Выталкиватель заготовок с трайбаппаратом




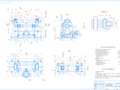
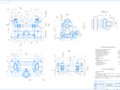
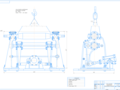
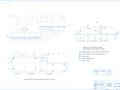
- Добавлен: 24.01.2023
- Размер: 3 MB
- Закачек: 0
Описание
Состав проекта
![]() |
![]() |
![]() ![]() ![]() |
![]() ![]() ![]() ![]() |
![]() ![]() ![]() |
![]() ![]() |
![]() ![]() ![]() |
![]() ![]() ![]() ![]() |
![]() ![]() |
![]() ![]() ![]() ![]() |
![]() ![]() ![]() |
![]() ![]() ![]() |
![]() ![]() ![]() ![]() |
![]() ![]() ![]() |
![]() ![]() ![]() |
![]() ![]() ![]() |
Дополнительная информация
ППР 2.doc
Капитального ремонта
Время выполнения работ
Трайбаппарат выталкивателя заготовок
Таблица 4.5 Годовой график плановых ремонтов трайбаппарата выталкивателя заготовок на 2006г
Виды ремонтов: Продолжительность ремонта:
Т1 - текущий; Т1 - 8 ч.
Строповка.cdw

выталкивателя заготовок
Ключи S= 17х22; 32х36; 41х46;
Рис схема цеха спц.doc
– правильная машина; 2 – загрузочные решетки; 3 – подводящий рольганг; 4 – рольганговые весы; 5 – нагревательная печь» 6 – возвратный рольганг; 7 – стеллаж; 8 – черновая группа клетей; 9 11 14 – кривошипные ножницы; 10 – промежуточная группа клетей; 12 – чистовая группа клетей; 13 – прибор для контроля геометрических параметров раската; 15 – трайбаппарат; 16 – линия охлаждения проката; 17 – моталки; 18 – шагающие транспортеры за моталками; 19 – рольганг №1; 20 – транспортер с шагающими колосниками; 21 – рольганг №2; 22 – вязальные машины; 23 – опрокидывающее устройство; 24 – бунтосъемные машины; 25 – корзины для складирования бунтов; 26 – установка для размотки и правки бунтов проката; 27 – проходные роликовые печи; 28 – колпаковые печи; 29 – кантователь мотков; 30 – передаточные тележки; 31 – переводная стрелка; 32 – участок промежуточного водяного охлаждения; 33 – подводящая проводка к чистовому блоку; 34 – трайбаппарат; 35 – универсальные иножницы; 36 – петлерегулятор; 37 – удерживающие ножницы; 38 – чистовой блок; 39 – приборы для контроля качества проката; 40 – отводящая проводка с водяным охлаждением; 41 – трайбаппарат; 42 – укладчик витков; 43 – транспортер витков; 44 – вентиляционная установка; 45 – накопитель витков; 46 – центрирующее устройство; 47 – поворотный стол; 48 – крюковой конвейер; 49 – инспекционный участок; 50 – устройство для подпрессовки и увязки бунтов; 51 – весы для взвешивания бунтов; 52 – разгрузочная тележка; 53 – шаговый транспортер; 54 – линия для изготовления маркировочных ярлыков; 55 – чеканочный механизм.
3.doc
Мелкосортные станы предназначены для прокатки углеродистой стали: круглой квадратной шестигранной полосовой угловой а также других профилей эквивалентного сечения.
Современные мелкосортные станы являются непрерывными т.е. прокатываемый металл находится одновременно в нескольких рабочих клетях.
Сталь прокатывают из заготовки сечением 60х6080х80120х120 или 150х150 мм длиной 12 м и массой соответственно от 340 кг до 2200 кг.
Поступающие на стан заготовки электромагнитным краном подаются пачками на загрузочные устройства с которых они передаются по одной на подводящий рольганг. По подводящему рольгангу заготовки транспортируются к вытаскивателю задающему их в печь. С противоположной стороны печи заготовки останавливаются стационарным упором. С торцевой стороны печи расположен толкатель служащий для перемещения заготовок по поду печи. При подаче очередной холодной заготовки в печь нагретая заготовка передвигается до выталкивателя которым она выталкивается из печи. Далее заготовка захватывается вытаскивателем и направляется распределительным устройством по желобам либо в левую либо в правую нитку стана (при прокатке в две нитки).
Область применения выталкивателя заготовок – металлургическое производство прокатные цеха мелкосортные станы.
2 Техническая характеристика трайбаппарата выталкивателя заготовок
Электродвигатель тип МТF411-6-С:
- число оборотов обмин 965
Редуктор тип ЦОМ-30-I-64:
- передаточное число 64
Пневмоцилиндр тип ПЦ-250-120:
- диаметр поршня мм 250
Рабочее давление МПа 04
Сечение сдвигаемой заготовки (max) мм 150х150
Длина сдвигаемой заготовки мм 12000
Производительность выталкивателя
3 Описание конструкции выталкивателя заготовок
Выталкиватель служит для поштучной выдачи заготовок из нагревательной печи.
Выталкиватель (рис. 3.1) состоит из толкающей штанги 2 опорного ролика который является опорой штанги при ее движении по поду печи; механизма поперечного перемещения штанги 6 холостой тележки 7 водяного желоба 8 служащего для охлаждения штанги и фотореле 9. Штанга передвигается в направляющих роликах 16 при помощи тянущих роликов: верхнего приводного 10 и нижних прижимных 3 прижатие которых осуществляется от пневмоцилиндров 15 через рычажную систему.
Привод верхнего ролика 10 состоит из электродвигателя 12 одноступенчатого цилиндрического редуктора 14. Привод оборудован тормозом 11.
Рисунок 3.1 Выталкиватель заготовок
- ролик; 2- толкающая штанга; 3- прижимные ролики;
- трайбаппарат; 6- штанга перемещения; 7- холостая тележка;
- водяной желоб; 9- фотореле; 10- приводной ролик; 11- тормоз;
- электродвигатель; 16- направляющие ролики; 14- редуктор;
- муфта; 14- редуктор; 15- пневмоцилиндр;
- направляющие ролики.
Механизм поперечного перемещения штанги (рис. 3.2) состоит из электродвигателя 2 соединенного муфтой 1 с винтом 9 который находится в зацеплении с гайкой 5 запрессованной в каретке 7. Каретка 7 своими ходовыми колесами 5 перемещается по направляющим 6.
Рисунок 3.2 Механизм поперечного перемещения штанги
- муфта; 2- электродвигатель; 5- гайка; 6- направляющие;
- каретка; 8- водяной желоб; 9- винт.
Для предотвращения аварий действие выталкивателя и толкателя заготовок должно быть сблокировано электросхемой так что каждый из механизмов может работать только в том случае если один из них отключен т. е. одновременная работа двух механизмов исключена. Поэтому толкатель и выталкиватель работают последовательно: заготовка подошедшая к штангам толкателя проталкивается в печь и сразу вслед за этим выталкиватель выдает одну нагретую заготовку из печи.
4 Анализ недостатков трайбаппарата выталкивателя заготовок
В трайбаппарате выталкивателя заготовок за период его эксплуатации наблюдались следующие недостатки:
- выход из строя подшипников приводного ролика вследствии недостаточного количества смазки;
- использование индивидуального резервного привода (в случае поломки основного привода) для каждого из выталкивателей так как хвостовик приводного вала выполнен только с одной стороны;
- ремонт прижимного ролика требует полной разборки конструкции трайбаппарата из-за невозможности снять его с кронштейнов;
- использование двух цилиндров в действиях которых при прижиме наблюдается не согласованность в результате чего штанга смещается относительно оси симметрии трайбаппарата что приводит к нарушению режима работы выталкивателя заготовок поскольку приходится перенаправлять штангу выталкивателя.
5 Предложения по модернизации трайбаппарата выталкивателя заготовок
Для модернизации трайбаппарата выталкивателя предлагается:
Обеспечить возможность подвода жидкостной смазки к подшипникам приводного ролика. Выполнить отверстия для подвода смазки в стойках трайбаппарата выталкивателя.
Изменить конструкцию верхнего приводного ролика трайбаппарата выполнив хвостовики вала с двух сторон обеспечив возможность присоединения привода с двух сторон.
Изменить конструкцию кронштейнов и нижнего прижимного ролика трайбаппарата закрепленного в них для удобства монтажа и демонтажа.
Замена двух пневмоцилиндров 200 мм прижима прижимного ролика на один пневмоцилиндр 250 мм исключение несогласованных действий двух пневмоцилиндров во время прижима ролика.
6 Описание конструкции модернизированной машины ее достоинства по сравнению с машиной-прототипом
Модернизированный трайбаппарат выталкивателя заготовок из нагревательной печи показан на рисунке 3.2. В модернизированном трайбаппарате используются стойки 1 2 старой конструкции в которых выполнены отверстия для подвода централизаванной жидкой смазки. Стойки скреплены стяжками 10 11.
Приводной ролик 3 устанавливается в корпуса подшипников стоек. Ролик выполнен цельнометаллическим с хвостовиками для присоединения привода с двух концов.
Прижимной ролик 4 укороченной конструкции устанавливается в разъемные кронштейны 5. Кронштейны установленные на общей оси 8 связаны между собой тягой 7 которая воспринимает усилие цилиндра 6. Движением цилиндра вперед нижний прижимной ролик отводится от верхнего приводного ролика а обратным ходом прижимается и прижимает штангу выталкивателя 9.
Рисунок 3.2 Трайбаппарат выталкивателя заготовок
Достоинства модернизированного трайбаппарата:
- использование базовой конструкции без значительных переделок;
- простота изготовления;
- относительная дешевизна изготовления;
- простота в обслуживании и ремонте;
- увеличение срока эксплуатационных характеристик.
7 Расчеты по модернизации
7.1 Расчеты нагрузок действующих на машину и определение исходных данных для расчета
- мощность кВт N = 22
- число оборотов обмин n = 965
- передаточное число i = 64
- приводного мм D = 200
- прижимного мм D1 = 200
- диаметр поршня мм d = 250
Рабочее давление МПа р = 04
Длина сдвигаемой заготовки мм L =12000
Расчетную схему действия сил в механизме трайбаппарата выталкивателя см. рис. 3.3.
Рисунок 3.3 Схема действия сил в механизме трайбаппарата выталкивателя
Определим крутящий момент приводного ролика трайбаппарата [4 т.2 стр. 18]
где 9750 – коэффициент перевода крутящего момента выраженного в Нм;
N = 22 – мощность двигателя кВт;
= 0922 – КПД привода;
n1 – число оборотов ролика обмин
n1 == 1508 обмин. (3.2)
Окружная скорость ролика [12]
где d = 200 мм – диаметр ролика;
n1 =1508 обмин – число оборотов ролика;
– коэффициент перевода скорости выраженной в мс.
