Технологический процесс обработки детали Корпус дросселя. НУТМ 752416.001




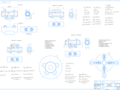
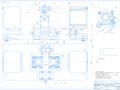
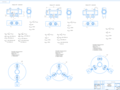
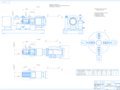
- Добавлен: 24.01.2023
- Размер: 3 MB
- Закачек: 1
Описание
Состав проекта
![]() |
![]() |
![]() ![]() ![]() |
![]() ![]() ![]() |
![]() ![]() ![]() |
![]() ![]() |
![]() |
![]() ![]() |
![]() ![]() |
![]() ![]() ![]() |
![]() ![]() ![]() |
![]() |
![]() ![]() |
![]() ![]() ![]() ![]() |
![]() |
![]() |
![]() |
![]() ![]() |
![]() ![]() ![]() ![]() |
![]() |
![]() ![]() ![]() ![]() |
![]() ![]() |
![]() |
![]() |
![]() ![]() ![]() |
![]() ![]() |
![]() ![]() ![]() ![]() |
![]() |
![]() ![]() ![]() |
![]() |
![]() |
![]() ![]() |
![]() ![]() |
![]() |
![]() ![]() ![]() ![]() |
![]() ![]() ![]() ![]() |
![]() |
![]() ![]() |
![]() ![]() |
![]() ![]() ![]() |
![]() ![]() ![]() |
Дополнительная информация
записка.docx
Служебное назначение .7
Отработка конструкции детали на технологичность 8
Выбор и технико-экономическое обоснование заготовки . . .. 11
Анализ технологического процесса 17
Маршрутный технологический процесс . . 26
Анализ точности механической обработки . 28
Расчет припусков и предельных размеров .. . . .. 30
Расчет режимов резания .. 40
Расчет норм времени .. . 43
Расчёт и конструирования станочного приспособления 45
Список литературы . .58
Приложение А спецификация к зажимному приспособлению 60
Приложение Б операционный техпроцесс ..63
Машиностроительная отрасль является основной технологической базой определяющей развитие всей промышленности любой страны. Поэтому темпы роста машиностроения должны значительно превышать аналогичные показатели других отраслей народного хозяйства. В настоящее время машиностроение как ни одна из других отраслей сильно отстает от научно-технического прогресса в связи со сложностью выпускаемого технологического оборудования. Поэтому в данный момент перед машиностроением стоит огромное число сложных и важных задач таких как: планирование и разработка перспективных технологий; создание высокопроизводительных энерго- и материалосберегающих технологий; повышение качества и технического уровня машиностроительной продукции; применение средств автоматизации и механизации производства.
Одной из основных задач машиностроения является производство корпусных деталей. К корпусным относят детали обеспечивающие взаимное расположение деталей узла и принятие основные силы действующей в машине. Корпусные детали обычно имеют довольно сложную форму поэтому их получают методом литья (в большинстве случаев) или методом сварки (при единичном и мелкосерийном производстве). Для изготовления корпусных деталей широко используют чугун сталь а при необходимости ограничения массы машин — легкие сплавы (алюминиевые магниевые).
В данной работе представлена разработка технологического процесса изготовления и обработки детали «Корпус».
Курсовое проектирование закрепляет углубляет и обобщает знания полученные во время лекционных или практических занятий учит пользоваться справочной литературой ГОСТами таблицами нормами умело сочетая справочные данные с теоретическими знаниями полученными в процессе изучения курса.
При выполнении проекта принятие решений по выбору вариантов технологических процессов оборудования оснастки методов получения заготовки производится на основании технико-экономических расчетов что дает возможность предложить оптимальный вариант.
В данном курсовом проекте произведен расчет припусков на заданную поверхность расчет режимов резания норм времени а также составлен маршрут обработки детали.
Определение типа производства.
Современное производство подразделяется на следующие типы: единичное серийное и массовое. От типа производства во многом зависит характер технологического процесса и его построение. Тип производства характеризуется количеством закрепленных операций за одним рабочим местом или за единицей оборудования. Тип производства зависит от 2 факторов: заданной программы и трудоемкости изготовления изделия.
Серийность определим по коэффициенту закрепления операций (ГОСТ 14.004-83)
- коэффициент серийности где
- суммарное число различных операций
-суммарное число рабочих мест.
Определим количество станков шт.
- действительный годовой фонд времени оборудования равный 3890 часов
шт. - годовая программа выпуска
Тшт - штучное или штучно-калькуляционное время на каждую операцию
з.н. =0.8 – нормативный коэффициент загрузки оборудования.
Использую справочник нормировщика найдем Тшт. для всех операций и занесем полученные данные в таблицу 1.
Таблица 1. Расчет коэффициента серийности.
Рассчитаем необходимое количество станков mр полученные данные занесем в таблицу 1.
Устанавливается принятое число рабочих мест или количество станков Р округляя до ближайшего целого числа полученные значения mp.
Для каждой операции вычисляется значение фактического коэффициента загрузки рабочего места:
Определяется количество операций выполняемых на рабочем месте:
Рассчитаем суммарные значения Р и О и рассчитаем коэффициент закрепления операций.
Так как соответствует массовому производству. Принимаем массовое производство.
Служебное назначение и конструкция детали.
Дроссельная заслонкаявляется конструктивным элементом впускной системы двигателей внутреннего сгорания с впрыском топлива и предназначена для регулирования количества воздуха поступающего в двигатель для образования топливно-воздушной смеси. Дроссельная заслонка устанавливается между воздушным фильтром и впускным коллектором.
