Кран велосипедный




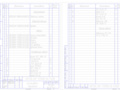
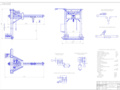
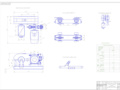
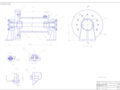
- Добавлен: 25.10.2022
- Размер: 3 MB
- Закачек: 0
Описание
Состав проекта
![]() |
![]() ![]() ![]() ![]() |
![]() ![]() |
![]() |
![]() ![]() ![]() |
![]() |
![]() ![]() ![]() ![]() |
![]() |
![]() ![]() |
![]() ![]() ![]() ![]() |
![]() |
![]() ![]() |
![]() ![]() |
![]() |
![]() |
![]() |
![]() ![]() ![]() |
![]() ![]() |
![]() ![]() |
![]() |
![]() ![]() ![]() ![]() |
![]() ![]() ![]() ![]() |
![]() |
![]() ![]() ![]() |
Дополнительная информация
ОбщийОВ.dwg

ВылетСБ.dwg

БарабанСБ.dwg

Барабан.dwg

Мех. изм. вылета.dwg

ПодъемОВ.dwg

Рекомендуемые чертежи
Свободное скачивание на сегодня
- 22.08.2014
- 29.08.2014