Технологический маршрут обработки детали вал-шестерня




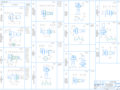
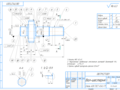
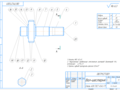
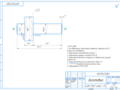
- Добавлен: 24.01.2023
- Размер: 2 MB
- Закачек: 0
Описание
Состав проекта
![]() |
![]() |
![]() |
![]() |
![]() ![]() ![]() |
![]() ![]() ![]() |
![]() ![]() ![]() ![]() |
![]() |
![]() |
![]() ![]() ![]() ![]() |
![]() |
![]() ![]() ![]() |
![]() ![]() ![]() ![]() |
![]() ![]() ![]() |
![]() ![]() ![]() ![]() |
![]() ![]() ![]() ![]() |
![]() ![]() ![]() |
![]() ![]() ![]() ![]() |
![]() ![]() ![]() ![]() |
![]() |
![]() |
![]() |
Дополнительная информация
продолжение пояс.записки.doc
Расположение поверхностей
Габариты заготовки мммм
Размеры обработ. поверхн.
Тип модель оборудования
Фрезерование сверление
Фрезерно-центровальный полуавтомат
Токарно-винторезный станок 16Б16Т1
Токарно-винторезный станок 16Б16ПТ1
Продолжение табл. 8.1
Токарно-винторезный станок 16Б16ПТ1
Горизонтальный шпоночно-фрезерный станок 692Р
Вертикальный зубофрезерный станок 53А20
Зубофасочный станок ВС-320А
Горизонтальный зубошевинговальный станок 5702В
Центрошлифовальный станок 3922Е
Круглошлифовальный станок 3А151
Зубошлифовальный станок 5851
Полировально-шлифовальный станок 3А352
Выбор приспособлений
Базовая поверхность.
Установочные элементы
Типоразмер приспособления
Фрезерно-центровальный МР-76АМ
Призма установочная
Тиски самоцентрирующиеся с призматическими губками 50 ГОСТ 12195-66
Токарно-винторезный станок
Центр подпружиненный
А1-3-НП-ЧПУ ГОСТ 8742-75
Патрон поводковый ГОСТ 2571-71.
Центр вращающийся ГОСТ 8742-75
Продолжение табл. 8.2.
Продолжение табл.8.2.
Вертикально шпоночно-фрезерный станок 692Р
Вертикальный зубофрезерный станок 52А20
Патрон цанговый. Центр вращающийся ГОСТ 8742-75
Зубофасочный станок ВС-320А
Зубошевинговальный станок 5702В
Центрошлифовальный станок 3К225В
Патрон мембранный ГОСТ 16157-70
Центр неподвижный ГОСТ 8742-75
Патрон поводковый ГОСТ 2571-71. Центр подвижный ГОСТ 8740-75
Центр неподвижныйГОСТ 8742-75
Патрон цанговый ГОСТ 2571-71. Центр вращающийся ГОСТ 8742-75
3. Выбор режущего инструмента
При выборе РИ будем руководствоваться следующими правилами:
)Выбор инструментального материала определяется требованиями с одной стороны максимальной стойкости а с другой минимальной стоимости.
)Следует отдавать предпочтение стандартным и нормализованным инструментам. Специальный инструмент следует проектировать в крупносерийном и массовом производстве выполнив предварительно сравнительный экономический анализ.
)При проектировании специального РИ следует руководствоваться рекомендациями по совершенствованию РИ.
Выбор режущего инструмента (РИ) будем производить в следующем порядке:
)Исходя из типа и модели станка расположения обрабатываемых поверхностей и метода обработки определяем вид РИ.
)Исходя из марки обрабатываемого материала его состояния и состояния поверхности выбираем марку инструментального материала.
)Исходя из формы обрабатываемой поверхности назначаем геометрические параметры режущей части (форма передней поверхности углы заточки: g a j j1 l; радиус при вершине).
)Исходя из размеров обрабатываемой поверхности выбираем конструкцию инструмента его типоразмер и назначаем период стойкости Т.
Данные по выбору РИ заносим в табл. 8.3.
4. Выбор средств контроля
При выборе средств контроля будем руководствоваться следующими правилами:
)Точность измерительных инструментов и приспособлений должна быть существенно выше точности измеряемого размера однако неоправданное повышение точности ведет к резкому удорожанию.
)В единичном и мелкосерийном производстве следует применять инструменты общего назначения: штангенциркули микрометры длинномеры и т.д.
)В крупносерийном – специальные инструменты.
)Следует отдавать предпочтение стандартным и нормализованным средствам контроля.
Данные по выбору средств контроля заносим в табл. 8.4.
Результаты выбора средств технологического оснащения заносим в табл. 8.5.
Выбор режущего инструмента
Обрабатываемый материал
Состояние поверхности
Размеры обработанной поверхности
Геометрия режущей части
Вид и конструкция РИ
Фрезерно-центровальный станок МР76АМ
Фреза торцовая ГОСТ 1695-80 70
Сверло центровочное А 63 ГОСТ 14952-80
g=10°a=10° j=90° r=1 мм
g=10°a=10°j=90° r=1 мм
g=10° a=10°j=90° r=05 мм
Вертикальный шпоночно-фрезерный станок 692Р
Вертикальный зубофрезерный станок 53А20
Фреза червячная двухзаходная
Фреза червячная 100 ГОСТ 9324-80
Продолжение табл. 8.3
Фреза червячная одновитковая
Фреза червячная одновитковая 50
Шевер дисковый А 180 ГОСТ 8570-80
Сталь 40ХГНМ закаленная
Головка шлифовальная
Головка шлифовальная алмазная АГК
Круг шлифовальный ПП
Круг шлифовальный ПП 500*203*80
Круг шлифовальный Т 225*50*20
Круг полировальный ПП 500*203*40
Выбор средств контроля
Контролируемый размер
Мерительный инструмент
Измерительное контрольное устройство
Штангенциркуль ШЦ-1 ГОСТ 160-80
Штангенциркуль ШЦ-1 ГОСТ160-80
Микрометр МК-50 ГОСТ 6507-78
Прибор БВ-5061 цехового типа
Продолжение табл. 8.4
Задача раздела - рассчитать такие режимы резания которые обеспечили бы заданный выпуск деталей заданного качества с минимальными затратами.
1. Определение режимов резания
Режим резания - это сочетание глубины резания подачи и скорости резания.
Наша задача состоит в том чтобы найти единственное возможное сочетание элементов режима резания которое обеспечивает экстремальное значение критериев оптимальности (например минимальная себестоимость).
) Рассчитаем режимы резания на операцию 130 шлифовальную.
Для выбранной операции - шлифование чистовое - применим таблично - аналитический метод определения режимов резания.
Данную операцию выполним за один переход - врезное шлифование широким кругом.
Разработку режима резания при шлифовании начинают с установления характеристики инструмента. Для окончательного шлифования шейки вала-шестерни - пов. 6 из стали 40Х шероховатости Rа = 08 мкм выберем материал шлифовального круга - 25А25СМ17К ГОСТ 2424-82 [10]. Окончательная характеристика абразивного инструмента выявляется в процессе пробной эксплуатации с учетом конкретных технологических условий.
Основные параметры резания при шлифовании:
скорость вращательного или поступательного вращения заготовки
где Vз. табл.– скорость вращения детали по таблице ммин;
К– коэффициент учитывающий особенности торцекруглошлифования.
Vз. табл. =25 ммин К=1 карта ШК-3 [14].
частота вращения заготовки
глубина шлифования t мм - слой металла снимаемый периферией круга в результате радиальной подачи Sр при врезном шлифовании; глубина шлифования =0006 мм
радиальная подача определяемая по формуле:
Sр = Sр табл × К1 × К2 × К3
где К1 - коэффициент зависящий от обрабатываемого материала и скорости круга;
К2 - коэффициент зависящий от точности обработки шероховатости поверхности и припуска на сторону;
К3 - коэффициент зависящий от диаметра шлифовального круга;
Sр. табл. - поперечная подача по таблице мммин.
Для того чтобы определить коэффициент К1 найдём скорость шлифовального круга Vкр= мс
где Dкр - диаметр шлифовального круга мм;
n – частота вращения шпинделя обмин.
К1 = 06; К2 = 06; К3 = 09; Sр табл = 16 мммин карта ШК-3 [14]:
Sр = 16 × 1 × 06 × 06×09 = 052 мммин.
Эффективная мощность при врезном шлифовании периферией круга:
где d - диаметр шлифования d = 30013 мм;
b - ширина шлифования мм равная длине шлифуемого участка заготовки при круглом врезном шлифовании; для пов. 6 b = 43 мм.
Значение коэффициентов входящих в формулу (12.1) определим по таблице [10]: СN = 014; r = 08; q = 02; z = 10.
Тогда эффективная мощность при обработке пов. 6 равно
N6 = 014 × 002508 × 5002 × 4310 = 067 кВт
что меньше паспортной мощности станка. Из этого следует что выбранное оборудование удовлетворяет требованиям режимов резания.
2. Расчет норм времени
Нормирование ТП - это установление технически обоснованных норм времени на обработку детали.
Норма времени - регламентированное время выполнения заданного объема работ в определенных условиях исполнителем заданной квалификации.
В нашем случае следует рассчитать нормы времени на операции 160 шлифовальной.
Основное время tо - время непосредственно на обработку определяется исходя из схемы обработки:
tо = t6 + t17 + t8 + t15
где t6 t17 t8 и t15 – основное время обработки пов. 6 17 8 и 15
S - величина подачи мммин;
tвых - время выхаживания мин;
Lp S=052 ммоб; tвых=01 мин [14 карта ШК-3].
где z- припуск на обработку мм;
t- глубина шлифования ммоб;
n1 - частота вращения заготовки обмин;
Kв - коэффициент учитывающий выхаживание;
z=01; t=0005; n1=159 ; К=125
Суммарное время tо :
tо = 106 + 106 + 016+ 016=244 мин
Штучное время - время на выполнение операции определяется суммированием основного и вспомогательного времени.
Вспомогательное время - время на установку и снятие заготовки управление станком подвод и отвод режущего инструмента контроль размеров определяется по справочным нормативам или экспериментально.
В общем случае для шлифовальной операции штучное время определим по формуле:
tшт = tо × j где коэффициент j = 11 [15].
tшт = 244 × 11 = 268 мин.
Список использованной литературы
Анурьев В. И. Справочник конструктора – машиностроителя. В 3-х томах. – 6-е изд. перераб. и доп. – М.: Машиностроение 1982.
Горбацевич А. Ф. Шкред В. А. Курсовое проектирование по технологии машиностроения: [Учеб. пособие для машиностроит. спец. вузов]. – 4-е изд. перераб. и доп. – Мн.: Выш. школа 1983. – 256 с. ил.
Допуски и посадки. Справочник. В 2-х томах.Под ред. В. Д. Мягкова. – Л.: Машиностроение 1982 – 545 с.
А. Г. Косилова Р. К. Мещеряков М. А. Калинин. Точность обработки заготовок и припуски в машиностроении. Справочник технолога. М.; Машиностроение 1976. 288 с. ил.
Справочник технолога – машиностроителя. В 2-х томах. Под ред. А. Г. Косиловой и Р. К. Мещерякова. – 4-е изд. перераб. и доп. – М.: Машиностроение 1986
Курсачь ТехМаш2009 записка.doc
Кафедра оборудования и технологии
машиностроительного производства
по дисциплине: «Технология машиностроения»
«Технологический маршрут обработки детали вал-шестерня»
Преподаватель: Гордеев А.В.
Студент: Саттаров П.В.
Содержание расчетно-пояснительной записки
Анализ исходных данных. Служебное назначение и условия работы детали. Систематизация поверхностей . Анализ технологичности детали.
Выбор стратегии разработки ТП.
Выбор метода получения заготовки.
Выбор методов обработки поверхностей.
Определение припусков на обработку.
Проектирование заготовки.
Разработка технологического маршрута.
Выбор СТО (оборудование приспособление режущий инструмент средства контроля).
Разработка плана обработки и схем базирования.
Проектирование технологических операций. Расчет режимов резания и норм времени. Шлифование черновое.
Список используемой литературы.
Содержание графической части
Технологические наладки.
Анализ исходных данных.
1 Служебное назначение и условия работы детали
Деталь «Вал-шестерня» черт. 09.TM.27.001 является быстроходным валом цилиндрического редуктора и предназначена для передачи крутящего момента от привода к промежуточному валу редуктора. Вал-шестерня получает вращение от привода через муфту установленную по пов. 4 на шлицах и воспринимает крутящий момент боковыми поверхностями 3 шлицевых пазов. Вал-шестерня передает крутящий момент боковыми поверхностями 13 зубьев зубчатого венца зубьям венца промежуточного вала. Вал-шестерня установлен в подшипниках качения в корпусе редуктора.
Вал-шестерня работает в условиях действия радиальной знакопеременной сосредоточенной нагрузки и крутящего момента. Зубья зубчатого венца испытывают действие изгибающего усилия контактного давления и сил трения. Под действием последних происходит нагрев и изнашивание зубьев.
2 Систематизация поверхностей
Все поверхности детали на эскизе нумеруем и систематизируем по их назначению.
Исполнительные поверхности (И) выполняющие служебные функции вала-шестерни – передачу крутящего момента - боковые поверхности 12 зубьев и боковые поверхности 3 шлицев.
Основные конструкторские базы (ОБ) определяющие положение вала-шестерни в редукторе цилиндрические подшипниковые шейки пов. 6 и 17 и торцовые поверхности 8 и 15
Вспомогательные конструкторские базы (ВБ) определяющие положение присоединяемых деталей – цилиндрическая пов. 6 шлицевая пов. 2 и 3 верхний профиль шлицев пов. 4
Свободные поверхности (С) не сопрягающиеся с другими деталями - пов. 1 5 7 9 10 11 13 14 16 18.
Номера поверхностей и их назначения заносим в графы1-3 таб. 1.4. В таблице приняты обозначения формы поверхностей:
Ц - цилиндрическая наружная
КВ - коническая внутренняя
3 Анализ технических требований
Марка материала – сталь 40Х ГОСТ 4543-71 указана в основной надписи. Твердость 40 45 HRC п.1 технических требований. На чертеже даны все размеры необходимые для изготовления и контроля детали. Точность размеров задана комбинированным способом в виде посадки квалитета точности и предельных отклонений по ГОСТ 2.307-79. Точность свободных размеров 14 квалитет п.2 технических требований. Шероховатость поверхностей указана непосредственно на изображении и в правом верхнем углу чертежа. Предельные отклонения формы и расположение поверхностей 6 8 15 17 заданы в виде условных обозначений по ГОСТ 2.308-79 отклонения для остальных поверхностей должны укладываться в допуск на размер. Формы размеры и точность шлицев определенны – по ГОСТ 1139-58. Фаски и радиусы закруглений выполнены по ГОСТ 10948-64.
Характеристики поверхности вал шестерня
Вывод: черт. 09. ТМ. 27. 001 содержит все необходимые сведения для разработки ТП обработки детали “Вал промежуточный”.
4 Анализ технологичности детали
Материал детали – сталь 40Х ГОСТ 4543-71: 036 044% С; 05 08% 08 110% . Твёрдость в состоянии поставки до 217 НВ после закалки - 45 HRC. Прочность sв в состоянии поставки до 795 МПа после закалки - 8801080 МПа. Эти механические характеристики обеспечивают нормальную работу вала-шестерни в редукторе. Материал не является дефицитным. Термообработка выполняется по типовому техпроцессу и не требует специальных условий. Сталь имеет удовлетворительную обрабатываемость резанием коэффициент обрабатываемости Ко=08 при обработке твёрдосплавным инструментом и Ко=07 при обработке инструментом из быстрорежущей стали.
Заготовку вала можно получить как из проката так и обработкой давлением – штамповкой или высадкой. В обоих случаях форма заготовки и её элементов достаточно простая.
Свободные поверхности выполнены по 14 квалитету точности. На заготовительных операциях такой точности не добиться поэтому предусматривается обработка всех поверхностей
Таким образом с точки зрения получения заготовки деталь можно считать технологичной.
5 Технологичность общей конфигурации
Вал-шестерню Радиусы закруглений и фаски выполняются по ГОСТ 10948-64 форма и размеры канавок – по ГОСТ 8820-69 формы размеры и точность шлицев определенны – по ГОСТ 1139-58. Такая унификация упростит обработку и контроль этих элементов вала-шестерни.
можно отнести к типу деталей “Валы” для которых разработан типовой ТП. Деталь не содержит каких-либо специфических особенностей формы поэтому может быть обработана непосредственно по типовому ТП.
Форма детали позволяет вести обработку одновременно нескольких
поверхностей – цилиндрических 4 6 9 11 и торцовых 8 10; цилиндрических 17 14 11 и торцовых 13 15 . Одновременно несколько заготовок удастся обработать только на многошпиндельном станке что вряд ли целесообразно для серийного производства. В остальных случаях оборудование может быть простым универсальным. Оснастку можно также применить универсальную. Все поверхности вала-шестерни доступны для контроля.
Таким образом с точки зрения общей компоновки детали её можно считать технологичной.
6 Технологичность базирования и закрепления
Черновыми базами для установки заготовки на 1-й операции могут быть цилиндрические шейки и торцовые поверхности заготовки. В дальнейшем за базы могут быть приняты как цилиндрические поверхности 4 7 так и специально выполненные центровые отверстия 19 и 20 по ГОСТ 14034-74.
Измерительные базы детали можно использовать в качестве технологических баз. Точность и шероховатость этих баз обеспечит требуемую точность обработки. Таким образом с точки зрения базирования и закрепления деталь следует считать технологичной.
7 Технологичность обрабатываемых поверхностей
Предполагается обработать все поверхности детали т.к. заданные точность и шероховатость не позволяют получить их на заготовительных операциях. Правда можно исключить из обработки торцы пов. 1 и 18 в случае обеспечения их точности и шероховатости при отрезке проката но целесообразность этого может быть установлена только после детального анализа. Всего обрабатывается 18 поверхностей: 6 цилиндрических 4 6 9 11 14 17 ; 7 торцовых 1 5 8 10 13 15 18 ; зубья 12 ; шлицы пов. 2 3 ; 2 канавки пов. 7 и 16 . Т.е. даже при полной обработке число
обрабатываемых поверхностей относительно невелико.
Протяжённость обрабатываемых поверхностей относительно невелика и определяется условиями компоновки редуктора и работы вала-шестерни.
Точность и шероховатость рабочих поверхностей 3 4 6 8 12 15 17 определяются условиями работы вала-шестерни. Уменьшение точности приведёт к снижению точности установки вала в редукторе и надёжности его работы. Увеличение шероховатости этих поверхностей приведёт к снижению надёжности сопряжений и интенсивному изнашиванию поверхностей.
Форма детали позволяет обрабатывать пов. 1 6 11 17 18 на проход.
Обработка поверхностей 3 4 5 7 8 9 10 13 14 15 16 в упор затруднений не вызывает.
Поверхности различного назначения разделены что облегчает обработку. Для выхода резца и шлифовального круга при обработке пов. 6 и 17 предусмотрены канавки 7 и 16 . Нетехнологичным следует считать отсутствие канавки для выхода шлифовального круга на пов. 4 что затрудняет её обработку. Таким образом с точки зрения обрабатываемых поверхностей деталь следует считать технологичной.
Поскольку деталь “Вал-шестерня” отвечает требованиям технологичности по всем 4 группам критериев можно сделать вывод о её достаточно высокой технологичности.
Выбор стратегии разработки ТП
Деталь «Вал-шестерня» черт. 09.ТМ.27.001. Объем выпуска N = 2000 детгод.
1. Определение типа производства
Тип производства определяем исходя из расчетного объема выпуска N0 детгод:
где m – масса детали m = 133кг;
KT – коэффициент трудоемкости изготовления для детали средней сложности KT = 1.
что соответствует среднесерийному производству.
2. Выбор стратегии разработки ТП
Пользуясь табл. 3.1 принимаем следующую стратегию разработки ТП:
) В области организации ТП:
Вид стратегии – последовательная в отдельных случаях циклическая; линейная в отдельных случаях разветвленная; жесткая в отдельных случаях адаптивная.
