Шпиндельный узел станка-гексапода и механизм зажима инструментальной оправки




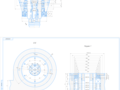
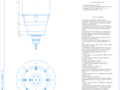
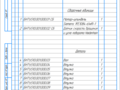
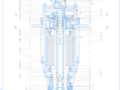
- Добавлен: 25.01.2023
- Размер: 4 MB
- Закачек: 1
Описание
Состав проекта
![]() |
![]() ![]() ![]() |
![]() ![]() ![]() ![]() |
![]() ![]() ![]() ![]() |
![]() ![]() ![]() ![]() |
![]() ![]() ![]() ![]() |
Дополнительная информация
общий вид.cdw

лист 3.cdw

спецификация1.spw

Мотор-шпиндель.cdw