Определим окружное усилие ролика см. рис. 3.1 [6 стр. 146].
где Мкр = 13513 Нм – крутящий момент приводного ролика;
d = 200 мм – диаметр ролика.
Определим необходимое расчетное усилие для сдвига заготовки штоком.
Вес заготовки [4 т.2 стр. 62]
Q = b2·L·ρ = (150·10-3)2·12·78500 = 21195 Н (3.5)
где b = 150 мм – сторона квадратной заготовки;
L = 12000 мм – длина заготовки;
ρ = 78500 Нм3 – плотность материала (для стали).
Вес штока [4 т.1 стр.62]
Q1 = = 20308 Н (3.6)
где Dшт = 114 мм – диаметр штока;
dшт = 100 мм – диаметр штока внутренний;
L = 11000 мм – длина штока;
Необходимое расчетное усилие для сдвига заготовки
Ррас = Q·fтр.с.+ Q1· fтр.к = 21195·015 + 2030·01 = 33823 Н (3.7)
где Q = 21195 – вес заготовки;
fтр.с = 015 – коэффициент трения скольжения [4 т.1 стр. 98];
Q = 2030 – вес штока;
fтр.с = 01 – коэффициент трения качения [4 т.1 стр. 99].
Сдвиг заготовки выполняется при условии что окружное усилие ролика будет превышать расчетное усилие сдвига;
условие выполняется.
7.2 Расчет мощности привода механизма
Выполним расчет потребляемой мощности двигателя.
Необходимое тяговое усилие [7 стр. 6]
Nвых == 176 кВт (3.9)
где Р = 31996 Н – расчетное усилие для сдвига заготовки;
= 158 мс – окружная скорость ролика;
00 – коэффициент перевода мощности выраженной в Нмс.
Определим требуемую мощность электродвигателя
Nтр == 191 кВт (3.10)
где общ= 1234 = 098·098·098·098 = 0922 (3.11)
где 1 = 098 – КПД электродвигателя;
= 098 – КПД редуктора (из кинематической схемы рис. 3.4);
= 098 – КПД соединительных муфт (из кинематической схемы рис.3.4).
На выталкивателе установлен двигатель тип МТВ411-6-С
Число оборотов обмин 965
7.3 Силовой и кинематический анализ механизмов
Силовой анализ механизма трайбаппарата выталкивателя сводится к определению необходимой силы прижима штока выталкивателя прижимным роликом трайбаппарата с условием исключения проскальзывания и остановки приводного ролика трайбаппарата. Проводим анализ кинематической схемы рис. 3.4.
Рисунок 3.4 Кинематическая схема трайбаппарата выталкивателя заготовок
Определим усилие прижима ролика.
Усилие развиваемое цилиндром по закону Паскаля [14]:
Рц.т = = 19625 Н (3.12)
где d = 250 мм – диаметр поршня;
р = 04 МПа – давление воздуха в цеховой магистрали;
Рц = = 16485 Н (3.13)
dшт = 100 мм – диаметр штока;
р = 04 МПа – давление воздуха в цеховой магистрали.
Прижим ролика осуществляется посредством тянущего усилия пневмоцилиндра.
Определим крутящий момент кронштейна (из формулы 3.4)
М = Рц·R = 16485·600·10-3 = 9891 Нм
где Рц = 16485 – тянущее усилие цилиндра;
R = 600 мм – плечо кронштейна (из рис. 3.3).
Усилие прижима ролика [9 стр. 288]
где М = 9891 Нм – крутящий момент кронштейна;
r = 200 мм – плечо кронштейна (из рис. 3.3);
fтр = 015 – коэффициент трения скольжения между прижимным роликом и штоком (из рис. 3.3).
Необходимое усилие прижима ролика исключающее проскальзывание должно превышать расчетное усилие прижима ролика на 25% а также быть меньше окружной скорости приводного ролика на 25% – исключая его остановку.
Расчетное усилие прижима ролика
Ррас. пр == 33823 Н (3.14)
где = 15 – коэффициент запаса сцепления;
Ррас = 33823 – расчетное усилие сдвига;
fтр = 015 – коэффициент трения скольжения между приводным роликом и штоком (из рис. 3.3).
Условие работоспособности выталкивателя:
исключение проскальзывания
5·33823 = 42279 Н 74183 Н.
исключение остановки
5·74183 = 92729Н 13513 Н
7.4 Расчет и выбор элементов кинематической схемы механизма
Вал электродвигателя согласно кинематической схемы привода трайбаппарата выталкивателя соединяется с быстроходным валом редуктора при помощи муфты. В нашем случае это упруго - втулочная пальцевая муфта.
Выбор муфты производится по диаметру соединяемых концов и расчетом крутящего момента.
Определим крутящий момент муфты (из формулы 3.1):
Мдвкр= Ммкр.п.= = 2228 Нм.
Далее используя условие выбора муфты согласно которому:
[Мм кр] ≥ Мм кр.п. (3.17)
[n м] ≥ n м.п. (3.18)
Выбираем по каталогам муфту типа МУВП-50 со следующей технической характеристикой (см. рис. 3.5):
Допустимый крутящий момент Нм 500
Допустимая частота вращения обмин 3600
Диаметр тормозного шкива мм 200
Количество пальцев 8
Рисунок 3.5 Соединение муфтой типа МУВП – 50
Схема соединения следующая полумуфта одевается на быстроходный вал редуктора ответная ей полумуфта с закрепленными на ней пальцами с упругими элементами - на валу электродвигателя.
Выбор тормоза производится по крутящему моменту муфты используя условие согласно которому
[Мт] ≥ Мм кр.п. (3.19)
Выбираем по каталогам тормоз колодочный ТКГ-200 со следующей технической характеристикой.
Тормозной момент Нм 300
Тормозной шкив мм 200
Далее чтобы компенсировать возможные перекосы момент с тихоходного вала редуктора через муфту зубчатую передается на вал ролика который передает движение штоку выталкивателя.
Зубчатая полумуфта соединяет тихоходный вал редуктора и вал ролика.
Выбор муфты производится по диаметру соединяемых концов и расчетом крутящего момента [4 т.2 стр.18].
Ммкр.з. = Ммкр.п. ·іред·ред (3.20)
где Ммкр.п = 2228 Нм – крутящий момент на быстроходном валу редуктора;
іред = 64 – передаточное число редуктора;
ред = 098 – КПД редуктора.
Ммкр.з. = 2228·64·098 = 13974 Нм.
Выбираем по каталогам муфту типа МЗ-3 со следующей технической характеристикой (см. рис. 3.6):
Допустимый крутящий момент Н м 3150
Допустимая частота вращения обмин 4000
Маховый момент Нм2 42
Рисунок 3.6 Соединение муфтой типа МЗ – 3
7.5 Прочностные расчеты деталей узлов подвергающихся модернизации
Расчет кронштейна на прочность.
Кронштейн передающий крутящий момент от пневмоцилиндра к прижимающему ролику воспринимает нагрузку Рц в зоне возможного излома сечение А-А (см. рис. 3.7).
Проверка сечения кронштейна на прочность А-А рис. 3.7.
Рисунок 3.7 Кронштейн
Определение нагрузки действующей на кронштейн:
где М = 11775 Нм – крутящий момент передаваемый кронштейном;
R = 350 мм – расстояние от точки закрепления до точки приложения силы.
Согласно условию прочности на изгиб [5]:
где М = 11775 Нм – изгибающий момент;
W – момент сопротивления сечения мм3;
[]из = 110 МПа –допускаемое напряжение изгиба для Ст 3 ГОСТ 380-94 [4 т.1 стр. 87].
Сечение А-А кронштейна рис. 3.7 имеет форму швеллера см. рис. 3.8. Для определения момента сопротивления сечения необходимо разбить сечение на простые части и вычислить главные моменты инерции этих частей [5]. Сечение А-А имеет две оси симметрии которые и являются главными центральными осями. Сечение рассматриваем как состоящее из независимых полос.
Определим положение центра тяжести сечения а следовательно и главных центральных осей.
Рисунок 3.8 Положение главных центральных осей составного сечения
Для данного сечения ось у0 является осью симметрии и положение центра тяжести определяется одной координатой.
Статический момент составной фигуры определяется как сумма статических моментов составляющих фигур [5 стр. 108].
Sx = F1y1 + F2y2 + F3y3 (3.23)
Sx = 90·30·135 + 90·25·125 + 95·30·725 = 599250 мм3
где F1 F2 F3 = ln ·bn – площадь полос мм2 (3.24)
b1 = 30 мм – толщина верхней полосы;
b2 = 25 мм – толщина нижней полосы;
b3 = 30 мм – толщина вертикальной полосы.
y1 = 135 мм – расстояние от центра тяжести верхней полосы точка О1 к оси симметрии х0;
y2 = 125 мм – расстояние от центра тяжести нижней полосы точка О2 к оси симметрии х0 ;
y3 = 725 мм – расстояние от центра тяжести вертикальной полосы точка О3 к оси симметрии х0 .
Координата центра тяжести сечения в системе оси х0 [5 стр. 108]
у0 = = = 768 мм. (3.25)
Определим момент инерции составных деталей относительно оси х.
Для верхней пластины
где момент инерции верхней пластины относительно оси х1 составит [5 стр. 110]:
а1 = (135–768) – расстояние между центром тяжести верхней полосы точка О1 и центром тяжести сечения точка О мм.
Jx = 81·104 + (135–768)2 ·90·25 = 9956·104 мм4.
где момент инерции нижней пластины относительно оси х2 составит:
а2 = (125–768) – расстояние между центром тяжести нижней пластины точка О2 и центром тяжести сечения точка О мм.
Jx = 469·104 + (125–768)2 ·90·25 = 9772·104 мм4.
Для вертикальной пластины
где момент инерции вертикальной пластины относительно оси х2 составит:
а3 = (725–768) – расстояние между центром тяжести вертикальной пластины точка О3 и центром тяжести сечения точка О мм.
Jx = 8574·104 + (725–768)2 ·95·30 = 8627·104 мм4.
Определим момент инерции сечения
Jx = Jx + Jx + Jx (3.27)
Jx = 9956·104 + 9772·104 + 8627·104 = 28355·104 мм4.
Тогда момент сопротивления составного сечения составит [5 стр. 85]:
W = = 3692038 мм3 (3.28)
где уmax = 768 мм – расстояние от точки приложения нагрузки до нейтрального слоя точки О.
Наибольшее нормальное напряжение в опасном сечении А-А:
Кронштейн состоит из двух частей и крепится к валу с помощью 4х болтов см. рис. 3.9. Определим необходимый диаметр болтов клемового соединения кронштейна [9 стр. 280].
