Механический участок обработки детали "Шестерня"




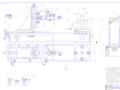
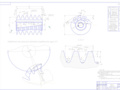
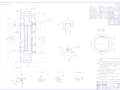
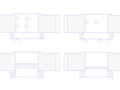
- Добавлен: 25.10.2022
- Размер: 9 MB
- Закачек: 0
Описание
Состав проекта
![]() |
![]() |
![]() |
![]() |
![]() |
![]() |
![]() |
![]() |
![]() |
![]() |
![]() |
![]() ![]() ![]() |
![]() ![]() ![]() |
![]() ![]() ![]() |
![]() ![]() ![]() |
![]() ![]() ![]() |
![]() ![]() ![]() |
![]() ![]() ![]() |
![]() ![]() ![]() |
![]() ![]() ![]() |
![]() ![]() ![]() |
![]() ![]() ![]() |
![]() ![]() ![]() |
![]() ![]() ![]() ![]() |
![]() |
![]() ![]() ![]() ![]() |
![]() ![]() ![]() ![]() |
![]() ![]() ![]() |
![]() ![]() ![]() |
![]() ![]() ![]() |
![]() |
![]() ![]() ![]() |
![]() ![]() ![]() |
![]() ![]() |
![]() ![]() |
![]() ![]() ![]() |
![]() ![]() ![]() |
![]() ![]() |
![]() ![]() |
![]() ![]() |
![]() ![]() |
![]() ![]() ![]() |
![]() ![]() ![]() |
![]() ![]() |
![]() ![]() ![]() |
![]() |
![]() ![]() ![]() ![]() |
![]() ![]() ![]() ![]() |
![]() ![]() ![]() |
![]() ![]() ![]() |
![]() ![]() ![]() |
![]() ![]() ![]() |
![]() ![]() ![]() ![]() |
![]() ![]() ![]() ![]() |
![]() ![]() ![]() |
![]() ![]() ![]() |
![]() ![]() ![]() ![]() |
![]() ![]() ![]() ![]() |
![]() ![]() ![]() |
![]() ![]() ![]() ![]() |
![]() ![]() ![]() ![]() |
![]() ![]() ![]() |
![]() ![]() ![]() |
![]() ![]() ![]() ![]() |
![]() ![]() ![]() ![]() |
![]() ![]() ![]() |
![]() ![]() ![]() ![]() |
![]() ![]() ![]() ![]() |
![]() ![]() ![]() ![]() |
![]() ![]() ![]() ![]() |
![]() ![]() ![]() ![]() |
![]() |
![]() ![]() ![]() ![]() |
![]() ![]() ![]() ![]() |
![]() ![]() ![]() ![]() |
![]() ![]() ![]() ![]() |
![]() ![]() ![]() ![]() |
![]() ![]() ![]() ![]() |
![]() ![]() ![]() ![]() |
![]() ![]() ![]() ![]() |
![]() ![]() ![]() ![]() |
![]() ![]() ![]() ![]() |
![]() ![]() ![]() ![]() |
![]() ![]() ![]() ![]() |
![]() ![]() ![]() ![]() |
![]() ![]() ![]() ![]() |
![]() ![]() ![]() ![]() |
![]() |
![]() |
![]() |
![]() ![]() ![]() |
![]() |
![]() |
![]() ![]() ![]() ![]() |
![]() |
![]() |
![]() |
![]() |
![]() |
![]() ![]() ![]() ![]() |
![]() ![]() ![]() ![]() |
![]() ![]() ![]() ![]() |
![]() ![]() ![]() ![]() |
![]() |
![]() ![]() ![]() |
![]() ![]() ![]() |
![]() ![]() ![]() |
![]() |
![]() |
![]() |
![]() ![]() ![]() |
![]() ![]() |
![]() ![]() ![]() |
![]() ![]() ![]() |
![]() |
Дополнительная информация
ГПС +7.dwg
Зубофрезерный полуавтомат с ЧПУ 53А50МФ6
Вертикальный зубодолбежный станок с ЧПУ ВС-123ВФ3
Зубозакругляющий станок PRAWEMA FA 400
Координатно-шлифовальный станок КШ-320
Зубошлифовальный станок 5Д833
Автоматизированный склад заготовок и готовых деталей
Автоматизированная система уборки отходов (АСУО)
Автоматизированная система инструментообеспечения (АСИО)
Координатно-измерительная машина (КИМ)
Участок автоматизированного контроля
Участок подготовки производства (УПП)
Робот-манипулятор L-2400
Условные обозначения
-подключение электроэнергии
Технология машиностроения
Склад цеховых заготовок
Фрагмент- Линейный размер 2(РТК) +7.dwg
технологического процеса
РТК токарная +7.dwg
ОПЕРАЦИЯ 005 ТОКАРНАЯ С ЧПУ. СТАНОК 1727Ф6
03-0060 Т5К10 ГОСТ 19049-80
91-0398 Т15К6 ГОСТ 19056-80
91-0398 Т15К6 ГОСТ 19069-80
05-055 Т5К10 ГОСТ 19064-80
Контрольное приспособление + 7.dwg
но без заеданий. Регулировать с помощью детали
поз. 19. Смазка направляющих ходовых винтов;
дет. 14 :ЦИАТИМ 201 ГОСТ 6267-74.
Направление движения угольника (поз.2)
должно совпадать с плоскостью
ось оправки (поз.3) с точностью 0
при любом положении на направляющих.
Качание детали поз. 5 в зоне крепления
шарового наконечника (замер индикатором на
стойке) в любой плоскости по отношению уголь-
ника (поз.2) не более 0
Наружные поверхности угольника и основа-
ния (поз.1) окрасить в черный цвет.
Маркировать Д85-095 шрифт 5 ГОСТ2.304-81.
для контроля радиального биения
шестерен с наружным зацеплением
РТК токарная 1 +7.dwg
ОПЕРАЦИЯ 005 ТОКАРНАЯ С ЧПУ. СТАНОК 1727Ф6
03-0060 Т5К10 ГОСТ 19049-80
91-0398 Т15К6 ГОСТ 19056-80
91-0398 Т15К6 ГОСТ 19069-80
05-055 Т5К10 ГОСТ 19064-80
Фреза + 7.dwg
Сталь Р18 ГОСТ 19265-73
На всех поверхностях фрезы не должно быть заусенцов и
на шлифованных поверхностях не должно быть
забоин и выкрошенных мест
Погрешность зацепления 0
Накопленная погрешность окружного шага стружечных
Определение максимального диаметра шлифовального круга (2:1)
деталь +7.dwg
сердцевина зуба 30 45 HRC.
Штамповочные радиусы не более 10мм.
Штамповочные уклоны не более 10
Переход от закругленной части зуба к
незакругленной должен быть плавным.
Клеймить Д395Б-04-045.
Маркировать номер детали на бирке
Допускается замена материала на сталь
*-Размеры обеспечиваются инструментом.
Коэффициент смещения
Допуск на радиальное биение
Ширина впадины по дуге
делительной окружности
Диаметр делительной
Сталь 25ХГТ ГОСТ 4543-71
Диаметр делительной окружности
Фрагмент- Диаметральный размер 2 (РТК) +7.dwg
технологического процесса
Экономика (на формате А3) + 7.dwg
разработанных с помощью САПР
Технико-экономические показатели
финансы и эффективность
Годовой объем продаж
Годовая выручка от реализации товара
контролируемая фирмой
Темп роста емкости рынка
Число потребителей товара фирмы
Уровень послепродажного обслуживания потребителей
Длительность жизненного цикла инвестиционного проекта
Удельный вес прогресивных технологий
Уровень гибкости производства
Уровень использования производственной мощности
Средний коэффициент загрузки оборудования
Средний возраст технологического оборудования
Число единиц технологического оборудования
Производственные площади
Численность персонала
Производственный персонал
Годовые текущие затраты
Себестоимость единицы продукции
Точка безубыточности
Капитальные вложения
Годовая сумма налогов
Годовая чистая прибыль
Годовая сумма амортизации
Годовая ставка дисконта
Чистый дисконтированный доход
Внутренняя норма доходности
Фрагмент- Диаметральный размер (РТК) + 7.dwg
технологического процесса
Чертеж станочного приспособления +7.dwg
Давление сжатого воздуха в заводской
Технические требования
Допуск соосности поверхности d относи-
тельно установочной поверхности приспособле-
*-Размеры для справок.
Маркировать Д75-1005СБ. шрифт 7
Фрагмент- Линейный размер 1(РТК) + 7.dwg
технологического процеса
Фрагмент- Линейный размер 2(РТК) +7.frw

технологического процеса
рис1-.frw

Длина общей нормали W=98.16
Фрагмент операционного эскиза
рис7-.frw

-соединительная муфта
-силовой пневмоцилиндр
Теоретическая схема закрепления
рис13-.frw

рис11 -.frw

рис4-.frw

рис8-.dwg
-установочная плоскость
рис10-.dwg
-быстросменная шайба
-фиксирующее устройство
-соединительная муфта
-силовой пневмоцилиндр
рис7-.dwg
-соединительная муфта
-силовой пневмоцилиндр
Теоретическая схема закрепления
рис1-.dwg
Установить заготовку
Фрагмент операционного эскиза
рис5-.frw

рис1-.frw

Длина общей нормали W=98.16
Фрагмент операционного эскиза
рис7-.frw

-соединительная муфта
-силовой пневмоцилиндр
Теоретическая схема закрепления
рис13-.frw

рис11 -.frw

рис4-.frw

рис5-.frw

рис2-.frw

рис10-.frw

-быстросменная шайба
-фиксирующее устройство
-соединительная муфта
-силовой пневмоцилиндр
рис14-.frw

рис3-.frw

рис8-.frw

-установочная плоскость
рис9-.frw

рис6-.frw

рис2-.frw

рис10-.frw

-быстросменная шайба
-фиксирующее устройство
-соединительная муфта
-силовой пневмоцилиндр
рис14-.frw

рис3-.frw

рис8-.frw

-установочная плоскость
рис9-.frw

рис6-.frw

Фрагмент- Диаметральный размер (РТК) + 7.frw

технологического процесса
РТК токарная +7.cdw

ОПЕРАЦИЯ 005 ТОКАРНАЯ С ЧПУ. СТАНОК 1727Ф6
03-0060 Т5К10 ГОСТ 19049-80
91-0398 Т15К6 ГОСТ 19056-80
91-0398 Т15К6 ГОСТ 19069-80
05-055 Т5К10 ГОСТ 19064-80
Контрольное приспособление + 7.cdw

но без заеданий. Регулировать с помощью детали
поз. 19. Смазка направляющих ходовых винтов;
дет. 14 :ЦИАТИМ 201 ГОСТ 6267-74.
Направление движения угольника (поз.2)
должно совпадать с плоскостью
ось оправки (поз.3) с точностью 0
при любом положении на направляющих.
Качание детали поз. 5 в зоне крепления
шарового наконечника (замер индикатором на
стойке) в любой плоскости по отношению уголь-
ника (поз.2) не более 0
Наружные поверхности угольника и основа-
ния (поз.1) окрасить в черный цвет.
Маркировать Д85-095 шрифт 5 ГОСТ2.304-81.
для контроля радиального биения
шестерен с наружным зацеплением
деталь +7.cdw

сердцевина зуба 30 45 HRC.
Штамповочные радиусы не более 10мм.
Штамповочные уклоны не более 10
Переход от закругленной части зуба к
незакругленной должен быть плавным.
Клеймить Д395Б-04-045.
Маркировать номер детали на бирке
Допускается замена материала на сталь
*-Размеры обеспечиваются инструментом.
Коэффициент смещения
Допуск на радиальное биение
Ширина впадины по дуге
делительной окружности
Диаметр делительной
Сталь 25ХГТ ГОСТ 4543-71
Диаметр делительной окружности
Фрагмент- Линейный размер 1(РТК) + 7.frw

технологического процеса
Фрагмент- Линейный размер 2(РТК) +7.frw

технологического процеса
Фрагмент- Диаметральный размер (РТК) + 7.frw

технологического процесса
РТК токарная +7.cdw

ОПЕРАЦИЯ 005 ТОКАРНАЯ С ЧПУ. СТАНОК 1727Ф6
03-0060 Т5К10 ГОСТ 19049-80
91-0398 Т15К6 ГОСТ 19056-80
91-0398 Т15К6 ГОСТ 19069-80
05-055 Т5К10 ГОСТ 19064-80
Контрольное приспособление + 7.cdw