Повторяемость изделий – периодическая партиями.
Форма организации ТП – переменно-поточная
) В области выбора и проектирования заготовки:
Метод получения заготовки – прокат или штамповка.
Выбор методов обработки – по таблицам с учетом коэффициентов удельных затрат Куд.
Припуск на обработку незначительный.
Метод определения припусков – укрупненный по таблицам в отдельных случаях расчёт по переходам.
) В области разработки технологического маршрута:
Степень унификации ТП – разработка ТП на базе типового ТП.
Степень детализации разработки ТП – маршрутный ТП в отдельных случаях – маршрутно-операционный ТП.
Принцип формирования маршрута – экстенсивная в отдельных случаях интенсивная концентрация операций.
Обеспечение точности – работа на настроенном оборудовании с частичным применением активного контроля.
Базирование – с соблюдением принципа постоянства баз и по возможности – принципа совмещения баз.
) В области выбора средств технологического оснащения (СТО):
Оборудование – универсальное в том числе с ЧПУ.
Приспособления – универсальные стандартные универсально-сборные в отдельных случаях специальные.
Режущие инструменты – стандартные в отдельных случаях специальные.
Средства контроля – универсальные в отдельных случаях модернизированные.
) В области проектирования технологических операций:
Содержание операций – по возможности одновременная обработка нескольких поверхностей исходя из возможностей оборудования.
Загрузка оборудования – периодическая смена деталей на станках.
Коэффициент закрепления операций Кзо = 20 30.
Расстановка оборудования – по типам и размерам станков местами по ходу ТП.
Настройка станков – по измерительным инструментам и приборам либо работа без предварительной настройки по промерам.
) В области нормирования ТП:
Определение режимов резания – по общемашиностроительным нормативам в отдельных случаях – по эмпирическим формулам.
Нормирование – укрупненное по опытно-статистическим нормам в отдельных случаях – детальное пооперационное.
Квалификация рабочих – достаточно высокая.
Технологическая документация – маршрутно-операционные карты.
Принятой стратегией мы будем руководствоваться при разработке ТП.
Выбор метода получения заготовки
Выбрать оптимальный метод получения заготовки детали «Вал-шестерня» черт. 09.ТМ.27.001. Производство среднесерийное.
По табл. 4.1 определяем что для детали типа «Валы» средней сложности из стали для серийного производства целесообразно применить в качестве заготовки прокат или горячую штамповку. Для окончательного выбора метода получения заготовки выполним сравнительный экономический анализ. В основу анализа положим сравнение суммарных стоимостей С переменной доли затрат на получение заготовки Сз и ее механическую обработку Собр:
где i — номер варианта получения заготовки. В нашем случае i=1 для заготовки из проката i=2 для штампованной заготовки.
Переменные затраты на получение заготовки Сз руб. составляют:
Сзi=Цмi Мзi Кспi Кслi (3.2)
Кспi Кслi— коэффициенты учитывающие соответственно способ получения заготовки и ее сложность.
Рассчитаем Сз для каждого из вариантов.
) Вычерчиваем контур детали (рис. 3.1). На этом же эскизе вычерчиваем контуры заготовки из проката рис 3.1 и штамповки рис 3.2 (без масштаба).
) По табл. 4.7 определяем ориентировочно припуск на обработку Z:
а) для заготовки из проката:
пов. 1 18 l1=145 l2=74 Z=4
пов. 11 l1=37 l2=145 Z=3.
б) для штампованной заготовки:
пов. 1 l1=95 l2=30 Z=3
пов. 6 l1=30 l2=95 Z=28
пов. 8 l1=4 l2=45 Z=22
пов. 11 l1=74 l2=18 Z=3
пов. 15 l1=3 l2=45 Z=22
пов. 17 l1=30 l2=25 Z=22
пов. 18 l1=25 l2=30 Z=22
Определяем размеры заготовки с учетом припусков и проставляем на рис. 3.1 3.2.
) Определяем напуски.
Для заготовки из проката принимаем ближайший диаметр прутка 80.
Для штамповки назначаем предварительно уклон 50 и радиусы переходов R2.
Вычерчиваем напуски на рис. 3.1 3.2 и проставляем размеры заготовки с учетом припусков и напусков.
) Определяем массу детали МД и заготовки МЗ кг:
МД=0785( d12l1 + d22 l2 + . . . + dn2ln ) r
n число элементарных объемов;
r плотность стали; r=000785 кгсм3.
МД=0785(28248 + 3247+45204+74218+45203+3225)000785=133 кг
где d—диаметр проката см;
l—длина заготовки см.
МЗ1=07858.062155000785=62 кг
МЗ2=0785·(3562958+494204+8224+4.9420.3+3.562×2.58)000785 =2 кг.
) Коэффициент использования материала:
КИМ1=МДМЗ1=133:62=021
КИМ2=МДМЗ2=133:2=066
) Определяем ЦМ руб.кг по табл. 4.2 и поправочные коэффициенты по табл.4.3-4.4:
) Подставляем найденные значения в формулу (3.2):
СЗ1 = 1462121 = 1041 руб.
СЗ2 = 142251 = 70 руб.
Переменные затраты на черновую обработку Собр руб. составляют:
СМi = Суд (Мзi — Мд) Ко (3.3)
где Суд — удельные затраты на снятие 1 кг стружки при черновой обработке руб.кг;
Ко — коэффициент обрабатываемости материала.
Рассчитаем СМ для каждого из вариантов.
)По табл. 4.5 определяем для среднесерийного производства Суд=26.
)По табл. 4.6 определяем для стали 40Х Ко = 08.
)Подставляем найденные значения в формулу (3.3):
СМ1=26(62-133)08=1583 руб.
СМ2=26(2–133)08=8645 руб.
Подставляя полученные значения Сз и СМ в формулу (3.1) получим:
С1 = 1041 + 1583 = 2624 руб.
С2 = 70 + 8645 = 1564 руб.
По минимуму переменных затрат принимаем 2-й вариант - штамповка
Выбор методов обработки поверхностей
Варианты обработки пов. 6 и 17
В табл. 4.1 обозначено:
ТП–точение получистовое
Ш–шлифование черновое
ШП–шлифование получистовое
ШЧ–шлифование чистовое
Рядом с обозначением метода обработки в скобках указан квалитет точности получаемый на данном переходе а сверху– коэффициент удельных затрат КУj для данного перехода.
Оптимальный вариант обработки выбираем по минимуму суммарных удельных затрат характеризуемых суммой КУi всех переходов данного варианта. При этом поскольку переходы Т(12) и ШЧ(6) а также ТО присутствуют во всех вариантах обработки их из расчёта исключаем.
Из табл. 4.1. видно что минимальный коэффициент удельных затрат КУ=61 соответствует варианту 3 предусматривающему ТО после чистовой токарной обработки. Поэтому примем этот вариант обработки:
Т(12; 125)–ТП(10; 63)– ТЧ(8; 16)–ТО(9)– ШП(8; 16)–ШЧ(6; 08).
Здесь в скобках указаны квалитет точности и шероховатость поверхности Ra мкм для каждого перехода.
Для обработки места под сальник пов. 6 (6-й квалитет Ra=04) принимаем дополнительный переход полирование.
Полученным выше результатом воспользуемся для назначения методов обработки других поверхностей.
Шейка под муфту пов. 4 (6-й квалитет Ra=08):
Т(12; 125)–ТП(10; 63)– ТЧ(8; 16)–ТО(9)– ШП(8; 16)–ШЧ(6; 08).
Наружная поверхность зубчатого венца пов. 11 (11; 63):
Т(12; 125)–ТП(10; 63)–ТО(11).
Свободные шейки пов. 9 и 14 канавки пов. 7 16 (14; 125):
Уступы пов. 8 и 15 (8; 16):
Т(12; 125)–ТП(10; 63)– ТЧ(8; 16)–ТО(9)– ШП(8; 16)..
Уступ пов. 5 (10; 32):
Т(12; 125)–ТП(10; 63)–ТО(11)
Торцы зубчатого венца пов. 10 и 13 (14; 125):
Торцы пов. 1 и 18 (14; 125):
Боковые поверхности Шлицев пов. 3 (6; 08)
Ф(8; 32)–ТО(9) – Шч(6; 08)
Впадины шлице пов. 2 (9; 32)
Зубчатый венец пов. 12 (6 степень точности Ra=08):
ЗФ(8 ст.; 63)–СФ–ШВ(7 ст.; 16)–ТО.
ЗФ–зубофрезерование
Центровые отверстия пов. 19 и 20
Методы обработки поверхностей сводим в табл. 4.2.
Методы обработки поверхностей
Т–ТП– ТЧ –ТО–ШП–ШЧ –ПО
Определение припусков на обработку поверхностей
Определить припуски на обработку детали “Вал-шестерня” черт. 09.ТМ.27.001. Метод получения заготовки – штамповка. Производство среднесерийное. Припуск на самую точную поверхность рассчитать суммированием по переходам на остальные поверхности – по табл. 4.7.
Самыми точными поверхностями детали “Вал-шестерня” являются пов. 6
) По данным работы 4 записываем в графы 1 3 № заготовительного перехода (№0) его наименование (способ получения заготовки) и квалитет точности. По данным работы 5 в эти же графы записываем №№ переходов мехобработки их наименование и квалитет точности.
) По табл. 1.1 определяем допуски Td для каждого перехода и заносим в графу 4 табл.5.1.
) Определяем допуск формы и расположения Тр=03Тd для каждого перехода и заносим в графу 5 табл. 5.1.
) По табл. 5.1 определяем толщину дефектного слоя а для каждого перехода и заносим в графу 6 табл. 5.1.
) По табл. 5.2 определяем допуск на точность установки заготовки в приспособлении для каждого перехода кроме заготовительного и заносим в графу 7 табл. 5.1.
) По формуле (5.1) рассчитаем припуск Z для каждого перехода кроме заготовительного. Полученные значения округляем до знака после запятой с которым задан допуск Td.
Результаты расчета заносим в графу 8 табл. 5.1 начиная с 1-го перехода.
) Определяем операционные размеры. Диаметр d5 задан на чертеже детали:
) Общий припуск на обработку составляет:
Рассчитываем припуск на пов 11.
Определяем операционные размеры. Диаметр d2 задан на чертеже детали:
Общий припуск на обработку составляет:
Рассчитываем припуск на пов 8.
Определяем операционные размеры. d4 задан на чертеже детали:
Рассчитываем припуск на пов 15.
Общий припуск на обработку составляет
Рассчитываем припуск на пов 1 18.
Определяем операционный размер. d4 задан на чертеже детали:
Общий припуск на обработку составляет
Сравнивая значения припусков полученных суммированием по переходам с табличными видим что переход от табличного метода определения припусков к расчетному приводит к существенному уменьшению припусков.
Проектирование штампованной заготовки
) Вычерчиваем контур детали. Проставляем размеры (рис. 6.1)
) Вычерчиваем контур заготовки заготовка будет содержать 3 ступени (рис. 6.1).
) Определяем припуски на обработку по таблице 4.7. Результаты заносим в графу 3 табл. 6.1. Определяем расчетные размеры заготовки путем прибавления припусков к размерам детали и округления их до 05 мм в сторону увеличения припуска. Результаты заносим в графу 4 табл. 6.1.
)Плоскость разъема – диаметральное продольное сечение заготовки. При таком положении плоскости разъема полость штампа имеет наименьшую глубину. В этой плоскости удобно контролировать смещение штампа. Заготовка получается симметричной что делает возможность поворачивания ее при штамповке и уменьшать износ штампа.
)В качестве технологических баз на 1-й операции мехобработки
целесообразно использовать – пов. 6 8 17 .
) Определяем класс точности Т штамповки. При открытой штамповке обеспечивается точность Т4.
Расчет размеров заготовки
Положение поля допуска
) Определяем группу стали М в зависимости от содержания углерода С и легирующих элементов Л. Для стали 40Х У=036 044% Л5% что соответствует группе М2.
) Определяем степень сложности заготовки в зависимости от коэффициента Кс=WзWо где – Wз – объем заготовки; Wо – объем описанного цилиндра.
где di и i - диаметр и длина соответствующей ступени заготовки.
где d – диаметр описанного цилиндра; - длина заготовки.
что соответствует степени сложности С2.
)Определяем исходный индекс И.
где Ио – начальный индекс зависящий от массы заготовки.
Им Ис Ит – добавочные индексы в зависимости от М С Т.
здесь – плотность стали
для mЗ=19 Ио=5; Им=1; Ис=1; Ит=4.
) Определяем допуски на размеры заготовки в зависимости от
исходного индекса по табл. 7.3 и заносим их значения в графу 5 табл. 6.1.
) Определяем штамповочные уклоны. Согласно рекомендациям принимаем значения уклонов 7º.
) Определяем радиусы закруглений R. По табл. 7.3 для глубины полости штампа 20 мм при массе заготовки mЗ=19кг R=2мм. Допуск на радиус для класса точности Т4 составляет ±025R=±05мм.
) Определяем допустимые значения остаточного облоя То и смещения штампа Тс. По табл. 7.4 для mЗ=19 кг и точности Т4 То=08мм Тс=06мм.
Разработка технологического маршрута
Разработать технологический маршрут обработки детали «Вал-шестерня» черт. 09.ТМ.27.001. Производство среднесерийное.
) Выписываем номера поверхностей их форму точность размеров формы и расположения шероховатость. Заносим эти данные в графы 1-5 табл. 7.1.
Методы обработки поверхностей детали «Вал промежуточный»
Т–ТП– ТЧ -ТО–ШП – ШЧ
Т–ТП– ТЧ –ТО–ШП–ШЧ–ПО
Т–ТП– ТЧ – ТО– ШП – ШЧ
)Для каждой поверхности определяем методы обработки и записываем их в графу 6 табл. 7.1 [1].
)Используя типовой технологический маршрут [2] определяем предварительно порядок и наименование операций по обработке поверхностей детали “Вал промежуточный”. Полученные данные заносим в табл. 7.2.
)Анализируем предварительный маршрут на предмет целесообразности перестановки объединения разделения или замены операций.
Учитывая серийный тип производства объединяем в одну операцию фрезерование торцов 1 18 и сверление центровых отверстий 19 20 полагая что они будут выполняться на фрезерно-центровальном станке.
Операции получистового и чистового точения объединим в одну для каждого конца вала.
) С учетом этих изменений формируем окончательный вариант технологического маршрута который представлен в табл. 7.3
Предварительный маршрут обработки детали “Вал промежуточный”
Сверление центровых отверстий
Черновое точение правого конца
Черновое точение левого конца
Получистовое точение правого конца
Получистовое точение левого конца
Зачистка центровых отверстий
Черновое шлифование правого конца
Черновое шлифование левого конца
Получистовое шлифование правого конца
Получистовое шлифование левого конца
Чистовое шлифование правого конца
Чистовое шлифование левого конца
Шлифование зубьев шлицев
Окончательный маршрут обработки детали “Вал промежуточный”
Наименование операции
Фрезерно-центровальная
Фрезерование торцов 118.
Сверление центровых отверстий 1920
Черновое точение пов. 1011897654.
Черновое точение пов. 13–17
Получистовое и чистовое точение пов. 11864
Получистовое и чистовое точение пов. 1517
Нарезание шлицев пов. 23
Фрезерование зубьев пов. 12
Снятие фасок пов. 12
Зачистка центровых отверстий 19 20
Черновое получистовое и чистовое шлифование пов. 867
Черновое получистовое и чистовое шлифование пов. 1517
Шлифование зубьев 12 и боковую пов. шлицев 3
Выбор средств технологического оснащения
1. Выбор оборудования
При выборе типа и модели металлорежущих станков будем руководствоваться следующими правилами:
) Производительность точность габариты мощность станка должны быть минимальными достаточными для того чтобы обеспечить выполнение требований предъявленных к операции.
) Станок должен обеспечить максимальную концентрацию переходов на операции в целях уменьшения числа операций количества оборудования повышения производительности и точности за счет уменьшения числа перестановок заготовки.
) В случае недостаточной загрузки станка его технические характеристики должны позволять обрабатывать другие детали выпускаемые данным цехом участком.
) Оборудование не должно быть дефицитным следует отдавать предпочтение отечественным станкам.
) В мелкосерийном производстве следует применять преимущественно универсальные станки револьверные станки станки с ЧПУ многоцелевые станки (обрабатывающие центры). На каждом станке в месяц должно выполняться не более 40 операций при смене деталей по определенной закономерности.
) Оборудование должно отвечать требованиям безопасности эргономики и экологии.
Если для какой-то операции этим требованиям удовлетворяет несколько моделей станков то для окончательного выбора будем проводить сравнительный экономический анализ.
Выбор оборудования проводим в следующей последовательности:
) Исходя из формы обрабатываемой поверхности и метода обработки выбираем группу станков.
) Исходя из положения обрабатываемой поверхности выбираем тип станка.
) Исходя из габаритных размеров заготовки размеров обработанных поверхностей и точности обработки выбираем типоразмер (модель) станка.
Данные по выбору оборудования заносим в табл. 8.1.
2. Выбор приспособлений
При выборе приспособлений будем руководствоваться следующими правилами:
) Приспособление должно обеспечивать материализацию теоретической схемы базирования на каждой операции с помощью опорных и установочных элементов.
) Приспособление должно обеспечивать надежные закрепление заготовки обработке.
) Приспособление должно быть быстродействующим.
) Зажим заготовки должен осуществляться как правило автоматически.
) Следует отдавать предпочтение стандартным нормализованным универсально-сборным приспособлениям и только при их отсутствии проектировать специальные приспособления.
Исходя из типа и модели станка и метода обработки выбираем тип приспособления.
Выбор приспособления будем производить в следующем порядке:
) Исходя из теоретической схемы базирования и формы базовых поверхностей выбираем вид и форму опорных зажимных и установочных элементов.
) Исходя из расположения базовых поверхностей и их состояния (точность шероховатость) формы заготовки и расположения обрабатываемых поверхностей выбираем конструкцию приспособлений.
) Исходя из габаритов заготовки и размеров базовых поверхностей выбираем типоразмер приспособления.
После расчета режима резания (разд. 12) определим силы резания по значению которых рассчитываем силу зажима достаточную для обеспечения надежного закрепления.
Учитывая передаточный коэффициент усиления определим усилие и мощность привода. Сравним эти значения с характеристиками приспособления. Если силы зажима или мощность превосходят допустимые значения то выбираем более мощное приспособление.
Данные по выбору приспособлений заносим в табл. 8.2.
Штамповка.frw

Штамповка рабочий чертеж.frw

продолжение пояс.записки.docx
Расположение поверхностей
Габариты заготовки мммм
Размеры обработ. поверхн.
Тип модель оборудования
Фрезерование сверление
Фрезерно-центровальный полуавтомат
Токарно-винторезный станок 16Б16Т1
Токарно-винторезный станок 16Б16ПТ1
Продолжение табл. 8.1
Токарно-винторезный станок 16Б16ПТ1
Горизонтальный шпоночно-фрезерный станок 692Р
Вертикальный зубофрезерный станок 53А20
Зубофасочный станок ВС-320А
Горизонтальный зубошевинговальный станок 5702В
Центрошлифовальный станок 3922Е
Круглошлифовальный станок 3А151
Зубошлифовальный станок 5851
Полировально-шлифовальный станок 3А352
Выбор приспособлений
Базовая поверхность.
Установочные элементы
Типоразмер приспособления
Фрезерно-центровальный МР-76АМ
Призма установочная
Тиски самоцентрирующиеся с призматическими губками 50 ГОСТ 12195-66
Токарно-винторезный станок
Центр подпружиненный
А1-3-НП-ЧПУ ГОСТ 8742-75
Патрон поводковый ГОСТ 2571-71.
Центр вращающийся ГОСТ 8742-75
Продолжение табл. 8.2.
Продолжение табл.8.2.
