Проект завода по капитальному ремонту строительных машин с разработкой разборочного цеха




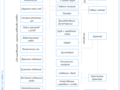
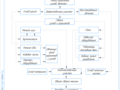
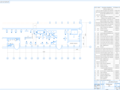
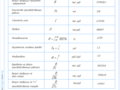
- Добавлен: 25.01.2023
- Размер: 738 KB
- Закачек: 1
Описание
Состав проекта
![]() |
![]() |
![]() |
![]() ![]() ![]() |
![]() ![]() ![]() |
![]() |
![]() ![]() ![]() |
![]() ![]() ![]() ![]() |
![]() ![]() ![]() ![]() |
![]() ![]() ![]() ![]() |
![]() ![]() ![]() ![]() |
![]() ![]() ![]() ![]() |
![]() ![]() ![]() ![]() |
![]() ![]() ![]() ![]() |
![]() ![]() ![]() ![]() |
Дополнительная информация
Пояснительная записка .doc
1 Анализ ремонтных предприятий 8
2 Последовательность проектирования ремонтных предприятий .10
1. Анализ ремонтной программы 14
2. Проектирование ремонтного предприятия ..24
2.1. Выбор типа ремонтного завода ..24
2.2. Расчет годовой производственной программы 26
2.3. Разработка схемы технологического процесса .32
2.4. Принятие структуры ремонтного завода 33
2.5. Расчет трудоемкости по цехам и отделениям 35
2.6. Расчет режима работы предприятия ..38
2.7. Расчет численности рабочего персонала 40
2.8. Расчет количества оборудования и рабочих мест 44
2.9. Расчет площадей ..47
2.10. Компоновка цехов 53
2.11. Разработка схемы генерального плана предприятия .55
Технологический раздел 57
Разработка разборочного цеха 65
Разработка стенда 73
1. Описание устройства и работы стенда .73
2. Выбор и расчет схемы привода .75
3. Расчет деталей стенда 77
Расчет технико - экономических показателей предприятия ..83
Охрана труда и техника безопасности на предприятии .87
Список использованной литературы 95
С целью увеличения темпов строительных работ осуществляется разработка и выпуск машин специально предназначенных для ликвидации ручного труда машин повышенной единичной мощности и производительности и наконец машин обеспечивающих существенную экономию топлива и других энергоресурсов. Большое значение придается насыщению строительного комплекса многофункциональными машинами оснащенными широким набором сменного рабочего оборудования.
В выполнении задач строительства содержание строительных машин в исправном состоянии играет не последнюю роль парк строительных машин в настоящее время достигает по численности одного миллиона единиц включая экскаваторы бульдозеры скреперы и т.д.
Плановый подход к организации ремонта машин позволяет внедрить метод индустриализации ремонтных работ. Индивидуальная основа и специализация в свою очередь позволяет снижать расходы на ремонтные работы.
Широкое применение в жизни современного человека разнообразных машин и механизмов поставило конкретную задачу в правильной организации их ремонта поддержания работоспособности с наименьшими затратами. Восстановление первоначальных свойств машин и механизмов или наука о ремонте требует знания основ технологии машиностроения базируется на ряде положений из других технологических дисциплин таких как «Технология металлов» «Металловедение и термическая обработка» «Станки и режущие инструменты» «Основы взаимозаменяемости и технические измерения» и т.д. но имеет целый ряд особенностей которые определяют специфику технологического процесса ремонтного производства.
В отличие от процесса производства машин и механизмов процесс ремонта начинается с их разборки. Разборочные работы – первая специфическая черта технологии ремонта. Изучая способы восстановления первоначальных свойств
машин и механизмов наука о технологии ремонта основывается на точных представлениях об их состоянии. Она изучает характер износов и дефектов деталей их сочетания и остаточную долговечность деталей.
В ремонтном производстве эти задачи решаются при дефектоскопии (контроле – сортировке) деталей разобранной машины что составляет вторую специфическую черту технологии ремонта.
При сборке новых машин и механизмов технические условия на сборку предопределяются техническими требованиями на изготовление деталей (рабочими чертежами). Сборку машин и механизмов при ремонте осуществляют в значительной части из работавших деталей (восстановленных и годных без ремонта) которые по отдельным параметрам отличаются от новых. В связи с этим замыкающее звено размерной цепи изменяется в допускаемых пределах. Таким образом технические условия на сборку восстановленных машин и механизмов имеют свою специфику. Это третья отличительная черта технологии ремонта.
Процесс восстановления деталей разобранной машины сводится к ряду операций при помощи которых деталям возвращают их первоначальную работоспособность. Отличие способов восстановления изношенных деталей от способов их изготовления является четвертой особенностью технологи ремонта.
Важной задачей ремонтного производства является модернизация. Под модернизацией понимается обновление машин и механизмов находящихся в эксплуатации устранение их морального износа посредством применения ряда технических достижений используемых в новейших разработках. Являясь одной из форм технического прогресса модернизация позволяет при сравнительно небольших затратах совершенствовать конструкцию ранее выпущенных машин и механизмов повышать их технический уровень и тем самым увеличивать сроки службы.
1. Анализ ремонтных предприятий
Технологический прогресс в ремонтном производстве неразрывно связан с ростом концентрации и развитием специализации и кооперирования производства. При специализированном производстве и при увеличенном количестве выпуска изделий резко повышается производительность труда уменьшаются трудовые затраты снижается себестоимость выпускаемой продукции.
Специализированное производство характеризуется однородностью выпускаемой продукции технологией производства наличием специализированного оборудования приспособлений и инструмента.
Специализация предприятий имеет три основные формы: предметную; технологическую; подетальную. Предметная специализация предусматривает выпуск ремонтным предприятием машин определенных типов или марок. В этом случае устраняется распыленность производства ремонта машин на многих заводах и появляется возможность сосредоточить его на одном или нескольких специализированных предприятиях. При технологической специализации ремонтные предприятия специализируются на работах определенных видов. Подетальная специализация характеризуется ремонтом отдельных узлов и деталей машин. В настоящее время наибольшее распространение получила предметная специализация Специализация предприятия приводит к значительному сокращению номенклатуры деталей материалов полуфабрикатов инструментов технической документации а следовательно и к упрощению организации производства. Специализация производства вызывает необходимость более широкого кооперирования при котором участие в ремонте машин принимают не одно а несколько предприятий. При такой кооперации смежные предприятия специализируются на ремонте отдельных узлов агрегатов и деталей поставляя свою продукцию на головной завод.
Непрерывный рост парка дорожно-строительных машин его концентрация в
отдельных районах сосредоточенного строительства намечаемые мероприятия по сокращению числа размеров машин дальнейшего производства универсальных машин унифицированных агрегатов и нормализованных деталей открывают перспективу более узкой специализации ремонтного открытого производства.
В целях сокращения времени на транспортирование ремонтного фонда готовой продукции ремонтные предприятия должны быть максимально приближены к районам сосредоточенного строительства. Капитальный ремонт машин на таких предприятиях целесообразно проводить на базе готовых агрегатов получаемых со специализированных агрегаторемонтных предприятий. В связи с тем что агрегаты более транспортабельны чем машины в сборе агрегаторемонтные предприятия могут быть рассредоточены на значительных расстояниях от ремонтных объектов и обслуживать как головные заводы так и крупные машинные парки.
Организация ремонтного хозяйства для дорожных и строительных машин несколько усложняется по сравнению с организацией автомобильного парка так как дорожные и строительные машины весьма различны по своей конструктивной сложности и к тому же во время эксплуатации находятся в различных хозяйствах расположенных друг от друга на значительных расстояниях. В этих наиболее целесообразно текущий ремонт производить специальными ремонтными бригадами или передвижными мастерскими непосредственно на месте используя готовые запасные детали и агрегаты.
Передвижные мастерские оборудуют либо в вагончиках перемещаемых тракторами или тягачами либо на грузовом автомобиле со специальным прицепом. Такие передвижные мастерские снабжены универсальным оборудованием и выполняют механические слесарные электротехнические сборочные кузнечные и сварочные работы.
Для обслуживания нескольких отрядов машин при значительном их количестве организуют районные мастерские временного типа. В состав таких районных мастерских входят передвижные мастерские.
Размеры таких мастерских и характер оборудования определяют объемом ремонтных работ.
Центральные ремонтные мастерские (ЦРМ) создают в управлении строительства или эксплуатации дороги. Производственная программа таких мастерских ориентировочно может быть от до 400 капитальных ремонтов машин в год приведенных к трактору С-80 (С-100).
Ремонтные заводы предназначены для выполнения капитального ремонта сложных дорожно-строительных машин тракторов агрегатов. На ремонтных заводах машины полностью - разбираются на агрегаты узлы и детали дефектуют ремонтируют и собирают вновь в соответствии с требованиями технических условий. Размеры и компоновка ремонтных заводов во многом зависят от объектов производства и принятого метода ремонта.
Производственная программа таких заводов ориентировочно может быть от 500 до 1500 и более капитальных ремонтов машин в год приведенных к трактору С-80 (С-100).
2. Последовательность проектирования ремонтных предприятий
Проектирование ремонтных предприятий производится на основе задания на проектирование составленного в соответствии с технико-экономическими обоснованиями целесообразности намечаемого строительства или реконструкции.
Задание на проектирование разрабатывается исходя из перспективного плана развития народного хозяйства. Оно должно предусматривать наиболее широкое применение типовых проектов использование проектов аналогичных предприятий. В задании на проектирование указываются основание для проектирования пункт строительства характеристика продукции и производственная мощность предприятия источники поступления ремонтного фонда источники снабжения производства водой топливом газом и электроэнергией сроки строитель-ства или реконструкции и очередность ввода перспектива его расширения ориен-
тировочные размеры капитальных вложений показатели себестоимости единицы продукции и производительности труда которые должны быть достигнуты при проектировании.
Проект охватывает весь комплекс вопросов связанных со строительством или реконструкцией предприятия и состоит из следующих частей: технологической архитектурно-строительной сантехнической энергетической сметно-финансовой экономической. Все части проекта взаимосвязаны между собой однако технологическая карта является одной из ведущих частей проекта.
Число стадий проектирования устанавливается при выдаче задания на проектирование. Как правило предприятия проектируются на две стадии: разрабатывается проектное задание а на основе после его утверждения разрабатываются рабочие чертежи.
