Кран на колонне г/п 3.2 т




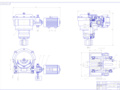

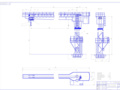
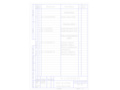
- Добавлен: 25.10.2022
- Размер: 2 MB
- Закачек: 0
Описание
Состав проекта
![]() |
![]() |
![]() ![]() |
![]() ![]() |
![]() ![]() ![]() ![]() |
![]() ![]() |
![]() ![]() ![]() ![]() |
![]() ![]() ![]() ![]() |
![]() ![]() |
![]() ![]() |
![]() ![]() ![]() ![]() |
![]() ![]() |
![]() ![]() ![]() ![]() |
![]() ![]() ![]() ![]() |
![]() |
![]() ![]() ![]() |
Дополнительная информация
Elektrotal.dwg

Болты по ГОСТ 15589-70
Гайка М10-6Н ГОСТ 5915-70
Винт М6х10 ГОСТ 11738-84
Винт М12х35 ГОСТ 1476-93
Манжеты по ГОСТ 8752-79
Подшипники по ГОСТ 8338-75
Электродвигатель АО2-52-8
Электромагнит МИС-4100
Шайбы по ГОСТ 6402-70
Mekhanizm_povorota_spec.dwg

Болт М8х30 ГОСТ 15589-70
Винт М10х25 ГОСТ 1477-93
Муфта МЗП-1 ГОСТ 5006-55
Vid_obschy_spec.dwg

Концевой выключатель КУ704
Вновь разрабатываемые
Механизм передвижения
Vid_obschy.dwg

Скорость подъёма груза 1
Скорость передвижения тали 2
Скорость вращения крана 1
Mekhanizm_povorota.dwg

Tormoz_TT-160.dwg

Размеры для справок.
Остальные технические требования по СТБ 1022-96.
Записка Испр.doc
К кранам на колонне общего назначения относятся краны предназначенные для работы с разнообразными грузами и имеющие в качестве грузозахватных органов грузовые крюки. Наиболее широко их используют в сборочных цехах (в качестве монтажных) в машинных залах электростанций.
Краны на колонне общего назначения имеют большую номенклатуру типоразмеров и исполнений.
Из основных тенденций развития ГПМ следует отметить:
-создание качественно новых ГПМ и механизмов а так же модернизация существующих;
-повышение грузоподъёмности ГПМ при снижении их массы благодаря применению новых кинематических схем рациональных профилей новых материалов (легированных сталей лёгких сплавов и пластмасс);
-улучшение условий труда крановщиков путём повышения эргономичности рабочих мест;
-создание блочных и унифицированных конструкций позволяющих получить наиболее высокий технико-экономический эффект при изготовлении и эксплуатации этих машин.
Основная цель курсового проекта по ПТМ – приобретение студентом навыков проектирования машины в целом в отличие от предыдущих курсовых проектов (детали машин) где необходимо было спроектировать отдельный узел машины. Работая над поставленной задачей студент выполняет расчёты учится рациональному выбору материалов узлов и форм элементов конструкции стремится обеспечить их высокую экономичность надёжность и долговечность. Приобретённый студентом опыт окажет неоценимую услугу при выполнении им курсовых проектов по другим дисциплинам дипломного проектирования а так же для всей дальнейшей конструкторской работы.
Расчёт механизма подъёма крана
грузоподъёмностьQ=3.2 т
скорость подъёма грузаVгр=11ммин
скорость вращения кранаn=1мин-1
скорость передвижения тали VT= 25 ммин
группа режима работы кранаА2
высота подъёма грузаН=6м
Рисунок 1.1 – Кинематическая схема механизма подъема.
2Выбор конструкции полиспаста кинематическая схема
полиспаста КПД полиспаста
По рекомендациям принимаем одинарный полиспаст (а=1)
Рисунок 1.2 – Схема полиспаста
КПД полиспаста определим по формуле:
где hбл=097 098 – КПД блоков
n=1 – количество подвижных и неподвижных блоков
3 Выбор каната и крюка
Максимальное натяжение в канате набегающем на барабан при подъёме груза определяется по формуле:
где Q - грузоподъемность;
hп – КПД полиспаста;
Канат выбираем по разрывному усилию:
где zp= 335 – коэффициент использования каната для режима работы А2.
По полученному разрывному усилию выбираем канат двойной свивки типа ЛК-Р конструкции 6x19(1+6+66)+1о.с. ГОСТ 2688-80 диаметром dк=11 мм и разрывным усилием Sр=6419 кН.
По номинальной грузоподъёмности и режиму работы выбираем крюк однорогий тип А №12 ГОСТ 6627-74.
4 Расчёт диаметров барабана и блоков определение длины барабана
Диаметр блоков по средней линии навитого каната определяем по формуле:
где h1=20 – коэффициент выбора диаметра для электроталей режима работы А2;
Диаметр барабана по средней линии навитого каната определяем по формуле:
Из конструктивных соображений принимаем диаметр барабанамм так как при меньшем диаметре значительно увеличивается длина барабана мм.