Рисунок 3.9 Схема крепления кронштейна к валу
Требуемый момент сил трения должен быть на 25% больше крутящего момента кронштейна [9 стр. 280].
Мт = 125·М = 125·9891 = 123638 Н (3.29)
где М = 9891 Нм – крутящий момент кронштейна.
Определим величину силы трения между валом и ступицей клеммы
Ртр == 131529 Н (3.30)
где Мт = 123638 Н – момент сил трения;
dв = 94 мм – диаметр вала (из чертежа).
Требуемая сила затяжки болтов обеспечивающая нормальное давление
Q = N == 219215 Н (3.31)
где Ртр = 131529 Н – сила трения между валом и ступицей клеммы;
fтр = 015 – коэффициент трения скольжения между валом и ступицей клеммы;
z = 4 – количество болтов.
Определим диаметр болтов по требуемому усилию затяжки.
Для болта с резьбой М24 из Ст 3 усилие затяжки 23500 Н [9 стр. 280 табл.36].
Принимаем диаметр болтов с резьбой М24.
Усилие пневмоцилиндра воспринимает тяга трайбаппарата выталкивателя. Произведем проверочный расчет тяги подверженной напряжению изгиба и определим наибольший прогиб тяги (см. рис. 3. 10 и рис. 3.11).
Рисунок 3.10 Схема сил действующих на тягу трайбаппарата выталкивателя
Составим схему сил нагружения тяги рис. 3.11.
Рисунок 3.8 Схема сил действующих на тягу трайбаппарата выталкивателя
Определим из условия равновесия реакции опор:
RА = RВ = 05·ql (3.32)
где q – нагрузка действующая на ролик;
l = 990 мм – расстояние между опорами.
где Р = 16485 Н – нагрузка действующая на тягу (тянущее усилие цилиндра).
RА = RВ = 05·166·990 = 8217 Н.
Наибольший изгибающий момент составит
Мmax = = 20337075 Нмм = 20337 Нм. (3.34)
Построим эпюру изгибающих моментов рис. 3.12:
Рисунок 3.12 Эпюра изгибающих моментов
Проверим на прочность сечение ролика под действием изгибающего момента (по формуле 3.22).
[]из = 115 Нмм2–допускаемое напряжение изгиба для стали 10.
Тогда момент сопротивления сечения тяги:
W = = 544099 мм3 (3.35)
где d = 76 мм – диаметр тяги;
s = 12 мм – толщина стенки тяги.
Наибольшее нормальное напряжение:
Определим наибольший прогиб тяги [4]
где Е = 21·105 МПа – модуль продольной упругости для стали;
[у] – допускаемый прогиб тяги мм;
Jx – осевой момент инерции мм4.
Jx = = 206757696 мм4. (3.37)
Допускаемый прогиб тяги не должен превышать 00001÷00005 расстояния между опорами [4 т. 2 стр. 16].
[у] =00001÷00005·l (3.38)
где l = 990 мм – из схемы выталкивателя.
[у] = 00001÷00005·990 = 0099÷0495 мм.
Наибольший прогиб ролика составит:
у = = 0478 мм 0495 мм.
Прогиб ролика не выходит за пределы допустимой величины.
Расчет пневмоцилиндра.
Проектируемый цилиндр изображен на рисунке 3.13. По особенностям напряженного состояния цилиндр можно условно разбить на три зоны: цилиндрическую А фланца Б и дно В.
Цилиндрическую зону достаточно удаленную от дна и
фланца допустимо рассматривать как толстостенную трубу и рассчитывать по формулам Ляме [13 14].
Рисунок 3.13 Пневмоцилиндр прижима ролика выталкивателя
- гильза пневмоцилиндра; 2- шток; 3- крышка передняя;
- крышка задняя; 5- поршень; 6- втулка направляющая;
9- кольца уплотнительные; 810- манжеты; 11- крышка;
- кольцо направляющее; 13- стяжки.
Допускаемое напряжение цилиндра находим из выражения [13 стр. 85]
где Т - предел текучести при растяжении МПа;
n - запас прочности по пределу текучести;
рпр – пробное давление МПа.
Так как цилиндры должны быть испытаны давлением 50% от номинального то в расчетах будем использовать это давление.
рпр = 15·р = 15·04 = 6 МПа. (3.40)
Величина допускаемого напряжения для из стали (03÷035% С) []=90-110МПа для цилиндров из низколегированной стали (15÷2% Ni) []=150-180 МПа.
Для гильзы цилиндра выбираем сталь 45 ГОСТ 1050-88.
Наружный радиус гильзы цилиндра.
Полученный размер показывает что рабочее давление действующее на стенки цилиндра незначительно. Так как цилиндр может быть подвержен случайным различным внешним нагрузкам толщину стенки гильзы принимаем исходя из опыта проектирования пневмоцилиндров машиностроительными заводами принимаем наружный радиус гильзы цилиндра равен rн = 1325 мм.
Если на цилиндр действует только внутреннее давление р то в стенках его возникают напряжения:
осевые от влияния дна
Наибольшие напряжения возникают на внутренней поверхности гильзы цилиндра (r=rв). По энергетической теории прочности эквивалентное напряжение определяется выражением
Максимальное напряжение будет на внутренней стенке
Запас прочности стенки гильзы цилиндра по пределу текучести находим из выражения (3.2)
где Т = 650 МПа - предел текучести при растяжении [4 т.1 стр.88].
По экспериментальным данным при конструировании прессов запас прочности по пределу текучести n ≥ 25 [14 стр. 89].
Условие выполняется.
Расчет резьбовых соединений пневмоцилиндра.
Определим количество стяжек необходимых для крепления задней и передней крышек к гильзе цилиндра. Расчет будем производить для стяжек различного диаметра с целью выбора оптимального варианта [6 стр. 57].
где Qрас – расчетная нагрузка в поршневой полости Н;
[]р – допускаемое напряжение МПа;
z – количество стяжек.
Расчетная нагрузка действующая на крышку с учетом предварительной затяжки крышки [6 стр. 63 ].
Qрас= [13·Кзат (1–) + ]·Рц.т (3.48)
где Рц.т = 19625 Н – расчетная нагрузка в поршневой полости;
Кзат =2÷4 – коэффициент запаса предварительной затяжки;
= 02÷03 – коэффициент внешней нагрузки [6 стр. 61].
Qрас= [13·3·(1–025) + 025]·19625 = 623094 Н.
Принимаем диаметр шпилек – резьба М16.
Допускаемое напряжение
где Т =315 МПа - предел текучести при растяжении для стали 35 ГОСТ 1050-88 [4 т.1 стр. 88];
[nТ] = 5 – запас прочности [6 стр. 55 табл. 3.3].
Допускаемая нагрузка действующая на витки резьбы шпильки по формуле
Qдоп == 1644657 Н. (3.50)
где d = 16 мм – диаметр резьбы;
z = 12 – количество стяжек;
[]р = 682 МПа – допускаемое напряжение.
Условие прочности резьбы стяжек
Определим длину свинчивания резьбы штока цилиндра из условия прочности если диаметр резьбы М48х3:
где []ср = 90 МПа – допускаемое напряжение при срезе [4 т.1 стр. 88];
где Р = 3 мм – шаг резьбы;
Н = 1866Р мм – рабочая высота профиля резьбы [4 т.1 стр. 447];
b = 075Р мм – толщина витка у основания [4 т.1 стр. 447];
[]из = 185 МПа – допускаемое напряжение при изгибе [5 стр. 88].
где d = 108Р мм – внутренний диаметр резьбы [4 т.1 стр. 447];
[]см = 220 МПа – допускаемое напряжение при смятии [4 т.1 стр.88].
Принимаем длину резьбы согласно нормальным линейным размерам
Выполним проверочный расчет оси крепления проушины пневмоцилиндра к кронштейну на смятие и срез.
Проверка оси на смятие [6 стр. 18]
где Р = 16485 Н – нагрузка действующая на ось (тянущее усилие цилиндра);
F = ds – площадь сечения оси в местах контакта с вилкой кронштейна мм2 [4 т.1 стр. 59];
где d = 40 мм – диаметр оси из чертежа;
s = 20 мм – толщина уха вилки кронштейна из чертежа;
[]см = 210 МПа – допускаемое напряжение при смятии для стали 45 ГОСТ 1050-88 [4 т.1 стр. 88].
Проверка оси на срез [6 стр. 18]
ср== 131 МПа (3.55)
F = r2 – площадь сечения оси мм2 [4 т.1 стр. 60];
где r = 20 мм – радиус оси из чертежа;
[]ср = 85 МПа – допускаемое напряжение при срезе для стали 45 ГОСТ 1050-88 [4 т.1 стр. 88].
7.6 Выводы по результатам расчетов
Стойки трайбаппарата выталкивателя были выполнены без возможности подвода жидкостной смазки к подшипникам приводного ролика.
Модернизация стоек (сверловка отверстий) обеспечивает централизованный подвод смазки к оси. Это обеспечит надежность работы роликов и увеличит срок их эксплуатации.
Верхний приводной ролик трайбаппарата был выполнен с хвостовиком с одной стороны и имел возможность присоединения только к приводу левого выталкивателя или только – правого. Для обеспечения бесперебойной работы выталкивателей в резерве имелись два двигателя для левого и правого выталкивателей.
Выполнение верхнего ролика приводным на обе стороны дает возможность применения на левом и правом выталкивателях. Применение ролика с двумя хвостовиками обеспечивает бесперебойную работу выталкивателей используя один резервный двигатель.
Монтаж и демонтаж нижнего прижимного ролика трайбаппарата и цельнолитых кронштейнов в которых он установлен был затруднен.
Выполнение укороченного прижимного ролика дает возможность его быстрой замены.
Выполнение кронштейнов разъемной конструкции дает возможность их демонтажа без снятия ролика.
Прижим прижимного ролика осуществляли два пневмоцилиндра 200 мм.
На основании результатов расчетов имеем возможность установки одного пневмоцилиндра 250 мм исключаем несогласованные действия двух пневмоцилиндров во время прижима ролика.
Модернизация конструкции трайбаппарата выталкивателя дает возможность уменьшить его себестоимость уменьшить сроки проведения ремонтов увеличить межремонтный цикл.
Нормы требований безопасности конструкции – соблюдены.
1.cdw

Трайбаппарат выталкивателя заготовок
1 Диаметр ролика приводного
2 Диаметр ролика прижимного
3 Сечение сдвигаемой заготовки (max)
4 Длина сдвигаемой заготовки
5 Пневмоцилиндр тип ПЦ-250-120:
1 Электродвигатель тип М ТВ4 11-6-С:
2 Редуктор тип ЦОМ-30-I-64
передаточное число 6
Технические требования
*Размеры для справок.