При проектировании особо сложных предприятий требующих разработки нового технологического процесса допускается проектирование в три стадии - проектное задание со сметно-финансовыми технический проект со сводной сметой и рабочие чертежи. С разрешения инстанции утверждающей задание на проектирование при проектировании несложных объектов допускается разработка проектов в одну стадию.
Целью проектного задания является определение технической возможности и экономической целесообразности строительства предполагаемого объекта в данном районе. На этой стадии обосновываются правильность выбора площадки для строительства источники снабжения водой топливом электроэнергией газом определяют стоимость строительства и основные технико-экономические показатели. В технологической части проектного задания решают следующие вопросы:
- определяют исходные данные для проектирования (задание на проектирование типовые проекты данные действующих аналогичных наиболее передовых предприятий нормативные материалы;
- разрабатывают основные положения по организации производства (схема производственного процесса ремонта машин и агрегатов взаимосвязь цехов и отделений и принцип их организации);
- определяют состав ремонтного предприятия (составляют перечень цехов отделений участков и складов);
- определяют режим работы и фонды времени рабочих и оборудования для каждого цеха (отделения);
- определяют годовой объем работ;
- рассчитывают различные цехи и отделения (оборудование состав работаю- щих площадь расход электроэнергии пара воды);
- выполняют компоновку всех цехов и служб предприятия;
- разрабатывают схему генерального плана;
- определяют ориентировочную стоимость предприятия и основные технико-экономические показатели.
При двухстадийном. проектировании финансирование всех строительных и монтажных работ ведется в соответствии с проектным заданием.
Технический проект при проектировании в три стадии должен разрабатываться на основе утвержденного проектного задания. Технический проект состоит из тех же частей и разделов что и проектное задание и в нем уточняются все материалы и данные принятые в проектном задании. В техническом проекте дополнительно составляют планы расстановки оборудования со спецификацией и технические сметы на приобретение и монтаж типового оборудования изготовление и монтаж нестандартизированного оборудования производственного инвентаря.
Планировка на стадии проектного задания выполняется в масштабе 1:200 а в техническом проекте - 1:100.
Технический проект определяющий основные технические решения и стоимость предприятия также подлежит утверждению вышестоящими организациями. По техническому проекту при трехстадийном проектировании производится финансирование строительства.
Рабочие чертежи являются документами для производства работ по строительству предприятия и монтажу оборудования двухстадийном проектировании рабочие чертежи являются второй стадией разрабатываемой на основе утвержденного проектного задания. При проектировании по трем стадиям рабочие чертежи разрабатываются на основе утвержденного технического проекта рабочие чертежи выполняются в виде монтажных планов в масштабе 1:100 с нанесением на них окончательного расположения производственного транспортного энергетического складского и другого оборудования.
На технологических монтажных планах указывается привязка оборудования которая выполняется обычно к осям колонн или стен здания. Технологическое оборудование можно привязывать по осям отверстий для фундаментных болтов по характерным осям по основанию станины или фундаменту станка. Переносное и второстепенное оборудование а также производственный инвентарь обычно привязке не подлежат.
Кроме монтажных планов по характерным отделениям участкам и узлам составляются разрезы особенно в тех случаях когда требуется вертикальная привязка оборудования и коммуникаций также разрабатываются рабочие чертежи на изготовление нестандартизированного оборудования специальных приспособлений вспомогательного инструмента.
1. Анализ ремонтной программы
Для выполнения анализа ремонтной программы приводим назначение и основные технические характеристики машин и двигателей ремонтируемых на проектируемом заводе в соответствии с заданием. Основные технические характеристики машин и двигателей приведены в табл. 1.
Таблица 1 – Годовая расчетная программа завода
Наименование машин и двигателей
Экскаватор ЭО - 2621А
Кран автомобильный КС – 2561К
Котлованокопатель МКТС – 2М
Буровая машина БТС - 150
Путеукладчик тракторный ПБ - 3
Таблица 2 – Годовая дополнительная программа завода
Трудоемкость работ в % от ремонтной программы
Изготовление запасных частей и узлов
Изготовление новых машин и выполнение заказов строительных организаций
Ремонт собственного оборудования завода и инструментальные работы
Приведем краткие технические характеристики ремонтируемых машин.
Экскаватор одноковшовый ЭО – 2621А
Экскаватор ЭО – 2621А предназначен для механизации земляных и погрузочных работ небольших объёмов.
Основной рабочий орган экскаваторного оборудования – ковш 025м3 прямой и обратной лопаты. Кроме того экскаватор может быть оснащён погрузочным ковшом – 05м3 крановой подвеской вилами отвалом и т. д.
Марка базовой машины трактор МТЗ-82Л;
Марка двигателя .. Д – 65Н;
Тип двигателя .. дизельный;
Мощность 441 кВт (60л. с.);
Тип ходового устройства . пневмоколесный;
Тип управления основными механизмами .. гидравлический;
Вместимость ковша экскаватора .. 025м3 ;
- ширина (база) 2500 (2450)мм;
- высота (по кабине) .. 3900 (2460) мм;
Эксплуатационная масса 545 – 57 т.
Трактор Т–100 МЗ предназначен для работы в агрегате со строительно-дорожными и сельскохозяйственными орудиями широко используется как тяговый модуль.
Марка двигателя .. Д – 108;
Тип двигателя дизельный;
Мощность номинальная при 1070 обмин 794кВт (108л.с.);
Тип ходового устройства гусеничный;
Номинальное тяговое усилие . 60 кН;
- ширина (база) . 2500 (2450)мм;
- высота (по кабине) . 3900 (2460) мм;
Масса трактора конструктивная 111 т.
Бульдозер ДЗ – 18 (Д – 493А) предназначен для выполнения землеройно-планировочных работ с перемещением грунта на расстояния не превышающие 100м и глубиной срезки не более 150мм.
Основным рабочим органом является отвал размерами 3970 х 1000мм.
Базовый трактор .. Т – 100 МЗ;
Марка двигателя Д – 108;
Мощность номинальная при 1070 обмин 794 кВт (108л.с.);
Тип ходового устройства .. гусеничный;
Тип управления рабочим органом
(подъём-опускание) . гидравлический;
Габаритные размеры бульдозера:
Масса бульдозера (общая с трактором) .. 141т.
Кран автомобильный КС – 2561К предназначен для выполнения погрузочно-разгрузочных работ.
Кран оснащён основной стрелой длиной 8м и сменным рабочим оборудованием: выдвижной стрелой 8 и 104м удлинённой стрелой 12м и гуськом 15м.
Грузоподъёмность крана автомобильного КС – 2561К . до 63т;
Марка базового автомобиля ЗИЛ – 130;
Марка двигателя ЗИЛ – 130;
Тип двигателя карбюраторный;
Мощность силовой установки шасси автомобиля .. 110 кВт;
Тип ходового устройства пневмоколесный;
- механизмами подъёма груза и стрелы . электропневматическое;
- механизмом вращения поворотной платформы . рычажное;
Масса крана в транспортном состоянии .. 897т.
Машина МКТС – 2М это баровый котлованокапатель предназначенный для рытья котлованов под опоры контактной сети со стороны поля смонтирован на тракторе Т-100М3 с уширенными гусеницами.
Рабочим органом машины МКТС – 2М является многоковшовый вертикальный бар.
Продолжительность рытья одного котлована размером 650 х 900мм в плане и глубиной до 4800мм машиной МКТС – 2М составляет от 4 до 6 мин.
Марка базовой машины трактор Т – 100;
Мощность номинальная при 1070 обмин 794кВт;
Тип управления основными механизмами электрический;
Габаритные размеры в транспортном положении:
- ширина (база) 3970 (2450)мм;
Масса машины . . 20т.
Буровая машина БТС – 150
Буровой тракторный станок БТС – 150М предназначен для проведения подготовительных работ при гидротехническом гражданском и промышленном строительствах в карьерах для шурфов под взрывчатку.
Базовой машиной станка БТС– 150М является гидрофицированный трактор Т – 130 Т – 170 М1.01 или Т – 10.
Марка базовой машины трактор Т – 170;
Марка двигателя . Д – 160;
Мощность номинальная при 1070 обмин ..125 кВт (170л.с.);
Габаритные размеры навесного оборудования:
- высота в рабочем положении .. .. 5840мм;
- высота в транспортном положении .. 3800мм;
- навесного оборудования .. .. 985т;
- полностью заправленного станка 2388т.
Путеукладчик тракторный ПБ – 3М
Путеукладчик тракторный портальный ПБ – 3М предназначен для механизированной укладки или разборки рельсовых звеньев длиной 25м с рельсами всех
типов на деревянных и железобетонных шпалах при строительстве железнодорожных путей.
Путеукладчик состоит из трактора Т – 100М со специальной навесной рамой и портала опирающегося шарнирно две гусеничные тележки.
Путеукладчик полностью электрифицирован.
Источником электроэнергии путеукладчика является генератор который приводится в действие от коленчатого вала двигателя трактора.
Мощность генератора .. 375 кВт;
Мощность электродвигателя:
- тяговой лебёдки 1104 кВт;
- лебёдки подъёма и опускания звеньев . 110 кВт;
Грузоподъёмность .. 45т;
- длина .. 27480 – 29780мм;
- высота .. 3970 – 5870мм;
Масса путеукладчика с трактором 31т.
Двигатель Д – 108 дизельный четырехтактный с камерой сгорания в днище поршня бескомпрессорный.
Мощность номинальнаямаксимальная при частоте
вращения коленчатого вала 1600 мин -1 . ..794кВт;
Максимальный крутящий момент . 820 Н·м;
Двигатель ЗИЛ-130 производства АМО ЗИЛ предназначен для установки на автомобили ЗИЛ-130 (431410) ЗИЛ-433360.
Двигатель карбюраторный бензиновый с V-образным расположением цилиндров. Двигатель внутреннего сгорания 4-тактный жидкостного охлаждения.
На двигателе установлены: бесконтактная система зажигания с датчиком Холла и повышенной энергией разряда; трехкомпонентный каталитический нейтрализатор с химическими блоками на металлоносителе в системе выпуска отработавших газов.
Тип двигателя .. карбюраторный;
Мощность номинальная при частоте
вращения коленчатого вала 3200 мин-1 .. 110 кВт;
Максимальный крутящий момент при частоте
вращения коленчатого вала 1800 – 2000 мин -1 . 402 Нм (41 кгс·м);
Двигатель Д – 48 ЛС дизельный четырехтактный с камерой сгорания в дни-
ще поршня бескомпрессорный.
