Совершенствование технологии восстановления гильзы Д-260




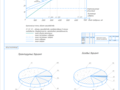
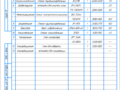
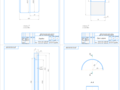
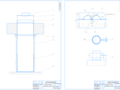
- Добавлен: 25.01.2023
- Размер: 755 KB
- Закачек: 4
Описание
Совершенствование технологии восстановления гильзы Д-260
Состав проекта
![]() |
![]() |
![]() |
![]() |
![]() ![]() ![]() |
![]() ![]() ![]() ![]() |
![]() ![]() ![]() |
![]() |
![]() ![]() ![]() ![]() |
![]() ![]() ![]() |
![]() ![]() ![]() |
![]() ![]() ![]() |
![]() ![]() ![]() ![]() |
![]() ![]() ![]() |
![]() ![]() ![]() |
![]() ![]() ![]() |
![]() ![]() ![]() |
![]() ![]() ![]() |
![]() ![]() ![]() |
![]() ![]() ![]() |
![]() |
![]() ![]() ![]() |
![]() ![]() ![]() ![]() |
![]() ![]() ![]() |
![]() ![]() ![]() |
![]() ![]() ![]() ![]() |
Дополнительная информация
ТЭО вmy.doc
1. Расчет инвестиций
Первоначальная стоимость основных фондов принимается по их фактической стоимости и включает в себя:
К = Кзд + Коб + Кпи (8.1)
где Кзд – сметная стоимость производственных зданий тыс. руб.
Коб – балансовая стоимость оборудования тыс. руб.
Кпи – стоимость приборов приспособлений инструмента и инвентаря тыс. руб.
Для определения балансовой стоимости оборудования пригодного к дальнейшей эксплуатации составляем смету на оборудование предприятия до реконструкции. На основании сметы производим выборку технологического оборудования подлежащего списанию и определяем его стоимость. Балансовая стоимость оборудования пригодного к дальнейшей эксплуатации составит:
Коб.ост = Коб.и – Коб.с (8.2)
где Коб.и – балансовая стоимость всего имеющегося оборудования тыс. руб.
Коб.с – балансовая стоимость оборудования подлежащего списанию тыс. руб.
Коб.ост = 282649 – 53942 = 188707 тыс. руб.
Аналогично стоимость приборов приспособлений инструмента и инвентаря которые пригодны к дальнейшей эксплуатации определяется по их фактической стоимости за вычетом суммы ежегодного их обновления.
Кп.и.ост = Ки.пи(1–g) (8.3)
где Кп.и.ост – стоимость приборов приспособлений инструмента и инвентаря пригодных к дальнейшей эксплуатации тыс. руб.;
Ки.пи – стоимость приборов приспособлений инструмента и инвентаря тыс. руб.;
g – коэффициент ежегодного обновления приборов приспособлений инструмента и инвентаря (g =025).
Кп.и.ост = 25632(1-025) = 19224 тыс. руб.
Тогда первоначальная стоимость основных фондов составит:
Кп = Кзд + Коб.ост + Кп.и.ост (8.4)
Кп = 460788+188707+19224 = 668719 тыс. руб.
Стоимость дополнительного оборудования определяется с использованием табл.8.1.
Расчет стоимости дополнительного оборудования
Наименование оборудования
Машина моечная УЗВ-35200 ТН
Станок отделочно-расточной 2Е78ПН
Гидравлический пресс ОРША-80
Станок внутришлифо-вальный 3К229В
Сумма транспортно-складских расходов (7 % от стоимости оборудования) тыс. руб.
Затраты на монтаж оборудования (4 % от стоимости оборудования) тыс. руб.
Капитальные вложения на приобретение дополнительного оборудования
Стоимость дополнительно приобретаемых приспособлений инструментов инвентаря определяем по укрупненным нормативам.
Кдпи = Кдоб g 100 (8.5)
где g – процент стоимости приборов приспособлений инструмента инвентаря от стоимости оборудования g = 8 %.
Кдпи = 25242544 8 100 = 2018 тыс. руб.
Таким образом капитальные вложения в реконструкцию равны:
Кд = Кдзд + Кдоб + Кдпи (8.6)
Кд = 278182+2018 = 298362 тыс. руб.
2. Расчет себестоимости гильзы цилиндров
2.1. Стоимость ремонтных материалов
Ср.м.= Н р.м. N2 (8.7)
где Нр.м - стоимость ремонтных материалов на единицу продукции тыс.руб
N2 – производственная программа предприятия штук.
Ср.м.=29х 7000 = 8125 тыс.руб.
2.2. Затраты на запасные части
Сз.ч. = Нз.ч. Сн.из. N2 (8.8)
где Нз.ч. – стоимость запасных частей на единицу продукции тыс.руб.
Сз.ч. = 097000 = 6300 тыс. руб.
2.3. Основная заработная плата производственных рабочих
Спр = Сср.ч Т Кув (8.9)
Сср.ч = Σ (Счi ni) Σni (8.10)
В проектируемом отделении работает 10 рабочих четвертого разряда часовая тарифная ставка четвертого разряда составляет 0725 тыс.руб. и 2 рабочий третьего разряда – ставка 07 тыс.руб.
Сср.ч = (0725 10+07 х 2) 12 = 072 тыс.руб.
Спр = 07210190 15 = 11000 тыс. руб.
2.4. Дополнительная заработная плата производственных рабочих
Сдоп = Ндоп Спр 100 (8.11)
Сдоп = 13211000 100 = 1452 тыс. руб.
2.5. Отчисления на социальное страхование
Ссоц = (Спр + Сдоп) Qсоц 100 (8.12)
Ссоц = (11000+1452) 35100 = 43582 тыс. руб.
2.6. Единый платеж чрезвычайного налога и обязательных отчислений в государственный фонд содействия занятости
Счз = Qчз (Спр + Сдоп)100 (8.13)
Счз = 5(11000+1452)100 = 622 тыс. руб
Спрн = Спр + Сдоп + Ссоц + Счз. (8.14)
Спрн = 11000+1452+43582+622 = 174322 тыс. руб.
2.7. Расходы на содержание и эксплуатацию оборудования
Сэксп. = Аоб + Апи + Ср.об. + Сэл + Св + Сп + Ссж + Спнр (8.15)
где Аоб – амортизация оборудования тыс.руб.
Апи – амортизация приспособлений тыс.руб.
Ср.об.– затраты на текущий ремонт оборудования тыс.руб.
Сэл.– затраты на электроэнергию тыс.руб.
Св – затраты на воду тыс.руб.
Сп – затраты на пар тыс.руб.
Ссж – затраты на сжатый воздух тыс.руб.
Спнр – прочие неучтенные расходы тыс.руб.
Затраты на амортизацию оборудования и приспособлений могут быть определены:
Аоб= Соб Наоб 100 (8.16)
Апи = Спи Напи 100 (8.17)
где Соб Спи – стоимость оборудования и приспособлений соответственно
Наоб Напи – норма амортизационных отчислений на оборудование и
приспособления соответственно %.
Аоб = (18870+253047) 5 100 = 220874 тыс.руб.
Апи = (19224+20244) 143 100 = 5644 тыс.руб.
Затраты на текущий ремонт оборудования равны:
Сроб = СобНроб 100 (8.18)
где Нроб – норматив отчислений на текущий ремонт оборудования %
Сроб = 441747 3 100 = 13252 тыс.руб
Затраты на потребление электроэнергии.
Сэл = Wэл С кВтч (8.19)
где Wэл – расход электроэнергии на выполнение производственной программы
СкВтч – стоимость 1 кВтч тыс.руб.
Сэл = 3000010410-3 = 3120 тыс.руб.
Прочие неучтенные расходы статьи «Расходы на содержание и эксплуатацию оборудования» принимаются в размере 5 % от суммы вышеперечисленных расходов
Спнр = 5(Аоб + Апи + Ср.об. + Сэл + Св + Сп + Ссж)100(8.20)
Спнр = 5(220874+5644+13252+3120)100 = 361 тыс.руб.
Сэксп. = Аоб + Апи + Ср.об. + Сэл + Св + Сп + Ссж + Спнр (8.21)
Сэксп =220874+5644+13252+3120+361= 75793 тыс.руб.
2.8.Цеховые (общепроизводственные) расходы
Цеховые расходы в общем виде определяются:
Соп = Спу + Сдоп.пу + Ссоц.пу + Сч.з.пу + Азд + Срзд + Спнр (8.22)
где Спу – основная заработная плата аппарата управления участком тыс.руб.
Сдоп.пу – дополнительная заработная плата управления участком тыс.руб.
Ссоц.пу – отчисления на социальное страхование аппарата управления участком тыс.руб.
Сч.з.пу – единый платеж чрезвычайного налога и отчислений в государст-
венный фонд содействия занятости тыс.руб.
Азд – амортизация производственного здания тыс.руб.
Срзд – текущий ремонт производственного здания тыс.руб.
Спнр – прочие неучтенные расходы статьи тыс.руб.
Спу =Σ (12СдiКув) (8.23)
где Сдi - должностной оклад по категориям общепроизводственного персонала
участка: ИТР МОП и т.д. тыс.руб.
Спу=12 (05 х 187440+05 х 76560)х15 = 2376 тыс.руб.
Сдоп.пу = Ндоп Сппу 100 (8.24)
Сдоп.пу = 1322376 100 = 3136 тыс.руб.
