Проектирование участка механического цеха для обработки детали вал-шестерня

- Добавлен: 02.06.2022
- Размер: 2 MB
- Закачек: 3
Описание
СОДЕРЖАНИЕ.
ВВЕДЕНИЕ
1. ОБЩИЙ РАЗДЕЛ.
- Описание конструкции. Служебное назначение детали.
- Технологический контроль чертежа детали и анализ
детали на технологичность.
- ТЕХНОЛОГИЧЕСКИЙ РАЗДЕЛ.
- Характеристика заданного типа производства.
- Выбор вида и обоснование способа получения заготовки.
- Выбор общих припусков и допусков на механическую обработку. Расчет массы заготовки и коэффициента использования материала.
- Выбор и обоснование технологических баз.
- Разработка маршрутного плана обработки детали с выбором оборудования и станочных приспособлений. Обоснование принятого маршрутного плана и характеристика оборудования.
- Поэлементный техпроцесс обработки детали.
- Определение операционных припусков и размеров:
2.7.1. Расчет межоперационных припусков и размеров на поверхность аналитическим способом.
2.7.2. Назначение припусков на обработку табличным способом.
- Выбор режущего вспомогательного и измерительного инструмента на операции технологического процесса.
- Выбор рациональных режимов резания и определение норм времени на операции механической обработки.
- КОНСТРУКТОРСКИЙ РАЗДЕЛ.
3.1 Описание устройства и принципа действия станочного приспособления для операции
3.2 Расчет и конструирование приспособления
3.3 Расчёт и конструирование червячной модульной фрезы для операции
3.4.Организация технического контроля на участке. Расчёт исполнительных размеров калибра-скобы для контроля размера
- ОРГАНИЗАЦИОННЫЙ РАЗДЕЛ.
4.1. Определение потребного количества оборудования, его загрузка
4.2 Расчет и организация многостаночного обслуживания на участке. Состав и расчет количества участников производства с учетом многостаночного обслуживания.
4.3 Планировка оборудования и расчет потребных производственных площадей
4.4 Транспортировка детали на участке
4.5 Организация ремонта оборудования на участке
4.6 Обеспечение нормальных условий и безопасности труда на участке.
4.6.1 Расчет вентиляции и освещения на участке
4.6.2 Электробезопасность и пожарная безопасность
4.7 Охрана окружающей среды
4.8 Удаление отходов производства с участка
- ЭКОНОМИЧЕСКИЙ РАЗДЕЛ.
- Расчет стоимости основных оборотных фондов участка
- Определение фонда оплаты труда для работающих
- Расчет общехозяйственных и общепроизводственных расходов
- Определение себестоимости детали, калькуляция и смета затрат.
5.5 Сводная ведомость показателей деловой активности
- ЗАКЛЮЧЕНИЕ
6.1. Технико-экономическое обоснование деловой эффективности проекта.
Библиографический список
Состав проекта
![]() |
![]() |
![]() ![]() ![]() |
![]() ![]() ![]() ![]() |
![]() ![]() ![]() ![]() |
![]() |
![]() ![]() ![]() |
![]() |
![]() |
![]() ![]() ![]() ![]() |
![]() |
![]() ![]() ![]() ![]() |
![]() ![]() ![]() ![]() |
![]() |
![]() ![]() ![]() ![]() |
![]() |
![]() ![]() ![]() ![]() |
![]() ![]() ![]() ![]() |
![]() |
![]() ![]() ![]() ![]() |
![]() ![]() ![]() ![]() |
![]() ![]() ![]() ![]() |
![]() ![]() ![]() ![]() |
![]() ![]() ![]() ![]() |
![]() ![]() ![]() ![]() |
![]() ![]() ![]() |
![]() |
![]() ![]() ![]() ![]() |
![]() ![]() ![]() |
![]() ![]() |
![]() |
![]() ![]() ![]() |
![]() ![]() ![]() ![]() |
![]() ![]() ![]() ![]() |
![]() ![]() ![]() ![]() |
![]() ![]() ![]() ![]() |
![]() ![]() ![]() |
![]() ![]() ![]() |
![]() ![]() ![]() |
![]() ![]() ![]() |
![]() ![]() ![]() |
![]() ![]() ![]() |
![]() ![]() ![]() |
![]() ![]() ![]() ![]() |
![]() ![]() ![]() ![]() |
![]() |
![]() ![]() ![]() |
![]() ![]() ![]() |
![]() ![]() ![]() |
![]() ![]() ![]() ![]() |
Дополнительная информация
DP_Baev_Ekonomika.docx
1 Выбор и характеристика заданного типа производства.
В машиностроении различают три основных типа производства: массовое серийное и единичное. В свою очередь серийный тип принято подразделять на крупносерийное и мелкосерийное производство.
Для определения типа производства можно пользоваться показателем коэффициента закрепления операции или специализации.
В условиях серийного производства рассчитываются следующие календарно-плановые нормативы:
Количество деталей в партии по упрощенному способу можно определить по формуле
N - годовой объем выпуска детали-представителя; шт
Ф – число рабочих дней в плановом периоде дни;
t – число дней на которые необходимо иметь запас деталей для бесперебойной работы сборочного цеха.
-3 дня для крупных деталей ;
-7 –дня для средних деталей;
-10 дней для мелких деталей.
Суточный выпуск деталей можно определить по формуле:
N сут = 670041 = 163 дет.
Период запуска – выпуска партии деталей в производство (ритм серийного производства ) можно определить по формуле:
Количество запусков партии деталей в плановом периоде можно определить по формуле:
обозначения прежние
Необходимо откорректировать
расчетное Sn к нормативному (4;6; 12; 24)
ОРГАНИЗАЦИОННЫЙ РАЗДЕЛ.
1 Определение потребного количества оборудования его загрузка
Расчет фондов времени за год можно определить следующим образом
Номинальный фонд времени.
Fн=(Дк-Дв-Дпр)·S·Дсм
где - количество календарных дней в периоде дней;
- количество праздничных дней в периоде дней;
- количество выходных дней в периоде дней;
S - количество смен;
Дсм - продолжительность одной смены час.
Fн=(365-14-104)·2·8=3952 час.
Действительный фонд времени работы оборудования.
где - коэффициент простоя оборудования
Fд 2 месяца = 5928 час.
Определение потребного количества оборудования.
где - коэффициент выполнения норм . Принимается .
N - производственная программа
На некоторых операциях используется коэффициент догрузки предполагающий догрузку оборудования подобными изделиями.
Операция 005 Токарная с ЧПУ (1А7434Ф3)
Операция 010 Токарная с ЧПУ (16К20Ф3С32)
Операция 015 Токарно – винторезная с ЧПУ (1716ПФ3)
Операция 020 Токарно – винторезная с ЧПУ (1716ПФ3)
Операция 040 Зубофрезерная (53А20)
Операция 045 Шлицефрезерная (5А352ПФ2)
Операция 055 Зубозакругляющая (5Е580)
Операция 060 Зубофрезерная (5306П)
Операция 065 Зубошевинговальная (5702В)
Операция 095 Торцекруглошлифовальная (3Т161Д)
Операция 100 Круглошлифовальная с ЧПУ (3М151Ф3)
Операция 105 Круглошлифовальная (3Т160)
Операция 110 Внутришлифовальная (3К225В)
Общее принятое количество станков – 15
Коэффициент загрузки оборудования:
Средний коэффициент загрузки оборудования.
Определение средней загрузки оборудования по участку.
Составление ведомости оборудования:
Таблица 4.1 – Ведомость оборудования.
Стоимость оборудования т.р.
Токарный с ЧПУ 1А734Ф3
Токарный с ЧПУ 16К20Ф3С32
Токарно – винторезный с ЧПУ 1716ПФ3
Шлицефрезерный 5А352ПФ2
Зубозакругляющий 5Е580
Зубошевинговальный 5702В
Торцекруглошлифовальный 3Т161Д
Круглошлифовальный с ЧПУ 3М151Ф3
Круглошлифовальный 3Т160
Внутришлифовальный 3К225В
2 Расчет и организация многостаночного обслуживания на участке. Состав и расчет количества участков производства с учетом многостаночного обслуживания.
К промышленно-производственному персоналу обслуживающему оборудование относятся основные и вспомогательные производственные рабочие. Рабочие по техническому обслуживанию оборудования как правило включаются в штат цеха.
Для расчета численности работающих на участке определяется действительный фонд времени рабочего:
Fдр = ( Д к – Дв – Дпр ) * s * Дсм * Кпотери где
Кпотери – коэффициент невыходов на работу
Fдр =(365-14-104) 8 1 (1-12100)= 17389 час
Fдр 2 месяца = 2898 час.
Определение количества рабочих по формуле осуществляется по формуле:
R = 670023428986011 = 082 Rпр = 1 чел
R = 67003228986011 = 112 Rпр = 2 чел
5 Токарно – винторезная с ЧПУ
0 Токарно – винторезная с ЧПУ
R = 670031228986011 = 109 Rпр = 1 чел
R = 670078728986011 = 28 Rпр = 3 чел
R = 67009728986011 = 34 Rпр = 4 чел
R = 670024728986011 = 087 Rпр = 1 чел
R = 670024928986011 = 087 Rпр = 1 чел
5 Зубошевинговальная
R = 67003528986011 = 123 Rпр = 2 чел
5 Торцекруглошлифовальная
R = 6700121328986011 = 13 Rпр = 2 чел
0 Круглошлифовальная ч ЧПУ
5 Круглошлифовальная
R = 670033628986011 = 118 Rпр = 2 чел
0 Внутришлифовальная
Общая численность основных производственных рабочих
Всего вспомогательных рабочих:
R всп пр = R контролер + R наладчик + R слесарь
R всп = 3 наладчика + 3 контролера +5 слесарей = 11 чел.
Численность наладчиков определяется по формуле:
R нал = (Спр Нобсл ) S
Нобсл - норма обслуживания станки
Количество АУП и специалистов определяется методом относительной численности:
Для организации работы на участке принимается 1 сменный мастер.
Таблица - Ведомость работающих на участке
Основные производственные рабочие
Вспомогательные рабочие
3 Планировка оборудования и расчет потребных производственных площадей
Площадь участка включает в себя производственную и вспомогательную площадь и бытовые помещения.
Производственная площадь – площадь занятая оборудованием рабочими местами. Производственная площадь определяется исходя из габаритов станков и их количества.
Определим площадь занимаемую каждым станком по формуле:
a и b - соответственно длина и ширина станка м.
Вспомогательная площадь – площадь занятая под проездами вспомогательным оборудованием складами составляет 10% от всей производственной площади.
Общая площадь = Sпр + Sвсп м2
К промышленно-производственному персоналу относятся основные вспомогательные рабочие младший обслуживающий персонал административно управленческий персонал специалисты и служащие.
Таблица 4.3 - Ведомость площади и объема помещения механического участка
Удельная площадь на 1 станок м2
Производственная площадь
Вспомогательная площадь
ЭКОНОМИЧЕСКИЙ РАЗДЕЛ
1 Определение стоимости основных и оборотных фондов участка
Экономическая часть дипломного проекта выполняется с целью расчета всех экономических затрат на производство продукции активное участие в формировании этих расходов принимают основные и оборотные фонды предприятий.
Основные производственные фонды (ОПФ) - это средства труда которые в процесс производства используются многократно постепенно изнашиваются не изменяют свою натуральную форму и переносят свою стоимость на себестоимость продукции по частям в виде амортизационных отчислений.
Классификация основных производственных фондов:
- передаточные устройства;
- силовые машины и оборудование;
- измерительные и регулирующие приборы и устройства не установленные непосредственно на агрегатах и машинах лабораторное оборудование;
- транспортные средства (средства передвижения грузов);
- производственный и хозяйственный инвентарь.
Определяется стоимость здания
где Цпом. - цена помещения за 1 .м3 р.
С зд. = 3432·24600=84427200 руб.
Стоимость оборудования определяется по ведомости оборудования (с учетом доставки установки стоимость которой примем 10 % от стоимости оборудования)
Соб. = Цоб. + 01 ·Цоб р
Соб. = 17253840+17252384001 = 18979224 р.
Стоимость приспособлений можно принять 10% от стоимости оборудования
Спр. = 0118979224=18979224 р.
Стоимость инвентаря (принимается 1% от стоимости оборудования)
Синв. = 001 · 18979224=18979224 р.
Таблица 5.1 -Стоимость основных фондов участка и расчет амортизационных отчислений
Стоимость ОПФ тыс.руб.
Амортизационные отчисления
Расчет амортизационных отчислений выполнен линейным способом исходя из первоначальной стоимости основных фондов и норм амортизации исчисленных с учетом срока полезного использования основных средств.
Оборотные средства-это активы предприятия которые в процессе производства участвуют однократно входят в состав готовой продукции и переносят свою стоимость на себестоимость готовой продукции полностью постоянно изменяя свою натуральную форму.
Оборотные фонды подразделяются на: производственные запасы в состав которых входят сырье основные и вспомогательные материалы топливо и энергия на технологические цели запасные части малоценные и быстроизнашивающиеся предметы покупные полуфабрикаты и комплектующие изделия.
Определяется стоимость основных материалов на производственную программу по формуле:
где m - масса заготовки кг.;
N - готовая программа выпуска шт.;
Цмат = стоимость основных материалов.
В=67007815832=8273830 руб.
Стоимость основных материалов вычисляется с учетом транспортно - заготовительных расходов (5% от стоимости основных материалов).
Стоимость основных материалов в расчете на 1 изделие:
Ц1=78·15832=12349 р.
Определение массы отходов на одно изделие:
- масса заготовки кг.;
- масса отходов кг.;
Определение стоимости отходов на одно изделие:
Сотх=4862·39=18962 р.
Определение стоимости отходов на партию:
Сотх=670018962=1270454 р.
Стоимость материала на одно изделие:
М=12349-18962=104528 р.
Стоимость материалов на программу:
Мпр=6700104528=7003376 р.
Стоимость вспомогательных материалов на одно изделие начисляется как 1% от стоимости материала.
Мвсп1=104528·001=1045 р.
Мвсп=67001045=70015 р.
Расчёт потребности во всех видах энергии.
По формуле определяется стоимость потребной силовой энергии:
где - суммарная мощность эл. двигателей кВт;
- действительный фонд времени работы оборудования ч;
- средний коэффициент загрузки оборудования;
- коэффициент учитывающий одновременную работу электродвигателей;
- коэффициент учитывающий потери энергии в сети;
- коэффициент учитывающий потери энергии в двигателе;
Ц - цена 1 кВт энергии р.
Стоимость осветительной энергии:
где - осветительный период ч.;
S - площадь участка кв.м.;
- норма освещения кВтч. (002 кВтч)
Ц - цена 1 кВт энергии р.;
Стосв. = 350002343237 = 88889 р.
Определение стоимости воды на бытовые нужды:
где - количество рабочих дней в периоде ;
R- численность всех работающих на участке чел.;
- норма потребления воды л.;
Ц - цена 1т. воды для бытовых нужд р..
Определение стоимости воды для технических нужд:
где - годовой расход води на один станок м3.
- коэффициент загрузки оборудования;
m - число смен работы оборудования;
К - количество оборудования работающего с водой на технические цели; шт.
- стоимость 1 м3. технической воды р.
С т.в. = 00659286059286 = 3601 р.
Определение стоимости сжатого воздуха:
где - количество станков с пневматическими зажимами;
- количество станков с применением обдувки;
q - расход сжатого воздуха на один станок с пневматическим зажимом (01 м3.ч.);
q'- расход сжатого воздуха на один станок с обдувкой (1 м3.ч.)
- цена 1.м3. сжатого воздуха р.
С ст.в. = 5928059150115122 = 960 р.
Определение стоимости отопления:
где - удельный расход теплоты
- отопительный период 4320 ч. за год;
V- объем помещения м3.
Ц- цена горячей воды за 1т. р.
Определение стоимости энергетических ресурсов на технологические цели на программу:
С эр. = 181845+3601+960=186406 р.
Определение стоимости энергетических ресурсов на 1 деталь:
Определение стоимости материальных затрат на программу с учетом осветительной энергии воды на бытовые нужды и отопление:
Определение затрат на осветительную энергию воды на бытовые нужды отопление:
Ст=Сосв+Ст.вб+Сtwo=88889+86906+126316=2221109 р
2 Определение фонда оплаты труда для работающих на участке.
