Совершенствование базового технологического процесса изготовления детали Вилка скользящая




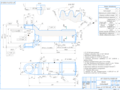
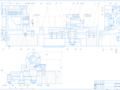
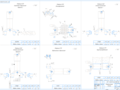
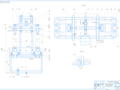
- Добавлен: 24.01.2023
- Размер: 1 MB
- Закачек: 9
Описание
Состав проекта
![]() |
![]() |
![]() ![]() ![]() |
![]() ![]() |
![]() ![]() ![]() |
![]() ![]() ![]() |
![]() ![]() ![]() |
![]() ![]() ![]() |
![]() ![]() ![]() |
![]() ![]() ![]() |
![]() ![]() ![]() |
![]() ![]() |
![]() ![]() ![]() |
![]() ![]() ![]() |
![]() ![]() ![]() |
![]() ![]() ![]() |
![]() ![]() ![]() |
![]() ![]() ![]() |
![]() ![]() ![]() |
![]() ![]() ![]() ![]() |
![]() ![]() ![]() |
![]() ![]() ![]() |
![]() ![]() ![]() |
![]() |
![]() ![]() ![]() ![]() |
![]() ![]() ![]() ![]() |
![]() ![]() ![]() ![]() |
![]() ![]() ![]() ![]() |
![]() ![]() ![]() ![]() |
![]() ![]() ![]() ![]() |
Дополнительная информация
спецификация станочное 1.doc
КП Т03.01.743.15.1 00
КП Т03.01.743.15.2 00
КП Т03.01.743.15.0 01
КП Т03.01.743.15.0 02
КП Т03.01.743.15.0 03
КП Т03.01.743.15.0 04
КП Т03.01.743.15.0 05
КП Т03.01.743.15.0 06
КП Т03.01.743.15.0 07
КП Т03.01.743.15.0 08
КП Т03.01.743.15.0 09
КП Т03.01.743.15.0 10
КП Т03.01.743.15.0 11
КП Т03.01.743.15.0 12
КП Т03.01.743.15.0 13
КП Т03.01.743.15.0 14
КП Т03.01.743.15.0 15
КП Т03.01.743.15.0 16
КП Т03.01.743.15.0 17
КП Т03.01.743.15.0 18
КП Т03.01.743.15.0 19
Поясняк.doc
1 Назначение и конструкция детали.4
2 Анализ технических условий изготовления детали.6
3 Анализ технологичности конструкции детали.7
4 Определение типа производства9
5Критический анализ базового ТП10
6 Выбор метода получения заготовки16
7 Выбор методов обработки поверхностей.19
8 Выбор технологических баз.22
9 Разработка технологического маршрута обработки детали.26
10 Разработка технологических операций.28
11 Расчёт припусков на обработку.32
12 Расчёт режимов резания.41
13 Определение норм времени на операции.44
14 Выявление и расчёт технологической размерной цепи.46
15 Определение количества оборудования и его загрузка.49
16 Уточнённый расчёт типа производства.51
Расчёт и проектирование средств технологического оснащения.53
1 Расчет и проектирование приспособления для алмазного растачивания.53
2 Служебное назначение и описание контрольного приспособления.59
Список литературы.61
Состояние и развитие производства на современном этапе зависит в значительной степени от технологии. Она определяет производительность труда экономичность использования материальных и энергетических ресурсов количество выпускаемой продукции и многое другое. В условиях современных рыночных отношений для развития машиностроительной промышленности получения максимальной прибыли от производства требуется разработка совершенно новых технологических процессов постоянное совершенствование традиционных методов обработки подготовки высококвалифицированных инженерных кадров.
Курсовой проект по данной дисциплине выполняется на основе материалов взятых на “Гродненском заводе карданных валов”. Цель курсового проекта - совершенствование базового технологического процесса изготовления детали “Вилка скользящая” действующего на предприятии с целью снижения себестоимости её изготовления повышения качества. В ходе курсового проекта должно быть разработано контрольное приспособление для контроля перпендикулярности оси отверстий ушек и оси цилиндра а также станочное приспособление для расточки отверстий в ушках.
Разработка технологического процесса изготовления детали.
1 Назначение и конструкция детали.
Вилка скользящая входит в состав сборочной единицы вал карданный привода генератора советских железнодорожных вагонов. Карданный вал служит для передачи крутящего момента от каретки к генератору. Применение карданного вала обусловлено тем что при повороте вагона расстояние и угол между генератором и направлением движения изменяется.
В данном случае карданная передача состоит из карданного вала выполненного в виде труб и двух жестких карданных шарниров. Шарнир соединяющий генератор с карданным валом выполнен таким образом что одна из его вилок выполнена удлинённой и соединена с валом при помощи подвижного шлицевого соединения. Это позволяет компенсировать перемещение генератора и каретки относительно друг друга при движении.
Конструкция данной детали предусматривает наличие двух ушек в которых выполнены отверстия. В отверстиях располагаются игольчатые подшипники. В этих подшипниках крестовина вращается вокруг своих осей что позволяет передавать крутящий момент под различными углами. Исходя из этого можно сделать вывод что ушки вилки работают на растяжение и сжатие. В вилке предусмотрено также шлицевой конец вала позволяющий устанавливать деталь в шлицевое отверстие. Посредством шлицевого соединения крутящий момент передается со шлицевого вала на вилку.
Основной конструкторской базой являются боковые поверхности шлицев. Отверстия в ушах являются вспомогательными конструкторскими базами.
Таким образом можно сделать вывод что наиболее ответственными поверхностями являются отверстия в ушах вилки и шлицевой конец вала и соответственно к изготовлению их будут предъявляться самые жесткие требования.
Вилка карданного вала изготовлена из стали 40 ГОСТ 1050-88 которая применяется для изготовления самых разнообразных деталей во всех отраслях машиностроения
В таблицах 1.1 и 1.2 приведены химический состав и механические свойства стали 40.
Таблица 1.1 Химический состав стали 40 ГОСТ 1050-88.
Массовая доля элементов % не более
Таблица 1.2 Механические свойства стали 40 ГОСТ 1050-88.
2 Анализ технических условий изготовления детали.
Исходя из служебного назначения детали проведём анализ технических условий её изготовления.
Изготавливаемая вилка входит в состав сборочной единицы “вал карданный”. При вращении вилка испытывает нагрузки. Такими нагрузками могут быть: кручение изгиб и т. д.
Отверстия выполняют по 7 квалитету. Этот размер необходимо точно выдержать так как он является конструкторской базой и необходим для правильной посадки и надёжного базирования подшипника и крестовины а следовательно и для его нормальной работы. Точность размера по 7 квалитету также удовлетворяет рекомендуемой точности диаметра отверстия для посадки подшипника. Отсюда можно сделать вывод о том что требуемая точность обоснована.
Жёсткий допуск на отклонение от соосности двух отверстий в ушках а также допуск на отклонение от перпендикулярности оси отверстий и наружного диаметра хвостовика необходим для точной ориентации крестовины относительно шлицевого хвостовика а следовательно для нормального выполнения служебного назначения вилки – передачи крутящего момента.
Точный размер проточки под стопорное кольцо соответствующий 9 квалитету точности а также допуски на отклонение от перпендикулярности проточки от оси отверстий в ушках и симметричности расположения относительно цилиндра Д необходимы для нормального соединения точно обработанных крестовины с вилкой при сборке. При невыполнении этих требований в результате возникновения перекоса осей отверстий и смещения проточек в осевом направлении больше допустимого установка крестовины может оказаться невозможной либо соединение не будет обладать достаточной надёжностью и точностью что приведёт к повышенному износу шуму при работе снижению КПД передачи.
Поверхность цилиндрического хвостовика 54 выполняют по 7 квалитету. Этот размер необходимо точно выдержать так как он необходим для правильной работы вилки в сборочной единице.
Поверхность наружного диаметра шлицев 62 выполняют по 7 квалитету. Этот размер необходимо точно выдерживать так как он является основной конструкторской базой и необходим для правильной посадки в шлицевое отверстие. Причем допуск на размер 62 по 7 квалитету равный Td=0030 не равен допуску указанному на чертеже (Td=0040). Но допущение о том что поверхность будет обрабатываться по 7 квалитету обеспечит требуемую на чертеже точность.
Допуск на радиальное биение цилиндрического хвостовика относительно наружного диаметра шлицев выдерживается на чертеже с заданной точностью для обеспечения правильной работы вилки и отсутствию дисбаланса.
3 Анализ технологичности конструкции детали.
