Валковая дробилка 3




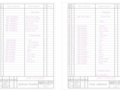

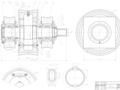
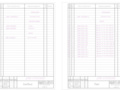
- Добавлен: 25.10.2022
- Размер: 891 KB
- Закачек: 1
Описание
Состав проекта
![]() |
![]() |
![]() ![]() ![]() ![]() |
![]() |
![]() |
![]() ![]() ![]() ![]() |
![]() ![]() ![]() ![]() |
![]() |
![]() ![]() ![]() ![]() |
![]() ![]() ![]() ![]() |
![]() |
![]() ![]() ![]() ![]() |
![]() ![]() ![]() |
![]() |
![]() ![]() ![]() ![]() |
![]() ![]() ![]() ![]() |
![]() ![]() ![]() ![]() |
![]() |
![]() ![]() ![]() |
Дополнительная информация
сборочный чертеж 3414234 07.dwg

Сварные швы по ГОСТ 5262-80. Наплавленный металл типа Э42А
* Размеры для справок
Сварные швы по ГОСТ 5264-80. Электрод Э-50А ГОСТ 9467-75
Сварные швы по ГОСТ 5264-80. Наплавленный металл типа Э50А
07-4.dwg

х30х368 ГОСТ 19803-74
Бст4 сп ГОСТ 8731-70
Плита верхняя.dwg

Предохранитель Е27В1
Датчик ВП15Д21Б111-54
07-2.dwg

Шпилька 10-6дх110.58
Шпилька 10-6дх75.58
Редуктор Ц2У-160-25-21У2
А112У3 ГОСТ 15150-69
07-3.dwg

Шпилька М20-6qх85.58
Двигатель 4А112МА8Р3
Выключатель кнопочный
РКВ 11-33-ТУХЛ4 220В
Описание принципиальной
упровления приводом
07.dwg

Технологическая схема
Экономические расчеты
Пояснительная записка
07 -1.dwg

Валок подвижный+.dwg

Дробилка валковая07.dwg

Частота вращения валков
Техническая характеристика
* Размеры для справок
Редуктор Ц2У-160-25-21 МУ2
Электродвигатель 4А112М4У3
Деталировка 2.dwg

(Modell- oder Gesenk-Nr)
БГТУ им. В. Г. Шухова
Сталь 20 ГОСТ 1050 - 74
БрАЖ 9-4 ГОСТ 18175 - 78
Неуказанные радиусы скрунглений 5мм
записка.doc
1. Технологическая схема производства 7
Специальная часть. 8
1. Конструкция и принцип действия валковой дробилки 13
2. Патентный поиск и анализ результатов. 15
3. Расчет кинематических параметров валковой дробилки 23
3.1. Определение угла захвата в валковых дробилках и соотношение
между диаметром валков и размерами поступающего
3.2. Определение числа оборотов валков 25
3.3. Определение производительности валковой дробилки 26
3.4. Определение мощности потребляемой валковой дробилкой 28
3.5. Определение усилий в частях валковой дробилки 34
3.6. Расчет вала. Определение диаметра выходного конца вала 37
3.7. Расчет подшипника 46
3.8. Расчет муфты 56
3.9. Расчет амортизирующего устройства 58
3.10. Расчет шпоночного соединения 61
4.. Эксплуатация и ремонт валковой дробилки. 64
Электрическая часть. 66
1.Схема силовых цепей 66
2.Схема управления 66
2.1Управление двигателем транспортера загрузки 67
БГТУ им. В.Г. Шухова
2.2.Управление двигателями дробилки 67
2.3. Запуск транспортера загрузки 68
3. Схема сигнализации 69
3.1. Световая сигнализация 69
3.2. Звуковая сигнализация 69
Безопасность жизнедеятельности 71
1.Организация охраны труда на предприятии ПСМ 71
2Характеристика и анализ производственных условий 73
3. Охрана окружающей среды 76
4.Пожарная безопасность 78
5.Мероприятия исключающие травматизм и профессиональные
6. Защита от поражения электрическим током 79
7. Расчет заземляющего устройства 82
Экономическая часть 86
1. Технико-экономическое обоснование 86
2 Оценка экономической эффективности инвестиционного проекта 88
2.1. Расчет капитальных вложений 88
2.2. Изменение текущих расходов(себестоимости продукции) по
2.3.. Изменение денежных потоков 92
2.4.. Расчет показателей экономической эффективности проекта 94
3.. Планирование себестоимости продукции и основных технико-
экономических показателей 97
3.1.Планирование себестоимости продукции 97
3.2.Корректировка основных технико-экономических показателей 101
Список литературы 105
Разработки и исследования российских ученых и специалистов в области дробильного оборудования позволили за последнее время создать более совершенные конструкции дробильных машин и разработать более строгие методы их расчета.
Основными факторами определяющими выбор схемы дробления сырьевых материалов являются физические свойства материалов и размеры кусков поступающих на измельчение.
Оптимальная степень измельчения зависит от размолоспособности сырьевых материалов: чем труднее они размалываются тем до меньших размеров куска требуется их измельчать. Дробление материалов можно производить в одну две или три стадии.
При дроблении влажных и глинистых материалов степень дробления снижается на 20-30 %. Сырьевые материалы поступающие непосредственно из карьеров обычно достигают значительных размеров (500-1500 мм) чтобы получить материал высокой степени измельчения в ряде случаев приходится дробление производить в несколько стадий в двух-трех последовательно установленных машинах. По размерам кусков конечного продукта условно различают стадии дробления:
- крупного (до кусков размером 350-100 мм);
- среднего (до кусков размером 100-40 мм);
- мелкого (до кусков размером 40-3 мм).
В решении проблем научно-технического процесса важное место занимает высшая школа научный потенциал которой широко используется как в хозяйстве страны в целом так и отдельных ее отраслях.
ТЕХНОЛОГИЧЕСКАЯ ЧАСТЬ
1.Технологическая схема производства
Независимо от применяемого оборудования и конкретной технологической схемы производства процесс изготовления керамзита состоит из следующих основных операций:
Добычи глинистого сырья его складирования и доставки к месту
Переработки сырья и приготовления исходного полуфабриката-
сырца пригодного для обжига со вспучиванием;
Обжига и охлаждения керамзита;
Сортировки и при необходимости до мола заполнителя;
Складирования и выдачи готовой продукции.