В частности деталь «Корпус дросселя» входит в изделие «Дроссельная заслонка». В отверстие 60Н7 устанавливается пружинный возвратный механизм в два отверстия 44Н8 устанавливаются система управления пружинно возвратным механизмом. С отверстием 75 соединяется система подачи воздуха или жидкости. Это же отверстие с противоположной стороны соединяется система с системой приема воздуха или жидкости. Два отверстия 18Н15- являются установочными в них входят два болта с помощь которых «Дроссельная заслонка» крепиться к кузову. Все детали соединяются с корпусом посредствам резьбового соединения на плоскость разъема устанавливаются прокладки.
Отработка конструкции детали на технологичность.
Заготовка в базовом варианте техпроцесса выполняется ковкой. Материал детали сталь 45 исключает обработку металла давление литье в кокиль литье под давлением а также использование многих других высокопроизводительных методов литья. Учитывая то что базовая заготовка не имеет ни одного отверстия то заготовку считаем абсолютно не технологичной. Замена материала стали 45 на сталь 45Л с почти аналогичными свойствами (таблица 2) сможем получить высокопроизводительную заготовку литьем в оболочковые формы.
Таблица 2. Выбор материала.
Химический состав в % материала
Склонность к отпускной хрупкости:
вал-шестерни коленчатые и распределительные валы шестерни шпиндели бандажи цилиндры кулачки и другие нормализованные улучшаемые и подвергаемые поверхностной термообработке детали от которых требуется повышенная прочность.
станины зубчатые колеса и венцы тормозные диски муфты кожухи опорные катки звездочки и другие детали к которым предъявляются требования повышенной прочности и высокого сопротивления износу и работающие под действием статических и динамических нагрузок
Деталь почти полностью симметрична относительно вертикальной плоскости симметрии.
Поскольку деталь имеет обрабатываемые поверхности либо типа отверстие либо типа плоскость то скорее всего в дальнейшем техпроцесс будет включать в себя только обработку осевым инструментом.
Конфигурация детали обеспечивает свободный доступ инструмента к обрабатываемым поверхностям обеспечивает необходимую жесткость. Все отверстия и плоскости располагаются параллельно и под прямым углом.
В конструкции детали имеется внутренняя резьба большого диаметра которую не возможно заменить другими конструктивными элементами по конструкторским соображениям.
Чертеж детали с конструкторской и технологической точек зрения выполнен на хорошем уровне: представлены основные отклонения размеров и форм. Отклонения линейных размеров выставлены от средних значений. Большинство линейных размеров проставлены от единой базы что является признаком технологичности конструкторских требований.
Технологичность детали можно определить с помощью коэффициентов:
-использования материала
где - средняя точность (значение квалитета)
N – число поверхностей данного квалитета.
коэффициент шероховатости
Где Шср – среднее значение шероховатости Ra мкм
В целом коэффициенты говорят о высокой технологичности детали (чем выше Кт и Кш тем технологичнее деталь).
Выбор и технико-экономическое обоснования заготовки.
Способ получения заготовок определяется назначением и конструкцией детали материалом техническими требованиями масштабом и серийностью выпуска а также экономичностью изготовления.
Спроектируем два вида заготовок:
Вариант 1 – Литье в оболочковые формы;
Вариант 2 – Обработка давлением (поковка).
Литье в оболочковые формы.
Спроектируем отливку полученную литьем в оболочковые формы по методике предложенной в ГОСТ 26645 – 85.
Способ получения заготовки – литье в оболочковые формы.
По таблице 13 выбираем класс точности отливки по массе – 7.
По таблице 11 определяем степень точности поверхности отливки-11.
По таблице 9 определяем класс размерной точности отливки – 9.
По таблице 14 определяем ряд припусков на обработку отливок – 3.
По таблице 1 определяем допуски размеров отливки:
Таблица 3. Допуск на литую заготовку.
По таблице 6 определяем общий припуск на сторону (чистовая обработка).
Таблица 4. Припуск на литую заготовку.
Номинальные размеры отливки.
Таблица 5. Номинальные размеры отливки.
Номинальный размер отливки
Обработка давлением (поковка)
Спроектируем поковку полученную методом пластической деформации по методике предложенной в ГОСТ 7505 – 89.
Исходные данные по детали.
Материал – Сталь 45Л
Берем из чертежа: m=43 кг
Исходные данные для расчета.
1.Масса паковки (расчетная):
Расчетный коэффициент: кр=1.8 (по приложению 3)
2.Класс точности: Т4 (по приложению 1)
3.Группа стали: М2 (по таблице 1)
4.Степень сложности: С2 (по приложению 2)
5.Конфигурация поверхности разъема штампа: П – плоская (по таблице 1)
6.Исходный индекс: 13 ( по таблице 20)
Припуски на механическую обработку.
Таблица 6. Припуски на механическую обработку.
Штамповочный уклон: (по таблице 8)
– не более 5о принимает 3о;
Таблица 7. Размеры паковки.
Радиус закругления наружных углов. (по таблице 7)
Допускаемые отклонения размеров. (по таблице 8)
Допускаемая высота торцевого заусенца – 3 мм.
Допускаемое отклонение от плоскостности – 05 мм.
Таблица 8. Размеры с отклонениями.
Размер с отклонениями
Проведем анализ технико-экономический показателей и выберем более подходящий вариант заготовки:
)Коэффициент использования материала
где q – масса готовой детали кг;
Q – масса заготовки кг.
)Снижение материалоёмкости
где Q1 Q2 – масса заготовок сравниваемых вариантов;
N – годовая программа выпуска деталей.
)Стоимость заготовки
где S – цена 1 кг материала заготовки руб.;
Sотх. – цена одной тонны отходов руб.
Определим экономию по стоимости:
где Sзаг1Sзаг2 – стоимость сравниваемых вариантов заготовок.
Так как в настоящее время цены все время изменяются необходимо выбирать заготовку по относительной стоимости:
Результаты расчетов занесем в таблицу 9.
Таблица 9. Сводная таблица.
