциалом и без дифференциала.
Почти во всех четырехколесных и реже в трехколесных вилочных погрузчиках с приводным передним мостом применяется механический дифференциал. Обычно передние колеса у электропогрузчиков приводятся в движение от одного двигателя через редуктор и механический дифференциал а у автопогрузчиков — через карданный вал коробку передач и специальный механизм обратного хода который соединен при помощи карданного вала с ведущим мостом. Применение карданного вала позволяет располагать двигатель в задней части погрузчика что дает возможность уменьшить массу противовеса а следовательно и всей машины. В отдельных случаях механический дифференциал применяется в трехколесных погрузчиках с приводным передним мостом.
Погрузчики в приводных мостах которых применяется механический дифференциал имеют относительно плохую проходимость в случае недостаточного сцепления с опорной поверхностью одного из ведущих колес а также сравнительно низкий к.п.д. (особенно при поворотах) что увеличивает непроизводительный расход электроэнергии. Широкое применение передние приводные мосты с механическим дифференциалом получили благодаря возможности использовать серийно выпускаемые узлы автомобилей и тракторов что снижает себестоимость изготовления погрузчиков.
Повышение проходимости и маневренности вилочных погрузчиков достигается применением ведущего моста с раздельным приводом передних колес и использованием электрического дифференциала. При прямолинейном движении погрузчика оба приводных двигателя работают синхронно а при проходе по кривой в момент поворота один из двигателей отключается. В электрических схемах привода предусматривается последовательное соединение электродвигателей при значительных радиусах поворота погрузчика и отключение одного из двигателей или изменение стороны его вращения при малых радиусах поворота (до 15 м) которые имеют место при работе погрузчика в закрытых помещениях и вагонах.[19]
8. Экономика(стр 108-120).docx
1.Характеристика конструкции разрабатываемого погрузчика
Данный раздел представляет собой расчет экономической эффективности применения разрабатываемого в данном дипломном проекте электропогрузчика грузоподъемностью 1 т с поворотным грузоподъемником.
а базовый вариант сравнения в расчете экономической эффективности принят электроштабелер CQD15L предназначенный для погрузочно-разгрузочных и подъемно-транспортных работ.
На заданном складе мы производим замену электроштабелеров CQD15L на разработанные электропогрузчики и определяем экономический эффект.
Учет фактора времени в расчетах осуществлялся с помощью дисконтирования т. е. приведения будущих результатов применения погрузчика в стоимостном выражении к нулевому году.
2 Сравнительная технико-экономическая характеристика электропогрузчиков и штабелеров.
2.1 Определяем количество электропогрузчиков и штабелеров при использовании базового и нового варианта
Находим время рабочего цикла погрузчиков:
Обозначения со знаком () относятся к базовому электропогрузчику.
где: L – длина рабочего плеча м;
HCP – средняя высота подъема и опускания вил м;
V’ – скорость передвижения электропогрузчика с грузом мс;
V’I – скорость передвижения электропогрузчика без груза мс;
’ – скорость подъема каретки с грузом мс;
’ – скорость подъема каретки без груза мс;
’ – скорость опускания каретки с грузом мс;
’ – скорость опускания каретки без груза мс;
а - ускорение погрузчика а=03 05мс2;
tВСП – время на вспомогательные операции с;
tпов –время затрачиваемое на повороты погрузчика с.
Для электропогрузчика:
Эксплуатационная производительность погрузчика:
П’Э = = 134 тчас (8.3)
где: КВР – коэффициент использования погрузчика по времени
КГР – коэффициент использования погрузчика по грузоподъемности.
Эксплуатационная сменная производительность погрузчиков.
’ = = 1072 тсмену (8.4)
Объем механизированных работ:
где: QC- суммарный суточный грузопоток т;
kП - коэффициент непосредственной перегрузки груза по прямому варианту.
Потребное количество погрузчиков:
где m – количество рабочих смен за сутки m = 2 см;
nВЫХ nПР – количество выходных и праздничных дней в году 115 дней;
nР – время нахождения погрузочно-разгрузочной машины в ремонте в течение года nР = 16 дней;
Принимаем необходимое число погрузчиков М’Э = 6
2.2 Расчет списочного числа рабочих для обслуживания погрузчиков.
Списочное число механизаторов для обслуживания машин и оборудования определяют учитывая следующие потребности:
водитель на каждый погрузчик;
ремонтник на каждый погрузчик;
аккумуляторщик на 7 погрузчиков.
Списочное число рабочих рассчитываем по формуле:
R’ = αmМэ’(1+1+15) = 1226(1+1+15) = 317 чел. (8.6)
где: a – коэффициент подмены α = 12;
m – количество рабочих смен m = 2.
Принимаем R’ = 32 человек.
R = αmМэ(1+1+17) = 1224(1+1+15) = 211 чел. (8.7)
Принимаем R = 22 человек.
2.3. Расчет энергоемкости батареи разрабатываемого погрузчика и времени его работы без перезарядки батареи.
Средняя затрата электроэнергии от батареи на один цикл погрузчика:
Wц = Wц1+Wц2+Wц3+Wц4 (8.8)
где: Wц1 – расход энергии на движение машины в цикле без груза
Wц2 – расход энергии на движение машины с грузом
Wц3 – расход энергии на подъем груза
Wц4 – расход энергии на подъем грузоподъемника без груза
где: 1–суммарный к.п.д. от зажимов батареи до обода ведущего колеса при движении без груза.
где: 2–суммарный к.п.д.
где: 3 и 3– к. п. д. механизма подъема гидропривода и электродвигателя насоса в режимах работы с грузом и без груза.
GГР – вес подвижных частей грузоподъемника.
Wц’ = 207+237+225+135=804 Втч
Wц = 325+343+225+135=1028 Втч.
Количество циклов разрабатываемого погрузчика в смену при заданном режиме работы (Тсм = 8 час)
Nц’ = (ТсмКвр3600) Тц’ = 80753600202 = 106 циклов.
Nц = (ТсмКвр3600) Тц = 80753600131 =164 циклов.
Энергоемкость батареи.
W6’ = Wц’ Nц’ = 00804 106 = 85 кВтч.
W6 = Wц Nц = 01028 164 =169 кВтч.
Время работы погрузчика без перезарядки батареи.
Тр’ = (Tц’W6’)(3600Wц’) = (20285)(360000804) = 59 час.
Тр = (TцW6)(3600Wц) = (131169)(360001028) = 6 час.
По величине энергоемкости выберем аккумуляторную батарею типа ТНЖ-450-У2 напряжение U = 40 В.