В зависимости от технологических приемов перерабатывания глинистых пород и приготовления гранулированного полуфабриката различают три способа производства керамзита: сухой пластический и мокрый.
Наиболее простым и экономичным является пластический способ. Пластический способ подготовки сырья и приготовления полуфабриката применяют при использовании уваженных пластичных и рыхлых глинистых пород как однородного так и неоднородного состава. При пластическом способе производства керамзита в глиняную массу могут вводиться добавки повышающие склонность к вспучиванию исходного сырья. Переработка вспучивающихся однородных глинистых пород по пластическому способу имеет целью их грануляцию а полуфабрикат
определенной формы с размером от 7 до 30 мм в поперечнике. Более тщательной переработки такому сырью не требуется.
Таким образом технология обработки однородных глин сводится к их грануляции. Затем полуфабрикат сушится в сушильной установке потом обжигается в печи.
Технологическая схема производства
керамзитового гравия.
Добавка (диз. топл.) Смеситель лопастной ← Вода
Накопительный бункер
Дозатор непрерывного действия
Колосниковый холодильник
Глина Терновского месторождения автотранспортом привозится на завод и разгружается в глинозапасник. Вместительность глинозапасника 4500 м2. Данного запаса хватает на 18 суток бесперебойной работы. Грейферным краном (грузоподъемность крана 5 тонн) глина попадает в приемный бункер который выполнен с рыхлителем. Рыхлителем глина разрыхляется разбиваются крупные куски. Попадая из рыхлителя на ящичный питатель глина распределяется определенным слоем на ленточный конвейер. Над ленточным конвейером расположен магнит. Он предназначен для улавливания в глине металлических включений. По ленточному конвейеру глина попадает через бункер на дырчатые вальцы (СМ 369А). Здесь происходит измельчение глины. Зазор между валками 3 мм. Производительность вальцов 40 тч. Из вальцов глина попадает на ленточный конвейер который подает ее в приемный бункер лопастного смесителя СМ-449. В смеситель подается органическая добавка (дизельное топливо солярка и т.п.); в зависимости от требуемой марки керамзита количество добавки регулируется но по массе должно составлять 1% от общей массы глины. Для марки керамзита М 400 скорость подачи дизельного топлива 37 лмин (мазута - 57 лмин). В смесителя производится перемешивание глины с добавкой. Необходимо тщательное перемешивание компонентов для создания равномерного распределения компонентов друг в друге.
Затем шихта поступает в ленточный пресс. На нем используется перфорированные решетки с диаметром отверстий 7-10 мм. Происходит формирование массы. Через отверстия продавливается масса образуются жгуты. Под собственной массой они отрываются и разбиваются на куски определенного размера. Полученный полуфабрикат попадает в приемный бункер сушильного барабана. Длина сушильного барабана 18 мм диаметр 26 м скорость вращения 38 обмин. Время прохождения материала в
сушилке 15 минут. Влажность свежесформированного полуфабриката 18-20% остаточная влажность после сушки 8-12%. После сушильного барабана полуфабрикат по трубопроводу попадает на элеватор а затем в накопительный бункер печи из него попадает в дозатор непрерывного действия. Дозатором полуфабрикат подается в печь. Печь вращающаяся с расширенным концом с увеличенной зоной вспучивания. Параметры печи 40×25×3. Производительность 10-12 м3ч (в среднем). Время прохождения материала в печи 35-45 минут. Печь вращается со скоростью 27 обмин. В печи происходит вспучивание керамзита. Температура полуфабриката поступающего в печь – 20°С а выходящего керамзита – 800°С. Вспучивание керамзита идет 1200°С. Из печи керамзит попадает в слоевой колосниковый холодильник. Время охлаждения 20 мин. Охлаждение до 700°С ведут быстро а затем медленнее до температуры 100°С. Это производится во избежание различных нежелательных превращений которые могут протекать в структуре керамзита. Дальше из холодильника охлажденный до 50-20°С керамзит попадает в валковую дробилку затем на элеватор. После материал поступает в силосы объемом 350 м3 а потом через конвейер отгрузки загружается в автотранспорт и отправляется потребителю.
1Конструкция и принцип действия валковой дробилки
Валковые дробилки применяют для среднего и мелкого дробления как твердых материалов прочностью сж ≤ 150МПа так и мягких и хрупких материалов сж ≤ 80МПа.
Основными рабочими органами валковой дробилки являются цилиндрические валки вращающиеся навстречу друг другу. Материал для измельчения подается в дробилку сверху затягивается валками раздавливается частично истирается и выгружается из нее. Для увеличения истирающего эффекта валки могут иметь разную окружную скорость вращения. Количество валков в дробилке бывает от одного до четырех. В четырехвалковой дробилке одна пара валков располагается над другой то есть в одном корпусе монтируют как бы две двухвалковые дробилки.
Рис. 2.1. Двухвалковая дробилка: 1- рама 23 – валки
– амортизационная пружина
В промышленности строительных материалов наиболее распространены двухвалковые дробилки.
Поверхности валков бывают гладкие рифленые (ребристые) и зубчатые. Сочетание дробящих поверхностей в дробилке может быть различным. Основными параметрами валковых дробилок являются Диаметр (D) и
длина (L) валков которые входят в их условное обозначение. Например дробилка с гладкими валками диаметром D = 600 мм и длиной L = 400 мм имеет обозначение ДГ-600×400 а дробилка с диаметром валков D = 400 мм – ДДЗ-4.
При одинаковом диаметре валков дробилки с рифлеными и зубчатыми валками захватывают более крупный чем дробилки с гладкими валками материал. Например наибольшая крупность исходного материала в дробилках с гладкими валками составляет 120 диаметра валка а в дробилках с рифлеными и зубчатыми валками – 16 диаметра валка.
Корпуса подшипников вала одного из валков дробилки подпружинены и могут перемещаться в результате попадания недробимого предмета. Привод валков может состоять: из электродвигателя клиноременной передачи приводного вала и зубчатой передачи с удлиненными зубьями; индивидуальных электродвигателей с отдельной передачей на каждый валок и электродвигателя редуктора синхронизатора и карданных валов.
Валковые дробилки получили наибольшее применение при измельчении глины известняка так как их эффективность при дроблении твердых пород ниже чем щековых и конусных дробилок. При работе валковых дробилок в основном изнашивается средняя часть бандажей по их длине в результате чего неоднородность продукта дробления увеличивается.