Длина барабана определяется по формуле:
где - длина концевых не нарезных частей барабана
- длина нарезанной части барабана
где мм – шаг винтовой нарезки канавок на барабане;
– общее число витков на барабане;
где – число рабочих витков;
– количество запасных витков которое остается на барабане при спуске груза на полную высоту;
5 Определение мощности на подъём груза номинальной массы при
установившемся движении механизма выбор двигателя
Определяем мощность на подъем груза номинальной массы по формуле :
Подбираем электродвигатель серии АО2-52-8 при ПВ=25% номинальная мощность (Nн) 64 кВт частота вращения ротора n1=660 мин-1 момент инерции ротора Iр=082 кг·м2=008210=082 Hм2.
Определяем частоту вращения барабана:
Следовательно требуемое передаточное отношение механизма:
Редуктор электротали двухступенчатый. Принимаем передаточное число тихоходной ступени: тогда передаточное число быстроходной ступени: .
Модуль быстроходной ступени мм тихоходной – мм.
Межосевое расстояние:
Фактическое передаточное число редуктора:
Фактическая скорость подъема
Разница скорости составляет:
что в пределах нормы.
Делительный диаметр:
Делительный диаметр dw мм
Ширина зубчатого венца b мм
Номинальный момент на валу электродвигателя:
Номинальные крутящие моменты на валах редуктора.
Статический крутящий момент на валу барабана при подъеме груза:
где – к.п.д. зубчатой передачи одной ступени.
7 Проверка редуктора на прочность и выносливость
Произведем проверочный расчет закрытых зубчатых передач на выносливость по контактным напряжениям и на прочность зубьев при изгибе.
Зубчатые колеса редуктора механизма подъема изготавливаются из материала сталь 45 и подвергаются термообработке до твердости НВ 241 277.
Определяем окружную силу в зацеплении:
Окружные скорости шестерен:
Коэффициент учитывающий динамическую нагрузку в зацеплении:
Коэффициент учитывающий неравномерность распределения нагрузки по ширине венца: кH =105
Удельная расчетная окружная сила:
Расчетные контактные напряжения:
zн =077 ( коэф. учитывающий форму сопряженных поверхностей зубьев )
zЕ =190 МПа ( коэф. учитывающий механические свойства матер. колес )
z =1.25 ( коэф. суммарной длины контактных линий)
Запас прочности по контактным напряжениям:
Условие прочности соблюдается.
Удельная расчетная окружная сила при изгибе:
Коэффициент учитывающий неравномерность распределения нагрузки по ширине венца: кF =1
Коэффициент учитывающий неравномерность распределения нагрузки для одновременно зацепляющихся пар зубьев: кFα =1
Коэффициент внешней динамической нагрузки: кА=1
Расчетные напряжения изгиба:
YFS=3.96 (коэффициент учитывающий форму зуба)
Y=1 (коэффициент учитывающий наклон зуба)
Y=1 (коэффициент перекрытия зубьев)
Запас прочности по напряжениям изгиба:
Условие прочности выполняется
8 Выбор тормоза проверочный расчёт тормоза
Статический момент на тормозном валу:
где – КПД полиспаста;
– КПД зубчатой передачи;
Нормальная сила давления колодок на тормозной шкив:
где f=0.42 – коэффициент трения вальцовой ленты по чугуну и стали
Расчет тормоза электротали.
Рисунок 1.8 – Расчетная схема
Расчетная схема тормоза приведена на рисунке 1.8. необходимое усилие пружины замыкающей тормоз:
где – к.п.д рычажной системы.
Усилие электромагнита :
где - 4H – вес рычага соединяющего якорь электромагнита с размыкающим пальцем.
Работа производимая силой нажатия колодок на тормозной шкив
Ход электромагнита :
По необходимому тяговому усилию и ходу подбираем электромагнит серии МИС 2100Е со следующими характеристиками:
Тормоз регулируется на необходимый тормозной момент.
Проверочный расчёт по удельному давлению:
где м – ширина тормозного шкива;
– допускаемое удельное давление;
– угол обхвата шкива
Удельное давление в допускаемых пределах.
Проверочный расчёт на нагрев:
где [qv] – допускаемая удельная мощность трения;
– окружная скорость вращения шкива;
Выбранный тормоз отвечает условию нагрева.
Грузоупорный тормоз расположен на втором(тихоходном ) валу редуктора.
Рисунок 1.9-Грузоупорный тормоз
Произведём его расчёт:
Угол подъёма трёхзаходней резьбы тормозного вала:
где - число заходов резьбы;
- средний диаметр резьбы;
Осевая сила возникающая при торможении и зажимающая фрикционные кольца тормоза
где - средний радиус винтовой резьбы
- угол трения в резьбовой паре при работе в масляной ванне;
- коэффициент трения вальцованной ленты по стали в масле;
- средний радиус поверхности трения.
