Разработка технологии механической обработки тихоходного вала



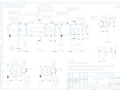
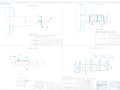
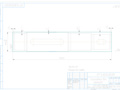
- Добавлен: 25.10.2022
- Размер: 2 MB
- Закачек: 2
Описание
Состав проекта
![]() |
![]() ![]() |
![]() |
![]() ![]() ![]() |
![]() ![]() |
![]() |
![]() ![]() |
![]() ![]() ![]() ![]() |
![]() ![]() |
![]() |
![]() ![]() ![]() |
![]() ![]() |
![]() ![]() ![]() |
![]() ![]() ![]() ![]() |
![]() ![]() ![]() ![]() |
![]() |
![]() ![]() |
![]() ![]() ![]() |
Дополнительная информация
rrrrsrrrrer.docx
Служебное назначение детали и анализ её технических требований . .5
Определение типа производства .. 7
Выбор вида и метода изготовления исходной заготовки . .8
План обработки поверхностей детали . . .10
Расчёт припусков на обработку и предельных размеров заготовки 11
Составление технологического маршрута обработки детали . 15
Выбор оборудования режущего и измерительного инструмента . .20
Расчет и назначение режимов резания .. 23
Нормирование технологического процесса . ..32
Тихоходный вал прокат.dwg

Пояснительная записка.docx
ТЕХНИЧЕСКИХ ТРЕБОВАНИЙ
Тихоходный вал является деталью горизонтального цилиндрического червячного редуктора. Он входит в состав тихоходной ступени редуктора и передает вращение от электродвигателя к ленточному конвееру. Вращение передается с помощью зубчатых передач. Тихоходный вал вращается на роликовых конических подшипниках №1027316 ГОСТ 27365-87 которые устанавливаются в корпус редуктора.
К изделию предъявляются следующие технические требования:
- материал детали Сталь 45 ГОСТ 1050-88;
- твердость свободных и вспомогательных поверхностей 235 НВ;
- твердость рабочих поверхностей закалка ТВЧ
с высоким отпуском 310 НВ;
- допуск цилиндричности шейки вала мм 0010;
- степень точности 8;
- поверхности под подшипники
- масса детали кг 195;
- допуск соосности посадочных поверхностей подшипников мм 0004;
- остальные поверхности H14h14 ±
- годовая программа выпуска штгод 500.
Химический состав изделия процент:
- сера не более 0004;
- медь не более 030;
- фосфор не более 0035;
- никель не более 025;
Механические свойства Стали 45 ГОСТ 1050-88 приведены в таблице 1.
Таблица 1 – Механические свойства Стали 45
Временное сопротивление
Относительное удлинение
Относительное сужение
ОПРЕДЕЛЕНИЕ ТИПА ПРОИЗВОДСТВА
Тип производства и соответствующая ему форма организации производственного процесса определяют характер технологического процесса и его структуру. Поэтому необходимо определить тип производства по заданным программе выпуска и форме детали.
Ориентировочно тип производства можно определить исходя из годовой программы выпуска деталей и их массы.
По таблице 2 определяем тип производства.
Таблица 2 – Зависимость типа производства от объема выпуска и массы детали
Годовая программа выпуска = 500 штгод
Объём детали определим по формуле [1]
l – длина i-той цилиндрической части вала м.
Массу детали кг определим по формуле [1]
где – удельный вес материала кгм3 = 7810 кгм3 [1]
Тип производства – мелкосерийное (10 .1000)
ВЫБОР ВИДА И МЕТОДА ИЗГОТОВЛЕНИЯ ИСХОДНОЙ
Т.к. производство детали мелкосерийное то целесообразно выбрать метод получения заготовки прокатом. При данной программе выпуска рационально изготовить заготовку из проката обычной точности так как это ведет к снижению количества операций обработки вследствие чего снижается количество снимаемого материала и износ инструмента отрезка мерных заготовок ведётся на фрезерно-отрезном станке.
Выбор диаметра заготовки для номинального диаметра детали D = 0044 м выполняется по отношению LD = 39 4. Выбираем заготовку выполненную из круглого проката диаметром 0044 м ГОСТ 2590-88.
Объём заготовки определяем в соответствии с рисунком 1.
Рисунок 1 – Заготовка
Объём заготовки определим по формуле [1]
где r – радиус заготовки м r = 0022 м;
l – длина заготовки м l = 0215 м
Массу заготовки кг определим по формуле [1]
где – удельный вес материала кгм3 = 7830 кгм3 [1]
Коэффициент использования материала определим по формуле [1]
где – масса готового изделия кг = 195 кг
Значение коэффициента показывает что материал для мелкосерийного производства расходуется рационально.