Определение ФОТ основных рабочих:
Прямой ФОТ о. р = Р сд N руб.
Прямой ФОТ = 67007972 = 534124 р.
5 Рсд=23496660=38 руб.
0Рсд = 3296660=52 руб.
5 Рсд = 3296660=52 руб.
0 Рсд = 31296660=502 руб.
0 Рсд = 78788460=116 руб.
5 Рсд = 9796660=156 руб.
5 Рсд = 24788460=36 руб.
0 Рсд = 24988460=37 руб.
5 Рсд = 3588460=52 руб.
5 Рсд = 121388460=54 руб.
0 Рсд = 3296660=52 руб.
5 Рсд = 33688460=50 руб.
0 Рсд = 3588460=52 руб.
Расчет основного ФОТ основных рабочих
ФОТ о.р. = ФОТ пр Кд где
Кд – коэффициент доплаты за условия труда
ФОТ осн = 185 534124 = 988129 руб.
Расчет общего ФОТ основных рабочих
ФОТ о.р. = ФОТ осн Кд
где Кд – коэффициент доплаты за отпуск
ФОТ общ = 988129 13 = 1284568 руб.
Определение ФОТ вспомогательных рабочих:
Прямой Фот всп = Тс Fдр R всп. р. где
Fдр – фонд рабочего времени;
Rвсп. р. – количество вспомогательных рабочих
ФОТ пр = 1128987129 =227258 руб.
Основной ФОТ вспомогательных рабочих
ФОТвсп = ФОТпр Кдопл
ФОТ = 227258 16= 363613 руб.
Общий ФОТ вспомогательных рабочих
ФОТвсп = 13 363613= 472697 руб.
ФОТ спец = 2116100=32200 руб.
ФОТ общ = 1932200=61180 руб.
Расчет общего ФОТ по всем категориям работающих:
ФОТ = ФОТ общ осн. р. + ФОТ общ. Всп. р. + ФОТ общ.АУП
ФОТ = 1284568+472697+61180 = 1818445 руб.
Определение заработной платы по категориям:
Где R – численность в соответствующей категории; чел
Тпл – плановый период месяц.
Вспомогательные рабочие:
3 Расчет общехозяйственных и общепроизводственных расходов.
К общепроизводственным расходам относятся: амортизация зданий и сооружений цехового назначения; амортизация основных фондов; заработная плата вспомогательных рабочих и административно управленческого персонала с отчислениями на социальные нужды; расходы по охране труда и т.п.
Таблица 5.2 - Смета общепроизводственных расходов
Наименование статьи затрат
Амортизация оборудования
Содержание оборудования
Затраты на энергетические ресурсы
Содержание специалистов и вспомогательных рабочих
Отчисления на социальное страхование:
Вспомогательных рабочих
Износ инструментов и приспособлений сроком эксплуатации до 12 месяцев
50 р. в расчете на 1-го основного рабочего
Амортизация приспособлений и инвентаря
Расходы на рационализаторство изобретательство
00 р. в расчете на 1-го работающего
Расходы по охране труда и технике безопасности
00 р. на 1-го работающего
Итого общепроизводственные расходы
Процент общепроизводственных расходов:
где ОР - сумма общепроизводственных расходов;
- основной фонд оплаты труда основных рабочих.
Общепроизводственные расходы на 1 деталь:
Общехозяйственные расходы - комплексная статья затрат в ее состав входит заработная плата управленческого персонала всего завода; амортизация зданий сооружений о6орудования производственного назначения и т.д.
Общехозяйственные расходы составляют 350% от ФОТосн.осн рабочих.
Общехозяйственные расходы на участке составят:
РО = 35·988129=3458452 р.
Общехозяйственные расходы на 1 деталь:
4. Определение себестоимости детали составление калькуляции и сметы затрат на производство детали.
Себестоимость продукции - затраты связанные с производством и реализации продукции. Классификация по ряду признаков:
По способу отнесения затрат на себестоимость - прямые косвенные;
По степени участия в производственном процессе - основные накладные;
В зависимости от объема - условно-переменные и условно-постоянные;
В зависимости от состава - простые (элементные) и сложные (комплексные).
При определении себестоимости изделия используется группировка затрат которая называется калькуляцией.
Расходы на продажу включают в себя затраты на упаковку доставку до станции отправления оплату дилеров посредников и других расходов.
Определение себестоимости детали по статьям калькуляции и экономическим элементам.
Таблица 5.3 - Калькуляция детали
Сырье и основные материалы
Транспортные расходы
Вспомогательные материалы
Энергетические ресурсы
Итого материальные затраты
Основная заработная плата рабочих
Дополнительная заработная плата рабочих
% от ЗП основных рабочих
Отчисление на социальное страхование
Общепроизводственные расходы
Общехозяйственные расходы
Итого производственная себестоимость
% от произ. себестоимости
Итого полная себестоимость
% от полной себестоимости
Таблица 5.4 – Смета затрат на производство
Материальные затраты
Расходы на оплату труда
Отчисления на социальные нужды
Амортизация основных фондов
5 Сводная ведомость показателей деловой активности.
Таблица 5.5 – Основные технико-экономические показатели деловой активности участка
Наименование показателя
Программа выпуска шт
Товарная продукция в оптовых ценах р.
Средняя загрузка оборудования %
Общая мощность эл. двигателей кВт·ч
Общая численность работающих чел:
Основных производственных рабочих
Среднемесячный доход р.
- 1 основного рабочего;
- 1 вспомогательного рабочего;
- 1 сменного мастера
Общая трудоемкость нормо-час
Производительность труда
Фондовооруженность руб.чел
Коэффициент использования материала
Рентабельность изделия %
Рентабельность продаж %
Товарная продукция определяется по формуле:
ТП=Цопт N = 6700 310825 = 20825275 руб.
Общая трудоемкость рассчитывается
Производительность труда рассчитывается
Фондовооруженность рассчитывается:
Коэффициент использования материла рассчитывается по формуле:
Прибыль определяется по формуле:
Пб=Пб1N =51804 6700 = 3470868 р.
Рентабельность изделия рассчитывается по формуле:
Рентабельность продаж рассчитывается по формуле:
Фондоотдача определяется по формуле:
1 Технико – экономическое обоснование деловой эффективности проекта.
На спроектированном механическом участке изготавливается деталь «Вал-шестерня» 145-4215011.
Программа участка – 32500программа детали – 6700 шт.
Для изготовления деталей необходимо 26 единиц оборудования из них 15 единиц металлорежущие станки. Средняя загрузка оборудования на участке 59%.
Для выполнения заданной программы деталей необходимо 37 человек из них 25 человек основные рабочие 11 человек вспомогательные рабочие и 1 человек сменный мастер. Среднемесячный доход 1 основного рабочего 25691 руб.1 вспомогательного рабочего 21486 руб. 1 сменного мастера 30590 руб.
Общая трудоемкость изготовления программы деталей 56057 час.
Производительность 1 основного рабочего 833011 руб.чел. Коэффициент использования материала Ким=05
Оптовая цена 1 детали 310825 руб.
Прибыль от реализации программы деталей 3470868 руб. Общая площадь участка 3432 м2. Фондовооруженность характеризует оснащенность работников основными производственными фондами Фв = 2851193 руб.чел.
График загрузки, план участка.frw
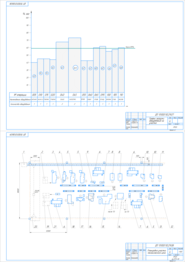
деталь, и загатока.frw
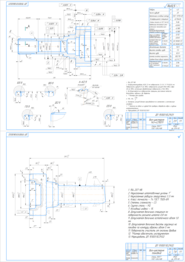
Поверхности зубьев 57 64 HRCэ
поверхности шлицев 51min HRCэ
остальные обработанные поверхности 47min HRCэ.
Не допускаются на поверхностях трещины
забоины и др. дефекты.
Размеры для справок.
Контроль шлицев должен производится по элементам и комплексным
Заточка на одном из зубьев для проверки твердости ядра и глубины
Маркировать ДП 151.001.10.29.01
Неуказанные штамповочные уклоны 7
Неуказанные радиусы закруглений 3 5 мм.
Класс точности - Т4 ГОСТ 7505-89.
Степень сложности - С3.
Исходный индекс - 15.
Допускаемая величина смещения по
поверхности разъема штампа 0
Допускаемая величина остаточного облоя 1
Допускаемая величина высоты заусенца на
поковке по контуру обрезки облоя 5 мм.
Поверхность очистить от окалины дробью.
*Размер обеспечить инструментом.
Маркировать ДП 151001.10.29.02
Нормальный исходный контур
Коэффициент смещения
Степень точности по ГОСТ 1643-81
Предельные отклонения изме-
рительного межосевого рас-
Наименьшее дополнительное
смещение исходного контура
Допуск на колебания
Суммарное пятно кон-
Диаметр основной окружности
Средняя длина общей нормали
Измерительные разме-
ДП 151001.01.08.00.01
ДП 151001.01.08.00.02
записка.doc
2.Технологический контроль чертежа детали и анализ
детали на технологичность.
ТЕХНОЛОГИЧЕСКИЙ РАЗДЕЛ.
1.Характеристика заданного типа производства.
2.Выбор вида и обоснование способа получения заготовки.
3.Выбор общих припусков и допусков на механическую обработку. Расчет массы заготовки и коэффициента использования материала.
4.Выбор и обоснование технологических баз.
5.Разработка маршрутного плана обработки детали с выбором оборудования и станочных приспособлений. Обоснование принятого маршрутного плана и характеристика оборудования.
6.Поэлементный техпроцесс обработки детали.
7.Определение операционных припусков и размеров:
7.1. Расчет межоперационных припусков и размеров на поверхность аналитическим способом.
7.2. Назначение припусков на обработку табличным способом.
8.Выбор режущего вспомогательного и измерительного инструмента на операции технологического процесса.
9.Выбор рациональных режимов резания и определение норм времени на операции механической обработки.
КОНСТРУКТОРСКИЙ РАЗДЕЛ.
1 Описание устройства и принципа действия станочного приспособления для операции
2 Расчет и конструирование приспособления
3 Расчёт и конструирование червячной модульной фрезы для операции
4.Организация технического контроля на участке. Расчёт исполнительных размеров калибра-скобы для контроля размера
ОРГАНИЗАЦИОННЫЙ РАЗДЕЛ.
1. Определение потребного количества оборудования его загрузка
2 Расчет и организация многостаночного обслуживания на участке. Состав и расчет количества участников производства с учетом многостаночного обслуживания.
3 Планировка оборудования и расчет потребных производственных площадей
4 Транспортировка детали на участке
5 Организация ремонта оборудования на участке
6 Обеспечение нормальных условий и безопасности труда на участке.
6.1 Расчет вентиляции и освещения на участке
6.2 Электробезопасность и пожарная безопасность
7 Охрана окружающей среды
8 Удаление отходов производства с участка
ЭКОНОМИЧЕСКИЙ РАЗДЕЛ.
1.Расчет стоимости основных оборотных фондов участка
2.Определение фонда оплаты труда для работающих
3.Расчет общехозяйственных и общепроизводственных расходов
4.Определение себестоимости детали калькуляция и смета затрат.
5 Сводная ведомость показателей деловой активности
1. Технико-экономическое обоснование деловой эффективности проекта.
Библиографический список
Ведущее место в дальнейшем росте экономики страны принадлежит отрасли – машиностроения которое обеспечивает материальную основу технического прогресса всех отраслей народного хозяйства Развитие технологии механической обработки и сборки и её направленность обуславливают стоящие перед машиностроительной промышленностью задачи совершенствовании технологических процессов. Изыскания и изучения новых методов и внедрения комплексной механизации и автоматизации производственных процессов на базе достижений науки и техники обеспечивают наиболее высокую производительность труда при надлежащем качестве и наименьшей себестоимости выпускаемой продукции.
В настоящее время возрастают запросы народного хозяйства в продукции выпускаемой машиностроителями поэтому надо увеличивать не только объём выпуска но и расширять номенклатуру изделий с наивысшими показателями и высокой эффективности эксплуатации.
Широкое внедрение оборудования с числовым программным управлением электронных вычислительных машин промышленных роботов достижений микроэлектроники существенно повысило возможности машиностроительного производства как в части совершенствования выпускаемых машин так и в части увеличения их выпуска без привлечения нового производственного персонала.
Эти обстоятельства обуславливают ту важную роль которая принадлежит специалистам: они должны участвовать в разработке проектов проектировании оборудования для этих производств в разработке технологических процессов и программно-математического их обеспечения.
Задачей дипломного проекта является проектирование участка механического цеха для обработки детали –Вал-шестерня 145-4215011 Т25 – 17011252Д с производственной годовой программой участка 32500и программой выпуска детали 6700
1 Описание конструкции и служебного назначения детали.
Деталь Т25-1701252-Д « Вал шестерня » - представляет собой тело цилиндрической формы типа вал с наружной ступенчатой поверхностью. На наружной поверхности которой имеются прямые зубья расположенные на цилиндрической поверхности модулем 45 мм и числом зубьев Z=25 и также на поверхности детали имеются эвольвентный шлицы 50х25х10d ГОСТ6033-80 центрирование осуществляется по внутреннему диаметру Габаритная длинна вала составляет 235 мм. Деталь имеет гладкие цилиндрические поверхности имеющие высокие требования по точности изготовления и шероховатости.
Вал-шестерня 145-4215011 входит в сборочный узел «Коробка передач» трактора ЛТЗ-145. На валу установлены неподвижные шестерни (шестой передачи блока передач блока ведомых шестерен передачи) и две неподвижные шестерни четвертой передачи и заднего хода и шестерни первой и замедленной передач. При перемещении одной из подвижных шестерен с помощью механизма переключения включается требуемая передача. При включении передачи заднего хода и замедленной вводиться в зацепление дополнительные шестерни установленные нижней части корпуса трансмиссии.
Обрабатываемые поверхности являются поверхностями простой формы которые могут быть получены при несложном относительном движении детали и режущего инструмента.
При обработке для крепления режущего инструмента может быть использована стандартная оснастка. В целом учитывая механизацию механической обработки можно сделать вывод о достаточно хорошей технологичности конструкции детали. Выполнение технических требований обеспечивается обработкой относительно одних технологических баз и за один установ. Деталь имеет свободный доступ режущего инструмента ко всем обрабатываемым поверхностям.
Конструкторский код детали:
Класс 71 – тела вращения типа валов;
Подкласс 5 – валы с L свыше 2D с наружной цилиндрической поверхностью;
Группа 1 – без закрытых уступов гладкие без наружной резьбы;
Подгруппа 4 – центральное отверстие гладкое;
Вид 3 – со шлицами по наружной поверхности без отверстия вне оси детали.
Полный конструкторско-технологический код детали:
Вал в процессе работы подвергается трению шлицы на валу подвергаются изгибу поэтому целесообразно применяется материал сталь 25ХГТ ГОСТ 4543-71 которая используется для изготовления шестерёнок валов осей муфт и других деталей работающих под нагрузкой.
Это легированная хромоникелевая сталь. Назначение – валы шестерни втулки силовые шпильки и другие улучшаемые и цементуемые детали от которых требуется высокая прочность вязкая сердцевина и высокая поверхностная твердость работающие при больших скоростях и повышенных удельных давлениях под действием ударных нагрузок.
Таблица 1.1 - Химический состав %
Таблица 1.2 - Механические свойства.
где – предел текучести условный;
В – временное сопротивление разрыву;
– относительное удлинение после разрыва %;
– относительное сужение %;
КСИ – ударная вязкость.
Технологические свойства:
Температура ковки С: начала 1220 конца – 800; свариваемость – ограничено свариваемая.
Способы сварки: РДС АДС под флюсом.
Обрабатываемость резанием – в горячекатаном состоянии при 177НВ
В=610 МПа; Кvб.ст.=095.
2 Технологический контроль чертежа детали и анализ детали на технологичность.