Тормозной момент грузоупорного тормоза :
где - число пар трущихся поверхностей.
Тормозной момент должен удовлетворять следующему условию:
Грузоупорный тормоз в электротали используется в качестве второго тормоза механизма подъёма поэтому коэффициент запаса торможения принимается равным 1.25.
Надёжность удерживания груза в подвешенном состоянии обеспечивается при соблюдении зависимости:
В рассматриваемом случае
Движущийся в низ груз остановится при условии:
Проверка винтовой резьбы на смятие:
где - диаметр наружный винтовой резьбы;
- диаметр внутренний винтовой резьбы;
9 Проверка двигателя на пусковые перегрузки
Для проверки электродвигателя на пусковые перегрузки определяем статический момент валу двигателя при пуске:
Минимальный пусковой момент электродвигателя
где y1 = 11 16 – кратность минимального пускового момента
Возможность пуска электродвигателя под нагрузкой определяется по условию т.е. 1482> 959. Условие выполняется.
где y2 = 21 – кратность максимального пускового момента
Определяем средний пусковой момент двигателя:
Потребное время пуска электродвигателя определим по формуле (4.1 [4]):
где с-1 – угловая скорость двигателя;
- момент инерции всех движущихся частей механизма приведенный к валу электродвигателя;
где - момент инерции вращающихся частей механизма;
- момент инерции поступательно движущихся частей механизма;
где g =11 12 – коэффициент учёта инерции вращающихся масс расположенных на втором третьем и последующих валах механизма
кг.м2 – момент инерции вращающихся масс на первом валу
где. – момент инерции тормозного шкива;
– момент инерции ротора электродвигателя.
где rб – радиус барабана по центру наматывания каната
Динамический момент при пуске определяем по формуле:
Определяем потребный средний пусковой момент:
Следовательно двигатель выдержит пусковые перегрузки.
10 Определение толщины стенки барабана
Барабан отлит из Чугун 15-32 с пределом прочности на сжатие (таблица 5.2 [4]).
Предварительно толщину стенки барабана определяем из расчёта на сжатие:
Из условия технологии изготовления литых барабанов толщина стенки их должна быть не менее 6 мм и может быть определена по формуле:
Принимаем толщину стенки мм.
11 Расчёт крепления каната к барабану
Рисунок 1.10. – Крепление каната к барабану.
Определим выдергивающее усилие:
где: a - угол обхвата канатом барабана принимаем a=3p
f - коэффициент трения между канатом и барабаном (f=0.10 0.16)
Необходимое осевое усилие болта:
Определим силу затяжки болтов:
где: f - коэффициент трения.
Расчетный внутренний диаметр резьбы болтов равен:
где – допускаемое напряжение растяжения стали 3;
– количество болтов;
– коэффициент запаса.
Принимаем винты М16 с внутренним диаметром резьбы мм.
12 Расчет валов тали
Произведём расчёт быстроходного вала редуктора.
Определим минимальный диаметр вала:
=226 МПа – допустимые касательное напряжение.
Принимаем диаметр вала под подшипники мм
Рассчитаем промежуточный вал:
Минимальный диаметр вала исходя из условия прочности равен:
Диаметр вала под подшипник принимаем мм.
Рассчитаем тихоходный вал.
Внутренний диаметр полого тихоходного вала принимаем мм внешний мм. Проверяем вал на прочность:
– допустимые касательные напряжения.
Условие прочности выполняется.
13 Выбор подшипников электротали
Выбор подшипников осуществляем по посадочному диаметру на валу и динамической нагрузке.
Определяем радиальные нагрузки действующие на подшипники быстроходного вала. Схема нагружения вала представлена на рисунке 1.14.1.
Определяем силу в месте посадки ротора электродвигателя:
Определяем усилия в зацеплении:
Строим эпюру изгибающих моментов в горизонтальной плоскости. Определим реакции опор в горизонтальной плоскости. Составим сумму моментов относительно опоры А.
Составим сумму моментов относительно опоры В.
Строим эпюру изгибающих моментов в вертикальной плоскости.
Запишем сумму моментов относительно опоры А:
Определяем суммарные реакции в опорах А и В:
Выбор подшипников производим по наибольшей нагрузке Н частота вращения вала обмин.
Требуемая долговечность: ч.
Предварительно принимаем шариковый радиальный однорядный подшипник №404 ГОСТ 8338-75 d = 20 мм; B = 17 мм; D = 72 мм; C =307 кН.
Определяем приведенную нагрузку подшипника.
где –коэффициент учитывающий динамичность внешней нагрузки;
–коэффициент учитывающий влияние температуры подшипникового узла;
Расчетная динамическая радиальная грузоподъемность.
где m = 3 – для шарикоподшипников;
n = 660 обмин – частота вращения быстроходного вала.
У принятого подшипника кН > кН. Следовательно подшипник подобран правильно.
