Электропогрузчик грузоподъемностью 1,25 т.




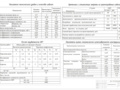

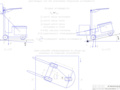
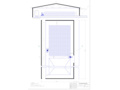
- Добавлен: 25.10.2022
- Размер: 2 MB
- Закачек: 0
Описание
Состав проекта
![]() |
![]() ![]() ![]() |
![]() ![]() ![]() |
![]() |
![]() ![]() ![]() ![]() |
![]() ![]() ![]() ![]() |
![]() ![]() ![]() ![]() |
![]() ![]() ![]() ![]() |
![]() ![]() ![]() ![]() |
![]() ![]() ![]() ![]() |
![]() ![]() ![]() ![]() |
![]() ![]() ![]() |
![]() ![]() |
![]() ![]() |
![]() ![]() |
Дополнительная информация
Записка без АПМ.doc
Современные поточные технологические и автоматизированные линии межцеховой и внутрицеховой транспорт погрузочно-разгрузочные операции требуют применения разнообразных типов подъемно-транспортных машин и механизмов обеспечивающих непрерывность и ритмичность производственных процессов. Именно поэтому подъемно-транспортное оборудование в настоящее время из вспомогательного превращается в один из решающих факторов производственного процесса определяющих возможности современного производства.
Насыщенность производства средствами механизации трудоемких и тяжелых работ уровень механизации технологического процесса определяют степень совершенства технологического процесса и производительность труда на предприятии.
В СНГ на погрузочно-разгрузочных транспортных и складских работах занято 18% всех промышленно-производственных рабочих. Наиболее сложной является проблема грузопереработки тарно-штучных грузов на выполнение которой занято более 23 всех рабочих осуществляющих перегрузочные операции 12 из которых выполняет их в условиях тяжелого физического труда.
Уровень комплексной механизации и автоматизации ПРТС работ в отраслях страны в значительной мере зависит от их оснащенности машинами напольного безрельсового транспорта (МНБТ) которые являются универсальными и наиболее массовыми машинами обеспечивающими высокую эффективность работ и высвобождающих большое количество подсобных рабочих занятых тяжелым физическим трудом.
О высокой эффективности применения МНБТ при перегрузочных и транспортных работах свидетельствуют общий парк и объемы производства этих машин.
Разработкой конструкций и производством занято более 250 фирм из них около 100 в Европе. Большинство фирм предлагает различные модели и типы МНБТ по исполнениям высот подъема взрывозащищенности типам двигателей (карбюраторные дизельные сжиженный газ дизель-электрические) видам трансмиссий (гидромеханические гидростатические механические) импульсный и контакторным системам управления электроприводом типам шин (массивные пневматические полу-пневматические суперэлластик) грузоподъемности видам грузозахватных приспособлений.
С увеличением объема пакетных перевозок эффективность использования МНБТ еще более возрастает. При пакетных перевозках производительность труда по сравнение с ручной поштучной погрузкой-выгрузкой увеличивается в 7-10 раз себестоимость обработки 1 т груза снижается в 6-10 раз простой вагонов уменьшается более чем в 2 раза а автомобилей — более чем в 6 раз.
Машины напольного безрельсового транспорта по сравнению с другими видами подъемно-транспортных средств более компактны и маневренны имеют меньшую массу и более высокие эксплуатационные показатели.
Эти машины мобильны и могут быть легко приспособлены к изменяющейся технологии перегрузочных и транспортных работ. Они могут работать везде где есть твердое покрытие а машины специальных типов — даже на строительных площадках и в условиях бездорожья. Путь следования машин может быть любым поэтому их можно использовать при различной технологии перегрузочных работ. Напольный транспорт не требует рельсовых путей токоподвода и легко взаимодействует с другими видами транспортных машин. При рациональной организации перегрузочного процесса не требуется вспомогательной рабочей силы — грузчиков такелажников и обеспечивается 100%-ная комплексная механизация погрузочно-разгрузочных и транспортных работ.
Во всех отраслях осуществляется последовательный переход от создания и внедрения отдельных машин оборудования приборов и технологических процессов к разработке производству и массовому использованию высокоэффективных систем особенно на транспортных и складских операциях. Успешно претворяется в жизнь программа ускоренного развития перегрузочных машин технического оснащения пунктов перегрузки и складов совершенствования технологии погрузочно-разгрузочных работ.
1 Цели и задачи проектирования
В данном дипломном проекте разработан электропогрузчик грузоподъемностью 125 т.
Электропогрузчик в передней части имеет грузоподъемный механизм состоящей из наружной неподвижной рамы шарнирно закрепленной в нижней части на шасси погрузчика и внутренней подвижной рамы имеющую возможность подниматься и опускаться за счет установленного гидроцилиндра по внутренней раме перемешается грузоподъемная каретка с установленными на ней вилами. Работа и управление обеспечивается с помощью гидравлической системы.
Основная часть разработок проекта направлена на определение усилий и параметров грузоподъемного оборудования.
Цели и задачи решаемые данным дипломным проектом направлены на повышение технико-экономических показателей электропогрузчика в целом путем реализации лучших решений и оптимизации расчетных параметров.
2 Выбор рациональной схемы машины
Машины напольного безрельсового транспорта (МНБТ) получили широкое распространение в промышленности на железнодорожном транспорте и в других отраслях для работы в крупнотоннажных контейнерах крытых вагонах автомобилях складах судах благодаря хорошей маневренности высоким эксплуатационным показателям
МНБТ относятся к погрузочно-разгрузочным машинам циклического действия и производят следующие операции: захват груза его подъем и опускание транспортирование освобождение груза с захвата. Некоторые операции могут совмещаться полностью или частично. Возможность совмещения операций — важный фактор повышения производительности перегрузочных работ зависящий от квалификации водителя и маневренности машины.
Захват тарно-штучных сыпучих грузов осуществляется погрузчиками без применения питателей или других дополнительных загрузочных устройств необходимых для работы машин непрерывного транспорта (конвейеров) и как правило без ручного труда стропальщиков и такелажников.
В отличие от рельсовых пневмоколесных гусеничных кранов погрузчики могут перемещаться с грузом на значительные расстояния и обслуживать большие складские и производственные площади. Возможность использования широкой номенклатуры быстро заменяемых грузозахватных приспособлений в сочетании с большой мобильностью автономностью привода (в большинстве случаев) и отсутствием привязки к ограниченному месту придает МНБТ свойство универсальности.
Машины в зависимости от типа силовой установки делятся на авто - и электропогрузчи. Тип силовой установки в большой степени определяет технические характеристики машин и области их применения. Из-за ограниченной энергоемкости аккумуляторных батарей электропогрузчики имеют невысокие скорости подъема и передвижения и предназначаются основном для работы на площадках с ровным асфальтовым или бетонным покрытием.
Автопогрузчики в сравнении с идентичными по грузоподъемности электропогрузчиками имеют повышенные скорости подъема в 2-25 и передвижения в 2-5 раз. Они предназначены для работы в более тяжелых дорожных условиях и имеют меньше ограничений в отношении проходимости. Сфера применения автопогрузчиков ограничивается вредными действиями выхлопных газов что практически не позволяет попользовать их в закрытых
плохо вентилируемых помещениях. Чтобы уменьшить этот недостаток ведутся большие исследовательские и конструкторские работы по использованию нейтрализаторов выхлопных газов способствующих уменьшению содержания вредных примесей в продуктах выхлопа и установках двигателей работающих на сжиженном газе. Для работы на автопогрузчиках требуется более высокая квалификация водителя и обслуживающего персонала так как они сложны в управлении и чаще требуют ремонта двигателя чем электропогрузчики.
Электропогрузчики — передвижные машины на колесном ходу оборудованные грузоподъемным устройством все механизмы которого приводятся в действие от электродвигателя получающего энергию от аккумуляторной батареи. Они предназначены для выполнения погрузочно-разгрузочных работ в железнодорожных вагонах контейнерах автофургонах морских и речных судах применяются для штабелирования тарно-штучных грузов в крытых складах а также для внутрицеховой транспортировки и обслуживания станочных и сборочных линий комплектовочных складов и др.
Электропогрузчики могут работать в помещениях или на открытых площадках при температуре от —40 до + 40° С и высоте над уровнем моря не более 1200 м.
У электропогрузчиков общего назначения грузоподъемный механизм расположен впереди машины вне опорного контура и предназначен для перемещения груза в вертикальной плоскости. Для удобства захвата транспортировки и укладки груза рама грузоподъемника при помощи механизма наклона отклоняется вперед на 3° и назад на 10°.
По конструкции рамы грузоподъемники делятся на простые (однорамные) телескопические (двухрамные) и двойные телескопические (трехрамные).
Конструкция грузоподъемника дает возможность устанавливать на нем различные сменные грузозахватные устройства что значительно расширяет область применения электропогрузчиков делает их универсальными. Однако следует учитывать что грузоподъемность и устойчивость универсальных электропогрузчиков снижается с удалением центра тяжести массы груза от оси передних колес. Для обеспечения продольной устойчивости сзади погрузчика устанавливается противовес.
Маневренные качества электропогрузчиков определяющие область их применения зависят от многих факторов. Наиболее важные из них — размеры машины и минимальный радиус поворота (чертеж ДП 883406.01.00.000.СБ)
На маневренные качества влияет и принципиальная схема компоновки узлов погрузчика особенно конструкция ходовой части. При большом многообразии ее конструктивных решений можно выделить следующие схемы:
трехопорные — ходовая часть опирается на грунт в трех точках. Заднее колесо может быть и ведущим и управляемым однако чаще ведущими служат передние колеса с индивидуальным приводом;
четырехопорные — ходовая часть опирается на грунт (дорогу) в четырех точках. Передние колеса ведущие а задние управляемые.
Каждая из этих схем обладает своими достоинствами и недостатками. Трехопорные схемы обеспечивают достаточное сцепление ведущих колес с покрытием пути и позволяют получить более высокую маневренность но несколько снижают поперечную устойчивость машины по сравнению с четырехопорными.
Трехопорные электропогрузчики сочетают высокую маневренность и малую собственную массу. Это позволяет применять их при загрузке крытых железнодорожных вагонов контейнеров автомашин и для работы в стесненных условиях складов и цехов промышленных предприятий.
А импульсные схемы управления тяговыми двигателями улучшают ходовые качества электропогрузчиков увеличивают величину и длину преодолеваемых уклонов и способствуют сохранению энергоемкости аккумуляторной батареи.
3.1. Характеристика объекта разработки
Объектом разработки является грузоподъемный механизм применяемый в электро и автопогрузчиках. Грузоподъемный механизм предназначен для комплектования электро и автопогрузчиков грузоподъемностью 125 т которые применяются на промышленных предприятиях складах базах где необходимо выполнять погрузочно-разгрузочные работы в стесненных условиях.
Механизм подъема содержит внутреннюю и наружную раму цилиндры наклона грузоподъемника и подъема внутренней рамы каретку и вилы .
Механизм подъема должен обеспечить подъем груза на определенную высоту.