Подшипниковые камеры заполнить смозкой УСс (солидол
синтетический) ГОСТ 4366-76.
Все нерабочие поверхности должны быть загрунтованы
грунтовкой ФЛ-03к ГОСТ 9109-93 и окрашены эмалью ПФ-115
Трайбаппарат виталкивателя.cdw

Трайбаппарат выталкивателя заготовок
1 Диаметр ролика приводного
2 Диаметр ролика прижимного
3 Сечение сдвигаемой заготовки (max)
4 Длина сдвигаемой заготовки
5 Пневмоцилиндр тип ПЦ-250-120:
1 Электродвигатель тип М ТВ4 11-6-С:
2 Редуктор тип ЦОМ-30-I-64
передаточное число 6
Технические требования
*Размеры для справок.
Подшипниковые камеры заполнить смозкой УСс (солидол
синтетический) ГОСТ 4366-76.
Все нерабочие поверхности должны быть загрунтованы
грунтовкой ФЛ-03к ГОСТ 9109-93 и окрашены эмалью ПФ-115
ППР 1.doc
Трудоемкость одного ремонта
Трудоемкость на один год
Общая в год проведения Кр
Трайбаппарат выталкивателя заготовок
Таблица 4.4 Периодичность продолжительность и трудоемкость ремонта трайбаппарата выталкивателя заготовок
1 Общая часть.doc
История рождения и развития Криворожского металлургического комбината "Криворожсталь" - это история поэтапного строительства ввода в эксплуатацию и освоения сверхмощных доменных печей сталеплавильных агрегатов прокатных станов разработки и создания уникальных технических средств и технологических процессов.
июня 1931 г. - председателем ВСНХ Г.К. Орджоникидзе подписывается приказ о строительстве Криворожского металлургического завода.
ноября 1931 г. - заложены первые кубометры бетона в фундамент первого промышленного объекта - доменной печи № 1.
августа 1934 г. – задута первая доменная печь ("Комсомолка") с комплексом энергетического и ремонтно-вспомогательного хозяйства.
августа 1934 г. - выдан первый чугун на доменной печи "Комсомолка". Этот день принято считать датой рождения "Криворожстали".
Май 1935 г. - задута доменная печь № 2.
Январь 1936 г. - получен первый криворожский кокс.
Март 1939 г. - задута доменная печь № 3
Август 1939 г. - с вводом в эксплуатацию бессемеровского цеха выплавлены первые тонны криворожской стали.
В 1941 г. должно было завершиться строительство мощнейшего на на тот период блюминга производилось опробование отдельны механизмов этого стана.
В августе 1941 г. оборудование предприятия было частично демонтировано и эвакуировано в г. Нижний Тагил на Урале.
Послевоенная история комбината фактически связана с его вторым рождением и непрерывным ростом. Первая доменная печь была восстановлена в марте 1949 г.
В январе 1950 г. выдала чугун вторая доменная печь а сентябре 1951 г. - третья. Начали производить продукцию аглофабрика кузнечный ремонтно-механический и другие цехи.
56г. - ввод в эксплуатацию первенца прокатного передела на предприятии - непрерывного мелкосортного стана "250-1" оборудование которого как и остальных 9 прокатных станов было изготовлено и поставлено фирмой СКЭТ из Германии.
57г - ввод в эксплуатацию проволочного стана "250-1"и наследника довоенного бессемеровского цеха - кислородно-конвертерного цеха №1.
58г.- ввод в эксплуатацию доменной печи № 4 и цеха"Блюминг-1" в составе блюминга "1150" с отделением нагревательных колодцев и непрерывно-заготовочным станом "730500".
58г. - сдан в эксплуатацию Новокриворожский ГОК позднее вошедший в состав "Криворожстали".
59 г. - ввод в эксплуатацию непрерывного мелкосортного стана"250-2".
59 г. - приняты в работу доменная печь № 5 полезным объемом 2000 куб.метров и непрерывный проволочный стан "250-2".
61г. - введены в эксплуатацию доменная печь № 6 полезным объемом 2000 куб.метров мартеновский цех с пятью 650-тонными мартеновскими печами и непрерывный мелкосортный стан "250-3".
62г. - получен первый чугун на доменной печи № 7 полезным объемом 2000 куб.метров.
64 г. - начали работать цех "Блюминг-2" в составе блюминга "1300" с отделением нагревательных колодцев и непрерывно-заготовочным станом "900700500" а также непрерывный штрипсовый стан "300".
66г. - приняты в эксплуатацию непрерывные мелкосортные станы "250-4" и "250-5".
67г. - задута доменная печь № 8 полезным объемом 2700куб.метров.
70г. - принят в эксплуатацию непрерывный проволочный стан "250-3".
71г. - введен в работу комплекс кислородно-конвертерного цеха №2.
73г. - приняты в эксплуатацию двухванный сталеплавильный агрегат № 1 в мартеновском цехе (взамен мартеновской печи № 1) а также цех "Блюминг-3" в составе блюминга "1150" с отделением нагревательных колодцев и непрерывно-заготовочным станом "850700500".
74г. - задута доменная печь № 9 полезным объемом 5000 куб.метров.
77 г. - введены в эксплуатацию двухванный сталеплавильный агрегат № 6 в мартеновском цехе и комплекс непрерывного мелкосортною стана "250-6".
83 г. - завод получил статус комбината.
96 г. - на основе металлургического комбината "Криворожсталь" коксохимического завода и Новокриворожского горно-обогатительного комбината создан Криворожский государственный горнометаллургический комбинат "Криворожсталь".
96г. - после реконструкции введен в эксплуатацию проволочный стан "150-1"в СПЦ №1 производящий катанку отвечающую требованиям международных стандартов.
97г. - введен в эксплуатацию мелкосортно-проволочный стан МС-250150 в прокатном цехе № 3.
01 г.- в состав комбината входит Шахтоуправление созданное на основе бывших подразделений шахтоуправления им. «Кирова».
03 г.- после ремонта первого разряда вступила в строй крупнейшая в Европе доменная печь № 9.
июнь 2004 г. – КГГМК «Криворожсталь» преобразовывается в Открытое Акционерное Общество.
ноябрь 2005 г. – «Криворожсталь» входит в состав «Mittel Steel».
В настоящее время комбинат «Криворожсталь» является флагманом украинской металлургии. На «Криворожстали» за последние годы весомо выросли производство прибыль и рентабельность заработная плата полным ходом идет обновление оборудования и основных фондов (капитальный ремонт с техперевооружением девятой и восьмой доменных печей; капитальный ремонт конвертеров №5 и №6 и т.д.) приобретается новая техника внедряются передовые технологии. За счет этого снижается себестоимость продукции уменьшается расход сырья и топлива на тонну чугуна стали проката экономится газ кокс электроэнергия другие ресурсы стоимость которых постоянно растет.
В 2004 году на капитальное строительство и техперевооружение на комбинате израсходовали 11 млрд. грн. в том числе на обновление производства – 4925 млн. грн. ремонтный фонд – 602 млн. грн.
В 2005 году – производство товарного проката на составило 63 млн. тонн рентабельность – плюс 1693% и чистая прибыль – более 1 млрд. грн. Из нее планируется направить на развитие предприятия 548 млн. грн.
Планируется увеличение производства длинномерного проката в течение 25-3 лет начать производство листового проката. Строительство непрерывной разливки заготовки стали.
Все вышесказанное а также большая работа по улучшению качества продукции постоянное совершенствование системы качества действующей на предприятии согласно международным стандартам ISO 9001-2000 и ISO 9004-2000 позволяет успешно продавать металлопрокат на внутреннем и внешнем рынках: в 2004-05г. Его экспортируют в более чем 80 стран мира покупают все метизные предприятия и многие строительные организации Украины.
Структуру комбината «Криворожсталь» можно представить в виде таблицы (рис. 1.1) на которой изображены все этапы производства продукции от получения исходного сырья до конечной продукции.
В целом же структура комбината состоит из следующих подразделений:
-Горно-обогатительный комплекс;
-Аглодоменное производство;
-Сталеплавильное производство;
-Прокатное производство;
Шахтоуправление представлено:
-шахтой им. Артема №1;
Горно-обогатительный комплекс представлен:
-дробильными фабриками;
-обогатительными фабриками;
Аглодоменное производство представлено:
-агломерационным цехом
-шлакоперерабатывающим цехом
Исходным сырьем для производства агломерата служит концентрат ГОКа аглоруда шахтоуправления и основная часть - утилизированные отходы производства: шламы шлаки отсевы колошниковая и известковая пыль и др. Полученный агломерат поступает в доменный цех №1 комбината.
В состав цеха входят 5 доменных печей №1 5 6 7 8 с суммарным полезным объемом 10419 м3 а также бункерная эстакада отделение приготовления огнеупорных масс и смесей участок десульфурации чугуна.
Сырьем для производства чугуна служит: агломерат агломерационного цеха и ГОКа окатыши Сев-ГОКа и ЦГОКа железная руда шахтоуправления скрап. В качестве топлива используется кокс коксохимического производства природный газ и антрацит.
В составе цеха - крупнейшая в Украине доменная печь №9 объемом 5000 м3. Это по сути агрегат нового типа вобравший в себя последние достижения технической мысли.
Темпом загрузки управляет вычислительный комплекс. В составе цеха участок разливочных машин.
Печь оснащена двумя установками придоменной грануляции шлака что обеспечивает полную его переработку.
Шлакоперерабатывающий цех
Основные задачи цеха - переработка огненно-жидкого шлака доменного цеха №1 и обеспечение этого цеха составами шлаковозов а также извлечение скрапа из шлаков текущего производства. В цехе производится:
-шлаковая вата и пемза;
-песчано-щебеночная смесь.
Сталеплавильное производство комбината - это шесть самостоятельных цехов основная деятельность которых направлена на выпуск стали соответствующей мировым стандартам. В состав производства входят:
-кислородно-конвертерный цех;
-цех подготовки составов:
-огнеупорно-известковый цех:
-цех ремонта металлургических печей
Кислородно-конвертерный цех
Оснащен шестью конвертерами емкостью 160 тонн. Продувка металла в конвертере кислородом осуществляется сверху. Для повышения стойкости конвертеров широко применяются горячие ремонты футеровки: торкретирование и азотирование. Монолитная футеровка сталеразливочных ковшей выполняется машинами "Орбита".
