Разработка завода по капитальному ремонту строительных машин




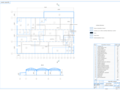
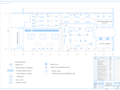
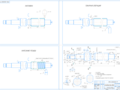
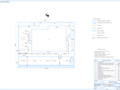
- Добавлен: 25.01.2023
- Размер: 2 MB
- Закачек: 0
Описание
Состав проекта
![]() |
![]() ![]() |
![]() |
![]() ![]() |
![]() ![]() ![]() ![]() |
![]() ![]() ![]() |
![]() ![]() ![]() ![]() |
![]() ![]() ![]() |
![]() ![]() ![]() |
![]() ![]() ![]() ![]() |
![]() ![]() ![]() ![]() |
Дополнительная информация
Генеральный план.cdw

Площадь застройки - 9888 м
Площадь под всеми сооружениями - 13766 м
Коэффициент застройки К
Коэффициент использования площади участка К
Наименование помещения
Производственное здание главного корпуса
Конторско-бытовое помещение (два этажа)
Трансформаторная подстанция
Площадка для машин поступивших в ремонт
Погрузочно-разгрузочная площадка
Площадка для отремонтированной техники
Испытательный полигон
Показатели генплана.
Условные обозначения
Сборное железобетонное ограждение
Железнодорожный путь нормальной колеи
Направление движения машин
ТЭП.docx
Выпуск продукции (программа завода)
Количество производственных рабочих
Стоимость завода (основные фонды)
Рентабельность завода
Окупаемость основных фондов
Выработка на одного производственного рабочего
Выпуск продукции на 1 станок
Выпуск продукции на 1 м2 производственной площади
Моторный цех.cdw

растачивания цилиндров
Копировально-шлифовальный станок для
кулачков распред. вала
Станок для шлифования шеек коленчатого
Хонинговальный (вертикально-доводочный)
Станок гор. расточной гнёзд под вкладыши
коренных подшипников и втулок распред. вала
Пресс для запрессовки втулок в верхнюю
Стенд для испытания и регулировки дизельной
топливной аппаратуры
Оборудование для ремонта приборов систем
Жестяницко-медницкий
Условное обозначение :
проходы не огражденные
- Роликовый приводной конвеер
- Тара для деталей и заготовок
- Рабочий( место обслуживания станка )
- Подвесной электрический однобалочный кран
Наименвание оборудования
Машина для мойки деталей двигателя
Гидравлический пресс
Стеллаж для подвешивания валов
Пресс для напресовки шестерен
Настольный сверлильный станок
Станок для растачивания шатунов
Прибор для проверки электрооборудования
Стенд для проверки форсунок высого давления
Стол для сборки двигателя
испытательный участок
Записка с формулами.docx
1.Анализ характеристик завода связанных с ремонтом строительных машин 3
2. Направление проектирования ремонтного предприятия ..8
1. Анализ ремонтной программы. 9
2.Проектирование ремонтного предприятия.. 12
3. Выбор производственной структуры ремонтного завода 18
4. Расчёт трудоёмкости моторного цеха .20
5. Распределение трудоемкости по цехам и отделениям. ..20
6. Расчет режима работы предприятия. 22
7.Расчет численности работающих.оборудования 23
8. Расчет количества оборудования и рабочих мест .. 25
9. Расчет площадей . 26
Технологический раздел. . 32
1. Разработка технологической схемы ремонта экскаватора 32
2. Компоновка цехов 35
3. Разработка схемы генерального плана предприятия 35
4. Разработка технологической схемы восстановления винта .37
5. Разработка операции восстановления .50
Проектирование моторного цеха 63
Разработка технико-экономических показателей завода ..66
Обеспечение безопасности труда работников моторного цеха.
1. Техника безопасности в моторном цехе .69
Расчет системы вентиляции 82
Список используемой литературы 87
Одним из ведущих факторов в решении задач сокращения себестоимости и сроков строительства повышения производительности труда и общей эффективности строительного производства является комплексное выполнение строительно-монтажных работ. Широкому внедрению комплексной механизации в строительное производство способствует насыщение строительства необходимым количеством высокопроизводительных машин освоении производства ряда новых типов машин расширения технологических возможностей средств механизации и совершенствование организации их эффективного использования.
На современном этапе развития строительного и дорожного машиностроения весьма актуальными проблемами являются повышение надежности и долговечности изготавливаемых машин рост эффективности их производства. Параллельно с развитием машиностроения требуется совершенствовать технологию и организацию ремонта машин. Однако показатели надежности и долговечности машин после капитального ремонта как правило ниже таких же показателей новых машин. С другой стороны трудоемкость и себестоимость ремонта машин составляет значительную величину. Поэтому для повышения качества ремонта и надежности машин с одновременным снижением стоимости и трудоемкости работ необходимо довести технический уровень технологии и организации работ машиноремонтного производства до уровня машиностроительного.
Выбор проекта ремонтного завода зависит от типов строительных машин которые будут поступать на ремонтное предприятие его территориального расположения количества ремонтируемых машин наличия родственных ремонтных предприятий в районе предполагаемого строительства нового предприятия и возможности кооперации назначения нового предприятия.
1. Анализ характеристик заводов связанных с ремонтом строительных машин
Капитальный ремонт основных строительных машин производят главным образом на ремонтных заводах которые в последнее время строили по типовым проектам.
Проектами предусмотрен ремонт машин и их агрегатов с применением передовой технологии и организации производства в основу которых положены: обезличенный метод ремонта машин; создание специализированных бригад на разборочных ремонтных и сборочных участках; применение поточных линий; широкая механизация подъемно-транспортных операций с использованием различных кранов конвейеров рольгангов и других средств.
Устанавливается номинальный годовой фонд времени в часах. Генеральный план типовых заводов унифицирован. Все производственные участки и большинство вспомогательных служб сосредоточены в одном главном корпусе. Административно-бытовые помещения размещены либо в отдельном здании соединенным крытым переходом с главным корпусом либо расположены в пристройке к главному корпусу. Отдельно размещаются склады металла и горюче-смазочных материалов. На территории завода размещены открытые площадки для хранения машин ожидающих ремонта и отремонтированных.
Основные общие и удельные показатели проектов типовых ремонтных заводов следующие:
- годовая производственная программа (в тыс. рублях) в нее входят: капитальный ремонт полнокомплектных машин капитальный ремонт комплектов агрегатов капитальный ремонт агрегатов для текущего ремонта машин эксплуатационными базами изготовление запасных частей;
- коэффициент сменности;
- число работающих (чел.) в том числе производственных;
- площадь участка в (га) в том числе площадь производственных закрытых помещений в (кв.м.);
- сметная стоимость общая (в тыс. руб.) в том числе сметная стоимость оборудования;
- потребная мощность электроэнергии в (КВТ).
Выпуск продукции (в руб.)
- на 1-го работающего
-на 1-го производственного рабочего
А также в характеристике показателей типовых проектов приняты нормативы трудоемкости на единицу ремонта отдельных специализированных и универсальных заводов (в чел.-ч.) в зависимости от марки машин по видам работ: слесарные станочные кузнечно-термические сварочно-наплавочные электроремонтные малярные и прочие.
Количественный анализ всех показателей позволяет сделать следующие выводы: трудоемкость ремонта на специализированных заводах ниже чем на универсальных; чем больше годовая программа ремонта данной марки машин тем ниже трудозатраты; выше экономическая эффективность производства ремонта; меньший срок проведения ремонта.
В качестве примера рассмотрим три наиболее характерных предприятия по капитальному ремонту строительных машин.
Специализированный завод по ремонту тракторов и строительных машин на базе тракторов.
Завод является крупным ремонтным предприятием специализированным для капитального ремонта строительных машин на базе тракторов Т-130 ДТ-75 МТЗ «Беларусь». Годовая производственная программа завода предусматривает следующее:
- капитальный ремонт полнокомплектных машин – 990 ед.
- капитальный ремонт комплектов агрегатов – 495 ед.
- капитальный ремонт агрегатов для текущего ремонта на эксплуатационных базах – 1385 ед.
- изготовление товарных запасных частей – 950 т.
- ремонт собственного оборудования с трудоемкостью ремонта:
- трактор Т-130 – 320 чел.-ч.
- трактор ДТ-75 – 240 чел.-ч.
- бульдозер Д-271 – 80 чел.-ч.
- погрузчик Т-157 – 160 чел.-ч.
- бульдозер Д-159Б – 70 чел.-ч.
- экскаватор Э-153 – 440 чел.-ч.
- экскаватор Э-302 – 690 чел.-ч.
Основные узлы и агрегаты для капитального ремонта вышеперечисленных машин поступают на кооперации с других заводов по изготовлению этих запасных частей что удовлетворяет и ускоряет ремонт.
Завод занимает территорию в 2.8 га. Расположение объектов общее для типовых проектов.
Завод имеет главный корпус площадью 9652 кв.м.; административно бытовой корпус – 950 кв.м.; открытые площадки (обслуживаемые козловыми кранами): для наружной мойки машин в летнее время для приема машин в ремонт для стоянки машин ожидающих ремонта для отремонтированных машин; склад металла; склад угля и металлолома; закрытый склад нефтепродуктов; площадь для испытания машин; склад баллонов ацетилена и кислорода.
Главный производственный корпус размещен в 3-х пролётном здании с шириной пролетов по 24 м. длиной 132 м. и высотой до низа несущих конструкций 9.6 м.
Административно-бытовой корпус расположен в трехэтажном здании длиной 48 м. и шириной 18 м. высота этажей по 3.3 м. Оно соединено с главным корпусом крытым теплым переходом.
Завод имеет общий для всех типовых ремонтных заводов состав производственных участков и вспомогательных служб.
Специализированный завод по ремонту экскаваторов типа Э-302.
Программой завода предусмотрен ремонт только одной марки экскаваторов.
Годовая программа следующая:
- капитальный ремонт полнокомплектных экскаваторов Э-302 – 420 шт.
- изготовление комплектов: узлов экскаватора для капитального ремонта в эксплуатационных условиях – 140 шт.; узлов экскаватора для текущего ремонта – 1120 шт.
- изготовление товарных запасных частей – 420 шт.
Территория завода составляет 233 га. На ней расположены:
производственный корпус – 6550 кв.м.;
административное здание – 520 кв.м.;
открытые площадки для хранения отремонтированных машин – 400 кв.м. и машин ожидающих ремонта для испытания машин; склад металла; склад отходов; склад узлов ожидающих ремонта; склад материалов; закрытые склады нефтепродуктов кислородных и ацетиленовых баллонов.
В производственном корпусе состоящем из трех пролетов по 18 м. каждый длиной 120 м. и высотой 108 м. размещены производственные участки и вспомогательные службы. Корпус оборудован электро - мостовыми кранами опорными однобалочными кранами грузоподъемностью 32 т.с. и подвесными кран-балками.
Трудоемкость ремонта составляет:
- экскаватор Э-302 полнокомплектный – 515 чел.-ч.
- узлы экскаватора Э-302:
двигатель – 55 чел.-ч.
передний мост – 53 чел.-ч.
задний мост – 36 чел.-ч.
главный редуктор – 94 чел.-ч.
платформа – 67 чел.-ч.
- изготовление товарных запчастей – 80 т.