В детали-«Вал-шестерня» обработке подвергаются цилиндрические поверхности поверхность ф75k6 () обрабатывается по 6 квалитету с наименьшей шероховатостью Ra 25 мкм на данной детали нарезаются прямые зубья z=25 с модулем m=45. Данная деталь имеет достаточно большую длину 235 мм технолог должен учитывать эти параметры и использовать как можно меньше установов и соблюдать постоянство баз. Так же на поверхности ф 495d96 () Ra 32 мкм данной детали присутствуют эвольвентные шлицы. Торцы детали обрабатывают по 11 квалитету. Также имеются канавки под выход шлифовального круга.
Заданная деталь имеет несколько ступеней поэтому для повышения технологичности изделия при обработки ее на станках с ЧПУ деталь отвечает ряду требований: имеет обработанные базовые поверхности унифицированные конструктивные элементы и простые геометрические формы и поверхности. Из этого можно сделать вывод что вал-шестерня 145-4215011 достаточно технологична.
Составляется технологический код детали:
Технологический код детали:
Размерная характеристика - 8Л0;
Группа материала - 04( Сталь 25ХГТ);
Вид детали по технологическому методу изготовления - 4 (резание);
Вид исходной заготовки - 24 (объёмная штамповка);
Наивысшая точность размеров:
наружных - 4 (86 квалитеты);
Параметр шероховатости или отклонения формы и расположения поверхностей
Степень точности - 4
Вид дополнительной обработки -4 ( с термообработкой между операциями)
Характеристика массы детали - Г ( 39 кг)
Технологический и конструкционный код детали: ЛМсК 715143 8Л04244044Г
Таблица 1.2-Анализ технических требований.
Условное обозначение технических требований
Содержание технического требования
поверхности детали 13h12(-0.18) составляет 0046 мм относительно базы И.
поверхности ф82 относительно базы З. База З –шейка вала..
ф56h10(-0.12) составляет 0025 мм относительно базы З. База З является шейка вала.
поверхности детали 30h12(-0.21) составляет 0054 мм относительно базы К.
отклонение от параллельности и круглости поверхности
ф75k6 () не должно превышать 001 мм
приспособление контрольное
поверхности шлицев ф45 относительно базы З. База З –шейка вала..
Нитроцементировать h08 13 мм 57 64 HRCэ ядро 30 46 HRCэ
Насыщение поверхности заготовки аммиаком и азотом на глубину 08 13 мм до твердости 57 64 HRCэ ядро 30 46 НRCэ
Нагрев в электроконтантной печи при t 8600±100С в смеси аммиака и азота
Твердость детали 42 47 HRCэ
Неуказанные пре-дельные отклонения; для отверстий Н14 для валов-h14 для остальных по симметрическому полю допуска 14 квалитета
1 Выбор и характеристика принятого типа производства.
В машиностроении различают три основных типа производства: массовое серийное и единичное. В свою очередь серийный тип принято подразделять на крупносерийное и мелкосерийное производство.
Для определения типа производства можно пользоваться показателем коэффициента закрепления операции или специализации.
В условиях серийного производства рассчитываются следующие календарно-плановые нормативы:
Количество деталей в партии по упрощенному способу можно определить по формуле
N - годовой объем выпуска детали-представителя; шт
Ф - число рабочих дней в плановом периоде дни;
t - число дней на которые необходимо иметь запас деталей для бесперебойной работы сборочного цеха.
-3 дня для крупных деталей ;
-7 дня для средних деталей;
-10 дней для мелких деталей.
Суточный выпуск деталей можно определить по формуле:
N сут = 670041 = 163 дет.
Период запуска выпуска партии деталей в производство (ритм серийного производства) можно определить по формуле:
Количество запусков партии деталей в плановом периоде можно определить по формуле:
обозначения прежние
Необходимо откорректировать
расчетное Sn к нормативному (4;6; 12; 24)
2 Выбор вида и обоснование способа получения заготовки.
В современном производстве одним из основных направлений развития технологии механической обработки является использование черновых заготовок с экономически конструктивными формами обеспечивающими возможность применения наиболее оптимальных способов их обработки т.е. обработка с наибольшей производительностью и наименьшими отходами. Это направление требует непрерывного повышения точности заготовок и приближения их к конструктивным размерам готовой детали что позволяет соответственно сократить объем обработки резанием ограничивая ее в ряде случаев чистовыми и отделочными операциями.
При выборе заготовки для заданной детали назначают метод её получения определяют конфигурацию размеры припуски и допуски на обработку. Т.к. материал детали – сталь 25ХГТ программа выпуска детали N=32500 деталей а также исходя из конструкции детали выбираем вид заготовки – штамповка. Детали – штамповки преимущественно работают на изгиб кручение растяжение. В серийном производстве применяют штамповки полученные на различном оборудовании с помощью штампа. Заготовки – штамповки получаемые свободной ковкой в единичном и мелкосерийном производствах при помощи ковочных молотов и гидравлических ковочных прессов характеризуются сравнительно грубым приближением к форме готовой детали. В серийном и массовом производствах штамповки изготавливают на штамповочных молотах прессах и горизонтально-ковочных машинах (ГКМ) в открытых и закрытых штампах. Метод получения заготовки вал вторичный– штамповка в открытом штампе на ковочном горячештамповочной машине.
3 Выбор общих припусков и допусков на механическую обработку. Расчет массы заготовки и коэффициента использования материала.
Исходные данные для расчета заготовки
Штамповочное оборудование - Горизонтально-ковочная машина.
Нагрев заготовки - пламенный
1 материал - сталь 25ХГТ ГОСТ 4543-71: С= 024 03%
2 масса детали- 39кг
исходные данные для расчета
1 масса поковки (расчетная)
где Mд -масса детали
Кр- расчетный коэффициент (13 16) принимаем Кр=16
Мз=3916=624 кг (8 прилож. 3 с34)
2 класс точности – Т4 (8 прилож.1 с34)
3 группа стали -М2 (8та5л 1 с9)
Средняя массовая доля углерода в стали 25ХГТ ГОСТ 4543-71 024% С
а суммарная доля легирующих элементов - 469
4 степень сложности - С3 (8прилож. 2 с31)
Размеры описывающей поковку фигуры (цилиндр) мм
Диаметр – 1275 мм (1275·105) =1339 мм
где 105 – коэффициент.
Длина – 235 мм (235·105)=24675 мм
Масса описываемой фигуры (расчетная) -624 кг
Сф=314·133922468·00078= 108кг
где V - объём фигуры
р= 00078кгсм2 –плотность
5 конфигурация поверхности разъёма штампа –П (плоская) (8 табл. 1 с9)
6 исходный индекс- 15 (8 табл. 2 с12)
Припуски и кузнечные напуски
1 основные припуски на размеры мм (8 табл. 3 с15)
5 - диаметр 1275 и чистота 32
- диаметр 95 и чистота 16
- диаметр 72 и чистота 16
-диаметр 65 и чистота 32
-диаметр 75 и чистота 32
5-диаметр 48 и чистота 32
- длина 50 и чистота 32
- длина 235и чистота 125
- длинна 38 и чистота 125
2 дополнительные припуски учитывающие:
Смещение по поверхности разъёма штампа 08 мм (8 табл. 4 с16)
Отклонение от плоскостности 05 мм (8 табл. 5 с16)
размеры поковки и их допускаемые отклонения
1 размеры поковки мм
Диаметр 1275+(275+08+05)2= 1331принимаем 133 мм.
Диаметр 95-(25+08+05)2=892 мм принимаем 890 мм
Диаметр 72-(25+08+05)2=661 принимаем 66 мм
Диаметр 65+(25+08+05)2=699 принимаем 70 мм
Диаметр 48+(275+08+05)2=553 принимаем 55 мм
Длина 50+(25+05)2=55 мм
2 радиус закругления наружных углов - принимаем 3 мм (8 табл. 7 с17)
3 допуски отклонения размеров мм (8 табл. 8 с19)
4 неуказанные предельные отклонения размеров 15 (8 пункт 5.5 с26)
5 неуказанные допуски радиусов закругления 05мм (8 пункт 5.23 с26)
6 допускаемая высота заусенца в плоскости разъема матриц 16мм (8 пункт 5.12 с23)
7 допускается высота торцового заусенца 4мм (8 пункт 5.11 с25)
8 допускаемое отклонение от плоскостности и от прямолинейности 10мм (8 пункт 5.16 с25)
9 допускаемое отклонение штамповочных углов(7±17) (8 пункт 5.24 с21)
Рисунок 1 – Эскиз заготовки.
где Vз – объём заготовки см3;
ρ – плотность стали; ρ=00078 кгсм3.
Vз=V1+V2+V3-V4-V5-V6 -V7-V8 (см3) (9)
где V1-8– объём цилиндра см3;
V1=31413.824.8=1505 см3; V5=3147.221.7=398 см3;
V2=3147.523.8=512 см3; V6=3145.221.3=212 см3;
V3=31412.725.0=1015 см3; V7=3147.523.8=421 см3;
V4=3149.522.0=487 см3; V8=3143.6213.8=856 см3;
Vз =1505+512+1015-487-398-212-421-856=11253см3
Коэффициент использования мата
% металла идёт на изготовление детали 45% - отходы; что допустимо для серийного производства кроме того много металла идет в отходы при нарезании шлицев и зубьев.
4 Разработка маршрутного плана обработки детали с выбором оборудования и станочных приспособлений.
Производственным процессом называется совокупность всех действующих людей и орудий производства связанных с переработкой сырья и полуфабрикатов в заготовки готовые детали сборочные единицы и готовые изделия на данном предприятии.
Технологический процесс - часть производственного процесса содержащая действия по изменению и последующему определению состояния предмета производства.
Технологический процесс непосредственно связан с изменением размеров форм и свойств обрабатываемой детали.
Таблица 2.4 - Маршрутный план механической обработки детали.
Полуавтомат токарный с ЧПУ 1А734Ф3
Патрон трехкулачковый
К20Ф3С32 – токарный патронно-центровой станок.
Токарно-винторезная с ЧПУ
Полуавтомат токарный патронный с ЧПУ 1П717Ф3
Зубофрезерный -полуавтомат 53А20
Приспособле-ние зубо-
А352ПФ2 – шлицефрезерный горизонтальный полуавтомат
06П – зубофрезерный полуавтомат.
Оправка зубошевинговальная.
Т161Д – торцекругло-
шлифовальный врезной автомат.
Круглошлифовальная с ЧПУ
М151Ф2 – круглошлифовальный автомат с ЧПУ
Приспособление станочное
Т160 –круглощлифовальный станок.
К225В – внутришлифовальный станок.
Приспособление установочное
Краткая техническая характеристика станков.
П717Ф3 – токарный патронный центровой полуавтомат
Наибольший диаметр устанавливаемой детали мм – 320
Наибольший ход суппорта мм
Диапазон частоты вращения шпинделя мин-1 – 40 1600
Диапазон подач суппорта мммин
Ускоренное перемещение суппорта мммин
Дискретность задания перемещения мм – 0001
Тип устройства ЧПУ – Контур 2ПТ.
Мощность главного привода кВт – 85
Габаритные размеры мм – 28000х2010х1800
06П – зубофрезерный полуавтомат .
Наибольший наружный диаметр обрабатываемых зубчатых колёс мм – 200
Наибольшая длина зубьев нарезаемых колёс мм
с прямым зубом – 180
при гуле наклона зубьев 30- 130
при гуле наклона зубьев 45- 80
Наибольший модуль нарезаемых колёс мм – 4
Число скоростей фрезерного шпинделя – 15
Пределы чисел оборотов фрезы мин-1 – 80 375
Пределы вертикальной подачи мммин – 25 100
Пределы радиальных подач мммин – 1 120
Мощность главного электродвигателя кВт – 64
Габариты – 1730х10501х2120.
Т161Д – торцекруглошлифовальный врезной автомат.
Класс точности автомата П
Наибольшие размеры устанавливаемого изделия мм:
Наибольший диаметр шлифования мм 200
Наибольшая длина шлифования мм 130
Длина перемещения стола (установочная) мм 700
Наибольшая высота шлифовального круга мм 130
Диаметр шлифовального круга по ГОСТ 2424-80 мм:
Скорость вращения шпинделя шлифовальной бабки мин -1 1250
Скорость вращения заготовки(регулируется ступенчато) мин-1
Величина хода шлифовальной бабки по винту мм 290
Скорость шлифования мс 50
Мощность электродвигателя шлифовальной бабки кВт 17
Общая установленная мощность кВт 2673
Габарит станка мм 5870х5000х3300
Масса станка кг 10500
М151Ф2 – круглошлифовальный автомат для врезного и продольного шлифования.
Наибольший размер устанавливаемой детали мм 200x700
Диапазон размеров шлифования с прибором активного контроля 20-85
Высота центров над столом мм 125
Наибольшее количество шлифуемых по программе ступеней за одну установку 8
Наибольший продольный ход стола мм 700
Ручное перемещение стола за один оборот маховика мм 53
Скорость гидравлического перемещения стола мммин 50-5000
Наибольший угол поворота стола град:
По часовой стрелке 30
Против часовой стрелке 4
Наибольший поперечный ход шлифовальной бабки в Горизонтальной плоскости от механизма поворота пиноли мм 01
диапазон частоты вращения шпинделя мин-1 50-500
Ускоренное перемещение мммин 1700-930
Размер шлифовального круга мм 600х80х305
Скорость поперечной подачи шлифовального круга мммин 12-002
Число программируемых осей координат (включая прибор активного контроля)
Число одновременно управляемых координат 1
Дискретность задания перемещений мм:
Шлифовальной бабки 0001
Суммарная мощность всех электродвигателей кВт 152
Габарит 5400x2500x2170
А352ПФ2 – шлицефрезерный горизонтальный полуавтомат.
Размер устанавливаемой детали мм
наибольший диаметр 500
Наибольший диаметр обрабатываемых деталей мм 200
Наибольшая длина нарезаемых шлицев мм 880
Наибольший модуль нарезаемых зубьевмм 8
Наибольший угол наклона зубьев град 30
от подошвы станины 1060
над направляющими 300
Расстояние между центрами мм 1080
Наибольший диаметр устанавливаемой червячной фрезы мм:
Расстояние между осями детали и инструмента мм 63-200
Диапазон частоты вращения шпинделя фрезы мин-1 25-400
Количество ступеней частоты вращения шпинделя фрезы 25
Диапазон подачи мммин:
Тип устройства ЧПУ Ф5007
Мощность главного привода кВт 563; 310
Масса полуавтомата с приставным оборудованием кг 8500
51В – шлицешлифовальный станок.
Наружный диаметр шлифуемых валов мм 25-125
Длина шлифуемых вылов мм 200-1500
Наибольшая длина шлифования мм 1350
Расстояние от оси щпинделя до рабочей поверхности стола мм 212-362
Размеры рабочей поверхности стола мм 250*2345
Продольное гидравлическое перемешение стола мм 200-1620
Диаметр и высота шлифовального круга . мм ( 9-200) * 30
Частота вращения шлифовального круга мин –1 2800;4550; 6300
Автоматическая подача круга ммоб 0005-007
Скорость перемещения стола мммин 1 – 15
Скорость перемещения каретки мммин 453
Мощность электродвигателя привода шлифовального круга кВт 3
Габаритные размеры мм 4450*6200*1900
5 Выбор и обоснование технологических баз.
При выборе баз обработки заготовки используется принцип совмещения баз. Лучшие результаты достигаются при совмещении измерительной конструкторской и технологической баз т.е. поверхностей с помощью которых определяется положение детали в собранном изделии.
В процессе обработки детали соблюдается принцип постоянства баз на всех основных технологических операциях необходимо использовать в качестве технологических баз одни и те же поверхности заготовки.
Принцип постоянства баз способствует повышению точности взаимного расположения поверхности детали. Соблюдение принципа постоянства баз повышает однотипность приспособлений и схем обработки что особенно важно при автоматизации обработки. При выборе баз используется удобство установки и снятия заготовки а так же надежность и удобство её закрепления в выбранных местах зажима возможность подвода режущего инструмента с различных сторон заготовки.
Для детали вал-шестерня чистовыми технологическими базами будут являться опорная шейка но т.к использовать их в качестве технологической базы очень затруднительно поэтому за технологические базы принимают поверхности центровых отверстий образованные на торцах вала.. На первой операции 005 –токарной с ЧПУ деталь заживается в трехкулачковый патрон и обтачивается торец и сверлиться внутренний диаметр для удобства обработки на последующих операциях.
