Цех стального литья производственной мощностью 40 000 тонн годного в год


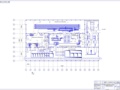
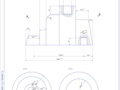
- Добавлен: 16.01.2023
- Размер: 3 MB
- Закачек: 0
Описание
Целью данного проекта являлось проектирование литейного цеха для производства 40 000 т годных отливок из стали в разовые песчано-глинистые формы. Описан технологический процесс получения отливки " Шкив привода генератора " из материала Сталь 35Л ГОСТ 977-88 и приведены расчеты литниковой системы для получения этой отливки. / Состав: 9 листов чертежи (отливка, модель верха отливки, модель низа отливки, стержень, ящик, форма, цех, цех разрез) + спецификации + практика + ПЗ (92 страницы, Технико-экономическая часть отсутствует) |
В разделе "Расчетно-проектная часть" спроектирован цех на выпуск 40 000 тонн годного стального литья в год и рассчитано необходимое количество технологического оборудования цеха. Оглавление Шкив привода генератора”, по номенклатуре 740-1318160: Заключение |
Состав проекта
![]() |
![]() ![]() ![]() ![]() |
![]() ![]() ![]() ![]() |
![]() ![]() ![]() ![]() |
![]() ![]() ![]() ![]() |
![]() ![]() ![]() ![]() |
![]() ![]() ![]() ![]() |
![]() ![]() ![]() ![]() |
![]() ![]() ![]() ![]() |
![]() ![]() ![]() ![]() |
![]() ![]() ![]() |
![]() ![]() |
![]() ![]() |
![]() ![]() ![]() |
![]() ![]() ![]() |
![]() ![]() ![]() |
Дополнительная информация
3 Мод. верх.cdw

Неуказанные радиусы 2 5 мм.
Формовочные уклоны по ГОСТ 3212-92
Остальные технические требования по ГОСТ 3212-92
Шкив привода генератора
Модель верха отливки.
Сталь 40Х ГОСТ 4543-2016
3 Мод. низ.cdw

Неуказанные радиусы 2 5 мм.
Формовочные уклоны по ГОСТ 3212-92
Остальные технические требования по ГОСТ 3212-92
Шкив привода генератора
Модель низа отливки.
Сталь 40Х ГОСТ 4543-2016
3 Отливка.cdw

Неуказанные литейные радиусы до 2 5 мм.
Величина и количество литейных дефектов по эталону
Формовочные уклоны по ГОСТ 3212-92
Остальные технические требования по ГОСТ Р 53464-2009
Шкив привода генератора
Сталь 35Л ГОСТ 977-88
3 Отливка2.cdw

Неуказанные литейные радиусы до 2 5 мм.
Величина и количество литейных дефектов по эталону
Формовочные уклоны по ГОСТ 3212-92
Остальные технические требования по ГОСТ Р 53464-2009
Шкив привода генератора
Сталь 35Л ГОСТ 977-88
3 Стержень.cdw

Остальные технические требования по ГОСТ 3212-92
Шкив привода генератора
3 Форма.cdw

3 Цех разрез.cdw

3 Цех.cdw

ВКР 1.15.03.01.19.17.0000
Смесеприготовительно стержневое отделение
Формовочное отделение
Плавильное отделение
Термообрубное отделение
3 Ящик.cdw

Формовочные уклоны по ГОСТ 3212-92
Остальные технические требования по ГОСТ 19376-74; ГОСТ 19409-74;
практика Алексей.docx
Технологическая часть7
1 Выбор способа изготовления отливки7
2 Выбор положения отливки в форме в период заливки и затвердения7
3 Определение поверхности разъема формы8
4 Определение припусков на механическую обработку формовочных уклонов радиусов закруглений8
5 Графическое оформление отливки8
6 Определение количества и конструкции стержней9
7 Формовочные и стержневые смеси9
7.1 Формовочные смеси9
7.2 Стержневые смеси11
8 Разработка конструкции модели и модельных плит12
8.1 Классификация моделей12
8.2 Выбор материала для изготовления модельного комплекта12
8.3 Металлические модельные комплекты12
9 Разработка конструкции литниковой системы13
10 Определение количества моделей на плите14
11 Выбор способа формовки14
12 Выбор способа плавки металла16
13 Разработка технологии заливки форм17
14 Разработка технологии охлаждения форм выбивки обрубки очистки18
15 Разработка системы контроля технологии и качества отливок19
16 Дефекты отливки мероприятия по предупреждению и способы исправления20
17 Расчет литниково-питающей системы20
18 Нововведения в технологии23
Характеристика Литейного завода ПАО «КАМАЗ»
В соответствии с учебным планом я проходил учебную практику на Литейном заводе ПАО «КАМАЗ» в Бюро ТО ПСЛ.
В ходе прохождения практики я полностью освоил и изучил технологические процессы проектирования.
Литейный завод - это специализированное предприятие с полным технологическим циклом изготовления отливок и литейной оснастки.
ЛЗ ПАО «КАМАЗ» осуществляет производство продукции диверсификации в следующих направлениях:
Специальные виды литья.
Продукция нашего предприятия сертифицирована и соответствует требованиям ГОСТ Р ISO 9001-2011 (ISO 9001:2008).
Предприятие работает в следующих сегментах рынка литья:
- Автомобилестроение;
- Железнодорожное и общее машиностроение.
Конкурентные преимущества:
Полный цикл создания новой продукции: маркетинговые исследования проектирование подготовка производства выпуск и реализация. Предприятие оснащено современным оборудованием и обладает широким спектром новых технологий литья.
Литейный завод многопрофильный: может работать не только на заказчиков предприятий автопрома но и достаточно быстро ориентироваться на другие рынки: литье для железных дорог нефтегазовой отрасли коммунального хозяйства.
Разработка конструкторско-технической документации производится с использованием пакетов: Un LVMF ProCAST2008 (моделирование литейных процессов).
Для контроля качества выпускаемых отливок на каждом этапе технологического процесса имеется весь арсенал контрольного оборудования. Экспресс-анализ химического состава применяемых в производстве сплавов производится в спектральной лаборатории.
Проектирование технологической оснастки ведется на основании технических заданий разработанных в соответствии с технологическим процессом изготовления изделия и утвержденных главным технологом предприятия.
Техническое задание включает:
) технологический процесс сборки и сварки;
) чертежи изделия (уточненный экземпляр);
) базовые и установочные поверхности собираемых в установке (приспособлении) деталей;
) схему расположения зажимных элементов их тип и развиваемые ими усилия;
) характер работы установки (приспособления) - подъемное поворотное подъемно-поворотное;
) задание на проектирование встроенной в установку (стенд) вытяжной (из зоны сварки) вентиляции;
) рабочее давление в цеховой пневмосети;
) рабочее напряжение электросети;
) коэффициент сменности режим работы и характер производства.
В техническом задании должен быть решен вопрос о способах загрузки изделия в технологическую оснастку и о связи ее с общим технологическим потоком изготовления.
После получения технического задания разработчик обязан изучить:
а) чертежи заготовки сварного узла и готовой детали а также технические требования на изготовление;
б) технологический процесс и техническое задание на проектирование технологической оснастки;
в) техническую характеристику (паспортные данные) и посадочные места оборудования на котором будет монтироваться проектируемая технологическая оснастка.
При проектировании технологической оснастки следует придерживаться следующего порядка:
) вычертить контур собираемого в приспособлении узла (в трех проекциях) расположив проекции так чтобы осталось достаточно места для размещения всех элементов приспособления; контур детали вычерчивают как правило цветным карандашом
) вычертить установочные или опорные элементы приспособления;
) вычертить зажимные и вспомогательные элементы приспособления;
) вычертить корпус выполнить все необходимые разрезы и сечения проставить габаритные и контрольные размеры а также задать необходимые технические требования на точность изготовления технологической оснастки; указать место маркировки;
) увязать технологическую оснастку со средствами межоперационного транспорта.
Наряду с этим необходимо выполнить расчеты по определению сил зажима изделия в зависимости от величин сварочных деформаций точности базирования в зависимости от требуемой точности изготовления основных параметров зажимных устройств (расчет на прочность и жесткость) основных параметров силового привода.
Разработчик должен изучить современные и перспективные стандарты и строго соблюдать государственные и отраслевые нормативы.
При достигнутом в настоящее время уровне нормализации большое число специальных и специализированных станков и оснастки может быть скомпоновано из нормализованных узлов.
Следовательно одной из важнейших предпосылок для сокращения сроков освоения производства новых изделий и повышения степени оснащенности технологических процессов является все более широкое применение стандартизированной технологической оснастки. Разработчику необходимо разрабатывать только рабочие компоновки приспособлений сборка которых происходит из заранее изготовленных стандартизированных элементов.
Технологическая часть
Анализируем конструкцию отливки “Шкив привода генератора” по номенклатуре 740-1318160.
Отливка по конструкции несложная (тело вращения с одним центральным отверстием). Конструкция отливки обеспечивает сборку форм. По массе деталь мелкая. По назначению деталь является ответственной конструкция детали отвечает как требованиям технологии механической обработки так и требованиям литейной технологии. Для изготовления отливки требуется один стержень простой формы.
1 Выбор способа изготовления отливки
Учитывая массовый тип производства а также несложную конфигурацию массу и габариты отливки класс точности приходим к выводу что данную отливку получаем литьем в песчано-глинистые формы. Используем машинную формовку отливку изготавливаем непосредственно на автоматической формовочной линии.
Принятый способ литья получает высокий выход годного литья при относительно невысоких затратах при осуществлении технологического процесса.
2 Выбор положения отливки в форме в период заливки и затвердения
Положение отливки в форме при заливке и затвердении определяет весь технологический процесс изготовления отливки.
Данная отливка располагается в обеих полуформах в вертикальном положении. Данное расположение обеспечивает: направленное затвердение наиболее простую литниковую систему простую сборку форм минимальные габариты форм.
Учитывая размеры отливки в форме можно расположить максимальное их количество и назначить минимальные припуски на механическую обработку.
3 Определение поверхности разъема формы
Форма имеет одну горизонтальную плоскость разъема поверхность разъема плоская.
Такая поверхность разъёма формы обеспечивает удобство формовки контроль качества сборки формы наиболее простую конструкцию модельной оснастки и формы минимальное искажение базовых поверхностей.
4 Определение припусков на механическую обработку формовочных уклонов радиусов закруглений
Величину припусков на механическую обработку определяют следующие характеристики: материал отливки; её класс точности положение поверхности при заливке габаритные размеры номинальный размер отливок.
Учитывая всё вышеизложенное выбираем согласно [6] следующие размеры припусков: торцевые поверхности 2 мм внешний диаметр 2 мм отверстие 4(2·2) мм.
Формовочные уклоны назначаем в соответствии с конфигурацией отливки [8]: 20 (наружные) радиусы закруглений: до 5 мм.
5 Графическое оформление отливки
Выполняем чертёж отливки с нанесением припусков на механическую обработку на обрабатываемых поверхностях. Отверстия не выполняемые литьём чертятся тонкой линией.
Выбираем и наносим на чертеже поверхность разъёма линией. Остаток прибыли и питателя наносятся тонкой линией.
6 Определение количества и конструкции стержней
Анализируя конструкцию отливки приходим к выводу о возможности получения внутренней полости отливки с помощью одного стержня. Стержень занимает горизонтальное положение в форме. Он имеет относительно несложную ступенчатую конфигурацию прост в изготовлении. Выбранная конструкция стержня обеспечивает: получение внутренней полости с заданной точностью удобную установку стержня допускающую просмотр и контроль размеров формы свободное удаление газов и легкое удаление стержневой массы из отливки в период её очистки механическую и термическую стойкость. Стержень имеет знаки достаточной прочности. Размеры уклоны и зазоры между знаком стержня и формой выбираем по ГОСТ 3212-93.
Стержни изготавливаются на стержневых линиях из жидких самотвердеющих смесей (ЖСС).
7 Формовочные и стержневые смеси
7.1 Формовочные смеси
Качество отливок в литейном производстве во многом определяется качеством формовочных смесей. Для отливки «Шкив привода генератора» применяем единую формовочную смесь. Состав формовочной смеси приведен в таблице 2.7.1.
Таблица 2.7.1 – Состав формовочной смеси
Составляющие формовочной смеси
Массовая доля составляющих смеси %
Суспензия бентонито-угольная
ЭКР – экструзионный крахмалосо-
В условиях автоматической формовки для приготовления формовочной смеси используем сложные системы смесеприготовления. Обычно эти системы состоят из двух комплексов: приготовления формовочной смеси и её регенерации.
Сухой песок по ленточному конвейеру подается в бункеры над бегунами. Отработанная смесь из-под выбивной решетки автоматической формовочной линии поступает на конвейер на котором собирается просыпь формовочной смеси из-под формовочных автоматов. Затем отработанная смесь поступает на ленту конвейера где подвергается магнитной сепарации над ленточным магнитным сепаратором. После этого смесь дробится и разрыхляется в рыхлителе просеивается через сито и на ленточном конвейере вторично подвергается магнитной сепарации над ленточным магнитным сепаратором. Далее отработанная формовочная смесь поступает в гомогенизационный барабан в котором увлажняется до определенной влажности. Вода в барабан подается через форсунки. Из барабана смесь поступает в охладитель испарительного типа представляющий собой камеру внутри которой движется сетчатый пластинчатый конвейер. Смесь из барабана попадает на этот конвейер и охлаждается продуваемым через нее воздухом; одновременно происходит удаление пыли из смеси. На выходе из установки смесь имеет температуру не выше 38 40°С. Далее по конвейерам и элеватору смесь поступает в бункеры над бегунами.
Из бункеров сухой песок и отработанная смесь тарельчатыми питателями подаются в бункеры-дозаторы бегунов. Бентонитоугольная эмульсия приготовляется в установках и по трубопроводам подается в бегуны. После перемешивания формовочная смесь выдается из бегунов в дозаторы. При перемешивании для охлаждения и обеспыливания смеси осуществляется ее продувка воздухом с помощью вентиляторов. Из дозаторов смесь по системе ленточных конвейеров подается в разрыхлитель пройдя через него по ленточным конвейерам поступает в бункеры над формовочными автоматами.
Физико-механические свойства смеси приведены в таблице 2.7.2.
Таблица 2.7.2 – Физико-механические свойства формовочной смеси
Прочность отверждённого образца на разрыв кгсм2
в холодном состоянии
7.2 Стержневые смеси
Для изготовления стержней применяем жидкую самотвердеющею смесь (ЖСС) при использовании которой отпадает необходимость сушки стержней а также процесс их уплотнения в стержневом ящике. Через 40 60 мин. после заливки жидкая стержневая смесь в ящике становится прочной н стержень можно извлекать из стержневого ящика.
Смеси состоят из жидкого стекла (крепитель) поверхностно-активного вещества - пенообразователя (мылящее вещество) который придает текучесть смеси отвердителя (феррохромовый шлак 2СаО*S все эти составляющие смешивают в определенных пропорциях. Принципиальная особенность ЖСС - их способность затвердевать одновременно по всему объему. Поэтому продолжительность затвердевания не зависит от размеров форм и стержней. Твердение начинается через 8 10 мин после заливки и заканчивается через 40 60 мин.
8 Разработка конструкции модели и модельных плит
8.1 Классификация моделей
Модели классифицируются по размерам. Модель отливки «Тормозной диск передний» относится к средним моделям. При проектировании данной отливки была разработана простая конструкция модели с разъёмом по плоскости проходящей через ось вращения изделия.
8.2 Выбор материала для изготовления модельного комплекта
При машинной формовке целесообразно изготавливать модели из стали (Сталь 40Х) которые предназначаются для серийного и массового производства (для изготовления мелких и средних моделей стержневых ящиков и модельных плит).
8.3 Металлические модельные комплекты
Металлические модели и стержневые ящики применяют в массовом производстве. Основными элементами металлического модельного комплекта являются модельная плита и стержневые ящики. Вспомогательными элементами являются сушильная плита вилочные съёмщики. Металлические модельные плиты делают составными и цельнолитыми.
Исходным документом при проектировании металлического модельного комплекта является чертеж отливки выполненный согласно ГОСТ 3.1125-88. По этому чертежу разрабатывают чертежи элементов металлического модельного комплекта: модельных плит моделей стержневых ящиков и т. д. При разработке чертежей металлического модельного комплекта модельных плит моделей стержневых ящиков широко используют нормали и стандарты в которых регламентированы конструкции элементов оснастки их размеры материал точность исполнения шероховатость поверхностей и т. д.
Металлические модели стержневые ящики модельные плиты рекомендуется делать тонкостенными усиливая их ребрами жёсткости. Толщину стенок моделей и стержневых ящиков назначаем по ГОСТ 19370-74.
Используем опочные модельные плиты односторонние.
Заготовки металлических моделей стержневых ящиков и плит получают литьём в песчаные формы по деревянным моделям то есть по промоделям.
Заготовки обрабатывают на обычных универсальных металлорежущих станках. После обработки резанием модели монтируют на заранее подготовленных плитах. При монтаже учитывают размеры и конструкции опок.
Модели литниковой системы монтируют на плитах после установки моделей отливки в соответствие с чертежом.
9 Разработка конструкции литниковой системы
При выборе способа подвода расплава в форму и разработке конструкции литниковой системы учитываем что расплав должен поступать в форму плавно без ударов о ее стенки и стержни без завихрений с заданной скоростью подъема уровня в форме и последовательным удалением воздуха и газов из формы. Кроме того способ подвода расплава обеспечивает направленное затвердение отливки с учетом ее конструкции и свойств сплава.
Тот или иной способ подвода расплава конструкции литниковой системы соотношение её размеров элементов назначают в зависимости от литейных свойств сплава - жидкотекучести усадки склонности к образованию трещин; конфигурации размеров массы и назначения отливки.
На основании всего вышеизложенного приходим к выводу что наиболее целесообразно использование литниковой системы с подводом металла по плоскости разъема. Она наиболее проста технологична для данного типа отливок.
К числу элементов питающей системы обеспечивающих питание отливки расплавом при затвердевании относятся питающие выпоры бобышки и прибыли.
Прибыли и питающие выпоры служат для компенсации усадки утолщённых мест отливки. Они должны располагаться над массивными частями имеют такие размеры и конфигурацию чтобы расплав в них застывал в последнюю очередь. Размеры должны быть достаточными для того чтобы компенсировать усадку отливки.