Капитальный ремонт одного типа машин – экскаваторов Э-302 позволяет унифицировать его организовать производство отдельных запчастей на собственном заводе что удешевляет сам ремонт снижает транспортные расходы на их доставку.
Специализированное предприятие по ремонту экскаваторов Э-153.
Годовая программа предприятия предусматривает ремонт:
- экскаваторов типа Э-153 Э-153А Э-1514 – 600 ед.
- комплектов агрегатов навесного оборудования – 300 ед.
Предприятие занимает территорию – 107 га на которой находится главный корпус площадью 2592 кв.м.
Все основные и вспомогательные отделения участки и службы размещены в главном корпусе представляющем одноэтажное 3-х пролётное здание размером в плане 72x36 м. с шириной пролетов по 12 м. и высотой до низа строительных конструкций 72 м.
Корпус оборудован подвесными кран-балками грузоподъемностью 32; 2 и 1 т.с.. Кроме того для механизации технологических и транспортных операций на участках установлены консольные пневматические краны на свободностоящих колоннах привозные рольганги монорельс с электротельфером транспортные тележки цепные конвейеры.
Для разгрузки и погрузки экскаваторов и навесного оборудования на площадях хранения установлен козловой кран грузоподъемностью 5 т.с. пролетом 113 м. с двумя консолями по 4 м.
Для транспортирования экскаваторов с площадки хранения ремфонда в главный корпус на участок наружной мойки запроектированы специальные тележки перемещаемые цепным конвейером со скоростью 6 м.мин.
Трудоемкость ремонта:
- полнокомплектных экскаваторов – 200 чел.-ч.
- комплектов узлов навесного оборудования – 83 чел.-ч.
Общее количество оборудования – 104 шт.:
- металлорежущего – 16 шт.;
- кузнечнопрессового – 11 шт.;
- сварочного – 5 шт.;
Общее число работающих – 137 чел. в том числе:
- производственных рабочих – 93 чел.
- вспомогательных – 14 чел.
2. Направление проектирования ремонтного предприятия
Анализируя характеристики ремонтных предприятий можно сделать вывод что при их проектировании в первую очередь рассматривается необходимость ремонтного предприятия в данной местности т.е. отсутствие других ремонтных заводов и наличие эксплуатационных баз темпов строительства и количества строительных объектов (жилищных производственных мостов и других дорожных сооружений) а также от способа доставки строительных машин для ремонта. Как правило эти заводы располагаются вблизи с железной дорогой или автомобильными трассами. Учитывается возможность подключения к энергообъектам и другим коммуникациям (водоснабжение и канализация технических и сточных вод).
Проект ремонтного завода также зависит от годовой программы. Чем больше годовая программа (в количественном или денежном выражение) тем больше общая территория предприятия больше зданий и сооружений на ней увеличивается количество оборудования и различных приспособлений для ремонта число работающих.
Возможности крупного ремонтного завода позволяют применять передовые технологии ремонта: автоматизировать и механизировать процессы ремонта использовать унифицированные узлы и агрегаты поступающие по кооперации при этом повышается производительность труда снижается трудоемкость ремонта повышается экономическая эффективность.
1. Анализ ремонтной программы
Анализ ремонтной программы выполним на основании исходных данных принятых по табл. 2 и 3. [1]. Исходные данные определяем по варианту определяемому по табл. 1 [1]. Исходные данные приведены в табл. 1 и 2.
Таблица 1 - Количество ремонтируемых машины и двигателей
Экскаваторы одноковшовые:
Автогрейдеры ДЗ-31*Д-557
Краны автомобильные КС-2561К
Краны пневмоколесные КС-4362
Таблица 2 – Дополнительные виды работ
Изготовление запасный частей и узлов
Изготовление новых машин и выполнение заказов строительных организаций
Ремонт собственного оборудования завода и инструментальные работы
Техническая характеристика машин ремонтируемых на предприятии:
ЭО-2621А – экскаватор пневмоколесный на базе трактора ЮМЗ-6А8М; мощность основного двигателя 44 кВт; марка двигателя Д-50 (Д65М) - дизель; вместимость ковша (геометрическая)- 04 м3; с жёсткой подвеской; с гидравлическим управлением; вид основного оборудования (рабочего) - обратная лопата отвал; эксплуатационная масса-545 т.; габариты-6500x2100x3900 мм. [5] стр. 10.
ЭО-3311БЭ-302Б – экскаватор на пневмоколёсном ходу канатный экскаватор с пневматическим управлением; мощность основного двигателя 368 кВт; марка двигателя Д-65ЛС - дизель; вместимость ковша 04 м3; рабочее оборудование – обратная лопата; габариты 10200х2920х3030 мм; масса-124 т. [5] стр. 20.
ЭО-4321 – экскаватор на пневмоколёсном ходу мощность основного двигателя 588 кВт (80 л.с.); двигатель-СМД-14Н-дизель; вместимость ковша- 065 м3; рабочее оборудование обратная лопата отвал; с жесткой подвеской; с гидравлическим управлением; габариты 10400х3000х3200 мм; масса-212 т. [5] стр. 10.
ДЗ-31Д-557 – автогрейдер на пневмоколёсном ходу; мощность двигателя 956 кВт; марка двигателя А-01М-дизельный; Рабочее оборудование - бульдозерный отвал грейдерный отвал кирковщик; с гидравлическим управлением; габариты 9620х2650х3475 мм; масса-131 т. [4] стр. 13.
КС-2561К – кран стреловой на базе автомобиля ЗИЛ-130; мощность двигателя 1103 кВт; марка двигателя ЗИЛ-130 - карбюраторный; С пневматическим управлением; грузоподъемность 63 т; длинна стрелы 8÷12 м; габариты 8535х2500х3665; масса-895 т. [4] стр. 19.
КС-4362 – кран стреловой на пневмоколёсном ходу (в основном транспортное перемещение с помощью тягачей); грузоподъемность 16 т.; с гибкой подвеской; с пневматическим управлением; мощность основного двигателя 552 кВт (75 л.с.); марка двигателя СМД-14А; габариты (без стрелы) 14000х3150х3930 мм; длинна стрелы 125÷20 м.; масса-237 т. [5] стр. 21.
Для всех указанных машин однотипность заключается в следующем - все машины на пневмоколёсном ходу. Также можно разбить машины на две группы: с гидравлическим управлением - (ДЗ-31 ЭО-2621А ЭО-4321) и с пневматическим управлением (ЭО-3311Б КС-4362 КС-2561К) с дизельным двигателем (ЭО-2621А ЭО-4321 ЭО-3311Б КС-4362) и с карбюраторным двигателем (ДЗ-31 КС-2561К).
Модели ЭО-3311Б ЭО-4321 КС-4362 имеют похожие по конструкции и принципу работы несущие кузова (кинематика поворотной платформы передвижения компоновка механизмов). Однотипность навесного оборудования прослеживается у всех экскаваторов. Но в годовую ремонтную программу входят еще и автогрейдеры ДЗ-31Д-557 и краны автомобильные КС-2561К значит номенклатуру ремонтируемых машин можно считать разнообразной.
Учитывая все вышеизложенное можно сделать вывод: что капитальный ремонт машин разнообразной номенклатуры целесообразно выполнять на универсальном ремонтном предприятии.
2. Проектирование ремонтного предприятия
2.1. Выбор типа ремонтного завода метода и формы организации ремонта
По степени специализации заводы разделяются на универсальные и специализированные. На универсальных заводах ремонтируют машины различных типов и марок и их агрегаты изготавливают запасные части к ним.
Специализированные заводы ремонтируют машины какого-нибудь одного типа например: тракторы и машины на их базе (бульдозеры краны).
Специализация ремонтных заводов носит серийный характер что позволяет применять передовую организацию и технологию производства оснастить предприятие поточными линиями и высокопроизводительным оборудованием (станки с программным управлением и т.п.) Это дает возможность значительно повысить производительность труда снизить себестоимость и самое главное сократить сроки ремонта резко повысить его качество.
Выбираем тип предприятия – универсальное в связи с тем что в годовую ремонтную программу завода входят машины разнообразной номенклатуры.
Для сокращения простоя техники в ремонте и сокращении себестоимости ремонта выбираем агрегатный метод ремонта. При таком методе ремонта снятые с машины детали и агрегаты обезличивают и после ремонта в специализированных цехах (участках) устанавливают на любую машину такой же серии. Для осуществления агрегатного метода ремонта необходимо иметь оборотный фонд деталей и агрегатов.
Выбираем поточную форму организации ремонта со своими особенностями. При поточной форме организации производства создаются поточные линии являющиеся самостоятельными участками в производственном процессе. В зависимости от выполняемых на поточной линии стадий процесса они специализируются на разборочные слесарно-ремонтные сборочные малярные и
т. д. Это значительно снижает специализацию рабочих но в значительной мере повышает их квалификацию следовательно повышает и качество ремонта.
Универсальность ремонтного завода обезличенный метод ремонта специализированные бригады при поточной форме организации производства все эти факторы значительно снижают трудоёмкость работ а следовательно снижают конечную себестоимость ремонта.
2.2. Годовая производственная программа
Годовую производственную программу определим исходя из задания по трудоёмкости и стоимости а также по показателям приложения 1. [1]
Таблица 3 – Ремонтные нормативы
Так как ремонтные нормативы дают усредненное значение трудоёмкости то при определении трудоёмкости годовой программы ремонта для каждой марки машин воспользуемся формулой (1) [1 стр.9].
Ти - трудоёмкость нормативная чел.-ч;
Км - коэффициент учитывающий метод ремонта;
Ко - коэффициент учитывающий форму организации ремонта;
Кс - коэффициент учитывающий серийность (однотипность ремонтируемых машин);
Для: ЭО-2621А- Кс=08;
ЭО4321 ДЗ-31 КС-2561К и КС4362- Кс=1;
ЗИЛ-130 Д-48ЛС СМД-14- Кс=07; приложение 2 [1 стр.38].
Определяем суммарную трудоёмкость годовой программы Т0 по формуле (2) [1 стр.9]
где m - количество марок машин;
- суммарная трудоёмкость годовой ремонтной программы чел.-ч;
- суммарная трудоёмкость дополнительной программы ремонтного предприятия чел. - ч;
То=804550+305729=1110279 чел.-ч.
Для расчёта стоимости капитального ремонта машин воспользуемся прейскурантом оптовых цен (приложение 1) [1 стр.37] коэффициент инфляции К принимаем равным 10. Полученные оптовые цены капитального ремонта сводим в табл. 4. При вычислении дополнительной программы исходим из того что за 1 нормо-час производится работ на 25К руб. т.е. на 25 руб.
Таблица 4 – Годовая программа
Распределим трудоёмкость годовой ремонтной программы по видам работ для каждого типа машин и марок двигателей (табл. 5).
ЭО - 2621А (105300-годовая трудоёмкость).
Таблица 5 – Распределение трудоёмкости ремонта по видам работ чел.-ч.
Марки машин и двигателей
Распределяем трудоёмкости дополнительных работ по видам.
Полученные данные заносим в табл. 6.
Таблица 6 – Распределение трудоёмкости дополнительных работ по видам чел-ч.