Произведём анализ конструкции детали с точки зрения возможности использования рациональных методов получения заготовки. При получении заготовки объёмной горячей штамповкой можно отметить следующие особенности:
материал заготовки сталь 40 хорошо поддаётся пластической деформации в нагретом состоянии;
симметричность детали что обуславливает простой профиль разъёма окончательного ручья проходящего через плоскость симметрии заготовки;
сложность пространственной формы заготовки обуславливает сложность формы внутренних полостей штампа и необходимость штамповки в многоручьевом штампе за несколько переходов;
отсутствие в конструкции элементов образование которых вызывало бы трудности при данном методе получения заготовки однако невозможно получение на этой стадии отверстий в ушках и торце.
При получении заготовки литьём несмотря на хорошие литейные свойства материала возникают примерно те же трудности что и при получении заготовки объёмной горячей штамповкой связанные со сложностью геометрической формы заготовки.
В целом конструкции детали с точки зрения получения заготовки можно дать удовлетворительную оценку т.к. при всех недостатках заготовка получается по форме и размерам приближенной к готовой детали что снижает стоимость механической обработки.
Проведём анализ технологичности конструкции детали с точки зрения механической обработки. При этом рассмотрим следующие факторы:
обрабатываемость резанием нормальная. Коэффициент обрабатываемости Коб=1;
сложная геометрическая форма детали и отсутствие удобных для базирования поверхностей вынуждает использовать при базировании специальные дорогостоящие приспособления. По этой же причине сокращение числа установов при обработке является затруднительным;
также в детали есть сложные контурные поверхности – это переходные поверхности ушек и эвольвентные поверхности шлицев однако переходные поверхности ушек не обрабатываются резанием а обработка эвольвентных поверхностей шлицев не вызывает затруднения при применении специального инструмента.
доступ к обрабатываемым поверхностям не вызывает проблем однако контроль выдерживания требуемых допусков формы и расположения поверхностей требует специальных измерительных приспособлений большинство линейных размеров (что характерно для крупносерийного и массового производства) контролируется калибрами;
в конструкции детали есть элементы с малой жёсткостью – это ушки. Этот фактор накладывает ограничение на применение высокопроизводительных методов при обработке ушек.
так как деталь имеет симметричную форму то размеры выдерживаемые при обработке обоих ушек одинаковые. Вследствии этого для обработки этих поверхностей можно применять один и тот же инструмент. Применение специального инструмента – раскатки обусловлено тем что при этом не только обеспечивается требуемая точность но и упрочняется поверхность под подшипники без термообработки;
на детали отсутствуют места в которых происходит резкое изменение формы.
для обеспечения соосности отверстий в ушках требуется применение точных методов обработки оборудования и приспособлений. Остальные требования можно обеспечить на станках нормальной и повышенной точности;
имеется возможность сквозной обработки отверстий отсутствуют торцы подрезаемые с внутренней стороны;
при использовании специального станка возможна одновременная обработка отверстий в ушках;
отсутствуют обрабатываемые поверхности расположенные не под прямым углом.
На чертеже указано необходимое количество размеров для определения положения всех поверхностей детали. Замкнутые размерные цепи отсутствуют.
На основании данного анализа сделаем вывод что для обеспечения требуемых параметров готовой детали необходимо применить специальные виды механической обработки что приводит к повышению затрат и уменьшению производительности.
Для обработки заготовки в большинстве операций следует применять не стандартные а специальные станочные приспособления из-за отсутствия поверхностей удобных для базирования.
4 Определение типа производства
Тип производства влияет на построения технологического процесса изготовления вилки скользящей и организацию работы на предприятии.
На первом этапе проектирования технологического процесса тип производства ориентировочно может быть определён в зависимости от годового объёма выпуска детали и её массы.
Годовой объём выпуска вилки скользящей составляет 80000 штук а масса детали равна 29 кг по таблице эти параметры соответствуют массовому типу производства.
После разработки технологического процесса и определения норм времени произведем уточненный расчёт типа производства.
5Критический анализ базового ТП
Анализ базового технологического процесса обработки детали приведём с точки зрения обеспечения заданного качества детали (точность и шероховатость обрабатываемых поверхностей а также технических требований к детали) производительности обеспечения заданного объёма выпуска.
Метод получения заготовки – штамповка на КГШП нерационально использовать для получения заготовки в принятом массовом производстве в связи с его трудоёмкостью и большими кузнечными напусками а также невозможностью получения отверстий в ушках. Заготовку целесообразнее получить с помощью литья в кокиль этот метод обеспечит получение заготовки более высокой чистоты что позволит сократить время на механическую обработку и количество переходов за счёт малых припусков а также позволит получить отверстия в ушках.
Результаты анализа базового технологического процесса сведём в таблицу 1.3.
Таблица 1.3 Анализ базового варианта техпроцесса.
Содержание операции.
Центровать деталь с двух сторон выдерживая размеры:
Двусторонний центровальный мод. 2912
Пневмоприспособление 7699-4047-01
Сверло комбинированное 23х8х10 2310-4011
Индикатор ИЧ10кл1 ГОСТ577-68; набор эталонов шероховатости
Горизонтально-фрезерная
Фрезеровать поверхности ушек в размер 1085-087
фрезерный па мод.ДФ700
Оправка 7290-4062; приспособление 7290-4085
Фреза правая 2214-4013; фреза левая 2214-4044
Скоба размер 1085-087 8120-4222-04 или ШЦ-1-125-01 ГОСТ166-89;
Набор эталонов шероховатости 8490-4054
Точить поверхности в размеры: 57-04; 53-062; 65-04; 67±05;71±10; Подрезать торец в размер: 35ma 5max
Токарный многорезцовый па мод.1А730
Резцедержатель 6799-4048; копирная рейка 7069-4060-02; резцедержатель 6099-4024
Резец 2102-4005; резец 2110-4010
Скоба 57-04 8113-4332; скоба 53-062 8113-4413; скоба 65-04; ШЦ-1-125-01 ГОСТ166-89; набор эталонов шероховатости 8490-4053
Точить поверхности в размеры:538-074; 548-02; 628-074; 173±05; 518-074.
Токарный многорезцовый па мод.ЕМ473
Резцедержатель при станке; копир 7199-4120-01
Скоба518-074 8113-4000; скоба 628-02 8113-4261; скоба 548-02 8113-4262; скоба 538-074 8113-4462-12; набор эталонов шероховатости 8490-4053
Сверлить в двух ушках отверстия в размер 25;
Зенкеровать в двух ушках отверстия в размер 30
Специальный агрегатно-сверлильный мод.5318
Толкатель 7390-4326; удлинитель 6290-4013; приспособление 7390-4344
Сверло 25 2301-0087 ГОСТ10903-77; зенкер 30 2320-4020
Пробка 30 8133-4151-04; ШЦ--125-01-2 образцы шероховатости 8490-4153
Зенкеровать 2 отверстия в размер 328±015
Специальный агрегатно-сверлильный станок мод.АМ5832
Пробка 328±015 8133-4151-05; набор эталонов шероховатости 8490-4153
Позиция 1. Расточить в 2х отв. напроход предварительно выдерживая размер 345-01;
Расточить окончательно напроход 2 отвю выдерживая размер 35
Расточить канавки в 2х отв. выдерживая размеры 37+025; 2+025; 1005
Алмазно-расточной станок мод.ОС3016
Борштанга 6390-4046; приспособление 7490-4061
Борштанга 6390-4048; борштанга 6390-4049; приспособление 7490-4061
Борштанга 7429-4029.013-02
Резец 2120-4022-01; Резец 2120-4022
Нутромер НИ18 50 ГОСТ9244-75 Кольцо для настройки нутромера 35 8125-6077; Калибр 37+025 02-8701-5115 или спецштанген- циркуль ШЦ-III-160-005 8900-4187; эталон для настройки 37+025 8490-4299; калибр 2+025 8151-4439-01; Набор эталонов шероховатости 8490-4048; ШЦ-1-125-01 ГОСТ166-89
Раскатать с переустановкой 2 отв. в размер 35
Вертикально-сверлильный станок 2Н125А
Приспособление 35-006-1
Нутромер НИ18 50 ГОСТ9244-75; кольцо для настройки нутромера 35 8125-6077; набор эталонов шероховатости
Фрезеровать 22 эвольвентных шлица модулем 25 выдерживая размеры: 67 77; 51m 666min
Шлицефрезерный па мод.5350А
Оправка 7200-0012; оправка для соосности центров 7290-4115-01; оправка для выставления фрезы 7590-4002
Фреза червячная 2520-4005
Ролики5493 ГОСТ2475-62 или 8900-4643-7; микрометр МК50 75 ГОСТ6507-78; Индикатор ИЧ10кл1 ГОСТ577-68; набор эталонов шероховатости 8490-4054
Зачистить заусенцы на шлицах в местах выхода инструмента
Напильник 2820-0017 ГОСТ1465-69
Шевинговать 22 шлица модулем 25 в размер 664min
Шевинговальный станок мод.5702
Центр 7034-4032; центр 7034-4031
Комплексный калибр 8М4556Пр.; микрометр МК50 75 ГОСТ6507-78; Ролики 5493 ГОСТ2475-62 или8900-4643-7;скоба размер 664m индикатор ИЧ10кл1 ГОСТ577-68
Моечная машина проходного типа
Шлифовать поверхности выдерживая размеры 543-006; 623-006; 86m 60min
Круглошли фовальный станок мод.3М161
Центр 3В161Н121-9702
Шлифовальные круги 1750х80х305 24А40с1 СТ16К5 35мсекА1кл; 1750х100х305 24А40С1 СТ16К5 35мсекА1кл ГОСТ2424-83 с доработкой до размера по ширине 90мм; алмазный карандаш 3908-0054
Скоба 623-006 8113-4257; скоба 543-006 8113-4000-09; набор эталонов шероховатости 8490-4045
Шлифовать поверхности в размер 54; 62; 86m 60min
Круглошли фовальный станок мод.3М161; 3В161Н218
Центр 3В161Н121-9702; копир 7069-4074
Скоба54; скоба 62; индикатор ИЧ10кл1 ГОСТ8900-4823; набор эталонов шероховатости 8490-4045
Зачистить заусенцы и притупить острые кромки на механически обработанных поверхностях
Напильник 2820-0023 ГОСТ1465-69
Промыть деталь в горячем содовом растворе
Основным недостатком базового технологического процесса является то что точные операции (растачивание и раскатка) выполняются не в конце техпроцесса а перед черновой обработкой шлицевого хвостовика. Что может привести к короблению хвостовика в следствии чего нельзя будет добиться допусков перпендикулярности и пересечения осей отверстий и цилиндра хвостовика. Также не рациональным является применение на токарных операциях разных моделей станков. Тем более можно применить станки с меньшими габаритами рабочей зоны. Также при получении в заготовке отверстий в ушках на агрегатной операции нет необходимости в сверлении достаточно будет выполнить только зенкерование что позволит объединить две агрегатных операции в одну за счёт сокращения переходов.