Отчисления на социальное страхование
Ссоц.пу = (Спу + Сдоп) Qсоц 100 (8.25)
Ссоц.пу = (2376+3136) 35 100 = 94136 тыс.руб.
Единый платеж чрезвычайного налога и обязательных отчислений в государственный фонд содействия занятости
Счз.пу = Qчз (Спу + Сдоп)100 (8.26)
Счз.пу = 5 (2316+3136)100 = 13448 тыс.руб.
Расходы на амортизацию производственных зданий определяются по формуле
Азд= СздНазд100 (8.27)
где Сзд – стоимость производственных зданий тыс.руб.
Назд – норма амортизации производственных зданий %.
Азд= 46078817100 = 7833 тыс.руб.
Затраты на текущий ремонт зданий определяются по формуле
Срзд = Сзд Нрзд 100 (8.28)
где Нрзд - норматив отчислений на текущий ремонт зданий %
( Нрзд = 1 - 15 % ).
Срзд =46078815100 = 69118 тыс.руб.
Прочие неучтенные расходы статьи «Цеховые (общепроизводственные) расходы» принимаются в размере 5 % от суммы вышеперечисленных расходов
Спр = 5 (Спу + Сдоп.пу + Ссоц.пу + Сч.з.пу + Азд + Срзд)100 (8.29)
Сппр = 5 (2376+3136+94136+13448+7833+69118)100 = 2619тыс.руб.
Соп =2376+3136+94136+13448+7833+69118+2619 = 218428 тыс.руб.
Прочие производственные расходы (Сппр) общехозяйственные (Ох) и внепроизводственные (К) расходы планируются в процентах от основной заработной платы производственных рабочих. Процентное соотношение (Rппр Rох Rвп) уточняется на базовом предприятии.
Сппр = Спр Rппр 100; (8.30)
Сох = Спр Rох 100; (8.31)
Свп = Спр Rвп 100. (8.32)
Сппр = 4515215 100 = 2258 тыс.руб.
Сох = 451521120 100 = 54183 тыс.руб.
Свп = 4515215 100 = 2258 тыс.руб.
Таким образом полная себестоимость восстановления гильз цилиндров равна
Спол = Спрн + Ср.м +Сз.ч.+Сэксп +Соп+Сппр+Сох +Свп. (8.33)
Спол=174322+20300+6300+715571+75793+2184+2258+54183+2258=
Себестоимость восстановления одной гильзы может быть определенна по формуле
Сед = Спол N2. (8.34)
Сед = 5582997000 = 8 тыс.руб.
Результаты расчетов себестоимости восстановления гильз цилиндров сводим в табл.8.2.
Структура себестоимости восстановления гильз цилиндров
Проектируемый вариант (2)
Расходы на оплату труда производственных рабочих с отчислениями
Затраты на ремонтные
Расходы на эксплуатацию и содержание оборудования
Цеховые (общепроизводственные) расходы
Прочие производственные расходы
Общехозяйственные расходы
Внепроизводственные расходы
Себестоимость гильз цилиндров
3.Определение отпускных цен на восстановленные гильзы цилиндров
В общем виде отпускная цена единицы продукции (услуги) складывается из следующих составляющих:
ОЦед = Сед + Мед+ Нв (8.35)
где Сед –себестоимость данного вида продукции (услуги)
Мед– прибыль на единицу продукции (услуги)
Нв – налоговые платежи из выручки.
Мед = Нр Сед 100 (8.36)
гдеНр – нормативная рентабельность продукции (услуги) %.
Мед = 208 100 = 16 т.р.
Нв=Q1*(Сед+Мед)(100-2)+Q2*(Сед+Мед+Q1*(Сед+Мед)(100-2))(100-25) (8.37)
где Q1 Q2 – ставки отчислений в республиканский фонд поддержки сельскохозяйственных производителей и аграрной науки и отчислений в местные бюджетные целевые фонды стабилизации экономики АПК.
Нв = 2(8+16)(100-2)+25(8+16+2(8+16)(100-2)) (100-25) = 045 т.р.
ОЦед = 8+16+045=1005 т.р.
Отпускная цена с учетом налога на добавленную стоимость (НДС)
ОЦед с ндс = ОЦед (100 + Qндс) 100 (8.38)
гдеQндс – ставка налога на добавленную стосмость%.
ОЦед с ндс = 1005(100 + 18)100 = 119 т.р.
4.Оценка эффективности инвестиций
При сравнении двух вариантов капиталовложений (базового и проектируемого) годовой доход определяют по формуле:
Дг = (М2 - М1) + (А2 - А1) - (Нп2 - Нп1) (8.39)
где М2А2Нп2 – прибыль амортизационные отчисления налоги в проектируемом варианте тыс. руб.;
М1А1Нп1 – прибыль амортизационные отчисления налоги в базовом варианте тыс. руб.
Значения М2 и А2 определяются с учетом приведенных выше расчетов по формулам
А2 = Азд + Аоб + Апи (8.41)
М2 =167000= 11175 тыс. руб.
М1= 1113000=3330 тыс. руб.
А2 =7833+220874+5644 = 35564 тыс.руб.
Величина налогов уплачиваемых из прибыли рассчитывается по формуле
Нп2 = Нн + Нпр + Нти (8.42)
гдеНн – налог на недвижимость тыс.руб.
Нпр – налог на прибыль тыс.руб.
Нти – транспортный сбор и отчисления на развитие инфраструктуры тыс.руб.
Нн = ( Сзд + Соб + Спи ) Qн 100 (8.43)
Нпр = ( М2 – Нн ) Qпр 100 (8.44)
Нти = ( М2 – Нн – Нпр ) Qти 100 (8.45)
гдеQн Qпр Qти – ставки налогов на недвижимость прибыль транспортный сбор и отчисления на развитие инфраструктуры %.
Значения М1 Нп1 А1 принимаются фактические по базовому предприятиюНн2= (460788+441747+39468) 10 100 = 942 тыс. руб.
Нпр2= (11175 - 942) 24 100=24559 тыс. руб.
Нти2= (11175–942-24559) 4 100=31108 тыс.руб.
Нп2=942+24559+31108 = 370898 тыс. руб
Дг =(11175 - 6226)+( 35564 - 2063)-( 370898 – 36954) = 932484 тыс.руб.
Показатели эффективности:
Чистый дисконтированный доход (NPV) при Дг = const.
ЧДД = Дг αт - Кд (8.46)
где αт – коэффициент приведения.
αт = --------------------- (8.47)
где Кд – величина инвестиций тыс.руб.
Е –процентная ставка %
Т–расчетный период лет.
αт = --------------------- = 502.
ЧДД = 932484 502 – 298426 = 16970 тыс.руб.
Срок окупаемости капитала (ДРР)
То = ------------------------ (8.48)
где Рв – коэффициент возврата капитала
Рв = Дг Кд – Е (8.49)
Рв = 932484 298426-015 = 016.
То = ------------------------ = 47 лет.
Индекс доходности (PI)
ИД = --------------- (8.50)
ИД = ------------------------- =16.
5.Расчет критических объемов производства
Объем производства (процент использования производственной мощности) в критических точках имеет следующие аналитические выражения:
Х1 = (Ип – А2) (Оцед - Иед) (8.51)
Х2 = Ип (Оцед - Иед) (8.52)
Х3 = (Ип + М2) (Оцед - Иед) (8.53)
где Х1Х2Х3 - соответственно объем производства (процент использования
производственной мощности) в точках: ликвидности безубыточности нормативной рентабельности шт;
Ип - постоянные издержки включающие производственные постоянные издержки и постоянные налоги тыс. руб;
А2 - амортизационные отчисления тыс. руб;
М2- заданная балансовая прибыль тыс. руб;
ОЦед - цена единицы продукции тыс. руб.;
Иед - переменные издержки на единицу продукции включающие переменные производственные издержки и переменную часть налогов тыс. руб.
Необходимо выделить из всего перечня рассчитанных затрат постоянную и переменную части.
Постоянные издержки – это издержки не зависящие от объема производства.
Ип =Аоб + Апи + Спнр + Ср.об + Соп + Сппр + Сох + Свп (8.54)
Ип = 220874+5644+24405+13252+55018+2258+54183+2258=
Переменные издержки - это издержки изменяющиеся при изменении объема производства.
Иед = (Сп - Ип) N2. (8.55)
Иед = (558299 – 1571409)7000 = 57 тыс. руб.
Х1 = (1571409–355644) (10 – 57)= 2828 шт;
Х2 = 1571409(10 – 57)= 3690 шт.;
Х3 = (1571409+11175) (10 – 57)= 6253 шт.
Технико-экономические показатели проекта
Наименование показателей
Годовая производственная программа шт.
Среднегодовое количество производственных рабочих чел
Энерговооруженность труда кВт.чел.
Энергоемкость продукции кВт*чшт.
Величина инвестиций тыс. руб.:
Себестоимость единицы продукции тыс. руб.
Отпускная цена единицы продукции тыс.руб.
Годовой доход от инвестиций тыс.руб.
Чистый дисконтированный доход тыс. руб.