Поэтому в некоторых конструкциях дробилок предусмотрены устройства для равномерного распределения материала а также приспособления для очистки и проточки бандажей.
2Патентный поиск и анализ результатов
Авторское свидетельство № 982790
МКЛВ 02с 428. Публикация 23.12.82. №47.
УДК 621.926.4(088.8)
Заявлено 19.01.81 323951129-33 (21)
Рис. 2.2. Двухвалковая дробилка:
Валковая дробилка содержащая размольную камеру установленную в ней в корпусах подшипников на опорах шейках пару гладких имеющих в поперечном сечении форму равностороннего треугольника с выпуклыми гранями валков кинематически связанных посредством толкателей и
шиберов с загрузочным бункером и разгрузочную воронку отличающаяся тем что с целью повышения качества измельчения один из валков выполнен неподвижным а другой - подпружиненным при этом неподвижный валок снабжен соосно выполненными его профиль кулачками кинематически связанными посредством упоров с корпусами подшипников опорных шеек подвижного валка.
Исходный материал загружают в бункер 6 и подают при помощи регулирующих подачу материала шиберов 7 на линию зазора двух вращающихся встречно с синхронной скоростью валков 2 и 3. Материал поступивший из бункера 6 на валки 2 и 3 раздавливается между ними и поступает далее через разгрузочную воронку 5 на разгрузку. Валок 2 работает в неподвижных подшипниках а другой валок 3 – в подвижных перемещающихся по горизонтали под действием амортизаторов 4. Назначение подвижного валка – осуществлять процесс обката валков предохранять дробилку от поломок при прохождении через нее недробимых предметов и регулировать расстояние между валками. Поддержание заданной величины зазора между рабочими поверхностями фигурных валков 2 и 3 осуществляется криволинейной поверхностью копирных кулачков 12 кинематически связанных через упоры 13 с корпусами подшипников опорных шеек валка 3. Плотный контакт упора с криволинейной поверхностью копирного кулачка осуществляется при помощи амортизатора 4. Поддержание заданной величины зазора между валками определяет максимальный размер частиц измельченного материала при проведении технологического процесса в результате чего обеспечивается заданная крупность материала и улучшается качество дробления материала.
Применение валков имеющих равноосный контур в поперечном сечении в виде равностороннего треугольника с выпуклыми гранями и
скругленными вершинами позволяет повысить угол захвата валковой дробилки и надежность захвата кусков материала в том числе шарообразных кусков уменьшить истирающий эффект при измельчении материала и уменьшить износ рабочей поверхности валков в результате чего удлиняется срок службы валков и повышается производительность при минимальном увеличении энергозатрат и уменьшении габаритов дробилки.
Авторское свидетельство № 264150
МКЛВ 02с 420. Публикация 10.11.70. №8.
УДК 621.926.3(088.8)
Заявлено 27.9.68. 127186129-33
Солянников Н.М. Кораблев Н.М.
Рис. 2.3. Валковая машина
Валковая машина для измельчения материалов низкой и средней твердости включающая корпус внутри которого помещены рабочие валки отличающаяся тем что с целью интенсификации процесса измельчения один из рабочих валков выполнен в виде пустотелого равностороннего многоугольника с вогнутыми гранями и округленными вершинами в которой встроен вибратор другой валок выполнен с гладкой цилиндрической рубашкой насаженной на вращающуюся скалку-водило с эксцентрично-смешенными опорными шейками; смонтированную с возможностью возвратно-поступательного движения.
Валковая машина состоит из корпуса 1 внутри которого помещены рабочие валки 2 и 3. Валок 2 выполнен из полой толстостенной трубы 4 например пятигранного профиля. Труба скреплена с консолями 5 и 6
которыми она опирается на подшипники 7 запрессованные в корпусе 8 прямоугольного сечения могущие перемещаться в окнах торцевых стенок корпуса 1 по горизонтали.
Внутри валка 2 вмонтирован вибратор 9 направленного действия опорные шейки корпуса вибратора покоятся на подшипниках запрессованных в консоли 5 и 6 валка. Возбуждение вибрации осуществляется за счет вращения двух пар дебалансов 10 11 и 12 13 закрепленных на валах 14 и 15 соосно вращающихся в противоположные стороны. Для изменения направления действия силового поля служит рукоятка 16.
Валок 3 выполнен с гладкой цилиндрической рубашкой 17 насаженной на вращающуюся скалку-водило 18 с эксцентрично-смещенными опорами шейками. Независимое вращение рубашки осуществляется через зубчатый венец 19. Возвратно-поступательное движение валка 3 осуществляется за счет набегания кулачков на шестернях 20 и 21 не подвижные упоры закрепленные на корпусе.
Вращение валков 2 и 3 а также рубашки 17 осуществляется посредством шестерен 20-25 и 19.
Степень измельчения можно регулировать путем изменения величины зазора между валками и подбора наивыгоднейшего числа оборотов валка 3 и направленного действия силового поля вибратора.
Авторское свидетельство № 1736036 А1
МКЛВ 02с 408. Публикация
Заявлено 13.11.89 476834233-137129
Севостьянов В.С. Романович А.А. Богданов В.С.
Платонов В.С. Ханин С.И.
строительных материалов им. И.А. Гришманова
Рис. 2.4. Валковая дробилка
Валковая дробилка содержащая пару валков на которых установлены съемные бронеплиты образующие рабочие поверхности с выступами расположенными в шахматном порядке отличающаяся тем что с целью интенсификации процесса измельчения и повышения срока службы валков каждая бронеплита в продольном сечении валка имеет форму прямоугольной трапеции которая состыкована с другими бронеплитами в том же сечении в кольцевой ряд таким образом что больше основание трапеции примыкает к большему основанию а меньшее – к меньшему.
Исходный материал через загрузочное отверстие поступает на вращающиеся навстречу друг другу валки 1 и 2 установленные в корпусе 3. Подаваемый материал захватывается валками и подвергается интенсивному раздавливающе-истирающему воздействию между спаренными бронеплитами 4 позволяющими получить необходимый уклон (в пределах 3-5%) на небольшой длине что обеспечивает наибольшую интенсивность процесса измельчения за счет рационального сочетания раздавливающе-истирающего воздействия. Наличие съемных конических бронеплит способствует быстрому восстановлению рабочих поверхностей при износе путем замены бронеплит.
Наличие впадин и выступов на поверхности валков способствует эффективному измельчению материалов за счет обеспечения повышенного коэффициента внешнего трения.