но без заеданий. Регулировать с помощью детали
поз. 19. Смазка направляющих ходовых винтов;
дет. 14 :ЦИАТИМ 201 ГОСТ 6267-74.
Направление движения угольника (поз.2)
должно совпадать с плоскостью
ось оправки (поз.3) с точностью 0
при любом положении на направляющих.
Качание детали поз. 5 в зоне крепления
шарового наконечника (замер индикатором на
стойке) в любой плоскости по отношению уголь-
ника (поз.2) не более 0
Наружные поверхности угольника и основа-
ния (поз.1) окрасить в черный цвет.
Маркировать Д85-095 шрифт 5 ГОСТ2.304-81.
для контроля радиального биения
шестерен с наружным зацеплением
деталь +7.cdw

сердцевина зуба 30 45 HRC.
Штамповочные радиусы не более 10мм.
Штамповочные уклоны не более 10
Переход от закругленной части зуба к
незакругленной должен быть плавным.
Клеймить Д395Б-04-045.
Маркировать номер детали на бирке
Допускается замена материала на сталь
*-Размеры обеспечиваются инструментом.
Коэффициент смещения
Допуск на радиальное биение
Ширина впадины по дуге
делительной окружности
Диаметр делительной
Сталь 25ХГТ ГОСТ 4543-71
Диаметр делительной окружности
Фрагмент- Линейный размер 1(РТК) + 7.frw

технологического процеса
Чертеж станочного приспособления +7.cdw

Давление сжатого воздуха в заводской
Технические требования
Допуск соосности поверхности d относи-
тельно установочной поверхности приспособле-
*-Размеры для справок.
Маркировать Д75-1005СБ. шрифт 7
Экономика (на формате А3) + 7.cdw

разработанных с помощью САПР
Технико-экономические показатели
финансы и эффективность
Годовой объем продаж
Годовая выручка от реализации товара
контролируемая фирмой
Темп роста емкости рынка
Число потребителей товара фирмы
Уровень послепродажного обслуживания потребителей
Длительность жизненного цикла инвестиционного проекта
Удельный вес прогресивных технологий
Уровень гибкости производства
Уровень использования производственной мощности
Средний коэффициент загрузки оборудования
Средний возраст технологического оборудования
Число единиц технологического оборудования
Производственные площади
Численность персонала
Производственный персонал
Годовые текущие затраты
Себестоимость единицы продукции
Точка безубыточности
Капитальные вложения
Годовая сумма налогов
Годовая чистая прибыль
Годовая сумма амортизации
Годовая ставка дисконта
Чистый дисконтированный доход
Внутренняя норма доходности
РТК токарная 1 +7.cdw

ОПЕРАЦИЯ 005 ТОКАРНАЯ С ЧПУ. СТАНОК 1727Ф6
03-0060 Т5К10 ГОСТ 19049-80
91-0398 Т15К6 ГОСТ 19056-80
91-0398 Т15К6 ГОСТ 19069-80
05-055 Т5К10 ГОСТ 19064-80
ГПС +7.cdw

Зубофрезерный полуавтомат с ЧПУ 53А50МФ6
Вертикальный зубодолбежный станок с ЧПУ ВС-123ВФ3
Зубозакругляющий станок PRAWEMA FA 400
Координатно-шлифовальный станок КШ-320
Зубошлифовальный станок 5Д833
Автоматизированный склад заготовок и готовых деталей
Автоматизированная система уборки отходов (АСУО)
Автоматизированная система инструментообеспечения (АСИО)
Координатно-измерительная машина (КИМ)
Участок автоматизированного контроля
Участок подготовки производства (УПП)
Робот-манипулятор L-2400
Условные обозначения
-подключение электроэнергии
Технология машиностроения
Склад цеховых заготовок
Фрагмент- Диаметральный размер 2 (РТК) +7.frw

технологического процесса
Фреза + 7.cdw

Сталь Р18 ГОСТ 19265-73
На всех поверхностях фрезы не должно быть заусенцов и
на шлифованных поверхностях не должно быть
забоин и выкрошенных мест
Погрешность зацепления 0
Накопленная погрешность окружного шага стружечных
Определение максимального диаметра шлифовального круга (2:1)
Чертеж станочного приспособления +7.cdw

Давление сжатого воздуха в заводской
Технические требования
Допуск соосности поверхности d относи-
тельно установочной поверхности приспособле-
*-Размеры для справок.
Маркировать Д75-1005СБ. шрифт 7
Экономика (на формате А3) + 7.cdw

разработанных с помощью САПР
Технико-экономические показатели
финансы и эффективность
Годовой объем продаж
Годовая выручка от реализации товара
контролируемая фирмой
Темп роста емкости рынка
Число потребителей товара фирмы
Уровень послепродажного обслуживания потребителей
Длительность жизненного цикла инвестиционного проекта
Удельный вес прогресивных технологий
Уровень гибкости производства
Уровень использования производственной мощности
Средний коэффициент загрузки оборудования
Средний возраст технологического оборудования
Число единиц технологического оборудования
Производственные площади
Численность персонала
Производственный персонал
Годовые текущие затраты
Себестоимость единицы продукции
Точка безубыточности
Капитальные вложения
Годовая сумма налогов
Годовая чистая прибыль
Годовая сумма амортизации
Годовая ставка дисконта
Чистый дисконтированный доход
Внутренняя норма доходности
РТК токарная 1 +7.cdw

ОПЕРАЦИЯ 005 ТОКАРНАЯ С ЧПУ. СТАНОК 1727Ф6
03-0060 Т5К10 ГОСТ 19049-80
91-0398 Т15К6 ГОСТ 19056-80
91-0398 Т15К6 ГОСТ 19069-80
05-055 Т5К10 ГОСТ 19064-80
Представители +7.frw

Представители +7.frw

ГПС +7.cdw

Зубофрезерный полуавтомат с ЧПУ 53А50МФ6
Вертикальный зубодолбежный станок с ЧПУ ВС-123ВФ3
Зубозакругляющий станок PRAWEMA FA 400
Координатно-шлифовальный станок КШ-320
Зубошлифовальный станок 5Д833
Автоматизированный склад заготовок и готовых деталей
Автоматизированная система уборки отходов (АСУО)
Автоматизированная система инструментообеспечения (АСИО)
Координатно-измерительная машина (КИМ)
Участок автоматизированного контроля
Участок подготовки производства (УПП)
Робот-манипулятор L-2400
Условные обозначения
-подключение электроэнергии
Технология машиностроения
Склад цеховых заготовок
Фрагмент- Диаметральный размер 2 (РТК) +7.frw

