Производство известково-шлакового вяжущего


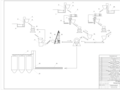
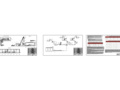
- Добавлен: 24.01.2023
- Размер: 779 KB
- Закачек: 0
Узнать, как скачать этот материал
Подписаться на ежедневные обновления каталога:
Описание
Производство известково-шлакового вяжущего
Состав проекта
![]() |
![]() |
![]() ![]() ![]() |
![]() ![]() ![]() ![]() |
![]() ![]() ![]() ![]() |
Дополнительная информация
Контент чертежей
Лист 1,2,3.frw

Лист 1,2,3.dwg

Рекомендуемые чертежи
- 12.12.2016
- 24.04.2014
Свободное скачивание на сегодня
Обновление через: 10 часов 4 минуты