Использование четкого количества бронеплит установленных по ширине валка обусловлено необходимостью компенсации осевых усилий возникающих при измельчении материала между валками.
Валковая дробилка с профильными валками наиболее приемлема в промышленности строительных материалов в частности для дробления керамзита.
Преимущество данной валковой дробилки заключается в том что она более удобна в эксплуатации на предприятиях и дешевле по сравнению с другими ранее предлагаемыми для предприятий промышленности строительных материалов.
3. Расчет кинематических параметров валковой дробилки
3.1. Определение угла захвата в валковых дробилках
и соотношение между диаметром валков и
размерами поступающего материала
Рис. 2.1. Схема определения угла захвата в валковых дробилках
В момент втягивания куска дробимого материала валками действуют следующие силы:
m – масса куска дробимого материала втягиваемого валками; из-за малой величины она практически не оказывает влияния на работу валков поэтому ею можно пренебречь.
P – давление валков на кусок дробимого материала.
Pf – сила трения дробимого материала о валки (f – коэффициент трения дробимого материала о валки).
Кусок дробимого материала втягивается валками при условии:
P cosα ≥ 2 P sinα (2.1)
Разделив левую и правую части уравнения (1) на 2Pcosα получим:
Заменив коэффициент трения углом трения φ получим:
Таким образом для затягивания валками куска дробимого материала угол захвата должен быть меньше угла трения.
Для определения соотношения между размером поступающего куска и диаметром валка также воспользуемся схемой:
где D – диаметр валка;
d – диаметр куска дробимого материала;
а – ширина выходной щели валковой дробилки.
Преобразуем уравнение (2.4) разделив правую и левую части на d.
Учитывая что степень измельчения в валковых дробилках в среднем равна четырем заметим что
Сделав необходимые преобразования в формуле (2.5) получим
Коэффициент трения керамзита равен 045. При таком коэффициенте трения угол захвата для керамзита равен 24°20.
3.2. Определение числа оборотов валков
Для работы валковой дробилки весьма важен правильный выбор числа оборотов валков.
Профессор Левинсон учитывая центробежную силу действующую на материал который находится во вращающемся цилиндре рекомендует определять число оборотов валков по формуле:
где f – коэффициент трения о вал
f = 03 для керамзита;
об – объемная масса материала
об = 2600 кгм3 для пеностекла;
d – диаметр поступающего куска определяем из формулы (6)
где D – диаметр валка
Практически число оборотов валка определяем по формуле
Для уменьшения износа бандажа и более устойчивой и спокойной работы валковой дробилки окружную скорость валков назначаем по ГОСТ 18266-72
что соответствует одному обороту валка. Тогда nраб=1сек-1.
3.3. Определение производительности валковой дробилки
Производительность валковой дробилки определяется по формуле
где В - ширина валка
а - зазор между валками
- окружная скорость валков мсек;
R - коэффициент учитывающий использование ширины валков и
степень разрыхления материала
R = 05 для керамзита.
n – число оборотов валка
Производительность в весовых единицах определяем по формуле:
где об – объемная масса материала
При измельчении и раздавливании керамзита валки за счет пружин раздвигается и зазор увеличивается. На основе практических данных зазора между валками в этом случае может принять вид
Вводя соответствующие данные и поправки формула принимает вид:
3.4. Определение мощности потребляемой валковой дробилкой
Среднее удельное давление на валок определим по формуле:
где R – коэффициент принимаемый равным 115
Gm – предел текучести
hн.с. – толщина нейтрального слоя м
– коэффициент определяющийся по соотношению
где – коэффициент трения материала о валок
α – угол захвата материала
Δh – линейное отжатие материала определяется по формуле
где hн – начальная толщина поступающего материала определяется по
hк – толщина выходной ленты
Площадь по которой будет действовать это давление определяется по формуле
где B – ширина валков
l – длина дуги на которой измельчается материал определяется по
Окончательно получим среднее удельное давление
Проекция Рср.ф. на горизонтальную ось принимаем приближенно что точка приложения этой силы находится на половине длины дуги 1 будет равна:
Суммарный путь который проходит точка приложения сил нажатия обоих валков на материал есть проекции перемещения точек приложения этих сил считая приближенно что точка приближения силы Рср.ф. лежит на половине дуги l получим величину горизонтального нуги проходимого точкой приложения этой силы равной (для обеих сил)
Работа совершаемая силой Рср.ф. на суммарном пути будет равна
При этом расход мощности расходуемой на измельчение составляет
Можно доказать что потребная мощность на преодоление трения материала о валок равна мощности затрачиваемой на измельчение материала умноженной на коэффициент трения.
Определим результирующую силу G
где Q – сила тяжести валков
g – ускорение свободного падения
Расход мощности на трение в подшипниках
Для нахождения общей мощности необходимо суммировать все мощности
где N1 – мощность затрачиваемая на измельчение;
N2 -мощность расходуемая на преодоление трения материала о валок;
N3 – мощность затрачиваемая на преодолевание трения в подшипниках.
Передача от двигателя на валки передается через редуктор передаточное отношение которого равно 125.
В связи с этим необходимая минимальная мощность будет равна
Тогда рабочая мощность двигателя будет равна
где – коэффициент полезного действия.
3.5.Определение усилий в частях валковой дробилки
Давление которое необходимо для дробления материала между валками создается пружинами установленными у подшипников подвижного валка.
Величина потребного давления зависит от ряда факторов учет которых весьма затруднителен. К числу этих факторов относятся физические свойства изменяемого материала как: твердость сопротивление дроблению степень измельчения модуль упругости и т.д. Вследствие этого величина давления которая должна быть обеспечена нажатием пружины может быть определена только приближенно на основе следующего допущения.
Предположим что суммарное давление (распорное усилие) между валками изменяется от 0 до Рнаиб тогда среднее давление будет равно
l – длина дуги на участке где измельчается материал
где R – радиус валка
α –угол захвата материала
Давление между валками составит
где - предел прочности при сжатии
R – коэффициент учитывающий использование длины валков и степень разрыхления материала
3.6. Расчет вала. Определение диаметра выходного конца вала.
При расчете на чистое кручение по нижним допускам напряжение
Определим диметр выходного конца вала
где Т – вращающий момент вала
где Nв – мощность на валу
n – частота вращения вала
где Nd – мощность двигателя
– коэффициент полезного действия вала.