В составе цеха двухванный сталеплавильный агрегат №6 и мартеновская печь №4. Выплавка стали производится путем интенсификации процесса кислородом подаваемым через сводовые фурмы. На двухванном агрегате внедрены желоба специальной конструкции для отсечки печного шлака освоен непрерывный контроль температуры металла. Система автоматического контроля и регистрации положения шиберов с цифровой индикацией двухкомпонентные весодозирующие бункера для выдачи ферросплавов в сталеразливочный ковш при сливе стали обеспечивают высокую производительность агрегатов повышают культуру производства.
Цех подготовки составов.
В цехе два отделения подготовки составов которые обслуживают мартеновский и конвертерный цехи. Отделения производят наборку составов под разливку стали сверху и сифонным способом а два отделения по раздеванию слитков обеспечивают обжимные цехи стальными слитками с высокой температурой прибытия. При непосредственном участии работников цеха решен ряд важных вопросов связанных с механизацией увеличением сроков службы кранового оборудования внедрены новые технологии:
- машина набивки прибыльных надставок для подготовки изложниц под разливку спокойных марок стали:
- механизирована выбивка прибыльных надставок.
Предназначен для разделки стального негабаритного и чугунного скрапа и лома. Цех расположен на двух участках: на 1-м размещены шлаковые отделения отделение огневой резки и копровое отделение №1; на 2-м - копровое отделение №2. В отделении огневой резки производится прием негабаритного лома переработка его газовой резкой и отправка сталеплавильным цехам. 6 шлаковых отделениях из шлаков сталеплавильных цехов извлекаются крупногабаритные куски металла и отправляются на переработку в копровые отделения. В отделении механической разделки установлены два гидравлических пакетирующих пресса усилием 1600 тонно-сил модели Б 1642 и БД 1642. производящие пакеты из металлолома поступающего в отделение.
Огнеупорно-известковый цех
Состоит из отделений:
-по производству извести;
-по производству огнеупоров и торкретмассы.
Производимой известью цех обеспечивает сталеплавильные цехи и аглофабрику. Процесс производства извести постоянно совершенствуется. С этой целью за вращающимися печами установлены новые высокоэффективные охладители извести а перед вращающейся печью N9 2 -подогреватель известняка который позволяет значительно сократить расход топлива. Торкретмасса производимая в цехе широко применяется для торкретирования конвертеров повышая их стойкость до 1000 плавок.
Цех ремонта металлургических печей
Основная функция цеха - ремонт мартеновских печей конвертеров миксеров методических печей прокатных станов кольцевой и вращающихся печей ОИЦ. За годы существования цеха ручные трудоемкие работы заменены на механизированные способы ведения ремонтов. В цехе также производятся торкрет-порошки и массы которые применяются при ремонтных работах и технологических процессах во многих цехах комбината. Применение технологии торкретирования повысило стойкость огнеупорной кладки металлургических агрегатов увеличив количество плавок на 10%.
Прокатное производство.
Для производства высококачественного проката комбинат располагает мощными современными автоматизированными станами специальными агрегатами и оборудованием для термической обработки и осуществления отделочных операций В состав прокатного производства входят:
Сортопрокатный цех №1.
Сортопрокатный цех №2.
Комбинат производит прокат по отечественным и зарубежным стандартам. Качество продукции прокатного производства отвечает требованиям международного стандарта ИСО 9001-2000.
В цехе установлены рекуперативные нагревательные колодцы стан 1250 и непрерывно-заготовочный стан 730500. Цех прокатывает слитки массой 85 т в квадратную заготовку сечением 125x125 мм и 80x80 мм которая затем передается для дальнейшего переката на мелкосортные и проволочные станы и отгружается товарной продукцией. В цехе осуществляется огневая зачистка блюмов в потоке что обеспечивает высокое качество продукции.
Нагрев слитков осуществляется в рекуперативных нагревательных колодцах а прокатка на обжимном стане 1350 и непрерывно-заготовочном стане 900700500. Цех прокатывает слитки массой 85 т в квадратную заготовку сечением 80x80 мм и 150x150 мм которая отгружается товарной продукцией и передается для переката на станы сортопрокатных цехов.
Сортопрокатный цех №1
В составе сортопрокатного цеха №1 три мелкосортных и один проволочный стан. Сортамент выпускаемой продукции: горячекатаная и термически упрочненная арматурная сталь диаметром от 10 до 14 мм круглые профили диаметром 10-14 мм угловая полосовая и квадратная сталь а также катанка диаметром 55 – 65 мм Продукция мелкосортных станов выпускается в прутках длиной 12 м а проволочных - бунтах до 1700кг.
Сортопрокатный цех №2
В его составе два мелкосортных стана и проволочный стан. Мелкосортные станы 250-4 5 выпускают круглую и арматурную сталь диаметром 14-32 мм квадратную сталь со стороной 16-22 мм шестигранную сталь 17-27 мм круглую сталь 14-28 мм. катанку диаметром 65 и 8 мм круглую арматурную сталь диаметром 6 и 8 мм. Готовая продукция мелкосортных станов выпускается в прутках длиной 12 м а проволочного - в бунтах массой 550 кг.
В состав цеха входит мелкосортно-проволочный стан 250150 производящий сортовой прокат диаметром 14-32 мм и катанку диаметром 55-18 мм в соответствии с мировыми стандартами е бунтах массой до 21 т.
Цех оснащен современными станками для калибровки прокатных валков ремонта подшипников жидкостного трения. В цехе производится ремонт прокатных валков методом микроплазменного напыления.
Сортамент продукции выпускаемой КГМК «Криворожсталь» приведен в таблице 1.1.
2 Характеристика цеха СПЦ-2 МС-250-5. Структура цеха применяемое оборудование и его характеристики
Мелкосортные станы предназначены для прокатки углеродистой стали: круглой квадратной шестигранной полосовой угловой а также других профилей эквивалентного сечения.
Эксплуатирующиеся на предприятиях отрасли мелкосортные станы характеризуются различным расположением рабочих клетей: линейным последовательным полу-непрерывным и непрерывным.
Современные мелкосортные станы являются непрерывными т.е. прокатываемый металл находится одновременно в нескольких рабочих клетях. Число клетей непрерывного стана равно требуемому числу проходов для получения из данной заготовки профиля предусмотренного сортаментом.
Сталь прокатывают из заготовки сечением 60х60 80х80 120х120 и 150х150 мм длиной 12 м и массой соответственно от 350 до2200 кг.
Готовый прокат выпускают в бунтах или прутках.
В бунты сматывают круглую квадратную шестигранную сталь диаметром по кругу от 8 до 25 мм а также полосовую сталь шириной до 70мм толщиной до 8 мм. Все остальные профили а в случае необходимости и перечисленные выше пропускают через холодильник после чего режут на мерные длины ножницами холодной резки.
На непрерывных станах в черновой группе клетей прокатку ведут одновременно в две нитки. Максимальная скорость прокатки в последней чистовой клети составляет 14 мс.
Характерной особенностью рассматриваемого оборудования непрерывного мелкосортного стана является широкое применение индивидуальных приводов и наличие вертикальных клетей.
Типовая схема расположения и состав оборудования непрерывного-· мелкосортного стана приведена на рисунке 1.2.
Рисунок 1.2 Схема расположения и состав оборудования МС-250-5
Поступающие на стан заготовки должны по геометрическим размерам химическому составу и состоянию поверхности соответствовать требованиям технических условий или ГОСТ. В случае необходимости производится их зачистка и правка. Подготовленные заготовки электромагнитным краном 1 подаются пачками на загрузочные устройства 2 с которых они передаются по одной на подводящий рольганг 3. По подводящему рольгангу заготовки транспортируются к втаскивателю 4 задающему их в печь. С противоположной стороны печи заготовки останавливаются стационарным упором 6. С торцевой стороны печи расположен толкатель 5 служащий для перемещения заготовок по поду печи. При подаче очередной холодной заготовки в печь нагретая заготовка передвигается до выталкивателя 7 которым она выталкивается из печи. Далее заготовка захватывается вытаскивателем 8 и направляется распределительным устройством по желобам либо в левую либо в правую нитку стана (при прокатке в две нитки). Перед первой клетью установлены ножницы 9 служащие для обрезки концов и деления заготовок на части. После прохождения заготовки через черновую группу клетей 10 поток прокатываемого металла направляется в левую и правую чистовые группы.
Чистовые группы 12 состоят из клетей с вертикальными и горизонтальными валками. Между черновой и чистовыми группами клетей установлены ротационные кривошипные ножницы 11. При нормальном процессе прокатки на этих ножницах обрезается только передний конец прокатываемого металла в каждой нитке. В случае нарушения нормального процесса прокатки когда возникает необходимость прекратить подачу металла в чистовые клети меняют режимы работы ножниц и они начинают работать непрерывно как аварийные и делят поступающий металл на куски длиной до 2000 мм.
По выходе из последних чистовых клетей прокатанный металл предназначенный для выпуска в прутках направляется главной стрелкой на холодильник а прокат предназначенный для выпуска в бунтах – к моталкам.
В первом случае прокатанный металл поступает к однобарабанным ножницам 14 где на ходу автоматически разрезается на мерные длины. В связи с тем что прокатка ведется двумя параллельными потоками холодильник 23 запроектирован сдвоенным с независимыми приводами. Перемещаясь при помощи реечных систем по холодильнику металл остывает.
Далее отводящим рольгангом металл транспортируется к ножницам холодной резки 24 где и разрезается на заданные длины. Пачки готовой продукции транспортируют погрузочными рольгангами 25 к карманам и сбрасывают в них специальным сбрасывателем. Из карманов кранами с поворотной тележкой 27 металл укладывают в штабели или подают на сортировку. Искривленный прокатанный металл правят на сортоправильных машинах 26.
Круглый квадратный и шестигранный прокат предназначенный для сматывания в бунты при помощи вспомогательной стрелки направляется к проволочным моталкам 13. Моталки работают поочередно. Бунт по окончании намотки подается сталкивающим устройством на ленточный транспортер за моталками и дальше к бунтовязальным машинам 16. Увязанный бунт подается под отводящее устройство которое направляет его на пластинчатый транспортер 17. Передвигаясь по транспортеру бунт подается на бунтопередаточное устройство 18 и далее навешивается на крюк канатного конвейера 21 где охлаждается и передается к бунтосъемному устройству 20 посредством которого бунт снимается с крюка конвейера и надевается на палец пакетирующей машины 19. С пакетирующей машины бунты снимаются краном 22.
Полоса предназначенная для сматывания в бунты при помощи вспомогательной стрелки направляется к ленточным моталкам 15.
Намотанный бунт при помощи отводящего устройства поступает на пластинчатый транспортер за моталками. С этого момента бунт полосы подвергается тем же операциям и в той же последовательности что и проволочный.