Изготовление запасных частей и узлов
Изготовление новых машин
Ремонт собственного оборудования завода
Составим сводную ведомость распределения трудоемкости всей годовой программы завода табл. 7.
Таблица 7 – Трудоёмкость годового объема работ
Трудоёмкость чел.-ч.
3. Выбор производственной структуры (состава) ремонтного завода
На предприятии работает 665 чел. (см. расчет численности работающих п. 3.7.) что менее 1000 чел - принимаем бесцеховую структуру завода. Цеха образуем только моторный механический слесарно-ремонтный т.к. в каждом из них более 100 чел.
4. Расчёт трудоемкости по цехам и отделениям
Для расчета всех параметров по цехам и отделениям определим трудоемкость в каждом из них. В начале находим трудоёмкость работ по ремонту двигателей выполняемую в моторном цехе учитывая при этом как товарные двигатели предусмотренные годовой программой так и двигатели снятые с ремонтируемых машин (процент распределения принимаем по приложению 3 [1 стр.37]).
Определим годовую трудоёмкость для каждой марки двигателя по формуле (1)
Км = 075 - для всех марок двигателей при обезличенном методе ремонта;
Ко = 09 - специализированных бригад;
Полученные результаты расчетов заносим в табл. 8.
5. Распределение трудоемкости по цехам и отделениям
Зная состав завода и работы которые выполняются в каждом отделении из общей трудоёмкости по видам работ (см. табл. 7) вычитаем трудоёмкость работ выполняемых в моторном цехе табл. 8. Результаты заносим в табл. 9.
Таблица 8 – Трудоёмкость работ выполняемых в моторном цехе
Таблица 9 – Трудоёмкость работ по цехам и отделениям
Трудоёмкость чел. ч.
Мойка агрегатов и узлов
Жестянико-медницкий отд.
Электротехнический отд.
Комплектовочный отд.
Слесарно-ремонтный цех
6. Расчет работы предприятия
Принимаем что предприятие в течение года загружено равномерно.
Для лучшего использования оборудования и площади работу предприятия запроектируем в две смены.
Определим действительные фонды времени рабочих оборудования и рабочих мест (постов).
Действительный фонд времени рабочих Фдр- определим по формуле:
Фдр=[dк–(dв+dп+do)]tсм–(dп–2)nсRп
где dк=365-число календарных дней в году;
dв=52- число выходных дней в году;
dп=10- число праздничных дней в году;
do- число отпускных дней в году:
do=24-маляры сварка медики испытатели кузнецы гальванисты;
do=18- электрики термисты мойщики;
do=15- слесари станочники дефектация сборка разборка комплектовка кузовной;
tсм- продолжительность смены ч;
tсм=82 ч.- электрики мойщики термисты слесари станочники дефектация сборка- разборка комплектовка кузовной сварка медики испытатели кузнецы.
nс=1- количество часов на которые сокращён рабочий день перед праздником;
Rп=096- коэффициент учитывающий потери рабочего времени по уважительным причинам.
Действительный годовой фонд времени работы оборудования и рабочих мест Фдо определим по формуле (4) [1 стр.13]
Фдо=[ dк–(dв+ dп)] tоnRp.
где tо=8 – продолжительность работы оборудования в течение смены ч.;
n=2- число смен в сутки;
Rp- коэффициент учитывающий простой в ремонте:
Rp=096 (при n=2) – для оборудования;
Rp=099-для рабочих мест.
Фдр=[365–(52+10+18)]82–(10–2)1096=2236 ч.
Фдо=[ 365–(52+ 10)] 82096=4654 ч.
7. Расчёт численности работающих
Расчёт численности работающих выполняется по категориям. В состав работников предприятия входят следующие категории: производственные и вспомогательные рабочие инженерно технические рабочие (ИТР) счётно-конторский персонал (СКП) и младший обслуживающий персонал (МОП).
Общую численность производственных рабочих определим по формуле (5) [1 стр. 14]
Фдп - действительный фонд времени рабочих соответствующей профессии ч. (равный Фдп см. пп 3.6.)
Общее число вспомогательных рабочих (ремонтные и транспортные рабочие разнорабочие наладчики контролёры-браковщики раздатчики инструмента) определим по формуле (6) [1 стр.14].
где Пв - процент вспомогательных рабочих по отношению к производственным для ремонтных предприятий принимаем равным Пв=16%.
Численность ИТР СКП и МОП определим в процентном отношении от общего числа производственных и вспомогательных рабочих:
ИТР-12% СКП-3% МОП-2%.
Предварительно найдем трудоёмкость работ выполняемых в «Ремонтно-механическом отд.» «Механическом цехе» и «Слесарно-ремонтном цехе».
Трудоёмкость работ в механическом цехе найдём путем вычитания из общей трудоемкости требуемой для выполнения станочных работ по предприятию в целом (без учёта трудоёмкости станочной в моторном цехе) трудоёмкость станочную для ремонта собственного оборудования завода взятую из табл. 6.
1133-14482=276651 чел.-ч. - трудоёмкость работ выполняемых в механическом цехе.
Аналогично найдём трудоёмкость работ выполняемых в других подразделениях завода. Результаты заносим в табл. 10.
Таблица 10 – Состав работников ремонтного завода
Ремон. механ. отделение
8. Расчёт количества оборудования и рабочих мест
Расчёт количества оборудования No и рабочих мест Nр выполним с учетом трудоёмкости работ Ti выполняемых в данном отделении по формуле (7) [1 стр.15].
где ФДО- действительный фонд времени работы оборудования (рабочих мест) ч.;
- коэффициент загруженности для оборудования =075 для рабочих мест =08 [1 стр.15]
Расчёт оборудования выполняем только для механических кузнечно-термических сварочно-наплавочных и гальванических цехов.
Результаты расчётов сводим в табл. 11 и табл. 12.
Таблица 11 – Количество оборудования
Действительный фонд времени работы оборудования ч.
Количество оборудования
Ремонтно-механический отд.
Таблица 12 – Количество рабочих мест
Ремонтно-механический отд:
9.1. Расчёт производственных площадей.
а) в зависимости от количества производственных рабочих по формуле
где FЦ- площадь цеха или отделения м2;
PП-количество производственных рабочих занятых в первую смену;
fпл.- удельная площадь на одного производственного рабочего м2 (прил. 6 [1 стр.40] ).
Наружная мойка: FЦ=1*35=35 м2;
Разборка: FЦ=10*25=250 м2;
Моечное: FЦ=3*35=105 м2;
Комплектовка: FЦ=7*18=126 м2;
Испытательное: FЦ=3*35=105 м2;
Электротехнический: FЦ=1*12=12 м2;
Жестяницкое: FЦ=5*10=50 м2;
Дефектация: FЦ=2*15=30 м2;
Слесарно-ремонтный: FЦ=47*18=846 м2;
Сборочный: FЦ=27*25=675 м2;
Кузовной: FЦ=2*25=50 м2;
Малярное: FЦ=4*40=160 м2;
Столярное: FЦ=4*15=60 м2;
Вулканизационное: FЦ=1*12=12 м2;
Ремонт шин: FЦ=3*20=60 м2;
б) в зависимости от площади рабочей зоны:
где- No- количество оборудования;
F3-площадь занимаемая оборудованием с учетом раб. зоны для станков в среднем равна 15 м2.
Механический цех: FЦ=79*15=1185 м2;
Сварочный отдел: FЦ=13*15=195 м2;
Кузнечно-термический отд.: FЦ=3*15=45 м2;
Гальванический отд.: FЦ=4*15=60 м2;
Рассчитаем моторный це
а) в зависимости от производственных раб.
Разборка: FЦ=3*25=75 м2;
Мойка агрегатов: FЦ=1*35=35 м2;
Жестяницкое: FЦ=2*10=20 м2;
Электротехнический: FЦ=2*12=24 м2;
Комплектовка: FЦ=2*18=36 м2;
Слесарно.-ремонтный: FЦ=20*18=360 м2;
Сборочный: FЦ=10*25=250 м2;
Испытательное: FЦ=2*35=70 м2;
Топливной аппаратуры: FЦ=9*12=108 м2;
Механический отд: FЦ=11*15=165 м2;
Итого площадь моторного цеха составит 1173 м2.
Рассчитаем ремонтно-механическое отделение
а) в зависимости от производственных рабочих.
Слесарный: FЦ=13*18=234 м2;
Механический отд: FЦ=4*15=60 м2;
Итого площадь ремонтно-механического отделения составит 294 м2.
Площадь складов подсчитаем по формуле
где -удельная площадь м2 (прил. 8 [1])
чел.-ч. - трудоёмкость ремонтной программы.
Таблица 13 – Количество оборудования в моторном цехе
Трудоемкость чел.-ч.
Количество обрудования
Жестяницко-медницкие
Ремонт топливной аппаратуры
Металла FСК=0001*05*1110279=555 м2;
Запасных частей FСК=0001*07*1110279=777 м2;
Материала FСК=0001*03*1110279=333 м2;
ГСМ FСК=0001*013*1110279=144 м2;
Утиля FСК=0001*017*1110279=188 м2;
Лесоматериалов FСК=0001*02*1110279=222 м2;
Топлива FСК=0001*06*1110279=666 м2;
Хранение двигателей и агрегатов FСК=0001*035*1110279=388 м2;
Размеры открытых площадок для хранения ремонтного фонда и отремонтированных машин определим по формуле
где m- количество марок машин;
5- календарных дней;
- срок хранения дни;
Определим площадь машин:
ЭО-2621А габарит 21х65; F1=2.1*6=13.65 м2;
ЭО-3311Б габарит 102х292; F2=102*292=2978 м2;
ЭО-4321 габарит 3х104; F3=3*104=312 м2;
ДЗ-31 габарит 962х265; F4=962*265=25493 м2;
КС-2561 габарит 8535х25; F5=2134 м2;
КС-4362 габарит 14х315; F6=14*315=441 м2;
Площадь бытовых и конторских помещений рассчитаем для завода по следующим нормативам:
Площадь раздевалок-08 м2 на одного рабочего (принимаем общее число рабочих 498+77=575 чел.) см. табл. 10.
Fраз=575*08=460 м2. Всю данную площадь определим в производственный корпус.
Площадь остальных бытовых помещений рассчитаем по числу всех работающих в первую смену(378 чел.)
Умывальников Fум=37810*1=378 м2;
Душевых Fдуш.=37810*45=1701 м2;
Уборных Fубор.=37820*3=567 м2;
Из суммы данных площадей (378-90)378=076 часть выделим в производственный корпус т.е. 201 м2
Буфетов и столовой Fбуф.=378*025=945 м2;
Площади конторских помещений:
СКП- Fскп=16*325=52 м2;
ИТР- Fитр=65*5=325 м2;
Компрессорная - Fком.=2*25=50 м2 (два компрессора);
Гараж (075 на 1000 чел.-ч.)
Fгар.=11102791000*075=8327 м2;
Таблица 14 – Основное технологическое оборудование
Вертикально- алмазно-
Вертикально-доводочный (хонинговальный) станок
Стенд для проверки форсунок насосов высокого давления
Стенд для испытания и регулировки дизельной топливной аппаратуры
Прибор для проверки электрооборудования автомобилей
Оборудование для ремонта приборов систем электрооборудования
Стол для комплектовки деталей
Технологический раздел
1. Разработка технологической схемы ремонта машины.