где р – коэффициент полезного действия редуктора
n – коэффициент полезного действия подшипников вала
m – коэффициент полезного действия на преодоление силы трения
Для построения эпюр необходимо определить какие силы действуют в какой плоскости.
Эпюры необходимы для определения критических точек вала.
В вертикальной плоскости на вал действуют 2 силы:
В горизонтальной плоскости на вал действуют 2 силы:
– давление материала на бандаж
Определим силу действующую от массы бандажа на вал.
где m – масса бандажа
Для упрощения расчетов силу Q разделим на две силы
Найдем силу действующую нот массы полумуфты на вал
где m1 – масса полумуфты
Давление материала на бандаж
Для упрощения расчетов разделим силу Рср на две силы
Крутящий момент на валу равен
Определим реакцию опор для схемы нагружения под х. Для нормальной работы вала сумма всех сил на ось х должна быть равна нулю.
Рис.2.6 Схема реакций опор
Для построения эпюры изгиба найдем критические точки Q1.
Для построения эпюры момента на ось х найдем критические точки Мxi.
Определим реакции опор для схемы нагружения по оси у. Для нормальной работы вала сумма всех сил на ось у должна быть равна 0.
Сумма моментов на ось (у) = 0
Для построения эпюры изгибающего момента на ось у найдем критические точки Qiy.
Для построения эпюр моментов на ось у найдем критические точки Myi.
Для построения суммарной эпюры реакций найдем критические точки.
Для построения суммарной эпюры найдем критические точки.
3.7. Расчет подшипника
В связи с большими нагрузками выбираем подшипник скольжения.
Диаметр подшипника d = 90мм.
Нагрузки действующие на подшипник F2 = 3·106 Н.
Частота вращения n = 60 мин-1
Длина шипа подшипника l = 100мм.
Диаметр зазора φ = 0002мм.
Масло Тп-22 вязкостью = 0018 Па-с.
Шероховатость поверхности Rz = 32 мкм.
Расстояние между опорами L = 512мм.
Максимальный прогиб ymax = 001мм.
Найдем среднюю удельную нагрузку на подшипник.
где F2 – нагрузка действующая на подшипник
l – длина шипа подшипника
d – диаметр подшипника
Определим соотношение длины шипа к диаметру.
Определим угловую скорость
где n – частота вращения.
Определим линейную скорость
где – угловая скорость
d – диаметр подшипника.
Определим коэффициент нагруженности
Для дальнейшей работы воспользуемся учебником «Расчет деталей машин» авторы Кузьмин А.В. Чернин И.М.
По таблице 15.10 найдем относительный эксцентриситет х = 055.
Определим толщину масляного слоя
где d – диаметр подшипника
х – относительный эксцентриситет
Определим прогиб шипа в подшипнике
L – расстояние между опорами;
уmax – максимальный прогиб.
Проверим соблюдается ли условие
Из таблицы 15.11 по полученным значениям х = 055 и найдем соотношение .
Откуда определим коэффициент трения в подшипнике
Тепловыделение в подшипнике определяется по формуле
где f – коэффициент тепловыделения
F2 – нагрузка действующая на подшипник
Допускаемое напряжение на срез болта
По этому условию болты выдержат нагрузку.
Определим силу затяжки для болтов
где Тр – крутящий момент
D0 – диаметр окружности на которой расположены болты
z – число болтов соединяющих две полумуфты
По условию прочности для затянутых болтов из таблицы
что соответствует условию.
Следовательно если поставить все шесть болтов по ГОСТ 7808-70 в отверстие с зазором муфта сможет передать заданный момент.
Передаваемый муфтой момент определяется по формуле
Принимаем коэффициент тепловыделения R = 12Вт (м с °С).
Температура воздуха tв = 20°С.
Определим площадь поверхности подшипника охлаждаемую воздухом.
l – длина шипа подшипника.
Теплоотдача подшипника определяется по формуле
где R – коэффициент тепловыделения
Ав – площадь поверхности подшипника охлаждаемую воздухом
tм – температура масла в нагруженной зоне
tв – температура воздуха
Можно полагать что для минеральных масел объемная теплоемкость при температуре 20 - 100°С
Задавшись температурным перепадом в подшипнике
Определим расход смазочного материала
где Р1 – теплота переносимая маслом.
Определим коэффициент истечения масла
По таблице найдем коэффициент расхода масла через торцы нагруженной зоны
Коэффициент расхода масла через торцы нагруженной зоны
Из таблицы определяем
– безразмерный коэффициент
Определим размеры зазоров a и b.
Определим коэффициент истечения масла через канавки для смазки.
Воспользуемся уравнением безразмерного коэффициента и определим давление при принудительной подаче масла в подшипник
Температура масла определяем по формуле
Из таблицы муфты кольцевые по диаметру посадки на вал и крутящему моменту подберем муфту
d – диаметр посадочного отверстия
Трр – крутящий момент
Трр = 1863Н·м расчетный
Тр – крутящий момент
Болтов соединяющих 2 полумуфты z = 6шт с резьбой М16. Болты выполнены из стали Ст3 с пределом текучести материала т = 210МПа.
Условие прочности на срез болтов
Где Тр – крутящий момент
z - число болтов соединяющих две полумуфты
3.9. Расчет амортизирующего устройства
В качестве материала для пружины принимаем согласно ГОСТ 2052-73 Сталь 65 Г рессорно-пружинную горячекатаную.
Расчет пружины сжатия из круглого сечения на момент кручения.
гдеt кр – действительное максимальное напряжение на пружине;
[] – допустимое напряжение на кручение для проволочной пружины;
ρ – коэффициент учитывающий кривизну витков;
Р – максимальная сила растягивающая или сжимающая пружину.
Определяем диаметр проволоки.
Средний диаметр D определяем по формуле
Изменение длины витой цилиндрической пружины растяжения или сжатие из проволоки круглого сечения определяется расчетом пружины на жесткость
что G – модуль сдвига материала пружины
G = 8·104МПа для стали.
Принимаем z = 10 витков.
Минимальный зазор между витками при максимальном сжатии пружины.
Длина пружины сжатой до прикосновения витков определим по формуле
Длина пружины в нерабочем состоянии равна 270мм.
3.10. Расчет шпоночного соединения
Размеры сечения шпонок по ГОСТам в зависимости от диаметра вала d. Ширину b и высоту h призматических шпонок берем по таблице 27.
Длина шпонки определяется в зависимости от длины ступицы.
