Разработка технологического процесса изготовления и обработки детали Стакан




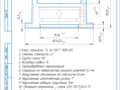
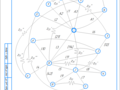
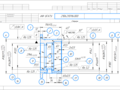
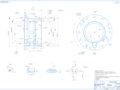
- Добавлен: 24.01.2023
- Размер: 1 MB
- Закачек: 1
Описание
Состав проекта
![]() |
![]() |
![]() ![]() ![]() ![]() |
![]() |
![]() ![]() ![]() |
![]() |
![]() |
![]() ![]() ![]() |
![]() |
![]() |
![]() ![]() ![]() ![]() |
![]() |
![]() ![]() ![]() |
![]() ![]() ![]() ![]() |
![]() |
![]() |
![]() ![]() ![]() ![]() |
![]() ![]() ![]() |
![]() ![]() ![]() ![]() |
![]() |
![]() |
![]() ![]() ![]() |
![]() |
![]() |
![]() ![]() ![]() |
![]() ![]() ![]() |
![]() |
![]() ![]() ![]() |
![]() ![]() ![]() ![]() |
![]() |
![]() ![]() ![]() |
![]() ![]() ![]() |
![]() ![]() ![]() |
![]() ![]() ![]() ![]() |
![]() ![]() ![]() |
![]() |
![]() |
![]() ![]() ![]() |
![]() |
![]() ![]() ![]() ![]() |
![]() ![]() ![]() ![]() |
![]() ![]() ![]() |
![]() |
![]() |
![]() |
![]() ![]() ![]() ![]() |
![]() |
![]() ![]() ![]() ![]() |
![]() |
![]() |
![]() ![]() ![]() ![]() |
![]() ![]() ![]() ![]() |
![]() ![]() ![]() ![]() |
Дополнительная информация
КЭ(055).cdw

КК (075).frw

КЭ(020).cdw

КЭ(025).cdw

КЭ(030).cdw

Заготовка.cdw

КК (075) 2.frw

КЭ(040).cdw

Стакан.cdw

Расчёт припусков.frw

Граф дерева.cdw

КЭ(050).cdw

КЭ(035).cdw

МОО.cdw

КЭ(045).cdw

Рекомендуемые чертежи
- 24.01.2023
- 24.01.2023
Свободное скачивание на сегодня
- 22.08.2014
- 29.08.2014
Другие проекты
- 22.08.2014