Марка двигателя . Д – 48 ЛС;
вращения коленчатого вала 1600 мин-1 .. 353 кВт;
Анализируя основные технические характеристики машин и двигателей ремонтируемых на проектируемом заводе в соответствии с заданием – можно отметить что эти машины имеют некоторые однотипные параметры.
По марке базовой машины
Базовой машиной для ремонтируемых на проектируемом заводе машин таких как:
- бульдозеры ДЗ – 18
- котлованокопатели МКТС - 2М
- тракторы Т – 100 МЗ
- путеукладчики тракторные ПБ – 3М (Т – 100М)
являются различные модификации трактора Т – 100.
Для экскаватора одноковшового ЭО – 2621А базовой машиной является – трактор ЮМЗ-6Л.
Для крана автомобильного КС – 2561К базовой машиной является – автомобиль ЗИЛ – 130.
Для буровой машины БТС – 150 базовой машиной является – трактор Т – 170.
На ремонтном заводе ремонту подлежат два типа двигателей – дизельные и карбюраторные.
Общее количество дизельных двигателей составляет – 2290 штук а карбюраторных – 400 штук).
Основной маркой двигателя для ремонтируемых на проектируемом заводе машин является – двигатель марки Д – 108 которые установлены на:
- тракторах Т – 100МЗ (их количество составляет – 300 шт.);
- бульдозерах ДЗ – 18 (их количество составляет – 200 шт.);
- котлованокопателях МКТС – 2М (их количество составляет – 120 шт.);
- путеукладчиках тракторных ПБ – 3М количество которых – 10 шт.;
- товарные двигатели Д – 108 (их количество составляет – 600 шт.).
Также большую группу дизельных двигателей подлежащих ремонту составляют товарные двигатели марки Д – 48ЛС количество которых – 800 шт.
По типу управления рабочими органами
Машины подлежащие ремонту можно разделить на две группы:
- с пневматическим управлением (кран КС – 2561 А);
- с гидравлическим управлением (все остальные).
По типу ходового устройства
Все машины можно разделить на две группы:
- на пневматическом ходу (экскаватор ЭО – 2621А и кран КС – 2561 А);
- на гусеничном ходу (все остальные).
2. Проектирование ремонтного предприятия
2.1. Выбор типа ремонтного завода метода и формы организации ремонта
Решающим фактором эффективной эксплуатации дорожных машин является хорошо организованный ремонт осуществляемый своевременно и высококачественно. Это обстоятельство вызывает необходимость создавать специальные ремонтные предприятия.
Каждое такое предприятие должно быть тщательно спроектировано. Проектирование осуществляют в две или в одну стадию. При двухстадийном проектировании вначале разрабатывают технический проект а затем рабочие чертежи; при одностадийном технический проект совмещается с рабочими чертежами (технорабочий проект). Количество стадий проектирования зависит от мощности будущего предприятия его сложности номенклатуры ремонтируемой техники места расположения предприятия ориентировочной стоимости его строительства предполагаемой оригинальности. Количество стадий указывается в задании на проектирование.
Задание на проектирование представляет собой документ разрабатываемый заказчиком с участием проектной организации в соответствии со схемой развития и размещения предприятий по ремонту дорожных машин. Перед утверждением задание предварительно согласовывается с заинтересованными организациями в части энерго и водоснабжения канализации транспортного обеспечения кооперирования с другими предприятиями.
Задание на проектирование - это основной документ на основе которого создается проект предприятия.
В задании указывают: наименование предприятия район пункт и площадку строительства; номенклатуру ремонтируемых машин и их количество по видам; режим работы предприятия; намечаемую специализацию; производственное и хозяйственное кооперирование. Основные источники обеспечения предприятия
при его эксплуатации и в период строительства должны быть обеспечены ремонтным фондом сырьем водой топливом и электроэнергией; условия по очистке и сбросу сточных вод; основные требования по автоматизации и механизации производственных процессов применению новых технологических процессов и оборудования; намечаемые сроки строительства и очередность ввода мощностей; размер капитальных вложений и основные технико-экономические показатели предприятия которые должны быть достигнуты при осуществлении проекта; данные для проектирования объектов жилищного и культурно-бытового строительства; стадийность проектирования; наименование проектной организации; наименование строительной организации - генерального подрядчика.
Производственный процесс капитального ремонта строительных дорожных и путевых машин состоит из следующих операций: прием машин в ремонт наружная мойка машин разборка машин на агрегаты узлы и детали мойка и очистка деталей дефектация деталей ремонт деталей комплектование деталей сборка узлов и агрегатов общая сборка машины испытание и окраска машины.
Номенклатура ремонтируемых машин приведена в таблице 1. Она довольно разнообразна поэтому завод считаем специализированным ремонтным предприятием. Форма организации ремонта – поточная. Метод ремонта – обезличенный.
Обезличенный метод ремонта характеризуется тем что узлы и детали устанавливаются на любую машину данной марки. Этот метод базируется на взаимо- заменяемости узлов и деталей используемых при изготовлении машин. Разно- видностью обезличенного метода является агрегатно – узловой метод. Он представляет собой систему замены неисправных составных частей (узлов агрегатов) машин на новые отремонтированные выполненные после выработки установленного ресурса до соответствующего вида ремонта.
Важнейшей характеристикой такого ремонта является сохранение неснижаемого расчетного числа узлов оборотного фонда так как в противном случае нарушается ритмичность производства.
2.2. Расчет годовой производственной программы
Годовая производственная программа проектируемого завода определяется по трудоемкости и стоимости ремонта.
Трудоемкости годовой программы ремонта для каждой марки машины определяется по формуле.
где - расчетная трудоемкость чел.-ч;
- трудоемкость челч;
- коэффициент учитывающий метод ремонта;
- коэффициент учитывающий форму организации труда;
- коэффициент учитывающий серийность (однотипность) ремонтируемых машин.
- для обезличенного метода ремонта;
- при поточной форме ремонта;
- при серийности до 150 машин;
- при серийности 151- 250 машин;
- при серийности 251-500 машин;
- при серийности 501-1000 машин.
Значения принимая по прил. 2.
Суммарная трудоемкость годовой программы определяется по формуле.
где - суммарная трудоемкость годовой программы чел.-ч;
суммарная трудоемкость дополнительной годовой программы чел.-ч.
Для годовой программы на 200 машин
При вычислении стоимости капитального ремонта машин цена ремонта берется по приложению 1 а вычисление дополнительной программы исходим из того что за один норма – час производится объем работ на руб. Здесь - коэффициент инфляции.
Полученные данные заносим в табл. 3.
Таблица 3 – Годовая производственная программа
Марка машин и виды работ
Трудоемкость ремонта чел.-ч
Стоимость ремонта руб
Окончание таблицы 3
Дополнительные работы
Изготовление новых машин и выполнение заказом строительных организаций
Таблица 5 - Распределение трудоемкости дополнительных работ по видам чел.-ч
Изготовление новой продукции
Составим сводную таблицу распределения трудоемкости все годовой программы завода в табл. 6.
Эти значения трудоемкости используем для расчета всех параметров по цехам и отделениям.
Таблица 6 – Трудоемкость годового объема работ
Дополнительная программа
мойка агрегатов и двигателей
кузнечные и термические
слесарно - ремонтные
столярно - обивочные
2.3. Разработка схемы технологического процесса
Общая схема производственного процесса ремонта ведущей машины экскаватора ЭО – 2621А. показана на рис. 1.
Рис. 1 Технологическая схема капитального ремонта ведущей машины ЭО – 2621А
Стрелками показана технологическая последовательность выполнения отдельных операций при ремонте агрегатно – узловым методом при котором сборка машины осуществляется с использованием заранее отремонтируемых или новых узлов и агрегатов поступающих со склада оборотного фонда. То есть после ремонта базовой детали без задержек осуществляется общая сборка машины.
Детали требующие ремонта поступают на склад а затем на участки ремонтных операций сварочно – наплавочный кузнечно – термический гальванический слесарно – механический и т.д.
Отремонтируемые детали подаются на участок комплектования где выполняются подготовительные операции по контролю и подбору деталей и при необходимости пригоночные работы с целью обеспечения высокого качества и ускорения сборочных операций. Собранные агрегаты и машины проходят испытания в соответствии с техническими условиями и окрашиваются.
2.4. Принятие структуры ремонтного завода
В зависимости от мощности завода характера и степени специализации производственного процесса отдельные составляющие организационной структуры предприятия могут изменяться. Основное производство может быть построено по цеховой или безцеховой структуре. При безцеховой структуре отдельные производственные участки возглавляются мастерами и подчиняются непосредственно руководству предприятия. Повышается роль мастера как основного руководителя производства.
В нашем случае объем ремонтируемых машин большой и велика численность работающих на предприятии поэтому принимаем цеховую структуру предприятия. Управление производством в цехе осуществляется начальником цеха мастерами есть плановый и технический отделы. При цеховой структуре более высокие затраты на аппарат управления чем при безцеховой структуре но при больших объемах производства целесообразней цеховая структура производства за счет лучшей организации производства оперативности ответственности служб
и отделов за свои участки работ работы. Производственная структура ремонтного завода приведена на рис. 2.
Рис. 2 Производственная структура предприятия
2.5. Расчет трудоемкости по цехам и отделениям
Для расчета всех параметров по цехам и отделениям необходимо определить трудоемкость работ в каждом из них.
С этой целью в начале определим трудоемкость работ по ремонту двигателей выполняемых в моторном цехе (см. табл. 7). Распределение трудоемкости показано (см. прил. 3).
Распределение трудоемкости ремонта двигателей принимаем по приложе- нию 3 для карбюраторных и дизельных.
Годовая трудоемкость ремонта двигателей
Д – 108 1701490=253300 чел.-ч
Д – 48ЛС 120800=96000 чел.-ч
ЗИЛ – 108 120400=48000 чел.-ч
При ремонте двигателей в моторном цехе часть работ будет выполнятся в других цехах завода например кузнечные термические (1% от трудоемкости) сварочные 12% гальванические 08% наружная мойка 12% малярные 05%.
Уменьшим годовую трудоемкость работ моторного цеха на величину трудоемкости этих работ. Тогда трудоемкость ремонта двигателей составит.