10 Определение количества моделей на плите
Отливка изготовляется на автоматической формовочной линии. Размер опоки 1000*800*300300.
Исходя из веса отливки (654кг) устанавливаем рекомендуемые минимально допустимые толщины слоя:
от верха модели до верха опоки 50 мм;
от низа модели до низа опоки 60 мм;
от модели до стенки опоки 30 мм;
между моделями 40 мм;
между моделями и шлакоуловителями 30 мм.
На основании этого принимаем 8 моделей на плите.
11 Выбор способа формовки
Для изготовления отливки «Шкив привода генератора» выбираем автоматическую линию опочной формовки. Такие формовочные линии эксплуатируются в литейных цехах машиностроительных заводов они имеют достаточно высокую производительность и надежность в эксплуатации.
Формовочная линия расположена с проездами с обеих сторон что облегчает доступ к отдельным агрегатам линии для их обслуживания замены и ремонта. Формовочная линия обслуживается непрерывно движущимся горизонтально-замкнутым тележечным конвейером Формовочная линия обеспечивается формовочной смесью от индивидуальной смесеприготовительной системы.
Формовочная линия имеет удобную компоновку которая позволяет в заданном темпе выполнять все необходимые операции. Имеется устройство для автоматической смены модельных плит на формовочном автомате без остановки линии. Изготовление форм производится встряхиванием с допрессовкой. Сборка форм заливка охлаждение производится на конвейере. Выбивка отливок производится на инерционных выбивных решетках. Перед установкой опоки модель обдувается и опрыскивается разделительным составом. Формовочная смесь поступает из стационарного бункера в бункер над формовочной машиной. В нижней части бункера имеется аэратор который разрыхляет смесь в процессе ее дозирования в опоку. Во время встряхивания излишек смеси срезается уровень срезки регулируется. Съем готовой полуформы производится строго вертикально с переменной скоростью это обеспечивает извлечение формы без повреждения. Снятая верхняя полуформа с формовочного стола последовательно поступает на позицию изготовления вентиляционных отверстий. Вентиляционные наколы снизу и сверху наносятся в заранее определенные координаты. Затем верхняя полуформа поступает в кантователь в котором переворачивается на 360° для сброса с нее излишков смеси и затем поступает на сборку.
Нижняя полуформа изготавливается аналогично верхней полуформе. Готовая нижняя полуформа поворачивается на 180° и ставится на платформу движущегося литейного конвейера по центрирующим штырям обдувается после чего осуществляется простановка стержней фильтров и т.д.
Сборка готовых полуформ производится сборщиком на движущемся литейном конвейере с применением специальных штырей которые точно ориентируют полуформы относительно друг друга. В конце хода сборки верхняя полуформа прижимается к нижней специальными цилиндрами т.к. масса верхней полуформы большая то нагружение форм или скрепление опок перед заливкой не производится.
12 Выбор способа плавки металла
Плавка стали осуществляется в электродуговых печах. Плавильные агрегаты имеют трансформаторы большой мощностью до 35000 кВт поэтому плавку можно вести в интенсивном режиме с выделением высокой мощности для расплавления шихты. Электродуговые агрегаты являются высокопроизводительными и обеспечивают выплавку стали с использованием различных шихтовых материалов.
Плавка имеет следующие преимущества: возможность получения в плавильном пространстве печи восстановительной среды угар элементов меньше меньшее содержание в печи кислорода и ведение окислительных процессов только путем подачи железной руды или кислорода вдуваемого в ванну.
При плавке стали в электродуговой печи используются следующие материалы: лом стальные отходы нелегированные возврат собственного производства ферромарганец ФМn 75-3 графит порошковый алюминий для раскисления известняк металлургический кварцевый песок.
Во время плавки стали электродуговая печь должна быть в исправном состоянии во время работы печи должен быть постоянный надзор за исправностью печи. Материалы для плавки должны находиться в закромах на расстоянии удобном для работы. Подина и откосы должны быть тщательно очищены от остатков металла и шлака осмотрены сталеваром после чего производится заправка подины и откосов кварцевым песком на жидком стекле. После заправки производят завалку шихты в печь. Перед завалкой на подину печи загружают графитовый порошок. Затем поднимают электроды и свод печи который отводится в сторону. С помощью крюка мостового крана открывают замок бадьи и загружают шихту в печь разравнивают ее специальным грузом и закрывают печь сводом.
После расплава всей шихты и прогрева жидкой ванны отбирают пробу для определения углерода. Если содержание углерода в ванне низкое то науглераживают металл чугуном. Если содержание углерода соответствует среднезаданному в готовой стали с учетом присадки ферромарганца то в ванну с учетом остаточного углерода дают по расчету кусковой ферросилиций и ферромарганец. Затем после 5 7 минут выдержки и тщательного перемешивания ванны отбирают пробу металла на раскислённость. По результатам экспресс-анализа при необходимости производят корректировку химического состава стали. Перед выпуском плавки замерить температуру металла в печи она не должна превышать 1700 °С. За пять минут перед выпуском подать ковш к печи нагретый до 800-900 °С. Плавку сливают и устанавливают ковш с металлом на стенд для раздачи металла в разливочные ковши.
Для управления процессом выплавки стали предусмотрена автоматизированная система контроля. Для плавки стали принята печь ДП-16 (см. п.1.5.2).
13 Разработка технологии заливки форм
По конструкции ковши бывают чайниковые барабанные и стопорные.
Ковш служит для транспортировки жидкого металла и заливки форм. Ковш имеет стальной кожух у которого стенки и дно изнутри выложены огнеупорным материалом. Для заливки чугуна ковш футеруют шамотом. Толщина слоя футеровки 65 180 мм.
Для заливки стали чаще применяют чайниковые ковши ковш с носком или ковш с перегородкой. В нашем случае это ковш с носком.
Ковши сушат и нагревают горелками работающие на природном газе. Ковш нагревают до 700 750°С. Ковш сразу же после прогрева заполняют расплавом.
Чугун перед разливкой должен быть очищен от шлака. В начальный момент заливки необходимо наклонять ковш плавно без рывков но достаточно быстро чтобы заполнить литниковую систему и чашу. В дальнейшем наклон ковша осуществляют с такой скоростью чтобы уровень расплава в чаше оставался по возможности постоянным. После появления расплава в чаше уменьшают скорость наклона ковша для того чтобы расплав не вытек из чаши.
14 Разработка технологии охлаждения форм выбивки обрубки очистки
После заливки формы отливка охлаждается и затвердевает. Полностью затвердевшая отливка должна определённое время охлаждаться в форме так как прочность металла при высоких температурах мала и отливка может разрушиться при выбивке её из форм.
Продолжительность выдержки отливки в форме при охлаждении до заданной температуры выбивки обуславливается длиной участка охлаждения на автоматической формовочной линии (100 минут).
Процесс выбивки отливок заключается в том что затвердевшие и охладившиеся до заданной температуры отливки извлекаются из формы. Форму разрушают а также отделяют литники и прибыли; после этого выполняют очистку наружной и внутренней поверхностей отливки от пригоревшей смеси.
Для выбивки отливок используют систему эксцентриковых выбивных решеток.
Технологический процесс очистки отливок включает следующие операции:
отделение литников;
очистка от приставшей формовочной смеси;
удаление окалины и заусенцев;
окончательный контроль качества отливок после обрубки и очистки.
Литники отделяют молотками.
Очистка отливок от пригоревшего песка и окалины осуществляется дробемётным способом.
Зачистка осуществляется абразивными материалами.
Термическую обработку отливки проводят для снижения литейных напряжений стабилизации размеров снижения твердости улучшения обрабатываемости износостойкости увеличивается ударная вязкость стали.
Для отливки «Шкив привода генератора» применяем нормализацию. Нормализацию применяют для устранения внутренних напряжений повышения механических свойств стали. Сталь после нормализации получает однородную мелкозернистую структуру. При нормализации отливки нагревают выше критической точки Ас3 для стали 35Л на 30°С затем производят выдержку при этой температуре для получения однородного аустенита. Затем отливки ускоренно охлаждают на воздухе до температуры 60°С. Прочность отливки «Шкив привода генератора» после нормализации составляет 137 197 НВ.
15 Разработка системы контроля технологии и качества отливок
Входной контроль - контроль прибывших шихтовых и формовочных материалов.
Контроль химического состава механических свойств и микроструктуры полученного чугуна.
Контроль формовочных и стержневых смесей.
Контроль моделей и полуформ верха и низа.
Контроль температуры и времени заливки.
Контроль и учёт залитых форм.
Контроль количества отливок и внешнего вида после выбивки.
Контроль после обрубки и очистки.
Контроль на соответствие чертежу отливки.
Завершающий контроль количества штук контроль внешнего вида.
16 Дефекты отливки мероприятия по предупреждению и способы исправления
Характерные дефекты для «Шкива привода генератора» - усадочные раковины шлаковые включения которые влияют на не герметичность отливки.
Усадочные раковины в отливках образуются при недостаточном питании отливки жидким металлом в процессе кристаллизации а также в утолщённых местах отливки. Для исключения данного дефекта в утолщённых местах отливки рекомендуется ставить прибыли изменять конструкцию отливки выравнивать толщину её стенок.
Шлаковыми называются включения имеющие вид и состав шлака. Чаще всего шлаковые включения расположены в верхних частях отливок или на их поверхности. Оставшиеся после удаления шлака полости в теле отливки могут иметь гладкую или шероховатую поверхность с неровными краями. В большинстве случаев серого цвета различных оттенков. Для удаления шлака из металла его перегревают и выдерживают в ковше для всплытия неметаллических включений и растворенного газа используют шлакоулавливающую литниковую систему.
Для уменьшения потерь от брака в ряде случаев производят исправление дефектов отливок. Заварку применяют для исправления дефектов отливок.
17 Расчет литниково-питающей системы
Объём отливки определяем по чертежу Vотл = 835·10-4 м3.
Плотность материала отливки (сталь 35Л ρс = 7830 кгм3).
Тогда масса отливки:
mo = ρо·Vотл = 7830·835·10-4 = 654кг (2.1)
Расчёт литниковой системы для отливки «Шкив привода генератора» сводится к определению площадей сечений и размеров питателей шлакоуловителя стояка.
Постоянство весовой скорости потока расплава за весь период заливки форм можно выразить уравнением:
где Gв - весовая скорость заливки кгс;
F - площадь контакта см2;
f = 00525 кг(с·см2) - фактор растворения.
Большое значение имеет при этом зернистость модификатора и его реакционная способность.
Расчет литниковой системы производится по способу Озанна-Диттерта.
Суммарная площадь сечений питателей:
ΣFп = М[ρ·t··√(2·g·Hp)] = 52300[70·23·042·√(2·g·277)] = 332 см2 (2.3)
где М = 523 кг = 52300 г - масса отливок в форме г;
ρ = 70 гсм3 - плотность расплава;
= 042 - коэффициент расхода литниковой системы;
Средняя толщина стенки отливки = 30мм.
Продолжительность заливки формы:
t = 2·3√(·М) = 2·3√(30·523) = 23 с
Расчетный напор металла:
Нр = Н - Р2(2·С) = 30 - 972(2·194) = 276см (2.4)
где Н = 30 см - высота стояка от места подвода расплава в форму;
Р = 97 см - высота отливки от места подвода расплава;
С = 194 см - высота отливки.
Площадь сечения одного питателя:
Fп = ΣFпno = 33216 = 207 см2 = 207 мм2 (2.5)
Лимитирующим при расчёте литниковой системы является время заливки одной формы. Так же при расчёте литниковой системы необходимо знать следующие соотношения проходных сечений литниковой системы [44].
Fст = 11·ΣFп15 = 11·33215 = 243 см2 = 2430 мм2 (2.6)
Площадь шлакоуловителя:
Fшу = 11·ΣFп13 = 11·33213 = 281 см2 = 2810 мм2 (2.7)
Масса модификатора 1% от массы жидкого металла на ковш кг.
mмод = (1·1200)100 = 12 кг (2.8)
dст = √(4·Fст) = √(4·2430) = 556 мм 56 мм (2.9)
Для обеспечения плотности фланца отливки устанавливаем на ней прибыль открытую конусную.
Средний диаметр прибыли можно принять равным толщине фланца Dп = 40мм.
Высота прибыли от фланца до верха формы Нп = 203 мм.
Тогда объём прибыли:
Vп ·Dп2·Нп 4 = ·0042·02034 = 255*10-4 м2 (2.10)
mп = ρс·Vп = 7830·255·10-4 = 200 кг (2.11)
Масса прибыли от массы отливки 2654 = 031 или 31% что с лихвой компенсирует усадку стали 35Л (~2%).
18 Нововведения в технологии
Нововведением в технологической части является добавление в литниковую систему кремнезёмной сетки для фильтрации расплава: задержания неметаллических включений (например осыпи формовочой смеси) и газов. Несмотря на то что это мероприятие вносит небольшие дополнительные расходы на изготовление отливки но благодаря уменьшению брака по раковинам пригарам и неметаллическим включениям и как следствие увеличению выхода годного эти расходы окупаются.
Кремнеземные материалы имеют низкую теплопроводность высокую стойкость к тепловому удару обладают превосходными электроизоляционными свойствами при высоких температурах могут длительно использоваться без изменения свойств при температуре 1000ºС (на новом материале Puresil до 1200ºС) и кратковременно при более высоких температурах (не плавятся не испаряются при температурах до 1700ºС). Изделия из кремнеземного стекла чрезвычайно инертны к большинству химических реагентов стойки к органическим и минеральным кислотам любых концентраций даже при повышенной температуре (за исключением плавиковой фосфорной соляной) и слабым щелочам расплавленных металлов (кроме Mg Na Si) и сплавам. Обладают высокой химической стойкостью к воде и пару высокого давления способны поглощать влагу но не расщепляются в присутствии воды стабильны в вакууме.
Кремнеземные сетки применяются в качестве эффективного фильтровального материала для очистки расплавов черных и цветных металлов при их заливке в литейные формы.
Фильтр необходимого размера вырезается и устанавливается в литниковую систему или непосредственно под литник между нижней и верхней опоками литейной формы.
Спецификации План цеха.doc
Линия формовочная ИЛ225
Печь отжига ферросплавов
Бункер свежего песка
Печь подогрева шихты
Барабан дробеметный
Проектирование специализированного цеха мелкого стального литья мощностью 10 тыс.т в год
Приложение приложения А
Автомат газированной воды
Бункер отработанной смеси
Будка электрооборудования
Тележка передаточная
Короб магнитных отходов
Короб немагнитных отходов
Кран мостовой Q=205т
Спецификации Разрез цеха.doc
Печь отжига ферросплавов
Печь подогрева шихты
Кран мостовой Q=205т
Тележка передаточная
Проектирование специализированного цеха мелкого стального литья мощностью 10 тыс.т в год
Цех СЛ 40000 в2.docx
Федеральное государственное автономное образовательное
учреждение высшего образования
Казанский (Приволжский) федеральный университет
ВЫПУСКНАЯ КВАЛИФИКАЦИОННАЯ РАБОТА
студента группы 1151109 Шнырёва А.А.
На тему: «Проектирование цеха стального литья с производственной мощностью 40 000 тонн годного в год»
Пояснительная записка на 112 листах
Графическая часть на 9 листах
Руководитель: Заведующий кафедрой
Андреев А. П. Шибаков В. Г.
По экономической части: Андреев А. П.
По технологической части: Андреев А. П.
По БЖД: Андреев А. П.
Набережные Челны 2019
Студент Шнырёв А. А. предварительную защиту
Аннотация студента группы 1151109
Шнырёва А. А. на тему дипломного проекта:
Проект цеха стального литья производственной
мощностью 40 тысяч тонн годного в год.
Проект содержит 112 страниц пояснительной записки.
Графическая часть выполнена на 9 листах формата А1.
В разделе "Расчетно-проектная часть" спроектирован цех на выпуск 40 000 тонн годного стального литья в год и рассчитано необходимое количество технологического оборудования цеха.
В разделе "Технологическая часть" описан технологический процесс получения отливки " Шкив привода генератора " из материала Сталь 35Л ГОСТ 977-88 и приведены расчеты литниковой системы для получения этой отливки.
В разделе "Технико-экономическая часть" произведен расчет затрат на производство и расчет капитальных вложений и срока окупаемости проекта.
В разделе "Безопасность жизнедеятельности и экологии" даны требования по обеспечению комфорта на рабочем месте описаны защита от негативных факторов производственной среды обеспечение безопасности труда на рабочем месте а также мероприятия по повышению устойчивости функционирования в условиях чрезвычайных ситуаций.
