Технологический процесс изготовления болта




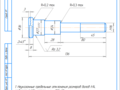
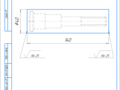
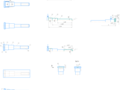
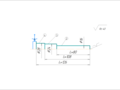
- Добавлен: 24.01.2023
- Размер: 421 KB
- Закачек: 1
Описание
Состав проекта
![]() |
![]() |
![]() ![]() ![]() |
![]() ![]() ![]() |
![]() ![]() ![]() |
![]() ![]() ![]() ![]() |
![]() ![]() ![]() ![]() |
Дополнительная информация
Карта эскизов (компас).cdw

Рисунки к пояснилке болта компас.frw

Чертеж Болта (компас).cdw

Чертеж заготовки (компас).cdw

Рекомендуемые чертежи
- 24.01.2023