6 Выбор метода получения заготовки
Выбор методов получения исходной заготовки оказывает большое значение на решение задачи экономии металла. При выборе методов получения исходных заготовок следует учитывать потери металла связанные с этими методами. При получении отливок из различных материалов потери составляют 35 54% и при изготовлении методами поверхностно-пластического деформирования потери изменяются в пределах 5 37%.
В базовом варианте технологического процесса обработки заготовки данной детали получают горячей объемной штамповкой на кривошипном горячештамповочном прессе. Горячая объемная штамповка осуществляется в открытых штампах. С целью получения наиболее точной и качественной поковки штамповка осуществляется в два перехода - предварительный и основной. Заготовками для горячей объемной штамповки служат изделия прокатного производства - прутки круглого сечения. При массовом типе производстве рентабельно использование высокоточных и высокопроизводительных методов получения заготовок.
Стоимость заготовки получаемой штамповкой на КГШП можно определить по следующей формуле:
где - базовая стоимость 1 тонны заготовок руб.;
- масса заготовки кг;
- коэффициенты зависящие от класса точности группы сложности массы марки материала и объёма производства заготовок;
=29 – масса готовой детали кг;
=248 – цена 1т отходов руб.
При штамповке получаем следующие значения:
кт = 1; кс = 0.84; кв = 0.87; км = 1; кп = 0.8.
Рассчитаем коэффициент использования материала КИМ:
Исходя из годового объёма выпуска деталей (80 тыс. штук) её конструктивной формы и размеров можно предложить более рациональный способ получения заготовки - литьё в кокиль. Литьё в кокиль экономически целесообразно при величине партии не менее 300 500для мелких отливок и 30 50для крупных отливок. Производительность способа – до 30 отливок в 1 час. Эти способом можно получать отливки массой 025 7 т. имеющих точность 13 16-го квалитета по СТ СЭВ 144-75 и параметр шероховатости поверхности Rz80 10. Литьё в кокиль позволяет автоматизировать процесс получения заготовки (отливки) сократить оперативное время уменьшить производственные площади улучшить условия труда рабочих.
Форму отливки выбираем приближенной к конфигурации вилки скользящей. В отливке возможным является получение отверстия 35мм. Допускается 4 раковины на 1 деталь. На поверхности перпендикулярные плоскости разъема формы назначаем уклоны по ГОСТ 3212-80: наружный 1-7% внутренний (со стороны стержня) 4-7%.
Таблица 1.4 Параметры точности отливки по ГОСТ 26645-85.
Параметры точности отливки
Класс размерной точности отливки
Степень корабления отливки
Степень точности поверхностей отливки
Шероховатость поверхности отливки Ra
Класс точности массы отливки
Ряд припусков на обработку отливки
Таблица 1.5 Припуски на механическую обработку заготовки по ГОСТ 26645-85.
Размер обрабатываемой поверхности мм
Допуски размеров отливки
Допуски форм и расположения отливки
Допуски масс отливки
Общий допуск элементов отливки
Допуск размеров детали
Соотношение между допуском размера детали и допуском размера отливки
Вид окончательной операции
Общий припуск на сторону элементов отливки
На размер 220 мм назначаем минимальный литейный припуск по ГОСТ 26645-85 06 мм.
Для определения массы заготовки рассчитаем массу снимаемого слоя металла:
Для отверстий в ушках:
Так как отверстия 2 то V=486624*2=973248 мм3.
Для цилиндрической поверхности хвостовика:
Для шлицевого конца вала:
Тогда общий объём снимаемого припуска будет равен:
V=973248+3016811+6255869=10245928 мм3
Тогда масса снимаемого припуска будет равна:
Тогда масса заготовки: mз=mд+mп=29+08=37 кг.
Определим стоимость заготовки получаемой литьём в кокиль:
кт = 103; кс = 083; кв = 093; км = 121; кп = 077
Подставляя значения в формулу получаем:
Сравнивая два вышеприведенных варианта получения заготовки (штамповка на КГШП и литьё в кокиль) по стоимости и коэффициенту использования материал (Sзаг1>Sзаг2 КИМ1КИМ2) можно сделать вывод что рациональным методом получения заготовки является литьё в кокиль.
7 Выбор методов обработки поверхностей.
Выбор методов обработки поверхностей вилки скользящей произведём на основании технологических требований чертежа детали формы поверхностей качества заготовки и типа производства. При назначении метода обработки будем стремиться к тому чтобы одним и тем же методов обрабатывалось возможное большее количество поверхностей заготовки. Это позволит разработать операции с максимальным совмещением обработки отдельных поверхностей сократить общее количество операций длительность цикла обработки повысить производительность и точность обработки.
В связи с тем что ушки обладают малой жёсткостью применение методов их обработки связанных с большими силами резания невозможно. Поэтому для их обработки будем применять двойное зенкерование двойное растачивание и раскатку для упрочнения поверхности под подшипники.
Для сокращения установов проточку под стопорное кольцо выполним также растачиванием.
Для цилиндрической поверхности хвостовика и наружного диаметра шлицев применим черновое получистовое и чистовое точение. Так как эти поверхности подвергаются термообработке то для исправления формы поверхности после термообработки выполним шлифование.
Так как к канавкам и торцу не предъявляется жёстких требований их обработаем однократным точением.
Для обработки наружных торцев ушек применим однократное фрезерование так как требования к точности выдерживаемого размера не велики.
Обработку шлицевого конца вилки выполним фрезерованием червячной фрезой с последующим шевингованием для уменьшения шероховатости.
Выбор методов обработки поверхностей сведём в таблицу.
Таблица 1.6 Методы обработки поверхностей.
Черновое зенкерование
Чистовое зенкерование
Предварительное врезное шлифование
Чистовое врезное шлифование
Проточка под стопорное кольцо
Однократное растачивание
Однократное фрезерование
Боковые поверхности шлицев
Однократное фрезерование червячной фрезой
Проверим правильность выбранных методов обработки для двух наиболее точных поверхностей: наружной поверхности 54 и внутренней поверхности 35.
По чертежу детали требуется обработать наружную поверхность 54 с шероховатостью Ra=063мкм. Диаметр поверхности отливки равен 572 (±06). Назначим виды обработки данной поверхности из следующих рекомендаций: точность на каждом последующем переходе обработки поверхности обычно повышается на черновых переходах на 3-4 квалитета на чистовых – на 2-3 квалитета:
переход: черновое точение 12 квалитет допуск d1=03мм
переход: чистовое точение 10 квалитет допуск d2=012 мм
переход: предварительное врезное шлифование 9 квалитет допуск d2=0074 мм
переход: чистовое врезное шлифование 7 квалитет допуск d2=003 мм
Требуемая величина уточнения:
Расчетное уточнение на 1 переходе
Расчетное уточнение 2 перехода:
После второго перехода делаем термообработку после которой качество поверхности ухудшается на 1 квалитет тогда расчетное уточнение 3 перехода:
Расчетное уточнение 4 перехода:
Общая расчетная величина уточнения:
т. к. 6879>40 Кур>КУ то назначенный маршрут обработки поверхности 54 вилки скользящей обеспечит заданную точность.