технологического процесса
Фреза + 7.cdw

Сталь Р18 ГОСТ 19265-73
На всех поверхностях фрезы не должно быть заусенцов и
на шлифованных поверхностях не должно быть
забоин и выкрошенных мест
Погрешность зацепления 0
Накопленная погрешность окружного шага стружечных
Определение максимального диаметра шлифовального круга (2:1)
ПЗ расчет оборудов..doc
Потребный годовой фонд времени для производства данного изделия Fg мингод
где: Ф – количество рабочих дней в году;
H – количество рабочих часов в смену;
m – количество смен работы оборудования в сутки;
k коэффициент использования номинального фонда времени в процентах от годового фонда времени; k=097.
Расчет потребного количества оборудования при серийном методе производства произведем по формуле:
где:– трудоемкость работ выполняемых на данной операции с учетом всей номенклатуры выполняемых работ;
– коэффициент норм времени; =10 12 ;
Определим коэффициент загрузки станков:
L-2400.doc
Номинальная грузоподъемность кг 681
Число степеней подвижности 5
Число рукзахватов на руку 11
Тип привода Гидравлический
Устройство управления Цикловое
Число программируемых координат 5
Способ программирования перемещений Обучение по первому циклу
Ёмкость памяти системы число положений рабочего органа 60
Погрешность позиционированиямм ±127
Максимальный радиус зоны обслуживания Rмм 2134
Линейные перемещения со скоростью 0914мс мм:
ГПСдля +7.doc
В настоящее время 90% машиностроительных производств - это серийное производство. Основным средством автоматизации является использование оборудования с ЧПУ промышленных роботов и универсальных автоматизированных средств контроля (КИМ). Все это оборудование обладает достаточной гибкостью за счет универсальных методов обработки и измерения и возможности быстрой смены программного управления рабочим циклом. Так же у оборудования с ЧПУ высокая производительность работы в автоматическом цикле. Современные станки с ЧПУ являются многоцелевыми и многофункциональными то есть обеспечивают обработку широкой номенклатуры заданного типоразмера различными методами обработки.
Все это является предпосылками внедрения для производства дипломной детали гибкой производственной системы (ГПС).
Исходя из номенклатуры выпускаемых изделий были выбраны станки удовлетворяющие всем условиям производства:
Многофункциональный токарный обрабатывающий центр 1727Ф6
Зубофрезерный полуавтомат с ЧПУ 53А50МФ6
Вертикальный зубодолбежный станок с ЧПУ ВС-123ВФ3
Зубозакругляющий снимающий заусенцы станок PRAWEMA FA 400
Координатно-шлифовальный станок КШ-320
Зубошлифовальный станок 5Д833.
Все станки снабжены автоматическими или автоматизированными приспособлениями для закрепления заготовки.
Складская система (СС):
СС в составе ГПС выполняет следующие функции: прием с внешней или внутренней транспортной системы (ТС) материальные потоки с определенными параметрами хранить обслуживать грузы и подавать их обратно в ТС по запросу.
Для выполнения всех перечисленных функций СС состоит из ряда стеллажей с общим количеством ячеек равным 90 позволяющих размещать одновременно около 750 заготовок и готовых деталей на приспособлениях спутниках что достаточно для бесперебойного функционирования ГПС длительное время. Так же в состав СС входит ряд промежуточных накопителей служащих для связи складской системы с участком подготовки производства и для передачи и приема спутников с деталями из ТС. Обслуживает СС кран-штабелер.
Для установки хранения и перемещения заготовок и деталей в пределах ГПС выбираем универсальную для всей выпускаемой номенклатуры изделий тару(спутник) позволяющую установить одновременно до восьми деталей.
Рисунок1: Универсальная тара.
Установка и снятие заготовки со стола или приспособления станка а так же перемещение ее до накопителя с тарой и обратно осуществляется при помощи робота-манипулятора L-2400 изображенного на рисунке 2 .
Рисунок 2: Робот-манипулятор L-2400.
Основное назначение — для установки заготовок на металлорежущие станки и снятие готовых деталей; штабелирование грузов; обслуживание конвейеров и другие операции.
Номинальная грузоподъемность кг 681
Число степеней подвижности 5
Число рукзахватов на руку 11
Тип привода гидравлический
Устройство управления цикловое
Число программируемых координат 5
Способ программирования перемещений обучение по первому циклу
Ёмкость памяти системы число положений рабочего органа 60
Погрешность позиционирования мм ±07
Максимальный радиус зоны обслуживания R мм 2134
Линейные перемещения со скоростью 0914мс мм:
Участок подготовки производства:
В ГПС существует масса механических операций которые не могут выполнить автоматические устройства или это экономически не выгодно. Складские ручные операции объединяют на специальных участках подготовки производства (УПП). В проектируемой ГПС такой участок встроен в СС а связь между ними осуществляется через накопители которые обслуживает непосредственно кран-штабелер. В УПП расположены стеллажи инструмент и оснастка необходимые для обслуживания грузов
Транспортная система (ТС):
Служит для доставки грузов от СС в заданный момент времени к требуемому месту или оборудованию установки и съема груза с вспомогательного оборудования доставки грузов на участок контроля и мойки а так же для обслуживания других систем функционирования ГПС(АСУОАСИО). Транспортным средством ТС является робокар.
Автоматизированная система инструментального обеспечения (АСИО):
Организация перемещения инструментов и инструментальных комплектов.
Хранение и настройка инструментов и инструментальных комплектов.
Сборка инструментальных комплектов.
Восстановление инструментов (заточка замена пластин напыление).
Очистка инструментов перед их промежуточным хранением.
Контроль за состоянием режущих инструментов.
Замену единичных инструментов наборов и комплектов осуществляют:
при смене номенклатуры обрабатываемых деталей при поломке или другом функциональном отказе режущего инструмента. Для уменьшения загрузки ТС необходимо увеличивать транспортную партию.
Участок автоматизированного контроля:
В настоящее время на станках с ЧПУ для измерения размеров деталей применяют универсальный мерильный инструмент: нутромеры микрометры индикаторы калибры. Для контроля проводимого вне станка на специальных контрольных постах (станциях) дополнительно используют специальные оправки рейсмусы иногда инструментальные микроскопы. Работа с таким мерительным инструментом требует большого внимания со стороны контролеров. Так как комплексную проверку деталей можно проводить только при наличии большой номенклатуры мерительных инструментов и это требует как специальных навыков так и кропотливых расчетов то на практике многие размеры часто не контролируются и проверяются лишь выборочные детали.
Именно для размерного контроля вне станка в составе ГПС имеется контрольный пост который оснащен координатно-измерительной машиной. В основу работы координатно-измеритепьных машин (КИМ) положен расчет контролируемых геометрических параметров поверхностей по результатам измерения положения отдельных точек на этих поверхностях. Для отсчета положений отдельных точек используется координатная система относительно которой положение измеряемого объекта фиксировано.
Компоновка используемой координатно-измерительной машины показана на рис. 3. Объект измерения располагают в рабочем пространстве машины т.е. в области доступной движению измерительной головки.
Рисунок 3: Координатно-измерительная машина.
— стол 2 — пиноль 3 — измерительная бабка 4 — портал
— измерительная головка
Использование в качестве системы управления индивидуального компьютера с клавиатурой для ввода данных и программ дисплеем и устройством печати позволяет ввести в память компьютера программу измерения отработать ее и вывести результаты измерения на печать или на дисплей.
Автоматизированная система утилизации отходов (АСУО):
Служит для обеспечения надежной работы оборудования за счет своевременного удаления стружки из зоны резания транспортирования ее от оборудования к месту складирования сортировки и утилизации а так же непосредственно для сортировки и утилизации. Транспортировка осуществляется оператором станка на тележке в конце смены.
В соответствии с требованиями по безопасности труда и пожарной безопасности предусмотрены все необходимые меры и средства.
Станки в ПЗ.doc
Предназначен для токарной обработки деталей (тел вращения) с выполнением фрезерных зубообрабатывающих сверлильно-расточных операций. Станок 1727Ф6 . многофункциональные токарные обрабатывающие центры обеспечивает последовательную двухстороннюю обработку с автоматической передачей детали из патрона в патрон двух шпиндельных бабок.
Базовый станок оснащен 2-мя револьверными головками.
Многофункциональность станка высокие точность (некруглость до 2 мкм) и скорость обработки позволяют использовать его для изготовления высокоточных и сложных деталей на предприятиях различных отраслей промышленности с применением современного инструмента.
Наклонная станина обеспечивает свободный сход стружки и удобный доступ к обрабатываемой детали.
Технические характеристики
Предельные размеры устанавливаемых поверхностей не менее мм:
наибольший диаметр над станиной
диаметр в гидропатроне левом
диаметр в гидропатроне правом
Предельные размеры обрабатываемых поверхностей не менее мм:
наибольший диаметр над суппортом
наибольшая длина (патронное исполнение)
Высота устанавливаемого резца в головке автоматической 4х позиционной с вертикальной осью мм
Высота устанавливаемого резца в 12-ти позиционной головке револьверной мм
Диаметр отверстия в 12-ти позиционной головке револьверной под цилиндрический хвостовик державки мм
Наибольшее перемещение бабки шпиндельной правой (по оси W) мм
Наибольшее продольное перемещение левого суппорта (по оси Z) мм
Наибольшее поперечное перемещение левого суппорта (по оси Х) мм
Наибольшее поперечное перемещение правого суппорта (по оси U) мм
Наибольшее вертикальное перемещение головки револьверной (по оси Y) мм
Дискретность задания перемещения по осям Х U Z Y W мкм
Пределы частот вращения шпинделей бабки шпиндельной левой и бабки шпиндельной правой обмин
Наибольшая частота вращения инструментального шпинделя 12-ти позиционной головки револьверной обмин
Наибольшая рабочая подача по осям Х U Z Y W мммин
Скорость быстрых перемещений по осям Х U Z Y W мммин
Наибольший крутящий момент на шпинделе бабки шпиндельной левой кНм
Наибольший крутящий момент на шпинделе бабки шпиндельной правой кНм
Наибольший крутящий момент привода 12-ти позиционной головки револьверной кНм
Cуммарная мощность электродвигателей кВт
Габаритные размеры станка (вместе с отдельно расположенными агрегатами и электрооборудованием) мм:
Масса станка (вместе с отдельно расположенными агрегатами и электрооборудованием) кг
Зубофрезерный полуавтомат с ЧПУ 53А50МФ6
предназначен для обработки цилиндрических прямозубых и червячных колес в условиях мелкосерийного и серийного производств.
Станок с основными технологическими возможностями базового станка мод.53А50 дополнительно оснащается следующими функциями:
Оснащен 6-ти координатным устройством ЧПУ фирмы Сименс в комплекте с 6-ю приводами подач;
Расширенный диапазон регулирования приводов главного движения и подач;
Герметизация зоны резания;
Повышенные средства безопасности работы на станке;
Оптимальная цена и экономичность эксплуатации.
Максимальный диаметр нарезаемых колес мм
Максимальный модуль нарезаемых зубьев мм
Максимальный угол наклона зубьев нарезаемых колес град
Расстояние между осями стола и фрезы мм
Максимальные размеры установленной червячной фрезы мм:
Максимальное вертикальное перемещение суппорта мм
Максимальное осевое перемещение фрезы мм
Частота вращения фрезерного шпинделя обмин
Дискретность задания перемещения по линейным осям мм:
Дискретность задания перемещения по угловым осям град:
Габаритные размеры станка мм:
Дополнительная комплектация
Гидрозажим ползушки суппорта.
Гидрозажим каретки суппорта.
Комплект технологической оснастки.
Приспособления для ремонта и обслуживания станка.
Вертикальный зубодолбежный станок с ЧПУ ВС-123ВФ3
Заготовка закрепляется в приспособлении на столе станка.
Станок имеет ряд преимуществ:
- трехкомпонентная система ЧПУ "S
- бесступенчатая регулировка частоты двойных ходов и круговой подачи; - современные провода и управление Сименс;
- пульт управления с визуализацией режимов и параметров обработки;
- точность позиционирования межцентрового рассстояния +- 3 мкм;
- точность позиционирования оборота заготовки +- 7";
- способы подачи на врезения: подача в обкатом и без обката;
- непрерывная или регрессивная радиальная подача;
- удобное рабочее пространство;
- система контроля за всеми фильтрами гидравлики смазки.
Наибольший диаметр обрабатываемых зубчатых колес мм
Наибольший модуль обрабатываемых зубчатых колес мм не менее
Наибольшая высота венца обрабатывемых колес мм
Наибольший номинальный делительный диаметр долбяка мм
Диаметр циллиндрической шейки для долбяка мм
Диаметр рабочей поверхности стола (фланца шпинделя изделия) мм
Рассстояние между осями стола и инструмента мм