ПЛАН ОБРАБОТКИ ПОВЕРХНОСТЕЙ ДЕТАЛИ
Исполнительные поверхности - это поверхности которыми деталь выполняет свое служебное назначение.
Основные поверхности - это поверхности которые определяют положение детали в машине.
Вспомогательные поверхности - это поверхности которые определяют положение детали присоединенной к данной.
Свободные поверхности - это поверхности завершающие конструктивные формы детали упрощающие изготовление и сборку.
Схема обозначения поверхностей представлена на рисунке 2.
15 – исполнительные поверхности;
– основные поверхности;
121359 – вспомогательные поверхности;
81011 – свободные поверхности.
Рисунок 2 – Схема обозначения поверхностей
План обработки поверхностей представлен в таблице 3.
Таблица 3 – План обработки поверхностей
Обозначение поверхности
Шероховатость Rа мкм
Фрезерование черновое
Наружные поверхн. 37
Шлифование предварительное
Фрезерование однократное
Торцевые поверхности 4 6
Торцевая поверхность 16
РАСЧЁТ ПРИПУСКОВ НА ОБРАБОТКУ И ПРЕДЕЛЬНЫХ РАЗМЕРОВ ЗАГОТОВКИ
Для каждой операции назначаем межоперационный (промежуточный) припуск – избыточный слой металла оставляемый при выполнении предшествующей операции и снимаемый на данной операции.
Величина межоперационного припуска зависит от:
- конечного геометрического размера и точности (квалитета) обрабатываемой в данной операции поверхности детали.
С целью компенсации погрешности размера при обработке каждой поверхности определяем величину общего припуска для каждой операции.
Схема расчета припусков и межоперационных размеров для наружной цилиндрической поверхности 40 представлена на рисунке 3.
Рисунок 3 – Схема расчёта припусков и межоперационных размеров для наружной цилиндрической поверхности 40
Межоперационные размеры припуски допуски для других поверхностей рассчитаем табличным методом [2] и сводим в таблицу 4.
Таблица 4 – Межоперационные размеры припуски допуски
Технологические операции переходы обработки отдельных поверхностей детали
Номинальное значение припуска мкм
Предельные размеры мм
Предельные припуски мкм
поверхн. вала 9 30n6)
Продолжение таблицы 4
СОСТАВЛЕНИЕ ТЕХНОЛОГИЧЕСКОГО МАРШРУТА ОБРАБОТКИ ДЕТАЛИ
Отрезать заготовку из прутка
Центровать отверстие
Выберем приспособления и разработаем маршрут обработки вала все данные маршрута сведем в таблицу 5.
Таблица 5 – Маршрут обработки вала
Продолжение таблицы 5
Снять фаску 25х45º на 3125 мм 3622 мм 3622 мм
Снять фаску 25х45º на 3522 мм 4175 мм
Фрезеровать шпоночную канавку B = 10 мм
Вертикально- фрезерный
Фрезеровать шпоночную канавку B = 12 мм
Шлифовать предварительно с
Шлифовать предварительно с
Кругло- шлифовальный
Шлифовать начисто с до на L = 92мм
Шлифовать начисто с до на L = 48 мм
Шлифовать начисто с до на L = 42 мм
Шлифовать начисто с до
ВЫБОР ОБОРУДОВАНИЯ РЕЖУЩЕГО И ИЗМЕРИТЕЛЬНОГО ИНСТРУМЕНТА
Основные характеристики используемого оборудования приведены в таблице 6.
Таблица 6 – Сводная ведомость по оборудованию
Отрезной-круглопильный
Токарно-винторезный с ЧПУ
Вертикально- фрезерный
Максимальная длина обрабатываемой заготовки мм
**-частота вращения заготовки
Основные характеристики используемого режущего инструмента приведены в таблице 7.
Таблица 7 – Сводная ведомость по режущему инструменту
Наименование режущего инструмента
Марка материала режущей части
Сверло центровочное комбинированное
A1250x40x3424АF30L5V35 Б 3
Круг шлифовальный чистовой
A1250x20x3430АF10G 11 V35 АА 3
Основные характеристики используемого измерительного инструмента приведены в таблице 8.
Таблица 8 – Сводная ведомость измерительного инструмента
Наименование инструмента
Штангенциркуль ЩЦ–I–250–005 ГОСТ 166-63
Штангенциркуль ЩЦ–III–350–01 ГОСТ 166-63
Штангенциркуль ЩЦ–I–250–001 ГОСТ 166-63
Микрометр МК25-1 ГОСТ 6507-90
РАСЧЕТ И НАЗНАЧЕНИЕ РЕЖИМОВ РЕЗАНИЯ
Расчет и назначение режимов резания аналитическим методом для чернового точения с 44 до 4112.