Вертикально шпоночно-фрезерный станок 692Р
Вертикальный зубофрезерный станок 52А20
Патрон цанговый. Центр вращающийся ГОСТ 8742-75
Зубофасочный станок ВС-320А
Зубошевинговальный станок 5702В
Центрошлифовальный станок 3К225В
Патрон мембранный ГОСТ 16157-70
Центр неподвижный ГОСТ 8742-75
Патрон поводковый ГОСТ 2571-71. Центр подвижный ГОСТ 8740-75
Центр неподвижныйГОСТ 8742-75
Патрон цанговый ГОСТ 2571-71. Центр вращающийся ГОСТ 8742-75
3. Выбор режущего инструмента
При выборе РИ будем руководствоваться следующими правилами:
)Выбор инструментального материала определяется требованиями с одной стороны максимальной стойкости а с другой минимальной стоимости.
)Следует отдавать предпочтение стандартным и нормализованным инструментам. Специальный инструмент следует проектировать в крупносерийном и массовом производстве выполнив предварительно сравнительный экономический анализ.
)При проектировании специального РИ следует руководствоваться рекомендациями по совершенствованию РИ.
Выбор режущего инструмента (РИ) будем производить в следующем порядке:
)Исходя из типа и модели станка расположения обрабатываемых поверхностей и метода обработки определяем вид РИ.
)Исходя из марки обрабатываемого материала его состояния и состояния поверхности выбираем марку инструментального материала.
)Исходя из формы обрабатываемой поверхности назначаем геометрические параметры режущей части (форма передней поверхности углы заточки: g a j j1 l; радиус при вершине).
)Исходя из размеров обрабатываемой поверхности выбираем конструкцию инструмента его типоразмер и назначаем период стойкости Т.
Данные по выбору РИ заносим в табл. 8.3.
4. Выбор средств контроля
При выборе средств контроля будем руководствоваться следующими правилами:
)Точность измерительных инструментов и приспособлений должна быть существенно выше точности измеряемого размера однако неоправданное повышение точности ведет к резкому удорожанию.
)В единичном и мелкосерийном производстве следует применять инструменты общего назначения: штангенциркули микрометры длинномеры и т.д.
)В крупносерийном – специальные инструменты.
)Следует отдавать предпочтение стандартным и нормализованным средствам контроля.
Данные по выбору средств контроля заносим в табл. 8.4.
Результаты выбора средств технологического оснащения заносим в табл. 8.5.
Выбор режущего инструмента
Обрабатываемый материал
Состояние поверхности
Размеры обработанной поверхности
Геометрия режущей части
Вид и конструкция РИ
Фрезерно-центровальный станок МР76АМ
Фреза торцовая ГОСТ 1695-80 70
Сверло центровочное А 63 ГОСТ 14952-80
Вертикальный шпоночно-фрезерный станок 692Р
Вертикальный зубофрезерный станок 53А20
Фреза червячная двухзаходная
Фреза червячная 100 ГОСТ 9324-80
Продолжение табл. 8.3
Фреза червячная одновитковая
Фреза червячная одновитковая 50
Шевер дисковый А 180 ГОСТ 8570-80
Сталь 40ХГНМ закаленная
Головка шлифовальная
Головка шлифовальная алмазная АГК
Круг шлифовальный ПП
Круг шлифовальный ПП 500*203*80
Круг шлифовальный Т 225*50*20
Круг полировальный ПП 500*203*40
Выбор средств контроля
Контролируемый размер
Мерительный инструмент
Измерительное контрольное устройство
Штангенциркуль ШЦ-1 ГОСТ 160-80
Штангенциркуль ШЦ-1 ГОСТ160-80
Микрометр МК-50 ГОСТ 6507-78
Прибор БВ-5061 цехового типа
Продолжение табл. 8.4
Задача раздела рассчитать такие режимы резания которые обеспечили бы заданный выпуск деталей заданного качества с минимальными затратами.
1. Определение режимов резания
Режим резания это сочетание глубины резания подачи и скорости резания.
Наша задача состоит в том чтобы найти единственное возможное сочетание элементов режима резания которое обеспечивает экстремальное значение критериев оптимальности (например минимальная себестоимость).
) Рассчитаем режимы резания на операцию 130 шлифовальную.
Для выбранной операции - шлифование чистовое - применим таблично - аналитический метод определения режимов резания.
Данную операцию выполним за один переход врезное шлифование широким кругом.
Разработку режима резания при шлифовании начинают с установления характеристики инструмента. Для окончательного шлифования шейки вала-шестерни - пов. 6 из стали 40Х шероховатости Rа = 08 мкм выберем материал шлифовального круга - 25А25СМ17К ГОСТ 2424-82 [10]. Окончательная характеристика абразивного инструмента выявляется в процессе пробной эксплуатации с учетом конкретных технологических условий.
Основные параметры резания при шлифовании:
скорость вращательного или поступательного вращения заготовки
где Vз. табл.– скорость вращения детали по таблице ммин;
К– коэффициент учитывающий особенности торцекруглошлифования.
Vз. табл. =25 ммин К=1 карта ШК-3 [14].
частота вращения заготовки
глубина шлифования t мм - слой металла снимаемый периферией круга в результате радиальной подачи Sр при врезном шлифовании; глубина шлифования =0006 мм
радиальная подача определяемая по формуле:
Sр = Sр табл К1 К2 К3
где К1 - коэффициент зависящий от обрабатываемого материала и скорости круга;
К2 - коэффициент зависящий от точности обработки шероховатости поверхности и припуска на сторону;
К3 - коэффициент зависящий от диаметра шлифовального круга;
Sр. табл. - поперечная подача по таблице мммин.
Для того чтобы определить коэффициент К1 найдём скорость шлифовального круга Vкр= мс
где Dкр - диаметр шлифовального круга мм;
n – частота вращения шпинделя обмин.
К1 = 06; К2 = 06; К3 = 09; Sр табл = 16 мммин карта ШК-3 [14]:
Sр = 16 1 06 0609 = 052 мммин.
Эффективная мощность при врезном шлифовании периферией круга:
где d - диаметр шлифования d = 30013 мм;
b - ширина шлифования мм равная длине шлифуемого участка заготовки при круглом врезном шлифовании; для пов. 6 b = 43 мм.
Значение коэффициентов входящих в формулу (12.1) определим по таблице [10]: СN = 014; r = 08; q = 02; z = 10.
Тогда эффективная мощность при обработке пов. 6 равно
N6 = 014 002508 5002 4310 = 067 кВт
что меньше паспортной мощности станка. Из этого следует что выбранное оборудование удовлетворяет требованиям режимов резания.
2. Расчет норм времени
Нормирование ТП - это установление технически обоснованных норм времени на обработку детали.
Норма времени - регламентированное время выполнения заданного объема работ в определенных условиях исполнителем заданной квалификации.
В нашем случае следует рассчитать нормы времени на операции 160 шлифовальной.
Основное время о - время непосредственно на обработку определяется исходя из схемы обработки:
где 6 17 8 и 15 – основное время обработки пов. 6 17 8 и 15
S - величина подачи мммин;
вых - время выхаживания мин;
Lp S=052 ммоб; вых=01 мин [14 карта ШК-3].
где z- припуск на обработку мм;
t- глубина шлифования ммоб;
n1 - частота вращения заготовки обмин;
Kв - коэффициент учитывающий выхаживание;
z=01; t=0005; n1=159 ; К=125
о = 106 + 106 + 016+ 016=244 мин
Штучное время - время на выполнение операции определяется суммированием основного и вспомогательного времени.
Вспомогательное время - время на установку и снятие заготовки управление станком подвод и отвод режущего инструмента контроль размеров определяется по справочным нормативам или экспериментально.
В общем случае для шлифовальной операции штучное время определим по формуле:
шт = о где коэффициент = 11 [15].
Список использованной литературы
Анурьев В. И. Справочник конструктора – машиностроителя. В 3-х томах. – 6-е изд. перераб. и доп. – М.: Машиностроение 1982.
Горбацевич А. Ф. Шкред В. А. Курсовое проектирование по технологии машиностроения: [Учеб. пособие для машиностроит. спец. вузов]. – 4-е изд. перераб. и доп. – Мн.: Выш. школа 1983. – 256 с. ил.
Допуски и посадки. Справочник. В 2-х томах.Под ред. В. Д. Мягкова. – Л.: Машиностроение 1982 – 545 с.
А. Г. Косилова Р. К. Мещеряков М. А. Калинин. Точность обработки заготовок и припуски в машиностроении. Справочник технолога. М.; Машиностроение 1976. 288 с. ил.
Справочник технолога – машиностроителя. В 2-х томах. Под ред. А. Г. Косиловой и Р. К. Мещерякова. – 4-е изд. перераб. и доп. – М.: Машиностроение 1986
Поверхности чертежа.cdw

Неуказанные предельные отклонения размеров диаметров h14
Кромки зубьев притупить фаской 0
Методичка 2007.doc
Практические работы
по дисциплине «Основы технологии
Проектирование технологического
процесса механической обработки
Методическое пособие
Гордеев А.В. Практические работы по дисциплине «Основы технологии машиностроения». Проектирование технологического процесса механической обработки. Методическое пособие для студентов машиностроительных специальностей вузов и колледжей. Тольятти Тольяттинский государственный университет 2007 90 с.
В пособии рассмотрены основные этапы разработки технологических процессов механической обработки деталей. Определен порядок работы на каждом этапе. Приведены справочные сведения. Рассмотрены примеры проектирования техпроцесса воспользоваться которыми студенты могут при самостоятельной разработке техпроцессов механической обработки. Пособие может быть использовано также при курсовом и дипломном проектировании.
Научный редактор к.т.н. доцент Воронов Д.Ю.
к.т.н. профессор Грисенко Е.В. (Пермский технический университет)
Цель практических работ по дисциплине «Основы технологии машиностроения» научиться разрабатывать оптимальный технологический процесс механической обработки деталей.
С этой целью студенту дается задание на разработку техпроцесса (ТП) обработки заданной детали.
Разработка ТП включает следующие основные этапы:
)Анализ исходных данных.
)Анализ технологичности детали.
)Выбор стратегии разработки техпроцесса.
)Выбор метода получения заготовки.
)Выбор метода обработки поверхностей.
)Определение припусков на обработку.
)Проектирование штампованной заготовки.
)Разработка технологического маршрута.
)Разработка схем базирования.
) Разработка плана обработки детали.
) Выбор средств технологического оснащения
Анализ исходных данных
Цель работы – научиться анализировать рабочие чертежи деталей при разработке технологических процессов (ТП) механической обработки.
Анализ исходных данных для проектирования ТП механической обработки детали начинают с анализа её чертежа.
Грамотно выполненный чертеж детали дает исчерпывающую информацию о её форме размерах точности размеров формы и расположения шерохова-тости поверхности материале его твердости качестве поверхностного слоя габаритах и массе детали использованных стандартах и технических условиях способе маркировки и т.д. Чертеж детали средней сложности содержит около сотни параметров характеризующих ее. Задача технолога – спроектировать ТП так чтобы ни один параметр не остался без внимания.
В первую очередь технолог должен четко представить себе служебное наз-начение детали и условия ее работы.
Под служебным назначением детали понимают характер выполняемых ею служебных функций (передача усилия или крутящего момента перемещение фиксация поворот базирование и т.п.) и требования к их выполнению (точ-ность быстродействие КПД долговечность надежность и т.п.)
Под условиями работы детали понимают качественную и количественную характеристику воздействующих на нее факторов (характер и величину нагру-зок напряжения в опасных сечениях трение в контакте скорости давления температуры характер изнашивания и т.п.)
Деталь содержит достаточно большое число поверхностей каждая из кото-рых выполняет определенные функции. С помощью одних поверхностей де-таль выполняет свое служебное назначение другие поверхности служат для установки детали в узле или для присоединения других деталей. Третьи повер-хности не участвуют в работе и служат для придания детали определенной формы. В соответствии с различным назначением поверхностей различаются и требования к ним. Чтобы проанализировать эти требования необходимо систе-матизировать поверхности детали по их служебному назначению.
Поверхности детали делятся на сопрягаемые взаимодействующие с повер-хностью другой детали и свободные (С) оформляющие конфигурацию дета-ли. В свою очередь сопрягаемые поверхности могут выполнять различные функции.
Поверхности детали выполняющие ее служебные функции называют исполнительными (И).
Поверхности детали определяющие положение данной и других деталей в узле (сборочной единице) называют конструкторскими базами. Различают основные и вспомогательные конструкторские базы.
Основные конструкторские базы (ОБ) – это конструкторские базы опре-деляющие положение детали в сборочной единице. ОБ лишают деталь необхо-димого числа степеней свободы – перемещения вдоль координатных осей и поворотов вокруг этих осей.
Вспомогательные конструкторские базы (ВБ) – это конструкторские базы определяющие положение присоединяемых деталей относительно данной де-тали. С помощью ВБ данная деталь лишает присоединяемые детали опреде-ленного числа степеней свободы.
Перед систематизацией все поверхности детали нумеруют по порядку на-чиная с 1. Номера поверхностей указывают на чертеже детали синим или фио-летовым цветом в кружках на выносках. При этом допускается пересечение выносками основных и вспомогательных линий чертежа (при выполнении уче-бного задания на ПК допускается обозначение поверхностей черным цветом при этом число пересечений необходимо свести к минимуму). Размер цифр обозначающих поверхность на 1 – 2 номера больше цифр обозначающих раз-меры.
При анализе исходных данных для разработки ТП механической обработки детали поверхности делят на 4 группы: И ОБ ВБ С. При этом некоторые по-верхности могут выполнять несколько функций и соответственно относиться к нескольким типам (например И и ВБ).
Далее технолог проверяет полноту задания требований к узлу или детали на чертеже. Так на чертеже детали должны быть указаны марка материала и вид заготовки (отливка поковка прокат) со ссылкой на соответствующие стандарты и задана твердость всех поверхностей. Должны быть представлены все размеры необходимые для изготовления и контроля – величина каждой поверхности (длина ширина высота радиус) ее положение (расстояние от оси или другой поверхности угол) справочные размеры (получаемые по другому чертежу замыкающие размеры цепи). На каждый размер должна быть задана точность в виде поля допуска или предельных отклонений проставленных возле номинального размера или в технических требованиях. На каждую поверхность должна быть назначена шероховатость условным знаком на контурной или выносной линии либо в правом верхнем углу чертежа. Должны быть заданы необходимые допуски формы и расположения – прямолинейности плоскостности круглости цилиндричности профиля продольного сечения и т. п. в виде условного обозначения или пункта технических требований.
Проверяют также правильность задания требований на чертеже. Все требо-вания должны быть заданы по ГОСТ и стандартам предприятий (СТП) чтобы исключить их неоднозначное толкование). Размеры должны задаваться преи-мущественно от одной базы. Форма и размеры шпоночных пазов фасок ка-навок радиусов переходов галтелей и др. элементов должны соответствовать ГОСТ.
После анализа чертежа детали исходные данные заносят в таблицу (см. табл. 1.4) в которой указывают номер тип и форму каждой поверхности их размеры с допусками и квалитет точности вид и величину погрешностей формы и расположения и соответствующий этой величине квалитет точности шероховатость.
Если точность размеров на чертеже указана в виде индекса посадки и квали-тета (например 50к6) или в виде предельных отклонений (например ) либо в пункте технических требований указанием посадки и квалитета (напри-мер h14 ±IT142) то недостающие для заполнения граф 5 и 6 табл. 1.4 сведения берут из табл. 1.1 и 1.2.
Если точность формы или расположения задана условным обозначением с указанием предельного отклонения Тр по ГОСТ 2.308-79 то условный квалитет точности определяют по табл. 1.3.
Допуски на размеры по ГОСТ 25346-82
Предельные отклонения валов по ГОСТ 25346-82
Предельные отклонения мкм
Допуски формы и расположения в мкм по ГОСТ 24643-81
Радиальное биение соосность симметричность для квалитета
Параллельность перпендикулярность торцевое биение для квалитета
Плоскостность прямолинейность цилиндричность круглость профиль продольного сечения для квалитета
По сборочному чертежу выполнить рабочий чертежа заданной детали.
Описать служебное назначение и условия работы детали.
Пронумеровать и систематизировать поверхности детали.
Проанализировать технические требования к детали.
Пример выполнения работы №1
Деталь «Вал-шестерня» черт. 07.ТМ.13.001.
1 Служебное назначение и условия работы детали
Деталь «Вал-шестерня» черт. 07.ТМ.13.001 является быстродным валом цилиндрического редуктора и предназначена для передачи крутящего момента от привода к промежуточному валу редуктора. Вал-шестерня получает вращение от привода через муфту установленную по пов. 4 на шпонке и воспринимает крутящий момент боковыми поверхностями 3 шпоночного паза. Вал-шестерня передает крутящий момент боковыми поверхностями 12 зубьев зубчатого венца зубьям венца промежуточного вала. Вал-шестерня установлен в подшипниках качения в корпусе редуктора.
Вал-шестерня работает в условиях действия радиальной знакопеременной сосредоточенной нагрузки и крутящего момента. Зубья зубчатого венца испытывают действие изгибающего усилия контактного давления и сил трения. Под действием последних происходит нагрев и изнашивание зубьев.
2 Систематизация поверхностей
Все поверхности детали на эскизе нумеруем и систематизируем по их назначению.
Исполнительные поверхности (И) выполняющие служебные функции вала-шестерни – передачу крутящего момента боковые поверхности 12 зубьев и боковые пов. 3 шпоночного паза.
Основные конструкторские базы (ОБ) определяющие положение вала-шестерни в редукторе цилиндрические подшипниковые шейки пов. 6 и
Вспомогательные конструкторские базы (ВБ) определяющие положение присоединяемых деталей – цилиндрическая пов. 4 торцовая пов. 5 шпоночный паз пов. 2 и 3 торцовая пов. 15 .
Свободные поверхности (С) не сопрягающиеся с другими деталями
пов. 1 7 9 10 11 13 14 16 18 .
Номера поверхностей и их назначение заносим в графы 1-3 табл. 1.4. В таблице приняты обозначения формы поверхностей:
Ц - цилиндрическая наружная
КВ - коническая внутренняя
3 Анализ технических требований
Марка материала – сталь 40ХГНМ ГОСТ 4543-71 указана в основной надписи. Твердость 46±2 HRC п.1 технических требований. На чертеже даны все размеры необходимые для изготовления и контроля детали. Точность размеров задана комбинированным способом в виде посадки квалитета точности и предельных отклонений по ГОСТ 2.307-79. Точность свободных размеров 14 квалитет п.2 технических требований. Шероховатость поверхностей указана
непосредственно на изображении и в правом верхнем углу чертежа. Предельные отклонения формы и расположения поверхностей 3 4 5 6 8 15 17 заданы в виде условных обозначений по ГОСТ 2.308-79 отклонения для остальных поверхностей должны укладываться в допуск на размер.
Форма и размеры шпоночного паза заданы по ГОСТ 23360-78. Фаски и радиусы закруглений выполнены по ГОСТ 10948-64.
Характеристика поверхностей детали «Вал – шестерня»
Вывод: черт. 07. ТМ. 13. 001 содержит все необходимые сведения для разработки ТП обработки детали “Вал промежуточный”.
Анализ технологичности детали
Цель работы – научиться анализировать технологичность конструкции детали по ее рабочему чертежу.
Под технологичностью детали понимают совокупность ее свойств позволяющих изготовить деталь с наименьшими затратами.
Перед тем как приступить к разработке ТП технолог должен проанализировать конструкцию детали с точки зрения ее технологичности и в случае необходимости дать предложения по изменению конструкции с целью повышения ее технологичности.
Оценку технологичности детали проводят по 4 группам признаков (критериев технологичности):
технологичность заготовки
технологичность общей конфигурации детали
технологичность базирования и закрепления
технологичность обрабатываемых поверхностей.
1.Технологичность заготовки
С точки зрения снижения себестоимости обработки заготовка должна быть максимально приближена по форме к готовой детали. Однако усложнение заготовки ведет к повышению ее стоимости. Оптимальную сложность заготовки и способ ее получения определяют путем экономического анализа (см. работу №4). Кроме того технологичность заготовки характеризуется следующими критериями:
) Обрабатываемость материала заготовки. Обрабатываемость материала – это способность его к обработке резанием. Характеризуется коэффициентом обрабатываемости
где V и V0 – скорость резания при стойкости инструмента 60 мин. при обработке соответственно данного материала и стали 45 твердостью HB 179. По значению К0 материалы разделяют на 5 групп: св.15 – высокая обрабатываемость; 15 10 – повышенная; 10 08 – удовлетворительная; 08 05 – пониженная; менее 05 – низкая. Ухудшение обрабатываемости снижает производительность и удорожает изготовление детали. Следовательно чем выше обрабатываемость тем выше уровень технологичности.