Расстояние между торцами стола и шпинделя инструмента мм
Наибольшая длина регулировочного перемещения шпинделя инструмента (салазок суппорта) мм
Частота двойных ходов шпинделя инструмента в минуту (дв.ходмин)
Диапазон круговых подач мммин бесступенчато
Диапазон радиальных подач мммин бесступенчато
Количество одновременно управляемых координат (ХВ)
Дискретность координаты Х мм
Дискретность координаты В угл.сек
Мощность главного привода кВт (двухскоростной двигатель)
Суммарная максимальная мощность приводов кВт
Габариты (с отдельно расположенными узлами и электрическим оборудованием) мм
Вес (с отдельно расположенными узлами и электрическим оборудованием) кг
Точность обработки зубчатых колес по DIN 3962
Возможные исполнения станка:
- с другим напряжением и частотой тока;
- экспортное и тропическое;
- с настройкой на обработку отдельной детали и способностью переналадки;
- с дополнительной стойкой для обработки вал-шестерен;
- с механизмом для долбления реек.
В комплект поставки входит комплект сменных зубчатых колес для регулировки гитары деления (обкат). Сменные и запасные части принадлежности и вспомогательный инструмент а также гидроциллиндр для зажима изделия.
Зубо- кромкозакругляющий снимающий заусенцы станок
* для снятия заусенцев зубо- кромкозакругляющий
* 3 шпинделя * Механическое делительное устройство
* Hydraulic operated bed-slide* Гидравлический зажим заготовки
* Центральная смазка * Кожух
Технические характеристики :
Макс диаметр заготовки 400 мм
макс модуль - фрезерование 6
- снятие заусенцев 12
минмакс число зубьев (в зависимости от делит диска ) 7 - 100
макс длина хода фрезерной бабки 120 мм
макс поворот фрезерной бабки +- 30°
Max stroke of positioning slide - mechanically400 мм
- hydraulically100 мм
макс диаметр инструмента 25 мм
частота вращения шпинделя 1400 - 6000 обмин
число ходов (acc. to indexing and stroke length)200 в мин
напряжение 500V 50Hz
двигатели привода шпинделя каждый 22 kW
общая требуемая мощность 10 kVA
масса прибл. 3000 кг
требуемая площадь Д x Ш x В прибл. 2500 x 2300 x 2250 мм
Станок координатно-шлифовальный КШ-320
Координатно-шлифовальный станок мод. КШ-320 с программным управлением предназначен для шлифования цилиндрических конических плоских винтовых поверхностей для координатного шлифования отверстий контурного и объемного шлифования обеспечиваемого движениями по линейным и круговым координатам с использованием линейной круговой винтовой и сплайновой интерполяций.
КШ-320 может поставляться в различных исполнениях (опции):
пятикоординатное исполнение с тремя линейными перемещениями (по
координатам X Y Z) и горизонтальным стационарным столом (базовый
шестикоординатное исполнение оснащенное поворотным столом с вращательным движением В';
шестикоординатное исполнение оснащенное поворотным столом с вращательным движением A' и задней бабкой установленными на горизонтальный стационарный стол (см. рис.);
семикоординатное исполнение оснащенное двухкоординатным столом с вращательными движениями B' и E'
В шести и семикоординатных исполнениях возможна обработка деталей имеющих сложную геометрическую форму (лопатки ГТД прессформы штампы цилиндрические удлиненные нежесткие детали требующие наличия заднего центра и т.д.).
Применение роликовых линейных направляющих качения обеспечивает высокую жесткость механической системы точность перемещения и низкое сопротивление при движении.
Привод главного шпинделя позволяет осуществлять планетарное движение с широким диапазоном регулирования частоты вращения а также работать в режиме “ось С”.
Поворотные столы могут поставляться с приводами подач выполненными как с применением высокооборотных электродвигателей и безлюфтовых шестеренчатых редукторов так и с мощными бескорпусными низкооборотными электродвигателями фирмы ETEL обеспечивающими высокие крутящий момент и частоту вращения
Современная система цифрового программного управления в комплекте с цифровыми приводами не требующими технического обслуживания обеспечивает отличные динамические характеристики станка высокую точность обработки и большую надежность. Наличие выносного оперативного пульта с электронным маховичком позволяет пользователю выбрать наиболее подходящий режим управления станком быстро производить его наладку.
Наименование параметров
Размеры базовой поверхности стационарного стола мм
Диаметр планшайбы поворотного стола мм
однокоординатного (координата А')
однокоординатного (координата В')
Наибольший диаметр шлифуемого отверстия мм
Наибольшие перемещения по координатам:
B'E' ° - двухкоординатный стол
A'B' ° - однокоординатные столы
Скорость быстрых перемещений по координатам:
Пределы рабочих подач по координатам:
Дискретность задания перемещений по координатам:
Шаг подачи электронным маховичком по координатам:
Точность позиционирования координатных перемещений:
Пределы частот вращения главного (планетарного) шпинделя (S1) обмин
Пределы частот вращения в комплекте сменных шлифовальных
шпинделей (S2) обмин
Зубошлифовальный станок 5Д833
Зубошлифовальный станок предназначен для шлифования цилиндрических прямозубых и косозубых колес в серийном и крупносерийном производстве. По сравнению с другими способами шлифования (профильным кругом с единичным делением дисковыми и тарельчатыми кругами методом обкатки с единичным делением и т.д.) метод непрерывной обкатки позволяет в 4-5 раз повысить производительность труда. На станке производится правка одно- и двухзаходных червячных кругов одно - и многониточными накатниками и алмазными резцами.
Технические характеристики
Диаметр установленной заготовки мм
Модуль обрабатываемой заготовки мм:
- наибольший при 2-заходном круге
- наибольший при 1-заходном круге
Максимальная ширина прямозубого венца обрабатываемой заготовки мм
Максимальный угол наклона зубьев обрабатываемой заготовки град.
Максимальный диаметр шлифовального круга мм
Число зубьев обрабатываемого изделия
Максимальный ход суппорта мм
Расстояние между центрами суппорта мм
Максимальное перемещение шлифовальной бабки мм
Вертикальная подача суппорта мммин:
- при ускоренном ходе
Автоматическая радиальная подача шлифовальной бабки за один ход суппорта мм
Частота вращения шлифовального круга обмин:
- при шлифовании (частоте тока 50 Гц)
Максимальное ручное перемещение стойки вдоль оси шлифовального круга мм
Диаметр отверстия цанги мм
Габаритные размеры станка без приставного оборудования мм:
Масса станка без отдельно расположенных агрегатов кг
Дополнительная комплектация
Накатанные червячные шлифовальные круги М=1; 3; 35; 4; 45; 5; 55; 6
Резцы алмазные для правки червячных шлифовальных кругов М=05-10; 10-25; 25-50; 55-80
Приспособление для правки червячного круга алмазными роликами
Тех Маш..doc
Построение размерных схем
Перед построением размерной схемы рисуем преобразованный чертеж детали. Линейная и диаметральная размерные схемы построены по данным чертежа детали операционных эскизов и маршрутной технологии действующего технологического процесса.
Определение замыкающих звеньев
При расчете размерной цепи решается обратная задача то есть по известным значениям номинальных размеров допусков и предельных отклонений составляющих звеньев определяем номинальные размеры предельные отклонения и поля рассеяния замыкающих звеньев.
Если размерная цепь содержит до четырех звеньев то расчет ведем по методу максимума-минимума а если пять и больше звеньев то расчет ведем вероятностным методом.
Три чертежных размера не выполняются в процессе обработки и остаются в роли замыкающих звеньев.
Расчет замыкающих звеньев - чертежных размеров и анализ результатов:
) [58_108]= -(108+146)+(36+146)-(36+58)=
Рисунок 1: Результаты расчета звена [58_108].
) [18_168]=+(148+168)+(38+148)+(18+38)=
Рисунок 2: Результаты расчета звена [18_168].
) [108_148]=+(37+148)-(37+147)+(36+147)-(36+146)+(108+146) =
W[108_148]=+(-025)-(-025)+(-05)-(+05)+(-35)=-45
во=W[108_148]+W[108_148]2= -45+1272=185
но= W[108_148]-W[108 148]2= -45-1272= -1085
Рисунок 3: Результаты расчета звена [108_148].
Расчет замыкающих звеньев-припусков и их анализ:
) [18_17]= -(17+37)-(37+148)+(38+148)+(18+38)=
Припуск недостаточный(-02)
) [48_47]= +(37+47)-(37+148)+(38+148)-(38+48)=
Припуск может быть избыточным (025) и недостаточным (-105)
) [178_177]=-(177+148)+(38+148)-(38+178)=
Припуск недостаточный (0)
) [38_37]=-(37+148)+(38+148)=
Припуск недостаточный (-05)
) [118_117]=-(117+138)+(118+138)=
Припуск недостаточный (-0925)
) [168_167]=+(147+167)+(37+147)-(37+148)-(148+168)=
Припуск может быть избыточным (2) и недостаточным (02)
) [128_127]=-(127+147)+(37+147)-(37+148)+(128+148)=
Припуск может быть избыточным (125) и недостаточным (-025)
) [177_176]=+(37+176)-(37+148)+(177+148)=
Припуск избыточный (35)
) [148_147]=+(37+147)-(37+148)=
Припуск избыточный (105)
) [176_175]=-(175+147)+(37+147)-(37+176)=
) [37_36]=-(36+147)+(37+147)=
Припуск недостаточный (-2)
)[167_166]=+(36+166)-(36+147)-(147+167)=
Припуск избыточный (7)
) [147_146]=+(36+146)-(36+147)=
Припуск избыточный (1)
)[138_137]=-(137+167)+(147+167)+(37+147)-(37+148)-
(148+168)+(138+168) =
W(138_137)=-(025)+(025)+(-025)-(-025)-(+015)+(+025)=01
Припуск избыточный (039)
) [17_16]=-(16+166)+(36+166)-(36+147)+(37+147)+(17+37)=
=-108+1035-77+72+45= -5
W(17_16)= -(+05)+(+05)-(-05)+(-025)+0=025
Припуск избыточный (086).
Анализ обеспечения точности детали
В результате расчетов можно сделать вывод что припуски либо избыточные - это приводит к перерасходу материала либо недостаточные что не отвечает требованиям чистоты поверхностей и точности размера а это ведет к браку.
Анализ эффективности применяемого
инструмента оснастки и оборудования
Анализ применяемого инструмента
При изготовлении детали используется инструмент с напайными пластинами (резцы) что не выгодно экономически т.к. при износе пластины державку больше нельзя использовать. Так же при обработке используется специальный инструмент который изготавливается специально для данной детали. Это приводит к дополнительным затратам что сказывается на увеличении себестоимости детали.
Анализ применяемой оснастки
Обработка детали производится на различном оборудовании за одним станком закреплена конкретная операция. Это приводит к необходимости применения дополнительных приспособлений для закрепления заготовок. Приспособления используются только для конкретной детали на одной операции то есть недостаточно универсальны. Приспособления не автоматизированы что увеличивает время на установку и закрепление детали. Всё это так же увеличивает затраты и время на изготовление детали.
Анализ применяемого оборудования
В процессе токарной обработки деталь обрабатывается на двух станках заготовка часто переустанавливается со станка на станок из-за недостаточной концентрации технологических переходов что приводит к возникновению относительно больших погрешностей установки и базирования. Это сказывается на качестве изготовления детали увеличивает время на обработку возникает необходимость промежуточного контроля выполнения размеров на операции что так же приводит к увеличению времени обработки а соответственно и к повышению затрат на изготовление детали.
Анализ маршрутной технологии
Имеет место несовпадение номеров операций при обработке резанием по технологии бюро ЧПУ с технологическим процессом механической обработки.
На всех операциях указанных в маршрутных картах правильно дана адресная информация: номер цеха участка а также правильно указаны наименования операций и технологического оборудования со всеми приспособлениями и инструментами.
Единица нормирования указана только на транспортные операции. На всех операциях не указаны коды профессии разряд рабочего.
Ни на одной операции за исключением плоскошлифовальной и зубошлифовальной не указано штучное время.
Анализ операционных эскизов
В документации на технологический процесс имеются операционные эскизы на все операции.
Операционные эскизы к технологическому процессу обработки резанием по технологии бюро ЧПУ:
Отсутствуют предельные отклонения у номинальных размеров фасок номинальный размер первой обрабатываемой поверхности проставлен не от базы не хватает шероховатости обрабатываемых поверхностей. Комплект баз: двойная опорная отнимающая две степени свободы и установочная отнимающая три степени свободы.
Не указаны предельные отклонения у номинальных размеров фасок номинальный размер первой обрабатываемой поверхности проставлен не от базы нет шероховатости обрабатываемых поверхностей. Комплект баз: двойная опорная отнимающая две степени свободы и установочная отнимающая три степени свободы.
Отсутствуют предельные отклонения у номинальных размеров фасок номинальный размер первой обрабатываемой поверхности проставлен не от базы недостаточное количество проставленных значений шероховатости. Комплект баз: двойная опорная отнимающая две степени свободы и установочная отнимающая три степени свободы.
Не указаны предельные отклонения у номинальных размеров фасок номинальный размер первой обрабатываемой поверхности проставлен не от базы нет шероховатости некоторых обрабатываемых поверхностей. Комплект баз: двойная опорная отнимающая две степени свободы и установочная отнимающая три степени свободы.
