Проект цеха цветного литья мощностью 2000 т/год по номенклатуре ОАО Гомельский завод литья и нормалей




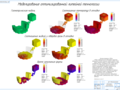
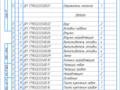
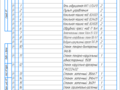
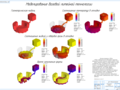
- Добавлен: 24.01.2023
- Размер: 18 MB
- Закачек: 2
Описание
Проект цеха цветного литья мощностью 2000 т/год по номенклатуре ОАО Гомельский завод литья и нормалей
Состав проекта
![]() |
![]() |
![]() ![]() ![]() ![]() |
![]() ![]() ![]() ![]() |
![]() ![]() ![]() ![]() |
![]() ![]() ![]() ![]() |
![]() ![]() ![]() ![]() |
![]() ![]() ![]() ![]() |
![]() ![]() ![]() ![]() |
![]() ![]() ![]() ![]() |
![]() |
![]() ![]() ![]() |
![]() ![]() ![]() |
![]() ![]() ![]() |
![]() ![]() ![]() |
![]() ![]() ![]() |
![]() ![]() ![]() |
![]() ![]() ![]() |
![]() ![]() ![]() |
![]() ![]() ![]() |
![]() ![]() ![]() |
![]() ![]() ![]() |
![]() ![]() ![]() |
![]() ![]() ![]() |
![]() ![]() ![]() |
![]() ![]() ![]() |
![]() ![]() ![]() |
![]() |
![]() |
![]() |
![]() |
![]() |
![]() |
![]() |
![]() |
![]() |
![]() |
![]() |
![]() |
![]() |
![]() |
![]() |
![]() |
![]() |
![]() |
![]() |
![]() |
![]() |
![]() |
![]() |
![]() |
![]() |
![]() |
![]() |
![]() |
![]() |
![]() |
![]() |
![]() |
![]() |
![]() |
![]() |
![]() |
![]() |
![]() |
![]() |
![]() |
![]() |
![]() |
![]() |
![]() |
![]() |
![]() |
![]() ![]() ![]() ![]() |
![]() ![]() ![]() ![]() |
![]() |
![]() |
Дополнительная информация
05. Кокиль для отливки Диск верхний ХМ 09.22.300А Сборочный чертёж.cdw

Диск верхний ХМ 09.22.300А
ГГТУ им. П.О. Сухого
Кокиль к машине мод. 82А405.
Крепёжные изделия (болты; винты) перед сборкой смазать
графитовой смазкой ГОСТ 3333-80.
Маркировать: номер чертежа; номер детали; номер комплекта;
массу кокиля; шрифтом 10-Пр.3 ГОСТ 26.020-80.
Литниковую систему доработать после испытания.
* Размер для справок.
Общие допуски по ГОСТ 30893.2-тК.
Остальные технические требования по СТБ 1014-95.
02. Планировка и разрез цеха.cdw

Водоизоляционный слой
Мелкозернистый бетон
ДМ 1790.01.02.00.00 ТЧ
мощностью 2000 тоннгод
Теоретический чертёж
ГГТУ им. П.О. Сухого
Склад готовой продукции
07. Моделирование оптимизированное.cdw

LVMFlow предназначен для моделирования процессов
формирования отливок в реальных цеховых условиях. В базе
данных программы данные по сплавам разбиты на классы:
силумины и т.д. Моделируемые процессы протекают в
широком температурном интервале
материалов форм так и для сплавов
температурные зависимости теплопроводности
плотности. Если база данных не содержит
нужных пользователю сплавов и материалов форм
может быть пополнена самим пользователем.
В LVMFlow заложена возможность моделирования
двух видов заливки: гравитационное литьё и литьё под
(Продолжение на листе 2)
(Окончание. Начало на листе 1)
На границе металл-форма можно ввести параметры
характеризующие противопригарное покрытие
учитывающие образование воздушных зазоров
между металлом и формой в процессе затвердевания
Результаты моделирования можно сохранять
автоматически для дальнейшего просмотра и создания
архива технологических решений. На отливку заводится
в который записываются все параметры каждого
моделирования. Результаты расчёта функций можно
сохранять в 2D и 3D видах.
Наличие такой системы как LVMFlow в руках
инженера-литейщика позволит значительно удешевить и
ускорить исследовательскую работу по проектированию
ГГТУ им. П.О. Сухого
Геометрическая модель
Соотношение температур в отливке
Время заполнения формы
Время кристаллизации отливки
Моделирование оптимизированной литейной технологии
Соотношение жидкой и твёрдой фазы в отливке
06. Моделирование базовое.cdw

LVMFlow предназначен для моделирования процессов
формирования отливок в реальных цеховых условиях. В базе
данных программы данные по сплавам разбиты на классы:
силумины и т.д. Моделируемые процессы протекают в
широком температурном интервале
материалов форм так и для сплавов
температурные зависимости теплопроводности
плотности. Если база данных не содержит
нужных пользователю сплавов и материалов форм
может быть пополнена самим пользователем.
В LVMFlow заложена возможность моделирования
двух видов заливки: гравитационное литьё и литьё под
(Продолжение на листе 2)
(Окончание. Начало на листе 1)
На границе металл-форма можно ввести параметры
характеризующие противопригарное покрытие
учитывающие образование воздушных зазоров
между металлом и формой в процессе затвердевания
Результаты моделирования можно сохранять
автоматически для дальнейшего просмотра и создания
архива технологических решений. На отливку заводится
в который записываются все параметры каждого
моделирования. Результаты расчёта функций можно
сохранять в 2D и 3D видах.
Наличие такой системы как LVMFlow в руках
инженера-литейщика позволит значительно удешевить и
ускорить исследовательскую работу по проектированию
ГГТУ им. П.О. Сухого
Геометрическая модель
Соотношение температур в отливке
Время заполнения формы
Время кристаллизации отливки
Моделирование базовой литейной технологии
Соотношение жидкой и твёрдой фазы в отливке
04. Матрица левая.cdw

Диск верхний ХМ 09.22.300А
ГГТУ им. П.О. Сухого
Материал-заменитель Сталь 35Л ГОСТ 977-88.
Неуказанные литейные радиусы 3 5 мм.
Неуказанные литейные уклоны - 2 .
Для формообразующих поверхностей шероховатость
неуказанные радиусы 3 5 мм
* Размер для справок.
Общие допуски по ГОСТ 30893.2-тК.
Остальные технические требования по СТБ 1014-95.
08. Экономика.cdw

показатели проектируемого
ГГТУ им. П.О. Сухого
Технико-экономические показатели проектируемого цеха
Внутренняя норма доходности
Показатели эффективности проекта
01. Структурная схема цеха.cdw

03. Диск верхний ХМ 09.22.300A Сборочный чертёж.cdw

Точность отливки 9-0-0-9 ГОСТ 26645-85.
Неуказанные литейные радиусы 3 7 мм.
Неуказанные литейные уклоны наружных поверхностей - 2°;
На поверхностях Ж и И трещины не допускаются.
На 12-ти отверстиях Ж допускаются несквозные раковины
наибольшим измерением до 5 мм
с расстоянием между ними 20 мм
Раковины больших размеров
не выходящие на поверхность И
допускается заделывать
эпоксидной смолой и композициями на основе эпоксидной смолы.
Допускается исправление дефектов отливок любым способом
обеспечивающим прочность и герметичность детали и не
ухудшающим ее товарный вид.
При отливке в кокиль термическую обработку не производить.
Маркировать- номер детали
Г0ГТ26.020-80 и товарный знак завода-изготовителя.
* Размер для справок.
Общие допуски по ГОСТ 30893.2-mK.
Остальные технические требования по СТБ 1014-95.
ГЛАВА 6 СТРОИТЕЛЬНАЯ ЧАСТЬ.docx
Проектирование нового предприятия (цеха) — это создание технического проекта и рабочих чертежей по которым строится новое предприятие или новый цех основного производства.
При проектировании предприятия (цеха) обеспечивается высокий технический уровень и экономическая эффективность максимально используя достижения науки и техники; широкое применение типовых и повторных экономических индивидуальных проектов а также типовых конструкций предприятия (цеха) уменьшает сроки и стоимость проектных работ.
В предпроектный период разрабатываются технико-экономическое обоснование (ТЭО) или технико-экономические расчёты (ТЭР) и задание на проектирование.
ТЭО (ТЭР) обосновывается необходимость и экономическая целесообразность проектирования нового предприятия (цеха). Указываются производственная мощность объекта номенклатура выпускаемой продукции обеспечение материальными топливно-энергетическими трудовыми и другими ресурсами все эти пункты рассмотрены в настоящей записке дипломного проекта.
2 Элементы конструкции цеха
Колонны здания являются основными несущими элементами нагрузки от покрытий ферм подкрановых балок мостовых кранов и других транспортных устройств а также ветровые нагрузки; кроме того колонны обеспечивают пространственную жёсткость здания. Колонны одноэтажного производственного здания выполнены железобетонными (рисунок 6.2.1). Для опирания мостового крана на колонне имеется площадка на которой расположен подкрановый путь.
Рисунок 6.2.1 – Колонны
Фундамент под колонны выполнен из сборного железобетона который состоит из колонны подколонника двух фундаментных плит и бетонных столбиков на которые опирается фундаментная балка. Толщина фундаментных плит 300 мм.
Глубина заложения фундаментов колонн здания подобрана в зависимости от характеристики грунта нагрузок которые несут колонны расстояния между фундаментными колон и фундаментами оборудования или вблизи расположенных котлованов.
Фермы в промышленных зданиях бывают стропильные и подстропильные.
Стропильные фермы служат для поддержания кровли и восприятия действующих на них нагрузок. В проектируемом цехе используются железобетонные сегментные фермы для скатных покрытий (рисунок 6.2.2).
Рисунок 6.2.2 – Ферма сегментная
Световые и аэрационные фонари устраивают для освещения удалённых от окон рабочих мест и для аэрации помещений в цехах.
Тип фонарей назначен в соответствии с технологическими и санитарно–гигиеническими требованиями и климатическими условиями района расположения завода. Для центральной климатической зоны использованы двусторонние фонари с вертикальным остеклением (рисунок 6.2.3.).
Расстояние от торцов фонарей до наружных стен здания или до стен в местах перепада высот здания принято равным шагу стропильных конструкций.
Рисунок 6.2.3 – Светоаэрационный фонарь
Полы в цехах воспринимают нагрузки от автотранспорта людского потока перетаскивания и складирования различных грузов и т.д.
Они должны быть достаточно устойчивыми к механическим тепловым и химическим воздействиям удовлетворять санитарно–гигиеническим требованиям (обеспечивать возможность содержания их в чистоте не выделять пыли не быть скользкими хорошо промываться). Полы проектируют по СНиП 2.03.13—88. Полы состоят из нескольких слоёв каждый из которых имеет определённое значение.
Конструктивные элементы пола принимаем следующими (рисунок 6.2.4): покрытие — верхний элемент пола непосредственно подвергающийся эксплуатационным воздействиям (чугунные дырчатые плиты); прослойка — промежуточный слой (мелкозернистый бетон); подстилочный слой — элемент пола на грунте (бетон); грунт.
Рисунок 6.2.4 – Конструктивные элементы пола
Рисунок 6.2.5 – Конструктивные элементы кровли
Кровля (рисунок 6.2.5) обеспечивает водонепроницаемость покрытия предотвращая проникновение в здание атмосферных осадков и талых вод. Кровли проектируют по СНиП II-26-76. На рулонный ковёр рулонных кровель нанесён защитный слой гравия. Покрытие состоит из: водоизоляционного ковра (рубероид); цементно-песчаный раствор; утепляющий слой; изоляционный слой; железобетонная плита покрытия.
ГЛАВА 8 ЭКОНОМИЧЕСКАЯ ЧАСТЬ.docx
1.1 Обоснование производственной программы литейного участка
Производственная программа (план производства продукции) является основным документом и исходной базой для организации и планирования производственно-хозяйственной деятельности литейного цеха и предприятия в целом.
Обоснование производственной программы проектируемого литейного цеха начинается с анализа номенклатуры отливок базового предприятия. Исследуются текущие годовые объёмы производства отливок и оцениваются перспективы наращивания объёмов производства. На этом основании разрабатывается годовая производственная программа литейного цеха на 2018 год. Результаты представлены в таблице 2.1.1.
1.2 Описание объекта производства и возможных вариантов его изготовления
С учётом конструкционно-эксплуатационных особенностей отливок вида литейного сплава и производственной программы цеха выбираются возможные варианты технологического процесса изготовления отливок.
В качестве отливки-представителя выбрана отливка «Диск верхний ХМ 09.22.300А» изготавливаемая из АК9 (ГОСТ 1583-93). Габаритные размеры детали 333х67 мм масса — 65 кг. Точность отливки 9–0–0–9 по ГОСТ 26645–85. Отливка имеет сложную плоскость разъёма что избавляет от необходимости изготовления отъёмных частей которые непосредственно усложнят сборку кокиля. Для получения данной отливки используется литьё в металлическую форму (кокиль).
Варианты технологических процессов изготовления отливок данной номенклатуры представлены в таблице 8.1.1.
Таблица 8.1.1 – Варианты технологических процессов изготовления отливок
Наименование операции технологического процесса
Краткая характеристика операций
Аналогичный технологический процесс
Плавильное отделение
Индукционная тигельная печь мод. ИЧТ-251С4
ёмкость 25 тонны промышленная частота 50 Гц
Заливочное отделение
Кокильная машина мод. 82А405
36 отлчас при массе отливки 42 кг
Обрубочно-зачистной участок
Станок горизонтально-фрезерный мод. 6Р82
Механический дисковый напильник
Участок термообработки
Проектируемый технологический процесс
Индукционная тигельная печь мод. ИАТ-104М3
промышленная частота 50 Гц
Кокильная машина мод. 82А303
6 отлчас при массе отливки 35 кг
6 отлчас при массе отливки 42 кг
Кокильная машина мод. 82А505
2 отлчас при массе отливки 42 кг
Обрубной пресс мод. П16А
Ленточнопильный станок Stalex BS-5030
Обдирочно-шлифовальный станок мод. ВШ-041
Воздушно-циркуляционный агрегат мод. ПАП-3М
2 Организация и планирование работы отделений литейного цеха
2.1 Организация и планирование работы плавильного отделения
Структурный баланс жидкого металла для проектируемого цеха приведён в таблице 3.1.1. Для обеспечения годовой производственной программы (2 тыс. тонн годного литья) плавильное отделение цеха должно быть обеспечено 2980075 тоннами металлозавалки.
