Спроектировать станочное приспособление для обработки детали



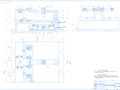
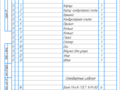
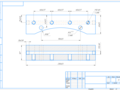
- Добавлен: 25.01.2023
- Размер: 362 KB
- Закачек: 0
Описание
Спроектировать станочное приспособление для обработки детали
Состав проекта
![]() |
![]() ![]() ![]() ![]() |
![]() ![]() ![]() ![]() |
![]() ![]() ![]() |
![]() ![]() ![]() ![]() |
![]() ![]() ![]() |
![]() ![]() ![]() |
Дополнительная информация
Спецификация.spw

Винт М4х14 ГОСТ 1491-80
Винт М6х18 ГОСТ 1491-80
Винт ступенчатый М6х18
Винт М*8х22 ГОСТ 1491-80
Втулка кондукторная
Втулка промежуточная
Гайка М12 ГОСТ 5915-70
Диафрагма ГОСТ 9887-70
Заклёпка ГОСТ 10249-80
Опорный диск ГОСТ 9887-70
Опора гладкая ГОСТ 3.1107-81
Опора плоская ГОСТ 3.1107-81
Фитинг ГОСТ 42705-81
Чертеж детали.cdw

Записка.docx
Заготовка в условиях серийного производства может быть получена путём газовой резкой из листового проката. Маршрутный технологический процесс изготовления детали представлен в таблице 1.
Расчёт режимов резания сил и мощности резания.
Станок радиально-сверлильный 2М55.
Для получения четырех отверстия М12 необходимы следующие переходы:
Переход 1 – сверление 4-х отверстий 102 мм.
Инструмент – сверло спиральное 102 мм 2301-0190 ГОСТ 10903-77 материал режущей части Р6М5.
Переход 2 снятие 4-х фасок 2х45 мм.
Инструмент зенковка 2353-0123 ГОСТ 14953-80 материал режущей части Р6М5.
Переход 3 нарезка резьбы М12 в 4-х отверстиях.
Инструмент метчик метрический М12 2620-1515 ГОСТ 3266-81 материал режущей части Р6М5.
Определяем режимы резания.
Принимаем по паспорту станка S0 = 022 ммоб.
Kv = К1К2К3К4К5К6К7К8
где Vт табличное значение скорости резания
К1 К2К3К4К5К6К7К8 поправочные коэффициенты
Kv = 1010091010101010 = 09
V = 216 09 = 1944 ммин
Частота вращения шпинделя
Корректируем частоту вращения шпинделя по паспорту станка: nпасп=500 обмин.
Фактическая скорость резания
где Nт табличное значение мощности резания
КNM поправочный коэффициент
N = 110 10 = 110 кВт
где Pт табличное значение силы резания
КРт поправочный коэффициент
Po = 3755 10 = 3755 Н
Мкр = 3755 001022 = 188 Нм
Режимы резания аналогичны переходу 1.
Kv = 1010081010101010 = 08
Корректируем частоту вращения шпинделя по паспорту станка: nпасп=160 обмин.
Обоснование выбора элементов и устройств приспособления.
Для установки заготовки в приспособлении по плоскости используются три плоских опорных пластины три опоры с плоской головкой.
В качестве привода зажима детали используется диафрагменный пневмопривод.
Расчётная схема и силовой расчёт приспособления.
Для расчёта силы закрепления детали составляем расчётную схему сил действующих на деталь при сверлении отверстия (рисунок 1).
Рисунок 1 – Схема сил закрепления детали.
Рассчитываем необходимую силу закрепления (силу на штоке) по формуле
где k коэффициент запаса;
Мкр крутящий момент при сверлении;
f коэффициент трения f = 025;
расстояние от оси обрабатываемого отверстия до оси приложения силы закрепления.
Коэффициент запаса рассчитывается по формуле
К = К0К1 К2 К3 К4 К5 К6
где Ко — гарантированный коэффициент запаса (К0=15);
К1 - коэффициент учитывающий составные поверхности заготовки (К=16);
К2 - коэффициент учитывающий увеличение сил резания от затупления инструмента (К2=10);
К3 - коэффициент усчитывающий увеличение силы резания при прерывистом точении (К3=10);
К4 - коэффициент усчитывающий постоянство силы зажима развиваемой приводом приспособления (К4=10);
К5 - коэффициент усчитывающий эргономику ручных зажимных элементов элементов (К5 = 10);
К6 - коэффициент зависящий от способа установки заготовки (К6=15).
К = 15161010101015 = 36
Расчет и выбор параметров механизированного привода.
Привод должен обеспечивать усилие на штоке. В приспособлении принят пневматический диафрагменный привод усилие на штоке которого рассчитывается по формуле:
где D - рабочий диаметр диафрагмы;
d - диаметр опорной шайбы;
р - давление сжатого воздуха (pmin= 04МПа).
Известна зависимость
Из этой формулы находим необходимый диаметр диафрагмы
Принимаем стандартное значение диаметра диафрагмы D=125мм. Тогда диаметр опорной шайбы
d = 07D = 07 125 = 88 мм.
Расчет деталей приспособления на прочность.
При закреплении детали максимальную нагрузку воспринимает шток привода. Самым слабым элементом штока является резьба M12 с помощью которой шток соединен с поршнем. Условие прочности резьбы имеет вид:
где d наружный диаметр резьбы;
d1 внутренний диаметр резьбы;
z число витков резьбы;
допускаемые напряжения на смятие.
d = 12 мм; d1 = 107 мм
= 08 = 360 МПа (для стали 45)
Таким образом прочность резьбы M12 обеспечивается так как т.е. 3598288.
Выбор расчетного параметра точности приспособления.
Расчетными параметрами точности приспособления являются:
Допуск перпендикулярности оси отверстия относительно поверхности А Т =0035 мм.
Допуск межосевого расстояния между отверстиями Т =007.
Допуск на размер 25 мм Т=02 мм.
Отверстие под резьбу М12-6Н имеет диаметр 102 мм и допуск Т =022 мм.
Расчет допуска на изготовление приспособления.
Допуск на изготовление приспособления рассчитываем по формуле:
где б - погрешность базирования
- погрешность закрепления
y - погрешность установки приспособления на станке
и - погрешность положения детали из-за износа установочных элементов приспособления
п - погрешность от перекоса (смещения) инструмента
где s максимальный диаметральный зазор между кондукторной втулкой и инструментом s=0005 мм.
- экономическая точность обработки
КТ - коэффициент учитывающий отклонение рассеяния случайных погрешностей от закона нормального распределения Кт = 10;
KТ1 - коэффициент учитывающий возможность уменьшения б при
работе на настроенных станках КТ1 = 08;
КТ2 - коэффициент учитывающий долю погрешности обработки вызванную факторами не зависящими от приспособления КТ2 = 07;
Для выполнения операции имеем:
= 0 (установочная и измерительная базы совмещены)
и = 0 (износ поверхности можно принять равномерным)
Подставив все значения в формулу получим допуск приспособления:
Определение допусков на звенья размерной цепи приспособления.
По допуску на приспособление назначаем допуски на составляющие звенья:
- допуск межосевого расстояния отверстий принимаем 003 мм.
- допуск перпендикулярности осей отверстий 002 мм
Технические требования к приспособлению.
Таким образом можно сформулировать требования к точности приспособления:
- допуск перпендикулярности отверстий равен 002 мм
- допуск параллельности осей отверстий равен 003 мм.
Описание конструкции устройства приспособления и принципа его работы.
Приспособление состоит из сварного корпуса 1 на верхней плоскости которого закреплен базирующие плоские опоры. Внутри сварного корпуса 1 установлен диафрагменный пневмопривод в состав которого входят: корпус 9 крышка 8 диафрагма 7 опорная шайба 5 и шток 2.
Для обработки деталь устанавливается плоской поверхностью на опоры и торцевыми поверхностями в упор на опоры. В верхнюю (штоковую) полость подается сжатый воздух. Под его действием опорная шайба 5 вместе со штоком 2 смещается вниз и через прихват 19 закрепляют деталь. Затем закрывается поворачиваемая кондукторная плита и сверлятся 4 отверстия после чего кондукторная плита откидывается и далее в отверстиях снимаются фаски и нарезаются резьбы.
Для открепления прихвата воздух подается в нижнюю полость пневмокамеры в результате чего опорная шайба 5 вместе со штоком 2 поднимаются вверх освобождая деталь.
Антонюк В.Е. Конструктору станочных приспособлений. Справ. Пособие. Мн.: Беларусь 1991.
Белоусов П.А. проектирование станочных приспособлений. Учебное пособие. М.: Высшая школа 1980.
Горохов В.А. Проектирование и расчёт приспособлений. Учебное пособие. Мн.: Высшая школа 1986.
Режимы резания металлов: Справочник. Под ред. Ю.В. Барановского.-М.: Машиностроение 1972.
Справочник технолога-машиностроителя. Т.2. Под ред. А. Г. Косиловой Р.К. Мещерякова. М.: Машиностроение 1985.
Чертеж приспособления.cdw

