Валковая дробилка. Диаметр загружаемого материала 85 мм.


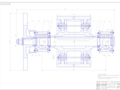
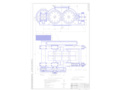
- Добавлен: 25.10.2022
- Размер: 2 MB
- Закачек: 1
Узнать, как скачать этот материал
Подписаться на ежедневные обновления каталога:
Описание
Валковая дробилка. Диаметр загружаемого материала 85 мм.
Состав проекта
![]() |
![]() |
![]() |
![]() ![]() ![]() ![]() |
![]() ![]() ![]() |
![]() ![]() |
![]() ![]() ![]() |
![]() ![]() ![]() ![]() |
![]() ![]() |
![]() ![]() ![]() |
Дополнительная информация
Контент чертежей
Валец в сборе.dwg

Полости подшипников заполнить смазкой ЦИАТИМ-221 ГОСТ
После сборки валец должен вращаться без заеданий.
Остальные ТТ по СТБ 1022-96.
ПЗ валковая дробилка 85 мм.doc
Пояснительная записка содержит 29 страниц 7 рисунков 1 лист А1 и 1 лист А1 .
Содержание записки рассматривает следующие вопросы:
Описание назначения конструкции и принципа работы;
Определение основных параметров;
Расчет силовых параметров;
Расчет производительности;
Расчет мощности привода;
Ключевые слова: валок известняк привод мощность производительность.
В процессе выполнения данного курсового проекта изучен принцип действия и алгоритм проектирования валковой дробилки.
Во многих отраслях промышленности строительных материалов керамической стекольной цементной и др.) широкое распространение получили валковые агрегаты (валковые дробилки и вальцы) предназначенные для крупного среднего мелкого и тонкого измельчения материалов малой и средней прочности удаления из глины каменистых включений и т.д.
Валковая дробилка имеет ряд преимуществ перед другими дробилками это простота конструкции удобство и безопасность эксплуатации и обслуживания минимальное число изнашиваемых деталей а также возможность их легкой замены относительно не высокий уровень вибрации из отсутствия вибрирующих частей рабочих органов наличие предохранительных устройств в виде подпружинивания одного из валка. Основным недостатком валковой дробилки является дробление только относительно непрочных материалов так как дробление более прочных материалов приводит к повышенному износу поверхностей валков.
Целью курсовой работы является проектирование валковой дробилки.
Назначение область применения и описание конструкции машины ее технологического процесса.
В промышленности строительных материалов наиболее распространены двухвалковые дробилки. Такие дробилки особенно удобны для измельчения влажных и вязких материалов так как другие дробилки забиваются подобными материалами а на валковых дробилках могут быть установлены специальные скребки снимающие налипший материал с поверхности валков.
Валковые дробилки для среднего и мелкого дробления материалов в основном средней прочности ( = 150 МПа) применяют с гладкими и рифлеными валками и для мягких и хрупких ( = 80 МПа) — с зубчатыми валками.
Основным рабочим элементом валковой дробилки является цилиндрический валок вращающийся на горизонтальной оси. Материал для дробления подается сверху затягивается между валками или валком и футеровкой камеры дробления и дробится.
Валковые дробилки бывают одно- двух- трех- и четырехвалковые. В четырехвалковой дробилке одна пара валков расположена над другой т. е. эта дробилка может рассматриваться как две двухвалковые дробилки смонтированные в один корпус.
Поверхности валков бывают гладкие рифленые ребристые и зубчатые. Сочетание дробящих поверхностей может быть различным например оба валка могут иметь гладкую поверхность или один гладкую другой — рифленую и т. д.
При одинаковом диаметре рифленые и зубчатые валки могут захватывать более крупные куски материала чем гладкие. Так если D — диаметр валка d — диаметр куска материала то при дроблении пород средней прочности соотношение Dd для гладких валков составляет 8—17 для рифленых и зубчатых 2—6.
Валковые дробилки имеют диаметр валка 400—1500 мм и длину равную 04—10 диаметра (длина зубчатых валков может быть больше чем диаметр).