Поправочный коэффициент учитывающий влияние физико-механических свойств обрабатываемого материала на скорость резания определяется по формуле [2]
где – коэффициент характеризующий группу стали по обрабатываемости = 1 [2];
– фактический параметр характеризующий обрабатываемый материал для которого рассчитывается скорость резания Нмм2 = 600 Нмм2;
– показатель степени при обработке резцами из твёрдого сплава = 10 [2]
Поправочный коэффициент учитывающий условия работы определяется по формуле [2]
где – поправочный коэффициент учитывающий влияние состояния поверхности заготовки на скорость резания = 09 [2];
– поправочный коэффициент учитывающий влияние инструментального материала на скорость резания = 065 [2]
Подачу выбираем по диаметру обрабатываемой детали и глубине резания.
Скорость резания при наружном продольном точении ммин определяется по формуле [2]
где – коэффициент зависящий от материала инструмента и заготовки = 340 [2];
Т – стойкость режущего инструмента мин Т = 60 мин [2];
t – глубина резания мм t = 17 мм;
s – подача ммоб s = 08 ммоб [2];
m – показатель степени m = 020 [2];
y – показатель степени y = 045 [2]
Частоту вращения шпинделя станка обмин определяется по формуле [2]
где D – диаметр обрабатываемой заготовки мм D = 44 мм
По паспорту станка 16К20Ф3 примем обмин.
Действительную скорость резания при наружном продольном точении ммин определяется по формуле [2]
Силу резания принято раскладывать на составляющие силы направленные по осям координат станка: тангенсальную радиальную и осевую .
Поправочный коэффициент учитывающий влияние качества обрабатываемого материала на силовые зависимости определяется по формуле [2]
где n – показатель степени n = 075 [2]
Поправочный коэффициент для тангенсальной силы резания определяется по формуле [2]
где – поправочный коэффициент = 10 [2];
– поправочный коэффициент = 115 [2];
– поправочный коэффициент = 10 [2];
– поправочный коэффициент = 093 [2]
Тангенсальную силу резания Н определяется по формуле [2]
где – постоянный коэффициент = 300 [2];
y – показатель степени y = 075 [2];
n – показатель степени n = -015 [2];
Мощность резания кВт определяется по формуле [2]
Мощность процесса резания не должна превышать мощности станка.
Мощность двигателя кВт определим по формуле [2]
где – КПД привода главного движения = 095 [2];
– мощность электродвигателя станка кВт = 10 кВт [2]
Условие выполняется.
Остальные расчеты режимов резания для токарной обработки проведем табличным методом и представим в таблице 9.
Таблица 9 – Сводная таблица режимов резания для токарной обработки [2]
Точить торец начерно с 215 мм до 209мм
Точить канавки начерно
Продолжение таблицы 9
Точить начисто с 36096 мм
Точить начисто с 4111 мм
Таблица 10 – Сводная таблица режимов резания для фрезерной обработки [4]
Фрезерование шпоночного
Паз шириной 10 мм длиной 70ммглубиной 5 мм
Паз шириной 10 мм длиной 20ммглубиной 5 мм
Шлифовать предварительно с 30128 мм до
Шлифовать предварительно с 35118 мм до
Шлифовать предварительно с 40118 мм до
Таблица 11 – Сводная таблица режимов резания для шлифовальной обработки[1]
Шлифовать начисто с
НОРМИРОВАНИЕ ТЕХНОЛОГИЧЕСКОГО ПРОЦЕССА
Основное время для чернового точения с 44 мм до 4112 мм мин определяется по формуле [4]
– величина врезания и перебега резца мм = 288 мм [4];
– дополнительная длина на взятие пробной стружки мм = 1 мм [4];
n – частота вращения шпинделя обмин n = 500 обмин;
S – подачана один оборот шпинделя ммоб S = 06 ммоб [3]
Основное время для чистового точения с 4111 мм до 40118 мм мин определяется по формуле [4]
– величина врезания и перебега резца мм = 099 мм [4];
– дополнительная длина на взятие пробной стружки мм = 05 мм [4];
n – частота вращения шпинделя обмин n = 800 обмин;
S – подачана один оборот шпинделя ммоб S = 03 ммоб [3]
Число проходов инструмента iопределяется по формуле [4]
где – глубина резания мм = 099 мм;
t – глубина врезания шлифовального круга мм t = 03 мм [3]
Основное время для получистового шлифования с 40118 мм до 40048мм мин определяется по формуле [4]
где L – длина обрабатываемой поверхности мм
– частота вращения детали мин-1 = 100 мин-1;
– ширина шлифовального круга мм = 40 мм [2];
– продольная подача ммоб = 0002 ммоб [3];
К – коэффициент учитывающий доводку и выхаживание при шлифовании К = 13 [4]
где – глубина резания мм = 037 мм;
t – глубина врезания шлифовального круга мм t = 0185 мм [3]
Основное время для тонкого шлифования с 40048 мм до 40018 мм мин определяется по формуле [4]
– ширина шлифовального круга мм = 20 мм [2];
Вспомогательное время на операцию мин определяется по формуле [4]
где – время на установку и снятие заготовки мин = 102 мин [5];
– время связанное с переходом мин = 0018 мин [5];
– время на измерение мин = 014 мин [5]
Оперативное время мин определяется по формуле [4]
где – поправочный коэффициент на вспомогательное время зависящий от серийности работ типа оборудования и трудоёмкости = 1 [5]
Время на обслуживание оборудования мин определяется по формуле [4]
Время нормированного отдыха мин определяется по формуле [4]
Штучное время для технологических операций выполняемых вручную мин определяется по формуле [4]
В данной курсовой работе был произведён анализ и назначение детали её технических требований определили тип производства выбрали метод изготовления исходной заготовки план обработки поверхности детали рассчитали припуски на обработку составили технологический маршрут обработки детали выбрали оборудование режущего и измерительного инструмента рассчитали режимы резанья выполнили расчёт основного машинного времени.