Способ получения заготовки
Литье в оболочковые формы
Коэффициент использования материала
Стоимость одной тонны заготовки руб.
Стоимость одной тонны отходов руб.
Стоимость заготовки руб.
Экономия стоимости по отношению к 2 варианту руб.парт. заг.
Относительная стоимость %
Снижение материалоемкости по отношению к 2 варианту кгпар. заг.
Так же учитываем что оборудование при изготовлении поковки более дорогостоящее имеет большую трудоемкость.
Таким образом вариант получения заготовки с помощью – литья в оболочковые формы следует считать наиболее предпочтительнее так как экономия относительной стоимости заготовки по отношению ко второму варианту составляет 59%.
Анализ технологического процесса.
Последовательность механической обработки корпуса с плоским основанием и основным отверстием с осью параллельной основанию следующая.
Рис.1. Эскиз детали.
Учитывая конфигурацию размеры допуски припуски на обработку технические условия изготовления условия работы детали – выбираем литье в оболочковые формы (отливка I класса).
Этот способ применяют в условиях массового производства и для изготовления наиболее сложных по конфигурации заготовок.
На данной операции механической обработки производится подготовка технологических баз для обработки главного цилиндрического отверстия. Фрезеровать плоскости основания L=180мм h=64мм и два торца главного цилиндра D= 100мм начерно и начисто.
Технологическая база: Необработанная окружность с осью параллельной обрабатываемой поверхности. Базирование производиться в 4 призмах данная схема (рис. 2) базирования достаточна для обеспечения точности.
Рисунок 2. Схемы базирования.
Оборудование: Учитывая конфигурацию детали размеры выбираем продольно-фрезерный станок модели 6Г605 (с одновременной обработкой трех поверхностей). Данный станок позволит обработать одновременно все торцы заготовки тем самым уменьшая основное технологическое время и погрешности обработки.
Режущий инструмент: Фреза 80 2214-0311 ГОСТ 22087-76 с механическим креплением пятигранных пластин Т14К8 число зубьев 5 две фрезы торцовых 120 ГОСТ 22075-76 с механическим креплением пятигранных пластин Т14К8 число зубьев 6.
Приспособление: Используем специальное приспособление.
На данной операции механической обработки производится подготовка технологических баз для последующих операций. Зенкеровать развернуть снять фаски нарезать резьбу для двух отверстий D=44мм в плоскости основания.
Технологическая база: Необработанная окружность с осью перпендикулярной обрабатываемой поверхности. Базирование осуществляется как в операции 005.
Оборудование: Учитывая факт обработки и подготовки технологические баз а также припуски и допуски выбираем пяти позиционный агрегатный станок с круговым перемещением заготовок с четырьмя вертикальными головками на центральной колонне. Компоновка станка представлены на рисунке 3. Данный станок позволит обработать одновременно оба отверстия с необходимой конфигурацией тем самым уменьшая основное технологическое время и погрешности обработки.
Режущий инструмент: Четыре зенкера специальные комбинированные с направляющей режущая часть по ГОСТ 12509-75; две развертки специальные комбинированные с направляющей режущая часть по ГОСТ 21527-76; две плашки ГОСТ 9740-71 .
Рис.3. Компоновка агрегатного станка используемого
Зенкеровать и развертывать отверстия D=60мм D=75мм с осью параллельной базовой поверхности.
Технологическая база: Базирование производится по плоскости основания и двум отверстиям (рис.4).
Оборудование: На данной операции обрабатываются основное рабочее отверстие. Выбираем четырех позиционный агрегатный станок с круговым перемещением заготовок. Компоновка агрегатного станка используемого на операции 020 представлена на чертеже «Наладка». Данный станок позволит обработать отверстие необходимой конфигурацией. Уменьшая основное технологическое время и погрешности обработки.
Рисунок 4. Схема базирования.
Режущий инструмент: Два зенкера специальные комбинированные с направляющей режущая часть по ГОСТ 12509-75; развертка специальная комбинированная с направляющей режущая часть по ГОСТ 21527-76.
Окончательно развернуть отверстие D=60мм с осью параллельной базовой поверхности.
Технологическая база: Аналогично базированию на операции 015.
На данной операции обрабатываются основное рабочее отверстие. выбираем двух позиционный агрегатный станок с круговым перемещением заготовок. Компоновка станка представлена на рисунке 5. Данный станок позволит обработать отверстие необходимой конфигурацией. Уменьшая основное технологическое время и погрешности обработки.
Режущий инструмент: развертка специальная с направляющей режущая часть по ГОСТ 21527-76.
Рис.5. Компоновка агрегатного станка используемого
Подрезание торцов D=100 мм и нарезание резьбы М75х1.5 в основном отверстии с осью параллельной базовой поверхности.
Технологическая база: Аналогично базированию на операции 015.
На данной операции обрабатываются основное рабочее отверстие. выбираем трех позиционный агрегатный станок с круговым перемещением заготовок. Компоновка станка аналогична представленной на рисунке 5 имеет три позиции. Данный станок позволит обработать отверстие необходимой конфигурацией. Уменьшая основное технологическое время и погрешности обработки.
Режущий инструмент: фреза торцовая 120 ГОСТ 22075-76 с механическим креплением пятигранных пластин Т14К8 число зубьев 6.
Плашка диаметра 75мм по ГОСТ 17587-72
Развертывание крепежных отверстий D=18 мм и снятие фаски.
На данной операции обрабатываются крепежные отверстия. Выбираем трех позиционный агрегатный станок с круговым перемещением заготовок. Компоновка станка аналогична представленной на чертеже «Наладка». Данный станок позволит обработать отверстие необходимой конфигурацией. Уменьшая основное технологическое время и погрешности обработки.
Режущий инструмент: две развертки специальные по ГОСТ 3231-71 две зенковки специальные по ГОСТ 3231-71.
Маршрутный технологический процесс.