Принципиальная схема двухвалковой дробилки показана на рис. 1. Валки вращаются навстречу один другому и дробят материал раздавливая его и частично истирая. Иногда для увеличения истирания необходимого при измельчении некоторых материалов валкам сообщают разную скорость.
Корпуса подшипников вала одного из валков опираются на пружины и могут перемещаться. В результате этого при попадании недробимого предмета один валок может отойти от другого и пропустить недробимый предмет после чего под действием пружин возвратиться в исходное положение.
Один валок 4 приводится во вращение (рис. 2) от двигателя через шкив 1 и шестеренчатую передачу 5. Другой валок 3 связан с первым шестернями 2 с удлиненными зубьями допускающими отход валков при пропуске недробимых предметов (рис. 2 а). Такое кинематическое решение довольно сложно кроме того оно не обеспечивает нормальную работу шестерен с удлиненными зубьями в условиях динамических нагрузок и абразивной пыли. Поэтому в последнее время каждый валок приводится во вращение от электродвигателя (рис. 2 б) или через редуктор 6 и карданные валы 7 (рис. 2 в).[1]
Рисунок 1 - Принципиальная схема двухвалковой дробилки
Рисунок 2 - Кинематические схемы валковых дробилок с приводом:
а — системой шестерен; б — индивидуальным для каждого валка; в — через редуктор и карданные валы
Работа валковой дробилки представленной на рис.3 происходит следующим разом.[1] Дробимый материал подается из загрузочного бункера 5. На раме дробилки параллельно валкам установлен приводной вал 18 со шкивом клиноременной передачи и цилиндрической шестерней. Вал вращается в роликоподшипниках и закрыт кожухом. Шестерня 11 находится в зацеплении с большим зубчатым колесом посаженным на вал 14 валка 3 дробилки шестерни закрыты кожухом 16. На втором конце вала насажено зубчатое колесо с высокими зубьями специального профиле которые находятся в зацеплении с зубьями такого же колеса насаженного на консольную часть вала 12 валка 6. Кожух 8 закрывает зубчатые передачи привода.
На валки надеты бандажи: рифленый 4 и гладкий 7 изготовленные из высокомарганцовистой стали. Регулировочные планки 13 позволяют устанавливать зазор между бандажами валков а следовательно изменять положение подшипников 11 вала подвижного валка.
Пружины 10 удерживают валок 6 на требуемом для дробления расстоянии от валка 3 и только при попадании между валками недробимого тела они деформируются и позволяют ему пройти между валками не повредив дробилку.
Рисунок 3 - Валковая дробилка
— рама; 2 11 — подшипники; 3 — неподвижный валок; 4 — рифленый бандаж; 5 —загрузочный бункер; 6 —подвижный валок; 7—гладкий бандаж; 816 — кожух; 9 — предохранительные кольца; 10 — пружина; 12 14—вал; 13— регулировочные планки; 15 17 — шестерни; 18 — приводной вал; 19— шкив.
При затягивании в зазор между валками крупных недробимых включений срезаются предохранительные кольца 9 подвижный валок отходит на значительное расстояние от неподвижного валка и зубья зубчатых колес выходят из зацепления.
Определение основных параметров и кинематический расчет.
Для осуществления процесса дробления необходимо обеспечить захват исходного материала т.е. камня рабочими органами установками.
Углом захвата α называют угол образованный касательными проведенными через точки соприкосновения куска материала с поверхностью валков. В момент захвата кусков материала диаметром в точках соприкосновения его с валками возникают силы нормального давления P действующего на материал под углом α2 (рис.4).[2]
Рисунок 4 – Схема к расчету геометрических параметров валковой дробилки.
Сила P раскладывается на составляющие силы P cos α2 и выталкивающую P sin α2 . С другой стороны под прямым углом к силе P действует сила трения F=Pf которая раскладывается на силу Pf sin α2 и втягивающую материал Pf cos α2. Очевидно для нормальной работы валковой дробилки необходимо чтобы было соблюдено условие
P sin α2 ≤ 2 Pf cos α2
Разделив обе части неравенства на 2 P cos α2 получаем
но f = tg ( - угол трения) тогда tg ≤ tg
Следовательно для нормальной работы валков необходимо чтобы угол захвата был меньше двойного угла трения. На практике в большинстве случаев принимают α=32-48° что соответствует коэффициенту трения f=03-045.