Раздел 1 Расчетно-проектная часть . .8
1 Расчет производственной программы ..9
2 Расчёт мощности литейного цеха 10
3 Режим работы цеха и фонды времени 11
4 Общая компоновка цеха и описание принятого технологического процесса . 14
4.1 Определение состава цеха. Выбор типа производственного здания вспомогательных и административно-бытовых корпусов 14
4.2 Служебно-бытовые помещения . 15
5 Расчет плавильного отделения ..17
5.1 Баланс металла по выплавляемым маркам ..17
5.2 Выбор типа плавильного агрегата 19
5.3 Расчет количества плавильных агрегатов 20
5.4 Расчет шихты 20
6 Расчет формовочно-заливочного отделения 21
6.1 Расчет производственной программы отделения .22
6.2 Расчет технологического оборудования формовочного отделения 24
7 Расчет стержневого отделения ..26
7.1 Расчет производственной программы отделения .27
7.2 Расчет количества стержневых машин ..29
8 Термообрубное отделение . 30
8.1 Технологический процесс термофинишной обработки. .31
8.2 Расчет количества оборудования 31
9 Складское хозяйство . ..32
10 Оборудование цеха 34
11 Расчет рабочей силы 36
Раздел 2 Технологическая часть ..40
1 Выбор способа изготовления отливки ..41
2 Выбор положения отливки в форме в период заливки и затвердения ..41
3 Определение поверхности разъема формы .42
4 Определение припусков на механическую обработку формовочных
уклонов радиусов закруглений .42
5 Графическое оформление отливки 42
6 Определение количества и конструкции стержней 42
7 Состав и свойства формовочной и стержневой смеси 48
7.1 Формовочная смесь .49
7.2 Состав стержневой смеси 50
8 Разработка конструкции моделей стержневых ящиков и модельных плит. .43
9 Разработка конструкции литниково-питающей системы .45
10 Определение количества моделей на плите. .46
11 Выбор способа формовки 47
12 Выбор оборудования и описание технологического процесса плавки сплава .52
13 Разработка технологии заливки форм .54
14 Охлаждение отливки в форме. Оборудование и технологический процесс выбивки обрубки очистки зачистки термической обработки отливки .. 55
15 Разработка системы контроля технологии и качества отливок 56
16 Дефекты отливки мероприятия по предупреждению и способы исправления . 57
17 Расчет литниковой системы 58
18 Нововведения в технологии. ..59
Технико-экономическая часть 56
1 Расчёт производственной программы ..56
2 Расчет выручки от реализации .57
3 Расчет затрат на покупные сырья и материалы .59
4 Планирование труда и заработной платы 62
5 Определение затрат на оборудование здания и сооружения 63
6 Определение себестоимости единицы продукции 65
7 Нормируемые текущие активы . 66
8 Нормируемые краткосрочные пассивы . 68
10 Отчет о движении денежных средств .69
11 Основные показатели проекта .70
Безопасность жизнедеятельности ..71
1 Требования по обеспечению комфортности на рабочем месте 86
2 Защита от негативных факторов производственной среды ..94
2.2 Акустические колебания
2.2.2 Ультразвук ..96
2.3 Защита от электромагнитных полей и излучений . 97
2.4 Защита от пожарной опасности .. 99
2.5 Защита от электрического тока ..101
3 Обеспечение безопасности труда на рабочем месте 101
4 Мероприятия по повышению устойчивости функционирования предприятия в чрезвычайных ситуациях .. 102
5 Подготовка и проведение спасательных работ при возникновении очага поражения ..103
6 Краткий итог по разделу БЖД .. . 104
В последние годы выпуск отливок из стали как в нашей стране так и во всем мире несколько стабилизировался и находится на самом высоком уровне.
Однако несмотря на это наше машиностроение почти постоянно испытывает дефицит в стальных отливках. Одновременно сложившаяся ситуация свидетельствует и о довольно больших технических возможностях стальных отливок для использования их в качестве заготовок для деталей всевозможных машин.
Стальные отливки используемые в самых различных областях техники и машиностроения отличаются исключительным разнообразием условий в которых им приходится работать. В соответствии с этим предъявляются и требования к их качеству и надежности в работе.
Целью данного проекта являлось проектирование литейного цеха для производства 40 000 т годных отливок из стали в разовые песчано-глинистые формы.
Проект содержит следующие разделы записки.
Расчет и проектирование литейного цеха включая:
а) расчет производственной программы;
б) расчет мощности литейного цеха;
в) режим работы и фонды времени;
г) расчет плавильного отделения;
д) расчет формовочно-заливочного отделения;
е) расчет стержневого отделения;
ж) расчет термообрубного отделения;
з) расчет рабочей силы.
Технологическая часть включает:
а) выбор способа получения отливки;
б) анализ конструкции;
в) технологический процесс получения отливки.
Технико-экономическая часть включает:
а) состав годовой сметы затрат на производство 1 тонны жидкого расплава;
б) составление калькуляции себестоимости 1 тонны жидкого расплава;
в) расчет себестоимости 1 тонны годных отливок;
г) расчет капитальных вложений на строительство цеха;
д) составление таблицы технико-экономических показателей цеха;
е) расчет эффективности и срока окупаемости проекта.
Раздел безопасности жизнедеятельности и экологии включает:
а) характеристика цеха с точки зрения опасных и вредных производственных факторов;
б) расчет зануления оборудования;
в) описаны основные принципы гражданской обороны и проведения неотложных спасательных работ в чрезвычайных ситуациях.
Графическая часть проекта содержит 9 чертежей формата А1:
а) планировку цеха.
в) комплект модельной оснастки низа и верха.
г) технико-экономические показатели.
Программа предусматривает производство 40 000 тонн годных стальных отливок.
Номенклатура отливок составляет 35 шт.
РАСЧЕТНО-ПРОЕКТНАЯ ЧАСТЬ
1 Расчет производственной программы
Производственная программа годового выпуска отливок цеха стального литья рассчитывается на 40000 тонн годного литья. Последовательность расчета производственной программы литейного цеха машиностроительного завода представлена в таблице 1.1.
Таблица 1.1 Номенклатура отливок изготавливаемых в цехе стального литья.
Годовой выпуск отливок4
Шифр детали принят в соответствии с отраслевым кодированием.
детали взята по конструкторскому чертежу.
Массу отливки определяем перемножением массы детали на коэффициент использования литой заготовки.
Годовую программу выпуска отливок принимаем согласно заданию (40000 т).
2 Расчет мощности литейного цеха
Расчет проектной мощности литейного цеха производится исходя из потребности в литье на основную программу потребности в запасных частях поставок по кооперации резерва мощности литья для собственных нужд.
При расчете проектной мощности цеха учитываются мощности необходимые для создания переходных заделов компенсации брака литейного цеха и механических цехов.
Выпуск жидкого металла:
Вж = Впр·(1 + Кз + Кб + Кбм)Кгод =
= 40000·(1 + 0015 + 005 + 0005)063 = 67936т 67900 т (1.1)
где Впр = 40000 т - программа производства (по заданию);
Кз = 0015(0008 0015) - коэффициент учитывающий нормативные заделы литья. В цехах серийного и мелкосерийного производства принимается двух-трех суточный задел литья.
Кб = 005 - коэффициент учитывающий нормативный брак при отливке заготовок;
Кбм = 0005 - коэффициент учитывающий нормативный брак при механической обработке;
Кгод = 063 - коэффициент учитывающий средний выход годного литья к залитому в форме по данной номенклатуре.
Результаты заносим в таблицу (таблица 1.2).
Таблица 1.2 Проектная мощность цеха.
Выпуск жидкого металла
3 Режим работы цеха и фонды времени
Принятые режимы работы отделений цеха приведены в таблице 1.3.1.
Таблица 1.3.1. Режимы работы отделений цеха
Наименование отделений
Продолжительность смены
Смесеприготовительное №1 (формовочного участка)
Смесеприготовительное №2 (стержневого отделения)
Формовочно-заливочно-выбивное
Продолжительность ночной (третьей) смены сокращается на один час
Определяем фонды времени.
Число рабочих дней в 2019 году Дрг = 247 [46];
Число сокращённых (предпраздничных) рабочих дней в 2019 году Дсрг = 6 [46];
Фонд времени рабочего места:
Фрм = nC·(Дрг·TC - Дсрг) (1.2)
Для шихтового двора плавильного формовочно-заливочно-выбивного стержневого и смесеприготовительных отделений:
Фрм = 2·(247·8 - 6) = 3940 ч.
Для термообрубного отделения:
Фрм = 2·(247*8 - 6) + (247·7 - 6) = 5663 ч.
Действительный фонд работы оборудования:
Коэффициент использования оборудования:
Ко = 1 - (К1 + К2 + К3 + К4) (1.4)
где: К1 - коэффициент учитывающий остановку оборудования на ремонт;
К2 - потери рабочего времени на переналадку оборудования;
К3 - коэффициент организационных потерь;
К4 - коэффициент на возмещение брака.
Плавильное оборудование.
К1 = 01; К3 = 012; К4 = 005;
Ко = 1 - (01+012+005) = 073;
Фро = 073·3940 = 28762 ч.
Формовочное и смесеприготовительное оборудование.
К1 = 01; К2 = 005; К3 = 012; К4 = 005;
Ко = 1 - (01 + 005 + 012 + 005) = 068;
Фро = 068·3940 = 26792 ч.
Стержневое оборудование.
Термообрубное оборудование (термопечи зачистные станки дробеметные барабаны).
Фро = 073·5663 = 41340 ч.
Годовой фонд времени рабочего:
Фрг = К5·ФрмnC (1.5)
где К5 - коэффициент учитывающий потери рабочего времени в связи с болезнью тарифным отпуском.
На вредных работах (заливка выбивка окраска плавка) при 24 рабочих днях отпуска К5 = 0885.
Стержневые формовочные отделения и другие при 18 рабочих днях отпуска
Годовые фонды времени рабочего по отделениям:
Фрг1 = 0896·39402 = 17651 ч;
Фрг2 = 0885·39402 = 17435 ч;
Фрг3 = 0896·39402 = 17651 ч;
Фрг4 = 0896·39402 = 17651 ч;
Фрг5 = 0896·39402 = 17651 ч;
Фрг6 = 0896·39402 = 17651 ч;
Фрг7 = 0885·56633 = 16706 ч;
Результаты оформляем таблицей (Таблица 1.3.2).
Таблица 1.3.2. Фонды времени.
4. Общая компоновка цеха и описание принятого технологического процесса
Сталилитейный цех состоит из следующих основных подразделений:
) плавильное отделение;
) смесеприготовительный участок формовочно-заливочно-выбивного отделения;
) смесеприготовительный участок стержневого отделения;
) формовочно-заливочно-выбивное отделение;
) стержневое отделение;
) термообрубное отделение с участками обрубки очистки термообработки заварки дефектов окраски испытания и контроля отливок;
) участок ремонтных служб механического оборудования;
) вентиляционный участок объекты вентиляционного оборудования;
) участок технического контроля;
) склады огнеупоров смол формовочных и вспомогательных материалов;
) лаборатории экспресс-анализа и испытания;
) административно-бытовые помещения.
4.2 Выбор типа производственного здания вспомогательных и административно–бытовых корпусов
Проектируемый цех имеет прямоугольную форму здания одноэтажного исполнения. Все здания спроектированы в металлическом каркасе и должны быть выполнены из унифицированных типовых секций. Наружные стены выполнены из керамзитных и бетонных панелей.
Принимаем литейный цех с двумя производственными пролётами шириной
В1 = В2 = 24 м высотой Н1 = 150 м Н2 = 108 м и одним административно-бытовым пролётом В3 = 9м высотой Н3 = 72м.
Согласно нормативам принимаем шаг сетки колонн 12м.
Производственная площадь 20000 м2.
Административно-бытовой корпус расположен на расстоянии 6 м от здания цеха и соединен с ним крытыми галереями.
Площадь административно-бытовых помещений 2530 м2.
Общие габариты производственного корпуса цеха В·Н = 48·204 м.
4.3 Служебно-бытовые помещения
В состав вспомогательных помещений входят: помещения бытового санитарно-гигиенического обслуживания медицинского обслуживания общественного питания помещения культурно-массового обслуживания и общественных организаций административных и технических служб. Площадь вспомогательных помещений и их оборудование принимается по укрупненным показателям исходя из количества работников цеха:
А = 205 чел.- списочное количество работающих во всех сменах;
В = 86 чел.- явочное количество работающих в наиболее многочисленной смене;
С = 47 чел. - количество служащих и ИТР.
Расчёты оформляем таблицей (таблица 1.4).
Таблица 1.4. Характеристики вспомогательных помещений цеха.
Наименование помещения
Расчетный показатель
Все вспомогательные помещения
Гардеробно-душевой блок
- количество шкафчиков
- количество умывальников
Душевые в составе гардеробно-душевого блока
- площадь преддушевых
Туалеты в составе гардеробно-душевого блока
Комнаты отдыха в цехе
Таблица 1.4. Продолжение.
Пункт первой медицинской помощи
- количество посадочных мест
- площадь произв. помещений
Культурно-массовый сектор
Административно-технические службы
- технические службы
5 Расчет плавильного отделения
Проектирование и расчет плавильного отделения литейного цеха заключается в определении следующих параметров:
) баланс металла по выплавляемым маркам;
) тип плавильного агрегата;
) количество плавильных агрегатов;
) расход шихтовых материалов на годовой выпуск литья;
) планировка отделения (участок плавки участок выдержки шихтовый двор огнеупорный участок).
5.1 Баланс металла по выплавляемым маркам
Рассчитываем потребности металла по маркам и определение металлозавалки.
Необходимое количество жидкого металла по маркам определяется по данным таблиц 1.1 и 1.2 с учетом принятого брака в соответствии с таблицей 1.5.1.
Таблица 1.5.1. Расчет количества жидкого металла и металлозавалки.
Угар и безвозвратные потери (5%)
Всего металлозавалки
Литейного цеха (5% от выпуска годного)
Механообрабатывающих цехов (05% от выпуска годного)
Сталь 35Л ГОСТ 977-88
В разовые песчано-глинистые формы
В таблице 1.5.1 данные для столбцов 4 6 берутся из таблицы 1.2. Угар и безвозвратные потери задаём в зависимости от предполагаемого способа выплавки и типа плавильного агрегата (дуговая электропечь). Угар при плавке металла в дуговых электропечах принимаем 5%.
Сливы и скрап принимаем из расчета 2%. Столбец 11 подсчитывается как сумма столбцов 5 10.
На основании расчета металлозавалки составляем баланс металла по выплавляемой марке (таблица 1.5.2).
В соответствии с балансом металла рассчитываем потребность в жидком металле (таблица 1.5.3).
Таблица 1.5.2. Баланс металла по выплавляемой марке.
Состав металлозавалки
Угар и безвозвратные потери
Итого металлозавалки Qмз
Таблица 1.5.3. Потребность в жидком металле.
Угар и безвозвратные потери
Потребность в жидком металле
Годовая потребность в жидком металле рассчитывается как разность между металлозавалкой и годовой массой угара и безвозвратных потерь. Средняя потребность в месяц получается делением годовой потребности на количество месяцев в году (12) в смену на количество смен (2·247 = 494) в час на количество рабочих часов (3940).
5.2 Выбор типа плавильного агрегата
В машиностроительной промышленности непрерывно расширяется использование электропечей для плавки стали.
В сравнении с традиционными плавильными агрегатами в литейных цехах такими как индукционными электропечами дуговые электропечи имеют целый ряд принципиальных металлургических отличий.
Прежде всего – это получение активного шлака и возможность менять его свойства в широких пределах это получение зон с особо высоким перегревом относительно большим градиентом температур. Роль и влияние огнеупорной футеровки в дуговых электропечах также значительно выше чем в индукционной печи. Эти обстоятельства оказывают влияние на угар компонентов шихты и особенности структурообразования в отливках содержание в них газов примесей что в свою очередь также сказывается как на первичной так и на вторичной кристаллизации стали. В сумме это определяет эксплуатационные свойства отливок.
При электроплавке возможно получение экономической эффективности за счет снижения стоимости шихтовых материалов снижения брака литья и повышения эксплуатационных свойств стали в отливке.
Также необходимо отметить что плавка стали в дуговых электропечах легко поддается автоматизации.
Исходя из вышеизложенного принимаем дуговую печь постоянного тока производстваООО «НПФ КОМТЕРМ» ДП-16 ёмкостью Gп = 16 т.
Комплекс патентованных решений для дуговых электропечей постоянного токапозволяет по сравнению с дуговыми печами переменного тока снизить: расход графитированных электродов до 15 кгтонну (вместо 6 7 кгтонну) угар металла до 2 5% расход ферросплавов на 15 20% пылевыбросов в 6-8 раз и фликер-эффекта на 50%.
- сокращение расходов на электроснабжение до 15% за счет более полного использования установленной мощности электрооборудования;
- сокращение времени плавки за счет увеличения эффективности использования установленной мощности источника питания;
- снижение потребления реактивной мощности за счет работы с высоким коэффициентом мощности (cosφ = 095);
- отсутствие необходимости установки фильтро-компенсирующих устройств для питающей сети (экономия не менее 10% от затрат на установку печи).
Дуговые электропечи оснащаются современными системами автоматизированного управления (САУ) которые обеспечивают: контроль параметров и управление электрическим режимом плавки с учётом технологических факторов; контроль и управление весодозирующим комплексом системы интенсификации плавки исполнительных механизмов электропечи; контроль параметров водоохлаждаемых элементов электропечи; контроль и управление системой удаления и очистки газов; визуализацию процесса плавки и работы оборудования электропечей; регистрацию паспортизацию и архивирование технологических параметров при работе электропечи.
Преимущества современных дуговых плавильных печей постоянного тока типа ДП перед индукционными:
- использование горячего активного шлака для десульфурации дефосфации и других металлургических процессов;
- либеральные требования к используемой шихте по влажности и химическому составу
- выше тепловой и электрический КПД (> 90%) коэффициент мощности;
- ниже удельный расход электроэнергии; высокая стойкость футеровки (до 2000 плавок и более);
- не требуется «болото» простая ликвидация «козла»;
- одноразовая загрузка всей шихты без тщательной сортировки по размеру.
Таблица 1.5.4. Технические характеристики электродуговой печи ДП-16 [47;48].
Мощность трансформатора Pт кВ·А
Напряжение питающей сети U кВ
Диаметр графитированного электрода dэ мм
Число подовых электродов nэ
Номинальная емкость Gп тонн
Время расплавления чугуна Тп мин.
Удельный расход электроэнергии Сэ кВт·чт
Производительность печи Пп тч
Расход воды на охлаждение Qв м3ч
Габариты печи Д·Ш·В м
Общий вид и компоновка оборудования дуговой печи даны на рисунке 1.1.
Рисунок 1.1. Общий вид и компоновка дуговой печи постоянного тока.
- кожух (ванна) печи с установленными подовыми электродами; 2 - свод печи;
-портал; 4 - сводовый электрод; 5 -люлька; 6 - загрузочное устройство; 7 -электрогидравлический механизм наклона печи; 8 - электропечной трансформатор; 9 - токоподвод переменного тока; 10 - выпрямитель; 11 - короткая сеть (токоподвод постоянного тока); 12 - реактор; 13 - теплообменник; 14 - фундамент печи; 15 - рабочая площадка; 16 - пульт наклона печи; 17 - комплект электротехнических шкафов и САУ печи.
5.3 Расчет количества плавильных агрегатов
Расчет количества плавильных агрегатов производится исходя из потребности жидкого стали коэффициента использования оборудования во времени часовой производительности плавильного агрегата планового фонда времени и режима работы печи.
Определение количества печей на выпуск расчетного количества жидкой стали по конкретной марке сплава может производиться по формуле:
Nпр = 60·Qмз·Кн(Пп·Фро) = 78060·12(175·28762) = 186 (1.6)
Принимаем Nп = 2 шт.
Коэффициент загрузки печи:
Кзп = NпрNп = 1862 = 093
Таблица 1.5.5. Потребное количество плавильных печей.