Таблица 10. Маршрутный технологический процесс.
Наименование Технологической операции
Заготовительная. Литье по оболочковым формам.
Фрезеровать торцы D=100 мм
Фрезеровать основание L=164мм h=64мм
Вертикально-фрезерный
Приспособление специальное
Зенкеровать на черно 2 отв. D=44мм
Зенкеровать на чисто
Нарезать резьбу М44 в 2отв.
Продольно-фрезерный станок модели 6Г605
Зенкеровать на черно с одной стороны отв. D=60мм и отв.D=75 мм.
Зенкеровать на чисто с одной стороны отв. D=60мм и отв. D=75мм.
Развертывать с одной стороны отв. D=60мм и отв. D=75мм.
Зенкеровать на черно с другой стороны отв. D=60мм и отв.D=75 мм.
Зенкеровать на чисто с другой стороны отв. D=60мм и отв. D=75мм.
Развертывать с другой стороны отв. D=60мм и отв. D=75мм.
Приспособление специальное;
Развернуть с одной стороны отв. D=60мм.
Развертывать с другой стороны отв. D=60мм.
Подрезать торец D=100мм с одной стороны.
Нарезать резьбу М75 с одной стороны.
Подрезать торец D=100мм с другой стороны.
Нарезать резьбу М75 с другой стороны.
Развертывать 2 отв. D=18мм на черно с одной стороны.
Развертывать 2 отв. D=18мм на чисто с одной стороны
Снятие фаски с двух отв. с одной стороны.
Развертывать 2 отв. D=18мм на черно с другой стороны.
Развертывать 2 отв. D=18мм на чисто с другой стороны
Снятие фаски с двух отв. с другой стороны.
Анализ точности обработки.
Погрешность механической обработки на настроенных станках может быть посчитана по формуле:
где б – погрешность базирования по данному параметру;
тс спиз –погрешность обработки по данному параметру полученная при использовании конкретной ТС СПИЗ приводиться в справочной литературе;
– общая погрешность механической обработки по какому-либо геометрическому параметру детали (размеру перпендикулярности соосности и т.п.).
На чертеже номер приведен анализ точности нескольких размеров полученные данные сносятся в таблицу 11.
Таблица 11. Анализ точности обработки.
Погрешности обработки
По данным таблицы проверяем выполнение условия :
Суммарная погрешность посчитанная по формуле:
- обязательно должна перекрываться припусками на поверхности соединяемые данным размером.
Данные условия (1) (2) выполняются для всех операций следовательно схемы базирования и маршрут обработки выбран верно.
Расчёт припусков и предельных размеров.
Припуск на обработку поверхностей детали может быть назначен по соответствующим справочным таблицам или на основе расчетно-аналитического метода определения припусков. Таблицы позволяют назначить припуски независимо от технологического процесса обработки детали и условий её осуществления и поэтому в общем случае является завышенными содержат резервы снижения расхода материала и трудоёмкости изготовления детали. Применение расчетно-аналитического метода сокращает в среднем расход металла в стружку по сравнению с табличными значениями создает единую систему определения припусков на обработку.
Рассчитаем припуски на обработку и промежуточные предельные размеры на размер детали D = 60мм D=75мм L=308 мм. На остальные обрабатываемые поверхности назначим припуски и допуски по ГОСТ 7505-89.
1.Расчет припусков и предельных размеров по технологическим переходам на обработку D =60 +0.03мм.
Таблица 12. Припуски и предельные размеры.
Технологи-ческие переходы обработки диаметра 60мм
Элементы припуска z мкм
Суммарное отклонение определяется по формуле:
Суммарное значение пространственных погрешностей определяем по формуле :
к – коробление корпусной детали 1.5 мкм на 1 мм [10таб.8]
где к - коэффициент уточнения к1=0.06; к2 =0.05
Рассчитываем минимальное значение припуска при односторонней обработке поверхности по формуле :
Зенкерование черновое:
Zmin=2(40+160+347)=1094мкм
Зенкерование чистовое:
Zmin=2(50+50+21)=242мкм
Развертывание нормальное:
Zmin=2(40+40+1.1)=162.2мкм
Развертывание точное:
Zmin=2(10+10+0)=40мкм
Определяем наибольший предельный размер по чертежу детали.
Для перехода предшествующему конечному определяем расчетный размер вычитанием из наибольшего предельного размера по чертежу расчетного припуска. Последовательно определяем расчетный размер для всех переходов.
Определяем предельные размеры. Наибольшие предельные размеры округляем уменьшением до того же знака десятичной дроби с каким задан допуск на размер для каждого перехода.
Рассчитаем наименьшие предельные размеры путем вычитания допуска из округленного наибольшего предельного размера.
Предельное значение припусков zmax определяем как разность наибольших предельных размеров и zmin как разность наименьших размеров предыдущего и выполняемого перехода.
Производим проверку:
Tзаг. – Tдет. = zmax - zmin
40 – 1530 = 740 – 30
Назначенные припуски верны полученные размеры соответствуют квалитету допускам и шероховатости.
Все данные о вычислении предельных размеров припусков заносим в таблицу 5 и строим схему (рисунок 6).
Рисунок 6. Распределение припусков и допусков на механическую обработку размера 60 +0.03мм
2. Расчет припусков и предельных размеров по технологическим переходам на обработку D =75 +0.03мм.
Таблица 13. Припуски и предельные размеры.
Zmin=2(40+160+271.94)= 941.88мкм
Zmin=2(50+50+16)=232мкм
00 – 1180 = 740 – 120
Все данные о вычислении предельных размеров припусков заносим в таблицу 6 и строим схему (рисунок 7).
Рисунок 7. Распределение припусков и допусков на механическую обработку размера 75 +0.03мм.
3.Расчет припусков и предельных размеров по технологическим переходам на обработку L=308+0.65 мм.