Выбираем призматическую шпонку 24×14×8 на 10мм короче ступицы.
Для шпонок осуществляется проверочный расчет по формуле
где см – действительное напряжение на смятие для шпоночного
[см] – допустимое напряжение на смятие для шпоночного
tс – действительное напряжение на срез для шпонки
[tс] – допустимое напряжение на срез для шпонки
Мк – крутящий момент передаваемый соединением
l – рабочая длина шпонки.
Призматические шпонки рассчитывают на смятие
где t1 – глубина паза
[см] – допустимое напряжение на смятие
М – передаваемый крутящий момент
Следовательно сечение шпонки выбрано правильно.
Шпонка проверяется на срез
где z – количество шпонок
[ср] – допустимое напряжение при срезе
Приняв напряжение при смятии шпонки [a] = 200 МПа проверим ее прочность Мк = 800 Н·м
4. Эксплуатация и ремонт валковой дробилки
Необходимость увеличения выпуска продукции обязывает ремонтников совершенствовать методы организации ремонта оборудования чтобы сократить простои машин в ремонте. Это может быть достигнуто путем перевода ремонтных работ на индивидуальные скоростные методы когда ремонтная площадка по существу превращается в собранную и на месте установки машины ее разбирают выбраковывают изношенные узлы а затем собирают из заранее заготовленных узлов и деталей.
При подготовке к пуску валковой дробилки необходимо проверить крепления состояние узлов и деталей и смазку подшипников.
У дробилок с гладкими валками больше всего изнашивается средняя часть валков. Чтобы этого избежать измельчаемый материал должен распределятся равномерно по всей длине валка. Изношенные валки восстанавливают путем наплавки сталинитом. Шестерни валы и другие детали ремонтируют установленными способами и методами
Валы при наличии износа подвергаются: токарной обработке наплавке термообработке.
При сборке корпус дробилки устанавливают так чтобы валы были горизонтальны (отклонение - не более - 02-0Змм на 1000мм длины).
Для повышения срока службы дробилки станину устанавливают на деревянные брусья укладываемые на бетонный фундамент. В результате сотрясения и толчки возникающие из-за наличия одного свободного валка смягчаются.
В процессе эксплуатации дробилки применяется система автоматической подачи керамзита.
Процесс заключается в контроле наличия керамзита в дробилке. При полной загрузке бункера дробилки керамзитом загрузочный транспортер отключается.
Ремонт дробилки осуществляется в соответствии со СТОиР.
Монтажные и демонтажные работы а также ремонтные выполняют специальные бригады.
Ремонт узлов а также изготовление запчастей осуществляются ремонтно-механическим цехом завода.
Безопасность жизнедеятельности
Бурный рост темпов развития строительной индустрии ведет к повышенному загрязнению окружающей среды производственных помещений атмосферного воздуха воды почвы что оказывает отрицательное воздействие на здоровье людей. Изменить технологию производства ввести новые эффективные комплексы очистных сооружений на всех действующих предприятий пока не всегда и не везде возможно.
В связи с этим особое значение приобретают разработки новых и
совершенствование имеющихся методов и средств изучения физико-
механических химических свойств и динамики пыли строительных
материалов в ограниченных пространствах определение ее
концентрации и влияние посторонних факторов на ее поведение. Все
это существенно сказывается на эффективности пылеулавливания и
очистки воздуха от пыли.
1. Характеристика и анализ производственных условий
Под производственными вредностями понимают те факторы трудового и производственного процесса которые смогут оказать вредное влияние - на состояние здоровья работающих и приводить к снижению работоспособности.
К основным вредным факторам относятся повышение запыленности воздуха повышение и понижение температуры относительная влажность атмосферное давление и подвижность воздуха на рабочем месте
повышенный уровень шума вибраций излучений магнитных и электрических полей а также повышение выделений вредных газов пара жидкостей токсичной пыли.
В последние годы приобрела важное значение борьба с вредными факторами которые являются производными неправильной организации трудового процесса. К ним относятся эмоциональная напряженность трудового процесса чрезмерная загруженность рабочего дня.
Из перечисленных вредных факторов строительной индустрии наиболее часто встречаются и более интенсивно действуют на организм человека шум вибрация и особенно загрязненность воздуха полидисперсной пылью.
Кроме того в настоящее время пока еще на многих предприятиях строительной индустрии метеорологические условия (температура относительная влажность и скорость движения воздуха) не соответствуют санитарным нормам. Значительное влияние пыли наблюдается при выполнении погрузочно-разгрузочных и транспортных работ и проведение технологических процессов в производственных помещениях по изготовлению строительных материалов (цемента глиняного кирпича и т.д.) а также во вспомогательных производствах например в складах инертных материалов и цемента готовой продукции смесеподготовительных участках и цехах.
Огромную роль в технологии производства цемента – важнейшего
вяжущего материала а также других неорганических вяжущих изготовление которых связано в большим выделением играет ее улавливание которое из-за вяжущих ее свойств представляет большие трудности. Запыленность воздуха в помещениях производства цемента достигает 100 120 мгм3 а запыленность окружающей техносферы 17 мгм3.
Таким образом производство строительных материалов связано с повышенным выделением пыли поэтому обеспыливание атмосферы производственных помещений и окружающей среды с предварительным исследованием физико-химических свойств и концентрации пыли является важной народно-хозяйственной проблемой требующей ее не отлагаемого решения.
Пыль строительных материалов и конструкций по своим физико-химическим и механическим свойствам очень разнообразна поэтому она отрицательно действует на многие человеческие органы.
Влияние пыли на организм человека усиливается из-за одновременного ее воздействия на несколько органов.
Наиболее серьезно пыли подвержены органы дыхания в меньшей степени кожа глаза кровь и желудочно-кишечный тракт. При воздействии пыли на органы дыхания возникает заболевание пневмокониоз разновидности которого силикатоз сименоз пневмокониоз цементный и прочие заболевания.
Производственная пыль может быть причиной заболевания глаз и кожи. Находящиеся в пыли раздражающие вещества нередко вызывают поражение переднего отрезка глаз. В более легких случаях развивается коньюктивит а в более тяжелых случаях возможны ожоги роговицы с последующим образованием Рубцовых изменений приводящих даже к полной потере зрения. Профессиональные заболевания кожи возникают в основном от физических факторов.