Производственный процесс капитального ремонта строительных и дорожных машин состоит из следующих основных операций: приёма машины в ремонт; наружной мойкой машины; разборкой машины на агрегаты и узлы; очистка и мойка агрегатов и узлов; разборки агрегатов и узлов на детали; очистки и мойки деталей; ремонт деталей; комплектования деталей; сборки узлов и агрегатов; общей сборки обкатки испытаний и окраски узлов и агрегатов; общей сборки обкатке испытанию и окраски машины; сдачи отремонтированной машины (агрегата).
Технологическая схема капитального ремонта ведущей машины завода ЭО-4321 приведена на рис 2.
На схеме стрелками показана технологическая последовательность выполнения отдельных операций при ремонте агрегатно-узловым методом при котором сборка машины осуществляется с использованием заранее отремонтированных или новых узлов (агрегатов) поступающих со склада оборотного фонда.
При поступлении машины в ремонт она поступает на площадку для машин ожидающих ремонт. После этого машина поступает на участок наружной мойки после мойки машина подвергается разборке на участке для разборки машин на агрегаты узлы детали. После чего узлы агрегаты и детали подвергаются мойке на участке для мойки агрегатов узлов и деталей. Помытые узлы агрегаты и детали поступают на участок разборки. Затем детали моют и передают на участок дефектации детали пришедшие в негодность и неподлежащие ремонту передаются на склад утиля. Детали подлежащие восстановлению передаются на участок для восстановления деталей а после восстановления поступают на склад запасных частей. После ремонта поступают на участок сборки узлов и агрегатов. Этот участок состоит из отдельных участков которые специализированы для сборки отдельных узлов и агрегатов. Из участков моторного цеха ходовой части и электрооборудования собранные агрегаты и узлы поступают на участок оборотного фонда агрегатов и узлов после чего по мере необходимости поступают на участок общей сборки машины. После сборки машина поступает на участок заправки и испытания. После испытаний машина подвергается окраске нанесению трафаретов. Окрашенная машина отправляется на площадку для отремонтированных машин.
Объединим производственные вспомогательные и складские и часть бытовых помещений в одном здании за исключением гаража складов металла ГСМ топлива утиля котельной подстанции.
Найдем размеры главного корпуса. Разделим его на производственную и бытовые части. Высоту производственной части выбираем 108 м бытовой – 42 м.
где F- площадь главного корпуса;
Σhгл.к.- сумма перекрытий глав. корпуса;
L’гл.к- длина производственной части главного корпуса;
F’= 5528+1770=7298 м2
Площадь бытовых помещений выносится на 2-й этаж главного корпуса
где -5528 - сумма площадей производственных;
70-сумма вспомогательных площадей и части складов.
Для учета проходов и проездов общую площадь главного корпуса увеличиваем на 10%
L’гл.к.=FΣhгл.к.=8028(24+24+24)=1115 м.
Принимаем L’гл.к=114 м (кратно 6)
3. Разработка схемы генерального плана предприятия.
Предварительно определим примерно площадь территории завода из расчета что на 100 чел.-ч. трудоёмкости для ремонтного завода отводят 25 м2.
Fтерр.=1110279100*25=27750 м2 - площадь территории завода.
Принимаем длинна-185 м; ширина - 150 м.
Сначала проектируем подкрановый путь на нем расположим козловой кран грузоподъемностью Q =30 т. Подкрановая колея будет равна 31 м. Прокладываем под краном ж.д. путь. Расстояние от крайней головки рельса до выступающей части крана 2 м.
Преобладают северо-восточные ветра-(согласно «розе ветров»). Проектируем склад топлива (10) и ГСМ (7) с подветренной стороны в целях пожарной безопасности.
Для ускорения и удобства погрузки и разгрузки грузов такие объекты как погрузочно-разгрузочная площадка (12) склад металла (11) склад топлива (10) склад утиля (9) площадку для машин поступивших в ремонт- располагаем между подкрановых путей козлового крана. Расстояние между объектами выдерживаем в соответствии с требованиями пожарной безопасности.
Главный корпус (3) располагаем в центре на территории завода с выдерживанием противопожарных расстояний между соответствующими зданиями складами площадками. С северо-западной стороны от главного корпуса на расстоянии 12 м. располагаем конторско-бытовое помещение (3) его мы проектируем в два этажа. На первом этаже расположим столовую и душевые помещения на втором- контору.
На расстоянии 16 м с восточной стороны от конторы располагаем гараж (4). С восточной стороны от главного корпуса располагаем трансформаторную подстанцию (6) и котельную (5). Также предусмотрим зону отдыха (15) с аллеями скамейками и озеленением.
Для технико-экономической оценки запроектированного генплана сравним расчётные коэффициенты КЗ и КИС с нормативами- КЗ=035÷045; КИС=045÷055.
КИС=FПСFТЕРР.=1376627750=0496 -коэфф. использования участка принимается.
FП С- 14010 м2 площадь под всеми сооружениями.
КЗ=FКПFТЕРР=988827750=0356-принемается.
FКП-10255 м2 площадь под всеми крытыми помещениями.
Техника поступающая в ремонт складируется на площадке (8) после чего поступает на участок наружной мойки главного производственного корпуса (3). При выходе из ремонта техника направляется на испытательный полигон (14) после чего направляется на площадку для отремонтированной техники (13) откуда после приёмки заказчиком отправляется к месту приписки.
4. Разработка технологического процесса восстановления винта
4.1. Исходные данные
Материал - сталь конструкционная качественная (сталь 45) термообработка – улучшение твердость НВ 241 285.
Поскольку при работе происходит износ резьбы: как винта так и гайки задаемся величиной износа профиля резьбы ходового винта 2 мм по ширине. Наружный диаметр изношенной резьбы принимаем 47 мм (табл. 3.1).
Таблица 15 - Исходные данные
Годовая программа шт.
Восстанавливаемый дефект
Ширина профиля резьбы по среднему диаметру мм
Предельная допустимая
4.2. Установление типа производства
Тип производства является организационно-технологической характеристикой производственного процесса. Он оказывает существенное влияние на разработку технологического процесса выбор способа восстановления выбор оборудования и инструмента [ 23 стр. 6 ].
В машиностроении и ремонтном производстве различают три основных типа производства: единичное серийное и массовое.
Тип производства выбирается исходя из годовой программы. Окончательно тип производства устанавливается по коэффициенту серийности Ксер после определения штучного времени.
гдеFд – действительный годовой фонд работы оборудования при одной смене ч.;
m – число рабочих смен в сутки;
N – годовая программа. шт.;
tшт – штучное время восстановления мин.
Действительный фонд времени определяется на основе номинального фонда и плановых простоев оборудования в ремонте. Для единицы оборудования он рассчитывается по формуле чед:
где Др - число рабочих дней в планируемом периоде;
Тсут - число рабочих часов в сутки;
Др.с. - число рабочих дней сокращенной продолжительности в планируемом периоде;
Тсокр - число часов на которое сокращаются рабочие сутки;
Ррем - время простоя оборудования в плановом ремонте выраженное в процентах от номинального фонда (для универсального оборудования примем 3%);
FД = (251 · 8 – 10 · 1) (1 - ) = 1938 ч.
В среднем в год ремонтируется не более 24 машин поэтому годовая программа ремонта не может быть больше этой цифры. Исходя из этого устанавливаем окончательно тип производства – единичный.
4.3. Выбор способа восстановления
Для восстановления трапецеидальной резьбы наиболее целесообразным является применение механизированной наплавки в среде защитного газа.
В данном случае возможны два варианта:
наплавка в среде углекислого газа;
наплавка в среде пара.
Наплавка производится без предварительного удаления старой резьбы с последующей холодной правкой вала и нарезанием резьбы номинального размера.
Выбранный способ включает четыре операции:
наплавку резьбовой поверхности в среде защитного газа;
холодную правку вала под прессом (при необходимости);
предварительную механическую обработку;
окончательную механическую обработку (нарезание резьбы).
Рис. 3 Параметры восстанавливаемой резьбы
Определяем площадь наплавляемой поверхности резьбы винта ходового
где L — длина образующих резьбу поверхностей (рис.3) мм;
n – количество витков резьбы.
Длина винтовой линии определяется через развертку цилиндрической винтовой линии которую можно представить как треугольник катетами которого являются шаг Р = 12 мм и длина окружности 2r2 = d2 (рис. 4) а гипотенуза будет равна длине винтовой линии.
Рис. 4 Длина винтовой линии
Тогда по теореме Пифагора длина винтовой линии
l = = = 13242 мм = 13242 см.
Количество витков резьбы
Площадь наплавляемой поверхности
После того как будет наплавлена резьбовая поверхность дальнейшая наплавка будет происходить по наружному диаметру резьбы 47 мм.
Площадь цилиндрической поверхности винта ходового под наплавку
где D — диаметр наружной поверхности резьбы мм;
l — длина резьбы мм.
Трудоемкость к-й операции определяется по формуле
где tk0 — трудоемкость обработки 1 м2 поверхности детали z-m способом на глубину (толщину) Нк чел.-ч;
hk — толщина фактически наращиваемого слоя или глубина обработки (на сторону) мм;
Нк — рациональная толщина покрытия z - m способом мм.
Резьбовая поверхность ходового винта должна быть наплавлена до определенного диаметра учитывающего припуск на снятие окалины и последнего наплавленного слоя имеющего твердость на 12-15% выше твердости остальной части наплавленного слоя а также припуск на чистовую обработку. Принимаем припуск на снятие окалины и корки по 2 мм на сторону.
Глубина предварительной механической обработки (точение с 52 мм до 48 мм)
Глубина окончательной механической обработки (нарезание трапецеидальной резьбы)
Трудоемкость наплавки в среде углекислого газа
t1 = 28 = 7735 чел.-ч.
Трудоемкость наплавки в среде пара
t1 = 28 = 5156 чел.-ч.
Трудоемкость предварительной механической обработки (точение с 52 мм до 48 мм)
t2 = 17 = 68 чел.-ч.
Трудоемкость окончательной механической обработки (нарезание трапецеидальной резьбы)
t3 = 17 = 27625 чел.-ч.
Расход материалов определяется по формуле
где gk0 — приведенный расход материалов на обработку 1м2 поверхности детали z-м способом на глубину (толщину) Нк кг;
Расход материалов при наплавке в среде защитного газа
Расход материалов при наплавке в среде пара
Расход материалов при механической обработке
Расход электроэнергии определяется по формуле
где Эk0 — энергоемкость кВт ч.
Расход электроэнергии при наплавке в среде углекислого газа
Э1 = 256 = 7072 кВт ч;
Расход электроэнергии при наплавке в среде пара
Э1 = 235 = 4328 кВт ч;
Расход электроэнергии при мехобработке
Э2 = 97 = 388 кВт ч;
Э3 = 97 = 2049 кВт ч;
Стоимость восстановления детали определяется по формуле
Сbz = C1 + C2 + C3 + C4
где С1 — заработная плата на выполнение всех технологических операций восстановления детали руб.;
С2 — стоимость материалов руб.;
С3 — стоимость электроэнергии руб.;
С4 — накладные расходы (затраты на содержание оборудования оснастку общецеховые расходы и т.д.) руб.