Определяем радиальные нагрузки действующие на подшипники быстроходного вала. Схема нагружения вала представлена на рисунке 1.14.2.
Предварительно принимаем шариковый радиальный однорядный подшипник №209 у которого: d = 45 мм; B = 19 мм; D = 85 мм; C = 332 кН.
n = 175 обмин – частота вращения промежуточного вала.
Определяем радиальные нагрузки действующие на подшипники быстроходного вала. Схема нагружения вала представлена на рисунке 1.14.3.
Определяем силу сгибающую барабан:
Предварительно принимаем шариковый радиальный однорядный подшипник №408 у которого: d = 40 мм; B = 27 мм; D = 110 мм; C = 637 кН.
n = 25 обмин – частота вращения тихоходного вала.
У принятого подшипника кН > кН. Следовательно подшипник подобран правильно. Из конструктивных особенностей на опору А подшипник серии 204 у которого: d=20мм; B=14мм; D=47мм; C=127 кН.
14 Расчёт подшипников блоков
Выбор подшипников производим по нагрузке Н частота вращения вала:
Dбл – диаметр блока по центру наматывания каната.
Предварительно принимаем шариковый радиальный однорядный подшипник №210 у которого: d = 50 мм; B = 20 мм; D = 90 мм; C = 351кН.
n = 1215 обмин – частота вращения тихоходного вала.
15 Проверочный расчёт крюковой подвески
15.1 Упорный подшипник
Расчётная нагрузка на подшипник должна быть равна или меньше статической грузоподъёмности:
где - коэффициент безопасности (прил. Х [1])
Для крюка диаметром шейки d1=35 мм выбираем упорный однорядный подшипник лёгкой серии 8207 (ГОСТ 6874-75) со статической грузоподъёмностью С0=68000 Н внутренний диаметр d=35 мм наружный D=62 мм .
16 Расчёт траверсы крюка
Траверса изготовлена из Стали 45 имеющей предел прочности sв=600Мпа предел текучести sт=600 МПа предел выносливости s1=240Мпа.
Траверсу рассчитывают на изгиб при допущении что действующие на неё силы сосредоточенные; кроме того считают что перерезывающие силы незначительно влияют на изгибающий момент. Расстояние между осями щек мм.
Максимальный изгибающий момент .
Момент сопротивления среднего сечения траверсы:
где [s] – допускаемое напряжение материала на изгиб
Рисунок 5 – Траверса
где d2 =d1+(2 5)=35+5=40 мм
b1 – ширина траверсы; назначается с учётом наружного диаметра D1 посадочного гнезда для упорного подшипника
b1=D+(10 20)=62+18=80 мм
Изгибающий момент в сечении Б – Б:
Минимальный диаметр цапфы под подшипник:
Расчёт механизма передвижения электротали
1 Выбор кинематической схемы
Механизм передвижения электротали состоит из электродвигателя закрытого одноступенчатого редуктора трех открытых зубчатых передач и четырех конических колес с ребордами два из которых (с одной стороны) на реборде имеют зубчатые венцы и приводятся во вращение от электродвигателя.
2 Определение полного статического сопротивления передвижению
Полное сопротивление передвижению электротали складывается из сопротивлений от трения при движении и от уклона пути. Груз перемещается электроталью по двутавровой балке на расстояние 7 м. Допустимый местный уклон .
Сопротивление передвижению от трения:
где – вес электротали;
– диаметр ходового колеса;
– коэффициент трения в шарикоподшипниках опоры;
– коэффициент учитывающий дополнительные сопротивления от трения реборд и торцов ступиц ходовых колес .
Сопротивление движению от уклона пути:
Полное статическое сопротивление передвижению электротали:
3 Выбор электродвигателя
Статическая мощность для перемещения электротали с грузом
где – скорость передвижения электротали;
– к.п.д. передачи при полной нагрузке.
Принимаем электродвигатель типа АОЛ 2-21-4 мощностью .
Частота вращения ходового колеса:
Передаточное число редуктора:
Фактическое передаточное отношение:
Фактическая скорость электротали:
Отклонение от заданной скорости:
Моменты действующие на валах редуктора:
5 Проверка редуктора на прочность и выносливость
Зубчатые колеса редуктора механизма подъема изготавливаются из материала сталь45 и подвергаются термообработке до твердости НВ 241 277. Расчет производим по шестерням 1 3 4.
Определяем окружные силы в зацеплениях:
Удельные окружные динамические силы:
где– коэффициент учитывающий влияние вида зубчатой передачи и модификации профиля на динамическую нагрузку;
– коэффициент учитывающий влияние разности шагов зацепления зубьев шестерни и колеса.
Удельная расчетная окружная сила в зоне ее наибольшей концентрации:
где – коэффициент учитывающий неравномерность распределения нагрузки по ширине венца.
Коэффициенты учитывающие динамические нагрузки в зацеплениях:
Удельные расчетные окружные силы:
где – коэффициент внешней динамической нагрузки.