Для обработки внутренней поверхности 35 мм с шероховатостью Rа=125 мкм диаметр поверхности отливки составляет 318 (±055) мм. Эту поверхность возможно обработать за четыре перехода:
переход: черновое зенкерование 13 квалитет допуск d1=0250 мм
переход: чистовое зенкерование 11 квалитет допуск d2=0100 мм
переход: черновое растачивание 9 квалитет допуск d3=0039 мм
переход: чистовое растачивание 7 квалитет допуск d3=0025 мм
Раскатка только упрочняет поверхность и не влияет на точность поверхности.
Расчетное уточнение на 1 переходе:
Расчетное уточнение 3 перехода:
Получим 6879>44 Кур>КУ значит назначенный маршрут обработки поверхности 35 вилки скользящей обеспечит заданную точность.
8 Выбор технологических баз.
Выбор баз для механической обработки производим с учётом достижения требуемой точности взаимного расположения поверхностей детали по линейным и угловым размерам обеспечения доступа инструментов к обрабатываемым поверхностям обеспечения простоты и унификации станочных приспособлений а так же удобства установки в них заготовки.
При шлифовании поверхностей 54 и 62 в качестве технологической базы принимаем ось центровочных отверстий. Такая схема базирования обеспечит доступ режущего инструмента к обоим поверхностям. При такой установке мы сможем окончательно обработать поверхности 54 и 62 обеспечив при этом высокую точность их взаимного расположения. Для реализации данной схемы базирования применяем центра и поводковый патрон.
Рисунок 1.8.1 Схема базирования используемая при шлифовании цилиндров 54 и 62.
Так как при шлифовании окончательно обрабатываются поверхности 54 и 62 то перед шлифованием мы должны совершить чистовую обработку этих поверхностей. Для обработки щлицевого хвостовика вилки за технологическую базу принимаем ось центровочных отверстий. Данная схема базирования соблюдает принцип постоянства баз. Такую схему можно реализовать с помощью специального поводкового патрона и центров.
Рисунок 1.8.2 Схема базирования используемая при обработке шлицевого хвостовика.
Так же перед окончательной обработкой поверхностей 54 и 62 обработаем отверстия в ушках вилки. При данной обработке мы отступим от соблюдения единства баз для точных допусков перпендикулярности и пересечения оси отверстий и оси цилиндра Д а также для размера 220 определяющего положение оси отверстий что позволит применить более простое приспособление. Точность этих допусков обеспечим наладкой станка.
Рисунок 1.8.3 Схема базирования используемая при обработке отверстий в ушках вилки.
Также необходимо обработать наружные поверхности ушек вилки. Для этого применим установку заготовки в равномерно сходящиеся призмы по поверхности 54. Отступление от принципа постоянства баз вызвано тем что при обработке этих поверхностей необходимо более жёсткое закрепление заготовки.
Рисунок 1.8.4 Схема базирования при обработке наружных поверхностей ушек.
При обработке наружных поверхностей ушек в качестве технологических баз мы использовали поверхность 54. Поэтому перед этой обработкой мы должны обработать эту поверхность а также подготовить к последующей обработке поверхность 62. В качестве технологической базы используем ось центровочных отверстий. Данную схему базирования можно реализовать с помощью поводкового патрона и центров. Такой выбор технологической базы позволит обработать всю наружную поверхность заготовки и обеспечить высокую точность взаимного расположения обрабатываемых поверхностей.
Рисунок 1.8.5 Схема базирования используемая при обработке цилиндрических поверхностей хвостовика вилки.
При сверлении двух центровочных отверстий которые используются в качестве технологических баз при последующей механической обработке в качестве технологической базы будем использовать ось симметрии цилиндрического хвостовика заготовки. Для реализации такой схемы базирования применяем специальное приспособление из двух равномерно сходящихся призм. Применение такой схемы позволит обеспечить равномерное распределение припуска по диаметру хвостовика что упростит последующую обработку.
Рисунок 1.8.6 Схема базирования при сверление двух центровочных отверстий
9 Разработка технологического маршрута
Определив схемы базирования составим технологический маршрут обработки вилки скользящей.
На первом переходе мы делаем центровочные отверстия которые будут использоваться как технологические базы для последующих операций. На данной операции применим схему базирования изображённую на рисунке 1.8.6.
На втором переходе мы будем использовать схему базирования показанную на рисунке 1.8.5 которая позволит произвести черновое точение хвостовика.
На третьем переходе произведём чистовое точение цилиндрических поверхностей хвостовика используя туже схему базирования.
На 4 переходе фрезеруем наружные поверхности ушек в размер 1085-087 применяя схему базирования указанную на рисунке 1.8.4.
На 5 переходе выполним черновое зенкерование отверстий в ушках используя схему базирования изображённую на рисунке 1.8.3
На 6 переходе зенкеруем отверстия в ушках начисто используя ту же схему базирования.
переход – Фрезеруем шлицы червячной фрезой используя схему базирования изображённую на рисунке 1.8.2.
переход – Шевенгование шлицев с использованием той же схемы базирования.
переход – закалка ТВЧ и химическое фосфатирование
На 10 переходе – черновое растачивание отверстий в ушках используя схему базирования изображённую на рисунке 1.8.3.
На 11 переходе расточим отверстия в ушках начисто используя ту же схему базирования.
На 12 переходе расточим в отверстиях канавки под стопорные кольца используя ту же схему базирования.
На 13 переходе выполним раскатку отверстий в ушках используя схему базирования изображённую на рисунке 1.8.3
переход – Предварительное шлифование наружного диаметра шлицев и цилиндрической поверхности хвостовика используя схему базирования на рисунке 1.8.1
переход – Чистовое шлифование поверхностей хвостовика выдерживая размеры 62 и 54 используя схему базирования на рисунке 1.8.1
После расточных переходов перед операцией раскатки необходимо предусмотреть слесарную операцию для удаления заусенцев после сквозной обработки отверстий. Такая же операция нужна и после чернового нарезания шлицев червячной фрезой. И так как по требованиям чертежа необходимо выполнить термообработку то перед ней так же предусматриваем слесарную операцию и моечную. Когда вся механическая обработка вилки завершена необходимо провести технический контроль. Для более точного и правильного контроля после механической обработки желательно было бы притупить острые кромки после шлифования и промыть деталь после чего обдуть её сжатым воздухом.
При составлении маршрута следует учитывать следующие положения:
-каждая последующая операция должна уменьшить погрешность и улучшить качество поверхности;
-в первую очередь следует обрабатывать те поверхности которые будут служить технологическими базами для следующих операций;
-не рекомендуется совмещение черновой и чистовой обработки немерным инструментом на одном и том же станке.
Все переходы будем выполнять на разных операциях. Исключения составят операции зенкерования отверстий в ушках их будем обрабатывать на агрегатном станке. А также операции растачивания отверстий в ушках их будем так же вести на одном станке что позволит выдержать необходимые отклонения от перпендикулярности. Обработку этих поверхностей будем производить за одну установку подводя инструмент одновременно с двух сторон. На этих операциях целесообразно применить двухместные приспособления что позволит снизить время на обработку одной детали.
Технологический маршрут обработки детали выглядит следующим образом:
0 Токарная - автоматная
5 Токарная - автоматная
0 Горизонтально - фрезерная
5 Агрегатно-сверлильная
5 Круглошлифовальная
0 Круглошлифовальная
10 Разработка технологических операций.
На этом этапе окончательно определяется состав и порядок выполнения переходов в пределах каждой технологической операции (структура операции) производится выбор моделей оборудования станочных приспособлений режущих и измерительных инструментов.
В соответствии с габаритными размерами вилки скользящей (1085х245 мм) с массовостью её производства со структурой технологических операций с требуемой точностью обработки и применяемым режущим инструментом выбираем станочное оборудование (таблица 1.7).
Таблица 1.7 Ведомость станочного оборудования
Габаритные размеры мм
Категория ремонтной сложности
Токарный многорезцовый
Горизонтально-фрезерный
Агрегатно-сверлильный
Вертикально-сверлильный
Общий план обработки имеет следующий вид:
5 Центровальная (2912)
Центровать деталь с двух сторон
Режущий инструмент: свёрла центровочные комбинированные тип В ГОСТ1952-75
Измерительный инструмент: Глубиномер
0 Токарная - автоматная (1716Ц)
Точить цилиндрический и шлицевой хвостовики начерно выдерживая размеры 57-04 65-04
Точить фаски в размер 2x300 и 5x450.
Точить торец выдерживая размер 200 65 173 мм
Точить канавки выдерживая размеры 12 10 мм 7°
Режущий инструмент: резцы проходные Р6М5 ГОСТ 18818-73.