Плановая потребность в сырье и материалах по плавильному отделению проектного литейного цеха представлена в таблице 3.1.5.
2.2 Организация и планирование работы заливочного отделения
Требуемое количество машин литья в кокиль рассчитывается исходя из производственной программы и производительности машины.
Расчёт потребного количества кокильных машин произведён в п. 3.2.2 и сведён в таблицу 8.2.1.
Таблица 8.2.1 – Расчёт числа кокильных машин
Производительность отлчас
2.3 Организация и планирование работы участка по обрубке и зачистке отливок
После извлечения отливок из кокильных машин они поступают на участок обрубки и зачистки. Расчёт годового производственного задания по отделению обрубки и зачистки отливок представлен в таблице 8.2.2.
Таблица 8.2.2 – Расчёт годового производственного задания
Наименование отливки
Ленточнопильный станок
Обдирочно-шлифовальный станок
норма на программу час
2.4 Организация и планирование работы участка термической обработки
В проектируемом цехе необходимо предусмотреть участок термической обработки отливок из алюминия. Термическая обработка является завершающей технологической операцией получения годных отливок. Количество воздушно-циркуляционных агрегатов рассчитывают из объёма производственной программы и производительности оборудования. Расчёт произведён в п. 3.5.
2.5 Выбор и расчёт технологического оборудования
Выбор и расчёт оборудования литейных цехов а также определение необходимых площадей следует производить в последовательности соответствующей технологическому процессу.
Расчёт количества плавильных агрегатов представлен в п. 3.1.5.
Расчёт количества кокильных машин представлен в п. 3.2.2.
Расчёт необходимого количества обрубочно-зачистного оборудования представлен в п. 3.3.
Расчёт необходимого количества агрегатов для термообработки представлен в п. 3.4.
Результат расчёта количества оборудования сведён в таблицу 8.2.3.
Таблица 8.2.3 – Расчёт количества оборудования
Производи-тельность тч (отлч)
Количество оборудования
Коэффи-циент загрузки
Воздушно-циркуляционный агрегат
2.6 Расчёт численности работающих на литейном участке
Расчёт численности работающих по категориям (основные рабочие вспомогательные служащие по категориям) производится отдельно по каждому участку (отделению) литейного цеха. Расчёт численности основных рабочих в проектном цехе представлен в таблице 8.2.4.
Таблица 8.2.4 – Расчёт численности основных рабочих в проектном цехе
Отделение и профессия рабочего-сдельщика
Годовая программа тонн
Коэффициент выполнения норм выработки основными рабочими Квн
Действительный годовой фонд времени работы одного рабочего час
Численность производственных рабочих
Расстановка по сменам
Плавильщик металлов и сплавов
Литейщик металлов и сплавов
Количество вспомогательных рабочих и служащих (руководителей специалистов и технических исполнителей) определяется посредством укрупненного расчёта на основании данных о сложившемся соотношении численности различных категорий работающих на базовом предприятии.
Результаты расчёта численности вспомогательных рабочих и служащих приведены в таблицах 8.2.5 и 8.2.6.
Таблица 8.2.5 – Расчёт численности вспомогательных рабочих
Количество единиц оборудования
Норма обслуживания в смену
Количество смен работы
Явочная численность рабочих чел
Коэффициент перевода явочного числа в списочное
Списочная численность рабочих чел
Монтажник санитарно-технических систем и оборудования (обслуживание плавильных печей)
Распределитель работ
Слесарь по ремонту и обслуживанию систем вентиляции и кондиционирования
Электромонтёр по ремонту и обслуживанию электрооборудования
Служба подготовки производства
Слесарь-инструментальщик
Участок плавки заливки алюминия футеровки печей в горячем состоянии обрубки и термообработки
Грузчик (управление с пола ГПМ)
Машинист крана (крановщик)
Наладчик автоматических линий и агрегатных станков
Наладчик литейных машин
Производственно-диспетчерское бюро
Уборщик помещений (производственных служебных)
Таблица 8.2.6 – Штатное расписание цехового персонала
Структурные подразделения и должностные наименование
Месячная заработная плата руб.
Годовой фонд заработной платы руб.
Заместитель начальника цеха по производству
Заместитель начальника цеха по технологической части
Заместитель начальника цеха по подготовке производства
Ведущий инженер по подготовке производства
Инженер по подготовке производства 1 кат.
Бюро организации и нормирования труда
Ведущий инженер по организации и нормированию труда
Инженер по организации и нормированию труда 2 кат.
Инженер по организации и нормированию труда
Техник по организации и нормированию труда
3 Расчёт величины инвестиций
3.1 Состав инвестиций
В выборе и экономическом обосновании целесообразности применения одного из вариантов технологического варианта важным этапом является оценка и анализ единовременных затрат по каждому варианту. Внедрение новых технологических проектов как правило сопровождается инвестиционным процессом.
Величину инвестиций можно определить по формуле:
где — инвестиции в основные фонды руб.;
— инвестиции в оборотные средства руб.
В общем виде величина инвестиций (капитальных вложений) в основные фонды может быть рассчитана как сумма капитальных вложений в здания () рабочие машины и оборудование () транспортные средства () инструмент () производственный инвентарь ():
В состав оборотных средств включают денежные средства необходимые для создания производственных запасов () основных и вспомогательных материалов топлива предметов в эксплуатации () незавершённого производства () а также для поддержания минимального запаса готовой продукции () на складах предприятия. Все составляющие оборотных средств рассчитываются прямым счетом.
Полная потребность в оборотном капитале определяется как:
3.2 Расчёт инвестиций в здания и сооружения
Величина инвестиций в здания и сооружения литейного цеха определяется по укрупнённым расценкам исходя из объёма здания и средней величины затрат приходящихся на строительство 1 м3 зданий различных типов (по данным ОКС или ОГМ базового предприятия). Объём здания рассчитывается по его наружной площади и высоте. Приближённо наружная площадь равняется 105–11 внутренней. Внутренняя площадь определяется по разработанной планировке основных отделений литейного цеха.
Площадь вспомогательных отделений составляет 25–35 % а конторских и административно-бытовых — 10–15 % от производственной площади.
Результаты расчёта стоимости зданий сооружений и помещений литейного цеха сводим в таблицу 8.3.1.
Таблица 8.3.1 – Стоимость зданий сооружений и помещений литейного цеха
Наименование отделений и участков цеха
Общая стоимость руб.
Производственные отделения
Участок термической обработки
Вспомогательные отделения
Участок для приготовления футеровочных масс
Участок для футеровки и ремонта ковшей
Участок сушки и подогрева ковшей
Участок ремонта индукторов
Участок хранения кокильной оснастки
Склад готовой продукции
Экспресс-лаборатория
Итого производственные помещения:
Конторские помещения
Итого капиталовложений по цеху:
3.3 Расчёт инвестиций в оборудование транспорт инструмент и инвентарь
Капитальные вложения в рабочие машины и оборудование помимо стоимости приобретения включают затраты на транспортировку и монтаж.
Их величина может быть определена следующим образом:
где — принятое количество единиц оборудования
— свободная отпускная цена единицы оборудования
— коэффициенты учитывающие транспортные расходы и расходы связанные с монтажом оборудования (005–010).
При расчёте стоимости инструмента производственного и хозяйственного инвентаря допускается укрупнённый расчёт: оснастка инструмент и приспособления приближённо составляют 10–15 % а производственный инвентарь — 15–2 % стоимости технологического оборудования; хозяйственный инвентарь — 1–15 базовой величины на одного рабочего (основного и вспомогательного) и 2–3 — на одного служащего. Полученные результаты с разбивкой по группам оборудования (технологическое подъёмно-транспортное энергетическое инструмент и т.д.) сводятся таблицу 8.3.2.
Таблица 8.3.2 — Стоимость оборудования инструмента и инвентаря литейного цеха
Наименование оборудования
Модель тип оборудования
Количество оборудования шт
Установленная мощность кВт
Суммарная мощность оборудования кВт
Отпускная цена за 1 ед. оборудования руб.
Стоимость оборудования всего руб.
Амортизационные отчисления
Индукционная тигельная печь
Продолжение таблицы 8.3.2
Подъёмно-транспортное оборудование (25%):
Энергетическое оборудование (20%):
3.4 Расчёт потребности в оборотных средствах
Потребность в оборотном капитале определяется в соответствии с общепринятой методикой на основании исходных данных базового предприятия.
Результаты расчёта оформляем в таблицу 8.3.3.
Таблица 8.3.3 – Расчёт потребности в оборотных средствах
Элементы нормируемых оборотных средств
Ср. дневной расход руб.
Норматив оборотных средств руб.
Незавершённое производство
Малоценная быстроизнашивающаяся оснастка
-50% от стоим. год. расхода
Запасные части для ремонта оборудования
-3% от стоимости оборудования цеха
Коэффициент оборачиваемости
Длительность одного оборота оборотного средства дней
Расчёт сводной ведомости потребности в инвестициях для реализации проекта сводим в таблицу 8.3.4.
Таблица 8.3.4 – Сводная ведомость потребности в инвестициях
Состав основных фондов
Стоимость основных фондов руб.
Структура основных фондов (в % к итогу)
Сумма амортизационных отчислений руб.
Рабочие машины и оборудование
Измерительные и регулировочные устройства
Транспортные средства
4 Калькулирование себестоимости продукции
В цехах цветного литья калькулирование себестоимости производится по одному переделу на 1 тонну годных отливок.
Калькулирование себестоимости 1 тонны годных отливок сведено в таблицу 8.4.1.
Таблица 8.4.1 – Плановая калькуляция 1 тонны алюминиевых отливок
Элементы и статьи расходов
Затраты на годовую программу руб.
На 1 тонну жидкого алюминия руб.
Итого жидкого металла
Отходы – литники прибыли сплески и сливы
Годные отливки за вычетом отходов и брака
Флюсы и модификаторы
Основная заработная плата производственных рабочих
Дополнительная заработная плата
производственных рабочих
Налоговые выплаты и отчисления
Общепроизводственные расходы
Цеховая себестоимость 1 тонны годных отливок
Общехозяйственные расходы
Производственная себестоимость 1 тонны годных отливок
Коммерческие расходы
Полная себестоимость 1 тонны годных отливок по проектному цеху
4.1. Расчёт затрат на основные материалы
Затраты на материалы определяются исходя из установленных на базовом предприятии или планируемых норм расхода и покупных цен на них. Цены на все виды материалов берутся по заводским данным а при их отсутствии — по прейскурантам предприятий-поставщиков или другим справочным источникам. Покупная цена помимо отпускной включает в себя транспортно-заготовительно-погрузочные расходы (франко-условия) которые составляют примерно 3–5% от отпускной цены основных и вспомогательных материалов.
Потребность в основных материалах и затраты сводятся в таблицу 8.4.2.
Таблица 8.4.2 – Потребность и затраты на основные материалы
Наименование материалов
Норма расхода на 1000 кг годного литья
Годовая программа по литью тонн
Годовая потребность на программу тонн
Цена на материалы руб. за 1 тонну
Расчёт затрат на основные материалы
Алюминий первичный А5
Алюминий вторичный АК9
Кремний технический КР00 КР0
Магний чушковый первичный МГ90
Лом АЛ кл. А гр. I IV сорт I
Флюс покровно-рафинирующий
Таблетки дегазирующие
Итого с учётом транспортно-заготовительных расходов:
4.2 Топливо и энергия на технологические и прочие цели
В литейном производстве к технологическому относится топливо и энергия расходуемые на осуществление процесса плавки. Силовая энергия — это различные виды энергии топлива сжатого воздуха и воды потребляемые на приведение машин и оборудования в движение. Данные расходы входят в смету затрат на содержание и эксплуатацию оборудования. Затраты на топливо энергию воду для хозяйственных нужд включаются в смету расходов по организации обслуживанию и управлению производством.
Затраты на различные виды энергии топлива и воды определяются исходя из их годового расхода в соответствии с нормами расхода и ценами (тарифами) на их приобретение. Результаты расчёта приведены в таблице 8.4.3.
Таблица 8.4.3 – Потребность и затраты на топливо и энергию для проектного участка
Наименование топлива и электроэнергии
Цена за единицу руб.
Годовая потребность на программу
Затраты на программу руб.
4.3 Расчёт фонда заработной платы работников участка
На основании плановой численности разных категорий работающих литейного цеха рассчитываются соответствующие годовые фонды заработной платы.
Общие затраты по заработной плате производственных рабочих слагаются из затрат на основную и дополнительную зарплату. Дополнительная заработная плата определяется в процентах от основной зарплаты.
Расчёт фонда заработной платы служащих определяется исходя из численности установленных окладов и числа месяцев работы. Результаты расчёта годового фонда заработной платы работающих сведены в таблице 8.4.4.
Таблица 8.4.4 – Годовой фонд заработной платы работающих для проектного цеха
Категории работников
Годовой фонд основной (тарифной) заработной платы руб
Годовой фонд дополнительной заработной платы руб
Основные производственные рабочие:
плавильного отделения
других отделений цеха
Вспомогательные рабочие:
Руководители специалисты
4.4 Общепроизводственные расходы
В данном статье учитываются расходы по организации обслуживанию и управлению производством и расходы по содержанию и эксплуатации машин и оборудования. Расчёт отдельных статей данной сметы расходов ведётся раздельно для плавильного и остальных отделений литейного участка. Смета общепроизводственных расходов приведена в таблице 8.4.5.