Срок окупаемости капитала лет
Внутренняя норма рентабельности %
Графикmy.cdw

- объёмы производства соответственно в точках
нормативной рентабельности;
линия объёма реализации;
линия постоянных издержек;
линия постоянных затрат;
Линия суммарных затрат
Структура себестоимости
восстановления гильзы
-Затраты на оплату труда производственных рабочих;
-Затраты на запасные части;
-Затраты на ремонтные материалы;
-Расходы на содержание и эксплуатацию оборудования;
-Цеховые (общепроизводственные) расходы;
-прочие производственные расходы;
-Общехозяйственные расходы;
-Внепроизводственные расходы.
Проектируемый вариант
введение.DOC
Достижение поставленной цели возможно путём надежного материально-технического обеспечения улучшения использования автотракторного парка за счёт выпуска более надёжной техники и восстановления утраченной работоспособности их на авторемонтных предприятиях.
С повышением интенсивности использования автотракторного парка растёт потребность в ремонте для выполнения которого необходимо хорошо организованное ремонтное производство оснащённое современной производственно-технической базой.
Повышение надёжности капитально отремонтированных автотракторных двигателей может быть достигнуто путём специализации и концентрации производства улучшения технологии ремонта механизации и автоматизации технологических операций на всех стадиях производственного процесса повышения технического уровня автотракторного производства на основе реализации организационной и технологической преемственности с автотракторостроением.
При становлении рыночных отношений должна произойти оптимизация эффективности производственной деятельности любых ремонтно-обслуживающих предприятий. Эффективное использование машин и оборудования обеспечивается высоким уровнем их технического обслуживания и ремонта наличием необходимого числа агрегатов узлов запасных частей. Обеспечение запасными частями ремонтных предприятий и сфер эксплуатации машин и оборудования как показывают технико-экономические расчёты целесообразно осуществлять с учётом периодического возобновления работоспособности деталей
восстанавливаемых современными способами. Восстановление деталей – не только экономически оптимальное решение но и является основой ресурсо- и энергосбережения в народном хозяйстве Республики Беларусь.
!ДЕТ.cdw

Сборочный1.doc
Пластина сталь 40ХНМ
Устройство для запрессовки пластин
Сборочный2.doc
Цилиндрический стержень
Устройство для свертывания пластин
Фрагмент.frw

1и2ВО.cdw

Н.контр. Круглый П.Е.
Т.контр. Бетеня Г.Ф.
Список использованной литературы.doc
Черноиванов В.И. Бледных В.В. Северный А.Э. и др. Техническое обслуживание и ремонт машин в сельском хозяйстве: Учебное пособие Под редакцией В.И.Черноиванова- Москва-Челябинск. ГОСТНИТИ ЧГАУ 2003.-992с.
Надёжность и ремонт машин. В. В. Курчаткин Н. Ф. Тельнов К. А. Ачкасов и др. Под ред. В. В. Курчаткина. – М: «Колос» 2000г.- 776 с.:ил. (Учебники и учебные пособия для ВУЗов).
Ремонт машин. Под ред. Тельнова Н.Ф. – М.: Агропромиздат 1992 560 с.: ил. – (Учебники и учебные пособия для ВУЗов).
Методические указания к практическому занятию на тему: «Обоснование производственной программы специализированного ремонтного предприятия» Бетеня Г. Ф. Миклуш В.П. – Мн: Ротапринтер БИМСХ
Справочник по восстановлению деталей Воловик Е. Л.: М.: Колос 1981г.-351с. ил.
Харламов Ю.А. Будагвянц Н.А. Основы технологии восстановления и упрочнения деталей машин. Учебное пособие в 2-х т. Том 1. – Луганск: ВУНУ и М.В. Даля 2003. – 496с.
Восстановление и упрочнение деталей сельскохозяйственной техники: Учеб. пособие М.И. Черновол. – К.: УМК ВО 1989. – 256 с.
Харламов Ю.А. Будагвянц Н.А.Основы технологии восстановления и упрочнения деталей машин. Учебное пособие в 2-х т. Том 2. – Луганск: ВУНУ и М.В. Даля 2003. – 480с.
Унифицированный технологический процесс восстановления гильз цилиндров. М. – 1982г.- 25с.
Каталог средств измерений испытаний контроля и диагностирования применяемых на ремонтных предприятиях Госкомсельхозтехники. Под ред. В. Н. Лосева.- ГОСТНИТИ М. 1984г.-180с.
Нормативы времени на разборочные сборочные и ремонтные работы.
В. Я. Трофименко И. И. Пустовлатов. - ГОСТНИТИ М. 1988г.-260с.
Применение способа ремонтных размеров для внутренних поверхностей деталей. Методические указания к лабораторной работе «Растачивание гильз цилиндров». Часть 1. - Мн.: БГАТУ 2003г – 26с.
Применение способа ремонтных размеров для внутренних поверхностей деталей. Методические указания к лабораторной работе «Хонингование гильз цилиндров». Часть 2. - Мн.: БГАТУ 2003г – 28с.
Справочник технолога-машиностроителя. В 2-ух т. Т.1 Под ред. А. Г. Косиловой и Р. К. Мещерякова.- 4-е изд. – М.: Машиностроение 1985. 656с. ил.
Справочник технолога-машиностроителя. В 2-ух т. Т.2 Под ред. А. Г. Косиловой и Р. К. Мещерякова.- 4-е изд. – М.: Машиностроение 1985. 496с. ил.
Организация ремонтно-обслуживающего производства и проектирование предприятий технического сервиса АПК: Учеб. пособие В.П. Миклуш Т.А. Шаровар Г.М. Уманский; Под ред. В.П. Миклуша. – Мн.: Ураджай 2001 – 662 с.: ил.: – (Учебники и учебные пособия для ВУЗов).
Основы расчетов на трение и износ И. В. Крагельский. – М. 1977.
С. М. Бабусенко “Проектирование ремонтно-обслуживающих
предприятий” - М.: ВО “Агропромиздат” 1990 352 с.
Дорофеюк А.Т. Квасов В.Т. Охрана труда в сельском хозяйстве: Учебное пособие.–Мн.: Ураджай 2000. – 247 с.
Защита населения и объектов народного хозяйства в чрезвычайных ситуациях: Учебник для вузов. А.Г. Богданов С.В. Бондарев В.Н. Колобков М.И. Постник. – Мн.: Унiверсiтэцкае 1997. – 278 с.: ил.
Экологическая безопасность объектов АПК. К.Ф. Саевич Л.В. Мисун А.И. Федорчук и др. – Мн.: Ураджай 1998. – 199 с.
Дарков А. В. Шпиро Г. С. Сопротивление материалов: Учеб. Для техн. вузов – 5-е изд. перераб. и доп. – М.: Высш. шк. 1989. – 624 с.: ил.
Эффективность капиталовложений в условиях рынка: Методы расчета
В. В. Ширшова Л. И. Мацкевич. – Мн.: 1994. – 106с.
Усков В.П. Справочник по ремонту базовых деталей двигателей. – Брянск 1998. – 589 с.
Дунаев П.Ф. Леликов О.П. Конструирование узлов и деталей машин: Учебное пособие для машиностроительных спец. ВУЗов. – 4-е изд. перераб. и доп. – М.: Выш. шк. 1985 – с. ил.
!заключение.doc
Преобразование Дзержинского МРЗ в центр фирменного технического сервиса двигателей УП «ММЗ» предполагает обязательное выполнение технологии восстановления деталей на индустриальной основе с обеспечением ресурса не менее 100% от величины этого показателя одноименных новых изделий.
На примере разработки технологического процесса восстановления гильзы цилиндров двигателя Д-260 обоснована технология их восстановления с ресурсом более 100% по сравнению с новыми гильзами. Технология предполагает выполнение 16 технологических операций по восстановлению и применение 14 единиц оборудования из которых станки 3К229В и 3Г833 относятся к специальному.
В дипломном проекте разработаны все этапы в технологической последовательности восстановления гильзы цилиндров. Годовая производственная программа составляет 7000 гильз в год что отвечает потребности в запасных частях сельхозпроизводителей. В последующем возможно увеличение программы с учетом расширения рынка потребления за счет качества и цены изделия.
Для ритмичной и бесперебойной работы центра фирменного технического сервиса требуется налаженное материально-техническое обеспечение производства. Логистический подход к обеспечению необходимыми материалами и минимизации расходов а следовательно и получение большей прибыли являются основными условиями получениями устойчивого функционирования центра технического сервиса.
Разработанный комплект технологической оснастки позволяет быстро и качественно запрессовать пластины в гильзу.
Согласно разработанным расчётом экономической эффективности проекта видно что основными статьями затрат себестоимости продукции являются расходы на оплату труда производственным рабочим и затраты на ремонтные материалы.
Годовой доход от инвестиций составит 93248 тыс. рублей. Срок окупаемости капитала 47 года это в 213 раза меньше среднего амортизационного срока службы.
При анализе объёмов производства мы определили точку ликвидности точку безубыточности точку нормативной рентабельности. При восстановлении гильз более 2828 штук мы имеем поток наличности от производителя ремонтного предприятия (издержки) равный потоку выручки от реализации продукции. При восстановлении 3690 штук производственные затраты (производственные издержки и постоянная часть налогов вместе с амортизационными отчислениями) по величине равны выручке от реализации. При восстановлении более 6253 штук мы имеем чистую прибыль (окупив привлечённые инвестиции). Производство можно считать выгодным т.к. наша программа составляет 7000 штук. Из расчётов видно что объём производства данного предприятия находится в интервале включающем объёмы производства большие чем в точке нормативной рентабельности. Предприятию обеспечена экономическая прибыль (экономический эффект). Этот проект привлекателен для инвесторов.