Измерительный инструмент: Скоба 57-04 скоба 65-04 ШЦ-I-125-01
5 Токарная - автоматная (1716Ц)
Чистовое точение цилиндрического и шлицевого хвостовика выдерживая размеры 548-02 628-02
Режущий инструмент: резцы проходные ГОСТ 18818-73.
Измерительный инструмент: Скоба 548-02 скоба 628-02 .
0 Горизонтально-фрезерная (6Р80)
Фрезеровать наружные плоскости ушек выдерживая размер 1085-087 Ra=125 мкм.
Режущий инструмент: набор фрез Р6М5 2245-4008 2245-4009.
Измерительный инструмент: скоба р-р 1085-087 ШЦ-I-125-01
ГОСТ 166-80 набор эталонов шероховатости 8490-4054.
5 Агрегатно-сверлильная (АБ3596)
Поз. 1. Черновое зенкерование отверстий в ушках выдерживая размер
Поз. 2. Чистовое зенкерование отверстий в ушках выдерживая размер 328±015
Режущий инструмент: зенкеры цельные Р6М5 с коническим хвостовиком 30 ГОСТ 12489-71 328 2320-4129-01
Измерительный инструмент: пробка 30 8133-4151-04 пробка 328±015 8133-4151-05.
0 Шлицефрезерная (5К301П)
Фрезеровать 22 эвольвентных шлица модулем 25 выдерживая размеры 67 77 51min 666min.
Режущий инструмент: фреза червячная 2520-4005.
Измерительный инструмент: ролики 5493 ГОСТ 2475-62 микрометр МК50 75 ГОСТ6507-78 индикатор ИЧ10кл1 ГОСТ577-68.
5 Слесарная (верстак)
Зачистить заусенцы на шлицах в местах выхода инструмента.
Режущий инструмент: напильник 2820-0017 ГОСТ 1465-69.
0 Шевинговальная (5702В)
Шевинговать 22 шлица модулем 25 в размер 664min.
Режущий инструмент: шевер 99-2570-4001.
Измерительный инструмент: комплексный калибр 8М4556 Пр. Микрометр МК50 75 ГОСТ 6507-78 Ролики 5493 ГОСТ 2475-62 скоба на размер 664min.
0 Моечная (моечная машина проходного типа)
Промыть деталь согласно инструкции
5 Термообработка по техпроцессу СГМ.
0 Алмазно-расточная (2706В)
Поз. 1. Расточить с двух сторон два отверстия предварительно выдерживая размер 345-01
Поз. 2. Расточить окончательно с двух сторон два отверстия выдерживая размер 35
Поз. 3. Расточить канавки в двух отверстиях выдерживая размеры 37+025 2+025 1005.
Режущий инструмент: резцы расточные Р6М5 ГОСТ18883-73 резец Р6М5 2120-4022-01 борштанга 6390-4048 борштанга 6390-4049 борштанга 7429-4029.013-02.
Измерительный инструмент: Нутромер НИ18 50 ГОСТ 9244-75 калибр на размер 37+025 02-8701-5115 калибр на размер 2+025 набор эталонов шероховатости 8490-4048.
Режущий инструмент: Напильник ГОСТ 1465-80
Раскатать с переустановкой два отверстия в размер 35.
Режущий инструмент: Раскатка 8Д-9697-01.
Измерительный инструмент: Нутромер НИ18 50 ГОСТ 9244-75 кольцо для настройки нутромера 35 8125-6077.
5 Круглошлифовальная (3М150)
Шлифовать поверхность наружного диаметра шлицев выдерживая размеры 623-006 60min. Шлифовать цилиндрическую поверхность выдерживая размеры 543-006 86min
Режущий инструмент: шлифовальные круги 400х80х305 24А25С2 СТ16К5354мс Акл1 ГОСТ 2424-83 400х100х305 24А25С СТ16К5 35мс Акл1 ГОСТ2424-83 с доработкой до размера по ширине 90 мм..
Измерительный инструмент: Скоба 623-006 Скоба 543-006 ИЧ10кл1 ГОСТ577-68.
0 Круглошлифовальная (3М150)
Шлифовать поверхности выдерживая размеры 54 62 86min 60min.
Режущий инструмент: шлифовальные круги 400х80х305 24А25С2 СТ16К5354мс Акл1 ГОСТ 2424-83 400х100х305 24А25С СТ16К5 35мс Акл1 ГОСТ2424-83 с доработкой до размера по ширине 90 мм.
Измерительный инструмент: Скоба 54 скоба 62 ИЧ10кл1 ГОСТ577-68.
Зачистить заусенцы и притупить острые кромки на механически обработанных поверхностях.
Режущий инструмент: напильник 2820-0023 ГОСТ 1465-69.
0 Моечная (моечная машина)
Промыть деталь в горячем содовом растворе согласно инструкции.
5 Контрольная (Стол ОТК)
Контролировать все размеры детали.
Измерительный инструмент: Образцы шероховатости 8490-4044 Калибр 8151-4501 Пр. калибр 8151-4501-01 Не. Нутромер НИ18 50 ГОСТ9244-75 Калибр 35+025 Спецштангенциркуль ШЦ-III-160-005 8900-4187 ШЦ-II-250-01 ГОСТ 166-89 Скоба 62 Скоба размер 664min скоба на размер 54 скоба размер 1085-087 калибр на размер 2+025 ШЦ-1-125-01 ГОСТ 166-89.
11 Расчёт припусков на обработку.
Припуски рассчитываем расчётно-аналитическим методом на две наиболее ответственные разнотипные поверхности: для поверхности 35 и для 54.
Рассчитаем припуск и межоперационные размеры для отверстия 35 мм.
Качество поверхности отливки Rz = 125 мкм h = 200. Размер отверстия в отливке 318±055
Технологический маршрут обработки данной поверхности следующий:
-ый переход: черновое зенкерование 13 кв. Rz = 100 мкм h=50мкм
-ой переход: чистовое зенкерование 11 кв. Rz = 63 мкм h=30мкм
-ий переход: черновое растачивание 9 кв. Rz = 25 мкм h=25мкм
-ый переход: чистовое растачивание 7 кв. Rz = 125 мкм h=10мкм
-ый переход: раскатка 7 кв. Rz = 5 мкм h =0 мкм
Пространственное отклонение формы поверхности заготовки рассчитываем по формуле:
где ρкор – коробление отверстия;
ρртб – погрешность расположения отверстия относительно технологической базы;
ρпер – погрешность перекоса отверстия.
Остаточное пространственное отклонение по переходам определяем по формуле
где Ку – коэффициент уточнения формы.
Погрешность установки детали на агрегатной операции определяем по формуле:
где Б – погрешность базирования
п =001мм – погрешность позиционирования инструмента
З =009 мм – погрешность закрепления при установке в приспособление с пневматическим зажимом.
В нашем случае Б =0095 мм и равна рассеиванию положения заготовки относительно жёсткого центра за счёт рассеивания диаметра центровочного отверстия.
Погрешность установки:
Остаточная погрешность установки:
у1 =006*0131=00079мм.
На операции расточки погрешность установки будет следующей:
б= 0095 мм; з= 009 мм.
У1= 006*0131=00079 мм.
Для операции раскатки:
Расчёт минимальных значений межоперационных припусков производится по следующей формуле:
Минимальные припуски по переходам:
переход. 2Zmin=2(125+200+)=2x506=1012 мкм
переход. 2Zmin=2(100+50+)=2x161=322 мкм
переход. 2Zmin=2(63+30+131)=2x224=448 мкм
переход. 2Zmin=2(20+25+79)=2х529=1058 мкм
h=001мм – величина наклёпа.
переход. 2Zmin=2(125-1)=2*135=27 мкм
переход. Dp.раскатка = 34992-0027 = 34965 мм
переход. Dp.чист.растач.= 34965-01058 = 34859 мм
переход. Dp.черн.растач.= 34859-0448 = 34411 мм
переход. Dp.чист.зенкер.= 34411-0322 = 34089 мм
переход. Dp.черн.зенкер.= 34089-1012 = 33077 мм
Допуски на размер принимаем по ГОСТ 7505-89 и заносим в таблицу 1.11.1.