Таблица 8.4.5 – Смета общепроизводственных расходов для проектного участка
А. Смета расходов на содержание и эксплуатацию оборудования
Величина расходов тыс. руб
Амортизация оборудования и транспортных средств
Содержание оборудования
Отчисления на социальное страхование
Основная и дополнительная заработная плата вспомогательных рабочих
Износ малоценных и быстроизнашивающихся инструментов и приспособлений
Продолжение таблицы 8.4.5
Б. Смета расходов по организации обслуживанию и управлению производства
Содержание аппарата управления
Амортизация зданий и инвентаря цеха
Содержание зданий сооружений и инвентаря цеха
Текущий ремонт зданий сооружений и инвентаря цеха
Испытания опыты и исследования рационализация и изобретательство
Износ малоценного и быстроизнашивающегося инвентаря
4.5 Общехозяйственные расходы
В статье «Общехозяйственные расходы» учитываются расходы на управление предприятием командировки работников аппарата управления расходы на содержание пожарной и сторожевой охраны канцелярские типографские и другие расходы.
Величина общехозяйственных расходов составляет 15% от величины годового фонда заработной платы основных производственных рабочих.
4.6 Коммерческие расходы
Коммерческие расходы включают расходы на рекламу участие в выставках маркетинг транспортно-экспедиционные расходы расходы на тару и упаковку оплата услуг и прочие расходы. Коммерческие расходы могут быть взяты в размере 5% производственной себестоимости 1 тонны годных отливок.
5 Оценка эффективности проектного варианта литейного участка
5.1 Расчёт свободной отпускной цены 1 тонны годного литья
Для расчёта свободной отпускной цены единицы продукции предлагается использовать метод прямого счета который учитывает полную себестоимость единицы продукции плановую норму рентабельности продукции отчисления в местные и республиканские целевые фонды и налог на добавленную стоимость. Расчёт представлен в таблице 8.5.1.
Таблица 8.5.1 – Расчёт свободной отпускной цены единицы продукции
Полная себестоимость единицы продукции
Отпускная цена единицы продукции без НДС
Налог на добавленную стоимость
Отпускная цена единицы продукции с НДС
5.2 Расчёт балансовой прибыли
Оценка прироста балансовой прибыли от внедрения новых технических и технологических решений осуществляется по одному из трёх вариантов выбираемых в зависимости от результатов предшествующих расчётов (изменение себестоимости выпуска продукции в натуральном выражении цены качества выпускаемой продукции).
В проектном варианте себестоимость единицы продукции снижается по сравнению с аналогичным вариантом а объём выпуска продукции (N) и её качество не изменяется. Расчёт прироста балансовой прибыли в данном случае проводим в следующем порядке (см. табл. 8.5.2).
Таблица 8.5.2 – Расчёт прироста величины балансовой прибыли в проектном варианте
Прибыль балансовая на единицу продукции
Прирост балансовой прибыли на единицу продукции
Прирост балансовой прибыли на весь объем выпуска продукции
5.3 Расчёт чистой прибыли
Определяем прирост величины чистой прибыли предприятия в результате проведения организационно-технических мероприятий. Результаты оформляем в таблицу 8.5.3.
Таблица 8.5.3 – Расчёт чистой прибыли технологического процесса для проектного участка
Налог на недвижимость
Прибыль налогооблагаемая
5.4 Расчёт показателей эффективности проекта
Оценка эффективности вариантов технологического процесса проводится на основании сравнения показателей эффективности использования ресурсов предприятия. Представлена в таблице 8.5.4.
Таблица 8.5.4 – Расчёт показателей эффективности инвестиционного проекта
Годовая производительность труда
Рентабельность инвестиций
Годовой экономический эффект
Срок окупаемости инвестиций
Расчёт денежного потока для проектируемого цеха представлен в таблице 8.5.5.
Таблица 8.5.5 – Расчёт денежного потока для проектируемого цеха
Расчёт величины ежегодных денежных потоков при r=14% представлен в таблице 8.5.6.
Таблица 8.5.6 – Расчёт величины ежегодных денежных потоков
Денежный поток нарастающим итогом
дисконтирования при r=14%
Дисконтированный денежный поток руб.
Расчёт величины ежегодных денежных потоков при r=45% представлен в таблице 8.5.7.
Таблица 8.5.7 – Расчёт величины ежегодных денежных потоков
дисконтирования при r=45%
Строим графики по полученным результативным данным (см. рис. 8.5.1 и 8.5.2).
Рисунок 8.5.1 — Финансовый профиль проекта
6 Основные технико-экономические показатели проекта
Все технико-экономические показатели по проектируемому цеху сводим в таблицу 8.6.1.
Таблица 8.6.1 – Технико-экономические показатели
Наименование показателя
б) по полной себестоимости
Основные производственные фонды
в т.ч. основных рабочих
вспомогательных рабочих
Затраты по участку на 1 тонну годного
Капиталовложения (инвестиции)
Годовой выпуск в тоннах
а) на 1 м² производственной площади
Среднемесячная зарплата
б) 1 основного рабочего
Удельные капиталовложения
Удельная себестоимость
Производительность труда
Чистая текущая стоимость NPV
Коэффициент эффективности проекта PI
Внутренняя норма доходности IRR
Срок окупаемости инвестиций PP
Дисконтированный срок окупаемости DPP
02. ЗАДАНИЕ.docx
механико-технологический
ПО ДИПЛОМНОМУ ПРОЕКТИРОВАНИЮ
группы Л-51 Шатило Леониду Леонидовичу
«Гомельский завод литья и нормалей»
(Утверждена приказом по вузу от
Сроки сдачи студентом законченного проекта
Исходные данные к проекту
Номенклатура отливок
Технологические инструкции и нормативы литейного цеха завода
Чертежи детали «Диск верхний ХМ 09.22.300А»
Данные для выполнения экономической части проекта
Содержание расчётно-пояснительной записки (перечень подлежащих разработке
Глава 1 Общая характеристика проектируемого цеха
Глава 2 Производственная программа цеха
Глава 4 Технологическая часть
Глава 5 Специальная часть
Глава 6 Строительная часть
Глава 7 Охрана труда и экология
Глава 8 Экономическая часть
Глава 9 Энергосбережение
Список использованных источников
Перечень графического материала (с точным указанием обязательных чертежей и
Структурная схема цеха — 1 лист (ф. А1)
Технологическая планировка цеха — 1 лист (ф. А2х3)
Разрез цеха — 1 лист (ф. А1)
Технологическая часть — 3 листа (ф. А1)
Специальная часть — 4 листа (ф. А1)
Технико-экономические показатели проекта — 2 листа (ф. А1)
Консультанты по проекту (с указанием относящихся к ним разделов проекта)
Руководитель и консультант — Герасимова О.В.
Консультант по охране труда — Герасимова О.В.
Консультант по экономической части — Астраханцев С.Е.
Нормоконтроль — Радькин Я.И.
Календарный график работы над проектом на весь период проектирования (с
указанием сроков выполнения и трудоёмкости отдельных этапов)
Введение 1-3 глава (1-3 лист) — до 12.04.18
глава (4-6 лист) — до 03.05.18
глава (7-10 лист) — до 24.05.18
-7 глава — до 07.06.2018
-9 глава (11-12 лист) — до 14.06.2018
Задание принял к исполнению (дата)
ГЛАВА 7 ОХРАНА ТРУДА И ЭКОЛОГИЯ.docx
Охрана труда — это система обеспечения безопасности жизни и здоровья работников в процессе трудовой деятельности включающая правовые социально-экономические организационные технические психофизиологические санитарно-гигиенические лечебно-профилактические реабилитационные и иные мероприятия и средства.
Полностью безопасных и безвредных условий работы не существует. Поэтому задача охраны труда сводится к тому чтобы путём осуществления разноплановых мероприятий свести к минимуму воздействие на человека опасных и вредных производственных факторов характерных для рабочих мест максимально уменьшить вероятность несчастных случаев и профессиональных заболеваний работающих обеспечить комфортные условия труда способствующие высокой производительности.
Мероприятия по охране труда и их проведение всегда экономически выгодны и целесообразны. К основным из них относятся: меры безопасности труда; механизация и автоматизация производственных процессов; улучшение санитарных условий рабочего помещения; меры личной гигиены работающих; меры общественного характера. Это стимулирует сокращение убытков от несчастных случаев уменьшение расходов на всевозможные компенсации промышленных вредностей и опасностей сохранение работоспособности и т.д. В этой связи можно выделить три ведущих направления совершенствования охраны труда: правовое направление — обоснование законодательных норм касающихся рабочего времени отдыха норм охраны труда женщин и подростков а также изучение практики проведения этих норм в жизнь; санитарное направление — изучение влияния вредных факторов на организм работника в процессе труда; техническое направление охраны труда — выявление и профилактика производственных опасностей связанных с условиями труда работающих.
1.1 Микроклимат на производстве
Оптимальные и допустимые величины температуры относительной влажности н скорости движения воздуха устанавливаются ГОСТ 12.1 005-88 с учётом периода (сезона) года категории выполняемых работ по тяжести и времени выполнения работы (является рабочее место постоянным или нет).
Периоды года условно разделены на: холодный (со среднесуточной температурой наружного воздуха менее +10°С); тёплый (со среднесуточной температурой наружного воздуха более +10°С).
Показателями характеризующими микроклимат в рабочей зоне являются:
-температура воздуха t °С;
-относительная влажность воздуха φ %;
-скорость движения воздуха F мс;
-интенсивность теплового облучения работающих от нагретых поверхностей оборудования изделий и открытых источников J Втм;
-атмосферное давление Р Па.
Оптимальные и допустимые величины температуры относительной влажности и скорости движения воздуха представлены в таблице 7.1.1.
Таблица 7.1.1 – Оптимальные и допустимые величины
Относительная влажность %
Скорость движения мс
Допустимая на рабочих местах постоянных и непостоянных не более
Оптимальная не более
Допустимая на рабочих местах постоянных и непостоянных*
Средней тяжести — IIб
* — большая скорость движения воздуха в тёплый период года соответствует максимальной температуре воздуха меньшая — минимальной температуре
Категория тяжести проектируемого цеха — средняя тяжесть — IIб (при тёплом периоде года).
Допустимые величины интенсивного теплового облучения работающих от нагретых поверхностей технологического оборудования материалов и изделий осветительных приборов и т.п. соответствовать показаниям представленным в таблице 7.1.2.
Таблица 7.1.2 – Допустимые величины интенсивного теплового облучения
Облучаемая поверхность тела %
Интенсивность теплового облучения Втм2 не более
Интенсивность теплового облучения от открытых источников (нагретый металл стекло открытое пламя и т.д.) не должна превышать 140 Втм2. При этом облучению не должно подвергаться более 25% поверхности тела и обязательным является использование средств индивидуальной защиты.
Температура наружных поверхностей технологического оборудования ограждающих устройств с которыми соприкасается в процессе труда человек не должна превышать 45°С.
Многие технологические процессы сопровождаются выделением в воздух производственных помещений вредных веществ.
Вредные вещества в воздухе принято подразделять по агрегатному состоянию на твёрдые вещества жидко-парообразные и газы. Пары и газы образуют с воздухом смеси а твёрдые и жидкие частицы вещества — дисперсные системы — аэрозоли которые делятся на пыль (размер твёрдых частиц более 1 мкм) дым (менее 1 мкм) и туман (размер жидких частиц менее 10 мкм).
Источником выделения вредных веществ в проектируемом цехе является технологический процесс плавки металла.
Мероприятия производственной санитарии с целью снижения вредного воздействия загрязнённого воздуха на организм человека предусматривают снижение концентрации вредных примесей до определённых норм. Концентрация этих веществ не должна превышать установленных для них норм (предельно допустимые концентрации ПДК) регламентируемых ГОСТом.
С этой целью на производственных участках проектируемого цеха устанавливается обще обменная и местная вытяжная вентиляция а также вытяжные зонты в местах обильного газовыделения (над плавильными печами).
Понижение температуры воздушной среды осуществляется за счёт применения общеобменной приточно-вытяжной вентиляции воздушного и водного охлаждения нагреваемых поверхностей установкой теплоизоляционных экранов.
1.2 Шум на производстве
Шум — это совокупность звуков различных по частоте и интенсивности вредно влияющих на организм человека. Возникает шум при механических колебаниях в твёрдых жидких и газообразных средах.
Источниками шума могут быть колебания возникающие при соударении трении скольжении твердых тел истечении жидкостей и газов. В производственных условиях источниками колебаний являются работающие станки ручные механизированные инструменты (отбойные рубильные молотки перфораторы) компрессоры кузнечно-прессовое подъёмно-транспортное вспомогательное оборудование (вентиляционные установки кондиционеры) и т.д.
В проектируемом цехе основными источниками шума является обрубное обрезное и зачистное оборудование. Параметры шума основных видов оборудования обрубочно-зачистного участка литейного цеха превышают допустимые значения на 18-27 дБА.
Шум создаваемый основными литейными машинами является широкополосным звуковое поле неоднородно в связи с наличием источников шума различных по уровню акустической мощности и характеру спектра.
Шум создаваемый оборудованием с ударным режимом работы непостоянный с максимальным уровнем звуковой мощности в области средних и высоких частот. Многообразие оборудования используемого на литейных предприятиях обусловливает наличие всех перечисленных разновидностей шума.
Снижения шума на пути его распространения осуществляются за счёт применения: кожухов экранов выгородок звукоизолирующих перегородок звукопоглощающих облицовок глушителей шума.
На рабочих местах где не получается снизить шум до допустимых уровней техническими средствами следует применять индивидуальные средства защиты (СИЗ). В соответствии с ГОСТом 12.1.029-80 СИЗ в зависимости от конструкции подразделяются на противошумные вкладыши противошумные наушники противошумные шлемы и каски и противошумные костюмы.
1.3 Вибрация на производстве
Вибрация — это колебательные процессы происходящие в механических системах.
Источниками вибрации являются технологические процессы оборудование механизмы машины и т.д.
Степень вредного воздействия вибрации на организм человека характеризуется величиной виброскорости (при частоте более 10 Гц) или виброускорением (при частоте колебаний до 10 Гц).
Неблагоприятное воздействие вибрации зависит также от способа её передачи на человека длительности её воздействие и т.д.
Вибрацию подразделяют на местную и общую. Местная вибрация в проектируемом цехе наблюдается при обрезке и зачистке отливок. В условиях литейного производства общая вибрация образуется при сотрясении пола и других частей здания вследствие ударного действия обрубного пресса и других машин.