6 Поэлементный техпроцесс обработки детали.
Составляется поэлементный техпроцесс обработки заготовки. Обрабатываемые поверхности изображены на рисунке 2.
Рисунок 2 – Поверхности подлежащие обработке.
Операция 005-Токарная с ЧПУ
Установить заготовку закрепить.
Точить торец 1 поверхность 2.
Центровать отверстия в торце 1.
Сверлить отверстие предварительно до ф20+012
Сверлить отверстие напроход ф355+062.
Снять заготовку контролировать размеры.
Операция 010-Токарная с ЧПУ
Расточить отверстие 4 фаску 5.
Точить поверхность 678.
Операция 015- Токарно-винторезная с ЧПУ
Точить по контуру поверхность 1 9 2.
Расточить отв. 11 предварительно
Расточить отв. 12 предварительно.
Расточит отв. 11 до выхода в канавку
Расточить фаски 151617.
Точить пов. 11 12 18 до выхода в канавки.
Точить канавку 28 с подрезанием торца.
Операция 020- Токарно-винторезная с ЧПУ
Точить деталь проточить канавку 19 с образованием фаски.
Точить пов.21 и галтель 22 R3.
Точить пов. 24 с подрезанием торца.
Точить пов. 25 с подрезанием торца.
Снять заготовку контролировать размеры
Операция 025-Слесарная.
Зачистить заусенцы и притупить острые кромки.
Операция 030-Моечная
Продуть сжатым воздухом.
Операция 035-Контрольная.
Операция 040-Зубофрезерная.
Фрезеровать начерно зубья 29.
Операция 045-Шлицефрезерная
Фрезеровать шлицы 30.
Операция 050-Моечная
Операция 055-Зубозакругляющая.
Фрезеровать фаски по венцу зуба.
Операция 060-Зубофрезерная.
Заострить торцы шлиц.
Операция 065- Зубошевинговальная.
Шевинговать зубья 29 .
Снять заготовку. Контролировать размеры параметры.
Операция 075-Слесарная.
Операция 080- Контрольная.
Операция 081-Транспортная
Операция 085-Термическая
Операция 086-Транспортная
Операция 090-Зубообкатная
Операция 095-Торцекруглошлифовальная.
Шлифовать поверхность 24
Операция 100-Круглошлифовальная.
Шлифовать поверхность 25 и 31.
Операция 105-Внутришлифовальная.
Операция 110-Слесарная.
Операция 115-Моечная
Продуть сжатым воздухом
Операция 120- Контрольная.
7. Определение операционных припусков и размеров: на одну поверхность ф75k6 () - аналитическим методом; на остальные - табличным.
Припуском на обработку называется слой металла подлежащий удалению с поверхности заготовки в процессе обработки для получения готовой детали.
Общим припуском на обработку заготовки называется слой металла удаляемый с поверхности заготовки в процессе механической обработки с целью получения готовой детали.
7.1 Определение припусков аналитическим методом.
7.1.Определение операционных припусков и размеров на поверхность ф75k6 () аналитическим методом.
ф75k6 () Ra 0.8 мкм.
- шлифование черновое
- шлифование чистовое
Для симметричных припусков величина расчётного припуска для первой операции или перехода:
zip = 2(Rzi-1 + h i-1 + ) + eii-1 (11)
Для последующих операций или переходов:
zip = 2(Rzi-1 + h i-1 + ) + ITii-1 (12)
h i-1 – глубина дефектного слоя оставшаяся от предшествующего перехода мкм.
- суммарное значение пространственных отклонений оставшихся от предшествующего перехода мкм;
Iti-1 – допуск размера после предшествующих операций или перехода мкм.
Суммарное значение пространственных отклонений для обработки в центрах наружной поверхности.
где - общая кривизна
где к –удельное значение кривизны после правки в зависимости от среднего диаметра мкммм;
l – общая длина заготовки
- погрешность зацентровки поковки.
где IT - допуск размера базовой поверхности заготовки использованной при зацентровки мм
=025 = 0838 мм ; = 838 мкм;
=006 = 006 1073 = 6438 мкм.
= 005 = 005 6438 = 322 мкм.
= 004 = 004 322 = 013 мкм.
Значение ввиду его малости можно пренебречь. Так как обработка ведётся в центрах то погрешность базирования равна нулю.
Таблица 2.5- Исходные данные для расчёта.
Предельные отклонения
Заготовка штамповка
Расчёт промежуточных припусков сводиться в таблицу 2.6.
Расчётные величины мкм
Расчётный припуск на черновое точение
z1p = 2(Rz0+h0+c0)+ei0 = 2(200+250++0)+4000=49655
Расчётный припуск на чистовое точение
z2p = 2(Rz1+h1+c1)+IT1= 2(50+50++0)+300=516
Расчётный припуск на шлифование черновое
z3p = 2(Rz2+h2+c2)+IT2 = 2(25+0++0)+120=1736
4. Расчётный припуск на шлифование чистовое
z4p = 2(Rz3+h3+c3)+IT3 = 2(10+0+0)+46=66
Расчёт промежуточных размеров ведётся в порядке обратном ходу технологического процесса.
Таблица 2.7-Промежуточные размеры.
Наименование размера припуск
Условное обозначение
Расчётные значения мм
Принятые значения мм
Размеры поверхности по чертежу.
Исходные расчётные размеры.
Припуск на шлифование чистовое
Размер после чернового шлифования
Припуск на черновое шлифование
Размер после чистового точения.
Припуск на чистовое точение.
Размер после чернового точения.
Припуск на черновое точение.
7.2 Назначение припусков на остальные поверхности табличным методом.
Определение операционных припусков и размеров на поверхности табличным методом.
Таблица – 2.8. Промежуточные припуски и размеры.
Методы обработки поверхности
Шероховатость поверхности Ra
Промежуточные размеры мм
Ф1275h11(-0.25)Ra 3.2 мкм.
Ф58Н9 (+0074)Ra 08 мкм.
- растачивание черновое
-растачивание чистовое
Остальные поверхности обрабатываются однократно.
8 Выбор режущего вспомогательного и измерительного инструмента на операции технологического процесса.
Таблица 2.9 - Режущий вспомогательный и измерительный инструмент на операции механообработки детали представителя «Вал вторичный» Т25-1701252Д
Измерительный инструмент
Резец токарный проходной
левый черновой с механическим креплением пластины ГОСТ 19056-80 Т15К10
Сверло центровочное комбинированное ф63 ГОСТ 14952-75 Р6М5
Сверло ф20 2301-0069 ГОСТ Р6М5 10903-77
Сверло ф355 2301-0123 ГОСТ 10903-77 Р6М5
Штангенциркуль ШЦ-1-250-01
левый черновой с механическим креплением пластины ГОСТ 19056-80 Т15К6
Резец токарный расточной 2141-0057 Т15К6 ГОСТ 18883-73
Резец контурный с механическим креплением пластины Т5К6 ГОСТ 9795-80
Резец токарный проходной левый черновой с механическим креплением пластины ГОСТ 19056-80 Т15К10
Резец токарный проходной левый чистовой с механическим креплением пластины ГОСТ 19056-80 Т5К6
Резец токарный расточной черновой 2141-0057 Т15К6 ГОСТ 18883-73 4. Резец токарный расточной чистовой 2141-0057 Т5К6 ГОСТ 18883-73
Резец канавочный 2130-0317 Т5К10 ГОСТ 18884-73
Резец токарный расточной чистовой 2141-0057 Т5К6 ГОСТ 18883-73
Калибр-пробка ф575+012
Калибр-пробка ф945+0017
Контрольное приспособление.
Резец канавочный в=4 мм 2130-0009 Т5К10 ГОСТ 18884-73
Резец контурный Т15К6
Резец канавочный в=316 мм 2130-0009 Т5К10 ГОСТ 18884-73
Микрометр МК50-1 ГОСТ 998-71
Прибор индикаторный ИРБ ГОСТ 5584-75
Фреза червячная ф125 z=14 m=45 мм Р6М5 ГОСТ 9324-80
Приспособление контрольное
Фреза червячная шлицевая ф70 мм ГОСТ 9489-37
Фреза цилиндрическая Р6М5.
Патрон цанговый для фрезы
Шевер дисковый 180 m=45 Р18 ГОСТ 8570-80
Приспособление зубоконтрольное. Биенемер Б10М
Образцовая шестерня.
1.500х63х203 25А 425-Н ССМ2 7К 50мс ГОСТ2424-83.
Карандаш алмазный3908-0052 1 ГОСТ 607-80
Индикатор ИЧ10Б ГОСТ 5584-75
1.600х63х305 25А25-НСМ27 К1 50мс а 1кл. ГОСТ2424-831. ГОСТ 2424-83
Индикатор ИЧ10Б ГОСТ 5584-75 577-68
Круг 6. 50х32х13 25А 16-П СМ17 К1 50мС ГОСТ 2424-83
Карандаш алмазный 3908-0052 1 ГОСТ 607-80
9Выбор рациональных режимов резания и определение норм времени на 4 - 5 разнохарактерных операций механической обработки.
Операция 005. Токарная с ЧПУ.
Переход 02. Точить торец и цилиндрическую пов-ть ф130-063 на длину 25 мм.
Подача S= 08-120 ммоб 8к.22.л.1.с.73
Принимается S= 10 ммоб.
Поправочный коэффициент: Кs = 09
v= 83 ммин 8. к.23 с. 76
Поправочные коэффициенты:
Kv1 =12; Kv2 =1; Kv3 =065; Kv4 =1.
v= 8312065 = 647 ммин
Частота вращения шпинделя:
Регулирование частот вращения бесступенчатое.
Мощность затрачиваемая на резание:
Nрез=34 кВт 8. к.24 с.77
Основное время на переход
где -длина рабочего хода мм
где - величина врезания мм
- величина перебега мм
- длина обработки мм
Переход 03. Центровать отверстие в торце.
Глубина резания (20)
Подача на оборот Sо = 006-008 ммоб. 8. к.41 с. 103.
Принимается Sд= 005 ммоб.
Скорость резания v рассчитывается по эмпирической формуле
где Т - период стойкости инструмента.
Cv = 70; q= 040; m = 02; y = 07 18 к.28с.278.
Поправочный коэффициент Kv= Кмv× Киv ×Кlv
Кмv = Кг( (22) 18. к.1с. 261
Кг= 08; nv= - 09 18. к.2. с.2
Частота вращения шпинделя
По паспорту nд = 1525 мин-1.
Sм= Sо × nд = 005 × 1525 = 75 мммин(24)
Lр.х- длина рабочего хода инструмента.
Переход 03.Сверлить отв. Ф35.
Сверление отверстия ф20+062 мм.
Глубина резания t =202= 100 мм.
Подача на оборот Sо = 006-008 ммоб. 12. к.41 с. 103.
Cv = 70; q= 040; m = 02; y = 07 19 к.28с.278.
Sм= 221 мммин 12. к. 10 с. 212.
Поправочный коэффициент Kv= Кмv× Киv ×Кlv (27)
Кмv = Кг( 19. к.1с. 261
Кг= 08; nv= - 09 19. к.2. с.2
По паспорту nд = 1125мин-1.
Sм= Sо × nд = 005 × 1125 = 5625 мммин. Принимается Sм=50 мммин
S=08-015 ммоб 12 к.43.с111
Принимается S=103 ммоб
V=1419 м мин 12 .к.44.с.112
Принимается n=100 мин-1
Время перекрывается временем на сверление отверстия.
Проверочный расчет по мощности проводится по самому нагруженному переходу- черновому точению
Следовательно на выбранных режимах обработка возможна.
Основное автоматическое время работы по программе на операцию:
То.а.=007+ 011+04+035+045= 138 мин.
Вспомогательное время работы по программе:
Тв.а.= Тх + Тост (31)
где Тх - время автоматической вспомогательной работы : на подвод детали или инструментов от исходных точек в зоны обработки и отвод установку инструмента на размер изменение величины и направления подачи.
Тост. - время технологических пауз остановок подачи и вращения шпинделя для проверки размеров осмотра или смены инструмента.
Та - время автоматической работы станка
где Тв.а. - время автоматическое вспомогательное
Та = 138+ 018=156 мин
Вспомогательное время ручной работы
где Тв.у. - вспомогательное время на установку и снятие детали
Тв.оп. - вспомогательное время связанное с операцией
Тв.и. - вспомогательное время на контрольные измерения.
Тв.у. = 024 мин 7 к.2 с.36
Тв.оп.=004+003+004+0044=027 мин.
Тв.и.=009+022=031 мин 7. к.8с.50
Тв.=024+027+031=082 мин
где Тотл- время на отдых и личные надобности %
КtВ- коэффициент учитывающий серийность производства.
Тотл=7 % 7. к.15с.62
Штучно-калькуляционное время
где Тп.з. -подготовительно-заключительное время
Тп.з. =4+2+3+14+412+403+15+405=325 мин. 7. к.13с.60
Переход 02: Фрезеровать зубья шестерни предварительно m=45; z= 25
Исходные данные: колесо зубчатое.
z=13 m=7 ширина венца L=50 степень точности 11 Ra=32 мкм материал Сталь 25ХГТ.
Режущий инструмент: Фреза червячная модульная m=45 мм; z=14 Dcр=125 мм число одновременно обрабатываемых деталей g=1.
Расчётные размеры обработки:
Z=25 m=45 l= 50мм i=1.
Глубина резания t=22m=2245=99 мм.(37)
Расчётная длина рабочего хода фрезы:
Lр=l0+l1=50+34=84 мм(38)
l1 – величина врезания и перебега фрезы
Подача при обработке по сплошному металлу
S0=26 30 ммоб [6 К. 2]
Принимаем по паспорту станка
Частота вращения фрезы
по паспорту станка принимаем n=120 мин-1
Мощность на шпинделе станка
Основное время на операцию
Вспомогательное время:
на установку и снятие детали массой 39 кг
Тв1=025 мин [7 К. 63]
Время контрольных измерений перекрывается машинным:
Операция 045 - Шлицефрезерная.
Переход 02- Фрезеровать шлицы 50х25х10d ГОСТ 6033-80.
Осевая подача Sо=125 ммоб 12. к.ШФ-2. с. 174
Sо=125 - 09=1125 ммоб.
Скорость резания v=65 ммин.
К2=09; К3=10 12. к.ШФ-2. с 175
v = 65 - 09 = 585 ммин
Действительная частота вращения nд= 150 мин-1
Действительная скорость резания
Длина рабочего хода
где L р.- длина шлица;
L п.- величина врезания и перебега.
L п.= 20 мм. 12. прил. 5. с.420
L р.х.= 42+20= 62 мм.
z-число нарезаемых шлиц;
Z- число заходов фрезы.
Тв= tуст.+ tпер.+ tизм..
tуст.= 046 мин. 10.к.6 с.38
Тп.з.=23+35+7=335 мин.
аобс.=4 % 10.к. 72 с.162
tизм..=029 мин. 10.к. 86 л 5 с. 189
Тв=046+05+029 = 125 мин.
аотл.=7 % 10.к.88с.203
Штучно-калькуляционное время :
Операция 055- Шевинговальная.
Переход 02: Шевинговать зубья шестерни;
Припуска на межосевое расстояние ра w и толщину зуба 2р мм.
р=01-02 мм. Принимается 2р=02 мм 13 ЗШц-3 с. 154
ра w=028-035 мм. Принимается ра w=03 мм.
Длина рабочего хода методом продольной подачи
Lр.х.=b+(2 4)=50+4=54 мм.
SМ=115 мм мин 13 ЗШц-4 с. 154
SР=004 мм дв. ход. 13 ЗШц-4 с. 154
Поправочный коэффициент К1=09
SР=004 09=0036 мм дв. ход.
По паспорту SРд. =003 мм дв. ход
Окружная скорость шевера:
VО=70-135 м мин. Принимается 100 ммин 13 ЗШц-4 с. 154
Поправочный коэффициент К2=09
Частота вращения шевера:
По паспорту пд =160 мин-1
Скорость резания:V=v0SinSCosa
Где S - угол скрещивания осей
a - Угол наклона зубьев колеса.
V=90Sin120 =187 ммин.
