Завод по производству известково-зольного кирпича на базе ТОО Силикат г.Семей




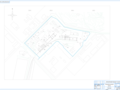
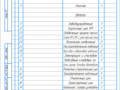
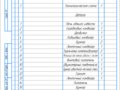
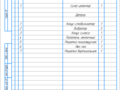
- Добавлен: 24.01.2023
- Размер: 7 MB
- Закачек: 1
Описание
Завод по производству известково-зольного кирпича на базе ТОО Силикат г.Семей
Состав проекта
![]() |
![]() |
![]() ![]() ![]() ![]() |
![]() ![]() ![]() |
![]() ![]() ![]() |
![]() ![]() ![]() |
![]() ![]() ![]() ![]() |
![]() ![]() ![]() ![]() |
![]() ![]() ![]() ![]() |
![]() ![]() ![]() |
![]() ![]() ![]() |
![]() |
![]() ![]() ![]() |
![]() ![]() ![]() |
![]() ![]() ![]() ![]() |
![]() ![]() ![]() |
![]() ![]() ![]() ![]() |
![]() ![]() ![]() ![]() |
![]() ![]() ![]() ![]() |
![]() ![]() ![]() |
![]() ![]() ![]() |
![]() ![]() ![]() |
Дополнительная информация
Силос-реактор.cdw

Специф.техология.spw

Специф.силос.spw

ген план мой.cdw

Основные показатели мои.cdw

технология.cdw

Специф.генплан.spw

планишкО.dwg

Рекомендуемые чертежи
- 18.02.2014
- 13.05.2023
- 20.08.2014
Свободное скачивание на сегодня
- 22.08.2014
- 29.08.2014