Определение соотношения между диаметром валков и размеров кусков материала поступающих в дробилку. [2]
Разделив уравнение на d получаем:
Принимая по данным практики d’d=14 (т.е. степень измельчения dd’ = 4) из уравнения получаем [2]
Величина коэффициента трения f кусков твердых пород (известняка песчаника гранита и т.д.) о поверхность стального валка в среднем равна 03 а для кусков влажной глины – 045. Для указанных значений f предельный угол
= α2 составляет соответственно 16°40’ и 24°20’.[2]
Таким образом отношение Dd для мягких пород
Тогда диаметра валка равен
Частота вращения валков с учетом действия на материал находящийся на вращающемся цилиндре центробежной силы определяется по формуле обс:[2]
где - плотность дробимого материала кгм для наглядности универсальности валковой дробилки используем плотности материалов от самого хрупкого -каменный уголь до самого прочного - известняка т.е.
Практически с целью уменьшения износа поверхности валков частоту их вращения принимают равной [2]
Т.е. для дробления каменного угля а для известняка .
Расчет основных силовых параметров определение мощности привода и выбор двигателя
Усилия в деталях валковой дробилки определяется нагрузкой которая создается пружинами предохранительного устройства. Эта нагрузка зависит от многих факторов и может быть вычислена лишь приближенно. [2]
Сила нормального давления действующая на материал (усилие раздавливание) H:[2]
где - предел прочности материала при сжатии МПа ;
- площадь дробления м;
- коэффициент разрыхления материала .
где - длина дуги на участке измельчения материала м;
Формула принимает следующий вид при
Полагая что точка приложения среднего нормального давления находится на половине дуги находим ее значение
Мощность электродвигателя валковой дробилки производим по наиболее прочным материалам кВт равна
где - мощность затрачиваемая на дробление материала кВт;
- мощность затрачиваемая на преодоление трения материала о валок кВт;
- мощность затрачиваемая на преодоление трения в цапфах валков кВт;
Мощность затрачиваемая на дробление материалов
где - среднее значение силы нормального давления кН;
- суммарный путь который проходит точка приложения сил нажатия обоих валков на материал м
Мощность мощность затрачиваемая на преодоление трения материала о валок
где - коэффициент трения материала о поверхность валков
Мощность мощность затрачиваемая на преодоление трения в цапфах валков
где - диаметр цапфы вала валков м ;
- результирующая сила от силы нормального давления (считается что она направлена горизонтально) и силы тяжести валка принимается равной
- приведенный к валу коэффициент трения качения
Тогда затрачиваемая мощность равна
Мощность двигателя равна
По расчетной мощности подбираем электродвигатель. Электродвигатель выбираем однофазный асинхронный марки АМУ160МА8 У2
мощность ------------50 кВт;
частота в сети -------50 Гц;
частота вращения ----1500обмин.
Крутящий момент электродвигателя равен
Теперь производим кинематический расчет механизма привода рис.5.
Рисунок 5 – Кинематическая схема привода валковой дробилки:
- электродвигатель; 2- клиноременная передача; 3- вал промежуточный; 4- зубчатая передача; 5 – зубчатая передача; 6-валки.
Передаточное число механизма равно
Разбиваем передаточное число по ступеням
- клиноременная передача – =14;
- цилиндрическая зубчатая передача – 46:
Произведем расчет клиноременной передачи.
Исходные данные для расчета клиноременной передачи:
частота вращения ведущего шкива n1=nэд=1500 мин-1
мощность на ведущем шкиву Р1=Рэд=50 кВт
крутящий момент на ведущем шкиву Т1=Тэд=3183 Н·м
передаточное число передачи uкл.рем=14
наклон передачи к горизонту a=0
режим работы передачи – тяжелый.