Стойкость шевера: Тр=100 ч. 13. ЗШц-4 с. 156
Количество предварительных ходов ппр=6;
Окончательных пок=3 13. ЗШц-4 с. 156
i - число рабочих ходов стола станка.
Тв=Туст+Т в.оп.+Тконтр
Туст=08 мин 10.к.67.с.157
Т в.оп=013 мин 10..к.67.с.157
Тконтр=019 мин 10.к.86.с.193
Тв= 08+013+019=112 мин.
КТв=087 10.к.56.с.143
Тп.з= 13+3+5=21 мин 10.к.67.с.157
КОНСТРУКТОРСКИЙ РАЗДЕЛ
1 Описание устройства и принципа действия станочного
приспособления для заданной операции
На операции 060- Зубофрезерная применяется станочное приспособление - оправка зубофасочная. Оправка состоит из корпуса с цилиндрическим отверстием основание крепится к столу станка с помощью четырёх болтов. Внутри корпуса проходит тяга поз.7 соединённая с помощью резьбы со штоком поз.8 гидроцилиндра. Деталь устанавливается на центр поз.4 и по внутренней поверхности и закрепляется по наружной поверхности зубьев детали рычагом поз.11.
Принцип работы приспособления:
Вал-шестерня устанавливается горизонтально на центр рукояткой распределительного крана подаётся сжатое масло в шоковую полость цилиндра. При этом поршень шток и тяга прижимает центр и закрепляет деталь. Для разжима сжатое масло подаётся в бесштоковую полость цилиндра шток и тяга поднимаются разжимается центр и деталь открепляется. Для установки детали в заданном положении применяется фиксатор который после зажима детали отводится в сторону.
2 Расчет u конструирование приспособления для заданной операции
Рисунок 3 – Схема расположения сил зажима и сил резания.
Величину сил зажима детали в приспособлении можно определять решив задачу статики на равновесие твердого тела находящегося под действием всех приложенных к нему сил и моментов возникающих от этих сил - резания и других стремящихся сдвинуть установленную деталь(силы веса инерционные центробежные) зажима и реакции опор . При обработке фасок на заготовку действует сила резания которая направлена параллельно силе зажима. Поэтому учитывая параллельное и одностороннее направление действия сил W и Pz можно принять:
Сила необходимая на резание определяется по формуле:
Nрез= 10-3 Sy CN mx Du zq V KN (41)
где СN х y u q KN – коэффициенты и показатели степени.
KN=11 –поправочный коэффициент на мощность учитывающий изменение условия эксплуатации
So = 012 ммоб подача на один оборот детали
V= 188 ммин скорость резания
D=18мм – диаметр пальцевой фрезы
Определяем мощность резания:
Nрез = 10-3 012 09 124 4 17 18-1 42 0 188 11 = 0500 кВт
Pz = 1020 60 0500 188 = 1627 Н
В данном приспособлении окружная сила Pz параллельна силе зажима W и они направлены в одну сторону. При этом требуется минимальная сила зажима.
В приспособлении оправка зубофасочная для зажима заготовки при обработке в качестве силового привода используется гидроцилиндр двухстороннего действия. Основным параметром гидроцилиндра является диаметр поршня D. Зажим детали происходит при подаче масла в штоковую полость поэтому:
где d-диаметр штока м;
Предварительно принимаем d=0032м.
Р – давление масла в гидросистеме
- коэффициент полезного действия гидроцилиндра
Диаметр поршня находится по формуле:
Принимается D=100 мм из стандартного ряда.
Действительное усилие на штоке гидроцилиндра определяется по формуле:
3 Расчет и конструирование режущего инструмента для операции
На зубофрезерной операции в качестве режущего инструмента используется червячная фреза модулем m=45 мм. Обработка производится по методу обката. Главное движение – вращение фрезы.
Основные конструктивные размеры фрезы определяются по ГОСТ 9324-80: наружный диаметр dао=125 мм; диаметр посадочного отверстия d=50 мм диаметр буртика d1=80 мм длина фрезы L=125 мм число зубьев Zо=14.
Размеры профиля зубьев в нормальном сечении: шаг профиля зуба Рпо=Пm=31445=1413 мм. Толщина зуба в нормальном сечении Sпо=05Р=051413=7065 мм.
Высота головки зуба ho=25 мм; высота ножки зуба до фланца hfo=55 мм; высота головки зуба hао=125 мм; толщина фланца наибольшая зуба rа=38 мм толщина фланца наибольшая af=008 мм; радиальное закругление ra=38 мм.
Размеры профиля зуба в осевом сечении: профильный угол профиля правой стороны зуба αпр=20008' а левой стороны зуба αп=19057'; средний расчетный диаметр фрезы dто=1125 мм; угол подъема винта равный углу наклона стружечной канавки γто=λто=3046'; затылование К=10 мм; дополнительное затылование К1=14К=14 мм; ход винтовой стружечной канавки Pz=7245мм.
Элементы стружечных канавок фрезы:
угол профиля стружечной канавки Q=180;
радиус закругления дна канавок
Размеры посадочного отверстия и шпоночного паза по ГОСТ 9472-83;
D=50Н6(-0016) ; С1=53Н12(+0074); а=
Размеры канавок для облегчения шлифования профиля зубьев hз=1 мм;rз=1 мм; b=03Sno=037065=2 мм.
Технические требования фрезы типа 1 класса АА принимаются по ГОСТ 9324-80.
Система контроля качества изделий предназначена для своевременного определения с требуемой точностью параметров качества изделий изготавливаемых на участке.
Контроль качества изделий на участке производится на контрольных столах контролёрами. Проверка производится после токарных операций перед нарезанием зубьев после нарезания зубчатого венца а также после изготовлении детали и перед термообработкой. Контрольный пункт промежуточного контроля располагается между станками. Это возможно из-за использования простых измерительных средств (калибров штангенциркулей штангенрейсмусов и т.п.) и контрольных приспособлений.
Проверка производиться после токарной обработки после нарезания зубчатого венца и перед термообработкой после изготовления детали.
Измерительные средства применяемые для промежуточного контроля заготовки и окончательного контроля детали в серийном производстве могут быть и стандартными и специальными.
Высокое качество зубчатых колёс обеспечивается при условии применения современных методов и средств контроля а так же технического контроля на протяжении технологического цикла изготовления начиная с заготовки заканчивая финишными операциями и сборкой.
При измерении поверхностей выполненных по допускам применяют предельные калибры т.к. измерение переставными инструментами является сложной и длительной операцией. Средства контроля должны соответствовать требованиям ГОСТ 8.001-71. К применению допускаются средства контроля признанные годными по результатам метрологического надзора в соответствии с требованиями ГОСТ 8. 002-71.
Для контроля размера на операции 095-Торцекруглошлифовальной применяется калибр-скоба. Это бесшкальный измерительный инструмент двухпредельный т.е. имеющий проходную (ПР) и непроходную (НЕ)стороны. Изделие считается годным если скоба опущенная под действием собственного веса проходит через проходную сторону и не проходит через непроходную.
. Определение исполнительных размеров калибра-скобы для контроля размера
Расчёт исполнительных размеров гладких калибров производится по формулам ГОСТ 24853-81.
Предельные отклонения размера вала:
es=21; ei=2 мкм. 3.т.7
Предельные размеры вала:
dmax=d+es=75+0021=75021 мм(47)
dmin=d+ei=75+0002=75002 мм(48)
Td=es-ei=0021-0002=0019мм. (49)
Отклонения и допуски на калибр-скобу для 6 квалитета:
Z1=4 мкм Y1=3 H=3 мкм Н1=5 мкм Hp=2 мкм
Расчёт размеров проходного нового калибра-скобы ПР:
ПР=dmax-Z1 ± H1 2=75021-0004± 00052=75017±0005 мм (50)
Предельные размеры проходного калибра:
-наибольший: ПРmax=75017+0005=75026 мм
- наименьший: ПРmin=75017-0005=75012мм
Исполнительный размер проходного калибра-скобы ПРисп:
Предельный размер изношенного проходного калибра ПРизн:
ПРизн= dmax +У1=70021+0003=70024 мм(51)
Расчёт размеров непроходного нового калибра-скобы НЕ:
НЕ= dmin ± H1 2=75002 ± 00052=75002±0005мм(52)
Предельные размеры непроходного калибра:
- наибольший: НЕmax=75002+0005=75007 мм
- наименьший: НЕmin=75002-0005=74993 мм
Исполнительный размер непроходного калибра-скобы НЕисп:
Расчёт размеров контрольного калибра К-ПР:
К-ПР=dmax-Z1 ±Hр2=75021-0004±00022=75017±0001 мм(53)
Предельные размеры контрольного калибра К-ПР:
К-ПРmax=75017+0001=75018 мм
К-ПР min=75017-0001=75016мм
Исполнительный размер контрольного калибра К-ПР:
Расчёт размеров контрольного калибра К-НЕ:
К-НЕ=dmin ± Hр2=75002 ± 00022=75002 ±0001 мм.(54)
Предельные размеры контрольного калибра К-НЕ:
- наибольший К-НЕmax=75002 +0001=75003 мм
- наименьший К-НЕmin=75002-0001=75001 мм
Исполнительный размер контрольного калибра К-НЕ:
Расчёт размеров контрольного калибра К-И:
К-И= dmax-У1 ±Hр2=70021-0003±00022=75018±0001 мм.(55)
Предельные размеры контрольного калибра К-И:
- наибольший К-Иmax=75018+0001=54956 мм
- наименьший К-Иmin=75018-0001=75017 мм
Исполнительный размер контрольного калибра К-И:
Рисунок 8 – Схема расположения полей допусков калибра-скобы для контроля размера .
ОРГАНИЗАЦИОННЫЙ РАЗДЕЛ
1 Определение потребного количества технологического оборудования и его загрузки
Расчет фондов времени за год можно определить следующим образом
Номинальный фонд времени.
Fн=(Дк-Дв-Дпр)·S·Дсм(56)
где - количество календарных дней в периоде дней;
- количество праздничных дней в периоде дней;
- количество выходных дней в периоде дней;
S - количество смен;
Дсм - продолжительность одной смены час.
Fн=(365-14-104)·2·8=3952 час.
Действительный фонд времени работы оборудования.
где - коэффициент простоя оборудования
Fд 2 месяца = 5928 час.
Определение потребного количества оборудования.
где - коэффициент выполнения норм . Принимается .
N - производственная программа
На некоторых операциях используется коэффициент догрузки предполагающий догрузку оборудования подобными изделиями.
Операция 005 Токарная с ЧПУ (1А7434Ф3)
Операция 010 Токарная с ЧПУ (16К20Ф3С32)
Операция 015 Токарно - винторезная с ЧПУ (1716ПФ3)
Операция 020 Токарно - винторезная с ЧПУ (1716ПФ3)
Операция 040 Зубофрезерная (53А20)
Операция 045 Шлицефрезерная (5А352ПФ2)
Операция 055 Зубозакругляющая (5Е580)
Операция 060 Зубофрезерная (5306П)
Операция 065 Зубошевинговальная (5702В)
Операция 095 Торцекруглошлифовальная (3Т161Д)
Операция 100 Круглошлифовальная с ЧПУ (3М151Ф3)
Операция 105 Круглошлифовальная (3Т160)
Операция 110 Внутришлифовальная (3К225В)
Общее принятое количество станков – 15
Коэффициент загрузки оборудования:
Средний коэффициент загрузки оборудования.
Определение средней загрузки оборудования по участку.
Кз.ср.= Кз.ср.·100%(61)
Составление ведомости оборудования:
Таблица 4.1 – Ведомость оборудования.
Стоимость оборудования т.р.
Токарный с ЧПУ 1А734Ф3
Токарный с ЧПУ 16К20Ф3С32
Токарно -винторезный с ЧПУ 1716ПФ3
Токарно - винторезный с ЧПУ 1716ПФ3
Шлицефрезерный 5А352ПФ2
Зубозакругляющий 5Е580
Зубошевинговальный 5702В
Торцекруглошлифовальный 3Т161Д
Круглошлифовальный с ЧПУ 3М151Ф3
Круглошлифовальный 3Т160
Внутришлифовальный 3К225В
2 Расчет и организация многостаночного обслуживания на участке. Состав и расчет количества участников производства с учетом многостаночного обслуживания
К промышленно-производственному персоналу обслуживающему оборудование относятся основные и вспомогательные производственные рабочие. Рабочие по техническому обслуживанию оборудования как правило включаются в штат цеха.
Для расчета численности работающих на участке определяется действительный фонд времени рабочего:
Fдр = ( Д к Дв Дпр ) * s * Дсм * Кпотери где(62)
Кпотери - коэффициент невыходов на работу
Fдр =(365-14-104) 8 1 (1-12100)= 17389 час
Fдр 2 месяца = 2898 час.
Определение количества рабочих по формуле осуществляется по формуле:
R = 670023428986011 = 082 Rпр = 1 чел
R = 67003228986011 = 112 Rпр = 2 чел
5 Токарно - винторезная с ЧПУ
0 Токарно - винторезная с ЧПУ
R = 670031228986011 = 109 Rпр = 1 чел
R = 670078728986011 = 28 Rпр = 3 чел
R = 67009728986011 = 34 Rпр = 4 чел
R = 670024728986011 = 087 Rпр = 1 чел
R = 670024928986011 = 087 Rпр = 1 чел
5 Зубошевинговальная
R = 67003528986011 = 123 Rпр = 2 чел
5 Торцекруглошлифовальная
R = 6700121328986011 = 13 Rпр = 2 чел
0 Круглошлифовальная ч ЧПУ
5 Круглошлифовальная
R = 670033628986011 = 118 Rпр = 2 чел
0 Внутришлифовальная
Общая численность основных производственных рабочих
Всего вспомогательных рабочих:
R всп пр = R контролер + R наладчик + R слесарь
R всп = 3 наладчика + 3 контролера +5 слесарей = 11 чел.
Численность наладчиков определяется по формуле:
R нал = (Спр Нобсл ) S
Нобсл - норма обслуживания станки
Количество АУП и специалистов определяется методом относительной численности:
Для организации работы на участке принимается 1 сменный мастер.
Таблица 4.2 - Ведомость работающих на участке
Основные производственные рабочие
Вспомогательные рабочие
3 Планировка оборудования и расчет потребных производственных площадей
Площадь участка включает в себя производственную и вспомогательную площадь и бытовые помещения.
Производственная площадь - площадь занятая оборудованием рабочими местами. Производственная площадь определяется исходя из габаритов станков и их количества.
Определим площадь занимаемую каждым станком по формуле:
a и b - соответственно длина и ширина станка м.
Вспомогательная площадь - площадь занятая под проездами вспомогательным оборудованием складами составляет 10% от всей производственной площади.
Общая площадь = Sпр + Sвсп м2
К промышленно-производственному персоналу относятся основные вспомогательные рабочие младший обслуживающий персонал административно управленческий персонал специалисты и служащие.
Таблица 4.3 - Ведомость площади и объема помещения механического участка
Удельная площадь на 1 станок м2
Производственная площадь
Вспомогательная площадь
4 Транспортировка деталей на участке.
В процессе производства в цехах предприятия регулярно перемещается большое количество сырья материалов топлива инструментов и готовой продукции доставка этих грузов на заводе а также вывоз готовой продукции и отходов производства является функцией промышленного транспорта. Согласованность транспортных и производственных процессов - необходимое условие бесперебойной работы отдельных цехов и предприятия в целом.
Для ликвидации тяжелых и трудоёмких работ сокращения продолжительности производственного цикла следует предусматривать механизированные транспортные средства. Выбор транспорта зависит от характера обрабатываемых на участке деталей массы и габаритов изделия или величины изготавливаемой партии типа производства грузооборота. Транспорт должен своевременно обеспечивать рабочие места заготовками чтобы снизить простои на местах и длительность производственного цикла.
В данном случае для перемещения деталей от станка к станку используется роликовый неприводной конвейер из цеха в цех – электрокары.
5 Организация ремонта оборудования на участке.
Для поддержания эффективной работы оборудования необходимо осуществлять надзор за состоянием оборудования. Чтобы оборудование было в постоянной готовности необходимо предупредить преждевременный износ обеспечить надлежащий уход и ремонт оборудования.