где– коэффициент учитывающий форму сопряженных поверхностей зубьев для прямых зубьев;
– коэффициент учитывающий механические свойства материалов колес;
– коэффициент учитывающий суммарную длину контактных линий для прямых зубьев;
Условие выносливости по контактным напряжениям выполняется.
где– коэффициент учитывающий влияние вида зубчатой передачи и модификации профиля на динамическую нагрузку.
Удельные расчетные окружные силы в зоне их наибольшей концентрации:
где– коэффициент учитывающий неравномерность распределения нагрузки по ширине венца.
Удельные расчетные окружные силы при изгибе:
Расчетные напряжения изгиба зубьев:
где– коэффициент учитывающий форму зуба;
– коэффициент учитывающий наклон зуба для прямых зубьев;
– коэффициент учитывающий перекрытие зубьев для прямых зубьев.
Условие прочности по напряжениям изгиба выполняется.
6 Проверочный расчет двигателя
Номинальный момент двигателя .
Статический момент при нагруженной тележке:
Момент электродвигателя при пуске .
Максимальный момент .
Средний момент электродвигателя при пуске:
Приведенный момент инерции тележки механизма передвижения с грузом:
Время пуска двигателя:
Путь электротали с грузом за время ее разгона:
Сила сопротивления передвижению электротали без груза:
Момент сопротивления передвижению электротали без груза:
Приведенный момент инерции механизма передвижения без груза:
Время пуска электродвигателя при незагруженной электротали:
Путь электротали без груза за время ее разгона:
Среднее ускорение при пуске механизма передвижения с грузом и без груза:
Коэффициент запаса сцепления нагруженной электротали:
где – суммарная сила давления двух приводных колес на рельсы (сцепной вес) электротали с грузом
– коэффициент сцепления колеса с рельсом
– число приводных колес
– общее число колес.
Коэффициент запаса сцепления электротали без груза:
где – сцепной вес ненагруженной электротали.
Ввиду того что в механизме передвижения нет тормоза время свободного выбега определяется по формуле:
Путь который пройдет электроталь до полной остановки:
Установка концевых выключателей производится на расстоянии 90см от конца пути электротали с каждой стороны.
1 Определение основных усилий
L=7 м. На основании рекомендаций определяем недостающие данные.
Рисунок 6- Расчётная схема механизма поворота
Gгр=Qg=32000 H- вес груза
mТЕЛ=210 кг – масса тележки
GПОВ=025QL=02532006=4800 кг – масса поворотной части
Gс=9800 Н-вес стрелы
Противовес определяем из условия равнопрочности колонны. Момент изгибающий колонну при подъёме номинального груза (тележка с номинальным грузом на максимальном вылете):
Ми1 = GTL+ GсC - GПРB
где GT – сила тяжести поднимаемого груза;
GПР - сила тяжести противовеса;
L – вылет стрелы крана.
(GПОВ -GT) – сила тяжести поворотной части крана со снятым грузом
Момент при снятом грузе (тележка без груза на минимальном вылете):
Условие равнопрочности [1]:
Находим моменты по приведенным выше формулам и определяем силу тяжести противовеса
GTL+ GсC - GПРB = GПРB- GсC
Вертикальная сила которая приходится на упорный подшипник:
RV = GПР+ Gс+ GT = 61500+9800+32000=103.3 кН
Горизонтальная сила определяется из уравнения моментов при работе крана с номинальным грузом.
2 Подбор подшипников колонны
Рисунок 7 – Схема верхнего поворотного устройства
На основании рекомендаций [4стр.37]:
Выбираем упорный шарикоподшипник 8124Н по ГОСТ 7872-89 внутренний его диаметр составляет 110 мм наружный 145 мм С0=186 кН; внутренний диаметр радиального шарикоподшипника 1320 (ГОСТ 28428-90) составляет 130мм наружный 195 мм С0=1336 кН [1].
Так как частота вращения крана незначительная то подшипники подбираем по статической грузоподъёмности которая больше чем нагрузки на подшипник.
Нижнее опорно-поворотное устройство включает ролики. Принимаем диаметры ролика [1] Dр = 250 мм цапфы dц.р = 60 мм коэффициент трения в цапфе fц.р = 003; коэффициент трения качения ролика по колонне mк = 005 диаметр колонны Dк=500 мм (смотри далее расчёт колонны).
Рисунок 8 – Схема нижнего опорно-поворотного устройства
3 Определение моментов сопротивления повороту
Определяем статический момент сопротивления повороту. Момент сопротивления в упорном подшипнике:
где dц.у = 0127м – средний диаметр упорного подшипника.
Момент сопротивления в радиальном подшипнике:
где dц.рад = 0162 м – средний диаметр радиального подшипника.
Коэффициент тяги опорных роликов:
Принимаем угол между осями роликов aр = 60°. Следовательно усилие на один опорный ролик:
Проверим беговую дорожку ролика на контактную прочность. Примем ширину дорожки bрол =100 мм. Приведенный радиус ролика:
Напряжение смятия по линии контакта ролик:
где Е = 21·105 МПа – модуль упругости для стали.
