Спроектировать мостовой опорный кран




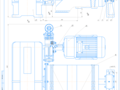
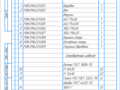
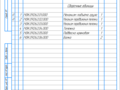
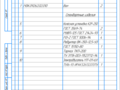
- Добавлен: 25.01.2023
- Размер: 865 KB
- Закачек: 0
Описание
Спроектировать мостовой опорный кран
Состав проекта
![]() |
![]() |
![]() ![]() ![]() ![]() |
![]() ![]() ![]() |
![]() ![]() ![]() ![]() |
![]() ![]() ![]() |
![]() ![]() ![]() ![]() |
![]() ![]() ![]() ![]() |
![]() ![]() ![]() ![]() |
![]() ![]() ![]() ![]() |
![]() ![]() ![]() |
![]() |
![]() ![]() ![]() |
Дополнительная информация
Передвижение тележки.cdw

Мостовой опорный кран _ МОК.09262.02.000.spw

Механизм передвижения тележки _ МОК.09262.01.000.spw

Механизм подъёма груза _ МОК.09262.01.000.spw

Общий вид готовое.cdw

подъём исправленое.cdw

Компановка.frw

Расчёт МК.frw