В контроль и оздоровление окружающей среды в производственных помещениях входит функции не только предприятий но и органов
здравоохранения а также профсоюзов. Они выступают за организацию безопасных условий труда контролируют соблюдение положений по охране труда проводят медицинское обследование каждый год трудящихся подверженных воздействию пыли обеспечивают санитарно-курортным лечением и так далее.
Для обеспечения чистоты воздушной среды производственный помещении предусматриваются технические технологические и организационные мероприятия. В качестве временной и срочной меры предотвращения воздействия пыли на организм работающих применяют индивидуальные средства защиты: марлевые повязки респираторы очки резиновые перчатки спец. одежду специальные шлемы и скафандры с подачей в них чистого воздуха.
Для нормализации состава воздушной среды на предприятиях строительных материалов проводят ряд организационно-технических и технологических мероприятий.
2. Охрана окружающей среды
Прежде всего необходимо организовать поведение технологических процессов таким образом чтобы исключалось или сводилось к минимуму выделение пыли и вредных газов в окружающую среду.
Для этого необходимо:
Эксплуатировать герметическое оборудование и предусматривать пневмотранспорт пылящих продуктов.
Максимально механизировать и автоматизировать технологические процессы что позволит исключить ручной труд и вывезти работающих из наиболее загрязненных зон.
Применять достаточно эффективные и надежные аспирационные устройства.
Использовать высокоэффективные средства пылегазоулавливания для очистки подходящих технологических газов и выбрасываемого вентиляционного воздуха.
Систематически удалять пыль с полов стен конструкций и технологического оборудования применяя передвижные и стационарные централизованные пылевакуумные системы.
Исключать перетекание загрязненного воздуха из части здания с повышенной концентрацией в другую часть здания с более низкой концентрацией.
Рациональными укрытиями при интенсивном пылевыделении технологического и транспортного оборудования являются герметические кожухи предотвращающие проникновение пыли в производственное помещение.
Валковые дробилки оборудуют герметичными укрытиями легкого типа. Длина и ширина укрытия определяются по размерам загрузочного отверстия. Высота укрытия загрузочных проемов для валковых дробилок принимается 14 07 ширины загрузочного отверстия. Верхняя часть укрытий объемная с герметичными смотровыми люками.
При значительных пылеобразованиях валковые дробилки закрываются кожухом с отсосом запыленного воздуха сверху через патрубок и снизу через патрубок.
Объем отсасываемого воздуха сверху принимается равным 65% от расчетного.
Механизация работ облегчает труд рабочего и делает его в целом более безопасным в то же время приводит к появлению ряда опасных моментов связанных с управлением машиной в процессе работы и выполнением операций технического обслуживания и ремонта.
Правила техники безопасности на производстве предусматривают предупреждение несчастных случаев. Соблюдение этих правил обеспечивает работающим безопасность труда сохранение здоровья и помогает добиваться высокой производительности. Для машинистов дробильных машин имеются инструкции по технике безопасности которые должны быть тщательно усвоены. Непременное условие безопасной работы машиниста - успешная сдача экзамена по технике безопасности.
Наряду с конкретными особенностями характерными для каждой машины существуют и общие правила техники безопасности которые должны сводиться к следующему: машинист должен знать устройство машин на которых он работает уметь управлять машиной и проводить основные операции технического обслуживания и ремонта.
Для обеспечения безопасной работы машины вводимые в эксплуатацию должны быть исправны их следует принимать по установленным правилам.
Рабочее место машиниста дробилки должно быть подготовлено таким образом чтобы обеспечивалась полная безопасность выполнения операций технологического процесса.
3. Пожарная безопасность
Строительные материалы по-разному реагируют на повышение температуры при пожаре.
Керамзит и отходы производства керамзита относятся к несгораемым материалам так как они под воздействием высокой температуры или огня не воспламеняются не тлеют и не обугливаются.
В то же время на предприятиях занятых переработкой каменных материалов применяют легко воспламеняющиеся материалы при неосторожном обращении с которыми может возникнуть пожар.
Кроме того причиной пожара может быть небрежное обращение с электрическими установками курение в недозволенных местах. Около машины должны постоянно находиться противопожарные средства:
-два ящика с песком;
4. Мероприятия исключающие травматизм и профессиональные заболевания
Уровень шума у дробилки составляет 10 дб. Допустимый уровень шума в помещении 50 дб. Максимальное расстояние на котором можно располагать пульт управления дробилки определяется по следующей формуле:
где - уровень шума у источника;
- допустимый уровень шума в нешумном помещении;
h - изолирующая конструкция ограждающая источник шума;
- изоляционный кожух.
Окна здания где находится пульт управления располагают в сторону источника шума.
Место пульта управления можно располагать на расстоянии больше или равным 10 м от дробилки.
5. Защита от поражения электрическим током
Для предупреждения поражений электрическим током необходима защита от трех опасных случаев возникновения неразмерных токов прикосновение к токоведущим проводам случайно оказавшимся под напряжением при перепаде напряжения. Для предотвращения коротких замыканий необходим правильный выбор монтаж и эксплуатация сетей машин и аппаратов соблюдение правил эксплуатации и ремонта электрического оборудования.
Для локализации последствий короткого замыкания используются быстродействующие установочные агрегаты и плавкие предохранители.
Для предотвращения перегрузки необходим правильный выбор сечения проводников недопущение включения в сеть непредусмотренных потребителей исключение нагрева электрических установок выше допустимого.
Для защиты электрических установок от токов перегрузки применяются плавкие предохранители и автоматы.
Расчет токов плавкой вставки
где =400А – пусковой ток.
По току плавкой вставки выбираем предохранитель (предохранитель трубчатый исполнения ПР-2)
Проверка предохранителя на короткозамкнутую цепь с изолированным нейтральным источником питания
где - сопротивление петли
- сопротивление фазы.
где Sш – сечение провода
– удельное сопротивление
= 0018 Оммм2·м для меди
Rmp – сопротивление трансформатора подстанции мощностью 560кВт
что удовлетворяет условию.
Защита от прикосновения к токоведущим проводам электрических установок достигается изоляцией ограждением дистанционным управлением предупредительной сигнализацией.
Защита от перехода напряжения на металлический корпус оборудования осуществляется защитным заземлением.
6. Расчет заземляющего устройства
В качестве заземления принимается прутковая сталь диаметром 12мм и длиной 54м. Грунт суглинок.