Сборочныйзахват.doc
Левое полукольцо захвата
Правое полукольцо захвата
6.doc
1. Обоснование актуальности разработки
При восстановлении гильз цилиндров методом пластинирования необходимо иметь комплект технологической оснастки для предварительного свертывания пластин и их перемещения в гильзу цилиндров. Конструкция оснастки должна быть надежной и гарантировать безопасность рабочего.
2. Анализ прототипов
В литературном источнике [6] приведены схемы технологической оснастки для запрессовки пластин в гильзу на основании которых в данном дипломном проекте разработаны конструкторские решения составляющих устройств применительно для двигателя Д-260.
3. Описание конструкции и принципа работы
Для выполнения облицовки поясами из стали необходимы следующие приспособления: пресс-форма для формирования цилиндрического пояса из прямоугольной пластины захваты с приспособлением для предварительного свертывания пластины и ввода ее в пресс-форму центрирующее кольцо для совмещения оси пояса пластин в пресс-форме с осью детали калиброванный ступенчатая оправка и гидравлический пресс.
Калиброванная ступенчатая оправка имеет две ступени. Разница между диаметрами ступеней равна удвоенной толщине пластины.
Для предварительного свертывания пластины необходимо захват установить на плиту в разведенном состоянии вставить пластину между опорной оправкой и захватом свести рукоятки и вставить свернутую пластину в пресс-форму. Пресс-форма устанавливается на центрирующее кольцо. Центрирующее кольцо имеет две выточки: первую – для установки кольца на деталь вторую - для установки пресс-формы на кольцо.
Для перемещения пояса пластин из пресс-формы в гильзу применяется гидравлический пресс ОРША-40 шток которого через ступенчатую оправку запрессовывает свернутую пластину.
4. Технические расчеты
Определим размеры пресс-формы и ступенчатой оправки. Для этого необходимо рассчитать диаметр отверстия под пластинирование.
Диаметр отверстия под пластинирование определяем в два этапа. Вначале рассчитываем приближенное значение диаметра:
D`p = D + 2*h (6.1) где D – номинальный диаметр рабочей поверхности отверстия;
h – толщина пластины.
Толщину пластины определяют из стандартизированных толщин катанной ленты:
hmin ≤ h ≥ hmax (6.2)
где hmin - наименьшее допустимое значение h по условиям эксплуатации
hmax - наибольшее допустимое значение h по условиям осуществления технологического процесса облицовки отверстия гильзы цилиндра пластиной
(возможности прогнуть пластину в цилиндр).
Наименьшая толщина пластины hmin должна быть равна или превышать предельный износ И рабочей поверхности. С учетом неравномерности изнашивания принимаем:
hmin = (15 20)*И (6.3)
hmin = 15*075 = 075 мм
Наибольшее значение толщины пластины:
hmax = [2]*(1-²)*(D + 2*hmin) E1 (6.4)
где 2 – значение прочности на разрыв материала пластины;
= 430÷780 МПа – для легированных конструкционных сталей;
E1 – коэффициент Пуассона и модуль упругости материала пластины;
hmax = 780*(1- 025²)*(110 + 2*075)(210*103) = 085 мм.
Из условия (6.2) принимаем толщину пластины равной 08 мм.
D`p = 110 + 2*08 = 1116 мм.
На втором этапе рассчитываем точное значение диаметра отверстия под пластинирование путем внесения поправок на деформацию и обработку:
Dp = D`p - 2*(05*Th + t) + λ1 - λ2 - 12*(Rz1 + Rz2) (6.5)
где Th – допуск на толщину пластины;
λ1 – уменьшение диаметра D рабочей поверхности гильзы;
λ2 – увеличение диаметра Dр после установки свернутой пластины с натягом;
t – припуск на обработку пластины установленной в гильзу цилиндров (на сторону);
Rz1 Rz2 – параметры шероховатости соответственно пластины и обработанной рабочей поверхности 12*( Rz1 + Rz2) = 5*(Rа1 + Rа2).
λ1 = *([2] – 1* ) . (6.6)
λ1 = *(780 – 025* ) = 03 мм.
где dнц - наружный диаметр гильзы цилиндра;
р – нормальное давление на стенки цилиндра;
р = 2*[2]*h(D + 2*h); (6.8)
p = 2*750*08(110 +2* 08) = 108 МПа.
Dp = 1116 - 2*(05*00006 + 004) + 03 – 0026 - 5*(000032 + 000032) = =1118 мм.
Наименьший диаметр пресс-формы определяем из условия что диаметр свернутой и радиально обжатой пластины помещенной в пресс-форму (рис.6.1) должен быть равен или несколько меньше диаметра отверстия обработанного для пластинирования.
где Dп - внутренний диаметр пресс-формы. Принимаем Dп=11175мм.
В этом случае обеспечивается беспрепятственный и достаточно плавный ввод свернутой пластины в отверстие гильзы.
Рассчитаем на прочность пресс-форму. Давление на стенки пресс-формы при запрессовке пластины из (6.8) рв=108 МПа.
Определим нормальные напряжения r [22]:
где рв и рн – внутреннее и наружное давление на стенки пресс-формы
rв и rн – радиусы пресс-формы (rв = 00558м и rн = 0122м);
r – расстояние от оси детали на котором необходимо определить напряжения.
С помощью полученных выражений находим:
r = -105 МПа; = 164 МПа;
r =- 67 МПа; = 83 МПа;
r = 0 МПа; = 288 МПа.
Построенные по этим значениям эпюры r и изображены на рис.6.2.
Опасными являются точки у внутренней поверхности гильзы в которых действуют главные напряжения 1== 164 МПа и 3=r = -105МПа.
По третьей теории прочности [22]:
где [] – допускаемое напряжение []=150 МПа – для стали.
4 + 105 = 269 МПа ≤150 МПа.
Следовательно прочность пресс-формы обеспечена.
Калиброванная ступенчатая оправка имеет две ступени. Разница между диаметрами ступеней равна удвоенной толщине пластины. Диаметры ступеней определяют по формулам [6]:
где d1 – диаметр первой степени оправки входящей во внутреннюю часть пояса пластин;
S1 – зазор между внутренней поверхностью пояса пластин и поверхностью первой ступени оправки;
d2 – диаметр второй ступени калибра входящей в отверстие детали;
S2 – зазор между поверхностью отверстия детали и поверхностью второй ступени;
d1= 110-003=10997 мм;
d2= 1118-003=11177 мм.
РЕФЕРАТ.doc
ТЕХНИЧЕСКИЙ СЕРВИС ЗАПАСНАЯ ЧАСТЬ МАТЕРИАЛЬНО-ТЕХНИЧЕСКОЕ ОБЕСПЕЧЕНИЕ ГИЛЬЗА ЦИЛИНДРОВ РЕМОНТНЫЙ ЧЕРТЕЖ ИЗНОС НАДЕЖНОСТЬ РЕМОНТОПРИГОДНОСТЬ ТЕХНОЛОГИЧЕСКИЙ ПРОЦЕСС ТРУДОЕМКОСТЬ ВОССТАНОВЛЕНИЕ КОНТРОЛЬ КАЧЕСТВО ПРОИЗВОДСТВЕННАЯ ПРОГРАММА
В дипломном проекте разработаны технология восстановления гильз цилиндров двигателей Д-260 методом поясного пластинирования комплект технологической оснастки для предварительного свертывания и запрессовки пластин в гильзы цилиндров проведен анализ состояния охраны труда разработаны мероприятия по обеспечению в отделении восстановления гильз цилиндров пожарной безопасности выполнены экономические расчеты эффективности проектных решений.
Выполненные проектные решения при использовании в производственных условиях позволят улучшить условия труда повысить качество ремонтных работ в соответствии с требованиями центров фирменного технического сервиса.
!заключение.doc
Преобразование Дзержинского МРЗ в центр фирменного технического сервиса двигателей УП «ММЗ» предполагает обязательное выполнение технологии восстановления деталей на индустриальной основе с обеспечением ресурса не менее 100% от величины этого показателя одноименных новых изделий.
На примере разработки технологического процесса восстановления гильзы цилиндров двигателя Д-260 обоснована технология их восстановления с ресурсом более 100% по сравнению с новыми гильзами. Технология предполагает выполнение 16 технологических операций по восстановлению и применение 14 единиц оборудования из которых станки 3К229В и 3Г833 относятся к специальному.
В дипломном проекте разработаны все этапы в технологической последовательности восстановления гильзы цилиндров. Годовая производственная программа составляет 7000 гильз в год что отвечает потребности в запасных частях сельхозпроизводителей. В последующем возможно увеличение программы с учетом расширения рынка потребления за счет качества и цены изделия.
Для ритмичной и бесперебойной работы центра фирменного технического сервиса требуется налаженное материально-техническое обеспечение производства. Логистический подход к обеспечению необходимыми материалами и минимизации расходов а следовательно и получение большей прибыли являются основными условиями получениями устойчивого функционирования центра технического сервиса.
Разработанный комплект технологической оснастки позволяет быстро и качественно запрессовать пластины в гильзу.
Согласно разработанным расчётом экономической эффективности проекта видно что основными статьями затрат себестоимости продукции являются расходы на оплату труда производственным рабочим и затраты на ремонтные материалы.
Годовой доход от инвестиций составит 93248 тыс. рублей. Срок окупаемости капитала 47 года это в 213 раза меньше среднего амортизационного срока службы.