Ремонтное хозяйство цеха возглавляет механик цеха в его подчинении находятся мастера и рабочие механики. На всем предприятии из вспомогательных рабочих 30% заняты ремонтом оборудования.
Планово-предупредительный ремонт оборудования - основа организации ремонта. Он включает в себя совокупность различного вида работ по техническому уходу ремонта оборудования и мероприятия межремонтного обслуживания.
Плановые ремонтные оборудования: малый средний и капитальный а также изготовление запасных частей в ремонтно-механических цехах завода.
Капитальный ремонт оборудования производится 1 раз в 4 года. Планово-предупредительный- 1 раз в 2 года. Текущий ремонт-1 раз в год. Осмотр оборудования производится 2 раза в год.
6 Обеспечение нормальных условий труда на участке.
Для скоординированной и планомерной работы в области безопасности труда на каждом предприятии создается служба охраны труда подчиняемая главному инженеру.
Главный инженер несет ответственность за безопасность производственных процессов и осуществляет контроль за всеми мероприятиями направленными на оздоровление условий труда. Всю практическую работу в подразделениях предприятий организуют начальники цехов участков смен а так же мастера. На участке обработки детали стакан подшипника - применяются токарно-револьверные токарно-винторезные сверлильные станки.
Отличительной особенностью токарных станков являются: вращающиеся станочные приспособления и заготовки а так же образующаяся в процессе резания стружка. Для безопасности работы на токарных станках должны применяться защитные устройства для предотвращения опасного соприкосновения рабочего с движущимися элементами станка и режущим инструментом а так же для локализации опасных зон куда отлетают частицы обрабатываемого металла.
При работе особое внимание должно быть уделено правильному и надежному закреплению заготовок. При установке инструмента необходимо соблюдать следующие правила:
) резцы следует закреплять с минимально возможным вылетом из резцедержателя (чтобы он не превышал более чем в 15 раза высоту державки) и не менее чем двумя болтами.
) не оставлять в задней бабке или револьверной головке инструменты которые не используются при обработке данной заготовки. На сверлильных станках выполнение установки детали осуществляют с соблюдением следующих общих правил безопасности: опорные поверхности выбирают так чтобы центр тяжести заготовки проходил возможно ближе к середине опорной поверхности если она одна и возможно ближе к общему центру поверхностей если их несколько; точки приложения усилий закрепления размещают так чтобы направление вектора силы не выходило за пределы поверхностей опор.
Основными опасными и вредными производственными факторами при шлифовальных работах являются: электрический ток быстроперемещающийся абразивный инструмент отлетающие от него частицы а также наличие СОЖ. К числу важнейших мероприятий обеспечивающих безопасность шлифовальщика относятся следующее соответствующее исполнение электрооборудования применение надёжных защитных и предохранительных устройств а также средства индивидуальной защиты.
Наиболее вероятным моментом получения травм рабочими обслуживающими фрезерные станки являются: Установка приспособлений и инструментов на станках наладка станка и удаление стружки.
Не допускается установка неисправной фрезы особенно с ненадёжно закреплёнными выкрошенными зубьями. Необходимо обеспечить жесткость закрепления фрезы на шпинделе прочное и надёжное закрепление заготовки в приспособлении. Подводить фрезу к заготовке следует постепенно без удара. При возникновении вибраций необходимо остановить станок проверить исправность гидросистемы станка крепёжных приспособлений крепление оправки фрезы. Останавливая станок сначала надо выключить подачу затем вращение шпинделя.
6.1 Расчет вентиляции и освещения на участке.
Вентиляцией называется организованный и регулярный воздухообмен обеспечивающий удаление из помещения воздуха «отработанного» и подачу свежего. По способу перемещения воздуха различают системы естественной механической и смешанной вентиляции.
Естественная вентиляция осуществляется за счет форточек фрамуг окон.
Площадь форточек принимается 6 размере не менее 2 4% площади пола.
Необходимый воздухообмен для всего производственного помещения в целом определяется:
Где п- число работающих в помещении чел
При правильно организованной вентиляции кратность воздухообмена должна быть от 1 до 10
Степень освещенности того или иного производственного помещения зависит от вида работ выполняемых в данном помещении. В производственном помещении предусматривается естественное и искусственное освещение.
Расчет естественного освещения.
Естественное освещение обеспечивается устройством окон и зенитных фонарей в крыше. Суммарная площадь окон определяется по формуле:
где Fn - площадь пола участка; Fn = 3432 м2
α - удельная площадь окон приходящаяся на 1 м2 пола; α = 01;
- коэффициент учитывающий потери света от загрязнения остекления; =06.
Расчет числа окон производится по формуле:
где Fок - площадь одного окна;
Fок = bок × hок (м2)
hок = H - (hпод + hнад) м
где Н - высота здания цеха; Н = 10 м
hпод - расстояние от пола до подоконника; hпод = 08;
hнад - расстояние от потолка до окна; hнад = 03 м.
Высота окна должна быть кратна 06 м.
hок = 10 - (08 + 03) = 89 м
Принимается hок = 9м
Расчет искусственного освещения.
Принимается значение освещённости Е=200 Лк
Суммарная мощность ламп определяется по формуле:
где Pу - удельная мощность осветительной установки; при высоте подвеса светильника 6 м площади пола Fуч = 402 м2 и освещенности Е = 200 Лк Ру = 166 Втм2.
ΣNл =1663432=6673 Вт
Выбирается мощность одной лампы. Люминесцентная лампа Nл =30 150 Вт.
Принимается Nл=150 Вт
Число ламп рассчитывается по формуле:
=44Принимается 44 штуки.
Расход электроэнергии на освещение:
Wосв = Tосв × ΣNл кВт (71)
где Tосв - годовое время работы освещения для географической широты 55о и работы в одну смену Tосв = 800 ч.
Wосв = 2800 × 6673= 10676800Вт=106768кВт
6.2 Электробезопасность u пожарная безопасность
Условием обеспечения электробезопасности является высокая техническая грамотность и дисциплина труда электротехнического персонала строгое соблюдение правил и инструкций.
При использовании электроинструментов запрещается передавать его другим лицам разбирать и самим ремонтировать работать с приставных лестниц работать на открытом месте под дождем или снегопадом оставлять его без надзора включенным в электрическую сеть.
На предприятиях следует заземлять емкости с горючими жидкостями; электрокары используемые для перевозки сосудов с горючими жидкостями и т.д.
Использование мер противопожарной защиты на объекте зависит от его особенностей (характер и особенности объекта его местоположение и размеры материальные ценности и вид оборудования) и от требований действующих норм. Все применяемые меры противопожарной защиты можно условно разделить на пассивные и активные.
Пассивные меры защиты сводятся к рациональным архитектурно-планировочным решениям. Ещё на стадии проектирования необходимо предусмотреть удобство подхода и проникновения в здание пожарных подразделений; уменьшение степени опасности распространения огня между этажами отдельными помещениями и зданиями промышленного объекта; конструктивные меры обеспечивающие незадымляемость зданий; рациональное использование производственного освещения и т.д.
К активным мерам защиты относят- системы автоматической пожарной сигнализации; установки автоматического пожаротушения; техническое оборудование первой пожарной помощи; специальные средства подавления пожаров и взрывов промышленных объектов; вспомогательное оборудование использование пожарными подразделениями.
К первичным средствам пожаротушения относятся огнетушители ведра
ёмкости с водой ящики с песком ломы топоры лопаты кошма и т.д. Размещают огнетушители в легкодоступных местах.
В дипломном проекте для зашиты от пожара используется функционально автоматическая пожарная сигнализация которая состоит из приемно-контрольной станции соединенной через сигнальные линии с пожарными извещателями. Задачей сигнальных извещателей является преобразование различных проявлений пожара в электрические сигналы. Приемно-контрольная станция после получения сигнала от первичного извещателя включает световую и звуковую сигнализацию и при необходимости автоматические установки пожаротушения и дымоудаления.
7 Охрана окружающей среды
Проблема охраны окружающей среды и рационального использования природных ресурсов является одной их наиболее актуальных среди глобальных общечеловеческих проблем так как от её решения зависит жизнь на земле здоровье и благосостояние человечества.
Определенную долю в загрязнении окружающей среды вносят и машиностроительные предприятия. Для снижения вредного воздействия машиностроительного завода на окружающую среду при проектировании строительстве и эксплуатации должны выполняться природоохранительные мероприятия.
Вокруг предприятия должна быть санитарно-защитная зона шириной не менее 50м. Эту зону озеленяют и благоустраивают. Зелёные насаждения обогащают воздух кислородом поглощают углекислый газ шум очищают воздух от пыли и регулируют микроклимат.
Производство с вредными выделениями (окрасочный кузнечно-рессорный деревообрабатывающий и другие участки) по возможности сосредотачивают в филиалах на окраине города.
С целью поддержания чистоты атмосферного воздуха в пределах норм на предприятии предусматривают предварительную очистку вентиляционных и технологических выбросов с их последующим рассеиванием в атмосферу.
Воздух удаляемый из окрасочного отделения с применением пульверизационной окраски перед выбросом в атмосферу очищают в гидрофильтрах. Очистка в них происходит за счет улавливания загрязняющих воздух веществ водой.
Для очистки воздуха удаляемого из сушильных камер применяют дожигание или каталитическое дожигание. В первом случае пары растворителей содержащиеся в воздухе сгорают в струе горящего природного газа. Во втором случае - загрязнённый воздух нагревается до температуры 4000С и подается на катализатор где и происходит дожигание вредных газообразных примесей.
Очищают воздух от древесной пыли образующейся в деревообрабатывающих цехах и шлифовальных станках с помощью циклонов: в них пыль отделяется от запылённого воздуха под действием центробежных сил и тканевых фильтров.
Для очистки воздуха от сварочного аэрозоля выделяемого при сборке используют мокрые пылеуловители например барбатеры где загрязнённый воздух в виде пузырьков проходит через слой жидкости и очищается. Могут быть использованы и пластинчатые электрофильтры в которых частицы пыли получают электрический заряд и оседают на электроде.
8 Удаление отходов производства с участка.
Удаление отходов металлической стружки с участка производится механически при этом выбор способа удаление и переработку отходов производства учитывают разновидность отходов их массу и тару в которой они транспортируются.
Для удаления стружки из рабочей зоны современные станки имеют специальные устройства которые перемещают стружку в короб или люк расположенные с тыльной стороны станка. Дальнейшее транспортирование стружки осуществляется с помощью шнекового транспортёра расположенного ниже уровня пола к разгрузочному люку а оттуда в специальный бункер. В системе удаления стружки предусмотрены стружкодробительные мельницы стружка упаковывается в блоки и транспортируется с помощью электрокара на переработку.
Для облегчения транспортировки стружки желательно чтобы её длина не превышала 200мм а диаметр витка был не более 25 30мм. Стружка на участке должна быть удалена своевременно чтобы не занимать производственной площади
ЭКОНОМИЧЕСКИЙ РАЗДЕЛ
1 Определение стоимости основных и оборотных фондов участка
Экономическая часть дипломного проекта выполняется с целью расчета всех экономических затрат на производство продукции активное участие в формировании этих расходов принимают основные и оборотные фонды предприятий.
Основные производственные фонды (ОПФ) - это средства труда которые в процесс производства используются многократно постепенно изнашиваются не изменяют свою натуральную форму и переносят свою стоимость на себестоимость продукции по частям в виде амортизационных отчислений.
Классификация основных производственных фондов:
- передаточные устройства;
- силовые машины и оборудование;
- измерительные и регулирующие приборы и устройства не установленные непосредственно на агрегатах и машинах лабораторное оборудование;
- транспортные средства (средства передвижения грузов);
- производственный и хозяйственный инвентарь.
Определяется стоимость здания
Сзд. = V·Цпом. р(72)
где Цпом. - цена помещения за 1 .м3 р.
С зд. = 3432·24600=84427200 руб.
Стоимость оборудования определяется по ведомости оборудования (с учетом доставки установки стоимость которой примем 10 % от стоимости оборудования)
Соб. = Цоб. + 01 ·Цоб р (73)
Соб. = 17253840+17252384001 = 18979224 р.
Стоимость приспособлений можно принять 10% от стоимости оборудования
Спр = 01 · Соб р(74)
Спр. = 0118979224=18979224 р.
Стоимость инвентаря (принимается 1% от стоимости оборудования)
Синв. = 001 · 18979224=18979224 р.
Таблица 5.1 -Стоимость основных фондов участка и расчет амортизационных отчислений
Стоимость ОПФ тыс.руб.
Амортизационные отчисления
Расчет амортизационных отчислений выполнен линейным способом исходя из первоначальной стоимости основных фондов и норм амортизации исчисленных с учетом срока полезного использования основных средств.
Оборотные средства-это активы предприятия которые в процессе производства участвуют однократно входят в состав готовой продукции и переносят свою стоимость на себестоимость готовой продукции полностью постоянно изменяя свою натуральную форму.
Оборотные фонды подразделяются на: производственные запасы в состав которых входят сырье основные и вспомогательные материалы топливо и энергия на технологические цели запасные части малоценные и быстроизнашивающиеся предметы покупные полуфабрикаты и комплектующие изделия.
Определяется стоимость основных материалов на производственную программу по формуле:
где m - масса заготовки кг.;
N - готовая программа выпуска шт.;
Цмат = стоимость основных материалов.
В=67007815832=8273830 руб.
Стоимость основных материалов вычисляется с учетом транспортно - заготовительных расходов (5% от стоимости основных материалов).
Стоимость основных материалов в расчете на 1 изделие:
Ц1=78·15832=12349 р.
Определение массы отходов на одно изделие:
- масса заготовки кг.;
- масса отходов кг.;
Определение стоимости отходов на одно изделие:
Сотх=4862·39=18962 р.
Определение стоимости отходов на партию:
Сотх=670018962=1270454 р.
Стоимость материала на одно изделие:
М=12349-18962=104528 р.
Стоимость материалов на программу:
Мпр=6700×104528=7003376 р.
Стоимость вспомогательных материалов на одно изделие начисляется как 1% от стоимости материала.
Мвсп1=104528·001=1045 р.
Мвсп=67001045=70015 р.
Расчёт потребности во всех видах энергии.
По формуле определяется стоимость потребной силовой энергии:
где - суммарная мощность эл. двигателей кВт;
- действительный фонд времени работы оборудования ч;
- средний коэффициент загрузки оборудования;
- коэффициент учитывающий одновременную работу электродвигателей;
- коэффициент учитывающий потери энергии в сети;
- коэффициент учитывающий потери энергии в двигателе;
Ц - цена 1 кВт энергии р.
Стоимость осветительной энергии:
где - осветительный период ч.;
S - площадь участка кв.м.;
- норма освещения кВтч. (002 кВтч)
Ц - цена 1 кВт энергии р.;
Стосв. = 350002343237 = 88889 р.
Определение стоимости воды на бытовые нужды:
где - количество рабочих дней в периоде ;
R- численность всех работающих на участке чел.;
- норма потребления воды л.;
Ц - цена 1т. воды для бытовых нужд р..
Определение стоимости воды для технических нужд:
где - годовой расход води на один станок м3.
- коэффициент загрузки оборудования;
m - число смен работы оборудования;
К - количество оборудования работающего с водой на технические цели; шт.
- стоимость 1 м3. технической воды р.
С т.в. = 00659286059286 = 3601 р.
Определение стоимости сжатого воздуха:
где - количество станков с пневматическими зажимами;
- количество станков с применением обдувки;
q - расход сжатого воздуха на один станок с пневматическим зажимом (01 м3.ч.);
q'- расход сжатого воздуха на один станок с обдувкой (1 м3.ч.)
- цена 1.м3. сжатого воздуха р.
С ст.в. = 5928059150115122 = 960 р.
Определение стоимости отопления:
где - удельный расход теплоты
- отопительный период 4320 ч. за год;
V- объем помещения м3.
Ц- цена горячей воды за 1т. р.
Определение стоимости энергетических ресурсов на технологические цели на программу:
С эр. = 181845+3601+960=186406 р.
Определение стоимости энергетических ресурсов на 1 деталь:
Определение стоимости материальных затрат на программу с учетом осветительной энергии воды на бытовые нужды и отопление:
Определение затрат на осветительную энергию воды на бытовые нужды отопление:
Ст=Сосв+Ст.вб+Сtwo=88889+86906+126316=2221109 р
2 Определение фонда оплаты труда для работающих на участке.