Расчетный передаваемый момент
гдеСр=08 – коэффициент учитывающий динамичность нагружения передачи и режим ее работы .[6]
Исходя из расчетного момента выбираем сечение ремня А. В соответствие с выбранным сечением принимаем минимальный диаметр ведущего шкива d1=540 мм; рабочая ширина ремня Вр=11 мм; полная ширина ремня В=13 мм; рабочая высота ремня Нр=8 мм; рабочая высота от средней линии Н=28 мм. [6]
Расчетный диаметр ведомого шкива
d'2=d1uкл.рем=54014=756 мм.
Принимаем по диаметр ведомого шкива d2=760мм.
Действительное передаточное число проектируемой передачи
гдеe = 0015 – коэффициент упругого скольжения [6]
uд=760[540 (1- 0015)]=143.
Минимальное межосевое расстояние
а'min=055(d1+d2)+Hр=055 (540+760)+8=723 мм.
Расчетная длина ремня
L'р=2а'min+05p(d1+d2)+025(d2-d1)2a'min=
=2723+05314 (540+760)+025 (760-540)2723=35037 мм.
Принимаем длину ремня 3600 мм. Однако по конструктивным соображениям чтобы более рационально разместить двигатель и редуктор на раме принимаем длину ремня Lр=5450 мм[6]
Действительное межосевое расстояние
а=а'min+05(Lp- L'р)=723+05(5450-3600)=1648 мм.
Коэффициент учитывающий длину ремня определяем по СL=089. [6]
Угол обхвата ремнем меньшего шкива
=180-57(760-540)1648=1876°.
Коэффициент угла обхвата принимаем Сa=095.[6]
v=pd1n1(60103)=3145401500(60103)=424 мс.
По выбранному сечению ремня и рассчитанной скорости определяем номинальную мощность передаваемую одним ремнем Р0=86 кВт [6]
Предварительно принимаем коэффициент учитывающий число ремней в передаче Сk=1.[6]
Число ремней передачи
z=Р1Ср(Р0СLCaCk)=501(860890951)=687.
Принимаем z=7 (округляем рассчитанное значение до ближайшего большего целого).[6]
Окружное усилие на ведущем шкиву
Ft=2103Т1d1=210003183540=1179 Н.
Предварительное натяжение ремня
F0=05Ftj =05117905=1179 Н
гдеj=05 – коэффициент тяги.[6]
Сила нагружающая вал редуктора
Fкл.рем= 2F0sin(2)=21179sin(1876°2)= 23528Н.
Производим расчет усилий в зубчатой передаче между валками.
Крутящий момент на валу валка равен
где - мощность двигателя Вт ;
- частота вращения валка обс .
Касательное усилие в зацеплении равно
где - диаметр зубчатого колеса мм .
Для расчета диаметра зубчатого колеса находим нужное межосевое расстояние с учетом максимального зазора между валками тогда
где - диаметр валка мм .
принимаем из стандартного ряда .[6]
Определяем суммарное число зубьев обоих колес так как передаточное число равно 1 имеем
Делительный диаметр зубчатого колеса равен
Диаметр вершин зубьев для шестерен с удлиненными зубьями равен
Радиальное усилие в зацеплении равно
где - угол зацепления . [6]
Расчет производительности валковой дробилки.
Производительность валковых дробилок по массе кгсм[4]
где - объем материала выходящего из дробилки за один оборот валка ;
- частота вращения валка ;
- коэффициент разрыхления дробимого материала .
При измельчении возрастает сопротивление раздавливанию: валки сжимая пружины раздвигаются на величину 125.[2]
где - диаметр валка м ;
Часовая производительность дробилки равна
Расчет вала дробилки.
При работе дробилки вал испытывает знакопеременные нагрузки которые изгибают его при незначительной прочности от усталости вал может сломаться.
Целью данного расчета является расчет изгибающих моментов действующих на вал определение минимально возможного диаметра вала и подбор опор вала.[6]
При работе вал испытывает нагрузки от силы нормального давления которая изгибает вал от силы тяжести валка сил в зубчатом зацеплении - касательной и радиальной касательное усилие заменяем действием крутящего момента который скручивает вал в продольном направлении (т.е. при заклинивании опоры момент может скрутить вал) передающийся от ведущего валка посредством зубчатой передачи.
