Дробилка валковая




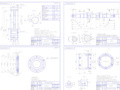
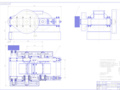
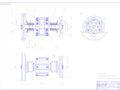
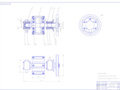
- Добавлен: 25.10.2022
- Размер: 2 MB
- Закачек: 3
Описание
Состав проекта
![]() |
![]() ![]() ![]() |
![]() |
![]() ![]() ![]() ![]() |
![]() ![]() ![]() ![]() |
![]() ![]() ![]() ![]() |
![]() ![]() ![]() ![]() |
![]() ![]() |
![]() ![]() ![]() |
![]() ![]() |
![]() ![]() |
![]() ![]() ![]() |
![]() ![]() ![]() |
![]() ![]() ![]() |
![]() ![]() |
![]() ![]() ![]() |
![]() |
![]() ![]() |
![]() ![]() |
![]() ![]() |
![]() ![]() |
![]() ![]() ![]() |
Дополнительная информация
Содержание.docx
Расчет основных параметров .. .. .
Расчет и назначение припусков . .
Расчёт на прочность
Метрология и стандартизация . ..
Выводы и рекомендации .
Список литературы .. .
Деталировка.dwg

**Размеры и параметр обеспечить инструментом
Остальные технические требования по СТБ1022-96
*Размеры для справок
Фаски в отверстиях 1х45
Остальные технические требования по СТБ 1022-96
Сталь 40Л ГОСТ 977-88
Сталь 40Х ГОСТ 4543-71
Отливка 2-й группы ГОСТ 977-88
Неуказанные формовочные уклоны по ГОСТ 32112-96
Неуказанные литейные радиусы 2-5мм
Точногсть отливки 11
-0-0-12 ГОСТ 26645-85
Остальные технические требования поСТБ 1014-95
Чертеж. общего вида.dwg

Размер выходного продукта
Технические требования
Техническая характеристика
Валок ведомый.dwg

Смазка подшипников Литол-24 ГОСТ 21150-88
Остальны технические требования по СТБ-1014-95
Валок ведущий.dwg

Смазка подшипников Литол-24 ГОСТ 21150-88
Остальны технические требования по СТБ-1014-95
спецификация Валок ведущий.docx
ДВ-150.02.01.01.000 СБ
ДВ-150.02.01.00.001
ДВ-150.02.01.00.002
Болт M12-6gX40.56.019
Гайка М64х2-6Н.11.019
спецификация Валок ведомый.docx
ДВ-150.02.01.01.000 СБ
ДВ-150.02.01.00.001
ДВ-150.02.01.00.002
Болт M12-6gX40.56.019
Гайка М64х2-6Н.11.019
Записка.docx
Валковые дробилки бывают одно- двух- трех- и четырехвалковые. Четырехвалковую дробилку в ряде случаев можно рассматривать как две двухвалковые смонтированные в одном корпусе.
Поверхности валков бывают гладкие рифленые ребристые и зубчатые длинно- и короткозубчатые (длиннозубчатые — при высоте зуба более 01 диаметра валка короткозубчатые при высоте зуба менее 01 диаметра валка). Сочетание дробящих поверхностей может быть различным: например оба валка могут иметь гладкую поверхность или один гладкую другой — рифленую. Дробилки с гладкими и рифлеными валками обычно применяют для дробления материалов средней прочности (до асж = 150 МПа); дробилки с зубчатыми валками применяют для измельчения каменного угля и подобных материалов малой прочности (до асш = 80 МПа). Крупность продукта дробления валковой дробилки зависит как от размера выходной щели между валками так и от типа поверхности рабочих органов. В мировой практике валковые дробилки используют как правило на заключительных стадиях дробления (среднее и мелкое дробление).
Патентно-технический анализ
Патент № RU0138 В1 (13) Валковая дробилка.
Изобретение относится к оборудованию предназначенному для дробления полезных ископаемых и может быть использовано в угольной горнорудной и других отраслях промышленности. Цель изобретения — повышение производительности и снижение расхода энергии при дроблении. Исходный материал через загрузочный патрубок поступает в корпус 7 на пару валков захватывается ими при вращении в противоположные стороны и раскалывается зубьями валков в поперечном направлении до величины щели между валками. Куски материала располагающиеся у торцов валков испытывают значительное давление со стороны заостренных кромок 9 измельчающих элементов 8 на боковых стенках корпуса 7 и раскалываются также и в продольном направлении. Измельчающие элементы выполнены дугообразными и расположены концентрично валкам с шагом между собой равным размеру щели между валками.