Для стали 45 при среднем режиме работы допускаемое контактное напряжение [sсм] = 600 МПа. Выбранный предварительно ролик работоспособен.
Усилие необходимое для перекатывания роликов по колоне:
Fрол = Fр fтяг.р = 26300·002 =526 Н.
Момент сил сопротивления повороту двух опорных роликов
Полный статический момент сопротивления повороту:
Тст = Ту + Трад + Трол = 984+ 553 + 3945 =5482Н·м.
Момент инерции поворотной части крана:
где mг mп mмп mпов – соответственно массы груза поворотной части механизма подъема и противовеса.
Исходя из условия обеспечения допускаемого линейного ускорения груза (принимая для крана общего назначения допускаемое ускорение [а] = 03 мс2) время пуска определим по формуле:
tп = 0105nкрL1 [а] = 0105·1·7 03 =245 с
где nкр =1 мин-1 – частота вращения стрелы крана.
По данным [2] время пуска:
где bпов – рекомендуемый угол поворота принимаемый p9.
По таблице при вылете до 20 м минимальное время пуска 8 с а максимальное 15 с. Принимаем время пуска tп =10 с. Момент сил инерции (предварительный) при принятом времени пуска:
Суммарный пусковой момент:
Тсум = Тст + (11 13) Тин.п =5482 + 11·1850=25832 Н·м.
Необходимая пусковая мощность:
где hм = 075 – КПД механизма поворота принятый предварительно.
Установочная мощность при коэффициенте перегрузки двигателя при пуске y = 20:
Мощность двигателя при установившемся движении:
Выбираем электродвигатель [1] MTF 011-6: мощность 1.7кВт при ПВ=60% частоте вращения ротора n1 = 850 мин-1. При этом максимальный момент Тмакс = 40 Н·м; момент инерции ротора Iр = 00216 кг·м2; масса двигателя 51 кг.
Передаточное отношение механизма определяем учитывая что последняя открытая передача имеет планетарное движение ведущей шестерни. При наружном зацеплении:
Рисунок 9 - Механизм поворота крана
Принимаем червячный редуктор с передаточным числом uр = 34 по ГОСТ 2144-76 и открытую зубчатую пару с передаточным числом uзуб = 25 по ГОСТ 2185-66 [4]m=8 z1=9 z2=225.
5 Расчет муфты предельного момента
Муфта предельного крутящего момента рассчитывается по моменту
где Тпуск - пусковой момент двигателя
ip - передаточное число редуктора
Средний радиус поверхности трения дисков:
Rср=(Rн+Rв)2=(013+008)2=0105 м
где Rн- наружный радиус диска
Rв- внутренний радиус диска
Осевое усилие сжатия необходимое для передачи момента:
где f=01- коэффициент трения стали по стали
z=9- число пар поверхностей трения
Давление на поверхностях трения:
Рабочая нагрузка на пружину:
Рраб=Qz=12952.46=2158.7 H
где z=6- число пружин
Допустимая предельная нагрузка на пружину[1]:
Pпр=(13 16)Pр=13·2158.7=2806.3 Н
Диаметр проволоки пружины из условий деформации при кручении [1]:
где k – коэффициент кривизны
λ – отношение среднего диаметра пружины к диаметру проволоки
Выбираем пружину диаметром прутка d =10 мм
Средний диаметр пружины[1]:
6 Расчет открытой пары механизма поворота
Для цилиндрических открытых зубчатых передач модуль зацепления:
где Т = 1224 Н×м – передаваемый момент;
g=15 – коэффициент учитывающий уменьшение момента сопротивления описного сечения зуба в открытых передачах из–за изнашивания;
z = 14 – число зубьев колеса для которого производится расчёт на изгиб;
YF = 0348 (при х = 0) – коэффициент формы зуба;
[sF] – достигаемое напряжение при изгибе МПа; [sF] = 500 МПа – для материала Сталь 45;
ym = 10 – коэффициент ширины зуба по модулю;
К = 1 – коэффициент нагрузки;
b = 0 – прямозубая передача;
КПF = 1 – коэффициент учитывающий повышение нагружающей способности;
Принимаем m=8 большего по СТ СЭВ 310-76.
Межосевое расстояние
Находим общее число зубьев
Принимаем число зубьев шестерни
Тогда число зубьев колеса Z2 = Z1 · u = 9 · 25 =225.
Делительный диаметр шестерни:
Делительный диаметр колеса:
d2 = 225 · 8 =1800 мм
Проверим данную передачу на изгиб по условию
Допускаемое напряжение:
Условие прочности на изгиб выполняются
Межосевое расстояние:
аm = (d1 + d2 ) 2 = (72 + 1800) 2 =936 мм.
Фактическое передаточное отношение механизма
uм.ф. = uр uзуб = 34·25 =850
Фактическая частота вращения крана
т.е. отклонение от заданной частоты вращения составляет 01 % что допустимо.