Учитывая использование погрузчика по времени (Кв = 075) энергоемкости выбранной батареи хватит для работы в течение смены.
Для зарядки выбранной батареи необходимо автоматическое зарядное устройство для тяговых аккумуляторных батарей типа ТПП 160-70 (мощность Nз = 12).[22]
Технико-экономические показатели разрабатываемого погрузчика и погрузчика ЭП -1008 приведены в таблице 9.1.
Таблица 8.1 Сравнительная технико-экономическая характеристика погрузчиков.
Разрабатываемый погрузчик
Высота подъема груза м
Максимальная скорость передвижения с грузом мс
Скорость подъема каретки с грузом мс
Скорость опускания каретки мс с грузом
Энергия аккумуляторной батареи кВтч
Время работы погрузчика без перезарядки батареи час
Нормативный срок службы лет
Продолжительность рабочего цикла с
Эксплуатационная производительность тчас
Мощность потребляемая зарядным устройством кВт
Продолжительность нормального заряда батарей час
Обслуживающий персонал чел
Цена батареи руб. за банку
Цена зарядного устройства руб
Количество погрузчиков для выполнения заданного объема работ шт
Основные вложения на организацию механизированной погрузки-разгрузки грузов на складе представляют собой расходы на приобретение:
комплекта сменных тяговых батарей;
зарядного устройства для тяговых батарей.
Обозначения со знаком (“) относятся к разрабатываемому погрузчику. Денежные потоки со знаком (-) представляют собой оттоки денежных средств.
3.1 Электропогрузчики.
Ип = (Мэ' Цп’)– (Мэ Цп) = (6750000)–(41400000) = -1100000 руб. (8.13)
3.2 Сменные аккумуляторные батареи.
Электропогрузчики работают в две смены то сменных аккумуляторных батарей требуется:
Иб = Nn * Цб * 34 - Nn" * Цб" * 34 =6 488634-4488634=332248 руб. (8.14)
3.3 Зарядное устройство.
Изу = Мэ’Цзу’ – МэЦзу =673854– 473854=147708 руб. (8.15)
3.4 Общий объем инвестиций:
Поскольку для выполнения заданного объема погрузочно-разгрузочных работ требуется меньшее количество разрабатываемых погрузчиков (по сравнению с базовым вариантом) но их сумма больше тем самым эта величина не войдет в расчет денежных потоков. Эти инвестиции осуществляются в нулевой год.
И = Ип + Иб + Изу = -1100000+332248+147708=-620044 руб. (8.16)
4. Изменение расходов.
4.1 Расходы на заработную плату.
= Згод R’ – Згод R = 122640(6–4) =245280 руб. (8.17)
где: Згод – годовой размер заработной платы
Згод = Змес 12 = 10220 12 = 122640 руб.
Змес - месячный размер заработной платы.
Змес =Зтариф "+ Д + Здоп =7300+2190+730=10220 руб.
где: Зтариф – тарифная ставка обслуживающего персонала.
Д – размер доплаты (30% размера тарифа)
Д = 730003 = 2190 руб.
Здоп – размер дополнительной заработной платы (10% размера тарифа)
Здоп = 730001=730 руб.
Таким образом общее снижение расходов на заработную плату составит 245280 руб.
Затраты на социальные нужды(26% размера тарифа)
С.Н.=245280026=637728 руб.
4.2 Расходы на электроэнергию:
Э = (Тзар’ Nзу пб Мэ’) Драб.п Цэл – (Тзар Nзу пб Мэ) Драб.пЦэл Э = (71226)34545 – (71224)34545 =521640 руб. (8.18)
где: пб – количество заряжаемых в день аккумуляторных батарей для одного погрузчика пб = 2 шт.
Тзар – продолжительность нормального заряда батарей.
Цэл = 45 руб. – цена 1 кВтчас электроэнергии
Драб.п – число дней работы погрузчика в году с учетом простоев связанных с ремонтом Драб.п = 345 дней.
4.3 Затраты на ремонт погрузчиков.
Затраты на ремонт погрузчиков рассчитываются укрупненно и составляют 12 % от стоимости погрузчиков.
Р = Ип 012 =1400000 012 = 168000 руб. (8.19)
4.4 Затраты на вспомогательные материалы.
Затраты на вспомогательные материалы определяются в размере 15% от стоимости электроэнергии.
Мвсп = Э015 = 521640 015 = 78246 руб. (8.20)
4.5 Амортизационные отчисления:
А = Aп + Азу +Аб = 233800+29542+66450 = 329792 руб. (8.21)
где: Aп – амортизационные отчисления по погрузчикам
Ап = Ип Nal = 14000000167= 233800 руб.
где: Nal =167% –норма амортизации по погрузчикам
Азу – амортизационные отчисления по зарядным устройствам
Азу = Изу Na2 = 147708 02 = 29542 руб.
где: Na2 = 20 %– норма амортизации по зарядным устройствам
Аб – амортизационные отчисления по батареям
Аб = Иб Na3 = 332248 02 =66450 руб.
где: Na3 = 20 %– норма амортизации по батареям.
5 Корректировка денежных потоков.
Корректировка денежных потоков проводится по амортизации.
Остаточная стоимость погрузчиков
Coп = Ип No = 140000001=140000 руб. (8.22)
где: No = 10 % - норма остаточной стоимости.
6 Расчет чистых денежных потоков.
Расчет чистых денежных потоков приведен в таблице 8.2. Чистые денежные потоки представляют собой разность результатов достигнутых в i-том году и затрат осуществленных в том же году. В качестве результатов выступает годовая величина чистой прибыли а в последнем году – также чистая выручка от ликвидации оборудования.
Таблица 8.2 Расчет чистых денежных потоков (тыс. руб.)
7. Определение барьерной ставки
Барьерная ставка определяет ту финансовую отдачу которую инвесторы ожидают от своих капиталовложений и включает в себя два компонента – свободную от риска ставку СРС и страховую премию СП.
БС = СРС + СП (8.23)
Стоимость капитала — это средневзвешенная цена (в процентах) которую предприятие уплатило за денежные средства использованные для формирования своего капитала. Эта величина определяется соотношением заемного и собственного капиталов в пассивной части баланса и может быть определена следующим образом:
СК = БС = ДД · СД + ДСК · ССК (8.24)
где СК – стоимость капитала %;
ДД – доля долга ДД = 02%;
ДСК – доля собственного капитала ДСК = 03 %;
СД– стоимость долга %;
CCК – стоимость собственного капитала %;
Так как выплаты процентов по займам уменьшают величину налогооблагаемой прибыли то собственно уменьшается и величина налоговых выплат. Экономия на налогах частично компенсирует выплаты по долгам. Поэтому процент выплат по займам с учётом этой экономии составит:
где СН – ставка налога на прибыль;СН=02
НСД – номинальная банковская ставка.