Д – 108 253300(100-47)100=241395 чел.-ч
Д – 48ЛС 96000(100-47)100=91488 чел.-ч
ЗИЛ – 108 48000(100-47)100=45744 чел.-ч
Таблица 7 – Распределение работ выполненных в разборочном цехе
Трудоемкость ремонта двигателей
Суммарная трудоемкость чел.-ч
мойка агрегатов и деталей
Отделение ремонта топливной аппаратуры
Зная состав завода и работы выполняемые в каждом отделении из общей трудоемкости работ вычитаем трудоемкость работ выполняемых в моторном цехе (см. табл. 7).
Таблица 8 – Трудоемкость работ по цехам и отделениям
Мойки агрегатов и деталей
Слесарно - ремонтное
Ремонта топливной аппаратуры
Ремонтно – механический цех
Цех восстановления деталей
Кузнечно - термическое
Сварочно - наплавочное
Электротехническое и аккумуляторное (учтена трудоемкость в неучтенных работах моторного цеха)
Столярно – обивочное
2.6. Расчет режима работы предприятия
Режим работы предприятия определяется количеством смен работы в сутки и продолжительностью смены зависит от годового объема работ типа предприятия и равномерности загрузки его в течение всего года. Число смен зависит от объема работ выполняемых цехами.
Действительный фонд времени определяется по формуле.
где - число дней в году календарных выходных праздничных и отпускных;
ч - продолжительность рабочей смены;
- количество часов на которое сокращен рабочий день перед праздниками ч;
- коэффициент учитывающий потери рабочего времени по уважительным причинам.
В расчетах принимаем 41- часовую рабочую неделю с двумя выходными днями.
Определим - для слесарей и станочников.
Определим - для электромонтеров термистов и мойщиков.
Определим - для кузнецов электросварщиков медников и рабочих испытательных станций.
Определим - для маляров гальванизаторов и аккумуляторщиков.
Действительный годовой фонд времени работы оборудования и рабочих мест.
где ч - продолжительность работы оборудования в течение смены;
- число смен в сутки;
- коэффициент учитывающий простой оборудования в ремонте.
Действительный годовой фонд времени работы оборудования при продолжительности рабочей смены 82ч в две смены.
При работе в одну смену
При работе в две смены при продолжительности смены 72ч
Действительный годовой фонд времени рабочего места при продолжительной рабочей смены 82ч и работе в одну смену.
При продолжительности смены 72ч при работе в две смены
При продолжительности смены 82ч при работе в две смены.
2.7. Расчет численности рабочего персонала
В состав работников предприятия входят следующие категории: производственные и вспомогательные рабочие инженерно – технические работники счетно - конторский персонал и младший обслуживающий персонал.
Общая численность производственных рабочих.
где - число производственных рабочих в цехах по профессиям чел
где - трудоемкость данного вида работ чел.-ч;
- действительный фонд времени рабочих соответствующей профессии ч.
Общее число вспомогательных рабочих (ремонтные и транспортные рабочие наладчики раздатчики инструмента контролеры – браковщики разнорабочие)
где - процент вспомогательных рабочих по отношению к производственным. Для ремонтных предприятий .
Численность инженерно – технических работников счетно – конторского персонала и младшего обслуживающего персонала определяется в процентном отношении от общего числа производственных и вспомогательных рабочих ориентировочно принимаем соответственно равными 12% 3% и 2%. Расчет численности выполняем производственных рабочих для каждого цеха и отделения а расчет численности остальных категорий работающих по цехам.
Результат расчета сводим в табл. 9.
Таблица 9 - Состав работников ремонтного предприятия
Действительный фонд рабочего времени ч
Продолжение таблицы 9
Столярно - обивочное
2.8. Расчет количества оборудования и рабочих мест
Расчет производим исходя из трудоемкости работ выполняемых в данном цехе по формуле.
где - действительный фонд времени работы оборудования (рабочих мест) ч;
- трудоемкость работ выполняемых в данном цехе;
- коэффициент загрузки.
Расчет рабочих мест выполняется для всех цехов кроме перечисленных выполняемых в соответствующих цехах. Во всех расчетах учитываем всю трудоемкость работ выполняемых в соответствующих цехах.
Результат расчета сводим в табл. 10.
Таблица 10 - Количество оборудования
Действительный фонд времени работы оборудования ч
Количество оборудования
Действительный фонд времени рабочего места ч
Количест во рабочих мест
Продолжение таблицы 10
Ремонт топливной аппаратуры
Окончание таблицы 10
2.9. Расчет площадей
Различают производственные вспомогательные конторские и бытовые площади. К производственным относятся - площади занятые оборудованием и рабочими местами. К вспомогательным - площади занятые складами и кладовыми а также проездами и коридорами. К конторским - площади цеховых и заводских контор а также бытовые площади гардеробов душевых умывальников туалетов.
Определяем расчет производственной площади следующим способом:
В зависимости от производственных рабочих.
где - площадь цеха м²;
- количество производственных рабочих в первую смену;
- удельная площадь на одного производственного рабочего м².
В зависимости от площади занимаемой оборудованием.
где - переходный коэффициент;
- площадь занимаемая оборудованием м².
В зависимости от площадей рабочей зоны.
где - количество оборудования шт;
- площадь занимаемая оборудованием м² с учетом рабочей зоны - для станков равная 15м².
Результат расчета сводим в табл. 11.
Таблица 11 – Производственные площади
Мойка агрегатов и деталей
Ремонтно – механческий цех
Цех восстановление деталей
Окончание таблицы 11
Площади складов рассчитываются по формуле
где - удельная площадь м²;
- трудоемкость ремонтной программы чел·ч.
Размеры открытых площадок для хранения ремфонда и отремонтируемых машин определяют по формуле.
где - количество марок машин;
- площадь одной машины ЗИЛ 130 -108м²; Д- 48ЛС - 12-18м²);
Площадь для хранения ремфонда 159м²;
Площадь для хранения отремонтируемых машин 159м²;
Аналогично рассчитываем и другие площади складов и расчет сводим в табл. 12.
Таблица 12 – Вспомогательные площади
Трудоемкость ремонтной программы
Окончание таблицы 12
Хранение двигателей и агрегатов
Отремонтируемых машин
Площади бытовых и конторских помещений рассчитывают для предприятия по следующим нормативам: площадь раздевалок – 08м² на одного рабочего площадь умывальников - 1м² на десять человек площадь душевых – 45м² на десять человек площадь туалетов - 3м² на двадцать человек площадь буфетов и столовой – 025м² на одного человека.
Площадь конторских помещений по нормам на одного работающего: для СКП – 325м² для ИТР - 5м² гаража - 075м² на 1000чел.-ч для компрессорной 20м² на один компрессор.
Принимаем что в первую смену работает 60% работающих.
Таблица 13 – Сводная ведомость площадей
На территории завода
Инструментально- раздаточная кладовая
Конторские помещения
2.10. Компоновка цехов
Компоновку цехов выполняем с учетом следующих соображений. Наиболее целесообразно в экономическом и техническом отношении объединить производственные вспомогательные и складские помещения в одном здании так как затраты на постройку и эксплуатацию в этом случае ниже чем при их размещении в нескольких зданиях. Исходными данными являются принятый метод ремонта и принятая схема технологического процесса. Взаимное расположение цехов и отделений должно обеспечивать соблюдение последовательности предусмотренной технологическим процессом. Пути грузопотоков деталей узлов материалов должны быть наиболее короткими без обратных движений. Форма производственного процесса должна быть простой.
Общую площадь главного корпуса определяют как сумму площадей производственных вспомогательных и бытовых помещений. Ее увеличивают на 10-15% для учета проходов и проездов. По площади главного корпуса определяют его габариты. При этом необходимо учитывать строительные нормы и правило по распределению колонны и размеров пролетов. Длина корпуса должна быть кратна шагу колонн. Шаг колонн – 12м высота помещений – 96м. Главный корпус трехпролетный ширина пролета – 24м проезды для автотранспорта – 4м конторские помещения располагаются на третьем этаже над бытовыми.
Общую площадь главного корпуса увеличим на 12%.
В соответствии с СНиП принимаю м.
Схему грузопотоков наносим на план главного корпуса. Она показывает движение объектов ремонта материалов запасных частей в соответствии с последовательность производственного процесса. Схема грузопотоков позволяет оценить правильность компоновки цехов с точки зрения выполнения одного из главных требований – кратчайшего движения грузов. При этом выявляются встречные и пересекающие грузопотоки которые по возможности должны быть устранены путем перекомпоновки отделений. Полосы грузовых потоков показывают пути движения грузов а их ширина изображает в масштабе массу грузов (напряженность грузопотока).
Ширину полос по отдельности берут в процентном отношении от ширины полной массы машин поступивших в ремонт. Полосы соединяют между собой согласно схемы технологического процесса ремонта ведущей машины. Полосы грузопотоков выполняем в масштабе.
В главном производственном корпусе в соответствии с технологическими требованиями выбраны следующие подъемно-транспортные средства:
Центральный пролет: два мостовых крана грузоподъемностью 5т;
Левый пролет: два мостовых крана грузоподъемностью 20т и 5т;
Центральный пролет: два мостовых крана грузоподъемностью 3т.
Исходя из размеров изделия высоты оборудования размеров и конструкции грузоподъёмных средств санитарных требований рассчитываем высоту корпуса.
Высоту цехов Н определяем по высоте от уровня пола до верха головки рельса подкранового пути.
где a - высота наиболее высокой части оборудования или наиболее высокого
узла (детали) над которыми возможно транспортирование деталей (узлов) равная 4м;
б - промежуток между транспортируемой деталью (узлом) поднятой краном в крайнее верхнее положение и станком (или наибольшим узлом) равный 05м;
в - наибольшая высота транспортируемого узла (детали) равная 12м;
г - расстояние между верхом транспортируемого узла (детали) и крюком крана равное 15м.
Высоту помещений (от отметки чистого пола до низа несущих конструкций покрытия) назначаем:
в центральном пролёте - Нцент.= 84м;
в обоих крайних пролётах - Hкрайн. = 72м.
2.11. Разработка схемы генерального плана
Схема генерального плана выполнена на листе формата А1 там приведена экспликация зданий сооружения и оборудования. При определении площади земельного участка следует руководствоваться годовым объемом работ на 100чел.-ч трудоемкости отводится 25м.