) Использование унифицированной заготовки. Применение проката в т.ч. профильного сокращает мехобработку. Применение одинаковых заготовок для групп деталей хотя и удорожает мехобработку может существенно снизить затраты на заготовку.
)Возможность получения заготовки рациональным способом. Рациональной считают заготовку в которой все элементы имеют простую геометрическую форму и плавно сопряжены друг с другом. Литая заготовка должна иметь достаточную толщину стенок литейные уклоны по возможности не иметь стержней. Штампованная заготовка должна иметь плоскую поверхность разъема штамповочные уклоны расположение выступающих элементов с одной стороны высоту меньше длины и ширины. Иногда целесообразно сложную заготовку выполнить сварной.
)Окончательное формирование свободных поверхностей на заготовительных операциях. Поскольку свободные поверхности не контактируют с др. деталями во время работы машины их следует по возможности получать без обработки резанием что существенно снизит затраты на обработку в целом.
2. Технологичность общей конфигурации
)Использование стандартных и унифицированных элементов. Унификация диаметров проката толщины листа диаметров валов и осей межосевых расстояний посадочных размеров галтелей фасок радиусов уклонов позволяет унифицировать инструмент и приспособления применять высокопроизводительное оборудование.
)Возможность применения типового ТП. Применение группового и типового ТП с наименьшими изменениями удешевляет разработку ТП и гарантирует его качество. Эта возможность повышается при приближении конструкции данной детали к базовой за счет унификации ее элементов.
) Возможность одновременной обработки нескольких заготовок. Конфигурация детали должна позволять устанавливать несколько заготовок в одном приспособлении обрабатывать совместно сопрягаемые детали.
) Возможность одновременной обработки нескольких поверхностей. Обрабатываемые поверхности следует располагать так чтобы можно было обработать их одновременно несколькими инструментами: торцы бобышек располагать в одной плоскости отверстия – с межцентровым расстоянием не менее 50 мм.
) Возможность применения простых средств технологического оснащения средств механизации и автоматизации. Следует избегать расположения отверстий и торцов бобышек под углом к базе обеспечивать вход и выход осевого инструмента под углом близким к 90º к поверхности избегать фасок на поверхностях сложного профиля.
) Доступ к местам обработки и контроля. Удобный доступ к обрабатываемым поверхностям позволяет применить более простую оснастку для обработки и контроля.
3. Технологичность базирования и закрепления
) Наличие опорных поверхностей (баз). Чтобы лишить заготовку определенного числа степеней свободы (перемещений поворотов) при установке в приспособлении она должна иметь соответствующее количество баз. Отсутствие баз требует дополнительной выверки каждый раз при установке новой заготовки. Наиболее технологичной является конструкция позволяющая полностью обработать деталь от одних и тех же баз. При этом базы должны иметь достаточные размеры обеспечивающие устойчивое положение при обработке.
) Совпадение технологической и измерительной баз. Технологическая база – это поверхность по которой заготовка устанавливается в приспособлении при обработке. Измерительная база – поверхность от которой производят измерение размера после обработки. Минимальная погрешность будет при их совпадении.
) Точность и шероховатость базовых поверхностей. Чтобы обеспечить точность установки при обработке и контроле базовые поверхности сами должны иметь достаточную точность формы и шероховатость.
) Возможность захвата роботом. При обработке с использованием роботов заготовка должна иметь поверхность захвата соответствующую типу схвата робота и расположенную возможно ближе к центру тяжести заготовки.
4. Технологичность обрабатываемых поверхностей
)Номенклатура обрабатываемых поверхностей. Уменьшение номенклатуры обрабатываемых поверхностей по форме размерам точности шероховатости за счет их унификации сокращает цикл обработки номенклатуру режущего и мерительного инструмента облегчает настройку станков.
)Количество и протяженность обрабатываемых поверхностей. Число
поверхностей обработки и их величина определяются служебным назначением детали. После достижения оптимального значения дальнейшее их увеличение не улучшает существенно выполнение деталью своих функций и в то же время удорожает обработку. Технологичной является замена сплошной опорной обрабатываемой поверхности опорными выступами.
)Точность и шероховатость. Эти показатели также обусловлены служебным назначением детали. Стоимость обработки резко возрастает с повышением требований к точности и шероховатости поверхности. Поэтому предельные отклонения размеров и формы шероховатость поверхностей детали должны быть максимальными допустимыми требованием к выполнению деталью своих функций.
)Возможность обработки на проход. Расположение поверхностей с возможностью обработки их при одном установе сокращает число переустановок заготовки что повышает точность обработки и сокращает вспомогательное время операции. Технологичными являются расположение поверхностей ступенчатого вала по одну сторону бурта отсутствие выступов на плоской обрабатываемой поверхности соосное расположение отверстий меньший диаметр внутреннего отверстия по отношению к наружному или их равенство замена отверстий с двух сторон одним сквозным отверстием замена глухих отверстий на сквозные.
)Разделение поверхностей различного назначения. Поверхности детали
имеющие различное служебное назначение различаются конфигурацией точностью шероховатостью что требует различных условий их обработки. Для обеспечения этого необходимо отделять поверхности различного назначения друг от друга канавкой уступом.
)Возможность выхода инструмента. При обработке поверхности инструмент не должен касаться других поверхностей. Конструкция детали должна предусматривать возможность выхода инструмента в конце рабочего хода например наличие канавки.
Проанализировать технологичность данной детали и в случае необходимости дать предложения по изменению конструкции детали.
Пример выполнения работы №2
1 Технологичность заготовки
Материал детали – сталь 40ХГНМ ГОСТ 4543-71: 036044 % С; 017037% S 0609% 0711% N 01503 Pb . Твёрдость в состоянии поставки до 241 НВ после закалки- 46 HRC. Прочность sв в состоянии поставки до 795 МПа после закалки-8801080 МПа [1] .Эти механические характеристики обеспечивают нормальную работу вала-шестерни в редукторе. Материал не является дефицитным. Термообработка выполняется по типовому техпроцессу и не требует специальных условий. Сталь имеет удовлетворительную обрабатываемость резанием коэффициент обрабатываемости Ко=08 при обработке твёрдосплавным инструментом и Ко=07 при обработке инструментом из быстрорежущей стали [1] .
Заготовку вала можно получить как из проката так и обработкой давлением – штамповкой или высадкой. В обоих случаях форма заготовки и её элементов достаточно простая.
Свободные поверхности выполнены по 14 квалитету точности. На заготовительных операциях такой точности не добиться поэтому предусматривается обработка всех поверхностей
Таким образом с точки зрения получения заготовки деталь можно считать технологичной.
2 Технологичность общей конфигурации
Радиусы закруглений и фаски выполняются по ГОСТ 10948-64 форма и размеры канавок – по ГОСТ 8820-69 размеры шпоночного паза – по ГОСТ 23360-78. Такая унификация упростит обработку и контроль этих элементов вала-шестерни.
Вал-шестерню можно отнести к типу деталей “Валы” для которых разработан типовой ТП. Деталь не содержит каких-либо специфических особенностей формы поэтому может быть обработана непосредственно по типовому ТП.
Форма детали позволяет вести обработку одновременно нескольких поверхностей – цилиндрических 4 6 9 11 и торцовых 5 8 10 ; цилиндрических 17 14 11 и торцовых 13 15 . Одновременно несколько заготовок удастся обработать только на многошпиндельном станке что вряд ли целесообразно для серийного производства. В остальных случаях оборудование может быть простым универсальным. Оснастку можно также применить универсальную. Все поверхности вала-шестерни доступны для контроля.
Таким образом с точки зрения общей компоновки детали её можно считать технологичной.
3 Технологичность базирования и закрепления
Черновыми базами для установки заготовки на 1-й операции могут быть цилиндрические шейки и торцовые поверхности заготовки. В дальнейшем за базы могут быть приняты как цилиндрические поверхности 4 6 17 так и специально выполненные центровые отверстия 19 и 20 по ГОСТ 14034-74.
Измерительные базы детали можно использовать в качестве технологических баз. Точность и шероховатость этих баз обеспечит требуемую точность обработки. В случае применения гибкого технологического модуля имеется возможность захвата заготовки роботом за пов. 9 .
Таким образом с точки зрения базирования и закрепления деталь следует считать технологичной.
4 Технологичность обрабатываемых поверхностей
Предполагается обработать все поверхности детали т.к. заданные точность и шероховатость не позволяют получить их на заготовительных операциях. Правда можно исключить из обработки торцы пов. 1 и 18 в случае обеспечения их точности и шероховатости при отрезке проката но целесообразность этого может быть установлена только после детального анализа. Всего обрабатывается 18 поверхностей: 6 цилиндрических 4 6 9 11 14 17 ; 7 торцовых 1 5 8 10 13 15 18 ; зубья 12 ; шпоночный паз пов. 2
; 2 канавки пов. 7 и 16 . Т.е. даже при полной обработке число обрабатываемых поверхностей относительно невелико.
Протяжённость обрабатываемых поверхностей относительно невелика и определяется условиями компоновки редуктора и работы вала-шестерни.
Точность и шероховатость рабочих поверхностей 3 4 5 6 8 12 15 17 определяются условиями работы вала-шестерни. Уменьшение точности приведёт к снижению точности установки вала в редукторе и надёжности его работы. Увеличение шероховатости этих поверхностей приведёт к снижению надёжности сопряжений и интенсивному изнашиванию поверхностей.
Форма детали позволяет обрабатывать пов. 1 6 11 17 18 на проход.
Обработка поверхностей 3 4 5 7 8 9 10 13 14 15 16 в упор затруднений не вызывает.
Поверхности различного назначения разделены что облегчает обработку. Для выхода резца и шлифовального круга при обработке пов. 6 и 17 предусмотрены канавки 7 и 16 . Нетехнологичным следует считать отсутствие канавки для выхода шлифовального круга на пов. 4 что затрудняет её обработку. По согласованию с конструктором введём такую канавку пов. 21 что не ухудшит эксплуатационные свойства детали но сделает её более технологичной.
Таким образом с точки зрения обрабатываемых поверхностей деталь следует считать технологичной.
Поскольку деталь “Вал-шестерня” отвечает требованиям технологичности по всем 4 группам критериев можно сделать вывод о её достаточно высокой технологичности.
Выбор стратегии разработки техпроцесса
Цель работы – научиться определять стратегию разработки ТП механической обработки.
Стратегия разработки ТП – принципиальный подход к определению его составляющих (показателей ТП) которые определяются в первую очередь типом производства а также его технологическими возможностями.
Тип производства характеризуется годовым объемом выпуска данных деталей и их сложностью размерами массой. Ориентировочно тип производства можно определить по формуле:
где m – масса детали кг;
N0 и N – расчетный и фактический объемы выпуска детгод;
KT – коэффициент трудоемкости изготовления (сложности) детали; для средней сложности KT = 1 простой – KT =075 сложной – KT = 135.
Тогда при N0 400 производство считают единичным
0 2300 – мелкосерийным
00 15000 – среднесерийным
000 100000 – крупносерийным
N0 >100000 – массовым.
Показатели ТП можно разделить на 6 групп характеризующих организацию ТП заготовку технологический маршрут средства технологического оснащения (СТО) технологические операции нормирование ТП.
Наиболее вероятные показатели по каждой из этих групп для единичного серийного и массового типов производства приведены в таблице 3.1. При мелкосерийном типе производства применяют промежуточные значения показателей между единичным и серийным типами а при крупносерийном – между серийным и массовым типами.
По заданному объему выпуска определить тип производства.
Для данного типа производства определить показатели ТП по всем 6 группам.
Показатели ТП для различных типов производства
1. Вид стратегии разработки ТП
2. Повторяемость изделий
3. Форма организации ТП
отсутствие заранее обусловленной повторяемости
групповая; как исключение – индивидуальная
промежуточные характеристики
периодическое повторение партий
переменно – поточная (партионная) или непоточная
непрерывный выпуск в течение длительного времени
1. Метод получения заготовки
2. Выбор последовательности обработки
3. Припуск на обработку
4. Метод определения припусков
прокат литье в землю свободная ковка
по укрупненным таблицам
укрупненный по таблицам
профильн. прокат литье в кокиль штамповка
по таблицам с учетом коэффициентов удельных затрат
спецпрокат точное литье штамповка редуцирование
аналитический по коэффициентам уточнения
детальный на базе размерного анализа
Продолжение табл.3.1
Технологический маршрут
1. Степень унификации ТП
2. Степень детализации разработки ТП
3. Принцип формирования
4.Синхронизация операций
5. Обеспечение точности
преимущественное использование типовых ТП
экстенсивная концентрация операций
разработка спец. ТП на базе типовых
маршрутно-операционный
на настроенном оборудовании с частичным применением активного контроля
постоянство и частичное совмещение баз
разработка спец. ТП на базе анализа
интенсивная концентрация операций дифференциация операций
на настроенном оборудовании с активным контролем и адаптивным управлением
совмещение и постоянство баз
3. Режущие инструменты
4. Средства контроля
универсальное в т.ч. с ЧПУ ГТС
универсальные универсально – сборные
стандартные нормализованные
универсальное и специализированное (модернизированное)
универсальные нормализованные специальные
стандартные нормализованные специальные
универсальные модернизированные
в основном специальные
Продолжение табл. 3.1
Технологические операции
1 Содержание операций
2. Загрузка оборудования
3. Коэффициент закрепления операций
4. Расстановка оборудования
5. Настройка станков
обработка нескольких поверхностей исходя из возможностей оборудования
загрузка различными деталями без закономерности
по типам и размерам станков (технологическая специализация участков)
отсутствие настройки работа по промерам
одновременная обработка нескольких поверхностей за счет модернизации СТО
периодическая смена деталей на станках
комбинированная (технологическая и предметная специализация)
по измерительным инструментам и приборам
одновременная обработка максимального числа поверхностей в т.ч. за счет применения спец. СТО
непрерывная загрузка станков одними деталями
по ходу ТП (предметная специализация участков)
1. Определение режимов резания
3. Квалификация рабочих
4. Технологические карты
по общемашиностроительным нормативам
укрупненное по опытно-статисти-ческим нормам
по отраслевым нормативам и эмпирическим формулам
детальное пооперационное
маршрутно-операционные
аналитически на базе математической модели
детальное на основании хронометража
низкая при высокой квалификации наладчиков
операционные с детализацией по переходам
Пример выполнения работы №3
Деталь «Вал-шестерня» черт. 07.ТМ.13.001. Объем выпуска N = 2000 детгод.
1. Определение типа производства
Тип производства определяем исходя из расчетного объема выпуска N0 детгод:
где m – масса детали m = 9 кг;
KT – коэффициент трудоемкости изготовления для детали средней сложности KT = 1.
что соответствует среднесерийному производству.
2. Выбор стратегии разработки ТП
Пользуясь табл. 3.1 принимаем следующую стратегию разработки ТП:
) В области организации ТП:
Вид стратегии – последовательная в отдельных случаях циклическая; линейная в отдельных случаях разветвленная; жесткая в отдельных случаях адаптивная.
Повторяемость изделий – периодическая партиями.
Форма организации ТП – переменно-поточная или непоточная.
) В области выбора и проектирования заготовки:
Метод получения заготовки – прокат или штамповка.
Выбор методов обработки – по таблицам с учетом коэффициентов удельных затрат Куд.
Припуск на обработку незначительный.
Метод определения припусков – укрупненный по таблицам в отдельных случаях расчёт по переходам.
) В области разработки технологического маршрута:
Степень унификации ТП – разработка ТП на базе типового ТП.
Степень детализации разработки ТП – маршрутный ТП в отдельных случаях – маршрутно-операционный ТП.
Принцип формирования маршрута – экстенсивная в отдельных случаях интенсивная концентрация операций.
Обеспечение точности – работа на настроенном оборудовании с частичным применением активного контроля.
Базирование – с соблюдением принципа постоянства баз и по возможности – принципа совмещения баз.
) В области выбора средств технологического оснащения (СТО):
Оборудование – универсальное в том числе с ЧПУ.
Приспособления – универсальные стандартные универсально-сборные в отдельных случаях специальные.
Режущие инструменты – стандартные в отдельных случаях специальные.
Средства контроля – универсальные в отдельных случаях модернизированные.
) В области проектирования технологических операций:
Содержание операций – по возможности одновременная обработка нескольких поверхностей исходя из возможностей оборудования.
Загрузка оборудования – периодическая смена деталей на станках.
Коэффициент закрепления операций Кзо = 20 30.
Расстановка оборудования – по типам и размерам станков местами по ходу ТП.
Настройка станков – по измерительным инструментам и приборам либо работа без предварительной настройки по промерам.
) В области нормирования ТП:
Определение режимов резания – по общемашиностроительным нормативам в отдельных случаях – по эмпирическим формулам.
Нормирование – укрупненное по опытно-статистическим нормам в отдельных случаях – детальное пооперационное.
Квалификация рабочих – достаточно высокая.
Технологическая документация – маршрутно-операционные карты.
Принятой стратегией мы будем руководствоваться при разработке ТП.
Выбор метода получения заготовки
Цель работы – овладеть методикой экономически обоснованного выбора оптимального метода получения заготовки детали.
Выбор метода получения заготовки определяется технологическими возможностями как заготовительного производства так и механической обработки. Чем точнее заготовка чем ближе она по форме к готовой детали тем меньше мехобработки она требует меньше расход металла дешевле мехобработка. Но сама заготовка при этом тоже становится дороже. Если же взять простую дешевую заготовку возрастают отходы металла и затраты на мехобработку.
На первой стадии разработки ТП при выборе вариантов метода получения заготовки можно руководствоваться таблицей 4.1. Согласно табл. 4.1 метод получения заготовки определяется типом детали (корпус вал диск втулка) видом материала (чугун сталь алюминиевый сплав бронза) сложностью фор-мы детали типом производства (единичное серийное массовое). Наиболее распространенными методами получения заготовок являются: литье в земляные (песчаные) формы (ЛЗ) литье в металлические формы (кокили) (ЛМ) литье по выплавляемым моделям (ЛВ) литье в оболочковые формы (ЛО) литье под давлением (ЛД) центробежное литье (ЦЛ) свободная ковка (К) штамповка (Ш) холодная штамповка (ХШ). Иногда целесообразно в качестве заготовки принимать прокат (П) – круг шестигранник трубу лист. Средняя точность заготовок обеспечиваемая этими методами приведена в табл. 4.3.
Следует иметь в виду что каждый метод имеет несколько технологических разновидностей из которых тоже важно выбрать оптимальные для данных условий.
Если имеется несколько альтернативных методов получения заготовки ни один из которых не имеет явного преимущества перед остальными необходимо провести экономический анализ. В качестве критерия оптимальности при выборе наивыгоднейшего метода получения заготовки в первом приближении можно принять минимальный объем С руб. переменной доли затрат на получение заготовки С3 и ее механическую обработку См которые зависят от метода получения заготовки:
Переменные затраты на получение заготовки С3 руб. составляют:
где Цм – цена 1 кг исходного материала которую определяют по действующим на момент анализа прейскурантам. Для некоторых конструкционных материалов ориентировочное значение Цм приведено в табл. 4.2;
Мз – масса заготовки кг;
Ксп Ксл – коэффициенты учитывающие соответственно способ получения заготовки и ее сложность. Ориентировочные значения этих коэффициентов для различных условий приведены в табл. 4.3 и 4.4
Переменные затраты на механическую обработку См руб. составляют:
где Суд – удельные затраты на снятие 1 кг стружки при черновой мехобработке руб.кг. Значение Суд берут по данным предприятия. При отсутствии таких данных для предварительных расчетов можно воспользоваться таблицей 4.5;
Мд – масса детали кг;
Ко – коэффициент обрабатываемости материала значения которого приведены в справочной литературе. Для некоторых конструкционных материалов значения Ко приведены в таблице 4.6.
Отметим что данная методика пригодна и при изменении цен поскольку их соотношение как правило сохраняется. Однако это справедливо только для оценки правильности выбора метода получения заготовки. При определении же себестоимости изготовления детали следует пользоваться специальной литературой.