Заработная плата в руб. на выполнение технологических операций восстановления вычисляется по формуле
где n — число операций;
tk — трудоемкость выполнения k-й операции чел.-ч;
Rk — тарифная ставка производственника выполняющего
k-ю операцию рубч. (принимаем равной на день расчета).
Учитывая что механическая обработка ведется по четвертому разряду определяем стоимость
при наплавке в среде углекислого газа
C1 = 7735 606 + 68 67 + 27625 67 = 27752 руб.
при наплавке в среде пара
C1 = 5156 606 + 68 67 + 27625 67 = 264893 руб.
Стоимость материалов
где gk — приведенное количество материалов идущих на операцию под номером k кг;
— средняя стоимость 1 кг материалов идущих на операцию руб.
Стоимость материалов при наплавке в среде углекислого газа
C2 = 829 049 + 1 074 + 528 074 = 871 руб.
Стоимость материалов при наплавке в среде пара
C2 = 571 056 + 1 074 + 528 074 = 784 руб.
Стоимость электроэнергии
где — энергоемкость операции k-го вида кВт-ч;
— стоимость 1 кВт-ч электроэнергии руб; принимается по действующим тарифам = 15 руб кВт-ч.
Стоимость электроэнергии при наплавке в среде углекислого газа
С3 = (7072 + 4074 + 2049) 15 = 47454 руб.
Стоимость электроэнергии при наплавке в среде пара
С3 = (4328 + 4074 + 2049) 15 = 43338 руб.
Накладные расходы определяют в зависимости от суммы заработной платы за выполнение операций восстановления С1:
где — коэффициент который принимается для ремонтных предприятий равным 20—25.
Накладные расходы при наплавке в среде углекислого газа
С4 = 20 27752 = 55504 руб.
Накладные расходы при наплавке в среде пара
С4 = 20 261893 = 523786 руб.
Общая стоимость восстановления при наплавке в среде углекислого газа
Сbz1 = 27752 + 871 + 47454 + 55504 = 880885 руб.
Общая стоимость восстановления при наплавке в среде пара
Сbz2 = 261893 + 784 + 43338 + 523786 = 829801 руб.
Для двух выбранных способов восстановления по технико-экономическому критерию Cz выбираем оптимальный вариант.
Критерий Cz предложенный проф. А.В. Каракулевым [23 стр. 8] представляет относительную стоимость:
где z = 12 14 — номера присвоенные способам восстановления;
Свz — стоимость восстановления z - м способом руб.;
az — коэффициент учитывающий возможные потери от неожиданного отказа детали восстановленной z - м способом;
Pz — показатель относительной долговечности детали восстановленной z - м способом.
Соответственно для правильного выбора способа восстановления необходимо определить стоимость Свz показатель относительной долговечности Pz и значение коэффициента az.
Показатель относительной долговечности восстановленной детали Pz определяют исходя из следующих основных положений. В общем случае отказ наугад выбранной сложной детали восстановленной произвольно взятым способом может явиться следствием износа от трения или перегрузки или усталости материала или отслоения от детали нанесенного на нее металла.
Нельзя наперед точно предсказать по какой причине наступит отказ детали. Поэтому для наугад выбранного отказа рассматриваемой детали будет справедливо соотношение
f1 + f2 + f3 + f4 = 1
гдеf1 f2 f3 f4 — статистическая вероятность того что отказ восстановленной детали явится следствием соответственно:
f1 — износа при трении;
f2 — недостаточной статической прочности материала;
f3 — недостаточной усталостной прочности материала;
f4 — отслоения материала покрытия от материала детали.
Для того чтобы получить значение относительной долговечности восстановленной детали Pz необходимо кроме fzn знать еще значение коэффициента относительной долговечности Кzn. Этот показатель характеризует сопротивляемость детали восстановленной z - м способом тому или иному причинному фактору появления отказа (по отношению к новой детали).
Поскольку наперед нельзя точно предсказать следствием какого причинного фактора будет отказ восстановленной детали то для оценки долговечности удобнее всего использовать математическое ожидание определяемое по формуле
где fzn — статистическая вероятность того что отказ обусловлен n - й причиной [23 табл. 5];
Кzn — коэффициент относительной долговечности восстановленной z-м способом детали в отношении n - го причинного фактора отказа.
Вероятность появления отказа детали по износу прочности усталостной прочности и отслаиванию покрытия соответственно равна: f1 = 01; f2 = 079; f3 = 006; f4 = 005.
При восстановлении детали наплавкой в среде углекислого газа коэффициент долговечности по отношению к названным причинным факторам составит: Кz1= 072; Кz2 = 095; Кz3 = 090; Кz4 = 100.
При восстановлении детали наплавкой в среде пара коэффициент долговечности составит: Кz1= 09; Кz2 = 095; Кz3 = 075; Кz4 = 100.
Показатель Рz для наплавки в среде углекислого газа
Рz1 = 01 072 + 079 095 + 006 09 + 005 1 = 09265.
Показатель Рz для наплавки в среде пара
Рz2 = 01 09 + 079 095 + 006 075 + 005 1 = 09355.
Следовательно относительная долговечность восстановленной детали оказалась меньше долговечности новой детали для которой Pz = 1.
Возможность отбрасывания потерь учитываемых коэффициентом аz зависит от характера последствий отказа. Если отказ произойдет из-за усталости восстановленной детали то такой отказ может привести не только к поломке узла но даже к катастрофе. Это значит что риск возможности появления отказа от усталости может на практике обойтись во много раз дороже выгоды полученной от применения способа обеспечивающего большой срок службы детали в условиях естественного изнашивания при трении.
Поскольку отказы детали происходят по мгновенной схеме значение показателя аz определяется по формуле
аz = a1 f1 + a2 ( f2 + f3 + f4 )
где а1 — коэффициент учитывающий потери от естественного износа при трении; а1 — 1;
а2 — коэффициент учитывающий потери обусловленные появлением мгновенных отказов из-за недостаточной прочности недостаточной усталостной прочности и отслоения материала покрытия от основного материала детали; в ремонтной практике а2 = 10;
; ; ; — вероятность того что деталь восстановленная s-м способом откажет соответственно из-за износа недостаточной прочности недостаточной усталостной прочности и недостаточной прочности сцепления слоя покрытия с основным материалом детали.
При наплавке в среде углекислого газа
= 1 – Kz1 = 1 – 072 = 028
= 1 – Kz2 = 1 – 095 = 005
= 1 – Kz3 = 1 – 09 = 01
= 1 – Kz4 = 1 – 1 = 0
При наплавке в среде пара
= 1 – Kz1 = 1 – 09 = 01
= 1 – Kz3 = 1 – 075 = 025
Пользуясь результатами приема найдем значение аz для детали восстановленной наплавке в среде углекислого газа
аz1 = 1 01 028 + 10(079 005 + 006 01 + 005 0) = 0483
аz2 = 1 01 01 + 10(079 005 + 006 025 + 005 0) = 0555.
Для выбора способа восстановления по экономическому критерию определяем Сz и выбираем тот способ который будет характеризоваться минимумом этой величины.
Наплавка в среде углекислого газа
Наплавка в среде пара
В итоге получаем что оба способа практически равноценны и разница между ними несущественна. Выбираем наплавку в среде углекислого газа как наиболее распространенный способ при восстановлении деталей наплавкой. Дальнейшую разработку производим для выбранного способа.
Сущность способа заключается в том что электрическая дуга горит между электродом и наплавляемой деталью в струе газа вытесняющего воздух из плавильного пространства и расплав металла защищается от действия кислорода и азота воздуха.
Рассмотрим процесс наплавки стальной детали в среде углекислого газа. Электродная проволока 5 (рис.5) подается с постоянной скоростью специальным механизмом в зону горения через мундштук 1 и наконечник 4.
Рис. 5 Наплавка в среде углекислого газа
По трубке 2 через газовое сопло 3 поступает углекислый газ под давлением 5—20 МПа. Наплавку ведут на постоянном токе обратной полярности что обеспечивает получение более качественного шва и уменьшает разбрызгивание металла. Электродную проволоку применяют с повышенным содержанием марганца и кремния (Св.-08Г2СА Св.-12ГС Св.-18ХГСА Нп-30ХГСА и др.).
4.4.Выбор установочных баз
В качестве установочной базы принимаем чистую базу которая служила для обработки восстановленной поверхности при изготовлении детали. Деталь крепится в трехкулачковом самоцентрирующем патроне токарного станка с упором в торец и с поджимом задней бабкой станка через центровое отверстие.
4.5. Установление маршрута восстановления изношенной поверхности
Для восстановления изношенной поверхности трапецеидальной резьбы ходового винта целесообразны следующие операции:
Моечная операция: ванна с содовым раствором подвеска для мойки деталей.
Дефектовочная промеряют размеры и определяют износы. Стол дефектовщика ОРГ-1468.
Наплавочная восстановление резьбовой поверхности наплавка в среде углекислого газа. Полуавтомат сварочный.
Контрольная визуальный осмотр штангенциркуль ШЦ-II-160-002 ГОСТ 166-80.
Рихтовочная холодная правка винта ходового под прессом (при необходимости).
Токарная обтачивание поверхности 48-06 мм. Станок токарно-винторезный 1К62 патрон трехкулачковый 7100-0009 ГОСТ 2675-80 центр вращающийся ГОСТ 8742-75 проходной отогнутый резец с пластинкой Т15К6 штангенциркуль ШЦ-II-160-002 ГОСТ 166-80.
Токарная точение фасок 15° 45°. Станок токарно-винторезный 1К62 патрон трехкулачковый 7100-0009 ГОСТ 2675-80 центр вращающийся ГОСТ 8742-75 проходной отогнутый резец с пластинкой Т15К6 штангенциркуль ШЦ-II-160-002 ГОСТ 166-80.
Токарная нарезание резьбы. Станок токарно-винторезный 1К62 патрон трехкулачковый 7100-0009 ГОСТ 2675-80 центр вращающийся ГОСТ 8742-75 резец резьбовой Р6М5 штангенциркуль ШЦ-II-160-002 ГОСТ 166-80 калибр-кольцо Tr 48×12 ПР 7е ГОСТ 10071-89 калибр-кольцо Tr 48×12 НЕ 7е ГОСТ 10071-89.
Магнитная дефектоскопия. Дефектоскоп ПМД-70. Установка для размагничивания.
Контрольная стол дефектовщика ОРГ штангенциркуль ШЦ-II-160-002-1 ГОСТ 166-80 калибр-кольцо Tr 48×12 ПР 7е ГОСТ 10071-89 калибр-кольцо Tr 48×12 НЕ 7е ГОСТ 10071-89.
5.Разработка операций восстановления
5.1. Расчет режимов наплавки
Важным этапом разработки операций восстановления является расчет режимов выполнения этих операций.
Последовательность расчета режимов наплавки:
определяем толщину наплавляемого слоя в зависимости от величины износа и припуска на механическую обработку.
выбираем марку и диаметр электродной проволоки применительно к материалу детали и твердости ее поверхности;
выбираем и рассчитываем электрические параметры наплавки выбираем род сварочного тока напряжение тока при наплавке рассчитываем силу сварочного тока;
выбираем и рассчитываем кинематические параметры наплавки: скорость подачи проволоки скорость наплавки частоту вращения детали.