При анализе объёмов производства мы определили точку ликвидности точку безубыточности точку нормативной рентабельности. При восстановлении гильз более 2828 штук мы имеем поток наличности от производителя ремонтного предприятия (издержки) равный потоку выручки от реализации продукции. При восстановлении 3690 штук производственные затраты (производственные издержки и постоянная часть налогов вместе с амортизационными отчислениями) по величине равны выручке от реализации. При восстановлении более 6253 штук мы имеем чистую прибыль (окупив привлечённые инвестиции). Производство можно считать выгодным т.к. наша программа составляет 7000 штук. Из расчётов видно что объём производства данного предприятия находится в интервале включающем объёмы производства большие чем в точке нормативной рентабельности. Предприятию обеспечена экономическая прибыль (экономический эффект). Этот проект привлекателен для инвесторов.
всё печать.doc
1. Краткая характеристика предприятия. Анализ состояния организации технологии восстановления деталей
В 1977 году была проведена реконструкция завода. До реконструкции на заводе отсутствовали: склад готовой продукции лаборатории отдел главного механика инструментальный участок участок грунтовки корпусных деталей а также с нарушением ГОСТа 6572-75 производились окраска двигателей; испытательная станция была выполнена павильонного типа что создавало шум и загазованность. При этом площадь завода увеличилась на 50% а программу планировалось увеличить до 10000-12000в год.
В настоящее время Дзержинский МРЗ производит капитальный ремонт дизельных двигателей Д-240 Д-240Л Д-245 и их модификаций СМД 6VД. Завод производит переоборудование грузовых автомобилей с карбюраторным двигателем на дизельный Д-245. Так же ведётся разработка
техпроцессов ремонта и наладка ремонта двигателей Д-260. В настоящее время производственная программа не превышает 2000 двигателей в год это приводит к неполной загрузке оборудования [8].
Более подробно виды выполняемых работ приведены в табл. 1.1.
Наименование продукции
Текущий и восстановительный ремонт двигателей
Текущий и восстановительный ремонт сборочных единиц
Как видно из табл. 1.1 фактические объемы производства значительно ниже планируемых что говорит о недогруженности производственных мощностей. В настоящее время данная проблема остается одной из самых актуальных.
На данном предприятии имеется небольшой машинно-тракторный
парк для эффективного использования которого необходимо обеспечить его
готовность к эксплуатации. В связи с этим одна из основных задач инженерной службы предприятия – постоянное обеспечение высокой готовности машинно-тракторного парка.
Основу МТП завода составляют грузовые автомобили что говорит о том что он применяется в основном для перевозки грузов – а это доставка запчастей горюче-смазочных материалов и т.п. МТП состоит из современных машин которые периодически обновляются часть из них относится к легковому транспорту.
Мотороремонтный завод оснащен в достаточной мере подъемно- транспортным оборудованием правильно выбраны и распределены грузовые потоки. Расстановка оборудования соответствует нормам технологического проектирования.
Дзержинский МРЗ имеет следующую производственную структуру: разборочно-моечный участок; участок дефектации деталей; участок комплектования деталей; участки восстановления деталей; участок сборки двигателей; испытательную станцию; малярный участок; участок переоснащения карбюраторных двигателей на дизельные; отдел главного механика; административный корпус; складские и подсобные помещения; склады для ремфонда и готовой продукции; электроремонтный участок.
Поступающие на завод двигатели проверяются на соответствие техническим условиям на сдачу в капитальный ремонт и после оформления приемо-сдаточного акта поступают на склад ремфонда. Склад ремфонда оборудован подвесным краном для разгрузки автотранспорта и установки на место хранения. Со склада ремфонда двигатели с помощью межцехового автотранспорта поступают в мотороремонтный цех на участок подразборки где с двигателя снимается электрооборудование. Затем двигатели помещаются на подвесной конвейер линии разборки и очистки.
После промывки внутренних полостей с двигателя снимается крышка
клапанов масляный картер и крышка распредшестерни. Снятые детали навешивают на подвесной конвейер. Подразобранные двигатели проходят очистку в наружной моечной машине и ополаскивание в струйной машине. После сушки двигатель разбирается на узлы на специализированных постах разборки. Снятые узлы разбираются на детали которые укладываются в соответствующую тару и проходят очистку в моечной машине. На заводе применяют обезличенный метод ремонта.
Детали прошедшие очистку рассортировываются на три группы: годные подлежащие восстановлению и утильные. Подлежащие восстановлению детали группируют по видам дефектов укладывают в специальные контейнеры и транспортируются на соответствующие линии ремонта и восстановления где имеются механизированные стеллажи-накопители элеваторного типа.
Годные детали в специальных контейнерах электрокарами доставляют в механизированные стеллажи элеваторного типа предназначенные для отремонтированных и годных деталей [3].
Ремонт и восстановление деталей осуществляется на участке восстановления деталей на специализированных линиях. На участке восстановления деталей имеются следующие линии:
-ремонта блоков двигателей;
-ремонта коленчатых валов;
-ремонта распределительных валов;
-ремонта головок блоков;
-ремонт корпусных деталей;
-ремонта пусковых двигателей компрессоров редукторов;
-групповой обработки деталей.
После ремонта и восстановления детали проходят контроль и поступают на участок комплектования.
Восстановленные годные детали а также запасные части поступают на участок сборки при этом блоки цилиндров и коленчатые валы проходят
очистку а головки блоков цилиндров проходят очистку после сборки и притирки клапанов. Собранные узлы поступают на линию сборки двигателей. Посты сборки двигателей оснащены пневмоинструментом а также специальными приспособлениями.
Собранные двигатели устанавливаются на специальные тележки и напольно-щелевым конвейером доставляются на участок обкатки и испытания двигателей.
После обкатки и испытания двигатели проходят контрольный осмотр и на подвесном конвейере направляются на участок окраски.
На линии окраски проходят подготовку поверхности сушку грунтовку сушку окраску и сушку. Окрашенные двигатели на подвесном конвейере транспортируются на склад готовой продукции где двигатели окончательно укомплектовывают и консервируют. Со склада отпускают отремонтированный двигатель.
Анализ технологического процесса ремонта двигателей показал что не всегда на заводе соблюдается технологическая дисциплина не внедряется прогрессивная технология восстановления отсутствуют средства контроля не проводится аттестация рабочих мест [8].
Все это является основной причиной сравнительно низкого качества ремонта двигателей и поступления сравнительно большого числа рекламаций на отремонтированные двигатели.
Анализ исследований состояния технологии восстановления деталей на Дзержинском МРЗ позволяет заключить следующее. На МРЗ имеется устаревшее оборудование несоответствующее современным требованиям к качеству и производительности. Как правило это оборудование имеет также значительный физический износ. Существующая система восстановления деталей не обеспечивает требуемого качества их ремонта и восстановления.
Основная причина – отсутствие прогрессивных ресурсо-энергосберегающих технологий восстановления изношенных деталей [8].
2. Анализ конструкции условий работы неисправностей
и ремонтной технологичности гильзы цилиндра двигателя Д-260
Конструкционно-технологические особенности детали характеризуются геометрической формой материалом точностью и качеством обрабатываемых поверхностей твердостью и структурой материала видом термической обработки покрытием поверхностей и т.п. [1].
Гильза цилиндра двигателя Д-260 изготавливается из специального чугуна литьем. Химический состав чугуна в %: С=33 36; S Mn= 05 08; Р до 015; S до 012. Чугун легирован следующими элементами в %: Cr= 08 12; Cu= 08 11; N V= 01 025.
Микроструктура чугуна гильз по ГОСТ 3443-87 должна быть следующей: металлическая основа - перлит пластинчатый и зернистый (Пт1-Пт2).Феррит допускается в виде мелких отдельных включений [П(ФеО)-П96(Фе4)]; структурно-свободные карбиды Ц4-Ц10; фосфидная эвтектика тройная мелкозернистая или игольчатая. Распределение фосфидной эвтектики равномерное или в виде разорванной сетки.
Чугун подвергается искусственному старению что должно обеспечивать стабильность допусковых размеров по времени.
Микрогеометрия внутренней поверхности гильзы должна представлять собой сетку впадин глубиной 12 50 мкм шириной
-70 мкм с площадками между ними с глубиной микронеровностей 01-1 мкм и шероховатостью поверхности гильзы. Суммарная площадь площадок должна составлять 60-85%. Маслоёмкость внутренней поверхности должна быть 0008- 0041 мм³см² [9].
Твердость: НВ 217 – 255 кроме металлизированного слоя наружной поверхности твёрдость которой HRC 33-36 на глубине 02-03 мм.детали – 445кг. Количество на двигатель: 6 шт.
Гильза устанавливается в блок цилиндров по двум центрирующим пояскам. В поясе со стороны головки цилиндров гильза закрепляется буртом а со стороны масляного картера уплотняется двумя резиновыми кольцами размещённых в канавках блока цилиндров [3].
На рисунке 1.1 приведена схема сил действующих на первое поршневое кольцо. С помощью этой схемы можно представить механизм изнашивания таких важных соединений как кольцо — цилиндр и поршневое кольцо — канавка поршня.