Методы получения заготовок
Стоимость исходного материала Цм
Значение коэффициентов Ксп
Литье в земляную форму
Литье по металлической модели
Литье в оболочковую форму
Литье по выплавляемой модели
Ковка в подкладных штампах
Значение коэффициента Ксл
Группа сложности отливки по
Степень сложности поковки по
Удельные затраты на снятие 1 кг стружки Суд
Значение коэффициента обрабатываемости Ко
Приблизительные значения припусков на обработку Z мм на сторону
Максимальный размер мм до
Способ получения заготовки
На основе экономического анализа вариантов выбрать оптимальный способ получения заготовки заданной детали для заданного типа производства.
Порядок выполнения работы
)Вычерчивают в масштабе контур детали с простановкой размеров
)По табл. 4.1 выбирают возможные методы получения заготовки (обычно
)По упрощенной методике табл. 4.7 определяют припуск на черновую
обработку для каждого метода. На том же эскизе вычерчивают контуры заготовки с учетом припусков для каждого метода.
)Исходя из технологических возможностей методов получения заготовки
(уклоны радиусы отверстия число ступеней и т.п.) устанавливают напуски. На том же эскизе вычерчивают контуры заготовки с учетом напусков для каждого метода проставляют размеры заготовки.
)Определяют объем и массу детали Мд и заготовок Мзi (i – порядковый
)По табл. 4.2 определяют цену материала Цм.
)По табл. 4.3 и 4.4 определяют Ксп и Ксл для каждого метода.
)По формуле (4.2) определяют Сзi для каждого метода.
)По табл. 4.5 и 4.6 определяют Суд и Ко.
) По формуле (4.3) определяют Смi для каждого метода.
) По формуле (4.1) определяют Ci для каждого метода получения заготовки. Метод получения заготовки обеспечивающий наименьшее значение Ci будет оптимальным для данных условий.
Пример выполнения работы №4
Выбрать оптимальный метод получения заготовки детали «Вал-шестерня» черт. 07.ТМ.13.001. Производство среднесерийное.
По табл. 4.1 определяем что для детали типа «Валы» средней сложности из стали для серийного производства целесообразно применить в качестве заготовки прокат или горячую штамповку. Для окончательного выбора метода получения заготовки выполним сравнительный экономический анализ. В основу анализа положим сравнение суммарных стоимостей С переменной доли затрат на получение заготовки Сз и ее механическую обработку Собр:
где i — номер варианта получения заготовки. В нашем случае i=1 для заготовки из проката i=2 для штампованной заготовки.
Переменные затраты на получение заготовки Сз руб. составляют:
Сзi=Цмi Мзi Кспi Кслi (4.2)
Кспi Кслi— коэффициенты учитывающие соответственно способ получения заготовки и ее сложность.
Рассчитаем Сз для каждого из вариантов.
) Вычерчиваем контур детали (рис. 4.1). На этом же эскизе вычерчиваем контуры заготовки из проката и штамповки (без масштаба).
) По табл. 4.7 определяем ориентировочно припуск на обработку Z:
а) для заготовки из проката:
пов. 1 18 l1=400 l2=128 Z=8
пов. 11 l1=64 l2=400 Z=42.
б) для штампованной заготовки:
пов. 1 l1=160 l2=50 Z=5
пов. 6 l1=50 l2=60 Z=35
пов. 8 l1=60 l2=70 Z=4
пов. 9 l1=70 l2=60 Z=4
пов. 10 l1=50 l2=128 Z=35
пов. 11 l1=128 l2=50 Z=5
пов. 13 l1=50 l2=128 Z=35
пов. 14 l1=60 l2=130 Z=5
пов. 18 l1=400 l2=50 Z=75
Определяем размеры заготовки с учетом припусков и проставляем на рис. 4.1.
) Определяем напуски.
Для заготовки из проката принимаем ближайший диаметр прутка 140.
Для штамповки назначаем предварительно уклон 50 и радиусы переходов R3.
Вычерчиваем напуски на рис. 4.1 и проставляем размеры заготовки с учетом припусков и напусков.
) Определяем массу детали МД и заготовки МЗ кг:
МД=0785( d12l1 + d22 l2 + . . . + dn2ln ) r
n число элементарных объемов;
r плотность стали; r=000785 кгсм3.
МД=0785(428 + 528 + 726 + 12825 + 627 + 526)000785=1135 кг
где d—диаметр проката см;
l—длина заготовки см.
МЗ1=0785142416000785=502 кг
МЗ2=0785·(572161 + 782605 + 138257 + 7213)000785 =161 кг.
) Коэффициент использования материала:
КИМ1=МДМЗ1=1135:467=023
КИМ2=МДМЗ2=1135:161=07
) Определяем ЦМ руб.кг по табл. 4.2 и поправочные коэффициенты по табл.4.3-4.4:
) Подставляем найденные значения в формулу (4.2):
СЗ1 = 1450.2121 = 8434 руб.
СЗ2 = 14161251 = 5635 руб.
Переменные затраты на черновую обработку Собр руб. составляют:
СМi = Суд (Мзi — Мд) Ко (4.3)
где Суд —удельные затраты на снятие 1 кг стружки при черновой обработке руб.кг;
Ко — коэффициент обрабатываемости материала.
Рассчитаем СМ для каждого из вариантов.
)По табл. 4.5 определяем для среднесерийного производства Суд=26.
)По табл. 4.6 определяем для стали 40ХГНМ Ко = 08.
)Подставляем найденные значения в формулу (4.3):
СМ1=26(502-1135):08=1262 руб.
СМ2=26(161–1135)08=1543 руб.
Подставляя полученные значения Сз и СМ в формулу (4.1) получим:
С1 = 8434 + 1262 = 21054 руб.
С2 = 5635 + 1543 = 7178 руб.
По минимуму переменных затрат принимаем 2-й вариант – штамповку.
Выбор методов обработки поверхностей
Цель работы овладеть методикой назначения оптимальных методов обработки поверхности детали и их последовательности.
Выбор методов обработки поверхностей детали и их последовательности для каждой поверхности определяются:
видом поверхности (наружная или внутренняя поверхность вращения плоскость фасонная поверхность и т.п.);
материалом заготовки и его состоянием (чугун незакаленная сталь закаленная сталь цветные сплавы и т.п.);
типом заготовки (литье штамповка их разновидности прокат и т.п.) ее точностью и состоянием поверхности;
требуемой точностью и шероховатостью поверхности детали;
типом производства (единичное серийное массовое).
Экономически целесообразно в результате каждого перехода:
начиная с 12 квалитета повышать точность не более чем на 2 квалитета (121086) а начиная с 6 квалитета – не более чем на 1 квалитет;
при черновой обработке (Ra≥32) шероховатость уменьшать не более чем в 4 раза а при чистовой обработке (Ra≤25) – в 2 раза.
Варианты экономических методов обработки приведены в табл. 5.1.
В табл. 5.1 обозначены:
АВ – алмазное выглаживание
о – обдирочноеп – получистовое ч – чистовое т – тонкое.
Выбор экономически целесообразных методов в каждом конкретном случае делают по результатам экономического анализа из условия минимума суммарных расходов на обработку. Для сравнения затрат при каждом из методов обработки в табл. 5.2 приведены значения коэффициента удельных затрат Ку представляющего отношение стоимости данного метода при данных условиях к стоимости базового метода при этих же условиях. Оптимальным сочетанием методов обработки поверхности следует считать такое которое обеспечивает минимальный суммарный коэффициент
Методы обработки поверхностей
– сталь 2 – чугун цветные сплавы
Примечание: Если ТП обработки детали пониженной жесткости (ld≥6) включает термообработку ТО ее точность в результате коробления при ТО снижается ~ на 1 квалитет.
Для каждой поверхности детали определить количество переходов мехобработки для достижения заданной точности и шероховатости поверхности и путем экономического анализа вариантов выбрать оптимальные для каждого перехода методы обработки при заданном типе производства.
Коэффициент удельных затрат Ку
Для типа производства
Примечание: Для мелкосерийного производства Ку соответствует среднему значению между единичным и серийным а для крупносерийного – между серийным и массовым.
Работу начинают с определения методов обработки самой точной поверхности.
) По табл. 5.1 для заданного типа поверхности и материала детали определяют варианты 1–го перехода обеспечивающего 12 квалитет точности и шероховатость Ra 125. Таким же образом определяют варианты последующих переходов до обеспечения заданной точности и шероховатости.
) Комбинируя методы обработки на каждом переходе записывают варианты последовательности обработки в виде цепочек переходов включая ТО. При этом сразу убирают варианты с несовместимыми переходами (например точение после шлифования).
) По табл. 5.2 определяют коэффициент удельных затрат Куj для каждого метода обработки.
) По формуле (5.1) для каждого варианта сочетания методов обработки определяют суммарный коэффициент удельных затрат
Вариант имеющий наименьшее значение Ку считают оптимальным.
Пример выполнения работы №5
Деталь «Вал-шестерня» черт. 07.ТМ.13.001. Производство среднесерийное.
При выборе методов обработки и их последовательности учитываем что:
кроме указанных в табл. 5.1 переходов необходимо согласно требованиям чертежа вала ввести ТО закалку с отпуском;
вал – деталь нежесткая (
заготовка вала — штамповка относительно чистая очищенная от окалины величина облоя и заусенцев не более 2 мм поэтому обдирочное шлифование перед механической обработкой вводить не следует;
обработку вала до ТО экономически целесообразно производить методами лезвийной обработки а после ТО методами абразивной обработки.
Выбор методов начинаем с самой точной поверхности. Такими поверхностями являются шейки под подшипники пов. 6 и 17 .
По табл. 5.1 определяем что для обработки пов. 6 и 17 (6 квалитет точности шероховатость Rа=08 мкм) могут быть применены следующие варианты последовательности методов обработки (табл. 5.3).
Варианты обработки пов. 6 и 17
В табл. 5.3 обозначено:
ТП–точение получистовое
Ш–шлифование черновое
ШП–шлифование получистовое
ШЧ–шлифование чистовое
Рядом с обозначением метода обработки в скобках указан квалитет точности получаемый на данном переходе а сверху– коэффициент удельных затрат КУj для данного перехода.
Оптимальный вариант обработки выбираем по минимуму суммарных удельных затрат характеризуемых суммой КУi всех переходов данного варианта. При этом поскольку переходы Т(12) и ШЧ(6) а также ТО присутствуют во всех вариантах обработки их из расчёта исключаем.
Из табл. 5.3. видно что минимальный коэффициент удельных затрат КУ=61 соответствует варианту 3 предусматривающему ТО после чистовой токарной обработки. Поэтому примем этот вариант обработки:
Т(12; 125)–ТП(10; 32)– ТЧ(8; 16)–ТО(9)– ШП(8; 16)–ШЧ(6; 08).
Здесь в скобках указаны квалитет точности и шероховатость поверхности Ra мкм для каждого перехода.
Для обработки места под сальник пов. 6 (6-й квалитет Ra=04) принимаем дополнительный переход полирование.
Полученным выше результатом воспользуемся для назначения методов обработки других поверхностей.
Шейка под муфту пов. 4 (8-й квалитет Ra=16):
Т(12; 125)–ТП(10; 32)– ТЧ(8; 16) –ТО(9)– ШП(8; 16).
Наружная поверхность зубчатого венца пов. 11 (11;32):
Т(12; 125)–ТП(10; 32)–ТО(11).
Свободные шейки пов. 9 и 14 канавки пов. 7 16 21 (14; 125):
Уступы пов. 8 и 15 (8; 16):
Т(12; 125)–ТП(10; 32)– ТЧ(8; 16) –ТО(9) – ШП(8; 16).
Уступ пов. 5 (10; 32):
Т(12; 125)–ТП(10; 32)–ТО(11) )– ШП(10; 32)..
Торцы зубчатого венца пов. 10 и 13 (14; 125):
Торцы пов. 1 и 18 (14; 125):
Шпоночный паз пов. 2 и 3 (9; 16):
Зубчатый венец пов. 12 (6 степень точности Ra=08):
ЗФ(8 ст.; 63)–СФ–ШВ(7 ст.; 16)–ТО–ШЧ(6 ст.; 08).
ЗФ–зубофрезерование
Центровые отверстия пов. 19 и 20
С(9; 16)–ТО(10)–ШЧ(9; 08)
Методы обработки поверхностей сводим в табл. 5.4.
Т–ТП– ТЧ –ТО–ШП–ШЧ–ПО
Определение припусков на обработку
Цель работы – овладеть методикой определения припусков на обработку в условиях единичного и серийного производства.
Припуск – слой материала который предстоит удалить с заготовки.
Операционный припуск – припуск который удаляется на данной операции.
Общий припуск – припуск который предстоит удалить с исходной заготовки для получения готовой детали. Общий припуск равен сумме всех операционных припусков.
Припуск включает расчетный припуск и напуск.
Расчетный припуск определяется необходимостью получения заданных точности и шероховатости поверхности детали.
Напуск определяется технологическими возможностями заготовительного производства (необходимость литейных или штамповочных уклонов облой заусенцы радиусы переходов упрощение конфигурации невозможность выполнить отверстие пазы канавки и т.п.).
Метод определения припусков определяется типом производства.
В единичном производстве применяют табличный метод. Припуски определяют по таблицам составленным на базе статистического анализа многочисленных практических данных и теоретических расчетов для различных условий обработки. Преимуществом табличного метода является его простота. Недостаток метода состоит в том что значения припусков получаются завышенными что удорожает обработку.
Таблицы определения припусков можно усовершенствовать конкретизировав условия получения заготовки и обработки введя дополнительные исходные параметры. Это позволяет получить значения припусков более близкие к оптимальным. Однако в этом случае метод становится более трудоемким.
Табличным методом приближенного определения припусков мы пользовались при выборе метода получения заготовки в работе №4.
В мелкосерийном и среднесерийном производстве применяют метод расчета припусков суммированием по переходам. В основе метода лежит определение припуска для каждого перехода с учетом точности операционной заготовки качества поверхностного слоя заготовки точности установки заготовки в приспособлении и последующее суммирование операционных припусков.
Операционный припуск включает:
) толщину а дефектного слоя операционной заготовки образовавшегося в результате выполнения предыдущего перехода или при получении исходной заготовки (шероховатость окалины упрочненный слой и др.);
) погрешность d размера полученного на предыдущем переходе максимальное значение которой регламентируется допуском
) погрешность р формы и расположения поверхности полученная на предыдущем переходе если она не является частью Td и регламентируется самостоятельным допуском Tр (непрямолинейность оси неплоскостность непараллельность неперпендикулярность несоосность неконцентричность несимметричность радиальное и торцовое биение);
) погрешность у установки заготовки в приспособлении на данном переходе которая регламентируется допуском на точность установки Ту.
Значение операционного припуска Zi для i-го перехода определяется суммой:
Такое представление суммы обусловлено тем что направления а и d совпадают с направлением припуска а направления погрешностей р и у неопределенны.
Индекс i-1 показывает что параметр относится к предыдущему переходу.
Структура припуска (для 4 переходов с ТО после 2-го перехода) приведена на рис. 6.1.
Толщина дефектного слоя а мм при различных методах
получения заготовки и обработки
Фрезерование черновое
Фрезерование чистовое
Шлифование черновое
Прокат калиброванный
Термообработка (дополнит.)
Допуски на установку заготовки в приспособлении Ту мм
Установка в трехкулачковом патроне в тисках
Штамповка открытая на ГКМ высадка
Штамповка закрытая прокатка поперечная
Штамповка холодная калибровка обкатка
Пруток калиброванный
После чернового точения
После чистового точения шлифования
Пруток; после чернового точения
Пруток калиброванный; после чистового
неподвижных по шлифованным отверстиям
неподвижных прецизионных
вращающихся подпружиненных
Определить припуски на обработку заданной детали табличным методом.
Рассчитать припуск на обработку данной детали методом суммирования по переходам.
Сравнить полученные значения.
Расчет припусков выполняют одновременно заполняя таблицу 6.3 (см.п.5).
) Определяют число переходов необходимое для получения заданной точности и шероховатости (табл. 5.1). Записывают их по порядку номеров в графу 1 табл. 6.3 начиная с заготовительной операции которой присваивают № 0.
) В графу 2 заносят наименование переходов.
) В графу 3 записывают квалитет точности получаемый на каждом переходе.
) По табл. 1.1 определяют допуски на размер Td для каждого перехода и заносят их в графу 4 табл. 6.3.
) По табл. 1.3 определяют допуски формы и расположения Tp для каждого перехода и заносят их в графу 5 табл. 6.3. В первом приближении можно принять Тр=03Тd (нормальная относительная точность).
) По табл. 6.1 определяют толщину дефектного слоя а для каждого перехода и заносят в графу 6 табл. 6.3.
) По табл. 6.2 определяют допуск точности установки заготовки в приспособлении для каждого перехода кроме заготовительной операции и заносят в графу 7 табл. 6.3.
) По формуле (6.1) рассчитывают припуск Z для каждого перехода кроме заготовительной операции и заносят в графу 8 табл. 6.3 округляя в сторону увеличения припуска до знака после запятой с которым задан допуск Td.
Если техпроцессами предусмотрена ТО то для i-го перехода следующего за ТО к толщине дефектного слоя предыдущей обработки ai-1 добавляют толщину дефектного слоя aто а допуск Tdi-1 принимают на 1 квалитет грубее:
) Определяют операционные размеры d для каждого перехода начиная с последнего размеры для которого заданы на чертеже детали.
для наружной поверхности:
Значения d заносят в графу 9 табл. 6.3 округляя в сторону увеличения до знака после запятой с которым задан допуск Td.
Пример выполнения работы №6
Определить припуски на обработку детали “Вал-шестерня” черт. 07.ТМ.13.001. Метод получения заготовки – штамповка. Производство среднесерийное. Припуск на самую точную поверхность рассчитать суммированием по переходам на остальные поверхности – по табл. 4.7.
Самыми точными поверхностями детали “Вал-шестерня” являются пов. 6
) По данным работы 4 записываем в графы 1 3 № заготовительного перехода (№0) его наименование (способ получения заготовки) и квалитет точности. По данным работы 5 в эти же графы записываем №№ переходов мехобработки их наименование и квалитет точности.
) По табл. 1.1 определяем допуски Td для каждого перехода и заносим в графу 4 табл.6.3.
) Определяем допуск формы и расположения Тр=03Тd для каждого перехода и заносим в графу 5 табл. 6.3.
) По табл. 6.1 определяем толщину дефектного слоя а для каждого перехода и заносим в графу 6 табл. 6.3.
) По табл. 6.2 определяем допуск на точность установки заготовки в приспособлении для каждого перехода кроме заготовительного и заносим в графу 7 табл. 6.3.
) По формуле (6.1) рассчитаем припуск Z для каждого перехода кроме заготовительного. Полученные значения округляем до знака после запятой с которым задан допуск Td.
Результаты расчета заносим в графу 8 табл. 6.3 начиная с 1-го перехода.
) Определяем операционные размеры. Диаметр d5 задан на чертеже детали:
) Общий припуск на обработку составляет:
Аналогично определяем припуски для остальных поверхностей. Результаты расчета заносим в табл. 6.3.
Сравнивая значения припусков полученных суммированием по переходам с табличными (см. работу №4) видим что переход от табличного метода определения припусков к расчетному приводит к существенному уменьшению припусков.
Расчет припусков и операционных размеров детали “Вал-шестерня”
Проектирование штампованной заготовки
Цель работы – Освоение методики проектирования заготовок деталей обеспечивающих их получение и обработку с наименьшими затратами.
Грамотно спроектированная заготовка обеспечивает ее получение и обработку с наименьшими затратами. Ниже изложена методика проектирования заготовки полученной методом штамповки как наиболее распространенным в серийном производстве.
Исходный индекс штампованной заготовки
Допуски Td на размеры штамповки
Радиусы закруглений Rmin
Допускаемая величина остаточного облоя То и
Допускаемая величина отклонения от
плоскостности (прямолинейности) Тп и от
концентричности отверстий Тк
Наибольший размер заготовки мм
Отклонение межцентрового расстояния Тмц
Межцентровое расстояние мм
Спроектировать заготовку заданной детали.