7 Расчёт червячного редуктора
Рассчитанное передаточное число редуктора Uр=34.
Выбираем для колеса материал БрА9Ж4 а для червяка – Сталь 40Х.
По рекомендации принимаем z1=1 m=5 q=16
Находим число зубьев червячного колеса:
Диаметры делительных окружностей:
Проверка выбранных параметров по контактным напряжениям
Условия прочности соблюдаются
Диаметр выходного вала червяка
Диаметр выходного вала червячного колеса
Берём время торможения равным времени пуска tт=tп =10 с. Тормозной момент на первом валу предварительно определим по формуле:
Выбираем по [1] тормоз ТT-160 имеющий тормозной момент при ПВ=100% - 100 Н·м масса 188 кг.
Уточняем тормозной момент с учётом момента инерции механизма поворота
где Iм – момент инерции муфты принимаем равным Iм = 003 кг×м2.
Выбранный тормоз регулируем на необходимый тормозной момент.
9 Проверка двигателя на нагрев
В пусковом режиме момент сил инерции на первом валу
Потребный среднепусковой момент без учёта дополнительного момента возникающего при прогибе колонны крана составляет: Н·м
Минимальный пусковой момент выбранного двигателя Н·м
Средний пусковой момент электродвигателя Н·м
Полученный средний пусковой момент оказывается больше потребного Тср.п=305 Н·м поэтому двигатель удовлетворяет условиям пуска.
Проверим электродвигатель на нагрев по методике ВНИИПТМаша [5]. Время рабочей операции при среднем угле поворота стрелы на 90° т.е. при 025 оборота.
Определим отношение времени пуска ко времени рабочей операции:
Эквивалентная по нагреву мощность
Рэкв = k40 · g · Pст.ф =075 · 155 · 01 = 012 кВт
где Рст.ф – фактическая мощность при установившемся движении определяемая для nкр.ф = 15 мин-1.
По графику [5] находим коэффициент g = 155.
кВт -необходимая мощность
кВт -эквивалентная мощность
кВт -номинальная мощность
Таким образом двигатель удовлетворяет условиям нагрева.
Расчёт металлоконструкции крана
Рисунок 11 - Колонна
Для расчета колонны определяем изгибающий момент в месте установки опорных роликов
Мизг = RH·h =45556 =2733 кН м
Диаметр колонны находим по формуле (пренебрегаем напряжением на сжатие):
где [s]и= 130 МПа – допускаемое напряжение для стали Ст 5 (1 МПа = =1Нмм2 ).
Принимаем диаметр колонны в рассматриваемом сечении равным 500 мм.
2. Проверка колонны на жёсткость
При проверке колонны на жесткость используем методику описанную в [1]. Принимаем колонну в виде усеченного конуса. Поэтому в верхней части колонны где устанавливаются подшипники упорный и радиальный наибольший диаметр Dк.в = 195мм.
Момент инерции сечения колонны в верхней части:
Момент инерции сечения колонны в нижней части:
Момент фиктивной нагрузки:
Прогиб конца колонны по методу Мора
Отношение прогиба к вылету крюка
Допускаемая величина относительного прогиба (010 015) 10-2. На основании полученного прогиба fкол = 17б7 мм можно не учитывать дополнительный момент сопротивления повороту крана под действием сил крена.
3 Расчёт опорной плиты крана
Опорные плиты используются для крепления колонн к фундаментам с помощью анкерных болтов. В центральное гнездо плиты с несколькими радиальными лапами имеющими на концах отверстия под крепёжные болты входит хвостовик колонны.
Для определения максимального усилия в болтах считаем что стрела расположена по оси Х-Х проходящей через центры двух болтов.
Рисунок 12 – Расчётная схема опорной плиты
Максимальная нагрузка на один болт от опрокидывающего момента:
где М=4555 кНм – изгибающий момент действующий на колонну
l1 l2 l3 – расстояние от оси у-у до соответствующего болта
i1 i2 in – количество болтов нагруженных соответствующим усилием
L1=085 m; L2=042 м; L3=08 м.
От действия вертикальных сил болты будут разгружаться. Величина разгружающей силы:
Расчётная нагрузка на болт:
Р=Р1-РV=3596-7.4=3522 кH
Затяжка болта должна быть такой чтобы при максимальном нагружении крана не произошло раскрытие стыка. Поэтому диаметр болта определяют исходя из двойной расчётной нагрузки:
Определяем диаметры болтов:
Принимаем фундаментные болты диаметром 48 мм. Болты диаметром менее 24 мм не применяются независимо от результатов расчёта.
Проверку на смятие фундамента проводят по условию:
где [p] = 1 2 мПа – напряжение смятия для бетона
FОП – площадь поверхности опорной плиты
Площадь данной опорной плиты 3460 см2 что больше чем расчётная.