Потребное количество жидкого металла т
Номинальная емкость
Производительность печи Пп
Расчет шихты заключается в определении среднегодовых норм расхода отдельных составляющих шихты исходя из баланса металла и требований выплавки нужных марок металла.
Расчет шихты ведется в следующий последовательности:
Из норм баланса шихты определяем количество возврата собственного производства образующегося по каждой марки сплава в расчете на 1т. годного литья и 1т. жидкой стали. Задаемся допустимым пределом применения стального лома для стального литья по условиям технологии плавки конструкции печи и требований к отливкам.
Допускаем применение стального лома при плавке в дуговых печах до 60 %. Остальными компонентами шихты задаемся стремясь к минимальному расходу литейных и передельных чушковых чугунов и максимальному использованию стального лома.
Расчет шихты на тонну жидкого металла приведён в таблице 1.5.6.
Таблица 1.5.6. Расчет шихты на 1 т. жидкой стали.
Наименование материала
В кг на 1 т. годного
Лом стали (бойизлом)
Возврат собств. пр-ва
Расчет кокса и модификаторов дан в таблице 1.5.7.
Таблица 1.5.7. Расчет кокса и модификаторов.
Графит гранулированный
Лигатура собственная
6 Расчет формовочно-заливочно-выбивного отделения
Проектирование и расчет формовочно-заливочно-выбивного отделения состоит из следующих разделов:
- расчет производственной программы отделения;
- выбор и обоснование принятых методов изготовления форм режимов заливки форм охлаждение отливок и методов выбивки форм;
- выбор обоснование характеристика и расчет технологического оборудования для изготовления форм их заливки и выбивки;
- расчет парка опок и потребности в прочей технологической оснастке;
- выбор и расчет транспортно-технологического оборудования;
- организация рабочих мест на участках формовки заливки и выбивки;
- планировка отделения с размещением оборудования.
Связь технологических операций осуществляется конвейерным транспортом.
Площадь механизированных формовочных отделений определяется по фактическому расположению оборудования с учетом проходов и норм обслуживания мест для оперативного складирования оснастки а также площадей находящихся в необслуживаемых кранами зонах (по 1 15 м вдоль каждого ряда колонн и по 3 4 м с торцов пролетов).
6.1 Расчет производственной программы отделения
Для расчета производственной программы отделения отливки группируем по маркам сплавов габаритам сложности (таблица 1.6.1). В соответствии с группировкой выбираем тип формовочного оборудования. Применяем для формовки формовочную смесь для литья(8..10% глины 05 1% каменного угля 4 6% воды остальноекварцевый песок) плотность уплотнённой смеси ρс = 18 тм3 [16;17].
Размеры опок Д·Ш·В = 1000·800·300300 мм.
Объём смеси в форме примерно равен объёму формы:
Vсф Vф = Д·Ш·2·В = 1·08·2·03 = 048м3 (1.7)
Таблица 1.6.1. Расчет программы формовочно-заливочно-выбивного отделения литейного цеха.
Годовая программа выпуска отливок на основную программу и запчачти
Количество отливок в форме шт.
Количество форм в год шт.
Объем смеси в форме
Объем смеси на годовую программу и запчачти м3
Масса смеси на годовую программу и запчачти mсоп т
6.2 Расчет технологического оборудования формовочного отделения
Учитывая что годовая программа Пг = 40000 тгод годного литья получаем
количество форм в год с учётом 5% брака:
nфг = nфоп095 = 338970095 = 356811 (1.8);
масса смеси на годовую программу выпуска отливок с учётом 5% брака:
mсг = mсоп095 = 292870095 = 308284 т (1.9).
Принимаем формовочную линию модели Л450. Характеристики линии:
- производительность расчетная Пфл = 240формчас;
- размеры опок в свету 1000×800×300300мм;
- габаритные размеры 105000×15800×6150мм:
- коэффициент загрузки линии kфл = 085 09;
- установленная мощность Nл =450кВт
- число рабочих обслуживающих линию в одну смену Nр = 6;
- усилие прессования Рп = 1250кН;
- давление прессования pп МПа:
на площадь опоки 15;
на площадь колодок 197;
- расход формовочной смеси 200м3ч.
Необходимое количество формовочных линий:
Nфл = nфг(kфл·Пфл·Фро) = 356811((085 09)·240·26792) = 062 065 (1.10)
Реальный коэффициент загрузки линии:
kфл = nфг(Nфл·Пфл·Фро) = 356811(1·240·26792) = 055 (1.11)
меньше нижнего предела (085) но производительность линии можно уменьшить за счёт изменения количества формовочных машин.
Рисунок 1.2.Планировка комплексной автоматической линии типа Л450
и 2 - формовочная установка 3019; 3 - распаровщик; 4 - центральный пульт управления; 5 - каретка силовых гидроцилиндров литейного конвейера; 6 - рольганг; 7 - устройство передачи верхних опок к формовочному автомату; 5 - устройство для замены модельных комплектов; 9 - брикеты на конвейере охлаждения; 10 - охладительный тоннель; 11 - место заливки; 12 - укладчик грузов; 13 - механизм накалывания вентиляционных каналов; 14 - кантователь верхних полуформ; 15 - сборщик форм; 16 - стержнеукладчик; 17 - устройство передачи нижних полуформ на литейный конвейер; 18 - устройство для срезания излишка смеси; 19 - тележка конвейера; 20 - устройство для очистки тележек; 21- устройство для передачи залитых форм с литейного конвейера на выбивку; 22 - охладительный конвейер; 23 - тоннель интенсивного охлаждения; 24 - толкатель брикетов на выбивку; 25 - выбивная решетка; 26 - толкатель брикетов на конвейер охлаждения; 27 - установка выдавливания брикетов с отливками из опок; 28 - устройство передачи комплекта пустых опок; 29 - литейный пульсирующий конвейер; 30 - кантователь нижних полуформ.
Количество смесителей для формовочного отделения (смесеприготовительное отделение №1):
Годовой расход формовочных смесей с учётом 5% производственного брака: mсг = 308284 т (см. формулу 1.8).
Принимаем смеситель вихревой модели S1426.
Вихревой смеситель - современное смесеприготовительное устройство использующее принцип равномерного распределения связующего в объеме смеси при интенсивном разнонаправленном поступательно-вращательном движении. Имеет три независимых рабочих органа: активатор и две вихревые головки.
Рисунок 1.3.Смеситель вихревой.
Характеристики смесителя S1426:
- производительность Псм = 140 тч;
- мощность активатора Ра = 132 кВт;
- мощность вихревой головки Рвг = 2·55 кВт;
- мощность смесителя Рс = 242 кВт;
- диаметр чаши d = 2500 мм
- масса смесителя m = 28 т;
- коэффициент загрузки kсм = 07 085.
Необходимое количество смесителей:
Nсм = mсг(k·Псм·Фро) = 308284(085·140·26792) = 096 (1.12)
Действительный коэффициент загрузки смесителя:
kсм = mсг(Nсм·Псм·Фро) = 308284(1·140·26792) = 082 (1.12)
7 Расчет стержневого отделения
7.1 Расчет производственной программы отделения
Расчет стержневого отделения производим в зависимости от программы отделения с учетом количества массы и габаритов стержней их сложности процента брака состава стержневой смеси и т.п. (см. таблицу 1.7.1).
Таблица 1.7.1 - Расчет годовой программы стержневого отделения.
Шифр и наименование детали
стержней на основную программу и запчачти шт.
стержней на основную программу и запчачти т.
Количество стержней в ящике шт
Количество съёмов на
основную программу и запчачти шт.
740-1307015-20 Корпус
740-1005120-91 Муфта
740-1008022 Коллектор
740-1011021-01 Корпус
5320-3103015 Ступица
5320-3501124 Кронштейн
740-1005120-91 Маховик
5320-3501125 Кронштейн
51-7029-5046-021 Корпус
51-7029-5044-021 Корпус
4310-2303019 Чаша диф.
4310-2303018 Чаша диф.
5511-2918072 Башмак
267.100.0001.00 Корпус
5320-3502124 Кронштейн
7.2. Расчет количества стержневых машин.
количество съёмов в год с учётом 5% брака:
nсг = ncоп095 = 350727095 = 369186 (1.13);
масса стержневой смеси на годовую программу выпуска отливок с учётом 5% брака:
mсг = mсоп095·ПгвПог = 11099095 = 11683 т (1.14).
Принимаем автоматизированную стержневую линию на базе пескодувных стержневых полуавтоматов с продувкой СО2 модели Л16С.
Характеристики линии [22]:
- производительность расчетная Псл = 110 съёмовчас;
- размеры стержневого ящика 630×500×(300 450) мм;
- габаритные размеры 8000×5000×3500 мм:
- коэффициент загрузки линии kсл = 07 085;
- установленная мощность Nл =45 кВт.
Необходимое количество стержневых линий при коэффициенте неравномерности потребления стержней kн = 12:
Ncл = ncг(kсл·Псл·Фро) = 369186·12((07 085)·110·26792) = 177 215
kсл = nсг·kн(Nсл·Псл·Фро) = 369186·12(2·110·26792) = 075 (1.15)
Рисунок 1.4.Схема автоматизированной стержневой линии Л16С.
- пескодувная машина; 2 -поворотно-вытяжная машина; 3 - установка для продувки СО2; 4 - камера очистки сушильных плит; 5 - шаговый конвейер;
- рольганг; 7 - подъемный стол; 8 - место сушки; 9 - место окраски стержней.
7.3. Расчет количества смесителей.
Принимаем установку непрерывного действия для ЖСС стационарную модели 19413.
Характеристики установки:
- производительность расчетная Псм = 6тчас;
- габаритные размеры 5700×5100×6455мм:
- коэффициент загрузки установки kсм = 07 085;
- установленная мощность Nл =219кВт.
Nсм = mсг(kсм·Псм·Фро) = 11683((07 085)·6·26792) = 085 104 (1.16)
kсм = mсг(Nсм·Псм·Фро) = 11683(1·6·26792) = 073 (1.17)
Рисунок 1.5.Схема установки для ЖСС модели 19415.
- лопастной смеситель; 2 - мешалка с дозатором; 3 - бак жидкой композиции;
- бункер песка; 5 - бункер феррохромового шлака; 6 - питатель;
- дозатор весовой; 8 - затвор.
8. Термообрубное отделение.
8.1. Ведомость термофинишных операций.
Расчет термообрубного отделения начинается с составления ведомости термофинишных операций приведенных в табл. 1.8.1.
Из общей трудоемкости изготовления отливок на долю финишной обработки приходится до 30% и более причем в очистных отделениях применяется
наибольшее количество ручного труда. Очистные работы трудно поддаются автоматизации поэтому при проектировании обрубно-очистных отделений особое внимание уделяем последним достижениям науки и техники и используем новое совершенное высокопроизводительное оборудование.
Финишная обработка отливок включает следующие операции: выбивку стержней удаление литников выпоров прибылей очистку поверхности отливок; удаление заливов приливов и других неровностей поверхности; разделку дефектных мест с целью подготовки их под заварку; исправление дефектов зачистку термическую обработку.
Выбивка стержней осуществляется на автоматической линии в формовочном отделении.
Для расчета термообрубного отделения составляем ведомость термофинишных операций таблица 1.8.1.
Таблица 1.8.1. Ведомость термофинишных операций.
Абразивная зачистка.
Шлифовально-зачистной станок.
Выбивка стержней и формовочной смеси.
Проходной дробеметный барабан непрерывного действия.
Дробеметная очистка.
Дробеметный барабан периодического действия.
Пробивка отверстий и удаление заливов.
Ручная обработка заусенец
Шлифстанок напильник.
Согласно техпроцессу.
Разбраковка сортирование.
Количество деталей на годовую программу выпуска принимаем исходя из предыдущих расчётов.
8.2. Расчет количества оборудования термообрубного отделения.
Расчет количества оборудования термообрубного отделения оформляем таблицей (таблица 1.8.2).
Таблица 1.8.2. Оборудование термообрубного отделения.
Наименование оборудования
Количество обрабатываемого литья т(щт)
Годовой фонд времени ч
Количество оборудования
Дробемётная камера непрерывного действия (среднее литьё) – первичная очистка
Печь для нормализации отливок
Камера заварки среднего литья
Пресс усилием 100 т для обрубки мелких отливок
Зачистной станок для мелкого литья
Дробемётный барабан периодического действия для мелких отливок - первичная очистка
Дробемётный барабан периодического действия для мелких отливок - вторичная очистка
Дробемётный барабан периодического действия для крупных и средних отливок - вторичная очистка
9 Складское хозяйство
Складское хозяйство литейного цеха должно обеспечить следующие основные функции:
- приемка материалов;
- подготовка материалов для использования;
- погрузка и транспортировка материалов со складов в цехе.
При определение размеров складов принимаем нормативы запасов:
- шихтовые материалы 5 дней;
- формовочные материалы 10 дней;
- горючие материалы 3 суток.
Межоперационные склады стержней должны обеспечивать хранение 7 9 часового запаса стержней.
Межоперационные склады литья в термообрубном отделение должны обеспечивать хранение суточного запаса литья.
Склад готовой продукции должен обеспечивать хранение 2-3 суточного запаса литья.
Склады технологической оснастки расположены в непосредственной близости от участков на которых используется оснастка.
Характерной особенностью литейного производства является потребление большого количества исходных материалов. При поступлении в цех неподготовленных материалов на складах должны быть предусмотрены подготовительные отделения: разделки шихты дробления размола и сушки глины песка и др. Склад шихтовых материалов располагается параллельно плавильному отделению литейного цеха а склад формовочных материалов - в противоположном торце литейного цеха параллельно стержневому или обрубному отделению
Исходной базой для проектирования складов служат результаты расчетов площади закромов и всех площадей складов выполняемые в соответствии с нормами проектирования литейных цехов. Этими нормами предусматриваются: расход материалов сроки их хранения режим работы и фонд времени литейных цехов. Для всех участков складов проектируемого литейного цеха устанавливаем - параллельный трехсменный режим работы. Количество материалов хранящихся на складах определяется согласно расчетам плавильного и смесеприготовительного отделений. Расход вспомогательных материалов устанавливают на основании принятых нормативных данных по каждому виду изделия.
Площадь на проходы и проезды составляет 10 - 15% полезной площади. Склады шихтовых материалов должны иметь участки приема и хранения составления шихты дробления известняка грануляции шлака и очистки литников. Основным подъемно-транспортным средством складов шихты являются электрические мостовые краны снабженные магнитной шайбой или грейфером.
Таблица 1.9. Нормативы складов.
Техническое требование норматив
Расстояние от стенки вагона до стены при расположении вдоль железнодорожного пути закромов и бункеров
Ширина свободного прохода вдоль и поперек шихтового двора
Ширина прохода между штабелями не менее
Общая высота закрома для хранения песка и глины при механизированном оборудовании
Высота хранения шихтовых формовочных материалов и чугуна в закромах
Лом чугунный и стальной в закромах
Литники чугунные в закромах
Ферросплавы в закромах
Кокс литейный в закромах
Известняк плавиковой шпат в закромах
Песок формовочный сырой и сухой в закромах
Огнеупорные изделия в штабелях
Штабели крупных опок
Штабели мелких и средних опок
9. Оборудование сталилитейного цеха.
Номенклатура применяемого оборудования в цехе стального литья с мощностью 40000 тонн годного литья из стали в год приведена в таблице 1.9.1.
Таблица 1.9.1. Номенклатура оборудования в цехе стального литья.
Краткая техническая характеристика
Электрическая дуговая плавильная печь ДП-16
производительность 175 тч
Гидростенд для опрокидывания ковшей B22D4106
Южно-Уральский машиностроительный завод
Формовочная линия Л450
Производительность 240 формч. Размер опок
Автоматизированная стержневая линия Л16С
Производительность 110 съёмовч. Размер ящика
Заливочная установка для формовочной линии 99413
Производительность 360 формч. Время заливки 7..10 с.
Смеситель для приготовления формовочной смеси S1426.
Производительность 140 тч
Установка для ЖСС модели 19415
Производительность 6 тч
Производительность 5250 кгчас
Пресс гидравлический
Дробеметная камера для первичной очистки среднего литья 24605.
0 подвесокчас (14 тч).
г. Комсомольск-на-Амуре
периодического действия 42216 (очистка мелкого литья).
Дробеметный барабан периодического действия 42216 (вторичная очистка среднего литья).
11 Расчет рабочей силы
Расчет количества производственных и вспомогательных рабочих определяем по рабочим местам соответствующих отделений и участков в зависимости от выбранных типов оборудования и норм производительности.
Таблица 1.10.1. Расчет производственных рабочих.
Наименование профессий
Плавильное отделение
Машинисты мостовых кранов.
Оператор поста управления шихтоподачей.
Плавильщик на заливочной линии.
Плавильщик на печах плавки.
Формовочно-заливочно-выбивное отделение
Рабочий формовочной линии
Стержневое отделение
Машинист передаточной тележки.
Стерженщик на линии.
Термообрубное отделение
Таблица 1.10.2. Расчет вспомогательных рабочих.
Водитель автопогрузчика.
Слесарь по отоплению и вентиляции
Слесарь по водоснабжению и канализации
Слесарь по электрооборудованию
Водитель автопогрузчика
Слесарь по отоплению и вентиляции
Слесарь по водоснабжению и канализации
Водитель автопогрузчика
Всего рабочих - 205 чел.
Численность ИТР и служащих принимаем по нормативам [19].
Руководители 13 чел.
Другие служащие 10 чел.
Рабочие-контролеры 13 чел.
Служащие-руководители 2 чел.
Служащие-специалисты 1 чел.
Численность МОП определяем в процентах от общего числа рабочих литейного цеха (15 2%): 4 чел.
Всего работающих 237 чел.
ТЕХНОЛОГИЧЕСКАЯ ЧАСТЬ
Анализируем конструкцию отливки “Шкив привода генератора” по номенклатуре 740-1318160.
Отливка по конструкции несложная (тело вращения с одним центральным отверстием). Конструкция отливки обеспечивает сборку форм. По массе деталь мелкая. По назначению деталь является ответственной конструкция детали отвечает как требованиям технологии механической обработки так и требованиям литейной технологии. Для изготовления отливки требуется один стержень простой формы.