3.2. Регламент поиска при исследовании на патентную чистоту
Регламент поиска при исследовании механизма подъема груза на патентную чистоту по Российской Федерации
Источники информации
Страны и классификационные
местонахождение источника
индексы предмета поиска
Грузоподъёмник электропогрузчика
Бюллетень изобретения
3.3. Отчет о патентном поиске
Поиск проведен по следующим материалам:
Классификационные индексы предмета поиска
№ авторских свидетельств
А.с. 2297300-2297400
А.с. 2005000-92006000
А.с.№2297383Предложение относится к погрузочно-транспортной технике и может быть использовано в авто- и электропогрузчиках.
Изобретение обеспечивает достаточную грузоподъемность и высоту подъема. Недостатком является ее недостаточная надежность и сложность и трудоемкость изготовления
А.с.№92005055Подъемное устройство относится к подъемно-транспортному оборудованию и может быть использовано в авто- электропогрузчиках штабелерах и др. позволяет снизить энергоемкость механизма подъема.
Механизм отличается сложностью конструкции а так же не обеспечивает требуемой надежность при эксплуатации
3.5. Библиографический перечень отобранной
в процессе поиска информации
Перечень отобранной в процессе поиска информации
№ авторского свидетельства
Грузоподъёмник погрузчика
3.6 Аннотация отобранной в процессе поиска информации
А.с. №2297383Использование: предложение относится к погрузочно-транспортной технике и может быть использовано в авто- и электропогрузчиках. Грузоподъемник содержит неподвижную и подвижную секции (НС и ПС) грузовую каретку с грузозахватным приспособлением гибкий тяговый элемент (например цепь) гидроцилиндр подъема ограничитель перемещения цепи. ПС соединена с НС с возможностью своего перемещения вверх каретка соединена с ПС с возможностью своего перемещения вверх первый второй и третий шкивы размещены на поршне гидроцилиндра ПС и НС соответственно один конец цепи прикреплен к грузовой каретке и далее последовательно огибает сверху второй снизу третий и сверху первый шкивы второй конец цепи прикреплен к ПС. Ограничитель перемещения гибкого тягового элемента выполнен с возможностью блокирования последнего в любых или некоторых фиксированных положениях. Изобретение обеспечивает исключение потери высоты подъема каретки в помещениях.
А.с. №92005055Подъемное устройство относится к подъемно-транспортному оборудованию и может быть использовано в авто- электропогрузчиках штабелерах и др. позволяет снизить энергоемкость механизма подъема. Подъемное устройство содержит неподвижную и подвижную рамы гидроцилиндр грузозахватный орган противовес. Противовес установлен подвижно относительно погрузчика и соединен с подвижной рамой и грузозахватным органом.
4 Техническая характеристика
Грузоподъемность 125 т.
Высота подъема груза 2 м.
Скорость подъема вил:
Скорость опускания вил:
Наибольшая скорость передвижения:
Дорожный просвет 100 мм.
Внешний радиус поворота 1340 мм.
Наименьшая ширина проездов под углом 1750 мм.
5 Описание конструкции разрабатываемого электропогрузчика
У электропогрузчиков повышенной маневренности (рис. 1.1) раздельный привод передних колес. Узел каждого из ведущих колес состоит из электродвигателя 13 двухступенчатого цилиндрического редуктора 11и массивной бандажной шины 9. Корпус редуктора прикреплен болтами к щекам корпуса погрузчика. Заднее управляемое колесо 3 состоит из собственно колеса на массивной шине свободно сидящего на оси и шарикового поворотного круга. Оно может поворачиваться на 90° в обе стороны при этом центр поворота находится в точке пересечения оси передних колес с продольной осью погрузчика т. е. радиус поворота минимально возможный.
Рис. 1.1 Общий вид электропогрузчика:
— аккумуляторная батарея; 2 — корпус; 3 — колесо управляемое; 4 — сигнал звуковой; 5 — привод тормоза; 6 — вал шарнирный; 7—грузоподъемник; 8 — панель контакторная; 9 — массивная шина; 10 — контроллер; 11—редуктор; 12 — шкив тормозной; 13 — электродвигатель передвижения; 14 — бак масляный; 15 — сопротивление пусковое; 16 — шкворень; 17 — крышка; 18 — противовес; 19 —насос; 20—электродвигатель насоса; 21 — цилиндр наклона; 22 — редуктор одноступенчатый цилиндрический; 23 — маслоуказатель.
Рулевое управление состоит из шарнирного вала 6 одноступенчатого цилиндрического редуктора 22 и цепной передачи. Погрузчик оборудован механическим ножным тормозом. Тормозные шкивы 12 расположены на ведущих валах редукторов передвижения 11. Для торможения погрузчика на стоянке служит тормоз 5.
На погрузчике можно устанавливать грузоподъемники двухрамной конструкции с высотой подъема 20 и 30 м. Последние — в двух исполнениях с высотой подъема вил на 200 и 1300 мм без увеличения габаритной высоты погрузчика. Основные узлы грузоподъемника 7 — телескопическая рама каретка цилиндры подъема и наклона. На каретку грузоподъемника навешиваются сменные грузозахватные устройства.
Гидропривод погрузчика состоит из электродвигателя 20 с шестеренчатым насосом 19 масляного бака 14 гидрораспределителя арматуры. Гидрораспределитель управляет цилиндрами подъема наклона и навесных грузозахватных приспособлений. Электроаппаратура управления смонтирована на панели 8 и связана с аккумуляторной батареей силовым штепсельным разъемом. Приборы управления собраны на панели расположенной под рулевым колесом. Для управления скоростью передвижения предназначен контроллер 10 с приводом от ножной педали. Устойчивость погрузчика обеспечивают аккумуляторная батарея 1 расположенная в задней части корпуса и противовес 18.
Корпус погрузчика выполнен в виде сварной рамы с двумя бортами днищем поперечными продольными связями и другими элементами предназначенными для крепления узлов и деталей.
Сиденье установлено на крышке аккумуляторного ящика. Конструкция сиденья позволяет регулировать его положение в продольном направлении и угол наклона спинки. Оператор и механизмы сверху защищены предохранительной решеткой от возможного падения поднимаемого груза в процессе штабелирования.
Электроаппаратура управления смонтирована на отдельной панели в задней части машины и связана с батареей силовым штепсельным разъемом.
Электрооборудование погрузчика может быть выполнено в контакторном или импульсном варианте. Импульсный вариант дает возможность бесступенчато регулировать скорость вращения электродвигателей передвижения от нуля до максимальной.
Кинематическая схема всех погрузчиков одинаковая (рис. 1.2) и включает следующие группы механизмов: корпус 3; два колеса ведущих 2; колесо управляемое 4; рулевое управление 1; тормозное устройство 5.
Рис.1.2 Кинематическая схема электропогрузчика
КОСТРУКТОРСКИЙ РАСЧЕТ
1 Проект склада штучных грузов для разрабатываемого электропогрузчика
Определим количество средств механизации погрузочно-разгрузочных работ требуемых для перерабатывания однотипного пакетного груза на складе
по прибытию =600000 тонн
по отправлению =700000 тонн.
Масса пакета qп =1250 кг.
Объем одного пакета Vп =(Д×Ш×В)=12×08×12=1152 м3.
Фактическая загрузка автомобиля qа=3т.
1.1 Расчетный суточный поток
где–годовой грузопоток по прибытию или по отправлению т;
Кн – коэффициент неравномерности прибытия или отправления грузаКн=11.
По отправлению груза:
Тогда суточный грузопоток в пакетах составляет:
где qп масса пакета кг.
1.2 Необходимое число вагонов
где qв – средняя загрузка вагона.
где Vв – внутренний объем крытого вагона м3;
qп – масса одного пакета т;
kу – коэффициент учитывающий плотность укладки kу=085-09;
Vп – объем одного пакета м3.
Для перевозки тарно-штучных грузов принимаем крытый четырехосный вагон модель 11-066 тип 264. Грузоподъемность 63 т Vв=120м3.
В вагоне умещается qв= 51 пакет.
В каждом вагоне размещаются пакеты с установкой их в два яруса. Высота пакета hП = 1200 мм. ([5] табл. 1.2).
1.3 Количество автотранспорта
где Тц – продолжительность транспортного цикла автомобиля с;
где а – дальность перевозки км (для внутригородских поставок а=25 км);
Т – средняя техническая скорость автомобиля кмч (Т=35 кмч);
– коэффициент пробега автомашины =09;
Тпр – время простоя под грузовыми операциями.
qа – фактическая загрузка автомобиля qа=5т;
Т – количество рабочих часов автомобиля в сутки Т=12 часов;
kt=07 – коэффициент использования автомобиля по времени.
1.4 Расчет параметров склада
Определение числа вагонов в одной подаче
где Z – число подач вагонов на грузовой пункт за сутки Z=4.
Определение длины фронта подачи вагонов
Lф.п.=Nв.·в+аm (2.8)
где в – длина вагона по автосцепке в=1473 м;
аm – удлинение фронта подачи вагонов для выполнения маневровых работ аm=2 м.
Lф.п=28·1473+2=41444 м
Определение длины фронта погрузки-выгрузки
где Zс – число смен вагонов на грузовом фронте Zс=1.
Определение вместимости склада
где kп – коэффициент непосредственной перегрузки kп=04;
tхр – время хранения по прибытию (tхр=3сут.) и отправлению (tхр=15сут);
k1 – коэффициент сгущения подач k1=13.
V=[(1-04)·18082·3+(1-04)·210958·15]·13=669939 т
Определение вместимости элементарной площадки.
Груз хранится на асфальтобетонной платформе. Для размещения груза применяем штабельный вид хранения. Пакеты размещены в два яруса. Пакеты ставятся длинной стороной (1200 мм.) вдоль штабеля в два ряда.
где Z Zb Zh – количество пакетов в элементарной площадке по длине ширине и высоте.
где Вскл – ширина склада принимаем 30000мм;
в2 – место под ж. д. путь в2=(2850+1920)мм;
Вш– расстояние от края рампы до штабеля Вш=3000мм;
впр– ширина проезда впр=800мм.
где вуз=2000мм – расстояние между штабелями.
где Нпод– высота подъема погрузчика Нпод=3000мм;
hп– высота пакетаhп=1350мм.
Определение общего количества площадок на складе.
Определение длины склада.
Δ l– величина запаса склада Δ l=52м.
Принимаем длину склада исходя из условия:
Определение полезной площади элементарной площадки.
где f - полезная площадь занимаемая одним пакетом.
Определяем полную площадь элементарной площадки.
Полная площадь склада.
Все линейные размеры склада сведем в таблицу (таблица 2.1).
Линейные размеры склада
Наименование размера
Высота рампы для ж.д. вагонов .
Ширина погрузочно-разгрузочной платформы для обслуживания ж.д. подвижного состава и автомобилей.
Расстояние от края платформы до оси ж.д. пути.
Расстояние от оси ж. д. пути до стены склада.
Ворота для пропуска ж. д. состава
Расстояние между дверьми для автотранспорта
Размеры раздвижных дверей для автотранспорта
Высота грузовой платформы для автотранспорта над уровнем проезжей части
Расстояние для погрузочно-разгрузочных операций погрузчика между штабелями
Количество штабелей.