Усилие зажима Q= 3248 Н при двалении в системе 0
Рабочий ход штока 10 мм
Технические требования
Допуск перпендикулярности обрабатываемых отверстий 0
Допуск межосевых расстояний обрабатываемых отверстий 0
* Размеры для справок
Станосное приспособление
маршрут.docx
Схема базирования и
операционный эскиз обработки
мерительный инструмент
Фрезеровать поверхность 14.
Фрезеровать поверхность 23.
Фрезеровать поверхности 1.
Сверлить отверстие 2.
Нарезать резьбу в отверстиях.
Радиально-сверлильная
Сверлить 4 отверстия
Нарезать резьбу М12 в 4-х отверстиях.
Сверлить 2 отверстия
СОДЕРЖАНИЕ.docx
Расчёт режимов резания сил и мощности резания ..4
Обоснование выбора элементов и устройств приспособления ..9
Расчётная схема и силовой расчёт приспособления 9
Расчет и выбор параметров механизированного привода .10
Расчет деталей приспособления на прочность .. 11
Выбор расчетного параметра точности приспособления .12
Расчет допуска на изготовление приспособления 12
Определение допусков на звенья размерной цепи приспособления ..13
Технические требования к приспособлению 13
Описание конструкции устройства приспособления и принципа его работы 13
Рекомендуемые чертежи
Свободное скачивание на сегодня
- 24.01.2023