Таблица 14. Припуски и предельные размеры.
Технологи-ческие переходы обработки L=308мм
Фрезерование черновое:
Фрезерование чистовое:
00 – 1320 = 1120 – 140
Все данные о вычислении предельных размеров припусков заносим в таблицу 6 и строим схему (рисунок 8).
Рисунок 8. Распределение припусков и допусков на механическую обработку размера L= 308+0.65мм
Расчёт режимов резания.
Расчёт режима резания агрегатной операции 015.
Рассчитаем режим резания на агрегатную операцию отверстия с диаметрами 60 мм.
Глубину резания при зенкеровании и развертывании берем из расчета припусков на данную операцию:
t1 =1мм; t2=0.825 мм; t3=0.13мм.
Подачу при зенкеровании берем из табл. 26 [5стр. 277]
S1=1.25ммоб. ;S2=1.25 мм об.
Из табл. 29 [5 стр. 279] выберем значения коэффициента CV и показателей степени в формуле скорости резания зенкеровании и развертывании табл. 29 [5 стр. 279]: для материала Ст 45Л для зенкера Т15К6 для S>01 ммоб. CV=16.3 q=03 y=06 m=03х=0.2 и для развертки Т15К6 для S>01 ммоб. . CV=10.5 q=03 y=065 m=03х=0
Из табл. 30 [5 стр. 280] определим период стойкости зенкера T=100 мин. (для обработки стали ) развертки Т=120 мин (для обработки стали).
Скорость резания при зенкеровании и развертывании
Из табл. 1 [5 стр. 261] для обработки зенкером и разверткой Т15К6
nv=0.9 (табл.2 [5 стр.262])
KИV=1 – для обработки зенкером и разверткой Т15К6 стали (табл. 6 [5 стр. 263]).
KпV=0.9(табл. 5 [5 стр. 263]).
Рассчитаем скорости резанья:
Рассчитаем число оборотов шпинделя:
Округляем до стандартного значения n1=n2=80 обмин n3=40обмин
Уточним скорости резания:
Определим силу резания.
Значение коэффициента Срхy для зенкерования и развертывания берется из табл.32[5 стр. 281].Выбираем
Поправочный коэффициент находится по формуле из табл.9 [5 стр. 264]
Определяем силу резания:
Значение коэффициента Смхyq для зенкерования и развертывания берется из табл.32[5 стр. 281].Выбираем
См= 0.106; х=0.92;у=08; q=1.
Определяем крутящий момент:
Мкр.1=100.10658 1 10.9 1.25 0.8 0.73=53.650 Нм.
Мкр.2=100.10659.65 1 0.8250.9 1.25 0.8 0.73=46.403 Нм
Мкр.3=100.10659.91 1 0.130.9 2 0.8 0.73=12.866 Н*м
Мощность резания определяем для второй позиции рассчитаем по формуле:
где Nдв=1.5 кВт – мощность двигателя; =071 – КПД станка.
Nшп.=1.5071=1.065 кВт.
Сравниваем мощность резания и мощность станка:
Мощность станка больше мощности резания следовательно обработка возможна.
Расчёт норм времени.
Штучное время для крупносерийного и массового производства определяется для каждой операции отдельно по формуле:
Tшт= Tо+Tв+Tобсл+Tот
Tо – основное время мин
Tв – вспомогательное время мин
Tобсл – время на обслуживание рабочего места мин
Tот – время перерывов на отдых и личные потребности мин
Определение норм времени на агрегатную операцию 015
Где L – длина пути проходимого инструментом в направлении подачи
Где для зенкера и развертки:
- калибрующая часть развертки или зенкера;
l12=0.825ctg600=0.526
l2 =1-4 мм – величина перебега инструмента.
Исходя из расчетов режимов резания имеем
n1 = 80обмин; n2 = 80обмин; n3 = 40обмин
Рассчитаем основное время:
Примем за основное время – время первого перехода.
Вспомогательное время Тв = 025мин (табл. 57[2 стр 202])
Оперативное время Топ = То + Тв = 1.85+0.25=2.1 мин
где Tтех – время технического обслуживания рабочего места
Tорг – время организационного обслуживания рабочего места
Tтех = 0063мин(табл. 517[2 стр 210])
Tорг = 4% от Топ (табл. 521[2 стр 213])
Tорг = 2.1*004 = 0084 мин
Tобсл= 0063+0.084=0.147мин
Тот = 8% от Топ (табл. 522[2 стр 213])
Тот = 0.08*1.45 = 0.116 мин
В результате штучное время
Tшт= 1.86 +025+0.05+0147=2.25 мин
но т.к. обработка ведется сначала с одной потом с другой стороны то
Нормы времени на остальные операции определяются аналогично и сведены в таблице 15.
Таблица 15. Нормы времени на операции механической обработки
Наименование операции
Расчёт и конструирования станочного приспособления.
Разработано приспособление для зенкерования и развертывания отверстия на четырехпозиционном агрегатном станке специальным инструментом (специальный двухступенчатый зенкер специальная двухступенчатая развертка). Приспособление состоит из плиты 2 на верхней плоскости которой установлены с помощью штифтов 26 и закреплены винтами 13 два корпуса направляющих 3 для инструмента. Направляющие втулки 4 запрессованный в корпус направляющей. В плиту (корпус) запрессованы цилиндрический и ромбический пальцы (19 и 20). А также на корпус установлен с помощью винтов пневмоцилиндр 1. Пневмоцилиндр с помощью откидного болта 10 и двух гаек 16 соединяется с прижимным устройством 6 которое крепится на корпусе с помощью винтов 13. На нижней плоскости плиты две привертные шпонки 24 для базирования приспособления на столе станка.