1.5 Выбор типа и расчет количества погрузочно-разгрузочных машин
Технические характеристики электропогрузчика грузоподъемностью 125 т даны в пункте 1.4
Техническая производительность машин используемых при переработке тарно-штучных грузов находиться по формуле:
где - грузоподъемность машины т;
-продолжительность времени цикла с.
Для погрузчика время цикла:
где -время затрачиваемое погрузчиком на продольные и поперечные передвижения по складу с грузом и без груза с;
- время затрачиваемое на подъем каретки погрузчика с грузом и без груза с;
-время затрачиваемое на опускание каретки с грузом и без груза с;
-время затрачиваемое на повороты погрузчика c;
-время затрачиваемое на вспомогательные операции c.
где - длина рабочего плеча м;
v- скорость движения погрузчика мс;
-ускорение погрузчика мс2.
Средняя высота подъема:
где: H-высота подъема груза погрузчиком м.
1.6Эксплуатационная и сменная производительность
Эксплуатационная производительность погрузчика:
где -коэффициент использования по времени.
Сменная производительность:
Объем механизированной переработки груза:
где-время нахождения машины в ремонте в течение года =20дней.
2 Расчет гидравлической системы
С помощью гидравлической системы осуществляется подъем вил наклон грузоподъемника рабочие движения навесных грузозахватных приспособлений. Гидравлическая система должна удовлетворять следующим требованиям:
создавать рабочее давление достаточное для осуществления всех рабочих операций с заданными скоростями;
производить регулируемую подачу и распределение потока рабочей жидкости;
обеспечивать предохранение рабочих органов от поломок при их перегрузке осуществлять очистку рабочей жидкости от загрязнителей.
Общая принципиальная схема гидравлической системы машин напольного транспорта показана на (рис. 2.1).
Гидравлическая схема включает в себя масляный бак 1 насос 2 гидрораспределитель 3 цилиндры подъема 4 и наклона 6 трубопроводы. Для регулировки расхода и давления рабочей жидкости в гидросистему включены предохранительные клапаны 8 и дроссели 5.
Гидросистему приводят в действие рычагами гидрораспределителя 3 который электрически сблокирован с электродвигателем подъема. При включении гидросистемы на подъем или наклон одновременно включается электродвигатель механизма подъема который приводя в действие насос 2 создает в магистрали высокого давления необходимое давление рабочей жидкости. Гидрораспределитель 3 оборудован редукционным клапаном отрегулированным на давление10+1 МПа. Колпачок которым он закрыт опломбирован. Доступ к клапану возможен через лючок на передней стенке корпуса электропогрузчика.
Опускается грузоподъемник под действием груза или только каретки с вилами без включения электродвигателя подъема. Рабочая жидкость из цилиндров по трубопроводам поступает в полость низкого давления гидрораспределителя откуда по шлангу сливается в бак через масляный фильтр 9. Контролируют уровень масла в баке сапуном на щупе которого нанесены две риски соответствующие верхнему и нижнему пределам уровня жидкости при опущенных вилах и грузоподъемнике наклоненном назад. Нижний конец щупа загнут что позволяет легко вынуть сетчатый фильтр из горловины бака.
Рис. 2.1 Гидравлическая схема
К цилиндру подъема рабочая жидкость подводится через дроссель постоянного расхода 5. Последний обеспечивает опускание вил электропогрузчика с небольшими отклонениями скорости от номинальной величины независимо от нагрузки на них. Дроссель постоянного расхода обеспечивает опускание груза со скоростью близкой к рабочей при аварийном обрыве рукава подводящего рабочую жидкость к цилиндру подъема.
В трубопроводе к цилиндрам наклона установлен дроссель для уменьшения скорости наклона и обеспечения плавной работы.
Цилиндр подъема в сборе одностороннего действия плунжерного типа (рис. 2.2) состоит из собственно цилиндра 11 плунжера 1 и направляющей — корпуса уплотнения 7 и втулки 10. Плунжер уплотнен шевронными манжетами 6. Для выпуска воздуха из гидросистемы в цилиндре предусмотрено отверстие закрываемое пробкой 9. От попадания грязи он защищен грязесъемником 2. Рабочая жидкость подводится к цилиндру через отверстие расположенное в его дне. В собранном грузоподъемнике цилиндр подъема нижним фланцем опирается на шаровую пяту обеспечивающую его самоустановку в нужное положение при работе погрузчика.
Рис. 2.2 Цилиндр подъема:
- плунжер; 2 - грязесъемник; 3 - гайка; 4 - кольцо; 5 - кольцо нажимное; 6 - манжета; 7 - корпус уплотнения; 8 - кольцо уплотнительное; 9 - пробка; 10 -втулка; 11- цилиндр
Цилиндр наклона (рис. 2.3) поршневого типа двустороннего действия. Корпус 15 его крепится к корпусу электропогрузчика а головка 1 штока - к кронштейну наружной рамы грузоподъемника посредством шарнирных подшипников 2. Поршень 13 уплотнен У-образными 11 а шток 17 — шевронными резиновыми манжетами 6.
Рис. 2.3 Цилиндр наклона:
-головка; 2-подшипник; 3-грязесъемник; 4 - крышка; 5 6 7 11-манжеты; 8 12 16-уплотнительные кольца; 9 15-корпуса; 10-втулка; 13-поршень; 14-корпус уплотнения; 17-шток; 18-гайка
2.2Выбор площади цилиндра подъема
Gпл – вес плунжера Gпл=44 кг;
Gв – вес вил Gв=78 кг;
Gк – вес каретки Gк=73 кг;
Gвн.р.– вес внутренней рамыGвн.р.=90 кг;
К=2 – кратность полиспаста грузоподъемника;
- допускаемое давление в цилиндре подъема ;
- допускаемое давление нагнетательного насоса ;
-давление настройки предохранительного клапана распределителя;
Δр– потери давления в линии нагнетания Δр=06 мПа;
гр– к.п.д. грузоподъемника гр=085;
мех.ц. к.п.д. учитывающий трение уплотнителей мех.ц.=097.
Принимаем диаметр цилиндра: 60 мм
2.3 Выбор типа насоса
Потребная удельная подача насоса:
где Q – потребная производительность насоса необходимая для получения скорости подъема ммин;
n– номинальная скорость вращения вала насоса n=2500 обмин;
v– объемный к.п.д. насоса v=095.
где v– скорость подъема v=11 ммин;
пр– объемный к.п.д. привода подъема пр.=099.
Принимаем насос С14Х имеющий удельную подачу q=53 см3об.
2.4 Определение скоростей подъема каретки
) Скорость подъема каретки с грузом.
Давление в цилиндре подъема:
Момент на валу электродвигателя соответствующий данной нагрузке:
где – к.п.д. учитывающий потери давления в линии =093;
– механический к.п.д. насоса =088.
Производительность насоса:
где n – по характеристике электродвигателяЗДН-32 обмин.
Скорость подъема каретки с грузом:
) Скорость подъема каретки без груза.
где мех.ц – к.п.д. механический цилиндра в режиме работы без груза мех.ц=085.
Момент на валу электродвигателя:
где – к.п.д. учитывающий потери давления в линии в режиме работы без груза=08;
– механический к.п.д. насоса в режиме работы без груза=085.
Скорость вращения вала при данном моменте n=3500обмин (определяется по характеристике электродвигателя).
Скорость подъема каретки без груза:
2.5 Расчет ёмкости масляного бака
Количество тепла выделяемого в результате нагрева рабочей жидкости за смену:
где - средне давление развиваемое насосом под нагрузкой=15мПа;
- средне давление развиваемое насосом без нагрузки =34 мПа;
- средний расход жидкости при работе под нагрузкой =16 лмин;
- средний расход жидкости при работе без нагрузки=19 лмин;
общ. -общий к.п.д. насоса общ.=08.
Среднее количество тепла выделяемого в результате нагрева рабочей жидкости за час.
ΔТ=30º - разность температур рабочей жидкости и окружающей среды.
Геометрический объем бака
Принимаем объем 16 л.
3 Тяговый расчет электропогрузчика
Тяговые качества являются важной характеристикой электропогрузчика. Они показывают какую силу тяги можно развить на ведущих колесах машины при движении на дорогах с различным покрытием при меняющейся весовой нагрузке различных скоростях движения и величинах преодолеваемых уклонов. Чем больше сила тяги машины тем выше ее проходимость. Поэтому для обеспечения требуемой эксплуатационной характеристики электропогрузчика при его проектировании необходим тяговый расчет при котором производится подбор мощности двигателя определения момента на валу ведущих колес и расчет потребного тягового усилия.
Грамотное использование тяговых способностей погрузчиков позволяет повысить производительность последних и определить рациональные сферы их эксплуатации в различных условиях.
Для определения тяговых качеств проектируемого электропогрузчика помимо предусмотренных техническим заданием веса машины с грузом и без груза величины преодолеваемого уклона и скорости передвижения должны быть известны характеристики выбранного двигателя.
3.1 Расчет тягового усилия
Потребное тяговое усилие при разгоне погрузчика при движении на подъем с углом наклона пути α составит:
гдеG-вес погрузчика G=2385кг;
Q-вес груза Q=1250кг;
- коэффициент сопротивления движения =0016;
α- угол наклона пути α =10о;
-ускорение погрузчика =03мс2.
3.2 Расчет момента на валу ведущих колес
Момент на валу ведущих колес диаметром Dk.
где Dk-диаметр ведущих колес Dk=04м.
3.3 Определение мощности двигателя передвижения
Мощность двигателя для передвижения погрузчика определяется по формуле:
гдеV - скорость передвижения погрузчика V=28мс;
- к.п.д. привода =098.
На рассчитываем погрузчике установлены два двигателя с мощностью N1=N2=15кВт. Суммарная мощность двух двигателей N1+N2=3кВт эта мощность больше расчетной значит её будет достаточно для передвижения электропогрузчика.
4 Электрооборудование погрузчика
4.1Элементы электрооборудования
Электрооборудование включает в себя элементы представленные на рис. 2.4.
Рис. 2.4. Электрооборудование:
11 13 - микропереключатели; 2 - звуковой сигнал; 3 - выключатель; 4 - вольтметр; 5 - реверсивный переключатель; 6 -выключатель; 7 - панель управления; 8 18 - штепсельные соединения; 9 - педаль контроллера; 10 - контроллер; 12 19- электродвигатели; 14 - панель; 15 - сопротивления; 16 - аккумулятор; 17 - аккумуляторный ящик.
Аккумуляторная батарея состоит из 34 аккумуляторов установленных в металлический сварной ящик. Плотная установка аккумуляторов в ящике достигается клиньями и прокладками из листового полиэтилена. В днище имеются желоба для сбора электролита в случае выплескивания его из аккумуляторов. Из желобов электролит можно слить через сливные пробки. Аккумуляторы соединены последовательно при помощи стальных шин. Батарея имеет три вывода: два силовых и один для питания цепи сигнализации.