Толщина наплавляемого слоя обычно составляет от 06 до 20 мм на сторону [6]. Наплавка осуществляется в углекислом газе проволокой сплошного сечения.
Выбираем марку и материал проволоки. Главная особенность сварки в углекислом газе плавящимся электродом заключается в применении электродной проволоки с повышенным содержанием элементов - раскислителей (Mn Si и др.) компенсирующих их выгорание в зоне сварки. Для большинства углеродистых и низколегированных сталей рациональными пределами содержания элементов в электродной проволоке являются 006 012 % углерода 06 10 % кремния и 14 24% марганца. Наибольшее применение получили проволоки марок Св-08ГС (010 % С 140 170 % Мп 060 085 % Si) и Св-08Г2С (05 011 % С 180 210 % Mn 070 095 % Si). Кроме того в этих проволоках содержится 020 % хрома 025 % никеля а также не более 0025 % серы и 0030% фосфора.
Выбираем проволоку 20 Св-08Г2С ГОСТ 2246-70.
Расчет силы тока А при наплавке проволокой сплошного сечения производится по формуле:
где а – плотность тока в электродной проволоке Амм² (при сварке в СО2 a = 110 130 Амм²);
dэ – диаметр электродной проволоки мм при толщине свариваемой детали выше 6 мм dэ = 2 мм.
Механизированные способы сварки и наплавки позволяют применять значительно большие плотности тока по сравнению с ручной сваркой и наплавкой. Это объясняется меньшей длиной вылета электрода. Напряжение дуги и расход углекислого газа выбираются в зависимости от силы сварочного тока. При наплавочном токе Iнп = 3768 А напряжение дуги Uд = 32 В расход СО2 составляет 20 лмин.
Скорость подачи электродной проволоки мч рассчитывается по формуле:
где αp – коэффициент расплавления проволоки гА·ч;
ρ – плотность металла электродной проволоки гсм3 (для стали ρ = 78 гсм3).
Значение αp рассчитывается по формуле:
αp = 30 + 008 = 3 + 008 = 1807 гА·ч.
Тогда скорость подачи электродной проволоки
Скорость наплавки мч рассчитывается по формуле:
где αн– коэффициент наплавки гАч;
Fв – площадь поперечного сечения одного валика см². При наплавке в СО2 принимается равным 03 ÷ 07 см².
где – коэффициент потерь металла на угар и разбрызгивание. При сварке в СО2 = 01 015;
αн = 1807 (1 - 012) = 159 гАч.
Масса наплавленного металла г при наплавочных работах рассчитывается по формуле:
где Vн – объем наплавленного металла см3;
ρ – плотность наплавленного металла ρ = 78 гсм3;
гдеVр – объем наплавленного металла заполняющего профиль резьбы до образования цилиндрической поверхности ограниченной наружным диаметром резьбы d3 (рис. 3.3);
Vц – объем металла наплавленного на наружный диаметр резьбы d3.
гдеS – площадь сечения профиля наплавляемой поверхности резьбы;
n – количество витков резьбы n = 2333.
Площадь сечения профиля наплавляемой поверхности резьбы S находим как площадь прямоугольника со стороной а равной высоте профиля резьбы Н и стороной b равной ширине профиля резьбовой поверхности под наплавку по среднему диаметру резьбы с учетом износа (рис. 3.3)
S = a · b = 6 · (6 + 15) = 45 мм2 = 045 см2.
Vр = 045 · 13242 · 2333 = 139 см3.
где rн – радиус наплавленной поверхности rн = 26 мм;
r3 – радиус ограниченный наружным диаметром резьбы r3 = 235 мм;
lн – длина наплавленной поверхности по наружному диаметру резьбы находим из чертежа lн = 2705 мм.
Vц = ( · 262 – · 2352 ) · 2705 105000 мм3 = 105 см3.
Vн = 139 + 105 = 1495 см3.
Масса наплавленного металла
Gн = 1495 78 = 11661 г.
Время горения дуги ч определяется по формуле:
to = = = 0195 ч. = 117 мин.
Полное время наплавки ч определяется по формуле:
где kп – коэффициент использования сварочного поста (kп = 06 ÷ 07).
Расход электродной проволоки г рассчитывается по формуле:
где Gн – масса наплавленного металла г; – коэффициент потерь ( = 01 ÷ 015).
Gпр = 11661 (1 + 012) = 1306 г.
Расход электроэнергии кВт · ч определяется по формуле:
где Uд – напряжение дуги В;
– КПД источника питания при постоянном токе = 06 ÷ 07 при переменном = 08 ÷ 09;
Wo – мощность источника питания работающего на холостом ходе кВт. На постоянном токе Wо = 20 ÷ 30 кВт на переменном Wо= 02 ÷ 04 кВт.
A = 0195 + 25 · (03 – 0195) = 388 кВт · ч.
Выбираем сварочный полуавтомат (табл. 16) по рассчитанным параметрам. Полуавтомат сварочный ПДГО-508 с питанием от выпрямителя типа ВДУ–506 предназначен для механизированной сварки низкоуглеродистых легированных и коррозионностойких сталей сварочной проволокой на постоянном токе.
Таблица 16- Характеристики сварочного полуавтомата ПДГО-508
Напряжение питающей сети В
Частота питающей сети Гц
Номинальный сварочный ток (при ПВ=60%) А
Пределы регулирования сварочного тока А
Напряжение холостого хода В
Номинальное рабочее напряжение В
Диаметр стальной электродной проволоки мм:
Скорость подачи электродной проволоки мч
Габаритные размеры (механизм подачи) мм не более
5.2. Расчет режимов резьбонарезной операции
Для механической обработки детали после восстановления принимаем универсальный токарно-винторезный станок 16К20.
При выборе режимов резания (глубины подачи и скорости резания) вначале устанавливается глубина резания в соответствии с назначенными припусками. При этом глубина резания черновой механической операции складывается из суммы припуска на эту операцию и припуска от неточности изготовления заготовки. Затем определяем подачу скорость резания частоту вращения шпинделя усилие и мощность резания [30].
Подачу назначаем максимально допустимую. При черновой обработке подача ограничивается прочностью самого слабого звена технологической системы СПИД (станок — приспособление — инструмент — деталь). При чистовой обработке и отделке подачу определяем в зависимости от заданных точности и шероховатости поверхности.
Скорость резания рассчитываем по формулам резания руководствуясь при этом экономической стойкостью режущего инструмента. По скорости резания находим частоту вращения шпинделя. Значение частоты вращения шпинделя и подачу согласовываем с паспортными данными станка принимая ближайшие наименьшие значения.
Производим расчет всех перечисленных режимов резания для одной операции механической обработки – нарезание трапецеидальной резьбы; для остальных операций режимы подбираются (табл.17) по справочным таблицам
[ 7; 24; 30 ] (рис.6).
Таблица17- Трапецеидальная резьба по ГОСТ 9484-81
Внутренний диаметр d1 мм
Рис.6 Номинальные профили наружной и внутренней
трапецеидальной резьбы
Существует несколько схем нарезания резьбы резцом. Если шаг резьбы меньше 25 мм поперечная подача имеет радиальное направление sp и образование резьбы происходит по профильной схеме (рис. 7 а). Резьбу большого шага (2 мм и более) нарезают не с поперечным а с боковым врезанием резца при котором работает только одна режущая кромка. Эта схема называется генераторной (рис. 7 б). При боковом врезании облегчается процесс резания повышается качество.
Для осуществления бокового врезания верхние салазки суппорта разворачивают под углом (для трапецеидальной резьбы 15°) относительно своего нормального положения. Врезание осуществляют рукояткой верхних салазок суппорта. Последние один - два чистовых рабочих ходов выполняют с поперечной подачей. В момент врезания резьбовой резец под действием осевой силы несколько отжимается и первый виток резьбы получается более полным чем остальные. Последний виток также получается более полным.
Рис. 7 Схемы нарезания резьбы резцами
Трапецеидальные резьбы нарезают по профильной схеме которая менее производительная чем генераторная но позволяет получать меньшую шероховатость поверхности резьбы. Итак черновые проходы осуществляем по генераторной схеме чистовые – по профильной схеме.
При нарезании резьбы резцами различают продольную подачу s равную шагу резьбы P и поперечную равную части высоты профиля соответствующей числу рабочих ходов i необходимых для образования резьбы.
Число рабочих ходов при нарезании наружной трапецеидальной резьбы по стали резьбовым резцом из быстрорежущей стали Р6М5 составит:
черновых ходов – 21;
чистовых ходов – 10.
Глубина резания при выполнении рабочих ходов в среднем составит
Принимаем для черновой обработки t = 025 мм. Тогда глубина резания для чистовой обработки
Скорость резания зависит от обрабатываемого материала резьбового резца: при обработке стали быстрорежущими резцами она составляет 20–35 ммин. Для чистовых проходов скорость резания увеличивают в 15–2 раза [28].
Скорость резания ммин при нарезании трапецеидальной резьбы резцами из быстрорежущей стали определяется по формуле
где – коэффициент зависит от условий резания материала режущей части резца и обрабатываемого материала ;
Т – период стойкости инструмента мин;
– общий поправочный коэффициент на скорость резания учитывающий условия резания.
гдеКмv – коэффициент учитывающий качество обрабатываемого материала;
Киv – коэффициент учитывающий материал режущей части инструмента;
Ксv - коэффициент учитывающий способ нарезания резьбы. Если резьба нарезается одним чистовым резцом Ксv = 075.
Коэффициент Кмv для стали определяется по формуле
гдев – фактический предел прочности обрабатываемого материала;
Кг – коэффициент характеризующий группу стали по обрабатываемости;
nv – соответствующий показатель степени.
= 1157 10 075 = 0868.
Для черновой обработки
v = 0868 = 21818 ммин.
Для чистовой обработки
v = 0868 = 5462 ммин.
После определения расчетной скорости резания необходимо проверить возможность осуществления ее на выбранном станке.
Для этого находим значение расчетной частоты вращения шпинделя станка обмин:
для черновой обработки
для чистовой обработки
nр2 = = 36239 обмин.
Полученные значения расчетной частоты вращения шпинделя сравниваем с имеющимися на станке 16К20 и принимаем ближайшие минимальные
n1 = 125 обмин n2 = 315 обмин.
Фактическая скорость резания
Тангенциальная составляющая силы резания Н при нарезании резьбы резцами на один рабочий ход определяется по формуле
гдеСp – коэффициент;
Kp – коэффициент учитывающий качество обрабатываемого материала Kp = Kmp
Где n – соответствующий показатель степени.
Для черновой обработки
Pz = 094 = 1690432 Н
Эффективная мощность кВт при нарезании резьбы резцами на один рабочий ход определяется по формуле
При нарезании резьбы за несколько проходов рассчитанная мощность умножается на отношение фактической высоты профиля срезаемой за один проход к высоте резьбы по ГОСТ.
Nэ = 298 · = 0114 кВт
Nэ = 1311 · = 0252 кВт.
Потребная мощность на шпинделе станка кВт
где ст – КПД станка для 16К20 ст = 075.
По паспорту мощность главного электродвигателя станка 16К20 равна 10 кВт.
Затем рассчитываем нормы времени на обработку детали.