Находим объем валка рис.6.
Общий объем валка равен
Находим реакции в опорах.
Реакция в опоре А равна
Реакция в опоре В равна
Строим эпюры изгибающего и крутящего момента рис.7.
Рисунок 7 – Схема нагружения вала и эпюры моментов.
Суммарныйизгибающий момент в сечении валка
Находим суммарный момент в опасном сечении
Тогда минимально допустимый диаметр вала без учета динамической составляющей и послабления шпоночными пазами равен
где - временное сопротивление для марки стали Сталь 45 МПа[4]
Выбираем диаметр под цапфы
Диаметр под валок с учетом послаблений шпоночным пазом и с учетом конструктивных особенностей .
Рассчитываем подшипники. В каждой из опор установлено по два одинаковых подшипника расчет ведем по более нагруженной опоре В.
Характеристика подшипников:
роликовый двухрядный подшипник 53619 ГОСТ 24698-81[4]
Требуемая долговечность:
Окружная скорость на валу равна
Эквивалентная нагрузка
Определение динамической грузоподъемности:
Определение долговечности подшипника:
т.к. подшипник пригоден.
Охрана труда при работе валковой дробилки.
ОБЩИЕ ТРЕБОВАНИЯ ОХРАНЫ ТРУДА
Общие требования охраны труда изложены в инструкции «Общие требования по охране труда для работников занятых в производстве строительных материалов».
ТРЕБОВАНИЯ ОХРАНЫ ТРУДА ПЕРЕД НАЧАЛОМ РАБОТЫ
1. Осмотреть привести в порядок и надеть спецодежду и спецобувь. Волосы убрать под головной убор. Надеть каску.
2. В соответствии с нормами выдачи спецодежды спецобуви и других средств индивидуальной защиты машинисту валковой дробилки выдаются средства индивидуальной защиты.
Работодатель обязан заменить или отремонтировать спецодежду спецобувь и другие средства индивидуальной защиты пришедшие в негодность до истечения установленного срока носки по причинам не зависящим от работника.
3. Перед началом работы машинист должен проверить:
наличие и исправность средств индивидуальной защиты (респиратор защитные очки перчатки и пр.) наличие и комплектность аптечки доврачебной помощи;
освещенность рабочего места в первую очередь пусковых устройств приводов ограждений натяжных устройств лестниц переходных мостиков и т.д. Неисправности в осветительной сети устраняет электромонтер;
наличие и исправность защитных и ограждающих устройств на всех открытых передачах валах муфтах и пр. Работать при снятых неисправных плохо закрепленных защитных и ограждающих устройствах запрещается;
исправность имеющихся средств сигнализации контрольно-измерительных приборов;
наличие и исправность рабочего инструмента (кувалды троса лопаты скребков и пр.);
чистоту и незагроможденность посторонними предметами рабочего места проходов площадок;
визуально - исправность заземления двигателей и пусковой аппаратуры;
наличие обтирочных и смазочных материалов. Их запас не должен превышать суточной потребности хранить их необходимо в металлических ящиках с плотно закрывающимися крышками;
наличие на рабочем месте журнала приема-сдачи смены инструкции по эксплуатации оборудования инструкции по охране труда и пожарной безопасности а также инструкции по сигнализации.
4. Все обнаруженные при приеме смены неполадки и нарушения отразить в сменном журнале и сообщить мастеру.
5. Если время приема смены совпало с моментом аварии или недопустимого отклонения в режиме работы агрегата смену необходимо принимать только с разрешения мастера начальника смены или начальника цеха.
6. Осмотр состояния валковой дробилки и комплектующего оборудования производить только при выключенных главных включающих аппаратах с ручным управлением (рубильники автоматы и т.п.) и вывешенных на них плакатах «Не включать - работают люди!».
7. Перед пуском убедиться в отсутствии людей в рабочей зоне оборудования и дать предупредительный сигнал.