Выполнить рабочий чертеж заготовки.
Проектирование заготовки выполняют в следующей последовательности:
) Вычерчивают тонкой линией контур детали в масштабе. Проставляют основные размеры буквами русского алфавита. Размеры заносят в табл. 7.7.
) Определяют припуски на обработку согласно методическим указаниям к работе 6 и заносят в табл. 7.7. Определяют расчетные размеры заготовки путем прибавления припусков к размерам детали и округления их до 05 мм в сторону увеличения припуска заносят в табл. 7.7
) Вычерчивают контур заготовки с учетом напусков. При этом перепад поверхностей должен быть не менее 5 мм. Следует также избегать резких перепадов по
) Определяют положение плоскости разъема штампа и положение «верх – низ» заготовки. Разъем выполняют в плоскости наибольших габаритов заготовки чтобы плоскость штампа имела наименьшую глубину по сравнению с длиной и шириной. Разъем должен быть по плоскости а не по ломаной или криволинейной поверхности. Разъем не должен проходить по поверхности заготовки чтобы иметь возможность контролировать смещение штампа. Заготовка должна быть по возможности симметричной относительно плоскости разъема.
) Определяют возможные технологические базы для 1-й операции мехобработки. Целесообразно в качестве технологических баз использовать основные конструкторские базы. На этих поверхностях не должно быть заусенцев облоя через них не должна проходить плоскость разъема уклоны должны быть минимальными.
) Определяют класс точности Т в зависимости от метода получения заготовки:
открытая штамповка штамповка на ГКМ–Т4;
закрытая штамповка выдавливание–Т3;
холодная штамповка калибровка–Т2
) Определяют группу стали М в зависимости от содержания углерода У и легирующих элементов Л:
У=035 065%Л=2 5%–М2;
) Определяют степень сложности С в зависимости от отношения Кс=WзWо (Wз – объем заготовки Wо – объем простейшей описанной фигуры–шара призмы цилиндра и т.п.):
) Определяют исходный индекс И по табл. 7.1 как сумму начального индекса Ио определяемого массой заготовки и добавочных индексов Ит Им Ис в зависимости от Т М С.
) Определяют допуски Td на размеры по табл. 7.2 в зависимости от исходного индекса И. При ориентировочных расчетах допуски можно назначать:
Поле допуска располагают следующим образом:
для охватываемых поверхностей (валов): (025 035) Td в “+” остальное в “-“;
для охватывающих поверхностей (отверстий): (025 035) Td в “-” остальное в “+“;
для остальных поверхностей – симметрично ± Td2.
Полученные данные заносят в табл. 7.1.
) Определяют штамповочные уклоны: для штамповки на прессах – 5 7º на ГКМ – 3 5º. Уклоны должны быть одинаковыми с противоположных сторон заготовки что позволит избежать бокового смещения штампов вследствие разницы горизонтальных составляющих усилия штамповки.
) Определяют радиусы закруглений R по табл. 7.3 в зависимости от глубины ручья штампа. Устанавливают допуск на радиус в зависимости от класса точности:
) Определяют допустимые значения остаточного облоя То смещения штампа Тс отклонений от плоскостности Тп концентричности отверстий Тк межцентрового расстояния Тмц по табл. 7.4 7.5 7.6.
Рабочий чертеж заготовки выполняют в соответствии с ГОСТ ЕСКД. При этом:
) Контур детали вычерчивают линией условного контура и совмещают с проекциями заготовки. Припуск на обработку можно показывать в увеличенном масштабе. Количество проекций видов сечений определяют из условия
достаточности информации для изготовления заготовки.
) Линию разъема штампа или литейной формы обозначают значками
по обе стороны изображения; направление верх–низ указывают стрелкой с надписями
) Около обозначений размеров заготовки или под ними в скобках
указывают размер детали без допусков.
) Шероховатость поверхностей указывают в верхнем правом углу
) Отклонение формы (неплоскостность непрямолинейность
нецилиндричность и т.д.) и расположения (неконцентричность непараллельность и т.д.) обозначают общепринятыми условными обозначениями либо указывают в технических требованиях.
) Поверхности принятые за технологичекие базы обозначают знаком
) Место маркировки указывают со ссылкой на соответствующий пункт
технических требований.
В технических требованиях указывают:
) Твердость материала заготовки в состоянии поставки (например 187±20НВ).
) Допускаемые дефекты поверхностного слоя их площадь и глубину (обычно 05 припуска на обработку).
) Неуказанные штамповочные уклоны и радиусы переходов с допусками.
) Неуказанные предельные отклонения размеров.
) Допускаемые отклонения формы и расположения поверхностей если они не показаны условными обозначениями на видах.
) Допустимую величину смещения по поверхности разъема штампа.
) Допустимую величину остаточного облоя.
Пример выполнения работы №7
Деталь – «Вал-шестерня» черт. 07.ТМ.13.001. Метод получения заготовки – штамповка в открытом штампе на прессе.
1. Проектирование заготовки
) Вычерчиваем контур детали. Проставляем размеры (рис. 7.1)
) Вычерчиваем контур заготовки заготовка будет содержать 3 ступени (рис. 7.1).
) Определяем припуски на обработку по таблице 4.7. Результаты заносим в графу 3 табл. 7.7. Определяем расчетные размеры заготовки путем прибавления припусков к размерам детали и округления их до 05 мм в сторону увеличения припуска. Результаты заносим в графу 4 табл. 7.7.
)Плоскость разъема – диаметральное продольное сечение заготовки. При таком положении плоскости разъема полость штампа имеет наименьшую глубину. В этой плоскости удобно контролировать смещение штампа. Заготовка получается симметричной что делает возможность поворачивания ее при штамповке и уменьшать износ штампа.
)В качестве технологических баз на 1-й операции мехобработки
целесообразно использовать ОБ – пов. 9 11 14 .
) Определяем класс точности Т штамповки. При открытой штамповке обеспечивается точность Т4.
Расчет размеров заготовки
Положение поля допуска
) Определяем группу стали М в зависимости от содержания углерода С и легирующих элементов Л. Для стали 40ХГНМ У=035 043% Л5% (см. пример выполнения работы №2) что соответствует группе М2.
) Определяем степень сложности заготовки в зависимости от коэффициента Кс=WзWо где – Wз – объем заготовки; Wо – объем описанного цилиндра.
где di и i - диаметр и длина соответствующей ступени заготовки.
где d – диаметр описанного цилиндра; - длина заготовки.
что соответствует степени сложности С2.
)Определяем исходный индекс И.
где Ио – начальный индекс зависящий от массы заготовки.
Им Ис Ит – добавочные индексы в зависимости от М С Т.
здесь – плотность стали
для mЗ=20 Ио=9; Им=1; Ис=1; Ит=4.
) Определяем допуски на размеры заготовки в зависимости от
исходного индекса по табл. 7.3 и заносим их значения в графу 5 табл. 7.7.
) Определяем штамповочные уклоны. Согласно рекомендациям принимаем значения уклонов 7º.
) Определяем радиусы закруглений R. По табл. 7.3 для глубины полости штампа 20 мм при массе заготовки mЗ=20кг R=3мм. Допуск на радиус для класса точности Т4 составляет ±025R=±05мм.
) Определяем допустимые значения остаточного облоя То и смещения штампа Тс. По табл. 7.4 для mЗ=20 кг и точности Т4 То=12мм Тс=1мм.
2. Выполнение рабочего чертежа заготовки.
Рабочий чертеж заготовки выполняем в соответствии с требованиями ЕСКД и рекомендациям [1].
Рабочий чертеж заготовки – черт. 06.ТМ.13.001.
Разработка технологического маршрута
Цель работы – приобретение навыка разработки технологического маршрута обработки деталей на базе типового маршрута.
Технологический маршрут – перечень операций ТП в их последовательности.
Оптимальным считается такой маршрут который обеспечивает минимальную себестоимость С обработки:
где С – себестоимость операции
Для большинства типов деталей разработаны так называемые типовые маршруты которые как правило обеспечивают выполнение условия (8.1). Поэтому маршруты обработки каждого конкретного наименования детали разрабатывают на базе типового маршрута внося в него необходимые изменения обусловленные особенностями конструкции данной детали и техническими возможностями производства.
При этом стараются выполнять следующие условия:
)Обработку целесообразно разделить на черновую и чистовую. Черновую обработку выполняют на станках пониженной точности с большими значениями глубины резания и подачи в приспособлениях обеспечивающих большую силу зажима режущим инструментом из высокопрочного материала. Чистовую обработку выполняют на станках повышенной точности с высокой скоростью резания в приспособлениях обеспечивающих высокую точность установки режущим инструментом из износостойкого материала.
Совмещать черновую и чистовую обработку на одной операции целесообразно только при высокой точности исходной заготовки либо в случаях когда установка заготовки связана с большими затратами времени (например в тяжелом машиностроении).
)На 1-ой операции обрабатывают поверхности используемые в дальнейшем как технологические базы (ТБ) при этом в качестве ТБ на 1-ой операции (черновые ТБ) целесообразно использовать основные конструкторские базы.
Если у детали обрабатываются не все поверхности то на 1-ой операции в качестве ТБ используют поверхность остающуюся черной. Это обеспечит правильное взаимное расположение обработанных поверхностей относительно необработанной.
)В целях уменьшения пространственных отклонений поверхностей связанных жесткими допусками их целесообразно обработать на одном установе. Если этого сделать не удается то при обработке одной из этих поверхностей другую используют в качестве ТБ.
Наиболее точные поверхности следует обрабатывать в конце технологического маршрута.
)При обработке ответственных деталей с целью снятия внутренних напряжений после операций черновой обработки проводят термообработку – стабилизационный отпуск.
)Термообработку – закалку с отпуском проводят перед чистовыми операциями мехобработки. При этом целесообразно как правило до термообработки выполнить операции лезвийной обработки а после термообработки – операции абразивной обработки.
На базе типового технологического маршрута разработать маршрут обработки детали при данном типе производства.
) Выписывают столбиком номера поверхностей их форму точность и шероховатость.
) Для каждой поверхности определяют последовательность обработки согласно методическим указаниям к работе № 5.
) Используя типовой технологический маршрут определяют порядок и наименование операций с указанием поверхностей обрабатываемых на каждой операции. Записывают их столбиком.
) Анализируют маршрут на предмет целесообразности перестановки объединения разделения или замены операций исходя из типа производства и наличия оборудования.
) Присваивают каждой операции номер кратный 10 и название в виде прилагательного по групповой или детальной форме. Групповая форма предполагает названия операций по виду обработки (агрегатная зубообрабатывающая протяжная расточная сверлильная токарная фрезерная шлифовальная) детальная – по типу оборудования (зубодолбежная зубострогальная зубофрезерная и т.п.)
Пример выполнения работы №8
Разработать технологический маршрут обработки детали «Вал-шестерня» черт. 07.ТМ.13.001. Производство среднесерийное.
) Выписываем номера поверхностей их форму точность размеров формы и расположения шероховатость. Заносим эти данные в графы 1-5 табл. 8.1.
Методы обработки поверхностей детали «Вал промежуточный»
)Для каждой поверхности определяем методы обработки и записываем их в графу 6 табл. 8.1 [1].
)Используя типовой технологический маршрут [2] определяем предварительно порядок и наименование операций по обработке поверхностей детали “Вал промежуточный”. Полученные данные заносим в табл. 8.2.
)Анализируем предварительный маршрут на предмет целесообразности перестановки объединения разделения или замены операций.
Учитывая серийный тип производства объединяем в одну операцию фрезерование торцов 1 18 и сверление центровых отверстий 19 20 полагая что они будут выполняться на фрезерно-центровальном станке.
Операции получистового и чистового точения объединим в одну для каждого конца вала.
) С учетом этих изменений формируем окончательный вариант технологического маршрута который представлен в табл. 8.3.
Предварительный маршрут обработки детали “Вал промежуточный”
Сверление центровых отверстий
Черновое точение правого конца
Черновое точение левого конца
Получистовое точение правого конца
Получистовое точение левого конца
Чистовое точение правого конца
Чистовое точение левого конца
Фрезерование шпоночного паза
Термообработка закалка
Зачистка центровых отверстий
Получистовое шлифование правого конца
Получистовое шлифование левого конца
Чистовое шлифование правого конца
Чистовое шлифование левого конца
Окончательный маршрут обработки детали “Вал промежуточный”
Наименование операции
Фрезерно-центровальная
Фрезерование торцов 118.
Сверление центровых отверстий 1920
Черновое точение пов. 101113–17
Черновое точение пов. 4–9 21
Получистовое и чистовое точение пов. 11 15 17
Получистовое и чистовое точение пов. 4-6 8
Фрезерование шпоночного паза пов. 23
Фрезерование зубьев 12
Продолжение табл. 8.3
Шевингование пов. 12
Зачистка центровых отверстий 19 20
Получистовое и чистовое шлифование пов. 17
Получистовое и чистовое шлифование пов. 46
Шлифование зубьев 12
Разработка схем базирования
Цель работы – овладение методикой разработки оптимальных схем базирования заготовки при мехобработке.
Установка заготовки на станке включает 2 этапа – базирование и закрепление.
Базирование – придание заготовке требуемого положения относительно направлений движения рабочих органов станка.
Закрепление – фиксация заготовки в требуемом положении.
Согласно положениям теоретической механики заданное положение тела относительно выбранной системы координат достигается лишением его 6 степеней свободы (перемещений вдоль трех координатных осей и поворотов вокруг этих осей) путем наложения жестких связей. Связи реализуются через контакт с поверхностями других тел в 6 точках – опорных точках (рис. 9.1).
Поверхности заготовки а также принадлежащие ей линии оси точки на которых расположены опорные точки при базировании заготовки в приспособлении называют технологическими базами (ТБ).
ТБ различают по числу лишаемых степеней свободы: установочная – лишает заготовку 3 степеней свободы (пов. 1 рис. 9.1) направляющая – 2 (пов. 2 ) упорная – 1 (пов. 3 ) а также двойная направляющая – 4 и двойная упорная – 2 степеней свободы.
ТБ различают и по характеру проявления: явные – реальные поверхности линии точки и скрытые (неявные) – воображаемые поверхности линии точки.
Схема расположения опорных точек на ТБ называется схемой базирования (СБ). Опорные точки обозначают на СБ условными знаками (см. рис. 9.1 б) и нумеруют.
Различают теоретическую СБ в которой используют как явные так и скрытые ТБ и реальную СБ в которой используют только явные ТБ.
Отклонение фактического положения заготовки от номинального называют погрешностью базирования . СБ при которой называют идеальной СБ. В идеальной СБ в качестве ТБ используют измерительные базы – поверхности линии оси и точки от которых задан измеряемый параметр (так называемый принцип единства баз).
Разработать теоретическую схему базирования для заданной операции (установа) техпроцесса мехобработки детали
) Определяют измерительные базы для каждого выполняемого на данном установе размера.
) На каждой измерительной базе размещают по одной опорной точке лишающей заготовку возможности перемещения вдоль координатных осей XYZ и обеспечивающей точность размеров.
) Определяют измерительные базы для каждого из требований расположения поверхностей (несоосность непараллельность биение и т.п.).
) На каждой измерительной базе добавляют необходимое число опорных точек лишающих заготовку поворотов вокруг координатных осей XYZ и обеспечивающих точность расположения поверхностей.
Необходимо иметь в виду что для обеспечения точности размера достаточно иметь 1 опорную точку а для обеспечения точности расположения – несколько опорных точек. При этом можно воспользоваться следующими рекомендациями табл. 9.1.(см. рис. 9.2).
Число опорных точек на схеме базирования обеспечивающее
выполнение технических требований расположения
Технические требования
В т.ч. на изм. базе не менее
Плоскость 1 плоскости 2
Плоскость 1 плоскости 3
Пример выполнения работы № 9
Разработать теоретическую схему базирования для фрезерной операции обработки детали “Корпус” рис. 9.3а.
На эскизе детали проводим оси координат Х Y Z за начало координат принимаем точку О (рис. 9.3б).
Определяем измерительные базы размеров А и Б. Измерительная база размера А – плоскость 2 . Располагаем на пов. 2 рис. 9.3б опорную точку 1. Измерительная база размера Б – плоскость 3 . Располагаем на пов. 3 опорную точку 2.
Измерительная база технического требования перпендикулярности –плоскость 1 проходящая через оси отверстий. Чтобы лишить эту плоскость возможности поворота вокруг оси ОY необходимо к имеющейся опорной точке 1 добавить опорную точку 3 расположив ее на плоскости 1 .
Мы выполнили заданные требования обеспечив точность размеров А и Б и положение обрабатываемой плоскости. Теперь заготовка лишена перемещений вдоль осей OX и OZ и поворота вокруг оси OY. Чтобы лишить заготовку остальных степеней свободы располагаем дополнительно на пов. 4 точки 4 (лишает перемещения вдоль оси ОY) 5 (лишает поворота вокруг оси ОХ) и 6 (лишает поворота вокруг оси OZ).
Из выбранных баз базы 2 3 4 являются явными а осевая плоскость
– неявной. На реальной схеме базирования базой опорной точки 3 будет поверхность одного из отверстий.
Разработка плана обработки детали
Цель работы – приобретение навыка разработки плана обработки детали.
План обработки – информация о технологическом маршруте обработки детали представленная в наглядной графической форме.
План обработки представляет таблицу из 3-х граф.
Графа 1: № и наименование операции
)№ операции по техпроцессу;
)№ установа в операции;
)Наименование операции установа;
)Предполагаемый тип станка его точность. Позднее здесь же указывают модель станка.
Графа 2: Схема обработки.
)Изображение заготовки в положении обработки на момент окончания обработки с выделением обрабатываемых поверхностей красным цветом (или жирной линией);
)Опорные точки схемы базирования показанные условными обозначениями по ГОСТ 3.1107 -81;
)Обозначение обработанных поверхностей измерительных и технологических баз в виде цифры (той же что на эскизе детали) в кружке на выноске с индексом – номером операции на которой получена данная поверхность;
)Размеры обработки получаемые на данной операции и расстояния от обработанных поверхностей до технологических баз обозначенные буквами русского алфавита с индексом операции на которой они получены; при этом перед буквой обозначающей диаметр ставят цифру 2.
)Шероховатость поверхности – в правом верхнем углу по
Графа 3: Технические требования.
)Условные обозначения допусков на размер в виде:
)Условные обозначения допусков формы и расположения в виде:
При назначении технических требований точность обработки определяется следующими факторами:
)точностью технологической системы станок-приспособление (так называемая среднестатистическая точность);
)точностью формы и расположения технологических баз;
)погрешностью базирования вследствие нарушения принципа единства баз;
)точностью настройки инструментов в блоке при многоинструментальной обработке;
)точностью инструментов работающих по методу копирования.
При назначении предельных значений погрешностей формы и расположения принимаем их равными в сумме 60% допуска на размер (так называемая нормальная относительная точность).
Для разработанного технологического маршрута обработки детали разработать план обработки.
Пример выполнения работы №10
Разработать план обработки детали «Вал-шестерня» черт. 07.ТМ.13.001 на базе технологического маршрута разработанного в работе №8.
горячая штамповка (JT 16)
0 фрезерно – центровальная
фрезерно – центровальный
токарно – винторезный
Продолжение табл. 10.1
0 – токарная чистовая
с ЧПУ 16Б16ПТ1 (JT 8)
горизонтальный шпоночно-фрезерный станок 692Р (JT 9)
вертикальный зубофрезерный станок 53А20
зубофасочный ВС-320А (JT 6)
зубошевинговальный 5702В (JT 6)
0 – центрошлифовальная
0 - зубошлифовальная
зубошлифовальный 5851 (JT 6)
полировально-шлифовальный станок 3А352 (JT 6)
Выбор средств технологического оснащения
Задача раздела – выбрать для каждой операции ТП такие оборудование приспособление режущий инструмент (РИ) и средства контроля которые бы обеспечили заданный выпуск деталей заданного качества с минимальными затратами.
При выборе типа и модели металлорежущих станков будем руководствоваться следующими правилами:
) Производительность точность габариты мощность станка должны быть минимальными достаточными для того чтобы обеспечить выполнение требований предъявленных к операции.
