Станок 2А 135




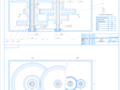
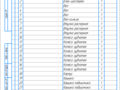
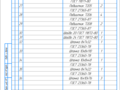
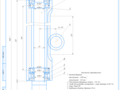
- Добавлен: 25.01.2023
- Размер: 522 KB
- Закачек: 0
Описание
Состав проекта
![]() |
![]() ![]() ![]() ![]() |
![]() ![]() ![]() ![]() |
![]() ![]() ![]() ![]() |
![]() ![]() ![]() ![]() |
![]() ![]() ![]() ![]() |
![]() ![]() ![]() ![]() |
![]() ![]() ![]() ![]() |
![]() ![]() ![]() |
Дополнительная информация
Спец_кс 2.cdw

Спец_кс 1.cdw

Лист 3 (шпиндель).cdw

максимальная - 2190 мин
мимнимальная - 140 мин
Максимальный вращающий момент - 274 Н
Гнездо для установки инструмента - конус диаметра 31
Наибольший диаметр сверления 35 мм
Технические требования
* Размеры для справок
Отклонение от соосности опор шпинделя не более 30 мкм
Радиальное биение конического отверстия шпинделя не
Осевое биение шпинделя не более 10 мкм
Торцевое биение опорного конца шпинделя не более 15 мкм
Для смазки подшипников и трущихся деталей применять
Лист 2 (кор. скор.).cdw

Количество скоростей
Технические требования
Отклонение от соосности не более 0
Радиальное биение валов не более
Осевое биение валов не более 0
* Размеры для справок
Натяг в подшипниках поз. 27
печивается подгонгкой распорными втул-
При сборке обеспечить плавное вращение
Трущиеся части и подшипники смазать
смазкой УС-2 ГОСТ 10701-75
Техническая характеристика
Спец ВО.cdw

Лист 1 (общ. вид).cdw

Частота вращения шпинделя
вертикально-сверлильного
Кинематическая схема
* Размеры для справок
Станок установить на индивидуальный фундамент
При установке станка обеспечить параллельность рабочего стола
Мощность электродвигателя главного движения
Наибольшее вертикальное перемещение стола
Наибольший ход шпинделя
Наибольший диаметр сверления
Технические требования
Технические характеристики станка
График частот вращения привода
Спец шпинд.cdw