В настоящее время на мелкосортных станах применяется бесконечная прокатка т. е. со сваркой переднего конца подаваемой заготовки с задним концом впереди идущей заготовки. Скорость прокатки при этом может быть повышена до 20 мс.
2.1 Техническая характеристика механического оборудования цеха
Техническая характеристика механического оборудования цеха приведена в таблицах 1.3 и 1.4.
Таблица 1.3 Грохота питателей
Электромеха-нический
Таблица 1.4 Бункерные весы
Электротензометрические
Наибольший предел взвешивания т
Циферблатный автоматический электронный компенсатор
Класс точности весов по ГОСТ 13712-68
Цена деления указательного прибора
Фундамент.cdw

трайбаппарата выталкивателя заготовок
Место установки плашки вспомагательной оси
Репер вспомагательный
Место установки плашки главной оси выталкивателя
Схема фундамента трайбаппарата выталкивателя заготовок
ППР 3.doc
выталкивателя заготовок
Таблица 4.6 Месячный график планового ремонта трайбаппарата выталкивателя заготовок
Виды ремонтов: Т1 - текущий; Т2 – текущий.
4.doc
1 Расчет фундамента или другого основания для монтажа оборудования. Геодезическая привязка его
Предлагаемый в настоящем проекте трайбаппарат выталкивателя устанавливается на существующей площадке СПЦ-2 МС-250-5 где уже существует бетонное основание (пол). Трайбаппарат и привод монтируются на собственные рамы рамы устанавливаются на фундамент.составных частей трайбаппарата не превышает величину 100 кН и отношение длины сборочных единиц l к высоте их сечения h не превышает значения lh= 8 то согласно рекомендациям СНиП 11-19-79 принимаем установку частей выталкивателя на утолщенную бетонную ленту устраиваемую на отметке пола двора СПЦ-2.
Высоту бетонной ленты принимаем согласно того же СНиП 11-19-79 равным 015 (4.1)
где l - длина фундамента на 05 м больше длины оборудования м.
Фундамент трайбаппарата состоит из двух отдельных частей (см. рис. 4.1 и вид А рис. 4.2):
Рисунок 4.1 Схема фундамента трайбаппарата выталкивателя
Рисунок 4.2 Схема фундамента трайбаппарата выталкивателя
для трайбаппарата с рамой (4.2)
для привода с рамой l = 128 + 05 = 178 м.
Высота бетонной ленты составит:
для трайбаппарата с рамой h = 015·= 02 м = 200 мм;
для привода с рамой h = 015·= 035 м = 350 мм.
Для крепления конвейера к полу предусматриваем установку фундаментных болтов. Это необходимо в таких случаях:
- по условиям техники безопасности;
- для обеспечения совместной работы станины с фундаментом;
- при динамических нагрузках от возвратно-поступательного перемещения частей машины.
Фундаментные болты также предотвращают от случайного смещения машины.
Подбор сечения болтов производится по прочности из условия нераскрытия стыка в системе "фундамент-оборудование" и проверяется на выносливость усталостному разрушению.
Определим необходимую площадь сечения болтов по формуле:
F – расчетная нагрузка Н;
Rв = 110 Нмм2 - расчетное сопротивление растяжению фундаментных болтов для стали ВСт 3;
Для трайбаппарата с рамой:
где F = 24823 Н – масса выталкивателя с рамой.
Aрасч = = 17376 мм2.
Согласно таблицы расчетных площадей поперечного сечения фундаментных болтов (ГОСТ 24379.0-80) принимаем диаметр болта М30 с такими характеристиками:
- Номинальный диаметр резьбы болта – 30 мм;
- Расчетная площадь поперечного сечения – 5187 мм2;
Тогда количество болтов необходимых для крепления:
Окончательно принимаем n = 4 шт.
А = 4·5187 = 20748 мм2 > Арасч = 17376 мм2. (4.5)
Для привода с рамой:
где F = 9040 Н – масса привода с рамой.
x = 5 – коэффициент учитывающий внешние нагрузки согласно СНиП 2.09.03-85
Согласно таблицы расчетных площадей поперечного сечения фундаментных болтов (ГОСТ 24379.0-80) принимаем диаметр болта М24 с такими характеристиками:
- Номинальный диаметр резьбы болта – 24 мм;
- Расчетная площадь поперечного сечения – 4129 мм2;
Окончательно по конструктивной необходимости принимаем n = 7 шт.
А = 7·4129 = 28903 мм2 > Арасч = 452 мм2.
Глубину заделки фундаментных болтов принимаем согласно
СНиП 2.09.03-85: для болта d =12 48 мм глубина заделки
где d – диаметр болта мм;
для трайбаппарата с рамой: h = 20·30 = 600 мм;
для привода с рамой: h = 20·24 = 480 мм.
Главной осью относительно которой производится привязка и монтаж трайбаппарата с приводом являются ось окна печи для выталкивания заготовок (ось выталкивателя).
При расположении монтажных осей учитывается удобство установки машины в проектное положение а также возможность использования этих осей для контроля положения технологического оборудования в процессе его эксплуатации.
2 Геодезическое обоснование монтажа машины
Геодезическое обоснование монтажа (см. рис. 4.3). Высотное положение фундаментов определяют нивелированием от реперов находящихся в близи сооружения или от реперов заложенных под оборудование.
Плановое положение рабочих монтажных осей фиксируют теодолитом на заделанных в бетонный массив знаках в арматуры кованые гвозди металлические скобы разных форм и др. Знаки сохраняются до окончания монтажных работ и их приемки. С помощью знаков устанавливают выталкиватель в проектное положение и контролируют возможные горизонтальные и вертикальные смещения фундаментов.
Одним из важнейших видов подготовки фундаментов к монтажу оборудования является установка анкерных болтов в проектное положение. Высокая прочность их установки обеспечивается специальными кондукторами изготовленными из профильной стали. Кондуктор устанавливают по рабочим монтажным осям на заданной проектом высоте. Анкерные болты вставляют в отверстия и подвешивают на гайках. Вертикальность болтов обеспечивается с помощью приваренных металлических распорок. До бетонирования фундамента составляют исполнительную схему на которой показывают плановые и высотные отклонения от проектного положения.
Привязка осей выталкивателя осуществляется относительно оси окна печи поперечная привязка осуществляется относительно колон цеха.
3 Способы доставки оборудования к месту монтажа
Выталкиватель заготовок состоит из отдельных узлов которые можно легко разобрать:
- стойки кронштейны;
- приводной и прижимной ролики тяги стяжки;
- электродвигатель редуктор;
- рама выталкивателя и рама привода.
Транспортировку выталкивателя наиболее целесообразно выполнять по узлам в разобранном виде с последующей сборкой на месте установки машины или со сборкой на ремонтных площадках с последующей транспортировкой готовых узлов транспортировка выполняется мостовым краном цеха.
При этом используют типовую такелажную оснастку (стропы) которые подбирают в зависимости от габаритов и веса перемещаемых компонентов. Этот выбор производят согласно требованиям стандарта предприятия СОУ 214-Т-028-2004 который распространяется на грузовые канатные и цепные стропы. Для подъема и перемещения трайбаппарата и привода используются стропы типа 4СК1 или 4СК2 (см. рис. 4.4) с диаметром стального каната – 36 мм и его длиной не менее 35 м. При этом должно выполнятся условие чтобы угол между ветвями стропов в любой плоскости не превышал 90о.
Рисунок 4.4 Строп типа 4СК
4 Технологическая карта монтажа выталкивателя заготовок
Выталкиватель является связующим звеном между .
Устанавливается выталкиватель посекционно: рама выталкиватель и рама привода а затем выталкиватель и элементы привода (электродвигатель редуктор).
- График производства работ по монтажу (см. таблица 4.1);
- Перечень монтажного оборудования инвентаря и приспособлений таблица 4.2.
Ключи S= 12х14; 17х19; 19х22; 32х36; 41х46; 46х50
Трехзахватный съемник
Контроль точности установки трайбаппарата выталкивателя.
Монтаж рам трайбаппарата и привода осуществляется последовательно одна за другой. Контроль и расположение рам по высоте и в горизонтальной плоскости осуществляется нивелиром плоскостность отдельных поверхностей контролируется уровнем. После выверки секции рамы крепятся к фундаментным болтам.
Положение стоек трайбаппарата в плане относительно вертикальной оси проверяют с помощью струны и отвеса. При выверке стоек относительно поперечной оси за базу принимают ось окна печи.
Положение роликов трайбаппарата установленных в корпуса подшипников стоек по горизонтали контролируют с помощью уровня который укладывается на бочку ролика а также нивелиром принимая за базу низ наружного диаметра приводного ролика. Контроль установки подшипников осуществляется с помощью щупа которым определяют величину необходимого зазора и наличие перекосов. После выверки роликов стойки окончательно крепятся к раме. После затяжки крепежных болтов стоек ролики выталкивателя должны легко вращаться.
Редуктор устанавливается на раму с пакетом подкладок. Положение редуктора в плане относительно оси ролика проверяют с помощью струны уровня и отвеса. При выверке относительно поперечной оси за базу принимают оси стоек используя нивелир. Положение редуктора по высоте контролируют с помощью нивелира принимая за базу ось приводного ролика. Соединение тихоходного вала редуктора с хвостовиком приводного ролика осуществляется посредством зубчатой муфты компенсирующей незначительные перекосы. После соединения редуктора с приводным роликом вращение ролика должно быть плавным без заеданий.
Электродвигатель устанавливается на раму с пакетом подкладок. Точность установки проверяют с помощью уровня используя регулировочные прокладки. Соединение с редуктором осуществляется при помощи упруго - втулочной пальцевой муфты. Радиальное биение вала электродвигателя и вала редуктора контролируют измерительной головкой.
Тормоз устанавливается аналогично электродвигателю только за базу принимается ось вала электродвигателя. Точность установки тормоза проверяется вращением вала двигателя. С разведенными колодками тормоза вращение вала электродвигателя должно быть без заеданий со сведенными колодками вращение – отсутствует.
5 Эксплуатация машины
5.1 Условия работы проектируемого оборудования
Выталкиватель смонтирован в цехе СПЦ-2 и технологически связан с работой основного оборудования стана МС-250-5. Режим работы выталкивателя непрерывный реверсивный с остановками на проведение профилактических осмотров в течение смены.
Гарантийный срок службы трайбаппарата выталкивателя модернизация которого является темой дипломного проекта составляет 10 лет (при условии нормальной эксплуатации). Реальная загрузка в течении года составляет около 7000 час. В течении суток загрузка выталкивателя а соответственно и трайбаппарата составляет 20-22 часов. Он работает в трехсменном режиме между сменами производятся остановки на профилактическое обслуживание.