Операционные эскизы к технологическому процессу механической обработки:
Не указан диаметр обрабатываемой поверхности и ее шероховатость а так же отсутствует погрешность между обрабатываемыми поверхностями и погрешность между установочной базой и обрабатываемыми поверхностями.
Диаметр обрабатываемой поверхности указан как справочный нет значения общей шероховатости отсутствует погрешность между установочной базой и обрабатываемыми поверхностями.
Не указан диаметр обрабатываемой поверхности с предельными отклонениями нет значения общей шероховатости проставлен диаметр без значения размера.
Номинальный размер первой обрабатываемой поверхности проставлен не от базы нет шероховатости обрабатываемого торца и допуска цилиндричности на отверстие. Комплект баз: двойная опорная отнимающая две степени свободы и установочная отнимающая три степени свободы.
Не указан диаметр обрабатываемой поверхности с предельными отклонениями.
По остальным операционным эскизам замечаний нет.
Анализ операционных карт
Наименования переходов заполнены правильно.
Обозначения приспособлений режущего и вспомогательного инструмента а так же средств измерения правильное и полное.
Используемые металлорежущие станки соответствуют содержанию операций и типу производства.
Информация о режимах резания в картах соответствует данным методам обработки.
Отсутствуют нормы штучного времени на некоторых операциях.
Анализ карт технического контроля
Наименования коды и обозначения средств технического контроля указаны правильно и полно.
В картах технического контроля под номерами 030 не указано ни одного времени необходимого для выполнения контрольного перехода а так же не указан процент контроля для измерения допуска торцового биения. На эскизах к картам 059 и 085 проставлены не все контролируемые размеры. Отсутствуют карты технического контроля для некоторых операций.
Выводы и предложения из анализа действующего
технологического процесса
В действующем технологическом процессе рассчитанном на массовое производство невозможно обеспечить сто процентное изготовление годных деталей так как значения полей рассеяния замыкающих звеньев больше значений допусков чертежных размеров и выходят за пределы допусков припуски либо избыточные либо недостаточные по сравнению с минимально необходимыми значениями. Для того чтобы избавиться от недостатков необходимо либо ужесточить операционные допуски составляющих звеньев в пределах экономической или статистической точности применяемого оборудования либо ввести операции на которых непосредственно выполняется данный чертежный размер либо уменьшить число составляющих звеньев в размерной цепи путем смены технологических баз в схемах наладки.
При изготовлении детали следует использовать современное оборудование с ЧПУ которое позволяет производить обработку на больших режимах резания и с высокой степенью точности. Использовать как можно меньше приспособлений которые в свою очередь должны быть универсальными и автоматизированными чтобы можно было использовать для других деталей. Автоматизировать зажим заготовки тем самым уменьшить время на установку закрепление и снятие ее. Использовать по возможности стандартный инструмент со сменными многогранными пластинами из твердого сплава что выгодно при серийном производстве. Составить техпроцесс так чтобы концентрация технологических переходов была максимальной и деталь обрабатывалась за меньшее количество операций что повысит производительность и качество изготовления а соответственно уменьшит затраты на производство.
Разработка проектного технологического процесса
Выбор исходной заготовки
Методом производства выбираем штамповку. Заготовкой служит поковка из легированной стали 25ХГТ (допускается сталь 18ХГТ). По сравнению с ковкой штамповка имеет ряд преимуществ: заготовка без напусков допуски на размеры в несколько раз меньше а следовательно уменьшается расход материала производительность выше но при всем этом выпускаемая партия заготовок должна быть достаточно большая так как у этого метода(штамповка) стоимость выше. Легирующие элементы: хром марганец и титан придают стали высокую поверхностную твердость и износоустойчивость. Эту сталь применяют при изготовлении деталей работающих при больших скоростях средних и высоких давлениях при наличии ударных нагрузок : валы зубчатые колеса червяки кулачковые муфты и втулки.
На заводе имеются все необходимые цеха и оборудование для производства данных заготовок а предполагаемые объемы производства оправдывают выбор этого метода производства.
Обоснование и разработка проектного технологического
На первом этапе мы заменяем старое универсальное оборудование на следующие станки:
Многофункциональный токарный обрабатывающий центр 1727Ф6
Предназначен для токарной обработки деталей (тел вращения) с выполнением фрезерных зубообрабатывающих сверлильно-расточных операций.
Станок 1727Ф6 (многофункциональные токарные обрабатывающие центры) обеспечивает последовательную двухстороннюю обработку с автоматической передачей детали из патрона в патрон двух шпиндельных бабок.
Базовый станок оснащен 2-мя револьверными головками.
Многофункциональность станка высокие точность (некруглость до 2 мкм) и скорость обработки позволяют использовать его для изготовления высокоточных и сложных деталей на предприятиях различных отраслей промышленности с применением современного инструмента.
Таблица 1: Технические характеристики многофункционального
токарного обрабатывающего центра 1727Ф6
Предельные размеры устанавливаемых поверхностей не менее мм:
наибольший диаметр над станиной
диаметр в гидропатроне левом
диаметр в гидропатроне правом
Предельные размеры обрабатываемых поверхностей не менее мм:
наибольший диаметр над суппортом
наибольшая длина (патронное исполнение)
Высота устанавливаемого резца в головке автоматической 4х позиционной с вертикальной осью мм
Высота устанавливаемого резца в 12-ти позиционной головке револьверной мм
Диаметр отверстия в 12-ти позиционной головке револьверной под цилиндрический хвостовик державки мм
Наибольшее перемещение бабки шпиндельной правой (по оси W) мм
Наибольшее продольное перемещение левого суппорта (по оси Z) мм
Наибольшее поперечное перемещение левого суппорта (по оси Х) мм
Наибольшее поперечное перемещение правого суппорта (по оси U) мм
Наибольшее вертикальное перемещение головки револьверной (по оси Y) мм
Дискретность задания перемещения по осям Х U Z Y W мкм
Пределы частот вращения шпинделей бабки шпиндельной левой и бабки шпиндельной правой обмин
Наибольшая частота вращения инструментального шпинделя 12-ти позиционной головки револьверной обмин
Наибольшая рабочая подача по осям Х U Z Y W мммин
Скорость быстрых перемещений по осям Х U Z Y W мммин
Наибольший крутящий момент на шпинделе бабки шпиндельной левой кНм
Наибольший крутящий момент на шпинделе бабки шпиндельной правой кНм
Наибольший крутящий момент привода 12-ти позиционной головки револьверной кНм
Cуммарная мощность электродвигателей кВт
Габаритные размеры станка (вместе с отдельно расположенными агрегатами и электрооборудованием) мм:
Масса станка (вместе с отдельно расположенными агрегатами и электрооборудованием) кг
Зубофрезерный полуавтомат с ЧПУ 53А50МФ6
предназначен для обработки цилиндрических прямозубых и червячных колес в условиях мелкосерийного и серийного производств.
Станок с основными технологическими возможностями базового станка мод.53А50 дополнительно оснащается следующими функциями:
Оснащен 6-ти координатным устройством ЧПУ фирмы Сименс в комплекте с 6-ю приводами подач;
Расширенный диапазон регулирования приводов главного движения и подач;
Герметизация зоны резания;
Повышенные средства безопасности работы на станке;
Таблица 2: Технические характеристики зубофрезерного полуавтомата
Максимальный диаметр нарезаемых колес мм
Максимальный модуль нарезаемых зубьев мм
Максимальный угол наклона зубьев нарезаемых колес град
Расстояние между осями стола и фрезы мм
Максимальные размеры установленной червячной фрезы мм:
Максимальное вертикальное перемещение суппорта мм
Максимальное осевое перемещение фрезы мм
Частота вращения фрезерного шпинделя обмин
Дискретность задания перемещения по линейным осям мм:
Дискретность задания перемещения по угловым осям град:
Габаритные размеры станка мм:
Дополнительная комплектация:
Гидрозажим ползушки суппорта.
Гидрозажим каретки суппорта.
Комплект технологической оснастки.
Приспособления для ремонта и обслуживания станка.
Вертикальный зубодолбежный станок с ЧПУ ВС-123ВФ3
Заготовка закрепляется в приспособлении на столе станка.
Станок имеет ряд преимуществ:
- трехкомпонентная система ЧПУ "S
- бесступенчатая регулировка частоты двойных ходов и круговой подачи; - современные провода и управление Сименс;
- пульт управления с визуализацией режимов и параметров обработки;
- точность позиционирования межцентрового рассстояния +- 3 мкм;
- точность позиционирования оборота заготовки +- 7";
- способы подачи на врезения: подача в обкатом и без обката;
- непрерывная или регрессивная радиальная подача;
- удобное рабочее пространство;
- система контроля за всеми фильтрами гидравлики смазки.
Таблица 3: Технические характеристики вертикального зубодолбежного
станка с ЧПУ ВС-123ВФ3
Наибольший диаметр обрабатываемых зубчатых колес мм
Наибольший модуль обрабатываемых зубчатых колес мм не менее
Наибольшая высота венца обрабатывемых колес мм
Наибольший номинальный делительный диаметр долбяка мм
Диаметр циллиндрической шейки для долбяка мм
Диаметр рабочей поверхности стола (фланца шпинделя изделия) мм
Рассстояние между осями стола и инструмента мм
Расстояние между торцами стола и шпинделя инструмента мм
Наибольшая длина регулировочного перемещения шпинделя инструмента (салазок суппорта) мм
Частота двойных ходов шпинделя инструмента в минуту (дв.ходмин)
Диапазон круговых подач мммин бесступенчато
Диапазон радиальных подач мммин бесступенчато
Количество одновременно управляемых координат (ХВ)
Дискретность координаты Х мм
Дискретность координаты В угл.сек
Мощность главного привода кВт (двухскоростной двигатель)
Суммарная максимальная мощность приводов кВт
Габариты (с отдельно расположенными узлами и электрическим оборудованием) мм
Вес (с отдельно расположенными узлами и электрическим оборудованием) кг
Точность обработки зубчатых колес по DIN 3962
Возможные исполнения станка:
- с другим напряжением и частотой тока;
- экспортное и тропическое;
- с настройкой на обработку отдельной детали и способностью переналадки;
- с дополнительной стойкой для обработки вал-шестерен;
- с механизмом для долбления реек.
В комплект поставки входит комплект сменных зубчатых колес для регулировки гитары деления (обкат). Сменные и запасные части принадлежности и вспомогательный инструмент а также гидроциллиндр для зажима изделия.
Зубо- кромкозакругляющий снимающий заусенцы станок
для снятия заусенцев зубо- кромкозакругляющий
шпинделя Механическое делительное устройство
Hydraulic operated bed-slideГидравлический зажим заготовки
Центральная смазка Кожух
Технические характеристики :
Макс диаметр заготовки 400 мм
Макс модуль – фрезерование ..6 - снятие заусенцев 12
минмакс число зубьев (в зависимости от делит диска ) 7-100
макс длина хода фрезерной бабки .120 мм
макс поворот фрезерной бабки . +- 30°
Max stroke of positioning slide:
-mechanically 400 мм
-hydraulically 100 мм
макс диаметр инструмента ..25 мм
частота вращения шпинделя .1400 - 6000 обмин
число ходов (acc. to indexing and stroke length) .200 в мин
напряжение 500V 50Hz
двигатели привода шпинделя каждый ..22 kW
общая требуемая мощность 10 kVA
требуемая площадь Д x Ш x В прибл. ..2500 x 2300 x 2250 мм
Станок координатно-шлифовальный КШ-320
Координатно-шлифовальный станок мод. КШ-320 с программным управлением предназначен для шлифования цилиндрических конических плоских винтовых поверхностей для координатного шлифования отверстий контурного и объемного шлифования обеспечиваемого движениями по линейным и круговым координатам с использованием линейной круговой винтовой и сплайновой интерполяций.
КШ-320 может поставляться в различных исполнениях (опции):
пятикоординатное исполнение с тремя линейными перемещениями (по координатам X Y Z) и горизонтальным стационарным столом (базовый
шестикоординатное исполнение оснащенное поворотным столом с вращательным движением В';
шестикоординатное исполнение оснащенное поворотным столом с вращательным движением A' и задней бабкой установленными на горизонтальный стационарный стол;
семикоординатное исполнение оснащенное двухкоординатным столом с вращательными движениями B' и E'.
В шести и семикоординатных исполнениях возможна обработка деталей имеющих сложную геометрическую форму (лопатки ГТД прессформы штампы цилиндрические удлиненные нежесткие детали требующие наличия заднего центра и т.д.).
Применение роликовых линейных направляющих качения обеспечивает высокую жесткость механической системы точность перемещения и низкое сопротивление при движении.