Моя П.З..doc
Обоснование технических характеристик станка .3
Кинематический расчёт привода 5
Геометрический и силовой расчёт привода 7
Определение модуля зубчатых колёс и
геометрический расчёт привода .9
Определение фактических контактных напряжений и
напряжений изгиба зубьев зубчатых колёс привода.
Выбор материала и термообработки 15
Расчёт валов коробки скоростей коробки .18
Проверочный расчёт подшипников 26
Расчёт шпиндельного узла ..28
Список используемой литературы .31
Техническое задание.
Модернизировать станок модели 2А135.
Рассчитать и сконструировать шпиндель станка на опорах качения.
Материал обрабатываемых изделий – цветные сплавы.
Материал режущего инструмента – алмазный.
Серийность производства – мелкосерийное.
Обоснование технической характеристики станка.
1 Определение предельных диаметров сверла и рациональных режимов резания.
Для заданной модели вертикально-сверлильного станка 2А135 наибольший диаметр сверления Dб = 35 мм тогда наименьший диаметр сверла:
При сверлении в сплошном материале глубина резания:
где D – диаметр сверла d – диаметр отверстия в заготовке.
Наибольший диаметр сверления Dб для универсальных вертикально и радиально-сверлильных станков является их основным параметром и должен соответствовать ГОСТ 1227-72. При зенкеровании и развёртывании глубина резания равна величине припуска на сторону tм = 05 мм tб = 2 мм. При чистовом развёртывании отверстий диаметром 5 80 мм припуск на сторону tм= 005 мм tб = 025 мм. При черновом развёртывании припуск на сторону tм= 01 мм tб = 02 мм.
Наибольшая и наименьшая подачи (для самого мягкого материала (цв. металлы) при работе со свёрлами наибольшего и наименьшего диаметра) по табл. 1.11 [1]:
Наибольшая и наименьшая скорости резания при сверлении:
сверления и характеристику инструмента;
Т – стойкость инструмента;
D - диаметр инструмента;
НВ – твёрдость обрабатываемого материала (табл. 1.25 [1])
Предельные значения частот вращения шпинделя:
Диапазоны регулирования привода главного движения и подачи:
2 Определение силовых параметров процесса резания и эффективной мощности привода.
Наибольшее осевое усилие действующее при сверлении:
Определим значение наибольшего крутящего момента при сверлении самого твёрдого материала:
Значения коэффициентов С1 z y n определяем по табл. 1.32 [1]
Мощность электродвигателя главного движения определяется по наибольшей эффективной мощности резания:
где: k – коэффициент перегрузки станка k = 12 13.
– КПД привода с вращательным главным движением ( = 07 085).
Так как модернизируемый станок имеет только один электродвигатель то при определении его мощности должна быть учтена мощность расходуемая также и в цепях привода подачи и вспомогательных движений. Мощность потребляемая на движение подачи обычно невелика и составляет от мощности привода главного движения для сверлильных станков 4 5%. Следовательно мощность электродвигателя станка будет равна:
По найденной мощности выбираем двигатель типа АИР100L2 для которого: Nдв = 55 кВт
Кинематический расчёт привода.
1 Определение числа скоростей привода
По известным значениям Rn (здесь Rv) и знаменателю геометрического ряда φ (примем φ = 141) находим число скоростей Z привода по формуле [1]:
Число скоростей принимаем Z = 9 как и в коробке скоростей модернизируемого станка 2А135.
где D1 = 140 мм D2 = 178 мм
Z1 = 27 Z2 = 34 Z3 = 21 Z4 = 55 Z5 =48 Z6 = 61 Z7 = 34 Z8 = 17 Z9 = 65
Z10 = 35 Z11 = 48 Z12 = 68 Z13 = 34 Z14 = 50
Зная числа зубьев шестерён определим передаточные числа:
Числа зубьев колёс привода.
Зная частоту вращения электродвигателя и передаточные числа всех ступеней построим график частот вращения привода:
График частот вращения привода.
Геометрический и силовой расчёт привода.
Так как для проектных расчетов нас интересует наиболее нагруженный режим то рассчитываем силовые и кинематические параметры для наименьших угловых скоростей валов.
Для расчётов примем [2]:
з = 097 – КПД зубчатой передачи;
м = 098 – КПД муфты;
пк = 099 – КПД подшипников качения;
рп = 088 – КПД клиноремённой передачи.
Определение модуля зубчатых колёс и геометрический расчёт привода.
1 Определение модуля зубчатых колёс
Модули зубчатых колёс рассчитываем исходя из прочности зуба на изгиб и усталости поверхностных слоёв по формулам:
где: k = kд kк kр = 24 – коэффициент учитывающий изменение нагрузки по
сравнению с номинальной от действия различных
где: kд 2 – коэффициент динамичности нагрузки;
kк 12 – коэффициент концентрации нагрузки;
kр 1 – коэффициент режима.
N – номинальная передаваемая мощность вала с шестерней;
n – минимальная частота вращения шестерни;
z – число зубьев шестерни;
y = (01 013) – коэффициент формы зуба;
= (6 10) – коэффициент ширины;
доп – допускаемое напряжение контактной нагрузки;
Rв – допускаемое напряжение изгибной нагрузки.
Первоначально предполагая что зубчаты колёса изготовлены из стали 40Х (в = 900 МПа т = 750 МПа) со средней твёрдостью шестерни НRCср = 45 (улучшение и закалка ТВЧ) по известным из курса «Детали машин» формулам [2] примем доп и Rв равными :