На этой площади указывается взаимное расположение всех зданий сооружений площадок рельсовых и безрельсовых дорог зеленых насаждений и ограждений.
Здания цехов складов и площадки расположены в соответствии с последовательным ходом производственного процесса. При разработки генерального плана стремимся к тому чтобы путь движения машин ремфонда отремонтированных машин и материалов был кратчайшим.
Взаимное расположение зданий и разрывы между ними должны удовлетворять нормам пожарной безопасности санитарно-техническим правилам светотехническим требованиям. Территория не использованная под застройку должна быть озеленена.
На чертеже генерального плана приведены показатели генерального плана условные обозначения его основных элементов а также размеры зданий и сооружений расстояния между ними ширина проездов.
ТЕХНОЛОГИЧЕСКИЙ РАЗДЕЛ
Механический цех производит работы по восстановлению изношенных деталей и изготовлению новых. В состав цеха входят участки: заготовительный станочный слесарный кроме того к этому цеху относятся – склад заготовок промежуточную и инструментально-раздаточную кладовые.
В моторном цехе выполняют весь комплекс работ по ремонту двигателей внутреннего сгорания. Моторный цех имеет в своем составе отделения разбороч- но-моечный механический сборочный ремонта топливной аппаратуры контрольно-испытательный. Кроме того из-за большой производственной про- граммы организуем участок по ремонту электрооборудования.
Ремонтно-механический цех
Ремонтно-механический цех - предназначен для ремонта собственного оборудования ремонтного предприятия. В состав цеха в зависимости от объема работ могут входить станочный и слесарный участки а также цеховые склады.
К площадкам для хранения ремонтного фонда (ремфонда) и отремонтированных машин а также к энергетическим устройствам (компрессорные котельные трансформаторные подстанции и т. п.) проложены подъездные пути дороги
Машины поступающие на завод подают на площадку ремонтного фонда. Для их разгрузки площадка оборудована козловым краном. Здесь снимают навесное оборудование которое направляют на ремонтный участок. Тем же краном машины устанавливают на специальные тележки широкой колеи и при помощи цепного конвейера перевозят в главный корпус в отделение наружной мойки в котором предусмотрены лебедки или тяговые цепями.
Отделение наружной мойки.
Перед наружной мойкой из картеров двигателя и трансмиссии спускают отработавшее масло. Наружную мойку машин и агрегатов ведут из шланга струей воды при давлении 06 07мПа или в специальных моечных камерах. Для очистки от грязи применяют ручные и механизированные скребки и щетки. Камерную машину для наружной мойки оборудуют электролебедкой и тяговой цепью насосом высокого давления и системой труб с гидрантами.
Отделение мойки узлов и деталей.
Обезжиривание крупных деталей удаление с их поверхности нагара накипи асфальтно-смолистых отложений (рама корпусные детали блоки) производится выварочных ваннах. Выварка деталей производится в горячем 10% растворе каустической соды с температурой 80-90ºС с последующей промывкой в горячей воде для удаления остатков щелочи. Топливные баки обезжириваются каустическим раствором в течение 20 минут при температуре 80-90ºС затем промываются горячей водой и подвергаются травлению ортофосфорной кислотой для удаления ржавчины с внутренних поверхностей бака а затем кальцинированной содой с последующим промывкой холодной водой.
Моющие средства Лабомид – 101 Лабомид – 102 МЛ-51 применяют в любых машинах струйного типа в концентрации 30..35гл. Средства Лабомид – 203 и МЛ-52 предназначены для очистки деталей от асфальтно-смолистых отложений. Моющие средства МС-5 МС-6 МС-8 используют при выварки деталей в ваннах.
Растворяющие – эмульгирующее средство (РЭС)АМ-15 используется для очистки деталей от смолистых загрязнений и восстановления пропускной способности фильтров грубой очистки масла. Точные детали топливной аппаратуры гидросистемы шариковые и роликовые подшипники промывают в керосине в ваннах или в ультразвуковых моечных установках.
Для удаления нагара с поверхностей детали можно применять:
- расплав солей при температуре 400±20ºС;
- механическим способом например шариковой крошкой;
- термическим способом т.е. выжиганием нагара пламенем газовой горелки.
Очистку деталей от коррозии производят вытяжкой суперфосфата нагретой до 80-90ºС или 25% соляной кислотой или 15% серной кислотой.
Отделение дефектации.
Детали очищенные от всех загрязнений контролируют для оценки технического состояния и возможности их дальнейшей эксплуатации. Дефектацию деталей ведут внешним осмотром. Проверкой на ощупь определяют износ и смятиерезьбы легкость проворачивания элементов подшипников качения легкость перемещения шестерен. Далее простукиванием выявляют плотность посадок штифтов в корпусах и крышках.
Затем измерением универсальными измерительными инструментами определяют отклонения сопряжений от заданного зазора или натяга от заданного размера от плоскости формы профиля. При этом используют штангенциркули нутромеры штангензубомеры индикаторы часового типа поверочные плиты щупы шаблоны скобы.
Гидравлическим или пневматическими испытаниями на стендах проверяют герметичность радиаторов трещины в блоке и головки блока выхлопных и всасывающих трубах. Биение и погнутость шеек валов проверяют в центрах.
Внутренные трещины раковины выявляют различными методами дефектоскопами (магнитной люминесцентной ультразвуковой).
При дефектации детали сортируют на три группы:
- требующие ремонта или восстановления;
- негодные (брак) подлежащие утилизации.
Отделение комплектации
Комплектование деталей заключается в подборе и пригонке полного комплекта деталей входящих в состав сборочной единицы или агрегата по спецификациям или комплектовочным картам. Комплектование деталей производится из годных и восстановленных деталей и из запасных частей. При комплектовании детали подбирают так чтобы соблюсти требуемые посадки и технические условия. Подобранные детали укладывают в ящики контейнеры корзины и доставляют в сборочный цех.
Сначала собирают отдельные узлы и агрегаты машин: двигатели ходовая часть электрооборудование. Собранное навесное оборудование радиаторы топливные баки кабины через обменный фонд поступают в комплектовочное отде-ление.
Скомплектованные агрегаты и узлы машин поступают либо на универсальные рабочие места при многономенклатурной производственной программе либо на конвейер при поточной форме организации ремонта в значительном объеме производства. Сборка на универсальных рабочих местах характеризуется неподвижностью собираемой машины к которой подаются все ее составные части. Поточная сборка осуществляется при принудительном передвижении собираемой машины на конвейере. Движение конвейера может быть периодическим или непрерывным в зависимости от размера производственной программы такта выпуска.
Процесс сборки начинается с установки рамы машины на которую в строгой технологической последовательности устанавливают все основные узлы и агрегаты: Двигатель коробку передач карданную передачу мосты рулевое управление радиатор кабину ходовую часть и остальные узлы и детали. При сборке проводят
все необходимые регулировочные работы. Также необходимо обращать внимание на строгое на строгое центрирование агрегатов относительно друг друга. Несоблюдение этого условия приводит к износу отдельных агрегатов и преждевременному выходу из строя в процессе эксплуатации.
Рабочие места располагают в порядке последовательности операции технологического процесса сборки. При выполнении сборочных работ должны соблюдаться правила техники безопасности. В качестве подъемно – транспортных средств используются подъемники кран – балки консольно – поворотные краны оборудованные электрическими талями мостовые краны.
Транспортировка узлов и деталей производится с помощью электрокар электропогрузчиков подвесных конвейеров.
При сборке агрегатов и узлов машин приходиться выполнять сборку резьбовых рельсовых прессовых соединений сборку зубчатых передач сборку соединений с подшипниками качения.
При сборке резьбовых соединений нужно обеспечить:
- соосность осей болтов шпилек винтов с резьбовыми отверстиями;
- отсутствие перекосов головки болта или торца гайки относительно поверхности сопрягаемой;
- соблюдение очередности и постоянство усилий затяжки крепежных деталей в групповых резьбовых соединениях.
Качество сборки прессовых соединений определяется многими факторами: значением натяга материалом сопрягаемых деталей усилие запрессовки наличия смазки.
Повышение прочности неподвижных соединений с натягом обеспечивается применением сборки с нагревом охватывающей или с охлаждением охватываемойдетали. При этом образуется зазор и требуется приложение осевой силы. Наг-
рев деталей осуществляется в масленых ваннах электропечах индивидуальных установках и др. а для охлаждения деталей применяют жидкий азот сухой лед в смеси с ацетоном бензином или спиртом.
Перед сборкой зубчатой пары нужно определить боковой зазор между зубьями для плавности работы пары. После установки зубчатые колеса проверяют по зазору заземлению и контакта.
При сборке с подшипниками качения внутреннее кольцо подшипника сопряженное с цапорой вала должно иметь посадку с натягом а наружное с небольшим зазором чтобы кольцо имело возможность во время работы незначительно проворачиваться. Необходимо соблюсти соосность посадочных поверхностей в корпусных деталях и шеек валов т.к. не соблюдение этого условия приводит к перекосам подшипников и заклиниванию шариков. Нагрев подшипников в масленой ванне до температуры 100ºС заметно уменьшает осевое усилие для запрессовки.
Отделение заправки и испытания машины.
После сборки отремонтированная машина поступает на испытание при котором проверяется комплектность машины качество сборочных крепежных и регулировочных работ. Машина заправляется топливом маслами специальными жидкостями и затем проводятся испытания машины на соответствие ее технических показателей требуемым техническим условиям на различных режимах работы. Все выявленные при испытании неисправности устраняются.
При отсутствии дефектов или после их устранения машина поступает на окончательную окраску.
Поверхности подлежащие окраске подвергают обезжириванию Уайт - спиритом или его заменителями (скипидар ацетон авиационный керосин и т.д.). После обезжиривания эти поверхности протирают насухо чистой и сухой ветошью. Перед нанесением лакокрасочного покрытия поверхности предварительно грун-
туют. Обязательной грунтовке подвергают лицевые стороны кабины детали капота топливного бака щитков тележек и других деталей. Из грунтовок применяют глифталевый грунт ГФ-020. Для разбавления грунта до рабочей вязкости используют сольвент. После сушки грунта производят местное шпатлевания и шлифовку. Поверхности требующие повышенной чистоты отделки перед окрашиванием шпатлюют стальными или резиновыми шпателями. После просушки. Зашпатлеванную поверхность шлифуют водостойкой наждачной шкуркой.