Техническая характеристика аккумуляторной батареи приведена.
Грузоподъемность электропогрузчика кг
Для электропогрузчиков грузоподъемностью 1250 кг аккумуляторную батарею заряжают не снимая с электропогрузчика на зарядном устройстве типа УЗА1-80-42У2.
Электродвигатели механизма передвижения ЗДТ31 пли ЗДТ32 постоянного тока четырехполюсные закрытого исполнения. Крепление фланцевое.
Техническая характеристика электродвигателей механизма передвижения
Частота вращения обмин
Электродвигатели гидронасоса ЗДН31 или ЗДН32 постоянного тока четырехполюсные закрытого исполнения.
Техническая характеристика электродвигателей гидронасоса
Частота вращения обмин .
Выключатели путевые 6 контактные мгновенного действия типа ВПК3112 предназначены для коммутации электрических цепей управления под действием рулевого механизма:
при повороте управляемого колеса на угол 30° двигатели передвижения переключаются с параллельного соединения на последовательное;
при повороте колеса на угол 50° двигатель колеса идущего по внутренней кривой отключается.
Микропереключатели. В электрической схеме погрузчика имеется несколько микропереключателей 11 13 использующихся для отключения двигателя передвижения при нажатии на тормозную педаль.. Номинальное напряжение 24В максимальный ток 48 А.
Реверсивный переключатель 5 изменяет направление движения электропогрузчика. Он изготовлен на основе переключателя ПКУ-3. У его рукоятки три фиксированных положения: одно — «Выключено» (среднее) и два — «Включено» («Вперед» и «Назад»). Номинальное напряжение 40 В максимальный ток 2 А.
Вольтметр щитовой ударостойкий установлен на панели приборов управления для контроля за напряжением аккумуляторной батареи.
4.2Описание работы электрической схемы электропогрузчика
Принципиальная электрическая схема электропогрузчика изображена (на чертеже ДП 883406.04.00.000) при нулевом положении контроллера и разомкнутом выключателе управления В1. Элементы цепей электрооборудования приведены в табл. 2.5.
Описание схемы дано в положении реверсивного переключателя «Вперед» и при повороте управляемого колеса.
Элементы цепи электрооборудования
Батарея аккумуляторная
Двигатель передвижения
Предохранитель силовой цепи
Предохранитель цепей
управления и сигнализации
Включатель управления
Схема управления включает цепи: катушки линейного контактора К1 включающего и отключающего электродвигатели M
контакторов К2 К3 К8 К9 реверсирующих электродвигатели M
катушки контактора К4 питающего на позиции 4—5 контроллер через контакты Кр4 и на позиции 6—7 через контакт Кр6;
катушек контакторов K5 К7 параллельно соединяющих электродвигатели M
катушки контактора К6 пускающего электродвигатель подъема М3.
Схема работает при углах поворота управляемого колеса электропогрузчика от 30 до 50°. При повороте колеса в любую сторону на угол больший 30° размыкаются контакты переключателей 2ВЗ и 2В4 и прерывается цепь питания контакторов К5 К7.
Если контроллер находится на позициях 5—6 и 6—7 то электродвигатели Ml и М2 переключаются с параллельного на последовательное соединение. Это обеспечивает электрический дифференциал.
При дальнейшем повороте управляемого колеса в зависимости от направления переключаются контакты переключателя В3 или В4 и получает питание катушка контактора К5 или К7 и на любой позиции контроллера работает только один из двигателей Ml или М2 последовательно соединенный с пусковым сопротивлением К1 или К2.
Работа электродвигателей передвижения Ml и М2. Скорость электропогрузчиков регулируют изменением напряжения подводимого к электродвигателям (рис. 2.5) переключением их с последовательного соединения на параллельное и выведением пусковых сопротивлений R1 и R2.
Коммутация электрических аппаратов силовой схемы двигателей передвижения происходит в соответствии с позициями контроллера. На позиции контроллера 0—1 не получает питание ни один контактор. На позиции 1—2 замыкаются силовые контакты реверсивных контакторов К8 К2 (или К9 К3) в зависимости от положения переключателя В6.
Рис. 2.5. Последовательность коммутации аппаратов
На позиции 2—3—4 замкнут силовой контакт контактора К1 введены пусковые сопротивления1 и 2 электродвигатели M1 и М2 включены последовательно (рис. 2.5 а). Эта позиция используется в качестве
На позиции 4—5 замкнуты силовые контакты контактора К4 электродвигатели M1 и М2 соединены последовательно сопротивления 1 и 2 зашунтированы (рис. 2.5 б).
На позиции 5—6 замкнуты силовые контакты контакторов К5 и К7 и разомкнут силовой контакт контактора К4. Электродвигатели M1 и М2 соединены параллельно пусковые сопротивления 1 и 2 введены в работу (рис. 2.5 в).
На позиции 6—7 включены силовые контакты контактора К4 пусковые сопротивления 1 и 2 выведены из работы.
Позиция соответствует максимальной скорости передвижения электропогрузчика (рис. 2.5 г).
Реверсирование электродвигателей M1 и М2 обеспечивают силовые контакты контакторов К2 КЗ К8 К9 и переключатель В6.
Работа электродвигателя насоса М3. Пуск электродвигателя безреостатный обеспечивает его контактор К6 включают и отключают который выключателями органов управления гидропривода. Защищают силовые цепи предохранители Пр1.
Защита. От токов короткого замыкания и токов длительных перегрузок силовые цепи защищены предохранителями Пр1 и Пр2 цепи управления — предохранителем Пр3 цепи сигнализации — предохранителем Пр4
1 Расчет грузоподъемного механизма
Грузоподъемный механизм предназначен для вертикального перемещения груза. Для удобства взятия и укладки груза а также для устойчивости груза при его транспортировке грузоподъемник имеет наклон вперед и назад из вертикально положения. Грузоподъемный механизм должен обеспечивать:
принудительную остановку вил в крайнем верхнем положении грузоподъемника и в крайних положениях при наклоне вперед и назад грузоподъемника;
прочность элементов грузоподъемника при поднятии на максимальную высоту груза массой равной 133Q (Q — номинальная грузоподъемность);
подъем на высоту не более 03-05 м груза массой 12Q;
скорость опускания груза при обрыве трубопровода не более 06 мс при температуре масла 40±10°С;
самовольное опускание груза со скоростью не более 10 мм за 10 минут при температуре масла от 25 до 40°С;
достаточную видимость водителю при движении и взятии груза.
Грузоподъемный механизм включает: вилы каретку для крепления вил неподвижную раму (наружную) гидроцилиндр цепи балансир с роликами для цепей (рис. 3.1). Гидроцилиндр через сферический подшипник крепится к нижнему основанию наружной рамы. На штоке гидроцилиндра закреплен балансир с двумя роликами для направления движения цепей. Каретка имеет четыре ролика для перемещения ее по направляющим грузоподъемника и восприятия нагрузок действующих перпендикулярно плоскости рамы и четыре ролика для восприятия нагрузок действующих в плоскости рамы. При подаче масла в полость гидроцилиндра начинает движение шток который действуя на балансир через цепи приводит в движение каретку. Скорость движения каретки вдвое быстрее скорости движения штока.
Максимальная высота подъема вил определяется расстоянием от уровня пола до нижней поверхности вил поднятых на максимальную высоту при вертикальном грузоподъемнике. Строительная высота грузоподъемника определяется расстоянием от уровня пола до верхней точки вертикально установленного грузоподъемника при полностью опущенных вилах.
Большинство конструкций грузоподъемников обеспечивают подъем вил до транспортного положения (на 300 мм) или на высоту 1200-1300 мм без увеличения строительной высоты грузоподъемника.
В зависимости от количества рам и высоты подъема вил без увеличения строительной высоты грузоподъемника различают следующие типы грузоподъемников:
а) однорамный без свободной высоты подъема вил;
б) двухрамный без свободной и со свободной высотой подъема вил;
в) трехрамный без свободной и со свободной высотой подъема вил.
В проектируемом погрузчике применяем двухрамный грузоподъемник с высотой подъема груза 3 м.
Рис. 3.1 Конструкция двухрамного грузоподъемника:
- цилиндр наклона; 2-цилиндр подъема; 3-тяга; 4-каток; 5-ролик боковой; 6-ролик; 7-звездочка; 8-внутренняя рама; 9- наружная рама; 10-балансир; 11-каретка
Конструкция грузоподъемника для высот 20-28 м двухрамного показана на рис.3.1. У двухрамного грузоподъемника наружная рама 9 неподвижная а внутренняя 8 подвижная цилиндр подъема 2 одностороннего действия и две цепи каретки. Внутренняя рама перемещается по роликам 5 и 6 вдоль наружной.Эксцентриковая ось боковых роликов 5 позволяет регулировать боковые зазоры между роликами и рамами. Натяжение цепей регулируют тяги 3 разницу в натяжении компенсирует балансир 10 закрепленный на оси каретки 11.
Двухрамные грузоподъемники крепят шарнирно на кожухах полуосей ведущего моста. К корпусу электропогрузчика они присоединены цилиндрами наклона.
Каретка и рамы грузоподъемников перемещаются на катках по направляющим грузоподъемников. В качестве направляющих используют швеллерный двутавровый и другие профили. Катки могут быть установлены как на наружной раме так и на внутренней подвижной раме. Сочетание профилей для внутренней и наружной рам должно иметь минимальное поперечное сечение для обеспечения лучшей видимости водителю.
1.2 Расчет сил действующих на рамы грузоподъемника
Рис. 3.2 Расчетная схема грузоподъемника.
)Расчет сил приложенных к грузоподъемнику.
где- масса поднимаемого груза =1250кг;
-масса каретки =193кг.
)Определение усилий действующих в плоскости рам
)Определение усилий действующих перпендикулярно плоскости рам:
1.3 Расчет наружной рамы
Рис. 3.3 Расчетная схема наружной рамы
Рассчитываемая рама имеет две стойки показанных на (рис. 3.3) цифрой 1 и три связи показанные номерами 23 и 4.
Рама рассчитывается смешанным методом сил и деформаций. По силам на рис.3.3 производим построение эпюр изгибающих моментов от сил действующих в плоскости рамы(рис. 3.4)
Рис. 3.4Суммарная эпюра изгибающих моментов от сил действующих в плоскости рамы.
) Расчет наружной рамы от сил действующих перпендикулярно плоскости рамы
Рис. 3.5 Расчетная схема рамы
Расчет рамы производится методом сил. Действующую на раму нагрузку разбиваем на симметричную и кососимметричною.
Рис. 3.6 Суммарная эпюра изгибающих моментов от крутящего момента.
а) Расчет рамы от симметричной нагрузки
Рис.3.7 Эпюра от симметричной нагрузки.
б)Учитывая действие кососимметричной нагрузки изгибающий момент увеличиваем на 20%.
)Определение напряжений.
где М1 и М2 - наибольшие изгибающие моменты действующие в плоскости рамы и перпендикулярно к плоскости рамы в одном и том же сечении Н;
WX и Wy-моменты сопротивления изгибу см3.