1 Выбор способа изготовления отливки
Учитывая массовый тип производства а также несложную конфигурацию массу и габариты отливки класс точности приходим к выводу что данную отливку получаем литьем в песчано-глинистые формы. Используем машинную формовку отливку изготавливаем непосредственно на автоматической формовочной линии.
Принятый способ литья получает высокий выход годного литья при относительно невысоких затратах при осуществлении технологического процесса.
2 Выбор положения отливки в форме в период заливки и затвердения
Положение отливки в форме при заливке и затвердении определяет весь технологический процесс изготовления отливки.
Данная отливка располагается в обеих полуформах в вертикальном положении. Данное расположение обеспечивает: направленное затвердение наиболее простую литниковую систему простую сборку форм минимальные габариты форм.
Учитывая размеры отливки в форме можно расположить максимальное их количество и назначить минимальные припуски на механическую обработку.
3 Определение поверхности разъема формы
Форма имеет одну горизонтальную плоскость разъема поверхность разъема плоская.
Такая поверхность разъёма формы обеспечивает удобство формовки контроль качества сборки формы наиболее простую конструкцию модельной оснастки и формы минимальное искажение базовых поверхностей.
4 Определение припусков на механическую обработку формовочных уклонов радиусов закруглений
Величину припусков на механическую обработку определяют следующие характеристики: материал отливки; её класс точности положение поверхности при заливке габаритные размеры номинальный размер отливок.
Учитывая всё вышеизложенное выбираем согласно [6] следующие размеры припусков: торцевые поверхности 2 мм внешний диаметр 2 мм отверстие 4(2·2) мм.
Формовочные уклоны назначаем в соответствии с конфигурацией отливки [8]: 20 (наружные) радиусы закруглений: до 5 мм.
5 Графическое оформление отливки
Выполняем чертёж отливки с нанесением припусков на механическую обработку на обрабатываемых поверхностях. Отверстия не выполняемые литьём чертятся тонкой линией.
Выбираем и наносим на чертеже поверхность разъёма линией. Остаток прибыли и питателя наносятся тонкой линией.
6 Определение количества и конструкции стержней
Анализируя конструкцию отливки приходим к выводу о возможности получения внутренней полости отливки с помощью одного стержня. Стержень занимает горизонтальное положение в форме. Он имеет относительно несложную ступенчатую конфигурацию прост в изготовлении. Выбранная конструкция стержня обеспечивает: получение внутренней полости с заданной точностью удобную установку стержня допускающую просмотр и контроль размеров формы свободное удаление газов и легкое удаление стержневой массы из отливки в период её очистки механическую и термическую стойкость. Стержень имеет знаки достаточной прочности. Размеры уклоны и зазоры между знаком стержня и формой выбираем по ГОСТ 3212-93.
Стержни изготавливаются на стержневых линиях из жидких самотвердеющих смесей (ЖСС).
7 Формовочные и стержневые смеси
6.1 Формовочные смеси
Качество отливок в литейном производстве во многом определяется качеством формовочных смесей. Для отливки «Шкив привода генератора» применяем единую формовочную смесь. Состав формовочной смеси приведен в таблице 2.7.1.
Таблица 2.7.1. Состав формовочной смеси.
Составляющие формовочной смеси
Массовая доля составляющих смеси %
Суспензия бентонито-угольная
ЭКР – экструзионный крахмалосо-держащий реагент
В условиях автоматической формовки для приготовления формовочной смеси используем сложные системы смесеприготовления. Обычно эти системы состоят из двух комплексов: приготовления формовочной смеси и её регенерации.
Сухой песок по ленточному конвейеру подается в бункеры над бегунами. Отработанная смесь из-под выбивной решетки автоматической формовочной линии поступает на конвейер на котором собирается просыпь формовочной смеси из-под формовочных автоматов. Затем отработанная смесь поступает на ленту конвейера где подвергается магнитной сепарации над ленточным магнитным сепаратором. После этого смесь дробится и разрыхляется в рыхлителе просеивается через сито и на ленточном конвейере вторично подвергается магнитной сепарации над ленточным магнитным сепаратором. Далее отработанная формовочная смесь поступает в гомогенизационный барабан в котором увлажняется до определенной влажности. Вода в барабан подается через форсунки. Из барабана смесь поступает в охладитель испарительного типа представляющий собой камеру внутри которой движется сетчатый пластинчатый конвейер. Смесь из барабана попадает на этот конвейер и охлаждается продуваемым через нее воздухом; одновременно происходит удаление пыли из смеси. На выходе из установки смесь имеет температуру не выше 38 40°С. Далее по конвейерам и элеватору смесь поступает в бункеры над бегунами.
Из бункеров сухой песок и отработанная смесь тарельчатыми питателями подаются в бункеры-дозаторы бегунов. Бентонитоугольная эмульсия приготовляется в установках и по трубопроводам подается в бегуны. После перемешивания формовочная смесь выдается из бегунов в дозаторы. При перемешивании для охлаждения и обеспыливания смеси осуществляется ее продувка воздухом с помощью вентиляторов. Из дозаторов смесь по системе ленточных конвейеров подается в разрыхлитель пройдя через него по ленточным конвейерам поступает в бункеры над формовочными автоматами.
Физико-механические свойства смеси приведены в таблице 2.7.2.
Таблица 2.7.2. Физико-механические свойства формовочной смеси.
Прочность отверждённого образца на разрыв кгсм2
в холодном состоянии
7.2 Стержневые смеси
Для изготовления стержней применяем жидкую самотвердеющею смесь (ЖСС) при использовании которой отпадает необходимость сушки стержней а также процесс их уплотнения в стержневом ящике. Через 40 60 мин. после заливки жидкая стержневая смесь в ящике становится прочной н стержень можно извлекать из стержневого ящика.
Смеси состоят из жидкого стекла (крепитель) поверхностно-активного вещества - пенообразователя (мылящее вещество) который придает текучесть смеси отвердителя (феррохромовый шлак 2СаО*S все эти составляющие смешивают в определенных пропорциях. Принципиальная особенность ЖСС - их способность затвердевать одновременно по всему объему. Поэтому продолжительность затвердевания не зависит от размеров форм и стержней. Твердение начинается через 8 10 мин после заливки и заканчивается через 40 60 мин.
8 Разработка конструкции модели и модельных плит
8.1 Классификация моделей
Модели классифицируются по размерам. Модель отливки «Шкив» относится к средним моделям. При проектировании данной отливки была разработана простая конструкция модели с разъёмом по плоскости проходящей через ось вращения изделия.
8.2 Выбор материала для изготовления модельного комплекта
При машинной формовке целесообразно изготавливать модели из стали (Сталь 40Х) которые предназначаются для серийного и массового производства (для изготовления мелких и средних моделей стержневых ящиков и модельных плит).
8.3 Металлические модельные комплекты
Металлические модели и стержневые ящики применяют в массовом производстве. Основными элементами металлического модельного комплекта являются модельная плита и стержневые ящики. Вспомогательными элементами являются сушильная плита вилочные съёмщики. Металлические модельные плиты делают составными и цельнолитыми.
Исходным документом при проектировании металлического модельного комплекта является чертеж отливки выполненный согласно ГОСТ 3.1125-88. По этому чертежу разрабатывают чертежи элементов металлического модельного комплекта: модельных плит моделей стержневых ящиков и т. д. При разработке чертежей металлического модельного комплекта модельных плит моделей стержневых ящиков широко используют нормали и стандарты в которых регламентированы конструкции элементов оснастки их размеры материал точность исполнения шероховатость поверхностей и т. д.
Металлические модели стержневые ящики модельные плиты рекомендуется делать тонкостенными усиливая их ребрами жёсткости. Толщину стенок моделей и стержневых ящиков назначаем по ГОСТ 19370-74.
Используем опочные модельные плиты односторонние.
Заготовки металлических моделей стержневых ящиков и плит получают литьём в песчаные формы по деревянным моделям то есть по промоделям.
Заготовки обрабатывают на обычных универсальных металлорежущих станках. После обработки резанием модели монтируют на заранее подготовленных плитах. При монтаже учитывают размеры и конструкции опок.
Модели литниковой системы монтируют на плитах после установки моделей отливки в соответствие с чертежом.
9 Разработка конструкции литниковой системы
При выборе способа подвода расплава в форму и разработке конструкции литниковой системы учитываем что расплав должен поступать в форму плавно без ударов о ее стенки и стержни без завихрений с заданной скоростью подъема уровня в форме и последовательным удалением воздуха и газов из формы. Кроме того способ подвода расплава обеспечивает направленное затвердение отливки с учетом ее конструкции и свойств сплава.
Тот или иной способ подвода расплава конструкции литниковой системы соотношение её размеров элементов назначают в зависимости от литейных свойств сплава - жидкотекучести усадки склонности к образованию трещин; конфигурации размеров массы и назначения отливки.
На основании всего вышеизложенного приходим к выводу что наиболее целесообразно использование литниковой системы с подводом металла по плоскости разъема. Она наиболее проста технологична для данного типа отливок.
К числу элементов питающей системы обеспечивающих питание отливки расплавом при затвердевании относятся питающие выпоры бобышки и прибыли.
Прибыли и питающие выпоры служат для компенсации усадки утолщённых мест отливки. Они должны располагаться над массивными частями имеют такие размеры и конфигурацию чтобы расплав в них застывал в последнюю очередь. Размеры должны быть достаточными для того чтобы компенсировать усадку отливки.
10 Определение количества моделей на плите
Отливка изготовляется на автоматической формовочной линии. Размер опоки 1000*800*300300.
Исходя из веса отливки (654кг) устанавливаем рекомендуемые минимально допустимые толщины слоя:
от верха модели до верха опоки 50 мм;
от низа модели до низа опоки 60 мм;
от модели до стенки опоки 30 мм;
между моделями 40 мм;
между моделями и шлакоуловителями 30 мм.
На основании этого принимаем 8 моделей на плите.
11 Выбор способа формовки
Для изготовления отливки «Шкив привода генератора» выбираем автоматическую линию опочной формовки. Такие формовочные линии эксплуатируются в литейных цехах машиностроительных заводов они имеют достаточно высокую производительность и надежность в эксплуатации.
Формовочная линия расположена с проездами с обеих сторон что облегчает доступ к отдельным агрегатам линии для их обслуживания замены и ремонта. Формовочная линия обслуживается непрерывно движущимся горизонтально-замкнутым тележечным конвейером Формовочная линия обеспечивается формовочной смесью от индивидуальной смесеприготовительной системы.
Формовочная линия имеет удобную компоновку которая позволяет в заданном темпе выполнять все необходимые операции. Имеется устройство для автоматической смены модельных плит на формовочном автомате без остановки линии. Изготовление форм производится встряхиванием с допрессовкой. Сборка форм заливка охлаждение производится на конвейере. Выбивка отливок производится на инерционных выбивных решетках. Перед установкой опоки модель обдувается и опрыскивается разделительным составом. Формовочная смесь поступает из стационарного бункера в бункер над формовочной машиной. В нижней части бункера имеется аэратор который разрыхляет смесь в процессе ее дозирования в опоку. Во время встряхивания излишек смеси срезается уровень срезки регулируется. Съем готовой полуформы производится строго вертикально с переменной скоростью это обеспечивает извлечение формы без повреждения. Снятая верхняя полуформа с формовочного стола последовательно поступает на позицию изготовления вентиляционных отверстий. Вентиляционные наколы снизу и сверху наносятся в заранее определенные координаты. Затем верхняя полуформа поступает в кантователь в котором переворачивается на 360° для сброса с нее излишков смеси и затем поступает на сборку.
Нижняя полуформа изготавливается аналогично верхней полуформе. Готовая нижняя полуформа поворачивается на 180° и ставится на платформу движущегося литейного конвейера по центрирующим штырям обдувается после чего осуществляется простановка стержней фильтров и т.д.
Сборка готовых полуформ производится сборщиком на движущемся литейном конвейере с применением специальных штырей которые точно ориентируют полуформы относительно друг друга. В конце хода сборки верхняя полуформа прижимается к нижней специальными цилиндрами т.к. масса верхней полуформы большая то нагружение форм или скрепление опок перед заливкой не производится.
12 Выбор способа плавки металла
Плавка стали осуществляется в электродуговых печах. Плавильные агрегаты имеют трансформаторы большой мощностью до 35000 кВт поэтому плавку можно вести в интенсивном режиме с выделением высокой мощности для расплавления шихты. Электродуговые агрегаты являются высокопроизводительными и обеспечивают выплавку стали с использованием различных шихтовых материалов.
Плавка имеет следующие преимущества: возможность получения в плавильном пространстве печи восстановительной среды угар элементов меньше меньшее содержание в печи кислорода и ведение окислительных процессов только путем подачи железной руды или кислорода вдуваемого в ванну.
При плавке стали в электродуговой печи используются следующие материалы: лом стальные отходы нелегированные возврат собственного производства ферромарганец ФМn 75-3 графит порошковый алюминий для раскисления известняк металлургический кварцевый песок.
Во время плавки стали электродуговая печь должна быть в исправном состоянии во время работы печи должен быть постоянный надзор за исправностью печи. Материалы для плавки должны находиться в закромах на расстоянии удобном для работы. Подина и откосы должны быть тщательно очищены от остатков металла и шлака осмотрены сталеваром после чего производится заправка подины и откосов кварцевым песком на жидком стекле. После заправки производят завалку шихты в печь. Перед завалкой на подину печи загружают графитовый порошок. Затем поднимают электроды и свод печи который отводится в сторону. С помощью крюка мостового крана открывают замок бадьи и загружают шихту в печь разравнивают ее специальным грузом и закрывают печь сводом.
После расплава всей шихты и прогрева жидкой ванны отбирают пробу для определения углерода. Если содержание углерода в ванне низкое то науглераживают металл чугуном. Если содержание углерода соответствует среднезаданному в готовой стали с учетом присадки ферромарганца то в ванну с учетом остаточного углерода дают по расчету кусковой ферросилиций и ферромарганец. Затем после 5 7 минут выдержки и тщательного перемешивания ванны отбирают пробу металла на раскислённость. По результатам экспресс-анализа при необходимости производят корректировку химического состава стали. Перед выпуском плавки замерить температуру металла в печи она не должна превышать 1700 °С. За пять минут перед выпуском подать ковш к печи нагретый до 800-900 °С. Плавку сливают и устанавливают ковш с металлом на стенд для раздачи металла в разливочные ковши.
Для управления процессом выплавки стали предусмотрена автоматизированная система контроля. Для плавки стали принята печь ДП-16 (см. п.1.5.2).
13 Разработка технологии заливки форм
По конструкции ковши бывают чайниковые барабанные и стопорные.
Ковш служит для транспортировки жидкого металла и заливки форм. Ковш имеет стальной кожух у которого стенки и дно изнутри выложены огнеупорным материалом. Для заливки чугуна ковш футеруют шамотом. Толщина слоя футеровки 65 180 мм.
Для заливки стали чаще применяют чайниковые ковши ковш с носком или ковш с перегородкой. В нашем случае это ковш с носком.
Ковши сушат и нагревают горелками работающие на природном газе. Ковш нагревают до 700 750°С. Ковш сразу же после прогрева заполняют расплавом.
Сталь перед разливкой должна быть очищена от шлака.
В начальный момент заливки необходимо проворачивать ковш плавно без рывков но достаточно быстро чтобы заполнить литниковую систему и чашу. В дальнейшем поворот ковша осуществляют с такой скоростью чтобы уровень расплава в чаше оставался по возможности постоянным. После появления расплава в чаше уменьшают скорость поворота ковша для того чтобы расплав не вытек из чаши.
14 Разработка технологии охлаждения форм выбивки обрубки очистки
После заливки формы отливка охлаждается и затвердевает. Полностью затвердевшая отливка должна определённое время охлаждаться в форме так как прочность металла при высоких температурах мала и отливка может разрушиться при выбивке её из форм.
Продолжительность выдержки отливки в форме при охлаждении до заданной температуры выбивки обуславливается длиной участка охлаждения на автоматической формовочной линии (100 минут).
Процесс выбивки отливок заключается в том что затвердевшие и охладившиеся до заданной температуры отливки извлекаются из формы. Форму разрушают а также отделяют литники и прибыли; после этого выполняют очистку наружной и внутренней поверхностей отливки от пригоревшей смеси.
Для выбивки отливок используют систему эксцентриковых выбивных решеток.
Технологический процесс очистки отливок включает следующие операции:
отделение литников;
очистка от приставшей формовочной смеси;
удаление окалины и заусенцев;
окончательный контроль качества отливок после обрубки и очистки.
Литники отделяют молотками.
Очистка отливок от пригоревшего песка и окалины осуществляется дробемётным способом.
Зачистка осуществляется абразивными материалами.
Термическую обработку отливки проводят для снижения литейных напряжений стабилизации размеров снижения твердости улучшения обрабатываемости износостойкости увеличивается ударная вязкость стали.
Для отливки «Шкив привода генератора» применяем нормализацию. Нормализацию применяют для устранения внутренних напряжений повышения механических свойств стали. Сталь после нормализации получает однородную мелкозернистую структуру. При нормализации отливки нагревают выше критической точки Ас3 для стали 35Л на 30°С затем производят выдержку при этой температуре для получения однородного аустенита. Затем отливки ускоренно охлаждают на воздухе до температуры 60°С. Прочность отливки «Шкив привода генератора» после нормализации составляет 137 197 НВ.
15 Разработка системы контроля технологии и качества отливок
Входной контроль - контроль прибывших шихтовых и формовочных материалов.
Контроль химического состава механических свойств и микроструктуры полученной стали.
Контроль формовочных и стержневых смесей.
Контроль моделей и полуформ верха и низа.
Контроль температуры и времени заливки.
Контроль и учёт залитых форм.
Контроль количества отливок и внешнего вида после выбивки.
Контроль после обрубки и очистки.
Контроль на соответствие чертежу отливки.
Завершающий контроль количества штук контроль внешнего вида.
16 Дефекты отливки мероприятия по предупреждению и способы исправления
Характерные дефекты для «Шкива привода генератора» - усадочные раковины шлаковые включения которые влияют на не герметичность отливки.
Усадочные раковины в отливках образуются при недостаточном питании отливки жидким металлом в процессе кристаллизации а также в утолщённых местах отливки. Для исключения данного дефекта в утолщённых местах отливки рекомендуется ставить прибыли изменять конструкцию отливки выравнивать толщину её стенок.
