Разработка технологии прокатки листа 3, 2×1320 мм из сляба 175×1320 мм



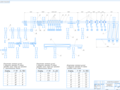
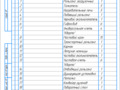
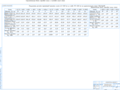
- Добавлен: 25.01.2023
- Размер: 1 MB
- Закачек: 0
Узнать, как скачать этот материал
Подписаться на ежедневные обновления каталога:
Описание
Разработка технологии прокатки листа 3, 2×1320 мм из сляба 175×1320 мм
Состав проекта
![]() |
![]() |
![]() |
![]() |
![]() ![]() ![]() ![]() |
![]() ![]() ![]() ![]() |
![]() ![]() ![]() |
![]() |
![]() |
![]() |
![]() |
![]() |
![]() ![]() ![]() |
![]() |
![]() ![]() ![]() |
![]() |
![]() |
![]() |
![]() ![]() ![]() ![]() |
![]() |
![]() ![]() ![]() |
![]() |
![]() |
![]() |
![]() |
![]() |
![]() |
![]() |
![]() |
Дополнительная информация
Контент чертежей
Спецификация.spw

Результаты расчета.cdw

Стан 1700 МарМК.cdw

Рекомендуемые чертежи
- 04.11.2022
- 10.12.2019
- 29.08.2014
- 18.06.2021
- 24.01.2023
Свободное скачивание на сегодня
Обновление через: 12 часов 50 минут