Привод главного шпинделя позволяет осуществлять планетарное движение с широким диапазоном регулирования частоты вращения
а также работать в режиме “ось С”.
Поворотные столы могут поставляться с приводами подач выполненными как с применением высокооборотных электродвигателей и безлюфтовых шестеренчатых редукторов так и с мощными бескорпусными низкооборотными электродвигателями фирмы ETEL обеспечивающими высокие крутящий момент и частоту вращения
Современная система цифрового программного управления в комплекте с цифровыми приводами не требующими технического обслуживания обеспечивает отличные динамические характеристики станка высокую точность обработки и большую надежность. Наличие выносного оперативного пульта с электронным маховичком позволяет пользователю выбрать наиболее подходящий режим управления станком быстро производить его наладку.
Таблица 4: Технические характеристики на координатно-
шлифовальный станок КШ-320
Наименование параметров
Размеры базовой поверхности стационарного стола мм
Диаметр планшайбы поворотного стола мм
однокоординатного (координата А')
однокоординатного (координата В')
Наибольший диаметр шлифуемого отверстия мм
Наибольшие перемещения по координатам:
B'E' ° - двухкоординатный стол
A'B' ° - однокоординатные столы
Скорость быстрых перемещений по координатам:
Пределы рабочих подач по координатам:
Дискретность задания перемещений по координатам:
Шаг подачи электронным маховичком по координатам:
Точность позиционирования координатных перемещений:
Пределы частот вращения главного (планетарного) шпинделя (S1) обмин
Пределы частот вращения в комплекте сменных шлифовальных
шпинделей (S2) обмин
Зубошлифовальный станок 5Д833
Зубошлифовальный станок предназначен для шлифования цилиндрических прямозубых и косозубых колес в серийном и крупносерийном производстве. По сравнению с другими способами шлифования (профильным кругом с единичным делением дисковыми и тарельчатыми кругами методом обкатки с единичным делением и т.д.) метод непрерывной обкатки позволяет в 4-5 раз повысить производительность труда. На станке производится правка одно- и двухзаходных червячных кругов одно - и многониточными накатниками и алмазными резцами.
Таблица 5: Технические характеристики на зубошлифовальный
Технические характеристики
Диаметр установленной заготовки мм
Модуль обрабатываемой заготовки мм:
- наибольший при 2-заходном круге
- наибольший при 1-заходном круге
Максимальная ширина прямозубого венца обрабатываемой заготовки мм
Максимальный угол наклона зубьев обрабатываемой заготовки град.
Максимальный диаметр шлифовального круга мм
Число зубьев обрабатываемого изделия
Максимальный ход суппорта мм
Расстояние между центрами суппорта мм
Вертикальная подача суппорта мммин:
- при ускоренном ходе
Автоматическая радиальная подача шлифовальной бабки за один ход суппорта мм
Частота вращения шлифовального круга обмин:
- при шлифовании (частоте тока 50 Гц)
Максимальное ручное перемещение стойки вдоль оси шлифовального круга мм
Диаметр отверстия цанги мм
Габаритные размеры станка без приставного оборудования мм:
Масса станка без отдельно расположенных агрегатов кг
Дополнительная комплектация
Накатанные червячные шлифовальные круги М=1; 3; 35; 4; 45; 5; 55; 6
Резцы алмазные для правки червячных шлифовальных кругов М=05-10; 10-25; 25-50; 55-80
Приспособление для правки червячного круга алмазными роликами
На данных станках мы сможем полностью изготовить зубчатое колесо что увеличивает производительность и уменьшает погрешности связанные с переустановкой так как обработка производится за меньшее количество операций.
Следующим шагом будет замена токарного инструмента с напайными пластинами на стандартный с использованием многогранных пластин. Следствием чего будет снижение затрат на инструмент и повысит его стойкость.
Снижаем количество токарных операций с четырех до двух за счет максимальной концентрации технологических переходов и уменьшения числа установовчто снизит погрешность при базировании и время на переустановку заготовки.
Маршрутная технология проектного технологического
Маршрутная технология проектного технологического процесса представлена в виде операционных эскизов изображенных на рисунках 45678910.
Рисунок 4: операция 005 токарная.
Поверхность 1 обрабатывается за три технологических перехода:
переход-припуск 3370 мм
переход -припуск 0255 мм
переход -припуск 008 мм
Поверхность 2 обрабатывается за три технологических перехода:
переход -припуск 5735 мм
переход -припуск 0440 мм
переход -припуск 0260 мм
Поверхность 3 обрабатывается за три технологических перехода:
переход -припуск 5620 мм
переход -припуск 0320 мм
переход -припуск 0210 мм
Поверхность 4 обрабатывается за три технологических перехода:
переход -припуск 3350 мм
переход -припуск 0550 мм
переход -припуск 0280 мм
Поверхность 5 обрабатывается за три технологических перехода:
переход -припуск 3250 мм
переход -припуск 0240 мм
Поверхности 678910 обрабатываются за один технологический переход
Рисунок 5: операция 010 токарная.
переход -припуск 5980 мм
переход -припуск 1240 мм
переход -припуск 0275 мм
переход -припуск 0189 мм
переход -припуск 3700 мм
переход -припуск 0693 мм
переход -припуск 0348 мм
Поверхности 356 обрабатываются за один технологический переход
Рисунок 6: операция 015 зубофрезерная.
Поверхность 2 обрабатывается за два технологических перехода:
переход -W=51.550-1.100 мм
переход -W=49.500-0.435 мм
Рисунок 7: операция 020 зубодолбежная.
Поверхность 7 –W=168 +0.70 мм
Рисунок 8: операция 025 зубозакругляющая.
Рисунок 9: операция 040 шлифовальная.
Поверхность 17 –припуск на обработку 0235 мм
Поверхность 10 –припуск на обработку 0315 мм
Рисунок 10: операция 045 зубошлифовальная.
Поверхность 2 –припуск на обработку 0376 мм
Размерный анализ проектного технологического процесса
Размерный анализ линейной и диаметральной цепей проектного технологического процесса приведен в чертежах.
При размерном анализе были посчитаны припуски на обработку замыкающие звенья и размеры не выполняемые непосредственно при обработке детали. В результате получили что все требования чертежа на деталь выполняются.
Расчет режимов резания и норм времени
Расчет режимов резания необходимо производить для нормирования объема работ. Производить расчеты будем по справочнику: общемашиностроительные нормативы режимов резания. Определение режимов резания сводится в основном к нахождению оптимальных глубин резания t величин подачи S стойкости T и скорости резания V при которых должна быть достигнута наибольшая производительность обработки на станке при наименьшей ее себестоимости и требуемого качества обработанной поверхности. Обычно в производственных условиях при назначении режимов резания используют нормативные таблицы. Найденную по таблицам подачу и число оборотов корректируют по станку.
Расчет режимов резания и норм времени на 005 операцию
В расчете используются номера поверхностей из линейной и диаметральной цепей проектного варианта.
Наименование детали – зубчатое колесо
Материал – сталь 18ХГТ (217 229 НВ)
Точность обработки поверхностей:
- 8- 9- 10- 11- 131416- 17-IT12
Шероховатость обработки поверхностей:
11416- 917- 813- 10-Rz10
Метод получения заготовки - штамповка(точность-IT16)
Состояние поверхности-с коркой
Припуск на обработку поверхностей:
Модель станка-1727Ф6
Частота вращения шпинделя nобмин : 5-1000
По оси координат х-1 1000
По оси координат z-1 1000
Наибольшая сила допускаемая:
Механизмом продольной подачи-
Механизмом поперечной подачи-
Мощность привода главного движения-13 кВт
Диапазон регулирования частоты вращения электродвигателя с постоянной мощностью обмин-
Базирование- в трехкулачковом патроне
Содержание операции- точить поверхности 689101113141617 по программе выдерживая размеры
Выбор стадий обработки:
Для обработки поверхностей 810131417 для увеличения периода стойкости инструмента выбираем обработку в три стадии(черновую получистовую и чистовую)
Обработку поверхностей 691116(канавки фаски) будем производить за один технологический переход.
Выбор глубины резания:
Глубины резания берем из линейной и диаметральной размерной цепи проектного варианта технологического процесса. Они равны припускам.
t=8мм 8 t=3.350мм 9 t=2.5мм 10 t=3.250мм 11 t=2.857мм
t=5620мм 14 =3.370мм 16 t=3286мм 17 t=5.735мм.
Получистовая стадия:
t=0.550мм 10 t=0550мм 13 t=04мм 14 t=0.255мм
t=0280мм 10 t=0240мм 13 t=026мм 14 t=0.095мм
На станке 1727Ф6 используют резцы с сечением державки 25X25мм. Исходя из условий обработки принимаем ромбическую форму пластины для черновой и получистовой стадий трехгранную форму пластины с углом при вершине E=60 для чистовой стадии. Материал пластин: Т5К10 черновая получистовая стадии Т30К4 чистовая стадия. Способ крепления пластин: чистовая стадия двуплечим прихватом за выемку черновая и получистовая стадии клин-прихватом.
Углы в плане:. Находим остальные геометрические параметры. Черновая и получистовая стадии : задний угол передний угол форма передней поверхности радиус скругления режущей кромки r=004 мм радиус вершины резца rв=1 мм. Чистовая стадия: задний угол передний угол форма передней поверхности радиус скругления режущей кромки r=003мм радиус вершины резца rв=1мм. Определяем нормативный период стойкости Т=30мин и толщину пластины h=64мм.
Подача для черновой стадии:
S0=SOT·Ksи·Ksp·Ksд·Ksh·Ks
где: SOT - рекомендуемое табличное значение
Поверхности 911- SOT = 130 ммоб
Поверхности 8101416 - SOT = 113 ммоб
Поверхности 61317- SOT = 098 ммоб
Ksи- поправочные коэффициенты на подачу в зависимости от инструментального материала;
Поверхности 911- Кsи=1.15 [карта52];
Поверхности 681013141617- Кsи=1.10 [карта52];
Ksp - поправочные коэффициенты на подачу в зависимости от способа крепления пластины Кsр=1.0[карта52];
Ksд - поправочные коэффициенты на подачу в зависимости от сечения державки резца Кsд=1.0 [карта52];
Ksh- поправочные коэффициенты на подачу в зависимости от прочности режущей части Ksh =
Ksn - поправочные коэффициенты на подачу в зависимости от состояния поверхности заготовки Ksn=085 [карта52];
Ksφ- поправочные коэффициенты на подачу в зависимости от геометрических параметров резца Kscp =10 [карта52];
Ksj- поправочные коэффициенты на подачу в зависимости от жесткости станка Ksj = 07 [карта52];
KSM- поправочные коэффициенты на подачу в зависимости от механических свойств обрабатываемого материала KsM=09 [карта52];
Окончательная подача черновой стадии
Поверхности 8101416:
Подача для получистовой стадии:
Для всех поверхностей
Окончательная подача получистовой стадии
Расчитанные подачи для черновой стадии проверяются по осевой Рх и радиальной Ру составляющим сил резания допустимыми прочностью механизма подач станка.
Составляющие сил резания определяются по формуле:
P=PT·Kpm·Kpφ·Kpγ·Kpλ
где: PT - табличные значения составляющих сил резания
Поверхности 911: РХт=1280 Н РУт=450 Н [карта 322];
Поверхности 8101416: РХт=2200 Н РУт=510 Н [карта 322];
Поверхности 61317: РХт=3200 Н РУт=640 Н [карта 322];
Kpm - поправочные коэффициенты на силы резания для измененных условий в зависимости от механических свойств обрабатываемого материалаКрм=10[карта 332];
Кpφ - поправочные коэффициенты на силы резания для измененных условий в зависимости от главного угла в плане КРφх=07 КРφу= 2 [карта 332];
Kpγ - поправочные коэффициенты на силы резания для измененных условий в зависимости от главного переднего угла Кpх=15Кpу=130 [карта 332];
Kpλ - поправочные коэффициенты на силы резания для измененных условий в зависимости от угла наклона кромки КРλх =09 КРλу=110 [карта 332];
Окончательно составляющие сил резания:
Поверхности 911 -РХт=1280·1·07·150·09=1209 Н
РУт=450·1·2·130·110=1287 Н
Поверхности 8101416- РХт=2200·1·07·150·09=2079 Н
Поверхности 61317- РХт=3200·1·07·150·09=3024 Н
РУт=640·1·2·130·110=1830 Н
Рассчитанные значения составляющих сил резания меньше чем допускается механизмом подач станка.
Выбираем рекомендуемые значения подач чистовой стадии [карта 62];
Определяем поправочные коэффициенты на подачу чистовой стадии обработки для измененных условий в зависимости от механических свойств обрабатываемого материала [карта 82];
KSM- поправочные коэффициенты на подачу в зависимости от механических свойств обрабатываемого материала KsM=1 [карта82];
KSу- поправочные коэффициенты на подачу в зависимости от схемы установки заготовки Ksу=08 [карта82];
KSr- поправочные коэффициенты на подачу в зависимости от радиуса при вершине Ksr=08 [карта82];
KSк- поправочные коэффициенты на подачу в зависимости от квалитета обрабатываемой деталиKsк=1 [карта82];
Окончательная подача чистовой стадии
Выбор скорости резания:
Скорость резания при черновой стадии обработки определяют:
v = vt ·Кvу·Кvc·Kvо·KVj·KvM·Kvφ·KvT·Куж;
где: vt рекомендуемые значения скорости резания для черновой стадии обработки[карта21 2];
Поверхности 911 vт=111 ммин;
Поверхности 8101416 vт=105 ммин;
Поверхности 61317 vт=88 ммин;
Кvу - поправочные коэффициенты в зависимости от инструментального материала KvH = 085 [карта 212];
Кvc- поправочные коэффициенты в зависимости от группы обрабатываемости материала Kvc =08 [карта 212];
Kv о - поправочные коэффициенты в зависимости от вида обработки Kv0=10 [карта 212];