переход. Dma Dmin= 34967 мм
переход. Dma Dmin= 34965-0025=3494 мм
переход. Dma Dmin = 34859-0062=34797 мм
переход. Dma Dmin = 34411-016=34251 мм
переход. Dma Dmin = 34089-039=33699 мм
Заготовка Dma Dmin = 33077-11=31977 мм
Минимальные и максимальные предельные отклонения припусков:
переход. 2ZmaxПР= 34967-3494=0027 мм
ZminПР= 34992-34965=0027 мм
переход. 2ZmaxПР= 3494-34797=0143 мм
ZminПР= 34965-34859=0106 мм
переход. 2Zmax ПР= 34797-34251=0546мм
Zmin ПР= 34859-34411=0448 мм
переход. 2Zmax ПР= 34251-33699=0552 мм
Zmin ПР= 34411-34089=0322 мм
переход. 2Zmax ПР= 33699-31977=1722 мм
Zmin ПР= 34089-33077=1012 мм
Предельные значения общих припусков 2ZОmin 2ZОmax определим суммируя промежуточные припуски:
ZОmin = 0027+0106+0448+0322+1012=1915 мм
ZОmax = 0027+0143+0546+0552+1722=299 мм
Общий номинальный припуск 2Zо.ном.= 2ZОmin+ВЗ-ВД
где ВЗ и ВД – соответственно нижние отклонения заготовки и готовой детали по ГОСТ 7505-89.
Zо.ном.= 1915+055-0008=2457 мм
Зная значение 2Zо.ном. находим номинальный диаметр заготовки:
Dз.ном = Dд.ном. - 2Zо.ном. =35-2457=32543 мм
Проверим правильность произведённых расчётов по уравнениям:
ZmaxПР - 2ZminПР = Di-1- Di
ZОmax - 2ZОmin = Dз- Dд
Для рассматриваемого случая проверка точности произведённых расчётов имеет следующие результаты:
переход. 1722-1012=11-039 т.е. 071=071
переход. 0552-0322=039-016 т.е. 023=023
переход. 0546-0448=016-0062 т.е. 0098=0098
переход. 0143-0106=0062-0025 т.е. 0037=0037
переход. 0027-0027=0025-0025 т.е. 0=0
Общий припуск: 299-1915=11-0025 т.е. 1075=1075
Следовательно расчёты межоперационных припусков произведены правильно. Все расчёты параметров припусков сведём в таблицу 1.8.
Таблица 1.8 Параметры припусков на размер 35 мм.
Технологические переходы обработки поверхности 35
Элементы припуска мкм
Расчётный припуск 2Zmin мкм
Расчётный размер Dp мм
Допуск на размер d мкм
Предельный размер мм
Предельные значения припусков мкм
(черн. зенкерование)
На основании данных таблицы 1.8 строим схему графического расположения припусков и допусков на обработку 35 мм.
Рисунок 1.11.1 Схема графического расположения припусков и допусков на обработку 35 мм.
Рассчитаем припуски для обработки поверхности 54.
переход: черновое точение 12 кв. Rz=100мкм h=50мкм;
переход: чистовое точение 10 кв. Rz=63мкм h=30мкм;
переход: предварительное врезное шлифование 9 кв. Rz=20мкм h=20мкм;
переход: чистовое врезное шлифование 7 кв. Rz=25мкм h=5мкм
где ρКОР – отклонение учитывающие коробление отливки;
ρСМ – отклонение учитывающие смещение оси обрабатываемой поверхности относительно оси центров;
ρЦ – погрешность центрирования.
Где l=1842=92 мм так как максимальная кривизна возможна посередине хвостовика.
- определяется как допус формы и расположения элементов отливки
где ц = 12мм – допуск на диаметральный размер поверхности используемой в качестве базовой на центровальной операции.
После термообработки:
где ρк=075мм – корабление детали из-за термообработки.
Погрешность установки детали У =0 так как установка осуществляется в центра.
переход. 2Zmin=2(125+200+771)=2x1096=2192 мкм
переход. 2Zmin=2(100+50+46)=2х196=392 мкм
переход. 2Zmin=2(63+30+750)=2x843=1686 мкм
переход. 2Zmin=2(20+20+225)=2х625=125 мкм
переход. dp.чист.шлиф.= 5392 мм
переход. dp.черн.шлиф.= 5392+0125=54045 мм
переход. dp.чист.точ.= 54045+1686=55731 мм
переход. dp.черн.точ.= 55731+0392=56123 мм
Заготовка dp. заготовка = 56123+2192=58315 мм
Допуски на размер принимаем по ГОСТ 7505-89 и заносим в таблицу 1.11.2.
переход. dm dmax=5392+003=5395мм
переход. dm dmax= 54045+0074=54119 мм
переход. dm dmax= 5573+012=5585 мм
переход. dm dmax= 561+03=564 мм
Заготовка dm dmax= 583+12=595 мм
переход. 2Zmin ПР= 54045-5392=0125 мм
Zmax ПР= 54119-5395=0169 мм
переход. 2Zmin ПР= 5573-54045=1685 мм
Zmax ПР= 5585-54119=1731 мм
переход. 2Zmin ПР= 561-5573=037 мм
Zmax ПР= 564-5585=055 мм
переход. 2Zmin ПР= 583-561=22 мм
Zmax ПР= 595-564=31 мм
ZОmin = 0125+1685+037+22=438 мм
ZОmax = 0169+1731+055+31=555 мм
Общий номинальный припуск 2Zо.ном.= 2ZОmin+HЗ-HД
где HЗ и HД – соответственно верхние отклонения заготовки и готовой детали по ГОСТ 7505-89.
Zо.ном.= 438+06-008=49 мм
dз.ном = dд.ном. + 2Zо.ном. = 54+49=589 мм
ZmaxПР - 2ZminПР = di-1- di
ZОmax - 2ZОmin = dз- dд
переход. 0169-0125=0074-0030 т.е. 0044=0044
переход. 1731-1685=012-0074 т.е. 0046=0046
переход. 055-037=03-012 т.е. 018=018
переход. 31-22=12-03 т.е. 09=09
Общий припуск: 555-438=12-003 т.е. 117=117
Следовательно расчёты межоперационных припусков произведены правильно. Все расчёты параметров припусков сведём в таблицу 1.9.
Таблица 1.9 Параметры припусков на размер 54 мм.
Технологические переходы обработки поверхности 54.
Расчётный размер dp мм
На основании данных таблицы 1.9. строим схему графического расположения припусков и допусков на обработку 54 мм.
Рисунок 1.11.2 Схема графического расположения припусков и допусков на обработку 54 мм.
12 Расчёт режимов резания.
Рассчитаем режимы резания для двух разнохарактерных операций по эмпирическим формулам теории резания [3]:
Операция 010 токарная-автоматная точить 564 мм.
Инструмент: проходной резец Т15К6
глубина резания t =08 мм
подача на оборот S =08 ммоб
стойкость инструмента Т =60 мин
KMV-коэффициент учитывающий качество обрабатываемого материала
KПV - коэффициент отражающий состояние поверхности заготовки
KИV - коэффициент учитывающий качество материала инструмента
частота вращения шпинделя n мин-1
принимаем стандартное значение n=800 мин-1
действительная скорость резания
Где Кр=КмрКfрКgрКlрКrр=
Операция 060 алмазно-расточная расточить 2 отверстия 34797 мм.
Инструмент: Расточной резец Т15К6
глубина резания t =0546 мм
подача на оборот S =01 ммоб
стойкость инструмента Т =50 мин
где KV=KMVKПVKИV=203*1*1=203
KИV - коэффициент учитывающий качество материала инструмента
Принимаем по паспарту станка стандартное значение n=2000 мин-1
На все остальные операции режимы резания определим по нормативам приводимым в технических справочниках и полученные результаты расчетов режимов резания сведём в таблицу 1.10.
Таблица 1.10 Сводная таблица режимов резания.
Наименование операции или перехода
Токарная - автоматная
Горизонтально - фрезерная
Агрегатно-сверлильная
растачивание канавок
13 Определение норм времени на операции.
При массовом производстве норма штучного времени определяется по формуле:
где: То—основное (машинное) время обработки детали мин;
Тв—вспомогательное время на операцию (время на установку и снятие детали подвод и отвод инструмента время на управление станком и т.д.) мин;
Тобс—время на техническое и организационное обслуживание рабочего места (время на замену затупившегося инструмента время на уборку рабочего места в конце работы) мин;
Тотд—время на отдых и личные надобности мин.
где: Тус—время на установку и снятие детали мин;
Тзо—время на закрепление и открепление детали мин;
Туп—время на приемы управления мин;
Тиз—время на измерение детали мин.
где: Ттех—время на техническое обслуживание рабочего места мин;
Торг—время на организационное обслуживание рабочего места мин.
Оперативное время Топ:
В массовом производстве Ттех определяется по следующей формуле:
где: tсм—время на смену инструментов и подналадку станка мин;
Т—период стойкости при работе одним инструментом или расчетный период стойкости лимитирующего инструмента при многоинструментальной обработке мин.
Время на организационное обслуживание определяется в процентах от оперативного времени.
где: П—затраты времени на отдых в процентном отношении к оперативному.
Расчёт норм времени проводим подробно для одной токарной - автоматной операции 010.