Заготовки устанавливаются на опорные пластины (14 и 18) и цилиндрический и ромбический пальцы (19 и 20) по отверстиям диаметром 42 мм выполненные в заготовке по 8 квалитету точности. Через штуцер 25 в пневмоцилиндр подается сжатый воздух в результате чего клапан и связанный с ним шток и откидной болт 10 перемещаются вниз прижим 6 прижимает заготовки к опорным пластинам (14 и 18).
При прекращении подачи сжатого воздуха прижим 6 и шток возвращается в исходное положение откидывается откидной болт 10.
1.Расчёт усилия зажима механизма.
Сдвигу заготовки под действием силы резания Р препятствуют силы трения(не показаны) возникающие в местах контактов заготовки с опорами и зажимающими инструментами(ЗМ)
Необходимую силу закрепления находим по формуле:
где Q – сила зажима заготовки;
f1и f2 – коэффициент трения табл. 10[5с 85] f 1= 025 f2=0.25;
К- коэффициент запаса определяется из формулы К=К0К1К2К3К4К5К6 где
К0-коэффициент гарантированного запасаК0=1.5[5с.85]
К1-учитывает увеличение сил резания случайных не ровностейК1=1[5с.85]
К2-характеризует увеличение сил резания вследствие затупления РИ табл.9 [5с.84]К2=1.6
К3-учитывает увеличение сил резания при торцовом фрезеровании. К3=12[5с.85]
К4-характеризует постоянство силы закрепления в ЗМ К4=12[5с.85]
К5- характеризует эргономику ручных ЗМ К5=12[5с.85]
К6-при установке на опорные пластины К6=5[5с.85]
Перемножив все показатели получи К=1.2
Подставляем в формулу (4.1.4)
Усилие в пневмоцилиндре по ГОСТ 15608 составляет Q1=1390 H (не менее).
Q1 Q условие работоспособности выполняется.
2.Прочностной расчёт
Выполним расчёт прижима 6 (номер по спецификации) на прочность по максимальным допускаемым напряжениям.
Рисунок 10. Схема конструкции и эпюра изгибающих моментов.
С помощью программы САПР Beam 2.1.1.108 определим реакции опор и построим эпюры моментов (рисунок 10). На прижим действует сила резанья Pb=1341.6 Н момент M=53.6 Нм и сила прижима пневмоцилиндра Pc=1390Н длины L1=0.080 м L2=0.090 м.
Возникающие реакции опор равны Rа=1034.79 Н направлена противоположно силе резания Rb=1083.19 Н.
Максимальный момент равен Мmax=796788 Нм.
Из эпюры видно что наиболее опасное сечение расположено в месте приложения силы резания для которого
Геометрические размеры прижима: l=162 мм b=38 мм h=18 мм. Момент сопротивления кулачка относительно оси у минимальный поэтому:
мм3 или 3078*10-9 м3.
Допускаемое напряжение []=160 МПа. [] следовательно конструкция не разрушится.
3. Расчет размерной цепи.
Рассчитаем размерную цепь за исходное звено примем – несоосность осей направляющих втулок 4 и оси отверстия заготовки ( обозначим АΔ) A= мм.
Рисунок 11. Эскиз приспособления.
Рисунок 12. Размерная цепь.
Размерная цепь – плоская с параллельными звеньями.
Находим передаточное отношение звеньев:
Исходя из чертежа и конструкторских соображений назначаем номинальные размеры всех звеньев кроме наименее важного звена А2- высота установочной плиты.
A1 = 96 мм – расстояние от оси главного отверстия заготовки до верхней плоскости установочных пластин;
A3 = 108 мм – расстояние от нижней плоскости установочной пластины до оси отверстия корпуса направляющей;
A4 = 0.02 мм – не соосность оси отверстия направляющей (наружного диаметра направляющей втулки) и оси внутреннего диаметра направляющей втулки.
Расчет номинальных размеров размерной цепи:
Используем уравнение:
AD – номинальный размер исходного звена;
m – число звеньев размерной цепи (включая исходное звено);
Найдём номинальный размер звена A2:
AD=(-1)A1+(-1)A2+A3+A4
1 = -96-А2+108+0.02 ;
Ориентируясь конструкторскими соображениями назначаем на все звенья кроме звена А2 допуски по СТ СЭВ 145 - 88:
T2 = -35+54+10-10=19 мкм
Допуск по 6 квалитету (Т2=19мкм (IT7))
По СТ СЭВ 145-88 назначаем для всех звеньев размерной цепи кроме наименее важного звена (А2) схемы расположения полей допусков и определяем КСПД.
Для звена А1 выбираем схему расположения допуска – Н7
Для звенавыбираем схему расположения допуска – Н8.
Для звена А4 выбираем схему расположения допуска – g6.
Величину DO 2 рассчитаем с помощью уравнения
– координата середины поля допуска исходного звена;
– координаты середины полей допусков составляющих звеньев;
(-1)(DO 2) =5-[ (-1)(175)+(+1)(27)+(+1)(-7) ]
2.6 Рассчитаем Dн6 и Dв6 по формулам:
Δв6=+2.5+192=+12 мкм
Проверяем правильность расчёта по уравнениям
ΔвΔ=(-1)(+175)+ (-1)(+2.5)+ (-1)(+27)+(+1)(-7)+(35+19+54+19+10)2=+10мкм
ΔнΔ=(-1)(+175)+ (-1)(+25)+ (-1)(+27)+(+1)(-7)-( 35+20+54+19+10)2=0
Следовательно расчёт произведён правильно.
Результаты расчёта заносим в таблицу 16.
Таблица 16. Результаты расчета размерной цепи МПВ
Обозна-чение звеньев
Ном. размер зв. Аi мм
Передат. отноше-ние xi
Коорд. середин полей допусков Doi мкм
Предельные отклонения размеров мкм
Квалитет точности по СТ СЭВ 145-88
Схема расположения допусков по СТСЭТ 145-88
Соосность направляющей втулки и главного отверстия будет соответствовать допуску при высоте опорной пластины равной h=12g7 мм. Что соответствует стандартным размерам пластины ГОСТ 4743-68.