Рис. 4.10. Схема сил действующих на поршневое кольцо
На верхний торец поршневого кольца действует давление газов рНг немногим отличающееся от давления в камере сгорания двигателя прижимающее его к нижнему торцу поршневой канавки. Снизу на кольцо воздействует давление газов р1 прошедших через зазоры между кольцом или гильзой кольцом или нижним торцом канавки. Это давление газов изменяется по ширине кольца и стремится оторвать его от плоскости соединения с канавкой. Однако давление газов на нижний торец значительно меньше чем на верхний из-за его дросселирования в зазорах. В результате кольцо прижимается к нижнему торцу канавки разностью давлений действующих на его
верхний и нижний торцы. Помимо давления газов на кольцо действует сила инерции рj. К зеркалу цилиндра кольцо прижимается силой величина которой пропорциональна разности давлений газа в заколечном пространстве (рНг) и на поверхности соединений с цилиндром. Давление газов на рабочую поверхность кольца (р1 и р2) меньше чем с внутренней стороны что объясняется дросселированием газа.
Между кольцом и поверхностью цилиндра возникает сила трения (Fтр) значение которой пропорционально давлению кольца на поверхность цилиндра возникающего в результате действия давления газов и силы упругости кольца. Эта переменная по величине сила направлена в сторону противоположную движению поршня. Работа сил трения вызывает износ цилиндра и рабочей поверхности кольца. На работу сил трения влияют: соотношение физико-механических свойств материалов кольца и цилиндра; состояние смазки и наличие в ней абразива; температура соединяемых деталей.
Работа сил трения нижних колец всегда меньше чем первого что объясняется с одной стороны лучшими условиями смазки а с другой — более низким давлением газов в лабиринтном уплотнении.
Вблизи верхней мертвой точки (в.м.т.) на тактах сжатия и рабочего хода происходит интенсивное изнашивание цилиндра усугубляющееся действием высокой температуры газа которая приводит к выгоранию смазочного материала на поверхности цилиндра. По мере движения поршня вниз работа сил трения колец в соединении уменьшается. Кольца заходят в зону цилиндра где всегда имеется масло на поверхности интенсивность изнашивания цилиндра по высоте уменьшается. Эпюра износа цилиндра (рис. 1.2)
имеет форму конуса большее основание которого расположено вблизи верхней мертвой точки [2].
В плоскости качания шатуна износ цилиндра несколько больше из-за действия нормальной силы. Участок цилиндра расположенный напротив огневого пояска поршня при положении его у в.м.т. изнашивается. Интенсивность изнашивания цилиндров помимо перечисленных факторов в значительной мере определяется условиями эксплуатации двигателя и совершенством его технического обслуживания. Неравномерный износ цилиндра по высоте приводит к радиальным перемещениям кольца в канавке. В результате и действия нормального усилия прижимающего его к нижнему торцу канавки между ними возникает сила трения F1 (см. рис.1.1). Работа силы трения вызывает износ поршневого кольца и канавки поршня который принято оценивать по увеличению торцевого зазора b. Чрезмерный износ этих деталей приводит к тому что дросселирующее действие кольца ослабевает. Газы свободно проходят в картер что ускоряет старение масла и изнашивание деталей цилиндропоршневой группы двигателя [2].
Наиболее распространенным дефектом гильз является износ рабочей поверхности гильзы цилиндра. Кроме износа внутренней поверхности гильзы встречаются следующие дефекты: износы нижней поверхности опорного бурта и посадочных поясков кавитационные разрушения наружной поверхности; отложение накипи [9].
Интенсивность изнашивания гильзы – 096 мкмч [17].
Выбраковочными признаками гильз цилиндра является наличие усталостных разрушений и трещин коррозионном износе и задирах рабочих рабочих поверхностей глубиной более 02 мм и кавитационных разрушениях наружных поверхностей глубиной более 15мм при наличии следов удара на поверхности [9].
3. Анализ существующих технологий восстановления гильз цилиндров
В ремонтной практике много различных способов восстановления внутренней поверхности гильзы цилиндра. Наиболее распространенными методами являются: ремонтных размеров восстановление центробежной наплавкой термопластическим обжатием поясным пластинированием.
3.1. Метод ремонтных размеров. Сущность метода заключается в следующем: у гильзы цилиндра механической обработкой устраняют искажения геометрических форм чистоты поверхности и нарушения взаимного расположения поверхностей вызванную износом а поршень заменяют новым с изменёнными размерами.
Обычно гильзы растачивают и подвергают двух- или трехкратному хонингованию. Растачивают гильзы на станках модели 278 или 278Н за один проход. При этом используют расточные резцы «Эльбор». Гильзу устанавливают в приспособление (рис. 1.3) размещенное на столе станка. Базовыми поверхностями при расточке служат посадочные пояски и торец опорного бурта. По неизношенному пояску в верхней части гильзы с помощью индикаторного приспособления или шариковой оправки совмещают оси шпинделя и гильзы. Гильзы растачивают а затем хонингуют.
После механической обработки гильзы контролируют в соответствии с техническими требованиями и сортируют на размерные группы по диаметру внутренней поверхности. Главным недостатком восстановления гильз обработкой под ремонтный размер является снижение (на 20-30%) их ресурса из-за уменьшения твёрдости поверхности. При использовании способа ремонтных размеров в процессе восстановления гильз цилиндров ресурс двигателей снижается на 30-50% [2]. Для его повышения гильзы упрочняют пластическим деформированием плосковершинным хонингованием закалкой ТВЧ лазерной обработкой и др. [3].
4.Метод восстановления центробежной наплавкой. На внутренней поверхности гильзы в верхней части (наиболее изношенной) на расстоянии 4мм от бурта протачивается кольцевое углубление (проточка) 30 50мм шириной 70мм. Деталь устанавливается в специальном патроне автоматизированной установки (рис 1.4). Гильзе придаётся частота вращения 750-950 мин-1 после чего в проточку подаётся шихта – смесь порошков флюса и наплавляемого материала. Шихта расплавляется в высокочастотном поле индуктора. Температура нагрева наружной поверхности в зоне наплавки 1300 1320К. Твёрдость наплавленного слоя колеблется в диапазоне НRС 55-58. К основным недостаткам технологии восстановления деталей данным способом следует отнести: низкую производительность процесса глубокое термическое влияние пятнистую твёрдость и нарушение структуры поверхностного слоя детали внутренние напряжения требующие последующего отпуска высокую трудоёмкость процесса восстановления искажение размеров и формы заготовки. Ресурс отремонтированных двигателей повышается на 80% [5].
3.3. Метод восстановления гильз термопластическим обжатием. Сущность способа состоит в том что изношенную гильзу устанавливают в охлаждаемую водой матрицу и с помощью индуктора нагревают током высокой частоты (рис.1.5). При нагреве выше 900С происходят структурные превращения и необходимый рост зерна. Вследствие ограничения свободного расширения в гильзе нарастают температурные напряжения вызывающие в радиальном направлении пластические деформации которые увеличиваются с ростом температуры.
При свободном остывании размеры гильзы уменьшаются (при оптимальных значениях температуры скорости нагрева усадка составляет 075 09 мм). Износостойкость восстановленных гильз цилиндров равна износостойкости новых гильз [7].
Некоторые предприятия восстанавливают гильзы газопламенным или пламенным напылением с последующим оплавлением ТВЧ дуговой наплавкой хромированием и железнением. Например для наплавки гильз цилиндров ЗИЛ-130 используют порошковую проволоку ПП-АН-124-О. Режим наплавки: напряжение 22 26В сила тока 110 130А скорость наплавки 15 22мч вылет электрода 20 25мм подача электрода 50-57мч его смещение с зенита 8-10мм шаг наплавки 5 6ммоб. Их долговечность после такого восстановления увеличивается в 13 16 раза [2].
3.4. Метод поясного пластинирования. Он предназначен для облицовки внутренних цилиндрических или конических поверхностей
деталей у которых отношение длины (высоты) цилиндра к его диаметру меньше четырех. Поясное пластинирование получило распространение при ремонте автомобилей строительных и дорожных машин
сельскохозяйственной техники.
Технологический процесс состоит
из следующих операций (рис.1.6):
расточки и хонингования цилиндра; изготовления из ленты мерных пластин; установки пластины в приспособлении и свёртывании её во втулку; снятия фаски в отверстии торца гильзы через который запрессовывается пластина; установки приспособления в сборе со свёрнутой пластиновтулкой на восстанавливаемую деталь и запрессовки последовательно нескольких пластин в гильзу; снятия фаски в отверстии втулки; хонингования «зеркала» цилиндра; контроля размеров [6].
Преимущества данного метода:
Ресурс восстановленных гильз выше ресурса новых деталей.
Возможность восстановления гильз вышедших за пределы ремонтного размера.
Высокая ремонтопригодность так как изношенный пояс легко заменить вновь свёрнутой и установленной в деталь пластиной.
Увеличение ресурса гильзы при установке в верхней части
пластины из высоколегированной стали.
Относительно простота технологического процесса так как не требуется использование специального дорогостоящего оборудования.
Метод пластинирования относится к числу энерго-ресурсосберегающих технологий является прогрессивным отвечающим требованиям высокой производительности качества и экономичности ремонтных работ.
4. Задачи решаемые в дипломном проекте
Обеспечение высокого качества и выбор наиболее рационального способа восстановления гильзы цилиндра.
Разработка ремонтного чертежа.
Обоснование технологического процесса.
Проектирование отделения по восстановлению гильз цилиндров.
Создание конструкторской разработки.
Обеспечение экономичности и безопасности проекта.