Шлаковыми называются включения имеющие вид и состав шлака. Чаще всего шлаковые включения расположены в верхних частях отливок или на их поверхности. Оставшиеся после удаления шлака полости в теле отливки могут иметь гладкую или шероховатую поверхность с неровными краями. В большинстве случаев серого цвета различных оттенков. Для удаления шлака из металла его перегревают и выдерживают в ковше для всплытия неметаллических включений и растворенного газа используют шлакоулавливающую литниковую систему.
Для уменьшения потерь от брака в ряде случаев производят исправление дефектов отливок. Заварку применяют для исправления дефектов отливок.
17 Расчет литниково-питающей системы
Объём отливки определяем по чертежу Vотл = 835·10-4 м3.
Плотность материала отливки (сталь 35Л ρс = 7830 кгм3).
Тогда масса отливки:
mo = ρо·Vотл = 7830·835·10-4 = 654кг (2.1)
Расчёт литниковой системы для отливки «Шкив привода генератора» сводится к определению площадей сечений и размеров питателей шлакоуловителя стояка.
Постоянство весовой скорости потока расплава за весь период заливки форм можно выразить уравнением:
где Gв - весовая скорость заливки кгс;
F - площадь контакта см2;
f = 00525 кг(с·см2) - фактор растворения.
Большое значение имеет при этом зернистость модификатора и его реакционная способность.
Расчет литниковой системы производится по способу Озанна-Диттерта.
Суммарная площадь сечений питателей:
ΣFп = М[ρ·t··√(2·g·Hp)] = 52300[70·23·042·√(2·g·277)] = 332 см2 (2.3)
где М = 523 кг = 52300 г - масса отливок в форме г;
ρ = 70 гсм3 - плотность расплава;
= 042 - коэффициент расхода литниковой системы;
Средняя толщина стенки отливки = 30мм.
Продолжительность заливки формы:
t = 2·3√(·М) = 2·3√(30·523) = 23 с
Расчетный напор металла:
Нр = Н - Р2(2·С) = 30 - 972(2·194) = 276см (2.4)
где Н = 30 см - высота стояка от места подвода расплава в форму;
Р = 97 см - высота отливки от места подвода расплава;
С = 194 см - высота отливки.
Площадь сечения одного питателя:
Fп = ΣFпno = 33216 = 207 см2 = 207 мм2 (2.5)
Лимитирующим при расчёте литниковой системы является время заливки одной формы. Так же при расчёте литниковой системы необходимо знать следующие соотношения проходных сечений литниковой системы [44].
Fст = 11·ΣFп15 = 11·33215 = 243 см2 = 2430 мм2 (2.6)
Площадь шлакоуловителя:
Fшу = 11·ΣFп13 = 11·33213 = 281 см2 = 2810 мм2 (2.7)
модификатора 1% от массы жидкого металла на ковш кг.
mмод = (1·1200)100 = 12 кг (2.8)
dст = √(4·Fст) = √(4·2430) = 556 мм 56 мм (2.9)
Для обеспечения плотности фланца отливки устанавливаем на ней прибыль открытую конусную.
Средний диаметр прибыли можно принять равным толщине фланца Dп = 40мм.
Высота прибыли от фланца до верха формы Нп = 203 мм.
Тогда объём прибыли:
Vп ·Dп2·Нп 4 = ·0042·02034 = 255*10-4 м2 (2.10)
mп = ρс·Vп = 7830·255·10-4 = 200 кг (2.11)
прибыли от массы отливки 2654 = 031 или 31% что с лихвой компенсирует усадку стали 35Л (~2%).
18 Нововведения в технологии
Нововведением в технологической части является добавление в литниковую систему кремнезёмной сетки для фильтрации расплава: задержания неметаллических включений (например осыпи формовочой смеси) и газов. Несмотря на то что это мероприятие вносит небольшие дополнительные расходы на изготовление отливки но благодаря уменьшению брака по раковинам пригарам и неметаллическим включениям и как следствие увеличению выхода годного эти расходы окупаются.
Кремнеземные материалы имеют низкую теплопроводность высокую стойкость к тепловому удару обладают превосходными электроизоляционными свойствами при высоких температурах могут длительно использоваться без изменения свойств при температуре 1000ºС (на новом материале Puresil до 1200ºС) и кратковременно при более высоких температурах (не плавятся не испаряются при температурах до 1700ºС). Изделия из кремнеземного стекла чрезвычайно инертны к большинству химических реагентов стойки к органическим и минеральным кислотам любых концентраций даже при повышенной температуре (за исключением плавиковой фосфорной соляной) и слабым щелочам расплавленных металлов (кроме Mg Na Si) и сплавам. Обладают высокой химической стойкостью к воде и пару высокого давления способны поглощать влагу но не расщепляются в присутствии воды стабильны в вакууме.
Кремнеземные сетки применяются в качестве эффективного фильтровального материала для очистки расплавов черных и цветных металлов при их заливке в литейные формы.
Фильтр необходимого размера вырезается и устанавливается в литниковую систему или непосредственно под литник между нижней и верхней опоками литейной формы.
ТЕХНИКО-ЭКОНОМИЧЕСКАЯ ЧАСТЬ
1 Расчёт производственной программы
2 Расчёт выручки от реализации
3 Расчёт затрат на покупные сырьё и материалы
4 Планирование труда и заработной платы
5 Определение себестоимости единицы продукции
6 Определение затрат на оборудование здания и сооружения
7 Нормируемые текущие активы
8 Нормируемые краткосрочные пассивы
10 Отчёт о движении денежных средств
11 Основные показатели проекта
БЕЗОПАСНОСТЬ ЖИЗНЕДЕЯТЕЛЬНОСТИ
1 Назначение раздела
В данном разделе рассматриваются вопросы безопасности жизнедеятельности человека и техники для чугунолитейного цеха при производстве отливок в песчано-глинистые разовые формы с программой выпуска 35000 тонн годного литья из серого чугуна в год.
2 Характеристика производства
Литейные цеха относятся к IV классу с шириной санитарно-защитной зоны 100 метров (СН 245-71). Промышленные предприятия выделяющие в процессе работы вредные вещества и загрязняющие распространяющие неприятные запахи шум не допускается располагать с подветренной стороны к жилому району; их следует отделять от жилых районов санитарно защитными зонами.
Между длинными сторонами и торцами зданий с оконными проемами предусматривают санитарные разрывы не менее 12 метров (СН 245-71).
По пожарной опасности цеха литейного производства относятся к категории "В".
Характеризуются следующими факторами пожарной опасности:
Наличием в оборудовании горючих веществ и масел с температурой вспышки 160°С технологической смазкой оборудования;
Наличием нагретого металла выделением паров масел;
Отложение пыли и масла в трубопроводах системы вентиляции.
Здания литейных цехов выполняются не ниже второй степени огнестойкости. В процессе работы в литейных цехах возникают следующие вредные факторы: шум повышенная температура влажность тепловое излучение пыль минеральные масла.
По условиям окружающей среды цеха литейного производства относят к горячему производству. Работники этого цеха имеют право выхода на пенсию по
льготному стажу (раньше на 10 лет).
На участках имеется пожарная сигнализация типа ДТЛ (датчик температурный линейный) срабатывающий при температуре свыше 60°С и подающий сигнал на систему автоматического пожаротушения. Затем к местам возгорания по трубопроводам подается гасящий состав. Кроме того на участках имеются следующие средства пожаротушения: ручные огнетушители пожарные рукава ведра лопаты багры топоры емкости с песком.
По опасности поражения электрическим током литейные цеха относят к помещениям с повышенной опасностью которые характеризуются наличием сырости относительная влажность более 75%; высокой температурой воздуха длительно превышающей +30°С; полы из токопроводящих материалов; большое количество токопроводящей пыли оседающей на проводах и проникающей внутрь установок.
Опасные места на участках ограждены. Для безопасной работы на автоматических линиях имеются блокировки препятствующие попаданию человека в опасную зону. Также существуют предохранительные устройства срабатывающие при перегрузке какого-либо механизма.
В административно-бытовом корпусе имеется раздевалка с душевыми. Есть столовая и буфет. Административно-бытовой корпус связан с производственным корпусом отапливаемыми галереями. Непосредственно на рабочем месте имеется умывальник. Есть комнаты отдыха санузлы. Предусмотрено снабжение питьевой водой.
Санитарные нормы предусматривают внутренние водопроводы в производственных и вспомогательных зданиях для подачи воды на производственные и хозяйственно-бытовые нужды. Источником водоснабжения является городская водопроводная сеть.
питьевая вода 45 литров;
умывальники 200 литров.
Температура воды +37°С.
Сточные воды удаляют из производственных вспомогательных и бытовых помещений через систему канализации. Из канализационной сети вода поступает в очистные сооружения канализационных станций а после очистки слив в водоемы.
На производстве используется приточно-вытяжная вентиляция: естественная и принудительная. Применяются местные отсосы зонты кожухи на участках где идет интенсивное выделение пыли. В ряде случаев в кабинах электрокранов на постах управления используют кондиционированный воздух.
3 Создание оптимальных условий труда. Общие требования комфортных условий на рабочем месте. Вентиляция освещение.
3.1 Общие требования
В литейных цехах основными опасными и вредными производственными факторами являются: пыль пары и газы избыточная теплота повышенный уровень шума вибрации электромагнитные излучения движущиеся машины и механизмы подвижные части производственного оборудования и др.
Пыль в литейных цехах мелкодисперсная: до 90% пылинок имеют размеры менее 2 мкм. При очистке отливок выделяется пыль которая содержит более 90% двуокиси кремния а при выбивке отливок около 90%.
Источниками выделения окислов углерода являются электродуговые плавильные печи а также залитые формы в процессе остывания сушильные печи и др.
Избыточное выделение тепла основным технологическим оборудованием плавильными агрегатами колеблется от 14 до 64% от общего расхода тепла на расплавление металла а при разливке металла составляет около 3000 МДжч интенсивность теплового потока на ряде рабочих мест достигает высоких значений.
Для создания комфортных условий на рабочем месте предусматривается соблюдение нормативных требований к параметрам микроклимата (ГОСТ 12.1.005 - 88).
В рабочей зоне участка с учётом интенсивности труда поставлены допустимые микроклиматические условия (табл. 4.1).
Таблица 4.1. Допустимые микроклиматические условия.
В холодный период года
В тёплый период года
Температура воздуха °С
Относительная влажность %
Скорость движения воздуха мс
Данные микроклиматических условий поддерживаются системами отопления и вентиляции. В соответствии со СП 60.13330.2012 в производственном помещении участка предусмотрена система водяного отопления. Вода в систему отопления подается от собственной котельной предприятия. Для воздухообмена на участке используется естественная и искусственная вентиляция. Аэрация осуществляется через светоаэрационный фонарь который оборудован приспособлением для дистанционного открывания фрамуг и рам со специальной площадки в помещении участка. Помещение участка оборудовано обще-обменной приточно-вытяжной вентиляцией. Воздух подаётся в верхнюю зону помещения с допустимой скоростью (см. таблицу 4.1). В зимнее время приточный воздух подогревается до 20°С.
Производственное помещение участка обеспечено искусственным и естественным освещением. Естественное освещение осуществляется через
светоаэрационные фонари. Так как естественное освещение зависит от погодных условий то расчёт проведём для искусственного освещения.
3.2 Вентиляция и отопление производственного корпуса участка цеха
Работа вентиляционных систем в комплексе с выбором технологических процессов по ГОСТ 12.3.002-2014 и производственного оборудования отвечающего требованиям ГОСТ 12.2.003 - 91 должна создавать на постоянных рабочих местах в рабочей и обслуживаемой зонах помещений метеорологические условия и чистоту воздушной среды соответствующие действиям санитарных норм.
Основным вредным фактором связанным с загрязнением воздушной среды является пыль и аэрозоли конденсации металлов выделения вредных паров и газов тепловыделения от технологического оборудования.
Вентиляцией называется комплекс взаимосвязанных устройств и процессов для создания требуемого воздухообмена в производственных помещениях. Основное назначение вентиляции – удаление из рабочей зоны загрязненного или перегретого воздуха и подача чистого воздуха в результате чего в рабочей зоне создаются необходимые благоприятные условия воздушной среды. Одна из главных задач возникающих при устройстве вентиляции - определение воздухообмена т.е. количество вентиляционного воздуха необходимого для обеспечения оптимального санитарно-гигиенического уровня воздушной среды помещений.
Естественная вентиляция производственных помещений осуществляется за счет разности температур в помещении наружного воздуха (тепловой напор) или действия ветра (ветровой напор). Естественная вентиляция может быть организованной и неорганизованной.
Искусственная (механическая) вентиляция устраняет недостатки естественной вентиляции. При механической вентиляции воздухообмен осуществляется за счет напора воздуха создаваемого вентиляторами (осевыми и центробежными); воздух в зимнее время подогревается в летнее - охлаждается и кроме того очищается от загрязнений (пыли вредных паров и газов). Механическая вентиляция бывает
приточной вытяжной приточно-вытяжной а по месту действия - общей и местной.
При вытяжной системе вентиляции и загрязненный и перегретый воздух удаляется из помещения через сеть воздуховодов с помощью вентилятора.
При работе большинства отделений возникают значительные выделения тепла для ассимиляции которого необходимо максимально использовать аэрацию.
В плавильных заливных и формовочных отделениях приточный воздух рекомендуется подавать в рабочую зону. Удаления воздуха производится из верхней зоны через аэрационные фонари. К рабочим местам у заливочного конвейера рекомендуется подавать приточный воздух по всему фронту заливки металла через воздухораспределители панельного типа. На участках с интенсивным выделением пыли: смесеприготовительных стержневых формовочных и других приточный воздух следует подавать выше рабочей зоны с меньшими скоростями. Расход воздуха на 1 т. отливок при выплавке чугуна ориентировочно составляет 380 м3час.
В литейном цехе имеется значительное количество источников выделения вредных веществ для локализации которых необходимо устанавливать местную вытяжную вентиляцию. Наиболее неблагоприятными (с точки зрения загрязнения воздушной среды) являются операции плавки заливки металла в формы выбивка форм и транспортировка горелой земли.
В проекте приняты: различные местные отсосы защитно-обеспыливающие кожухи и другие системы.
Цель отопления помещений поддержание в них в холодное время года заданной температуры воздуха.
Система отопления должна компенсировать потери теплоты через строительные ограждения а также нагрев проникающего в помещение холодного воздуха поступающих материалов и транспорта.
В настоящее время наиболее распространены системы водного и парового отопления.
Системы водяного отопления наиболее эффективны в санитарно-гигиеническом отношении. Они подразделяются на системы с нагревом воды до 100°С и выше. В качестве побудителей движения воды используются водяные насосы и элеваторы.
В проекте приняты: вода в систему отопления подается от собственной котельной предприятия.
К числу отапливаемых помещений относятся: административный корпус и бытовые помещения гардероб душевые санузлы стержневые окрасочные и вспомогательные участки.
3.2.1 Расчет вентиляции
В формовочном отделении воздух который загрязнен вредными парами газами и пылью количество приточного воздуха м3ч необходимого для разбавления вредных выделений до допустимых концентраций рассчитывают по формуле:
L = 1000·G·φ(СПДК - СПР) = 1000·20·15(20 - 6) = 2100 м3с (4.1)
где G = 20 мгм3 – масса вредных веществ выделяющихся в рабочее помещение в единицу времени;
φ = 12 2 - коэффициент неравномерности распределения вредных веществ по помещению;
СПДК = 20 мгм3 – предельно допустимая концентрация (ПДК) вредных веществ по санитарным нормам;
СПР = 6 мгм3 – концентрация вредных веществ в приточном воздухе.
Согласно ГОСТ 12.2.003-91 значение СПР не должно превышать 30% СПДК.
Кратность воздухообмена:
R = LS = 2100300000 = 007ч-1 (4.2)
где S = 300000 м3 - объем помещения.
В плавильном отделении со значительными тепловыделениями количество приточного воздуха необходимого для поглощения избытка тепла рассчитывается по формуле:
L = ΣQизб(С·(tуд - tпр)·γпр) = 106·1010(1000·(28 - 21)·12) = 126·106 м3с (4.3)
где ΣQизб = 106·1010 Джч - избытки теплоты;
С =1000 Дж(кг град) - теплоемкость воздуха;
tуд = 28°С - температура удаляемого из помещения воздуха;
tпр = 21°С - температура приточного воздуха;
γпр = 12 кг м3 - плотность приточного воздуха.
Избытки теплоты Q определяют как разницу между суммарным количеством тепловыделений в помещении - теплота выделяемая горячими поверхностями остывающими массами электропечами и т.п. - и суммарными потерями в помещении.
R = 126·10610000 = 126ч-1
Объем удаляемого воздуха при расчете местной вытяжной вентиляции для выбивной решетки принимается в зависимости от характера вредных выделений скорости и направления их движений и от конструкции местного отсоса:
Lвыт = F·V·3600 = 1·14·3600 = 5040 м3ч (4.4)
что соответствует ГОСТ 12.2.003-91
где F = 1 м2 – площадь открытого сечения вытяжного устройства;
V = 1.4 мс – скорость движения всасываемого воздуха в этом проеме.
3.3 Освещение рабочего участка
Нормальные условия работы в производственных помещениях могут быть обеспечены лишь при достаточном освещении рабочих зон и проходов.
Нормативными документами по освещению рабочего места являются
СП 52.13330.2016 ГОСТ 17677-88* ГОСТ 24940-96.
Рабочие зоны освещаются в такой мере чтобы рабочий имел возможность хорошо видеть процесс работы не напрягая зрения и не наклоняясь для этого к инструменту и обрабатываемому изделию расположенному на расстоянии не далее 05 м от глаза.
Освещение обеспечивающее нормальные зрительные условия работы является важным фактором в организации производства.
Классификация производственного освещения.
Естественный (солнечный) свет. Естественное освещение осуществляется через окна в наружных стенах.
Искусственное освещение предусматривается в помещениях при недостаточном естественном свете или для освещения помещения в те часы суток когда естественный свет отсутствует.
По конструктивному исполнению искусственное освещение может быть двух видов – общее и комбинированное когда к общему освещению добавляется местное концентрирующее световой поток непосредственно на рабочих местах.
Общее освещение подразделяется на общее равномерное освещение (при равномерном распределении светового потока без учета расположения оборудования) и общее локализованное освещение (при распределении светового потока с учетом расположения рабочих мест).