Эффективные ставки то есть ставки с учётом реинвестиций по месяцам:
НСД = ((Нкб р) + 1)р – 1 (8.25)
где р – число периодов начисления процентов в течение года р=2
НКБ – номинальная кредитная банковская ставка НКБ = 02
НСД = ((02 2) + 1)2 – 1 = 021
СД = (1 – 02) · 021 = 0168.
НСК = ((Ндб р) + 1)р – 1
Ндб – номинальная депозитная банковская ставка Ндб = 01
НСК = ((01 2) + 1)2 – 1=0103
ССК = (1 – 02) · 0103 = 00824.
СК = БС = 02 · 0168 + 03 · 00824 0103 = 103%
8. Оценка эффективности инвестиций.
8.1 Определение чистой текущей стоимости.
Показателем эффективности инвестиций является чистая текущая стоимость (NPV) представляющая собой сумму дисконтированных чистых денежных потоков от инвестиций за весь расчетный период. Дисконтирование (т.е. учет фактора времени) осуществляется следующим образом:
Значение номинальной банковской ставки рассчитывается как среднее по десяти банкам.
Если значение NPV положительно то инвестиционный проект является эффективным и может рассматриваться вопрос о его осуществлении. Чем больше NPV тем эффективней проект.
Чистая текущая стоимость:
Положительное значение чистой текущей стоимости (NPV) говорит об эффективности рассматриваемого варианта применения разрабатываемого погрузчика (при работе в две смены по 8 часов).
Анализ зависимости экономической эффективности применения разрабатываемого погрузчика от величины барьерной ставки.
Рассмотрим зависимость чистой текущей стоимости от величины барьерной ставки для варианта работы предприятия в две смены по 8 часов (по данным таблицы 8.3) т.е. NPV = (БС)
Внедрение и использование электропогрузчика новой конструкции увеличивает производительность погрузочно-разгрузочных работ позволяет сократить количество обслуживающего персонала и получить экономический эффект.
NPV=868314 тыс. руб.
содержание(стр2).doc
Обзор существующих конструкций и выбор рациональной
Анализ различных вариантов конструктивного исполнения
электропогрузчика 14
Описание конструкции и предварительная разработка
общего вида машины .. 18
Разработка отдельных механизмов и узлов . . . 22
1 Разработка механизма передвижения . 22
2 Расчет грузоподъемного механизма .. . 45
3 Гидравлическая система 60
Организация работ . .72
Автоматизация управления . .. .83
Технология изготовления оси приводного колеса 88
Экономический расчет . .108
Обеспечение безопасности жизнедеятельности .. 121
Список используемой литературы . 132
6. автоматизация(стр 83-87).docx
1 Устройство и принцип работы гидрораспределителя с пропорциональным электрическим управлением.
Одной из наиболее актуальных задач в промышленном использовании грузоподъемных машин является применение пропорционального электрического управления.
PVG 32 является распределителем чувствительным к нагрузке разработанным для обеспечения максимальной гибкости.
При работе насоса главные золотники в рабочей секции (11) находятся в нейтральном положении масло поступает от насоса через соединение P через золотник (6) клапана регулирования давления в бак. Поток масла идущий через золотник клапана регулирования давления определяет давление насоса (давление разгрузки).
Когда приводятся в действие один или более золотников рабочих секций максимальное давление нагрузки подается через клапан «ИЛИ» (10) в полость пружины за клапаном регулирования давления (6) который полностью или частично перекрывает соединение с баком.
Давление насоса воздействует на правую сторону золотника клапана регулирования давления (6). Клапан ограничения давления (1) будет открыт если давление превысит установленное значение возвращая поток от насоса назад в бак.
В рабочей секции с компенсатором давления клапан (14) поддерживает постоянный перепад давления на главном золотнике в двух случаях: когда изменяется нагрузка или когда включается рабочая секция с большей нагрузкой.
В случае рабочей секции без компенсирующего клапана в канал Р встроен обратный клапан противотока (18) который предотвращает возврат потока масла.
Рабочая секция может быть запитана без обратного клапана противотока в канале P если присутствует тормозной клапан.
Предохранительные клапаны PVLP (13) с фиксированной установкой и подпиточные клапаны PVLA (17) в каналах A и B используются для защиты индивидуальных рабочих операций от перегрузки иили кавитации.
Регулирующий LS-давление предохранительный клапан (12) может быть встроен в каналы А и В рабочих секций с компенсирующим клапаном для ограничения давления индивидуальных рабочих операций.
Рисунок 6.1 Гидрораспределитель PVG:
Клапан ограничения давления; 2. Редукционный клапан подачи маcла к системе управления; 3. Соединение датчика давления; 4. Вставка открытый центр; 5. Жиклер закрытый центр; 6. Золотник для регулирования давления; 7. Вставка закрытый центр; 8. Соединение 9. Сигнал 10. Клапан «ИЛИ»; 11. Главный золотник; 12. Клапан ограничивающий LS- давление; 13. Предохранительный и подпиточный клапан 14. Компенсатор давления; 15. LS -соединение канал A; 16. LS -соединение канал B; 17. Подпиточный клапан 18. Обратный клапан противотока; 19. Вспомогательная подача потока управления для 20. Винты регулирования максимального расхода масла для каналов A и B.[21]
При электрическом пропорциональном управлении положение главного золотника регулируется так чтобы оно соответствовало электрическому сигналу например от блока дистанционного управления.
Сигнал (задающий сигнал) преобразуется в гидравлическое давление которое перемещает главный золотник. Положение главного золотника преобразуется датчиком положения (C) в электрический сигнал (сигнал обратной связи). Этот сигнал регистрируется электроникой. Разность между задающим сигналом и сигналом обратной связи приводит в действие электромагнитные клапаны. Электромагнитные клапаны приводятся в действие таким образом чтобы гидравлическое давление перемещало главный золотник в нужное положение.
Электрические соединения с блоком дистанционного управления PVE приводами и источниками питания выполняются с использованием обычных гребенок контактов соединителя.
Рисунок 6.2 Схема электрического соединения.
Фильтрация масла должна предотвращать превышение допустимого уровня содержания час-тиц т.е. превышение допустимой степени заг-рязнения. Максимальное загрязнение для PVG 32 фирмы Sauer - Danfoss составляет 1916 (см. ISO 4406 калибровка в соответствии с методом ACFTD).