Определение ФОТ основных рабочих:
Прямой ФОТ о. р = Р сд N руб.
Прямой ФОТ = 67007972 = 534124 р.
5 Рсд=23496660=38 руб.
0Рсд = 3296660=52 руб.
5 Рсд = 3296660=52 руб.
0 Рсд = 31296660=502 руб.
0 Рсд = 78788460=116 руб.
5 Рсд = 9796660=156 руб.
5 Рсд = 24788460=36 руб.
0 Рсд = 24988460=37 руб.
5 Рсд = 3588460=52 руб.
5 Рсд = 121388460=54 руб.
0 Рсд = 3296660=52 руб.
5 Рсд = 33688460=50 руб.
0 Рсд = 3588460=52 руб.
Расчет основного ФОТ основных рабочих
ФОТ о.р. = ФОТ пр Кд где(87)
Кд - коэффициент доплаты за условия труда
ФОТ осн = 185 534124 = 988129 руб.
Расчет общего ФОТ основных рабочих
ФОТ о.р. = ФОТ осн Кд (88)
где Кд - коэффициент доплаты за отпуск
ФОТ общ = 988129 13 = 1284568 руб.
Определение ФОТ вспомогательных рабочих:
Прямой Фот всп = Тс Fдр R всп. р. где(89)
Fдр - фонд рабочего времени;
Rвсп. р. - количество вспомогательных рабочих
ФОТ пр = 1128987129 =227258 руб.
Основной ФОТ вспомогательных рабочих
ФОТвсп = ФОТпр Кдопл(90)
ФОТ = 227258 16= 363613 руб.
Общий ФОТ вспомогательных рабочих
ФОТвсп = ФОТосн Кд(91)
ФОТвсп = 13 363613= 472697 руб.
ФОТ спец = 2116100=32200 руб.
ФОТ общ = 1932200=61180 руб.
Расчет общего ФОТ по всем категориям работающих:
ФОТ = ФОТ общ осн. р. + ФОТ общ. Всп. р. + ФОТ общ.АУП
ФОТ = 1284568+472697+61180 = 1818445 руб.
Определение заработной платы по категориям:
ЗП =ФОТобщ R Тпл(92)
Где R - численность в соответствующей категории; чел
Тпл - плановый период месяц.
Вспомогательные рабочие:
3 Расчет общепроизводственных и общехозяйственных расходов.
К общепроизводственным расходам относятся: амортизация зданий и сооружений цехового назначения; амортизация основных фондов; заработная плата вспомогательных рабочих и административно управленческого персонала с отчислениями на социальные нужды и т.п.
Таблица 5.2 - Смета общепроизводственных расходов
Наименование статьи затрат
Амортизация оборудования
Содержание оборудования
Затраты на энергетические ресурсы
Содержание специалистов и вспомогательных рабочих
Отчисления на социальное страхование:
Вспомогательных рабочих
Износ инструментов и приспособлений сроком эксплуатации до 12 месяцев
50 р. в расчете на 1-го основного рабочего
Амортизация приспособлений и инвентаря
Расходы на рационализаторство изобретательство
00 р. в расчете на1-го работающего
Расходы по охране труда и технике безопасности
00 р. на 1-го работающего
Итого общепроизводственные расходы
Процент общепроизводственных расходов:
где ОР - сумма общепроизводственных расходов;
- основной фонд оплаты труда основных рабочих.
Общепроизводственные расходы на 1 деталь:
Общехозяйственные расходы - комплексная статья затрат в ее состав входит заработная плата управленческого персонала всего завода; амортизация зданий сооружений о6орудования производственного назначения и т.д.
Общехозяйственные расходы составляют 350% от ФОТосн.осн рабочих.
Общехозяйственные расходы на участке составят:
РО = 35·988129=3458452 р.
Общехозяйственные расходы на 1 деталь:
4. Определение себестоимости детали составление калькуляции и сметы затрат на производство продукции
Таблица 5.4 – Смета затрат на производство
Себестоимость продукции - затраты связанные с производством и реализации продукции. Классификация по ряду признаков:
По способу отнесения затрат на себестоимость - прямые косвенные;
По степени участия в производственном процессе - основные накладные;
В зависимости от объема - условно-переменные и условно-постоянные;
В зависимости от состава - простые (элементные) и сложные (комплексные).
При определении себестоимости изделия используется группировка затрат которая называется калькуляцией.
Расходы на продажу включают в себя затраты на упаковку доставку до станции отправления оплату дилеров посредников и других расходов.
Определение себестоимости детали по статьям калькуляции и экономическим элементам.
Материальные затраты
Расходы на оплату труда
Отчисления на социальные нужды
Амортизация основных фондов
Сырье и основные материалы
Транспортные расходы
Вспомогательные материалы
Энергетические ресурсы
Итого материальные затраты
Основная заработная плата рабочих
Дополнительная заработная плата рабочих
% от ЗП основных рабочих
Отчисление на социальное страхование
Общепроизводственные расходы
Общехозяйственные расходы
Итого производственная себестоимость
% от произ. себестоимости
Итого полная себестоимость
% от полной себестоимости
Таблица 5.3 - Калькуляция детали
5 Сводная ведомость показателей деловой активности.
Таблица 5.5 – Основные технико-экономические показатели деловой активности участка
Наименование показателя
Программа выпуска шт
Товарная продукция в оптовых ценах р.
Средняя загрузка оборудования %
Общая мощность эл. двигателей кВт·ч
Общая численность работающих чел:
Основных производственных рабочих
Среднемесячный доход р.
- 1 основного рабочего;
- 1 вспомогательного рабочего;
- 1 сменного мастера
Общая трудоемкость нормо-час
Производительность труда
Фондовооруженность руб.чел
Коэффициент использования материала
Рентабельность изделия %
Рентабельность продаж %
Товарная продукция определяется по формуле:
ТП=Цопт N = 6700 310825 = 20825275 руб.
Общая трудоемкость рассчитывается
Производительность труда рассчитывается в нормо – часах
в рублях П = руб.чел.
Фондовооруженность рассчитывается:
Коэффициент использования материла рассчитывается по формуле:
Прибыль определяется по формуле:Пб=Пб1N =51804 6700 = 3470868 р.
Рентабельность изделия рассчитывается по формуле:
Рентабельность продаж рассчитывается по формуле:
Фондоотдача определяется по формуле:
1 Технико-экономическое обоснование деловой эффективности проекта.
На спроектированном механическом участке изготавливается деталь «Вал-шестерня» 145-4215011.
Программа участка - 32500программа детали - 6700 шт.
Для изготовления деталей необходимо 26 единиц оборудования из них 15 единиц металлорежущие станки. Средняя загрузка оборудования на участке 59%.
Для выполнения заданной программы деталей необходимо 37 человек из них 25 человек основные рабочие 11 человек вспомогательные рабочие и 1 человек сменный мастер. Среднемесячный доход 1 основного рабочего 25691 руб.1 вспомогательного рабочего 21486 руб. 1 сменного мастера 30590 руб.
Общая трудоемкость изготовления программы деталей 56057 час.
Производительность 1 основного рабочего 833011 руб.чел. Коэффициент использования материала Ким=05
Оптовая цена 1 детали 310825 руб.
Прибыль от реализации программы деталей 3470868 руб. Общая площадь участка 3432 м2. Фондовооруженность характеризует оснащенность работников основными производственными фондами Фв = 2851193 руб.чел.
Список используемой литературы:
Белоусов А. П. «Проектирование станочных приспособлений» М.: Высшая школа. 1980.
Гельфоргат Ю. И. «Дипломное проектирование в машиностроительных техникумах» М.: Машиностроение. 1992.
Данилевский В.В. Справочник технолога машиностроителя. – М.: Высшая школа 1962.
Мовчин В.В. Мовчин С.В. Сборник задач по техническому нормированию труда в механических цехах. М.: Машиностроение. 1989.
Общемашиностроительные нормативы времени и режимов резания для нормирования работ выполняемые на универсальных и многоцелевых станках с числовым программным управлением. Часть 1 М.: Экономика труда. 1990.
Общемашиностроительные нормативы режимов резания для технического нормирования работ на металлорежущих станках. Часть 2 3 Зубофрезерные зубодолбёжные горизонтально - расточные резьбонакатные и отрезные станки. М.: Машиностроение. 1974.
Общемашиностроительные нормативы времени вспомогательное на обслуживание рабочего места и подготовительно - заключительного для технического нормирования станочных работ. Серийное производство. М.: Машиностроение. 1984.
Справочник технолога - машиностроителя. Том 1. Под редакцией А. Г. Косиловой и Р. К. Мещерякова. М.: Машиностроение 1986.
Справочник технолога - машиностроителя. Том 2. Под редакцией А. Г. Косиловой и Р. К. Мещерякова. М.: Машиностроение 1986.
Общие машиностроительные нормативы времени и режимы резания на станках с ЧПУ.-М.:Машиностроение1980 г.
Курсовое проектирование по технологии машиностроения .Под редакцией А.Ф. Горбацевича-М.;Машиностроение 1974г.
Технологический классификатор деталей машиностроения и приборостроения. М.: издательство стандартов. 1987.
деталь, и загатока.frw
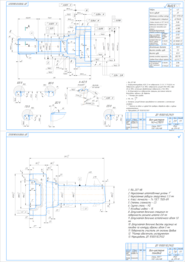
Поверхности зубьев 57 64 HRCэ
поверхности шлицев 51min HRCэ
остальные обработанные поверхности 47min HRCэ.
Не допускаются на поверхностях трещины
забоины и др. дефекты.
Размеры для справок.
Контроль шлицев должен производится по элементам и комплексным
Заточка на одном из зубьев для проверки твердости ядра и глубины
Маркировать ДП 151.001.10.29.01
Неуказанные штамповочные уклоны 7
Неуказанные радиусы закруглений 3 5 мм.
Класс точности - Т4 ГОСТ 7505-89.
Степень сложности - С3.
Исходный индекс - 15.
Допускаемая величина смещения по
поверхности разъема штампа 0
Допускаемая величина остаточного облоя 1
Допускаемая величина высоты заусенца на
поковке по контуру обрезки облоя 5 мм.
Поверхность очистить от окалины дробью.
*Размер обеспечить инструментом.
Маркировать ДП 151001.10.29.02
Нормальный исходный контур
Коэффициент смещения
Степень точности по ГОСТ 1643-81
Предельные отклонения изме-
рительного межосевого рас-
Наименьшее дополнительное
смещение исходного контура
Допуск на колебания
Суммарное пятно кон-
Диаметр основной окружности
Средняя длина общей нормали
Измерительные разме-
ДП 151001.01.08.00.01
ДП 151001.01.08.00.02
карты наладок.frw
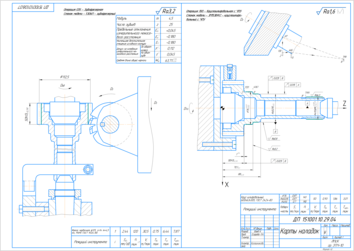
Станок модели - 5306П - зубофрезерный
Предельные отклонения
измерительного межосе-
Наименьшее дополнительное
смещение исходного контура
Допуск на колебания
Средняя длина общей нормали
Фреза червячная ф125
Операция 100 - Круглошлифовальная с ЧПУ
Станок модели - 3М153ВФ2 - круглошлифо-
РТК.frw
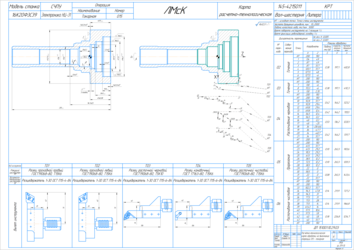
карта обработки на выполнение
опереации 015 - токарная
расчетно-технологическая
ИТ - исходная точка. Точка смены инструмента
Частота вращения шпинделя
Подача холостого хода
Время поворота инструмента на 1 позицию 1 с
Время фиксации револьверной головки 1 с
Дискретность перемещения
Растачивание черновое
Растачивание чистовое
Резец проходной правый
Резец проходной левый
Резец расточной черновой
Резец расточной чистовой
Резцедержатель 1-30 ОСТ П15-4-84
Резцедержатель 1-30 ОСТ П15-6-84
приспособление зубофасочное.frw
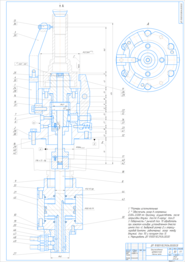
*Размеры исполнительные.
Обеспечить зазор в сопряжении
8 мм. Пригонку осуществлять после
заприсовки втулки (поз.14) в корпус (поз.2).
Поверхность Г рычагов (поз. 11) обработать
установленном вместо
выдержав размер Д и отрегу-
лировав винтами равномерный зазор между
втулкой (поз. 15) и ползуном (поз. 5).
Маркировать ДП 151001.10.29.04.00.00
ДП 151001.01.08.04.00.00.СБ
калибр скоба 05.cdw
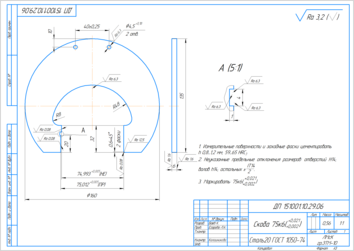
Измерительные поверхности и заходные фаски цементировать
Неуказанные предельные отклонения размеров: отверстий
Фреза червячная м=4,5.cdw
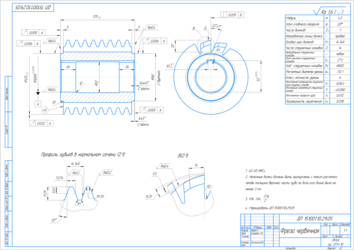
чтобы толщина верхней части зуба по всей его длине была не
Маркировать ДП 151001.10.29.05
Угол главного профиля
Направление линии витка
Число стружечных канавок
Направление стружечных
Угол наклона стружечных
Ход стружечных канавок
Расчетный диаметр фрезы
Класс точности фрезы
Накопленная погрешность окружного
шага окружных канавок
Отклонение направления стружечных
Отклонение профиля зуба
Погрешность зацепления
Профиль зубьев в нормальном сечени (2:1)
График загрузки, план участка.frw
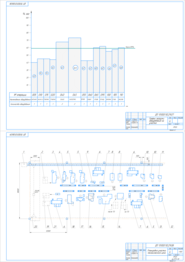
калибр скоба 05.cdw
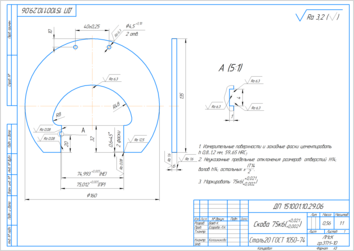
Измерительные поверхности и заходные фаски цементировать
Неуказанные предельные отклонения размеров: отверстий
карты наладок.frw
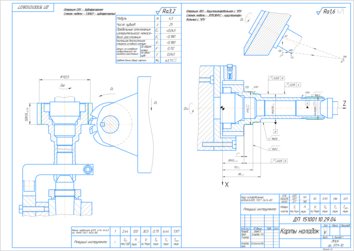
Станок модели - 5306П - зубофрезерный
Предельные отклонения
измерительного межосе-
Наименьшее дополнительное
смещение исходного контура
Допуск на колебания
Средняя длина общей нормали
Фреза червячная ф125
Операция 100 - Круглошлифовальная с ЧПУ
Станок модели - 3М153ВФ2 - круглошлифо-
контрольное.frw
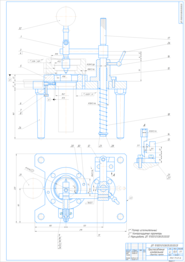
Размер исполнительный.
Контролируемые параметры.
Маркировать ДП 151001.01.08.05.00.00
приспособление зубофасочное.frw
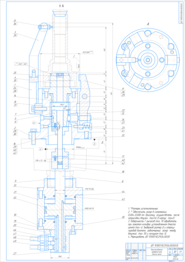
*Размеры исполнительные.
Обеспечить зазор в сопряжении
8 мм. Пригонку осуществлять после
заприсовки втулки (поз.14) в корпус (поз.2).