KVj- поправочные коэффициенты в зависимости от жесткости станка KVj=1 [карта 21 2];
KvM- поправочные коэффициенты в зависимости от механических свойств обрабатываемого материала KvM = 10 [карта 212];
Kvφ - поправочные коэффициенты в зависимости от геометрических параметров резца для поверхностей Kvφ = 10 [карта 212];
KvT - поправочные коэффициенты в зависимости от периода стойкости режущей части KvT =10 [карта 212];
Kvж- поправочные коэффициенты в зависимости от наличия охлаждения
КУж=10 [карта 21 2];
Окончательно скорость резания при черновой стадии обработки определяем:
v = 111·085·08 = 76 ммин
v=105·085·08 = 71 ммин
v = 88·085·08 = 60 ммин
Скорость резания для получистовой стадии обработки :
Рекомендуемое значение скорости резания для получистовой стадии обработки [карта212];
Поправочные коэффициенты для получистовой стадии обработки равны поправочным коэффициентам для черновой стадии.
Окончательно скорость резания для получистовой стадии обработки определяем:
v = 185·085·08 = 126 ммин.
Скорость резания для чистовой стадии обработки:
Рекомендуемое значение скорости резания для чистовой стадии обработки [карта212]
Поправочные коэффициенты для получистовой стадии обработки равны поправочным коэффициентам для черновой стадии за исключением KvH=080 и Kvφ = 115 [карта 212];
Окончательно скорость резания для чистовой стадии обработки определяем:
v = 348·080·115=256 ммин.
Частота вращения шпинделя:
где: D – диаметр обрабатываемой поверхности;
Для черновой стадии:
Принимаем частоту вращения которая имеется на станке nф =140 обмин.
Фактическая скорость резания будет Vф=769 ммин.
Принимаем частоту вращения которая имеется на станке nф=140 обмин.
Фактическая скорость резания будет Vф=747ммин.
Принимаем частоту вращения которая имеется на станке nф =180 обмин.
Фактическая скорость резания будет Vф=694 ммин.
Фактическая скорость резания будет Vф=747 ммин.
Принимаем частоту вращения которая имеется на станке nф =100 обмин.
Фактическая скорость резания будет Vф=562 ммин.
Принимаем частоту вращения которая имеется на станке nф =71 обмин.
Фактическая скорость резания будет Vф=464 ммин.
Принимаем частоту вращения которая имеется на станке nф =100обмин.
Фактическая скорость резания будет Vф=435 ммин.
Фактическая скорость резания будет Vф=1176 ммин.
Принимаем частоту вращения которая имеется на станке nф =280 обмин.
Фактическая скорость резания будет Vф=1079 ммин.
Принимаем частоту вращения которая имеется на станке nф =200 обмин.
Фактическая скорость резания будет Vф=1124 ммин.
Фактическая скорость резания будет Vф=1067 ммин.
Принимаем частоту вращения которая имеется на станке nф =355 обмин.
Фактическая скорость резания будет Vф=2319 ммин.
Принимаем частоту вращения которая имеется на станке nф =630 обмин.
Фактическая скорость резания будет Vф=2427 ммин.
Фактическая скорость резания будет Vф=1995 ммин.
Принимаем частоту вращения которая имеется на станке nф =500 обмин.
Фактическая скорость резания будет Vф=2669 ммин.
Корректируем подачу для чистовой стадии обработки в зависимости от шероховатости обработанной поверхности [карта252]:
Поверхность 17- Ra =10мкм
Поверхность 14- Ra =20мкм
Поверхность 13- Ra =5мкм
Поверхность 10- Ra =25мкм
Поверхность 8- Ra = 5мкм
Поправочные коэффициенты на подачу в зависимости от шероховатости обработанной поверхности для измененных условий [карта262]:
KSM- поправочные коэффициенты на подачу в зависимости от механических свойств обрабатываемого материала KsM=1;
Ksи- - поправочные коэффициенты на подачу в зависимости от инструментального материала Ksи=1;
Ksо- - поправочные коэффициенты на подачу в зависимости от вида обработки Ksо=1;
Ksж- - поправочные коэффициенты на подачу в зависимости от наличия охлаждения Ksж=1;
Окончательно определяем максимально допустимую подачу для чистовой стадии обработки по шероховатости обработанной поверхности :
Проверка выбранных режимов по мощности привода главного
Для черновой стадии обработки табличную мощность резания определяем аналогично табличной скорости резания [карта212].
Поверхности 8101416
Табличную мощность резания корректируем по формуле:
где: Kn – поправочный коэффициент Kn=10;
Для получистовой стадии обработки табличную мощность резания также определяем аналогично табличной скорости резания [карта212].
Для всех поверхностей :
Корректируем табличную мощность резания :
Определение минутной подачи:
Минутную подачу рассчитывают по формуле:
Черновая стадия обработки:
SМ= 140·091= 1274 мммин.
SМ= 180·076= 1368 мммин.
SМ= 140·076= 1064 мммин.
SМ= 100·076= 76 мммин.
SМ= 71·066= 467 мммин.
SМ= 100·066= 66 мммин.
Получистовая стадия обработки:
SМ= 180·047= 846 мммин.
SМ= 280·047= 1316 мммин.
SМ= 200·047= 94 мммин.
Чистовая стадия обработки:
SМ= 355·038= 1349 мммин.
SМ= 630·038= 2394 мммин.
SМ= 355·045= 1598 мммин.
SМ= 500·030= 150 мммин.
Таблица 6: Режимы резания для 005 операции(токарная)
Определение времени цикла автоматической работы станка по программе:
Для станка 1727Ф6 на котором производится токарная обработка детали время поворота инструмента на одну позицию Тип = 2с время фиксации револьверной головки Тиф = 2с .
Время автоматической работы станка по программе определяется по формуле:
где: основное время работы станка в автоматическом режиме по программе [таблица 22]
машинно-вспомогательное время [таблица 22];
Тца = 6288+2014= 8302 мин
Определение нормы штучного времени:
Норму штучного времени определяют по формуле:
Тш = (Тца+Тв) · (1+)
где: Тца время автоматической работы станка по программе
ТВ - вспомогательное время ;
где: Твуст вспомогательное время на установку и снятие детали Твуст.=36 мин;
Твоп вспомогательное время связанное с операцией включает в себя время на включение и выключение станка проверку возврата инструмента в заданную точку после обработки установку и снятие щитка предохраняющего от разбрызгивания эмульсии [карта 142]
Твоп=015+003=018 мин
Тиз вспомогательное время на контрольные измерения Твиз =106 мин
Тогда: Тв = 36+018+106 = 484 мин
() - коэффициент учитывающий расход времени на личные надобности он равен 008; [карта 162]
Таким образом штучное время всей операции равно:
Тш = (8302+484) · (1+008) = 1419 мин.
Расчет режимов резания и нормы штучного времени на 015
операцию(зубофрезерную)
Наименование детали –зубчатое колесо
Точность наружного зацепления колеса-9
Масса детали 453 кг(по чертежу детали)
Операция зубофрезерная : фрезеровать зубья m=7д=200z=45
Шероховатость поверхностей зубьев Rz20
Выбор режущего инструмента:
Выбираем червячную фрезу m=7 д=200
Выбор режимов резания:
Режимы резания приведены в таблице 7.
Таблица 7: Режимы резания для зубофрезерной операции.
где: То - время обработки мин
где: В-высота зуба В=17мм
z-число зубьев нарезаемого колеса z=45
D-наружный диаметр нарезаемого колеса D=3307мм
V-скорость резанияV=28
S-подача S=1ммоб.дет.
где: Твуст - вспомогательное время на установку и снятие детали
Твуст.=212 мин; [карта 62]
Твоп - вспомогательное время связанное с операцией включает в себя время на включение и выключение станка проверку возврата инструмента в заданную точку после обработки[карта 142]
Твоп = 015+003=018 мин
Тш=(264+23) · (1+008)=3098 мин.
Режимы резания и норма штучного времени на 020 операцию(зубодолбежная)
Точность внутреннего зацепления колеса-9
Масса детали 451 кг(по чертежу детали)
Операция зубодолбежная : долбить зубья
Рисунок 11: Параметры внутреннего зубчатого венца.
Установка детали на стационарном столе
Для обработки внутреннего зацепления выбираем чашечный прямозубый долбяк по ГОСТ 6762-79
Расчет режимов резания:
где L-путь который проходит долбяк за всю обработку м
V-скорость движения долбяка ммин
где: Nобщ-общее число ходов долбяка
l - путь долбяка для обработки одного зуба l =0.019мм
где: N1- число ходов долбяка для обработки одного зуба
z - число зубьев обрабатываемого колеса z=36
где: m-модуль обрабатываемого колеса m=5
Sкруг- круговая подача Sкруг=01ммдв.ход
где: n- частота двойных ходов шпинделя иструмента n=300дв.ходмин.
Таким образом получим:
tв - вспомогательное время на операцию
где: tв.уст - время на комплекс приемов по установке заготовок на столе станка с выверкой ее положения tв.уст=24 мин[карта 22]
tв время на комплекс приемов связанных с обработкой и измерениями
tв пер=18 мин[карта 352]
Тш=tосн +tв=132+42=174мин
Режимы резания и норма штучного времени на 025 операцию(зубозакругляющая)
Деталь – зубчатое колесо.
Рисунок 12: Параметры зубьев после зубозакругления.
Операция зубозакругления: зубозакруглить зубья по программе
Зубозакругляющий PRAWEMA FA 400
Фреза зубозакругляющая Д25-007-11
Выбор режимов резания и норм времени:
Таблица 8: Режимы резания и норма штучного времени для
зубозакругляющей операции.
Расчет режимов резания и нормы штучного времени на 040 операцию (шлифовальная)
Деталь: Наименование детали –зубчатое колесо
Точность обработки отверстия по шестому квалитету
Масса детали 45 кг(по чертежу детали)
Операция шлифования : шлифовать отверстие(шлифование внутреннее с продольной подачей)
Шероховатость поверхности Rz10
Припуск на диаметр 2П=004мм
Выбор шлифовального круга:
Тип шлифовального круга-прямого профиля ПП
Основные размеры и характеристики:
Рисунок 13: Основные размеры шлифовального круга.
Форма шлифовального круга - 6А2С ГОСТ 16170-81
где: 6-форма корпуса
С-модификация корпуса.
Эффективная мощность рассчитывается по формуле:
где: СN-коэффициент мощности СN=036
t-глубина резания t=004 мм
Vк-скорость кругаVк=35 мс
Vз-скорость заготовкиVз=40 мс
где: В-толщина круга В=50 мм
d-диаметр шлифования d=170 мм
Штучное время определяется по формуле:
где: tоп - оперативное время основное время на операцию
где: tо- основное время на операцию
где: Lрх - длина рабочего хода Lрх=806 мм
П - припуск на обработку(один проход) П=002 мм
Sм - минутная подача Sм=2040 мммин
St-продольная подача St=0006 ммдв.ход.
где: tв.уст - время на комплекс приемов по установке заготовок в патроне с выверкой ее положения по индикатору tв.уст=24 мин[карта 22]
tв пер - время на комплекс приемов связанных с обработкой tв пер = 08 мин[карта 352]
tоп = 026+32=346 мин
tоб-общее время на обслуживание рабочего места
где: tтех - техническое время
где: Тn-время на одну правку Тn=15 мин[карта 452]
Т-период стойкости шлифовального круга Т=6 мин
tорг - время на организационное обслуживание в % от tоп
tорг=25% tоп=009 мин[карта 452]
tотл - время на отдых и личные надобности tотл=4% tоп=014 мин[карта 462]
Тогда норма штучного времени:
Тшт=346+019+014=379 мин .
Расчет режимов резания и нормы штучного времени на 045 операцию(зубошлифовальную)
Операция зубошлифовальная : шлифовать зубья m=7 д=200 z=45
Шероховатость шлифуемых поверхностей зубьев Rа=125
Зубошлифовальный 5Д833
Выбираем червячный шлифовальный круг m=7 д=200
Таблица 9: Режимы резания и нормы времени на
зубошлифовальную операцию.
Проектирование расчет и описание станочного
контрольного приспособлений и режущего инструмента
Проектирование расчет и описание работы станочного
Анализ технологической операции (Этап I)
Цель этапа – выявить ограничения накладываемые на проектируемое станочное приспособление.
Разработка эскиза обрабатываемой детали (рисунок14).
Рисунок 14: Результаты разработки эскиза детали.
Определение сведений о выполняемой операции.
Количество одновременно обрабатываемых заготовок: 1 шт.
Материал: Сталь 18ХГТ ГОСТ 4543-71.
Твердость: 229 НВ (материала).
Твердость зубьев: 54 62 HRC.
Масса детали: 45 кг.
Станок: Зубошлифовальный станок с ЧПУ 5Д833.
Режимы: t=004 мм S=1.1мм n=71 дв.хмин.
Режущий инструмент: Круг 4400*20*127 25А 40П СМ-1 7К5 35 мс
Разработка эскиза заготовки поступающей на выполняемую операцию.
На этой стадии определяются параметры заготовки поступающей на выполняемую операцию и влияющие на проектирование станочного приспособления (рисунок 15).
Рисунок 15: Результаты разработки эскиза заготовки поступающей на операцию.
Разработка упрощенного операционного эскиза.
На этой стадии проектирования определяются те параметры операционного эскиза выполнение которых зависит от конструкции станочного приспособления.
При шлифовании зубьев колеса необходимо выполнить длину общей нормали с полем допуска: 9816-0275-0415 и обеспечить допуск радиального биения зубчатого венца относительно оси отверстия Fr =0112 мм.
Принимаем что точность выполнения длины общей нормали обеспечивается методом и инструментом обработки - шлифованием и шлифовальным кругом а допуск радиального биения Т = 0112мм в значительной степени зависит от конструкции станочного приспособления так как оно определяет положение обрабатываемой поверхности заготовки относительно её базовой поверхности.
Рисунок 16: Результаты разработки упрощенного операционного эскиза.
Уточнение схемы обработки.
На этой стадии проектирования уточняются особенности выполнения операции связанные с конструкцией станочного приспособления путем разработки схемы обработки (рисунок 17).
Рисунок 17: Результаты разработки схемы обработки.
Уточнение задачи проектирования.