Выбираем профиль для стоек и связей и определяем моменты сопротивления изгибу для каждого сечения:
а)Стержень 1-1(рис. 3.3)
Рис. 3.8 Профиль направляющей рамы
Характеристика профиля
Рис.3.9 Сечение связи 2
Рис.3.10 Сечение связи 3
Рис.3.11 Сечение связи 4
Характеристика сечения
По формуле (3.21) определяем напряжения в каждой точке рамы. Точки для расчета указаны на (рис. 3.4). Момент М1 берем с (рис. 3.4) а М2 с (рис. 3.6) и (рис. 3.7)
)Напряжение в т. А направляющей:
) Напряжение в т. В связи:
) Напряжение в т. С связи:
) Напряжение в т. D связи:
) Напряжение в т. Е направляющей:
Для стали 35 т=320мПа.
1.4 Расчет внутренней рамы
)Расчет внутренней рамы от сил действующих в плоскости рамы.
Рис. 3.12 Расчетная схема
Рассчитываемая рама имеет две стойки показанных на (рис. 3.12) цифрой 1 и две связи показанные номерами 2 и 3.
Рама рассчитывается смешанным методом сил и деформаций. По силам на рис.3.12 производим построение эпюр изгибающих моментов от сил действующих в плоскости рамы(рис. 3.13)
Рис.3.13Эпюра изгибающих моментов от сил действующих в плоскости рамы
)Расчет рамы от сил действующих перпендикулярно плоскости внутренней рамы
Рис.3.14 Расчетная схема
Расчет рамы производим методом сил. Действующую на раму нагрузку разбиваем на симметричную и кососимметричною.
а)Расчет рамы от симметричной нагрузки.
Рис. 3.15 Эпюра симметричной нагрузки.
)Выбираем профиль для стоек и связей и определяем моменты сопротивления изгибу для каждого сечения:
Рис. 3.16 Сечение 1-1
Рис. 3.17 Сечение связи 2
Рис. 3.18 Сечение связи 3
По формуле (3.21) определяем напряжения в каждой точке рамы. Точки для расчета указаны на (рис. 3.13). Момент М1 берем с (рис. 3.13) а М2 с (рис. 3.15)
Напряжение в т. А направляющей:
Напряжение в т. В связи:
Напряжение в т. С связи:
1.5 Расчет напряжений на отгиб полки
Рис. 3.19 Сечение полки
Напряжения отгиба полок направляющих под воздействие усилий от роликов могут быть определены по формуле:
где Р- нагрузка от ролика на полку кг;
Т- толщина полки см.
Для стали 35 т=320мПа
1.6 Расчет направляющей рамы на отгиб полки
Рис. 3.20 Сечение полки
Напряжения отгиба полок направляющих под воздействие усилий от роликов определяем по формуле(3.46):
1.7Определение усилий на шток цилиндра.
Рис.3.21Расчетная схема усилия на шток цилиндра
-масса каретки =193кг;
-масса внутренней рамы =190кг;
Тогда усилие на шток цилиндра:
При подготовке производства новых изделий необходимо проанализировать спрос на разрабатываемые изделия размеры финансирования на разработку проекта и освоение производства с целью обоснования целесообразности принятых решений которые определят экономический успех предприятия в случае успешной реализации новой продукции.
В связи с ограничением финансовых ресурсов и конкуренции в условиях рыночных отношений крайне важно на ранних стадиях конструкторской проработки оценить техническую и экономическую целесообразность проектов и своевременно прекратить финансирование неперспективных вариантов.
Вывод о целесообразности проектирования и производства новых видов продукции возможен с помощью предлагаемых методических указаний.
1 Оценка технической целесообразности конструкции изделия
Сравнительный анализ проектируемого изделия на техническом уровне является первым этапом оценки и отбора лучших вариантов.
- установить техническую целесообразность спроектированной конструкции на основе сравнения с аналогом по основным группам функционально-технических показателей;
- обеспечить расчет минимальной цены изделия.
1.1 Выбор перечня показателей оценки технического уровня конструкций
Все показатели используемые для оценки технического уровня конструкции можно классифицировать на:
- показатели назначения и тактико-технические данные изделия;
- конструкторские (специальные) показатели влияющие на функционирование изделия;
- общие конструкторские (технические) показатели влияющие на условия производства.
В качестве показателей значения выбраны: энергия аккумуляторной батареи скорость подъёма груза скорость передвижения; в качестве технических показателей: габаритные размеры высота подъема груза наименьший радиус поворота масса погрузчика; в качестве технологических показателей: коэффициент унификации коэффициент стандартизации коэффициент повторяемости
Таблица экономических показателей.
Проектируе-мое изделие
Эталонное значение показателя
Высота подъема груза м
Скорость подъёма груза мс
Скорость передвижения кмч
Наименьший радиус поворота мм
Энергия аккумуляторной батареи кВ·ч
Коэффициент унификации
Коэффициент стандартизации
Коэффициент повторяемости
1.2 Оценка весомости (значимости) показателя
Оценка весомости показателей изделия осуществляется на основе экспертных оценок. Наиболее простым методом индивидуальной экспертизы используемой для оценки весомости показателей является метод попарных сравнений.
Результаты экспертизы представляются в виде матрицы (табл.4.2.) в которой на пересечении строки и столбца фиксируются индексы тех показателей которые являются более важными в оценке качества изделия при попарном их сравнении.
Далее для каждого показателя определяется количество предпочтений полученных им по отношению ко всем остальным показателям. Полученное значение увеличивается на единицу. Количественное представление весомости (значимости) показателей может быть получено по формуле:
где kj - количество предпочтений i - го показателя.
Матрица попарного сравнения показателей.
Индексы показателей
1.3 Расчет комплексного показателя технического уровня и качества конструкции
Комплексный показатель позволяет дать обобщенную оценку совокупной технической ценности изделия. В основе оценки лежит сравнение значений выбранного набора показателей базового и проектного варианта с эталонными значениями. В качестве эталонных могут использоваться наилучшие (идеальные) технически достижимые значения рассматриваемых показателей.
Комплексный показатель рассчитывается по формуле:
где q - безразмерный показатель качества по
r Относительный показатель качества по i - му параметру может быть рассчитан с помощью формулы:
где Pjn pjэ - количественные значения i - го показателя соответственно сопоставляемых вариантов и эталонного значения.
Первая формула используется для показателей при увеличении абсолютных значений которых возрастает обобщенный показатель в противном случае вторая формула.
Сопоставление комплексных показателей качества по потенциально возможным вариантам конструкций позволяет сделать вывод о технической целесообразности новой разработки определить коэффициент изменения качества при сравнении изделия с аналогом:
где Wn Wб - комплексные показатели качества проектного и базового вариантов. Данный коэффициент используется при определении лимитной цены проектируемого изделия.
Оценка технической целесообразности конструкции по вариантам (П - проектный Б - базовый).
Наименование показателей по
Коэффициент значимости
Оценка значения показателя по отношению
. Высота подъема груза
Скорость подъёма груза
З. Скорость передвижения
Наименьший радиус поворота
Энергия аккумуляторной батареи
2 Расчет трудоемкости ОКР
Многообразие существующих методов нормирования ОКР можно свести к трем основным: экспертному опытно-статистическому и расчетно аналитическому. Первый метод базируется на экспертных оценках второй -на сравнении нормируемого объекта с аналогичным нормативы на который известны третий - на корреляционных зависимостях трудоемкости работ от основных технических параметров изделия.
В основу предложенной методики по определению трудоемкости ОКР положен бальный метод.
С помощью бальных оценок по отдельным факторам определяется суммарный показатель объема работ в единицах сложности (баллы) который затем с помощью удельного норматива переводится в трудоемкость. Оценка факторов выполняется дифференцированно по главным узлам и видам работ.
Выделено два вида работ: расчетно-аналитические и чертежно-графические для которых порядок расчета объемных показателей различен.
Расчет выполняют в следующей последовательности:
Осуществляется сбор исходной информации о проектируемом объекте:
-наличие аналога или прототипа оценка общей сложности схемы объекта;
- состав главных узлов объекта;
-характеристики узлов (степень новизны конструкции количество кинематических пар количество оригинальных деталей объем конструкции по внешним контурам количество сложных деталей в узлах).
На основании значений исходных показателей таблицы 4.4 – 4.8 выбираются по каждому узлу нормативы объемов работ в баллах для первой и второй групп QH QH а также корректирующие коэффициенты к0 к1 к2 к3 к4. Результаты сведем в табл.4.9.
Показатель объема работ 1-й группы в единицах сложности (баллах)
Характеристика группы новизны
Имеется близкий аналог (отличия не более 20%).
Имеется аналог с небольшими отличиями (20 – 50%).
Имеется прототип похожий по принципу действия и конструкции отдельных узлов. Отличается по многим параметрам.
Известен прототип из информационных и патентных источников. Нет чертежей.
Прототипа нет или он неизвестен.
Нет прототипа в основе конструкции лежит новая идея.
Показатель объема работ 2-й группы в единицах сложности (баллах).
Группа насыщенности узла деталями
Примерное число оригинальных деталей
Группа сложности по числу кинематических пар
Группа объемности конструкции узла
Объем по внешним контурам дм3
Группа насыщенности узла сложными деталями*
Примерное количество сложных деталей
* К сложным относятся детали имеющие сложную форму требующие при конструировании специальных расчетов а также расчеты размерных цепей.
Исходные данные для расчета трудоемкости ОКР.
Характеристика объектов
Сложность схемы изделия
Новизна конструкции
Сложность узла по количеству кинематических пар
Насыщенность оригинальными деталями
Объем конструкции по внешним контурам
Насыщенность сложными деталями
Коэффициент К0 учитывающий сложность и степень автоматизации схемы объекта
Группа сложности схемы
Простейшая схема с одним энергопотоком без управления процессом.
Простая схема с разветвлением энергопотока с частично автоматическим или ручным управлением
Схема средней сложности с ветвящимся энергопотоком наличием блокировочных регулирующих и других элементов.
Сложная схема с автоматизацией рабочего цикла имеются взаимодействия механических электрически гидравлических и других связей в конструкции
Схема повышенной сложности с полной автоматизацией наличием обратных связей управление от устройства автоматики по заданной программе.
Осуществляется расчет показателей.
Показатель объема работ первой группы по узлу i определяется по формуле:
где QH - нормативное значение объема работ (первой группы в баллах) выбираемое в зависимости от группы новизны узла;
K1 - корректирующий коэффициент учитывающий влияние сложности узла по числу кинематических пар.
Показатель объема работ второй группы по узлу i определяется по формуле:
где QH2 - нормативное значение объема работ второй группы в баллах выбираемое в зависимости от количества оригинальных деталей в узле;
К2 К3 К4 - корректирующие коэффициенты учитывающие влияние группы сложности по числу кинематических пар группы объемности насыщенности узла сложными деталями соответственно.