Изобретение относится к дробильному оборудованию предназначенному для дробления полезных ископаемых различных строительных материалов и может быть использовано в угольной горнорудной и других отраслях промышленности.
Цель изобретения - увеличение производительности и снижение расхода энергии при дроблении.
Рисунок 1.1- Дробилка валковая.
Дробилка содержит привод 1 приводной вал 2подвижный 3 и неподвижный 4 валки амортизирующее устройство 5 редуктор 6 корпус 7. На боковых стенках корпуса со стороны торцов валков в зоне дробления концентрично валкам установлены измельчающие элементы 8шаг которых а равен величине щели между валками. Измельчающие элементы имеют дугообразную форму а их кромка 9 заострена.
Дробилка работает следующим образом.
С помощью привода 1 приводного вала 2 редуктора 6 вращение передается валкам 3 и 4. Исходный кусковый материал через загрузочный патрубок корпуса 7 поступает в зону дробления захватывается вращающимися навстречу друг другу валками 3 и 4 раскалывается зубьями в поперечном направлении до величины щели между валками. Крупные куски материала которые располагаются у боковых стенок корпуса испытывая значительные удельные давления со стороны заостренных кромок измельчающих элементов 8 раскалываются также и в продольном направлении. Таким образом наличие измельчающих элементов на боковых стенках корпуса в зоне дробления позволяет разрушать крупнокусковой материал находящийся у боковых стенок корпуса одновременно в двух направлениях продольном и поперечном. Шаг между измельчающими элементами равный щели между валками исключает переизмельчение материала.
Предлагаемая дробилка позволяет увеличить производительность снизить расход энергии при дроблении не изменяя основных параметров машины.. Дробилка содержащая корпус неподвижный и подвижный валки расположенные в корпусе и привод отличающаяся тем что с целью увеличения производительности и снижения расхода энергии при дроблении стенки корпуса со стороны торцов валков выполнены с дугообразными измельчающими элементами расположенными над крайними участками валков и концентрично им с шагом равным величине щели между валками причем кромка каждого дугообразного измельчающего элемента обращенная к среднему участку валка выполнена заостренной.
Патент №RU20001158C1 Рабочий валок дробилки.
Рабочий валок дробилки содержащий барабан с зубьями на его периферии и бандаж выполненный из продольных секций каждая из которых закреплена посредством болтов на зубьях барабана отличающий с я тем что с целью повышения надежности и долговечности крепления и снижения металлоемкости и трудоемкости изготовления секций барабан выполнен с ячейками между зубьев каждая продольная секция в местах ее крепления имеет ширину равную размеру ячейки между зубьями оперта на боковые грани зубьев своими боковыми гранями и имеет высоту не превышающую высоту зуба.
Рисунок 1.2.- Валок общий вид;
Рисунок 1.3.- Сечение А-А на рис.1.
Изобретение относится к дробильному-размольному оборудованию и направлено на совершенствование конструкций рабочих органов дробилок валкового типа.
Известен рабочий валок дробилки содержащий установленный на оси барабан и бандаж который выполнен цельным в виде кольцевой обечайки.
Недостаток такой конструкции заключается в значительной трудоемкости процесса замены изношенного бандажа так как неизбежен полный демонтаж всего валка из корпуса дробилки.
Известен также рабочий валок содержащий барабан установленный на оси и бандаж. Барабан этого валка выполнен в виде шестигранной призмы а бандаж - в виде набора секций. Крепление секций на барабане осуществлено соединением шип-паз расположенным симметрично относительно радиальной плоскости секции. Кроме того каждая секция соединена с барабаном болтовым креплением по концам секций с обеих сторон от соединения шип-паз которое предназначено для передачи крутящего момента от барабана к секции а болты воспринимают радиальную нагрузку от инерции массы секции при вращении и от момента стремящегося повернуть секцию при дроблении.
Этот момент возникает в результате того что сила направленная по касательной к окружности валка приложена с наружной стороны секции а реакция - в соединении шип-паз т.е. с внутренней стороны секции.
Таким образом силы противоположного направления приложенные на расстоянии друг от друга образуют вращающий секцию момент.
Однако так как секции выполнены в виде отливок из износостойкой стали не подвергающейся механической обработке не представляется возможным с достаточной точностью выполнить соединение шип-паз поэтому между стенками паза и шипа имеется зазор. В болтовом соединении также имеется зазор.