Основными мероприятиями по устранению вредного воздействия вибрации применяемые в цехе:
-конструктивные технологические и эксплутационные меры снижения вибрации в источнике;
-использование динамически нагруженных фундаментов;
-ограничение вибрации по пути распространения (вибропоглотители виброизоляция);
-использование средств индивидуальной защиты.
1.4 Пожаро- и взрывобезопасность производства
Пожарная безопасность — это состояние объекта при котором с регламентируемой вероятностью исключается возможность возникновения и развития пожара а также обеспечивается защита людей и материальных ценностей от воздействия его опасных факторов. Опасными факторами пожара являются факторы воздействие которых приводит к травме отравлению или гибели человека а также к материальному или экологическому ущербу.
Пожарная безопасность проектируемого цеха определена типовыми правилами пожарной безопасности для промышленных предприятий. Наиболее пожароопасные участки: плавки и заливки. На данных участках в целях пожарной безопасности полы выполнены из огнеупорного кирпича и покрыты металлической плиткой. Между участками плавки и заливки спроектирован пожарный проезд для машин заводской пожарной службы.
Согласно СНиП II-90-81 в зависимости от характеристики обращающихся в производстве веществ и их количества производства подразделяются по взрывной взрыво-пожарной и пожарной опасности на категории А Б В Г Д и Е. Проектируемый цех относится к категории Г: характеризуется наличием несгораемых веществ и материалов в горячем раскалённом или расплавленном состоянии процесс обработки которых сопровождается излучением теплоты искр и пламени; твёрдых жидких и газообразных веществ которые сжигаются или утилизируются в качестве топлива.
Для обеспечения при пожаре безопасной эвакуации людей находящихся в зданиях производственного вспомогательного и другого назначения предусматриваются эвакуационные выходы. Они должны обеспечивать безопасный выход людей наружу кратчайшим путём в минимальное время. Эвакуационными считаются выходы если они ведут из помещения первого этажа наружу непосредственно или через коридор вестибюль лестничную клетку; из помещений любого этажа кроме первого в коридор или проход ведущий к лестничной клетке или в лестничную клетку имеющую самостоятельный выход наружу или через вестибюль; из помещения в соседние помещения в том же этаже обеспеченные выходами наружу. Эвакуационных выходов должно быть как правило не менее двух.
Помещения где хранятся или производятся работы со взрыво- и пожароопасными веществами должны быть оборудованы средствами пожаротушения и приняты пожарной охраной.
Запрещается производство работ со взрывоопасными и пожароопасными веществами в грязной промасленной спецодежде а также в одежде из синтетических волокон. Во взрывоопасной среде работы должны выполняться инструментом изготовленным из цветных металлов.
Меры пожарной профилактики должны предотвращать загорания и обеспечить локализацию пожара. Противопожарные мероприятия проводятся в соответствии с требованиями правил пожарной безопасности типовых инструкций строительных норм и правил в части противопожарных требований.
Применяемые средства пожаротушения должны максимально ограничивать размеры пожара и обеспечивать его тушение.
Для предотвращения пожара в начальной стадии в цехе используются первичные средства пожаротушения: огнетушители; пожарные щиты укомплектованные шанцевым инструментом; ящики с песком; асбест войлок ёмкости с водой. Они предназначены для ликвидации начинающихся очагов пожара силами персонала обнаружившего загорание. Они располагаются в открытых и доступных местах и должны постоянно находиться в состоянии «боевой готовности».
В качестве средств индивидуальной защиты на участках должны храниться респираторы или противогазы с расчётом на количество людей в смену.
1.5 Электробезопасность на производстве
Электробезопасность — система организационных и технических мероприятий и средств обеспечивающая защиту людей от вредного и опасного воздействия электрического тока электрической дуги электромагнитного поля и статического электричества.
Проектируемый цех относится к помещениям с повышенной опасностью — помещения характеризующиеся наличием в них одного из следующих условий создающих повышенную опасность поражения людей электрическим током: высокая температура сырость или токопроводящая пыль; токопроводящие полы (металлические земляные железобетонные кирпичные и др.); возможность одновременного прикосновения человека к металлоконструкциям зданий имеющих соединение с землёй технологическим аппаратам механизмам и другому с одной стороны и к металлическим корпусам электрооборудования (открытым проводящим частям) с другой стороны.
Для создания производственных условий при которых воздействие электрического тока полностью исключается необходимо стремиться к тому чтобы конструкция элементов электрооборудования его устройство и монтаж в производственных помещениях а также техническое состояние электрооборудования устройств защитного заземления и зануления находились в полном соответствии со специальными требованиями правил соблюдение которых строго обязательно для всех рабочих.
Рабочий не должен прикасаться к токоведущим элементам электрооборудования и освещения и к электропроводке не должен открывать дверей электрошкафов. Рабочему запрещается прикасаться к неизолированным или повреждённым проводам и электрическим устройствам наступать на переносные электрические провода лежащие на полу самостоятельно производить ремонт неисправного электрооборудования и инструмента. Обо всех замеченных неисправностях рабочий должен немедленно извещать администрацию цеха и в первую очередь мастера.
К индивидуальным средствам защиты относятся: диэлектрические резиновые коврики диэлектрические боты и изолирующие подставки.
1.6 Расчёт искусственного освещения
Для расчёта равномерного освещения при горизонтальной рабочей поверхности применяют метод светового потока (коэффициент использования) учитывающий отражающий световой поток.
Световой поток лампы рассчитывают по формуле:
где — нормированная минимальная освещённость лк;
— площадь освещаемого участка м2;
— коэффициент минимальной освещённости;
— коэффициент запаса;
— число светильников;
— коэффициент использования светового потока значение которого определяют по таблице с учётом показателя помещения.
Показатель помещения рассчитывается по формуле:
где и — габариты цеха м;
Общая потребляемая мощность определяется по формуле:
Исходные данные для расчёта приведены в таблице 7.1.3.
Таблица 7.1.3 – Исходные данные
Напряжение осветительной сети
Коэффициент запаса kз
Коэффициент минимальной освещённости z
Для освещения проектируемого цеха выбраны газоразрядные лампы ДРЛ и светильники УПМ-15.
Для нахождения значения рассчитываем показатель помещения:
Световой поток ламп:
Окончательно выбираем для цеха лампы ДРЛ 250 со световым потоком 13000 лм. Количество ламп в цеху — 52 шт.
Общая потребляемая мощность:
Охрана окружающей среды от загрязнения промышленными технологическими и вентиляционными выбросами относятся к числу актуальных проблем и имеет огромное социальное экономическое и экологическое значение.
Источниками пыли и газовыделений в литейном цехе являются плавильные агрегаты участки очистки литья формовки и изготовления стержней. При производстве 1 тонны отливок в атмосферу выделяются: 10–50 кг пыли 150–300 кг СО 15–2 кг — СО2 и SО2.
В связи с постоянным ростом количества литейных предприятий возрастает опасность существенного увеличения валовых выделений пыли газов изменение и усложнение их состава. Основой решения задачи создания благоприятных санитарно–гигиенических условий в литейном цехе и защиты окружающей среды является разработка и внедрение малоотходных и безотходных технологий герметизированного оборудования нетоксичных материалов экологически эффективного оборудования очистки выбросов позволяющих минимизировать попадание в атмосферу вредных и токсичных веществ.
В настоящее время затраты на санитарно–технические средства (вентиляцию пылеудаление очистку воздуха и сточных вод защиту от шума и вибрации) при строительстве литейного цеха составляют 20–30 % всех капитальных затрат.
В современных условиях когда происходит неуклонная интенсификация производственных процессов наиболее радикальными способами борьбы с выделяющимися вредными веществами являются: устройства местной вентиляции и в первую очередь местных отсосов встроенных непосредственно в оборудование. Таким способом это позволит максимально очистить воздух.
ГЛАВА 9 ЭНЕРГОСБЕРЕЖЕНИЕ.docx
Проблема энергосбережения является комплексной и включает целый ряд задач. Поэтому попытки решать отдельные вопросы обособленно чаще всего не приводят к хорошему результату. Только рассмотрение их оптимальных сочетаний позволит достигнуть необходимого эффекта.
Выделяются два пути энергосбережения: использование первичных и вторичных энергоресурсов. Причём при использовании первичных источников энергии образовавшихся в результате геологического развития Земли главный упор необходимо сделать на использование первичных возобновляемых источников энергии (использование энергии Солнца ветра приливов-отливов геотермальной энергии и т.д.) или иначе альтернативных источников энергии. В данном случае предполагается альтернатива использованию первичных невозобновляемых источников энергии (уголь нефть газ слюда сланцы и т.д.).
Использование вторичных источников энергии — является главным резервом сохранения энергии и главным образом это — применение энергосберегающих технологий основными из которых являются:
-совершенствование конструктивных решений систем вентиляции средств регулирования микроклимата эксплуатации теплового оборудования и т. д.;
-использование тепловых насосов;
-регенерация теплоты на животноводческих фермах;
-использование биогаза;
-использование естественного холода;
-использование отходов (солома стебли опилки ветки деревьев и т. д.) для целей отопления;
-использование вторичных энергоресурсов промышленных предприятий.
Конечно же все мероприятия по энергосбережению должны проводиться на различных уровнях их реализации. И первый уровень включает мероприятия которые зависят от работников хозяйств и выражается в поддержании технических параметров машин и оборудования в процессе эксплуатации на уровне их значений в соответствии с ГОСТами на их изготовление. Это например регулировка зазоров между клапанами и толкателями двигателя между контактами прерывателя-распределителя сцепления тормозов и т.д. своевременная замена неисправных деталей системы питания (форсунок свечей) устранение подтекания трубопроводов и др. Сюда также относятся и мероприятия по рациональному использованию и обслуживанию машин: повышение загрузки использования пробега квалификации а также обеспечение механизированной доставки хранения и заправки машин ТСМ. Развитие второго уровня зависит от работников управленческих структур и отраслей АПК научно-конструкторских организаций обслуживающих и снабженческих предприятий. К этому уровню относят в основном мероприятия научно-технического прогресса. Создание новой техники позволит снизить расход или уменьшить потери топлива и электроэнергии которые возникают из-за несовершенства имеющихся конструкций. Третий уровень зависит от политики государства проводимой в сфере энергосбережения.
ГЛАВА 2 ПРОИЗВОДСТВЕННАЯ ПРОГРАММА ЦЕХА.docx
1 Расчёт производственной программы цеха
Производственная программа определяет общий объём производства и является основой при проектировании. Она может быть точной приведённой или условной. Для серийного и мелкосерийного производства обычно оформляют приведённую производственную программу в которой сведения об отливках для изделий обеспеченных исходными данными распространяются на остальную часть программы.
Производственная программа проектируемого цеха рассчитывается по формуле:
гдеN — годовая программа выпуска отливок т;
A — заданная годовая программа выпуска изделий шт;
m — масса отливок на одно изделие кг;
n — количество конкретных видов изделий шт.
Расчётные данные сведены в таблицу 2.1.1.
Таблица 2.1.1 – Производственная программа
Наименование отливки
Годовой выпуск изделий шт
Продолжение таблицы 2.1.1
Итого по всей номенклатуре:
Таким образом производственная программа цеха предполагает выпуск отливок массой от 011 до 15 кг в количестве 1035010 штгод общей массой 2000050 тонн.
Для расчёта приведённой производственной программы необходимо рассчитать коэффициенты приведения. Коэффициент приведения определяется как отношение годовой программы цеха к программе отливки-представителя.
Коэффициенты приведения рассчитываем по группам. Для этого в каждой группе выбираем по две отливки-представителя (см. таблицу 2.1.1).
Коэффициенты приведения по группам:
Расчётные данные сведены в таблицу 2.1.2.
Таблица 2.1.2 – Приведённая производственная программа
Наимено-вание отливки
Коэф-фициент приведения
Приведён-ный годовой выпуск шт
2 Режимы работы и фонды времени
Среди режимов работы литейных цехов различают: параллельный ступенчатый и комбинированный. Цехи массового крупносерийного и частично серийного производства работают на параллельном режиме который предусматривает совмещение отдельных операций по времени и месту (отделению участку).
Для проектируемого цеха принимаем параллельный режим работы в две смены. Расчёт фондов времени производится исходя из 40-часовой рабочей недели. Продолжительность рабочей смены 8 часов. Количество праздничных дней в году — 8.
Режимы работы и фонды времени представлены в таблице 2.2.1.
Таблица 2.2.1 – Режим работы и фонды времени
Наименование цехов отделений участков групп и отдельных видов оборудования
Количество рабочих смен в сутки
Действительный годовой фонд времени
Литейное оборудование: цех серийного производства
Индукционные тигельные печи для алюминиевых сплавов
Автоматизированные абразивные линии для очистки литья
Металлорежущее и деревообрабатывающее оборудование
Годовой фонд времени рабочих мест (без оборудования) — 4140
Таблица 2.2.2 – Режим работы отделений и участков
Наименование отделений и участков
Режим работы шихтового и плавильного отделения сдвигается на 1–15 часа для организации плавки к началу первой смены
Плавильное отделение
Участок обрубки и очистки
Участок ремонта тех. оснастки
ЗАКЛЮЧЕНИЕ.docx
В технологической части проекта рассмотрена технология изготовления отливки-представителя «Диск верхний ХМ 09.22.300А».
В специальной части проекта было проведено моделирование базовой литейной технологии изготовления отливки-представителя с целью выявления и устранения дефектов путём изменения литниково-питающей системы.
В экономической части были получены экономические показатели подтверждающие целесообразность внедрения вышеупомянутых технологических процессов. Рассчитав полную себестоимость единицы продукции в проектном варианте (398821 руб.) было выяснено что она меньше на 5979 руб. чем в аналогичном технологическом варианте (404800 руб.). Это связано с изменением затрат на основные материалы а также уменьшением трудо- и энергозатрат.
ГЛАВА 3 РАСЧЁТ ЦЕХА.docx
1.1 Структурный баланс металла
Баланс жидкого металла составлен на основании заданной программы.