Для окраски кабин капота и других деталей из тонколистового материала используют нитроэмали синтетические эмали МЛ-2 и нитроглифталевые эмали НКО. Количество наносимых слоев краски определяется технологическим процессом обычно это два слоя для нитроэмали и синтетических эмалей а при перхлорвиниловой эмали достаточно один слой. Для нанесения краски используют краскораспылительные установки. Лакокрасочные покрытия сушат в сушильных камерах. На сборку машин агрегаты и узлы подаются окрашенными.
Двигатель и коробку передач окрашивают в два слоя алюминиевой краской корпуса трансмиссии ходовые тележки окрашивают нитроэмалью или двойным слоем асфальтового лака.
Топливные баки окрашивают двумя слоями бензостойких эмалей. Все масленки крышки пробки заливных горловин масломерные линейки покрывают красной эмалью А-67Ф или эмалью НКО – 21.
После окраски машина предъявляется отделу технического контроля. Окрашенные машины передаются на площадку отремонтируемых машин.
Отделение приемки и выдачи машин.
Качество отремонтируемых машин должно соответствовать техническим условиям. Приемка отремонтируемых машин производится в соответствии с ГОСТ 19504-74 составляется приемо – сдаточный акт в двух экземплярах. Один экземп-ляр этого акта паспорт машины ремонтный журнал акт об испытания двигателя
паспорт на вновь поставленные канаты и цепи ремонтное предприятие передает заказчику а другой остается на предприятии. На отремонтированную машину составляется гарантийный паспорт в котором указывается гарантийный срок работы машины.
Ремонтное предприятие несет ответственность за качество ремонта в течение гарантированного срока. Все дефекты возникшие по вине ремонтного предприятия в течение гарантийного срока устраняется бесплатно. Рекламации на недоброкачественный ремонт в течение гарантийного срока можно предъявить ремонтному предприятию если эксплуатация отремонтированной машины производилась в соответствии с предписаниями заводской инструкции.
ПРОЕКТИРОВАНИЕ РАЗБОРОЧНОГО ЦЕХА
Разборочный цех предназначен для выполнения следующих видов работ: наружная мойка поступающих в ремонт их разборка на агрегаты и узлы мойка агрегатов и узлов дефектация деталей. В состав разборочного цеха входят следующие участки: наружной мойки машин разборки мойки узлов и деталей дефектации. Наружная мойка осуществляется в установке наружной мойки. Разборка машин на ремонтных заводах обычно ведется на тупиковых постах мойку агрегатов и деталей производят в моечных машинах и выварочных ваннах. Участок дефектации с минимальным количеством оборудования необходим для выполнения контрольных операций по выявлению пригодности деталей к дальнейшей эксплуатации и выбраковке негодных деталей.
Режим работы цеха - 82ч. в две смены; действительный фонд рабочего времени мойщиков – 3952ч рабочих занятых разборкой машин и дефектацией деталей – 40752ч.
Трудоемкость годовой программы разборочного цеха составляет - 360263 чел.-ч.
Отделение наружной мойки – 51302 чел.-ч.
Отделение разборочное – 226921 чел.-ч.
Отделение мойки узлов и деталей – 43322 чел.-ч.
Отделение дефектации – 38714 чел.-ч.
Численность производственных рабочих по профессиям – 19чел из них на участке наружной мойки – 3чел участок разборки – 12чел участок мойки узлов и деталей – 2чел участок дефектации – 2чел ИТР – 3чел общее число вспомогательных рабочих – 3чел СКП – 1чел МОП – 1чел.
Всего работающих в разборочном цехе – 27чел.
Отделение наружной мойки
Число установок наружной мойки рассчитывается по формуле.
ч – время наружной мойки одной машины;
ч – действительный годовой фонд времени работы моечной камеры;
- коэффициент использования моечной машины.
Площадь отделения наружной мойки определим по площади пола занятого оборудованием с учетом коэффициента плотности расстановки оборудования.
где - коэффициент плотности оборудования;
- площадь занимаемая оборудованием.
Разборочное отделение
Разборка ведется на тупиковых постах. Число постов разборки определим по
где чел.-ч – общая трудоемкость разборочных работ;
ч – действительный годовой фонд времени работы моеч-
чел – количество слесарей занятых одновременно на разборке одной машины.
Перечень оборудования разборочного отделения приведены в табл. 14.
Площадь разборочного отделения определяем по площади пола занятого оборудованием с учетом коэффициента плотности оборудования.
Отделение мойки агрегатов и деталей
Число моечных машин камерного типа определим по формуле.
где кг – масса деталей подлежащих мойке в машине (30% от массы машины);
ч – время одной загрузки;
кг – одновременная загрузка моечной машины;
- коэффициент использования камеры по габаритам;
- коэффициент использования моечной машины по времени.
Перечень выварочно – моечного оборудования приведен в табл. 14.
Необходимое количество выварочных ванн.
где кг – масса деталей подлежащих мойке в выварке в ваннах;
ч – время мойки одной загрузки;
кг – одновременная загрузка моечной ванны;
- коэффициент использования моечной ванны по времени.
Площадь отделения мойки агрегатов и деталей определяем по площади пола занятого оборудованием с учетом коэффициента плотности оборудования.
Отделение дефектации
Отделение дефектации предназначено для контроля и сортировки деталей. На участке устанавливается пригодность деталей к дальнейшей эксплуатации.
Число постов дефектации определим по формуле.
где чел.-ч – общая трудоемкость работ;
ч – действительный годовой фонд времени работы;
чел – коэффициент загрузки рабочего места.
Площадь отделения дефектации определяем по площади пола занятого оборудованием с учетом коэффициента плотности оборудования.
Оборудования для всех участков разборочного цеха выбираем технологическим комплектом необходимым и достаточным для выполнения всех ремонтных работ. При выборе оборудования используем опыт передовых ремонтных предприятий а также справочную и техническую литературу. Перечень оборудования всех участков разборочного цеха приведен в табл. 14.
Таблица 14 – Перечень основного технологического оборудования и инвентаря разборочного цеха
Обозначение (тип модель)
Наименование оборудования
Габарит- ные размеры мм
Машина для наружной мойки тракторов
Моечная установка для наружной мойки машин
Бак для сбора отработавшего масла
Продолжение таблицы 14
Ларь для обтирочных материалов
Стенд для разборки крупногабаритных узлов
Стенд для разборки реверса главной лебедки экскаватора
Стенд для разборки поворотной рамы экскаватора
Стенд для разборки ходовой рамы экскаватора
Стенд для разборки опорно-поворного круга экскаватора
Стенд для разборки главной лебедки экскаватора
Стенд для разборки передних и задних мостов экскаватора
Пресс гидравлический
Стенд для разборки механизма натяжения гусениц
Стенд с гайковертом для разборки ходовых тележек
Стенд для разборки опорных катков и натяжных колес
Стенд для разборки коробок передач
Стол для разборки бортовых фрикционов
Стенд для разборки лебедок бульдозера
Тележка для разборки шасси трактора
Кран мостовой Q = 5т
Кран консольный поворотный
Окончание таблицы 14
Ванна для выварки и ополаскивания рам
Ванна для выварки кабин и оперения
Стенд для промывки топливных баков
Машина для наружной мойки агрегатов
Установка для мойки деталей
Ларь для обтирочных материалов
Стол для контроля и сортировки деталей
Магнитный дефектоскоп
Центра для проверки валов
1. Описание устройства и работы стенда
Стенд предназначен для ремонта двигателей ЗИЛ-130 в условиях ремонтного предприятия и автохозяйств.
Техническая характеристика.
Тип - стационарный с поворотом двигателя вокруг оси перпендикулярной оси коленчатого зала.
Способ крепления двигателя - на поворотной раме в задней части - за опорные лапы картера сцепляется болтами в передней - за корпус блока цилиндров специальным упором и винтовым зажимом.
Способ поворота двигателя - вручную через червячный редуктор с передаточным числом i = 34.
Максимальное усилие на приводной рукоятке кг - не более 10
Стенд состоит из трех основных узлов: станины 1 рамы 2 и редуктора привода вращения рамы 4.
Станина 1 представляет собой гнутую из труб пространственную конструкцию. В нижней части стенд имеет две опорных площадки с отверстиями под фундаментные болты. Боковые стойки станины оканчиваются опорами под оси крепления поворотной рамы 2. Рама - сварной конструкции. В передней части рамы
имеется упор и винтовой зажим крепления блока цилиндров двигателя. В задней части расположены лапы с отверстиями под опоры картера сцепления двигателя.
Конструкция винтового зажима представлена на разрезе "Б-Б".Редуктор стандартный самозатормаживающийся червячного типа. Червяк выполнен из стали червячное колесо - из антифрикционного чугуна. Вал червяка вращается в 2-х роликовых конических подшипниках а червячное колесо – из бронзы. Затяжка роликовых конических подшипников регулируется с помощью стальных прокладок между
крышками и корпусом редуктора. Регулировка положения червячного колеса производится с помощью прокладок между торцами червячного колеса и подшипников скольжения. В нижней части корпуса редуктора имеется пробка для слива масла. Маслозаливная пробка расположена на боковой части корпуса редуктора.
Связь червячного колеса редуктора с поворотной рамой осуществляется при помощи шарнирного вала 6.
Стенд устанавливается в удобном для работы месте и прикрепляется фундаментными болтами к полу. Перед работой на стенде необходимо отвернуть пробку на боковой поверхности корпуса редуктора и проверить наличие в редукторе масла. Смазать солидолом через пресс-масленки опоры вращения рамы. Вращением рукоятки редуктора до проворачивания рамы на полный оборот проверить исправность стенда.
Вращением рукоятки редуктора установить раму в горизонтальном положении. Вывернуть болты 12 крепления из отверстий в лапах рамы и ввернуть снизу направляющие штифты. Установить двигатель передней частью блока на непод-вижный упор отверстиями в опорах картера сцепления - на отверстия в лапах.
Поджать винтовым зажином блок цилиндров при этом подвижный упор винтового зажима должен войти в полукруглой формы прилив в корпусе блока цилиндров. Поставить болты 12 и закрепить снизу гайками. После этого враще-нием маховика винтового зажима окончательно зажать переднюю часть блока ци-
Закрепление двигателя на стенде рекомендуется производить при частичном вывешивании его на грузоподъемном приспособлении так как при этом отсутствует деформация рамы что значительно облегчает ввертывание болтов.