где ρ – удельное сопротивление грунта сопротивление заземляющего
устройства не более 4Ом
Сопротивление одиночного заземления для прутков определяется по следующей электрической формуле
где ρ – удельное сопротивление грунта
Rс – коэффициент сезона
Rс = 14 для средней полосы России
Общее число заземлений определяем
где R03 – сопротивление одного заземления
R3 – допустимое значение сопротивления заземляющего устройства
По таблице выбираем коэффициент использования заземления при n = 8 и а·l = 2 значение будет равно 072.
Сопротивление одиночной полосы определяется по формуле
где a – расстояние между стержнями
n – коэффициент использования полосы
b – глубина заземленной полосы
Сопротивление заземляющего устройства с учетом сопротивления одиночной полосы
что удовлетворяет условию техники безопасности.
Рисунок 4.1. Схема заземляющего устройства
излучений магнитных и электрических полей а также повышение выделений вредных газов пара жидкостей токсичной пыли.
Валковая дробилка является неотъемлемым звеном в технологической схеме производства керамзита. Работа валковой дробилки как и всего дробильного и помольного оборудования сопровождается шумом который оказывает неблагоприятное психофизическое действие на организм
человека а наличие вибрации затрудняет работу обслуживающего персонала. Вышеизложенные аргументы свидетельствуют о том что работа в таких условиях без проведения соответствующих мероприятий по безопасности жизнедеятельности является опасной для организма человека.
Обслуживающий персонал валковой дробилки включает одного рабочего IV разряда. В табл. 4.1. указаны факторы влияющие на условия труда обслуживающего персонала валковой дробилки.
Факторы условий труда
- скорость движения воздуха мс
Электрическая часть.
Описание принципиальной электрической
схемы управления приводом валковой дробилки.
Электрическая схема состоит из трех частей:
)схема силовых цепей
1. Схема силовых цепей
Схема силовых цепей состоит из четырех электродвигателей М1 М2 М3 и М4 питающихся от сети 380В. Управление осуществляется блоком контактов КМ1 КМ2 КМ3 КМ4 КМ5 и КМ6. Питание к блокам контактов подается через выключатели автоматические QF1 QF2 QF3 и QF4 так же в схеме силовых цепей находится реле контроля за напряжением KV1 KV2 KV3 KV4 KV5 KV6 KV7 и KV8 и тепловые реле КК1 КК2 КК3 и КК4 для защиты двигателя от перегрузки.
Схема управления состоит из трех частей:
)управление двигателем транспортера загрузки
)управление двигателями дробилки
)управление двигателями транспортера разгрузки
2.1. Управление двигателем транспортера загрузки
После включения выключателя автоматического QF4 питания подается на реле контроля за напряжением КV7 и КV7 контакты которого подготавливают цепь для включения КСС контакты которого подготавливают цепь пускателя KM6 работе.
При нажатии кнопки пуск SBC1 срабатывает пускатель KM6 который блокирует кнопку SBC1 и дает команду на включение двигателя М4 разгрузочного транспортера.
Контроль за работой транспортера разгрузки ведется датчиками частоты вращения SR1 и путевым SQ1 с помощью с реле времени KT1 выставляют время прохождения материала от начала прохождения по транспортеру загрузки до конца транспортера выгрузки. В этот период контроль за транспортером разгрузки осуществляется визуально.
Реле времени КТ2 служит для корректировки сигналов датчика SQ1 и выставляется на 2-3 секунды. Реле промежуточное KL1 служит для блокировки контакта КТ1 во время пуска.
2.2. Управление двигателями дробилки
Двигатели дробилки работают в ручном и автоматическом режиме. Ручное управление осуществляется с помощью переключения ключа SA режим ручного управления H и нажатием на кнопку SBC2 включаются пускатели KМ4 двигатели работают в реверсивном режиме. Эта цепочка служит для удаления неразмалываемого материала из под валка дробилки.
Автоматическое управление дробилки переводом ключа SA в положение (В) автоматически. К этому времени автоматы QF1 и QF2 должны быть включены. Цепь нормально разомкнутых контактов KV1 KV2 KV3 и KV4 замкнута транспортер разгрузки включен и поворотом ключа из (0) в положение (В) включает пускатели КМ1 и КМ3 через контакт КТ4. После выхода дробилки в рабочий режим через 3-5 секунд контакт размыкается но к этому времени контакт КТ4 замкнется и будет осуществлять контроль за работой дробилки. Контроль осуществляется датчиком SQ2 - за недробящимся материалом и SR2 SR3 – за вращением валков.
2.3. Запуск транспортера загрузки
Запуск транспортера загрузки осуществляется только в автоматическом режиме.
После включения автомата QF3 подготавливается цепочка KV5 и KV4 к этому времени дробилка выйдет в рабочий режим займет КТ4 и через нормально замкнутый контакт КТ5 включается пускатель КМ5 и включается двигатель транспортера загрузки М3. КТ5 остается замкнут до полного запуска транспортера в работу.
Контроль за работой транспортера ведется датчиками SQ3 и SR4. При заполнении бункера валковой дробилки транспортер останавливается датчиком SQ3 и включается автоматически с помощью реле времени КТ8 и реле включения КСС3. При остановке (аварийной) транспортера привод автоматически блокирует память КL4 и последующий запуск транспортера возможен после остановки дробилки.
3. Схема сигнализации
Схема сигнализации разделяется на две группы:
световая сигнализация;
звуковая сигнализация.
3.1. Световая сигнализация
В схеме световой сигнализации введены аварийные контакты нормально замкнутые от блоков управления (транспортера разгрузки КТ1 и КСС1 дробилки KL2 KL3 КСС2 транспортера загрузки KL1). Кнопка SBT2 служит для корректировки сигналов в цепях световой и звуковой сигнализации. После полного запуска транспортеров и дробилки оператор нажимает на кнопку SBT2 подготавливая схему к приему аварийных сигналов. Как только один из выше перечисленных контактов во время работы замкнется сработает самоблокирующая схема и включается световое табло после чего включается схема звуковой сигнализации и отсекает прохождение в схему световой сигнализации последующих сигналов.
3.2. Звуковая сигнализация
Звуковая сигнализация состоит из блока контактов введенных из схемы световой сигнализации реле промежуточного KL1 реле времени КТ7 кнопки SBС3 и прибора звуковой сигнализации НА.
После включения световой сигнализации подается команда на включение звуковой сигнализации замыканием одного из контактов в блоке промежуточных контактов срабатывает промежуточное реле KL17 и включается прибор звуковой сигнализации НА.