Тус=01 мин – установка и снятие детали в центрах;
Тзо=0024 мин – закрепление и открепление детали с помощью пневмо-зажима рукояткой;
Туп=001 мин—время на включение станка кнопкой.
Тиз=038 мин—время на измерение скобами и штангенциркулем.
Вспомогательное время:
Тв=01+0024+001+038=0514 мин.
Топ=0162+0514=0676 мин
Время на смену резца tсм=24 мин тогда время на техническое обслуживание:
Затраты времени на организационное обслуживание в процентном отношении к оперативному равно 21% тогда:
Торг=0162·21100=0003 мин.
Время на обслуживание рабочего места:
Тобс=0056+0003=0059 мин.
Определяем затраты времени на отдых Пот=65%. Время на отдых:
Тотд=0059·65100=00038 мин.
Тшт=0162+0514+0059+0038=0773 мин.
Нормы времени по остальным операциям сведём в таблицу 1.11
Таблица 1.11 Технические нормы времени по операциям мин.
Наименование операции
14 Выявление и расчёт технологической размерной цепи.
При растачивании отверстий в ушках принцип единства баз для размера определяющего положение оси отверстий 220мм не соблюдается так как установка осуществляется в центра в специальном приспособлении. А1 – глубина центровочного отверстия; А2 – погрешность базирования за счёт колебаний диаметра центровочного отверстия;- является настроечным размером инструмента.
Рисунок 1.14.1 – размерная цепь.
Необходимо решить проектную задачу то есть по номиналу допуску и предельным отклонениям исходного звена определить аналогичные параметры составляющих звеньев. Применим способ равноточных допусков.
Аоmin=2774 мм Аоmax=2826 мм.
Середина поля допуска ЕоСР=0 мм.
Величина единицы допуска для каждого составляющего звена:
где АСТ.j – среднее геометрическое границ интервала размеров
в который попадает Аj.
Среднее число единиц поля допуска приходящееся на составляющее звено:
Значение аСР находится между 12 и 13 квалитетами. В качестве корректирующего звена выбираем А1. Назначаем допуски на
составляющие звенья:
ТА1=015 мм по 12 квалитету;
ТА2=012 мм по 12 квалитету;
ТА3=025 мм по 12 квалитету.
На увеличивающее звеноотклонения назначаем как на основное отверстие ES3=TA3=025 мм; EI3=0. середина поля допуска
Е3СР=0125 мм. Предельные размеры:
A3max=A3+ES=435+025=4375 мм.
Можно записать А3=435+025 мм.
На уменьшающее звено А2 отклонения назначаем как на основной вал e es2=0. середина поля допуска
Е2СР=006 мм. Предельные размеры:
A2max=A2-es=0095-0=0095 мм.
Можно записать А2=0095-0.12 мм.
Середина поля допуска корректирующего звена А1:
Е1СР=Е3СР- Е2СР -ЕDСР=0125-006-0=0065 мм
Определим предельные отклонения корректирующего звена А1:
ES1=E1CP+TA12=0065+0152=014 мм;
EI1=ES1-TA1=014-015=-001 мм.
Можно записать А1=10 мм.
Назначенные допуски технологически достижимы на выбранном оборудовании при принятых методах обработки поверхностей. Значит данные технологические переходы и принятая схема базирования обеспечивают требуемую точность замыкающего звена.
15 Определение количества оборудования и его загрузка.
Для поточного производства количество станков S определяется по формуле:
Тшт—штучное время обработки изделия мин;
F—действительный годовой фонд времени работы оборудования час.
Коэффициент загрузки оборудования:
где: Sпр—принятое количество станков.
На основании рассчитанных коэффициентов строим график загрузки оборудования.
Рисунок 1.12 График загрузки оборудования.
16 Уточнённый расчёт типа производства.
Уточненный расчет типа производства основывается на определении коэффициента закрепления операций Кзо:
где: О—количество всех различных технологических операций выполненных в течении месяца;
Р—число рабочих мест необходимых для выполнения месячной программы.
Согласно ГОСТа для массового типа производства Кзо=1.
Число рабочих мест для выполнения определенной i-ой операции определяем по формуле:
где: Nм—месячный объем выпуска детали;
Тшт—штучное время на выполнение определенной операции мин;
Fм—месячный фонд времени работы оборудования (335 час);
Кв—коэффициент выполнения норм времени. Кв=11
Рассчитанное число рабочих мест округляем до ближайшего большего целого числа Рi. Коэффициент загрузки данных рабочих мест выполняемой операцией:
Количество операций выполняемых на этом рабочем месте при его нормативной загрузке определяем по формуле:
где: hн=065—нормативный коэффициент загрузки для массового производства.
Общее количество операций выполняемых на всех рабочих местах проектируемого техпроцесса и общее количество рабочих мест определяется как сумма всех операций и сумма всех рабочих мест соответственно.
Результаты расчетов сведем в таблицу.
Таблица 1.12 Определение типа производства.
Определяем коэффициент закрепления операций:
Так как Кзо=2 10 то принимаем крупносерийное производство.
Определим такт выпуска продукции t:
где: F—действительный годовой фонд времени работы оборудования при 2-ух сменной работе (4015 час).
Расчёт и проектирование средств технологического оснащения.
1 Расчет и проектирование приспособления для алмазного растачивания.
1.1 Служебное назначение и описание приспособления.
Проектируемое приспособление используется на операции алмазного растачивания отверстий в ушах вилки.
Приспособление позволяет обрабатывать одновременно две заготовки.
Принцип работы приспособления заключается в следующем:
Шток гидроцилиндра под действием давления перемещается а соответственно перемещается коромысло и вместе с ним два центра которые прижимают заготовки. Гидроцилиндр приводится в действие от гидропривода станка.
Базирование заготовки на приспособление осуществляется в центра. В призме предусмотрены планки позволяющие фиксировать угловое положение заготовок относительно оси. Фиксируются же эти планки при помощи дополнительного гидроцилиндра. Приспособление устанавливается на станок при помощи шпонок и закрепляется болтами.
1.2 Расчет сил зажима заготовки.
Расчет сил зажима сводится к решению задачи статики на равновесие твердого тела под действием внешних сил. Величина сил зажима определяется из условия равновесия всех сил при полном сохранении контакта технологических баз обрабатываемой заготовки с установочными элементами приспособления и невозможности ее сдвига или поворота в процессе обработки.
Исходные данные для силового расчета. Производство крупносерийное; составляющая силы резания в вертикальном направлении Рz = 792 H; давление газа в пневмоцилиндре Р = 05 МПа ; материал заготовки – Сталь 40.
Рисунок 2.1—Схема для
определения силы зажима заготовки.
Произведём расчёт сил действующих на заготовку при её обработке в приспособлении. Для этого составим уравнение равновесия сил действующих на заготовку (без учета веса заготовки):
Преобразуем полученные выражения:
Подставив численные значения получим:
R=792*17399(39*08660)=408 Н
Q=792+792*17399*05(39*08660)=996 Н
Силу действующую на шток пневмоцилиндра находим из следующего выражения:
Где К=К1*К2*К3*К4*К5*К6 —коэффициент запаса
К1=15 – гарантированный коэффициент запаса;
К2=12 – коэффициент учитывающий колебание силы резания из-за непостоянства припуска;
К3=11 – учитывает увеличение силы резания в результате износа инструмента;
К4=10 – учитывает непостоянство силы зажима;
К5=10 – учитывает удобство расположения рукояток;
К6=10 – учитывает наличие момента стремящегося повернуть заготовку на плоскости.
К=15*12*11*10*10*10=198 тогда
Pпр=198·2·996=3944 H.
Исходя из полученной силы Pпр находим параметры пневмоцилиндра:
Принимаем стандартный пневмоцилиндр d=40мм.
Тогда действительная сила зажима:
1.3 Расчет приспособления на точность.
Цель расчета приспособления на точность заключается в определении требуемой точности изготовления приспособления по выбранному точностному параметру и задании допусков размеров деталей и элементов приспособления.
Расчет точности изготовления приспособления из условия обеспечения размера 28±026 мм.
Определяем погрешность изготовления приспособления ПР :
В нашем случае Б =0095мм и равна рассеиванию положения заготовки относительно жесткого центра за счёт рассеивания диаметра центрового отверстия.
Определяем погрешность закрепления. Для данного случая:
Погрешность установки приспособления на станке:
где m-длина шпонки m=20 мм
SMAX-максимальный зазор в сопряжении шпонка-стол станка (Н7g6) мкм
L - расстояние между шпонками мм
Погрешность от перекоса (смещения) инструмента.
Так как в приспособлении отсутствуют направляющие элементы:
Погрешность от изнашивания установочных элементов. Изнашивание центров можно определить по формуле:
где: 1 - постоянная зависящая от вида установочных элементов и условий контакта 1 = 0.3;
N - количество контактов заготовки с опорой за год
После подстановки получим:
и = 0.5·0.3×800000.5 = 424 мкм;
Погрешность от изнашивания установочных элементов принимаем:
При этом в ТУ на эксплуатацию приспособления указать что проверку приспособления и ремонт (замену) установочных элементов необходимо производить 2 раза в год.