Наличие бокового люфта (зазора) в соединении работающем в весьма тяжелом режиме при резких пульсирующих нагрузках приводит к ослаблению крепления в результате вытяжки болтов смятия резьбы развинчивания гаек притирки контактируемых поверхностей барабана и секции пр. В конечном результате это приводит к разрушению соединения в результате обрыва болтов.
Наиболее близким к изобретению по технической сущности является рабочий валок дробилки содержащий барабан с зубьями на его периферии и бандаж выполненный из продольных секций каждая из которых посредством болтов на зубьях барабана закреплена.
Недостатками известного валка являются недостаточная надежность долговечность крепления и трудоемкость изготовления.
Цель изобретения - повышение надежности и долговечности крепления а также снижение металлоемкости и трудоемкости изготовления продольных секций.
Поставленная цель достигается тем что в рабочем валке дробилки содержащем барабан с зубьями на его периферии и бандаж выполненный из продольных секций каждая из которых закреплена посредством болтов на зубьях барабана последний выполнен с ячейками между зубьев каждая продольная секция в местах ее крепления имеет ширину равную размеру ячейки между зубьями оперта на боковые грани зубьев своими боковыми гранями и имеет высоту не превышающую высоту зуба.
Валок содержит ось 1 на которой смонтирован барабан 2 соединенный с осью посредством шпонки 3 и бандаж 4 выполненный из продольных секций 5 закрепленных на барабане 2 болтами 6 с гайками 7. По краям барабана имеются зубья (кулаки) 8 которые могут быть выполнены заодно целое с барабаном и между ними образованы ячейки. Боковые поверхности соседних зубьев 8 расположены друг к другу под углом т.е. клинообразно с вершиной клина направленной в сторону центра валка. Боковые грани продольных секций 5 выполнены аналогично. Кроме того они выполнены ступенчатыми по длине секции так что у концов их образованы впадины.
В процессе сборки секции 5 крепят болтами 6 с гайками 7 и боковые грани их упираются в боковые поверхности зубьев 8 а б радиальном направлении между барабаном 2 и внутренней поверхностью секций 5 остается гарантированный зазор необходимый для обеспечения требуемой затяжки секций с учетом возможной неточности изготовления сопрягаемых деталей.
В процессе работы болты 6 воспринимают растягивающие усилия от центробежной силы вращающихся масс продольных секций и от радиальной составляющей силы возникающей при дроблении зубья 8. передают продольным секциям 5 крутящий момент.
Изобретение позволит обеспечить повышение долговечности и надежности рабочего валка дробилки исключить возможность истирания и среза болтов которые воспринимают теперь только растягивающую нагрузку.
Расчет основных параметров
Конструктивные параметры. Угол захвата в валковых дробилках — это угол между двумя касательными к поверхностям валков в точках соприкосновения с дробимым материалом.
На кусок дробимого материала имеющего форму шара и массу т которой ввиду ее незначительности можно пренебречь действуют силы Р давления от обоих валков и силы трения равные fP где f —- коэффициент трения материалов о валок (для упрощения эти силы показаны на рис. 4.20 для одного валка).
Кусок затягивается валками если 2Pf cos a > 2Р sin а или f > tg а а так как f = tg где — угол трения то а . Но = 2а значит 2 т. е. так же как для щековых и конусных дробилок угол захвата у валковых дробилок для нормального процесса дробления не должен превышать двойной угол трения.
Размер куска захватываемого валками можно определить пользуясь схемой на рисунке 2.1.
Рисунок 2.1 - Расчетная схема двухвалковой дробилки.
Если D— диаметр валка d- диаметр куска материала а—
ширина выходной щели то
Разделив левую и правую часть выражения 2.1 на d получим:
По исходным данным диаметр куска материала d=100 мм а ширина выходной щели а=30 мм тогда степень измельчения в дробилке ad=03. Подставив это значение в уравнение получим:
Коэффициент f трения для прочных пород принимают равным 03. При таких значениях f угол будет соответствовать 24°20' а отношение Dd для прочных пород:
Обычно для гладких валков отношение Dd принимают равным 20 для рифленых 10 а для зубчатых валков 2 так как в последнем случае кусок материала затягивается при непосредственном захвате его поверхностью рабочего органа. Мы будем разрабатывать валковую дробилку с рифлеными валками следовательно диаметр валков определяется следующим образом:
Соотношение диаметра валков и их длины принимают в пределах L:2R=1:25.