Степень загрязнения 1916 может быть поддержана применением фильтра тонкой очистки.
Эффективная фильтрация является наиболее важным предварительным условием в обеспечении надежной работы гидравлической системы и ее длительного срока службы. Производители фильтров сопровождают свою продукцию инструкциями и рекомендациями. Было бы разумно следовать им.
Там где требования безопасности и надежности очень высоки рекомендуется напорный фильтр с байпасом и индикатором. Желателен фильтр с номинальной тонкостью фильтрации 10 мкм (или тоньше) или абсолютный фильтр 20 мкм (или тоньше). Фильтр в сливной магистрали применим для клапанной группы только с механическим приводом.
Тонкость очистки напорного фильтра должна быть выбрана так как это предлагается производителем фильтра с тем чтобы не был превышен уровень частиц 1916.
Для контроля условий работы фильтра он должен быть установлен с датчиком давления или индикатором загрязнения.
В системах с дифференциальными цилиндрами или аккумуляторами фильтр сливной магистрали должен быть выбран по размеру с учетом макс. расхода масла в сливной магистрали. Напорный фильтр должны быть установлен в соответствии с макс. подачей насоса.
Фильтры установленные в PVG 32 имеют задачу не на обеспечение фильтрации в системе а на защиту основных компонентов от больших частиц. Такие частицы могут появляться в системе как результаты поломки насоса появления частиц от шланга использования быстросоединяемых элементов неисправности фильтра запуска загрязнения и т.д.
Фильтр расположенный в электрическом приводе PVE защищающий электромагнитные клапаны имеет ячейку 150 мкм. Разрушающий перепад давления для внутренних фильтров составляет 25 бар (25 МПа).
4.1.Привод(стр 22-42).docx
1 Разработка механизма передвижения.
1.1 Описание механизма передвижения
Рис. 4.1.1 Механизм передвижения
Механизм передвижения погрузчика (рисунок 4.1.1) состоит из тягового электродвигателя 26 и двухступенчатого цилиндрического редуктора 3. В отверстие вала двигателя входит шлицевый конец ведущего вала-шестерни 4 который вращается на двух шариковых подшипниках 20 и 21. На шейке вала-шестерни установлена манжета 24 уплотняющая редуктор.
Промежуточная шестерня 5 установлена на шариковом подшипнике 16 на оси 6 неподвижно закрепленной в крышке 7 редуктора. Ось 6 уплотнена с помощью резиновых колец 15.
Первая ступень редуктора — ведомая цилиндрическая шестерня 8 насажена на шлицевый конец вала-шестерни 9 установленного на двух подшипниках 19. Зазор в зацеплении шестерен в заданных пределах регулируется прокладками 18. На шейке вала-шестерни установлена манжета 23 уплотняющая редуктор.
Вторая ступень редуктора — внутреннее зацепление шестерен — выполнена в колесе и состоит из ведущей вала-шестерни 9 и зубчатого венца 10 прикрепленного к ступице 1. Ось 11 колеса заварена во фланце и неподвижно соединена с крышкой 7 редуктора болтами. Ступица 1 посажена на ось 11 на подшипниках 22 осевое перемещение которых регулируется гайкой 12. В качестве уплотнителя внутреннего зацепления использовано войлочное кольцо 25. Корпус тормозного устройства 2 закреплен на крышке 7 редуктора болтами и служит для установки на нем тормозных колодок. Шина 13 ведущего колеса массивная.
Кинематическая схема механизма передвижения представлена на
Рис. 4.1.2 Кинематическая схема механизма передвижения
1.2 Выбор электродвигателя передвижения
расстояние от центра тяжести груза до спинки вил Lq
скорость передвижения
расстояние от оси механизма поворота грузоподъемника до оси передних колес L
расстояние от центра тяжести погрузчика до оси
механизма поворота грузоподъемника Lg
расстояние от оси передних колес до оси механизма поворота грузоподъемника
габаритные размеры: длина с вилами
шины массивные: передние
Рис. 4.1.3 Расчетная схема для определения сопротивления передвижению погрузчика
Определяем момент сопротивления передвижению (рис. 4.1.3.).
Из условия равновесия определяем критическую скорость при повороте:
где R - радиус поворота центра тяжести погрузчика при повороте грузоподъемника на 90°;
Q - нормируемый (контрольный) угол подъема наклонной плиты при испытании вилочного погрузчика на поперечную устойчивость по стандарту СЭВ.
Определяем центробежные силы центров тяжести погрузчика и груза:
где L - база погрузчика м;
- угол поворота заднего колеса град;
G - вес погрузчика Н;
V - скорость погрузчика мc;
Lg - расстояние от центра тяжести погрузчика до оси передних
где Q - вес груза Н;
Lq - расстояние от центра тяжести груза до оси передних колес м;
Определяем реакции в колесах:
где Hg - высота центра тяжести погрузчика м;
Hq - высота центра тяжести груза м;
Впк- колея передних колес м.
Определяем радиальную просадку шин:
где Н - толщина массивной шины м;
b - ширина массивной шины м;
E - модуль упругости шины Па;
D - наружный диаметр шины м.
Находим длину отпечатка шины:
Определяем приведенное плечо трения отпечатка:
Определим суммарный момент сопротивления повороту приведенный к диаметру ведущего колеса:
где f - коэффициент сопротивления качению;
-коэффициент сопротивления трению колеса относительно опорной поверхности.
Определяем мощность двигателя:
Подбираем по каталогу электродвигатель механизма передвижения 3ДТ-32:
- режим работы ПВ % 40;
- частота вращения обмин 2750.
Определим число оборотов колеса:
где vп - скорость электропогрузчика мс;
Определим общее передаточное число редуктора.
Подбираем расчетом передаточное число передач редуктора до получения общего передаточного числа редуктора i=154.
1.3 Кинематический расчет редуктора
Определяем вращательные моменты на валах :
Определяем частоту вращения валов:
Результаты расчетов сведем в таблицу 4.1.45
Наименование параметра
Критическая скорость при повороте
Центробежные силы центров тяжести погрузчика и груза:
Радиальная посадка шин:
Длина отпечатка шины:
Приведенное плечо трения отпечатка:
Суммарный момент сопротивления повороту приведенный к диаметру ведущего колеса
Число оборотов колеса
Общее передаточное число редуктора
Вращательные моменты на валах
Частота вращения валов:
1.5 Расчет валов и осей на прочность
Выполним расчет вала-шестерни редуктора. Материал – среднеуглеродистая сталь 45. Расчет произведем при помощи программы АРМ «WinShaft». Значения напряжений сведем в таблицу 4.1 а значения коэффициента запаса по усталостной прочности – в таблицу 4.2.