Приборы безопасности
К управлению краном допускаются лица не моложе 18 лет имеющие соответствующее удостоверение и прошедшие медицинский осмотр для пригодности работы на кране.
Перед началом работы машинист обязан проверить техническое состояние основных механизмов и узлов крана (тормозов крюка канатов блоков металлоконструкции крана) и исправной работы приборов безопасности.
Эксплуатация электроталей и надзор за ними должны производится в соответствии с изданными Госгортехнадзором «Правилами устройства и безопасной эксплуатации грузоподъемных кранов».
Надзор за электроталями возлагается распоряжением администрации на определенное лицо технического персонала обладающее соответствующей квалификацией и опытом которое и является ответственным за исправное состояние электроталей и их безопасную эксплуатацию.
Напряжение в электросети не должно быть ниже действующих норм в противном случаи электроталь тормоз и магнитные пускатели будут работать ненормально.
Не допускается подъем грузов превышающих номинальную грузоподъемность а также превышение указанного в технической характеристике режима работы и эксплуатация электроталей в условиях не допускающих их применение.
При управлении электроталью рабочему следует находиться со стороны открытой части барабана.
Нельзя допускать такой подвески груза при которой получается недопустимое нагружение острия крюка. В таких случаях крюк может заметно разогнуться.
Подтаскивание грузов электроталью при косом натяжении канатов отрывание прикрепленных предметов а также производство с помощью электротали несвойственных для нее работ запрещается.
Категорически запрещается пользоваться шланговым проводом в качестве тяги для горизонтального перемещения электротали.
Правилами ГГТН а также стандартом СЭВ 725-77 на грузоподъёмных кранах с электрическим приводом предусмотрена установка концевых выключателей для автоматической остановки:
крана если его скорость может превышать 0533 мс (по стандарту СЭВ–05 мс);
механизма подъёма грузозахватного устройства перед подходом к упору.
При подъеме груза не следует доводить обойму крюка до конечного выключателя.
Конечный выключатель является аварийным ограничителем. Пользоваться им как постоянно действующим автоматическим остановом не разрешается.
Совершенно необходимо в начале каждой смены проверять исправность действия конечного выключателя.
Концевой выключатель механизма подъёма устанавливают так чтобы после остановки грузозахватного устройства зазор между ним и упором на тележке составлял не менее 200 мм. Для этой цели применяют выключатели типа КУ 703 имеющий двуплечий рычаг.
Смазка узлов и деталей крана
В зависимости от требований предъявляемых к смазочным материалам они делятся на смазочные материалы для : редукторов и зубчатых муфт открытых передач подшипников качения и скольжения реборд ходовых колес рельс и направляющих канатов.
Для редуктора применимы трансмиссионные масла. По ГОСТ 23652-79 – основными свойствами трансмиссионных масел являются: всесезонность длительность срока службы и высокая нагрузочная способность.
Для подшипников качения предпочтительны всесезонные смазки из числа обладающих хорошим антикоррозионным действием и длительным сроком службы.
Рельсы тележек смазывают в зависимости от температуры воздуха солидолами или графитной смазкой.
Реборды ходовых колес тали смазывают с помощью графитных стержней (ТУ 32ЦТ 558-74).
Пресс солидол - смазка для подшипников открытых передач направляющих.
Графитная смазка применяется для смазки рельс реборд ходовых колёс и канатов.
Основной целью данного курсового проекта было обучение основам конструирования сложной машины закрепление углубление и обобщение знаний приобретенных при изучении теории дисциплины “ Подъемно-транспортные машины и оборудование ”.
В данном курсовом проекте был спроектирован кран на колонне грузоподъемностью 32 т. Произведены расчеты механизмов крана подобраны двигатели редуктора а так же даны рекомендации по технике безопасности при работе с краном и условия смазки узлов. Проверочные расчёты показали что спроектированный кран отвечает всем требованиям стандартов и способен выполнять необходимые технологические операции.
Список использованных источников
Курсовое проектирование грузоподъёмных машин. Руденко Н.Ф. Александров М.П. и Лысяков А.Г. Изд. 3-е перераб. и доп. М.: Машиностроение 1971 464 с.
Справочник по кранам. Т. 2. Под ред. А.И. Дукельского. – Л.: Машиностроение 1973. – 472с.
Иванченко Ф.А. и др. Расчеты грузоподъемных и транспортирующих машин.-2изд. перераб. и доп.-Киев.: Вища школа 1978.-574 с.
Курсовое проектирование грузоподъёмных машин: Учеб. Пособие для студентов машиностр. вузов; Под ред. С.А. Казака.-М.:Высш. Шк. 1989. – 319 с.
Мостовые краны общего назначения. Парницкий А.Б. Шабашов А.П. и Лысяков А.Г. Изд. 4-е перераб. и доп. М.: Машиностроение 1971 с. 352.
Марон Ф.Л. Кузьмин А.В. Справочник по расчетам механизмов подъемно-транспортных машин. Минск "Вышэйш. школа" 1977. 272 с. с ил.