Из полученных модулей выбираем наибольший и округляем его до ближайшего стандартного значения и принимаем для всех пар данной групповой передачи.
Первая ступень (зацепление 21:61 валы I – II):
Вторая ступень (зацепление 34:48 валы II – III):
Третья ступень (зацепление 17:68 валы III – IV):
1 Расчёт геометрических параметров зубчатых колёс
Делительный диаметр: мм
Диаметр вершин зубьев: мм
Диаметр впадин зубьев: мм
Диаметр впадин зубьев: м
Ширина шестерён ступени:
Ширину колёс данной ступени конструктивно принимаем на 3 – 5 мм меньше ширины шестерён.
Ширина шестерни ступени:
Ширину колеса данной ступени конструктивно принимаем на 3 – 5 мм меньше ширины шестерни.
2 Определение степени точности зубчатых колёс
Определяем степень точности зубчатых колёс данной группы исходя из допускаемой окружной скорости по таблице 3.34 [1]:
Для проектируемого привода окружная скорость шестерни Z1 равна:
Назначаем 7-ую степень точности.
2 Определение диаметров валов
Диаметры валов рассчитываем приближённо по формуле:
М = Т – крутящий момент равный вращающему моменту на валу;
[] – допускаемое напряжение на кручение
Определение фактических контактных напряжений и напряжений изгиба зубьев зубчатых колёс привода. Выбор материала и термообработки.
Контактные напряжения н в зацеплении определим по формуле [1]:
где: K – вспомогательный коэффициент (для прямозубых колес K = 438);
Ft = 2T103d – окружная сила в зацеплении;
Kнα = 1 (для прямозубых колёс) – коэффициент учитывающий распреде-
ление нагрузки между зубьями;
Kн = 1 – коэффициент концентрации нагрузки [2];
Kнv – коэффициент концентрации нагрузки зависящий от окружной ско-
Напряжения изгиба F для шестерни и колеса определим по формулам [1]:
где: YF1 и YF2 – коэффициенты формы зубьев шестерни и колеса [2];
KFα аналогичен Kнα;
KFv аналогичен Kнv;
После определения контактных напряжений и напряжений изгиба подбираем материал и термообработку обеспечивающие прочность на изгиб и износостойкость.
Материал обоих колёс – сталь 40Х т. о. – закалка до твёрдости 45 50 HRC.
Расчёт валов коробки скоростей.
Вертикальная плоскость:
Определим реакции в опорах:
Эпюра изгибающих моментов:
Горизонтальная плоскость:
Суммарные реакции в опорах:
Суммарный изгибающий момент в опасном сечении:
Проверочный расчёт подшипников.
Пригодность выбранных подшипников определяем сопоставлением расчётной динамической грузоподъёмности Сrр с базовой Сr gпо условию [1]:
Расчётную динамическую грузоподъёмность определим по формуле [1]:
где: m = 3 – показатель корня дл конических роликоподшипников;
– угловая скорость вращения рассматриваемого вала;
Lh = 10000 ч – ресурс работы для зубчатых передач;
RE – суммарная реакция подшипника определяемая по формуле:
Где: V = 1 – коэффициент вращения;
Rr – суммарная реакция подшипника;
Kб = 13 – коэффициент безопасности для металлорежущих станков;
Kт = 1 – температурный коэффициент.
а) Опора А: подшипник 7205 (Сr = 23900 Н лёгкая серия [2])
Данный подшипник пригоден
б) Опора В: подшипник 7205 (Сr = 23900 Н лёгкая серия [2])
а) Опора А: подшипник 7206 (Сr = 29800 Н лёгкая серия [2])
б) Опора В: подшипник 7205 (Сr = 29800 Н лёгкая серия [2])
а) Опора А: подшипник 7208 (Сr = 42400 Н лёгкая серия [2])
б) Опора В: подшипник 7208 (Сr = 42400 Н лёгкая серия [2])
Расчёт шпиндельного узла.
1Расчёт на жесткость
При расчётах на жёсткость будем учитывать горизонтальную составляющую силы резания - Ру:
Допускаемое смещение переднего конца шпинделя:
Жёсткость переднего конца шпинделя:
где Е = 21105 Нмм2 – модуль Юнга для стали;
а – расстояние от конца шпинделя до первой опоры;
- момент инерции переднего конца шпинделя;
- приведённый диаметр переднего конца шпинделя.
Тогда смещение переднего конца шпинделя будет равно:
y [y] – условие выполняется.
2 Расчёт шпинделя на виброустойчивость
При расчёте шпинделей на виброустойчивость сравнивают частоту собственных колебаний шпинделя и частоту вынужденных колебаний с целью избежать явления резонанса [3].
– коэффициент расстройства системы
где: – вынужденные колебания системы;
– собственные колебания системы.
где: n = 2190 – максимальная частота вращения шпинделя;
где: g – ускорение свободного падения [смс2];
y – смещение переднего конца шпинделя;
> следовательно явления резонанса не произойдёт.
3Расчёт подшипников в шпиндельном узле
Упорный подшипник в т. В будет воспринимать только осевую нагрузку Рх:
Радиальные подшипники в т. А и В будут воспринимать осевую нагрузку Ру:
Статическая грузоподъёмность радиальных подшипников шпиндельного узла:
Опора A: подшипник 207 (Сr = 20100 Н лёгкая серия [2])
Опора В: подшипник 207 (Сr = 20100 Н лёгкая серия [2])
Список использованной литературы.
Металлорежущие станки: учеб. пособие для выполнения курсового проекта В.Н. Жарков В.В. Морозов В.Г. Гусев; Владим. гос. ун-т – Владимир: Ред.-издат. комплекс ВлГУ 2005. – 160 с.
Конструирование узлов и деталей машин: Учеб. пособие для машиностроит. спец. вузов П.Ф. Дунаев О.П. Леликов – 4-е изд. перераб. и доп. – М.: Высш. шк. 1985 – 416 с.
Расчёт и конструирование металлорежущих станков А.С. Проников – 2-е изд. – М.: Высш. шк. 1968 – 431с.
Рекомендуемые чертежи
- 22.08.2014
- 22.08.2014
- 04.05.2019