Рисунок 4.1.4 Исходные данные для расчета вала-шестерни
Рисунок 4.1.5 Эпюра эквивалентных напряжений
Распределение эквивалентных напряжений по участкам вала
Эквив. напряжение Нкв.мм
Предел прочности В = 600 Нмм2;
1 600 Условие выполняется.
Рисунок 4.1.6 Эпюра коэффициента запаса по усталостной прочности
Значение коэффициента запаса на участках вала
Наименьший допускаемый коэффициент запаса прочности по пределу усталости К = 2.
304 Условие выполняется.
Произведем расчет оси колеса. Ось колеса не вращается поэтому расчетной схемой будет являться консольная балка с глухой заделкой. Максимальная нагрузка на ось - нагрузка от веса электропогрузчика. Запас прочности колесной оси рассчитываем по сопротивлению пластическим деформациям.
Для упрощения расчетов принимаем что вес погрузчика приходящийся на любое из передних приводных колес приложен в виде сосредоточенной силы на конце консольной балки.
Расчет напряжений произведем при помощи программы «АРМ Beam».
Рисунок 4.1.7 Эпюра эквивалентных напряжений в сечениях оси приводного колеса
Значения эквивалентных напряжений в сечениях оси приводного колеса
Экв. напряжения Нкв.мм
Ось изготавливаем из стали 45. Термообработка – улучшение. Предел прочности по пластическим деформациям МПа.
Находим коэффициент запаса прочности по сопротивлению пластическим деформациям:
где [nS]=2 - нормативный коэффициент запаса прочности.
Условие прочности выполняется.
1.6 Расчет подшипников
Произведем расчет подшипников ведущей цилиндрической шестерни.
Рис. 4.1.8 Схема для расчета сил действующих на подшипники цилиндрической шестерни
Реакции в вертикальной плоскости:
Реакции в горизонтальной плоскости:
Наиболее нагруженным является подшипник А. Произведем его расчет с помощью программы «АРМ WinBear».
Подшипник шариковый радиальный однорядный 104 ГОСТ 8338-75
Коэффициент динамичности
Средняя долговечность
Максимальные контактные напряжения
Выполним расчет подшипника промежуточной оси.
Рис. 4.1.9 Схема для расчета сил действующих на подшипник
Вертикальная реакция:
Горизонтальная реакция:
Произведем расчет подшипника с помощью программы «АРМ WinBear».
Выполним расчет подшипников вала-шестерни.
Рис. 4.1.10 Схема сил действующих на подшипники вала-шестерни
Горизонтальные и вертикальные реакции известны из расчета вала-шестерни. Н Н.
Подшипник в опоре А нагружен больше (RA>RB) но так как размеры подшипников в обоих опорах разные то расчет ведем по обоим подшипникам в программе «АРМ WinBear».
Подшипник шариковый радиальный однорядный 406 ГОСТ 8338-75
Подшипник шариковый радиальный однорядный 305 ГОСТ 8338-75
Выполним расчет подшипников оси колеса.
Рис. 4.1.7 Схема сил действующих на подшипники оси колеса
RB >RA поэтому расчет ведем по подшипнику В. Расчет будем производить в программе «АРМ WinBear».
Подшипник роликовый радиально-упорный 7208 ГОСТ 333-79
3.описание(стр 18-21).doc
Электропогрузчик (Рис.3.1) представляет собой самоходную четырехопорную машину.
Техническая характеристика.
расстояние от центра тяжести груза до спинки вил Lq
скорость передвижения
габаритные размеры: длина с вилами
шины массивные: передние
Корпус представляет собой несущую конструкцию состоящую из рамы капота отсека противовеса.
вилы; 2. передний мост; 3. грузоподъемник; 4- механизм поворота грузоподъемника; 5. защитная рамка; 6. пульт управления;
рулевое колесо; 8. сиденье водителя; 9. аккумуляторная батарея; 10. задний мост.
Сваренные между собой борта поперечины уголки планки листы и кронштейны образуют раму к которой крепятся узлы и детали электропогрузчика. При снятии полика обеспечивается доступ к рулевому управлению приводу.
Хорошая устойчивость погрузчика помимо четырехопорной схемы обеспечивается расположением аккумуляторной батареи в задней части шасси. Передний ведущий мост включает в себя тяговый электродвигатель и двухступенчатый цилиндрический редуктор на каждое переднее колесо с массивной литой шиной. Двигатель прикреплен к корпусу редуктора четырьмя шпильками. В отверстие вала двигателя входит шлицевый конец ведущего вала-шестерни который вращается на двух шариковых подшипниках. На конусном его выходном конце установлен тормозной шкив. Манжеты уплотняют выходные концы ведущего вала-шестерни. Подшипники установлены в распор. Зазор для нормальной работы подшипников регулируют необходимым числом прокладок.
Промежуточная шестерня установлена на шариковом подшипнике на оси неподвижно закрепленной в крышке редуктора. Ось уплотнена с помощью резиновых колец.
Первая ступень редуктора — ведомая цилиндрическая шестерня насажана на шлицевый конец вала-шестерни установленного на двух подшипниках. Зазор в зацеплении шестерен в заданных пределах регулируется прокладками. На шейке вала-шестерни установлена манжета уплотняющая редуктор.
Вторая ступень редуктора — внутреннее зацепление шестерен — выполнена в колесе и состоит из ведущей вала-шестерни и зубчатого венца прикрепленного к ступице. Ось колеса заварена во фланце и неподвижно соединена с крышкой редуктора болтами. Ступица посажена на ось на подшипниках осевое перемещение которых регулируется гайкой. В качестве уплотнителя внутреннего зацепления использовано войлочное кольцо. Корпус тормозного устройства закреплен на крышке редуктора винтами и служит для установки на нем тормозных колодок. Шина ведущего колеса массивная.[20]
Колеса ведущего моста оборудованы колодочными тормозами установленные на ведущих валах редукторов и выполняют функции рабочего и стояночного тормозов.
На электропогрузчике установлен грузоподъемник 3 с высотой подъема 655 м трехрамной конструкции. Грузоподъемник расположен в передней части машины и состоит из внутренней и двух наружных рам каретки цилиндра подъема и цепи. Наклон грузоподъемника от вертикального положения производится цилиндрами наклона. Рамы представляют собой вертикальные стойки выполненные из двутаврового (внутренняя рама) и швеллерного (наружные рамы) профилей соединенные между собой поперечными связями. В нижней части внутренней рамы и в верхней части наружных рам закреплены катки. Катки выполнены на подшипниках качения служат для подвижного соединения рам.
