Разработка техпроцесса производства детали типа Рычаг запирающий




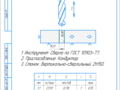
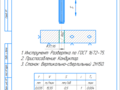
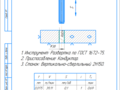
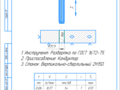
- Добавлен: 24.01.2023
- Размер: 1 MB
- Закачек: 3
Описание
Состав проекта
![]() |
![]() ![]() ![]() ![]() |
![]() |
![]() ![]() ![]() ![]() |
![]() ![]() ![]() ![]() |
![]() ![]() ![]() ![]() |
![]() |
![]() ![]() ![]() ![]() |
![]() ![]() ![]() ![]() |
![]() ![]() ![]() ![]() |
![]() ![]() ![]() ![]() |
![]() ![]() ![]() ![]() |
![]() ![]() ![]() |
![]() ![]() ![]() ![]() |
![]() ![]() ![]() ![]() |
![]() ![]() ![]() ![]() |
![]() ![]() ![]() |
![]() |
![]() ![]() ![]() ![]() |
![]() ![]() ![]() ![]() |
![]() ![]() ![]() ![]() |
![]() ![]() ![]() ![]() |
![]() ![]() ![]() ![]() |
![]() ![]() ![]() ![]() |
![]() ![]() ![]() ![]() |
![]() ![]() ![]() ![]() |
![]() ![]() ![]() ![]() |
![]() ![]() ![]() ![]() |
Дополнительная информация
чертеж детали.cdw

Сверло 37.cdw

Зенкер 37,7.cdw

Развертка38.cdw

3 операция развертывания.cdw

5 операция развертывания.cdw

1 операция рассверливания.cdw

2 операция зенкерования.cdw

4 операция развертывания.cdw

КАЛИБР38Н7.cdw

чертеж заготовки.cdw

мой кондуктор(на печать).cdw

035 фрезерная.cdw

05 фрезерная.cdw

020 фрезерная.cdw

025 фрезерная.cdw

045 сверлильная.cdw

030 фрезерная.cdw

015 фрезерная.cdw

040 сверлильная.cdw

050 сверлильная.cdw

010 фрезерная.cdw

Рекомендуемые чертежи
- 24.01.2023
- 24.01.2023