Наиболее ответственные детали подвергаются воздействию динамических нагрузок (момент прижима и передачи движения штоку выталкивателя с заготовкой). Оценка факторов производственной сферы:
Вредные химические вещества:
нормативное значение 10 мгм
фактическое значение 1.1 мгм
нормативное значение 20 мгм
фактическое значение 5 мгм
Запылённость окружающей среды составляет около 20-30гм3 основным компонентом пыли являются окислы железа (окалина).
Продолжительность действия фактора - 89 % времени за смену.
нормативное значение 80 дБЛ
фактическое значение 78 дБЛ.
Вибрация (общая и локальная)
нормативное значение 101
фактическое значение 85.
Микроклимат в помещении
а) температура воздуха С
нормативное значение 20
фактическое значение 11
б) скорость движения воздуха мс
нормативное значение 02
фактическое значение 01
в) относительная влажность
нормативное значение 75%
фактическое значение 35%
Продолжительность действия факторов - 89 % времени за смену.
5.2 Характер износа наиболее ответственных деталей проектируемого оборудования в процессе эксплуатации
В процессе работы трайбаппарата являющегося частью комплекса оборудования выталкивателя установленных в одну линию связанных между собой его отдельные части получают характерный износ. Отметим наиболее ответственные детали трайбаппарата и характер их износа и представим их в виде таблицы 4.3.
Наименование детали узла
Рабочая поверхность роликов
Выработка рабочей поверхности ролика вследствии истирания механические повреждения от воздействия внешних нагрузок
Подшипниковые опоры роликов
Износ подшипников вследствии нарушения подачи смазки
Износ зубьев муфты вследствии больших нагрузок
Металлоконструкции трайбаппарата
Механические повреждения от воздействия внешних нагрузок коррозионный износ
Выработка посадочных мест. Большие динамические нагрузки неточность сборки.
Сроки службы отдельных узлов трайбаппарата:
- ролики от 2 до 3 лет;
- редуктор до 10 лет;
- подшипники 15 до 2 лет;
- тяги кронштейны - 35 года;
- электродвигатель – до 25 лет.
5.3 Анализ мероприятий по техническому обслуживанию выталкивателя в целях поддержания его работоспособности
В целях поддержания работоспособности выталкивателя предлагается проводить ряд технических и организационных мероприятий.
Техническое обслуживание выталкивателя заключается в регулярном наблюдении за работой его составных частей и механизмов периодическом пополнении и смазки трущихся частей в ремонте отдельных узлов и трайбаппарата в целом.
При текущем обслуживании в течении смены эксплуатационный и ремонтный персонал обязан:
- содержать оборудование и рабочие места в чистоте;
- контролировать поступление смазочных материалов к узлам трения механизмов оборудованных централизованными системами густой и жидкой смазки;
- следить за непрерывным поступлением воды для охлаждения механизмов;
- проверять исправность трубопроводов и аппаратуры магистралей воды сжатого воздуха и смазки;
- проверять нет ли утечки масла из зубчатой муфты редуктора и применять меры к их устранению;
- проверять крепление крышек подшипников. Редуктора корпусов механизмов рычагов а также других деталей и узлов а при необходимости закрепить их;
- проводить уход и надзор за подшипниками муфтами редуктором резьбовыми и шпоночными соединениями;
- проверять действие конечных выключателей тормозного устройства и системы сигнализации.
Эксплуатационный персонал обязан выполнять ремонтные работы по устранению неисправностей появляющихся при работе обслуживания им оборудования для чего он должен пройти специальное обучение второй профессии (слесарь по ремонту оборудования) и иметь необходимый инструмент.
При внезапном возникновении аварийной ситуации в результате которой возможен вывод из строя оборудования или появляется опасность для жизни людей необходимо немедленно сообщить лицу управляющему агрегатом и руководству смены.
В случае обнаружения неисправностей поломок и др. оператор должен немедленно сообщить об этом своему непосредственному начальнику и сделать соответствующую запись в журнале приема-передачи смены. Приказом по цеху за выталкивателем заготовок закрепляется инженерно - технический работник (мастер по ремонту механического оборудования СПЦ-2) ответственный за техническое состояние выталкивателя и который осуществляет технический контроль за работой выталкивателя заготовок. Следит за выполнением вышеперечисленных пунктов обслуживающим персоналом графиком проведения ППР и др. Также в каждой бригаде назначается рабочий (оператор работающий на выталкивателе) ответственный за работу машины в обязанности которого входит поддержание его в работоспособном состоянии.
5.4 Предложения по совершенствованию организационного и технологического характера направленного на поддержание исправного состояния оборудования
В целях совершенствования мероприятий организационного и технологического характера направленных на поддержание в исправном состоянии выталкивателя заготовок предлагается:
- для всех работников (технологический ремонтный персонал) в обязательном порядке провести обучение в процессе которого ознакомить их с конструкцией выталкивателя заготовок принципам и приемам работы правилам техники безопасности;
- для работников занятых непосредственно обслуживанием и ремонтом выталкивателя проводить курсы повышения квалификации (изучение и практическое применение новинок отечественной и зарубежной промышленности в области смазки новейших методов ремонта);
- инженерно-техническим работникам ответственным за подготовку и проведение ремонта выталкивателя своевременно и в полном объеме выдавать заявки на изготовление и приобретение запасных частей. Особенно большое внимание уделить вопросам контроля изготовления запасных частей их приема и хранения. Имеется в виду следующее: нередки случаи изготовления запасных частей с отступлением от проектной документации (отклонение от проектных размеров отсутствует необходимая термообработка) а также допускаются неудовлетворительные условия их хранения в межремонтный период;
- для более полного контроля за работой трайбаппарата на участке его ремонта предлагается завести оперативный журнал в который ежедневно вносятся данные о его работе обнаруженных неполадках даты проведения технических и профилактических ремонтов с указанием наименования и количества замененных деталей и узлов.
- для увеличения гарантийного срока службы трайбаппарата а следовательно увеличения межремонтного периода и снижения затрат времени и средств на его ремонт необходимо: применять передовые технологии ремонта изготовление запасных частей из износоустойчивых материалов приобретение современных долговечных частей оборудования.
6 Ремонт оборудования
6.1 Выбор формы и метода проведения ремонтов выталкивателя
Процесс ремонта трайбаппарата выталкивателя заготовок должен быть организован таким образом чтобы обеспечить выполнение производственного плана с высоким качеством в срок и с минимальными затратами труда и материальных средств.
Ремонт оборудования в СПЦ-2 производится по графику это позволяет исключить аварии или случайный выход из строя оборудования.
Подготовка к ремонту начинается заблаговременно с определения объемов работ установления необходимого количества запасных частей.
Подготовка проводится в два этапа:
Мелкие детали простой конфигурации изготавливаются силами механической мастерской цеха. На изготовление наиболее сложной и узлов составляются заявки – заказы в управлении главного механика завода.
Составляется оперативный или сетевой графики ремонта в зависимости от сложности и объема работ. При составлении графиков необходимо предусматривать уменьшение трудоемкости и сроков ремонта путем применения узлового или агрегатного ремонта механизации и централизации всех работ.
Все это обуславливается скоротечными методами ремонтов оборудования. Периоды между текущими ремонтами устанавливаются исходя из регламентированных сроков службы изнашивающихся узлов и деталей. При этом принимается во внимание то что по истечении этих сроков дальнейшая эксплуатация оборудования привела бы к прогрессирующему износу и выходу из строя всего механизма.
Для составления графика текущего ремонта определяют объем работы по ремонтным ведомостям.
Объем и состав текущего ремонта определяется предельным состоянием деталей и узлов конвейера. Узел или деталь достигнувшие предельного состояния должны быть отремонтированы или заменены новыми.
Текущий ремонт конвейера производится ремонтными мастерскими оборудованными грузоподъемными средствами.
Персонал осуществляющий ремонт выталкивателя должен знать его конструкцию а так же правила безопасности изложенные в паспорте выталкивателя заготовок.
Для грамотного обслуживания оборудования необходимо прежде всего установить наиболее характерные причины вызывающие преждевременный выход из строя деталей и узлов и в целом механизмов:
- нарушение взаимного расположения деталей и узлов за счет ослабления шпоночных болтовых и других соединений;
- нарушение режима смазки несоответствие смазочных материалов отсутствие смазочных материалов или недостаток смазки;
- неправильное определение сроков службы узлов.
Междусменные остановки как правило предусматривают выполнение мероприятий по устранению перечисленных выше причин износа и поломок оборудования.
Основными мероприятиями по сокращению затрат на проведение ремонтных работ увеличение межремонтных периодов является:
- межцентрализация и механизация ремонтов металлургического оборудования;
-поузловой метод ремонта;
-термическая обработка деталей;
-повышение квалификации ремонтного персонала и приобретения ими смежных специальностей;
-производство капитальных ремонтов по рассредоточенному графику.
Применение поузлового метода ремонта позволит значительно сокращать время ремонта оборудования и использовать технологические паузы для ремонта агрегатов. На место снятых узлов устанавливаются отремонтированные узлы находящиеся в резерве.
Термическая обработка деталей удлиняет их срок службы более чем в 2 раза.
Время ремонтов можно сократить за счет качественного изменения ремонтного персонала т.е. за счет повышения его квалификации. Персонал осуществляющий ремонт трайбаппарата выталкивателя должен знать его конструкцию а так же правила безопасности изложенные в паспорте выталкивателя.
Профилактический текущий ремонт и межремонтное обслуживание осуществляется цеховой ремонтной службой а именно бригадой по ремонту оборудования стана МС-250-5 цеха СПЦ-2.
6.2 Разработка перспективного графика планово-предупредительных ремонтов машины на год
Нормативы периодичности продолжительности ремонтов а также их трудоемкость и структура ремонтного цикла приведена в таблице 4.4.
Основой для проведения ремонтов является годовой график планово-предупредительных ремонтов составляемый к началу планируемого года и охватывающий все виды ремонта машины который утверждается главным механиком и главным инженером комбината.
Основным фактором определяющим успешное проведение ремонта является тщательная подготовка к нему. Наиболее прогрессивной формой ремонта является агрегатный метод при котором ремонт производится с заменой заранее подготовленных узлов и механизмов.
Планы планово-предупредительных ремонтов оборудования оформляются в виде графика. Годовой график планово-предупредительных ремонтов (ППР) для проведения ремонтов выталкивателя заготовок стана МС-250-5 приведен в таблице 4.5.
Месячный график ППР составляется в цехе на основе годового графика. В месячный график могут быть включено оборудование проведение ремонтов которых не предусмотрено годовым графиком см. табл. 4.6.