В проекте по полученным в задании данным определил тип производства рассчитав коэффициент закрепления операций. Полученный мной коэффициент kз.о.=0.62 kз.о.≤1 соответствует массовому производству.
На основании изучения и анализа чертежа (лист №1) определил служебное назначение детали корпус дросселя. Деталь - корпус дросселя является конструктивным элементом узла «дроссельная заслонка» входящего в систему двигателей внутреннего сгорания.
Была произведена отработка конструкции детали на технологичность. На основании анализа чертежа детали (лист №1) расчета коэффициентов технологичности определил соответствие конструкции детали материала размеров допусков и шероховатости поверхностей её служебному назначению. Полученные результаты удовлетворяют всем необходимым требованиям в целом считаем деталь технологичной.
Был произведен расчет двух методов получения исходной заготовки: литой и покованной заготовки. Проведя технико-экономический анализ с помощью коэффициентов использования материала снижения материалоемкости относительной стоимости и т.д. получили оптимальный метод получения исходной заготовки (литье в оболочковые формы) при данном виде производства этот метод будет соответствовать требованиям предъявляемым к конструкции детали материалу и технологическим условиям. Выполнен чертеж исходной заготовки (лист 2) в трех проекциях.
Разработан маршрутный технологический процесс для механической обработки детали.
Проведен подробный пооперационный анализ технологического процесса где учитывая тип производства конструкцию детали метод получения исходной заготовки технико-экономические показатели был сделан выбор типа станков инструмента приспособлений описаны схемы базирования в приспособлениях.
Выполнен анализ точности (лист 3 и 4) включающий операционные эскизы расчет погрешностей компоновки агрегатных станков. Проведенный анализ точности обработки показал что разработанный технологический процесс удовлетворяет необходимым требованиям.
Для трех поверхностей детали расчетно-аналитическим методом рассчитаны припуски для остальных поверхностей припуски были назначены опытно-статистическим методом.
Для агрегатной операции 015 включающей черновое чистовое зенкерование и нормальное развертывание произведен расчет режимов резания. Произведен расчет норм времени на все операции технологического процесса.
Для агрегатной операции 015 разработано одноместное пневматическое приспособление для зенкерования и развертывания отверстия на четырехпозиционном агрегатном станке. Выполнен сборочный чертеж приспособления (лист 5) в трех проекциях и спецификация на двух листах. Для данного приспособления произведен расчет силы зажима и соответствие данной силы усилию в пневмоцилиндре. Полученные результаты удовлетворяют необходимые требования.
Произведен расчет прочности на изгиб детали зажим 5 входящей в конструкцию разработанного приспособления. Конструкция детали удовлетворяет требованиям прочности.
Рассчитана размерная цепь на несоосность оси главного отверстия детали и оси отверстия направляющей втулки.
Разработана технологическая наладка (лист 6) на агрегатную операцию зенкерования и развертывания отверстия на четырехпозиционном агрегатном станке специальным инструментом: двухступенчатый зенкер двухступенчатая развертка.
Список использованной литературы.
Ансеров М.А. Приспособление для металлорежущих инструментов. М.-Л. изд. «Машиностроение» 1964 – 652 с.
Горбацевич А.Ф. Шкред В.А. Курсовое проектирование по технологии машиностроения - М.: Высшая школа 1983 – 256 с.
Горошкин А.К. Приспособления для металлорежущих станков: Справочник. – 7-е изд перераб. и доп. М.: Машиностроение 1979. – 303 с. ил.
Корсаков В.С. Основы конструирования приспособлений: Учебник для ВУЗов. – М.: Машиностроение 1983. – 277 с. ил.
Косилова А.Г. Мещеряков Р.К. Справочник технолога-машиностроителя в 2-х т. М.: Машиностроение 1985 – 656 с.
Обработка металлов резанием. Справочник технолога-машиностроителя А.А. Панов В.В. Аникин Н.Г. Бойни и др. М.: Машиностроение 1988 – 736 с.
Общемашиностроительные нормативы режимов резания: Справочник: В 2 т. – М.: Машиностроение 1991.
Общемашиностроительные нормативы режимов резания для механического нормирования работ на металлорежущих станках. М.: Машиностроение 1974 – 432 с.
Производство зубчатых колёс. Под ред. Б.А. Тайца. Изд. 2-е перераб. и доп. М.: Машиностроение 1975. – 708 с. ил.
Проектирование механосборочных участков и цехов: Метод. указ.сост. Ю.В. Дубровский НовГУ; Новгород 1994 – 34 с.
Технико-экономический анализ решений при дипломной проектировании: Метод. указ. Сост. А.А. Пиковский А.Л. Ганенков Т.О Задорина А.В. Новиков. Новгород НПИ 1992.
Шайдоров А.А. Ланцев И.А. Безопасность жизнедеятельности. Ч.2 Инженерные решения при проектировании условий обеспечивающих безопасность жизнедеятельности: Учеб. пособие НовГУ им. Ярослава мудрого. – Новгород 1995. – 116 с.
титуль.docx
Государственное образовательное учреждение
высшего профессионального образования
Новгородский Государственный университет имени Ярослава Мудрого
Кафедра технологии машиностроения
Курсовой проект по дисциплине
ТЕХНОЛОГИЯ МАШИНОСТРОЕНИЯ
Пояснительная записка
титульник.docx
Государственное образовательное учреждение
высшего профессионального образования
Новгородский Государственный университет имени Ярослава Мудрого
Кафедра технологии машиностроения
По технологии машиностроения
Технологический процесс обработки детали
листок задания.docx
Федеральное государственное бюджетное образовательное учреждение высшего профессионального образования
Новгородский государственный университет им. Ярослава Мудрого
Кафедра «Технология машиностроения»
УТВЕРЖДАЮ Зав.кафедройТимофеев В.В.