Каретка подвешена на двух цепях переброшенные через гладкие ролики установленные на траверсе цилиндра подъема. На плиту каретки навешиваются вилы 1 или сменные грузозахватные приспособления.
Привод грузоподъемника гидравлический. Гидравлическая схема включает в себя: электродвигатель гидронасос масляный бак гидрораспределитель трубопровод гибкие рукава и гидравлические устройства. Для регулировки расхода и давления рабочей жидкости в гидросистему включены предохранительные клапаны и дроссели. Источником питания служит аккумуляторная батарея установленная в задней части электропогрузчика.
Все приборы управления размещены на передней панели у рабочего места оператора.
4.3. Гидравлическая система(стр 60-71).docx
3.1. Устройство и принцип работы
Гидравличесий привод электропогрузчика обеспечивает подъем подвижных элементов грузоподъемного механизма поворот и наклон грузоподъемника работу усилителя рулевого управления.
Рисунок 4.3.1 Гидравлическая схема электропогрузчика
Основные узлы гидропривода (см.рис.1): бак масляный насосы Н1 и Н2 гидрораспределители P1 и P2 фильтр Ф1 дроссели клапаны предохранительные КП1 цилиндры Ц1 Ц2 Ц3 Ц4 трубопроводы рукава высокого давления. Наибольшее давление рабочей жидкости в гидросистеме 18 МПа. Рабочие жидкости в гидросистеме - масло Дп-11 (в интервале температур окружающей среды от +10 до +40 %) Всесоюзное масло гидравлическое (ВМГЗ) (от -10 до +40 Х2) допускается масло веретенное АУ (до -30 С).
Гидропривод работает следующим образом. При переключении любого из 4-х распределителей в рабочее положение соответствующее указаниям приведенным в табличке на капоте корпуса погрузчика срабатывает микровыключатель и включается электродвигатель насоса Н1. Масло из бака нагнетается через распределитель в соответствующую полость одного из цилиндров. Одновременно рабочая жидкость из другой полости цилиндров возвращается в масляный бак Б1.
При снятии усилия с джойстика управления распределителем электродвигатель насоса выключается золотник устанавливается в нейтральное положение запирая обе полосы цилиндра.
При опускании грузоподъемника электродвигатель не включается. Дроссель постоянного расхода ДР1 в линии подъема каретки обеспечивает одинаковые скорости опускания каретки с грузом и без груза.
3.2 Расчет требуемого усилия на гидроцилиндре поворота.
При повороте грузоподъемника поворотный механизм должен развить крутящий момент достаточный для преодоления сопротивления качению колеса а также момента трения колес:
где f – коэффициент сопротивления качению;
ВПК – колея передних колес м;
Этот момент нагружает зубья силой Q.
где: r= 80мм -радиус начальной окружности шестерни.
рисунок 4.3.2 Схема сил действующих на цилиндр
Рисунок 4.3.3 схема цилиндра
Расчет изгибающих моментов
Материал Сталь 35 ГОСТ 1050-74 HRC 28-32
3.4 Расчет гидроцилиндра поворота грузоподъемника
Таблица 4.3.1 - Исходные данные
Расчет гидравлического привода c гидроцилиндром.
Исходные параметры для расчета гидравлического привода:
Заданное усилие гидроцилиндра
Заданная скорость движения цилиндра
Коэффициент запаса на износ гидроагрегатов
Расчетная скорость движения цилиндра
Рабочая полость цилиндра
Коэффициент гидроцилиндра
Коэфф. расхода слива
Число включенных параллельно гидроцилиндров
Предварительная оценка параметров привода.
Расчетная эффективная мощность привода
Расчетная гидравлическая мощность насоса
Расчетная мощность привода насоса
Параметры зависящие от условий работы привода:
Расчетное давление жидкости в гидросистеме
Расчетная температура воздуха
Перепад температур воздуха и жидкости
Сорт рабочей жидкости
Рабочая температура жидкости
Вязкость жидкости при рабочей температуре
Коэффициент теплоотдачи
Коэффициент использования по времени
Плотность рабочей жидкости
Расчетный расход в напорной линии
Расчетный расход в сливной линии
Параметры гидравлических линий
Длина РВД напорной линии
Длина РВД сливной линии
Длина жесткого трубопровода напорной линии
Длина жесткого трубопровода сливной линии
Расчетная скорость течения жидкости
Расчетный диаметр трубопровода
Принятый диаметр РВД напорной линии
Принятый диаметр РВД сливной линии
Принятый диаметр жесткого трубопровода напорной линии
Принятый диаметр жесткого трубопровода сливной линии
Параметров привода насоса.
Двигатель привода насоса
Мощность двигателя привода насоса
Номинальная частота вращения двигателя
Передаточное отношение раздаточной коробки
Частота вращения вала насоса
КПД раздаточной коробки
Расчет потерь давления в трубопроводах и на гидравлических аппаратах
Исходные данные для определения потерь давления
Расход в напорной линии
Расход в сливной линии
Число Re для РВД напорной линии
Коэффициент потерь давления для РВД напорной линии
Число Re для жесткой напорной линии
Коэфф. потерь давления для жесткого трубопровода напорной линии
Число Re для РВД сливной линии
Коэфф. потерь давления по длине для РВД сливной линии
Число Re для жесткой сливной линии
Коэфф. потерь давления для жесткого трубопровода сливной линии
Расчет суммы коэффициентов местных сопротивлений
Гидрозамки клапаны с коническим запорным элементом
Вход в фильтры .гидропневмоаккумуляторы и т.д.
КОЭФФИЦИЕНТ МЕСТНЫХ ПОТЕРЬ НА НАПОРЕ
Выход жидкости в гидробак
КОЭФФИЦИЕНТ МЕСТНЫХ ПОТЕРЬ НА СЛИВЕ
Расчет потерь на гидравлических аппаратах
Потери на распределителе из Р в А
ПОТЕРИ НА АППАРАТАХ НА НАПОРЕ
Потери на распределителе из В в Т
Потери на теплообменнике
ПОТЕРИ НА АППАРАТАХ НА СЛИВЕ
Основные параметры насоса.
Рабочий объем насоса
Максимальное рабочее давление
Коэффициент подачи (объемный КПД)
Гидромеханический КПД
Допустимая частота вращения
Проверка по допустимой частоте вращения
Расход насоса в расчетном режиме
Основные параметры гидравлического цилиндра
Диаметр поршня расчетный
Диаметр поршня принятый
Диаметр штока расчетный
Диаметр штока принятый
Суммарная площадь поршней
Суммарная площадь поршневых колец
Гидромеханический КПД цилиндра
Номинальная скорость цилиндра
Расчетная скорость гидроцилиндра
Проверка по допустимой скорости цилиндра
Давление в гидросистеме.