Частоту вращения валков (c-1) определяют по формуле предложенной проф. Л. Б. Левинсоном:
где —коэффициент трения материала о валок; р — плотность материала; d — диаметр куска исходного материала м; D — диаметр валка м
Значит частота вращения валка должна быть тем меньше чем больше его диаметр чем больше диаметр поступающих кусков и их плотность и чем меньше коэффициент трения между куском материала и валками. По данной формуле определяют максимально возможную частоту вращения валков.
Обычно конструктивно предусматривают минимальную и максимальную частоту вращения которую затем выбирают по конкретным условиям эксплуатации(например при дроблении мате-
риалов с малым пределом прочности при сжатии можно принять
более высокую частоту чем при дроблении материалов средней -
Для определения и (обс) частоты вращения валков используется эмпирическая зависимость где диаметр валка D - в «м»:
Принимаем n=1 обс = 60 мин-1.
При этом окружная скорость для рабочей поверхности валков всех дробилок получается в пределах 3—6 мс. что обеспечивает спокойную и устойчивую работу машины и соответствует сложившейся практике эксплуатации валковых дробилок.
Производительность дробилки. Производительность валковых дробилок можно вычислить если представить процесс дробления как движение ленты материала шириной равной длине L валка и толщиной равной ширине а выходной щели.
Производительность дробилки рассчитывается по формуле:
где а – зазор между валками принимаем равным среднему диаметру конечного продукта а = 003мм - КПД дробилки = 0 75 n=60 обмин.
В этом случае производительность дробилки будет равна:
Сила дробления Р зависит от нагрузки которая создается пружинами предохранительного устройства. Среднее значение этой нагрузки определяется из формулы:
где -предел прочности материала на сжатие =150 МПа по условию задания курсового проекта;
- коэффициент разрыхления материала;=02 03 - для прочных материалов;
- длина дуги валка на участке измельчения материала м;
Находим длину дуги валка на участке измельчения материала l
Рассчитываем Силу дробления Р:
Мощность двигателя валковой дробилки с учетом затрат мощности на преодоление всех сопротивлений при работе машины:
где - мощности расходуемые на дробление с учетом трения материала о валок и на трение в подшипниках;
- КПД передачи =095.
Мощность необходимая на дробление (Вт):
где - коэффициент учитывающий одновременность раскалывания
- коэффициент трения
Мощность необходимая на преодоление сил трения в подшипниках (Вт):
где - диаметр шейки вала м;
- коэффициент трения качения ;
- нагрузка на подшипники Н.
где Q- сила тяжести валка Н.
В существующих методиках расчета мощности валковых дробилок кроме момента силы трения fPcpR дополнительно учитывается действие силы Рср на дуге l. Cилами препятствующими вращению валка могут являться лишь те которые создают момент относительно его оси а эти силы полностью учитываются в приведенных выражениях для определения N и N.
Тогда окончательно формула установочной мощности электродвигателя валковой дробилки высчитывается как:
Если перемножить рекомендуемые значения всех входящих в формулу коэффициентов и постоянных величин а также исключить незначительный расход мощности на преодоление трения р подшипниках т. е. если не стремиться к большой точности то получим сравнительно простую но вполне достаточную для практических расчетов формулу установочной мощности (Вт) электродвигателя валковой дробилки:
Расчеты на прочность
Нагрузки на детали дробилки зависят от усилия дробления. Для измельчения прочных материалов усилие дробления Fdp H
Это усилие создается на поверхности валков и направлено вдоль нормали к точке касания валка и дробимого материала. Затягивание куска породы между валками осуществляется за счет сил трения. Поэтому вращающий момент который необходим для работы дробилки равен
Для прочных материалов = 02-03.
При выполнении проектных расчетов учитывают изгибающую нагрузку на валы валков от усилия дробления а силой тяжести самих валков и другими нагрузками в виду их сравнительно небольшой величины пренебрегают. В таком случае нагрузки вызывают напряжения изгиба и кручения и диаметр валов определяют из условия прочности которое имеет вид
Уточненный расчет вала ведется после проработки конструкции дробилки на стадии технического проекта.
При этом учитывают все нагрузки на валы и их направления:
Крутящий момент определяем по следующей формуле:
где N – мощность на валу л.с. N =21000 Вт = 285 л.с.
n – число оборотов вала в минуту n = 60обм .
