Металлическая конструкция крана-манипулятора




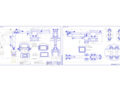
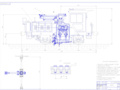
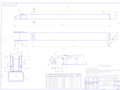
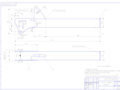
- Добавлен: 25.10.2022
- Размер: 2 MB
- Закачек: 2
Описание
Состав проекта
![]() |
![]() ![]() |
![]() ![]() ![]() ![]() |
![]() ![]() |
![]() ![]() ![]() ![]() |
![]() ![]() ![]() ![]() |
![]() ![]() |
![]() ![]() |
![]() ![]() |
![]() ![]() ![]() ![]() |
![]() ![]() |
![]() ![]() |
![]() ![]() |
![]() ![]() |
![]() ![]() |
![]() ![]() ![]() ![]() |
![]() ![]() ![]() |
Дополнительная информация
КМ 12.02.00.000 СБ.dwg

КМ 12.02.05.000 СБ.dwg

КМ 12.02.06.000 СБ.dwg

КМ 12.00.00.000 СБ.dwg

КМ 12.02.07.000 СБ.dwg

Рекомендуемые чертежи
- 24.04.2014
Свободное скачивание на сегодня
Другие проекты
- 09.07.2014