ТРЕБОВАНИЯ ОХРАНЫ ТРУДА ВО ВРЕМЯ РАБОТЫ
1. При обслуживании дробилки необходимо следить за равномерной подачей и габаритом материала не допускать попадания в него металлических предметов.
2. Удалять негабаритный материал производить чистку дробилки или ремонтные работы только при отключенных главных включающих аппаратах с ручным управлением и вывешенных на них плакатах «Не включать - работают люди!».
Работы внутри дробилки производить только по наряду-допуску.
3. При обслуживании работающего оборудования запрещается:
работать без средств индивидуальной защиты;
прикасаться руками одеждой или какими-либо другими предметами к движущимся частям оборудования;
снимать защитные и ограждающие устройства;
облокачиваться и садиться на ограждения перила кожухи;
производить очистку и уборку просыпи под питателем;
производить натяжку ленты питателя;
исправлять деформированные детали пластинчатого транспортера;
работать с неисправными грузоподъемными тросами при истекшем сроке испытания тросов;
производить смазку движущихся частей дробилки и другого оборудования не имеющих специальных приспособлений для безопасного проведения ручной дистанционной смазки;
регулировать любые механизмы;
пользоваться для освещения факелом или переносной лампой напряжением выше 12В.
4. Следить за сигналами предупреждающими возникновение опасности соблюдать меры личной безопасности.
5. Оборудование необходимо остановить при:
угрозе аварии или несчастного случая;
неисправной системе звуковой и световой сигнализации;
отключении освещения цеха;
попадании на питатель посторонних предметов или негабаритных кусков материала;
неисправностях оборудования работа при которых запрещена правилами технической эксплуатации.
ТРЕБОВАНИЯ ОХРАНЫ ТРУДА В АВАРИЙНЫХ СИТУАЦИЯХ
1. При аварийной поломке валковой дробилки или вспомогательного оборудования угрозе несчастного случая необходимо остановить работу и сообщить об этом мастеру или начальнику цеха.
2. В случае пожара необходимо остановить оборудование полностью обесточить установку вызвать пожарную охрану сообщить мастеру или начальнику цеха принять меры к тушению очага возгорания имеющимися средствами.
ТРЕБОВАНИЯ ОХРАНЫ ТРУДА ПО ОКОНЧАНИИ РАБОТЫ
1. До окончания смены произвести уборку рабочего места. Запрещается протирать перильные ограждения рабочие площадки ступени лестниц ветошью смоченной горюче-смазочными материалами а также производить уборку с помощью сжатого воздуха.
2. Ручной инструмент и инвентарь привести в порядок сложить в отведенном месте. Поврежденный в течение смены инструмент или инвентарь отремонтировать самостоятельно или сдать для ремонта мастеру смены
3. Использованный обтирочный материал сложить в предназначенное место.
4. Ознакомить сменщика со всеми неполадками имевшими место при эксплуатации оборудования в течение смены произвести соответствующую запись в журнале приема-сдачи смен доложить мастеру или начальнику цеха.
5. При неявке сменщика доложить мастеру или начальнику смены и в дальнейшем руководствоваться его указаниями.[5]
Список использованных источников.
Константопуло Г.С. Механическое оборудование заводов железобетонных изделий и теплоизоляционных материалов. М. Высш. школа 1988
Константопуло Г.С. Примеры и задачи по механическому оборудованию заводов железобетонных изделий. М. Высш. школа 1986
Мартынов В.Д. Строительные машины и монтажное оборудование М. Высш. школа 1984.
Сапожников М.Я. Механическое оборудование для производства строительных материалов и изделий. Машгиз 1962.
Сапожников М.Я. Дроздов Н.Е. Справочник по оборудованию заводов строительных материалов. Машгиз 1970.
С.М. Агеев. Детали машин. – Херсон.: 2003. – 170с.
Чертеж Общего вида85.dwg

Предел регулирования разгрузочной щели
Частота вращения валков
Размеры для справок.
Остальные ТТ по СТБ 1022-96.
Техническая характеристика
Технические требования
Рекомендуемые чертежи
Свободное скачивание на сегодня
Обновление через: 10 часов 30 минут