При проектировании станочного приспособления на операцию шлифования зубьев необходимо спроектировать разработать конструкцию станочного приспособления шпиндельного типа для обработки детали «Шестерня» на станке с ЧПУ: 5Д833 при выполнении условий установленных на предыдущих стадиях.
Разработка принципиальной схемы станочного
приспособления (Этап II)
Разработка схемы установки
На этой стадии осуществляется переход от теоретической схемы базирования к схеме расположения установочных элементов в станочном приспособлении на уровне принципиальных решений.
При заданной схеме простановки опор показывающей что базирование заготовки осуществляется по внутренней поверхности отверстия и торцу возможно две теоретические схемы базирования: (рисунок 18).
Рисунок 18: Результаты разработки вариантов схемы установки.
Рассмотренные варианты схем базирования заготовки не равнозначны.
Учитывая что заготовка в процессе обработки испытывает большие усилия в направлении установочной плоскости то примем схему установки б (цилиндрическая оправка с упором в торец) (рисунок 19).
Рисунок 19: Результаты разработки схемы установки.
Разработка схемы закрепления.
Схемой закрепления предусматривается приложение силы закрепления форма контактной поверхности – плоская силовой привод пневматический.
На этой стадии осуществляется переход от теоретической схемы устройства к схеме зажимного устройства станочного приспособления на уровне принципиальных решений (рисунок 20).
Рисунок 20: Результаты разработки схемы закрепления.
Разработка схемы дополнительного устройства.
Дополнительное устройство предназначено для осуществления вспомогательных функций в данном случая целесообразно и необходимо применить дополнительное устройство фиксирования заготовки в определенном заданном положении (рисунок 21).
Рисунок 21: Результаты разработки схемы дополнительного устройства.
Разработка схемы корпуса.
На данном этапе проектирования станочного приспособления осуществляется компоновка принципиальной схемы на основе принятых условий базирования (рисунок 22)
Рисунок 22: Результаты разработки схемы корпуса.
На данной стадии проектирования формируется принципиальная схема станочного приспособления (рисунок 23).
Рисунок 23: Результаты разработки принципиальной схемы станочного приспособления.
Определение условий закрепления заготовки в станочном
приспособлении (Этап III)
Определение теоретической силы закрепления
Определение лимитирующего силового параметра обработки
При решении этой задачи необходимо решить установить параметры обработки силы и моменты которой оказывают наибольшее неблагоприятное воздействие на заготовку вызывающие смещение или поворот.
При закреплении заготовки создаются силы W и N стремящиеся удержать её в неизменном положении. Действие этих сил в данном случае распределённое.
Принимаем допущение что их действие имеет точечный характер а в точках их приложения возникают пары сил трения удерживающих заготовку от вращения под действием сил резания (в нашем случае Ру –«пытается» повернуть заготовку вокруг оси) Pz – прижимает заготовку к установочной плоскости и не изменяет её положения; Рx – также не изменяет положения заготовки на станочном приспособлении а воздействует на цилиндрическую оправку (рисунок 24).
Рисунок 24: Результаты определения лимитирующего силового параметра.
Разработка расчетной схемы
На данной стадии проектирования осуществляется разработка расчетной схемы путем определения всех сил действующих на заготовку и принятие необходимых допущений плюс – отсутствие сил в самой опорной плоскости.
Используем допущения принятые в предыдущем пункте (рисунок 25).
Рисунок 25: Результаты разработки расчетной схемы.
Определение расчетного уравнения
Расчетного уравнения в общем виде:
Муд=МF1+ МF2=F12в+ F22а=Nfв +Wf1a но N=W
тогда: Муд =Nfв +Wf1a
Определение параметров входящих в расчетное уравнение
Из условий выполнения операции определили режимы резания:
Сила резания Рz =346 Н.
Но Py(0.3 0.4)Рz принимаем Py=03 346=1038 Н.
Коэффициенты трения материалов: f = 01; f1 =01 .
Коэффициент надежности закрепления K
Установили значения промежуточных коэффициентов:
Ko = 1.5; K1= 1; K2 = 1; K3 =1; K4 = 1; K5 = 1; K6 = 1.5
по которым вычислили значение коэффициента надежности закрепления:
K = 1.511111.5=2.25.
Размеры (указаны на рисунке 24) :
Расчет теоретической силы закрепления
Подставляя соответствующие значения параметров в расчетное уравнение получили значение силы W:
Определение параметров зажимного устройства
При решении этой задачи устанавливается связь между теоретической силой закрепления W и параметрами силового привода (рисунок 26).
Рисунок 26: Результаты разработки схемы зажима.
Уравнение силового замыкания:
- коэффициент полезного действия
S = 0.785xqж x (D2-d2) где: D- диаметр цилиндра d- диаметр штока
i=1 т.к. СМ отсутствует
= 095 – так как станочное приспособление простое
qж =04 МПа – давление в заводской воздушной магистрали
Расчет параметров зажимного устройства
Производим приближенное вычисление так как неизвестен диаметр штока d:
По диаметру цилиндра D=987 мм подберём Dстанд=100мм отсюда:
Проведём коррекционный проверочный расчет:
Полученное D=991 мм очень близко к стандартному D=100 мм которое мы и принимаем.
Расчеты точности обработки(Этап IV)
Определение лимитирующего параметра точности
Лимитирующий параметр – допуск радиального биения зубчатого венца (Т=0112).
Рисунок 27: Определение лимитирующего параметра точности.
Рисунок 28: Расчетная схема точности обработки.
При решении этой задачи определяется вид расчетного уравнения:
способ: предельный расчет -=тп+бп+с+нп..;
способ: вероятностный расчет - ;
Определение параметров входящих в расчетное уравнение:
=с – погрешность из-за радиального биения посадочной поверхности шпинделя станка
и 4; 3 и 5 – следует рассматривать как одну погрешность:
н.п1.= 2+4 и н.п2=3+5
=тп – технологическая погрешность
с=001 мм – определяется по таблице характеристик станка
н.п1=025Т=0250112=0028 мм;
н.п2=025Т=0250112=0028 мм – погрешность пространственного расположения;
Определение результатов ожидаемой точности обработки
Суммирование всех результатов предыдущего раздела даёт следующие результаты:
=001+0028+0028+0020=009 мм –по предельным значениям.
==00831 мм –вероятностным методом.
Сопоставляя результаты: 009 0112мм и 00831мм 0112мм устанавливаем что по двум расчетам точность выполняемого параметра будет обеспечиваться. Следовательно проектируемая конструкция станочного приспособления будет обеспечивать требуемую точность обработки.
Описание работы станочного приспособления
Спроектированное станочное приспособление для шлифовки зубьев служит установочным базирующим элементом при данной обработке и является одним из главных элементов от которых зависит обеспечение точности обработки.
Рассматриваемое приспособление состоит из тумбы 6 сменой втулки 4 устанавливаемой в тумбу на которую отверстием устанавливается и базируется шестерня. Для прижима заготовки служит пневмопривод который состоит из пневмоцилиндра с воздухопроводом штока 5 который посредством быстросменной шайбы 3 прижимает заготовку к опорной плоскости тумбы с усилием достаточным для обеспечения неподвижности заготовки в процессе обработки.
Расчет режущего инструмента(червячная фреза)
Червячная фреза – лезвийный инструмент для обработки зубчатых колес с вращательным главным движением резания инструмента без возможности изменения радиуса траектории этого движения и хотя бы с одним движением подачи направление которого не совпадает с осью вращения. Фрезы представляют собой тела вращения с формой производящей поверхности зависящей от формы обрабатываемой поверхности и расположения оси фрезы относительно детали.
Червячные фрезы относят к группе обкатных многолезвийных инструментов с конструктивным движением обката. Режущие кромки зубьев расположены на винтовой поверхности. При работе ось фрезы и нарезаемого колеса перекрещиваются. Образование обработанной поверхности зубьев заготовки происходит при профилировании по методу огибания.
Классификация червячных фрез:
По назначению зуборезные червячные фрезы используют для нарезания:
-цилиндрических колес с прямыми и винтовыми зубьями
-конических колес с криволинейными зубьями
-глобоидальных колес
По конструкции крепления:
По конструкции в целом:
Стандартные зубчатые колеса обычно имеют эвольвентную поверхность. Винтовая поверхность зубьев червячной фрезы образует витки червяка называемого основным. Имеются три типа червяков применяемых для проектирования червячных фрез : эвольвентные архимедовы и конволютные. Только эвольвентный червяк обеспечивает правильное зацепление с эвольвентным зубчатым колесом но ввиду сложности их изготовления в основном применяют архимедовы червячные фрезы с прямолинейным профилем в осевом сечении и конволютные червячные фрезы с прямолинейным профилем в нормальном сечении.
В данном проекте предлагается расчет цельной насадной зуборезной червячной фрезы на базе конволютного червяка для нарезания цилиндрических колес с прямыми зубьями.
Исходные данные для расчета
Модуль нормальный: мм
Толщина зуба нарезаемого колеса по дуге делительной окружности:
Высота головки зуба: мм
Высота ножки зуба :
Коэффициент высоты зуба:
Направление винтовых канавок : левое
Конструктивные элементы
Цельные червячные фрезы для обработки углеродистых конструкционных сталей рекомендуется изготовлять из быстрорежущих сталей Р6М5 10Р6М5 по ГОСТ 19625-83 поэтому материалом фрезы выбираем быстрорежущую сталь Р6М5 по ГОСТ 19625-83.
Наружный диаметр фрезы выбирают с учетом его влияния на конструкцию фрезы в целом. С его увеличением можно увеличить число стружечных канавок что повышает точность обработки зубчатых колес меньшая огранку эвольвентной поверхности зубьев нарезаемого колеса. При большем наружном диаметре можно увеличить диаметр посадочного отверстия то повышает жесткость системы. При этом возможно увеличение режимов обработки и производительности фрезерования. Но с увеличением наружного диаметра увеличивается расход материала и трудоемкость изготовления фрезы. С учетом этого рассчитаем наружный диаметр:
Рисунок 29: Конструктивные элементы фрезы.
где : размер шпоночной канавки
толщина тела фрезы в опасном сечении
где: - диаметр отверстия обеспечивающий необходимую жесткость оправки для крепления фрезы
принимаем =40мм. из стандартного ряда по ГОСТ 9472-60
глубина стружечной канавки которую предварительно рассчитаем по формуле:
Примем из стандартного ряда.
) Угол подъема витков
где: число заходов червяка
С целью повышения производительности зубонарезания фрезы
Для обеспечения постоянного профиля зубьев применим затылование зубьев
средний диаметр фрезы со шлифованным профилем
где: К-коэффициент затылования
где : задний угол на вершине зубьев
число стружечных канавок фрезы
Для повышения технологичности конструкции фрезы выберем четным и равным 10 .
) Расчет общей длины и длины рабочей части фрезы
Длина рабочей части для полного профилирования по высоте зуба нарезаемого колеса должна быть не менее длины проекции активной части линии зацепления на начальную прямую рейку.
Расчет длины рабочей части определяется по формуле:
Для разгрузки профилирующих зубьев и распределения резания на большее число режущих кромок увеличения числа возможных переточек при затуплении фрезы длину рабочей части увеличим в 17 раза:
Общая длина фрезы определяется по формуле:
где : длина буртика по бокам фрезы [рисунок 30]
Буртики применяют для контроля погрешностей установки фрезы на станке и проверки величины радиального биения при изготовлении и заточке фрезы.
Шпоночный паз на посадочном диаметре выполняют по ГОСТ9472-83 для облегчения шлифования отверстия и лучшей посадки фрезы на оправку в нем делают выточку глубиной до 1 мм и длиной около 03L=48мм [рисунок 30].
Рисунок 30: Общая длина фрезы.
Геометрические параметры профиля и лезвий:
) Шаг профиля зуба в нормальном сечении [рисунок 31]:
где : n-число заходов фрезыn=2.
) Профильный угол по нормали:
Угол профиля заменяющего червяка:
где : Т - теоретический шаг винтовой канавки
) Толщина зуба в нормальном сечении с учетом боковых зазоров в передаче:
где: утолщение зубьев фрезы для обеспечения зазора в зубчатой передаче [ГОСТ 9324-80Е].
) Высота зуба фрезы:
где: высота головки зуба фрезы равная
высота ножки зуба фрезы
где : с - коэффициент радиального зазора
Рисунок 31: Профиль зубьев в нормальном сечении.
) Осевой шаг между витками червяка:
) Радиусы скругления вершины и впадины зубьев а так же радиус дна стружечной канавки выполнять в пределах величины радиального зазора то есть равными 2мм. [Рисунок 31].
) Геометрические элементы лезвия фрезы:
Так как с увеличением переднего угла улучшаются условия резания и повышается стойкость фрезы примем
Задний угол на вершинах зубьев
Задние углы на боковых поверхностях приближенно определяют по формуле:
что удовлетворяет условию .
) Размеры стружечной канавки:
Для повышения точности фасонного профиля зубья фрезы необходимо шлифовать.
где: величина дополнительного затылования
) Угол канавки фрезы:
По ГОСТ 9324-80Е при .
Рисунок 32: Радиус дна стружечной канавки.
Рекомендуемые чертежи
- 23.10.2015
- 05.01.2022
- 02.05.2022