Суммарная трудоемкость ОКР определяется по формуле:
где tн - норматив удельной трудоемкости чел.-дн.бал. Норматив устанавливается на основе статистических данных по результатам проектирования аналогичных изделий;
Ко - коэффициент учитывающий сложность и степень автоматизации управления объектов в целом. Расчет трудоемкости ОКР проведем в табл.4.11
Объем работ по группам в баллах
Расчетно-аналитические
Чертежно-графические
Норматив удельной трудоемкости на 1 балл чел-дн
Коэффициент сложности схемы К0
3 Расчет временных и стоимостных затрат на проектирование изделия
Важными показателями используемые при технико-экономическом анализе изделия являются стоимостные затраты на разработку и срок реализации проекта.
Укрупненный способ расчета основанный на данных о трудоемкости ОКР известной структуре распределения трудозатрат по стадиям проектирования (таблица 4.12) и норматив длительности стадии (таблица 4.13).
Расчет реализуется в табличной (таблица 4.14) форме в следующей последовательности:
) по типу производства выбирается соотношение трудоемкости
стадий проектирования %; tуд;
) рассчитывается трудоемкость отдельных стадий проектирования
)по суммарной трудоемкости ОКР выбирается нормативная длительность цикла технического и рабочего проектирования Ттпи и Трпи
)определяется длительность цикла технологической подготовки
производства по формуле:
) определяется потребная численность исполнителей по стадиям проектирования:
где Fpн - месячный фонд времени работника (176 часов);
Квн - коэффициент выполнения нормы Квн=11 12.
) Определяется фонд заработной платы на разработку проекта:
где 3jм - средняя месячная заработная плата исполнителей
Нсн - коэффициент отчисления на социальные нужды (Нсн=26%);
) определяются полные затраты на разработку проекта:
где Кзп - удельный вес заработной платы в общей структуре себестоимости выбирается по статистическим данным (Кзп=08);
) осуществляется оценка срока реализации проекта:
Где Кпар - коэффициент параллельности учитывающий величину совмещения стадий (Кпар=07).
Соотношение трудоемкости стадий проектирования %
Стадии и этапы работ
Разработка ТЗ и эскизное проектирование
Техническое проектирование (ТП)
Рабочее проектирование (РП)
Технологическая подготовка
Проектирование технологических процессов
Проектирование спецоснастки
Нормативы длительности стадий конструкторской подготовки производства
Общая трудоемкость проектирования н–ч.
Длительность цикла мес.
Расчет временных и стоимостных затрат на проектирование изделия.
Соотношение трудоемкости стадий проектирования %
Трудоемкость нормо-час.
Длительность производственного цикла мес.
Потребное количество исполнителей чел.
Средняя заработная плата исполнителей руб.
Фонд зарплаты по стадиям руб.
Единый фонд зарплаты на проектирование руб.
Оценка затраты на разработку проекта руб.
Оценка срока реализации мес.
4 Прогнозирование себестоимости изделия
На стадии конструкторской подготовки проекта когда отсутствуют необходимые технологические документы и нормативы для расчета себестоимости приходится применять различные методы прогнозирования: удельных весов и коэффициентов приведения известной структуры себестоимости аналогов.
Прямыми стадиями определяющими себестоимость конструкции являются:
- затраты на основные материалы;
- затраты на комплектующие основные изделия;
- заработная плата производственных рабочих.
4.1 Расчет затрат на основные материалы
Расчет затрат на основные материалы при небольшом количестве деталей и узлов можно выполнять в целом по изделию.
Стоимость основных материалов определяется на основе норм расхода каждого вида материала и цен за вычетом стоимости отходов.
Расчет затрат на основные материалы производим в табличной форме.
Затраты на основные материалы по базовому узлу можно рассчитать по формуле:
Цм - цена материала руб;
Ц° - цена отходов руб;
Котх - средний процент реализации отходов (табл. 4.15);
Ктз - коэффициент транспортно-заготовительных расходов (Ктз=103 -107).
Нормы планируемых отходов %
Расчет затрат на основные материалы.
Стоимость материала с учетом транспортно-заготовительных расходов рубт
Стоимость материала за вычетом реализованных отходов руб.
Итого по базовому узлу
4.2 Затраты на комплектующие покупные изделия
Затраты на покупные комплектующие изделия осуществляются на основе спецификаций применяемости Рij и цен Цкi по формуле:
Расчет затрат на комплектующие покупные изделия см. табл. 4.17.
Расчет затрат на комплектующие покупные изделия и полуфабрикаты по базовому узлу.
С учетом транспортно-заготовительных расходов руб.
Расчет затрат на основные материалы в целом по изделию.
Комплектующие изделия
4.3 Расчет затрат на заработную плату производственных рабочих
На стадии конструкторской подготовки производства расчет заработной платы базируется на показателе удельной трудоемкости на 1 кг массы конструкции изделия аналога. При отсутствии таких данных для приближенных расчетов можно использовать усредненные отраслевые значения.
Расчет заработной платы (основной и дополнительной) производственных рабочих.
Трудоемкость изделия
tуд - удельная трудоемкость 1 кг массы конструкции; G - масса конструкции.
Ти=18 ·2385=4293н-ч
Трудоемкость годового выпуска
Nг-прогнозируемый объм выпуска
Т=10 ·4293=42930н-ч
Потребное количество основных производственных рабочих
Fpr - годовой действительный фонд времени одного рабочего
R=429301860=24 чел.
Годовой фонд ЗП основной и дополнительный
Зср-средняя заработная плата ОПР
=12 ·24·5000= 1440000р.
ЗП с учетом отчислений на соц. нужды.
Нсн - коэффициент расходов на социальные нужды Нсн=26%
= 144000010 = 144000руб.
4.4 Расчет полной себестоимости изделия
Расчет полной себестоимости изделия осуществляется по формуле:
Нвн - норматив внепроизводственных расходов %; (для данного типа производства 7%);
З0и - заработная плата производственных рабочих на единицу изделия.
5 Определение прогнозируемой цены изделия
Прогнозируемая цена изделия выражает предельно допустимый уровень цены проектируемого изделия с учетом улучшения потребительских свойств замещаемого изделия при котором обеспечивается относительное удешевление его для потребителей.
При наличии аналога прогнозируемая цена может определяться на основе оценки изменения совокупности технических параметров по формуле:
Цп=09 ·Цб ·Ки (4.17)
где 09 - коэффициент характеризующий моральное старение базового изделия за период проектирования и освоения нового изделия;
Цб - цена базового изделия принимаемого в качестве аналога =1200т.р.;
Ки - коэффициент изменения качества изделия.
Цп =09·1200·122=13176 т.р.
6 Расчет уровня капитальных вложений в НИОКР и освоение производства
В условиях ограничения финансовых ресурсов технический и коммерческий успех проекта во многом определяется величиной новых капитальных вложений при его разработке и реализации. Капитальные затраты на всех этапах жизненного цикла изделия являются важной оценкой экономической эффективности новых проектов.
Единовременные затраты в сфере производства включают предпроизводственные затраты Кппз и капитальные вложения в производственные фонды завода изготовителя Кпф
Укрупненный расчет капитальных вложений в производственные фонды завода может производиться по формуле.
где Коб - капитальные вложения в оборудование и оснастку руб;
Кос - капитальные вложения в оборотные средства руб.
где Цп - прогнозтруемая цена изделия руб;
Nе- прогнозируемый объем выпуска шт;
Коб - отраслевой норматив удельных капитальных вложений в оборудование на один рубль объема реализации новых изделий; =06
- коэффициенты учитывающие соответственно годовой объем производства для данного типа производства соответственно 1 и 09
Kоб = 13176 · 10 · 1· 09 · 06 = 711504 т.руб.
Кпф = 711504 + 711504 · 03 = 9249552 т.руб.
Кп = 171360 + 9249552= 9420912 т.руб.
7. Оценка экономической эффективности производства разрабатываемого электропогрузчика
Расчет прибыли на единицу изделия
Э=13176 – 817902=499698 т.руб.
Период возврата капитальных вложений:
8. Сводные показатели оценки экономической целесообразности
Заключительным этапом технико-экономического обоснования проектируемого изделия является составление таблицы показателей оценки экономической целесообразности конструкции (табл. 4.20.).
Показатели оценки экономической целесообразности конструкции
Наименование показателя
Прогнозируемый объем выпуска
Единовременные капитальные вложения
Производственные затраты
Вложения в производство
Текущие издержки на производство
На заработную плату
Полная себестоимость
Прибыль на единицу изделия
Прогнозируемая цена изделия
Срок реализации проекта
Срок возврата капитальных вложений
Проведенные технико-экономическое обоснование производства выявило перспективность осуществления этого проекта. Проведенные экономические расчеты себестоимости и цены изделия позволяют определить планируемую прибыль и рентабельность а также годовой экономический эффект при производстве проектируемого изделия. Срок возврата капитальных вложений относительно невелик что также свидетельствует о перспективности данного проекта.
1 Обеспечение эргономических требований к месту водителя электропогрузчика
Конструкция рабочего места и взаимное расположение его элементов должны соответствовать характеру работы обеспечивать удобное положение водителя его безопасность а также возможность выполнения рабочих манипуляций. Для выполнения этого рабочие место должно отвечать всем ниже перечислимым требованиям
1.1 Требования к средствам доступа на рабочее место
Для доступа водителя на рабочее место машины должны быть оборудованы подножками и лестницами с поручнями (ручками). Допускается использовать в качестве поручней и промежуточных подножек конструктивные элементы машин.
Параметры средств доступа мм:
высота расположения нижней ступени относительно опорной поверхности колес машин (пола) — не более 450;
ширина ступени — не менее 130;
глубина ступени — не менее 100;
высота ступени — не менее 80;
интервал между ступенями — 200—300;
длина охватываемой части поручня или ручки — не менее 120;
диаметр поручня или ручки — 15—20;
расстояние от поверхности захвата поручня или ручки до любого элемента конструкции машины — не менее 50.
1.2 Требования к сидению водителя
Параметры сиденья и его элементов должны быть увязаны с положением точки отсчета сиденья (ТОС).
Требования к обивочному материалу сиденья — по ГОСТ 23367.
Конструкция сиденья должна обеспечивать регулирование его положения в горизонтальном (продольном) направлении относительно среднего положения не менее чем на 50 мм в каждую сторону.
Конструктивные элементы машины расположенные под сиденьем не должны выступать за передний край подушки сиденья находящегося в крайнем переднем положении более чем на 50 мм в верхней части и более чем на 80 мм в нижней части.
Параметры сиденья находящегося в среднем положении (рис. 5.1) должны соответствовать значениям:
ширина сиденья (измеренная на расстоянии 150—200 мм от ТОС) b — не менее 430 мм;
высота спинки сиденья h — (400±20) мм;
ширина спинки сиденья (измеренная на расстоянии 150—200 мм от ТОС) b1 — не менее 430 мм;
угол наклона подушки сиденья α— 0—5°;
угол наклона спинки сиденья — 5—20°;
расстояние от сиденья до наружного контура машины — не менее 50 мм.
Рис. 5.1 Параметры сиденья находящегося в среднем положении.
1.3 Требования к рычагам управления
Общие эргономические требования к рычагам управления — по ГОСТ 21753;
Минимальная длина свободной части рычага управления (вместе с рукояткой) в любом его положении должна быть не менее 50 мм — для захвата пальцами и 150 мм — для захвата всей кистью.
