Разработка технологии механической обработки заготовки вал



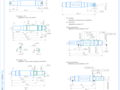
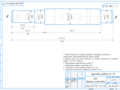
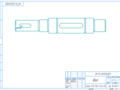
- Добавлен: 24.01.2023
- Размер: 480 KB
- Закачек: 2
Узнать, как скачать этот материал
Подписаться на ежедневные обновления каталога:
Описание
Разработка технологии механической обработки заготовки вал
Состав проекта
![]() |
![]() ![]() ![]() |
![]() ![]() ![]() ![]() |
![]() ![]() ![]() ![]() |
![]() ![]() ![]() ![]() |
Дополнительная информация
Контент чертежей
Т.Пправ. .cdw

Чертеж4.cdw

ШТАМПОВКА uВал ghfd18 тыс в год.cdw

Рекомендуемые чертежи
- 02.05.2022
- 09.04.2021
- 23.04.2016
Свободное скачивание на сегодня
Обновление через: 16 часов 44 минуты
- 22.08.2014
- 29.08.2014