Исследование нагруженности привода перемещения каретки механизма смены трубы МНЛЗ



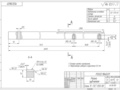
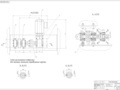
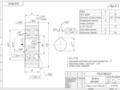
- Добавлен: 26.03.2021
- Размер: 2 MB
- Закачек: 0
Описание
Курсовой проект: “Исследование нагруженности привода перемещения каретки механизма смены трубы МНЛЗ”
Состав проекта
![]() ![]() ![]() ![]() |
![]() ![]() ![]() |
![]() ![]() ![]() ![]() |
![]() ![]() ![]() ![]() |
Дополнительная информация
А1-привод перемещ. кар. мех. смены трубы-ВО.frw

А3-рейка.cdw

А3-колесо реечное..cdw

Рекомендуемые чертежи
- 21.12.2020