Обоснование ТЭП проектных решений.
Решение этих задач позволит внедрить современные технологии ремонта двигателей увеличить программу ремонта занять недогруженные производственные мощности что сократит простой и недогруженность оборудования создать новые рабочие места обеспечить прибыль предприятию что положительно скажется на экономическом состоянии мотороремонтного завода.
5..doc
В данном отделении производится восстановление гильзы цилиндров двигателей Д-260 Д-240 и их модификаций. Выполняются следующие работы:
- восстановление внутренней поверхности гильз цилиндров;
- восстановление поверхности посадочных поясков гильз;
- восстановление наружной поверхности гильзы.
Ремонт производится на специализированных рабочих местах. Отделение работает в тесной производственной связи с другими производственными подразделениями Дзержинского МРЗ на которых выполняются сопутствующие работы. Номенклатуру работ выполняемых на каждом рабочем месте подбирают исходя из общности работ и полной загрузки рабочего персонала.
Отделение по восстановлению гильз цилиндров имеет важное значение так как от качества гильз цилиндров зависит ресурс двигателя в целом.
2.Обоснование технологического процесса
Последовательность устранения дефектов выбор технологических баз расчет режимов подбор инструмента и оборудования подробно изложены в разделе 4 дипломного проекта.
3. Производственная программа и годовой объём работ отделения
Производственная программа и годовой объём работ отделения по восстановлению гильз цилиндров принимались с учетом выполненных расчетов в разделе 2. В количественном отношении производственная программа составляет:
Годовой объем работ отделения равен:
4. Режим работы и годовые фонды рабочего времени
Исходя из принятого режима работы по действующим нормативам устанавливаем годовой номинальный фонд времени рабочего Фнр [16]:
Фнр=(Np – Nвых - Nпр)tсм – tскNд (5.1)
где Np – количество дней в году;
Nвых – количество выходных дней;
Nпр – количество праздничных дней;
tсм – продолжительность смены;
tск – сокращение смены в предпраздничные дни;
Nд – количество предпраздничных дней.
Фнр=(365 – 104 – 9)8 – 91 = 2007ч.
Действительный фонд времени рабочего учитывает потери по отпускам по болезни и на выполнение общественных и государственных обязанностей [16]:
Фдр = [(Np - Nвых - Nпр – Nотп) tсм – tск Nд]К (5.2)
где Nотп – продолжительность отпуска;
К – коэффициент использования времени;
Nотп = 24дня; К = 096.
Фдр = [(365 – 104 – 9 – 24)8 – 91]096 = 1743ч.
Номинальный годовой фонд времени оборудования характеризует суммарный годовой баланс времени его работы без учета потерь и определяется [16]:
Фо.н.=((365-Nв-Nп)*tсм–nпп*tсп)*С (5.3)
где С – число рабочих смены.
Фо.н.=((365-104-9)*8-1*9)*1 =2007 ч.
Действительный годовой фонд времени учитывает наличие потерь рабочего времени связанных с проведением капитального и среднего ремонтов оборудования (малые ремонты и осмотры производятся в межсменное время) [16]:
Фо.д.=((365-Nв-Nп)*tсм–nпп*tсп)*1*hо (5.4)
где hо – коэффициент характеризующий использование оборудования по времени в связи с потерями рабочего времени на капитальный и средний ремонт оборудования.
Фо.д.=((365-104-9)*8-1*9)*1*098 = 1966 ч.
5. Расчет количества рабочих
В зависимости от характера выполняемых функций все работающие подразделяются на следующие группы: производственные рабочие (ПР); вспомогательные рабочие; инженерно-технические работники; служащие; младший обслуживающий персонал (МОП); пожарно-сторожевая охрана (ПСО).
Явочное число производственных рабочих определяют по номинальному фонду времени. Явочным составом называют состав рабочих фактически являющихся на работу. Явочное число рабочих определяется по формуле [16]:
где ТГ –годовой объём работ ч;
Фнр Фдр- соответственно номинальный и действительный рабочий фонд времени.
nр.я.= 101902007»5;
nр.с.= 10190 1743»6;
Окончательно количество рабочих определяется с учетом количества рабочих мест и оборудования. Таким образом в производственном отделении ремонта гильз цилиндров должно работать 6 человек.
6. Расчет количества и подбор оборудования
Количество единиц одноименного оборудования исходя из величины годового объема i-го вида работ определяется по формуле [16]:
Фдо – годовой фонд оборудования ч
hu - коэффициент использования загрузки оборудования;
Расчёты сведены в табл. 5.1.
Технологическая операция
Годовой объем работ ч
Количество оборудования принятое
Выбранное оборудование обеспечивает выполнение запланированного технологического процесса. Ведомость оборудования представлена в приложении дипломного проекта.
7. Расчёт количества рабочих мест
При расчете количества рабочих мест в отдельности по каждому виду работ учитывается годовой объем работ годовой фонд времени рабочего времени и принятый метод производства.
При тупиковом методе ремонта количество рабочих мест:
nр – количество рабочих на одном рабочем месте nр=1 ;
с – число смен работы с=1.
Число рабочих мест будет равно количеству выбранного оборудования (см. табл. 5.1).
8. Технологическая планировка
На технологической планировке обозначены структурные элементы здания оказывающие влияния на расстановку оборудования технологического и подъёмно-транспортного оборудования местонахождение рабочих при выполнении операций места подвода электроэнергии сжатого воздуха и др. Оборудование располагаем таким образом что к нему имеется доступ для подвоза гильз цилиндров соблюдены нормы технологического проектирования и обеспечиваются правила безопасности труда. Принятое оборудование расстанавливаем на участке придерживаясь следующих принципов: расстояние от стены до задней поверхности оборудования 600мм; между двумя соседними станками
00-2100мм. Электроэнергия подводится практически ко всему оборудованию вода к моечной машине. Проходы проезды и расположение оборудования позволяет проводить монтаж демонтаж и ремонт оборудования а так же убирать стружку и другие отходы [1618] .
Технологическая планировка участка по восстановлению гильз цилиндров приведена в графической части проекта.
9. Расчёт потребности в энергоресурсах
При разработке проекта необходимо произвести расчёт потребности в энергоресурсах. Для расчёта среднегодового расхода электрической энергии необходимо по ведомости оборудования определить мощность электроприёмников (Pобi) коэффициенты спроса (сi) и коэффициент загрузки оборудования (з i). На участке ремонта гильз установлен ряд оборудования с суммарной мощностью Pоб.
Мощность электроприёмников определяется по формуле [16]:
где Рi – мощность каждого электроприёмника кВт.
Роб = 05+22+75+2+3+10+10+85+45 = 482 кВт
Коэффициенты спроса определяем из табл. 7.4. [16].
Тогда годовой расход силовой электроэнергии определим из формулы [16]:
Pc = ΣPод i Фоб i с i з i (5.10)
где Фод – действительный годовой фонд времени работы оборудования ч;
зi – коэффициент загрузки оборудования по времени (з i = 065).
Pc = 482*1966*02*065= 12319 кВт*ч
Годовой расход электроэнергии на освещение определяется исходя площади пола освещаемого помещения удельной мощности на 1м2 и среднегодовой продолжительности электрического освещения. Расход энергии на освещение определим из формулы [16]:
Ро = 10-3 t ΣРуд iSi (5.11)
t – среднегодовой продолжительности электрического освещения ч
Si – площадь пола освещаемого помещения м2.
Ро = 10-3 4500 25 160 = 18000 кВт*ч.
10. Проектирование элементов производственной эстетики
Внедрение производственной эстетики на ремонтных предприятиях — один из важных резервов повышения производительности и улучшения условий труда уменьшения травматизма и профессиональных заболеваний а также снижения текучести кадров.
Для визуальной организации производственной среды отдельные отрасли промышленности и фирмы разрабатывают и принимают определенную цветовую гамму которую и используют при внедрении производственной эстетики.
Для предприятий АПК принят фирменный цвет — коралловая эмаль МЛ-12-95 и восемь вспомогательных цветов: бежевый — 991 желтый — 230 фисташковый — 939 светло-серый — 894 белый — 803 голубой —423 красный — 9 и черный - 837. Число указывает номер эталона цвета соответствующего эталону картотеки цветов лакокрасочных материалов.
Фирменный и вспомогательные цвета необходимо точно выдерживать. В цветовом решении производственных комплектов принятые цвета имеют определенное назначение. Коралловый фирменный цвет применяют в информационных системах-бланках деловой документации при оформлении транспорта обслуживания рекламы и полиграфической продукции; бежевый— для зданий и сооружений непроизводственного назначения. В желтый цвет окрашивают подъемно-транспортное оборудование в фисташковый — ворота производственных зданий в светло-серый — прочие металлоконструкции. Красный используют для обозначения устройств и средств тушения пожара. Белый голубой черный и фирменный цвета образуют цветовое решение указателей в информационных системах.
Эвакуационные выходы окрашивают в выделяющиеся цвета но гармонирующие с общим колоритом помещения. Магистральные проезды выделяют белым серым или черным цветом.
Отражательная способность окраски основных поверхностей оборудования должна находиться в пределах 25 55%. Стенки окрашивают в один основной цвет или два близких по насыщенности то есть верхнюю часть в более светлый тон нижнюю в более темный панели управления выделяют особым цветом. Обычно основные поверхности оборудования окрашивают в благоприятные для глаз цвета—сине-зеленые зеленые и др.