) Станок должен обеспечить максимальную концентрацию переходов на операции в целях уменьшения числа операций количества оборудования повышения производительности и точности за счет уменьшения числа перестановок заготовки.
) В случае недостаточной загрузки станка его технические характеристики должны позволять обрабатывать другие детали выпускаемые данным цехом участком.
) Оборудование не должно быть дефицитным следует отдавать предпочтение отечественным станкам.
) В мелкосерийном производстве следует применять преимущественно универсальные станки револьверные станки станки с ЧПУ многоцелевые станки (обрабатывающие центры). На каждом станке в месяц должно выполняться не более 40 операций при смене деталей по определенной закономерности.
) Оборудование должно отвечать требованиям безопасности эргономики и экологии.
Если для какой-то операции этим требованиям удовлетворяет несколько моделей станков то для окончательного выбора будем проводить сравнительный экономический анализ.
Выбор оборудования проводим в следующей последовательности:
) Исходя из формы обрабатываемой поверхности и метода обработки выбираем группу станков.
) Исходя из положения обрабатываемой поверхности выбираем тип станка.
) Исходя из габаритных размеров заготовки размеров обработанных поверхностей и точности обработки выбираем типоразмер (модель) станка.
Данные по выбору оборудования заносим в табл. 11.1.
Выбор приспособлений
При выборе приспособлений будем руководствоваться следующими правилами:
) Приспособление должно обеспечивать материализацию теоретической схемы базирования на каждой операции с помощью опорных и установочных элементов.
) Приспособление должно обеспечивать надежные закрепление заготовки обработке.
) Приспособление должно быть быстродействующим.
) Зажим заготовки должен осуществляться как правило автоматически.
) Следует отдавать предпочтение стандартным нормализованным универсально-сборным приспособлениям и только при их отсутствии проектировать специальные приспособления.
Исходя из типа и модели станка и метода обработки выбираем тип приспособления.
Выбор приспособления будем производить в следующем порядке:
) Исходя из теоретической схемы базирования и формы базовых поверхностей выбираем вид и форму опорных зажимных и установочных элементов.
) Исходя из расположения базовых поверхностей и их состояния (точность шероховатость) формы заготовки и расположения обрабатываемых поверхностей выбираем конструкцию приспособлений.
) Исходя из габаритов заготовки и размеров базовых поверхностей выбираем типоразмер приспособления.
После расчета режима резания (разд. 12) определим силы резания по значению которых рассчитываем силу зажима достаточную для обеспечения надежного закрепления.
Учитывая передаточный коэффициент усиления определим усилие и мощность привода. Сравним эти значения с характеристиками приспособления. Если силы зажима или мощность превосходят допустимые значения то выбираем более мощное приспособление.
Данные по выбору приспособлений заносим в табл. 11.2.
Выбор технологического оборудования
Расположение поверхностей
Габариты заготовки мммм
Размеры обработ. поверхн.
Тип модель оборудования
Фрезерование сверление
Фрезерно-центровальный полуавтомат
Токарно-винторезный станок 16Б16Т1
Токарно-винторезный станок 16Б16ПТ1
Продолжение табл. 11.1
Токарно-винторезный станок 16Б16ПТ1
Горизонтальный шпоночно-фрезерный станок 692Р
Вертикальный зубофрезерный станок 53А20
Зубофасочный станок ВС-320А
Горизонтальный зубошевинговальный станок 5702В
Центрошлифовальный станок 3922Е
Круглошлифовальный станок 3А151
Зубошлифовальный станок 5851
Полировально-шлифовальный станок 3А352
Базовая поверхность.
Установочные элементы
Типоразмер приспособления
Фрезерно-центровальный МР-76АМ
Призма установочная
Тиски самоцентрирующиеся с призматическими губками 50 ГОСТ 12195-66
Токарно-винторезный станок
Центр подпружиненный
А1-3-НП-ЧПУ ГОСТ 8742-75
Патрон поводковый ГОСТ 2571-71.
Центр вращающийся ГОСТ 8742-75
Продолжение табл. 11.2.
Продолжение табл.11.2.
Вертикально шпоночно-фрезерный станок 692Р
Вертикальный зубофрезерный станок 52А20
Патрон цанговый. Центр вращающийся ГОСТ 8742-75
Зубофасочный станок ВС-320А
Зубошевинговальный станок 5702В
Центрошлифовальный станок 3К225В
Патрон мембранный ГОСТ 16157-70
Центр неподвижный ГОСТ 8742-75
Патрон поводковый ГОСТ 2571-71. Центр подвижный ГОСТ 8740-75
Центр неподвижныйГОСТ 8742-75
Патрон цанговый ГОСТ 2571-71. Центр вращающийся ГОСТ 8742-75
Выбор режущего инструмента
При выборе РИ будем руководствоваться следующими правилами:
)Выбор инструментального материала определяется требованиями с одной стороны максимальной стойкости а с другой минимальной стоимости.
)Следует отдавать предпочтение стандартным и нормализованным инструментам. Специальный инструмент следует проектировать в крупносерийном и массовом производстве выполнив предварительно сравнительный экономический анализ.
)При проектировании специального РИ следует руководствоваться рекомендациями по совершенствованию РИ.
Выбор режущего инструмента (РИ) будем производить в следующем порядке:
)Исходя из типа и модели станка расположения обрабатываемых поверхностей и метода обработки определяем вид РИ.
)Исходя из марки обрабатываемого материала его состояния и состояния поверхности выбираем марку инструментального материала.
)Исходя из формы обрабатываемой поверхности назначаем геометрические параметры режущей части (форма передней поверхности углы заточки: g a j j1 l; радиус при вершине).
)Исходя из размеров обрабатываемой поверхности выбираем конструкцию инструмента его типоразмер и назначаем период стойкости Т.
Данные по выбору РИ заносим в табл. 11.3.
Выбор средств контроля
При выборе средств контроля будем руководствоваться следующими правилами:
)Точность измерительных инструментов и приспособлений должна быть существенно выше точности измеряемого размера однако неоправданное повышение точности ведет к резкому удорожанию.
)В единичном и мелкосерийном производстве следует применять инструменты общего назначения: штангенциркули микрометры длинномеры и т.д.
)В крупносерийном – специальные инструменты.
)Следует отдавать предпочтение стандартным и нормализованным средствам контроля.
Данные по выбору средств контроля заносим в табл. 11.4.
Результаты выбора средств технологического оснащения заносим в табл. 11.5.
Выбор режущего инструмента
Обрабатываемый материал
Состояние поверхности
Размеры обработанной поверхности
Геометрия режущей части
Вид и конструкция РИ
Фрезерно-центровальный станок МР76АМ
Фреза торцовая ГОСТ 1695-80 70
Сверло центровочное А 63 ГОСТ 14952-80
g=10°a=10° j=90° r=1 мм
g=10°a=10°j=90° r=1 мм
g=10° a=10°j=90° r=05 мм
Вертикальный шпоночно-фрезерный станок 692Р
Фреза шпоночная =12
Вертикальный зубофрезерный станок 53А20
Фреза червячная двухзаходная
Фреза червячная 100 ГОСТ 9324-80
Продолжение табл. 11.3
Фреза червячная одновитковая
Фреза червячная одновитковая 50
Шевер дисковый А 180 ГОСТ 8570-80
Сталь 40ХГНМ закаленная
Головка шлифовальная
Головка шлифовальная алмазная АГК
Круг шлифовальный ПП
Круг шлифовальный ПП 500*203*80
Круг шлифовальный Т 225*50*20
Круг полировальный ПП 500*203*40
Контролируемый размер
Мерительный инструмент
Измерительное контрольное устройство
Штангенциркуль ШЦ-1 ГОСТ 160-80
Штангенциркуль ШЦ-1 ГОСТ160-80
Микрометр МК-50 ГОСТ 6507-78
Прибор БВ-5061 цехового типа
Продолжение табл. 11.4
Задача раздела - рассчитать такие режимы резания которые обеспечили бы заданный выпуск деталей заданного качества с минимальными затратами.
Определение режимов резания
Режим резания - это сочетание глубины резания подачи и скорости резания.
Наша задача состоит в том чтобы найти единственное возможное сочетание элементов режима резания которое обеспечивает экстремальное значение критериев оптимальности (например минимальная себестоимость).
) Рассчитаем режимы резания на операцию 160 шлифовальную.
Для выбранной операции - шлифование чистовое - применим таблично - аналитический метод определения режимов резания.
Данную операцию выполним за один переход - врезное шлифование широким кругом.
Разработку режима резания при шлифовании начинают с установления характеристики инструмента. Для окончательного шлифования шейки вала-шестерни - пов. 6 и 17 и уступов пов. 8 и 15 - из стали 40ХГНМ шероховатости Rа = 08 мкм выберем материал шлифовального круга - 25А25СМ17К ГОСТ 2424-82 [10]. Окончательная характеристика абразивного инструмента выявляется в процессе пробной эксплуатации с учетом конкретных технологических условий.
Основные параметры резания при шлифовании:
скорость вращательного или поступательного вращения заготовки
где Vз. табл.– скорость вращения детали по таблице ммин;
К– коэффициент учитывающий особенности торцекруглошлифования.
Vз. табл. =25 ммин К=1 карта ШК-3 [14].
частота вращения заготовки
глубина шлифования t мм - слой металла снимаемый периферией круга в результате радиальной подачи Sр при врезном шлифовании; глубина шлифования =0008 мм
радиальная подача определяемая по формуле:
Sр = Sр табл × К1 × К2 × К3
где К1 - коэффициент зависящий от обрабатываемого материала и скорости круга;
К2 - коэффициент зависящий от точности обработки шероховатости поверхности и припуска на сторону;
К3 - коэффициент зависящий от диаметра шлифовального круга;
Sр. табл. - поперечная подача по таблице мммин.
Для того чтобы определить коэффициент К1 найдём скорость шлифовального круга Vкр= мс
где Dкр - диаметр шлифовального круга мм;
n – частота вращения шпинделя обмин.
К1 = 06; К2 = 06; К3 = 09; Sр табл = 16 мммин карта ШК-3 [14]:
Sр = 16 × 1 × 06 × 06×09 = 052 мммин.
Эффективная мощность при врезном шлифовании периферией круга:
где d - диаметр шлифования d = 50016 мм;
b - ширина шлифования мм равная длине шлифуемого участка заготовки при круглом врезном шлифовании; для пов. 17 b = 60 мм для пов. 6 b=80 мм.
Значение коэффициентов входящих в формулу (12.1) определим по таблице [10]: СN = 014; r = 08; q = 02; z = 10.
Тогда эффективная мощность при обработке пов. 6 и 17 соответственно равны
N6 = 014 × 002508 × 5002 × 8010 = 128 кВт
N17= 014 × 002508 × 5002 × 6010 = 096 кВт
что меньше паспортной мощности станка. Из этого следует что выбранное оборудование удовлетворяет требованиям режимов резания.
Шлифование уступов пов. 8 и 15 производится с помощью ручного продольного перемещения Sпр шлифовальной бабки. Примем значение Sпр= Sр=052 мммин.
Нормирование ТП - это установление технически обоснованных норм времени на обработку детали.
Норма времени - регламентированное время выполнения заданного объема работ в определенных условиях исполнителем заданной квалификации.
В нашем случае следует рассчитать нормы времени на операции 160 шлифовальной.
Основное время tо - время непосредственно на обработку определяется исходя из схемы обработки:
tо = t6 + t17 + t8 + t15
где t6 t17 t8 и t15 – основное время обработки пов. 6 17 8 и 15
S - величина подачи мммин;
tвых - время выхаживания мин;
Lp S=052 ммоб; tвых=01 мин [14 карта ШК-3].
где z- припуск на обработку мм;
t- глубина шлифования ммоб;
n1 - частота вращения заготовки обмин;
Kв - коэффициент учитывающий выхаживание;
z=01; t=0005; n1=159 ; К=125
Суммарное время tо :
tо = 106 + 106 + 016+ 016=244 мин
Штучное время - время на выполнение операции определяется суммированием основного и вспомогательного времени.
Вспомогательное время - время на установку и снятие заготовки управление станком подвод и отвод режущего инструмента контроль размеров определяется по справочным нормативам или экспериментально.
В общем случае для шлифовальной операции штучное время определим по формуле:
где коэффициент j = 11 [15].
tшт = 244 × 11 = 268 мин.
Найденные значения режима резания заносим в операционную карту.
Список использованной литературы
Чертеж1.cdw

припуска на обработку
Неуказанные штамповочные уклоны 7
Неуказанные радиусы галтелей R2
Допускаемая величина смещения по поверхности разьема
Допускаемая величина остаточного облоя 1
Черновые технологические базы.
Маркировать 09.ТМ.27.001
Чертеж.cdw

Сталь 40Х ГОСТ 4543-71
Неуказанные предельные отклонения размеров диаметров h14
Кромки зубьев притупить фаской 0
Курсачь ТехМаш2009 записка.docx
Кафедра оборудования и технологии
машиностроительного производства
по дисциплине: «Технология машиностроения»
«Технологический маршрут обработки детали вал-шестерня»
Преподаватель: Гордеев А.В.
Студент: Саттаров П.В.
Содержание расчетно-пояснительной записки
Анализ исходных данных. Служебное назначение и условия работы детали. Систематизация поверхностей . Анализ технологичности детали.
Выбор стратегии разработки ТП.
Выбор метода получения заготовки.
Выбор методов обработки поверхностей.
Определение припусков на обработку.
Проектирование заготовки.
Разработка технологического маршрута.
Выбор СТО (оборудование приспособление режущий инструмент средства контроля).
Разработка плана обработки и схем базирования.
Проектирование технологических операций. Расчет режимов резания и норм времени. Шлифование черновое.
Список используемой литературы.
Содержание графической части
Технологические наладки.
Анализ исходных данных.
1 Служебное назначение и условия работы детали
Деталь «Вал-шестерня» черт. 09.TM.27.001 является быстроходным валом цилиндрического редуктора и предназначена для передачи крутящего момента от привода к промежуточному валу редуктора. Вал-шестерня получает вращение от привода через муфту установленную по пов. 4 на шлицах и воспринимает крутящий момент боковыми поверхностями 3 шлицевых пазов. Вал-шестерня передает крутящий момент боковыми поверхностями 13 зубьев зубчатого венца зубьям венца промежуточного вала. Вал-шестерня установлен в подшипниках качения в корпусе редуктора.
Вал-шестерня работает в условиях действия радиальной знакопеременной сосредоточенной нагрузки и крутящего момента. Зубья зубчатого венца испытывают действие изгибающего усилия контактного давления и сил трения. Под действием последних происходит нагрев и изнашивание зубьев.
2 Систематизация поверхностей
Все поверхности детали на эскизе нумеруем и систематизируем по их назначению.
Исполнительные поверхности (И) выполняющие служебные функции вала-шестерни – передачу крутящего момента - боковые поверхности 12 зубьев и боковые поверхности 3 шлицев.
Основные конструкторские базы (ОБ) определяющие положение вала-шестерни в редукторе цилиндрические подшипниковые шейки пов. 6 и 17 и торцовые поверхности 8 и 15
Вспомогательные конструкторские базы (ВБ) определяющие положение присоединяемых деталей – цилиндрическая пов. 6 шлицевая пов. 2 и 3 верхний профиль шлицев пов. 4
Свободные поверхности (С) не сопрягающиеся с другими деталями - пов. 1 5 7 9 10 11 13 14 16 18.
Номера поверхностей и их назначения заносим в графы1-3 таб. 1.4. В таблице приняты обозначения формы поверхностей:
Ц - цилиндрическая наружная
КВ - коническая внутренняя
3 Анализ технических требований
Марка материала – сталь 40Х ГОСТ 4543-71 указана в основной надписи. Твердость 40 45 HRC п.1 технических требований. На чертеже даны все размеры необходимые для изготовления и контроля детали. Точность размеров задана комбинированным способом в виде посадки квалитета точности и предельных отклонений по ГОСТ 2.307-79. Точность свободных размеров 14 квалитет п.2 технических требований. Шероховатость поверхностей указана непосредственно на изображении и в правом верхнем углу чертежа. Предельные отклонения формы и расположение поверхностей 6 8 15 17 заданы в виде условных обозначений по ГОСТ 2.308-79 отклонения для остальных поверхностей должны укладываться в допуск на размер. Формы размеры и точность шлицев определенны – по ГОСТ 1139-58. Фаски и радиусы закруглений выполнены по ГОСТ 10948-64.
Характеристики поверхности вал шестерня
Вывод: черт. 09. ТМ. 27. 001 содержит все необходимые сведения для разработки ТП обработки детали “Вал промежуточный”.
4 Анализ технологичности детали
Материал детали – сталь 40Х ГОСТ 4543-71: 036 044 С; 05 08 08 110% . Твёрдость в состоянии поставки до 217 НВ после закалки - 45 HRC. Прочность в в состоянии поставки до 795 МПа после закалки - 8801080 МПа. Эти механические характеристики обеспечивают нормальную работу вала-шестерни в редукторе. Материал не является дефицитным. Термообработка выполняется по типовому техпроцессу и не требует специальных условий. Сталь имеет удовлетворительную обрабатываемость резанием коэффициент обрабатываемости Ко=08 при обработке твёрдосплавным инструментом и Ко=07 при обработке инструментом из быстрорежущей стали.
Заготовку вала можно получить как из проката так и обработкой давлением – штамповкой или высадкой. В обоих случаях форма заготовки и её элементов достаточно простая.
Свободные поверхности выполнены по 14 квалитету точности. На заготовительных операциях такой точности не добиться поэтому предусматривается обработка всех поверхностей
Таким образом с точки зрения получения заготовки деталь можно считать технологичной.
5 Технологичность общей конфигурации
Вал-шестерню Радиусы закруглений и фаски выполняются по ГОСТ 10948-64 форма и размеры канавок – по ГОСТ 8820-69 формы размеры и точность шлицев определенны – по ГОСТ 1139-58. Такая унификация упростит обработку и контроль этих элементов вала-шестерни.
можно отнести к типу деталей “Валы” для которых разработан типовой ТП. Деталь не содержит каких-либо специфических особенностей формы поэтому может быть обработана непосредственно по типовому ТП.
Форма детали позволяет вести обработку одновременно нескольких
поверхностей – цилиндрических 4 6 9 11 и торцовых 8 10; цилиндрических 17 14 11 и торцовых 13 15 . Одновременно несколько заготовок удастся обработать только на многошпиндельном станке что вряд ли целесообразно для серийного производства. В остальных случаях оборудование может быть простым универсальным. Оснастку можно также применить универсальную. Все поверхности вала-шестерни доступны для контроля.
Таким образом с точки зрения общей компоновки детали её можно считать технологичной.
6 Технологичность базирования и закрепления
Черновыми базами для установки заготовки на 1-й операции могут быть цилиндрические шейки и торцовые поверхности заготовки. В дальнейшем за базы могут быть приняты как цилиндрические поверхности 4 7 так и специально выполненные центровые отверстия 19 и 20 по ГОСТ 14034-74.
Измерительные базы детали можно использовать в качестве технологических баз. Точность и шероховатость этих баз обеспечит требуемую точность обработки. Таким образом с точки зрения базирования и закрепления деталь следует считать технологичной.
7 Технологичность обрабатываемых поверхностей
Предполагается обработать все поверхности детали т.к. заданные точность и шероховатость не позволяют получить их на заготовительных операциях. Правда можно исключить из обработки торцы пов. 1 и 18 в случае обеспечения их точности и шероховатости при отрезке проката но целесообразность этого может быть установлена только после детального анализа. Всего обрабатывается 18 поверхностей: 6 цилиндрических 4 6 9 11 14 17 ; 7 торцовых 1 5 8 10 13 15 18 ; зубья 12 ; шлицы пов. 2 3 ; 2 канавки пов. 7 и 16 . Т.е. даже при полной обработке число
обрабатываемых поверхностей относительно невелико.
Протяжённость обрабатываемых поверхностей относительно невелика и определяется условиями компоновки редуктора и работы вала-шестерни.
Точность и шероховатость рабочих поверхностей 3 4 6 8 12 15 17 определяются условиями работы вала-шестерни. Уменьшение точности приведёт к снижению точности установки вала в редукторе и надёжности его работы. Увеличение шероховатости этих поверхностей приведёт к снижению надёжности сопряжений и интенсивному изнашиванию поверхностей.