Для сборки вытекающего при разборке двигателя масла необходимо установить поддон 3 который можно использовать также и для хранения мелких деталей.
Не реже одного раза в 6 месяцев необходимо производить замену масла в червячном редукторе. Для смазки редуктора используется масло автол 18.
Регулярно не реже одного раза в месяц производить смазку опор вращения рамы и подшипников скольжения червячного колеса редуктора. Смазка производится солидолом через пресс-масленки (три точки смазки).
При люфте на рукоятке редуктора (за счет износа роликовых конических подшипников червяка более 30°) необходимо с помощью прокладок произвести подтяжку их до величины люфта в пределах 15°.
Запрещается работать на стенде без крепления его фундаментными болтами к полу. Перед поворотом двигателя в наклонное положение необходимо проверить надежность затяжки винтового зажима и болтов крепления задней опоры двигателя.
При появлении рывков и колебаний при вращении рамы с установленным на ней двигателем (что может быть вызвано деформацией станины или рамы) работу на стенде необходимо прекратить до тех пор пока дефект не будет устранен.
2. Выбор и расчет схемы привода
Спроектированный стенд используется при ремонте двигателя ЗИЛ – 130 для поворота двигателя в положение разборки сборки осмотра и регулирования. Для фиксации двигателя в удобном положении привод стенда должен быть самотор-
мозящимся и иметь небольшое число оборотов. Эти цели легко выполнимы с помощью червячного редуктора приводимого в движение усилием рабочего.
Рис. 3 Кинематическая схема стенда
Принимаем усилие на рукоятке редуктора в соответствии с требованиями техники безопасности и охраны труда равным Н.
Условно принимаю дисбаланс массы двигателя при сборке установленного на раму стенда равным Н. Тогда крутящий момент на выходном валу редуктора должен быть равен (с учетом высоты двигателя).
где Н – усилие на рукоятке редуктора;
м – высота двигателя.
Принимаю частоту вращения двигателя на стенде - обмин частоту вращения рукоятки червячного редуктора - обмин. Тогда передаточное число редуктора
где обмин - частота вращения двигателя;
обмин - частота вращения рукоятки червячного редуктора.
Принимаю стандартное передаточное число редуктора равное
Принимаю стандартный редуктор с крутящим моментом Нм с передаточным числом .
Длину рукоятки редуктора рассчитываем следующим образом:
- крутящий момент на рукоятке будет
где - крутящий момент на выходном валу редуктора;
- передаточное число.
- учитываемое допускаемое усилие на рукоятке Н имеем длину рукоятки.
где - крутящий момент на рукоятке;
Н - допускаемое усилие на рукоятке.
Принимаю длину рукоятки см.
3. Расчет деталей стенда
Расчет выполняется для проверки выбранных размеров основных деталей стенда.
Опорные поверхности для двигателя при расчете можно принять за консольную балку с жесткой заделкой. Приняв массу двигателя за 2000кг нагрузка на одну консоль будет 1000кг. Значение длины l = 150мм принимаю конструктивно.
Построим эпюры поперечных сил Q и изгибающих моментов М.
Для построения эпюры Q проведем сечение на произвольном расстоянии z от свободного конца консоли мысленно отбросим левую часть и рассмотрим равновесие правой части консоли.
Рис. 4 Построение эпюры поперечных сил Q и изгибающих моментов М.
Алгебраическая сумма всех сил приложенных слева от сечения постоянна и Q(z) = - P т.е. эпюра Q параллельна оси балки z. Строим эпюру Q.
В сечении z изгибающий момент равен Mz = -Pz - наклонная прямая при z = 0 (на свободном конце консоли) Mz = 0.
Условие прочности при изгибе имеет вид
где - момент сопротивления поперечного сечения консоли.
где b и h - размеры сечения b = 50мм h = 50мм.
Опора изготовлена из стали Ст. 3 ГОСТ 380-88 для которой
где - предел текучести стали равный 320 МПа;
- коэффициент запаса прочности.
Так как расчетное напряжение МПа меньше допускаемого
МПа прочность применяемая при расчете обеспечена.
Проверим вертикальные стойки стенда на продольный изгиб.
Рис. 5 Продольный изгиб вертикальной стойки.
Стойка равноустойчива во всех направлениях так как центральные моменты инерции имеют постоянное значение
Определим радиусы инерции
где мм – диаметр стойки.
Расчетная схема относится к основному случаю продольного изгиба.
Определим гибкость длины стойки по формуле.
где - коэффициент приведения длины стержня;
Предельное значение гибкости стойки для стали Ст. 3 с МПа МПаГПа
Если рассчитываемый стержень оказался малой гибкости то опасность потери устойчивости меньше опасности разрушения и такой стержень нужно рассчитать на прочность а не на устойчивость.
Нагрузка в этом случае экономически не допустима.
Расчеты показывают что диаметр стойки можно принять меньшим. Принимаю диаметр стойки мм.
В этом случае для определения критической силы используем формулу Ясинского – Тетмайера.
где a и b – коэффициенты зависящие от материала стойки. Для стали Ст. 3 ГОСТ 380-88 принимаю a = 304 МПа и b = 112МПа.
Запас устойчивости по гибкости обеспечен.
РАСЧЕТ ТЕХНИКО-ЭКОНОМИЧЕСКИХ ПОКАЗАТЕЛЕЙ ПРЕДПРИЯТИЯ
Для оценки проекта следует сравнить технико – экономические показатели с показателями эталона. За эталон принимаем типовой проект действующего предприятия.
Определяем стоимость завода.
где - стоимость зданий и сооружений;
- стоимость производственного оборудования с учетом его монтажа
где - стоимость дорогостоящего инструмента и инвентаря.
где - стоимость силового транспортного оборудования и передаточных устройств.
Стоимость зданий и сооружений укрупнено определяется по стоимости 1м³ объема здания. Ориентировочно стоимость 1м³ зданий для производственных зданий – 200руб; для вспомогательных – 180руб; для бытовых и конторских – 150руб.
Определим объем зданий.
Определим себестоимость выпускаемой продукции.
где - заработная плата производственных рабочих;
- стоимость запасных частей и ремонтных материалов;
- накладные расходы.
где - общая трудоемкость годовой программы;
руб – часовая тарифная ставка рабочего по среднему (3 раз- ряд) для ремонтных рабочих;
- коэффициент учитывающий доплаты к основной зарплате.
Определим стоимость запасных частей и материалов.
Определим накладные расхода.
Определим прибыль завода.
Определим нормированные оборотные фонды.
Определим плату за производственные фонды.
Определим рентабельность предприятия
Полученные результаты сводим в таблицу 15.
Таблица 15 - Технико – экономические показатели предприятия
Наименование показателей
Обозначение и формулы для расчета
Значение показателей
Количество производственных рабочих
Рентабельность предприятия
Окупаемость основных фондов
Выработка на одного производственного рабочего
Выпуск продукции на один станок
Выпуск продукции на 1м² производственной площади
ТЕХНИКА БЕЗОПАСНОСТИ И ОХРАНА ОКРУЖАЮЩЕЙ СРЕДЫ
Основная задача техники безопасности состоит в создании таких условий которые не приводили бы к несчастным случаям. В проекте соблюдаются все требования по технике безопасности. Прежде всего соблюдаются требования в части санитарно-гигиенических условий.
Помещения с вредными и опасными выбросами изолированы от других помещений и цехов.
Во всех помещениях предусмотрена втяжная и вытяжная вентиляция. Наиболее вредные участки ограждены и находятся вдоль наружных стен. Все рабочие места оборудованы в соответствии с нормами. Бытовые помещения оборудованы умывальниками душевыми шкафами для спецодежды.
Весь инструмент после рабочего дня сдается в инструментальную кладовую где проходит осмотр на пригодность. Также мерительный инструмент проходит обязательную поверку.
Испытательные стенды ограждены защитными кожухами или металлической сеткой к работе на них допускаются обученные люди.
Станочное оборудование надежно закреплено и заземлено. Освещение це- хов - люминесцентное соответствует требованиям.
Цеха оснащены грузоподъемной техникой спецтележками для перемещения деталей и узлов.
При выполнении разборочно-сборочных работ должны выполнятся общие требования по технике безопасности при работах на промышленных предприятиях включая требования в отношении освещения вентиляции шума и виброзащиты защиты от других вредных и опасных факторов производства. Особо важно соблюдать правила устройства и безопасной эксплуатации грузоподъёмных уст-
ройств включая стропы захваты и другие приспособления к ним поскольку они являются источником повышенной опасности находят весьма низкое применение при сборочно-разборочных работах. Они должны своевременно освидетельствоваться и использоваться только специально обученными людьми. Нельзя выполнять работы с узлами подвешенных на грузоподъёмных устройствах и занимающими неустойчивое положение на подставках или прокладках. Работы должны выполнятся только с использованием исправных устройств и приспособлений.
Особая осторожность должна соблюдаться при разборке и сборке узлов с пружинными устройствами. Эти работы должны выполняться при строгом выполнении установленной технологии и применении приспособлений обеспечивающих безопасность. Все гидравлические и пневматические устройства должны быть снабжены предохранительными и перекусными клапанами. Устройства с электроприводами должны быть надёжно заземлены а работа с электроинструментом напряжением 220 В допустима только в резиновых перчатках на резиновых ковриках. Подвижные части приспособлений должны быть в максимальной степени закрыты.
В соответствии с требованиями пожарной безопасности количество горюче- смазочных материалов хранимых в зоне разборочно-сборочных работ ограничивается: курение в специально отведенных местах и соответственно оборудованных запрещается.
Правила техники безопасности разрабатываются с учетом конкретных местных условий применительно к каждому виду работ и машин на основе общих требований установленных стандартами системы ССТБ. Строительными нормами и правилами и другими руководящими документами. Ответственность за соблюдение требований техники безопасности возлагается на администрацию организации – начальников главных инженеров и главных механиков начальников цехов и мастеров а также на инженерно-технических работников непосредственно руководящих производством работ. Они же являются ответственными за обу-
чение всего персонала организации правилам техники безопасности и за соблюдение установленной системы инструктажей рабочих которая включает вводные инструктажи и инструктажи проводимые мастерами и механиками на рабочих местах при переводе рабочего с одного вида работы на другой.