Норма времени на выполнение операции по обработке одной заготовки (штучное время) состоит из нескольких элементов
tшт = tо + tв + tт + tорг + tп
гдеtо – основное (технологическое) время;
tв – вспомогательное время;
tт – время технического обслуживания рабочего места;
tорг – время организационного обслуживания рабочего места;
tп – время перерывов.
Основное время при станочной обработке определяют расчетом для каждого технологического перехода
где L — расчетная длина обработки мм;
Sм — минутная подача инструмента мм равная произведению частоты вращения шпинделя n обмин на подачу за один оборот S.
При работе инструмента значение L определяется по формуле
lсх — путь схода режущего инструмента мм.
Длину l берем из чертежа заготовки. Значения lвр и lсх находят из геометрических соотношений инструмента и детали.
L = 280 + 12 + 20 = 312 мм.
tо = · 21 = 4368 мин.
tо = · 10 = 0825 мин.
Вспомогательное время включает время на установку закрепление и снятие обрабатываемой заготовки на управление механизмами оборудования на подвод и отвод рабочего инструмента а также на измерение обрабатываемой заготовки.
Рассмотрим составляющие вспомогательного времени подробно для выполнения трапецеидальной резьбы.
При обработке резьбы время на установку закрепление и снятие обрабатываемой заготовки исключается поскольку деталь была закреплена ранее при обработке поверхности 48-06 мм под нарезание резьбы и установочные базы не изменяются. Время на установку режимов резания на станке принимаем 1 мин. Время на подвод и отвод инструмента а также время на обратный (холостой) ход зависит от числа проходов принимаем 025 мин. на проход.
Время на измерения при черновой обработке резьбы назначаем 1 мин. При чистовой обработке резьбы время на измерения и контроль возрастет из-за использования проходного и непроходного резьбового калибра-кольца для чего нужно отводить задний центр и наворачивать проходной калибр-кольцо на всю длину резьбы. Принимаем время на измерения при черновой обработке резьбы 5 мин.
При чистовой обработке резьбы назначаем время на снятие детали 05 мин.
tв черн = 1 + 025 · 21 + 1 = 725 мин.
tв чист = 1 + 025 · 10 + 5 + 05 = 90 мин.
Сумма основного и вспомогательного времени дает оперативное время ton.
ton черн = 4368 + 725 = 1162 мин.
ton чист = 0825 + 90 = 9825 мин.
Время технического и организационного обслуживания рабочего места составляет 4 - 8% от оперативного времени.
tт черн = 1162 · 006 = 07 мин.
tт чист = 9825 · 006 = 06 мин.
tорг черн = 1162 · 004 = 046 мин.
tорг чист = 9825 · 004 = 04 мин.
Время перерывов tп для механических цехов составляет 25% от оперативного времени.
tп черн = 1162 · 0025 = 03 мин.
tп чист = 9825 · 0025 = 025 мин.
tшт черн = 4368 + 725 + 07 + 046 + 03 = 13078 мин.
tшт чист = 0825 + 9 + 06 + 04 + 025 = 11075 мин.
Проектирование моторного цеха
В моторном цехе производят разборку ремонт и сборку двигателей внутреннего сгорания выполняют все виды ремонтных работ. Работы по восстановлению двигателей (сварка и наплавку гальваническое наращивание) выполняют в соответствующих отделениях ремонтного завода.
Расчет основного оборудования выполнен в п. 3.8.3. Вспомогательное оборудование и производственный инвентарь принимаем без расчета по необходимому технологическому комплекту. Количество испытательных стендов определяем по формуле:
где: tд – время на установку и снятие двигателя tд = 06 ч [1];
tи – время обработки и испытания двигателя tи=15 ч;
Nд – годовая программа выпуска двигателей Nд=3325 шт.;
Кст – коэффициент использования стенда по времени Кст=08 [1стр.];
Кпо – коэффициент учитывающий повторную обработку Кпо=11[1стр.].
Принимаем 2 обкаточных стенда. Остальное оборудование определяем по трудоемкости работ. Результаты расчета заносим в табл. 15. На основании расчета принимаем конкретные модели оборудования и заносим их обозначение в табл.16
Таблица 18 – Количество оборудования в моторном цехе
Таблица 19 – Основное технологическое оборудование
Разработка технико-экономических показателей завода
Определим основные показатели завода рассматриваемые в данном проекте. Нормируемые оборотные средства W тыс.руб. условно принимаем равным W=03*В=03*64813225=19443968 тыс. руб.
Себестоимость выпускаемой продукции S тыс. руб. составит
где Зр- заработная плата производственных рабочих;
М- стоимость запасных частей и ремонтных материалов (условно принимаем равной 28* Зр).
где То- общая трудоёмкость годовой программы-1110279 чел.-ч.;
Сч- часовая тарифная ставка рабочего по среднему разряду (принимаем 70 руб.- с учётом коэф. инфляции К=10);
kдоп- коэффициент учитывающий доплаты к основной зарплате
( принимаем kдоп=13);
Зр=1110279*70*13=10103539 руб.
М=28*Зр=28*10103539=28289909 руб.
Н=2*Зр=2*10103539=20207078 руб.
S=10103539+28289909+20207078=58600526 руб.
Стоимость завода С (при укрупненном расчёте) составит:
С=СЗД+ СОБ+ СИИ+ СТР
где СЗД- стоимость здании и сооружений;
СОБ- стоимость производственного оборудования с учетом монтажа: СОБ=075* СЗД;
СИИ- стоимость дорогостоящего инвентаря и инструмента: СИИ=03* СЗД;
Стоимость зданий и сооружений укрупнено определяется по стоимости 1 м3 объема здания. Ориентировочно стоимость 1 м3 зданий принимают равной: для производственных зданий 40 руб.; для вспомогательных 28 руб.; для административных 88 руб.
Определим объём зданий.
Главный производственный корпус:
Объём производственный VП1=5528*108=59702 м3.
Объём вспомогательный VВ1=1770*108=19494 м3.
Объём вспомогательный VВ2=661*42=27762 м3.
На территории завода:
Объём административного здания VА1=12*24*6=1728 м3.
Объём вспомогательного здания (гараж) VВ2=12*69*42=3477 м3.
Объём вспомогательного здания (котельная) VВ3=18*12*42=907 м3.
Объём вспомогательного здания (ГСМ) VВ4=12*12*42=604 м3.
Объём вспомогательного здания (трансформаторная подстанция) VВ5=6*6*42=151 м3.
Производственный объем зданий VП=59702 м3;
Вспомогательный объем зданий VВ=272582 м3;
Административный объём зданий VА=1728 м3.
СЗД=59702*40+272582*28+1728*88=3303374 руб.
С=СЗД+075СЗД+006СЗД+03СЗД=3303374+2477531+198202+
+991012=6970119 руб.
Прибыль. П=В-S=64813225-58600526=6212699 тыс. руб.
Рентабельность завода %
Фп- 1584845 т. руб. плата за производственные фонды составляющая 6% от (С+W)
Полученные данные заносим в табл. 17 там же произведём остальные расчеты.
Таблица 20 –Технико-экономические показатели.
Выпуск продукции (программа завода)
Количество производственных рабочих
Стоимость завода (основные фонды)
Рентабельность завода
Окупаемость основных фондов
Выработка на одного производственного рабочего
Выпуск продукции на 1 станок
Выпуск продукции на 1 м2 производственной площади
Обеспечение безопасности труда работников моторного цеха. Защита от шума.
1. Техника безопасности моторном цехе
Оценка параметров шума проводиться по предельному спектру (ПС) и по
эквивалентному уровню звука.
Рис.8 Оценка параметра шума
Шум по временной характеристике делится на постоянный и непостоянный (рис.8). Критерием оценки является диапазон изменения УЗД за рабочую смену. Если разность уровней звукового давления за время наблюдения меняется в пределах 5 дБ то шум считается постоянным.
Рис. 9 Классификация шума
Аттестация рабочих мест показывает что уровни шума в помещении моторного цеха в настоящее время превышают все допустимые нормы. По величине УЗД оценивается класс рабочего места и при присвоении любой степени класса 3 (вредный) разрабатываются мероприятия по снижению шума до нормы а на период их внедрения рабочему выплачиваться надбавка за вредные условия труда. Если рабочему месту присваивается класс 4 то такое рабочее место должно быть ликвидировано или переоборудовано.
Предельно допустимые уровни (ПДУ) звукового давления для рабочих мест установлены вне зависимости от смены (ночная или дневная) и зависят только от вида трудовой деятельности на данном рабочем месте. При этом для тонального и импульсного шума номер предельного спектра принимается на 5 дБ ниже нормируемого.
Основными источниками шума являются двигатели внутреннего сгорания металлообрабатывающие станки компрессоры тормозные стенды вентиляционные системы и т.п.
Основными методами защиты от шума рабочего места являются звукоизоляция звукопоглощение экранирование и снижение шума в источнике. Наиболее эффективным является снижение шума в источнике возникновения.
Если не удается снизить шум в источнике рационально прибегнуть к его звукоизоляции. Для этого используются капоты (кожухи) выгородки или переносят источник в отдельное изолированное помещение.
Рис.10 Схема определения шума
Этим методом достигается наибольшее снижение шума на рабочем месте величина которого определяется исключительно расходами на его организацию.
Экранирование широко применяется самостоятельно исключительно в открытом пространстве. Применение экранирования источника или рабочего места в закрытом помещении целесообразно только совместно с системой звукопоглощения. Иначе отраженный от ограждающих поверхностей звук имея высокую интенсивность сводит на нет защитные свойства экрана. Эффект от экранирования растет с ростом частотного состава шума.
Рис.11 Схема экранирования источника шума
Обработка ограждающих поверхностей помещения во всех случаях дает положительный эффект и должно применяться при каждой возможности Пример конструктивного исполнения звукопоглощающей облицовки приведен на рис.10 Это подвесной потолок типа ЛАП 06-06. Рабочим телом такой конструкции является минераловатная плита 2 обтянутая синтетической пленкой 1 для предотвращения высыпания частиц плиты. Крепление потолка выполняется с помощью крюковой подвески 3. Для защиты конструкции от повреждения снизу она запирается перфорированным алюминиевым листом 4 с диаметром перфорации 5 мм.
Наряду со звукопоглощающими облицовками нашли применение штучные поглотители шума. Они представляют собой пространственные конструкции небольшого размера в виде куба параллелепипеда или иной геометрической фигуры которые размещаются непосредственно у источника шума. Установка штучных поглотителей способствует потере энергии звуковой волны еще до распространения ее в пространстве.
На рис.12 приведена конструкция объемного поглотителя выполненного в виде конуса с диаметром у основания 600 мм при полной высоте 900 мм. С помощью колец 1 звукопоглощающий материал 2 крепиться к каркасу и удерживается внутри конуса который обтянут капроновой сетчатой тканью или стеклотканью 3. Вся конструкция собирается на кронштейне 4 и может устанавливаться на полу или закрепляться с помощью крюковой подвески.
Кроме рассмотренных методов в практике борьбы с шумом применяются кабины дистанционного наблюдения (управления) за шумным технологическим процессом например в деревообработке компрессорных станциях (рис.12) и т.п.
Рис.12 Кабина дистанционного наблюдения
Конструктивно кабины выполняются открытыми и закрытыми. В последнем случае вход в кабину располагается с противоположной от источника шума стороны а на некотором расстоянии от него устанавливается звукопоглощающий экран.