Находим касательное напряжение:
Нормальное напряжение находится по формуле :
Эквивалентное напряжение рассчитывается по формуле :
Для стали 45 []=275МПа.
Имеем 168 МПа ≤275 МПа. Условие выполняется.
Переходим к расчету основных параметров клиноременной передачи.
Передаточное число с учётом упругого скольжения
где n1 и n2 – частоты вращения ведущего и ведомого шкивов мин-1.
Диаметр большого шкива определяется как:
где D1 и D2 – диаметры ведущего и ведомого шкивов мм
- коэффициент упругого скольжения (для кордошнурованных клиновых ремней =001)
D2=3·180·(1-001)=535мм
Угол обхвата на малом шкиве:
где а – расстояние между осями шкивов (а=2230мм).
Рекомендуется для клиноременных ремней 120º
Длина ремня встык (без учёта припуска на соединение концов ремня провисания и начального деформирования):
гдеn1- частота вращения на ведущем валу (n1=120мин-1)
Число ремней передачи:
гдеP – передаваемая мощность кВт;
– мощность допускаемая на один ремень кВт
Cz – коэффициент учитывающий неравномерность распределения нагрузки между ремнями в комплекте
Примем число ремней 7.
Выбираем ремень D(Г) 6000 ГОСТ 1284.1
Стандартизация и метрология
При выполнении проекта использованы следующие ГОСТы:
-ГОСТ 2.105-95 ЕСКД. Общие требования к текстовой документации;
-ГОСТ 2.104-68 ст СЭВ 104-74;
-ст СЭВ 3657-76 ЕСКД. Основные надписи;
-ГОСТ 2.105-95 ЕСКД. Текстовые документации;
-ГОСТ 2.106-68 ст СЭВ 2516-80 ЕСКД. Спецификации;
-ГОСТ 2.109-73 ст СЭВ 858-78;
-ст СЭВ 1182-78 ЕСКД. Основные требования к чертежам;
-ГОСТ 2.103-68 ст СЭВ 1181-78 ЕСКД. Форматы;
-ГОСТ 2.302-68 ст СЭВ 1187-78 ЕСКД. Масштабы;
-ст СЭВ 1178-78 ЕСКД. Линии;
-ГОСТ 2.305-68 ЕСКД. Изображения виды сечения и разрезы;
-ГОСТ 2.307-68 ЕСКД. Нанесение размеров и предельных отклонений;
-ГОСТ 2.308-79 ЕСКД. Указание на чертежах допусков формы и расположения поверхностей;
-ГОСТ 2.309-68 ст СЭВ 1632-79 ЕСКД. Обозначение шероховатости поверхности;
-ГОСТ 2.311-68 ст СЭВ 284-76 ЕСКД. Изображение резьбы;
-ГОСТ 2.136-68 ст СЭВ 856-78 ЕСКД. Правила нанесения на чертежах надписей технических требований и таблиц;
-ГОСТ 2789-73 ст СЭВ 638-77. шероховатость поверхностей. Параметры и характеристики;
-ГОСТ 25346-88 ст СЭВ 145-75. единая система допусков и посадок. Общие положения ряды допусков и основных отклонений;
-ГОСТ 77696-70. Болты с шестигранной головкой;
-ГОСТ 6401-70. Шайбы;
Выводы и рекомендации.
Существенным недостатком валковых дробилок является интенсивное и неравномерное изнашивание рабочих поверхностей валков (бандажей) при обработке прочных и абразивных горных пород. Бандаж изнашивается в основном в средней части валка что не дает возможности поддерживать стабильный размер выходной щели по всей ее длине. Кроме того валковые дробилки обладают сравнительно невысокой удельной производительностью.
Распространение валковых дробилок различных конструкций для дробления самых разнообразных материалов особенно в составе передвижных дробильно-сортировочных установок объясняется тем что валковые дробилки наиболее приспособлены для переработки очень распространенных материалов склонных к налипанию или содержащих липкие включения. Во время работы дробилок налипший на поверхность валков материал срезается скребками и при необходимости отводится на сторону.
Применение дробилок других типов на переработке таких материалов или вообще невозможно или вызывает частые простои связанные с длительной и трудоемкой работой по очистке камеры дробления. Возможность перерабатывать материалы склонные к налипанию на рабочих органах выгодно отличает валковые дробилки от других типов дробильного оборудования.
Рекомендуемые чертежи
Свободное скачивание на сегодня
- 24.01.2023