Элементы строительных конструкций оборудования и внутрицеховой транспорт представляющие опасность а также устройства и средства тушения пожара и обеспечения безопасности производственные знаки безопасности окрашивают в соответствии с требованиями ГОСТ 12.4.026-76.
Для сигнально-предупреждающей окраски установлены три основных цвета: красный желтый зеленый и вспомогательный — синий.
Красный цвет сигнализирующий об опасности используют для окраски запрещающих знаков противопожарных устройств а также для выделения в производственной среде трубопроводов баллонов и резервуаров СО взрывоопасными и легковоспламеняющимися жидкостями и т. п. Запрещающий знак представляет собой круг окрашенный в красный цвет.
Желтый цвет используют в качестве сигнала к осторожным действиям он предупреждает об опасности. В желтый цвет окрашивают строительные конструкции представляющие собой опасность кромки оградительных устройств подъемно-транспортное оборудование и предупреждающие знаки (желтый треугольник). Для лучшего восприятия желтые полосы чередуют с черными под наклоном 45° и при соотношении ширины полос 1:1.
Зеленый цвет применяют для обозначения средств обеспечения безопасности зон безопасности эвакуационных дверей и выходов мест хранения спасательных средств (носилок кислородных подушек противогазов и т. п.) а также для оформления плакатов по технике безопасности и предписывающих знаков (зеленый квадрат).
Вспомогательный синий цвет служит для оформления стендов с производственно-технической информацией и указателей визуальной информации представляющих собой синий треугольник.
На производственные знаки и указатели наносят символическое изображение того что запрещается о чем предупреждается и что предписывается или указывается. Знаки размещают в местах способствующих их хорошему восприятию [1618].
11. Мероприятия по обеспечению охраны труда строительные и противопожарные требования
Основные требования к размещению наиболее опасных видов производств. Размещение производств категорий А и Б в подвальных и цокольных помещениях не допускается. В многоэтажных зданиях помещения
с этими категориями производства рекомендуется располагать в верхних этажах. Производства категорий В Г и Д могут быть размещены в подвальных и цокольных помещениях если это допускается требованиями технологии и если при этом обеспечивается наиболее рациональное объемно-планировочное решение.
Наиболее опасные в пожарном отношении производственные подразделения—зарядную аккумуляторных батарей окрасочную склады смазочных материалов шин и др. — располагают у наружных стен.
Подразделения с производствами категорий А Б и В размещаемые в отдельных помещениях зданий I и II степени огнестойкости отделяют от других помещений несгораемыми перегородками с пределом огнестойкости 075 ч а двери в этих перегородках должны иметь предел огнестойкости не ниже 06 ч.
Наружные ограждающие строительные конструкции зданий и помещений с производствами категорий А и Б должны быть легко сбрасываемыми в случае аварийного взрыва. Трудно сбрасываемые конструкции допускается применять в случаях когда суммарная площадь верхних фонарей ворот дверей окон легкосбрасываемых панелей покрытий и стен составляет не менее 005 м2 на 1 м3 взрывоопасного помещения для производства категории А и не менее 003 м2 для производства категории Б.
Производственные участки (рабочие места) с применением взрыво- и пожароопасных жидкостей в малых количествах когда расчетный объем взрывоопасной смеси не превышает 5% общего объема помещения не выгораживают а располагают в общем технологическом потоке. Такие участки могут быть в отделениях ремонта силового и автотракторного электрооборудования ремонта агрегатов гидросистем шиноремонтных и др. При необходимости разрешается устанавливать в общем потоке окрасочное оборудование также не выгораживая его стенами. В этих случаях взрыво- и пожароопасной зоной считают зону в радиусе до 5 м от места применения
опасных смесей и жидкостей. Во взрыво- и пожароопасной зоне все силовое и осветительное электрооборудование должно быть выполнено во взрывозащищенном исполнении. Запрещается открытый огонь (сварочные и другие работы) на расстоянии до 15 м от ванн с взрыво- и пожароопасными жидкостями. Рабочие места и участки с опасными взрывопожарными зонами запрещается располагать под вспомогательными и административно-бытовыми помещениями в подвалах вблизи подвальных помещений и над ними. Запрещается также использовать подпольные воздуховоды для отвода паров пожароопасных жидкостей. На этих участках предусматривают устройства препятствующие растеканию жидкостей. Ванны и оборудование снабжают поддонами а участки ограждают бортиками. Кроме того такие участки обеспечивают внутренним водопроводом с пожарными кранами оборудуют автоматическими средствами тушения пожара пожарной сигнализацией и дополнительно стационарными воздушно-пенными огнетушителями ручного действия. На полу помещения по периметру взрывоопасной зоны проводят красную полосу а у границ зоны размещают аншлаг с надписью: «Взрывоопасная зона строгий противопожарный режим».
Для участков окраски деталей окунанием предусматривается подземный резервуар аварийного слива лакокрасочных материалов. Резервуар располагают за пределами здания на расстоянии не менее 1 м от глухой стены и не менее 5 м от стены с проемами. Диаметр сливной трубы и ее уклон должны быть такими чтобы лакокрасочные материалы из ванны в резервуар сливались за 3 4 мин.
Наряду со стационарными средствами тушения пожара в помещениях должны предусматриваться первичные средства: оборудованные щиты огнетушители ящики с песком кошмы и др. — согласно действующим нормам средств тушения пожара.
Противопожарные требования к помещениям складов. Склады ремонтных химикатов лакокрасочных и топливно-смазочных материалов размещают в изолированных помещениях I и II степени огнестойкости имеющих выход непосредственно наружу.
В складских помещениях не допускается размещение участков расконсервации и входного контроля упаковки и консервации зарядных станций аккумуляторов электротележек и других вспомогательных производств. При необходимости такие участки должны быть отделены от складских помещений несгораемыми перегородками. Если склад связан с технологическими процессами выгрузки консервации (расконсервации) складирования упаковки и отправки единой конвейерной системой то проемы в стенах должны быть защищены автоматическими дренчерными завесами.
Автоматическими средствами тушения пожара оборудуют следующие складские помещения:
помещения складов сгораемых материалов площадью 1000м2 и более несгораемых материалов в сгораемой упаковке площадью более 1500 м2 а также аналогичные склады площадью более 700 м2 расположенные в подвальных и цокольных помещениях;
помещения складов сгораемых материалов и несгораемых материалов в сгораемой упаковке при высоте стеллажей или штабелей более 55 м;
помещения складов лакокрасочных материалов и ЛВЖ насосных ЛВЖ горючих жидкостей и смазочных масел площадью 500 м2 и более а также склад резины и резинотехнических изделий площадью более 750 м2.
Требования к эвакуационным выходам и пожарным подъездам. Во всех производственных вспомогательных и складских помещениях должны быть предусмотрены эвакуационные выходы на случай аварийной обстановки.
Эвакуационными считаются выходы:
- из помещений первого этажа непосредственно наружу или через вестибюль лестничную клетку;
- из помещения любого этажа кроме первого на лестничную клетку в проход или коридор имеющие непосредственный выход наружу на лестничную клетку в вестибюль;
- из помещения в соседнее помещение на том же этаже с огнестойкостью ниже III степени не содержащее производств категории А или Б и имеющее выход непосредственно наружу через вестибюль лестничную клетку.
Количество эвакуационных выходов из здания или помещения должно быть в основном не менее двух. Ко всем зданиям и сооружениям ремонтного предприятия должен быть устроен подъезд для пожарных автомобилей [1618].
отделение.cdw

Многостаночное обслуживание одним рабочим
Подвод электроэнергии
Подвод сжатого воздуха
Слив отработанной жидкости в канализацию
Подвод холодной воды
Планировка отделения
Механический участок
Участок ремонта головки блока
Компоновка.cdw
Участок окраски двигателей
Склад готовой продукции
Участок ремонта КП и ВОМ
Участок ремонта гидро и топливной аппаратуры
Гальванический участок
Сварочно-наплавочный участок
Участок реставрации деталей
Участок досборки и контрольного осмотра двигателей
Участок обкатки и испытания двигателей
Участок сборки двигателей
Участок сборки узлов двигателя
Участок подготовки двигателя к разборке
Разборочно-моечный участок
Механический участок
Отделение восстановления гильз цилиндров
Участок ремонта головки блока
Участок ремонта коленчатого вала
Участок ремонта блока
Участок грунтовки двигателей
Отдел главного механика
Участок ремонта шатунов
Участок изготовления нестандартизарованного оборудования
с вертикальным разрезом
Таблица оборуд.doc
Габаритные размеры мм
Потребляемая мощность кВт
Станок отделочно-расточной 2Е78ПН
Станок внутришлифовальный
Установка для очистки гильз
ОМ-21601-ТГК ГОСНИТИ
Станок электрометаллизационный
Станок круглошлифовальный
Гидравлический пресс ОРША-80
Установка для консервации
оборуд.cdw

Станок внутришлифовальный
Установка для очистко гильз
Станок электрометаллизационный
Станок круглошлифовальный
Пресс гидравлический
Станок хонинговальный
Установка для консервации
Отделение по восстановлению
Спецификация оборудования.
Рекомендуемые чертежи
- 25.10.2022
- 10.05.2019
- 25.10.2022
- 24.01.2023
- 29.04.2021
- 28.03.2021
Свободное скачивание на сегодня
Другие проекты
- 30.03.2025
- 04.11.2022