Применение одного местного освещения внутри зданий не допускается.
Рекомендуется применять систему комбинированного освещения там где оборудование создает глубокие резкие тени или рабочие поверхности расположены вертикально (штампы прессы).
Источники искусственного света:
В качестве источников света для освещения промышленных предприятий в настоящее время применяются лампы накаливания и газоразрядные лампы. Лампы накаливания относятся к источникам света теплового излучения и пока еще являются распространенными источниками света.
В проекте приняты: различные типы ламп накаливания: вакуумные (НВ) газонаполненные биспиральные (НБ) биспиральные с криптоноксеноновым наполнением (НБК). Также на предприятии установлено аварийное освещение для эвакуации людей при аварийных ситуациях.
4 Защита от негативных факторов производственной среды
Нормативными документами по шуму являются СН 2.2.42.1.8-96 ГОСТ 12.1.003-2014.
Шумом принято называть любой нежелательный звук воспринимаемый органом слуха человека. Шум представляет собой беспорядочное сочетание звуков различной интенсивности и частоты.
Шум на производстве неблагоприятно воздействует на работающего: ослабляет внимание увеличивает расход энергии при одинаковой физической нагрузке замедляет скорость психических реакций. В результате снижается производительность и ухудшается качество работы. Шум затрудняет также своевременную реакцию работающих на предупредительные сигналы подаваемые персоналом обслуживающим внутрицеховой транспорт (мостовые краны автопогрузчики и т. п.) что может стать причиной несчастного случая.
Мероприятия по борьбе с шумом:
Звукопоглощение основано на том что звуковые волны падающие на преграды поглощаются в большей или меньшей степени. Чем больше звуковых волн будет поглощаться тем меньше их отразится и это приведет к снижению общего уровня шума в помещении. Поглощение звука обусловлено переходом колебательной энергии в тепловую вследствие потерь на трение в звукопоглотителе.
Средства индивидуальной защиты.
Средства индивидуальной защиты органов слуха работающих установлены ГОСТ 12.4.011-89; это противошумные шлемофоны (шлемы) наушники заглушки вкладыши. Они эффективно защищают организм от раздражающего действия шума предупреждая возникновение различных функциональных нарушений и расстройств если правильно подобраны и систематически используются. Однако они должны использоваться лишь как дополнение к коллективным средствам защиты когда последние не могут решить проблему борьбы с шумом.
В проекте приняты: противошумные шлемофоны (шлемы) наушники заглушки вкладыши.
4.2 Производственная вибрация. Источники вибрации и ее влияние на человека
Вибрацией называют механические колебания упругих тел или колебательные движения механических систем.
Регламентируемые параметры введены санитарными нормами СН 245-71. Они не распространяются на средства транспорта и самоходные машины находящиеся в движении. Для ручных машин предельно допустимые уровни вибрации введены ГОСТ 17770-83.
Их параметры определяют: действующие значения колебательной скорости или их уровни в октавных полосах частот в местах контакта машин с руками работающего; силу нажатия (подачи) прикладываемую в процессе работы к ручной машине руками работающего; массу ручной машины или ее частей воспринимаемую в процессе работы руками работающего.
Масса ручной машины или ее частей воспринимаемая руками сила тяжести или ее составляющая передающаяся на руки работающего в процессе работы не должна превышать 100Н.
Поверхности машин в местах их контакта с руками работающего должны иметь коэффициент теплопроводности не более 05 Вт(м·К).
Источниками общей вибрации в литейных цехах являются выбивные решетки пневматические формовочные центробежные и другие машины а источниками локальных пневматические рубильные молотки трамбовки и др.
Мероприятия по устранению вибрации.
Общие мероприятия по борьбе с вредным воздействием вибрации могут проводиться по трем направлениям: инженерно-техническому организационному и лечебно-профилактическому.
Инженерно-технические мероприятия включают: внедрение средств автоматизации и прогрессивной технологии исключающих контакт работающих с вибрацией; изменение конструктивных параметров машин технологического оборудования и механизированного инструмента.
Организационные мероприятия включают контроль за монтажом оборудования на производственных площадках; своевременным и качественным проведением планово-предупредительного обслуживания и ремонта; выполнением правил технической эксплуатации машин и агрегатов.
К средствам защиты отнесены следующие устройства: оградительные виброизолирующие виброгасящие и вибропоглощающие (см. ГОСТ 12.4.011-89) а также средства автоматического контроля сигнализации дистанционного управления.
Лечебно-профилактические мероприятия обеспечивают необходимый микроклиматический режим и комплекс физиотерапевтических процедур (водные ванны массаж гимнастика и ультрафиолетовое облучение).
В проекте приняты: оградительные виброизолирующие виброгасящие и вибропоглощающие устройства (см. ГОСТ 12.4.011-89) а также средства автоматического контроля сигнализации дистанционного управления.
4.3 Электромагнитное излучение
Электромагнитное поле (ЭМП) характеризуется напряженностью электрического поля и напряженностью магнитного поля. Влияние на организм человека ЭМП радиочастот большой интенсивности связано с частичным поглощением их энергии тканями тела что вызывает тепловой эффект.
В соответствии с требованиями ГОСТ 12.1.006-84 ЭМП в диапазоне частот 60 300 кГц должно оцениваться напряженностью его составляющих а в диапазоне частот 300 МГц 300 ГГц - плотностью потока энергии.
Для защиты персонала от воздействия ЭМП используют различные способы и средства. Уменьшают напряженность и плотность потока энергии ЭМП; экранируют рабочие места от источника ЭМП; рационально размещают в рабочем помещении оборудование излучающие электромагнитную энергию; применяют средства индивидуальной защиты (спец. халаты и комбинезоны очки ОРЗ-5 экраны и т.п.).
В проекте приняты: экранирование рабочих места от источника ЭМП средства индивидуальной защиты (спец. халаты и комбинезоны очки ОРЗ-5 экраны и т.п.).
5 Основные положения действующего законодательства РФ об охране труда
Законодательство об охране труда состоит из соответствующих положений Конституции РФ настоящего Закона и иных законодательных актов действующих на территории РФ.
Государственная политика РФ в области охраны труда предусматривает совместные действия органов государственной власти и управления объединений работодателей профессиональных союзов в лице их соответствующих органов и иных уполномоченных работниками представительных органов по улучшению условий и охраны труда предупреждению производственного травматизма и профессиональных заболеваний.
Основными направлениями государственной политики в области охраны труда являются:
признание и обеспечение приоритета сохранения жизни и здоровья работников по отношению к результатам производственной деятельности организации;
принятие нормативных правовых актов способствующих достижению высокого уровня безопасности труда и предотвращению несчастных случаев на производстве и профессиональных заболеваний;
защита прав работников на безопасные и здоровые условия труда;
координация деятельности в области охраны труда с другими направлениями экономической и социальной политики а также в области охраны природной среды;
установление единых нормативных требований по охране труда обязательных к исполнению для организаций;
государственное управление деятельностью в области охраны труда включая экспертизу условий труда надзор и контроль за соблюдением законодательных и иных нормативных правовых актов по охране труда;
содействие общественному контролю соблюдения законных прав и интересов работников в области охраны труда на производстве осуществляемому профсоюзами и иными уполномоченными работниками представительными органами;
взаимодействие и сотрудничество органов государственного управления в области охраны труда с работодателями профессиональными союзами в лице их соответствующих органов и иными уполномоченными работниками представительными органами заинтересованными в разработке и практической реализации государственной политики в области охраны труда;
содействие работодателям в организации обучения работников безопасным приёмам труда в проверке знаний правил норм и инструкций по охране труда у работников организаций;
экономическое стимулирование деятельности по созданию благоприятных и безопасных условий труда разработке и внедрению безопасных техники и технологий средств коллективной и индивидуальной защиты работников;
применение санкций экономического административного и уголовного характера в случаях нарушения работодателями и представляющими их должностными лицами нормативных требований по охране труда;
установление компенсаций и льгот за тяжёлые работы и работы с вредными или опасными условиями труда не устранимыми при современном техническом уровне производства и организации труда;
проведение регулярной оценки состояния условий и безопасности труда в организациях;
защита интересов работников пострадавших от несчастных случаев на производстве или получивших профессиональные заболевания а также членов их семей;
установление порядка и норм обеспечения работников специальной одеждой специальной обувью средствами коллективной и индивидуальной защиты лечебно-профилактическим питанием необходимыми профилактическими средствами за счёт средств работодателя;
установление порядка расследования каждого несчастного случая на производстве и профессионального заболевания;
подготовка специалистов в области охраны труда в том числе в образовательных учреждениях высшего и среднего профессионального образования а также в учреждениях имеющих лицензию на право их подготовки;
установление государственной статистической отчётности об условиях труда о
несчастных случаях на производстве и профессиональных заболеваниях и их материальных последствиях;
осуществление мероприятий по пропаганде передового опыта в области охраны труда;
международное сотрудничество в области охраны труда.
6 Электробезопасность
Электробезопасность на участке обеспечивается следующими мероприятиями согласно ГОСТ 12.1.038-82:
заземление станин оборудования корпусов электродвигателей и оборудования пультов и приборов управления;
изоляция токоведущих частей;
защитное отключение электроустановок;
средства индивидуальной защиты.
Заземленное устройство состоит из заземлителя (одного или нескольких металлических элементов погруженных на определенную глубину в грунт) и заземляющих проводников соединяющих заземленное оборудование с заземлителем.
Защитное заземление – это преднамеренное электрическое соединение с землей или ее эквивалентом металлических нетоковедущих частей электрического и технологического оборудования которые могут оказаться под напряжением.
Конструктивными элементами защитного заземления являются заземлители – металлические проводники находящиеся в земле и заземляющие проводники соединяющие заземленное оборудование с заземлителем.
При защитном заземлении используется явление возникающее во время стекания тока в землю при котором происходит резкое снижение потенциала заземлившейся токоведущей части до значения
где φз - потенциал заземлителя В;
Iз - ток стекающий в землю А;
Rз - сопротивление стеканию тока Ом.
Заземлители могут быть естественные и искусственные.
На рассматриваемом нами участке в качестве искусственных заземлителей применяются стальные полосы уложенные под пресса.
Кроме заземления на производстве используется еще и зануления. Зануление является одним из средств обеспечивающих безопасную эксплуатацию электроустановок. Оно выполняется присоединением к неоднократно заземленному нулевому проводу корпусов и других конструктивных металлических частей электрооборудования которые нормально не находятся под напряжением но могут оказаться под ним при повреждении изоляции.
Зануление как и защитное заземление предназначено для устранения опасности поражения людей электрическим током при пробое изоляции и проходе напряжения на корпус. Но выполняется эта задача другим способом - автоматическим отключением оборудования поврежденной установки от сети.
Защитное отключение обеспечивает автоматическое отключение электроустановки при возникновении в ней опасности поражения током.
Принцип защиты человека в этом случае заключается в ограниченном времени протекания через тело человека опасного тока.
Устройство защитного отключения (УЗО) постоянно контролирует сеть и при изменении ее параметров вызванном подключением человека в сеть отключает сеть или ее участок.
Действие электрического тока на организм человека своеобразно и носит разносторонний характер. Электрический ток проходящий через тело человека оказывает термическое электролитическое и биологическое воздействие на различные системы организма. При этом могут возникнуть нарушения деятельности жизненно важных органов человека: мозга сердца и легких. Все виды действия электрического тока на организм человека можно объединить в два основных: электрические травмы и электрические удары.
Электрические травмы - это местные повреждения тела: ожоги металлизация кожи механические повреждения кожи.
Ожог может быть вызван прохождением электрического тока непосредственно через тело человека. Механические повреждения являются следствием непроизвольных сокращений мышц организма под действием тока. При этом возможны разрывы кожи кровеносных сосудов и нервной ткани вывихи суставов и даже переломы костей. К данному виду травм относятся ушибы и переломы связанные с падением человека с высоты ударами об оборудование или элементы здания в результате непроизвольного движения или потери сознания при воздействии электрического тока. Электрический удар вызывает возбуждение живых тканей организма проходящим через него электрическим током сопровождающееся непроизвольными судорожными сокращениями мышц в том числе мышц сердца. В результате могут возникнуть различные нарушения жизнедеятельности организма и даже полное прекращение деятельности органов дыхания и кровообращения.
Причины несчастных случаев от электрического тока разнообразны и многочисленны но основными из них при работе с электроустановками напряжением до 1000В можно считать:
) случайное прикосновение к токоведущим частям находящимся под напряжением;
) прикосновение к нетоковедущим частям электроустановок случайно оказавшимся под напряжением вследствие повреждения изоляции или другой неисправности;
) попадания под напряжение во время проведения ремонтных работ на отключенном электрооборудовании из-за ошибочного его включения;
) замыкание провода на землю и возникновение шагового напряжения на поверхности земли или основания на котором находится человек.
По степени опасности поражения электрическим током рассматриваемый цех относится к помещениям с повышенной опасностью характеризуется наличием в нем токопроводящих полов возможностью одновременного прикосновения к имеющим соединения с землей металлическим элементам технологического оборудования или металлическим конструкциям здания и металлическим корпусом электрооборудования.
В проекте приняты: защитное заземление от поражения электрическим током при прикосновении к металлическим поверхностям оказавшимся под напряжением. Обеспечивается это снижением напряжения между оборудованием оказавшимся под напряжением и землей до безопасной величины.
7 Противопожарная безопасность
Предприятия машиностроительной промышленности нередко отличаются повышенной пожарной опасностью так как их характеризует сложность произ-водственных установок значительное количество легковоспламеняющихся и горючих жидкостей сжиженных горючих газов твердых сгораемых материалов большое количество емкостей и аппаратов в которых находятся пожароопасные продукты под давлением разветвленная сеть трубопроводов с запорно-пусковой и регулирующей арматурой.
В соответствии со СНиП2.01.02-85* все производства делят по пожарной взрывной и взрывопожарной опасности на категории. Категории для производств и помещений для чугунного литья представлены в таблице 4.2.
Таблица 4.2. Категории для производств и помещений для чугунного литья.
Операции и помещения
Категория производства по СНиП
Степень пожаро- и взрывоопасности
Степень опасности помещения
Плавка выдержка и заливка металла в формы
Обрубка обрезка механическая обработка резанием
Приготовление формовочных и стержневых смесей и изготовление форм форм и стержней
Обработка отливок на шлифовальных полировальных наждачных и заточных станках
пожаро-взрывоопасное
Нанесение лакокрасочных покрытий на изделия из магниевых сплавов
Склады изделий из чугуна и его сплавов
Применение автоматических средств обнаружения пожаров является одним из основных условий обеспечения пожарной безопасности в машиностроении так как позволяет оповестить дежурный персонал о пожаре и месте его возникновения. Система пожарной сигнализации состоит из пожарных извещений линий связи и приемных станций.
В проекте приняты: все пожароопасные помещения оснащаются средствами пожаротушения. Для проектируемого цеха средства пожаротушения представлены в таблице 4.3.
Таблица 4.3 Средства пожаротушения.
Материалы и область тушения
Средства пожаротушения
Твердые горючие материалы (в том числе металлы)
Порошковые сухие огнетушители
Формовочные и стержневые отделения
Горючие жидкости с температурой вспышки более 45°С
Модельное и шихтовое отделение
Дерево уголь пластмассы и др.
Вода в виде компактной струи пена водяной пар
Участки сушки форм и стержней
Легковоспламеняющиеся и горючие жидкости твердые сгораемые материалы
Небольшие очаги пожаров легковоспламеняющихся и горючих жидкостей
8 Мероприятия по повышению устойчивости функционирования предприятия в чрезвычайных ситуациях
Чрезвычайная ситуация - состояние при котором в результате возникновения чрезвычайных ситуаций на объекте определенной территории или акватории нарушаются нормальные условия жизни и деятельности людей возникает угроза их жизни и здоровью наносится ущерб имуществу населения народному хозяйству и окружающей природной среде.
Чрезвычайная ситуация в том числе аварии на промышленных объектах в своем развитии проходят пять условных типовых фаз:
I. - накопление отклонений от нормального состояния или процесса;
II. - инициирование чрезвычайного события (аварии катастрофы или стихийного бедствия). Этот период можно назвать «аварийной ситуацией» - авария еще не произошла но ее предпосылки налицо. В этот период в ряде случаев существует реальная возможность ее предотвратить либо существенно уменьшить ее масштабы;
III. - процесс чрезвычайного события во время которого происходит непосредственное воздействие на людей объекты и природную среду первичных поражающих факторов;
IV. - выход аварии за пределы предприятия и действия остаточных факторов поражения;
V. - ликвидация последствий аварий и природных катастроф устранение результатов действия опасных факторов порожденных аварией или стихийным бедствием проведение спасательных работ в очаге аварии или в районе стихийного бедствия и в примыкающих к объекту пострадавших зонах.
Среди мероприятий по подготовке к работе в условиях чрезвычайной ситуации можно выделить следующие мероприятия:
обеспечение безопасности всех работающих;
защита оборудования и коммуникации;
создание минимального запаса необходимых материально-технических ресурсов;
подготовка к использованию местных ресурсов;
обеспечение автономными источниками энерго- и водоснабжения;
обеспечение аварийного освещения территорий и помещений.
При угрозе наступления чрезвычайной ситуации главные специалисты предприятия обеспечивают:
работоспособность технологического оборудования составление заявок на получение и замену оборудования и разработку графика безаварийной остановки производства – главный механик;
разработку и хранение технологической документации – главный технолог;
энергоснабжение работу коммунальных систем в пределах заводской территории установку систем пожаротушения – главный энергетик;
защиту рабочих и практические работы по защите технологического оборудования - начальники цехов;
снабжение сырьем материалами комплектующими изделиями сбыт продукции – служба снабжения и сбыта;
укрытие рабочих и членов семей в загородной зоне обеспечение всеми видами продовольствия и медикаментами – отдел быта.
Под устойчивостью функционирования промышленного предприятия понимают возможность выпуска продукции с заданной номенклатурой в установленное время а также восстановление производства при средних и слабых разрушениях. Повышение устойчивости технических систем и объектов достигается проведением инженерно-технических и организационных мероприятий которым всегда предшествует исследование устойчивости конкретного объекта.