Потери давления на сливной линии
Скорость жидкости в РВД
Потери давления в РВД
Скорость жидкости в жестком трубопроводе
Потери давления в жестком трубопроводе
Потери давления на местных сопротивлениях
Потери давления на гидроаппаратах
ОБЩИЕ ПОТЕРИ НА СЛИВЕ
Давление на гидроцилиндре
Давление на выходе из цилиндра
Давление на входе в цилиндр
Потери давления на напорной линии
ОБЩИЕ ПОТЕРИ НА НАПОРЕ
Максимальное давление в гидросистеме.
Давление на выходе из насоса
Проверка по максимальному давлению
Выходные параметры привода
Скорость гидроцилиндра
Коэффициент запаса по скорости
Наибольшее усилие создаваемое цилиндром
Коэффициент запаса по максимальному усилию
Мощность выходная наибольшая
Мощность необходимая для привода насоса
Гидравлический КПД привода
Потери мощности в гидравлической системе
Необходимая площадь поверхности теплоотвода
Расчетный момент привода насоса
Результаты проверки соответствия исходным требованиям
Проверка по частоте вращения насоса
Проверка по скорости цилиндра
Проверка по мощности приводного двигателя
3.5 Расчет гидроцилиндра подъема
Выполним расчет гидроцилиндра подъема. Исходные данные и результаты расчета сведем в таблицы 4.3.5-4.3.8.
4.2.Расчет грузоподъемного механизма(стр 45-59).doc
2. Описание конструкции грузоподъемника.
Грузоподъемный механизм служит с целью вертикального перемещения груза. Для удобства взятия и укладки груза а также для устойчивости груза при его транспортировке подъемник имеет наклон вперед и назад из вертикально положения. Грузоподъемный механизм должен обеспечивать:
а)стабильность прочность элементов грузоподъемника при поднятии на максимальную высоту груза массой равной 12Q (Q — номинальная грузоподъемность);
б)подъем на высоту не более 03-05 м груза массой 133Q;
в)скорость опускания груза при обрыве шлангов не более 06 мс при температуре масла 40±10°С;
г)самопроизвольное и неконтролируемое опускание груза со скоростью не больше 10 мм за 10 минут и при температуре масла от 25 до 40°С;
д)необходимую видимость оператору погрузчика при движении и взятии груза.
Максимальная высота подъема вил определяется расстоянием от уровня пола до нижней части вил поднятого на максимальную высоту при вертикальном подъеме. Рабочая высота грузоподъемника определяется расстоянием от поверхности пола до верхней точки вертикально установленного грузоподъемника при полностью опущенных вилах. Большинство конструкций грузоподъемников обеспечивают подъем вил до транспортного положения (на 300 мм) или на высоту 1200-1300 мм без увеличения рабочей высоты грузоподъемника.
В зависимости от количества рам и высоты подъема вил без увеличения строительной высоты грузоподъемника различают такие типы грузоподъемников как:
а) однорамный без свободной высоты подъема вил;
б) двухрамный без свободной и со свободной высотой подъема вил;
в) трехрамный без свободной и со свободной высотой подъема вил.
В проектируемом погрузчике применяем трехрамный грузоподъемник с высотой подъема груза 655 м.
Конструкция грузоподъемника для высот 595-75 м трехрамного показана на рис. 4.2. У трехрамного грузоподъемника наружная рама 5 неподвижная а средняя 4 и внутренняя 3 подвижные цилиндр подъема 9 одностороннего действия и две цепи каретки. Средняя рама перемещается по роликам 6 вдоль наружной а внутренняя рама вдоль средней.
Рисунок 4.2. Конструкция трехрамного грузоподъемника
Эксцентриковая ось боковых роликов 6 позволяет регулировать боковые зазоры между роликами и рамами. Натяжение цепей регулируют тяги
разницу в натяжении компенсирует балансир 13 закрепленный на оси каретки 12.
Трехрамный грузоподъемник закреплен шарнирно на кожухах полуосей ведущего моста.
Каретка и рамы грузоподъемников перемещаются на катках по направляющим грузоподъемников. В качестве направляющих используют швеллерный двутавровый и другие профили. Катки могут быть установлены как на наружной раме так и на внутренней подвижной раме. Сочетание профилей для внутренней и наружной рам должно иметь минимальное поперечное сечение для обеспечения лучшей видимости водителю.
2.1.Расчет грузоподъемника.
Рисунок 4.2.1 Расчетная схема грузоподъемника.
Определение усилий действующих в плоскости рам
Определение усилий действующих перпендикулярно плоскости рам:
Расчет внутренней рамы от сил действующих в плоскости рамы.
Рама рассчитывается методом сил:
Рисунок 4.2.3.Сечение 1-1
Рисунок4.2.4. Сечение связи 2
Характеристика сечения
Рисунок 4.2.5.Сечение связи 3
Рисунок 4.2.6 Эпюра изгибающих моментов от сил действующих в плоскости
Расчет рамы от сил действующих перпендикулярно плоскости внутренней рамы.
Рисунок 4.2.7. Расчетная схема
Расчет рамы производим методом сил. Действующую на раму нагрузку разбиваем на симметричную и кососимметричною.
Расчет рамы от симметричной нагрузки.
Рисунок 4.2.8. Эпюра симметричной нагрузки.
Учитывая действие кососимметричной нагрузки изгибающий момент увеличиваем на 20%.
Определение напряжений:
Напряжение в т. А направляющей:
Напряжение в т. В связи:
Напряжение в т. С связи:
Для стали 35 т=3200 Па.
Расчет напряжений на отгиб полки.
Рисунок 4.2.9.Сечение полки
Расчет корневого сечения полки от изгиба в плоскости z
От изгиба в плоскости yz
Расчет свободного края полки
Для стали 35 т=3200 Па
Расчет направляющей рамы на отгиб полки
Рисунок 4.2.10. Сечение полки
Напряжение в точке 0 полки
Для внутренней поверхности
Для внешней поверхности
Напряжение в точках 1 полки
Напряжение в точках 0 стенки
Определение контактных напряжений
а) r1=49 мм; r2=150 мм; Р=1466 кг
б) r1=24 мм; r2=50 мм; Р=346 кг
Определение усилий на шток цилиндра.