Э.Л.Жуков С.Л. Мурашкин. Технология машиностроения: В 2кн. Кн.1. Основы технологии машиностроения: Учеб. пособ. для вузов. – М.: Высш. шк. 2003. – 278с.
Г. А. Косилова. Справочник технолога-машиностроителя Т.2 – М.: Машиностроение 1985. – 496 с.
Г.А. Монахов. Обработка металлов резанием. Справочник технолога. Изд 3-е. М.:Машиностроение 1974. – 598 с.
Общемашиностроительные нормативы вспомогательного времени и времени на обслуживание рабочего места на работы выполняемые на металлорежущих станках. М.:Машиностроение. 1980.
Общемашиностроительные нормативы времени и режимов резания на работы выполняемые на металлорежущих станках с ЧПУ – ЦБПНТ при НИИ труда. М.:Машиностроение. 1980.
Титульный лист.doc
ФЕДЕРАЛЬНОЕ ГОСУДАРСТВЕННОЕ БЮДЖЕТНОЕ ОБРАЗОВАТЕЛЬНОЕ УЧРЕЖДЕНИЕ ВЫСШЕГО ОБРАЗОВАНИЯ
«ИВАНОВСКИЙ ГОСУДАРСТВЕННЫЙ ПОЛИТЕХНИЧЕСКИЙ УНИВЕРСИТЕТ»
КАФЕДРА ТЕХНИЧЕСКОЙ КИБЕРНЕТИКИ И РАДИОЭЛЕКТРОНИКИ
Расчетно-пояснительная записка к курсовой работе
По дисциплине «Технология производства ПТСДСиО»
На тему: «Разработка технологии механической обработки тихоходного вала»
студент группы сПТМ – 51
Тихоходный вал.dwg

Неуказанные предельные отклонения размеров: H14
Острые кромки притупить радиусом 0
Сталь 45 ГОСТ 1050-88
Схемы наладок.dwg

Наименованиие и модель станка
Вертикально фрезерный 6М11
Круглошлифовальный 3М153
Инструмент: Резец проходной Т15К6 ГОСТ 18878-73
Инструмент: Резец канавочный Т15К6 ГОСТ 18878-73
Резец торцевой Т15К6 ГОСТ 18878-73
Инструмент: Сверло центровочное комбинированное Р6М5 ГОСТ 14952-75
* Размер для справок
Операция 010 Центровальная
Операция 015 Токарная
Инструмент: Фреза шпоночная Р6М5 ГОСТ 9140-78
Операция 020-025 Фрезерная
Инструмент: Круг шлифовальный 1А1 250х40х34 24А F30 L 5 V 35 Б 3 ГОСТ 2424-83
Операция 035-040 Шлифовальная
Введение.doc
При оказании механического воздействия на поверхность наблюдается образование новой поверхности образуется она путем деформации и дальнейшего отдаления слоев от основной части материала. Сопровождается появлением стружки. Часть материала которую снимают металлорежущие станки называется припуском. Она является избыточной. После того как с детали снимается припуск она приобретает определенную форму.
При производстве следует делать небольшой припуск так как это позволит уменьшить трудоемкость процесса и себестоимость детали а также сэкономит материал
Помимо обработки резанием существуют такие видымеханической обработки металлов как обработка методом деформирующего реза методом пластической деформации а также электрофизическая обработка.
Обработка методом пластической деформации осуществляется под силовым воздействием внешней среды. Это приводит к глобальному изменению формы конфигурации и свойств детали. Обработка методом деформирующего резания является способом объединившим обычное воздействие резом и метод пластической деформации. Этот способ применяют для восстановления первоначальной формы изношенных деталей.
Рекомендуемые чертежи
- 24.05.2017
- 24.01.2023