Поверхность Г рычагов (поз. 11) обработать
установленном вместо
выдержав размер Д и отрегу-
лировав винтами равномерный зазор между
втулкой (поз. 15) и ползуном (поз. 5).
Маркировать ДП 151001.10.29.04.00.00
ДП 151001.01.08.04.00.00.СБ
РТК.frw
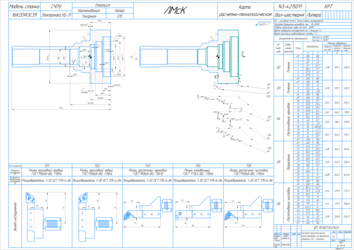
карта обработки на выполнение
опереации 015 - токарная
расчетно-технологическая
ИТ - исходная точка. Точка смены инструмента
Частота вращения шпинделя
Подача холостого хода
Время поворота инструмента на 1 позицию 1 с
Время фиксации револьверной головки 1 с
Дискретность перемещения
Растачивание черновое
Растачивание чистовое
Резец проходной правый
Резец проходной левый
Резец расточной черновой
Резец расточной чистовой
Резцедержатель 1-30 ОСТ П15-4-84
Резцедержатель 1-30 ОСТ П15-6-84
спецефик для контрольного.doc
ДП 151001.01.08.04.01.00.СБ
ДП 151001.01.08.04.02.00.СБ
Передача индикаторная
ДП 151001.01.08.04.00.01
ДП 151001.01.08.04.00.02
ДП 151001.01.08.04.00.03
ДП 151001.01.08.04.00.04
ДП 151001.01.08.04.00.05
ДП 151001.01.08.04.00.06
ДП 151001.01.08.04.00.07
ДП 151001.01.08.04.00.08
ДП 151001.01.08.04.00.09
ДП 151001.01.08.04.00.10
ДП 151001.01.08.04.00.11
ДП 151001.01.08.04.00.12
ДП 151001.01.08.04.00.13
ДП 151001.01.08.04.00.14
ДП 151001.01.08.04.00.15
ДП 151001.01.08.04.00.16
ДП 151001.01.08.05.00.00
Винт ВМ5-8g x20.58.05
Кольцо А20 ГОСТ 13942-86
Ведомость ДП.spw
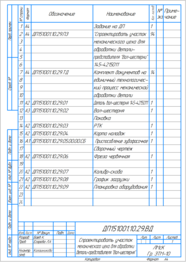
механического цеха для обработки
детали-представителя "Вал-шестерня
Спроектировать участок
механического цеха для
представителя "Вал-шестерни
Комплект документов на
единичный технологичес-
кий процесс механической
Деталь вал-шестерня 145-4215011
ДП151001.10.29.05.00.00.
Приспособление зубофасочное
Планировка оборудования
График загрузки, план участка.doc
Бункер для заготовок
Полуавтомат токарный с ЧПУ 1А734Ф3
Станок токарный патронно-центровой 16К20Ф3С32
Зубофрезерный полуавтомат 53А20
Шлицефрезерный горизонтальный полуавтомат 5А352ПФ2
Станок зубозакругляющий 5Е580
Зубофрезерный полуавтомат 5306П
Станок зубошевинговальный 5702В
Торцекругло-шлифовальный врезной автомат 3Т161Д
Круглошлифовальный автомат с ЧПУ 3М151Ф2
Станок круглощлифовальный 3Т160
Станок внутришлифовальный 3К225В
Бункер готовой продукции
Кран мостовой одноблочный
Планировка участка механического цеха
спецефик для приспособление зубофасочное.doc
ДП 151001.10.29.04.00.CБ
ДП 151001.10.29.04.00.01
ДП 151001.10.29.04.00.02
ДП 151001.10.29.04.00.03
ДП 151001.10.29.04.00.04
ДП 151001.10.29.04.00.05
ДП 151001.10.29.0400.06
ДП 151001.10.29.04.00.07
ДП 151001.10.29.04.00.08
ДП 151001.10.29.04.00.09
ДП 151001.10.29.04.00.10
ДП 151001.10.29.04.00.11
ДП 151001.10.29.04.00.12
ДП 151001.10.29.0400.13
ДП 151001.10.29.04.00.14
ДП 151001.10.29.04.00.15
ДП 151001.10.29.04.00.16
ДП 151001.10.29.04.00.17
ДП 151001.10.29..04.00.18
ДП 151001.10.29.04.00.19
ДП 151001.10.29.04.00.00
ДП 151001.10.29..04.00.20
ДП 151001.10.29.04.00.21
ДП 151001.10.29.04.00.22
ДП 151001.10.29.04.00.23
ДП 151001.10.29.04.00.24
ДП 151001.10.29.04.00.25
ДП 151001.10.29.04.00.26
Болт М12-6g x40.58.05
Винт BM16-6g x40.14H.05
Винт М10-6g x20.58.05
(d-04xD5xHo-23xt-183)
9(d-10xD-13xHo-47xt-4732)
Гайка накидная 10-22
Труба ДКРНМ 10 х1НДМ2
ДП 151001.10.29.00.00
допуски на пробки.frw
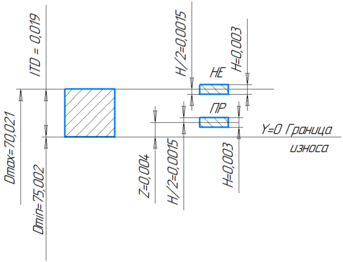
карта эскизов 040.frw
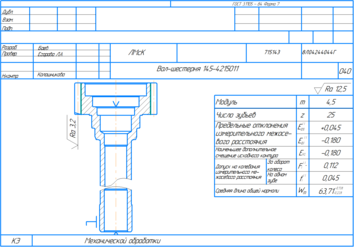
измерительного межосе-
Наименьшее дополнительное
смещение исходного контура
Допуск на колебания
Средняя длина общей нормали
ГОСТ 3.1105 - 84 Форма 7
Механической обработки
Вал-шестерня 145-4215011
карта эскизов 045.frw

Механической обработки
Вал-шестерня 145-4215011
*-размер для справок
карта эскизов 065.frw
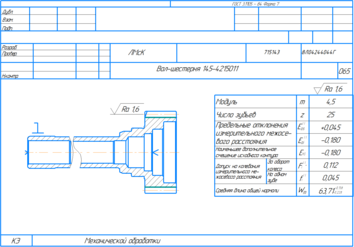
измерительного межосе-
Наименьшее дополнительное
смещение исходного контура
Допуск на колебания
Средняя длина общей нормали
ГОСТ 3.1105 - 84 Форма 7
Механической обработки
Вал-шестерня 145-4215011
карта эскизов005.frw
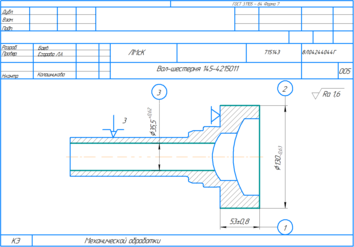
Механической обработки
Вал-шестерня 145-4215011
Операционная 005.doc
Сталь 25ХГТ ГОСТ 4543-71
Оборудование устройство ЧПУ
Обозначение программы
Установить заготовку закрепить. Выставить инструмент относительно баз приспособления точностью 005 мм.
6100 ХХХХ Патрон 3-х кулачковый кулачки К9687-4204005
Точить торец в размер 1 точить пов-ть в р-р 2 напроход.
1895 ХХХХ Резец токарный проходной левый черновой с механическим креплением пластины ГОСТ 19056-80 Т15К10 395245ХХХХ резцедержатель
Центровать отверстие 3.
1895 ХХХХ Сверло центровочное комбинированное ф63 ГОСТ 14952-75 Р6М5 39 1782ХХХХ патрон для сверла.
Сверлить отверстие 3.
1895 ХХХХ Сверло ф20 2301-0069 ГОСТ Р6М5 10903-77 39 1782ХХХХ патрон для сверла.
Механической обработки
1895 ХХХХ Сверло ф355 2301-0123 ГОСТ 10903-77 Р6М5 39 1782ХХХХ патрон для сверла.
Снять заготовку. Контроль размеров.
3311 ХХХХ Штангенциркуль ШЦ-1-250-01 ГОСТ 166-80
Операционная 040.doc
Сталь 25ХГТ ГОСТ 4543-71
Оборудование устройство ЧПУ
Обозначение программы
Зубофрезерный -полуавтомат 53А20
Установить заготовку закрепить. Выставить инструмент относительно баз приспособления точностью 005 мм.
6100 ХХХХ Наладка зубофрезерная.
Фрезеровать зубья согласно таблице эскиза.
1895 ХХХХ Фреза червячная ф125 z=14 m=45 мм Р6М5 ГОСТ 9324-80 39 1782ХХХХ оправка для фрезы.
Снять заготовку. Контроль размеров.
3311 ХХХХ приспособление при станке Межосиметр МЦ-400.0001 эталон.
Механической обработки
Операционная 045.doc
Сталь 25ХГТ ГОСТ 4543-71
Оборудование устройство ЧПУ
Обозначение программы
А352ПФ2 – шлицефрезерный горизонтальный полуавтомат
Установить заготовку закрепить. Выставить инструмент относительно баз приспособления точностью 005 мм.
6100 ХХХХ Наладка при станке.
Фрезеровать шлицы выдержав размеры 1-4.
1895 ХХХХ Фреза червячная шлицевая ф70 мм ГОСТ 9489-37
Снять заготовку. Контроль размеров.
3311 ХХХХ Штангенциркуль ШЦ-1-250-01 ГОСТ 166-80 Скоба ф445-025. колибр-кольцо шлицевый комплексный 9566-2122.
Механической обработки
Операционная 065.doc
Сталь 25ХГТ ГОСТ 4543-71
Оборудование устройство ЧПУ
Обозначение программы
Полуавтомат зубошевинговальный 5702В
Установить заготовку закрепить.
6100 ХХХХ Наладка при станке.
Шевинговать зубья согласно эскиза.
1895 ХХХХ Шевер дисковый 180 m=45 Р18 ГОСТ 8570-80.
Снять заготовку. Контроль размеров.
3311 ХХХХ Штангенциркуль ШЦ-1-250-01 ГОСТ 166-80 Центр грибковый 9572-3157 колесо измерительное 9588-1742.
Механической обработки
тех.процесс.doc
Сталь 25Х ГТГОСТ 4543-71
Код и наимен. операции
Обозначение документа
Код наименование оборудования
5 4233 Токарная с ЧПУ ИОТ№ 63
0 4233 Токарная с ЧПУ ИОТ№ 63
5 4233 Токарно-винторезная с ЧПУ ИОТ№ 63
0 4233 Токарно-винторезная с ЧПУ ИОТ№ 63
5 0108 Слесарная ИОТ №84
0 0108 Моечная ИОТ № 84
Механической обработки
5 0220 Контрольная ИОТ№31
0 4165 Зубофрезерная ИОТ№73
5 4165 Шлицефрезерная ИОТ №73
5 4156 Зубозакругляющая ИОТ№ 73
0 4165 Зубофрезерная ИОТ№73
«Вал вторичный» Т25-1701252-Д
Сталь 45Х ГОСТ 4543-71
5 4157 Зубошевинговальная ИОТ№ 73
0 0220 Контрольная ИОТ№31
5 5030 Термическая ИОТ № 76
Наименование детали сб.единицы или материала
0 4256 Зубообкаточная
5 4146 Торцекруглошлифовальная ИОТ № 76
0 4125 Круглошлифовальная с ЧПУ ИОТ№76
5 4125 Круглошлифовальная с ЧПУ ИОТ№76
0 4125 Внутришлифовальная с ЧПУ ОТ№76
техконтколь125.doc
«Вал-шестерня» 145-4215011
Наименование операции
Наименование марка материала
Сталь 25ХГТ ГОСТ 4543-71
Наименование оборудования
Контролируемые параметры
Наименование средств ТО
Образцы шероховатости ГОСТ 9378-75
Размер 3 10 11 12 14
Штангенциркуль ШЦ-I -125-01 ГОСТ 166-80
Калибр-пробка ПР ф58Н9(+0074) 8136-0003 Н9 ГОСТ14815-69
Калибр-пробка НЕ ф58Н9(+0074) 8136-0103 Н9 ГОСТ14815-69
Калибр-пробка ПР ф72К7() 8136-0010 Н9 ГОСТ14815-69
Калибр-пробка НЕ ф72К7() 8136-010 Н9 ГОСТ14815-69
Калибр-пробка ПР ф95К7() 8136-0010 Н9 ГОСТ14815-69
Калибр-пробка НЕ ф95К7() 8136-010 Н9 ГОСТ14815-69
Приспособление контрольное
Калибр-кольцо непроходной поэлементарный 5226()
Технического контроля
Калибр-скоба 8113-5643
Проверить расположение шлиц
Калибр-кольцо шлицевый комплексный
Проверить допуск непостоянства диаметра пов-ти В
Скоба СР75 ГОСТ 11098-75
Проверит допуск радиального биения пов-ей Д и Е
Проверить допуск радиального биения пов-ти В
Прибор ПБ-250 центр грибковый 9572-3156 центр грибковый 9572-3125.
Проверить допуск радиального биения шлиц относительно пов-ти Б
Проверить точность зубчатого венца
Колесо измерительное 9588-1742 Оправка 9588-1922 центр грибковый нижний 9588-1923 верхний 9588-1925
Клеймить годную деталь
Титульник.doc
Г(О)БОУ СПО «Липецкий машиностроительный колледж»
Комплект документов на единичный
технологический процесс механической
обработки детали «Вал-шестерня»
эскиз контроля 2лист .frw
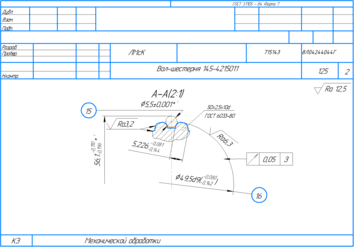
Механической обработки
Вал-шестерня 145-4215011
эскиз контроля.frw
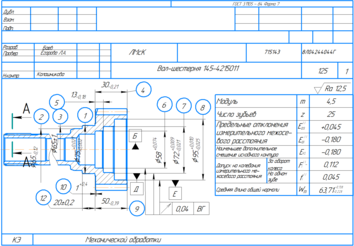
измерительного межосе-
Наименьшее дополнительное
смещение исходного контура
Допуск на колебания
Средняя длина общей нормали
ГОСТ 3.1105 - 84 Форма 7
Механической обработки
Вал-шестерня 145-4215011
2.frw
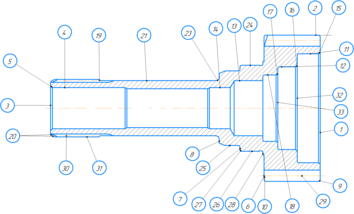
Фрагмент п.3,2.frw
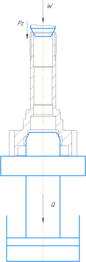
Фрагмент.frw
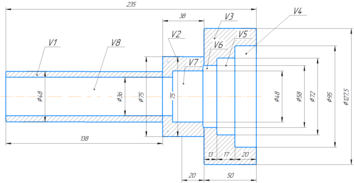
Фреза, карты наладок.frw
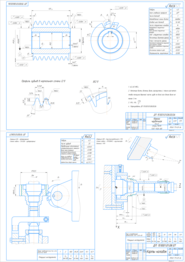
Неполные витки должны быть притуплены с таким расчетом
чтобы толщина верхней части зуба по всей его длине была не
Маркировать ДП 151.001.01.08.00.06
Операция 035 - Зубофрезерная
Станок модели - 53А20В - зубофрезерный
Угол главного профиля
Направление линии витка
Число стружечных канавок
Направление стружечных
Угол наклона стружечных
Ход стружечных канавок
Расчетный диаметр фрезы
Класс точности фрезы
Накопленная погрешность окружного
шага окружных канавок
Отклонение направления стружечных
Отклонение профиля зуба
Погрешность зацепления
Предельные отклонения
измерительного межосе-
Наименьшее дополнительное
смещение исходного контура
Допуск на колебания
Средняя длина общей нормали
Операция 085 - Круглошлифовальная с ЧПУ
Станок модели - 3М153ВФ2 - круглошлифо-
Профиль зубьев в нормальном сечени (2:1)
Рекомендуемые чертежи
- 11.03.2024
- 05.01.2022