Определяем экономическую точность обработки = 33 мкм.
Принимаем значения коэффициентов и определяется погрешность изготовления приспособления ПР.
Коэффициент учитывающий отклонение рассеяния значений составляющих величин от закона нормального распределения: kт = 1.2.
Коэффициент учитывающий уменьшение предельного значения погрешности базирования при работе на настроенных станках: kт1 = 0.8.
Коэффициент учитывающий долю погрешности обработки в суммарной погрешности вызываемой факторами не зависящими от приспособления: kт2 = 0.6 .
Допуск на изготовление детали = 0062 мм.
На основании расчета можно сделать вывод что допуск на пересечение осей отверстий под подшипники и швостовика составляет 0242 мм.
1.4 Расчет приспособления на прочность.
Проанализировав конструкцию приспособления можно прийти к выводу что одним из наиболее нагруженных звеньев является ось (поз. ) передающая силу зажима от пневмоцилиндра траверсе.
Составим схему силового нагружения и произведем расчет оси на срез и смятие.
Рисунок 2.2 – Схема приложенных сил
На рисунке сила R=Р2=2041 Н – сила реакции со стороны заготовки равная действительной силе зажима.
Условие обеспечивающее работу оси на срез
где [s]cp =320 МПа – допустимое напряжение среза для материала оси сталь 40.
[s]cp=025sТ=025·320=80 МПа
где d – диаметр рассчитываемой оси мм.
Условие sср=203[s]cp=80 МПа выполняется.
Условие прочности оси на смятие:
где [s]СМ=120 МПа – допустимое напряжение смятия.
где АСМ – площадь смятия мм2.
где b – длина поверхности смятия мм.
Условие sСМ=255[s]СМ=120 МПа выполняется.
2 Служебное назначение и описание контрольного приспособления.
Проектируемое контрольное приспособление предназначено для контроля допуска перпендикулярности оси отверстий под подшипники и цилиндра швостовика детали. Контроль осуществляется при помощи оправки и индикатора.
Приспособление состоит из плиты с центрами и стойкой на которую устанавливаются деталь с оправкой.
Порядок проведения контроля:
Вставить оправку в деталь.
Установить деталь с оправкой в центра и стойку.
Выставить показания индикатора на ноль.
Снять деталь с оправкой повернуть вокруг оси на 180 и снова закрепить в центрах.
2.1 Расчет приспособления на точность.
Для того чтобы контрольное приспособление обеспечивало правильность контроля требуется чтобы его погрешность была не более 13 допуска на контролируемый параметр.
где i - суммарное значение погрешностей в процессе измерения.
Погрешности в процессе измерения:
б - погрешность базирования;
З - погрешность закрепления;
И - погрешность в результате износа установочных элементов;
пер. мех - погрешность передаточных механизмов;
изм. средства - погрешность средств измерения (индикатора).
б – так как оправка устанавливается в отверстие с зазором то возникнет перекос равный половине максимального зазора. Цапфы оправки выполнены по 6кв: es=-005ei =-007. Тогда Smax=0062мм
З = 0 так в нашем случае закрепление детали на контрольном приспособлении осуществляется в центрах;
И = 0 так как износ оправки по всей длине одинаковый и при установке контрольного приспособления на деталь индикатор каждый раз выставляется на “0”;
изм. средства = 0005 так как в качестве средства измерения используется индикатор часового типа (ИЧ) у которого цена деления равна 0005мм.
что меньше допустимой погрешности ΔПР = 0067мм.
В данном курсовом проекте на основе базового технологического процесса мы разработали технологический процесс изготовления детали “Вилка скользящая”.
Предложенный технологический процесс является более эффективным и прогрессивным по сравнению с базовым.
В проекте был принят другой метод получения заготовки был изменён маршрут механической обработки.
Таким образом в ходе выполнения курсового проекта закрепили теоретические знания ознакомились со специальной технической литературой научились самостоятельно разрабатывать технологические процессы.
Горбацевич А.Ф. Шкред В.А. Курсовое проектирование по технологии машиностроения - Мн: Высшая школа 1983г. 256с.
Справочник технолога-машиностроителя под редакцией Косиловой А.Г. том 1. Машиностроение 1985г. 656с.
Справочник технолога-машиностроителя под редакцией Косиловой А.Г. том 2. Машиностроение 1985г. 496с.
Проектирование технологических процессов механической обработки в машиностроении (под редакцией Бабука В.В.) Мн. Высшая школа 1987г. 260с.
Методические указания по расчёту припусков расчётно-аналитическим методом Брест 1996г.
Методические указания по нормированию технологических процессов для выполнения курсового и дипломного проектирования для студентов специальности Т03.01. Брест 1999г.
Методические указания по выполнению курсового проекта по курсу “Технология машиностроения” для студентов специальности Т 03.01.00 Брест 1996г.
Методические указания по расчету припусков расчетно-аналитическим методом. Брест 2000г.
спецификация контрольное 1.doc
КП Т03.01.743.15.001
КП Т03.01.743.15.002
КП Т03.01.743.15.003
КП Т03.01.743.15.004
КП Т03.01.743.15.005
КП Т03.01.743.15.006
КП Т03.01.743.15.007
КП Т03.01.743.15.008
КП Т03.01.743.15.009
КП Т03.01.743.15.010
КП Т03.01.743.15.011
КП Т03.01.743.15.012
КП Т03.01.743.15.013
КП Т03.01.743.15.014
КП Т03.01.743.15.015
КП Т03.01.743.15.016
Пружина ГОСТ 13767-68
Рукоятка ГОСТ 8924-69
Станочная приспособа.cdw

АННОТАЦИЯ.doc
Учреждение образования «Брестский государственный технический университет»
В курсовом проекте дано описание объекта производства его конструктивные и технологические особенности. Произведен анализ служебного назначения вилки скользящей анализ ее технологичности и обоснован выбор метода получения заготовки что позволило повысить коэффициент использования металла и снизить себестоимость заготовки. Разработан технологический процесс изготовления детали. Установлена последовательность переходов дано обоснование выбора технологических баз выполнены аналитические расчеты припусков и режимов резания. Произведен выбор типов станков и определены коэффициенты его загрузки.
Спроектировано специальное расточное приспособление на станок 2706В для растачивания отверстий под подшипники 35; контрольное приспособление.
Заготовка.cdw

КП Т03.01.743.11.000 00
Допускается изготовление из стали 45 ГОСТ 1050-88
Твёрдость 217 255 HB.
Неуказанные литейные уклоны по ГОСТ 26645-85.
Неуказанные радиусы 2 4мм.
Неуказанные отклонения по ГОСТ 26645-85.
Точность отливки 8-4-13-10 ГОСТ 26645-85.
Группа сложности отливки 3.
В узлах скопления металла допускается внутренние усадочные раковины и рыхлоты.
На необрабатываемых поверхностях отливки допускаются без исправлений:
- раковины по найдольшему измерению не более 4 мм
глубиной не более 2мм в
количестве не более 4 штук на деталь;
- ситовидная пористость не более 6%.
На подлежащих механической обработке поверхностях отливки допускаются
поверхностные дефекты
не превышающие по велечине припуск на механическую
Операционные эскизы1.cdw

Горизонтально-фрезерная
Агрегатно-сверлильная
Приспособление для расточки.cdw

Деталь.cdw

Профильный угол исходного контура
Смещение исходного контура
Диаметр делительной окружности
Диаметр перехода эвольвенты
Шероховатость поверхности
боковых поверхностей шлица
ТВЧ h2 4 от пов.К; 44 55 HRCэ
Сталь 40 ГОСТ1050-88
КП Т03.01.743.11.000 00
217 255 НВ кроме указанной.
Материал заменитель Сталь 45 ГОСТ 1050-88.
Неуказанные литейные радиусы 2 3 мм.
Точность отливки 8-4-13-10 ГОСТ 26645-85.
Остальные технические требования по ГОСТ 26358-84 и
Разность размеров толщин ушек 1
Ось двух диаметрально расположенных шлицев А и ось Г должны
лежать в одной плоскости. Отклонение не более
Неуказанные предельные отклонения размеров: Н15
*Размер обеспечивается инструментом.
**Измерять вдоль шлица.
Покрытие Хим. фос. антифрикционное h 0
КМФ ГОСТ 212-76 на длину L
Контрольное приспособление.cdw

Операционные эскизы2.cdw

Агрегатно-сверлильная
Вертикально сверлильная
Рекомендуемые чертежи
- 10.05.2019
- 24.01.2023
- 24.01.2023
- 13.12.2022
- 24.01.2023