При составлении баланса жидкого металла была учтена не только номенклатура изделий вид и марки сплава но и тип плавильного агрегата и главное принятая технология. С учётом этих особенностей были назначены нормы брака безвозвратных потерь и выхода годного.
Расчёт баланса жидкого металла для сплава алюминия АК9 ГОСТ 1585-93 для данного цеха сводим в таблицу 3.1.1.
Таблица 3.1.1 – Структурный баланс жидкого металла
Статья баланса металла
Металл литниковых систем
Технологически неизбежный отход + брак
Стружка АЛ (возврат собств. про-ва)
Угар (в т.ч. угар стружки)
Безвозвратные потери
Итого металлозавалки:
Таким образом для обеспечения годовой производственной программы (2 тыс. тонн годного литья) плавильное отделение цеха должно быть обеспечено 2980075 тоннами металлозавалки.
1.2 Технологический процесс плавки алюминиевых сплавов
Основным плавильным агрегатом для плавки алюминиевых сплавов является индукционная тигельная печь.
Приготовление алюминия (АК9) ведётся в индукционной печи футерованной кварцем. Силумины характеризуются хорошими литейными свойствами и герметичностью средней прочностью и достаточной коррозионной стойкостью. Они применяются для изготовления сложных отливок.
В качестве шихтовых материалов используются силумин в чушках марки СИЛ-1 алюминий первичный (А5) алюминий вторичный (АК9) кремний технический (КР00 КР0) возврат собственного производства стружка АЛ (возврат с производства) магний чушковый (МГ90) марганец (Мн965). Шихтовые материалы загружаются в таком порядке: алюминий чушковый возврат собственного производства лигатуры.
Печь нагревается до температуры 600–700°C после чего в неё загружают чушки силумина и очищенный возврат. В период расплавления металла температура ванны поддерживается в пределах 680–700°C. Затем сплав перегревают до температуры 720–730°C рафинируют его хлористым цинком (01% от массы шихты) и производят модифицирование. Модификатор в виде смеси фтористых и хлористых солей калия наносят на очищенную поверхность сплава и выдерживают его в течение 12–14 мин так как процесс плавки алюминиевых сплавов представляет ряд трудностей вследствие их сильного окисления и насыщения газами при нагревании свыше 700°С.
Для измельчения зерна и следовательно улучшения механических свойств силумины модифицируют натрием в количестве 005–008% от массы сплава.
Модификатор вводят в расплав в виде смеси галоидных солей натрия и калия. В силумины вводят также модифицирующие добавки иттрия стронция циркония бора титана и др.
1.3 Расчёт шихтовых материалов
Расчёт шихты производится с целью подбора шихтовых материалов обеспечивающих в процессе плавки в печи заданный химический состав металла.
Данными для расчёта шихты являются: химический состав шихтовых материалов химический состав металла угар и пригар элементов в процессе плавки.
Расчёт шихты производим методом подбора при этом массовые доли компонентов выражаются в процентах. Метод основан на определении среднего химического состава сплава с учётом влияния на химический состав процесса плавки.
Требуемый средний химический состав сплава АК9 приведён в таблице 3.1.2.
Таблица 3.1.2 – Химический состав сплава АК9 ГОСТ 1583-93
Легирующие элементы %
Химический состав чушкового силумина и первичного алюминия представлены в таблицах 3.1.3 и 3.1.4.
Таблица 3.1.3 – Химический состав чушкового силумина
Содержание элементов %
Таблица 3.1.4 – Химический состав первичного алюминия
Ведомость расхода шихтовых материалов представлена в таблице 3.1.5.
Результат расчёта шихтовых материалов сводим в таблицу 3.1.6. Примесями содержащимися в исходном материале и готовом сплаве при расчёте пренебрегаем.
Таблица 3.1.5 – Ведомость расхода шихтовых материалов
Наименование марка шихтового материала
Норма расхода на годовую программу
Шихтовые материалы для марки сплава АК9
Алюминий первичный А5
Алюминий вторичный АК9
Кремний технический КР00 КР0
Магний чушковый первичный МГ90
Лом АЛ кл. А гр. I IV сорт I
Флюсы и модификаторы
ТУ ВУ 400069905039-2010
Флюс покровно-рафинирующий
ТУ РБ 100.196035.005-2000
Таблетки дегазирующие
ТУ РБ 14744129004-98
Таблица 3.1.6 – Расчёт шихтовых материалов
Магний чушковый МГ90
1.4 Расчёт складов шихтовых материалов
Одним из основных условий надёжности работы плавильных агрегатов обеспечения ими заданной производительности и высокого качества выплавляемого сплава является своевременная и бесперебойная загрузка печей точно дозированной шихтой. Индукционные печи загружают дозами равными или несколько меньшими массы жидкого сплава единовременно выдаваемого из тигля.
Технологический процесс набора дозирования и загрузки шихты в плавильную печь можно разбить на следующие операции: набор всех металлических и неметаллических компонентов шихты в весовую тележку с помощью пластинчатого дозатора; взвешивание компонентов; перемещение взвешенной дозы шихты в вибролоток; загрузка в печь.
В проектируемом цехе принят следующий способ хранения материалов:
-металлическая шихта — площадка суточные бункера;
-флюсы и модификаторы — цеховые кладовые.
Расчёт складов шихтовых материалов приведён в таблице 3.1.7.
Окончательные размеры складов шихтовых материалов принимаем исходя из планировки и рациональных соображений.
Таблица 3.1.7 – Расчёт складов шихтовых материалов
Годовая потребность т
Количество материала на складе т
Криолит марка КА ТУ ВУ 400069905039-2010
Итого общая площадь хранения шихты:
1.5 Расчёт потребного количества плавильных агрегатов
Расчёт одновременно работающих плавильных агрегатов ведём в соответствии с рассчитанными ранее потребностями в металлозавалке [табл. 3.1.1]:
Исходя из применения системы сдвоенных печей с одним источником питания и перераспределением мощности принимаем число плавильных агрегатов равное 2.
В этом случае ориентировочная расчётная производительность печей должна составлять:
где — потребление сплава цехом тгод;
— коэффициент неравномерности потребления металла;
[1 с. 28] принимаем
— действительный годовой фонд времени печи часгод;
— расчётное число одновременно работающих печей.
По расчётной производительности из стандартного ряда выбрана индукционная тигельная печь типа ИАТ-104М3.
Принимаем производительность печи равной 067 тчас.
Количество печей определено по формуле:
где — потребление сплава цехом или участком;
— коэффициент неравномерности потребления металлом;
— действительный фонд времени работы печи;
— часовая производительность печи тчас.
Принимаем 2 печных индукционных установки ИАТ-104М3. Технические характеристики печи представлены в таблице 3.1.8.
Определим коэффициент загрузки плавильного оборудования:
где — принятое количество оборудования.
Коэффициент загрузки соответствует рекомендуемым нормам.
Таблица 3.1.8 – Технические характеристики индукционной тигельной печи ИАТ-104М3
Наименование параметра
Мощность установленная кВт
Мощность потребляемая кВт
Ёмкость номинальная т
Число фаз питающей сети
Номинальное напряжение В:
Температура перегрева металла °С
Производительность по расплавлению и перегреву тч
Удельный расход электроэнергии на расплавление и перегрев кВт чт
Продолжение таблицы 3.1.8.
Масса металлоконструкций электропечи т
Масса электропечи (комплекса) т
Расход охлаждающей воды м3ч
1.6 Принцип действия и конструкция плавильных агрегатов
Электропечь работает по принципу трансформатора у которого первичной обмоткой является водоохлаждаемая катушка-индуктор вторичной обмоткой и одновременно нагрузкой – находящийся в тигле металл. Нагрев и расплав металла происходит за счёт протекающих в нем токов которые возникают под действием электромагнитного поля создаваемого индуктором. При этом возникают также электродинамические силы которые создают интенсивное перемещение металла обеспечивающее равномерность температуры и однородность расплавленного металла.
Электропечь индукционная тигельная ИАТ-104 М3 состоит из собственно индукционной электропечи и комплекта оборудования необходимого для ее работы. Индукционная электропечь конструктивно выполнена в виде опорной рамы внутри которой размещается быстросъёмный плавильный узел состоящей из индуктора магнитопроводов сварного корпуса футеровки подины набивного тигля и верхнего футерованного пояса-воротника. Плавильный узел извлекается краном за специальные проушины.
Рама состоит из двух частей: верхней поворачивающейся с помощью двух плунжеров и нижней неподвижной. В верхней части рамы закрепляется узел плавки. Индуктор представляет собой многовитковую водоохлаждаемую катушку выполненную из трубки специального профиля и состоящую из двух секций — холостой и рабочей. Холостая секция катушки используется для охлаждения стенки тигля.
Для защиты металлоконструкций печи от полей рассеяния индуктор окружён снаружи магнитопроводами набранными из стали. Тигель печи закрывается бетонированной крышкой открывающейся листов трансформаторной гидроцилиндром. Электроэнергия подаётся гибкими водоохлаждаемыми кабелями подвод охлаждающей воды — резинотканевыми рукавами с быстроразъёмными соединениями. Тигли печей для плавки алюминия изготавливаются из жаростойкого бетона способом набивки. Средняя стойкость футеровки тигля достигает 12 и более месяцев зависит от режима работы печи (наплавка ведётся с полным сливом металла при этом тигель испытывает частые теплосмены или с остаточной ёмкостью) и от культуры обслуживания — способа загрузки периодической чистки мелкого ремонта и качества изготовления тигля а также от соблюдения технологического режима обжиговой плавки. Печь питается от сети ВН через специальный печной трансформатор. Мощность электропечи регулируется переключением ступеней напряжения трансформатора вручную со щита управления.
Для компенсации естественного низкого коэффициента мощности (cos) электропечь снабжается батареей конденсаторов. Батарея состоит из двух групп: одна подключена постоянно вторая — по ходу плавки в зависимости от необходимости в компенсации реактивной мощности индуктора. Переключение этой группы производится вручную и регулятором БУМС который автоматически поддерживает заданное значение cos на протяжении всего периода плавки. Наклон печи для слива металла управляется со специального пульта. Установка электропечи и комплектующего оборудования (рис. 3.1.1) выполняется по проекту разрабатываемому для конкретных условий цеха. При изменении планировки размещения установки электропечи конденсаторную батарею следует размещать как можно ближе к электропечи с целью уменьшения потерь в короткой сети. Размещение остального оборудования выполняется с соблюдением нормированных требований и исходя из удобства управления печью и её эксплуатации. Электропечь устанавливается на специальный фундамент. Уровни опорных площадок могут быть изменены в зависимости от условий разливки металла.
Рисунок 3.1.1 – Габаритные установочные размеры и рекомендуемое размещение комплектующего оборудования электропечи.
– электропечь индукционная ИАТ-104МЗ; 2 3 – панели управления; 4 – щит управления;
– трансформатор ЭОМП-100010-72 УЗ; 6 – пульт управления; 7 – установка маслонапорная;
– панель гидравлическая; 9 – блок конденсаторов.
2 Заливочное отделение
Вид оборудования и его количество в цехе литья цветных металлов в первую очередь зависят от способа изготовления отливок. В нашем случае отливки изготовляются литьём в кокиль что и определяет перечень выбранного оборудования.
2.1 Выбор оборудования для изготовления отливок
В гамму входит четыре типа машин:
-с одной подвижной плитой;
-с двумя подвижными плитами и поддоном с нижним стержнем;
-с двумя подвижными плитами поддоном с нижним стержнем и плитой верхнего стержня;
-с двумя подвижными плитами поддоном с нижним стержнем плитой верхнего стержня и плитой торцевого стержня.
В конструкции машин предусмотрено:
-выталкивание отливки из основных плит;
-выталкивание отливки из поддона;
-подрыв стержней с увеличенным усилием;
-поворот верхнего стержня для удобства съёма;
-съем отливки манипулятором.
В цеху предполагается использовать кокильные машины модели 82А303 82А405 82А505.
Технические характеристики кокильных машин представлены в таблице 3.2.1.
Таблица 3.2.1 – Технические характеристики кокильных машин
Размеры рабочего места на основных плитах для крепления частей кокиля мм
Наименьшее расстояние между основными плитами мм
Продолжение таблицы 3.2.1
- выталкивание поддона
Усилие раскрытия кокиля кН
Усилие извлечения стержня кН
Машинное время цикла с
Габариты (без электрошкафа и гидроагрегата) мм
Максимальная производительность отлчас
2.2 Расчёт потребного количества оборудования
Требуемое количество машин литья в кокиль рассчитывается исходя из производственной программы и производительности машины.
Количество машин для литья в кокиль определяем по формуле:
где — годовой выпуск изделий шт;
— коэффициент неравномерности работы оборудования;
[1 с. 28] принимаем ;
— действительный годовой фонд работы кокильной машины часгод;
— производительность кокильной машины залч.
Результат расчёта числа кокильных машин приведён в таблице 3.2.2.
Таблица 3.2.2 – Расчёт числа кокильных машин
Производительность отлчас
3 Обрубочно-зачистной участок
Расчёт обрубочно-зачистного оборудования выполняется исходя из производительности оборудования и производственной программы.
Рассчитываем необходимое количество обрубных прессов по формуле:
где — количество заготовок требующих обработку тонн;
— действительный годовой фонд работы оборудования час;
— производительность оборудования тоннчас.
Принимаем количество прессов мод. П 16А – 6 шт.
При этом коэффициент загрузки равен:
Таблица 3.3.1 – Техническая характеристика обрубного пресса мод. П 16А
Наибольший ход подвижной плиты мм
Расстояние между колоннами мм
Габаритные размеры (длинаширинавысота) мм
Мощность двигателя кВт
После обрубки литников отливки поступают на участок обрезки на котором происходит удаление прибылей.
Рассчитываем необходимое количество ленточнопильных станков по формуле:
Принимаем количество ленточнопильных станков Stalex BS-5030 – 3 шт.
Технические характеристики оборудования приведены в таблице 3.3.2.