Рисунок 4.2.11. Расчетная схема усилия на шток цилиндра
Усилие на шток цилиндра
Список литературы.docx
Конструирование узлов и деталей машин под ред. Дунаева П.Ф. Леликова О.П. М. Издательский центр «Академия» 2003.
Краткий справочник металлиста под ред. Орлова П.Н. Скороходова Е.А. М. “Машиностроение” 1987.
Справочник технолога-машиностроителя. В 2-х т. Т. 1 Под ред. А.Г. Косиловой и Р.К. Мещерякова.- 4-е изд. перераб. и доп.- М.: Машиностроение 1986.
Справочник технолога-машиностроителя. В 2-х т. Т. 2 Под ред. А.Г. Косиловой и Р.К. Мещерякова.- 4-е изд. перераб. и доп.- М.: Машиностроение 1985.
Обработка металлов резанием.- М.: Машиностроение 1988.
Единая система допусков и посадок СЭВ в машиностроении и приборостроении: Справочник в 2 т т. 1. М.: издательство стандартов 1989 – 263 с.
Общемашиностроительные нормативы режимов резания для технического нормирования работ на металлорежущих станках. Часть 1. Токарные станки.- М.: Машиностроение 1974.
Электропогрузчики: СправочникИ.И Мачульский В.И. Капырина Е.А. Алепин. – М.: Транспорт 1987.
Мачульский И.И. Погрузочно-разгрузочные машины. – М.: Желдориздат 2000.
Свешников В.К. Станочные гидроприводы: Справочник: Библиотека конструктора. – М.: Машиностроение 2004.
Васильченко В.А. Гидравлическое оборудование мобильных машин: Справочник. – М.: Машиностроение 2000.
Комплексная механизация и автоматизация погрузочно-разгрузочных работ: Учебник для вузов ж.-д. трансп.А.А. Тимошин И.И. Мачульский В.А Голутвин А.Л. Клейнерман В.И. Капырина: Под ред. А.А. Тимошина и И.И. Мачульского. – М.: Маршрут 2003.
Методические указания к курсовому проекту по дисциплине «Комплексная механизация и автоматизация погрузочно-разгрузочных работ». – М.: МИИТ 1996.
Охрана труда на железнодорожном транспорте. Под ред. Ю. Г. Сибарова. М.: Транспорт 1981
Безопасность в чрезвычайных ситуациях. Гражданская оборонаМ.А Шевандин Б.Б. Ботоев Б.Н. Рубцов С.Д. Тыльков и др.: Учебное пособие для студентов вузов ж.-д. трансп.; Под ред. М.А. Шевандина. – М.: Маршрут 2004.
Безопасность жизнедеятельности: Учебник для вузовС.В. Белов А.В Ильницкая А.Ф. Козьяков и др.; Под общ. ред. С.В. Белова. – М.: Высш. шк. 2004.
Введение(стр 3-5).doc
Современные поточные технологические и автоматизированные линии межцеховой и внутрицеховой транспорт погрузочно-разгрузочные операции требуют применения разнообразных типов подъемно-транспортных машин и механизмов обеспечивающих непрерывность и ритмичность производственных процессов. Именно поэтому подъемно-транспортное оборудование в настоящее время из вспомогательного превращается в один из решающих факторов производственного процесса определяющих возможности современного производства.
Насыщенность производства средствами механизации трудоемких и тяжелых работ уровень механизации технологического процесса определяют степень совершенства технологического процесса и производительность труда на предприятии.
По подсчетам зарубежных и наших экономистов затраты на погрузочно-разгрузочные и транспортно-складские (ПРТС) работы составляют 25-50% общих издержек производства поэтому в развитых странах темпы выпуска средств механизации перегрузочных и транспортных работ опережают рост продукции промышленности в целом а в западноевропейских странах — рост продукции машиностроения.
В СНГ на погрузочно-разгрузочных транспортных и складских работах занято 18% всех промышленно-производственных рабочих а с учетом привлечения к таким работам персонала основных профессий эта доля увеличивается до 28-30% (по данным Госкомстата число занятых соответственно 8 млн. чел. и 2 млн. без учета предприятий торговли и сельского хозяйства). Наиболее сложной является проблема грузопереработки тарно-штучных грузов на выполнение которой занято более 23 всех рабочих осуществляющих перегрузочные операции 12 из которых выполняет их в условиях тяжелого физического труда.
Уровень комплексной механизации и автоматизации ПРТС работ в отраслях страны в значительной мере зависит от их оснащенности машинами напольного безрельсового транспорта (МНБТ) которые являются универсальными и наиболее массовыми машинами обеспечивающими высокую эффективность работ и высвобождающих большое количество подсобных рабочих занятых тяжелым физическим трудом.
О высокой эффективности применения МНБТ при перегрузочных и транспортных работах свидетельствуют общий парк и объемы производства этих машин. По экспертным оценкам парк погрузчиков в технически развитых странах составляет более 2 млн. штук: в США — около 700 тыс. в Японии — 300 тыс. в ФРГ — 250 тыс. в Великобритании — 200 тыс. в Италии — 180 тыс. во Франции — 170 тыс.
Разработкой конструкций и производством занято более 250 фирм из них около 100 в Европе.
Большинство фирм предлагает различные модели и типы МНБТ по исполнениям высот подъема взрывозащищенности типам двигателей (карбюраторные дизельные сжиженный газ дизель-электрические) видам трансмиссий (гидромеханические гидростатические механические) импульсный и контакторным системам управления электроприводом типам шин (массивные пневматические полу-пневматические суперэлластик) грузоподъемности видам грузозахватных приспособлений.
С увеличением объема пакетных перевозок эффективность использования МНБТ еще более возрастает. При пакетных перевозках производительность труда по сравнение с ручной поштучной погрузкой-выгрузкой увеличивается в 7-10 раз себестоимость обработки 1 т груза снижается в 6-10 раз простой вагонов уменьшается более чем в 2 раза а автомобилей — более чем в 6 раз.
Универсальность машин напольного безрельсового транспорта предопределяет крупносерийный характер их производства в сравнении с другими видами подъемно-транспортного оборудования. Это снижает расходы на изготовление и эксплуатацию этих машин упрощает решение вопросов обеспечения запасными частями и оснасткой при ремонте.
Во всех отраслях народного хозяйства осуществляется последовательный переход от создания и внедрения отдельных машин оборудования приборов и технологических процессов к разработке производству и массовому использованию высокоэффективных систем особенно на транспортных и складских операциях. Успешно претворяется в жизнь программа ускоренного развития перегрузочных машин технического оснащения пунктов перегрузки и складов совершенствования технологии погрузочно-разгрузочных работ.