Рис.13 Схема снижения шума в моторном цехе
Рассмотрим снижение шума в помещении моторного цеха при помощи звукопоглощения.
Звукопоглощение как физическое явление представляет собой потерю энергии звуковой волны на перемещение воздуха в порах при ее падении на преграду. Энергия волны расходуется на преодоление сопротивления трения воздуха о стенки пор ограждающей конструкции и переходит при этом в тепло. Полная картина взаимодействия звуковой волны с преградой показана
Рис. 14 Баланс энергии звуковой волны
Энергия звуковой волны при своем падении на преграду перераспределяется в трех направлениях: поглощается — IПГЛ отражается — Iотр и проникает через преграду — IПРШ . Эти процессы характеризуются соответствующими коэффициентами:
—проницаемости (за преграду)
Материалы и конструкции считаются звукопоглощающими если коэффициент звукопоглощения α>025 (таб.21). Все мягкие и пористые материалы обладают хорошей звукопоглощающей способностью и характеризуются высоким коэффициентом звукопоглощения. Значение этого коэффициента зависит от особенностей материала частоты падающего звука и приводится в таблицах в зависимости от среднегеометрической частоты октавной полосы
Рис.15 Принцип расположения звукопоглощающей облицовки: 1 — поддерживающий элемент; 2 — звукопоглощающий материал
Практическое снижение уровня звукового давления (уровня звука) за счет звукопоглощения не превышает 10 дБ.
Таблица 21 – Коэффициенты звукопоглощения α материалов конструкций
Материал конструкция
Величина коэффициента на среднегеометрической частоте Гц
Паркет по деревянному основанию
Линолеум толщиной 5 мм по твердому основанию
Ограждающие конструкции (стены потолок)
Стена оштукатуренная и окрашенная масляной краской
Деревянная обивка (сосновая доска толщиной 10 мм)
Деревянная панель толщиной 10 мм с воздушным промежутком 50 мм
Звукопоглощающие конструкции
Плиты минераловатные акустические:
перфорированные (ПАО) без воздушного промежутка
то же с воздушным промежутком 100 мм
то же с воздушным промежутком 50 мм
гладкие декоративные (ПАД) без воздушного промежутка
Остекление силикатным стеклом
Звукопоглощение реализуется в виде разнообразных конструкций которые закрепляются на ограждениях помещения— потолках стенах — (рис ) или вывешиваются в зоне действия источника шума (штучные звукопоглотители).
Звукопоглощающий материал закрепляется непосредственно на ограждении либо в конструкции размещенной на некотором расстоянии D от ограждения. Величина этого расстояния выбирается таким чтобы четверть длины волны звука λ уровень звукового давления на которой требует снижения приходилась на толщу материала.
Длина волны (λ) — это расстояние на которое распространяется волна в течение одного периода определяется известной зависимостью:
где v — скорость звука (в воздухе v=340 мс)
Т— период колебаний с.
При решении задачи на звукопоглощение за величину f (частота звука Гц) принимают среднегеометрическую частоту октавной полосы fст. Звукопоглощающим материалом или конструкциями в первую очередь облицовывают потолок стены на расстоянии выше 2 м от пола а также межоконные пространства.
Расчетное выражение определяющее эффективность звукопоглощения представляется в виде
где Аобя — эквивалентная площадь звукопоглощения после облицовки помещения м2;
Ао — эквивалентная площадь звукопоглощения необлицованного помещения м2.
Обе величины рассчитываются по общей формуле с подстановкой своих площадей и соответствующих коэффициентов звукопоглощения:
где n - число поверхностей с коэффициентами звукопоглощения α
Si — площади этих поверхностей м2.
Эквивалентная площадь звукопоглощения необработанного помещения может быть представлена выражением
Aо= (αS)пот + (αS)пол + (αS)стен + (αS)окн + (αS)двр
где Sпот Sпол Sстен Sокн Sдвр площади потолка пола стен окон и дверей м2 а α- соответствующий коэффициент звукопоглощения.
Соответствующее выражение для обработанного помещения Аобл будет отличаться от рассмотренного выражения значениями коэффициентов звукопоглощения тех поверхностей на которые нанесена звукопоглощающая облицовка.
Характеристика помещения: длина — 10 м ширина — 7 м высота — 35 м
площадь окон с двойным остеклением 20 м;
материал пола — линолеумом по твердому основанию
дверь — деревянная панель толщиной 10 мм с воздушным промежутком 50 мм площадью 25 м2.
Измеренные уровни звукового давления в помещении моторного цеха до акустической обработки в сравнении с нормами даны в табл.22
Таблица 22 - Уровни звукового давления
Измерительные и аналитические работы в лаборатории
Значение уровня звукового давления дБ на среднегеометрической частоте Гц
Из табл. 23 видно что наибольший уровень звукового давления находится на среднегеометрической частоте 125 Гц. Поэтому в качестве звукопоглощающей облицовки предполагается использовать плиты минераловатные гладкие с воздушным промежутком 100 мм которые на этой частоте дают наибольший эффект. Дверь не обрабатывается.
Подробный расчет выполним для fсг = 1000 Гц.
Определим площади ограждающих конструкций
—потолка и пола Sпол=Sпот = 1070=70 м2;
—стен Sct=(1003520)+(703520)+200+25=965 м2.
Рассчитаем эквивалентные площади звукопогло
щения необработанного помещения выбирая значения
коэффициентов звукопоглощения из табл. [10]:
—потолок A0пот= (αS)пот = 002700= 14 м2;
—пол:A0пол= (αS)пол = 003700=21 м2;
—стен:Аостн= (αS)стен = 003965=29 м2;
—окно:Aоокн= (αS)окн = 012200=24 м2
—дверь:Aoдвр=(αS)двр=00525=012 м2.
Эквивалентную площадь звукопоглощения всего помещения получим сложив полученные значения для каждого ограждения:
Ао= Aопот +Аопол+ Аостн + Aоокн +Аодвр=891 м2
Выполнив аналогичные расчеты для остальных среднегеометрических частот их результаты сведем в табл. 23
Таблица 23 – Результаты расчетов эквивалентной площади звукопоглощения необработанного помещения А0 пом
Значения параметра на среднегеометрической частоте октавной полосы Гц
Потолок Sпот = 700 м2
Эквивалентная площадь звукопоглощения помещения Апом
Эквивалентные площади звукопоглощения обработанного помещения (кроме окон и
дверей т.к. они не обрабатываются). Подробный расчет также выполним для fсг =1000 Гц:
—потолок Aпот= (αS)пот = 050700=350 м2;
—пол Aпол= (αS)пол =008700=56 м2
—стена Астн= (αS)стен =050965=482 м2;
—окно Aокн= (αS)окн =012200=24 м2;
—дверь Aдвр=(αS)двр =005-25=012 м2.
Аналогичные расчеты проведем для октавных полос во всем диапазоне среднегеометрических частот от 125 до 1000 Гц а необходимые данные для окон и двери найдем в табл ..
Эквивалентную площадь звукопоглощения обработанного помещения получим сложив значения полученные для каждого ограждения:
Аобл = Aпот + Aпол + Астн + Aокн + Aдвр =913 м2.
Все результаты расчета параметров акустически обработанного помещения сведем в табл. 24
Таблица 24 – Результаты расчетов эквивалентной площади звукопоглощения обработанного помещения Апом
Рассчитаем эффективность (снижение уровня звукового давления) от применения выбранных конструктивных решений. дБ.
Гигиеническая оценка проведенных мероприятий по снижению шума в помещении. С этой целью необходимые результаты сведем в табл. 25
Таблица 25 – Оценка эффективности принятого решения
Значение параметра дБ на среднегеометрической частоте Гц
УЗД на рабочем месте дБ
Допустимый УЗД дБ (ПС-55)
Превышение допустимого УЗД дБ
Эффективность звукопоглощения дБ
Эффективность звукопоглощения выше превышения допустимого УЗД на рабочих местах моторного цеха.
Расчет вентиляции производится для моторного цеха. Исходными являются кратность обмена воздуха в 1 час и кубатура помещения.
Кубатура цеха имеющего затяжку определяется по формуле:
где F – площадь пола цеха -84000м2
h – высота цеха -10800 м
h3 - высота от затяжки до конца кровли в м =15 м
производительность вентилятора Wв определяется по формуле:
где V – кубатура здания в м3
Кв – кратность обмена воздуха в 1 час = 15
Мощность электромотора Nв для вентилятора определяется из выражения:
где Hв – напор воздушного столба вентилятора равный 100 – 200 мм вод ст.
– коэффициент запаса мощности вентилятора (принимается=110 – 150)
в – к.п.д. вентилятора (принимается в=040 +058)
р – к.п.д. ременной передачи (принимается р=09)
По производительности вентилятора Wв выбираются тип и модель вентилятора а к ним электромотор. Принимаем по справочнику [8] осевой вентилятор модели У-12.
Требуемая мощность ;
Производительность – 25000 м3час;
Потребляемая мощность:;
Полное давление: 20 Н;
где I-передаточное число.
Диаметр шкива вентилятора – 240 мм.
Диаметр шкива электродвигателя – 140 мм.
Число и тип клиновидных ремней 3хБ.
Рис.16 Осевой вентилятор У-12
Туревский И.С. Дипломное проектирование автотранспортных предприятий. – М.: ИД «Форум»- ИНФРА-М 2008.
Лебедев В.А. и др. Технология машиностроения. Проектирование технологий изготовления изделий. – Ростов нД: Феникс 2008.
Мачульский И.И. Погрузочно-разгрузочные машины. – М.: 2000.
Абрамов И.В. и др. Сборка машин и механизмов. – Ижевск.: 2000.
Ковшов А.Н. Технология машиностроения.- М.: Машиностроение 1987.
Панова А.А. Обработка металлов резанием; справочник техголога. – М.: Машиностроение 1988.
Я кубович А.А. Задание по черчению для строителей. – М.: Высшая школа 1989.
Рысин С.А. Вентиляционные установки машиностроительных заводов. – М.: Машгиз 1961.
ГОСТ 12.1.003-83. ССБТ. Шум. Общие требования безопасности. – М.: Изд-во стандартов 1983 8с.
Бекасов В.И. Васин В.К. Снижение шума в расчетной точке. М. РГОТУПС 2007 61с.
Главный корпус new.cdw

Наименование помещения
Участок наружной мойки
Слесарно ремонтный цех
Комплектовочный участок
Участок испытательный
Ремонтно-механическое отделение
Сварочно-наплавочный участок
Кузнечно-термический участок
Жестяницко-медницкий участок
Электротехнический участок
Склад запасных частей
Склад двигателей и агрегатов
Склад лесоматериалов
-Машины поступившие в ремонт
узлы и детали проходящие дефектацию и ремонт
-Отремонтированные машины
Условные обозначения
Технология.cdw

Восстановление винта ходового
В-II-50 ГОСТ 2590-88
-3ГП-М1-ТВ1 ГОСТ 1050-88
*Размеры для справок
** Размер обеспечивается инструментом.
Маркировать шрифтом 10-Пр3 ГОСТ 26.020-80.
Рекомендуемые чертежи
- 09.07.2014