Таблица 3.3.2 – Техническая характеристика ленточнопильного станка Stalex BS-5030
Максимальное сечение круглого профиля при 90° мм
Максимальное сечение прямоугольного профиля при 90° мм
Мощность гидравлической станции кВт
Мощность системы СОЖ кВт
Скорость резания ммин
Рабочая высота стола мм
Объём гидравлического бака л
Габариты станка (ДхШхВ) мм
После обрезки прибылей отливки транспортируются на участок шлифования на котором происходит дальнейшая обработка.
Рассчитываем необходимое количество шлифовальных машин по формуле:
Принимаем количество обдирочно-шлифовальных станков мод. ВШ-041 – 4 шт.
Технические характеристики станка приведены в таблице 3.3.3.
Таблица 3.3.3 – Техническая характеристика обдирочно-шлифовального станка мод. ВШ-041
Параметры шлифовального круга
(D наружн. d посадочн. B) мм
Частота вращения шпинделя обмин
Расстояние между кругами мм
Мощность привода главного движения кВт
Высота оси шпинделя шлиф. кругов от пола мм
Диаметр выходного патрубка мм
Напряжение питания В
Габаритные размеры (LBH) мм
4 Участок термической обработки
В проектируемом цехе необходимо предусмотреть участок термической обработки отливок из алюминия. В зависимости от применяемых сплавов и их назначения применяют различные виды термической обработки.
Для термической обработки отливок из алюминиевых сплавов применяют воздушно-циркуляционные агрегаты ПАП. Нагрев осуществляется за счёт механической энергии вентилятора создающего поток воздуха движущегося с большой скоростью в замкнутом объёме печи. Передача тепла отливки осуществляется конвекцией что обеспечивает быстрый и равномерный нагрев.
В проектируемом цехе используется воздушно-циркуляционный агрегат модели ПАП-3М который полностью механизирован. Технические характеристики агрегата приведены в таблице 3.4.1.
Таблица 3.4.1 – Технические характеристики агрегата мод. ПАП-3М
Установленная мощность кВА
Номинальная температура °С
Частота вращения роторного нагревателя обс
Время разогрева рабочего пространства до номинальной температуры ч не более
Размеры рабочего пространства камеры мм
Габаритные размеры агрегата мм
Количество агрегатов рассчитывают из объёма производственной программы и производительности оборудования:
Принимаем количество воздушно-циркуляционных агрегатов модели ПАП-3М – 2 шт.
5 Вспомогательные отделения
Вспомогательные службы литейного цеха включают следующие подразделения: участок подготовки шихтовых материалов; ковшевой участок; ремонтную службу цеха с участком ремонта футеровки ковшей тиглей и печей; участок ремонта и хранения оснастки; экспресс-лаборатории для оперативного контроля материалов; цеховые кладовые.
5.1 Участок подготовки шихтовых материалов
В шихтовом отделении есть участок подготовки шихтовых материалов который предназначен для сортировки и очистки поверхности от ненужных примесей.
5.2 Ковшевой участок
Ковшовое отделение предназначено для капитального ремонта и футеровки ковшей а также для сушки ковшей после ремонта. Сушка осуществляется на стендах.
Для проведения ремонтных работ на участке имеется следующее оборудование:
-стенд для ремонта и сушки;
-сварочное оборудование.
Ковшовое отделение располагается рядом с плавильным площадь его определяется планировкой.
5.3 Ремонтная служба цеха
Ремонтная служба цеха выполняет только межремонтное обслуживание цеха. Все другие виды ремонта выполняются централизовано ремонтными службами завода.
В действующей системе планово-предупредительного ремонта учитываемой при проектировании литейных цехов предусмотрено централизованное выполнение службами завода малого среднего и капитального ремонта механического и электротехнического оборудования а также ремонта инструмента и оснастки.
Цеховая служба текущего ремонта оборудования должна иметь разветвлённую систему контроля его работы и вызова дежурных слесарей и электриков.
5.4 Участки ремонта и хранения оснастки
Отделения ремонта и хранения оснастки располагаются вблизи с ремонтными мастерскими цеха. На участках устанавливаются металлообрабатывающие станки (токарный сверлильный фрезерный); сварочное и другое оборудование. Площади ремонтных служб принимают 28–34 м3 на 1000 тонн отливок.
5.5 Экспресс-лаборатория
Экспресс-лаборатория предназначенные для оперативного контроля качества металла и располагаются вблизи плавильного отделения. Общая площадь лабораторий определяется планировкой.
5.6 Цеховые кладовые
Цеховые кладовые размещаются на площадях основных отделений в местах доступных для посещений но непригодных для производственных отделений.
Площади кладовых зависят от принятого технологического процесса объёма производственной программы. Ориентировочно принимают площади кладовых 13–17 м3 на 1000 тонн отливок.
01. ТИТУЛЬНИК.docx
Учреждение образования
«Гомельский государственный технический университет имени П.О. Сухого»
Кафедра «Металлургия и технологии обработки материалов»
ПОЯСНИТЕЛЬНАЯ ЗАПИСКА
к дипломному проекту
По экономической части
Руководитель проекта
Дипломный проект допущен к защите
Государственной Экзаменационной Комиссией
пояснительная записка
04. ВВЕДЕНИЕ.docx
Выжить и развиваться в конкурентной борьбе литейное производство сможет лишь в том случае если оно будет постоянно заботиться о повышении производительности труда снижении трудозатрат и доли ручного труда на всех переделах литейного производства. При этом оно должно стремиться к повышению качества отливок (их геометрической точности снижению шероховатости поверхности и припусков на механическую обработку улучшению качества выплавляемых сплавов и повышению их служебных характеристик) снижению металлоёмкости заготовки за счёт получения тонкостенных отливок и улучшения их товарного вида и др.
Все эти задачи нельзя решить сохраняя неизменным технический уровень литейного производства и не занимаясь реконструкцией техническим перевооружением а также проектированием и строительством новых цехов на базе совершенных и прогрессивных технологических процессов [6 с. 2].
В производстве литых заготовок для деталей машин и приборов значительное место занимают так называемые специальные-способы литья: например литьё в металлические формы (кокиль) позволяющее получить отливки повышенной точности с чистой поверхностью минимальными припусками на обработку (а иногда и полностью исключающие её) и высокими служебными свойствами.
Технологические процессы получения отливок этим способом в сравнении с литьём в песчаные формы отличается меньшей материало- и энергоёмкостью меньшими трудозатратами что позволяет существенно улучшить условия труда и уменьшить вредное воздействие на окружающую среду [7 с. 3].
Металлические формы являются многократно используемыми что значительно облегчает упрощает и ускоряет процесс получения отливок с хорошей поверхностью. Однако процесс изготовления металлического кокиля довольно трудоёмок и длителен и поэтому такой способ литья применяют только в крупносерийном и массовом производстве когда себестоимость кокиля распределяется на тысячи и десятки тысяч отливок.
ЛИТЕРАТУРА.docx
Основы проектирование литейных цехов и заводов: Л.И. Фанталов Б.В. Кнорре С.И. Четвертухин [и др.]; под общ. ред. Б.В. Кнорре. – Москва: Машиностроение 1979. – 376 с.
Цветное литьё: Справочник Н.М. Галдин [и др.]; под общ.ред. Н.М. Галдина – Москва: Машиностроение. 1989. – 528 с.
Межгосударственный стандарт. Сплавы алюминиевые литейные. Технические условия: ГОСТ 1583-93 – Введ. 01.01.97. – Минск: ИПК Изд-во стандартов 2003. – 28 с.
Литьё в кокиль С.Л. Бурлаков [и др.]; под общ.ред. А.И. Вейника – Москва: Машиностроение. 1980. – 415 с.
Технология литейного производства: Специальные виды литья Ю.А. Степанов [и др.]; под общ. ред. Ю.А. Степанова. – Москва: Машиностроение 1983. – 287 с.
Проектирование новых и реконструкция действующих литейных цехов: Учебное пособие А.Ф. Миляев. – Магнитогорск: МГТУ им. Г.И. Носова 1999. – 410 с.
Проектирование и реконструкция литейных цехов: учебное пособие к выполнению дипломного проекта Б.А. Кулаков Л.Г. Знаменский О.В. Ивочкина [и др.]. – Челябинск: Изд. ЮУрГУ 2001. – 144 с.
Лазаренков А.М. Охрана труда: Учебник А.М. Лазаренков. – Минск: БНТУ 2004. – 497 с.
Астраханцев С.Е. Организация и планирование производства. Управление предприятием С.Е. Астраханцев. – Гомель: ГГТУ им. П.О. Сухого 2006. – 37 с.
ГЛАВА 4 ТЕХНОЛОГИЧЕСКАЯ ЧАСТЬ.docx
1 Технологический процесс изготовления отливки «Диск верхний ХМ 09.22.300А»
Разработка технологии изготовления отливки «Диск верхний ХМ 09.22.300А» состоит из выбора и обоснования материала отливки способа литья а также разработки последовательностей технологических операций.
Точность размеров отливок зависит не только от технологии производства но и от наибольшего габаритного размера отливки и её сложности.
Начальными данными для определения техпроцесса изготовления отливки являются требования к отливке и точность размеров по ГОСТ 26645-85.
2 Назначение и характеристика отливки
В качестве отливки-представителя выбран «Диск верхний ХМ 09.22.300А» (рисунок 4.2.1).
Рисунок 4.2.1 – Эскиз детали «Диск верхний ХМ 09.22.300А»
По сплаву отливка «Диск верхний ХМ 09.22.300А» относится к отливкам из цветных металлов она изготавливается из алюминиевого литейного сплава марки АК9 ГОСТ 1585-93.
Литейные алюминиевые сплавы имеют ряд особенностей: повышенную жидкотекучесть обеспечивающую получение тонкостенных и сложных по конфигурации отливок; сравнительно невысокую линейную усадку; пониженную склонность к образованию горячих трещин; механическую прочность удовлетворительную свариваемость и обрабатываемость резанием. Кроме того алюминиевые сплавы обладают высокой склонностью к окислению насыщению водородом что приводит к таким видам брака отливок как газовая пористость шлаковые включения и оксидные включения. Основными недостатками являются сравнительно сложная технология литья пониженная жаропрочность повышенная газовая пористость
Наибольшее распространение в промышленности имеют сплавы Аl–Si Аl–Si–Mg (АЛ2 АЛ4 АЛ4-1 АЛ9 АЛ9-1 АЛ34 АК9 АК7) которые отличаются хорошими технологическими свойствами определяемыми видом диаграмм состояния. Литейные свойства обеспечиваются наличием в сплавах большого количества двойной эвтектики α+Si (40—75 %) каркасно-матричного типа основой которой является α-твёрдый раствор что обусловливает высокую жидкотекучесть сплавов а также низкую литейную усадку и пониженную склонность к образованию горячих трещин [2 с. 178].
Таблица 4.2.1 – Химический состав алюминиевого сплава АК9 [3 табл. 1 с. 4]
Основных компонентов примесей не более
Сумма учитываемых примесей
Алюминий-кремний-магний
Таблица 4.2.2 – Механические свойства алюминиевого сплава АК9 [2 табл. 9 с. 175]
Временное сопротивление в МПа
Относительное удлинение %
Твёрдость по Бринеллю HB
Сплав АК9 применяется для:
-изготовления чушек и отливок различными способами литья (в песчаные формы по выплавляемым моделям в кокиль литьём под давлением);
-изготовления фасонных отливок деталей горно-металлургического оборудования;
-отливок деталей металлургического оборудования (крупных и средних сложных по конфигурации деталей картеров и блоков двигателей работающих при температуре не выше 200°С [2 с. 178].
3 Оценка технологичности конструкции детали
Масса детали составляет 65 кг что относится к 1-й группе по массе (до 8 кг). Деталь соответствует 2-й группе сложности т.к. деталь имеет форму тела вращения а также имеет цилиндрические отверстия.
К полученному изделию предъявляются следующие требования:
Точность отливки 9–0–0–9 ГОСТ 26645–85.
Отливка является 9-го класса размерной точности; к степени коробления и к степени точности поверхностей требований не предъявляется; степень точности массы отливки соответствует 9-му классу.
Отливка имеет шероховатость получаемую литьём Ra=25.
На 12-ти отверстиях допускаются несквозные раковины наибольшей глубиной до 5 мм с расстоянием между ними 20 мм минимум.
Допускается исправление дефектов отливок любым способом обеспечивающим прочность и герметичность детали и не ухудшающим её товарный вид.
Геометрически отливка представляет собой тело вращения с незначительно выступающими цилиндрами сверху и снизу. Имеет четыре ребра жёсткости тепловые узлы расположенные у краёв диска. Деталь имеет 12 отверстий 35 мм а также одно центральное отверстие 29 мм с углублением под шпонку; два технологических окна в теле диска на расстоянии 124 мм друг от друга и шириной по 65 мм. Габаритные размеры детали 333х67 мм.
Деталь является ответственной тонкостенной и применяется в машиностроении.
Изучив приведённые выше факты можно сделать вывод что деталь «Диск верхний ХМ 09.22.300А» является технологичной для получения её литьём.
4 Обоснование выбора положения отливки в форме и плоскости разъёма
Плоскость разъёма выбираем сложную т.к. отливка симметричная и имеет в себе поднутрения. Отсутствие плоского разъёма избавляет от необходимости изготовления отъёмных частей которые непосредственно усложнят сборку кокиля. Части которые выполняют функцию болвана изготавливаются в поддоне а литниковая система с прибылями располагается в половинках кокиля. Тип кокиля — створчатый. Все вышеперечисленные факты необходимы для возможности автоматизации процесса и исключения ручного труда.
В отливке «Диск верхний ХМ 09.22.300А» механически будут обрабатываться практически все поверхности на фланце до Ra=16 при помощи токарного резца. Припуски на механическую обработку назначаем по ГОСТ 26645-85 для класса точности размеров — 9 и общего допуска — 9 (значения указаны в тех. требованиях на чертеже детали).
Отверстия в отливке полностью заливаем в связи с тем что их достаточно много располагается на фланцевой поверхности что сделает невозможным извлечение отливки из-за того что её может заклинить в форме кокиля после кристаллизации металла. Поэтому все 28 отверстий изготавливаются при помощи сверления с чистотой поверхности Ra=63.