ЗАДАНИЕ НА КУРСОВОЙ ПРОЕКТ ПО ДИСЦИПЛИНЕ
«ТЕХНОЛОГИЯ МАШИНОСТРОЕНИЯ»
Студенту гр. 8041 Баталову Александру Сергеевичу
Тема: «Технологический процесс изготовления детали: корпус
Срок сдачи законченного проекта: июнь 2012 года
Исходные данные к проекту: чертеж детали годовая программа выпуска N= 90000 шт.год
заводской или типовой тех. процесс.
Содержание пояснительной записки:
Технологическая часть
Конструкторская часть
Перечень графического материала
Чертеж детали и исходной заготовки формата А 1: 1- 15 листа;
Технологические эскизы с анализом точности 1 л.;
Приспособления 1 л.;
Технологические наладки 1 л.;
Итого: min 4 листа формата А1.
Дата выдачи задания « » 2012 г.
Руководитель проекта Емельянов В.Н.
Задание принял к исполнениюБаталов А.С.
Корпус_1.cdw

Неуказанные предельные отклонения размеров механической
обрабатываемых поверхностей: отверстий по H14
Неуказанные радиусы не более 3мм..
* Размеры для справок.
наладка.cdw

I. Загрузочнаяразгрузочная позиция.
II. Зенкерование черновое.
III. Зенкерование чистовое.
IV. Развертывание нормальное.
Операция 015. Агрегатная
Оборудование: Четырехпозиционный агрегатный станок
Приспособление: Специальное
Корпус заготовка.cdw

Точность отливки 7-11-9-3 ГОСТ 22645-85
Формовочные уклоны по ГОСТ 3212-80 не указанные литейные
Предельные отклонения размерав необрабатываемых
поверхностей по 1 классу точности по ГОСТ 1855-55.
Остальные ТТ по ГОСТ 26358-84.
Спецификация_пр-2.DOC
Винт М6x25 ГОСТ 15589-70
Шайба А 12.01.ГОСТ 11371-78
Шайба А 6.01 ГОСТ 11371-78
НУТМ. 293.194.001 СБ
Чертеж.cdw

Допуск несовпадения осей отверстий втулок 4 с общей осью
пальцев 19 и 20 не более - 0
Сила зажима заготовки в приспособлении - не менее 1390 Н.
Диаметр поршня - 50мм.
Рабочий ход поршня в пневмоцилиндре- 5 мм.
Рабочее давление в системе - 1.00 МПа.
Спецификация_пр-1.DOC
Болт 2аМ12x75 ГОСТ7817-80
Болт 2аМ8x22 ГОСТ7817-80
Винт М6x25 ГОСТ 11738-84
Винт М8x25 ГОСТ 15589-70
Винт М10x25 ГОСТ 15589-70
НУТМ. 293.194.001 СБ
погрешности 2.cdw

I. Загрузкаразгрузка.
II. Нарезание резьбы.
III. Подрезка тореца.
II. Зенкерование черновое.
III. Зенкерование чистовое.
Операция 025 - Агрегатная
Операция 030 - Агрегатная
Операция 020 - Агрегатная
погрешности.cdw

I. Загрузкаразгрузка.
II. Зенкерование черновое.
III. Зенкерование чистовое.
V. Нарезание резьбы.
Компоновка четырехпозиционного
I. Загрузочнаяразгрузочная позиция.
IV. Развертывание нормальное.
Операция 005 - Фрезерная
Операция 010 - Агрегатная
Операция 015 - Агрегатная
721.010.001 корпус - MO-1118F1-2--622175029.doc
Б Печь для разогрева расплава
О 1 Отлить деталь по технологии цеха № 1 с Т.О.
О 2 Срезать литники
О 3 Обдуть технической дробью cоблюдая инструкцию №425
О 4 Термообработать по ТПП цеха в соответствие с ТУ чертежа.
А 1 1 1 010 Фрезерная ИОТ N 3 380
Б Продольно-фрезерный 6Г605
О 1 А. Установить деталь на станке закрепить и снять после обработки
Т РИ. Фреза D100-z18 2210-0075 ГОСТ 9304-69
А 1 2 1 015 Агрегатная ИОТ N 5 325
О 2 Зенкерование черновое 2 отв D=44мм
Т РИ. Зенкер D44 Специальный
О 3 Зенкерование чистовое 2 отв D=44мм Снять фаску
О 4 Развернуть 2 отв. D=44мм
Т РИ. Развертка D44 Специалная
А 1 3 1 020 Агрегатная ИОТ N 5 325
О 2 Зенкерование черновое
Т РИ. Зенкер Специальный
О 3 Зенкерование чистовое Снять фаску
О 4 Развернуть отверстие
Т РИ. Развертка Специальная
А 1 4 1 025 Агрегатная ИОТ N 5 325
О 2 Развернуть отверстие на чмсто
А 1 5 1 030 Агрегатная ИОТ N 5 325
Т РИ. Плашка M75x15 2650-1657 6g ГОСТ 9740-71
А 1 6 1 035 Агрегатная ИОТ N 5 325
О 2 Развернуть на черно 2 отверстия
О 3 Развернуть 2 отверстия на чисто
Т РИ. Развертка D18 2363-3001 №1 ГОСТ 21526-76
Т РИ. Зенковка D18 2353-0082 ГОСТ 14953-80
721.010.001 корпус - TL-1105F2-2--622175029.doc
Технический директор
К О М П Л Е К Т Д О К У М Е Н Т О В
на технологический процесс
Директор по качеству Главный технолог
Рекомендуемые чертежи
- 14.06.2023
- 24.01.2023
- 29.08.2014
- 29.08.2014