Форма и размеры рукояток рычагов должны обеспечивать максимальное удобство их захвата и надежного удержания в процессе управления. При этом предпочитают рукоятки с плавными округлыми формами близкими к шаровидной и удлиненной — цилиндрической тщательно обработанной гладкой или рифленой поверхностью без острых углов и заусенцев.
Рукоятки рычагов используемых в условиях низкой температуры окружающей среды должны изготовляться из материалов или покрываться материалами которые обладают низкой теплопроводностью.
Рычаги управления необходимо устанавливать на рабочем месте так чтобы их рукоятки при любом положении рычага находились «пределах зоны досягаемости моторного поля оператора.
Рукоятки рычагов перемещаемых одной рукой необходимо размещать на стороне соответственно действующей правой или левой руки в пределах досягаемости при сгибе ее в локтевом суставе под углом 90-135° и приложении усилия по направлению прямо «на себя — от себя».
Кодирование рукояток рычагов управления в том числе и рычагов специального назначения (аварийных противопожарных и др.) а также рычагов объединенных в функциональные группы необходимо проводить выбором соответствующей формы размера и цвета а также расположением.
Рычаги управления должны иметь хорошо видимые надписи означающие их назначение а также указатели положения направления перемещения и его следствия помещаемые как непосредственно на рычагах так и рядом с ними.
Рычаги применяемые для дискретных (ступенчатых) переключений должны иметь надежную фиксацию промежуточных и конечных положений.
Рычаги управления должны быть установлены так чтобы при их перемещении исключалась возможность случайного включения (выключения) смежного рычага.
1.4 Требования к выключателям и переключателям
Требования выключателям и переключателям типа «Тумблер» — по ГОСТ 22615.
Выключатели и переключатели типа «Тумблер» должны применяться для осуществления операций быстрого включения—выключения и переключения электрических цепей при необходимости зрительного контроля положения переключателей.
Форма и размеры приводного элемента (ПЭ) выключателей и переключателей типа «Тумблер» должны соответствовать антропометрическим данным пальцев человека и обеспечивать максимальное удобство захвата приводного элемента в процессе управления с учетом спецснаряжения.
В выключателях и переключателях типа «Тумблер» при переводе приводного элемента из одной позиции в другую должен ощущаться перепад величины упругого сопротивления и быть слышен характерный щелчок.
Положение приводного элемента выключателей и переключателей типа «Тумблер» «вверх» «вправо» «от себя» должно со ответствовать рабочему состоянию «включено» а положение приводного элемента «влево» «вниз» «к себе» — состоянию «выключено».
Тумблеры используемые как аварийные следует защищать специальными крышками или размещать в углублении панели.
Для обозначения функции приводных элементов выключателей типа «Тумблер» следует применять надписи или символы.
Располагают надписи и символы на панели управления в непосредственной близости от приводных элементов с любой стороны при условии что сами приводные элементы а также рука человека—оператора не будут перекрывать обозначения во время манипулирования приводными элементами.
При размещении тумблеров на панели управления в ряд расстояние
Расстояние между осевыми линиями тумблеров и другими элементами управления лицевой панели должно быть не менее 25 мм.
1.5 Требования к индикаторным устройствам
Эргономические требования к индикаторным устройствам на рабочем месте водителя — по ГОСТ 22902.
Тип отсчетного устройства выбирают исходя из функционального назначения индикатора требований к точности и скорости считывания а также внешних условий деятельности оператора.
Лицевая поверхность отсчетного устройства должна быть окрашена в черный (или белый) цвет исключающий блескость при допустимых углах считывания.
Окраска лицевых сторон шкал и указателей должна удовлетворять следующим требованиям:
при использовании черного цвета коэффициент отражения должен быть не более 01 при освещении источником белого света с цветовой температурой 2400 К;
при использовании белого цвета — не менее 07 при освещении источником белого света с цветовой температурой 2400 К.
Отсчетные устройства должны быть снабжены индивидуальной подсветкой с плавной или ступенчатой регулировкой яркости. Освещенность отсчетного устройства должна быть выше освещенности фона не менее чем на 10% и не более чем на 300% при контрасте информационного изображения с фоном не менее 06.
1.6 Требования к органам управления
Параметры расположения и размеры органов управления (рис. 5.2) должны соответствовать значениям:
расстояние от ТОС до центра рулевого колеса мм:
по горизонтали l1 — 520—625
по вертикали h1 — 325—450;
угол наклона плоскости рулевого колеса относительно горизонтали α1 — 10—45°;
наружный диаметр рулевого колеса —340—450 мм;
диаметр обода рулевого колеса — 20—40 мм;
осевое смещение рулевого колеса от продольной оси симметрии сиденья водителя — ±40 мм;
ширина свободного пространства вокруг рулевого колеса не менее — 50 мм;
длина хода педалей мм не более:
приводимых в действие всей ногой — 200
приводимых в действие ступней — 150;
ширина площадки педалей не менее — 60 мм;
угол наклона к горизонтали опорных площадок педалей приводимых в действие всей ногой 1 — 30—60°;
угол наклона к горизонтали опорных площадок педалей приводимых в действие стопой 2 — не более 45°;
угол между продольной осью опорных площадок педалей приводимых в действие стопой и продольной осью машины α2 — не более 15°;
расстояние от центров опорных площадок педалей до продольной оси сиденья мм:
для педалей приводимых в действие стопой b2 — 75—300
для педалей приводимых в действие всей ногой b3 —75—200;
расстояние между центрами рядом расположенных педалей b4— 120—320.
Рис. 5.2 Параметры расположения и размеры органов управления
Расстояние от элементов конструкции расположенных под сиденьем до кожуха рулевого управления на уровне пола должно быть не менее 300 мм.
1.7 Требования к обзорности с рабочего места водителя
Конструкция машин должна обеспечивать обзорность с рабочего места водителя при движении и выполнении погрузочно-разгрузочных операций.
Обзорность электропогрузчиков и электроштабелеров оценивают визуально с помощью испытательной установки (рис. 5.3) которая состоит из вертикальной и горизонтальной таблиц (экранов).
Горизонтальная таблица (таблица пола) предназначена для определения «близкой» обзорности (отъезда и подъезда машины аварийного торможения).
Вертикальная таблица предназначена для определения обзорности при передвижении машины маневрировании и перемещении груза.
Каждая таблица представляет собой светлую плоскость разграфленную на квадраты 500X500 мм. В центре каждого квадрата нанесен буквенно-цифровой знак.
На полу по центральной линии таблиц проводится ось АА.
Под прямым углом к оси АА на расстоянии 500 мм от горизонтальной таблицы— ось ВВ.
Рис. 5.3 Вид и основные размеры таблиц:
—вертикальная таблица; 2—горизонтальная таблица
При оценке обзорности водитель может перемещаться в пространстве ограниченном прозрачным цилиндром. Цилиндр необходимо отрегулировать по высоте чтобы голова водителя находилась в пределах цилиндра.
Рис. 5.4 Размеры и положение цилиндра:
—Прозрачный цилиндр; 2—центр цилиндра
Испытание на обзорность должно проводиться на горизонтальной площадке (на полу) с наклоненным назад грузоподъемником вилами поднятыми на высоту 300 мм над испытательной площадкой и симметрично расположенными на плите. Сиденье и органы управления должны быть установлены в среднее регулируемое положение.
Обзорность определяют в четырех положениях машины.
Водитель должен занять на машине рабочее положение и перемещая голову в пространстве ограниченном цилиндром(рис. 5.4) рассматривать буквенно-цифровые знаки от А1 до П8.
Буквенно-цифровые знаки на шкалах которые не видны или видны не полностью должны быть перечеркнуты на соответствующей таблице протокола крестом.
2 Расчет устойчивости электропогрузчика
Для безопасной работы погрузчики должны быть устойчивыми при работе и в нерабочем состоянии.
Безопасность работы погрузчиков определяется не только их продольной статической устойчивостью но и динамическими нагрузками связанными с условиями работы и прежде всего инерционными силами возникающими:
при трогании с места и торможении погрузчика или при движении его по кривой во время поворота;
в начале и конце подъема пути или при опускании груза и подвижных элементов конструкции грузоподъемника;
в начале или в конце наклона рамы грузоподъемника с грузом на вилах;
при раскачивании груза и элементов конструкции сменного рабочего оборудования.
Погрузчик может потерять устойчивость из-за нарушения силового баланса когда точка приложения равнодействующей всех сил выйдет за пределы опорного контура машины. Для правильного выбора методов расчета устойчивости необходимо учесть влияние всех сил действующих на погрузчик как в продольном так и в поперечном направлении. При этой необходимо рассматривать устойчивость погрузчика не только в статическом состоянии но и в движении.
Для расчета устойчивости разбираем узлы электропогрузчика на две группы:
I группа – узлы не изменяющие своего положения относительно шасси при работе погрузчика
II группа – узлы изменяющие свое положение относительно шасси: грузоподъемник вилы с рамкой натяжное устройство груз.
2.1 Расчет координат центра тяжести узлов первой группы
Вес и координаты центров тяжести узлов I группы
Колесо ведущее (два)
Устройство тормозное
Двигатель передвижения (два)
Аккумуляторная батарея
Гидропривод (с маслом)
Цилиндр наклона (два)
Находим координаты центра тяжести узлов первой группы:
где Х1- координата центра тяжести узлов первой группы по оси Х см;
Z1- координата центра тяжести узлов первой группы по оси Z см;
Zi-координата i-тог узла по оси Z см.
2.2 Расчет координат центра тяжести узлов второй группы
Вес и координаты центров тяжести узлов II группы
по оси Z при высоте подъема мм
Находим координаты центра тяжести второй группы при вертикальном грузоподъемнике для высот подъема 300 мм и 3000 мм соответствующих нахождению груза в транспортном положении и при штабелировании.
2.3 Расчет продольной устойчивости
По нормам СЭВ продольная устойчивость погрузчика должна удовлетворять следующим условиям:
) Устойчивость при штабелировании – груз на максимальной высоте грузоподъемник перпендикулярен платформе которая наклонена на угол φ=2о16 (4%).
Условие устойчивости:
Удерживающий момент:
гдеG1-вес всех узлов первой группы кг.
Опрокидывающий момент:
где G2-вес всех узлов второй группы кг.
.Коэффициент запаса устойчивости:
Условие устойчивости удовлетворено
) Устойчивость при движении с грузом – груз на высоте 300 мм грузоподъемник наклонен назад платформа наклонена на угол φ=10о13 (18%)
Коэффициент запаса устойчивости:
) Допустимое ускорение при передвижении.
где x и z – координаты центра тяжести погрузчика с грузом в транспортном положении
2.4 Расчет поперечной устойчивости
По нормам СЭВ поперечная устойчивость погрузчика должна удовлетворять следующим условиям:
) Устойчивость при штабелировании – груз на максимальной высоте грузоподъемник наклонен назад платформа наклонена на угол φ=3о26 (6%).