Центральное отверстие в отливке будет изготавливаться с помощью металлического стержня что позволит избежать использование стержневой смеси улучшить качество внутренней поверхности отливки а также облегчить процесс автоматизации и механизации. Материал стержня — Сталь У8А ГОСТ 1345-90.
Технологические окна будут выполняться с помощью верхнего и нижнего стержней. Материал стержней — Сталь 40Х ГОСТ 4543-71.
В связи с особыми свойствами алюминиевых сплавов (повышенная усадка возможность окисления при заливке склонность к образованию плен газовой пористости и др.) возникает необходимость устройства особых литниково-питающих систем и наличие прибылей. С целью более плавного поступления металла и очистки его от плен и шлака будем использовать литниково-питающую систему зигзагообразного типа в виде «гусиной шейки».
Прибыли необходимы для компенсации усадки алюминевого сплава.
Для наилучшего питания и качественной проливки стенок отливки подвод металла к полости формы будет осуществляться через щелевой вертикальный питатель неодинакового сечения по высоте [4 с. 277–278].
Эскиз детали «Диск верхний ХМ 09.22.300А» с нанесённой технологией представлен на рисунке 4.4.1.
Рисунок 4.4.1 – Эскиз детали «Диск верхний ХМ 09.22.300А» с нанесённой технологией
5 Обоснование способа изготовления отливки
Проанализировав требования предъявляемые к отливке учитывая её массу серийность выпуска и сплав из которого она изготавливается наиболее целесообразно будет использовать способ литья в кокиль.
Сущность процесса литья в кокиль заключается в изготовлении отливок из жидкого расплава свободной заливкой его в многократно используемые металлические формы — кокили обеспечивающие высокую скорость затвердевания жидкого расплава и позволяющие получать в одной форме от нескольких десятков до нескольких тысяч отливок.
Преимуществами литья в металлические формы являются:
-многократное использование формы;
-повышение точности размеров отливок уменьшение шероховатости их поверхности что позволяет снизить припуск на механическую обработку в 2–3 раза а иногда и полностью устранить её. Это увеличивает выход годного до 75–90%;
-повышение плотности отливки улучшение её структуры на 15–30% возрастают механические свойства;
-сокращение а во многих случаях полное исключение расхода формовочных и стержневых смесей;
-исключение трудоёмких операций формовки сборки и выбивки форм. Это создает условия для полной механизации и автоматизации технологического процесса роста производительности труда;
-увеличение съёма с 1 м2 производственной площади и снижение себестоимости отливок [5 с. 123].
Недостатками данного метода являются:
-высокая стоимость металлической формы сложность и длительность ее изготовления;
-ограниченная стойкость измеряемая числом годных отливок которое можно получить в данной форме до её выхода из строя;
-плохая заполняемость форм при изготовлении тонкостенных (25–3 мм) протяжённых отливок вследствие высокой теплопроводности формы;
-трудность получения отливок с поднутрениями для выполнения которых необходимо применять стержни и вставки;
-неподатливая металлическая форма вызывает появление в отливках внутренних напряжений коробление а иногда и трещины [5 с. 124].
Общие характерные дефекты отливок при литье в кокиль следующие:
-недоливы и неслитины возникающие при низкой температуре расплава и кокиля перед заливкой или малой скорости заливки большой газотворности краски и плохой вентиляции кокиля;
-шлаковые включения из-за недостаточного рафинирования сплава;
-трещины возникающие из-за высокой температуры заливки длительного охлаждения металла в кокиле;
-усадочные дефекты (раковины утяжины пористость) из-за нарушения направленного затвердевания и недостаточного питания массивных частей отливки из-за перегрева кокиля.
Высокая прочность материала металлической формы позволяет выполнять рабочие полости формы с более точными стабильными размерами и соответственно получать отливки с размерами до 5-го класса точности. Минимальное физико-химическое взаимодействие металла отливки и формы способствует повышению качества поверхности отливки и полностью устраняет пригар; шероховатость поверхности отливки может достигать 3–5-го классов чистоты по ГОСТ 2789–73. Благодаря высокой теплопроводности материала формы тепло быстро отводится от отливки что повышает скорость ее затвердевания и положительно сказывается на её механических свойствах [5 с. 97].
Литьё в кокиль относится к трудо- и материалосберегающим малооперационным и малоотходным технологическим процессам. Оно улучшает условия труда в литейном производстве и уменьшает воздействие на окружающую среду.
Отливка «Диск верхний ХМ 09.22.300А» может быть выполнена литьём в кокиль так как этим способом получается необходимая точность размеров и низкая шероховатость поверхности.
6 Разработка конструкции литейной оснастки
Основные узлы детали и механизмы кокиля в зависимости от назначения подразделяются на:
Формообразующие элементы;
Конструктивные элементы;
Самую большую роль в получении качественной отливки играют формообразующие элементы так как они непосредственно контактируют с расплавом. Для получения максимального качества формообразующих элементов к ним предъявляются следующие требования:
-шероховатость поверхности должна быть минимальной чтобы обеспечить максимальное качество поверхности отливки;
-износостойкость должна быть максимальной чтобы обеспечить максимальный срок службы элементов;
-должны обладать химической инертностью чтобы не взаимодействовать с расплавленным металлом;
-должны быть жаростойкими чтобы не терять своих свойств при контакте с жидким металлом;
-не должны изменять своих габаритных размеров чтобы обеспечивать заданную точность размеров.
К формообразующим элементам относятся:
-Левая и правая матрицы: будут выполнены литьём из СЧ20 ГОСТ 1412-85. Так как температурный режим кокиля будет регулироваться то данный серый чугун обеспечит нам достаточную жаростойкость. Толщина стенки матриц равна 40 мм. Данная толщина стенки обеспечивает конструктивную жёсткость и прочность формы. Также при такой толщине стенки выполняются необходимые условия затвердевания отливки (толщина стенки меньше глубины проникновения тепла значит внешняя поверхность стенки будет охлаждаться).
-Нижний и верхний стержни будут выполнены точением из стали 40Х ГОСТ 4543–71. Центральный стержень изготавливается точением из стали У8А ГОСТ 1345-90. Стержни работают в тяжёлых условиях (большая часть их поверхности омывается жидким металлом) поэтому они должны быть стойкими к влиянию высоких температур. Данные марки стали обеспечат достаточную жаростойкость. Также на стержнях предусмотрен уклон 2° для их лёгкого извлечения.
-Выталкиватели будут выполняться точением из стали 40Х ГОСТ 4543–71. Они необходимы для извлечения отливки из матриц. Выталкиватели будут подвергнуты термообработке (закалка с последующим низким отпуском) до твёрдости 49 53 HRC. Данная сталь совместно с термообработкой дадут нам необходимую износостойкость.
-Поддон кокиля будет выполнен литьём из СЧ20 ГОСТ 1412-85. В нём будут выполнены окна для его облегчения. Поддон будет установлен на основание машины для литья в кокиль и будет служить опорой под матрицы. Вставка в поддоне будет выполняться литьём из легированной стали 35Л ГОСТ 977–75. В данном случае вставка поддона выполняет формообразующую роль так как она непосредственно контактирует с жидким металлом в связи с этим и была выбрана данная сталь которая обеспечит нам достаточные механические свойства.
К конструктивным элементам не предъявляется таких высоких требований как к формообразующим так как они не контактируют с жидким металлом. К конструктивным элементам относится плита толкателей. Она будет выполнена механической обработкой из стали 45 ГОСТ 1050–88. Конструкция плиты будет иметь прямоугольную форму с отверстиями для установки выталкивателей и крепления к подвижным плитам машины. Так как в некоторых случаях отливку может заклинить в форме нагрузка на плиту будет достаточно высокой и выбранная сталь обеспечит достаточную прочность плиты.
7 Разработка технологических этапов производства отливки
Процесс получения отливки состоит из следующих этапов:
Плавка шихты производится при температуре 700±20°С в индукционной тигельной печи типа ИАТ-104М3. Такая температура обеспечивает перегрев расплава достаточный для того чтобы переместить его к месту заливки в раздаточном ковше. Техническая характеристика печи ИАТ-104М3 представлена в таблице 3.1.8.
Подготовка кокиля начинается с нанесения на него краски с целью повышения его стойкости. Краски предупреждают привар металла отливок к кокилю снижают теплопроводность кокиля повышают его стойкость. Краску наносят на горячий кокиль с помощью пульверизатора. Составы красок для цветных сплавов приведены в таблице 4.7.1.
Таблица 4.7.1 – Состав красок для кокиля
Литье из алюминиевых сплавов
Для покрытия поверхности литниковых каналов
Далее кокиль нагревают до температуры 370±30°С. Такая температура выбрана из интервала для тонкостенных отливок из алюминиевых сплавов. Нагрев кокиля полный будет применяться газовая горелка.
Кокиль устанавливается на однопозиционной кокильной машине мод. 82А405. Данная машина выбрана в связи с тем что она подходит по металлоёмкости и развесу отливки-представителя. Техническая характеристика кокильной машины мод. 82А405 представлена в таблице 3.2.1.
-ввод нижнего стержня;
-ввод бокового стержня;
-заливка кристаллизация;
-подрыв нижнего и бокового стержней;
-выталкивание отливки.
Особенность конструкции данной машины в том что у неё две боковые плиты и поддон подвижны что позволит установить нам необходимые стержни.
Расплав после плавки заливают из печи в ковш с поворотным устройством и электропогрузчиком доставляют к магнитодинамическому насосу. Из ковша расплав заливается в тигель магнитодинамического насоса где температура расплава поддерживается индукционным способом нагрева.
Заливка осуществляется при помощи магнитодинамического насоса МДН-6А-025. В магнитодинамическом насосе сочетается электромагнитный принцип подачи металла с индукционным способом нагрева. Установка МДН предназначена для механизации и автоматизации заливки алюминиевых и цинковых сплавов в кокильные машины.
При заливке отливка в форме будет располагаться горизонтально т.к. это обеспечит лучший вывод газов из формы и более плавное её заполнение и как следствие меньшую вероятность получения газовых дефектов.
После заливки отливка выдерживается в кокиле до полной кристаллизации и остывания до температуры 40°С после чего кокиль раскрывается и отливка выталкивается плитами толкателей с толкателями установленными на кокильной машине.
Обрубка и механическая обработка отливок.
Годные отливки складываются в контейнер и электропогрузчиком перемещаются на обрубку. Бракованные отправляют на исправление брака.
У отливок обрубаются стояки питатели и заливы по плоскости разъёма после чего они подаются на обрезку где удаляют прибыли. После обрезки отливки перемещаются на зачистку. Отливки зачищаются по контуру и в труднодоступных местах. Далее отливки проходят термическую обработку в воздушно-циркуляционном агрегате. После чего отливки подаются на механическую обработку где они обрабатываются в соответствии с чертежом.
8 Расчёт литниково-питающей системы
Литниково-питающая система — это система каналов для подвода жидкого металла в полость литейной формы отделения неметаллических включений и обеспечения подпитки отливки при затвердевании. При выборе конструкции ЛПС необходимо стремиться к соблюдению следующих принципиальных положений направленных на получение годных отливок и на экономичность их производства:
Обеспечивать принцип направленного затвердевания т.е. последовательного затвердевания от наиболее тонких частей отливки через её массивные узлы к прибыли которая должна затвердевать последней;
Наиболее протяжённые стенки и тонкие кромки ориентировать в форме вертикально т.е. наиболее благоприятно для их спокойного и надёжного заполнения;
Создавать условия для экономичного и механизированного производства отливок в том числе: унификацию типоразмеров ЛПС и их элементов с учётом эффективного использования оснастки имеющегося технологического оборудования печей; удобство выполнения и минимальный объём механической обработки при отрезке отливок и последующем изготовлении из них деталей.
Определяем оптимальную продолжительность заливки метала по формуле:
где — коэффициент равный 17 – 20; принимаем равным 18;
— толщина стенок мм;
— вес одной отливки плюс вес литников и прибылей на одну отливку кг;
— число отливок в форме шт.
Скорость поднятия уровня металла в форме (ммс) определяется по формуле:
где — высота отливки мм.
Общая площадь сечения питателей на одну отливку определяется по формуле (см2):
где — масса отливки кг;
— коэффициент расхода отличается от литья в песчано-глинистые формы и находится в пределах 024–043; принимаем =03;
— расчётный статический напор металла см.
где — высота стояка в см считая от уровня чаши до питателя;
— часть высоты отливки в см исчисляемая от верхней кромки ввода питателя до наиболее высоко расположенной точки отливки;
— общая высота отливки в форме см.
Определяем общую площадь поперечных сечений стояка из соотношения:
Для определения диаметра стояка сначала определяем радиус:
ГЛАВА 1 ОБЩАЯ ХАРАКТЕРИСТИКА ПРОЕКТИРУЕМОГО ЦЕХА.docx
1 Задание по дипломному проектированию
Исходными данными для выполнения дипломного проекта являются:
-задание для дипломного проектирования;
-заданная номенклатура отливок;
-технологические инструкции и нормативы литейного цеха завода изготовителя;
-чертёж отливки представителя — Диск верхний ХМ 09.22.300А;
-задание и документация для выполнения специальной части проекта.
2 Общая характеристика проектируемого цеха
Исходя из общей классификации [1 с. 14] и данных о номенклатуре [табл. 2.1.1] цех имеет следующую характеристику:
По роду сплава — цех цветного литья;
По массе отливки — цех мелкого литья;
По серийности и отраслевому назначению — цех серийного производства отливок для автомобильной отрасли;
По технологическому процессу и объёму производства — цех литья в кокиль.
Сущность процесса литья в кокиль заключается в изготовлении отливок из жидкого расплава свободной его заливкой в многократно используемые металлические формы — кокили обеспечивающие высокую скорость затвердевания жидкого расплава и позволяющие получать в одной форме от нескольких десятков до нескольких тысяч отливок.
Структура цеха включает шихтовое отделение плавильное отделение заливочное отделение участок обрубки и зачистки участок термической обработки склад готовой продукции.
Для транспортных перемещений в цеху предлагается использовать: автомобильный транспорт для доставки материала и отгрузки продукции; электропогрузчики для перемещения расплавленного металла к раздаточным печам отливок к обрубочно-зачистному участку а также для перемещения готовой продукции на склад; подвесной транспорт в виде мостового крана для разгрузки и загрузки шихтовых материалов в суточные бункера а также перемещению весовой тележки к вибролоткам для загрузки шихтовых материалов в индукционную печь.