Форма детали позволяет обрабатывать пов. 1 6 11 17 18 на проход.
Обработка поверхностей 3 4 5 7 8 9 10 13 14 15 16 в упор затруднений не вызывает.
Поверхности различного назначения разделены что облегчает обработку. Для выхода резца и шлифовального круга при обработке пов. 6 и 17 предусмотрены канавки 7 и 16 . Нетехнологичным следует считать отсутствие канавки для выхода шлифовального круга на пов. 4 что затрудняет её обработку. Таким образом с точки зрения обрабатываемых поверхностей деталь следует считать технологичной.
Поскольку деталь “Вал-шестерня” отвечает требованиям технологичности по всем 4 группам критериев можно сделать вывод о её достаточно высокой технологичности.
Выбор стратегии разработки ТП
Деталь «Вал-шестерня» черт. 09.ТМ.27.001. Объем выпуска N = 2000 детгод.
1. Определение типа производства
Тип производства определяем исходя из расчетного объема выпуска N0 детгод:
где m – масса детали m = 133кг;
KT – коэффициент трудоемкости изготовления для детали средней сложности KT = 1.
что соответствует среднесерийному производству.
2. Выбор стратегии разработки ТП
Пользуясь табл. 3.1 принимаем следующую стратегию разработки ТП:
) В области организации ТП:
Вид стратегии – последовательная в отдельных случаях циклическая; линейная в отдельных случаях разветвленная; жесткая в отдельных случаях адаптивная.
Повторяемость изделий – периодическая партиями.
Форма организации ТП – переменно-поточная
) В области выбора и проектирования заготовки:
Метод получения заготовки – прокат или штамповка.
Выбор методов обработки – по таблицам с учетом коэффициентов удельных затрат Куд.
Припуск на обработку незначительный.
Метод определения припусков – укрупненный по таблицам в отдельных случаях расчёт по переходам.
) В области разработки технологического маршрута:
Степень унификации ТП – разработка ТП на базе типового ТП.
Степень детализации разработки ТП – маршрутный ТП в отдельных случаях – маршрутно-операционный ТП.
Принцип формирования маршрута – экстенсивная в отдельных случаях интенсивная концентрация операций.
Обеспечение точности – работа на настроенном оборудовании с частичным применением активного контроля.
Базирование – с соблюдением принципа постоянства баз и по возможности – принципа совмещения баз.
) В области выбора средств технологического оснащения (СТО):
Оборудование – универсальное в том числе с ЧПУ.
Приспособления – универсальные стандартные универсально-сборные в отдельных случаях специальные.
Режущие инструменты – стандартные в отдельных случаях специальные.
Средства контроля – универсальные в отдельных случаях модернизированные.
) В области проектирования технологических операций:
Содержание операций – по возможности одновременная обработка нескольких поверхностей исходя из возможностей оборудования.
Загрузка оборудования – периодическая смена деталей на станках.
Коэффициент закрепления операций Кзо = 20 30.
Расстановка оборудования – по типам и размерам станков местами по ходу ТП.
Настройка станков – по измерительным инструментам и приборам либо работа без предварительной настройки по промерам.
) В области нормирования ТП:
Определение режимов резания – по общемашиностроительным нормативам в отдельных случаях – по эмпирическим формулам.
Нормирование – укрупненное по опытно-статистическим нормам в отдельных случаях – детальное пооперационное.
Квалификация рабочих – достаточно высокая.
Технологическая документация – маршрутно-операционные карты.
Принятой стратегией мы будем руководствоваться при разработке ТП.
Выбор метода получения заготовки
Выбрать оптимальный метод получения заготовки детали «Вал-шестерня» черт. 09.ТМ.27.001. Производство среднесерийное.
По табл. 4.1 определяем что для детали типа «Валы» средней сложности из стали для серийного производства целесообразно применить в качестве заготовки прокат или горячую штамповку. Для окончательного выбора метода получения заготовки выполним сравнительный экономический анализ. В основу анализа положим сравнение суммарных стоимостей С переменной доли затрат на получение заготовки Сз и ее механическую обработку Собр:
где i — номер варианта получения заготовки. В нашем случае i=1 для заготовки из проката i=2 для штампованной заготовки.
Переменные затраты на получение заготовки Сз руб. составляют:
Сзi=Цмi Мзi Кспi Кслi (3.2)
Кспi Кслi— коэффициенты учитывающие соответственно способ получения заготовки и ее сложность.
Рассчитаем Сз для каждого из вариантов.
) Вычерчиваем контур детали (рис. 3.1). На этом же эскизе вычерчиваем контуры заготовки из проката рис 3.1 и штамповки рис 3.2 (без масштаба).
) По табл. 4.7 определяем ориентировочно припуск на обработку Z:
а) для заготовки из проката:
пов. 1 18 l1=145 l2=74 Z=4
пов. 11 l1=37 l2=145 Z=3.
б) для штампованной заготовки:
пов. 1 l1=95 l2=30 Z=3
пов. 6 l1=30 l2=95 Z=28
пов. 8 l1=4 l2=45 Z=22
пов. 11 l1=74 l2=18 Z=3
пов. 15 l1=3 l2=45 Z=22
пов. 17 l1=30 l2=25 Z=22
пов. 18 l1=25 l2=30 Z=22
Определяем размеры заготовки с учетом припусков и проставляем на рис. 3.1 3.2.
) Определяем напуски.
Для заготовки из проката принимаем ближайший диаметр прутка 80.
Для штамповки назначаем предварительно уклон 50 и радиусы переходов R2.
Вычерчиваем напуски на рис. 3.1 3.2 и проставляем размеры заготовки с учетом припусков и напусков.
) Определяем массу детали МД и заготовки МЗ кг:
МД=0785( d12l1 + d22 l2 + . . . + dn2ln ) r
n число элементарных объемов;
r плотность стали; r=000785 кгсм3.
МД=0785(28248 + 3247+45204+74218+45203+3225)000785=133 кг
где d—диаметр проката см;
l—длина заготовки см.
МЗ1=07858.062155000785=62 кг
МЗ2=0785·(3562958+494204+8224+4.9420.3+3.562×2.58)000785 =2 кг.
) Коэффициент использования материала:
КИМ1=МДМЗ1=133:62=021
КИМ2=МДМЗ2=133:2=066
) Определяем ЦМ руб.кг по табл. 4.2 и поправочные коэффициенты по табл.4.3-4.4:
) Подставляем найденные значения в формулу (3.2):
СЗ1 = 1462121 = 1041 руб.
СЗ2 = 142251 = 70 руб.
Переменные затраты на черновую обработку Собр руб. составляют:
СМi = Суд (Мзi — Мд) Ко (3.3)
где Суд — удельные затраты на снятие 1 кг стружки при черновой обработке руб.кг;
Ко — коэффициент обрабатываемости материала.
Рассчитаем СМ для каждого из вариантов.
)По табл. 4.5 определяем для среднесерийного производства Суд=26.
)По табл. 4.6 определяем для стали 40Х Ко = 08.
)Подставляем найденные значения в формулу (3.3):
СМ1=26(62-133)08=1583 руб.
СМ2=26(2–133)08=8645 руб.
Подставляя полученные значения Сз и СМ в формулу (3.1) получим:
С1 = 1041 + 1583 = 2624 руб.
С2 = 70 + 8645 = 1564 руб.
По минимуму переменных затрат принимаем 2-й вариант - штамповка
Выбор методов обработки поверхностей
Варианты обработки пов. 6 и 17
В табл. 4.1 обозначено:
ТП–точение получистовое
Ш–шлифование черновое
ШП–шлифование получистовое
ШЧ–шлифование чистовое
Рядом с обозначением метода обработки в скобках указан квалитет точности получаемый на данном переходе а сверху– коэффициент удельных затрат КУj для данного перехода.
Оптимальный вариант обработки выбираем по минимуму суммарных удельных затрат характеризуемых суммой КУi всех переходов данного варианта. При этом поскольку переходы Т(12) и ШЧ(6) а также ТО присутствуют во всех вариантах обработки их из расчёта исключаем.
Из табл. 4.1. видно что минимальный коэффициент удельных затрат КУ=61 соответствует варианту 3 предусматривающему ТО после чистовой токарной обработки. Поэтому примем этот вариант обработки:
Т(12; 125)–ТП(10; 63)– ТЧ(8; 16)–ТО(9)– ШП(8; 16)–ШЧ(6; 08).
Здесь в скобках указаны квалитет точности и шероховатость поверхности Ra мкм для каждого перехода.
Для обработки места под сальник пов. 6 (6-й квалитет Ra=04) принимаем дополнительный переход полирование.
Полученным выше результатом воспользуемся для назначения методов обработки других поверхностей.
Шейка под муфту пов. 4 (6-й квалитет Ra=08):
Т(12; 125)–ТП(10; 63)– ТЧ(8; 16)–ТО(9)– ШП(8; 16)–ШЧ(6; 08).
Наружная поверхность зубчатого венца пов. 11 (11; 63):
Т(12; 125)–ТП(10; 63)–ТО(11).
Свободные шейки пов. 9 и 14 канавки пов. 7 16 (14; 125):
Уступы пов. 8 и 15 (8; 16):
Т(12; 125)–ТП(10; 63)– ТЧ(8; 16)–ТО(9)– ШП(8; 16)..
Уступ пов. 5 (10; 32):
Т(12; 125)–ТП(10; 63)–ТО(11)
Торцы зубчатого венца пов. 10 и 13 (14; 125):
Торцы пов. 1 и 18 (14; 125):
Боковые поверхности Шлицев пов. 3 (6; 08)
Ф(8; 32)–ТО(9) – Шч(6; 08)
Впадины шлице пов. 2 (9; 32)
Зубчатый венец пов. 12 (6 степень точности Ra=08):
ЗФ(8 ст.; 63)–СФ–ШВ(7 ст.; 16)–ТО.
ЗФ–зубофрезерование
Центровые отверстия пов. 19 и 20
Методы обработки поверхностей сводим в табл. 4.2.
Методы обработки поверхностей
Т–ТП– ТЧ –ТО–ШП–ШЧ –ПО
Определение припусков на обработку поверхностей
Определить припуски на обработку детали “Вал-шестерня” черт. 09.ТМ.27.001. Метод получения заготовки – штамповка. Производство среднесерийное. Припуск на самую точную поверхность рассчитать суммированием по переходам на остальные поверхности – по табл. 4.7.
Самыми точными поверхностями детали “Вал-шестерня” являются пов. 6
) По данным работы 4 записываем в графы 1 3 № заготовительного перехода (№0) его наименование (способ получения заготовки) и квалитет точности. По данным работы 5 в эти же графы записываем №№ переходов мехобработки их наименование и квалитет точности.
) По табл. 1.1 определяем допуски Td для каждого перехода и заносим в графу 4 табл.5.1.
) Определяем допуск формы и расположения Тр=03Тd для каждого перехода и заносим в графу 5 табл. 5.1.
) По табл. 5.1 определяем толщину дефектного слоя а для каждого перехода и заносим в графу 6 табл. 5.1.
) По табл. 5.2 определяем допуск на точность установки заготовки в приспособлении для каждого перехода кроме заготовительного и заносим в графу 7 табл. 5.1.
) По формуле (5.1) рассчитаем припуск Z для каждого перехода кроме заготовительного. Полученные значения округляем до знака после запятой с которым задан допуск Td.
Результаты расчета заносим в графу 8 табл. 5.1 начиная с 1-го перехода.
) Определяем операционные размеры. Диаметр d5 задан на чертеже детали:
) Общий припуск на обработку составляет:
Рассчитываем припуск на пов 11.
Определяем операционные размеры. Диаметр d2 задан на чертеже детали:
Общий припуск на обработку составляет:
Рассчитываем припуск на пов 8.
Определяем операционные размеры. d4 задан на чертеже детали:
Рассчитываем припуск на пов 15.
Общий припуск на обработку составляет
Рассчитываем припуск на пов 1 18.
Определяем операционный размер. d4 задан на чертеже детали:
Общий припуск на обработку составляет
Сравнивая значения припусков полученных суммированием по переходам с табличными видим что переход от табличного метода определения припусков к расчетному приводит к существенному уменьшению припусков.
Проектирование штампованной заготовки
) Вычерчиваем контур детали. Проставляем размеры (рис. 6.1)
) Вычерчиваем контур заготовки заготовка будет содержать 3 ступени (рис. 6.1).
) Определяем припуски на обработку по таблице 4.7. Результаты заносим в графу 3 табл. 6.1. Определяем расчетные размеры заготовки путем прибавления припусков к размерам детали и округления их до 05 мм в сторону увеличения припуска. Результаты заносим в графу 4 табл. 6.1.
)Плоскость разъема – диаметральное продольное сечение заготовки. При таком положении плоскости разъема полость штампа имеет наименьшую глубину. В этой плоскости удобно контролировать смещение штампа. Заготовка получается симметричной что делает возможность поворачивания ее при штамповке и уменьшать износ штампа.
)В качестве технологических баз на 1-й операции мехобработки
целесообразно использовать – пов. 6 8 17 .
) Определяем класс точности Т штамповки. При открытой штамповке обеспечивается точность Т4.
Расчет размеров заготовки
Положение поля допуска
) Определяем группу стали М в зависимости от содержания углерода С и легирующих элементов Л. Для стали 40Х У=036 044% Л5% что соответствует группе М2.
) Определяем степень сложности заготовки в зависимости от коэффициента Кс=WзWо где – Wз – объем заготовки; Wо – объем описанного цилиндра.
где di и i - диаметр и длина соответствующей ступени заготовки.
где d – диаметр описанного цилиндра; - длина заготовки.
что соответствует степени сложности С2.
)Определяем исходный индекс И.
где Ио – начальный индекс зависящий от массы заготовки.
Им Ис Ит – добавочные индексы в зависимости от М С Т.
здесь – плотность стали
для mЗ=19 Ио=5; Им=1; Ис=1; Ит=4.
) Определяем допуски на размеры заготовки в зависимости от
исходного индекса по табл. 7.3 и заносим их значения в графу 5 табл. 6.1.
) Определяем штамповочные уклоны. Согласно рекомендациям принимаем значения уклонов 7º.
) Определяем радиусы закруглений R. По табл. 7.3 для глубины полости штампа 20 мм при массе заготовки mЗ=19кг R=2мм. Допуск на радиус для класса точности Т4 составляет ±025R=±05мм.
) Определяем допустимые значения остаточного облоя То и смещения штампа Тс. По табл. 7.4 для mЗ=19 кг и точности Т4 То=08мм Тс=06мм.
Разработка технологического маршрута
Разработать технологический маршрут обработки детали «Вал-шестерня» черт. 09.ТМ.27.001. Производство среднесерийное.
) Выписываем номера поверхностей их форму точность размеров формы и расположения шероховатость. Заносим эти данные в графы 1-5 табл. 7.1.
Методы обработки поверхностей детали «Вал промежуточный»
Т–ТП– ТЧ -ТО–ШП – ШЧ
Т–ТП– ТЧ –ТО–ШП–ШЧ–ПО
Т–ТП– ТЧ – ТО– ШП – ШЧ
)Для каждой поверхности определяем методы обработки и записываем их в графу 6 табл. 7.1 [1].
)Используя типовой технологический маршрут [2] определяем предварительно порядок и наименование операций по обработке поверхностей детали “Вал промежуточный”. Полученные данные заносим в табл. 7.2.
)Анализируем предварительный маршрут на предмет целесообразности перестановки объединения разделения или замены операций.
Учитывая серийный тип производства объединяем в одну операцию фрезерование торцов 1 18 и сверление центровых отверстий 19 20 полагая что они будут выполняться на фрезерно-центровальном станке.
Операции получистового и чистового точения объединим в одну для каждого конца вала.
) С учетом этих изменений формируем окончательный вариант технологического маршрута который представлен в табл. 7.3
Предварительный маршрут обработки детали “Вал промежуточный”
Сверление центровых отверстий
Черновое точение правого конца
Черновое точение левого конца
Получистовое точение правого конца
Получистовое точение левого конца
Зачистка центровых отверстий
Черновое шлифование правого конца
Черновое шлифование левого конца
Получистовое шлифование правого конца
Получистовое шлифование левого конца
Чистовое шлифование правого конца
Чистовое шлифование левого конца
Шлифование зубьев шлицев
Окончательный маршрут обработки детали “Вал промежуточный”
Наименование операции
Фрезерно-центровальная
Фрезерование торцов 118.
Сверление центровых отверстий 1920
Черновое точение пов. 1011897654.
Черновое точение пов. 13–17
Получистовое и чистовое точение пов. 11864
Получистовое и чистовое точение пов. 1517
Нарезание шлицев пов. 23
Фрезерование зубьев пов. 12
Снятие фасок пов. 12
Зачистка центровых отверстий 19 20
Черновое получистовое и чистовое шлифование пов. 867
Черновое получистовое и чистовое шлифование пов. 1517
Шлифование зубьев 12 и боковую пов. шлицев 3
Выбор средств технологического оснащения
1. Выбор оборудования
При выборе типа и модели металлорежущих станков будем руководствоваться следующими правилами:
) Производительность точность габариты мощность станка должны быть минимальными достаточными для того чтобы обеспечить выполнение требований предъявленных к операции.
) Станок должен обеспечить максимальную концентрацию переходов на операции в целях уменьшения числа операций количества оборудования повышения производительности и точности за счет уменьшения числа перестановок заготовки.
) В случае недостаточной загрузки станка его технические характеристики должны позволять обрабатывать другие детали выпускаемые данным цехом участком.
) Оборудование не должно быть дефицитным следует отдавать предпочтение отечественным станкам.
) В мелкосерийном производстве следует применять преимущественно универсальные станки револьверные станки станки с ЧПУ многоцелевые станки (обрабатывающие центры). На каждом станке в месяц должно выполняться не более 40 операций при смене деталей по определенной закономерности.
) Оборудование должно отвечать требованиям безопасности эргономики и экологии.
Если для какой-то операции этим требованиям удовлетворяет несколько моделей станков то для окончательного выбора будем проводить сравнительный экономический анализ.
Выбор оборудования проводим в следующей последовательности:
) Исходя из формы обрабатываемой поверхности и метода обработки выбираем группу станков.
) Исходя из положения обрабатываемой поверхности выбираем тип станка.
) Исходя из габаритных размеров заготовки размеров обработанных поверхностей и точности обработки выбираем типоразмер (модель) станка.
Данные по выбору оборудования заносим в табл. 8.1.
2. Выбор приспособлений
При выборе приспособлений будем руководствоваться следующими правилами:
) Приспособление должно обеспечивать материализацию теоретической схемы базирования на каждой операции с помощью опорных и установочных элементов.
) Приспособление должно обеспечивать надежные закрепление заготовки обработке.
) Приспособление должно быть быстродействующим.
) Зажим заготовки должен осуществляться как правило автоматически.
) Следует отдавать предпочтение стандартным нормализованным универсально-сборным приспособлениям и только при их отсутствии проектировать специальные приспособления.
Исходя из типа и модели станка и метода обработки выбираем тип приспособления.
Выбор приспособления будем производить в следующем порядке:
) Исходя из теоретической схемы базирования и формы базовых поверхностей выбираем вид и форму опорных зажимных и установочных элементов.
) Исходя из расположения базовых поверхностей и их состояния (точность шероховатость) формы заготовки и расположения обрабатываемых поверхностей выбираем конструкцию приспособлений.
) Исходя из габаритов заготовки и размеров базовых поверхностей выбираем типоразмер приспособления.
После расчета режима резания (разд. 12) определим силы резания по значению которых рассчитываем силу зажима достаточную для обеспечения надежного закрепления.
Учитывая передаточный коэффициент усиления определим усилие и мощность привода. Сравним эти значения с характеристиками приспособления. Если силы зажима или мощность превосходят допустимые значения то выбираем более мощное приспособление.
Данные по выбору приспособлений заносим в табл. 8.2.
1план обр А1.cdw

фрезерно-центровальный
вертикально зубофрезерный станок
Сталь 40Х ГОСТ 4543-71
ПРокат.frw

Рекомендуемые чертежи
- 02.05.2022
- 22.05.2024