При работе разрешается пользоваться только исправными инструментами. При пользовании электроинструментом нужно следить за исправностью кабеля и состоянием заземления. Нельзя работать с электроинструментом без индивидуальных средств защиты. Пневматический инструмент присоединяют к шлангу только после его продувки и при включенной подаче воздуха. Включают инструмент после установки его в рабочее положение. Подъёмно-транспортные операции разрешается производить только с использованием проверенного и исправного оборудования соответствующей грузоподъемности.
Электро и газосварочные работы могут выполнять только лица имеющие удостоверение на право производства этих работ.
Нормативными документами установлены максимальные допускаемые уровни звука в различных частотных полосах звукового спектра от 63 до 8000 Гц и время их воздействия. Так например недопустимо даже кратковременное пребывание людей без специальных средств защиты в зонах с октавными уровнями звукового давления свыше 135 дБ в любой октавной полосе. Измерение звукового давления производится специальными приборами - шумомерами.
Допустимые уровни шума (дБ) и дозы шума учитывающие акустическую энергию воздействующую на человека за определённый период времени (Пач.) нормированы стандартами для различных условий работы (в производственном помещении в конторе в кабине машины и т. д.)
Например в производственных помещениях допускаемый уровень шума составляет 85 дБ.
Допустимая продолжительность пребывания людей в условиях повышенно
го шума резко снижается с увеличением уровня шума. Так если при уровне шума 85 дБ человек может работать 8 часов то при повышении шума на каждые последующие 3дБ допускаемая продолжительность сокращается в 2 раза.
Снижением уровня шума достигают применением удовлетворяющих по эффективности но малошумных рабочих процессов и соответствующего оборудования а также такими конструктивными мерами как изоляция источников шума путём введения звукопоглощающих капотов экранов и других устройств подобного типа а также применением специальных глушителей для двигателей внутреннего сгорания и некоторых пневматических машин. Кроме того операторы работающие в условиях повышенного шума должны пользоваться индивидуальными средствами защиты для снижения вредного воздействия шума на организм а в необходимых случаях укрыты звукопоглощающими кабинами.
Контроль уровня шума на рабочих местах должен проводиться не реже одного раза в год. Влияния вибрации на человека зависит от его спектрального состава места приложения поправления и продолжительности действия. Наиболее опасны вибрации с частотой от 1 до 30Гц так как в этом диапазоне (4-30Гц) находятся собственные частоты большинства внутренних органов человека и могут возникнуть неблагоприятные резонансные явления.
Характеристиками вибрации определяющими её воздействие на человека являются средние квадратичные значения виброскорости или её логарифмические уровни в октавных полосах частей относительно стандартного нулевого порога. В нормах допустимой вибрации указан вид вибрации (общая транспортная транспотно-технологическая локальная) направления по которым нормирована вибрация (вертикальное горизонтальное) и относящиеся к ним допускаемые уровни вибрации в децибелах применительно к различным условиям.
Октавный ряд частотных полос для норм вибрации укладывается между 1 и 63Гц кроме локальной вибрации которая нормируется от 8 до 1000Гц.
Вибрации измеряют по стандартной методике с помощью виброметров или
вибрографов (с записью результатов). Для уменьшения вибрации применяют различного вида виброгасители виброизоляторы и другие устройства.
Источником загрязнения водоемов и канализационных сетей являются сточные воды в которых после мойки машин их агрегатов деталей и систем содержится большое количество взвешаных частиц грязи и различных нефтепродуктов. Так при общей мойке машин в 1 литре стоков содержится до 2500мг и 800-1200мг нефтепродуктов и взвеси. Для очистки сточных вод от взвешенных веществ и нефтепродуктов обычно применяют грязеотстойники с бензомаслоуловителями. Принцип действия их основан на разнице плотностей воды взвеси и нефтепродуктов. Грязеотстойник и бензомаслоуловитель заглублены в грунт. Сточная вода по подводящей трубе подается в грязеотстойник где осаждаются взвешенные частицы грязи а затем переливаются во вторую камеру из которой выплывающие наверх нефтепродукты отводятся по маслоотводящей трубе в маслосборный колодец. Окончательная очистка воды происходит при прохождении её через стекловолокнистый фильтр.
Естественное освещение
Выполним расчет освещения главного корпуса ремонтного завода естественного и искусственного освещение для одного цеха или отделения ремонтного предприятия.
Общая площадь окон при естественном освещении определяется по формуле.
где - площадь пола в м²;
- коэффициент естественной освещенности.
Для цехов и отделений предприятия коэффициент естественной освещености
по методическим указаниям принимаем .
При выборе стандартных окон необходимо учитывать что расстояние от пола до подоконника должно быть не менее м а расстояние от верхней части окна до затяжки (потолка) - не менее м.
Высота окна определяется по формуле.
- расстояние от пола до подоконника м;
- расстояние от верхней части окна до потолка в м.
Приведенная суммарная ширина окна определяется по формуле.
Количество окон определяется по формуле.
где - ширина окна м.
Ширина окна принимаем по нормам строительного производства м.
Искусственное освещение
Световой поток необходимый для освещения главного корпуса определяется по формуле.
где - световой поток в люменах;
- площадь пола главного корпуса в м²;
- коэффициент запаса;
- норма искусственной освещенности люкс;
Для отделений наружной мойки разборочного слесарно – механического столярного для складов и бытовых помещений принимаю люкс а для сборочного топливной аппаратуры кузнечного сварочного механического малярного принимаю люкс.
- КПД источника света;
- коэффициент использования светового потока.
Определим количество ламп из соотношения.
где - световой поток одной лампы.
Принимаю мощность Вт лм при напряжении В.
Исходя из полученных результатов полученных при расчете и в табл. 15 я получил следующие показатели спроектированного предприятия. Годовая программа предприятия составила В = 51116983 тыс. руб.; количество производственных рабочих РП = 538 человек и прибыль П = 988867 тыс. руб.; стоимость завода С = 4576156 тыс. руб.; рентабельность завода R = 2289 % а окупаемость основных фондов ТФ = 45 года. Полученные значения рентабельности завода и окупаемости основных фондов являются хорошими показателями для ремонтных предприятий.
Таким образом задача поставленная передо мной в задании на дипломное проектирование выполнена.
Соколов В. С. Ровках С. Е. Технология машиностроения производство и ремонт подъёмно-транспортных строительных и дорожных машин. Задание на курсовой проект с методическими указаниями для студентов V курса. № 2972: – М.: РГОТУПС 2004. – 45 с.
Журба В. А. Тараканов Г. П. Xайкис М. Л. Машины для транспортного строительства. Справочник Под ред. Г. Л. Вутечича. – М: Транспорт 1984. – 429 с.
Епифанов С. П. и др. Строительные машины (справочное пособие). Общая часть. – М.: Стройиздат 1991. – 176 с.
Строительные машины. Справочник Под ред. Э. Н. Кузина. Т.1. – М: Машиностроение 1991. – 496 с.
Воробьев Л. Н. Технология машиностроения и ремонт машин: Учебник для вузов. – М.: Высшая школа 1981. – 344 с.
Страмоус М. Ф. Ровках С. Е. Ремонтно-механические предприятия строительных организаций. – М.: Стройиздат 1972. – 240 с.
Колясинский Б. С. Зеленков Г. И. Проектирование предприятий по ремонту дорожно-строительных машин. – М.: Высшая школа 1971. – 240 с.
Прейскурант оптовых цен № 26-05-18 на капитальный ремонт и оборудования. – М.: Минтранстрой 1982. – 38 с.
Ровках С. Е. Фейгин А. Л. Техническое обслуживание и ремонт транспортного строительства. – М.: Транспорт 1985. – 338с.
Каракулев А. В. и др. Ремонт строительных путевых и погрузочно - разгрузочных машин. – М.: Транспорт 1988. – 330 с.
Таблица 4.doc
мойка агрегатов и двигателей
кузнечные и термические
слесарно - ремонтные
3 Разборочный цех.CDW

8 Экономика.cdw

Количество производственных
Выработка на одного
производственного рабочего
Выпуск продукции на
Выпуск продукции на 1 м
производственной площади
Окупаемость основных фондов
9 Техника безопасности.cdw

- Сердечник электромагнита
- Конечный выключатель ВК11
- Электродвигатель станка
- Кронштейн рамы ходовой тележки
- Рычажный конечный выключатель
- Амортизирующие упоры
- Наклонный боковой отсос
- Нулевой магистральный провод сети
- Соединительный нулевой провод
- Четвертая (нулевая) жила кабеля
- Заземляющий проводник
- Четырехжильный кабель
- Болтовое соединение
- Местная вентиляция
- Установка плазменного напыления
- Естественный заземлитель
- Искусственный заземлитель
Схема автоматизированного защитного экрана с электромеханическим приводом
Ограничитель передвижения кран -балки
Местное вытяжное устройство с верхним отсосом
Схема заземления и зануления установки плазменного напыления
7 Деталировка.cdw

Число витков червяка
Степень точности по ГОСТ 3675-81
Неуказанные литейные радиусы R5.
Чугун антифрикционный
Межосевое расстояние
Коэффициент смещения
Сталь 45 ГОСТ 1050-88
Бр. ОЦС 6-6-3 ГОСТ 613-65*
6 Общий вид стэнда.cdw

2 Главный корпус.cdw

Отделение наружной мойки
Комплектовочный склад
Отделение комплектации и подгонки
Кузнечно-термическое отделение
Сварочно-наплавочное отделение
Склад отремонтированных агрегатов
Окрасочное отделение
Участок металлоконструкций
Отдел главного механика
Инструментальный участок
Участок общей сборки
Участок ремонта и сборки двигателей
Деревообрабатывающий участок
Отделение ремонта топливной аппаратуры
Испытательная станция
производственный корпус
1 Генеральный план.cdw

Административно-бытовой корпус
Склад запасных частей
Склад лесоматериалов
Газораспределительный пункт
Открытая площадка для приема и сдачи техники
Гараж для служебных автомобилей
следующих из гаражаи приемно-сдаточной площадки
Трансформаторная подстанция
Условные обозначения
5 Технологическая схема.cdw

Заправка и испытание
отремонтированных машин
Дефектовочный участок
4 Структура завода.cdw

Вспомогательные участки
Основное производство