Для хранения и перемещения грузов в цехе предлагается использовать производственную тару в виде металлических контейнеров.
ГЛАВА 5 СПЕЦИАЛЬНАЯ ЧАСТЬ.docx
Программа LVMFlow предназначена для моделирования процессов формирования отливок в реальных цеховых условиях. Промышленные сплавы в подавляющем большинстве являются многокомпонентными системами. Для моделирования кристаллизации сплава необходима его фазовая диаграмма. К сожалению полных многокомпонентных диаграмм состояния не существует. Достаточно изученными являются фазовые диаграммы двухкомпонентных систем. В связи с этим в базе данных производится приближенный расчёт положения фазовых равновесий многокомпонентного сплава методом деформации двухкомпонентной диаграммы состояния.
С этой целью данные по сплавам в базе данных разбиты на классы: углеродистые стали легированные стали чугуны бронзы силумины и т.д. Класс характеризуется бинарной (базовой) равновесной диаграммой состояния параметрами определяющими деформацию диаграммы при добавлении к двойной системе других элементов и кинетическими коэффициентами фазовых превращений. Для конкретного сплава принадлежащего определённому классу введены: химический состав теплоты фазовых переходов и порог протекания. Химический состав сплава теплоты фазовых переходов и характеристики класса позволяют определить интервал и кинетику кристаллизации данного сплава.
Кроме классов литейных сплавов в базе данных существует класс материалов форм куда занесены наиболее часто применяемые формовочные материалы огнеупоры изоляционные материалы и металлы.
Система LVMFlow удобна и достаточно проста в эксплуатации. Её интерфейс полностью лежит в рамках стандарта интерфейса Windows. Терминология меню и диалогов привычна и понятна для специалиста работающего в литейном производстве. Меню системы продублировано панелью инструментов с иконками довольно точно отражающими суть инструмента и позволяющими сократить число операций при работе с системой. При возникновении затруднений всегда можно воспользоваться справочной системой.
Моделируемые процессы протекают в широком температурном интервале на котором значения теплофизических свойств материалов могут меняться в несколько раз. Поэтому как для материалов форм так и для сплавов введены температурные зависимости теплопроводности теплоёмкости плотности.
Если база данных не содержит нужных пользователю сплавов и материалов форм она может быть пополнена самим пользователем. Ввод и корректировка данных осуществляется в простом диалоге и сопровождается графическим отображением вводимых значений. Корректируются только данные по сплавам и материалам форм параметры классов пользователем откорректированы быть не могут.
В LVMFlow элементарной ячейкой разностной сетки является куб. Поэтому для автоматической генерации сетки достаточно ввести один параметр — размер ячейки (шаг сетки) либо задать общее количество узлов сетки. Чем меньше шаг сетки тем точнее решение которое получится в процессе счета.
Задание граничных условий на границе расчётной области осуществляется выбором одного из четырёх вариантов: а) на границе расчётной области поддерживается заданная температура; б) граница расчётной области является плоскостью симметрии; в) за пределами границы расчётной области располагается бесконечная форма; г) граница расчётной области является границей форма-воздух.
Созданную в системе геометрического моделирования конструкцию можно дополнить построением оболочки вокруг любой части отливки. Для этого достаточно указать эту часть отливки и задать толщину оболочки. Оболочка становится таким же элементом технологической оснастки как и те детали что построены в системе геометрического моделирования. В случае неоднородной технологической оснастки для каждого материала можно задать свою собственную начальную температуру.
В LVMFlow заложена возможность моделирования двух видов заливки: гравитационное литьё и литьё под давлением. Задание места питания металлом (литниковой точки) производится на границе расчётной области в точке принадлежащей отливке или литниково-питающей системе. Для гравитационного литья задаётся напор — высота столба жидкого металла над сечением в котором установлена литниковая точка и коэффициент характеризующий уменьшение потока расплава вызванное трением жидкости о стенки заливочного устройства. Для литья под давлением задаётся либо скорость входного потока либо массовый расход расплава. При задании одного из параметров второй автоматически рассчитывается. Изменение скорости входного потока во времени можно задать изначально формированием таблицы «время-скорость» или организацией системы сенсоров. Установленные в отливку сенсоры работают следующим образом: когда фронт расплава проходит через сенсор происходит смена скорости входного потока.
На границе металл-форма можно ввести параметры характеризующие противопригарное покрытие а также параметры учитывающие образование воздушных зазоров между металлом и формой в процессе затвердевания отливки.
Для более детального анализа пользователь может установить датчики в любом месте расчётной области (в отливке или оснастке). Показания датчиков выводятся в виде графиков временной зависимости выводимой функции (температуры скорости изменения температуры доли жидкой фазы скорости течения расплава входного потока расплава).
Вывод образа отливки (так же как и полей функций характеризующих её состояние) производится в виде изометрического изображения (3D) и в произвольном плоском сечении (2D) в цветовой гамме соответствующей установленной шкале. Функции вращения и масштабирования дополняют возможности просмотра. Для получения более детальной информации можно считать численное значение поля (температуры доли жидкой фазы скорости доли дефектов и т. д.) в произвольной точке расчётной области.
Результаты моделирования можно сохранять автоматически для дальнейшего просмотра и создания архива технологических решений. На отливку заводится «паспорт» в который записываются все параметры каждого моделирования. Результаты расчёта функций можно сохранять в 2D и 3D-виде.
В просмотр результатов включена возможность создания и просмотра результатов с помощью анимации. Это позволяет к примеру просмотреть процесс заполнения отливки в режиме реального времени. В дальнейшем паспорт может быть использован модулем «Начальные установки» в качестве прототипа для нового варианта моделирования заполнения и затвердевания.
Наличие такой системы как LVMFlow в руках инженера-литейщика позволит значительно удешевить и ускорить исследовательскую работу по проектированию отливок.
LVMFlow предлагает широкий набор инструментов для моделирования исследования и создания оптимальной литейной технологии. LVMFlow можно использовать в учебных заведениях при подготовке квалифицированного персонала для литейных производств.
2 Моделирование в программе LVMFlow
Для начала моделирования необходимо создать трёхмерную геометрическую модель отливки с литниково-питающей системой. Для этого воспользуемся программным комплексом геометрического проектирования КОМПАС-3D V16. Сохраняем готовую модель в формате stp и импортируем в программу LVMFlow 4.6r6. Назначаем материалы формы и расплава а также их начальную температуру указываем литниковую точку (точку через которую будет заливаться расплавленный металл) устанавливаем параметры заливки: тип литья величину напора и диаметр струи расплавленного металла.
В модуле «Заполнение и затвердевание» моделируется заполнение формы и кристаллизация расплава который рассматривается как течение вязкой жидкости с учётом процессов теплопередачи.
2.1 Результаты моделирования базового технологического процесса
Рисунок 5.2.1 – Геометрия базовой литейной технологии
Рисунок 5.2.2 – Соотношение температур в отливке
Рисунок 5.2.3 – Соотношение жидкой и твёрдой фазы
На рис. 5.2.4 видны дефекты усадочного характера в массивной центральной части отливки. На рис. 5.2.5 можно наблюдать скопление микропористости в центре отливки и на её поверхности.
Рисунок 5.2.4 – Усадочные раковины
Рисунок 5.2.5 – Микропористость
Рассмотрев полученные результаты прихожу к выводу что при проектировании базовой литейной технологии выбор типа и расчёт литниково-питающей системы произведён неправильно. Мною было принято решение оптимизировать технологию: убрать третью прибыль для сокращения расхода металла а также спроектировать литниково-питающую систему типа «гусиная шейка».
2.2 Результаты моделирования оптимизированного технологического процесса
Рисунок 5.2.6 – Геометрия оптимизированной литейной технологии
Рисунок 5.2.7 – Соотношение температур в отливке
Рисунок 5.2.8 – Соотношение жидкой и твёрдой фазы
Из рис. 5.2.9 видно что усадочные раковины присутствуют исключительно в системе прибылей и литниковой чаше.
Рисунок 5.2.9 – Усадочные раковины
На рис. 5.2.10 также видно улучшение — газовая микропористость в теле отливки и на её поверхности отсутствует.
Рисунок 5.2.10 – Микропористость
Проанализировав полученные данные можно понять что изменение литниково-питающей системы и системы прибылей было оправданным решением которое позволило улучшить качество отливки за счёт плавного подвода жидкого металла к полости формы что исключило захват воздушных масс потоками расплава а также уменьшило разрушающее воздействие струи жидкого металла на стенку кокиля. Помимо этого был повышен выход годного за счёт уменьшения количества металла вследствие сокращения числа прибылей.
03. СОДЕРЖАНИЕ.docx
1 Задание по дипломному проектированию10
2 Общая характеристика проектируемого цеха10
Глава 2 Производственная программа цеха12
1 Расчёт производственной программы цеха13
2 Режимы работы и фонды времени15
Глава 3 Расчёт цеха17
1 Плавильное отделение18
1.1 Структурный баланс металла18
1.2 Технологический процесс плавки алюминиевых сплавов18
1.3 Расчёт шихтовых материалов19
1.4 Расчёт складов шихтовых материалов23
1.5 Расчёт потребного количества плавильных агрегатов25
1.6 Принцип действия и конструкция плавильных агрегатов27
2 Заливочное отделение29
2.1 Выбор оборудования для изготовления отливок30
2.2 Расчёт потребного количества оборудования31
3 Обрубочно-зачистной участок32
4 Участок термической обработки35
5 Вспомогательные отделения37
5.1 Участок подготовки шихтовых материалов37
5.2 Ковшевой участок37
5.3 Ремонтная служба цеха38
5.4 Участки ремонта и хранения оснастки38
5.5 Экспресс-лаборатория38
5.6 Цеховые кладовые39
Глава 4 Технологическая часть40
1 Технологический процесс изготовления отливки «Диск верхний ХМ 09.22.300А»41
2 Назначение и характеристика отливки41
3 Оценка технологичности конструкции детали43
4 Обоснование выбора положения отливки в форме и плоскости
5 Обоснование способа изготовления отливки46
6 Разработка конструкции литейной оснастки48
7 Разработка технологических этапов производства отливки49
8 Расчёт литниково-питающей системы51
Глава 5 Специальная часть54
1 Предназначение компьютерной программы LVMFlow её описание и возможности55
2 Моделирование в программе LVMFlow58
2.1 Результаты моделирования базового технологического
2.2 Результаты моделирования оптимизированного технологического
Глава 6 Строительная часть63
2 Элементы конструкции цеха64
Глава 7 Охрана труда и экология68
1.1 Микроклимат на производстве69
1.2 Шум на производстве72
1.3 Вибрация на производстве73
1.4 Пожаро- и взрывобезопасность производства73
1.5 Электробезопасность на производстве75
1.6 Расчёт искусственного освещения76
Глава 8 Экономическая часть79
1 Организационно-техническое обоснование варианта технологического процесса80
1.1 Обоснование производственной программы литейного
1.2 Описание объекта производства и возможных вариантов его изготовления80
2 Организация и планирование работы отделений литейного цеха82
2.1 Организация и планирование работы плавильного отделения82
2.2 Организация и планирование работы заливочного отделения82
2.3 Организация и планирование работы участка по обрубке и зачистке отливок82
2.4 Организация и планирование работы участка термической
2.5 Выбор и расчёт технологического оборудования83
2.6 Расчёт численности работающих на литейном участке84
3 Расчёт величины инвестиций88
3.1 Состав инвестиций88
3.2 Расчёт инвестиций в здания и сооружения89
3.3 Расчёт инвестиций в оборудование транспорт инструмент и инвентарь90
3.4 Расчёт потребности в оборотных средствах91
4 Калькулирование себестоимости продукции92
4.1. Расчёт затрат на основные материалы93
4.2 Топливо и энергия на технологические и прочие цели94
4.3 Расчёт фонда заработной платы работников участка95
4.4 Общепроизводственные расходы96
4.5 Общехозяйственные расходы97
4.6 Коммерческие расходы97
5 Оценка эффективности проектного варианта литейного участка98
5.1 Расчёт свободной отпускной цены 1 тонны годного литья98
5.2 Расчёт балансовой прибыли98
5.3 Расчёт чистой прибыли99
5.4 Расчёт показателей эффективности проекта100
6 Основные технико-экономические показатели проекта103
Глава 9 Энергосбережение104
Список использованных источников109
02. Кокиль для отливки Диск верхний ХМ 09.22.300А.spw

ГГТУ им. П.О. Сухого
ДМ 1790.02.03.00.00 СБ
Выталкиватель отливки
Колонка направляющая
Плита крепления левая
Плита крепления правая
Гайка М16.5 ГОСТ 5915-70
Рым-болт М24 ГОСТ 4751-73
01. Планировка цеха цветного литья.spw

ГГТУ им. П.О. Сухого
ДМ 1790.01.02.00.00 ТЧ
Теоретический чертёж
Печь индукционная ИАТ-10
Кокильная машина мод. 82А303
Кокильная машина мод. 82А405
Кокильная машина мод. 82А505
Обрубной пресс мод. П 16А
Ленточнопильный станок Stalex BS-5030
Обдирочно-шлифовальный станок ВШ-041
Воздушно-циркуляционный агрегат ПАП-3М
Станок токарно-винторезный
Станок токарно-карусельный
Станок карусельно-фрезерный
Станок заточный ЗБ667
Станок заточный ЗН64М
Станок заточный 360М
Станок горизонтально-расточный
Станок заточный универсальный
Станок образивно-отрезной
Станок точильно-шлифовальный
Станок заточный ЗД692
Станок горизонтально-фрезерный
Станок вертикально-сверлильный
Полуавтомат круглошлифовальный
повышенной точности ЗМ162
Станок заточый ЗН64М
Кран мостовой Q=10 т
Дозатор пластинчатый
Электропогрузчик FB50-MQJZ2
Раздаточная печь САТ-0
Рекомендуемые чертежи
- 25.01.2023
- 13.05.2023
Свободное скачивание на сегодня
- 24.01.2023