К ликвидации последствий чрезвычайной ситуации в зависимости от масштаба очага поражения могут привлекаться:
при местном очаге поражения - невоенизированные формирования повышенной готовности предприятия войсковые части гражданской обороны;
при региональном или областном очаге поражения - те же формирования плюс военные части Вооруженных сил по разрешению Президента РФ также невоенизированные формирования повышенной готовности родственных предприятий из других городов;
при больших очагах поражения - те же формирования и спасательные формирования МЧС РФ.
Ликвидация чрезвычайных ситуаций считается завершенной по окончании проведения аварийно-спасательных и других неотложных работ.
Спасательные и другие неотложные работы в очагах поражения включают:
разведку очага поражения принятие решения на порядок проведения спасательных работ в том числе распределение сил и средств на локализацию и тушение пожаров спасение людей из горящих зданий;
розыск и вскрытие заваленных защитных сооружений гражданской обороны
розыск и извлечение из завалов пострадавших;
санитарная обработка людей обеззараживание транспорта технических сооружений зданий систем и промышленных объектов;
подготовка к проведению восстановительных работ на промышленных объектах.
Спасательные формирования в зависимости от масштабов очага поражения могут быть подчинены:
при местном очаге поражения - директору завода или главе администрации города;
при региональном или областном очаге поражения - начальнику гражданской обороны республики или области;
при больших очагах поражения – начальнику гражданской обороны РФ.
Организация спасательных работ на объекте. При прибытии команды в очаг поражения необходимо:
доложить о начале спасательных работ;
получить разведывательные данные;
определить возможность выполнения задачи своими силами;
разместить пункт управления работами в районе наиболее сохранившегося защитного сооружения;
выставить постоянный химический наблюдательный пост для контроля за воздушной средой и передачи сигналов управления работами;
продемонстрировать сигналы управления работами («Приступить к работе!» «Прекратить работу! Стоп!» «Тревога! (в укрытие)»);
определить размещение площадки сбора пораженных и путей подъезда транспорта.
Таким образом работы описанные в данном разделе позволяют правильно проводить организацию спасательных работ в зоне чрезвычайной ситуации лучше подготовиться к защите работников предприятия членов их семей производственного оборудования и повысить устойчивость работы предприятия в условиях чрезвычайных ситуаций мирного и военного времени.
9 Проведение спасательных работ
Спасательные и другие неотложные работы (АСИДНР) в очагах поражения будут проводиться в сложной обстановке в условиях полных и сильных разрушений сплошных завалов пожаров поражения атмосферы и местности и возможного затопления.
При определении объема работ и оценке степени возможных разрушений очаг поражения вызванный ядерным взрывом принято условно делить на зоны каждая из которых имеет свои особенности. Применительно к гражданским и промышленным зданиям степени разрушения характеризуются следующим состоянием конструкций:
Зона полного разрушения. Промышленные и общественные здания и технологическое оборудование восстановлению не подлежат.
Зона сильного разрушения. Промышленные и общественные здания восстановлению не подлежат. Дополнительно сохраняются усиленные ПРУ.
Зона средних разрушений. Здания требуют среднего и капитального ремонта.
Зона слабых разрушений. Здания требуют текущего ремонта.
Все спасательные формирования МЧС во взаимодействии с формированиями служб должны приступить к спасению людей находящихся под обломками разрушенных зданий и других сооружений к обеспечению выхода из убежищ МЧС с заваленными или поврежденными выходами.
Для устройства проходов в первую очередь используют пустоты и щели образовавшиеся между обрушившимися элементами зданий. Проходы между крупными глыбами можно устраивать если они хорошо зажаты не опрокидываются и не проваливаются.
АСИДНР проводятся с целью: спасения людей и оказания помощи пораженным; локализации аварий и устранения повреждений препятствующих проведению спасательных работ. Для организации более эффективного управления проведением АСИДНР с учетом их характера и объема рационального использования имеющихся сил и средств на территории объекта определяются места работ учитывая особенности территории объекта характера планировки и застройки расположение защитных сооружений и технологических коммуникаций а также транспортных магистралей.
Содержание спасательных работ: ведение разведки маршрутов выдвижения формирований и участков (объектов) работ; локализация и тушение пожаров на участках (объектах) проведения работ и на путях выхода к ним; подача воздуха в заваленные защитные сооружения; розыск пораженных и извлечение их из завалов поврежденных и горящих зданий загазованных и задымленных помещений; вскрытие разрушенных поврежденных заваленных защитных сооружений и спасение находящихся в них людей; оказание первой медицинской и первой врачебной помощи пораженным людям и эвакуация их в лечебные учреждения; вывод населения из опасных мест (сильно зараженных и затапливаемых районов) в безопасные (менее зараженные) или незараженные районы; санитарная обработка людей и обеззараживание их одежды территории сооружений техники.
Содержание неотложных работ: прокладка колонных путей и устройств проездов в завалах и на зараженных участках; локализация аварий на газовых энергетических и других сетях; укрепление или обрушение конструкций зданий и сооружений угрожающих обвалом препятствующих безопасному движению и проведению спасательных работ.
АСИДНР организуются в минимально короткие сроки и проводят непрерывно днем и ночью в любую погоду до полного их завершения.
Успешное проведение спасательных и других неотложных работ достигается: своевременной организацией и непрерывным проведением разведки; созданием группировки сил и средств быстрым их выдвижением на объект работ; умелым руководством со стороны начальников штабов и служб МЧС деятельностью подчиненных при организации и проведении АСИДНР; организацией и поддержанием непрерывного взаимодействия органов управления формирований и других сил и средств привлекаемых к спасательным и другим неотложным работам.
Группировка сил МЧС для организованного проведения АСИДНР создается в мирное время решением начальника МЧС города. Состав и построение группировки уточняется при угрозе нападения противника а также после нанесения ядерных ударов в соответствии со сложившейся обстановкой наличием и состоянием сохранившихся сил средств и объемов работ в очагах поражения.
В группировку сил включаются объектовые и территориальные формирования городских и сельских районов а также воинские части МЧС и воинские части Вооруженных сил РФ по приказу Президента РФ. Она может состоять из формирований первого эшелона второго эшелона и резерва. Формирования входящие в состав эшелонов распределяются по сменам с соблюдением целостности их организационной структуры и производственного принципа. Состав эшелонов количество и состав смен определяются исходя из конкретной обстановки сложившейся в очагах поражения а также наличия сил и средств.
Для организации спасательных работ в очаге поражения исключающих травматизм выполняются следующие мероприятия:
С прибытием в очаг поражения им ставится задача проведения разведки;
Определяется место размещения пункта управления работами;
Выставляется постоянный химический наблюдательный пост;
Демонстрируются сигналы управления работами «Начать работу» «Прекратить работу» «Тревога» (в укрытие);
Определяется размещение площадки сбора пораженных;
Принимается решение по данным разведки на порядок проведения спасательных работ;
Ставится задача первой смене на начало работ и определяется порядок укрытия неработающей смены. На этом этапе работой первой смены руководит заместитель командира формирований. На втором этапе то есть при работе второй и последующих смен спасательными работами руководит командир формирований.
10 Вопросы рассмотренные разделе
Назначение раздела.
Характеристика производства.
Создание оптимальных условий труда. Общие требования комфортных условий на рабочем месте. Вентиляция освещение.
1. Общие требования.
2. Вентиляция и отопление производственного корпуса участка цеха.
2.1. Расчет вентиляции.
3. Освещение рабочего участка.
Защита от негативных факторов производственной среды.
2. Производственная вибрация. Источники вибрации и ее влияние на человека;
3. Электромагнитное излучение.
Основные положения действующего законодательства РФ об охране труда.
Электробезопасность.
Противопожарная безопасность.
Мероприятия по повышению устойчивости функционирования предприятия в чрезвычайных ситуациях;
Проведение спасательных работ.
Целью данного проекта являлось проектирование литейного цеха для производства 40 000 т годных отливок из стали в разовые песчано- глинистые формы.
Проект содержит следующие разделы записки.
а) расчет производственной программы;
г) расчет плавильного отделения;
е) расчет стержневого отделения;
з) расчет рабочей силы.
б) анализ конструкции;
в) технологический процесс получения отливки.
Экономическая часть включает:
а) состав годовой сметы затрат на производство 1 тонны жидкого расплава;
б) составление калькуляции себестоимости 1 тонны жидкого расплава;
в) расчет себестоимости 1 тонны годных отливок;
г) расчет капитальных вложений на строительство цеха;
е) расчет эффективности и срока окупаемости проекта с помощью программы «Альт-Инвест».
Все формовочные и шихтовые материалы поступают на склады где должны быть минимальные но достаточные для обеспечения нормальной работы цеха их запасы.
Чугунный и стальной лом ферросплавы прибывают на склады в открытых вагонах на платформах и на машинах. Разгрузку лома и ферросплавов имеющих магнитные свойства из вагонов в закрома выполняют магнитными мостовыми кранами грузоподъемностью 10 т с грузоподъемными магнитами обеспечивающими быструю разгрузку вагонов.
Ферросплавы немагнитные разгружают грейфером.
Известня к и другие флюсы поступают на склад в открытых полувагонах или на платформах как правило в дробленом виде; их разгружают в приемную яму из которой грейфером передают в закрома для хранения и затем грейфером транспортируют в расходные бункера для шихтовки.
Огнеупорные изделия прибывшие в пакетах и в контейнерах или на поддонах в открытых вагонах разгружают с рампы погрузчиками которые доставляют их к местам складирования и затем к потребителям. Огнеупорные материалы идущие на приготовление футеровочной массы (огнеупорная глина песок бой огнеупорного кирпича и др.) хранятся в закромах и транспортируются на участок подготовки грейфером.
Плавка металла осуществляется в дуговых электрические печах из которых металл передается с помощью раздаточных кранов на формовочные линии для заливки в формы.
Изготовление форм заливка выбивка производится на комплексно автоматизированных формовочных линиях.
В цеху установлены: одна линия с размерами опок 1500х1100х400400 с производительностью 220 форм в и одна линия с размерами опок 1100х750х300300 с производительностью 250 форм в час.
Линии снабжены заливочными установками для автоматической и механизированной заливки стали в формы.
Приготовление формовочной смеси осуществляется в смесеприготовительных установках отдельно для каждой лини что обеспечивает снабжение формовочных линий смесью в необходимом количестве и требуемого качества. В состав смесеприготовительной установки входят высокопроизводительные смесители непрерывного действия оборудование для дробления просеивания увлажнения охлаждения и разрыхления формовочной смеси.
Изготовление стержней предусмотрено на стержневых машинах методом изготовления по ненагреваемой оснастке. Стержни извлеченные из оснастки проходят зачистку ок раску и сушку после окраски.
Подача стержней на формовочную линию осуществляется через систему ПТК и погрузчиками.
Выбитая из формы отливка вместе с литниками поступает в охладительную галерею. Охлажденные отливки поступают на дробеметную очистку. Основная масса отливок очищается в проходных дробеметных камерах и барабанах.
Отделение литников и сортировка отливок происходит на пластинчатых и ленточных конвейерах. Нормализация отливок осуществляется в проходных термических печах.
После снятия напряжений отливки проходят вторичную очистку в очистных барабанах периодического действия и проходных дробеметных камерах.
Технологическая цепочка тесно связывает все подразделения цеха.
Плавильное отделение связано с формовочным монорельсовую систему раздачи жидкого металла.
Единая монорельсовая система позволяет передать металл от любой раздаточной печи к любой формовочной линии. Стержневое отделение связано с формовочным через склад стержней. Формовочно- заливочное отделение связано с термообрубным через охладительную галерею и межоперационные склады литья.
Ввиду большой разницы в производительности формовочных и очистных агрегатов в состав термообрубного отделения входят межоперационные склады литья для непрерывной отгрузки готовой продукции потребителю.
ГОСТ 7.32 - 2017. Правила оформления текстовых документов.
ГОСТ 2.101-2016 Единая система конструкторской документации (ЕСКД). Виды изделий (с Поправкой).
ГОСТ 2.316-2008 Единая система конструкторской документации (ЕСКД). Правила нанесения надписей технических требований и таблиц начертежах.
ГОСТ 2.109-73 Единая система конструкторской документации (ЕСКД). Основные требования к чертежам (с Изменениями N 1-11).
ГОСТ 27884-93 Оборудование литейное. Ряды главных параметров.
ГОСТ Р 53464-2009. Отливки из металлов и сплавов. Допуски размеров массы и припуски на механическую обработку.
ГОСТ 26358-84 Отливки из чугуна. Общие технические условия.
ГОСТ 3212-92 Комплекты модельные. Уклоны формовочные стержневые знаки допуски размеров.
ГОСТ 12.1.005-88 Система стандартов безопасности труда Общие санитарно-гигиенические требования к воздуху рабочей зоны.
ГОСТ 12.3.002-2014 Система стандартов безопасности труда (ССБТ). Процессы производственные. Общие требования безопасности.
ГОСТ 12.2.003-91 Система стандартов безопасности труда (ССБТ). Оборудование производственное. Общие требования безопасности.
ГОСТ 12.4.011-89 Система стандартов безопасности труда (ССБТ). Средства защиты работающих. Общие требования и классификация.
ГОСТ17770-86 «Машины ручные. Требования к вибрационным характеристикам».
ГОСТ 12.4.011-89Система стандартов безопасности труда. Средства защиты работающих. Классификация.
ГОСТ 12.1.006-84 «ССБТ. Электромагнитные поля радиочастот. Допустимые уровни на рабочих местах и требования к проведению контроля».
ГОСТ 12.1.038-82 Система стандартов безопасности труда. Электробезопасность. Предельно допустимые значения напряжений прикосновения и токов.
ГОСТ 17677-82* «Светильники. Общие технические условия».
ГОСТ 24940-96Здания и сооружения. Методы измерения освещенности.
ОНТП 07-95 «Отраслевые нормы технологического проектирования предприятий автомобильной промышленности. Литейные цехи и склады шихтовых и формовочных материалов».
СН 2.2.42.1.8.562-96 Шум на рабочих местах в помещениях жилых общественных зданий и на территории жилой застройки. Санитарные нормы.
СН 245-71 Санитарные нормы проектирования промышленных предприятий.
СНиП2.01.02-85*: Противопожарные нормы
СП 60.13330.2012 Отопление вентиляция и кондиционирование воздуха Актуализированная редакция СНиП 41-01-2003.
СП 52.13330.2016 Естественное и искусственное освещение. Актуализированная редакцияСНиП 23-05-95.
Анурьев В.И. Справочник конструктора машиностроителя: 3 т. - М. Машиностроение 1992. с ил.
Аксенов П.Н. Оборудование литейных цехов. - М.: Машиностроение 1977.
Горский А.И. Расчет машин и механизмов автоматических линий литейного производства. М. Машиностроение 1978.- 551 с ил.
Основы проектирования литейных цехов и заводов. Учебник для ВУЗов по специальности "Машины и технология литейного производства" и "Литейное производство черных и цветных металлов" (Л.И. Фонталов Б.В. Кнорре С.И. Четвертухин и др. под редакцией Б.В. Кнорре) - М. Машиностроение 1979. - 376 с ил.
Титов Н.Д. Степанов Ю.А. Технология литейного производства. Учебник для машиностроительных техникумов 3-е издание переработанное и дополненное. М. Машиностроение 1985 400с.
Методические указания по проектированию литейных цехов. Технико-экономическая часть (Составитель Б.Л. Кузнецов - г. Брежнев).
Сафронов В.Я. Справочник по литейному оборудованию. М. Машиностроение 1985. - 320 с. ил.
Грачев В.А. Воздвиженский В.М. В.В. Спасский. Литейные сплавы и технология их плавки в машиностроении. М. Машиностроение 1984. - 432 с. ил.
Долин П.А. Справочник по технике безопасности - 5-е издание переработанное и дополненное – Москва Энергоиздат 1982 - 800 с. иллюстрированная.
Князевский Б.А. Охрана труда в электроустановках. Учебник для вузов . 3-е издание переработанное и дополненное - Москва Энергоиздат 1983 - 336 с. иллюстрированная.
Козьяков А.Ф. Морозова Л.Л. Охрана труда в машиностроении. Учебник для учащихся среднеспециальных учебных заведений - Москва: Машиностроение 1990 - 256 с. иллюстрированная. 11. Полтев М. К. Охрана труда в машиностроении. Учебник - Москва: Высшая школа 1980 - 294 с. иллюстрированная.
Русак О.Н. Бектобеков Г.В. Справочная книга по охране труда в машиностроении. Л.: Машиностроение. Ленинград. отделение 1989 - 541 с. иллюстрированная.
Шариков Л.П. Справочник по охране труда. В четырех томах. Л.: “Судостроение” 1975 - 536 с. иллюстрированная.
Юдин Е.Я. Белов С.В. Охрана труда в машиностроении. Учебник для машиностроительных вузов - 2-е издание переработанное и дополненное - Москва: Машиностроение 1983 - 432 с. иллюстрированная.
Атаманюк В.Г. и др. Гражданская оборона: Учебник для вузов. Под редакцией Михайлика - Москва: Высшая школа 1986 - 207с.: иллюстрированная.
Пермяков М.А. Лекции по предмету “Гражданская оборона”.
Проектирование новых и реконструкция действующих литейных цехов. Методические указания к выполнению курсового проекта. Сост. Зинин Ю.Н. - СПб.: СЗТУ 2006. - 60с.
Мостовой Н. И. Проектирование новых и реконструкция действующих литейных цехов. Справочные материалы по выполнению курсовой работы и проведения практических занятий для студентов направления 150400.62 БМЕТ - Литейное производство черных и цветных металлов. - Хабаровск.: Тихоокеанский государственный университет 2013. - 31с.
Михайловский В. Н. Электрометаллургия и производство ферросплавов. Методика определения технических показателей плавки в дуговой шахтной электросталеплавильной печи: учеб. пособие В. Н. Михайловский П. В. Ковалев. – СПб. : Изд-во Политехн. ун-та 2011. – 140 с.
Производственный календарь 2019[электронный ресурс]. Код доступа URL:
НПФ КОМТЕРМ Дуговые печи - Российская ассоциация литейщиков [электронный ресурс].
Формовочные и стержневые смеси в литейном производстве [электронный ресурс]. Код доступа URL:
Технология плавки чугуна монопроцессом в дуговой печи [электронный ресурс]. Код доступа URL:
Рекомендуемые чертежи
- 25.01.2023
- 24.01.2023