Подготовка к ППР начинается с составления дефектной ведомости на ремонт. Ведомость составляется механиком цеха. Ремонтная ведомость является основанием для последней подготовки к проведению ремонта. Подготовка выдачи в производство заказов на изготовление необходимых деталей для ремонта обеспечение покупными изделиями - подшипниками качения метизами и др. составление сметы ремонта и присвоение номера заказа.
На основании ремонтных ведомостей механик цеха составляет сводный график ремонта оборудования цеха. На основании сводных ремонтных ведомостей суммируется общая потребность в материальном техническом снабжении ремонта а за неделю до начала ремонта она обсуждается на совещании у начальника цеха где производится увязка всех служб цеха механиков электриков технологов.
Следующий этап работы по подготовке работы является изготовление необходимых деталей узлов в ремонтно-механических цехах. Сокращение времени и затрат возможно при унификации деталей и узлов машины изготовление однотипных деталей по одному чертежу или в изготовлении из одинаковых заготовок что позволяет изготавливать детали из штамповок снижая затраты на механические обработки.
За три дня до остановки цеха на ремонт производится совещание руководителей отделов завода и начальников вспомогательных цехов обеспечивающих ремонт. После совещания издается приказ по заводу об остановке цеха на ремонт где указывается начальник ремонта. С этого времени утвержденный график ремонта является обязательным документом для использования.
При завершении подготовительных работ в срок предусмотренный планом выталкиватель заготовок останавливается на ремонт. Вывод машины в ремонт производится лицом ответственным за исправное состояние машины. На ремонт выдается наряд-допуск в котором указываются меры безопасности условий выполнения ремонтных работ.
После окончания ремонта готовность цеха или участка к работе и качество проведения ремонта принимается комиссией назначенной в приказе по заводу.
Для проведения ППР привлекаются следующие организации:
- цеховой ремонтный персонал;
- ремонтные цехи УГМ;
- энергоремонтный цех.
6.3 Описание методов восстановления наиболее часто изнашивающихся деталей
Существует два основных метода восстановления деталей металлургических машин с изменением первоначальных параметров (размеров) деталей и без изменения их.
К основным технологическим способам восстановления деталей трайбаппарата выталкивателя относятся следующие
- восстановление металлических деталей и узлов - сварочно-наплавочные (ручная электродуговая и газовая сварка и наплавка автоматическая и полуавтоматическая сварка и наплавка под слоем флюса в среде защитных газов и др.) металлизация гальванический способ (хромирование) химический (никелирование) пластическая деформация (холодная и горячая) покрытие полимерными материалами электроискровое наращивание.
При выборе способа восстановления следует руководствоваться в первую очередь величиной выбраковочного износа или характером повреждения детали а также ее твердостью конфигурацией размерами условиями работы и конкретными возможностями предприятия.
Восстановление полученных повреждений можно производить следующими способами
а) дефекты истирания – наплавкой металлизацией заменой части детали с последующей механической обработкой;
б) восстановление деталей имеющих коррозию производят механическим способом подвергая их пескоструйной обработке;
в) усталостные трещины – ручной электродуговой сваркой;
г) деформация деталей рамы – пластическая деформация холодная и горячая;
д) дефекты от перегрева (когда на деталях появляются цвета побежалости) – шлифовка до удаления цветов побежалости;
е) восстановление деталей имеющих нагар производят механическим способом растворителями выжиганием ультразвуком и др.
Сильному механическому износу вследствие трения подвержены ролики трайбаппарата при этом изменяется их геометрическая форма чистота поверхности. К восстановлению таких деталей можно применить такой способ как наплавка под флюсом (рис. 4.5 4.6). При этом в металле наплавленном под флюсом содержится меньше азота и кислорода и поэтому не содержит шлаковых включений и пор. С целью повышения производительности наплавкии применяют многоэлектродную наплавку а также наплавку пластинчатыми электродами или электродной лентой. Для получения требуемых свойств наплавленного металла необходимо вводить в него легирующие элементы.
Применяют многоэлектродную наплавку а также наплавку пластинчатыми электродами или электродной лентой. Для получения требуемых свойств наплавленного металла необходимо вводить в него легирующие элементы. После наплавки деталь подвергают механической обработке на станке до требуемых размеров а затем цементируют закаливают в печи и отпускают.
Рисунок 4.5 Схема наплавки изношенной поверхности под
- флюс 2 - электродная проволока
- шлаковая корка4 - наплавленный металл
- расплавленный металл 6 - деталь
- электрическая дуга.
Рисунок 4.6 Схема автоматической наплавки изношенной поверхности под слоем флюса:
- наплавляемая деталь; 2 - рамка для удержания флюса;
- оболочка из расплавленного флюса; 4 - электроды;
- газовый пузырь; 6 - наплавленный металл.
Кроме наплавки восстановление рабочих поверхностей валов осей и др. производится механической обработкой (метод ремонтных размеров). Сопрягаемые детали восстанавливают введением деталей-компенсаторов или изготовляют новые обеспечивая первоначальные (номинальные) посадки.
Ремонт посадочных поверхностей осуществляется путем наплавки изношенных участков с последующей их мехобработке до проектного размера или проточкой посадочной поверхности вала до ремонтного размера с одновременным изготовлением новых втулок под этот размер (рис. 4. 7).
Рисунок 4.7 Восстановление валов методом ремонтных размеров.
7 Смазка оборудования
7.1 Выбор системы смазки для узлов трайбаппарата выталкивателя заготовок и смазочные материалы
Оборудование прокатных цехов работает в тяжелом режиме поэтому для обеспечения его надежности работы на протяжении длительного времени необходима правильная организация смазочного хозяйства. Важным условием нормальной эксплуатации механизмов оборудования в течении всего межремонтного периода является строгое соблюдение периодичности смазочных работ и применение соответствующих смазочных материалов. Применением смазки решаются две основные задачи: сокращается расход энергии на преодоление сил трения в узлах оборудования и уменьшается износ трущихся поверхностей деталей. Последнее обстоятельство позволяет продлить
сроки службы оборудования без его ремонта.
Все оборудование мелкосортного стана МС-250-5 и в частности выталкиватель заготовок смазывается от централизованных систем жидкой смазки а также индивидуальных систем густой смазки.
Для всех узлов и механизмов трайбаппарата в которых присутствует трение устанавливаем индивидуальный способ смазки а именно:
- закрытые зубчатые передачи (редуктор) смазываются погружением в маслянную ванну;
- открытая зубчатая муфта смазывается путем нанесения на нее пластичного смазочного материала;
- подшипники качения находящиеся в роликоопорах ролика приводного – жидкосная смазка;
- подшипники качения находящиеся в роликоопорах ролика прижимного подшипников скольжения цапф пневмоцилиндра смазываются путем заполнения подшипниковых камер пластичным смазочным материалом.
Смазка подшипников роликоопор ролика прижимного подшипников скольжения цапф пневмоцилиндра трайбаппарата производится вручную с периодичностью 1 раз в 3 месяца масло ИП-1.
Смазка редуктора трайбаппарата картерная заливная – масло ТАП-15В периодичность проверки и заливки через 90 дней.
Муфта зубчатая - Пресс-солидол С периодичность проверки и смазки 1 раз в 3 месяца.
Смазка подшипников роликоопор ролика приводного – жидкосная. Смазка производится станцией жидкой смазки № 2. Система (рис. 4.8) состоит из резервуара (бака) 2 трех насосных установок 3 двух фильтров 4 пресс-бака 5 маслоохладителя 6 и фильтра грубой очистки который устанавливается па сливном трубопроводе. Производительность станций в зависимости от режима работы и числа обслуживаемых механизмов составляет 18 125 300 и 1200 лмин. Станции обслуживаются насосными установками типа РЗ-60 РЗ-ЗОИ ШДП-125 ШДП-18 и фильтрами типа ФДЖ-150 ФДЖ-80 Г41-43. Масла в основном применяются следующих сортов: П-28 АК-15 и турбинное 30.
Рисунок 4. 8 Система жидкой смазки:
7.2 Расчеты основных параметров системы смазки
Для подшипников качения ролика приводного применяется централизованная жидкая циркуляционная смазка.
В состав трайбаппарата выталкивателя входит - один редуктор ЦОМ-30-I-64 с емкостью ванны более 20 л.
Определим долив масла в редуктор за сутки
q = k·Q = 22·35 = 77 г. (4.7)
где k = 22 гл - для ванн вместимостью более 20 л;
Q = 35 л - вместимость ванны редуктора.
Определим расход смазки для подшипников ролика прижимного (№3618):
q = 75·10-4 ·d·b·n = 75·10-4·90·64·2 = 086 г; (4.8)
где d = 90 мм - внутренний диаметр подшипника;
b = 64 мм - ширина обоймы подшипника;
n = 2- кол-во подшипников.
Определяем годовой фонд рабочего времени работы конвейера
Ф = [ t·( 365 - В - С )]·n·k (4.9)
где t = 8 ч - продолжительность рабочей смены;
В = 105 - число выходных дней в году;
С = 8 - число праздников;
k = 085 - коэффициент использования механизма по времени.
Ф = [ 8·( 365 - 105 - 8 ) ]·3·085 = 51408 ч.
Определяем общегодовой расход смазочных материалов
а) для редуктора ( жидкая смазка )
Q = = 165 кг; (4.10)
где n = 365 - В - С = 365 - 105 - 8 = 252 сут - кол-во рабочих дней в году.
7.3 Разработка карты смазки узлов машины
С целью обеспечения нормальной работоспособности трущихся поверхностей снижения износа деталей и повышения срока их службы детали должны находится в постоянно смазанном состоянии соответствующими видами смазки.
Особо нужно подчеркнуть то что трущиеся детали должны смазыватся вовремя.
Для решения задач связаных с выщеуказанными требованиями создается карта смазки которая содержит полную информацию о проведении смазочных работ и включает в себя схему местонахождения точек смазки и информацию о мероприятиях по проведению смазочных работ см. табл. 4.7 4.8.
Составим карту смазки для трайбаппарата выталкивателя заготовок предварительно составив схему расположения точек смазки. см. рис. 4.9.
Рисунок 4.9 Точки смазки трайбаппарата выталкивателя заготовок
Таблица 4.7 Карта смазки
Указания по выполнению операций смазки
камеры ролика приводного
камеры ролика прижимного
Подшипники скольжения
Масла и смазки применяемые для смазывания узлов и механизмов трайбаппарата выталкивателя приведены в таблице 4.6.
Таблица 4.8 Масла и смазки для узлов и механизмов конвейера
Наименование марка масла смазки ГОСТ( ТУ )
Масло трансмиссионное ТАП-15В ГОСТ 23652-79
Пресс-солидол С ГОСТ 4366-76
П-28 АК-15 турбинное 30
ИП-1 ТУ 38.101820-80
ЛКС - металлургическая ТУ 38.401124-85