Находим координаты центра тяжести погрузчика для рассматриваемого положения
Рис. 5.5 Расчетная схема для определения боковой устойчивости погрузчика
Рис. 5.6 Расчетная схема для определения угла опрокидывания погрузчика на платформе
Найдем угол опрокидывания погрузчика на платформе
) Устойчивость при движении – грузоподъемник без груза наклонен назад вилы подняты на 300 мм платформа наклонена на
Находим координаты центра тяжести для одного положения:
Критическая скорость центра тяжести погрузчика без груза на повороте
На основе базовых вариантов учитывая их достоинства и недостатки был разработан электропогрузчик грузоподъемностью 125т .
Основная часть разработок проекта направлена на определение усилий и параметров грузоподъемного оборудования. В проекте предложено снижение металлоемкости металлоконструкции за счет использования рационального распределения металла в сечениях грузоподъемника.
Использование проектной конструкции обладающей рядом преимуществ перед рассмотренными вариантами позволяет снизить себестоимость работ по производству и обслуживанию электропогрузчика и получить значительный экономический эффект величина которого обоснована в экономической части.
СПИСОК ИСПОЛЬЗОВАННОЙ ЛИТЕРАТУРЫ
Белов С.В. Безопасность производственных процессов: Справочник. - М.: Машиностроение 1985. – 675с.
Векснер В.М. Муха Т.И. Проектирование и расчет перегрузочных машин. Погрузчики и вибропогрузчики. – Л. «Машиностроение» [Ленинградское отделение] 1971. – 319с.
Голутвин В.А. Вилочные погрузчики: Учебное пособие. Тула1974.-90с.
Гриневич Г.П. Мачульский И.И. Алепин Е.А. Вилочные погрузчики. - М.: Машиностроение 1974.–213с.
ГОСТ Р 50570-93 Машины напольного безрельсового электрифицировано транспорта. Рабочее место водителя. Общие эргономические требования.
Курский В.Н. Курский В.А. Ратников О.А. Методические указания по организационно-экономическому обоснованию дипломных проектов Тула: ТулГУ 1996. – 34с.
Мачульский И.И. Капырина В.И. Алепин Е.А. Электропогрузчики: Справочник. - М.: Транспорт1987.-238с.
Мачульский И.И. Киреев В.С. Подъемно-транспортные и погрузочно-разгрузочные машины на железнодорожном транспорте: Учебник для студентов вузов железнодорожного транспорта. - М.: Транспорт1989.-319с.
Мачульский И.И. Алепин Е.А. Машины напольного безрельсового транспорта. - М.: Машиностроение 1982.–232с.
Тройнин М.Ф. Ушаков Н.С. Электрокары и электропогрузчики. Издание 3-е доп. и переработанное. – Л. «Машиностроение» [Ленинградское отделение] 1973. – 264с.
Тимошин А.А. Мачульский И.И. Голутвин В.А. Клейнерман А.Л. Капырина В.И. Комплексная механизация и автоматизация погрузочно-разгрузочных работ: Учебник для вузов ж.-д. трансп. – М.: Маршрут2003.-400с.
Юдин Е.Я. Охрана труда в машиностроении: Учебник для ВУЗов. - М.: Машиностроение 1985. – 432с.
Апм.doc
Рис. 6.1 Наружная рама грузоподъемника.
Наружная рама грузоподъемника (рис.6.1) выполнен из конструкционной стали 35 имеющего следующие характеристики: предел прочности –315 МПа; модуль Юнга – 210000 МПа; коэффициент Пуассона – 03; плотность – 7800кгм3.
Расчетная схема барабана механизма подъема показана на рис. 6.2. Нагрузки на узлы конечно-элементной модели согласно расчетной схеме указаны в таблице 6.1. Программный модуль расчета и проектирования пространственных конструкций производит при расчете автоматическое разбиение каждого из стержней на сто частей (конечных элементов).
Рис. 6.2 Расчетная схема наружной рамы
Нагрузки на узлы наружной рамы (Рис. 6.2)
Наружная рама грузоподъемника состоит из 12 стержней показанных на (Рис.6.2) синим цветом. Каждому из 12 стержней для расчета было присвоено свое сечение.
Стержень 0(Рис.6.3)имеет следующие параметры:
Площадь 1599.97 кв.мм
Центр масс: X= 8.000 Y= 49.999 мм
относит. оси X 1333176.29 мм4
относит. оси Y 34042.82 мм4
полярный 1367219.10 мм4
Угол наклона главных центральных осей 0.00 град
Рис.6.3 Поперечное сечение стержня 0
Стержень 1(Рис.6.4)имеет следующие параметры:
Площадь 1490.78 кв.мм
Центр масс: X= 0.006 Y= -0.007 мм
относит. оси X 1921380.50 мм4
относит. оси Y 1109225.20 мм4
полярный 3030605.70 мм4
Угол наклона главных центральных осей -0.01 град
Рис.6.4Поперечное сечение стержня 1
Стержни со 2 по 9 имеют одинаковое сечение показанное на (Рис.6.5) и имеют следующие параметры:
Площадь 1325.91 кв.мм
Центр масс: X= -36.512 Y= 60.106 мм
относит. оси X 3043476.63 мм4
относит. оси Y 311938.66 мм4
полярный 3355415.30 мм4
Угол наклона главных центральных осей -0.03 град
Рис.6.5 Поперечное сечение стержней со 2 по 9
Стержни 10 и 11 имеют одинаковое сечение показанное на (Рис. 6.6) и имеют следующие параметры:
Площадь 2033.16 кв.мм
Центр масс: X= 2.470 Y= 38.070 мм
относит. оси X 2094527.48 мм4
относит. оси Y 622719.91 мм4
полярный 2717247.40 мм4
Угол наклона главных центральных осей 12.65 град
Рис.6.6 Поперечное сечение стержней 10 и 11
По результатам расчета общая масса конструкции 5838кг. Эпюра изгибающего момента в плоскости XZ [Нxм] показана на (Рис.6.7). Максимальное нагрузка показана на рисунке (Рис.6.8) ММАХ=56 кН·м. Максимальное перемещение 303мм (рис.6.9). Максимальное напряжение 169.5 МПа (Рис.6.10).
Рис. 6.7 Эпюра изгибающих моментов в плоскости XZ.
Рис. 6.8 Карта нагрузки
Рис. 6.9 Карта перемещений.
Рис. 6.10 Карта напряжений.
Эквивалентное напряжение в наружной раме.
Рис. 6.11 Распределение напряжений по сечениям.
гидросхема.dwg

Пневмоцилиндр дозатора
Подача мороженого в цилиндр
Позиционные обозначения
Предохранительный клапан
грузоподъемник.dwg

Устойчивость электропогрузчика.dwg

действующих сил при испытаниях продольной устойчивости
Схема установки электропогрузчика на стенде при
испытании па поперечную устойчивость
Условие устойчивости:
-центр массы погрузчика
Ось наклона платформы
-коэффициент запаса устойчивости
Схемы устойчивости электропогрузчика
общий вид.dwg

экономика.dwg

Пневмоцилиндр дозатора
Подача мороженого в цилиндр
Показатели технического уровня и качества изделия
Временные и стоимостные затраты на проектирование изделия
Расчет трудоемкости ОКР
Показатели оценки экономической целесообразности конструкции
ДП 315720.00.00.000
Сравнительная характеристика.dwg

чертёж склада.dwg

Количество элементарных площадок
тарно-штучных грузов
СОДЕРЖАНИЕ.doc
2 Выбор рациональной схемы машины
3.1. Характеристика объекта разработки
3.2. Регламент поиска при исследовании на патентную чистоту
3.3. Отчет о патентном поиске
3.5. Библиографический перечень отобранной
в процессе поиска информации
3.6 Аннотация отобранной в процессе поиска информации
4 Техническая характеристика
5 Описание конструкции разрабатываемого электропогрузчика
КОСТРУКТОРСКИЙ РАСЧЕТ
1 Проект склада штучных грузов для разрабатываемого электропогрузчика
1.1 Расчетный суточный поток
1.2 Необходимое число вагонов
1.3 Количество автотранспорта
1.4 Расчет параметров склада
1.5 Выбор типа и расчет количества погрузочно-разгрузочных машин
1.6Эксплуатационная и сменная производительность
2 Расчет гидравлической системы
2.2 Выбор площади цилиндра подъема
2.3 Выбор типа насоса
2.4 Определение скоростей подъема каретки
2.5 Расчет ёмкости масляного бака
3 Тяговый расчет электропогрузчика
3.1 Расчет тягового усилия
3.2 Расчет момента на валу ведущих колес
3.3 Определение мощности двигателя передвижения
4 Электрооборудование погрузчика
4.1Элементы электрооборудования
4.2Описание работы электрической схемы электропогрузчика
1 Расчет грузоподъемного механизма
1.2 Расчет сил действующих на рамы грузоподъемника
1.3 Расчет наружной рамы
1.4 Расчет внутренней рамы
1.5 Расчет напряжений на отгиб полки
1.6 Расчет направляющей рамы на отгиб полки
1.7Определение усилий на шток цилиндра
1 Оценка технической целесообразности конструкции изделия
1.1 Выбор перечня показателей оценки технического уровня конструкций
1.2 Оценка весомости (значимости) показателя
1.3 Расчет комплексного показателя технического уровня и качества конструкции
2 Расчет трудоемкости ОКР
3 Расчет временных и стоимостных затрат на проектирование изделия
4 Прогнозирование себестоимости изделия
4.1 Расчет затрат на основные материалы
4.2 Затраты на комплектующие покупные изделия
4.3 Расчет затрат на заработную плату производственных рабочих
4.4 Расчет полной себестоимости изделия
5 Определение прогнозируемой цены изделия
6 Расчет уровня капитальных вложений в НИОКР и освоение производства
7. Оценка экономической эффективности производства разрабатываемого электропогрузчика
8. Сводные показатели оценки экономической целесообразности проекта
1 Обеспечение эргономических требований к месту водителя электропогрузчика
1.1 Требования к средствам доступа на рабочее место
1.2 Требования к сидению водителя
1.3 Требования к рычагам управления
1.4 Требования к выключателям и переключателям
1.5 Требования к индикаторным устройствам
1.6 Требования к органам управления
1.7 Требования к обзорности с рабочего места водителя
2 Расчет устойчивости электропогрузчика
2.1 Расчет координат центра тяжести узлов первой группы
2.2 Расчет координат центра тяжести узлов второй группы
2.3 Расчет продольной устойчивости
2.4 Расчет поперечной устойчивости
РАСЧЕТ МЕТАЛЛОКОНСТРУКЦИИ НАРУЖНОЙ РАМЫ В СРЕДЕ АВТОМАТИЗИРОВАННОГО ПРОЕКТИРОВАНИЯ И РАСЧЕТА АПМ WINMACHINE
СПИСОК ИСПОЛЬЗОВАННОЙ ЛИТЕРАТУРЫ
Рекомендуемые чертежи
- 20.08.2014
- 20.08.2014
- 20.08.2014
Свободное скачивание на сегодня
- 24.01.2023